SolutionAir GRW Safety guide

MANUAL – INSTALLATION
GRW
Precision Environmental Control Unit
v003 –Issue Date: 03/03/20 © 2020 SolutionAir Group. All rights reserved.
TM

GRW
Table of Contents
SolutionAir Group
404 Egesz Street
Winnipeg, MB R2R 1X5
115 Turnbull Court
Cambridge, ON N1T 1C6
MANUFACTURED BY
NOTE: This document is customer property and must
be retained by the unit’s owner for use by maintenance
personnel.
Overview
Description......................................................................................................... 1
General Safety Information ........................................................................... 1
Submittal Documents...................................................................................... 1
Unit Nameplate .................................................................................................2
Unit Inspection..................................................................................................2
Storage ................................................................................................................2
Installation Instructions
Mechanical Installation...................................................................................3
Electrical Installation........................................................................................5
Drain Lines & Condensate Traps ..................................................................7
Split Roof-Seam Installation and Sealing ...................................................8
Split Roof-Seam Sealing Procedure .......................................................... 11
Installation Checklist ....................................................................................15
Maintenance
Filters..................................................................................................................16
Fan and Motor Assembly...............................................................................16
Service and Warranty Procedure................................................................16
Maintenance Checklist..................................................................................17
Troubleshooting..............................................................................................18
Start-up Instructions......................................................................................19
Typical Unit Sequence of Operation ....................................................... 20
GRW Start-Up Request Form & Pre-Start-Up Checklist ......................21
Limited Warranty ........................................................................................... 26
WARNING
Fire or Explosion Hazard
Failure to follow safety warning exactly could result in
serious injury, death or property damage.
Be sure to read and understand the installation,
operation and service instructions in the manual.
Improper installation, adjustment alteration, service
or maintenance can cause serious injury, death or
property damage.

1
SolutionAirGroup.com |GRW - Manual
GRW
Product Overview
Description
The GRW unit is a precision air conditioning and
dehumidifying system specifically designed for the indoor
horticultural environment. Each unit is precisely sized
for the specific application to energy eciently provide
precision temperature and control over a wide range of
space and plant loads over the entire year.
SolutionAir is pleased that you have put your faith in the
GRW and we look forward to it providing years of trouble
free performance.
General Safety Information
This manual provides information on installation, start-up
and maintenance for an indoor horticultural unit. Improper
installation can lead to unsatisfactory operation or
dangerous situations. This unit should only be installed and
maintained by qualified personnel.
Qualified personnel should have a clear understanding of
the contents of this manual prior to installation. Improper
installation may lead to electric shock, possible injury
from contact with moving parts and/or possible burns
from contact with heating components. Additional safety
concerns can arise from unit location such as a roof or
inclement weather (outdoor installations). Additional safety
precautions may be required.
Installer shall follow this manual and project submittals. If
these instruction conflict with any applicable national or
local code requirements such as, but not limited to: the
National Electrical Code (NEC); the Canadian Electrical
Code (CEC) in Canada; or, local building codes, those
codes shall supersede the factory directions.
WARNING
Fire or Explosion Hazard
The manufacturer’s warranty does not cover any
damage or defect caused by modifications to the
unit including unauthorized attachments of other
components. Such activity may lead to unsatisfactory
performance and may endanger life and property.
Submittal Documents
Detailed submittals are available for this and all related
units. These submittals contain pertinent information
required to properly install the equipment. Please review
them thoroughly before commencing the installation.

2GRW - Manual |SolutionAirGroup.com
GRW
Product Overview
Unit Nameplate
Figure 1 shows a typical nameplate for a GRW. The
nameplate is generally located near the main electrical
connection The nameplate includes model number, serial
number, electrical characteristics and other pertinent data.
Unit Inspection
This unit has been inspected and tested prior to shipment
to make sure the unit is free from manufacturer defects. It
is possible that damage may occur during shipping, rigging
and installation.
Upon receiving the unit, check that all items have been
delivered by comparing the Bill of Lading to the equipment
received. If anything is missing or damaged, notify the
carrier immediately. The carrier should note this on the
packing slip or other form of documentation and provide a
copy.
NOTE: it is a good idea to take a photograph of any possible
damage for record purposes.
Check the unit model number to make sure that it is
correct. If there are any issues, do not proceed with the
installation. Contact your sales representative.
Storage
If the unit is to be stored, take precautions to prevent
condensate from forming inside the unit’s electrical
compartments. Make sure the equipment is protected
from weather and dust from site conditions by temporarily
sealing all openings to the air tunnel for outdoor units and
completely covering indoor units.
Do not use the unit for temporary conditioning without
first completing the full start-up procedure. If the unit
is used for conditioning during construction, protect
evaporators from construction dust. SolutionAir will not
assume any responsibility for equipment damage resulting
from condensate accumulation on the unit’s electrical and
/ or mechanical components nor from any damage that
results from improper coil protection during operation
during construction.
FIGURE 1 - TYPICAL NAMEPLATE

GRW
Installation
3
SolutionAirGroup.com |GRW - Manual
Mechanical Installation
Location
GRW units are approved for both indoor and outdoor
installations.
The GRW unit is designed for complete field serviceability
including the removal of evaporator and condenser coils.
Also, the air-cooled condensers, if equipped, require clear
unfettered airflow for proper operation. The submittals
include recommended service areas for these features,
these areas should be accessible, open, and free of other
equipment.
In addition, for roof top installations, consideration should
be made to ensure that normal service trac to the unit
will not cause damage to the roof system. If the equipment
is located on a sloped roof or a raised structure, the
platform should be suciently large to allow for the unit to
be safely serviced.
Clearances
The GRW unit is designed to be field-serviceable, which
includes the coils, filters, fans/motors, dampers, and
electronics. Refer to the submittal engineering drawings for
the locations of access doors and safety/service areas, and
ensure there is sucient clearance for safety, inspection,
and service.
Roof Curb or Base
GRW units can be installed on a concrete housekeeping
pad, sleepers or a roof curb. The unit must be adequately
supported with either field supplied sleepers or structural
metal. Details of the required support can be found in the
submittals. Make sure that the unit supports are the correct
dimensions and that they are flat and level.
Check that the housekeeping pad is the correct dimensions
for the unit and that it is flat and level. If there is an external
condensate drain check that there is enough height for the
required condensate traps and that a means of removing
the condensate is located nearby.
Generally the curb is shipped in advance of the unit
delivery. It should be installed along with any required
ductwork prior to unit installation. Where a roof curb has
been supplied in knocked-down condition, absolute care
must be taken to make sure that all corners are square, and
that finished dimensions exactly match those provided on
the drawings. If this is not done, problems could arise with
the installation and seal of the unit to the curb.
First insure that the top of the curb is level and flat, shim
the curb to the roof deck as required. Then, check diagonal
dimensions prior to securing the curb to ensure that
dimensional integrity has been maintained during shipping.
Finally, complete roofing in accordance with accepted
roofing practices.
Prior to the installation of the unit, check that the curb
is the correct dimensions for the unit and that the curb
profile is correct (this is especially important if the curb
is not supplied by SolutionAir). Curb ductwork and
condensate drains that pass down through the curb must
be installed by installing contractor prior to unit placement.
Gasketing or other forms of sealant must be used around
the curb perimeter and at the duct connections. When
the curb is supplied by SolutionAir, a neoprene gasket is
included. Prior to the installation of the unit, secure the
gasket to the mating surface of the curb by peeling the
backing o the gasket material and applying adhesive-side
down.
NOTE: To minimize sound transmission, only cut openings
in roof deck for ductwork penetrations. Do not cut out the
entire roof deck within in the curb perimeter.

