Shihlin SS2 Series User manual

Shihlin Electric SS2 Series AC Drive
Installation Guide
Compact Design Vector control AC Drive
SS2-021-0.4K~2.2K
SS2-023-0.4K~3.7K
SS2-043-0.4K~5.5K
Thank you for choosing Shihlin SS2 series AC Drive.
The instruction will describe on the use and points for attention of products. Before installing, please be sure to carefully read the
Instruction, so that the inverter can be used in proper and safe way.
1) Safety Instructions
Safety Instructions
Installation, operation, maintenance and inspection must be performed by qualified personnel.
In this instruction, the safety instruction levels are classified into "Warning" and "Caution".
Warning: Incorrect handling may cause hazardous conditions, resulting in death or severe injury.
Caution: Incorrect handling may cause hazardous conditions, resulting in medium or slight injury, or may cause only material damage.
Warning
While the inverter power is ON, do not open the front cover or the wiring cover. Do not run the inverter with the front cover or the wiring cover
removed. Otherwise you may access the exposed high voltage terminals or the charging part of the circuitry and get an electric shock.
It is crucial to turn off the motor drive power before any wiring installation or inspection is made. Even if power supply was cut off, residual voltage is
in the internal capacitor. After the power cut off, waiting time should be no shorter than the time in inverter logo.
The inverter must be connected to the ground properly.
Do not operate or touch the radiator or handle the cables with wet hands. Otherwise you may get an electric shock.
Do not change the cooling fan while power is ON. It is dangerous to change the cooling fan while power is ON.
Caution
The voltage applied to each terminal must be the ones specified in the Instruction Manual. Otherwise burst, damage, etc. may occur.
Don't conduct a pressure test on components inside inverter, for semiconductor of inverter is easily to be broke down and damaged by high voltage.
While power is ON or for some time after power-OFF, do not touch the inverter as it will be extremely hot. Touching these devices may cause a burn.
The cables must be connected to the correct terminals. Otherwise burst, damage, etc. may occur.
The polarity (+ and -) must be correct. Otherwise burst, damage, etc. may occur.
Inverter must be installed on a nonflammable wall without holes (so that nobody touches the inverter heat sink on the rear side, etc.). Mounting it to
or near flammable material may cause a fire.
If the inverter has become faulty, the inverter power must be switched OFF. A continuous flow of large current may cause a fire.
2) Description of Product Model Number
SS2 - 043 - 0.75K - * *
Series category
Voltage level
Capacity
Others
SS2 series
-043:440V three-phase
-023:220V three-phase
-021:220V single-phase
0.75kW
None:General model
-**:Customer motor or dedicated motor or region
difference
3) Installation Environment
Ambient temperature
-10 ~ +50℃(non-freezing).
Ambient humidity
Below 90%Rh (non-condensing).
Storage temperature
-20 ~ +65℃.
Surrounding environment
Indoor, no corrosive gas, no flammable gas, no flammable powder.
Altitude
Altitude below 1000 meters
Vibration
Below 5.9m/s2(0.6G).
Grade of protection
IP20
The degree of pollution
2
4) Installation and Wiring
Please ensure vertical arrangement to keep the cooling effect:
A
ABDE
C
C
F
(a) Vertical arrangement (b)Horizontal arrangement (c) Level arrangement
Please comply with installation conditions shown below to ensure enough ventilation space and wiring space for inverter
cooling
Arrangement of single or paralleling inverter:
A
ABDE
C
C
F
Unit :mm
Arrangement of multiple inverters:
Enclosure
Guide
Inverter Inverter Inverter Inverter
Inverter Inverter
Guide Guide
Enclosure
(a)Horizontal arrangement (b)Vertical arrangement
Note1: When mounting inverters of different sizes in parallel, please align the clearance below each inverter to install, which is easy to change the cooling
fan.
Note2: When it is inevitable to arrange inverters vertically to minimize space,take such measures as to provide guides since heat from the bottom
inverters can increase the temperatures in the top inverters, causing inverter failures.
Installation of DIN rail:
2
1
1
2
(a) installation (b) disassembly
5) Terminal Connection Diagrams
6) Main Circuit Wiring and Terminal Specification
The inverter
model
Terminal
screw
specifications
Tightening
torque
(Kgf.cm)
Recommended wiring specification(mm2)
Recommended wiring specification (AWG)
R、S、T
U、V、
W
+/P、
PR
Grounding
Cable
R、S、T
U、V、
W
+/P、
PR
Grounding
Cable
SS2-043-0.4K
M3.5
12.2
1.5
1.5
1.5
1.5
16
16
16
16
SS2-021-0.4K
2.5
2.5
2.5
2.5
14
14
14
14
SS2-023-0.4K
2.5
2.5
2.5
2.5
14
14
14
14
SS2-043-0.75K
2.5
2.5
2.5
2.5
14
14
14
14
SS2-021-0.75K
2.5
2.5
2.5
2.5
14
14
14
14
SS2-023-0.75K
2.5
2.5
2.5
2.5
14
14
14
14
SS2-043-1.5K
2.5
2.5
2.5
2.5
14
14
14
14
SS2-023-1.5K
2.5
2.5
2.5
2.5
14
14
14
14
SS2-021-1.5K
M4
18
2.5
2.5
2.5
2.5
14
14
14
14
SS2-043-2.2K
2.5
2.5
2.5
2.5
14
14
14
14
SS2-021-2.2K
4
4
4
4
12
12
12
12
SS2-023-2.2K
4
4
4
4
12
12
12
12
SS2-043-3.7K
2.5
2.5
2.5
2.5
10
14
14
14
SS2-043-5.5K
2.5
2.5
2.5
2.5
14
14
14
14
SS2-023-3.7K
4
4
4
4
12
12
12
12
7) Control Terminal
Arrangement of control terminal
Control terminal description
Terminal type
Terminal name
Function instructions
Terminal specifications
Digital signal
input
STF
There are totally eight multi-function control
terminals, which can switch the mode of
SINK/SOURCE.
Input impedance: 4.7 kΩ
Action current:5mA (when 24VDC)
Voltage range: 10~28VDC
Maximum frequency: 1kHz
STR
M0
M1
M2
RES
SD
Digital signal ground
---
PC
In Source mode, digital signal power.
The voltage is +24V, the allowable load current is 50mA
Analog signal
input
10
The terminal inside with +12v power is allowable
load current with 5 mA..
Maximum current:10mA
Input impedance:10 kΩ
2
Voltage is 0~5v or 0~10v or 4~20mA input point,
to set the target frequency.
