SIGNALCORE SC5406B Owner's manual

SC5406B Operating & Programming Manual Rev 1.1 ii
CO N T E N T S
Important Information 1
Warranty 1
Copyright & Trademarks 2
International Materials Declarations 2
CE European Union EMC & Safety Compliance Declaration 2
Recycling Information 3
Warnings Regarding Use of SignalCore Products 3
Getting Started 4
Unpacking 4
Verifying the Contents of your Shipment 4
Setting Up and Configuring the SC5406B 4
Signal Connections 5
Communication and Supply Connection 6
Mini-USB Connection 7
Reset Button (Pin Hole) 7
Indicator LEDs 7
SC5406B - Theory of Operation 8
Overview 8
Signal Path Description 9
Local Oscillator Description 11
Frequency Tuning Modes 13
Setting the SC5406B to Achieve Best Dynamic Range 13
Operating the SC5406B Outside Normal Range 14
SC5406B Programming Interface 15
Device Drivers 15
The SC5406B USB Configuration 15
Writing the Device Registers Directly 16
Reading the Device Registers Directly 16
Using the Application Programming Interface (API) 16

SC5406B Operating & Programming Manual Rev 1.1 iii
Setting the SC5406B - Writing USB Configuration Registers Directly 17
Configuration Registers 17
Tuning the RF Frequency 17
Changing the Attenuator Settings 18
Enabling and Disabling the Internal Tone Generator 18
Changing the RF Synthesizer Mode 18
Selecting the IF Filter Path 18
Enabling the Internal IF Signal Generator. 19
Setting the Reference Clock Behavior 19
Adjusting the Reference Clock Accuracy 19
Setting Spectral Inversion in the RF 19
Storing Data into the User EEPROM Space 19
Setting the Phase of the RF Signal 19
Querying the SC5406B - Writing USB Request Registers Directly 20
Reading Device Status Data 20
Reading Temperature Data 21
Reading Calibration EEPROM Data 22
Reading User EEPROM Data 22
Working With Calibration Data 23
EEPROM Data Content 24
Frequency Correction 26
Gain Correction 26
IF Response Correction 28
Software API Library Functions 30
Constants Definitions 31
Type Definitions 32
Programming the USB interface 34
Programming the RS232 interface 49
Function Definitions and Usage of the RS232 API 49
Addressing the RS232 Registers Directly 49

SC5406B Operating & Programming Manual Rev 1.1 iv
Writing to the device via RS232 50
Reading from the device via RS232 50
Programming the SC5406B Serial Peripheral Interface 51
The SPI Communication Connector 51
The SC5406B SPI Architecture 51
SPI Clock Rates and Modes 52
Writing Configuration Data via the SPI Bus 54
Reading Requested Data via the SPI Bus 55
Calibration & Maintenance 57
Revision Notes 58

SC5406B Operating & Programming Manual Rev 1.2 1
IM P O R T A N T IN F O R M A T I O N
Warranty
This product is warranted against defects in materials and workmanship for a period of three years from
the date of shipment. SignalCore will, at its option, repair or replace equipment that proves to be
defective during the warranty period. This warranty includes parts and labor.
Before any equipment will be accepted for warranty repair or replacement, a Return Material
Authorization (RMA) number must be obtained from a SignalCore customer service representative and
clearly marked on the outside of the return package. SignalCore will pay all shipping costs relating to
warranty repair or replacement.
SignalCore strives to make the information in this document as accurate as possible. The document has
been carefully reviewed for technical and typographic accuracy. In the event that technical or
typographical errors exist, SignalCore reserves the right to make changes to subsequent editions of this
document without prior notice to possessors of this edition. Please contact SignalCore if errors are
suspected. In no event shall SignalCore be liable for any damages arising out of or related to this
document or the information contained in it.
EXCEPT AS SPECIFIED HEREIN, SIGNALCORE, INCORPORATED MAKES NO WARRANTIES, EXPRESS OR
IMPLIED, AND SPECIFICALLY DISCLAIMS ANY WARRANTY OF MERCHANTABILITY OR FITNESS FOR A
PARTICULAR PURPOSE. CUSTOMER’S RIGHT TO RECOVER DAMAGES CAUSED BY FAULT OR
NEGLIGENCE ON THE PART OF SIGNALCORE, INCORPORATED SHALL BE LIMITED TO THE AMOUNT
THERETOFORE PAID BY THE CUSTOMER. SIGNALCORE, INCORPORATED WILL NOT BE LIABLE FOR
DAMAGES RESULTING FROM LOSS OF DATA, PROFITS, USE OF PRODUCTS, OR INCIDENTAL OR
CONSEQUENTIAL DAMAGES, EVEN IF ADVISED OF THE POSSIBILITY THEREOF. This limitation of the
liability of SignalCore, Incorporated will apply regardless of the form of action, whether in contract or
tort, including negligence. Any action against SignalCore, Incorporated must be brought within one year
after the cause of action accrues. SignalCore, Incorporated shall not be liable for any delay in
performance due to causes beyond its reasonable control. The warranty provided herein does not cover
damages, defects, malfunctions, or service failures caused by owner’s failure to follow SignalCore,
Incorporated’s installation, operation, or maintenance instructions; owner’s modification of the product;
owner’s abuse, misuse, or negligent acts; and power failure or surges, fire, flood, accident, actions of
third parties, or other events outside reasonable control.

SC5406B Operating & Programming Manual Rev 1.2 2
Copyright & Trademarks
Under the copyright laws, this publication may not be reproduced or transmitted in any form, electronic
or mechanical, including photocopying, recording, storing in an information retrieval system, or
translating, in whole or in part, without the prior written consent of SignalCore, Incorporated.
SignalCore, Incorporated respects the intellectual property rights of others, and we ask those who use
our products to do the same. Our products are protected by copyright and other intellectual property
laws. Use of SignalCore products is restricted to applications that do not infringe on the intellectual
property rights of others.
“SignalCore”, “signalcore.com”, and the phrase “preserving signal integrity” are registered trademarks
of SignalCore, Incorporated. Other product and company names mentioned herein are trademarks or
trade names of their respective companies.
International Materials Declarations
SignalCore, Incorporated uses a fully RoHS compliant manufacturing process for our products.
Therefore, SignalCore hereby declares that its products do not contain restricted materials as defined by
European Union directive 2002/95/EC (EU RoHS) in any amounts higher than limits stated in the
directive. This statement is based on the assumption of reliable information and data provided by our
component suppliers and may not have been independently verified through other means. For products
sold into China, we also comply with the “Administrative Measure on the Control of Pollution Caused by
Electronic Information Products” (China RoHS). In the current stage of this legislation, the content of six
hazardous materials must be explicitly declared. Each of those materials, and the categorical amount
present in our products, are shown below:
組成名稱
Model Name
鉛
Lead
(Pb)
汞
Mercury
(Hg)
镉
Cadmium
(Cd)
六价铬
Hexavalent
Chromium
(Cr(VI))
多溴联苯
Polybrominated
biphenyls
(PBB)
多溴二苯醚
Polybrominated
diphenyl ethers
(PBDE)
SC5406B
USB/RS-232/SPI
✓
✓
✓
✓
✓
✓
A ✓indicates that the hazardous substance contained in all of the homogeneous materials for this
product is below the limit requirement in SJ/T11363-2006. An Xindicates that the particular hazardous
substance contained in at least one of the homogeneous materials used for this product is above the
limit requirement in SJ/T11363-2006.
CE European Union EMC & Safety Compliance Declaration
The European Conformity (CE) marking is affixed to products with input of 50 - 1,000 VAC or 75 - 1,500
VDC and/or for products which may cause or be affected by electromagnetic disturbance. The CE
marking symbolizes conformity of the product with the applicable requirements. CE compliance is a
manufacturer’s self-declaration allowing products to circulate freely within the European Union (EU).
SignalCore products meet the essential requirements of Directives 2004/108/EC (EMC) and 2006/95/EC

