Sherline Products CNC Metric Linear Controller Guide

WEAR YOUR
FORESIGHT IS BETTER
THAN NO SIGHT
READ INSTRUCTIONS
BEFORE OPERATING
SAFETY GLASSES
SHERLINE PRODUCTS INC. •3235 Executive Ridge •Vista •California 92081-8527 •FAX: (760) 727-7857
Toll Free Order Line: (800) 541-0735 •International/Local/Tech. Assistance: (760) 727-5857 •Internet: www.sherline.com
8/1/18
Installing and Using
the Sherline CNC Linear Controller
By Bryan Mumford and Joe Martin
Using the Template Blocks to Locate New Mounting
Holes for the Stepper Motor Mounts
This kit contains a template block that will help you locate
the holes needed to t stepper motor mounts to your Sherline
mill table (X-axis) or base (Y-axis). (Sherline machines
manufactured after 9/99 have the stepper motor mount
holes predrilled to make this job easier.) The rectangular
template block is used to aid in drilling these holes on the
mill. These blocks are not hardened, because they will only
be used once or twice. To drill the holes for the stepper
motor mount for each axis, follow the steps below:
1. Using the handwheels, move the table and saddle so
that they are as close to the handwheel as possible.
2. On models with standard handwheels, break loose the
5-40 screw in the center of the face of the handwheel
before removing the handwheel. The handwheel gives
you a way to hold the leadscrew while breaking the
center screw loose.
3. Remove the handwheel by loosening its set screw with
a 3/32" hex wrench and pulling it o the shaft. (For
adjustable “zero” handwheels, rotate the engraved red
collar until the hole lines up with this set screw.)
4. Remove the leadscrew thrust from the table or base by
removing the single 5-40 screw.
5. Remove the 5-40 screw from the end of the leadscrew
being careful not to damage threads or shaft as you
keep the screw from rotating.
6. Bolt the template parallel to the table or base with the
5-40 SHC Screw provided with the kit.
7. Using the holes in the template as a drill guide, start
each hole about 1/16" deep with a #29 drill (0.136").
8. Remove the template block and drill each hole .25"
deep backing the drill out to clear chips add cutting
oil and nish drilling the hole in two more steps until
a depth of 0.5" is reached. Countersinking the holes
will make it easier to start a tap.
9. Tap the holes to 8-32 to 0.4" depth. Be sure to use
cutting oil. Remember the part is relatively expensive
to replace. Take your time. Remove any burrs from the
surface of the part after tapping the hole.
Installing the Stepper Motor Mount
1. Thread the preload nut onto the leadscrew.
2. Slide the stepper motor mount over the X- or Y-axis
leadscrew end.
3. Push a coupler through the bearings and over the
tapered end of the leadscrew. Attach it to the leadscrew
with the new 5-40 screw provided. To tighten, put a
hex key through the hole in the side of the mount and
into the handwheel shaft set screw. Hold the key to
keep the shaft from turning while tightening the 5-40
SHCS in the end of the coupling.
4. Using a 3/8” wrench, adjust the preload nut snugly
against the end of the bearing. Tighten to remove
all endplay. (See Figure 3 to understand how the nut
preloads the bearings.) Turn the coupling by hand to
make sure it turns freely, then put a little LocTite®on
the threads behind the preload nut and let capillary
action draw the uid in. Figure 2 shows how to use
a hex key through the hole in the mount to keep the
coupler from turning while tightening the preload nut.
5. With the leadscrew screwed into the mill saddle as
far as practical and the table moved to its extreme left
position, attach the stepper motor mount to the table
FIGURE 1—The rectangular block is used for the mill table and
base. On the table, the two new drilled holes are ABOVE the
existing center hole. On the base, the two new holes go BELOW
the center hole as shown in the drawings above.
Template Block
(Holes ABOVE center hole)
Template Block
(Holes BELOW center hole)
2 Holes—Drill .5" Deep,
Tap 8-32 X .4" Deep
MILL BASE
CAUTION: The power cord
receptical in the control box is
easily damaged. Plug and unplug
the power connector with care!
CNC Metric Linear Controller
P/N 8851
NOTE: The power supply included with this indexer (linear controller) is intended to
operate only on 115/120 VAC, 60 Hz (38 W) current. For countries operating on 100,
220 or 240VAC and/or 50Hz a transformer will be required. As an alternative, this power
supply outputs 24VDC, 1 Amp (1000 mA). If you can purchase an appropriate power
supply that operates on local current and outputs 24VDC, 1A current, it could be used to
power the unit instead of the one supplied. Sherline Products does not provide a 220V
power supply or transformer.

P/N 8851, Pg. 2 OF 10
by installing two 8-32 x 3/4" SHCS provided. This will
assure proper alignment. The 8-32 socket head cap
screws go inside the motor mount and thread into the
tapped holes in the table. Before tightening the screws,
turn the coupler by hand to make sure the mount is
properly aligned and is not putting tension on the
leadscrew. The holes in the mount are slightly oversize
to allow for minor alignment adjustments. Check again
for proper alignment by again hand turning the coupler
to assure there is no binding after nal tightening of
the screws.
