Sperian MILLER Vi-Go Operator's manual


2
Table of Contents
1.0 Purpose........................................................................................................................3
2.0 General Requirements, Warnings and Limitations...................................................... 3-4
2.1 General Fall Protection Warnings
2.2 System Warnings and Limitations
3.0 System Requirements..................................................................................................5
4.0 System Diagrams and Description of Components.....................................................6-8
4.1 Vi-GoAUTOMATIC PASS-THROUGH System
4.2 Vi-Go MANUAL PASS-THROUGH System
4.3 System Replacement Parts
5.0 System Installation.......................................................................................................8-14
5.1 Installation of Top Bracket Assembly
5.2 Installation of Cable to Top Bracket Assembly
5.3 Installation of Intermediate Cable Guides
5.4 Installation of Bottom Bracket Assembly
5.5 Installation of Cable and Tensioning Assembly to Bottom Bracket Assembly
5.6 Options for Terminating Cable in the Field
5.7 Optional Vi-GoAnchorage Connector
6.0 System Operation........................................................................................................14
7.0 Training........................................................................................................................14
8.0 Inspection and Maintenance........................................................................................15
Labels.......................................................................................................................... 15
Inspection and Maintenance Log.................................................................................16
Warranty.......................................................................................................................17

3
User Instructions - English
Questions? CALL
1.800.873.5242
It is crucial that the authorized person/user of this fall protection equipment read and understand these instruc-
tions. In addition, it is the employer’s responsibility to ensure that all users are trained in the proper use, inspec-
tion, and maintenance of fall protection equipment. Fall protection training should be an integral part of a compre-
hensive safety program.
Proper use of fall arrest systems can save lives and reduce the potential of serious injuries from a fall. The user
must be aware that forces experienced during the arrest of a fall or prolonged suspension may cause bodily injury.
Consult a physician if there is any question about the user’s ability to use this product. Pregnant women and
minors must not use this product.
2.0 General Requirements, Warnings and Limitations
Thank you for your purchase of Miller Fall Protection equipment. Miller brand products are produced to meet the
highest standards of quality at our ISO 9001:2000 certied facility. Miller Fall Protection equipment will provide
you with years of use when cared for properly.
Thank You
2.1 General Fall Protection Warnings
All warnings and instructions shall be provided to
authorized persons/users. Warnings and instructions
must be read and understood prior to using this
equipment.
All authorized persons/users must reference the
regulations governing occupational safety, as well
as applicable standards (i.e, ANSI or CSA). Refer to
product labeling for information on specic OSHA
regulations, and ANSI and CSA standards met by
this system.
Proper precautions should always be taken to remove
any obstructions, debris, material, or other recognized
hazards from the work area that could cause injuries or
interfere with the operation of the system.
All equipment must be inspected before each use
according to the manufacturer’s instructions.
All persons using this equipment must read, understand and follow all instructions.
Failure to do so may result in serious injury or death. Do not use this equipment
unless you are properly trained.
WARNING
All equipment should be inspected by a qualied person
on a regular basis.
To minimize the potential for accidental disengagement,
a competent person must ensure system compatibility.
Equipment must not be altered in any way. Repairs
must be performed only by the equipment manufacturer,
or persons or entities authorized, in writing, by the
manufacturer.
Any product exhibiting deformities, unusual wear, or
deterioration must be immediately discarded.
Do not use if the unit or any part of the system appears
to be damaged.
Any equipment subject to a fall must be removed from
service.
Vi-Go Vertical Cable Lifeline Systems are innovative climbing and fall arrest systems that provide superior fall
protection for xed ladder applications.
1.0 Purpose

