Spector Sci-Tech IN-01m User manual

Spector Sci-Tech LLC
IN-01m
METAL STRESS INDICATOR
USER MANUAL
Russia – Ufa – 2020
2

3
CONTENTS
Page
1. Purpose.............................................................................. 4
2. Technical specifications ..................................................... 5
3. Device and principle of operation....................................... 7
4. Safety instructions............................................................ 13
5. Preparing the metal stress indicator for work.................... 13
6. Operating procedure......................................................... 14
6.1. Measuring the mechanical stress of metal of steel parts
and metal structures .......................................................... 14
6.2. Measuring the tension of steel studs and bolts ............ 15
6.3. Charging or replacing the battery................................ 16
7. Maintenance service......................................................... 19
8. Troubleshooting ............................................................... 20
9. Transportation and storage rules....................................... 22
Appendix. Mechanical and magnetic parameters of frequently
arrived Russian grades of structural steels ............................ 23
4
This operating manual allows you to acquaint you with
the device and operation of the IN-01m metal mechanical
stress indicator (hereinafter referred to as the stress indicator)
and sets the rules for its operation, transportation and storage,
compliance with which ensures that it is maintained in
constant readiness for operation.
1. PURPOSE
1.1. The IN-01m metal mechanical stress indicator is
intended for indirect estimation of the value of the metal
mechanical stress of a local section of a steel product or a
metal structure made of structural steel by the value of the
field strength of the residual magnetization of the metal.
1.2. The stress indicator can also be used to measure
the tightening force of steel studs and bolts of housing
equipment.
1.3. The stress indicator can be used in field, workshop
and laboratory conditions.
1.4. Sources of electromagnetic industrial interference
must be removed from the stress indicator at a distance of at
least 3 m.
1.5. Degree of protection against penetration of solids
and water for the stress indicator IP41 according to GOST
14254-80.
1.6. Display of measurement results are digital in units
of the measured value of the field strength of the residual
magnetization of the metal (mT), or the mechanical stress of
the metal (MPa).
1.7. Indication of readouts is liquid crystal
alphanumeric display with backlight for working in conditions
the natural environment lighting is not enough.

5
1.8. According to the operating conditions, the stress
indicator belongs to the type of climatic version of UHL 3.1
according to GOST 15150-69 and can work steadily when:
- ambient temperature from minus 20ºC to plus 70ºC,
- relative humidity up to 98 % at +25ºC,
- atmospheric pressure from 84 kPa to 106.7 kPa.
2. TECHNICAL SPECIFICATIONS
2.1. The range of measurement of the field strength of
the residual magnetization of the metal, mT: - from 0 to 20.00
2.2. Measuring range of mechanical stress of metal of
steel products, metal structures, MPa: - from 0 to σB
where σB is the ultimate strength of the metal.
2.3. The limit of the allowed basic error in measuring
the mechanical stress of the metal of a steel product or metal
structure is determined by the formula:
0.5 + 0.05 σi (2.1)
where σi is the stress indicator readout in MPa.
2.4. The metal stress indicator is powered by a PP3
element with nominal electric voltage of 9V.
2.5. Electric current consumed from a freshly charged
PP3 element, mA:
- when working without the display backlight - 7 ± 0.5
- when working with the display backlight - 16 ± 0.5
2.6. Operating time of stress indicator when powered
from freshly charged element PP3, in hours, at least: - 20
6
2.7. Time to set the metal stress indicator's operating
mode, s, not more than: - 10
2.8. Time of one measurement, s, not more than: - 5
2.9. Time of continuous operation of the stress
indicator, h, not less than: - 16
2.10. Battery charge time, minutes, not more: - 80
2.11. The stress indicator has a memory card with a
capacity of more than 60000 measurements.
2.12. The stress indicator has a standard output for
transmitting measured information to a personal computer via
a mini-USB connector.