4
5
common reference of 10, 2, 4, and AM terminal
---
Relay output
A
Multi-function relay output terminals.
A-C is the normally open contact, B-C is the
normally close contact.
Contact ability VDC30V/VAC230V-0.3A
B
C
Communication
terminal
RJ45
The communication interface of frequency
converter and the upper machine/DU06.
Highest rate:19200bps
Longest distance:500m
Analog output
terminals
AM
External simulation table, indicating the output
frequency or output current。
Note: output voltage of AM is PWM pulse form,
therefore the analog voltage only is suitable for
external moving coil type header, not suitable for
connect to the digital meter header or as A/D
conversion signal to PLC and controller use.
Output signal: DC 0~10V
Load current : 1mA
Collector output
SO
This terminal is also known as the "multi-function
output terminal".
Contact ability VDC 24V-0.1A
SE
Reference to the open collector output
Note1:When connecting control terminal with external devices, please pay attention to the voltage and current specifications of terminals, avoiding
damaging the inverter.
Note2:The function of the control terminal is decided by inverter parameters, please refer to Instruction Manual for setting.
Note3:Please pay attention to polarity when connecting external power and devices.
Wiring method
Power supply connection
For the control circuit wiring, strip off the sheath of a cable, and use it with a blade terminal. For a single wire, strip off the sheath of
the wire and apply directly.
Insert the blade terminal or the single wire into a socket of the terminal.
(1) Strip off the sheath for the below length. If the length of the sheath peeled is too long, a short circuit may occur with neighboring
wires. If the length is too short, wires might come off.
Wire the stripped cable after twisting it to prevent it from becoming loose. In addition, do not solder it.
7mm
(2) Crimp the blade terminal.
Insert wires to a blade terminal, and check that the wires come out for about 0 to 0.5 mm from a sleeve.
Check the condition of the blade terminal after crimping. Do not use a blade terminal of which the crimping is inappropriate, or the
face is damaged.
0~0.5mm
Please do use blade terminals with insulation sleeve. Blade terminals commercially available:
Cable gauge
(mm²)
Blade terminals model
L (mm)
d1
(mm)
d2 (mm)
Manufacturer
Crimping tool
product number
0.3
AI 0,25-6 WH
10.5
0.8
2
Phoenix Contact
Co., Ltd.
CRIMPFOX 6
0.5
AI 0,5-6 WH
12
1.1
2.5
0.75
AI 0,75-6 GY
12
1.3
2.8
0.75(for two wires)
AI-TWIN 2×0,75-6 GY
12
1.3
2.8
Wiring Precautions
After wiring, wire offcuts must not be left in the inverter.
Wire offcuts can cause an alarm, failure or malfunction. Always keep the inverter clean.
When drilling holes in a controller, please take caution not to allow chip powder to enter the inverter.
To prevent a malfunction due to noise, keep the signal cables 10 cm (3.94 inches) or more away from the power cables. Also,
Separate the main circuit cables at the input side from the main circuit cables at the output side.
Set the voltage/current input switch correctly. Incorrect setting may cause a fault, failure or malfunction.
Size
Frame A
Frame B
A
50
50
B
50
50
C
100
100
D
50
50
E
50
50
F
ventilation direction
Note1: Please Use a small flat head screw driver (tip thickness: 0.6 mm, width: 3.0mm). If a flat head screw driver with a narrow tip is used, terminal
block may be damaged.
Note2: Tightening torque is 3.2~4.8kgf.cm, too large tightening torque can cause screw slip, too little tightening torque can cause a short circuit or
malfunction.

8) Appearance and Dimensions
Frame A
H
W
D
Read the manual and follow the safety
instructions before use
Isolate from supply and wait 10 minutes
before removing this cover
Ensure proper earth connection
CAUTION:Risk of fire
Mount the inverter on a non combustible
surface
危险:可能导致伤害和触电
安装运转之前请详细阅读说明书,并按
指示操作
通电中或切断电源后10分钟内请勿打开
上盖
请确保可靠接地
注意:可能导致火灾
请安装于金属等不燃物上
DANGER:Risk of injure and electric shock
W1
H1
13
4.5
2×R2.5
H2
Unit: mm
Type
W
W1
H
H1
H2
D
SS2-021-0.4K
80
58
174
165
51.5
134
SS2-021-0.75K
SS2-023-0.4K
SS2-023-0.75K
SS2-023-1.5K
SS2-043-0.4K
SS2-043-0.75K
SS2-043-1.5K
Frame B
DANGER:Risk of injure and electric shock
请安装于金属等不燃物上
注意:可能导致火灾
安装运转之前请详细阅读说明书,并按
指示操作
通电中或切断电源后10分钟内请勿打开
上盖
请确保可靠接地
危险:可能导致伤害和触电
Mount the inverter on a non combustible
surface
CAUTION:Risk of fire
Read the manual and follow the safety
instructions before use
Isolate from supply and wait 10 minutes
before removing this cover
Ensure proper earth connection
H1
H
D
2×R2.5
4.5
43.5
W1
W
H2
Unit: mm
Type
W
W1
H
H1
H2
D
SS2-021-1.5K
110.5
58
174
165
51.5
134
SS2-021-2.2K
SS2-023-2.2K
SS2-023-3.7K
SS2-043-2.2K
SS2-043-3.7K
SS2-043-5.5K
9) Optional Equipment
Category
Name
Description
Order code
Manipulator
DU06
LED Manipulator
SNKDU06
10) Parameter table
Parameter
number
Name
Setting range
Default
User setting
P.0
Torque boost
0~30%
6%(0.4kW~0.75kW)
4%(1.5kW~3.7kW)
3%(5.5kW)
P.1
Maximum frequency
0~120Hz
120Hz
P.2
Minimum frequency
0~120Hz
0Hz
P.3
Base frequency
0~650Hz
50Hz/60Hz(Note)
P.4
Speed 1 (high speed)
0~650Hz
60Hz
P.5
Speed 2 (medium speed)
0~650Hz
30Hz
P.6
Speed 3 (low speed)
0~650Hz
10Hz
P.7
Acceleration time
0~360.00s/0~3600.0s
5s(3.7KW and below)
10s(5.5KW)
P.8
Deceleration time
0~360.00s/0~3600.0s
5s(3.7KW and below)
10s(5.5KW)
P.9
Electronic thermal relay capacity
0~500A
0A
P.10
DC injection brake operation frequency
0~120Hz
3Hz
P.11
DC injection brake operation time
0~60s
0.5s
P.12
DC injection brake operation voltage
0~30%
4%
P.13
Starting frequency
0~60Hz
0.5Hz
P.14
Load pattern selection
0:Applicable to constant torque
loads(convey belt, etc.)