LEADSCREW
COUPLER
5-40 SCREW
PRELOAD NUT
OUTER BEARING
STEPPER MOTOR MOUNT
FLAT
SET SCREW ACCESS HOLE
FIGURE 3—A cross-section of the stepper motor mount shows
how the coupler is attached to the leadscrew.
Attaching a Stepper Motor to the Mount
Push the shaft into the coupling and tighten the set screw,
being sure that it is aligned with the at. Attach the stepper
motor to the mount using the three SHCS provided. The
fourth hole can be used for a “cable tie” to secure the cable
or a screw at your discretion. Attach the handwheel to the
shaft to the other end of the stepper motor, aligning the set
screw with the at on the shaft.
Overview
Bryan Mumford, who designed the electronics and did the
programming, and I have written the basic instructions for
the computer. Even though the computer is small, it is a
very complex device that both computes and drives the
stepper motor in microsteps. Like all electronic devices,
the easier it is to operate, the harder it was to design and
program. These instructions are easy to read and shouldn’t
give you any problems, but if they do, please notify us at
Sherline, and we will attempt to improve them. We want
our instructions to be the best in the business. The most
important rule is to always work safely and accurately.
Power of the Motor
The stepper motor is rated at over 136 oz-in of torque,
with the highest power being achieved at low RPM
(feed rates). The maximum speed of 600mm/min, with
a 1.0mm leadscrew pitch, provides high speed but very
little power. To use that setting for positioning, the system
must be completely free from drag. We recommend using
a maximum speed of 300mm/min as a positioning speed to
avoid stalling the stepper motor. When cutting, a slow speed
should be used to take advantage of the motor’s power.
Positioning Accuracy
The rst thing you have to understand about a CNC
stepper motor powered machine slide is that its accuracy is
determined by the leadscrew, not the stepper motor. Properly
powered and installed, stepper motors essentially have no
error. Sherline leadscrews are manufactured “in house” on a
precision thread roller and will reliably repeat a movement
to less than 0.001" (0.025mm). Rolled threads were chosen
because they have excellent wear characteristics.
The Importance of Reading the Instructions
It is impossible to make a product this complex “idiot proof”.
The best rule I’ve ever come up with when dealing with
any type of CNC equipment is this: “You have to know
what the unit will do after you push the button BEFORE
you push the button.” This can only be accomplished by
reading the instructions and playing with the table drive
without cutters or the possibility of a crash at the same time
until you thoroughly understand how the features of this
unit work. Again, don’t have a cutter in the spindle until
you truly understand how to operate it.
Precautions when Turning the Unit On and Off
• As with any piece of electronic equipment, make sure
the power is o before plugging the stepper motor
connecting cord into the control unit.
• If a part has been aligned on the table and the power is
switched o, the part should be realigned after turning
the unit back on before continuing. Electrical “spikes”
can cause the motor to move a few steps when turning
it on. The power can be left on continuously for several
hours without damage; however, the controller should
be left in the [JOG] mode. Otherwise the motor may
be left in an energized state. This may cause the motor
and controller to heat up to an undesirable temperature
over an extended period of time. Don’t leave the unit
turned on and unattended for long periods of time. If
you turn it o, record the handwheel position so you
can reconrm the correct starting position when turning
it back on.
Precautions Regarding Manual Mode
When hand cranking the handwheel in the manual mode,
the stepper motor acts as a generator. If you crank the
handwheel rapidly, there is a chance that the control box
electronics could be damaged by the current generated. If
the unit is to be used extensively in the manual mode, it
is recommended that you disconnect the cable from the
motor to the controller.
FIGURE 2—Using a hex key to keep the leadscrew from turning
while tightening the 5-40 screw and preload nut.
Leadscrew
Preload Nut
Coupler
Hex key used to keep
shaft from turning

P/N 8851, Pg. 3 OF 10
Operating Instructions
The Sherline Linear Controller is a self-contained,
microprocessor-based controller that will automate the
motion of any axis on a Sherline machine without losing
the option of manually moving the slide. If used on the
Z-axis (leadscrew) of a lathe or mill it serves the function
of a power feed. The controller is designed to drive the table
in precise, measured steps controlled by simple programs
that you enter by using keys on the keypad.
123
456
78
0
9
Minus Enter
Slow Fast
Mode
Prv
Nxt
Stop
Jog
JOGJOG
FIGURE 4—Layout of the keypad.
Moving the Table
There are three primary ways to drive the table:
1. Using the POSITIONING MODE you can specify the
exact distance you want the table to move and the speed
at which it moves. For example, if you enter 25.40,,
the table will move 25.40mm at the programmed rate.
2. Using the PROGRAM MODE you can enter a series
of programmed steps. For example, you can have the
table move 20.5mm at a rapid feed rate up to the work,
then move at a slower programmed feed rate for 10mm
while making your cut, then reverse rotation and move
30.5mm to a home position. You can enter up to 40
steps in each of two separate programs. You can also
specify the feed rate for each step, and whether the
table is to pause and wait after a step is taken or move
continuously.
3. In the JOG MODE the controller will move the table
to the left or to the right using the [ 1 ] or [ 3 ] buttons
on the keypad on the controller. Jog mode also allows
the stepper motor to be turned manually.