2.13. Overall dimensions, mm, not more than:
- Electronic unit (length × width × thickness)
- 136×72×28
- Sensor (diameter × length) - 20×15
- Sensor cable length -950±50
- Magnetizing device (diameter × length) - 20×190
2.14. Weight, g:
- Electronic unit with battery - 200
- Sensor with cable - 40
- Magnetizing device - 300
2.15. Average recovery time, h: - 5
2.16. Full average service life, years: - 10
2.17. Established service life, years: - 2

7
3. DEVICE AND PRINCIPLE OF OPERATION
3.1. The principle of operation of the metal stress
indicator is based on the measurement of the magnetic field
strength over the surface of the residual magnetized area of the
metal (the field strength of the residual magnetization of the
metal).
3.2. The block diagram of the stress indicator is shown
in Fig.3.1.
Fig.3.1. Block diagram of IN-01m the metal stress indicator
1 – magnetizing device, 2 – integrated Hall effect
sensor chip, 3 – pulse voltage stabilizer, 4 – scaling amplifier
combined with a low-pass filter, 5 – threshold indication unit,
6 – microcontroller, 7 – memory card, 8 – alphanumeric liquid
crystal display.
The stress indicator works as follows. Magnetization of
the metal of a steel product, metal structure is carried out by
the magnetic field of a single-pole magnetizing device 1.
The Sensor with the integrated chip of the Hall effect
sensor 2 is powered by a constant electric current from a
stabilized pulse voltage source 3. Voltage from the output of
the Hall effect sensor 2 via a scale amplifier combined with a
4 6
7
5 3
2
1
8
8
low-pass filter 4 to the input of the signal level exceeding light
indication unit 5 and the input of the analog-to-digital
converter of the microprocessor controller.
To detach from the influence of temperature changes
the amplifier 4 has an automatic gain control unit controlled by
an electrical signal coming from the output of the temperature
sensor, which is located inside the housing of the Hall sensor
integrated circuit 2.
The voltage from the output of the scale amplifier 4 is
supplied to the comparator of the light indication unit 5 for
exceeding the signal level corresponding to the metal yield
point, and the input of the analog-to-digital converter of the
microprocessor controller 6.
One of the outputs of the microprocessor controller 6 is
connected to the electronic memory card 7, the other output of
the microprocessor controller 6 is connected to the input of the
alphanumeric liquid crystal display 8.
3.3. The appearance of the stress indicator with a
Sensor and a magnetizing unit is shown in Fig.3.2.
Fig.3.2. Appearance of IN-01m the metal stress indicator
1 – magnetizing unit, 2 – electronic unit, 3 – sensor.
1
2
3

9
3.3.1. The stress indicator consists of a magnetizing
device 1, an electronic unit 2, and a sensor 3 connected to the
electronic unit via a connector.
3.3.2. On the front panel of the electronic unit, there is
a digital liquid crystal display 4, a power button 5, a button for
turning on the device's screen backlight 6, a button for
recording the measurement in memory 7, and a button for
displaying the current date and time 8 (Fig.3.3).
3.3.3. The battery cover is located on the back of the
electronic unit housing. To remove the battery from the battery
compartment, press the battery cover slightly and slide it
down.
3.3.4. In the upper part of the electronic unit housing,
there is a panel of connectors (Fig.3.3).
3.3.4.1. Connector 9 is used for connecting to the
electronic unit of the Sensor.
3.3.4.2. Connector 10 is used for placing a memory
card (flash card) in the electronic block.
3.3.4.3. The mini-USB 11 connector is used for
transmitting measured data via a cable to a personal computer
and receiving service information from the computer.
3.3.4.4. Connector 12 is used to connect the charger's
network adapter to the electronic unit for recharging the
battery (battery).
3.4. The purpose of the controls of stress indicator
3.4.1. The liquid crystal display 4 is used to display
information during the operation of the stress indicator.
3.4.2. Button 5 is used to turn on the electric power of
the stress indicator.