0
1:Applicable to variable torque loads
(fans and pumps, etc.)
2, 3: Applicable to ascending /
descending loads.
4: Multipoint VF curve.
5~13:Special two-point VF curve.
P.15
JOG frequency
0~650Hz
5Hz
P.16
JOG acceleration/deceleration time
0~360.00s/0~3600.0s
0.5s
P.17
Input signal across terminal 4-5
selection
0:Current signal valid
0
1:0~10V voltage signals across
terminal
2:0~5V voltage signals across terminal
P.18
High-speed maximum frequency
120~650Hz
120Hz
P.19
Base frequency voltage
0~1000V, 9999
9999
P.20
Acceleration/deceleration reference
frequency
1~650Hz
50Hz/60Hz(Note)
P.21
Acceleration/deceleration time
increments
0:Minimum setting increment:0.01s
0
1:Minimum setting increment:0.1s
P.22
Stall prevention operation level
0~250%
200%
P.23
Compensation factor at level reduction
0~200%, 9999
9999
P.24
Speed 4
0~650Hz, 9999
9999
P.25
Speed 5
0~650Hz, 9999
9999
P.26
Speed 6
0~650Hz, 9999
9999
P.27
Speed 7
0~650Hz, 9999
9999
P.28
Output frequency filter constant
0~31
0
P.29
Acceleration/deceleration curve
selection
0: Linear acceleration /deceleration
curve
0
1: S pattern acceleration /deceleration
curve 1
2: S pattern acceleration /deceleration
curve 2
3: S pattern acceleration /deceleration
curve 3
P.30
Regenerative brake function selection
0:If regenerative brake duty is 3%
fixed, the value of parameter 70 is
invalid.
0
1:The regenerative brake duty is the
value of parameter 70 setting
P.31
Soft-PWM selection
0~2
0
P.32
Serial communication Baud rate
selection
0:Baud rate: 4800bps
1
1:Baud rate: 9600bps
2:Baud rate: 19200bps
3:Reserved
P.33
Communication protocol selection
0: Modbus protocol
1
1: Shihlin protocol
P.34
Communication EEPROM writing selection
0: Write parameters in communication
mode, write into RAM and EEPROM.
0
1: Write parameters in communication
mode, write into only RAM .
P.35
Communication Running and Speed
Command Selection
0: In communication mode, operating
instruction and setting frequency is set
by communication.
0
1: In communication mode, operating
instruction and setting frequency is set
by external.
P.36
Inverter station number
0~254
0
P.37
Speed display
0~5000.0r/min, 0~9999r/min
0 r/min
P.38
The maximum operation frequency (the
target frequency is set by the input
signal of terminal 2-5)
1~650Hz
50Hz/60Hz(Note)
P.39
The maximum operation frequency (the
target frequency is set by the input
signal of terminal 4-5)
1~650Hz
50Hz/60Hz(Note)
P.40
Multi-function output terminal pattern
0:RUN (Inverter running): Signal will
be output when the output frequency is
equal to or higher than the starting
frequency.
0
1:SU (Up to frequency): Signal will be
output once the output frequency has
reached the set region of frequency.
2:FU (Output frequency detection):
Signal will be output once the output
frequency has reached or exceeded
the detection frequency set
3:OL (Overload detection): Signal will
be output once the current limit function
is triggered. (About OL2 detection,
please refer to over torque detection
selection P.260)
4:OMD (Zero current detection): If the
output current percentage of the
inverter is less than the set value of
P.62, and lasts for the pre-defined time
(the setting value of P.63), OMD will
output signal
5:ALARM (Alarm detection): Alarm
detection
6:PO1 (Section detection): At the
programmed operation mode, PO1
signal will be output in the end of each
section
7:PO2 (Periodical detection): At the
programmed operation mode, PO2
signal will be output at the end of each
cycle.
Parameter
number
Name
Setting range
Default
User
setting
P.40
Multi-function output terminal pattern
8:PO3 (Pause detection): At the programmed
operation mode, PO3 signal will be output when
the inverter pauses
0
9:BP (Inverter output): Switch between the inverter
operation and commercial power-supply operation
function. During the inverter operation, BP will
output signals
10:GP (Commercial power-supply output): Switch
between the inverter operation and commercial
power-supply operation function. During the
commercial power-supply operation, GP will output
signals
11:OMD1(zero current detection): When the
output frequency of inverters reach to the target
frequency and the percentage of the output current
is lower than the set value of P.62, OMD1 will
output signal after a certain time set by P.63
12:OL2 (Over torque alarm output): Please refer to
over torque detection selection P.260
17:RY (the inverter running preparation
accomplishment): RY signal will be sendout if
inverter is in the state of being able to run
18:Maintenance Alarm detection
19~40:Reserved
41: Output when PID feedback signal disconnect:
(refer to P.254 Analog signal feedback loss action
selection)
P.41
Up-to-frequency sensitivity
0~100%
10%
P.42
Output frequency detection for forward
rotation
0~650Hz
6Hz
P.43
Output frequency detection for reverse
rotation
0~650Hz, 9999
9999
P.44
The second acceleration time
0~360.00s/0~3600.0s,9999
9999
P.45
The second deceleration time
0~360.00s/0~3600.0s,9999
9999
P.46
The second torque boost
0~30%,9999
9999
P.47
The second base frequency
0~650Hz, 9999
9999
P.48
Data length
0:8bit
0
1:7bit
P.49
Stop bit length
0:1bit
0
1:2bit
P.50
Parity check selection
0: No parity verification
0
1: Odd
2: Even
P.51
CR & LF selection
1: CR only
1
2: Both CR and LF
P.52
Number of communication reties
0~10
1
P.53
Communication check time interval
0~999.8s, 9999
9999
P.54
AM terminal function selection
0: Output frequency, frequency display reference (P.55)
is 100%.
0
1: Output current, use 02-52 (P.56) value as 100%.”