SC5406B Operating & Programming Manual Rev 1.2 3
(product safety), and comply with the relevant standards. Standards for Measurement, Control and
Laboratory Equipment include EN 61326 and EN 55011 for EMC, and EN 61010-1 for product safety.
Recycling Information
All products sold by SignalCore eventually reach the end of their useful life. SignalCore complies with EU
directive 2002/96/EC regarding Waste Electrical and Electronic Equipment (WEEE).
Warnings Regarding Use of SignalCore Products
(1)
PRODUCTS FOR SALE BY SIGNALCORE, INCORPORATED ARE NOT DESIGNED WITH COMPONENTS NOR TESTED FOR A LEVEL OF
RELIABILITY SUITABLE FOR USE IN OR IN CONNECTION WITH SURGICAL IMPLANTS OR AS CRITICAL COMPONENTS IN ANY LIFE SUPPORT
SYSTEMS WHOSE FAILURE TO PERFORM CAN REASONABLY BE EXPECTED TO CAUSE SIGNIFICANT INJURY TO A HUMAN.
(2)
IN ANY APPLICATION, INCLUDING THE ABOVE, RELIABILITY OF OPERATION OF THE SOFTWARE PRODUCTS CAN BE IMPAIRED BY ADVERSE
FACTORS, INCLUDING BUT NOT LIMITED TO FLUCTUATIONS IN ELECTRICAL POWER SUPPLY, COMPUTER HARDWARE MALFUNCTIONS,
COMPUTER OPERATING SYSTEM SOFTWARE FITNESS, FITNESS OF COMPILERS AND DEVELOPMENT SOFTWARE USED TO DEVELOP AN
APPLICATION, INSTALLATION ERRORS, SOFTWARE AND HARDWARE COMPATIBILITY PROBLEMS, MALFUNCTIONS OR FAILURES OF
ELECTRONIC MONITORING OR CONTROL DEVICES, TRANSIENT FAILURES OF ELECTRONIC SYSTEMS (HARDWARE AND/OR SOFTWARE),
UNANTICIPATED USES OR MISUSES, OR ERRORS ON THE PART OF THE USER OR APPLICATIONS DESIGNER (ADVERSE FACTORS SUCH AS
THESE ARE HEREAFTER COLLECTIVELY TERMED “SYSTEM FAILURES”). ANY APPLICATION WHERE A SYSTEM FAILURE WOULD CREATE A
RISK OF HARM TO PROPERTY OR PERSONS (INCLUDING THE RISK OF BODILY INJURY AND DEATH) SHOULD NOT BE SOLELY RELIANT
UPON ANY ONE COMPONENT DUE TO THE RISK OF SYSTEM FAILURE. TO AVOID DAMAGE, INJURY, OR DEATH, THE USER OR
APPLICATION DESIGNER MUST TAKE REASONABLY PRUDENT STEPS TO PROTECT AGAINST SYSTEM FAILURES, INCLUDING BUT NOT
LIMITED TO BACK-UP OR SHUT DOWN MECHANISMS. BECAUSE EACH END-USER SYSTEM IS CUSTOMIZED AND DIFFERS FROM
SIGNALCORE' TESTING PLATFORMS, AND BECAUSE A USER OR APPLICATION DESIGNER MAY USE SIGNALCORE PRODUCTS IN
COMBINATION WITH OTHER PRODUCTS IN A MANNER NOT EVALUATED OR CONTEMPLATED BY SIGNALCORE, THE USER OR
APPLICATION DESIGNER IS ULTIMATELY RESPONSIBLE FOR VERIFYING AND VALIDATING THE SUITABILITY OF SIGNALCORE PRODUCTS
WHENEVER SIGNALCORE PRODUCTS ARE INCORPORATED IN A SYSTEM OR APPLICATION, INCLUDING, WITHOUT LIMITATION, THE
APPROPRIATE DESIGN, PROCESS AND SAFETY LEVEL OF SUCH SYSTEM OR APPLICATION.

SC5406B Operating & Programming Manual Rev 1.2 4
•Ground yourself using a grounding strap or by touching a grounded metal object.
•Touch the antistatic bag to a grounded metal object before removing the hardware
from its packaging.
•Never touch exposed signal pins. Due to the inherent performance degradation
caused by ESD protection circuits in the RF path, the device has minimal ESD
protection against direct injection of ESD into the RF signal pins.
•When not in use, store all SignalCore products in their original antistatic bags.
GE T T I N G ST A R T E D
Unpacking
All SignalCore products ship in antistatic packaging (bags) to prevent damage from electrostatic
discharge (ESD). Under certain conditions, an ESD event can instantly and permanently damage several
of the components found in SignalCore products. Therefore, to avoid damage when handling any
SignalCore hardware, you must take the following precautions:
Remove the product from its packaging and inspect it for loose components or any signs of damage.
Notify SignalCore immediately if the product appears damaged in any way.
Verifying the Contents of your Shipment
Verify that your SC5406B kit contains the following items:
Quantity
Item
1
SC5406B USB RF Upconverter
1
USB flash drive with installation software
Setting Up and Configuring the SC5406B
Figure 1 Front view of the SC5406B connectors.
The SC5406B is a core module-based RF upconverter with all user I/O located on the front face of the
module as shown in Figure 1. Each location is discussed in further detail below.
!