When you turn on button 5 information about the type
of stress indicator appears on its screen for a short time and its
serial number (Fig.3.4 a).
10
Fig.3.3. Location of controls and connectors of the
electronic unit of IN-01m the metal stress indicator
4 – alphanumeric liquid crystal display, 5 – power
button, 6 – screen backlight button, 7 – button to perform
recording measurements in memory, 8 – button for displaying
the date and time, 9 – sensor connector, 10 – memory card
slot, 11 – mini-USB connector, 12 – connector for charger
network adapter.
After setting the measurement mode, the stress
indicator screen displays a digital indication of the output
signal of the sensor (mT or MPa) the battery charge level of
the stress indicator in % , and its ready state (Fig.3.4 b).
4
5 6 7 8
9
10
11 12

11
(a) (b)
Fig.3.4. Displaying information on the IN-01m stress
indicator screen when the power is turned on (a) and after the
measurement mode is set (b)
3.4.3. Button 6 is used to turn on the stress indicator
screen backlight. When you turn on button 6, the screen is
illuminated with additional light to improve the display of
digital stress indicator readouts.
3.4.4. Button 7 is used to save measurements to the
electronic memory of the stress indicator. When the button 7 is
turned on or off, the current transmitter reading displayed on
the screen is recorded in the stress indicator memory.
3.4.5. When connecting a cable connected to the USB
port of a personal computer to the mini-USB 11 connector,
information about establishing a connection with the personal
computer appears on the stress indicator screen (Fig. 3.5).
Fig.3.5. Displaying information on the IN-01m stress
indicator screen when connected to a personal computer
Using of the IN-01m Connect software application pre-
installed on a personal computer, the measured information
from the stress indicator's electronic memory is transmitted
over a cable and stored in the personal computer's memory.
3.4.6. Button 8 displays the current date and time of
stress indicator on the screen.
12
3.5. Magnetizing unit
3.5.1. The magnetizing unit of the stress indicator is
used for magnetizing the local metal section of a steel product
or metal structure with a constant magnetic field, the intensity
vector of which is directed perpendicular to the metal surface.
3.5.2. The magnetizing device is non-volatile, single-
pole, rod type. It uses permanent magnets made from rare earth
metals.
3.5.3. The pole of the magnetizing device is protected
by an overlay to ensure convenience in the process, the handle
of the magnetizing device is provided with a strap.
3.6. Sensor
3.6.1. The stress indicator sensor is designed to
measure the field strength of the residual magnetization of
metal over the surface of a local section of a steel product or
metal structure.
3.6.2. The sensor contains a precision integrated Hall
Effect sensor chip and a precision integrated temperature
sensor chip with an analog signal output, which are located in
a single housing.
3.6.3. The Hall sensor plane is located in the center of
the transducer housing parallel to the working surface at a
distance of 0.5 mm from it.
3.6.4. To measure the field strength of the residual
magnetization of the metal, the center of the working surface
of the stress indicator sensor is set in the middle of the residual
magnetized area of the metal.

13
4. SAFETY INSTRUCTIONS
4.1. Persons who have studied sections 2-5 of this
operating manual, as well as those who have received
instructions on safety and fire safety when working with
electrical installations, are allowed to operate, maintain and
repair the stress indicator.
4.2. Replacement of elements of the electrical diagram
of the stress indicator at the setup stage should be carried out
when the power supply voltage is switched off.
4.3. When working with the stress indicator, the
requirements of the Rules of technical operation of electrical
installations of PTE-84 consumers and Safety rules for the
operation of electrical installations of PTB-84 consumers must
be met.
5. PREPARING THE METAL STRESS
INDICATOR FOR WORK
Preparation for work includes preparation of the stress
indicator, the magnetizing device and preparation of the
inspected metal surface of a steel product, a metal structure.
5.1. Before turning on the stress indicator after
transporting it in cold weather, it under normal conditions of
use for at least 2 hours.