2: Output DC bus voltage, the OV level is 100%
3: Output the temperature rising accumulation rate of
inverter, the NTC level is 100%
4: Output the electronic thermal rate of the inverter, the
electronic thermal relay running (06-00(P.9)≠0) or the
electronic thermal relay of the inverter’s IGBT module
running (06-00(P.9)=0) is 100%
5:The output corresponding to a set frequency
P.55
Frequency display reference
0~650Hz
50Hz/60Hz(Note)
P.56
Current monitoring reference
0~500A
Rated output
current
P.57
Restart coasting time
0~30s, 9999
9999
P.58
Restart cushion time
0~60s
10s
P.59
The choice of locking operation
keyboard knob setting
XXX0: the default value, reserved
0
XXX1: The knob on the DU08 set frequency
effectively
XX0X: No shuttle knob SET function
XX1X: The shuttle knob as a function of the SET
X0XX: Changing frequency and automatic storage
within 30 s
X1XX: Changing frequency and automatic storage
within 10 s
X2XX: After changing the frequency,doesen’t
storge automatically Setting Range
0XXX: After to shuttle set frequency, the frequency
of changes take effect immediately
1XXX: After to shuttle set frequency and the set
key run , the frequency of change take effect
P.60
Input signal filtering constant
0~31
31
P.61
Remote setting function selection
0: No remote setting function.
0
X1: Remote setting function, frequency setup
storage is available.
X2: Remote setting function, frequency setup
storage is not available.
X3: Remote setting function, frequency setup
storage is not available, the remote setting
frequency is cleared by STF/STR “turn off”.
X4: Remote control function, frequency save in memory
every 5s
1X:Frequency command range P.2~P.1, frequency
command value from RH,RM setting
P.62
Zero current detection level
0~200%, 9999
5%
P.63
Zero current detection time
0.05~60s, 9999
0.5s
P.64
Pulse output selection
0:SO function
0
1:FM/10X function
P.65
Retry selection
0: Retry is invalid.
0
1: Over-voltage occurs, the AC Drive will perform
the retry function.
2: Over-current occurs, the AC Drive will perform
the retry function.
3: Over-voltage or over-current occurs, the AC
Drive will perform the retry function.
4: All the alarms have the retry function.
P.66
Stall prevention operation reduction
starting frequency
0~650Hz
50Hz/60Hz(Note)
P.67
Number of retries at alarm occurrence
0~10
0
P.68
Retry waiting time
0~360s
6s
P.69
Retry accumulation time at alarm
0
0
P.70
Special regenerative brake duty
0~30%
0
P.71
Idling braking and linear braking
selection
0:Idling brake
1
1:Dc brake
P.72
Carrier frequency
1~15
5

Parameter
number
Name
Setting range
Default
User
setting
P.73
Voltage signal selection
0: The range for the input voltage signal
(terminal 2-5) is 0~5V
1
1:The range for the input voltage signal
(terminal 2-5) is 0~10V
P.74
10X output selection
0~10
0
P.75
Stop or Reset function selection
0: Press STOP button and stop the operation
only in PU and H2 mode
1
1: Press STOP button and stop the operation
in all mode.
P.76
Reserve
---
---
P.77
Parameters write protection
0: Parameters can be written only when the
motor stops.
0
1: Parameters cannot be written.
2: Parameters can also be written when the
motor is running.
4: Parameters cannot be written when in
password protection.
P.78
Forward/reverse rotation prevention
selection
0, 1, 2
0
P.79
Operation mode selection
0~8
0
P.80
Multi-function terminal M0 function
selection
0: STF(the AC Drive runs forward)
2
1: STR(the AC Drive runs reverse)
2: RL(Multi-speed low speed)
3: RM(Multi-speed medium speed)
4: RH(multi-speed high speed)
5: AU
6:OH
7:MRS
8:RT
9:EXT
10: STF+EXJ
11: STR+EXJ
12: STF+RT
13: STR+RT
14: STF+RL
15: STR+RL
16: STF+RM
17: STR+RM
18: STF+RH
19: STR+RH
20: STF+RL+RM
21: STR+RL+RM
22: STF+RT+RL
23: STR+RT+RL
24: STF+RT+RM
25: STR+RT+RM
26: STF+RT+RL+RM
27: STR+RT+RL+RM
28: RUN(the AC Drive runs forward)
29: STF/STR(it is used with RUN, when
STF/STR is ”on”, AC Drive runs reverse;
when STF/STR is “off”, the AC Drive runs
forward)
30: RES(external reset function)
31: STOP(it can be used as a three-wire
mode with the RUN signal or the
STF-STR terminal)
32: REX(multi-speed set (16 levels))
33: PO(in “external mode", programmed
operation mode is chosen)
34: RES_E (external reset become valid only
when the alarm goes off.)
P.80
Multi-function terminal M0 function
selection
35: MPO (in “external mode” manually
operation cycle mode is chosen.)
2
36: TRI(triangle wave function is chosen)
37:GP_BP
38:CS
39: STF/STR +STOP (The motor has a
reverse rotation when the RUN signal is on.
When it is off, stop the motor and then run
the motor for forward rotation.)
40: P_MRS (the AC Drive output
instantaneously stops, The MRS is pulse
signal input)
43: RUN_EN (the digital input terminal
running enable)
44: PID_OFF (digital input terminal stopping
PID enable)
45: The second mode
P.81
Multi-function terminal M1 function
selection
Same as P.80
3
P.82
Multi-function terminal M2 function
selection
Same as P.80
4
P.83
Multi-function terminal STF function
selection
Same as P.80
0
P.84
Multi-function terminal STR function
selection
Same as P.80
1
P.85
Function selection for multi-function relay
0: RUN(AC Drive running)
5
1: SU(reaching the output frequency)
2: FU(output frequency detection)
3: OL(overload detection)
4: OMD(zero current detection)
5:ALARM (Alarm detection)
6:PO1 (Section detection)
7: PO2
8:PO3
9:BP (Inverter output)
10:GP
11:OMD1(zero current detection)
12:OL2(Over torque alarm output)
13~16: Reserve
17: RY(the accomplishment of AC Drive
running preparation)
18: Maintenance alarm detection
19~40:Reserved
41: Output when PID feedback signal
disconnect:(refer to P.254 Analog signal
feedback loss action selection)
P.86
Multi-function terminal RES function
selection
Same as P.80
30
P.87
Multi-Function control terminal input
positive/negative logic selection
0~63
0
P.88
Multi-function output terminal
positive/negative logic selection
0~3
0
P.89
Slip compensation coefficient
0~10
0
P.90
The inverter model
---
---
P.91
Frequency jump 1A
0~650Hz, 9999
9999
P.92
Frequency jump 1B
0~650Hz, 9999
9999
P.93
Frequency jump 2A
0~650Hz, 9999
9999
Parameter
number
Name
Setting range
Default
User
setting
P.94
Frequency jump 2B
0~650Hz, 9999
9999
P.95
Frequency jump 3A
0~650Hz, 9999
9999
P.96
Frequency jump 3B
0~650Hz, 9999
9999
P.97
The second frequency source
0:Frequency is given by operation panel PU
0
1:Frequency is given by communication
2:Frequency is given by external terminal
P.98
Middle frequency 1
0~650Hz
3Hz
P.99
Output voltage 1 of middle frequency
0~100%
10
P.100
Minute/second selection
0: The minimum increment of run time is 1 minute.