SC5406B Operating & Programming Manual Rev 1.2 5
Signal Connections
All signal connections (ports) to the SC5406B are SMA-type. Exercise caution when fastening cables to
the SMA connections. Over-tightening any connection can cause permanent damage to the device.
The condition of your system‘s signal connections can significantly affect measurement
accuracy and repeatability. Improperly mated connections or dirty, damaged or worn
connectors can degrade measurement performance. Clean out any loose, dry debris from
connectors with clean, low-pressure air (available in spray cans from office supply stores).
If deeper cleaning is necessary, use lint-free swabs and isopropyl alcohol to gently clean
inside the connector barrel and the external threads. Do not mate connectors until the
alcohol has completely evaporated. Excess liquid alcohol trapped inside the connector may
take several days to fully evaporate and may degrade measurement performance until fully
evaporated.
Tighten all SMA connections to 8.8 in-lb max (100 N-cm max)
RF OUT This port outputs 1 MHz to 3.9 GHz signals from the upconverter. The nominal output
impedance is 50 Ω.
IF IN This port outputs the 70 MHz IF signal from the downconverter. The nominal input
impedance is 50 Ω. Maximum input power is +23 dBm
REF IN This port accepts an external 10 MHz reference signal, allowing an external source to
synchronize the internal reference clock. This port is AC-coupled with a nominal input
impedance of 50 Ω. Maximum input power is +13 dBm.
REF OUT This port outputs the internal 10 MHz or 100 MHz reference clock. If the internal reference
clock is synchronized to an external reference clock through the 10 MHz “ref in”port, this
output port will also be synchronized. This port is AC-coupled with a nominal output
impedance of 50 Ω.
!
!

SC5406B Operating & Programming Manual Rev 1.2 6
Communication and Supply Connection
Power and communication to the device is provided through a Molex Milli-GridM2.00mm, 30 position,
male header connector, whose part number is 87833-3020. A suggested receptacle female connector is
the crimp terminal type 51110-3051 or ribbon type 87568-3093 from Molex. The pin definitions of this
I/O connector are listed Table 1 below.
Table 1 Communication IO connector pin definitions
PIN #
Description
PIN #
Description
1,3
12V Supply rail
21
Device Active
2,4,10,16,
20,24,28
GND
22
Device Status
5,6,7,8,9,
15,18,21
Reserved, do not connect
23
Baudrate/Spi Mode
11
USB+
25
CTS/. This pin is CTS for RS232 or device
select for SPI
13
USB-
26
SPI Clock
14
USB_VBUS
27
TX/MISO. This pin is TX for RS232 or MISO
for SPI
17
Reserved, pull high to 3.3V or
DNC
29
RX/MOSI. This pin is RX for RS232 or MOSI
for SPI
19
, logic 0 to reset device
30
RTS/SRDY. This pin is RTS for RS232 or
serial ready for SPI

SC5406B Operating & Programming Manual Rev 1.2 7
Mini-USB Connection
The SC5406B uses a mini-USB Type B connector for USB communication with the device using the
standard USB 2.0 protocol (full speed) found on most host computers. The pinout of this connector,
viewed from the board edge, is shown in the table above.
Reset Button (Pin Hole)
Behind this pin hole is the reset button. Using a pin and lightly depressing this momentary-action push
button switch will cause a hard reset to the device, putting it back to its default settings. All user settings
will be lost. System reset capability can also be accessed through the communication header connector.
Indicator LEDs
The SC5406B provides visual indication of important modes. There are two redundant pairs of LED
indicators on the device, two to the left of the micro-D connector and two on the opposite side of the
module. The LED closest to the micro-D connector indicates STATUS. The LED to the left of the STATUS
LED indicates ACTIVE. The pair of LEDs on the opposite side of the module are oriented the same way.
Their behavior under different operating conditions is shown in the table below.
Pin
USB
Function
Description
1
VBUS
Vcc (+5 Volts)
2
D -
Serial data
3
D +
Serial data
4
ID
Not used
5
GND
Device ground (also tied to
connector shell)
LED
Color
Definition
STATUS
Green
“Power good” and all oscillators phase-locked
STATUS
Red
One or more oscillators off lock
STATUS
Off
Power fault
ACTIVE
Green/Off
Device is open (green) / closed (off)
This indicator is also user programmable (see register map)
ACTIVE
Orange
User initiated standby mode

SC5406B Operating & Programming Manual Rev 1.2 8
SC5 4 0 6 B -TH E O R Y O F OP E R A T I O N
Overview
The SC5406B operates on the principle of heterodyning, a process whereby an incoming RF/IF signal is
mixed with specific oscillator frequencies in stages, producing both sum and difference frequency
products. At each stage, the summed frequency product (or image) is removed through low-pass
filtering, allowing the difference frequency product to continue through the signal path. Repeating this
process several times using carefully selected local oscillators (LOs) and well-designed band-pass
filtering, the original signal is translated, or “up-converted” in frequency from low IF to higher RF. Using
a tunable LO as the final mixing oscillator allows the upconverter to translate a fixed IF input frequency
to a broad range of RF frequencies.
The SC5406B is a three-stage superheterodyne upconverter that delivers superior image rejection over
single stage conversion and offers both high signal-to-noise dynamic range and high spurious-free
dynamic range. The RF input ranges from 1 MHz to 3.9 GHz and the IF output is fixed at 70 MHz. When
the output frequency is lower than the intermediate frequency, the device technically behaves as a
downconverter. The converted spectrum polarity may be inverted or non-inverted by programming the
device accordingly.
Fundamentally, each conversion stage consists of a frequency mixer that mixes two input signals and
produces a wanted third. The wanted third component is selected via a frequency filter among other
signals generated in the mixing process. The three primary components of the signals in each conversion
mixer are commonly known as the local oscillator (LO), radio frequency (RF), and the intermediate
frequency (IF) as shown in Figure 2.
Figure 2. Frequency conversion stage using a mixer.
Where R represents the RF component, L represents the LO component, and I represents the IF
component. The LO is resident in the upconverter and is either frequency tunable or fixed in frequency
depending on the stage.
The final IF stage (IF1) is a down-conversion stage –the RF signals are down converted from this IF and
its frequency is higher than the highest output RF frequency specified. The second and third stages
successively convert the 70 MHz IF up to the final IF1, which is at 4675 MHz. Having a high final IF allows
the upconverter to suppress internal IF frequencies from appearing at the RF output port.
The SC5406B exhibits very low phase noise of -107 dBc/Hz at 10 kHz offset on a 1 GHz RF carrier with a
typical noise floor of -150 dBm/Hz. The noise floor can be further reduced below -165 dBm/Hz by
enabling the internal preamplifier. With gain control between -100 dB to +30 dB, capable of generating
RF signals with levels between -100 dBm to +15 dBm with 0 dBm at the IF port. The excellent close-in
L
RI
RF
LO
IF