5.1.2. Attach to the battery compartment freshly
charged battery type PP3, with respect to the polarity of the
contacts.
5.1.3. Connect the sensor to the electronic unit using the
connector by inserting the cable part of the connector into the
instrument part of the connector until it stops.
5.1.4. Turn on the stress indicator by pressing the
power button. In this case, the stress indicator screen should
light up, where the service information first appears, then the
value of the measured signal of the Sensor is set (see section
3.4.2 of current document).
14
5.1.5. In low light conditions, to improve the visibility
of the stress indicator screen, turn on the screen backlight
button.
5.2. Preparation of the magnetizing unit consists in
external inspection and cleaning of the surface of the magnetic
pole from stuck metal particles and dirt. To do this, use a rag.
5.3. Preparation of the controlled metal surface of a
steel product or metal structure consists in pre-cleaning it from
insulation, dirt, oil, and stuck metal particles. To do this, use
an appropriate hand or electric tool, rag, sandpaper, or file.
6. OPERATING PROCEDURE
6.1. Measuring the mechanical stress of metal of
steel parts and metal structures
Measurement of the mechanical stress of the metal of a
steel product or metal structure consists in preliminary
magnetization of a local section of metal by a constant
magnetic field of the magnetizing device and measurement of
the field strength of the residual magnetization over this
surface.
6.1.1. Install the pole of the magnetizing device on the
local area of the metal surface of the steel product, metal
structure and smoothly remove it from the magnetized surface
in the vertical direction.
Note: lateral displacement of the magnetic pole of the
magnetizing device is not allowed to reduce the accuracy of
measurements.
If the magnetic pole is allowed to shift laterally on the
metal surface when the magnetizing device is removed, repeat
the magnetization operation in accordance with step 6.1.1.
6.1.2. Install the stress indicator sensor in the middle of
the magnetized area of the metal surface.

15
6.1.3. To measure the field strength of the residual
magnetization on the surface (in mT) and to assess the value of
the mechanical stress of the metal based on the dependence of
the field strength of the residual magnetization on the
magnitude of mechanical stress of the metal (see the
Appendix), appropriate to the grade of steel.
If the calibration constants programmed into the
memory of the stress indicator in manufacture, the display on
the stress indicator screen will correspond to the value of the
mechanical stress of the metal for this steel grade (in MPa).
6.1.4. To measure the mechanical stress of the metal on
another section of the steel product, the metal structure should
repeat the operation according to steps 6.1.1-6.1.3.
6.2. Measuring the tension of steel studs and bolts
Measuring the tension of steel studs and bolts of
threaded connections consists in pre-magnetizing their end
surface with a constant magnetic field of the magnetizing
device and measuring the field strength of the residual
magnetization of the metal above it.
6.2.1. Install the magnetizing device on the end surface
of the steel stud or bolt and smoothly remove it from the
magnetized surface in a perpendicular direction.
Note: lateral displacement of the magnetic pole of the
magnetizing device is not allowed to reduce the accuracy of
measurements.
If the magnetic pole is allowed to shift laterally on the
metal surface when the magnetizing device is removed, repeat
the magnetization operation according to step 6.2.1.
6.2.2. Install the stress indicator sensor in the middle
area of the magnetized end surface of the steel stud or bolt.
6.2.3. To measure the field strength of the residual
magnetization on the surface (in mT) and to assess the value of
the mechanical stress of the metal (torque) on the basis of
dependence of the field strength of the residual magnetization
16
on the magnitude of mechanical stress of the metal (see the
Appendix) for the corresponding grades of steel studs, bolts.
6.2.4. When checking a large number of steel studs,
bolts located on a separate unit of the body product, the
operations according to steps 6.2.1-6.2.3 should be performed
for each steel stud, bolt.
Note: uniformity of the tightening force of all steel
studs, bolts is achieved when the stress indicator readouts on
all controlled studs, bolts have approximately the same value
within the measurement error.