1
1: The minimum increment of run time is 1 second.
P.101
Runtime of section 1 in programmed
operation mode
0~6000s
0s
P.102
Runtime of section 2 in programmed
operation mode
0~6000s
0s
P.103
Runtime of section 3 in programmed
operation mode
0~6000s
0s
P.104
Runtime of section 4 in programmed
operation mode
0~6000s
0s
P.105
Runtime of section 5 in programmed
operation mode
0~6000s
0s
P.106
Runtime of section 6 in programmed
operation mode
0~6000s
0s
P.107
Runtime of section 7 in programmed
operation mode
0~6000s
0s
P.108
Runtime of section 8 in programmed
operation mode
0~6000s
0s
P.110
Operation panel monitoring selection
0: When AC Drive starts, the operation panel enters
the monitoring mode automatically, and the screen
displays the output frequency.( this frequency for slip
compensation)
0
1: When the AC Drive starts, the screen of the
operation panel displays the target frequency.
2: When AC Drive starts, operation panel enters
monitoring mode automatically, and screen displays
current output frequency.
3:When inverter starts, built-in keypad enters monitor
mode automatically, screen displays current pressure
and feedback
pressure of the constant pressure system in
percentage (note)
4: When AC Drive starts, operation panel doesn’t
enter monitoring mode automatically, and screen
displays the mode of starting.
5:When inverter starts, built-in keypad enters monitor
mode automatically, screen displays current pressure
and feedback
pressure of the constant pressure system (Only valid
on built-in keypad)
P.111
Acceleration/deceleration time of section 1
0~600s/0~6000s
0s
P.112
Acceleration/deceleration time of section 2
0~600s/0~6000s
0s
P.113
Acceleration/deceleration time of section 3
0~600s/0~6000s
0s
P.114
Acceleration/deceleration time of section 4
0~600s/0~6000s
0s
P.115
Acceleration/deceleration time of section 5
0~600s/0~6000s
0s
P.116
Acceleration/deceleration time of section 6
0~600s/0~6000s
0s
P.117
Acceleration/deceleration time of section 7
0~600s/0~6000s
0s
P.118
Acceleration/deceleration time of section 8
0~600s/0~6000s
0s
P.119
The dead time of positive and reverse
rotation
0~3000s
0s
P.120
Output signal delay time
0~3600s
0s
P.121
Run direction in each section
0~255
0
P.122
Cycle selection
0~8
0
P.123
Acceleration/deceleration time setting
selection
0: The acceleration time is determined by P.7the
deceleration time is determined by P.8.
0
1: The acceleration time and deceleration time are
both determined by P.111~P.118.
P.131
Frequency of section 1
0~650Hz
0Hz
P.132
Frequency of section 2
0~650Hz
0Hz
P.133
Frequency of section 3
0~650Hz
0Hz
P.134
Frequency of section 4
0~650Hz
0Hz
P.135
Frequency of section 5
0~650Hz
0Hz
P.136
Frequency of section 6
0~650Hz
0Hz
P.137
Frequency of section 7
0~650Hz
0Hz
P.138
Frequency of section 8
0~650Hz
0Hz
P.139
Voltage signal bias
0%~100%
0%
P.140
Voltage signal gain
0.1%~200%
100%
P.141
Voltage signal bias direction and rotational
direction setup
0~11
0
P.142
Speed 8
0~650Hz
0Hz
P.143
Speed 9
0~650Hz, 9999
9999
P.144
Speed 10
0~650Hz, 9999
9999
P.145
Speed 11
0~650Hz, 9999
9999
P.146
Speed 12
0~650Hz, 9999
9999
P.147
Speed 13
0~650Hz, 9999
9999
P.148
Speed 14
0~650Hz, 9999
9999
P.149
Speed 15
0~650Hz, 9999
9999
P.150
Restart mode selection
XXX0:No frequency search
0
XXX1:Reserve
XXX2:Reduced voltage way
XX0X: Electricity once
XX1X: Every time I start
XX2X: Only the instantaneous stop to rev.
P.151
Zero-speed control function selection
0, 1
0
P.152
Voltage instruction at zero-speed control
0~30%
5%
P.153
Communication error handling
0: Warn and call to stop
0
1: Don't alarm and continue running
P.154
Modbus communication data format
0:1、7、N、2 (Modbus, ASCII)
4
1:1、7、E、1 (Modbus, ASCII)
2:1、7、O、1 (Modbus, ASCII)
3:1、8、N、2 (Modbus, RTU)
4:1、8、E、1 (Modbus, RTU)
5:1、8、O、1 (Modbus, RTU)
P.155
Over torque detection level
0~200%
0%
P.156
Over torque detection time
0~60s
1s
P.157
External terminals filter adjusting function
0~200ms
4ms
Parameter
number
Name
Setting range
Default
User
setting
P.158
External terminal power enable
0: Digital input terminal power unable
0
1: Digital input terminal power enable
P.159
energy-saving control function
0: Normal running mode.
0
1: Energy-saving running mode.
P.160
Reserve
---
---
P.161
Multi-function display selection
0~9, 11~13, 19~21
0
P.162
Middle frequency 2
0~650Hz, 9999
9999
P.163
Output voltage 2 of middle frequency
0~100%
0
P.164
Middle frequency 3
0~650Hz, 9999
9999
P.165
Output voltage 3 of middle frequency
0~100%
0
P.166
Middle frequency 4
0~650Hz, 9999
9999
P.167
Output voltage 4 of middle frequency
0~100%
0
P.168
Middle frequency 5
0~650Hz, 9999
9999
P.169
Output voltage 5 of middle frequency
0~100%
0
P.170
PID function selection
0:PID function non-selected
0
1:The target value is determined by P.225. The feedback
value is determined by the voltage of terminal 2-5.
2:The target value is determined by P.225. The feedback
value is determined by the voltage of terminal 4-5.
