Siebring FOX User manual


TABLE OF CONTENTS:
1. Cover
2. Table of Contents
3. Warranty / Shading Information
4. Features
5. Accessories
6. General Safety
7. Consumer Product Safety Commission Warning
8. Precautions / Back-flush Procedures
9. Operating Instructions / Cordage Chart
10. Operating Instructions (continued)
11. How it works
12. Tank & Components
13. Tank & Component Diagram
14. Unloader Description
15. Unloader Diagram –Spray Mode
16. Unloader Diagram –By-pass Mode
17. Pump / plumbing –By-pass mode
18. Pump / plumbing –Re-circulate mode
19. Flow Diagram –Pump / Plumbing
20. Flow Diagram –Typical system
21. Electrical Diagram –Low Voltage
22. Electrical Diagram –High Voltage
23. Troubleshooting Index
24. Troubleshooting (continued)
25. Troubleshooting (continued)
26. Troubleshooting (continued)
27. Troubleshooting (continued) / Winterizing
28. Parts List
29. Parts Diagrams
30. Parts Diagrams (continued)
31. Warning & Caution Labels
32. Warning & Caution Labels (continued)
2
Included: ELEY Hose Reel Instructions, CAT 2SF Data Sheet, CAT SF Service
Manual & Honda Manual (if applicable).

Shading:
Continental Products Company’s “Kool Ray” liquid shading products are the only brands
authorized for use in the Siebring “Mist R’ Drench,” “Fox” and “Kruser” line of sprayers.
DO NOT USE LATEX PAINT!
Use of unauthorized products can damage the sprayer pump and components and will
void the warranty.
Prior to applying shading, install a 0° tip and a 50 mesh screen (not included) in the filter
bowl assembly.
CONDITION OF SALE
SIEBRING MANUFACTURING, INC.
GEORGE, IA 51237
Pursuant to Magnuson-Moss Warranty Federal Trade Commission Improvement Act
P.L. 93-637, 88 STAT.2183-2193; U.P.C. 2301-2312 (Jan. 4, 1975), the following
limited warranty will now replace all prior warranties issued by Siebring
Manufacturing, Inc.
We warrant the equipment manufactured by us to be free from defects in material
and workmanship under normal use and service, our obligation under this warranty
being limited to replacing at our factory any product, or parts thereof, which shall
within one year after delivery thereof to the original purchaser be returned to us with
transportation (UPS Ground) charges prepaid, and which our examination shall
disclose to our satisfaction to have been thus defective. We neither assume nor
authorize any other person to assume for us any other liability in connection with
such equipment. “Overnight”, “Next Day” or any shipping method other than UPS
Ground will the responsibility of the customer. This warranty shall not apply to any
equipment which shall have been repaired or altered outside of our factory in any
way so as to affect its stability and reliability, nor which has been subject to misuse,
negligence or accident, nor to any equipment, which shall have been operated
beyond factory rated capacity. We shall not be liable for consequential damages
caused by defective materials, equipment or parts warranted by their respective
manufacturers.
Siebring MFG will not warranty any sprayer manufactured with brass components that has
been used to apply Zerotol or similar products. Sprayer warranties on units manufactured
with stainless steel pumps and associated components will be honored.
Any implied warranty (including the warranty of merchantability), to the extent
permitted by law, is excluded.
We will not grant any allowance for any repairs or alterations without written approval
of an executive officer, and we reserve the right to make changes in design, or to
make additions to, or improvements in, our products without imposing any
obligations upon the company to install them on products previously manufactured.
3

1. Bypass Valve
2. Liquid filled gauge
3. Oil filler cap
4. Oil sight glass
5. Brake to prevent unwanted spool run-off
6. Crank Handle
7. Reel Lock
8. Filter Bowl Assembly
9. Quick Disconnect
10. Bottom Tank Drain
11. IncludedAccessories (see next page)
- 2 Spray guns
-2 - 18” & 1 - 12” wand
-1 - 12” curved (hook) extension
- 3 piece misting tip & water breaker
- Back-flush fitting
- 0° & 15° pressure nozzles
3
2
1
6
5
4 10
9
11
FOX Features & Accessories
4
7
8