SC5406B Operating & Programming Manual Rev 1.2 9
spurious free dynamic range is achieved using low noise linear amplifiers, low loss mixers, and high
performance solid state attenuators. State-of-the-art solid state attenuators have improved linearity
over earlier designs. Their attenuation level changes settle under a microsecond, and for applications
that involve frequent range changing, they offer a vastly superior lifetime over mechanical attenuators.
The real-time bandwidth is shaped primarily by the surface acoustic wave (SAW) filter at the front IF
(IF3). Filters in the final (IF1) and second IF stages are not as selective as the final IF filter but they ensure
good isolation between local oscillators (LO). Keeping each LO isolated helps to suppress unwanted
spurious signals.
Frequency accuracy is provided by an onboard 10 MHz temperature compensated crystal oscillator
(TCXO) which can be phase-locked to an external reference source if required, and it is recommended to
do so in applications that may require a more stable and accurate base reference.
Signal Path Description
Figure 3 depicts an overall block diagram of the SC5406B. Starting from the upper right, the IF3 input of
the SC5406B is AC coupled, followed by a switch set by default to switch in the IF port, but it will switch
to the signal generator path when the device enables internal signal generation. When internal signal
generation is not selected, the signal generator is powered down to prevent possible leakages into the IF
path. It is strongly recommended that the IF source be disconnected when internal generation is
selected to prevent external leakages. Furthermore, the internal switch does not terminate the external
port to a load, possibly causing unwanted signal reflections.
Following the switches are two digital step attenuators that are cascaded together to form a 60 dB
attenuation range with 1 dB step increment. These attenuators control the signal level to the IF2 mixer,
determining the linearity and noise dynamic ranges of the device. For better linearity the input levels
should be lower, and to improve the signal-to-noise ratio (SNR) the levels should be higher. For a
compromise, the level at the mixer should be about -16 dBm to -18 dBm, so for a 0 dBm IF input the IF3
attenuator(s) should be set to 16 –18 dB attenuation respectively.
After the attenuators, the IF3 filter shapes the bandwidth of the device. It is the most selective of all the
IF stages. This filter has significant loss so a linear LNA is required to boost the signal prior to passing it
through the filter. Following the filter is the IF2 mixer, driven by local oscillator LO3. This LO frequency
switches between 745 MHz and 605 MHz to convert the 70 MHz IF to 675 MHz, which is the center
frequency of IF2. The default LO2 frequency is 745 MHz, which preserves the spectral polarity of the IF
at the RF. Selecting 605 MHz will invert the spectral content of the RF with respect to the IF. This could
be useful for some systems, especially those where the IF is digitally sampled up and is spectrally
inverted.

SC5406B Operating & Programming Manual Rev 1.2 10
Figure 3. Block diagram of SignalCore 3.9 GHz upconverters.
R
I
LR
I
LR
I
L
N.M
N
R
I
L
10 MHZ
TCXO 100 MHZ
VCXO
Ref.
Detector
4000 MHz
PLL 605/745 MHz
PLL
4675MHz to
8575MHz PLL
YIG Driver
Fine Tune
DDS
Coarse Tune
PLL
DDS
DAC
RF
Filter
RF Atten1
0-30 dB 4675 MHz
Filter IF3 Atten2
0-30 dB IF3 Atten1
0-30 dB
675 MHz
Filter IF3 FL
RF Out
1 MHz –
3900 MHz
IF In
70 MHz
Ref. In
10 MHz
Ref. Out
10/100 MHz
3.9 GHz Three Stage Upconverter
Output level
-110 dBm to 15 dBm
Nom input level 0 dBm
Max input level 13 dBm
10
Module B
Module A
MCU
Power
Regulation
Digital Interface
Temp
Sensor
Calibration
EEPROM
PLL,
Attenuator,
ADC, DAC,
other devices
SPI, RS-232, USB
PCIe Bridge
PXIe
Switchers
Linear Reg.
Module C
Digital Interface Attenuators, Switches
SigGen
IF2 Atten
0-30 dB
RF Atten2
0-30 dB IF2
Mixer
IF1
Mixer
RF
Mixer

SC5406B Operating & Programming Manual Rev 1.2 11
The second IF (IF2) is filtered to remove LO leakages and images and is well-conditioned by the use of
linear LNA to keep the signal levels at an optimum so that SNR is not lost. There is another digital step
attenuator in this IF to balance device to device gain variation. It is also used when large amount of
attenuation is required by the device to produce extremely low level signals such as -100 dBm. IF2 is
mixed with LO2 at the IF1 mixer to obtain the IF1 frequency of 4675 MHz, which is in turn
“downconverted” by LO1 and the RF mixer to obtain the RF frequency range of 1 MHz to 3.9 GHz.
The RF mixer, due to its non-ideal nature, leaks IF1 and LO1 signals through to the RF port. So at the RF
port of the mixer, all components as well as their harmonics are present. Although IF1 and LO1 signals
are relatively low compared to the RF component and well filtered at the output port, their harmonics
could intermodulate with each other and the RF to produce unwanted spurious products inside the RF
band. It is important to keep IF1 at the RF mixer low enough but not too low, so that these spurious
products are kept to at least -65 dBc below the RF level. The API function
sc5406B_CalcAutoAttenuation has an input parameter call “perfSelect” (short for performance
selection) that computes the attenuation requirement for all the attenuators to meet the performance
selected. For best signal-to-noise ratio, the IF at the RF mixer is high, causing larger in-band spurs but
greatly improving the close-in signal to noise power.
Following the RF mixer is an elliptic low-pass filter to suppress both IF1 and LO1 leakages from exiting at
high levels out of the RF port. The final two RF attenuators are used to control the RF output levels.
Local Oscillator Description
The signal path circuit is separate from the local oscillator generation circuits to maximize isolation
between the RF/IF signals and the local oscillators, except for the LO injection paths into the mixers.
Although both circuits reside within the same module, well-designed shielding and circuit layouts ensure
leakages between them are kept to a minimum.
The first local oscillator, LO1, is an agile and tunable phase-lock synthesizer. The synthesizer tunes from
4675 MHz to 8575 MHz, a tuning range of 3900 MHz. The minimum step size is 1 Hz and is accomplished
through a multiple phase-locked loop and DDS hybrid architecture. The use of a hybrid tuning
architecture is important for improved phase noise and improved close-in phase spurious responses.
Operating LO1 at such high frequencies internally to obtain a 1 MHz to 3.9 GHz RF range requires that
the phase noise at these frequencies is sufficiently low so that the converted RF signal phase noise is not
degraded significantly. For example, to produce a 100 MHz RF signal, LO1 is tuned to 4775 MHz, which is
about 48 times higher in frequency than the output frequency. To further ensure phase noise remains
low farther away from the carrier, especially at 100 kHz and 1 MHz offsets, a YIG oscillator is used. It is
important to realize that having a phase noise “plateau” out to several tens of MHz, which is a common
phenomenon with VCO-based synthesizers, is not acceptable for many applications.
Another reason for a hybrid tuning architecture is to reduce the phase spurs associated with phase-
locked loops. A simple fractional PLL may provide resolution to 1 Hz, but it cannot provide 1 Hz
frequency tuning steps with low fractional phase spurs. By using two DDS circuits to provide the 1 Hz
tuning steps and mathematically ensuring that DDS-generated spurs are suppressed within the
architecture, LO1 is made to fine tune to exact frequencies, that is, the frequency synthesized is an exact
integer multiple or division of the reference signal.