P.171
PID feedback control method selection
0: Negative feedback control
0
1:Positive feedback control
P.172
PID proportion gain
1~100
20
P.173
PID integration gain
0~100s
1s
P.174
PID differential gain
0~1000ms
0 ms
P.175
Abnormal deviation level
0~100%
0
P.176
Exception duration time
0~600s
0s
P.177
Exception handling mode
0: Free stop
0
1: Decelerate and stop
2: Continue to run when the alarm goes off
P.178
Sleep detects deviation
0~100%
0
P.179
Sleep detects duration time
0~255s
1s
P.180
Revival level
0~100%
90%
P.181
Outage level
0~120Hz
40Hz
P.182
Integral upper limit frequency
0~120Hz
50Hz/60H
z(Note)
P.183
Deceleration step length with stable
pressure
0~10Hz
0.5Hz
P.184
4-5 terminal disconnection handling
0: No disconnection selection is available.
0
1: Decelerate to 0Hz, the digital output terminal will set off
the alarm
2: AC Drive will stop immediately, and the panel will display
“AErr” alarm.
3: AC Drive will run continuously according to frequency
reference before disconnection. The digital output terminal
will set off alarm.
P.185
Proportion linkage gain
0~100%
0
P.187
FM calibration parameter
0~9998
220
P.188
Firmware version
---
---
P.189
Factory setting function
0: The frequency parameter default value is 60Hz system.
60Hz
1: The frequency parameter default value is 50Hz system.
50Hz
P.190
AM output bias
0~8192
0
P.191
AM output gain
0~8192
600
P.192
2-5 terminal minimum input voltage
0~10
0
P.193
2-5 terminal maximum input voltage
0~10
0
P.194
Frequency corresponds to the minimum
input voltage of terminal 2-5
0~60Hz
0Hz
P.195
Frequency corresponds to the maximum
input voltage of terminal 2-5
0~650Hz
50Hz/60H
z(Note)
P.196
Frequency corresponds to the minimum
input current/voltage across terminal 4-5
0~60Hz
0Hz
P.197
Frequency corresponds to the maximum
input current /voltage across terminal 4-5
0~650Hz
50Hz/60H
z(Note)
P.198
Minimum input current/voltage across
terminal 4-5
0~20
0
P.199
Maximum input current/voltage across
terminal 4-5
0~20
0
P.219
Remote function acc/dec time selection
0:Use default acc/dec time(same as regular mode)
0
1:Use second acc/dec time
P.223
Analog feedback bias pressure
0~100%
0%
P.224
Analog feedback gain pressure
0~100%
100%
P.225
Panel command
0~P.251,9999
20%
P.226
The paver function selection
0:Reciprocating mechanical function is invalid
0
1:Reciprocating mechanical function effectively
P.227
The limit time of positive rotation
0~3600s
0
P.228
The limit time of reverse rotation
0~3600s
0
P.229
Backlash compensation and
acceleration/deceleration interrupted for
waiting function selection
0: None.
0
1: Backlash compensation function.
2: Acceleration and deceleration interrupt waiting function.
P.230
The acceleration interrupt frequency
0~650Hz
1Hz
P.231
The acceleration interrupt time
0~360s
0.5s
P.232
The deceleration interrupt frequency
0~650Hz
1Hz
P.233
The deceleration interrupt time
0~360 s
0.5s
P.234
Triangular wave function selection
0: None.
0
1: External TRI is turned on, triangular wave function will be
valid.
2: The triangular wave function is effective at any given
time.
P.235
Maximum amplitude
0~25%
10%
P.236
Amplitude compensation for deceleration
0~50%
10%
P.237
Amplitude compensation for acceleration
0~50%
10%
P.238
Amplitude acceleration time
0~360s/0~3600 s
10 s
P.239
Amplitude deceleration time
0~360s/0~3600 s
10s
P.240
Auxiliary frequency function selection
0:Auxiliary frequency function is not selected
0
1: operation frequency = basic frequency + auxiliary
frequency (2-5)
2: operation frequency = basic frequency + auxiliary
frequency (4-5)
3: operation frequency = basic frequency - auxiliary
frequency (2-5)
4: operation frequency = basic frequency - auxiliary
frequency (4-5)
5: 2-5 terminals given as a proportion linkage signal
6: 4-5 terminals given as a proportion linkage signal.

Parameter
number
Name
Setting range
Default
User
setting
P.242
DC injection brake function before starting
selection
0: DC injection brake function is not available
before starting.
0
1: DC brake injection function is selected before
starting.
P.243
DC injection brake time before starting
0~60s
0.5s
P.244
DC injection brake voltage before starting
0~30%
4%
P.245
Cooling fan operation selection
0:The fan will be turned on when running. The
fan will be turned off 30 seconds after inverter
stops.
1
1:Turning on the power will turn on the fan.
When the power is turned off, the fan will be off,
too.
P.245
Cooling fan operation selection
2:The fan will be turned on if the temperature of
the heat sink is higher than 40℃. When the
power is turned off, the fan will be turned off,
too.
1
3:The fan will be turned on when the
temperature of the heat sink is higher than 60℃.
When it is lower than 40℃, the fan will be turned
off.
P.247
MC switchover interlock time
0.1~100s
1s
P.248
Start waiting time
0.1~100s
0.5s
P.249
Automatic switchover frequency from inverter
to commercial power supply frequency
0~60Hz,9999
9999
P.250
Automatic switchover frequency range from
commercial power supply to inverter
0~10Hz,9999
9999
P.251
PID target value from keypad
1.0~100.0
100.0
P.253
Analog signal feedback loss detection time
0~600.0s
0.0s
P.254
Analog signal feedback loss action selection
0:Alarm AErr and inverter stop freely
0
1:Slow down to stop then alarm AErr
2:Alarm AErr and continue operation
P.255
S pattern time at the beginning of
acceleration
0~25s
0.2s
P.256
S pattern time at the end of acceleration
0~25s,9999
9999
P.257
S pattern time at the beginning of
deceleration
0~25s,9999
9999
P.258
S pattern time at the end of deceleration
0~25s,9999
9999
P.259
Speed unit selection
0: Speed display selection unit is 1
1
1: Speed display selection unit is 0.1
P.260
Over torque detection selection
0: The OL2 alarm is not reported after the over
torque detection, and the inverters continue to
running.
1
1: The OL2 alarm is reported after the over
torque detection, and the inverters stop.
P.261
Maintenance alarm time
0~9998day
0
P.268
Voltage stall level
220V :155~410V
380V
440V : 310~820V
760V
P.286
High frequency vibration inhibition factor
0~15
0
P.287
Short circuit protection function selection
0: No output short-circuit protection function
1
1: if the output end is short, the operation panel
will display the “SCP” abnormal alarm and the
inverter will stop the output.