GRW
Installation
4GRW - Manual |SolutionAirGroup.com
Roof Curb Supports and Levelling
To ensure the roof curb and GRW unit is properly braced,
the curb must be supported at all indicated roof curb beam
intersection points, as shown in Figures 2 and 3. The red
circles indicate intersections that must be supported. The
support structure is to be determined at the discretion of
the unit’s owner.
Figure 2 depicts the required roof curb support points
for units 180” wide and less. Figure 3 depicts the required
roof curb support points for units over 180” wide. Refer to
submittal drawings for the exact width of the unit.
To ensure proper drainage, the roof curb must be installed
more level or equal to 1/100” per 1’, measured from corner
to corner of the curb as shown in Figure 4. The maximum
deviation in height between any two corners is ¼”.
Unit Width Number of Roof Curb
Support Points
180” or less 8
Over 180” 12
FIGURE 2 – ROOF CURB SUPPORT POINTS FOR UNITS 180”
WIDE AND LESS
FIGURE 3 – ROOF CURB SUPPORT POINTS FOR UNITS OVER
180” WIDE
FIGURE 4 –CORNER TO CORNER MEASUREMENTS FOR CURB
LEVELING

GRW
Installation
5
SolutionAirGroup.com |GRW - Manual
Rigging
WARNING
Never lift in windy conditions. Use properly-sized
cables, chains, or slings only as shown. Each cable,
chain, or sling must be capable of supporting the
weight of the entire unit or component. Adjust cable,
chain, or sling length for an even lift. Other lifting
arrangements may damage unit or component. Failure
to properly lift unit or component may result in death
or serious injury.
NOTE: All GRW units are designed to be lifted from the base.
Each section of the unit is provided with lifting points at
each corner and sometimes at intermediate points.
Duct Connections
On outdoor units with ducting passing down through the
curb, the ducting will be installed prior to unit placement
and attached to the curb. For all other duct connections,
the ductwork will be connected to the unit casing using
sheet metal screws by the installing contractor. Unless
indicated on the submittal drawings, the weight of the
ducting should not be placed directly on the unit. The
installing contractor should provide an external means to
carry the duct weight.
Access panels in the ducting near the unit are
recommended. Where no access to the unit inlet or
discharge section is provided as part of the unit (for
example an access door in the unit), access panels are
strongly recommended for inspection and service.
Blower or Fan
GRW units include direct plenum fans. The motor, fan,
frame, and mounts should be visually inspected before
initial start-up and at every fan service.
The blower/fan and motor are aligned before shipping
from the factory, shipping and or mounting may result
in misalignment, proper motor fan alignment should be
checked and adjustments should be made, if required, prior
to unit start up.
GRW units come equipped with variable frequency drives
for speed adjustment. The unit controller allows a broad
range of blower speeds to accommodate necessary field
balancing, see the controller manual for directions on
adjustment.
If the blower can not be properly balanced using the
controller settings, please contact SolutionAir for further
instructions.
Variable Frequency Drive (VFD)
Variable frequency drives are used to control the speed of
the motor and fan. Fan speed is controlled either with a set
point, or with a controlling signal. Refer to the submittal
for control and wiring specifics. For specifics regarding
the VFD supplied with this unit, refer to the attached
documentation.
Final Assembly
Before proceeding with the electrical installation, remove
all shipping braces (such as fan shipping brackets), packing,
etc.

GRW
Installation
6GRW - Manual |SolutionAirGroup.com
FIGURE 5 – TYPICAL SPLITTER/TERMINAL BLOCK
Electrical Installation
NOTE: Use Copper Conductors Only: Unit terminals are
designed for copper conductors only. Failure to use copper
conductors may result in unit damage.
Main Power Connection
All connections to the unit and the main disconnect switch
must conform to the applicable Electrical Codes
1. Before proceeding, ensure that the electrical
connections on the unit and supply match. The proper
voltage for connection is listed on the rating plate
attached to the unit.
2. Unit must be electrically grounded in accordance with
local codes, or in the absence of local codes, with the
National Electrical Code, ANSI/NFPA 70, and/or the
Canadian Electrical Code, CSA C22.1, if an external
electrical source is utilized.
3. Refer to the unit submittal drawing to determine the
suggested location of the field wired power supply.
Where a disconnect is supplied as part of the unit, the
main power connection will be the line side of the
disconnect.
4. If the unit is not supplied with a factory mounted
disconnect, a field supplied disconnect must be
installed in accordance with local codes, or in the
absence of local codes, with the National Electrical
Code, ANSI/NFPA 70, and /or the Canadian Electrical
Code, CSA C22.1. Where a disconnect is supplied by
others, the main power connection to the unit will be
the line side of the main splitter block. Refer to unit
electrical wiring diagrams for details.
5. Ensure that the routing of the power supply wiring
does not interfere with removal of any unit access
door, or in any way hinder servicing of the unit.
6. Refer to the submittals for electrical service routing.
Unless indicated on the submittals, DO NOT penetrate
the floor of the unit to route electrical conduits to
the unit control panel. Provide a pitch pocket in
accordance with standard roofing practice.
7. For units that are shipped in multiple sections, some
electrical connections may have to be made by the
installer in the field. Field wiring to be done by the
installer appears as a dotted line on the wiring diagram.
Wiring to connect two sections of a unit will be marked
by the factory and a terminal block will be provided for
such connections (as shown in Figure 5).

