Sharp VL-A10S User manual

VL-E990E
1
VL-A10S/H/E
VL-AH30S/H/E
Page
1. SPECIFICATIONS .............................................................................................................................. 2
2. PART NAMES AND FUNCTION .........................................................................................................3
3. DISASSEMBLY OF THE SET.............................................................................................................4
4. MECHANISM ADJUSTMENT ........................................................................................................... 10
5. ADJUSTMENT OF VCR AND CAMERA...........................................................................................22
6. SYSTEM BLOCK DIAGRAMS .......................................................................................................... 35
7. SCHEMATIC DIAGRAMS ................................................................................................................. 42
8. SEMICONDUCTOR LEAD IDENTIFICATION ..................................................................................80
9. PRINTED WIRING BOARD ASSEMBLIES.......................................................................................82
10.REPLACEMENT PARTS LIST.......................................................................................................... 93
11.PACKING OF THE SET .................................................................................................................. 111
S30Y3VL-A10S/
SERVICE MANUAL
LIQUID CRYSTAL CAMCORDER Hi 8 PAL
CONTENTS
SHARP CORPORATION
In the interests of user-safety (Required by safety regula-
tions in some countries) the set should be restored to its
originalcondition andonly partsidenticaltothosespecified
be used.
MODELS
SERVICE MANUAL MODELS VL-A10S/H/E/AH30S/H/E
LIQUID CRYSTAL CAMCORDER Hi PAL
8
VL-A10S/H/E
VL-AH30S/H/E
VL-A10S/H/E
VL-AH30S/H/E

VL-E990E
VL-A10S/H/E
VL-AH30S/H/E
2
Signal System: PAL standard
Recording System: 2 rotary heads, helical scanning system
Cassette: 8 mm video tape, MP type or Hi8 MP, ME type
Recording/Playback Time: 120 minutes (P5-120)
Tape Speed: 20.051 mm/second
Pickup Device: 1/4" (6.4mm, effective size: 4.5 mm) CCD image sensor (with approx.
320,000 pixels including optical black)
Lens: 16 ×power zoom lens (F1.4, f=4.0-64.0 mm), and full-range auto focus
Lens Filter Diameter: 46 mm
Monitor: 3" (7.5 cm) full-color LCD screen (TFT active matrix)
Microphone: Electret monaural microphone
Color Temperature Compensation: Auto white balance with white balance lock
Minimum Illumination: 0.8 lux* (with gain-up, F1.4)
Video Output Level: 1.0 Vp-p 75-ohm unbalanced
Audio Output Level: –8 dBs, impedance less than 2.2 kohms
Speaker Output: 200 mW
Power Requirement: DC 3.6V (with battery pack)
DC 7.0V (with AC adapter)
Power Consumption:
4.9W (during camera recording in full auto mode with zoom motor off
and backlight in normal mode)
Operating Temperature: 0°C to + 40°C
Operating Humidity: 30% to 80%
Storage Temperature: –20°C to +60°C
Dimensions (approx.): 183 mm (W) ×109 mm (H) ×99 mm (D)
Weight (approx.): 710g
(without battery pack, lithium battery, video cassette, and lens cap)
1. SPECIFICATIONS
AC Adapter (UADP-0313TAZZ)
Power Requirement: AC 110-240 V, 50/60 Hz
DC Output: 7.0 V
Power Consumption: 15 W
Dimensions (approx.): 68 mm (W) ×37 mm (H) ×130 mm (D)
Weight (approx.): 233 g
Specifications are subject to change without notice.
*Minimum illumination: Since there is no widely accepted testing procedure for determining minimum illumination
capability, lux ratings are comparable only between models from the same manufacturer.

VL-E990E
3
VL-A10S/H/E
VL-AH30S/H/E
2. PART NAMES AND FUNCTION
For details on the use of each control.
Front view
When the cassette compartment door is open
Terminal cover
Microphone
Zoom lens
AUDIO jack
DC IN jack
Lens hood
Cassette holder
Shoulder strap loop
Lithium battery holder
Cassette compartment door
release
Cassette compartment door
Speaker
Rear view
Bottom view
Shoulder strap
loop
Hand strap
RECord START/STOP button
Battery compartment door
CHARGE indicator
MENU button
Remote sensor
LCD monitor screen
Tripod socket
Power switch (CAMERA/VCR
select switch)
DISPLAY button
Operation buttons
Power Zoom Wide angle/
Telephoto control
VOLume control
FADE button
Battery compartment door release
VIDEO jack

VL-E990E
VL-A10S/H/E
VL-AH30S/H/E
4
3. DISASSEMBLY OFTHE SET
3-1. REMOVAL OF THE CAMERA SECTION
Note:
Before removing the cabinet, turn off the power supply, and ascertain that the battery has been removed.
Pull out
Lens connector
(d)
(b) Pull out (a)
(a)
(1)
Camera front cabinet
1. Remove one screw ((d)XiPSF20P04000), one screw ((b)LX-
HZ0018TAFF), two screws ((a)LX-HZ0018TAFN), and pull
out the camera front cabinet (1).
(c)
Lens holder
4. Pulling the lens holder, and pull out the lens upwards. Then,
remove the lens connector.
(b)
Connector
(c)
Connector
2. Remove one screw ((b)LX-HZ0018TAFF), one screw
((d)XiPSF20P04000) and two screws ((a)LX-HZ0018TAFN)
and pull out the camera rear cabinet (2) backwards.
Remove the FPC in the camera rear cabinet.
(b)
(d)
Connector
(a)
(a)
Pull out
(2)
Camera rear cabinet
1
2
6. Remove two screws ((b)LX-HZ0018TAFF) and pull out the
camera side cover from the tilt frame C.
Tilt frame C (b)
(b)
Pull out
9. After removing the camera PWB from the tilt frame, remove
the connector on the rear of the PWB.
Connector
8.Remove one connectorofthecameraPWB,andremovetwo
screws ((c)LX-HZ0045TAFN) fixing the PWB.
7. Remove the battery catcher from the camera side cover.
3. Firstly,removetheCCDconnector fromtheCamera PWB,then
removeonescrew((c)LX-HZ0045TAFN),thereversesideinthis
figure (Not remove the lens holder in this section).
5. Remove the connector of the 6-cell detection switch, and
remove two screws ((b)LX-HZ0018TAFF) fixing the battery
catcher.
CCD connector

VL-E990E
5
VL-A10S/H/E
VL-AH30S/H/E
3-2. DISASSEMBLY OF THE VCR MAIN BODY
(1) Slide the “VCR lid knob” in the arrow direction, and slide the
VCRlidinthearrowdirectionasfarasthecabinetLfastening
screw is visible. (Left figure) Since the connector of the
microphone is still connected, take care to prevent exces-
sively sliding the VCR lid.
<2. Disassembly of the cabinet L>
(3) Pull out the VCR lid shaft head which projects beyond the
surface of the VCR lid.
VCR lid shaft
VCR lid Frame V
VCR lid shaft
<DetailofareaA>
(2) Bring the jig (example: slotted precision screwdriver) into
contact with the removal groove of the VCR lid shaft, and
slidethescrewdriverwithcaretopreventinjuringtheVCRlid
and frame V.
(1) Remove one screw ((k)LX-HZ0063TAFC). (2) Remove five screws ((b)LX-HZ0018TAFF).
(3) Turn the tilt frame C so that the screwdriver can be easily
inserted, and remove two screws ((i)XiPSN20P04000).
(4) Remove one screw ((i)XiPSN20P04000).
Cabinet L
FPC connector
(b)
(i)
(i)
(k)
VCR lid knob
VCR lid
Tilt frame C
(5) RemovethecabinetLtothemidway,anddisconnecttheFPC
connector.
<1. Removal of the VCR lid shaft>
Area A

VL-E990E
VL-A10S/H/E
VL-AH30S/H/E
6
<3. Removal of the VCR lid>
Frame V Microphone wire spacer
Microphone connector
Caution for installation of the VCR lid
<Detail of area B>
<Detail of area B>
Microphone connector
Microphone connector
Microphone wire
spacer
VCR Lid
VCR lid
When installing the VCR lid, move the VCR lid in the arrow
direction, keeping the VCR lid parallel to the main body as
shown above.
(2) Removetheconnectorcablefromtheholeofthemicrophone
wire spacer.
(1) Disconnect the microphone connector.
(3) Remove the microphone wire spacer from the Frame V.
Wirefixingtape
(4) Pulloutthemicrophonewirecablewithcaretopreventitfrom
interfering with the mechanical parts, and remove the VCR
lid.
Pull out
Area B
Microphone connector
AV unit wire
AV unit FPC
(b)
(b)
<4. Removal of the AV unit and AV unit cover>
<5. Disassembly of the LCD holder>
Tripod angle
(b)
(b) (b)
(1) Peel the wire fixing tape.
(2) Remove the AV unit wire.
(3) Remove the AV unit FPC.
(4) Removetwoscrews ((b)LX-HZ0018TAFF) fixing theAVunit
and LCD holder.
(d)
(d)
(1) Remove three screws ((d)XiPSF20P04000) pull out the
tripod angle.
(2) Removethreescrews((b)LX-HZ0018TAFF)onthetiltframe
V.
Move the tilt frame V by a looseness of the tilt FPC.
(d)

VL-E990E
7
VL-A10S/H/E
VL-AH30S/H/E
(b)
Inverter transformer
Main PWB
Connector
Lithium PWB
LCD unit
Battery terminal
unit
<6. Removal of the tilt unit>
Tilt frame V
Main PWB
Connector
Tilt frame C
Connector
(e) Mechanism unit
(e) (e)
A
D
C
B
E
F
C
<10. Removal of the cassette compartment lid>
(1) Using the slotted precision screwdriver, push and turn the
two claws (C and D) which fasten the cassette compartment
lid, and the cassette compartment lid will be removed from
the hook area of the cassette component.
(2) Turning the cassette compartment lid in the arrow direction,
liftit,andtheclawsAandBwill bedisengagedto removethe
cassette compartment lid.
Note:
Take care to prevent breaking the claws of the cassette com-
partment lid.
B
D
Frame V
Connector
(1) Remove three screws ((e)LX-BZ0191TAFD) and one con-
nector, and remove the frame V from the main body.
(1) Disconnect three connectors.
Remove the tilt unit from the cabinet of the main body.
(3) Remove two screws ((b)LX-HZ0018TAFF) and two connec-
tors, and remove the LCD unit (with inverter) from the main
body.
(1) Remove the connector of the Lithium PWB from the Main
PWB.
(2) Move the lithium unit in the direction of the arrow.
<8. Removal of the Lithium PWB>
<7. Removal of the speaker cover>
<9. Disassembly of the frame V>
(b)
(2) Remove the screw ((b)LX-HZ0018TAFF) fixing the speaker
cover.
(3) Move the speaker holder in the direction of the arrow to
remove it.
(1) Remove the connector of the speaker from the Main PWB.