P.288
Alarm code display option
0~12
0
P.289
Alarm code
---
0
P.290
The latest alarm status selection
0~6
0
P.291
The latest alarm message
---
0
P.292
Accumulative motor operation time (minutes)
0~1439min
0 min
P.293
Accumulative motor operation time (days)
0~9998day
0 day
P.294
Decryption parameter
0~9998
0
P.295
Password setup
2~9998
0
P.300
Motor control mode selection
0: Induction motor V/F control
0
1: Reserve
2: General flux vector control
P.301
Motor parameter auto-tuning function
selection
0: No motor parameter auto-tuning function
0
1: Motor parameter auto-tuning measuring the
running motor
2: Motor parameter auto-tuning measuring the
stopped motor
3: Online auto measurement function
P.302
Motor rated power
0~160
0
P.303
Motor poles
0~8
4
P.304
Motor rated voltage
0~440V
220/440V
P.305
Motor rated frequency
0~650Hz
50Hz/60Hz(Note)
P.306
Motor rated current
0~500A
Horsepower-base
d
P.307
Motor rated rotation speed
0~9998 r/min
1410/1710 r/min
(Note)
P.308
Motor excitation current
0~500A
Horsepower-base
d
P.309
Stator resistance
0~99.98Ω
Horsepower-base
d
P.320
Sliding compensation gain
0~200%
80%
P.321
Torque compensation filter coefficient
0~32
16
P.996
Alarm history clear
---
---
P.997
Inverter reset
---
---
P.998
Restoring all parameters to default values
---
---
P.999
Restoring some parameters to default
values
---
---
Note: The default value is determined by the set value of P.189. When P.189=0, the default value is 60Hz, which is applicable to 60Hz systems. When
P.189=1, the default value is 50Hz, which is applicable to 50Hz systems.
11) Parameter setting process
The flow chart for transferring operation modes with operation panel:
The flow chart for transferring working modes with operation panel:
Operation flow chart for the monitoring mode with operation panel:
Operating flow chart for the frequency setting mode with operation panel:
PU
MON
RUN
Hz
V
A
PU
MON