GRW
Installation
7
SolutionAirGroup.com |GRW - Manual
8. Fuses are furnished and installed by the factory in
accordance with the National Electrical Code, ANSI/
NFPA 70, and /or the Canadian Electrical Code, CSA
C22.1. If replacement of any fusing is necessary, the
replacement MUST be of the same amperage as the
original. Failure to use equivalent replacement fuses
may result in damage to components within the
electrical system of the unit and/or the building. If any
of the original wires need to be replaced, they must
be replaced with type TEW 105° or equivalent except
where noted.
9. On units with three-phase power supplies, make sure
that motor rotation is correct as connected.
Auxiliary Power Connections
A separate 120/1/60 power supply may be required on
units with convenience outlets and lights. Refer to unit
wiring diagrams for wiring sizing details and connection
points.
Control Installation
All field wiring must be in accordance with local codes, or
in the absence of local codes, with the National Electrical
Code, ANSI/NFPA 70, and/or the Canadian Electrical Code,
CSA C22.1.
Control wiring will depend on the controls provided with
the unit. A controller is provided with the unit unless
otherwise specified in the submittal documents. Refer to
unit electrical wiring diagrams for details.
Control Connections
Units supplied with controllers may require field-wiring to
a remote sensor or control panel. Refer to unit electrical
wiring diagrams for details.
An optional space thermostat or sensor may be shipped
loose for field installation. The sensor may be duct
mounted and/or wall mounted.
1. Locate space sensors or thermostats where they
will provide a representative reading of the space
condition.
2. Avoid areas with cold drafts or in the warm supply-air
stream of the unit.
3. On indoor units, do not mount the thermostat or
sensor on the unit casing, as it may be aected by heat
radiating o the unit.
4. Do not place near other sources of warmth, such as
lamps, appliances, etc.
5. Refer to unit electrical wiring diagrams for details on
how to wire the sensor to the control panel.
6. Ensure that all remote wiring is equivalent to factory
installed wiring and that voltage drop does not exceed
10 percent.
An optional duct mounted discharge air temperature
sensor may be shipped loose for field installation.
1. The sensor strip must be parallel to the flow of air.
2. The sensor must be mounted as close to the center of
the duct as possible.
3. The sensor must be located in a straight section of the
duct and must be 8-10 feet (2.4 to 3m) downstream
from the supply air connection.
4. Do not install temperature sensors near any elbows or
transitions.
5. Refer to unit electrical wiring diagrams for details on
how to wire the sensor to the control panel.
6. Ensure that all remote wiring is equivalent to factory
installed wiring and that voltage drop does not exceed
10 percent.
An optional remote control panel may be shipped loose for
field installation.
7. Locate the indoor panel where operation and
maintenance personnel have ready access.
8. Follow the manufacturer’s installation instructions.
9. Refer to unit electrical wiring diagrams for details on
how to wire the sensor to the control panel.
10. Ensure that all remote wiring is equivalent to factory
installed wiring and that voltage drop does not exceed
10 percent.
Where possible, the low limit temperature sensor is factory
mounted. Some unit configurations require the sensor
to be field mounted in the supply air ductwork. In this
situation, the sensor and field wiring will be coiled up in the
weather housing. The installing contractor shall install the
sensor approximately 10 ft. (3 m) down the supply air duct.

GRW
Installation
8GRW - Manual |SolutionAirGroup.com
FIGURE 7: EMSEAL PATTERN TOP CORNER VIEW
Split Roof-Seam Installation
and Sealing
Inspection:
1. Check for visual damage on the
exterior of all sections.
2. Closely inspect the lifting-lugs,
ensure there is no visual distortion
or cracking of the welds.
3. Remove wrapping and plywood
(ensure all fasteners are accounted
for).
4. Remove installation materials
from the unit prior to lifting (see
Materials List below). You will
require these to prepare the curb/
unit for installation.
5. Check for visual damage on the
interior of all sections.
6. Clean any debris accumulated
during shipping from air-tunnels
as required.
Materials List
7. Remove shipped-loose
components from the filter/
blower sections that are
necessary for unit installation,
including:
a) Curb acoustic sealant (if
included)
b) Unit-split sealing materials:
i) Foam gasket (Emseal or
similar)
ii) Outdoor-rated
polyurethane sealant (3M
550 or similar)
iii) Foam backer-rod (if
included)
iv) Stainless steel fasteners
(bolts, washers, nuts)
TOP CORNER EMSEAL DETAIL
FIGURE 6: TOP VIEW OF ACOUSTIC SEALANT PATTERN
Acoustic Sealant
Roof Curb

GRW
Installation
9
SolutionAirGroup.com |GRW - Manual
1/4” X 2” WIDE
EMSEAL
ACOUSTIC SEALANT
PLEASE ENSURE
THIS PIECE OF
EMSEAL IS IN
TIGHT CONTACT
WITH CURB
FIGURE 8: EMSEAL PATTERN BOTTOM CORNER DETAIL
Roof-Curb Preparation:
8. Prior to lifting, prepare the roof-curb.
a) With the roof-curb in place, check that the curb is
square and the dimensions/orientation match the
provided curb drawing(s).
b) Ensure the upper flange of the roof-curb is dry and
free of dust/debris.
9. Apply a generous (~1/2” wide) bead of acoustic sealant,
centered on the top flange of the curb as illustrated in
Figure 6.
a) Ensure no gaps/breaks in the sealant bead(s).
b) Sealant is only necessary on the parts of the curb
which come in contact with the unit. Duct supports
and cross-members (if present) do not require
sealant as illustrated in Figure 6.
10. Proceed with installation of the unit sections.
Coil-Section Installation:
11. Lift the coil section into place, ensuring that orientation
and placement on the roof-curb match the provided curb
drawing(s).
Blower-Section:
12. Apply supplied Emseal (sealing strips) to the coil-
section on the blower-side, as indicated on the
drawing (see Figure 7 and Figure 8 and submittal
drawings).
a) Ensure no overlapping Emseal sections.
13. Clean the coil-section receiver-flange on the blower-side,
then apply a generous amount of acoustic sealant (see
Figure 9).

GRW
Installation
10 GRW - Manual |SolutionAirGroup.com
FIGURE 9: SECTION PLACEMENT
FIGURE 10: POSITIONED SECTION FASTENING BOLTS
FIGURE 11: TIGHTENED SECTION FASTENING BOLTS
14. Install the blower-section, by lowering it down within
1” of the coil-section.
NOTE: the blower-section must be lowered into the
coil-section receiver flange, which will aid in guiding
the sections together. If the gap between the sections
is more than 1.0”, the blower section cannot be pulled
into place without damaging the coil-section receiver.
a) A centering-punch shall be used (through the
lifting-lug bolt-holes) to guide and align the
sections together.
b) Ensure less than a 1.0” gap between the blower
and coil sections (Figure 9).
c) Fasten the blower and coil sections together (with
the provided stainless steel hardware).
i) Insert 2” stainless steel bolts (with washers)
into the holes on the coil-section lifting lug,
through to the matching blower section holes
(Figure 10).
ii) Finger-tighten a stainless steel nut (backed by
a washer) onto the 4 bolts, as illustrated above.
iii) Install and finger-tighten the supplied side-
flange bolts (stainless steel 1” bolts, washers,
and nuts), starting at the base on both sides,
moving towards the top of the unit.
iv) Apply a light bead of outdoor-rated
polyurethane caulking to the side-seams,
ensuring the caulking covers the Emseal
and touches the aluminum on both sections
(Figure 11).
v) Gradually bring the units together by
tightening the 4 lifting-lug nuts (2 on each
side), until there is less than a 1/8” gap
between the lifting lugs.
vi) Once the four lifting-lug nuts are tight, tighten
the side-flange bolts from bottom to top.
I) Clean o any sealant squeeze-out with a
dry disposable rag.
15. Once complete, repeat the above steps for the filter-
section.