VL-E990E
VL-A10S/H/E
VL-AH30S/H/E
8
<11. Disassembly of the LCD panel>
(2)
Claw (A) Claw (A)
(1)
Light guide plate
Reflection sheet
Lugs
Lugs
(3)
(C)
(4)
(2)
Claw (B) Disengage the claw, and remove the
LCD panel.
Arm(E) Arm(D)
FPC
Prism sheet
Diffusion sheet
1. Disengage two claws (A), and remove the lamp inverter unit (1) from the LCD holder (2).
2. Remove the sheets from the LCD holder (2).
3. Pull the LCD glass retaining (3).
4. Remove the FPC from Arm(D) and (E).
5. Disengage the claw (B), and slide the LCD panel (4) in the (C) direction to remove the LCD holder (2).
Note:
When handling the prism sheet, diffusion sheet, light guide plate, reflection sheet and reflection polarizing sheet do not touch any parts
other than lugs and sides.
Put the light guide plate and reflection sheet between reflectors of lamp. Therefore, install them together with the lamp ass'y.
Note:
Whenfixingthecassettecompartmentlid,firstengagetheclaws
A and B, and then engage the claws C and D, verify that the four
claws (A, B, C and D) of the cassette compartment lid are
securely engaged as shown in the view above.
Claw C
Claw A
Claw B
Claw D
View E
View F

VL-E990E
9
VL-A10S/H/E
VL-AH30S/H/E
3-3-2. REMOVAL OF CCD
1) Unsolder the CCD sensor leads from the sensor PWB.
2) Take out the sensor PWB.
3) Remove the two screws (6), and remove the sensor holder and CCD sensor.
3-3-3. MOUNTING OF CCD
1) Place the lens unit upright (since the CCD sensor mount ID faces upward, care must be taken so as not to damage the front lens of
unit),putthe crystal filter firstandthenthedust protection rubberintotheCCDholder of lensunit.Setthecrystal unit withitsthinside
toward the lens unit.
2) Place the CCD sensor so that the its No. 1 pin is at the right lower (Positioning hole to be at right), and put the CCD sensor into the
CCD holder. For smooth and tight fitting, press the right lower part of back of CCD sensor, and then press the left upper part.
Note: Pay attention to the direction of CCD sensor.
3) Placethesensorholdersothatitstworoundmarkingsbevisible,andfixthesensorholderwiththetwoscrews((6)LX-HZ0013TAFF).
4) Mount the sensor PWB so that the CCD sensor leads go thorough the PWB holes.
5) Solder the CCD sensor lead to the sensor PWB.
Note: Take care not to apply excessive heat.
Rubber
Lens
Side CCD
Side
The THIN SIDE
faces the lens
Crystal
CCD Sensor
Sensor Holder
(6)
Mark
The mark must be on
this face.
3-3. REPLACEMENT OF CCD SENSOR
3-3-1. BEFORE REPLACEMENT
1) The CCD image sensor is more sensitive to electrostatic breakage than C-MOS LSI. Therefore sufficient means to prevent
electrostatic damage must be taken when it is replaced.
•Ground the soldering iron.
•Ground also the human body, using the wrist strap(through an 1 Mohm resistor).
•Until the CCD sensor is mounted on the PWB, fit it to the conductive sponge, and short-circuit the foot lead.
2) TakeutmostcaresothatthesurfaceglassofCCDsensorandopticalfilterarenotcontaminatedanddamaged.Ifanycontamination
is found, for example fingerprint, wipe it off with silicon paper or clean chamois skin.
3) When replacing the CCD sensor, use the static electricity prevention grounded soldering-iron, and perform quickly soldering.
JAPAN
SHARP
Index Mark
LZ2423H5
YYWWXXX
17
14 8

VL-A10S/H/E
VL-AH30S/H/E
10
4. MECHANISM ADJUSTMENT
4-1. MECHANISM CHECKING/ADJUSTING JIGS, TOOLS AND PARTS
4-1-1. Mechanism checking/adjusting jigs and tools
<Note: The entries of list>
Configuration
1. Name
2. Part No.
3. Code
* Model, Uses Remarks
1. Screw locking agent
(1401B)
* Three Bond
1. Cleaning liquid
(Industrial-useethylalcohol)
1. Oil
COSMOHYDRO HV100
* Cosmo Oil Co., Ltd.
1. Greases
Morycoat YM-103/X5-6020
* Dow Coaning 1. Superfine swab
* Commercially available
item
1. Cleaning paper
2. JiGDUSPER
3. AP
* Dusper ∑(Sigma) (Ozu Co., Ltd.)
1. Height adjusting jig
2. 9DAGH-E31S
3. BM
* For adjustment of Tu
guide height and Si
roller height
1. Master plane
2. JiGMP-MX7U
3. CG
* For adjustment of Tu guide
height, Si roller height and
checking of reel disk height
<Others>
(1) Slide calipers
(2) High-precisionscrew-
drivers(Phillipshead,
slotted head)
(3)Radiopliers(withthin
jaws)
(4) A pair of tweezers
<Note: The entries of list>
Configuration
1. Name
2. Part No.
3. Code
* Model, Uses Remarks
1. Cassette torquemeter
for PB
2. JiG8T-012
3. CV
* (10 g·cm/25 g·cm)
1. Cassette torquemeter
for VS-REW
2. JiG8T-032
3. CV
* (50 g·cm/25 g·cm)
1. Torque gauge
2. JiGTG0045
3. CN
* For measurement of
loading brake torque
1. Torque gauge head
2. JiGTH-MX7U
3. BS
* For torque gauge listed
left
1. Torque driver
(1.5 kg·cm)
2. JiGTD1500RT0H
3. CB
1.8
4
Tolerance±0.1
Edge
thickness 0.5
2
4-1-2. Parts for periodic inspection and maintenance.
1. Alignment tape
2. VR2DBOPS
3. BT TAPE CONTENTS
VIDEO IMAGE AUDIO TIME
MONOSCOPE L-CH 400Hz 30MIN
R-CH 1,000Hz
1. Tu guide height
adjusting driver
2. 9EQDRiVER-V712
3. BL
1. Guide roller height adjusting driver
2. JiGDRiVERHMX7U
3. BU
* Bit shape (See the figure above.)
1. Hex wrench
3. —
*
For loosening or tight-
ening of Motor stator
(1.3mm)
1.TensionBandandPlate
Adjusting Jig
2. JiGDRiVERMX7U2
3. BN

11
VL-A10S/H/E
VL-AH30S/H/E
4-2. ITEMS AND TIMINGS OF INSPECTION AND MAINTENANCE
ThemechanismofVCRneedsthefollowingperiodicinspectionandmaintenanceinorderthatitmaintainsitshighquality.Also,
after the machine is repaired, execute the following maintenance and checks regardless of how long it has been used.
4-2-1. Inspection and maintenance list
Checking/Maintenance point Usage time (hrs.)
500 1,000 1,500 2,000 3,000
• Improper S/N ratio
• No color appears.
Tape travelling route
(Refer to Section)
Drum (Refer to Section)
Video head
Tape travel system
Timing belt
Pinch roller
Capstan D.D. motor
★★★
• Tape does not run.
• Tape slackens.
• Screen shakes.
Rollers
• If abnormal rotation or de-
flection (significant) is
found, replace the roller.
Other than rollers
• Clean the tape contacting
areas. Be sure to use the
specified cleaning agent.
• Lateral noise
• Unclean head
• Screen shaking
• Replace if failure is found.
∆∆∆
Relay Pulle shaft
Pulle gear shaft
Drive gear shaft ∆∆∆
Driving system
Figure 2
4-2-2. Notes and cautions
(1) Any cut washers, once removed for parts replacement or for other
reason, must be replaced with new ones.
(2) ThemechanismofthisVCRdoesnotinvolveanyvolumeadjustment.
If the specified range is not satisfied, either cleaning or replacing the
parts is required.
(3) Oils
a) Be sure to use the specified oils (different viscosity may cause
troubles).
b) For the bearings, be sure to use oil that is free form dust and other
foreign substances. (Dust or foreign substance contained in the oil
may cause wear or seizure of the bearings.)
c) Adropofoilrepresentstheamountofoilwhichisheldontheneedle
top as shown in the figure 1.
(4) The circuit repair must be executed without removing the V frame.
(5) For operating the mechanism alone, actuate it with the motor. The
terminal-to-terminal voltage must be DC4V or less.
(6) Wheninstallingthecassettecontrol,pressthepartAshowninFigure
2.
*Do not press other parts.
(7) Take care so that the whole mechanism is not deformed.
Loading motor ★★★
Abnormal sound
PB/VS-REW take-up torque
PB/VS-REW back tension torque
Tu brake
HC (Head Cleaner)
★★★★★
★★★
★★★
★★★
Note:
After oil is applied to the
drive gear shaft, slightly
wipe it off with swab.
Oil: COSMOHYDRO HV100
Greases: MORYCOAT YM-103/X5-6020
Screw locking agent: THREE BOND 1401B
Cleaning liquid: Industrial-use ethyl alcohol
: Replace.
: Clean.
∆: Apply oil.
★: Check.
Performance check
A
Oil
Diameter φ1.5 or less
Figure 1
Possible symptom
encountered Remarks
• Abnormal sound • Apply oil.
(Oil : COSMOHYDRO
HV100)
• Not ejectable
• The specific mode cannot
be set.
• Replace if failure (abnor-
mal sound) is detected.
• If conformance to the
standard is not ensured,
replace part.