SC5406B Operating & Programming Manual Rev 1.2 12
The second local oscillator, LO2, is fixed at 4.0 GHz, synthesized using an integer PLL and a fixed narrow
tune VCO with very low phase noise. The typical raw phase noise of the second stage oscillator is less
than -150 dBc/Hz @ 1 MHz offset. LO2 phase noise contribution to the overall phase noise of the device
is less than 1 dB. LO1 dominates the phase noise of the device.
The third local oscillator, LO3, is synthesized using a fractional PLL and has phase noise lower than both
LO1 and LO2. LO3 is switchable between two frequencies: 605 MHz and 745 MHz, the latter frequency
being the default. Both of these frequencies will set the IF center frequency at 70 MHz. However, at the
default frequency the final RF output spectral polarity is the same as that of the input IF, whereas the
605 MHz frequency will create an inverted RF spectrum. If LO3 is set to 605 MHz by calling the
sc5406B_SetIfInversion function or register, the RF output spectral content will be inverted with respect
to the input IF spectrum. See Figure 4 for a graphical representation of this process.
Figure 4. Graphical representation of RF inversion.
All local oscillators are phase-locked to an internal 100 MHz voltage controlled crystal oscillator (VCXO),
which sets their close-in phase noise performance. The 100 MHz VCXO is in turn phase-locked to the
internal 10 MHz TCXO for frequency accuracy and stability. For better frequency accuracy and stability
than the TCXO onboard the SC5406B, or for frequency synchronization, the user can programmatically
set the device to phase lock the TCXO to an external 10 MHz reference source by programming the
REFERENCE_SETTING register. It is important to note that the TCXO will only attempt to lock to an
external source if one is detected. A typical external reference source minimum level of -10 dBm is
required for detection to be successful. A reference source level of 0 dBm to +3 dBm is recommended
for normal operation. The reference source is fed into the device through the “ref in” port. The device
can also export a copy of its internal reference through the “ref out” port. The output reference
frequency is selectable for either 10 MHz or 100 MHz output. By default, routing of the reference signal
to the “ref out” port is disabled. It can be enabled by programming the REFERENCE_SETTING register.
This reference frequency is sourced from the internal 100 MHz OCXO, and the default output selection is
10 MHz, which is divided down from the 100 MHz VCXO. The output reference level is typically +3 dBm.
RF
A
fc
A
IF
A
ifc
Non Inverted Conversion
Inverted Conversion
RF
fc

SC5406B Operating & Programming Manual Rev 1.2 13
Frequency Tuning Modes
Tuning of the SC5406B superheterodyne upconverter is accomplished through the tuning of LO1. LO1
has two sets of control parameters that can be explored to optimize the device for any particular
application. The first set of parameters, TUNE SPEED, sets the tuning and phase lock time as the
frequency is changed. TUNE SPEED consists of two modes - Fast Tune and Normal; both of these modes
directly affect the way the YIG oscillator is configured. Fast Tune mode deactivates a noise suppression
capacitor across the tuning coil of the YIG oscillator. Doing so increases the rate of current flow through
the coil, correspondingly increasing the rate of frequency change. In Normal mode the capacitor is
activated, slowing down the rate of frequency change. The advantage of activating the capacitor is that
it shunts the noise developed across the coil, decreasing close-in phase noise.
The other set of control parameters, FINE TUNE, sets the tuning resolution of the device. There are three
modes: 1 MHz, 25 kHz, and 1 Hz tuning step sizes. The first two modes use only fractional phase
detectors to tune the frequency of the LO1 synthesizer, while the third mode enables the DDS to
provide 1 Hz resolution. The PLL-only modes (1 MHz and 25 kHz) provide the ability to realize exact
frequencies with tuning as fine as 25 kHz. Use of these modes offers several advantages - lower phase
spurs and less computational burden to set a new frequency. These modes have the lowest phase
spurious signals, below the levels published in the product specification. The DDS mode also tunes to
exact frequencies; however, it requires many more computing cycles and additional register-level writes
in order to set a new frequency. Comparing times, the device requires up to 175 microseconds to
compute and change to a new frequency in PLL only modes but requires up to 350 microseconds in the
DDS tuning mode. At first glance it may seem that these differences would directly impact frequency
tuning times. However, tuning times are predominantly set by the physical parameters of the YIG
oscillator. Computation and register writes typically account for less than 25% of the total tune time of a
10 MHz step change in frequency.
It is important to note that although the synthesized frequencies are exact frequencies, there are
observable random phase drifts in the up converted signals. These drifts are due to PLL non-idealities
rather than a frequency error in the DDS tuning circuit. Having exact frequency synthesis is important for
many applications. Published phase noise and spurs specifications are based on the 1 Hz (DDS) mode.
Setting the SC5406B to Achieve Best Dynamic Range
The SC5406B is designed to achieve high dynamic range. It is designed as a receiver for signal analyzers,
which require the ability to handle larger signals well. The design ensures the SFDR dynamic range
specification is met when the IF signal is at 0 dBm, 18 dB of IF3 attenuation, and the RF level is at 0 dBm.
For applications where the SNR must be maximized, such as an optimal sine tone, little to no IF3
attenuation should be applied, setting most of the attenuation in the RF attenuators. The IF2 attenuator
should be adjusted to lower in-band intermodulation spurs.
The SC5406B is designed for a nominal input IF level of 0 dBm. Depending on the application, the user
will need to set the appropriate gain of the device (via attenuation), and the output level, to suit the
particular application. For broadband signals, where the absolute noise power is relatively high, the
upconverter should be adjusted for improvement in the SNR; that is, decrease IF3 attenuation and

SC5406B Operating & Programming Manual Rev 1.2 14
increase RF attenuation as necessary to adjust for the desired output level. The optimal setting occurs
when the total in-band noise power is at the same level as the IMD products.
For applications that require better linearity to improve close-in inter-modulated products, the IF3
attenuation should be increased. The user should adjust these IF attenuators carefully so that the noise
does not dominate.
SignalCore provides a simulation tool that mimics the behavior of the SC5406B. The user may run the
simulator to get an understanding of what the parameters need to be set to on the upconverter to
achieve certain performance. Additionally, the function sc5406B_CalcAutoAttenuation helps the user
obtain the necessary attenuator parameters to set up the device for the best compromise of linearity
and noise performance for a given set of input and output parameters.
Operating the SC5406B Outside Normal Range
The SC5406B is capable of tuning below 1 MHz and above 3.9 GHz. These frequencies lie outside of the
specification range and performance will be degraded if operated in these outer margins. For some
applications, the reduced dynamic range or elevated spurious levels in these ranges may not pose an
application concern. The lowest tunable frequency is 0 MHz (DC). However, for input frequencies below
1 MHz, the AC coupling capacitors in the circuit limit/attenuate the signal significantly. On the upper end
of the spectrum, the input low-pass filter will attenuate the signal rapidly as the frequency increases
above 3.9 GHz. Calibration stored on the device EEPROM does not account for these out of range
frequencies, so applying any correction using the stored calibration is not valid.