General Specifications
• Resolution of positioning is governed by the leadscrew.
However, the stepper motor will stop within 1/400 of
a revolution.
• The speed of the slide can be set from very slow rate
of 20mm per minute to a maximum of 600mm per
minute. Note that the higher speeds do not have much
power and will only be used for positioning the table
quickly, not for cutting operations.
• The controller allows a programmable amount of
backlash compensation.
Using the Controller
The controller must be plugged into its AC adapter power
supply. The power jack is located on the end of the unit.
It is turned on with the toggle switch located next to the
power jack. We wish that the power supply connector
had a better locking system, but we had to use what was
commercially available. With the power turned o, the
motor cable must be plugged into the 5-pin DIN connector
next to the power switch.
The basic operation of the controller is to press the [MODE]
key to advance from one mode of operation to the next.
This will cycle through the various modes of operation.
When the mode you wish to use is displayed, press the
[ENTER] key to start that mode and enter the parameters
of operation. The three modes are:
• Positioning
• Program
• Settings
PANIC STOP—Any time the table is moving you can stop
it immediately by hitting the [STOP] (Jog) key. This will
stop all motion and put you into the JOG mode. Remember
that the motor must be moving for the jog key to stop the
program; therefore, hold it down long enough to be sure
the program has been shut down. You will lose your place
in the program you were running and will have to start
over, but if you record the handwheel settings at home
position before starting to run your program, this can be
easily accomplished.
The “Positioning” Mode
The Positioning Mode allows you to specify the exact
amount you want the table to move. This amount of motion
will occur each time that you signal the controller to advance.
The resolution of the controller is .01mm.
When the display reads “Sherline Metric Slide” press the
[MODE] key once to advance to the Positioning Mode.
The display will read:
Positioning Mode
Press Enter
To use the Positioning Mode, press the [ENTER] key. The
display will read:
mm: 00.000
Enter a number
You can now enter the distance you wish to travel. When
you press a number key, that number will appear on the
display where the cursor is blinking. To move the cursor
left, press the [PRV] (Previous) key. To move the cursor
right, press the [NXT] (Next) key or type any digit. The
speed at which the table moves is controlled by the number

P/N 8851, Pg. 4 OF 10
entered in the “Speed” parameter of the Settings Mode.
You can also specify whether the table is to move left or
right when you enter the amount you wish to move. Normal
motion is to the right. To enter a table movement to the
left, when viewed from the front of the machine, press
the [MINUS] key. This will add a minus sign before the
distance of move requested. When the move is entered as
a negative value, the [NXT] key will move the table to the
left. However, if you press the [PRV] key, the table will
move to the right. To make a negative value positive, press
the [MINUS] key again. (Standard CNC congurations
have the + and – signs used in the same manner as an x-y
coordinate grid.)
When the number you want is displayed, press [ENTER].
For example, suppose you typed “25.50” for the distance
to move. After you hit [ENTER], the display will read:
25.50 00.000
Press Nxt or Prv
The rst number is the movement and direction you selected
(25.50mm to the right). The second number is the current
position (000.00mm). The controller is waiting for you to
press the [NXT] or [PRV] keys. If you press [NXT], the
table will advance to the right 25.50mm, and the display
will read:
025.50, 025.50
Press Nxt or Prv
The current position is now shown to be 025.50mm. If you
press [NXT] again, the display will read:
025.50, -051.00
Press Nxt or Prv
The current position is now shown to be 051.00mm.
If you had pressed the [PRV] key the rst time, the table
would move 25.50mm to the left, and the display would read:
025.50, – 0025.50
Press Nxt or Prv
The current step is shown to be 25.50 and the current
position is minus 25.50.
PANIC STOP—Any time that the table is moving, you
can stop it immediately by hitting the [STOP] (Jog) key.
This will stop all motion and put you into the JOG mode.
You will lose your place in any program you were running
and will have to start over.
To exit from the Positioning Mode, press the [MODE] key.
Note: To keep these instructions from becoming too
cumbersome, we haven’t listed every keystroke (such as
[ENTER]) from this point on. Use the choices listed on
the controller display.
The “Program” Mode
The Program Mode allows you to prepare a sequence of
motions to take one after another. Each motion is called a
“block”, and for each block you will enter four parameters:
1. The distance to move.
2. The direction of travel.
3. The feed rate for that move.
4. Whether or not the table should wait for you to hit the
[NXT] key after each step is taken.
The program you enter will be remembered indenitely
(unless you change it), even if you turn the controller o.
There is room for two separate programs of 40 blocks each.
Before you enter your program blocks, you’ll want to plan
them carefully to be sure they’re correct before typing them
all in. Write them down on paper and check for errors.
The Program Mode comes after the Positioning Mode.
Press the [MODE] key until the screen says:
Program Mode
Press Enter
Then press the [ENTER] key. The display will read:
Which program?
Press 1 or 2...
You can now select which program you will use. Enter the
digit “one” or “two” and the screen will display:
Program 1
Run = [NXT] Edit = [PRV]
This indicates which program you’ve selected, and that
you should press the [NXT] key to run the program that
was stored previously, or press the [PRV] key to enter a
new program or edit the existing one.