RUN
Hz
V
A
Read previous target
frequency Read new target
frequency
Operating flow chart for the parameter setting mode with operation panel:
Operating flow chart for the HELP mode with operation panel:
12) Others
To improve our products, the parameters and contents may be modified, please contact the agent or refer to Shihlin websites
(http://automation.seec.com.tw/en/index.html) to download the latest version.
V1.04February, 2021
PU
MON
RUN
Hz
V
A
PU
MON
RUN
Hz
V
A
PU
MON
RUN
Hz
V
A
P.79=0
PU
MON
RUN
Hz
V
A
PU
MON
RUN
Hz
V
A
P.79=1
PU
MON
RUN
Hz
V
A
PU
RUN
Hz
V
A
PU
MON
RUN
Hz
V
A
PU
MON
RUN
Hz
V
A
PU
MON
RUN
Hz
V
A
Power on
state
MON
PU
MON
RUN
Hz
V
MODE
MODE
MODE MODE
MODE
A
After 2 seconds
PU
MON
RUN
Hz
V
A
PU
MON
RUN
Hz
V
A
PU
MON
RUN
Hz
V
A
PU
MON
RUN
Hz
V
A
SET
SET
SET
SET
Aalarm record
Display output
frequency Display
output voltage
Display output
current
Over
0.5 s
PU
MON
RUN
Hz
V
A
PU
MON
RUN
Hz
V
A
PU
MON
RUN
Hz
V
A
PU
MON
RUN
Hz
V
A
PU
MON
RUN
Hz
V
A
PU
MON
RUN
Hz
V
A
PU
MON
RUN
Hz
V
A
PU
MON
RUN
Hz
V
A
PU
MON
RUN
Hz
V
A
PU
MON
RUN
Hz
V
A
PU
MON
RUN
Hz
V
A
SET
SET
SET
SET
SET
SET
SET
SET
SET
The first bit flashes The second bit flashes The third bit flashes
Read new set value
Set value written
and it flashes
Enter the next
setting mode Read previous set value
PU
MON
RUN
Hz
V
A
PU
MON
RUN
Hz
V
A
PU
MON
RUN
Hz
V
A
PU
MON
RUN
Hz
V
A
SET
SET SET
SET
This manual suits for next models
15
Popular DC Drive manuals by other brands
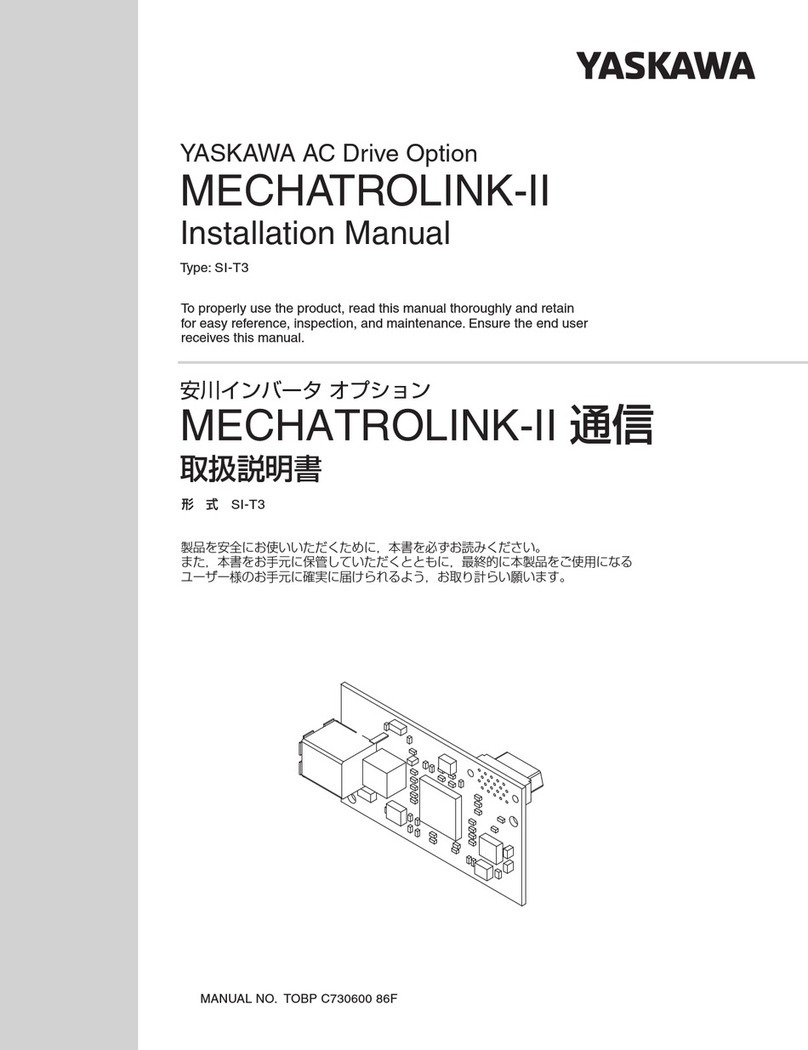
YASKAWA
YASKAWA MECHATROLINK-II installation manual

DEMAG
DEMAG Dedrive Pro 880 Series Quick installation guide

D+H
D+H FRA 11-BSY Plus Original instructions
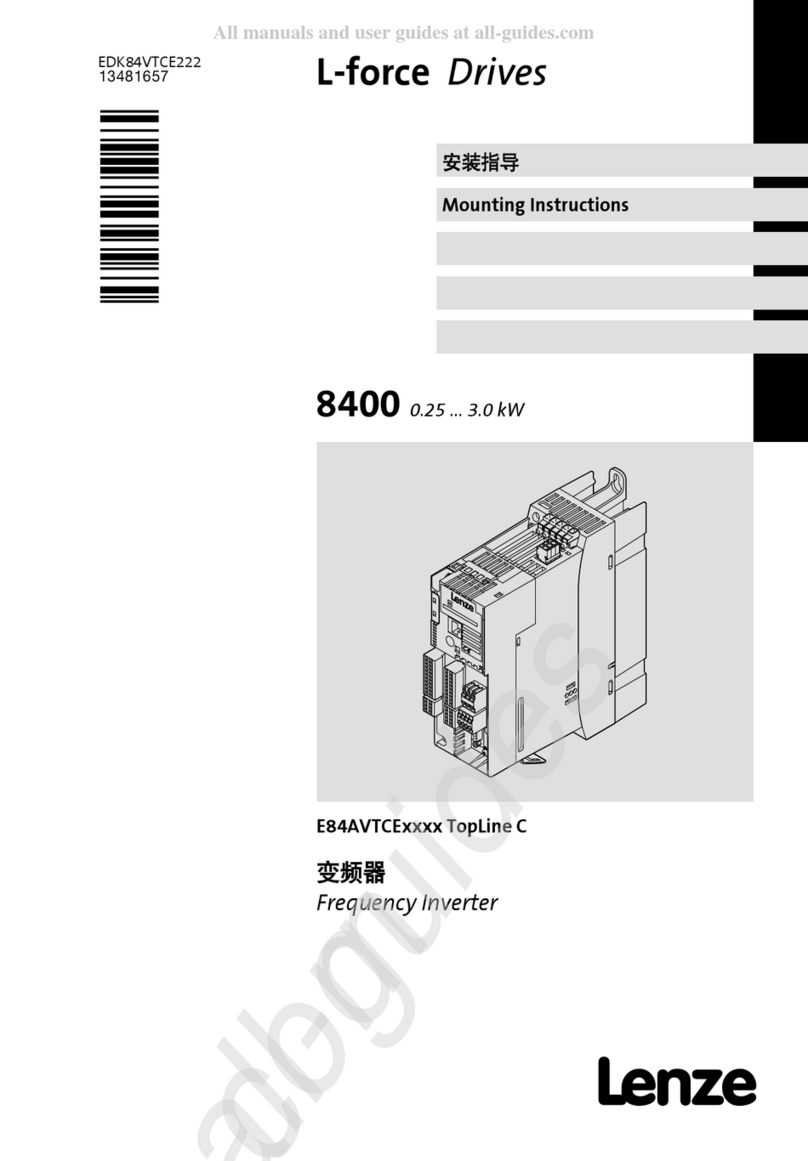
Lenze
Lenze L-force 8400 TopLine C Mounting instructions

IACDRIVE
IACDRIVE I5300 Series user manual
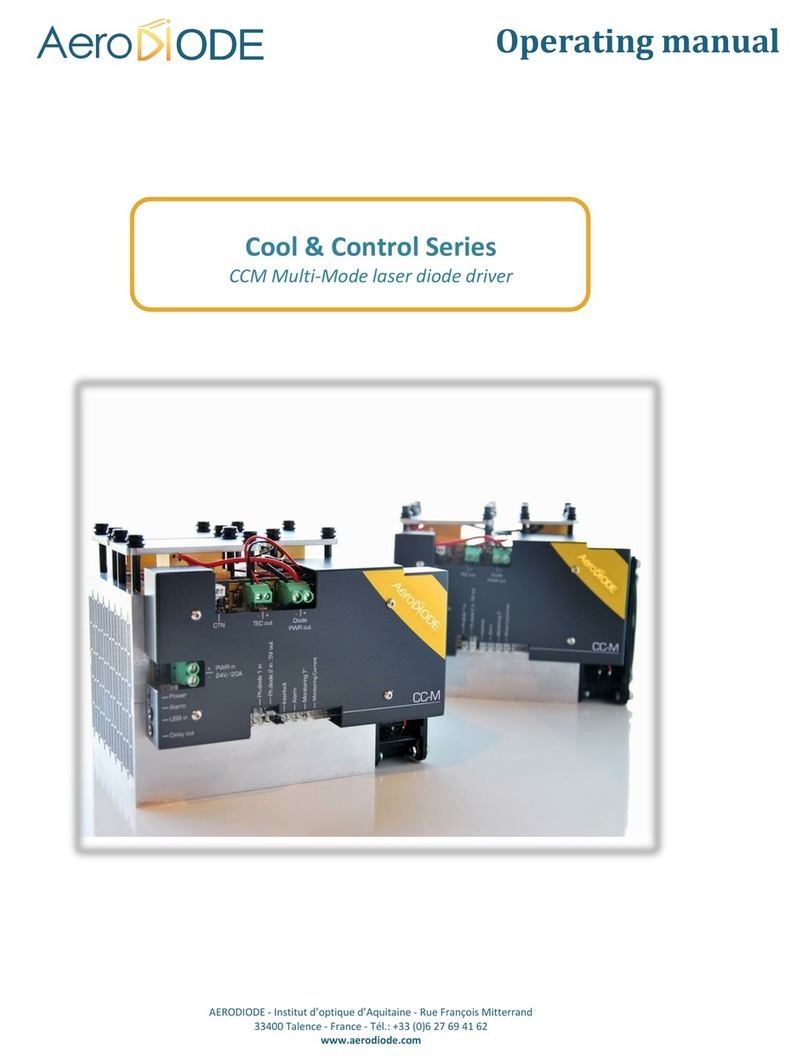
ALPhANOV
ALPhANOV AeroDIODE Cool & Control Series operating manual