SC5406B Operating & Programming Manual Rev 1.2 15
SC5 4 0 6 B PR O G R A M M I N G IN T E R F A C E
Device Drivers
The SC5406B is programmatically controlled by writing to its set of configuration registers, and its status
read back through its set of query registers. The user may choose to program directly at the register
level or through the API library functions provided. These API library functions are wrapper functions of
the registers that simplify the task of configuring the register bytes. The register specifics are covered in
the next section. Writing to and reading from the device at the register level involves calls to the
sc5406B_RegWrite and sc5406B_RegRead functions respectively. These functions are accessible in the
API library.
For USB communication, there are many USB drivers available that can be used to directly access the
registers of the device - WinUSB, libusb-1.0, libusb-win32, and NI-VISA are a few examples. The SC5406B
API is based on the libusb-1.0 driver and is provided as a Microsoft Windows dynamic linked library
(sc5406B.dll) or Linux shared library (libsc5406B.so). For more information on the libusb driver, visit
www.libusb.org. For the Windows platform, libusb-1.0 relies on WinUSB at the kernel level. For libusb-
1.0 to function properly on Windows platforms, WinUSB must be installed on the host.
For LabVIEW support on Windows operating systems, SignalCore provides two types of APIs - an API
consisting of simple wrapper VIs that make calls to the libusb-based sc5406B.dll, and a separate API with
all device functions written as native G-code VIs based on NI-VISA.
For other operating systems or embedded systems, users will need to access the registers through their
own proprietary USB driver or through one of the drivers mentioned above. Should the user require
additional assistance in writing an appropriate API other than that provided in the software installation,
please contact SignalCore.
The SC5406B USB Configuration
The SC5406B USB interface is USB 2.0 compliant running at Full Speed, capable of 12 Mbits per second.
It supports 3 transfer or endpoint types:
•Control Transfer
•Interrupt Transfer
•Bulk Transfer
The endpoint addresses are provided in the C-language header file and are listed below.

SC5406B Operating & Programming Manual Rev 1.2 16
The buffer lengths are sixty-four bytes for all endpoint types. The user should not exceed this length or
the device may not respond correctly. Furthermore, all registers require five bytes or less with the
exception of registers 0x24 (GET_CAL_EEPROM_BULK) and 0x25 (GET_USER_EEPROM_BULK). These two
registers return sixty-four bytes of valid data upon executing a device read.
Writing the Device Registers Directly
Device commands for the SC5406B vary between two bytes and five bytes in length. The most significant
byte (MSB) is the command register address that specifies how the device should handle the subsequent
configuration data. The configuration data likewise needs to be ordered MSB first, that is, transmitted
first. For configuration commands, an output buffer of five bytes long is sufficient. To ensure that a
configuration command has been fully executed by the device, reading a few bytes back from the device
will confirm a proper command write because the device will only return data upon full execution of a
command. A map of the configuration registers for the SC5406B is provided in Table 2. Details for
writing the registers are provided in the next section.
Reading the Device Registers Directly
Valid data is only available to be read back after writing one of the query registers. With the exception
of registers 0x24 (GET_CAL_EEPROM_BULK) and 0x25 (GET_USER_EEPROM_BULK), where sixty-four
bytes of valid data are returned, only the first two bytes of the device IN endpoints contain valid data.
When querying the device, the MSB is returned as the first byte. A map of the query registers for the
SC5406B is provided in Table 3. Details for reading the registers are provided in the next section.
Using the Application Programming Interface (API)
The SC5406B API library functions make it easy for the user to communicate with the device. Using the
API removes the need to understand register-level details - their configuration, address, data format,
etc. Furthermore, the user does not need to understand the different transfer types of the USB
interface. For example, to obtain the device temperature the user simply calls the function
sc5406B_GetTemperature. The software API is covered in detail in the "Software API Library Functions"
section.
// Define SignalCore USB Endpoints
# define SCI_ENDPOINT_IN_INT 0x81
# define SCI_ENDPOINT_OUT_INT 0x02
# define SCI_ENDPOINT_IN_BULK 0x83
# define SCI_ENDPOINT_OUT_BULK 0x04
// Define for Control Endpoints
# define USB_ENDPOINT_IN 0x80
# define USB_ENDPOINT_OUT 0x00
# define USB_TYPE_VENDOR (0x02 << 5)
# define USB_RECIP_INTERFACE 0x01
Table of contents
Other SIGNALCORE Control Unit manuals
Popular Control Unit manuals by other brands

LS Industrial Systems
LS Industrial Systems XGT Series user manual
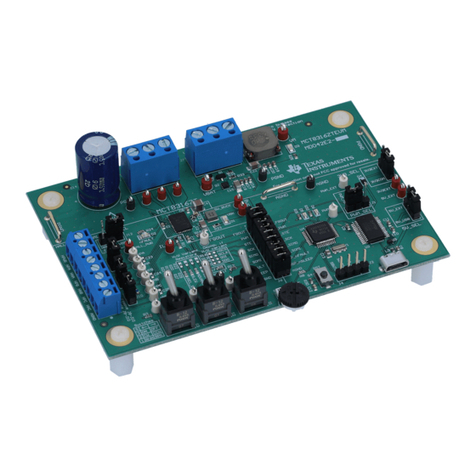
Texas Instruments
Texas Instruments MCT8316ZT user guide