VL-A10S/H/E
VL-AH30S/H/E
12
4-3. MECHANISM CHECKS AND ADJUSTMENTS
The description given below relates to the general field services, but does not relate to the adjustment and replacement that require
high level equipments, jigs, and technical skills.
In order to maintain the initial characteristics of the machine, it is necessary to execute the maintenance and check and to prevent
damage to tapes and other parts. For adjustments which need jigs, be sure to use the jigs.
Notes and cautions
(1) For mechanism checks and adjustments, be sure to use the AC adapter as the power supply.
(2) For running the tape, be sure to install the cassette control ass’y in advance. (If the cassette control ass’y is to be removed
subsequently after its installation.)
4-3-3. Checking and adjusting the back tension torque for playback (recording)
4-3-1. Checking the reel disk height
(1) Remove the cassette control ass’y.
(2) Taking due care not to let the master plane touch the tape running areas such as the drum and the guide rollers, position the
master plane so that the two guides (A and B in the figure 1) are set in the holes of master plane, then properly set it in the
mechanism.
(3) Using the slide callipers or the like, check that the distance from the upper surface of master plane to the reel support surface
of the S/Tu reel disk is within the specified range. (Figure 2)
Note:
When measuring, do not apply excessive force to the reel support surface of reel disk.
(4) If the measurement is not within the specified range, replace the reel disk ass’y.
(5) Check the items (2) to (4) above in the following two modes.
a) Standby mode
b) Playback (recording) mode
4-3-2. Checking the take-up torque for playback (recording)
(1) Set the torque cassette (JiG8T-012) in position, and check in the SP-mode recording mode (tape recorded in SP mode) that
the torque at the tape taking-up side is within the standard range.
Standard of take-up torque for SP-mode recording (playback)
9 ±3 g·cm with ripples less than 4 g·cm
(If the torque ripples appear, read the center value of torque between the ripples.)
4.4 ±0.15
Reel support surface
4.4 ±0.15
Figure 2Figure 1
(1) Checking
1) Setthetorquecassette(JiG8T-012) in position, and check intheSP-moderecordingmode
(tape recorded in SP mode) that the torque at the tape supply side is within the standard
range.
Standard of back tension torque for SP-mode recording (playback):
8 ±2 g·cm with ripples of less than 2 g·cm
(Torque ripple must be within 8 ±2g·cm)
(2) Adjustment
1) Ifthebacktensiontorqueisnotwithinthestandardrange,adjustthetensionspringhooking
position.If thebacktensionistoohigh,hookthe springinthedirectionA. Ifthebacktension
is too low, hook the spring in the direction B.
Note:
1. After back tension torque adjustment be sure to check the tension pole position.
A
B
A
B

13
VL-A10S/H/E
VL-AH30S/H/E
4-3-4. Checking and adjusting the tension pole position
(1) Check
When winding of P5-120 tape is started, check whether the tension pole is in the
specified position against Si roller as shown or not.
If it is not in the specified position, remove the cassette and adjust the position
in the following procedure.
(2) Adjustment
1. Don’t set up any tape, and select the PB mode. (Refer to Item 4-5-1-(4).)
2. Slightly loosen the screw (a) (to such a strength as the T band holder B can
be moved).
3. If the tension pole is in the inner position than specified, dislocate the T band
holder B in the arrow (A) direction and if it is in the outer position, dislocate it
inthearrow(B)position.Then,tightenthescrew(a).(For reference,dislocate
it 0.4 to 0.8 mm outer from the position specified above.) For the position
adjustment, it is convenient to use the position adjustment screwdriver
(JiGDRiVERMX7U2). (Set it in the hole (C).)
4. Check the position in the “(1) Check” procedure described above.
5. If it is not in the specified position, repeat the adjusting procedure 1 thru 3.
Note:
• Tightening torque of screw (a) 70 mN·m
• To check the position, be sure to run the tape.
• If the cassette compartment assembly is removed, it makes the work easier. (Refer
to Item 5-5-3.)
3 – 0.5
0
Si roller
Tension pole
T Band
Holder B
Screw
(a)
(B)
Hole (C)
(A)
4-3-5. Checking the take-up torque for rewind playback (VS-REW)
(1) Remove the cassette compartment ass'y and set to the sensor OFF mode.
(2) Setthetorquegauge(JiGTG0045)onthe S reel disk, and check in therewindplayback(VS-REW)thatthetorqueatthe supply
side is within the specified range.
Standard of take-up torque in rewind playback (SP mode)
31 ±5 g·cm with ripples less than 5 g·cm.
(If the torque ripples appear, read the center value of torque between the ripples.)
4-3-6. Checking the back tension torque for rewind playback (VS-REW)
(1) Set the torque cassette (JiG8T-032) in position, and check in the rewind playback (VS-REW) mode that the torque at the tape
take-up side is within the specified range.
Standard of back tension torque in rewind playback (SP mode):
14 ±5 g·cm with ripples less than 5 g·cm
(If the torque ripples appear, read the center value of torque between the ripples.)

VL-A10S/H/E
VL-AH30S/H/E
14
4-4. ADJUSTMENT OF MECHANISM TAPE TRAVEL SYSTEM
4-4-1. Preparation for adjustment
Tape travel system (Figure 1)
,,
,,
,,
,,,,
,,,,
,,,,
,,,,
,,,,
Drum
Reel
Tension pole
Si roller
Sup GR
Sup tilted pole
Tu tilted pole A Tu GR Tu tilted pole B
Capstan shaft
Tu guide
Pinch roller
4-4-2. Adjusting the Sup GR and Tu GR
(1) Turn the Sup and Tu guide rollers to get the flat waveform at the inlet and outlet sides.
Inlet side Outlet side
(a) Normal (b) Inlet side
waveform is disturbed. (c) Outlet side
waveform is disturbed.
Figure 2
4-4-3. Adjusting the Si roller height
After replacement of Si roller preset and adjust the Si roller
height.
(1) Si roller height presetting
Adjust the height from the upper surface of mechanism
chassistotheuppersurfaceoflowerflangewiththeaidofjig.
Then lower it by 90°(clockwise).
Upper flange
Lower
flange
Height adjusting jig
Master plane
(JiGMP-MX7U)
Upper flange (A)
Si roller
REV mode
Lower flange (B)
Tape must be free from folden
g
.
(2) Adjusting the Si roller
1 Playback the tape to set the V/SR mode.
2 Ascertain that the tape is not folded on the lower flange (B) of Si roller. (Figure 4)
If tape folding is found, turn the upper flange (A) of Si roller with the driver (clockwise) to eliminate the folding.
3 Playback the alignment tape (VR2DBOPS).
4 Adjust the Sup GR and Tu GR by the procedure described in section 4-2 above.
5 After V/S F,R perform playback so as to ascertain that the waveform rises horizontally within 2 seconds.
6 Unless the normal waveform is obtained (Figure 5), turn counterclockwise the upper flange (A) of Si roller, and repeat the step
(5) above. Repeat the steps (5) and (6) until the normal waveform is obtained. At this time ascertain that the inlet travel does
not change in the normal playback state. If any change is found, adjust the Sup GR, and redo the step (5).
Figure 3
Rise waveform
REV OK Playback
REV NG Playback
Figure 4 Figure 5
(1) Clean the tape running areas (guide poles, rollers, drum,
Capstan shaft, Pinch roller) (Figure 1)
(2) Connect the oscilloscope to the following TPs.
RF output..... TL7410
H-SW-P ....... TL7417
GND............. TL7413
(3) Playback the alignment tape (VR2DBOPS).
(4) Ascertain that each guide is free from remarkable curl.
(5) Ascertainthat theRFwaveform ofinletand outletsidesis flat
on the oscilloscope (Figure 2, (a)). Unless the waveform is
flat, (Figure 2, (b), (c)), make an adjustment as follows.

15
VL-A10S/H/E
VL-AH30S/H/E
4-4-4. Adjusting the Tu guide
After replacement of Tu guide preset and adjust the height.
(1) Tu guide height presetting (Figure 6)
Adjust the height from the upper surface of mechanism chassis to the
upper surface of lower flange with the aid of jig.
(2) Adjusting the Tu guide (Figure 7)
1 Playback the alignment tape (VR2DBOPS).
2 Check that the tape runs at the same height near the capstan shaft in case of
V/S F and V/S R.
3 If the tape running position in case of V/S R is higher than the tape running
position in case of V/S F, turn clockwise the Tu guide nat.
If the tape running position in case of V/S R is lower than the running position
in case of V/S F, turn counterclockwise the Tu guide nat.
4-4-5. Checking the V/S F and R waveforms (Figure 8)
(1) Playback alignment tape (VR2DBOPS), and set the V/S R mode. At this time
ascertainthatthewaveformcrestpitchiskeptconstantformorethan5seconds.
(2) Set the V/S F mode. At this time ascertain that the waveform crest pitch is kept
constant for more than 5 seconds.
Unlesstheconstant pitch isobtained,executethe checksofSection4-2,3, and
4.
Figure 6
4-4-6. Checking after adjustment
(1) Envelope check
1 Playback the alignment tape (VR2DBOPS).
2 Ascertain that the envelope maximum to minimum ratio is 65% or more. (Figure 9)
3 Ascertain that the waveform does not change remarkably. (Figure 10)
Figure 10
E
MAX
E
MIN
E
MAX
E
MIN
65 (%)
Figure 9
AC
C
C 1/8A
(2) Rise check
1 Playback the alignment tape (VR2DBOPS).
2 Once eject the cassette, and then load it again.
3 Settheplaybackmode,andascertainthattheRFwaveformriseshorizontally
within 2 seconds. At this time ascertain that there is no tape slackness near
the pinch roller.
4 After V/S F, R and FF/REW execute playback, and ascertain that the RF
waveformriseshorizontally within 2seconds.Atthis timeascertainthatthere
is no tape slackness near the pinch roller.
Capstan shaft
Tu guide
Tape slackness Tu GR
Figure 11
Tension pole
Si roller
Sup tilted pole
Sup GR Drum
Drum
Tu GR
Pinch roller Tu guide
Tu tilted pole
Figure 12
(3) Checking the tape travel
1 When the tape is played back, ascertain that tape lift and tape curl of 0.3 mm
or more do not occur at the lower flange of Si roller, upper flange of Sup GR,
upper flange of Tu GR, and upper/lower flange of Tu guide.
2 In case of V/S F and R ascertain that no curl is found at each flange.
4-4-7. Checking and adjusting the playback switching point
Refer to the description of playback switching point adjustment in section of VCR circuit adjustment.
Figure 8
abcd
a b c d
Figure 7
Nat
Capstan shaft
Pinch roller
Upper flange
Lower
flange
Height setting jig
Master plane
(JiGMP-MX7U)

VL-A10S/H/E
VL-AH30S/H/E
16
4-5. MECHANISM ASSEMBLING AND PARTS REPLACEMENT
(DISASSEMBLING AND ASSEMBLING)
Below is given an explanation of assembling of mechanism and its parts replacement.
The removal of cabinet and Circuit Board is explained in the relevant service manual.
Notes
1 After removal of cut washers be sure to replace them with new ones.
2 Donotplacethe mechanism upside downonthetable.Otherwise, the mechanism partmaybedeformedor damaged, resulting
in malfunction.
3 When assembling, take care so that screw, washer or other foreign substance do not enter. Otherwise mechanism malfunction
may occur.
4 Be sure to use the specified cleaning liquid, oil, grease and screw lock as listed below. Otherwise mechanism malfunction may
occur.
Oil: Cosmo Oil Co., Ltd.
COSMOHYDRO HV100
Greases: Dow Coaning
MORYCOAT YM-103/X5-6020
Screw lock: THREE BOND
1401B
Cleaning liquid: Industrial-use ethyl alcohol
4-5-1. Mechanism modes
Toactuatethemechanism,applyDC3to4VtotheLmotor.AtthistimetheLmotorconnectormusthavebeendisconnectedinadvance.
Below is given an explanation of the mechanism mode necessary for mechanism check, adjustment and replacement.
(1). EJ (Eject) mode (See Figure 1)
In this mode, it is mechanically positioned to eject the
cassette.ItisthepositionwheretheEJECTleverismoved
the farthest in the direction A in the S/B mode. (In this
mode, the cassette compartment assembly can not be
locked.)
(2). S/B (Standby) mode (See Figure 2)
When the cassette is loaded, the mechanism is set to the
S/B mode. In this mode the slide chassis is most far from
thedrum.Inthismode the Eject lever is inpositionshown
in Figure 2 (in position where the cassette control ass’y
can be locked).
Slide
chassis
EJECT
Lever
A
Slide
chassis
A
EJECT
Lever
(4). PB mode (See Figure 4)
In this mode, it is positioned for the replay, record and so
on. It is the mechanical position where the pinch roller is
pressed against the capstan shaft to make the pinch-
pressing spring the most longest.
(3). STOP mode (See Figure 3)
In the STOP mode the S.T pole base is depressed in the
STOP position (or Rec Lock position in CAMERA mode),
and the S brake is in contact with the S reel disk.
EJ mode
Figure 1 S/B mode
Figure 2
Figure 3
STOP mode Figure 4
PB mode
S pole base T pole base
S reel disk
S brake
Capstan
shaft
Pinch
Spring
Pinch roller