Fox, MD83, MD83BW, MD100, MD200 Included Accessories:
1. Small water breaker
2. 18” extension (2)
3. Gun (2)
4. Cap
5. 0° Tip
6. 15° Tip
7. 12” Hook
8. Backflush fitting
9. 12” Extension
10. Disk
11. Core
12. Brass Strainer
3
2
1 2
3
7
654
1110
4
8 12
9
5

GENERAL SAFETY
1. WARNING –Do not pump flammable or explosive fluids such as gasoline, fuel oil,
kerosene, etc. Do not use in explosive atmospheres. The pump should only be used
with liquids compatible with the pump component materials. Failure to follow this
warning can result in personal injury and/or property damage and will void the product
warranty.
2. Do not run the pump faster than maximum recommended speed.
3. Do not attempt to pump at pressures higher than rated, motor damage may result.
4. Maximum liquid temperature through pump is 140°.
5. Make certain that the power source conforms with the requirements of your equipment
(see cord chart on page 8).
6. Do not operate machine with belt guard, shaft guard or similar safety devices
removed.
7. Prior to servicing, disconnect power, stop engine.
8. Relieve system pressure prior to servicing.
9. Drain all liquids from system before servicing.
10. Secure quick couplers on lines and guns before starting the pump. A loose quick
coupler may cause a hose whip around under pressure causing personal injury and/or
property damage.
11. Check hoses for weak or worn conditions before each use. Make certain that all
connections are tight and secure.
12. Periodically inspect the pump and system components. Perform routine maintenance
as required. See maintenance section in this manual, CAT pump Service Manual and
Honda engine manual as applicable.
13. Electric motors must be adequately grounded.
14. Do not operate a gasoline engine in an enclosed area. Be sure the area is well
ventilated.
15. Gasoline is a highly combustible fuel. The improper use, storage or handling of
gasoline can be dangerous. Never fill or touch a hot engine.
16. Do not handle a pump or motor with wet hands or when standing on a wet or damp
surface.
17. Use only pipe, hose and fittings rated for the maximum P.S.I.G. rating of the pump. If
an unloader is used, use pipe, hose and fittings rated for the pressure at which the
unloader bypass operates.
6

The U.S. Consumer Product Safety Commission has issued a warning to
consumers who use electrically powered pressure washers for cleaning milk tanks,
spray tanks, and other farm equipment.
According to a federal safety alert, consumers can receive a fatal electrical shock
from pressure washers if the power cord connections become wet or an internal
short exists.
Since pressure washers are used to spray water, the power cord, washer and
consumer are often wet, and this can be fatal, especially if the machine is not
properly grounded, the report explained.
Consumers should not use adaptor plugs to connect the three-wire plug to a two-
prong household receptacle without properly grounding the adaptor plug. Power
cord connections should never be allowed to lie in water.
The commission urges these precautions:
- Always plug a three-wire grounded pressure washer into a properly grounded
receptacle. If possible, use a receptacle protected by a ground fault circuit
interrupter (GFCI).
- Check all flexible cords, plugs and sockets before each use. Replace any
damaged items.
- If an extension cord must be used, use the heavy-duty three-wire, properly
grounded type, and keep the power cord connection out of the water and away from
the item being washed.
- Wear eye protection when using sprayers or pressure washers.
- Wear rubber-soled footwear when operating the washer.
- Never cut or splice the power cord or extension cords.
- Do not leave hoses or cords where they can be run over and damaged.
- Never remove the grounding prong from the power cord plug.
- Never operate the washer after it has tripped a ground fault interrupter or circuit
breaker without first having it examined by a competent repair person.
- Never allow children to operate a pressure washer, and keep them away from the
washer when an adult is using it.
- Never spray the cleaner at yourself or others. The pressure can cause the water
and cleaner to blast under the skin.
- Never start the washer until you have checked to make sure all coupler hose
connections are in place and locked.
FOR MORE INFORMATION, CONSUMERS CAN CALL THE CPSC TOLL-FREE
HOTLINE, 800-638-CPSC.
WASHERS DANGEROUS, SAFETY PANEL WARNS
7