LOVATO ELECTRIC
LOVATO ELECTRIC EXM10 10 instruction manual
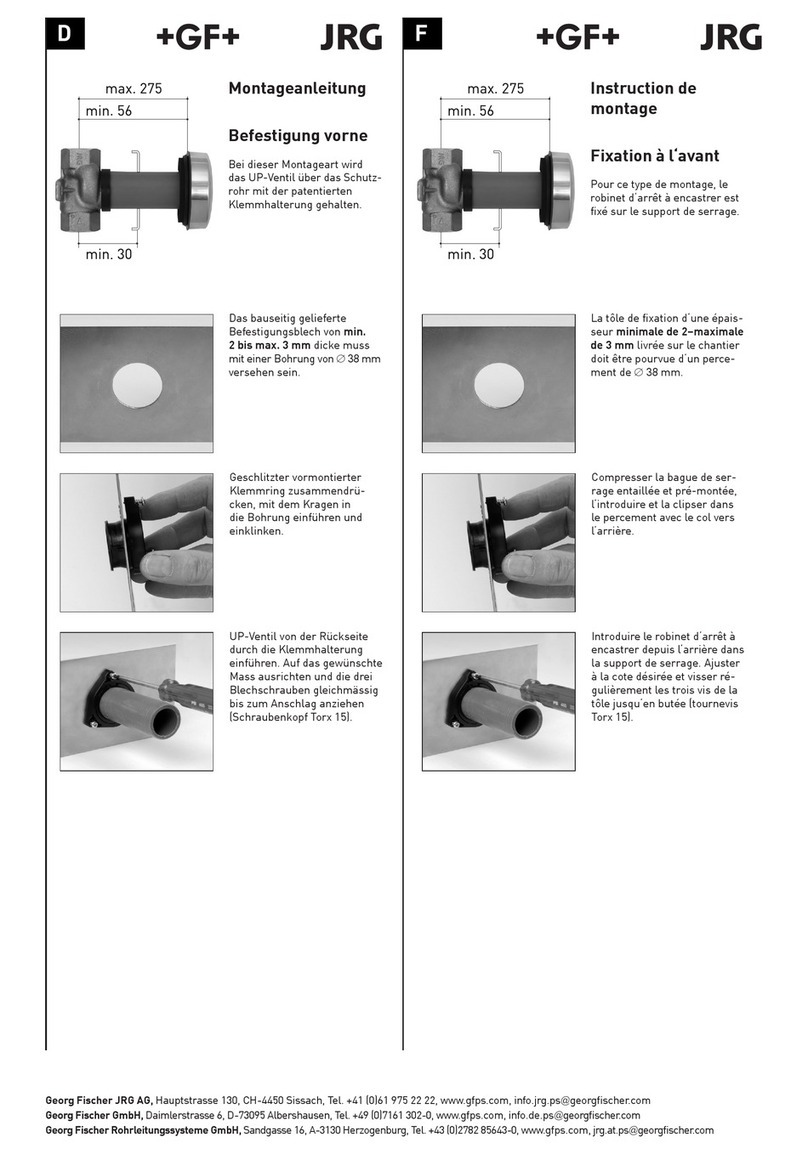
GF
GF JRG Installation
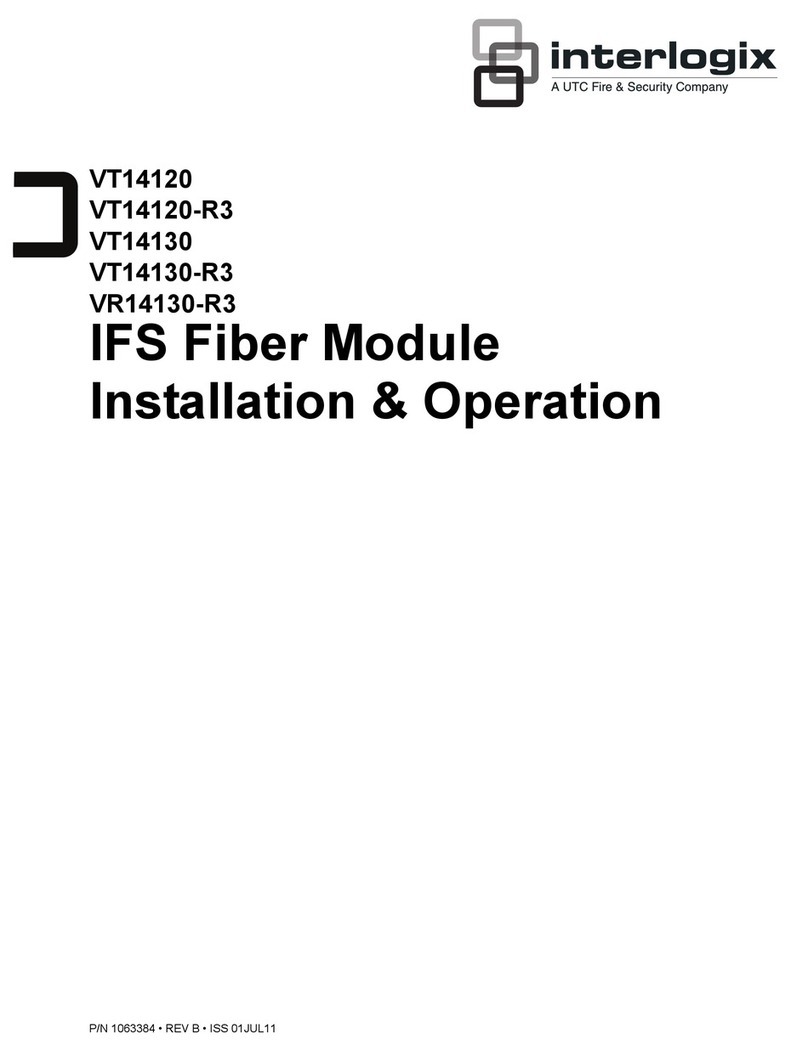
UTC Fire and Security
UTC Fire and Security interlogix VT14120 Installation & operation