6.3. Charging or replacing the battery
6.3.1. As the resource of the PP3 type battery is used
up, the stress indicator screen in the zone indicating the battery
charge level (see Fig.3.4 b) set the current charging level in %.
6.3.2. When the battery charge level decreases relative
to the allowed threshold value, the stress indicator screen will
display a flashing message Recharge battery! (Fig.6.1).
Fig.6.1. Message on IN-01m the stress indicator about
the need to charge or replace the battery
When you reach that level you need to charge the
battery, which in the electronic connector block to connect the
power adapter cable of the charger and connect it to the
network voltage of 220V, 50 Hz.
Fig.6.2. Indication of the battery charge process on the
IN-01m stress indicator screen

17
6.3.3. If it is necessary to completely replace the
battery, turn off the power of, open the battery cover of the
electronic unit and remove the used PP3 battery.
Insert a freshly charged battery, observing the polarity
of the contacts, and close the battery cover of metal stress
indicator.
6.4. Working with metal stress indicator memory
6.4.1. The stress indicator is equipped with a memory
card to quickly save the results of a large number of
measurements. The measured values of the output signal of the
Sensor are sequentially recorded in the electronic memory of
the stress indicator.
6.4.2. To record the measured signal reading displayed
on the screen into the stress indicator memory is switched on
and off once (see Fig.3.3). In the process of recording the
stress indicator readings in electronic memory, the stress
indicator screen displays the inscription Writing.
The measured data is saved to the built-in memory card
of the IN-01m metal mechanical stress indicator in files of the
DDMMYYYY type CSV, where DD is the current day, MM is
the month, and YYYY is the year.
The CSV (Comma Separated Values) format is a
common standard supported by MS Excel and compatible with
any text editor.
Structure of IN-01m stress indicator data files Table 6.1
Beginning of file
Measurement time 1 Measurement 1
Measurement time 2 Measurement 2
… …
Measurement time N Measurement N
End of file
18
The data file represents sequentially recorded
measurement results (see table 6.1).
6.4.3. Transfer of data recorded in the stress indicator's
electronic memory to a personal computer.
6.4.3.1. Turn on IN-01m the metal stress indicator
power with button 5.
6.4.3.2. Turn on the personal computer and launch the
pre-installed software application IN-01m.
6.4.3.3. Insert a connecting cable into the mini-USB
connector of the stress indicator's electronic unit and connect it
to the corresponding connector of the personal computer. A
message appears on the stress indicator screen about
establishing a communication channel with the personal
computer via the mini-USB connector of the electronic unit of
the stress indicator (Fig.6.3).
Fig.6.3. Indication of data exchange of the IN-01m
metal stress indicator with a personal computer via USB
6.4.3.4. In the IN-01m CONNECT software
application, open the File menu and select Receive data. After
receiving information from the electronic memory of the stress
indicator, a graph of the distribution of the measured values of
the Sensor in the Cartesian coordinate system appears on the
screen of the personal computer.
6.4.3.5. To select the type of graphical display of the
measured values of the stress indicator and to save them on a
personal computer, use the corresponding menu items of the
IN-01m CONNECT software application, which are described
in the program's user guide.
6.4.3.6. To stop transmitting data from the metal
mechanical stress indicator to the personal computer,

19
disconnect the cable from the mini-USB connector of the
electronic indicator unit.
7. MAINTENANCE SERVICE
7.1. Maintenance of the stress indicator is performed by
technical personnel from the departments of the control and
measuring devices service (KIP) or similar.
7.2. Maintenance of the stress indicator consists of a
preventive inspection, scheduled maintenance, and routine
maintenance.
7.3. The frequency of planned inspections is set
depending on the production conditions, but at least once a
month. During a routine inspection, the fastening of all
components, the condition of controls and paint coatings, and
the integrity of the measuring transducer are checked.
7.4. Scheduled maintenance is performed after the
warranty period expires and then at least once a year.