17
VL-A10S/H/E
VL-AH30S/H/E
4-5-2. Cassette control ass’y
<Disassembling>
(1) Set the unit to the EJECT mode, and let the housing stand upright. Or set the
unit to the STANDBY mode, press the lock lever in the arrow direction, and
let the housing stand upright. (See Fig. 5: in the direction aor b) (When
pushinginthedirection a,slightlyliftthehousingbyhandtoreleasethelock
lever.)
(2) Remove the four screws 2and take out the down guide 3.
(3) Slide the two link support shafts cand the two roller shafts dto the round
openings
g
on their respective slide chassis slits (two at eand two at f).
(4) Deflecttherollershafts dalittleinwardtogetthemoutoftheroundopenings
g
on the slide chassis. (Be careful not to deform the inner links.)
Figure 2
4-5-3. Actuating the mechanism with the cassette
control ass’y removed
(1) Turn on the power supply with the cabinet and camera unit removed,
referring to the Service Manual (so as to actuate the mechanism).
(2) Put the cap on the light guide.
(3) Press the cassette control down switch through the adhesive tape in
the arrow direction so as to turn it on. At this time take care to avoid
contact with the cassette. Keep the switch pressed (if the switch is
turned off, unloading occurs).
Note: To set the Rec mode, press the pin (marked with the asterisk *)
of recognition switch (this operation is not necessary in other
modes).
<Reassembling>
(1) Set the unit to the STANDBY mode.
(2) Deflecttherollershafts dalittleinward,andfitthemintotheroundopenings
g
on the slide chassis. (Be careful not to deform the inner links.)
(3) Align the flanges of roller shafts dwith the slide chassis slits f. While
sliding the flanges, fit the support shafts cin the slide chassis slits e, and
slide them until they reach the slits.
(4) Attach the down guide. (While pressing the guide in the direction i, tighten
thescrewsuntilthegap jbetweenthedownguide3andthesupportshafts
cbecomes zero.)
Tightening torque: 70±7 mN·m (0.7±0.07 kg·cm) Screw tightening
torque (4 locations)
0.069±0.007 N·m
(0.7±0.07 kg·cm)
c
i
bj
a
Lock Lever Down Guide
Screw
Figure 5. Lock lever section
1
d
f
m
4
m
l
d
k
n
e
e
2
2
2
2
3i
i
g
f
g
r
c
c
Figure 6
4-5-4. Drum and Drum base
<Removal>
Forthedrum mounted in this model, there are 2 types. One isthesameconfigurationasthe former type, which the rotary transformer
rotor ass'y and balancer can be removed. When replacing the upper drum, use the upper drum for service (CDRMU0032GE02) as
before. The disassembly/assembly procedure is the same as before.
Theotherisatypedirectlybondingtherotarytransformerrotor. Forthistypeofdrum,therotary transformerrotorandbalancercannot
be removed. Therefore, the disassembly procedure is partially different. When replacing the upper drum, use the dedicated service
unit (CDRMU0033GE02) including the following parts. The assembly procedure becomes equal to that of the former drum.
* To replace the upper drum, be sure to put on gloves. Due care is required so that the drum is not damaged.
• Upper drum ass'y (former type)
• Balancer
• Balancer mounting screw
• Rotary transformer rotor ass'y (former type)
Recognition switch
Cap
Cassette control
down switch Light guide
Adhesive tape
*
(1) Drumbase(Bothcommontype)
Removethe3mountingscrews
as shown in Figure 1, and re-
move the drum base.
Mounting
screw
Drum base
Upper/lower
drum ass'y Positioning
hole
Earth spring
Figure 1
(2) Drum motor stator
(Both common type)
Remove the stator mounting
screw with the hexagonal
wrench as shown in Figure 2,
remove the motor stator.
Upper/lower
drum ass'y
Motor stator
Stator mounting
screw
Phase matching
hole

VL-A10S/H/E
VL-AH30S/H/E
18
(3) Upper drum ass’y
(Both common type)
Remove the upper drum
ass’y from the lower drum
ass'yasshowninFigure3.
Atthis timetakecare soas
not to lose the gap shim.
In this state put the motor rotor on the upper surface of upper
drum ass'y, and tighten the mounting screw. At this time make
sure that the head screw in the three places is visible through
the motor rotor hole (Figure 8). The screw tightening torque
must be 0.1N·m (1 kg·cm).
Figure 7
<Installation>
Install the upper drum in the reverse order of removal.
(1) Balancer
Mount the balancer to the upper drum ass'y with the balancer mounting screw. The screw tightening torque must be 0.1N·m
(tighting torque 1kg·cm). (Figure 5)
(2) Motor rotor, rotary transformer rotor ass’y
Clean the contact surfaces of rotor ass’y holder and upper drum ass'y, and ascertain that there are no contamination and flaws.
Next, adjust the phase so that the positioning pin of rotor ass'y is inserted into the positioning hole of upper drum, and tight fit the
rotor ass'y to the lower surface of upper drum ass'y (Figure 7).
(4)-a Motor rotor ass'y and ro-
tary transformer rotor
ass'y(former type)
Remove the 2 rotor
mounting screws as
showninFigure 4-a, and
remove the motor rotor
and the rotary trans-
former ass'y.
(4)-b Motor rotor ass'y
(bonded type)
Remove two screws fix-
ing the rotor as shown in
Figure 4-b, then remove
only the motor rotor.
Balancer mounting
screw Balancer
Upper drum
ass'y
Figure 5
Motor rotor
Positioning
hole Upper drum
ass'y
Rotor mounting
screw
Positioning pin
Figure 4-a
Motor rotor
Upper drum
ass'y
Rotor mounting
screw
Figure 4-b
Upper drum
ass'y
Gap shim
Lower drum
ass'y
Figure 3
(5)-a Balancer
(former type)
Remove the balancer
mounting screw as
shown in Figure 5, and
remove the balancer.
(5)-b. Balancer
(bonded type)
For the bonded type of
drum, the balancer can-
not be removed.
(6) Lower drum ass'y
(Both common type)
Remove the FPC mounting
screw from the lower drum
ass'y as shown in Figure 6.
Figure 6
Lower drum
ass'y
FPC mounting
screw
Rotary transformer
rotor
Positioning pin
Cleaning (shaded area)
(holder)
Mounting screw hole
Rotary transformer
Rotor ass'y
Positioning hole
To be aligned with
RTr rotor side position
pin.
Cleaning
Alignment position (3 pcs.)
L ch
R ch
Motor rotor Mounting screw
Upper drum ass'y
Head mounting
screw
Screw relief hole
Motor rotor
Upper drum ass'y
Rotor mounting screw
Rotary transformer
rotor ass'y
Figure 8

19
VL-A10S/H/E
VL-AH30S/H/E
(3) Lower drum ass'y
Tighten the FPC mounting screw to the lower drum ass'y. The screw
tightening torque must be 0.08N·m (tighting torque 0.8kg·cm). (Fig-
ure 6)
(4) Upper drum ass’y
After fitting the gap shim which was removed when the upper drum
ass'y was dismantled to the shaft of lower drum ass’y, fit the upper
drum ass’y. (Figure 3)
Atthistimeslightlyturntheupperdrumass'ybyhandtoascertainthat
RTrdoesnotscrape.Ifscrapeisfound,replacethegapshimwiththe
gapshim packagedtogetherwiththereplacementupperdrumass’y.
(5) Drum motor stator
Fitthemotor stator totheshaft.Then,apply thepreliminarypressure
0.07N·m (0.7kg) to the motor stator, tighten the stator mounting
screw. The tightening torque must be 0.15N·m (1.5kg·cm).
Install the stator so that the chassis line is nearly parallel with the
motor stator straight section when it is installed on the chassis.
(Figure 9)
(6) Drum base
Align the positioning pin, and tighten the screws (3 pcs.).
(7) Drum ass’y
Install the drum ass’y on the main chassis, and tighten the screws (3
pcs.).
(8) Tape guide
Align the positioning pin, and tighten the screw (one pc.).
Motor stator
Stator set
screw
Figure 9
4-5-5. Phase matching
The phase of the following parts must be matched as
shown in the figure right.
(Ascertain that the marks and round holes align.)
(1) Lo relay gear (2) Main cam
(3) Sub-cam (4) Mode switch
Lo relay gear
Phase
alignment mark
(Round hole)
Phase alignment
mark ( Mark) Phase alignment mark
(Round hole)
Mode switch
4-6. MECHANISM ASSEMBLING METHOD
a
B
T arm guide
Segment gear M-function lever
Move claw
to rear side.
Move claw to
rear side.
(1) Adjust the phase of each part.
(2) Install screws and washers.
(3) Installthe segment gear, T arm guideand the M-function
lever. Install the eject lever.
Item Tightening torque Quantity
a S Tight M1.4 x 3 70mN·m (0.7kgf·cm) 1
B ø0.8-ø3-t0.2 1
Arrange parallel.
Motor stator
circuit board
Chassis line
FPC