Entering a New Program
Press the [PRV] key and the display will show the rst
program step.
For example, the display may read:
Block 1:1
mm: 10.50
The “1:1” means you’re working on program 1, block
number 1. A block is considered as the complete set of
instructions for a programmed instruction. The rst
instruction in this example is to move the table 10.5mm
to the right (left movement would have had a minus sign
displayed). Edit this number if necessary and press the
[ENTER] key.
The display may then read:
Block 1:1
Feed rate: 50
This means that the feed rate for this programmed move is
50mm per minute. The number you enter will be the fastest
rate the table will reach during a move. By pressing [NXT]
or [PRV] you can increase or decrease the speed setting to
a higher or lower speed setting. This control comes with a

P/N 8851, Pg. 5 OF 10
choice of (8) speed settings: 20mm/min, 50, 100, 200, 300,
400, 500 and 600mm/min. Edit this number if necessary
and press the [ENTER] key.
The display will read:
Block 1:1
Pause (or No Pause)
Ending a block with “Pause” means you must hit the [NXT]
key during program execution before it will advance.
Ending a block with “No Pause” means that the program
will advance to the next block without stopping. Press the
[ 7 ] key to enter “Pause” or the [ 9 ] key for “No Pause.”
(Pressing the [ 8 ] key will enter a “Stop” command. Its use
is described later in “Linking Controllers.”)
After entering the PAUSE parameter the display will read:
Block 1:2
mm: 00.000
This indicates that you’re ready to program the movement
for block 2 in program #1. You can now dene the step size,
feed rate, and pause status just as you did for the rst block.
When you’ve entered all of the program blocks you wish,
terminate the program by entering “000.00” for the amount
of travel. This tells the controller to stop asking for new
input. After this, you will be able to run the program you’ve
just entered. Remember that the program you write should
have the total distance programmed equal to zero when all
motions are added together. This will insure that you return
to your home position. However, it would be wise to check
the handwheel position to verify this.
Insert and Delete
When entering a program, you may make a mistake and
wish to omit a block after the entire program has been
written. You can INSERT and DELETE complete blocks
to correct or modify an existing program. Without this
feature you would have to rewrite all the blocks after the
error. To access the INSERT and DELETE functions, press
the [MODE] key while the controller is waiting for you
to enter the distance for any program step. (You can’t use
INSERT or DELETE after entering the distance). When you
press the [MODE] key, the controller will cycle through
four choices: “Start Loop”, “Insert”, “Delete”, and “Exit”.
The “Start Loop” command will be explained later in these
instructions.
When the display is at the “Insert” point it may say:
Block 1:5
Insert?
You can now insert a new block by pressing the [ENTER]
key. If you wish to delete the current block, press the
[MODE] key again and then [ENTER]. Press the [MODE]
key a third time and the controller says “Exit?”. If you press
[ENTER] here, you will terminate the programming session
entirely. To return to the program block that is already
stored without making any changes, press the [MODE]
key a fourth time.
The Loop Command
If you press the [MODE] key at the very start of a new
block the display will read
Block 1:1
Begin Loop?
This means that the instructions entered from this point
to the point that an “End Loop” is entered, in the same
manner, will be repeated for as many times as entered after
entering the command “End Loop.” The “End Loop” can
only be entered after a “Begin Loop” has been entered. It is
acceptable to have a “Pause” command entered in the loop
program. This would require you to press [NXT] for each
stage of the loop; however, keep track of the loops made.
(The lower right corner of the display displays how many
times the loop has left to cycle.) You could inadvertently
start into another set of loops by pressing the [NXT] key
one time too many. Remember that the only time you will
be oered the loop command choice is when the mode key
is pressed before entering a movement number.
The LOOP COMMAND allows you to easily program a
series of identical movements.
Running a Stored Program
Enter the Program Mode using the [MODE] key and press
the [ENTER] key. You now have a choice of program 1 or
2. Enter your choice using the [ 1 ] or [ 2 ] key. Then press
the [NXT] key to run the program. The program will start.
While the table is in motion, the display will read:
Moving...
Controlling the Program while It Is Running with the Stop, Mode
and Pause Commands
The [ 8 ] key can be entered at anytime a program is running,
with or without loops and put the program in a ‘Pause”
mode. The program will stop running after the computer
completes the block it was running when the command
was entered; however the key must be held down until the
program ends its present movement. The program can be
restarted with the [NXT] key and will resume running the
program from its last completed command.
You can terminate execution at any time by pressing the
[MODE] key, which will allow you to go back and enter
a new program or start running the same one over again.
Again, the key must be held down until the move for that
block was completed.
You can press the [STOP] key at any time to abort table
motion and it will enter you into the Jog Mode. Remember
that you will lose your place and have to manually move to
your home position before running your program.
Restarting the Program
After all of the steps in the program are completed, the
program will stop and wait for you to hit the [NXT] key if
you stored a “Pause” at the end. If you stored “No Pause”,
the program will start over again immediately.