User Instructions - English
4
System Compatibility
Vi-Go Vertical Cable Lifeline Systems are designed for
use with Miller approved components. Substitution or
replacement with non-approved component combina-
tions, sub-systems, or both, may affect or interfere
with the safe function of each other and endanger the
compatibility within the system. This incompatibility
may affect the reliability and safety of the total system.
Vi-Go Systems must be used in conjunction with a
Vi-Go Cable Sleeve with auto-locking carabiner (or
other Miller approved connector) and a Miller full-body
harness equipped with a front attachment point desig-
nated for ladder climbing.
[NOTE: All instructions and warnings provided with
the cable sleeve, connector and harness must be read
and understood before using the equipment.]
System Capacity
A maximum of four users may simultaneously be
connected to a Vi-Go Vertical Cable Lifeline System so
long as the load-bearing capacity of the base structure
is adequate. For Vi-Go Systems using the 10 ft. (3m)
top bracket assembly, the number of users is limited to
two.
The distance between users must not be less than
5-1/4 ft. (1.6m) to ensure that, in the event of a fall,
the person falling will not strike a user below. (Note:
According to ANSI A14.3, only one worker may be on
the system between cable guides.)
Fall Clearance
Ensure that adequate clearance exists in the fall path
to avoid striking a lower level, some other object, or
another user.
2.2 System Warnings and Limitations
Environmental Hazards
Use of this equipment in areas where environmental
hazards exist may require additional precautions to
limit the possibility of injury to the user or damage
to the equipment. Hazards may include, but are not
limited to, extreme temperatures, caustic chemicals,
corrosive environments, high voltage power lines,
explosive or toxic gases, moving machinery, and sharp
edges. Do not expose the equipment to any hazard
which it is not designed to withstand. Consult the
manufacturer in cases of doubt.
• Ensure that the system is free of grease, oil and ice.
• Cable lifeline must be kept clean.
• Use of this system is not suitable when the user
is positioned on an unstable surface, fine-grain
material, or particulate.
The user shall have a rescue plan and the means at
hand to implement it when using this equipment.
Never use fall protection equipment for purposes other
than those for which it was designed. Fall protection
equipment should never be used for towing or hoisting.
Never remove product labels, which include important
warnings and information for the authorized person/user.

5
User Instructions - English
3.0 System Requirements
Before installation of a Vi-Go System, the structure or ladder on which the system is to be afxed must be certied
to be capable of withstanding the potential loads that may be applied in the event of a fall arrest and must meet
the specied ladder requirements.
Ladder Requirements
A ladder must be a xed ladder with rungs having outer diameters between 3/4 inch and 1-1/8 inches. According
to ANSI A14.3, the minimum width of the ladder should be 18 inches from inside rail to inside rail.
A system may be attached to square, diamond or L-shaped (angle iron) rungs so long as the rungs meet the mini-
mum 3/4 inch and maximum 1-1/8 inches outer diameter requirements. A spacer may be required for angle iron
installations. Please contact Miller Technical Services at 800-873-5242 for additional information and installation
assistance.
Top Bracket
Connection loads include system pretension and forces generated by arresting a fall. The load requirements vary
due to number of users on the system and installation to the structure (i.e., number of rung clamp assemblies
used).
For calculation purposes in determining the load each ladder rung must be able to withstand, assume the maxi-
mum load on each bracket is distributed evenly throughout the number of top bracket rung clamp assemblies.
[Example: Based on a single-user system with the top bracket installed with three rung connections, the assumed
load for each rung would be 1,100 lbs. (3,300/3).] An additional top bracket rung clamp assembly can be pur-
chased separately and used to spread the load requirements over four (4) rungs rather than three (3). [Example:
For a system with two (2) users the loads transmitted to each rung is reduced from 1,267 lbs. (3,800/3) to 950 lbs.
(3,800/4).]
Number of Simultaneous Users Maximum Load (lbs.)*
For Vi-Go AUTOMATIC and MANUAL Systems:
1 3,300 lbs.
2 3,800 lbs.
3 4,300 lbs.
4 4,800 lbs.
*The maximum load calculations provide a 2:1 safety factor.
Bottom Bracket
The bottom bracket connection must be capable of supporting a system load of 750 lbs. in the direction of loading.

User Instructions - English
6
4.1 Vi-Go AUTOMATIC PASS-
THROUGH System
4.0 System Diagrams and
Description of Components
4) Automatic Pass-Through Cable Guide
• Holds the cable in position, preventing it from moving ex-
cessively in windy conditions and from coming in contact
with the ladder or structure.
• Accommodates curved structures.
• Automatic pass-through feature allows the Vi-Go Au-
tomatic Pass-Through Cable Sleeve to bypass guide
without manual assistance, offering the user greater
comfort through hands-free trailing, quicker climbing and
descending, and the highest level of safety.
5) Vi-Go Automatic Pass-Through
Cable Sleeve
• Cable sleeve purchased separately. Available with
integral swivel and auto-locking carabiner, with the
carabiner only, or without a connector.
• Stainless steel construction offers corrosion-resistance.
• Quick and easy to install with absolute single-hand
operation.
• Integrated mechanism prevents upside-down installation
of the cable sleeve to the cable.
• Hands-free trailing while climbing and descending.
• Spring-activated mechanisms always move device back
to initial position.
• Dual locking mechanism prevents accidental unlocking
of the cable sleeve from the cable.
• Locks instantly in the event of a fall.
• Built-in shock absorber/fall indicator further reduces fall
arrest forces and provides for ease of inspection.
3) Cable Lifeline
• 3/8” galvanized steel cable lifeline.
1
3
4
5
6
2
1) Top Bracket Assembly
with Inline Shock Absorber
• Inline shock absorber reduces the forces imposed on the
system and structure in the event of a fall.
• May be installed to extend above the ladder to allow
workers to step safely onto the platform without discon-
necting from the lifeline for maximum protection.
• Also available with a 7 ft. (2m) or 10 ft. (3m) top bracket.
6) Bottom Bracket Assembly
with Lifeline Tensioner
• Dual function lifeline tensioner indicates when the lifeline
is properly adjusted and prevents ladder rung deforma-
tion.
2) Quick Link
• Provides a quick and easy connection of the lifeline to
the inline shock absorber.