VL-A10S/H/E
VL-AH30S/H/E
20
(4) Install the loading block assembly and the capstan motor.
(5) Install the drive gear. At this time, pay attention to the
direction of gear. (The small gear must be located in the
chassis side.)
Insert the part in the
rail and slide it down.
Make sure not to
deform the arm.
Insert the part in the rail
and slide it down.
(6) Install the guide rail assembly.
(7) Install the guide rail assembly taking care to position it
correctly.
Make sure not deform the arm.
A
a
A
CD
B
Segment gear
Su arm Ass'y T Lo arm Ass'y
Square Hollow Mark Triangle Mark
Edge A
Round Hole
Align the marks on the parts.
aAaa
a
Loading motor
Drive gear
Position the small gear of the drive
towards the chassis.
Capstan motor
Move FF
downwards
Install the
motor under
this plate.
Item Tightening torque Quantity
A S Tight M1.4 x 2.5 70mN·m 1
a S Tight M1.4 x 3 70mN·m 4
Item Tightening torque Quantity
A S Tight M1.4 x 2.5 70mN·m 2
B S Tight M1.4 x 4 40mN·m 1
C ø0.8-ø3-t0.2 1
D ø2.1-ø5-t0.25 1
a S Tight M1.4 x 3 70mN·m 1
This manual suits for next models
5
Table of contents
Other Sharp Camcorder manuals
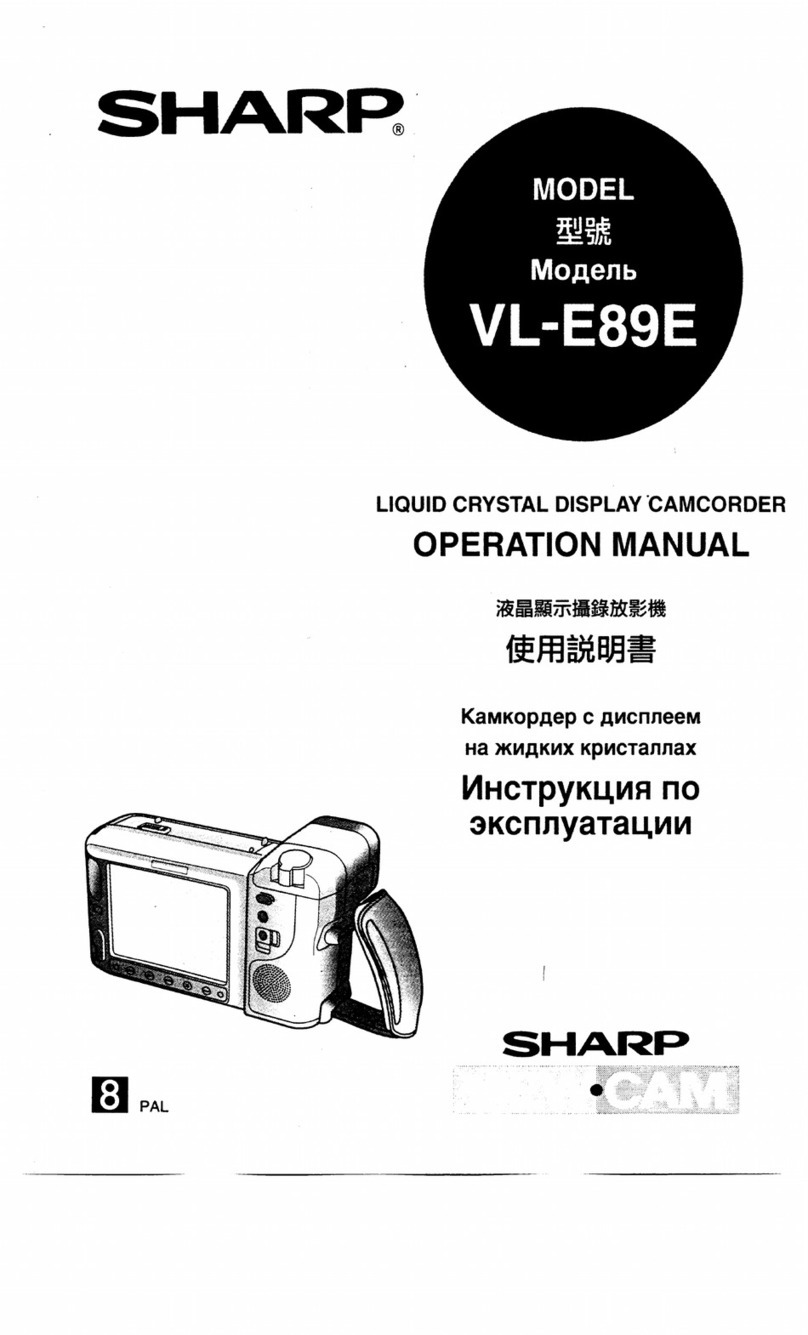
Sharp
Sharp ViewCam VL-E89E User manual
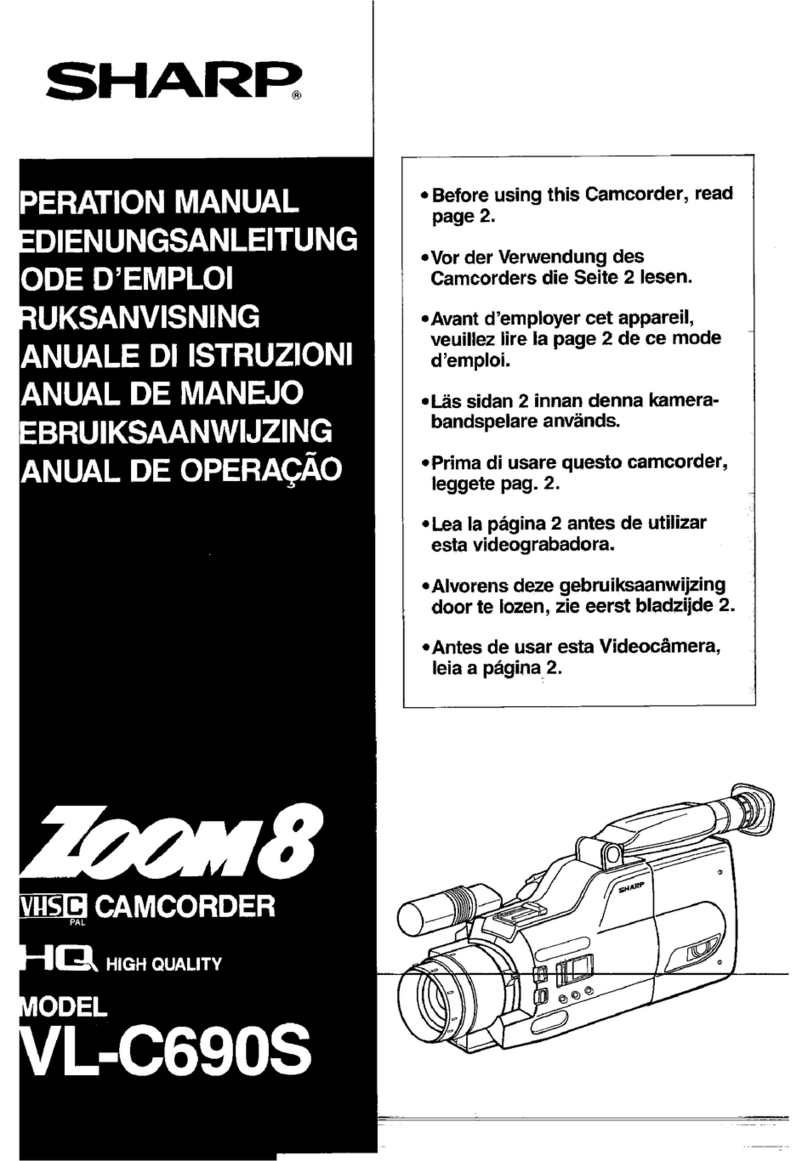
Sharp
Sharp VL-C690S User manual
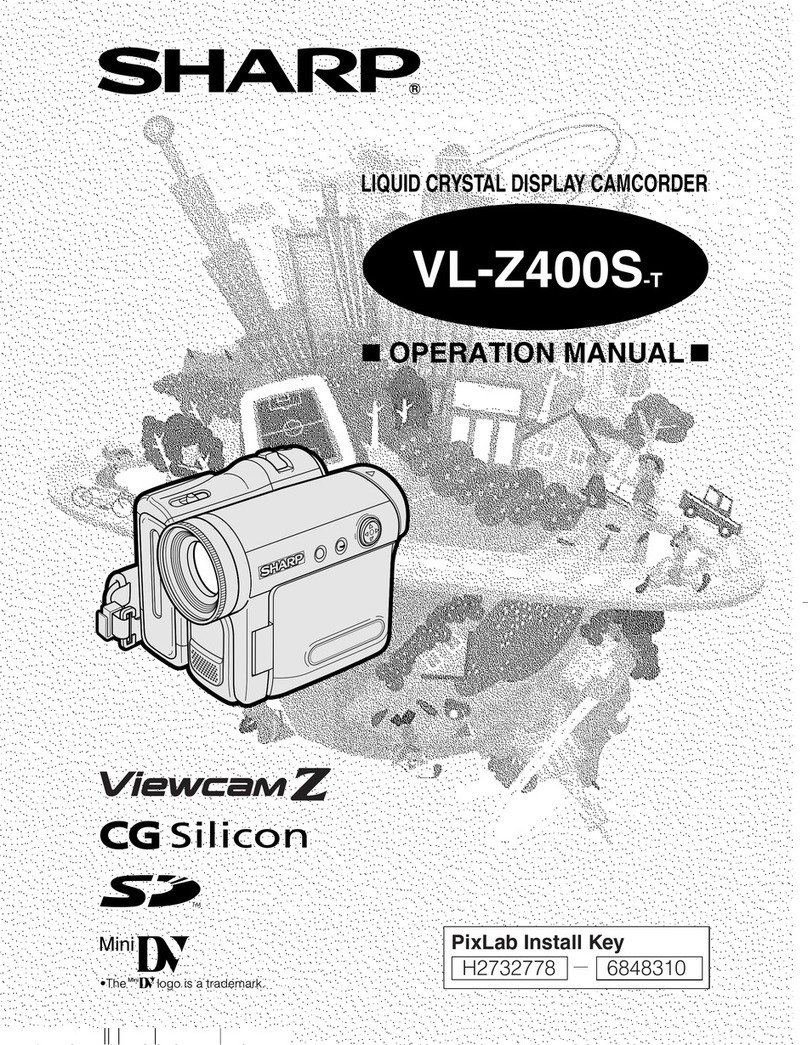
Sharp
Sharp VL-Z400S User manual