NOTE: If the controller seems to refuse to run a program,
it is probably because the rst movement in the program

P/N 8851, Pg. 6 OF 10
has been dened as “0000.00” degrees. If this happens, go
to EDIT and check the program has been edited to zero.
Old programs can be erased by holding down the [9] when
the controller is turned o and turning it on. We recommend
doing this occasionally so you can start with a “clean slate.”
The “Settings” Mode
The next mode after the Program Mode is the Settings Mode.
This allows you to enter some parameters of operation for
the controller. The controller will remember these settings.
You have a choice of Slow, Fast, Direction and Backlash.
You should be familiar enough with the controller by now
to make these entries without step-by-step instructions.
Speed Setting
This is the maximum speed the table reaches in each
movement. The units are always in millimeters per minute,
and your choices are 20, 50, 100, 200, 300, 400, 500 or
600 mm/min. The table does not have as much power at
the fastest settings, so very fast settings should only be
used for positioning.
The rst parameter that shows on the screen when you hit
[ENTER] for settings is "Speed." The default setting that
shows on the screen is 400mm/min. Below that you will
see "Press NXT or PRV." By pressing [NXT] or [PRV]
you will increase or decrease the speed setting to the next
value. For example, if you press [NXT], the value will
increase to 500mm/min. If you press [PRV], the value will
decrease to 300mm/min.
Direction Setting
This parameter allows you to enter the default direction of
travel. The default setting of “3” assumes that the controller
will be driving a RH leadscrew on the X axis of a Sherline
mill, and positive values will move the table to the right. If
the controller is used to control a dierent device, a setting
of “1” may keep programming standards conventional.
Setting the Electronic Backlash Compensation
The physical backlash in the leadscrew can be minimized
with proper adjustment; however, it cannot be eliminated.
The controller supports automatic backlash correction to
compensate for whatever actual backlash remains between
the nut and leadscrew. You can enter a two-digit number. The
number entered represents steps of the stepper motor. The
motor takes 400 steps to make one revolution. Therefore,
4 steps on a Sherline metric mill equal 0.01mm of travel.
It works in this way: Every time the table makes a motion
in the “reverse” direction, it will overshoot the amount of
travel by the backlash amount, and then move “forward”
by the same amount. This will take up any backlash. You
can set the backlash correction to any amount you like.
If you set it to zero, it will not be used. If you set it to a
small amount, it can just exactly take up the backlash in the
leadscrew. If you set it to a relatively large value, you can
see the table overshoot and then return to correct position.
You can determine how much backlash to use by trial and
error and your own preference. To evaluate the current
backlash setting, go to the Positioning Mode. Enter
something like 00.500 inches. Press the [PRV] key. The
table will move in the reverse direction and overshoot the
distance specied by the backlash amount, then change
direction and move forward by the backlash amount. If the
backlash setting is small, you won’t notice it. If it is large,
it will be easy to see.
The “Jog” Mode
The Jog Mode allows you to quickly move the table with the
keypad. In Jog Mode, with no keys held down, the motor
is unpowered. This means you can turn the crank by hand
for ne positioning. You can drive the table using the [ 1
] or [ 3 ] keys for rapid, motorized motion. The [ 7 ] and
[ 9 ] keys will move the table at the “Slow” speed set in
the SETTINGS Mode. You can also take very ne, slow
steps with the [NXT] and the [PRV] keys. When you are
nished with the Jog Mode, press the [MODE] key until
the controller is in the Mode of your choice.
Remote Trigger Switch
The controller can be operated from a remote switch. This
will allow you to keep the controller in a more “friendly”
environment and have a more durable switch used for
starting a programmed sequence. To incorporate this feature,
connect the remote trigger switch that is normally open to
the SENSE INPUT and GROUND wires of the included
8-pin connector cord. Refer to Figure 5 below. (NOTE: The
rst time a program is run, it must be initiated by hitting
the [NXT] button on the keyboard. After that, it can be
initiated from the remote switch.)
FIGURE 5—Layout of the interface male connector viewed from
the back side
Cable Color Code
Colors of the wires inside the cable are not consistent from
batch to batch, so we cannot provide a reliable color code.
Use a continuity checker and the pin map shown in Figure
5 to determine the color of the wire connected to each pin.
Note the colors on the chart in Figure 5 for future reference.
Limit Switches
The Sherline Linear Controller supports the use of limit
switches to avoid running a cutter into a xture or clamp.
The limit switches should be simple “normally open
momentary contact” type switches. You can place a limit
switch at each end of the mill table if you wire them in
parallel. Arrange the switches so they will be closed by the
motion of the table when it gets too close to something you
don’t want it to reach. The limit switches are wired into
the 8-pin interface connector at the end of the controller.
(See Figure 5.)

P/N 8851, Pg. 7 OF 10
The limit switches will be active in all motion modes,
including the JOG mode. When the controller moves into
a limit switch, it will remember that it cannot move any
farther in that direction. The controller will consider the
move complete. Any further commands to move in that
direction will also “pretend” to execute, but no actual
motion will take place. Instructions to move in the opposite
direction will work ne.
This feature will allow you to start a programmed move
from a known position with the use of a quality limit switch.