FOX PRECAUTIONS
ALWAYS - RINSE AND FLUSH OUT THE FOX AFTER EACH USE.
ALWAYS - DRAIN ANY REMAINING FLUIDS FROM THE SPRAYER TO
PROTECT IT FROM FREEZING.
ALWAYS - READ AND FOLLOW ALL DIRECTIONS OF THE CHEMICAL
MANUFACTURER (CHECK MSDS).
ALWAYS - PUT FRESH, CLEAN WATER IN THE FOX AND TEST THE
SPRAYER FOR PROPER OPERATION BEFORE ADDING ANY SPRAYS.
ALWAYS - WEAR PROTECTIVE GEAR WHEN MIXING OR APPLYING ANY
CHEMICALS. THIS INCLUDES MASK, RESPIRATOR, GLOVES,
GOWN, ETC.
ALWAYS - MAINTAIN THE FOX IN GOOD REPAIR. THIS WILL HELP
PREVENT LEAKS, ETC. AND ADD TO THE LIFE OF THE MACHINE.
8
BACKFLUSH PUMP FITTINGS FOR FOX SPRAYER
PARTS INCLUDED:
1 –50MP QUICK COUPLER
1 –GARDEN HOSE SCREEN
1 –¾ X ½ SWIVELADP. (S11) GARDEN HOSE FITTING
HOW TO USE
**TANK MUST BE EMPTY**
1. DISCONNECT BLACK RUBBER SUCTION HOSE FROM TANK AT QUICK
COUPLER
2. SNAP SUPPLIED FITTINGS INTO HOSE QUICK COUPLER
3. ATTACH GARDEN HOSE TO FITTING
4. TURN ON WATER SUPPLY
5. RUN PUMP/SPRAY TO FLUSH PUMP
*** WINTERIZE PUMP IF FREEZING TEMPERATURES ARE EXPECTED ***

FOX SPRAYER OPERATING INSTRUCTIONS
PRIOR TO START UP
Completely uncrate unit. Inspect for shipping damages that could interfere with unit
operation. Check for crating/shipping materials lodged in pump/motor assembly, belt
drive (if applicable) steering mechanism and wheel & tire area. Check for foreign debris
in sprayer tank.
Read this manual and comply with all of the safety instructions. Familiarize yourself with
the operating instructions and component location prior to using the unit.
If you have a gas engine powered unit, read and familiarize yourself with the Honda
Owner’s Manual.
Read and be familiar with the CAT Pump manual and operating instructions.
If electrically powered unit, ensure adequate power and extension cords are available to
operate the unit (see chart below).
MOTOR
HP 100 FT. 200 FT. 300 FT. 500 FT.
115V 230V 115V 230V 115V 230V 115V 230V
1/4 # 14 # 14 # 10 # 12 # 8 # 10 # 6 # 8
1/3 # 12 # 14 # 10 # 12 # 6 # 10 # 4 # 8
1/2 # 10 # 12 # 8 # 10 # 6 # 8 # 4 # 6
3/4 # 10 # 12 # 6 # 10 # 4 # 8 # 2 # 6
1 # 8 # 10 # 6 # 8 # 4 # 6 # 4
1 ½ # 4 # 10 # 0 # 8 # 6 # 4
2 # 8 # 6 # 4 # 2
3 # 8 # 6 # 4 # 2
5 # 6 # 4 # 2 # 0
Wire Size for 115 & 230 Volt Single Phase Circuits
Distance –Motor to Fuse or Motor to Meter Box
9