Sharp
Sharp VL-SD20H User manual
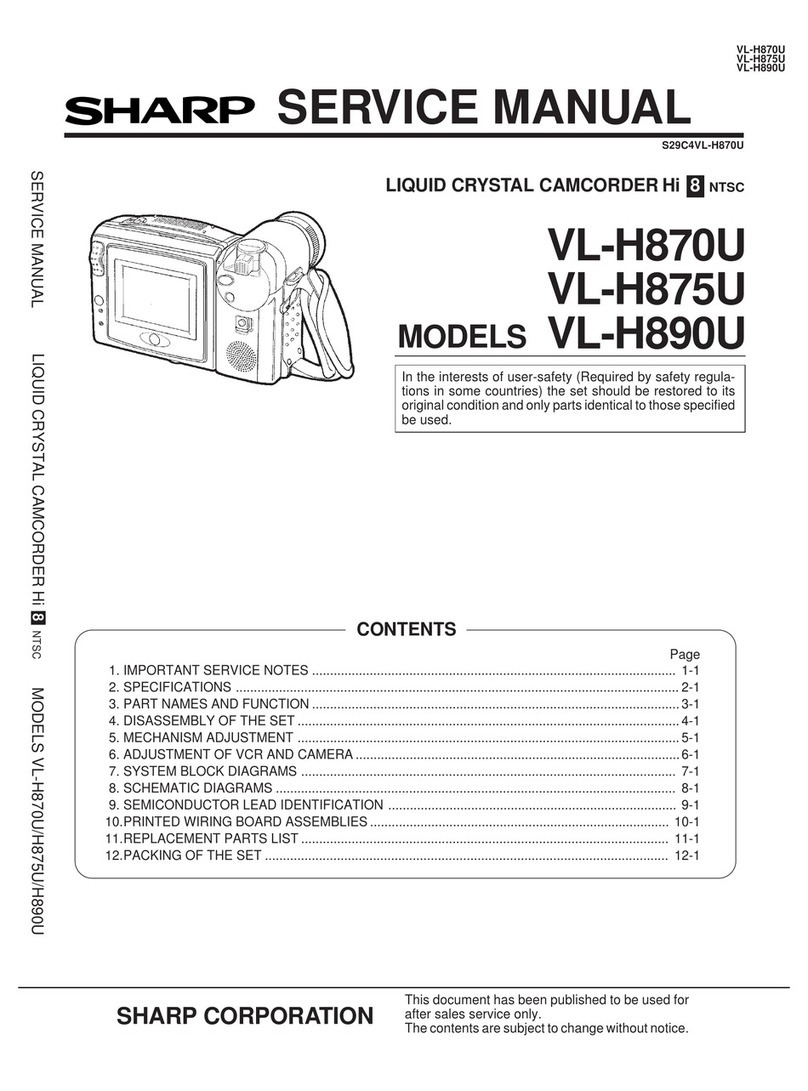
Sharp
Sharp VL-H870U User manual
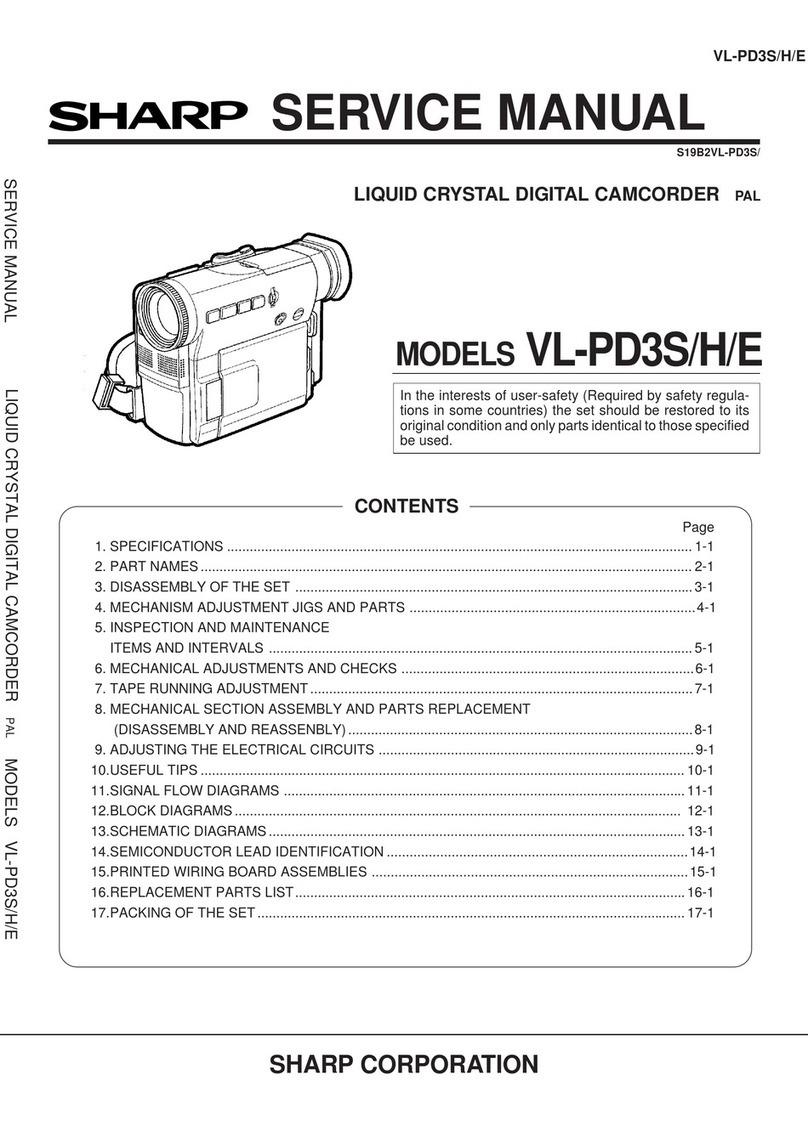
Sharp
Sharp VL-PD3S User manual
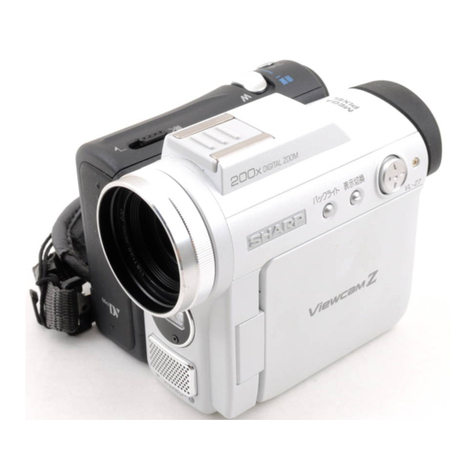
Sharp
Sharp VL-Z7E-A User manual
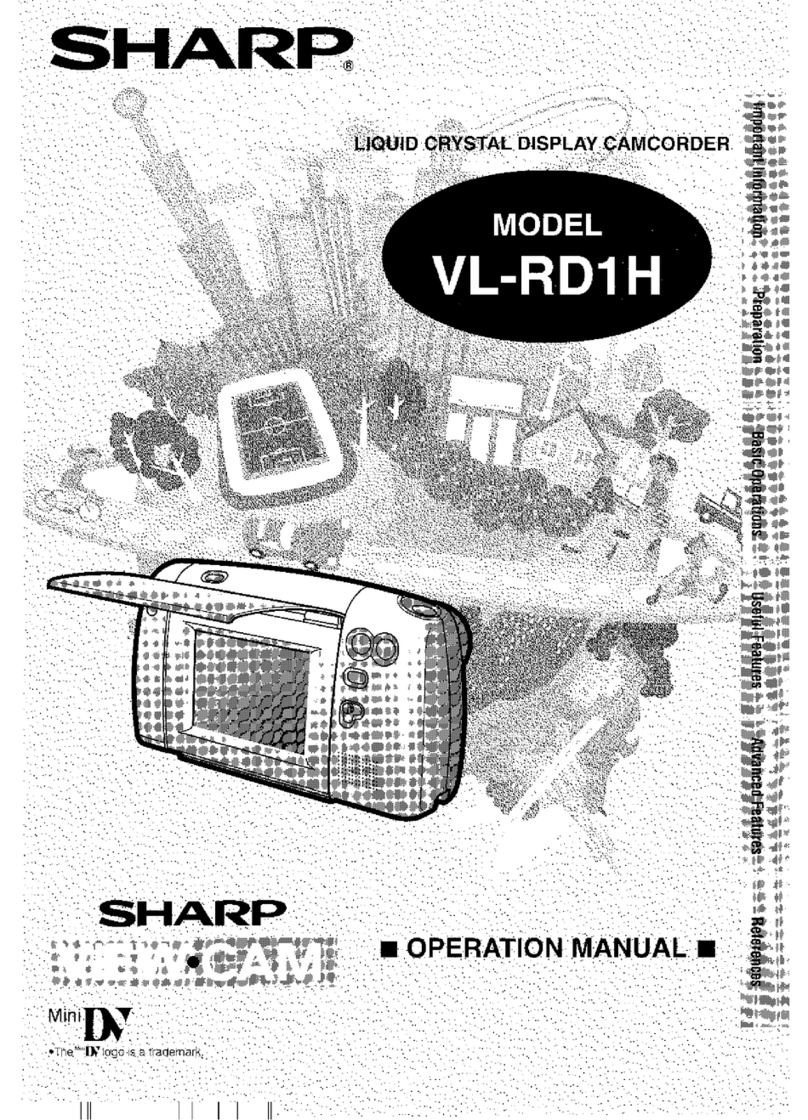
Sharp
Sharp VL-RD1H User manual
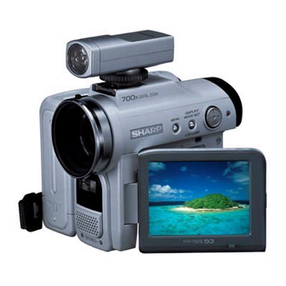
Sharp
Sharp VL-Z950S User manual
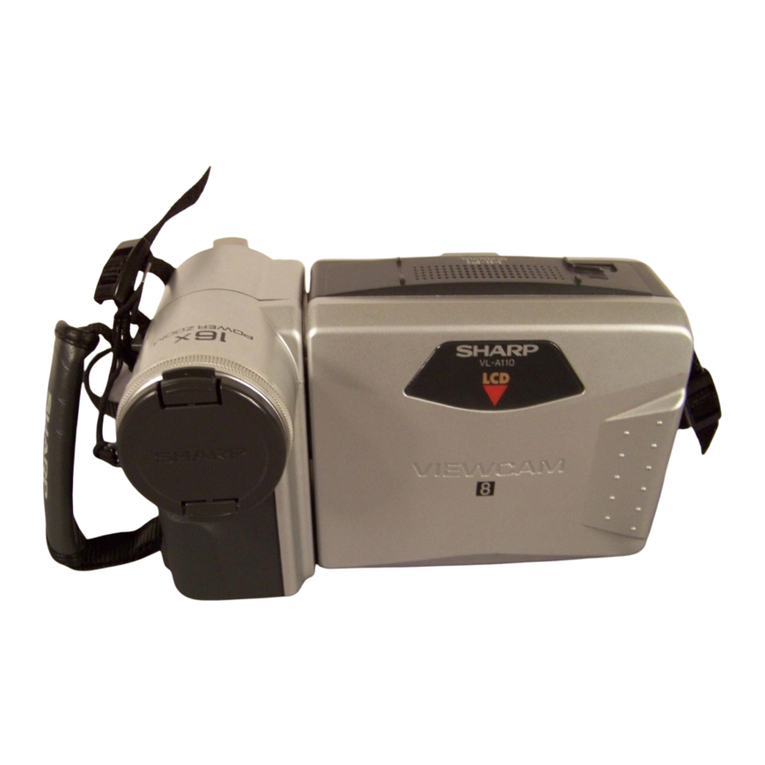
Sharp
Sharp VIEWCAM VL-A110U User manual
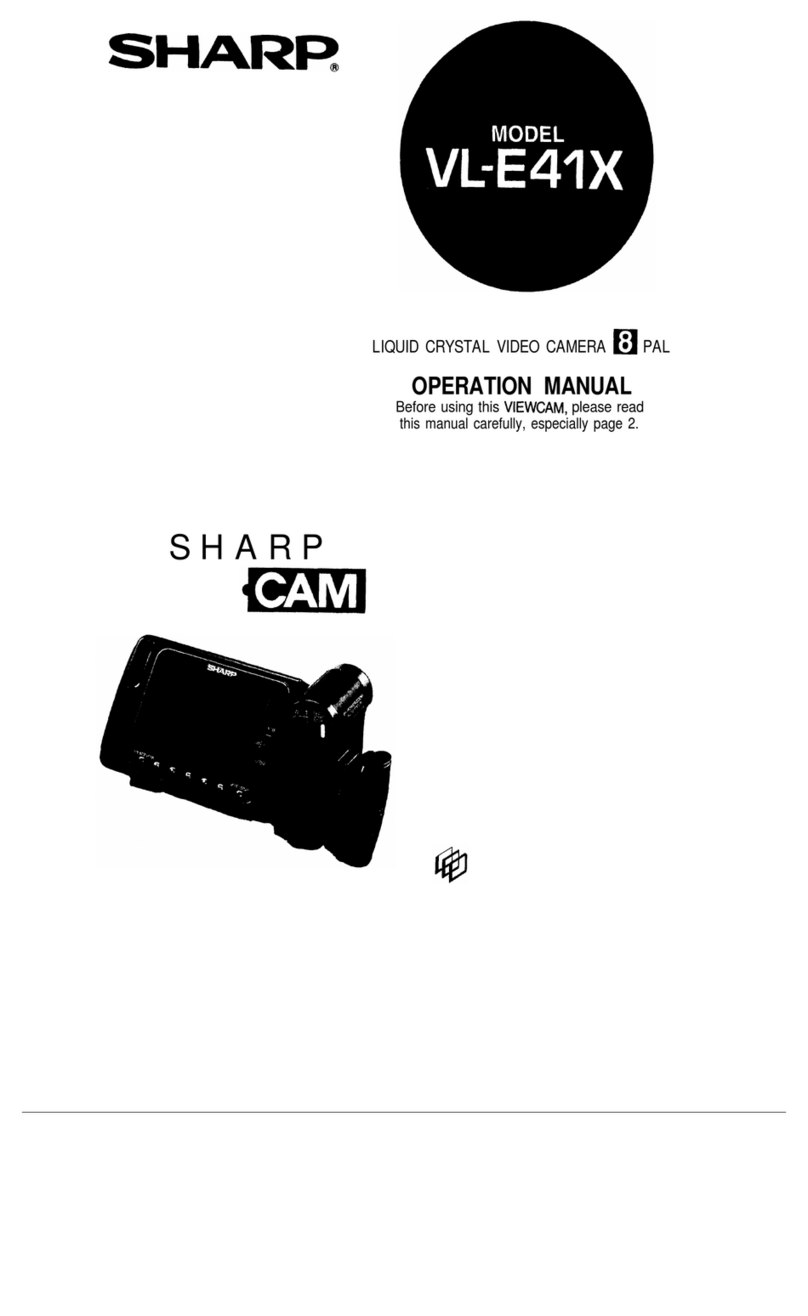
Sharp
Sharp VL-E41X User manual
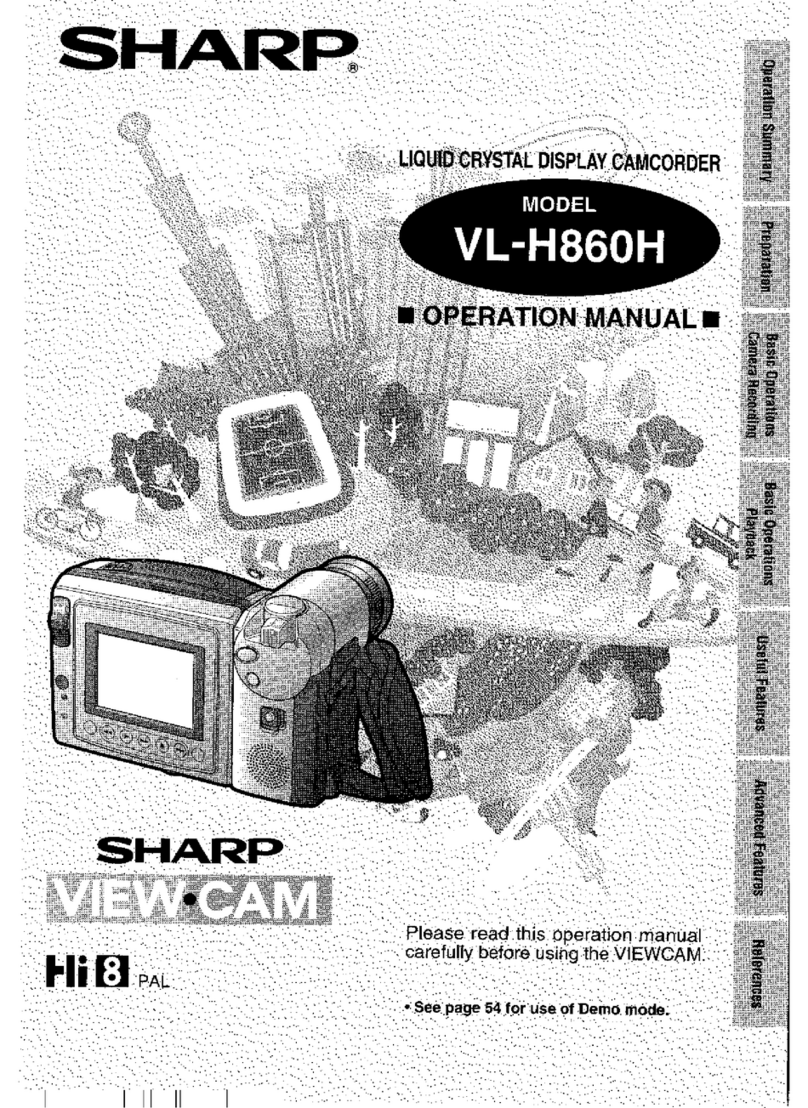
Sharp
Sharp VL-H860H User manual