Repairs include visual inspection of the stress indicator,
inspection of the internal state of the installation, verification
of the reliability of the contact connections, and removal of
dust and dirt. At the same time, all types of work are
performed, the need for which was identified during the
preventive inspection of the stress indicator. In the event of
failure of the electronic components of the stress indicator,
they must be replaced.
7.5. Current repairs are made during the operation of
the stress indicator. At the same time, faults detected during
routine inspection are eliminated by replacing or restoring
individual parts of the stress indicator (replacing radio
elements, restoring broken electrical connections, etc.).
20
8. TROUBLESHOOTING
8.1. Possible malfunctions and ways to fix them are
shown in table 8.1.
Table 8.1.
Possible
malfunction Probable cause Remedy
When the power is
turned on, there is
no information on
the stress indicator
screen
1. The battery is
low.
2. Poor contact in
the power supply
circuit.
Charge the
battery.
Replace the
battery.
Clean the contacts
in the battery
compartment.
When metal stress
indicator is powered
on, the message
"FAT32!"
The file system
of the memory
card is different
Remove the
memory card and
format its file
system on the
computer.
When the power is
turned on, the
message "SD error"
Appears on the
screen if memory
card is Faulty
Replace the
memory card.
When the power is
turned on, "No card"
Appears on the
screen if no card
presented inside
of the slot 10
Insert a memory
card into slot 10.
When you click the
record measurement
button, the message
"Error!" appears
Faulty memory
card
Replace the
memory card.

21
Possible
malfunction Probable cause Remedy
When installing the
sensor on a metal
surface, stress
indicator reading
does not change
There is a break
in the connection
of the cable to the
sensor.
The sensor is
faulty.
Find the place of
the break and, if
possible, fix it.
Replace the
sensor.
22
9. TRANSPORTATION AND STORAGE RULES
9.1. The stress indicator must be transported in a
package with the battery disconnected from the electronic unit.
9.2. Transportation of the packed stress indicator can be
performed in closed railway cars or containers, on motor
vehicles, as well as in heated compartments of aircraft.
9.3. The packed metal stress indicator must be fixed in
vehicles, and when using open vehicles, in case of short-term
transportation, it must be protected from the effects of
precipitation and water.
9.4. Placement and attachment of the packed stress
indicator in vehicles must ensure their stable position, exclude
the possibility of collision with other objects, as well as against
the walls of the vehicle.
9.5. Conditions of transportation:
- temperature, ºC - from minus 30 to plus 80
- relative humidity at a temperature of +35ºC, % - 95
9.6. The stress indicator in the transport package can
withstand shaking with an acceleration of 15 m/s2 at from 10
to 120 beats per minute or 7500 beats with the same
acceleration.
9.7. The packed stress indicator with the battery
disconnected from the electronic unit should be stored on racks
in a dry room in the absence of acid vapors, alkalis and other
aggressive impurities in the air.
9.8. Storage conditions in terms of the impact of
climatic factors should correspond to the requirements of the
Appendix L of GOST 15150-69.
9.9. The location of the stress indicator in storage
should ensure its free movement and access to it.
9.10. If the stress indicator is stored for more than 6
months, it should be released from the transport package and
kept in accordance with the above storage conditions in
consumer packaging.