Check “Quick Couplers” for secure connection: Hose reel to unloader, Return line to tank
& Supply (suction) line on the bottom of the tank.
Open valves: Bypass valve (unloader) & Supply (suction) valve below tank.
Depress spray gun trigger during start-up to allow for “Load Free” run-up.
Check sight glass on filter bowl during start-up. Air bubbles during operation may indicate
a cracked filter bowl or missing o-ring or gasket.
START UP
1. Put 10 gallons of water into the sprayer tank. DO NOT ADD SPRAY YET!!!
TESTS
2. Test the sprayer. It should have up to 800 PSI when spraying with the misting wand.
The bypass valve must be shut for this test.
TANK AGITATION
3. The water in the tank should be agitating whenever the pump is on (but not spraying)
or when the ball valve is open.
LEAK INSPECTION
4. Check for any leaks. Find the source of any and all dripping water. Be sure to
confirm that the filter is clean and that the filter bowl is tightly screwed on.
ADD SPRAY
5. Additional water and spray may now be added to the tank. Any products that are
heavy solids may be added to the tank slowly. Additional water should be added to
the tank to keep the powder well diluted. Some sprays may also be harmful to the
pump seals if used at full strength. Check CAT pump manual for compatibility.
CLEAN UP
6. Cleaning herbicide from the Sprayer: Use one quart of household ammonia per 60
gallons of water (1:240 ratio). Stir well!! Start the pump and run the unit until the
ammonia fills the MD83 hose and wand. Allow to stand for 24 hours.
RINSING
7. Flush with fresh water. Triple rinse with clear water. Winterize for cold weather.
10

11
How it Works
First, when you start the GAS-POWERED ENGINE, or ELECTRIC MOTOR, of
your sprayers, the motor drives a crankshaft inside the water pump that starts
the pistons or plungers.
Fresh water, coming in from your fluid supply tank, through the intake hose,
picking up fluid near the bottom of the sprayer tank to the inlet side of the
pump manifold.
The CAT pump produces flow and sends it to the unloader. Pressure is
created by restricting the flow at the nozzle. At a given flow, the smaller the
restriction nozzle the higher the pressure; the larger the restriction nozzle the
lower the pressure.
The unloader acts like a traffic cop, sending the preset amount of flow
through the hose and towards the spray gun and nozzle, and sending the by-
pass fluid back to the pump manifold or through the recirculation hose and
back into the tank (depending on the ball valve position). See page 14 - 16
to learn about the unloader.
Water is pushed through the high pressure hose, through the spray gun that's
controlled by a trigger. The trigger on the spray gun is actually a valve that
controls the flow through the wand. Squeezing the trigger opens the valve,
releasing the trigger closes the valve. The spray gun has a trigger lock
feature that will lock the trigger closed for safety to prevent accidental
activation of the spray gun.
The pump produces flow. The pressure is created by restricting the flow
through the use of an appropriate sized nozzle or tip.
The sizes and flow rate calculations of the nozzles and tips provided with the
Fox sprayer line have been predetermined at the factory. Altering the size and
flow rates of the nozzles and tips can hinder sprayer performance. Wear in a
nozzle or tip can cause pressure drop.
Note: Spray angle does not affect nozzle flow rate.
For twenty-five years, Siebring Manufacturing has been listening to and
incorporating customer suggestions and criticisms to develop a dependable
and user friendly product. The paragraphs below briefly describe the
Siebring “FOX” line of sprayers and how they operate.