Sharp
Sharp ViewCam VL-DC1S User manual
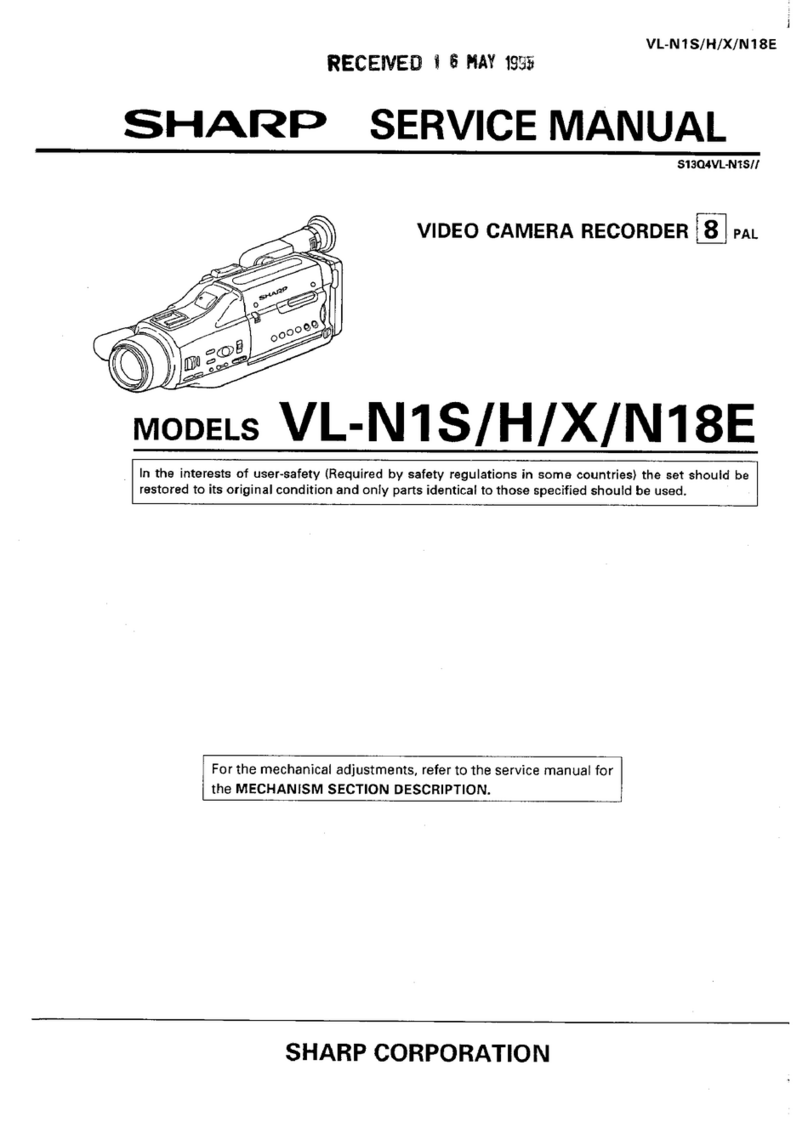
Sharp
Sharp VL-N1S User manual