The program could drive the slide to the limit switch at
a slow feed and then start its next move from where the
limit switch stopped the movement of the slide. You could
program the last move to end against the limit switch but
in doing so you would lose the advantage of knowing that
the program will always start from the same place. Be sure
the move to the limit switch will have enough extra travel
to compensate in case an operator moved the hand wheels
between cycles.
To incorporate this feature, connect the limit switches that
have been wired in the “normally open” position to the two
pins of the included 8-pin connector cord noted as “LIMIT
SWITCH” in Figure 5.
Once the controller has moved away from the limit switch,
commands to move in that direction will again be honored.
Start-up Commands
There are several utility commands that can be issued
by holding down certain keys when the controller is rst
turned on. For example, to enter the SLAVE MODE (to run
the controller with STEP and DIRECTION signals from
another CNC controller) hold down the [ 1 ] key when you
rst turn the controller on.
The four start-up commands are:
[ 1 ] - Enter “Slave” mode.
[ 7 ] - Show the revision date of the rmware.
[ 9 ] - Erase all program memory locations.
[MODE] - Erase all program memory locations and
initialize all settings to factory defaults.
Interface Options
The following features were incorporated into the controller,
primarily to allow the Sherline CNC rotary table to be
used with standard CNC machines. They probably will
not be used with a linear slide; however, the code has been
written and may be useful in a way in which We have not
yet anticipated.
There are two interface options for the controller. They
both use the 8-pin mini-DIN connector at the top end of
the controller case. The interface options are:
• “Step” and “direction” signals for use with other motor
controllers.
• “Sense” and “acknowledge” signals for handshaking
with other CNC controllers.
Step and Direction Input
If you have a motor controller that outputs STEP and
DIRECTION signals for a fourth axis, you can use the
Sherline controller to receive these signals and move
the table. You’ll need a cable to connect the STEP and
DIRECTION signals of your other controller to the proper
pins of the interface connector on the end of the Sherline
controller.
You must put the Sherline controller into a special “Slave
Mode” to work with these signals. To do this, hold down
the [ 1 ] key on the keypad when you rst turn on the
controller. The display should read:
Slave Mode
In this mode, the controller will wait for a low-going STEP
command. As soon as it is found, the motor will move a
single step in the forward direction if the DIRECTION
input is high. If the DIRECTION input is low, the table will
move a single step in the opposite direction. There are 400
steps in a full rotation of the stepper motor. To stop using
the slave mode, turn the controller o, wait 5 seconds, and
turn it on again.
Sense and Acknowledge Input
Some CNC controllers support a SENSE and
ACKNOWLEDGE (ACK) protocol for a fourth axis with
an “M” command. When the “M” command is executed,
the controller closes a relay and then waits for the “M-FIN”
input line to go high (open circuit) while the remote device
is operating. When the remote device has nished, it must
short the M-FIN line to ground to acknowledge that the
action is complete.
The Sherline controller supports this M protocol. There is a
SENSE input line and an ACK output line in the interface
connector. The SENSE input is made active by shorting it
to ground. It is left inactive by leaving it unconnected to
ground, or by pulling it to 5 volts. The ACK output is an
“open collector” drive signal. It can be used like a switch
closure. When it is active, it will be connected to ground.
When inactive, it will be an open circuit. The ACK output
will work with signals as high as 30 volts.
The SENSE input works just like the [NXT] key on the
controller. In either of the motion modes (Positioning or
Program) where you can move the table by pressing the
[NXT] key on the keypad, you can also move the table by
shorting the SENSE input to ground. You can use some
other CNC controller to make the SENSE input low (for
example, the M command).
To connect your CNC controller to the Sherline controller,
add a relay to your CNC machine. Connect the relay switch
contacts to the Sherline controller SENSE and GROUND
lines. When your controller closes the relay, it will trigger
the Sherline controller.
Every time the [NXT] key or the SENSE input initiate a
motion, the ACK output of the Sherline controller will be
shorted to ground. As soon as the Sherline controller has
completed the motion, the ACK output will be opened (will
not be shorted to ground).

P/N 8851, Pg. 8 OF 10
Linking Two Sherline Controllers Together
The Sherline stepper motor controller has a unique feature
that allows two controllers to be linked together and perform
simple programs in unison. This allows the controllers
to perform operations that are much more complex than
what a single controller can do. They are linked together
with an optional cord plugged into the back of each unit.
It would be dicult to describe the many combinations
that could be generated using this method, so I’ll give you
a general “overview” of the rules and leave the rest up to
your imagination.
1. The Master controller that initiates the sequence may
be in any motion mode. Note: the controllers may be
either a linear or rotary type or a combination of both.
The dierence between the two is they each have code
written specically to control a linear slide or a rotary
table.
2. The second controller (called the “Controllee”) will
start its program when the Master program comes to
a block that is terminated with a “Pause” command or,
if it’s a rotary controller, it has completed a Division
Mode or Degree Mode movement.
3. The Master will be restarted when the Controllee
program comes to a block that is terminated with a
“Pause” command, or, if it’s a rotary controller, it
has completed a Division Mode or Degree Mode
movement.