35 GALLON TANK COMPONENTS & DESCRIPTIONS
1. Tank Lid –(spin-on lid) vented, allows access to the tank for filling & mixing
and allows air to displace fluid being pumped out.
2. 35 gallon horizontal tank - 29” overall length, 19” in wide & 18.5” high.
Gallon markers on side. Tapered bottom sump for complete fluid pick-up,
draining and cleaning.
3. Buckle & Straps –Secures tank to sprayer frame.
4. Suction FittingAssembly –Connected to the pump suction line and located
just off the bottom of the sump in the tank. The fitting is raised off the bottom
slightly and has two ¼” holes in the end to prevent unmixed chemical
powder and to filter out large chunks of unmixed chemicals, shading or
debris in the water such as chemical packaging materials.
5. Suction Hose –¾” non-reinforced hose. Supplies water/chemical to pump.
6. Filter assembly –Mounted in the supply line to remove dirt & sediment
before the fluid enters the pump. The 4 main components are the housing
assembly, bowl, gasket and screen.
7. Filter Bowl & gasket.
8. Mesh Filter screen –3 screen sizes are available for various applications;
30, 50 & 80. Siebring Fox sprayers are delivered with # 80 screens unless
otherwise specified.
9. Plastic Street Elbow –connects suction fitting assembly with the suction
hose and the by-pass assembly with the bypass hose.
10. Drain valve –Located in the lowest part of the tank for tank draining. Male
threads are ½” NPT.
11. By-pass hose –Approximately 10% fluid by-pass from the unloader returns
to the tank to agitate fluids and for suspending wettable powders.
12. Back-flushAssembly –Installed in the suction line, the assembly has an
adapter to connect a standard garden hose in line to the pump. The fitting
can be used for flushing, cleaning and winterizing.
12
(See page 13 for tank & component diagram)

FOX 35 GALLON TANK & COMPONENTS
13
5
10
15
20
25
30
6
12
1. Tank Lid
2. Tank
3. Buckle & Strap
4. Suction Fitting Assembly
5. Suction (supply) hose
6. Filter Assembly
Top, cutaway view
9
10
4
4
2
3
1
1
1
2
2
3
10
7. Filter Bowl
8. Mesh Filter screen
9. Plastic Street Elbow –½”
10. Drain Valve
11. By-pass (return) hose
12. Back-flushAssembly
Top view
Side view
5
5
6
6
5
7, 8
9
65
11

This type of unloader may be referred to as a “Trapped Pressure” type or just
"Pressure" type. This type of valve opens to bypass when it senses the pressure
build up of the pump output having nowhere to go. The main characteristic of this
most commonly used valve is how it traps the pressure in the hose when the
trigger of the pressure gun is released and unloading excess pressure between
the pump & unloader.
The disadvantage of this type of valve is the spike of pressure felt by the
operator and sprayer/pressure washer components when the trigger is again
squeezed. This creates a "kickback" effect on the gun/wand so be careful when
using ladders or other types of access equipment. The “kickback” effect is most
noticeable when working with pressures above 1000 PSI. The “Fox” sprayer line
is factory set at 800 PSI for customer comfort and safety.
Pressure Sensitive Regulating Unloader
When your system uses a trigger gun that stops the water flow from the pressure
pump the unloader valve must be employed. Understand that when the trigger of
the gun is released the water flow to the nozzle is interrupted. The power source
and the pressure pump are still running, without some pressure system safety
device the water would have nowhere to go, building pressure until pump
damage occurs.
Enter the Unloader Valve. The most basic function of the unloader is to act as a
"traffic cop" to the water flow in your system as soon as it senses "pressure
build". When the “Pressure Build” condition is met the unloader will then actuate
the piston assembly to divert the water flow toward the bypass port. When this
is occurring the pump is said to be in "bypass mode" and the unloader valve is
said to be "cycling". This scenario ends when the trigger is squeezed alerting
the unloader valve to redirect the flow to the gun and high pressure nozzle once
again.
14
The Siebring sprayers have a ball-valve installed down stream from the pump
and just before the unloader. In the open position, the majority of the by-pass
fluid is directed back to the pump. In the closed position, the majority of the by-
pass fluid is directed to the tank, the remainder circulates through the manifold.
This design constantly supplies cool fluid to the pump & manifold, eliminating
concerns regarding manifold temperatures.

Pressure Sensitive Regulating Unloader
15
Spray Mode
Bypass
To
Gun
Gun trigger is depressed with gun in
use. Pump flow enters from the left
of the diagram (inlet port), passes
through the unloader, out of the
outlet port, to the gun.
CAUTION: A minimum bypass of 5 -
10% of the UNLOADER RATED
FLOW CAPACITY is required for
proper unloader performance.
Additional bypass fluid
may be the excess
pressure - the difference
between the pump output
and the unloader setting.
Inlet Port Outlet Port
Bypass Port
Check
Valve
Piston Assembly
Pump
Flow
5 - 10 %
Min.