7
User Instructions - English
4.2 Vi-Go MANUAL PASS-
THROUGH System
1) Top Bracket Assembly
with Inline Shock Absorber
• Inline shock absorber reduces the forces imposed on
the system and structure in the event of a fall.
• May be installed to extend above the ladder to allow
workers to step safely onto the platform without dis-
connecting from the lifeline for maximum protection.
• Also available with a 7 ft. (2m) or 10 ft. (3m) top
bracket.
6) Bottom Bracket Assembly
with Lifeline Tensioner
• Dual function lifeline tensioner indicates when the
lifeline is properly adjusted and prevents ladder rung
deformation.
4) Manual Pass-Through Cable Guide
• Holds the cable in position, securing it away from the
ladder or structure.
• Fully convertible to accommodate low and high wind
conditions.
• Manual pass-through feature requires cable to be
released from the clamping position before the cable
sleeve can pass by it.
5) Vi-Go Manual Pass-Through
Cable Sleeve
• Cable sleeve purchased separately. Available
with integral swivel and auto-locking carabiner,
with the carabiner only, or without a connector.
• Easily attaches to the cable and offers hands-
free trailing operation between intermediate cable
guides.
• Locks instantly in the event of a fall.
3) Cable Lifeline
• 3/8” galvanized steel cable lifeline.
3
4
5
6
1
2
2) Quick Link
• Provides a quick and easy connection of the lifeline
to the inline shock absorber.