4. When a programmed block is terminated with the
“Stop” command (entered with the [ 8 ] key at the end
of a program block), the program will stop and not
trigger the other controller. The operator must press
[NXT] to continue. It would be advisable to enter just
one “Stop Command”, and for it to be in a block in the
Master controller. This keeps the operator from having
to press [NXT] on both controllers to run a program.
Cutting a Gear Using All the Features of Both Linear and Rotary
Sherline Controllers
Example:
The following procedure gives you an idea of how easy it
would be to program a complex set of operations to produce
a 53-tooth gear. We chose 53 teeth because it is a prime
number and can’t be produced with simple indexing.
Linear Controller Program:
1. Rapid feed up to gear blank from home position.
No Pause
2. Slow feed across gear face with cutter. No Pause
3. Slow feed back across gear face for quality nish.
No Pause
4. Rapid feed to home position. Pause
Sherline CNC Rotary Table Controller Program:
1. Using the Division Mode, enter the number 53
With ve lines of code (keypad entries) you have now
entered all the information needed to produce a 53-tooth
gear. Think about it. The slide will rapid up to the cutter,
slow down and make a cut, feed back across the part at
a programmed feed rate, and rapidly return to its home
position. The rotary table will then index, and initiate the
next cut. This will be repeated until the required 53 indexes
have been made. After the last index, the program will
stop and wait for an operator. This has been accomplished
inexpensively with a very clever design and program, and
we at Sherline and Bryan and quite proud of it.
Two Linear controllers could be linked to produce any
number of sequences for simple but useful movements. For
example, one controller could drive the mill table X-axis,
and the other could drill with the Z-axis.
Thanks for Your Support
We at Sherline wish to thank our customers for their
continued support. It is becoming very dicult to compete
in a world market where employers in the US pay more in
benets each month than the entire wage paid to workers
in third world countries. We survive by having modern
equipment and facilities with skilled workers who care
about our customers and product line. We believe it shows,
and it is our way of thanking you.
Thank you,
Sherline Products Inc.
Technical Assistance
For technical assistance regarding the mechanical portions
of this product, please call Sherline Products Inc. at (760)
727-5857, fax (760) 727-7857. For technical assistance
regarding the electronic portion of this product, please
contact Bryan Mumford and the following address:
Bryan Mumford, Mumford Micro Systems
3933 Antone Road, Santa Barbara, CA 93110
Phone: (805) 687-5116
Fax: (805) 687-4905
http://www.bmumford.com
A Note Regarding Speed Control
The metric linear controller utilizes an 8-bit computer
chip which does not provide the innite speed control
possible in a larger computer. It was designed to oer a cost
eective solution in a small package with intuitive operation
compared to using an expensive personal computer. Eight
speeds from 20mm/min to 600mm/min are oered that
should accommodate the needs of virtually all users of
this type of control.

P/N 8851, Pg. 9 OF 10
Parts List
NO.
REQ.
PART
NO.
DESCRIPTION
4 12050 8-32 x 3/8" SHC Screw
1 40520 10-32 x 3/16" cup point set screw
1 67102 Stepper motor mount
1 67105 CNC Coupling
1 67106 CNC Coupling Preload nut (RH)
1 67107 CNC Coupling Preload nut (LH)
2 67111 8-32 x 7/8" SHC Screw
1 67115 5-40 x 7/8" SHC Screw
1 67117 CNC Template, side bushing (rectangular)
2 67120 Stepper motor preload bearing
1 8800 Linear controller (for CNC-Ready)
Sherline Industrial Products Division
Sherline has now introduced a line of small machine slides
and spindles for use in industrial and production line
applications. Based on components of the Sherline lathe
and mill, these slides can be assembled in “building block”
fashion to make a wide variety of movements possible.
Special tooling can be built up quickly and at a very low
cost as long as the size is appropriate. Manual and CNC-
ready components are available. With the use of stand-alone
CNC controllers like this P/N 8850 linear controller, tooling
can be assembled and on the job in a matter of hours, not
days. For details, see:
www.sherlineIPD.com.
NOTE: The power supply included with this indexer is intended to operate only on
115/120 VAC, 60 Hz (38 W) current. For countries operating on 100, 220 or 240VAC
and/or 50Hz a transformer will be required. As an alternative, this power supply
outputs 24VDC, 1 Amp (1000 mA). If you can purchase an appropriate power supply
that operates on local current and outputs 24VDC, 1A current, it could be used to power
the unit instead of the one supplied. Sherline Products does not provide a 220V power
supply or transformer.

P/N 8851, Pg. 10 OF 10
Block Move Feed Pause Block Move Feed Pause
(Copy this page and save it as a master for future program records.)