Pressure Sensitive Regulating Unloader
Bypass Mode
Bypass
To
Gun
Gun trigger valve is closed, gun is
not in use. Pump flow enters from
the left of the diagram (inlet port),
dead ends against output check
valve, overcomes the spring
pressure holding the piston
assembly and is forced down
through the bypass port.
CAUTION: A minimum bypass of 5 -
10% of the UNLOADER RATED
FLOW CAPACITY is required for
proper unloader performance.
Inlet Port Outlet Port
Bypass Port
Piston Assembly
WARNING: DO NOT
OPERATE THE PUMP
IN BYPASS MODE
LONGER THAN 2
MINUTES.
Pump
Flow
Check
Valve
16

Direct Drive Pump & Associated Plumbing
To pump intake
from supply tank
To Spray Gun By-pass mode –Ball valve
open, by-pass fluid returns
to pump manifold and
supply tank at low pressure
17
Pump
Intake
Port
Some recirculation back
to Tank (low pressure).
Filter bowl o-ring in place,
no cracks in sight glass

To Spray Gun
Direct Drive Pump & Associated Plumbing
Recirculate mode –Ball
valve closed, by-pass fluid
flows to tank.
18
Pump
Intake
Port
Full Re-circulation
back to tank under
increased pressure
Filter bowl o-ring in place,
no cracks in sight glass
To pump intake
from supply tank

Recirculate mode –Ball valve
closed, unloader by-pass fluid
flows to tank. Select this mode to
mix chemicals, keep wettable
powders suspended or to check
pump operating pressure.
By-pass mode –Ball valve open,
Unloader by-pass fluid returns to
pump manifold. Pressure gauge
drops to near zero (0 –25 PSI).
Supply
Pressure
By-pass
Typical Flow Diagram –Siebring “Fox” Sprayer
Minimum amount of
by-pass back to tank.
19
This manual suits for next models
1
Table of contents
Other Siebring Paint Sprayer manuals
Popular Paint Sprayer manuals by other brands

Graco
Graco UNICARB Pro AA4500 Instructions-parts list
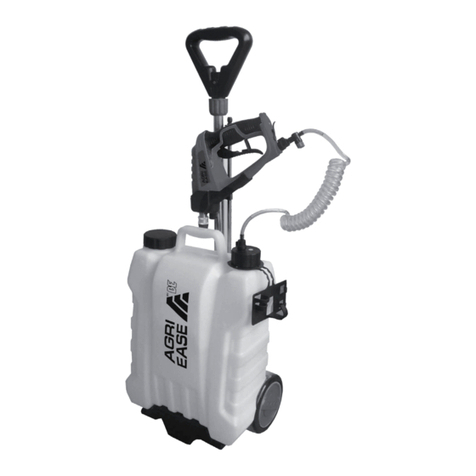
BE
BE Agri Ease GS7.2R Operation manual
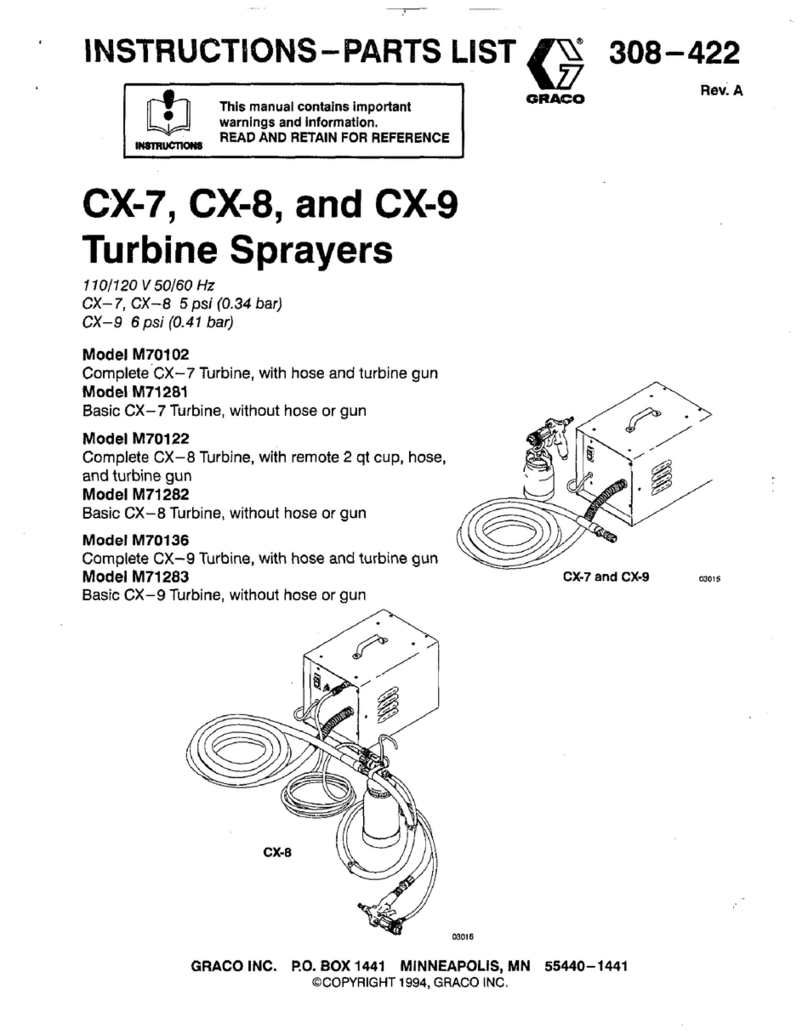
Graco
Graco CX-7 instruction manual