GRW
Installation
11
SolutionAirGroup.com |GRW - Manual
Split Roof-Seam Sealing
Procedure
Sealing Roof Seams at GRW Splits:
1. Seal ends of roof-seam at GRW
unit splits with Emseal end-dams.
a) Cut Emseal strips roughly 1”
longer than the distance from
the existing Emseal to the
blower/coil roof flange. Do not
remove backing.
b) Cut black Emseal sponge
back by roughly 1.25”, without
cutting the clear backing
(Figure 12).
c) Dog-ear the top of the Emseal
strip (partially remove the clear
plastic backing), enough to be
able to firmly grasp from the
edge.
d) Place Emseal strip firmly
against existing Emseal
(spanning the split between
the sections) and ¼” from
edge of coil/blower roof
(Figure 13).
e) Once satisfied with the
placement, carefully remove
clear backing. Let Emseal strip
expand into place (may take
5-60 minutes, depending on
outdoor temperature and
humidity).
f) Repeat the above steps for
each roof-seam end (four total
for each unit).
2. Firmly apply sealing tape (such as
3” wide 3M 8777) over the interior
roof-seams between the coil and
blower/filter sections, to prevent
any sealant drips from entering the
unit.
3. Firmly apply removable tape
(painters tape) along the blower/
filter roof flange (Figure 14), to help
prevent any sealant drips.
FIGURE 12: DOG EARRING INSTRUCTIONS
FIGURE 13: EMSEAL BACKING PLACEMENT
DOGEARED BACKING
TOP VIEW SIDE VIEW TOP VIEW BOTTOM VIEW
SIDE VIEWTOP VIEW
BACKING
EMSEAL
EMSEAL
ENDDAM
COIL
SECTION
COIL ROOF
FILTER/
BLOWER ROOF
FILTER/
BLOWER ROOF
~1.25
~0.25”
FIGURE 14: REMOVABLE TAPE PLACEMENT
SIDE VIEWTOP VIEW
PAINTER’S TAPE
COIL
SECTION
COIL ROOF
FILTER/
BLOWER ROOF
FILTER/
BLOWER ROOF

GRW
Installation
12 GRW - Manual |SolutionAirGroup.com
4. Seal and adhere Emseal into roof
seam.
a) Ensure the Emseal has
completely expanded into the
unit split.
b) Apply a weather resistant
polyurethane adhesive (such
as 3M 550) around all edges of
the Emseal end-pieces (Figure
15). Tool sealant along the top
and side to be smooth/flush
with adjacent pieces.
c) Repeat for each Emseal end-
piece.
5. Inspect the blower/filter roof
flange.
a) Caulk any gaps/cracks/
holes with weather-resistant
polyurethane adhesive sealant
(such as 3M 550) on the split-
side, inspection points (Figure
16). Best applied with finger
while wearing disposable
gloves.
b) Ensure Emseal is fully
expanded along the bottom
and sides of the roof-seam. If
not, please contact SolutionAir
engineering for further
instructions.
6. Apply bottom of seam with
weather-resistant polyurethane
adhesive sealant (such as 3M
550 [with accelerator if ambient
temperature is below 10°C]).
a) Apply a layer of polyurethane
adhesive sealant to a depth of
about ½” the entire length of
the roof-seam, back-filling to
ensure there are no bubbles or
gaps in the sealant (Figure 17).
FIGURE 16: GAP/CRACK VOID FILLING WITH POLYURETHANE ADHESIVE
FIGURE 17: APPLICATION OF BOTTOM LAYER WEATHER RESISTANT POLYURETHANE
ADHESIVE SEALANT
TOP VIEW
CROSS-SECTION
TOP VIEW
CAULKING
COIL ROOF
COIL ROOF
FILTER/
BLOWER ROOF
FILTER/
BLOWER ROOF
EMSEAL
CAULKING APPLICATOR TIP
CROSS
SECTION “A”
3/4” DEEP CAULKING BEAD
FIGURE 15: EMSEAL POLYURETHANE ADHESIVE PLACEMENT
SIDE VIEWTOP VIEW
CAULKING
COIL
SECTION
COIL ROOF
FILTER/
BLOWER ROOF
FILTER/
BLOWER ROOF

GRW
Installation
13
SolutionAirGroup.com |GRW - Manual
FIGURE 18: BACKER ROD PLACEMENT
7. Add a backer-rod (shipped with
unit).
a) Stu a backer rod into the gap,
ensuring no air-gap between
the backer rod and previous
layer of polyurethane adhesive
(by looking for squeeze-
out around backer-rod, for
example) (Figure 18).
NOTE: if using accelerated (fast-curing)
polyurethane sealants, backer-rod
must be added within ~1 minute of
sealant being applied.
b) Repeat for each roof split
(between the blower/filter and
coil sections).
c) Let cure for at least 1-hour
to ensure sucient skin-over
(longer if very cold/dry).
8. Apply a second layer of weather-
resistant polyurethane adhesive
sealant (such as 3M 550).
a) Apply a second ½” layer of
polyurethane adhesive sealant
(Figure 19). Back-fill along the
entire length of the roof-seam
to ensure there are no bubbles
or gaps in the sealant, and
there is full coverage over the
backer-rod.
b) Repeat for each roof split
(between the blower/filter and
coil sections).
c) Let cure for at least 1-hour
to ensure sucient skin-over
(longer if very cold/dry).
9. Repeat steps 7 and 8 until roof
split gap is filled to within ½” of
the blower/filler roof flange (likely
between one and three backer-
rods, depending on the unit).
FIGURE 19: APPLICATION OF TOP LAYER WEATHER RESISTANT POLYURETHANE
ADHESIVE SEALANT
TOP VIEW
TOP VIEW
CROSS-SECTION
CROSS-SECTION
COIL ROOF
COIL ROOF
FILTER/
BLOWER ROOF
FILTER/
BLOWER ROOF
EMSEAL
EMSEAL
CAULKING APPLICATOR TIP
CROSS
SECTION “A”
CROSS
SECTION “A”
CAULKING BEAD
BACKER ROD

GRW
Installation
14 GRW - Manual |SolutionAirGroup.com
10. Apply a final layer of weather-
resistant self-leveling sealant (such
as NovaLink SL).
a) Fill the last ½” of the roof-split
gap with self-leveling sealant
until it is level with the top of
the blower/filter roof flange.
Back-fill along the entire
length of the roof-seam to
ensure there are no bubbles or
gaps in the sealant. The final
outcome should look similar to
what is shown in Figure 20.
b) Repeat for each roof split gap
(between the blower/filter and
coil sections).
c) Let cure for at least 3-hours
to ensure sucient skin-over
(longer if very cold/dry).
11. Prepare the roof-split covers.
a) Clean the roof-split cover
angles with isopropyl alcohol,
on the side to which the VHB
tape will be applied.
b) Apply 1” VHB tape to the entire
back of the roof-split angles as
shown below.
c) Dog-ear the tape on each end
of the roof-split cover angles
(Figure 21).
d) Prep all roof-split cover angles.
12. Install the roof-split covers.
a) Starting from one side of
the unit, install the roof-
split covers as shown in the
attached drawing (removing
VHB tape backing by pulling
on the previously-prepared
“dog-ears”).
b) Press the roof-split covers
firmly into place, ensuring no
gaps between the tape and
coil section.
c) Caulk the gap between the
roof-split covers and coil
section as shown on the
attached drawing.
FIGURE 20: APPLICATION OF FINAL LAYER WEATHER RESISTANT SELF-LEVELLING
SEALANT
FIGURE 21: ROOF SPLIT ANGLE TAPE PLACEMENT
TOP VIEW
END VIEWSIDE VIEW
CROSS-SECTION
COIL ROOF
FILTER/
BLOWER ROOF
EMSEAL
CAULKING
APPLICATOR TIP
CROSS
SECTION “A”
SELFLEVELING SEALANT BEAD
DOGEARED TAPE
BACKING