Sharp
Sharp NU-AK300 installation manual
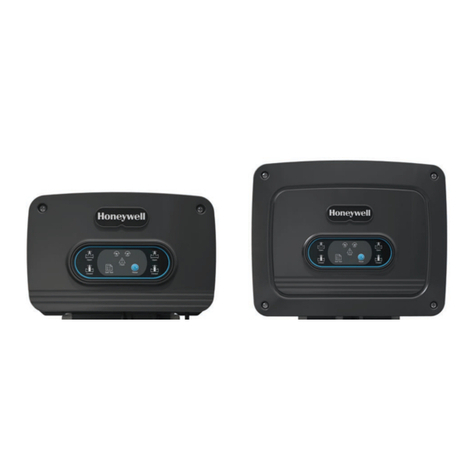
Honeywell
Honeywell SV2 Series installation instructions
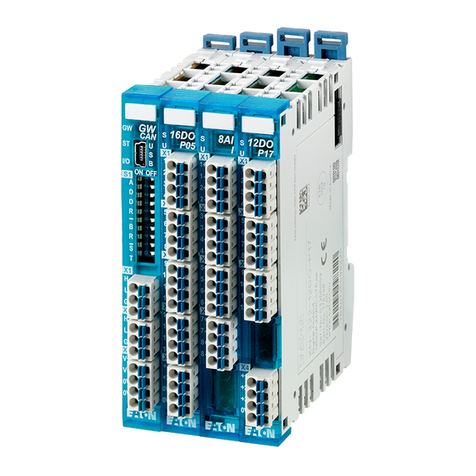
Eaton
Eaton XN300 manual
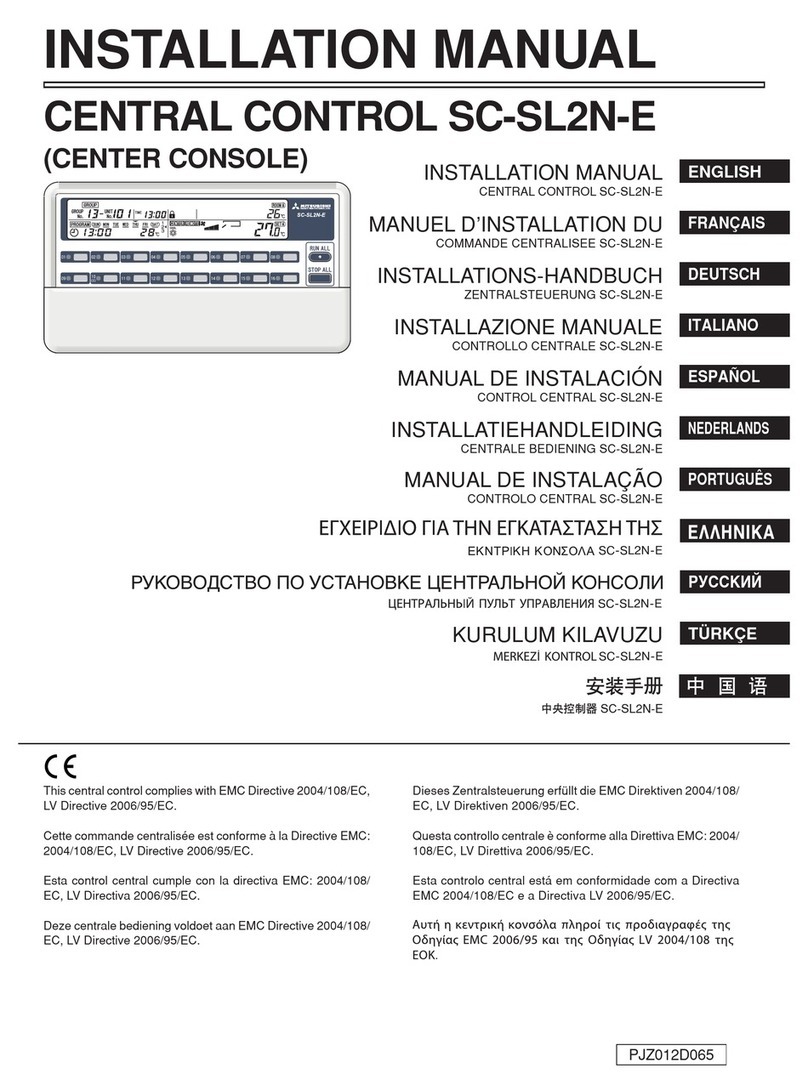
Mitsubishi Heavy Industries
Mitsubishi Heavy Industries SC-SL2N-E installation manual
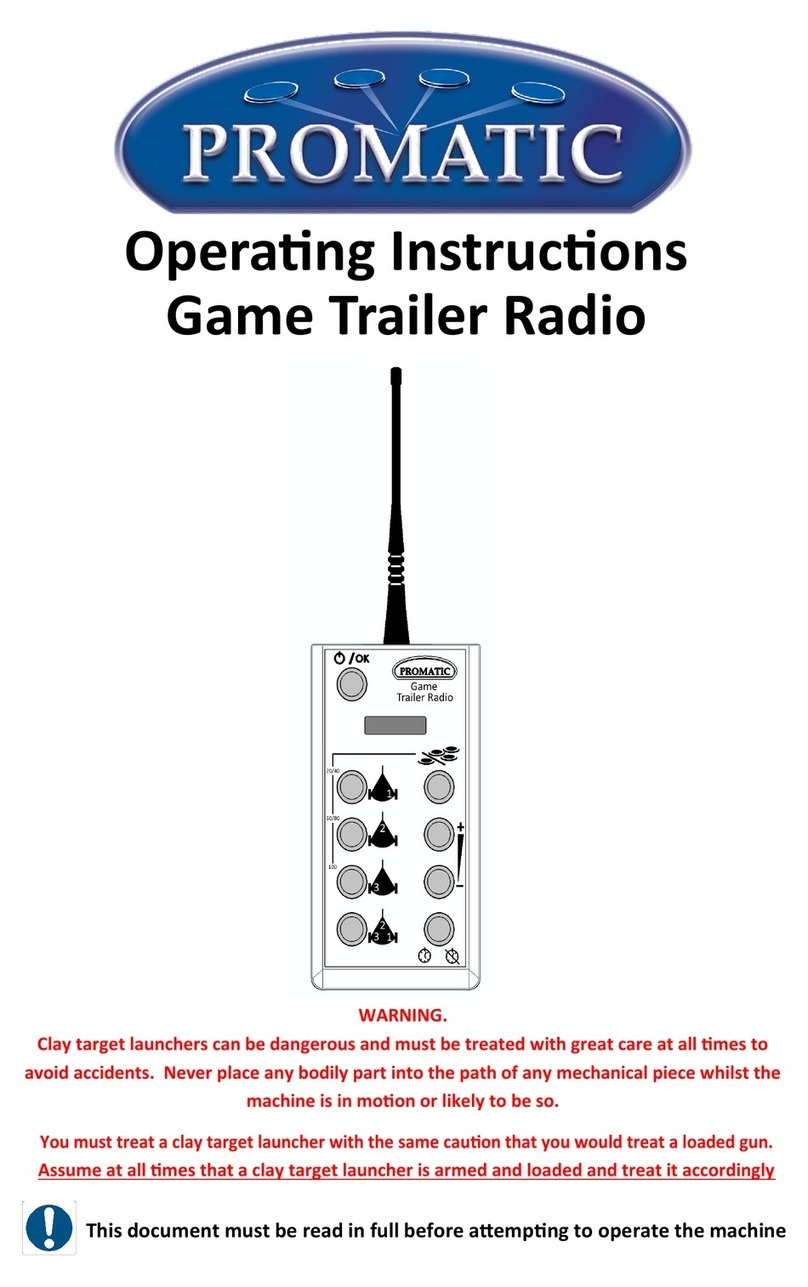
Promatic
Promatic Game Trailer Radio operating instructions
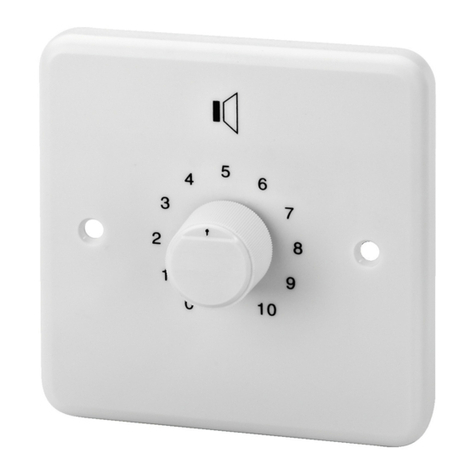
Monacor
Monacor ATT-135/SI quick guide

Johnson Controls
Johnson Controls GS-20 Series Installation Sheets Manual