Program Sheet
Program 1 Program 2
This manual suits for next models
1
Table of contents
Other Sherline Products Controllers manuals
Popular Controllers manuals by other brands
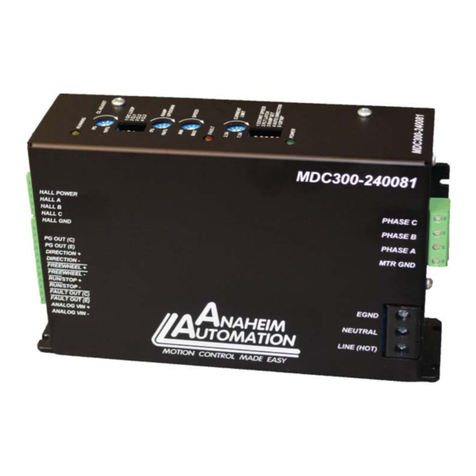
Anaheim Automation
Anaheim Automation MDC300-240081 Series user guide
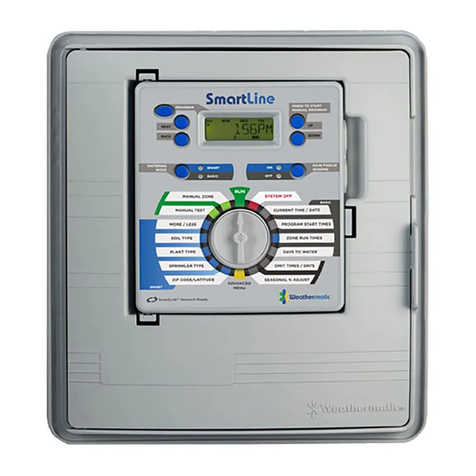
Weathermatic
Weathermatic smartline SL800 owner's manual
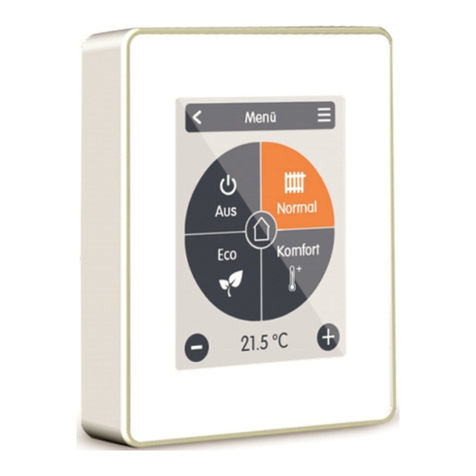
Sorel
Sorel CALEON Smart Installation and operating instruction

Panduit
Panduit Atlona AT-DISP-CTRL installation guide

Icop
Icop VDX2-6524 user manual
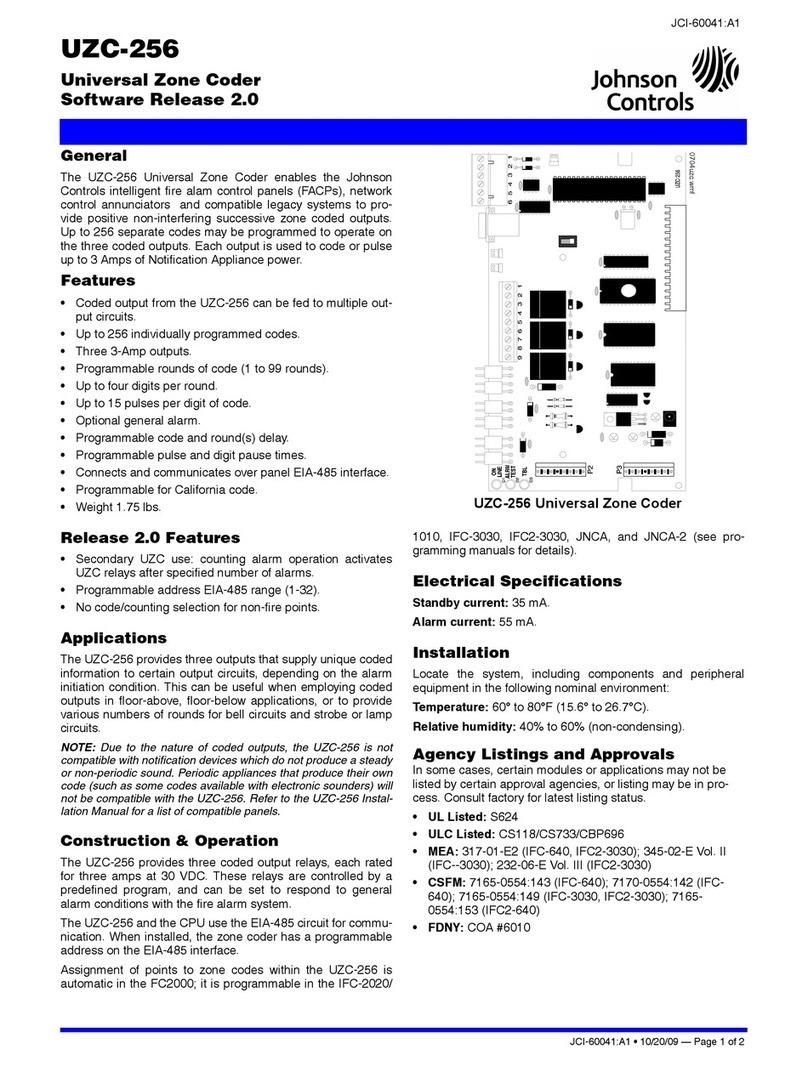
Johnson Controls
Johnson Controls UZC-256 manual