User Instructions - English
8
4.3 System Replacement Parts
Part
No. Component Description
TRTB Top Bracket Assembly 5 ft. (1.5m) galvanized steel bracket (1-1/2” x 1-1/2” tube) includes inline shock absorber with shackle, two rung clamp
assemblies (each w/4-hole mounting plate for 1-1/2" tube, two 3/8"-16 x 1-5/8" x 3-1/2" U-bolts, four 3/8" lockwashers, and
four 3/8"-16 hex nut fasteners), and bottom rung clamp assembly (w/3/8"-16 x 1-5/8" x 3-1/2" U-bolt, two 3/8" lockwashers,
two 3/8"-16 hex nut fasteners and two fastener caps).
TRTB-7 7 ft. (2m) Top Bracket
Assembly 7 ft. (2m) galvanized steel bracket (2” x 2” tube) includes inline shock absorber with shackle, two rung clamp assemblies
(each w/4-hole mounting plate for 2" tube, two 3/8"-16 x 1-5/8" x 3-1/2" U-bolts, four 3/8" lockwashers, and four 3/8"-16 hex
nut fasteners), and bottom rung clamp assembly (w/two 3/8"-16 x 4" bolts, two 3/8" at washers, 2-hole mounting plate,
two 3/8" lockwashers, and two 3/8"-16 hex nut fasteners).
TRTB-10 10 ft. (3m) Top Bracket
Assembly 10 ft. (3m) galvanized steel bracket (2” x 2” tube) includes inline shock absorber with shackle, two rung clamp assemblies
(each w/4-hole mounting plate for 2" tube, two 3/8"-16 x 1-5/8" x 3-1/2" U-bolts, four 3/8" lockwashers, and four 3/8"-16 hex
nut fasteners), and bottom rung clamp assembly (w/two 3/8"-16 x 4" bolts, two 3/8" at washers, 2-hole mounting plate,
two 3/8" lockwashers, and two 3/8"-16 hex nut fasteners).
TRRCA Extra Rung ClampAssembly
(for 5 ft. top bracket) Includes 4-hole mounting plate for 1-1/2" tube, two 3/8"-16 x 1-5/8" x 3-1/2" U-bolts, four 3/8" lockwashers, and four 3/8"-
16 hex nut fasteners
TRRCA-10 Extra Rung ClampAssembly
(for 7ft. & 10 ft. top brackets) Includes 4-hole mounting plate for 2" tube, two 3/8"-16 x 1-5/8" x 3-1/2" U-bolts, four 3/8" lockwashers, and four 3/8"-16
hex nut fasteners
TRLL Cable Lifeline 3/8” diameter galvanized steel cable with thimble. Various lengths available.
TRQL Quick Link Galvanized steel quick-link used for connecting cable to shackle on inline shock absorber.
VGCG Automatic Pass-Through
Cable Guide Galvanized steel cable guide bracket includes M10-1.5mm x 1-1/2" x 2-9/16" U-bolt, two M10 at washers and two M10-
1.5mm locknuts.
TRCG Manual Pass-Through
Cable Guide Galvanized steel cable bracket with convertible polyurethane cable retainer head includes 3/8"-16 x 1-1/4" x 2" U-Bolt, two
3/8" lockwashers, two 3/8"-16 hex nuts, two 1/4"-20 x 1-1/4" bolts, four 1/4" at washers, and two 1/4"-20 locknuts.
TRBB Bottom BracketAssembly Galvanized steel bracket (1-1/2” x 1-1/2” tube) includes rung clamp assembly (w/4-hole mounting plate for 1-1/2" tube, two
3/8"-16 x 1-5/8" x 3-1/2" U-bolts, four 3/8" lockwashers, and four 3/8"-16 hex nut fasteners), bottom rung clamp assembly
(w/two 3/8"-16 x 3" bolts, two 3/8" at washers, 2-hole mounting plate, two 3/8" lockwashers, and two 3/8"-16 hex nut
fasteners), and tensioning rod assembly (w/compression spring, two saddle clips, 7/16" washer, and six 7/16"-14 hex nut
fasteners).
Model
No. Cable Sleeve
VGCS Vi-GoAutomatic Pass-Through Cable Sleeve [Also available with carabiner (VGCS-C) or with integral swivel and carabiner (VGCS-SC)]
TRCS Vi-Go Manual Pass-Through Cable Sleeve [Also available with carabiner (TRCS-C) or with integral swivel and carabiner (TRCS-SC)]
5.0 System Installation
• Before installation, carefully inspect all components of the system according to the manufacturer’s instructions
(see 8.0 Inspection and Maintenance). Do not use if there are any damaged or missing parts (see 4.3 System
Replacement Parts).
• Ensure that the structure/ladder on which the Vi-Go System is to be afxed is capable of withstanding loads
resulting from a fall (see 3.0 System Requirements).
• For ease of installation, the Vi-Go Installation Kit (TRIK) may be purchased
separately. Contact your Miller distributor.
WARNING: Personal fall protection is required during installation.
Persons installing the system must use caution and shall not be ex-
posed to a fall hazard during the installation procedure. Do not con-
nect to any component of a partially installed system.
System Installation Overview: The recommended installation procedure of the Vi-Go Vertical Cable Lifeline Sys-
tem is to install from the top of the ladder down.
Tools Required for Installation: Torque wrench, standard sockets--7/8" and 3/4", deep socket--9/16", standard
wrenches--7/16", 11/16" and 3/4", crowfoot wrench--17mm (for part VGCG only), cable cutters--minimum 3/8"
capacity needed (5/8" capacity preferred), and a tape measure.
TRIK