Boyens Backservice
Boyens Backservice Spruhboy 14 Airmix instruction manual
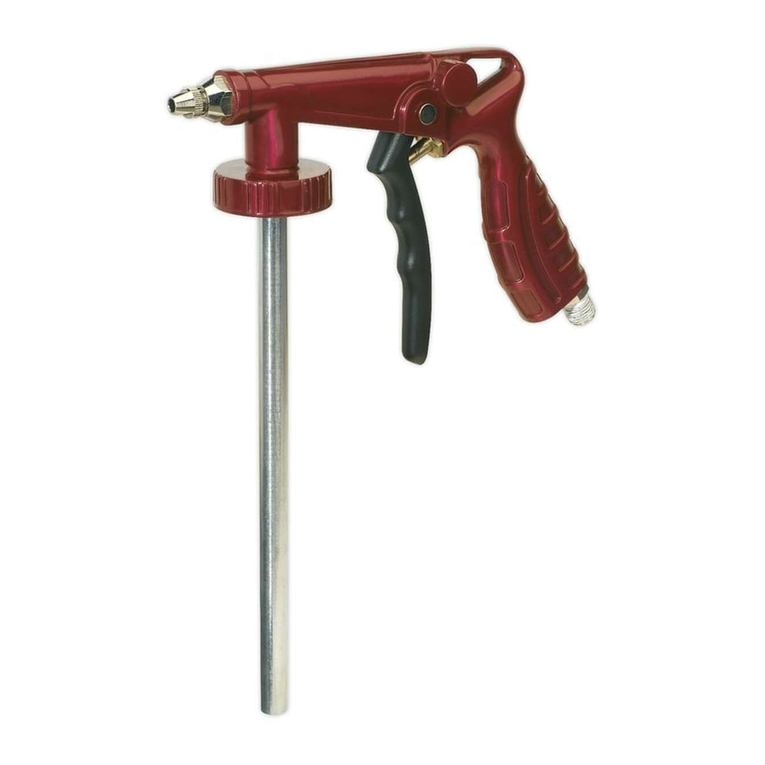
Sealey
Sealey POWER PRODUCTS SG14.V3 instructions

Lafferty
Lafferty 925025 Installation & operation instructions