GRW
Installation
15
SolutionAirGroup.com |GRW - Manual
Installation Checklist
The following checklist is a summary of all the steps necessary for a successful start-up. This is not intended to replace the
detailed information in the applicable sections of this manual.
General Installation Date Completed Signed
Inspect unit for freight damage or missing items on the Bill of Lading.
Confirm the installation location meets the necessary clearances.
Assemble, square, and level the roof curb if required.
Install ductwork and attach to curb (for units with bottom supply/return).
Install pitch pocket for electrical supply if required.
Set unit on curb or housekeeping pad.
Ensure unit is level.
Seal, bolt, and cap all split joints as required.
Remove shipping hold downs, shipping braces etc. from unit.
Check all fan isolators for proper adjustment and operation.
Install filters as required.
Electrical Connections
Confirm that main electrical supply matches the name plate requirements.
Inspect control cabinets and tighten any loose connections.
Provide a disconnect if one is not factory supplied.
Connect power to factory or field-supplied disconnect.
Properly ground the unit.
Interlock unit to exhaust system
Control Wiring Connections
Complete controls wiring as per the wiring diagrams.
DX Coils & Condensing Sections
Visual inspections for damaged coils, condenser fan guards and condenser fans.

GRW
Maintenance
16 GRW - Manual |SolutionAirGroup.com
WARNING
Hazardous Service Procedures
During installation, testing, servicing and
troubleshooting of this product it may be necessary
to work with live electrical components and moving
mechanical components. Have a qualified technician
who has been properly trained in handling live
electrical components perform these tasks. Failure to
follow all electrical safety precautions when exposed
to like electrical and mechanical components could
result in death or serious injury.
Regular maintenance is the best way to avoid untimely
and expensive repairs, and it extends the useful life of
the equipment. Maintenance should only be performed
by qualified service personnel familiar with air-handling
equipment and the local codes and requirements.
Filters
It is important to replace filters with the same eciency
filters as used when the air balance is done. Filters with
dierent eciencies may cause a change in airflow.
A regular filter maintenance schedule should be set-up
and followed. The controller (if equipped with this option)
allows the user to set the run hours between filter changes
and the controller will notify the user when the desired
interval has been reached.
The filters are located close to the fans; therefore, it is
recommended that the unit be shut down while the filters
are being changed.
When replacing the filters, inspect the louvers and clean if
necessary.
Fan and Motor Assembly
The fan/motor access panel should only be opened if the
power has been shut o and locked o for the unit.
Review the blower service label on the blower for the
recommended service frequency. The controller (if
equipped with this option) allows the user to set up blower
service notifications when a desired interval has been
reached.
Blower service includes:
1. Greasing the bearings on the fan as well as the on the
blower motor, as required.
The controller (if equipped with this option) allows the user
to set the run hours for belt replacement and the controller
will notify the user when the desired interval has been
reached.
Service and Warranty Procedure
Replacement Parts
Replacement parts can be obtained from SolutionAir at
When contacting SolutionAir for replacement parts, refer to
the model number and serial number on the name plate.
Warranty Parts
See limited warranty below for what is covered. Contact
797-0760 for warranty parts instructions. Please have the
unit model and serial numbers available. The warranty part
may need to be returned to SolutionAir to obtain a new
warranty part. SolutionAir reserves the right to repair or
replace a part under warranty.

GRW
Maintenance
17
SolutionAirGroup.com |GRW - Manual
Maintenance Checklist
General Maintenance Quarterly Annually
Inspect inside of unit for water leaks, foreign material etc. X
Clean or replace filters with equivalent to those supplied by manufacturer. X
Check cooling device drain pans and traps for cleanliness and blockage – ensure chemical cleaner is
compatible with aluminum. X
Check all dampers and damper actuators, adjust and tighten as required. X
Check cooling coils for cleanliness and clean as necessary. X
Inspect for worn compressor contactors annually and replace every 5 years X
Remove and lubricate stainless steel bolts X
Blower/Fan Maintenance
Check all bearings and lubricate as necessary. X
Inspect fan wheel and housing. Clean as necessary. X
Electrical Maintenance
Check for loose wire connections in control panel. X
Check motor amp draw against name plate. X
Inspect all contactors to ensure they are clean and making good contact. X
Check all safeties. X

GRW
Maintenance
18 GRW - Manual |SolutionAirGroup.com
Troubleshooting
Symptom Possible Cause Corrective Action
Blower/Fan fails to turn
Blown fuse or tripped circuit breaker. Reset breaker or replace fuse. Check current draw.
Electrical circuit problem. Check supply voltage. Check VFD status. Check control
wiring.
Motor overloaded. Change unit filters if clogged. Reset VFD and check current
draw.
Problem with motor or capacitor. Repair or replace.
Low airflow
Dirty filters. Replace filters.
Supply and/or return static pressure is higher than design. Replace filters if clogged. Reduce pressure-drops within
ductwork. Increase fan size.
Ductwork losses too high. Ensure proper ducting practices are followed. Remove
elbows and/or restrictions near the blower/fan.
Leaks in ductwork. Repair as required.
Excessive noise/vibration
Fan/Wheel rubbing. Align/adjust inlet cone. Check bearing/shaft alignment.
Tighten shaft collars.
Bearings. Lubricate bearings. Replace worn bearings.
Motor-frame dampers loose/ineective. Tighten mounting bolts. Check springs/dampers, replace
as required.
Dampers loose. Check damper blades, if moving in airstream, tighten
linkages as required.
High temperature fault
Low refrigerant charge. Will require mechanical service.
Faulty expansion valve. Service or replace valve motor.
Faulty temperature sensor. Service or replace sensor.
High head
pressure fault
Condenser VFD fault. Contact SolutionAir.
Plugged condenser coil. Clean.
Faulty condenser fans. Service or replace.
Low head
pressure fault
Condenser VFD fault. Contact SolutionAir.
Condenser damper fault. Service or replace.
Low suction
pressure fault
Digital scroll controller fault. Contact SolutionAir.
Plugged air filters or dirty evaporator coil. Clean.
Faulty blower motor. Service or replace motor.
Faulty electronic expansion valve. Service or replace valve motor.
Low refrigerant charge. Will require mechanical service
Controller fault/error Problem with controller/software. Contact SolutionAir. Describe error number.
SolutionAir Mechanical Support:
1-866-797-0760
Table of contents
Popular Control Unit manuals by other brands
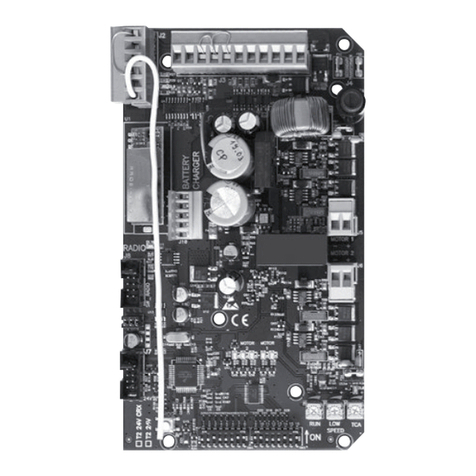
Vimar
Vimar ELVOX RS12 Installation and operation manual