9
User Instructions - English
5.1 Installation of Top Bracket Assembly
Mounting
Plate
Washer
Fastener
Cap
Fastener
U-Bolt
Fig. 1a
Fig. 1d
Fastener
Washers
Mounting
Plate
Bolt
Fig. 1b
Shown with Extra
Rung Clamp Assembly
to reduce the loads
transmitted to each
ladder rung.
Fig. 1c
This installation configuration ►
is only permitted with the 5 ft.
(1.5m) top bracket assembly
and limits the number of users
on the system to one (1).
The top bracket assembly may be installed to
extend above the ladder to allow workers to
step safety onto the platform without disconnect-
ing from the lifeline. It is recommended to be
mounted at the center of the ladder for ease of
use and access, but can be installed toward the
side of the ladder if required.
For typical installation of the 5 ft.
(1.5m) top bracket assembly, refer to
Figure 1a. This installation congura-
tion will accommodate up to four (4)
users simultaneously. The 7 ft. (2m)
and 10 ft. (3m) top bracket assemblies
are installed as shown in Figure 1b.
[Note: All systems using the 10 ft.
(3m) top bracket assembly are lim-
ited to two (2) users.]
An extra rung clamp assembly may
be used in the installation of the top
bracket to lower the loads transmitted
to each ladder rung (see Fig. 1c).
For systems limited to one (1) user,
the 5 ft. (1.5m) top bracket may be
installed with two rung clamp assem-
blies (see Fig. 1d). Ensure the
ladder will withstand the loads be-
tween the two rungs.
1. Place the top bracket against the
rungs of the ladder at the desired
height (see either Fig. 1a or 1b). In-
stall bottom rung clamp assembly rst.
For 5 ft. (1.5m) bracket: Place U-bolt around the
rung of the ladder and through the holes provided at
the bottom of the bracket.
For 7 ft. (2m) or 10 ft. (3m) bracket: Place bolts
through the holes provided at the bottom of the
bracket and through mounting plate on opposite side
of ladder rung as shown.
Install washers and torque fasteners to 20 plus or
minus 2 ft. lbs.
WARNING: The bottom U-clamp must be installed
correctly or the bracket may slip under load.
2. Continue to hold bracket against the rungs of the
ladder. Install rung clamp assembly by placing U-bolts
around the rung of the ladder and inserting through the
mounting plate. Install washers and torque fasteners
to 20 plus or minus 2 ft. lbs. Repeat procedure for
remaining rung clamp assemblies.

User Instructions - English
10
5.2 Installation of Cable to Top Bracket Assembly
Use only Miller approved cable. Inspect cable before installation. Do not install damaged cable. Safety
glasses and gloves should be worn when handling cable.
When cutting the cable on site during the installation procedure is preferred or necessary, refer to 5.6 Options for
Terminating Cable in the Field. WARNING: All instructions and warnings provided with the cable
termination ttings must be read and understood before using the equipment.
1. Install quick link to cable thimble (see Fig. 2).
2. Then connect quick link with cable to the shackle
on the underside of the inline shock absorber.
Tighten quick link until snug. Do not use if quick
link does not close and tighten.
NOTE: Ensure the cotter pin is through the
shackle bolt and bent over so that it will not back
out. DO NOT USE SYSTEM IF COTTER PIN IS
MISSING.
5.3 Installation of Intermediate Cable Guides
Intermediate Cable Guides are designed to keep the climber from
excessively deecting the cable and to protect the cable from chaf-
ing against the ladder or structure. Cable guides should be placed
at 25 ft. (7.6m) minimum to 40 ft. (12.2m) maximum intervals along
the cable from the top bracket to the bottom bracket. Cable guides
may be placed at any point along the cable that may come in con-
tact with the ladder or structure. For installations in situations of
vibration or high wind, consideration should be given to placing the
intermediates closer together.
AUTOMATIC Pass-Through Cable Guides
1. Place intermediate cable guide against ladder rung (see Fig. 3).
2. Install U-bolt around ladder rung and through holes provided in
guide as shown.
3. Install washers and torque fasteners to 20 plus or minus 2 ft. lbs.
Fig. 3
Inline
Shock
Absorber
Shackle
Quick
Link
Cotter
Pin
Fig. 2

11
User Instructions - English
Washer
Fastener
U-Bolt
Mounting
Plate
Mounting
Bolt
Typical Installation 90 Degree Installation
Fig. 4a
90 Degree Installation
Note: High wind areas permit rotating the end of this cable
guide 90 degrees in either direction. When installation requires
this option, cable guides should be alternated from left to right
throughout the length of the system.
1. Remove fasteners from cable guide end.
2. Rotate end 90 degrees and reinsert fasteners (see Fig. 4b).
3. Torque fasteners to 20 plus or minus 2 ft. lbs.
4. To install cable guide with 90 degree end, follow above pro-
cedure except insert U-bolt through the two holes furthest
from the cable end on the guide bracket.
Fig. 4b
MANUAL Pass-Through Cable Guides
Typical Installation
1. Place cable guide on top of ladder rung (see Fig. 4a).
2. Install U-bolt around underside of ladder rung and through holes
provided in cable guide.
3. Install washers and torque fasteners to 20 plus or minus 2 ft. lbs.
5.4 Installation of Bottom
Bracket Assembly
WARNING: Inspect the bottom bracket assembly.
Do not use if there are any damaged or missing
components. Missing, damaged or omitted com-
ponents can result in the bracket slipping under a
load.
1. Place bottom bracket against the rungs of the lad-
der at the desired location aligning the bracket so
that the ladder rung is centered between the two
vertically placed holes in the bottom of the bracket.
(see Fig. 5).
2. Install bolts through holes in bottom of bracket and
through plate on opposite side, including washers,
as shown. Torque fasteners to 20 plus or minus
2 ft. lbs.
3. Install U-bolts around ladder rung at top of bracket
and through mounting plate. Install washers and
torque fasteners to 20 plus or minus 2 ft. lbs.
Fig. 5