Sharp
Sharp VL-E630U/T User manual
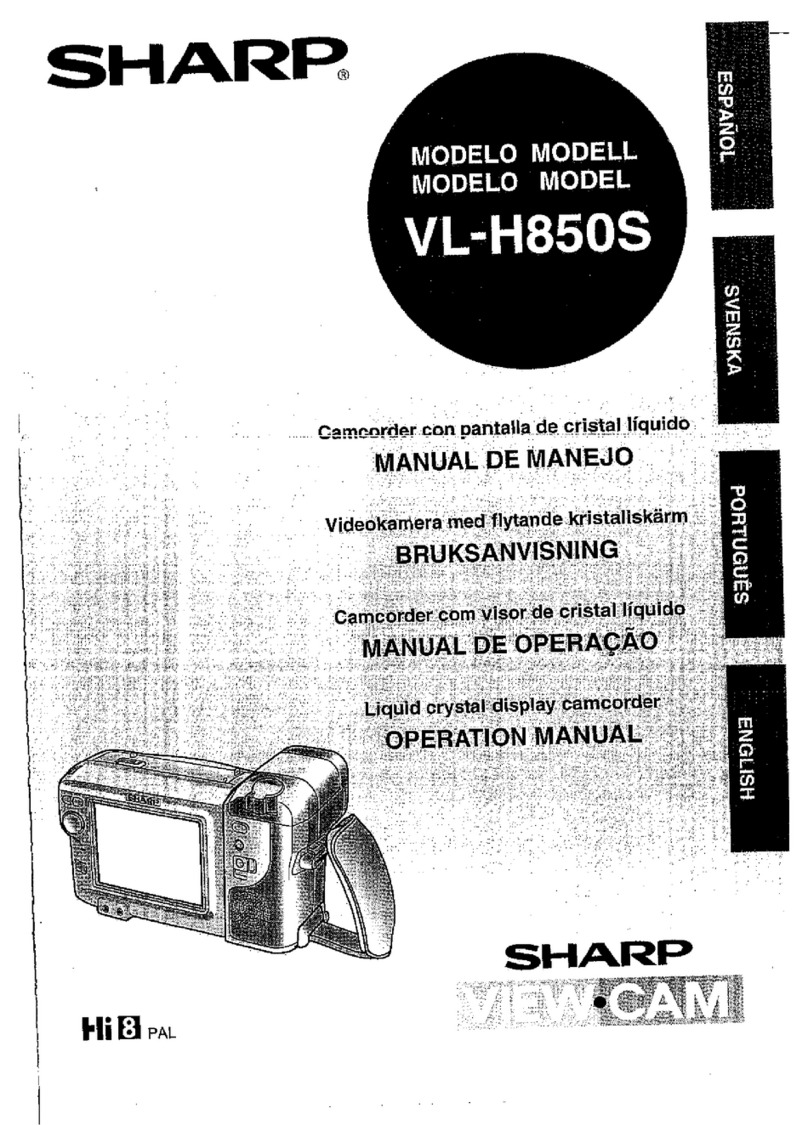
Sharp
Sharp ViewCam VL-H850S User manual
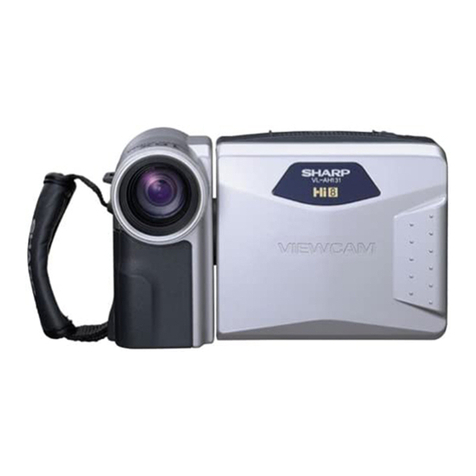
Sharp
Sharp VL-A111S/H/E User manual
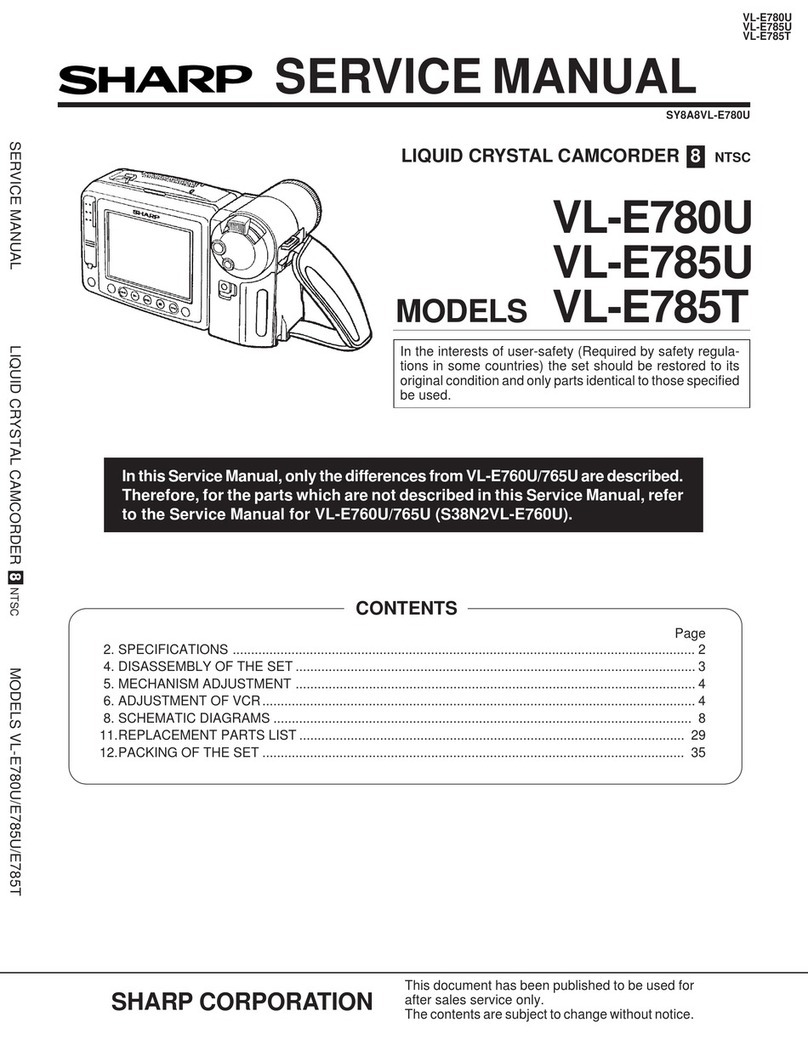
Sharp
Sharp VL-E780U User manual
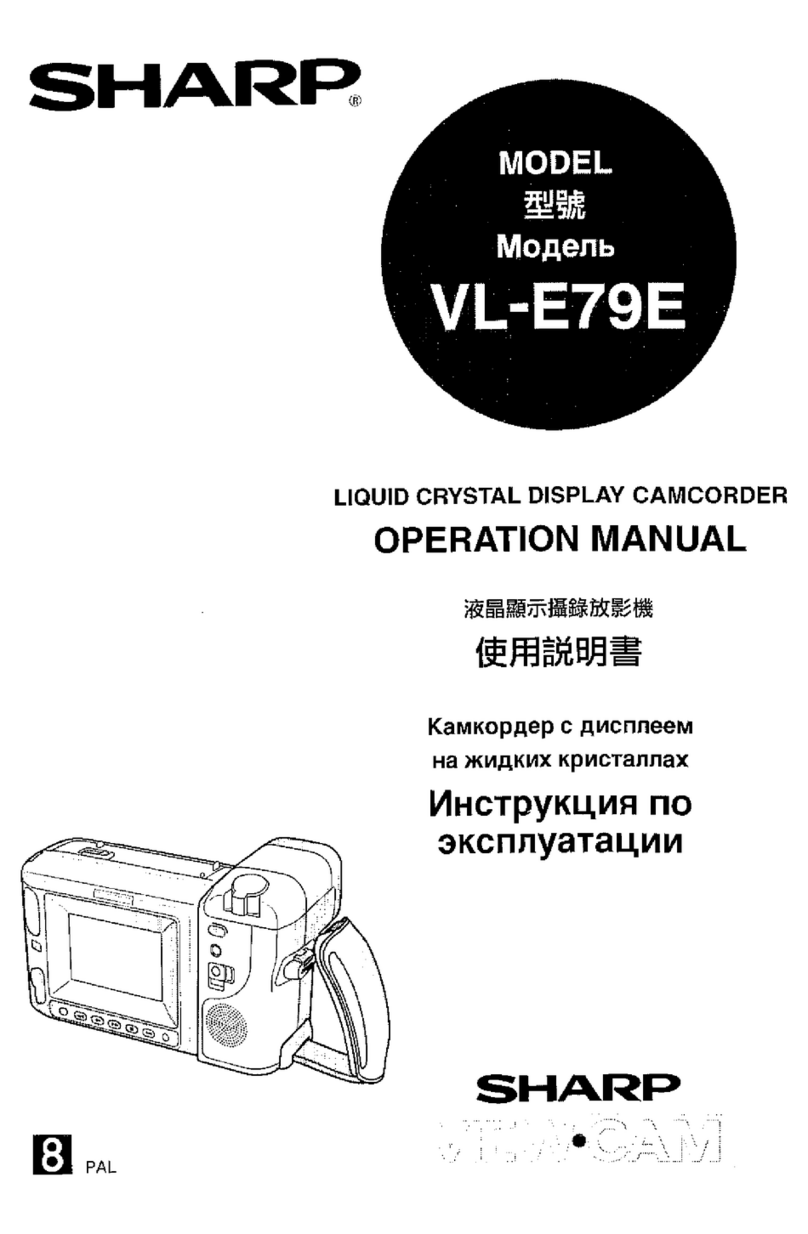
Sharp
Sharp ViewCam VL-E79E User manual
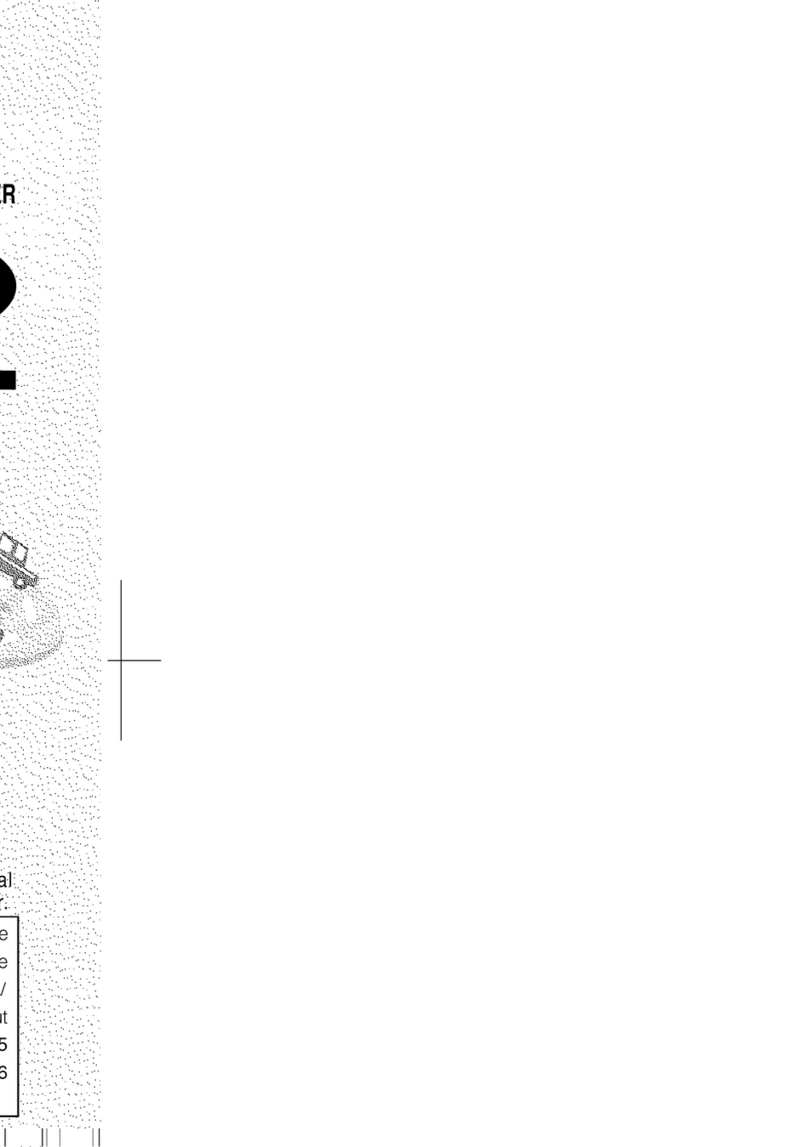
Sharp
Sharp ViewcamZ VL-Z3H User manual