Zator
Zator MZL100 User and maintenance manual
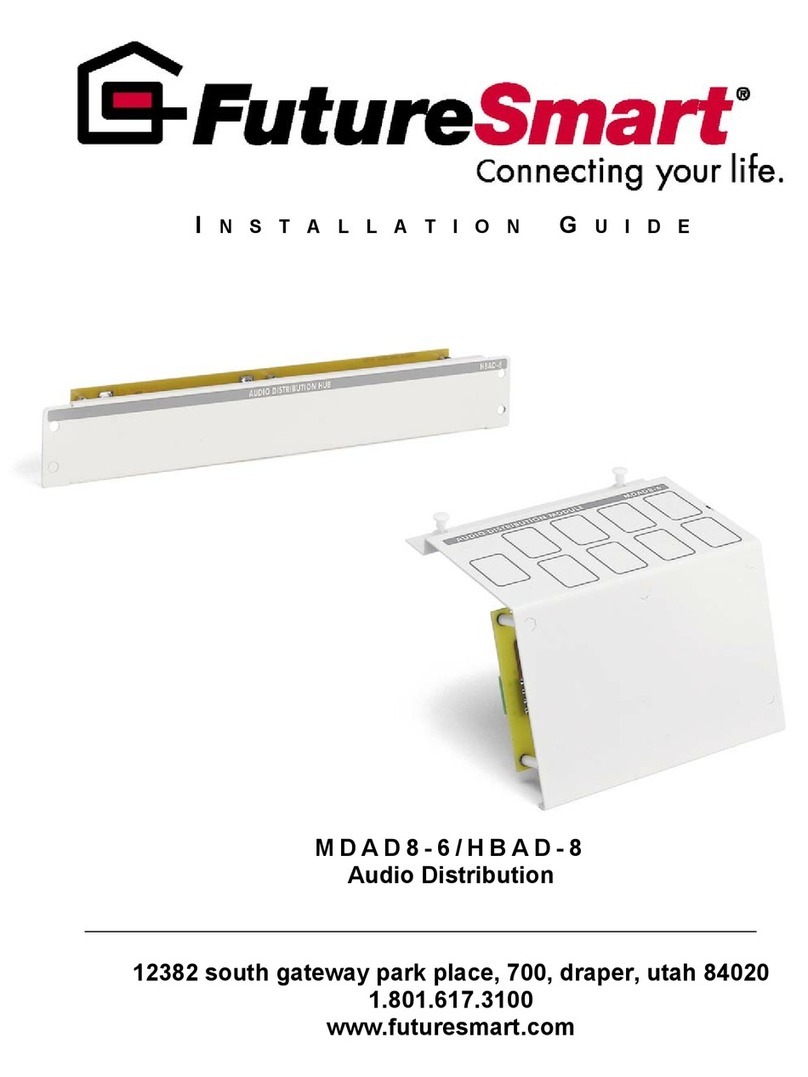
FutureSmart
FutureSmart MDAD8-6 installation guide