23
Appendix. Mechanical and magnetic parameters of
frequently arrived Russian grades of structural steels
Table A.1
Нс, A/cm Steel
grade
B,
MPa
Y,
MPa
=0 =Y =B
Ст 3 350 210 1.7 5.0 6.0
09Г2С 470 325 3.0-4.0 7.5-7.8 9.5
17Г1С 520 350 4.0 10 11
Steel 20 420 230 3.8-4.5 8.0-10.5 12.0-13.5
10ХСНД 540 400 4-5 11.0-11.5 12-14.5
Ст Дс 650 400 5-6 8.0-8.5 10-11
Table A.2
Нr, mT Steel
grade
B,
MPa
Y,
MPa
=0 =Y =B
Ст 3 350 210 0.62 1.69 2.0
09Г2С 470 325 1.06-1.38 2.43-2.79 2.98
17Г1С 520 350 1.38 3.12 4.12
Steel 20 420 230 1.32-1.54 2.57-3.25 3.63-4.0
10ХСНД 540 400 1.38-1.7 3.38-3.5 3.63-4.24
Ст Дс 650 400 1.7-2.0 2.57-2.71 3.12-3.38
Accepted designations:
Y – metal yield limit (MPa),
B – the strength limit of the metal (MPa),
Нc – coercive force of the metal (A/cm),
Нr – the field strength of the residual
magnetization of the metal (mT).
Table of contents
Popular Touch Panel manuals by other brands

Philips
Philips DTP100 installation manual
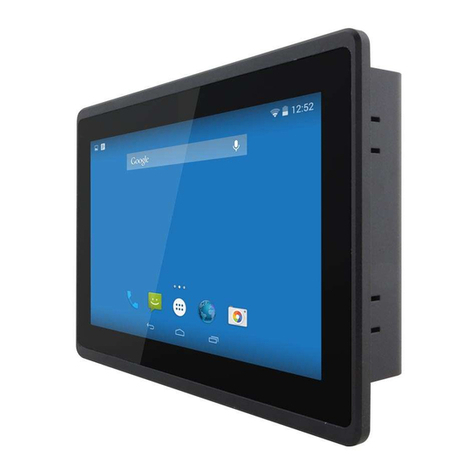
Winmate
Winmate W07FA3S-EHT1 quick start guide
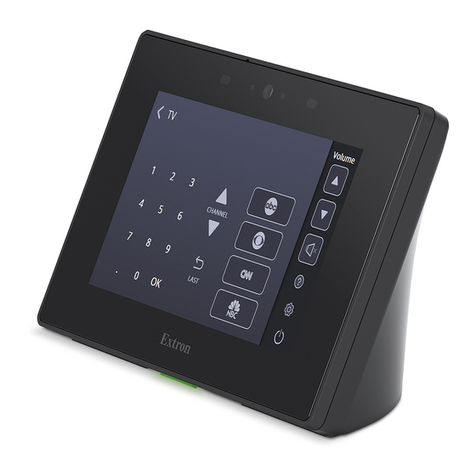
Extron electronics
Extron electronics TLP Pro 725T Setup guide
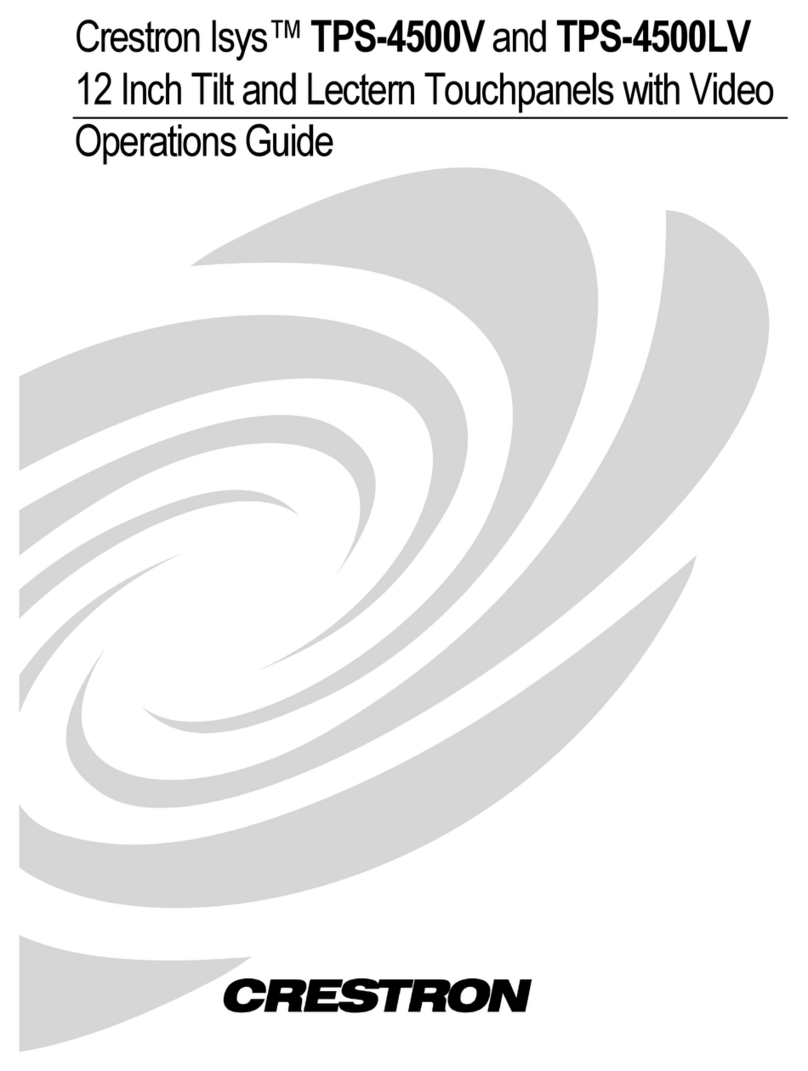
Crestron
Crestron Isys TPS-4500LV Operation guide
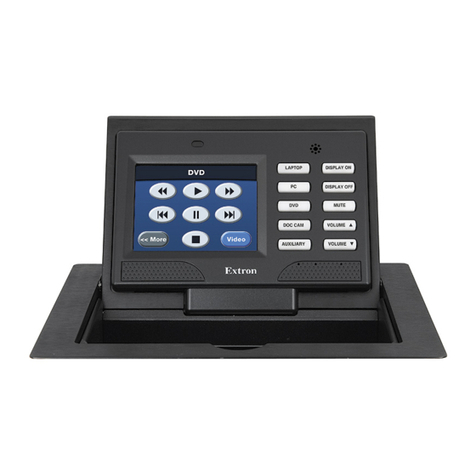
Extron electronics
Extron electronics TouchLink TLP 350CV installation guide
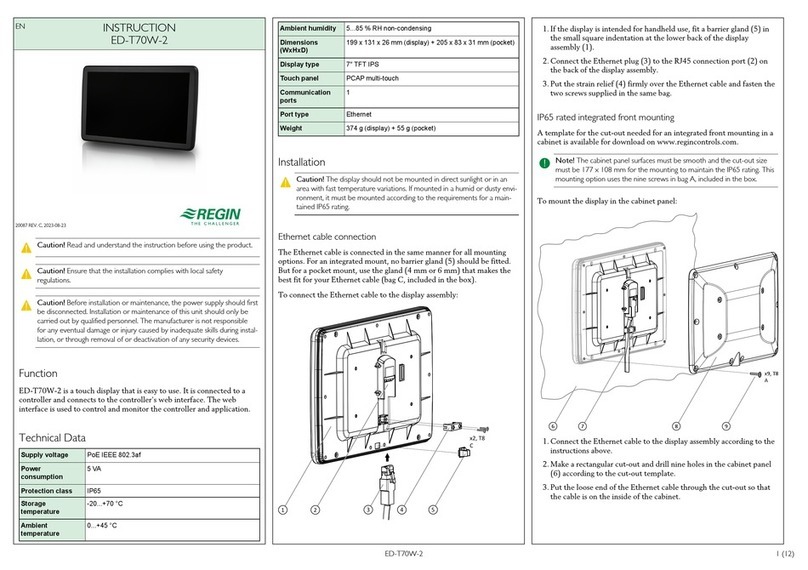
Regin
Regin ED-T70W-2 instructions