LGB
LGB 10345 Operating instruction
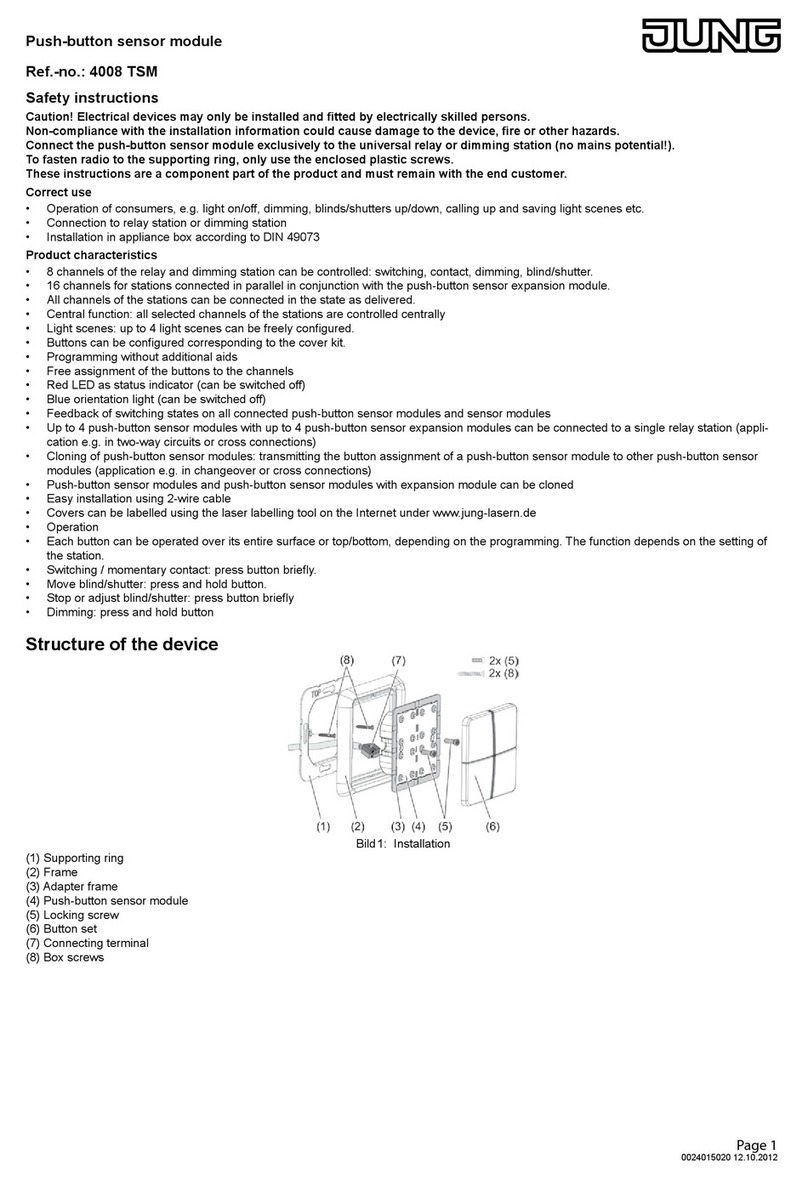
Jung
Jung 4008 TSM Safety instructions
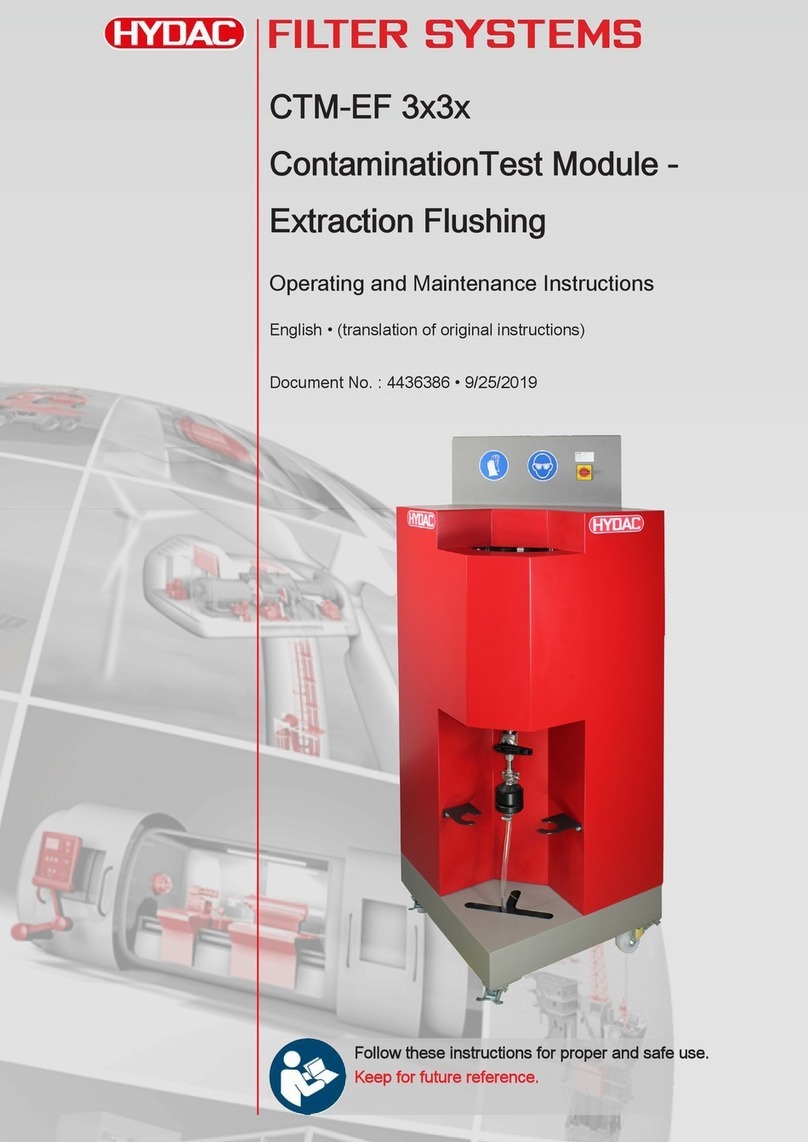
HYDAC FILTER SYSTEMS
HYDAC FILTER SYSTEMS CTM-EF 3 3 Series Operating and maintenance instructions
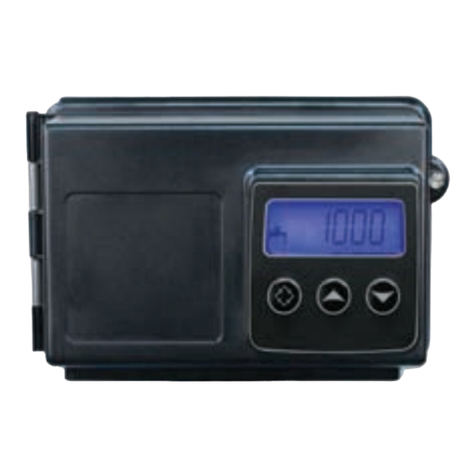
Pentair
Pentair Fleck 2510 ECONOMINDER Service manual
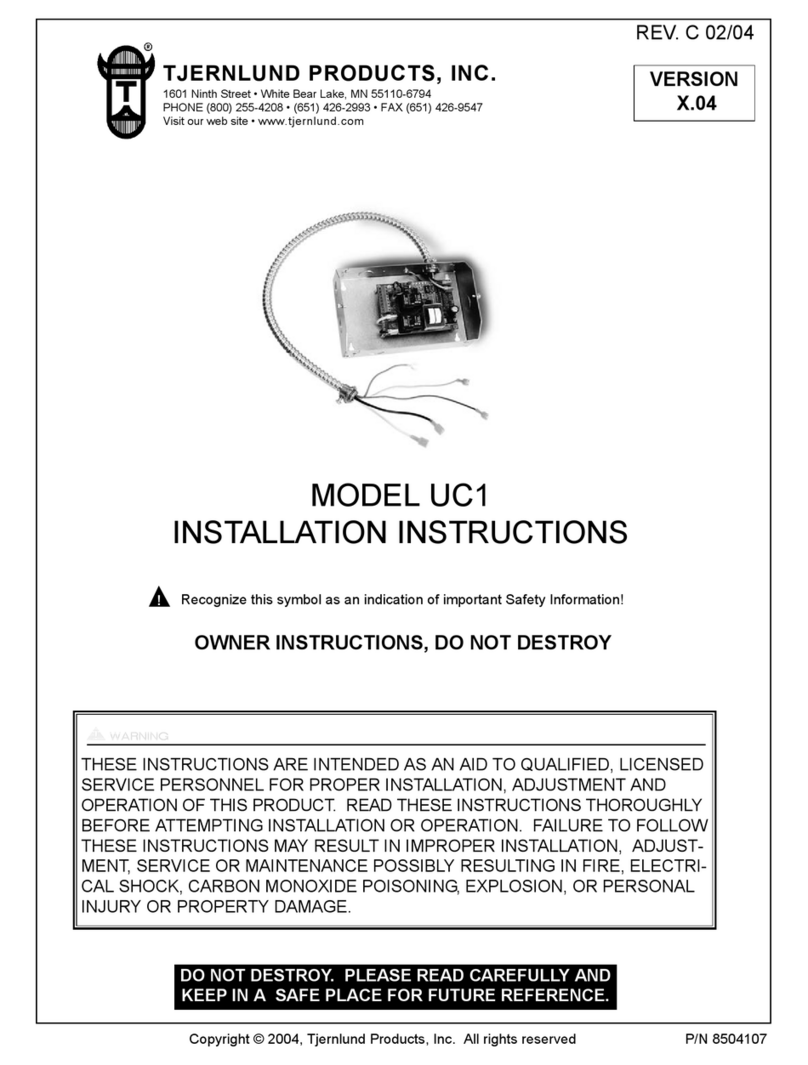
TJERNLUND
TJERNLUND UC1 UNIVERSAL CONTROL (VERSION X.04) 8504107 REV C... installation instructions

Viessmann
Viessmann 5561 Operation manual
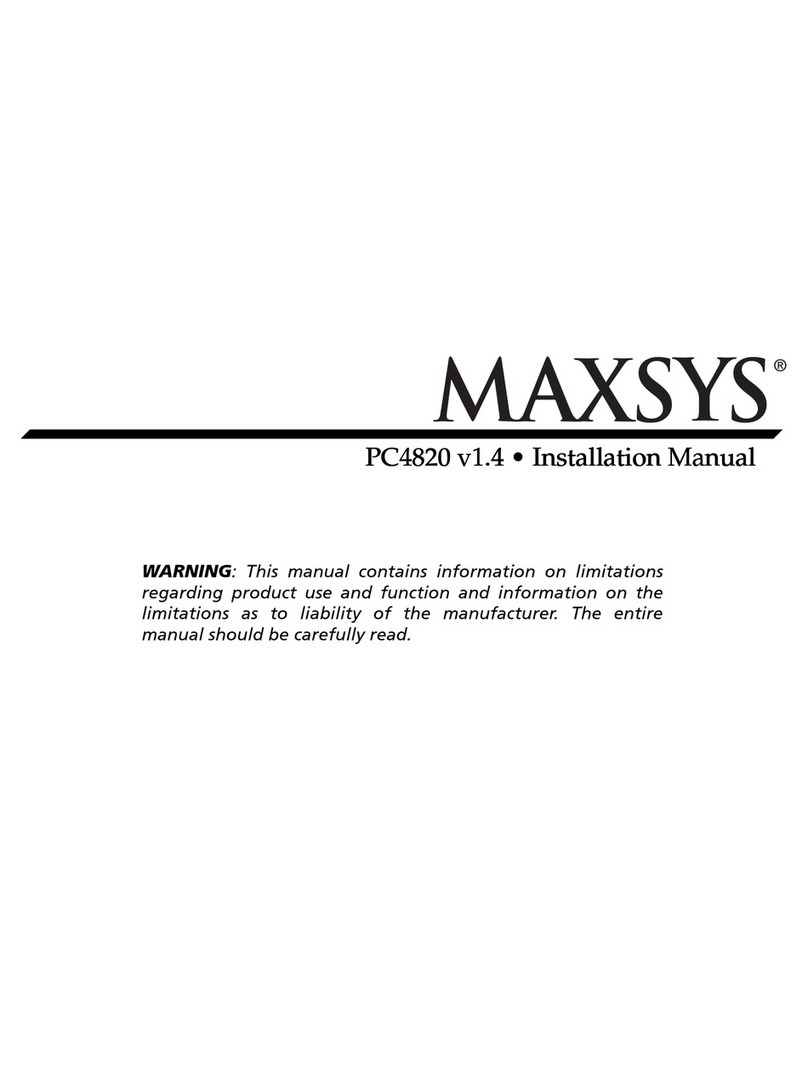
Maxsys
Maxsys PC4820 v1.4 installation manual
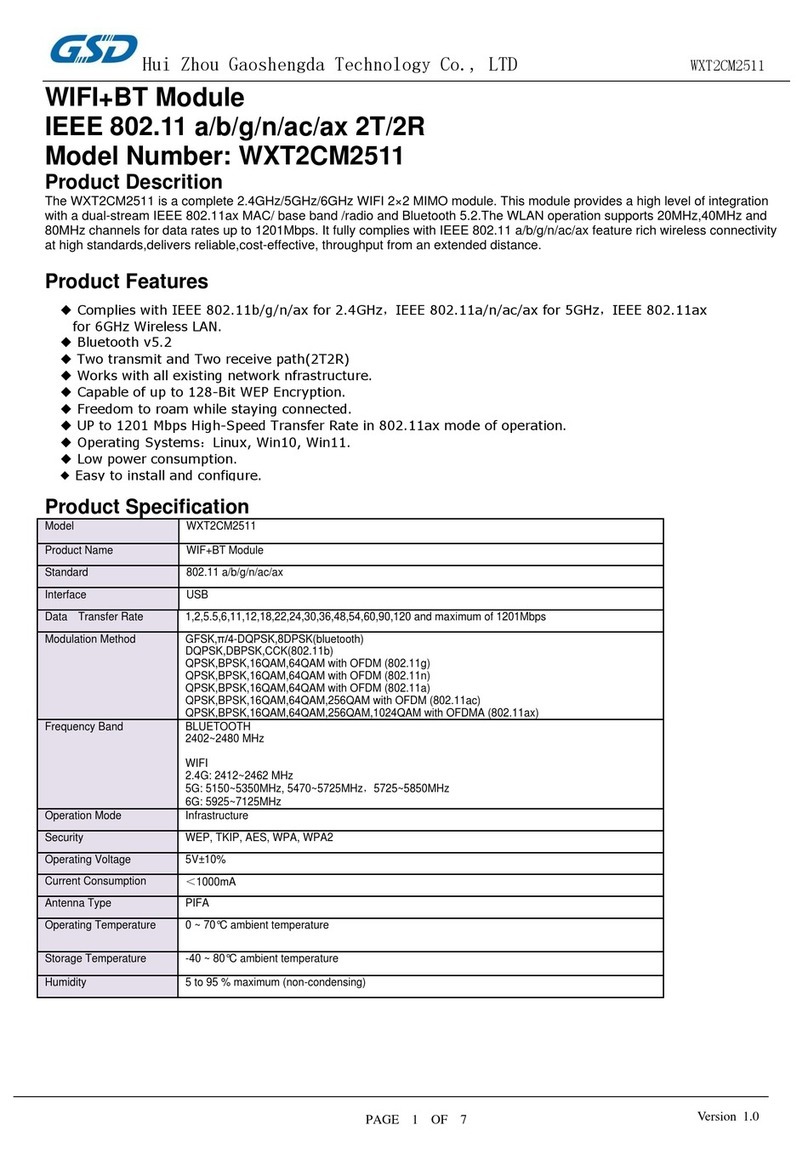
GSD
GSD WXT2CM2511 quick start guide
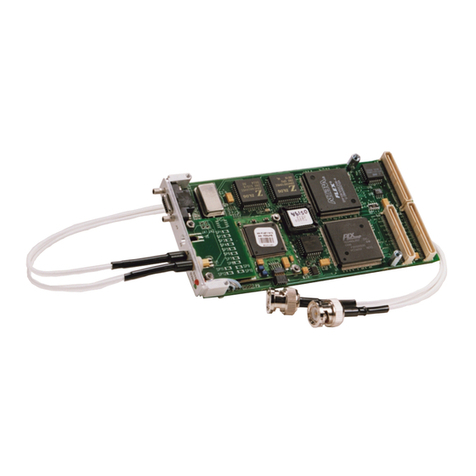
Brandywine
Brandywine PMC-SYNCCLOCK32-UNIV Operation & maintenance manual