User Instructions - English
12
5.5 Installation of Cable
and Tensioning Assembly
to Bottom Bracket Assembly
1. Install saddle clips loosely around cable attached
to tension rod (see Fig. 6).
2. Slide the tension rod down the cable and through
the hole in the bottom bracket until a sufcient
amount of threads are through to install the com-
pression spring, washer and tensioning nut.
3. Remove excess cable by pulling cable through the
saddle clips. Tighten and torque saddle clips to 40
to 45 ft. lbs.
4. Tighten tensioning nut until cable is taut. Com-
press spring until the distance of 5-1/2” is
achieved. Do not completely compress spring. If
an insufcient amount of threads are exposed,
repeat procedure from Step 3.
5. When proper tensioning of cable is achieved,
install jam nut against tensioning nut.
6. Discard excess cable by cutting below the lower
saddle clip, leaving approximately 3” of cable
below the lower saddle clip (3” is recommended; a
minimum of 1” is required).
Fig. 6
Saddle
Clip
Compression
Spring
Tension
Rod
Washer
Jam Nut
Tensioning
Nut
IMPORTANT: After installation is complete, a nal inspection of the system, ladder and structure is
required. Using a hand punch, designate the appropriate system capacity rating, installation date and service/in-
spection dates using the spaces provided on the label. Attach the label to the ladder or structure with the nylon tie
provided. Attach the label to the system where it is easily accessible to anyone using the system. Record system
identication information in the inspection and maintenance section of this manual.
▲ Complete Bottom Bracket
Assembly with
Tensioning Assembly and
Cable Installed
5-1/2"

13
User Instructions - English
5.6 Options for Terminating Cable in the Field
Thimble and Wire Rope
Cable Termination Kit (VGTWC)
Fast-Attach Fitting for 3/8” Diameter Approved Cable (VGF-1)
Dead End
1 Clip Base Width (1-1/8")
from Dead End
Live End
Options are available for terminating the cable in the eld
for increased versatility during installation to accommodate
variable cable lengths. These options are compatible
with 3/8” diameter approved cable only.
1. Feed cable around cable thimble, turning back 5-1/4" of cable from
thimble end. Install rst cable clip one clip base width (1-1/8") from
dead end of rope. Use torque wrench to tighten evenly, alternating
from one nut to the other until reaching a torque of 45 ft. lbs.
2. Install second cable clip as close to the thimble as possible. Again,
use torque wrench to tighten evenly to 45 ft. lbs.
Completely Assembled
*Wedge Set includes three toothed
wedges and retaining ring.

User Instructions - English
14
7.0 Training
It is the responsibility of the user and the purchaser of this equipment to assure they are familiar with these in-
structions and are trained in the proper use, installation, operation, inspection, maintenance and limitations of this
product. Training should be conducted periodically and without exposing the trainee to a fall hazard.
Training is an integral part of our Total Solution in fall protection, since no fall protection equipment – regardless of
how effective – can save an employee who is not trained in its use. To meet this crucial requirement, Miller Train-
ing provides the knowledge and skills necessary to achieve a safe, more productive work environment. For more
information on Miller Training, contact a representative today: 800.873.5242.
6.0 System Operation
1. Don a Miller full-body harness according to the manufacturer’s instructions.
2. Install the Vi-Go Cable Sleeve to the vertical cable lifeline according to the manufacturer’s instructions.
3. Attach the cable sleeve to the front attachment point, designated for ladder climbing, of the full-body harness
using a Miller approved auto-locking carabiner or other Miller approved connector.
4. Verify that the carabiner (or connector) keeper/gate is closed and locked.
5. Ascend and descend the ladder passing intermediate cable guides per the manufacturer’s instructions sup-
plied with the cable sleeve.
5.7 Optional Vi-Go Anchorage Connector
The Vi-GoAnchorage Connector is designed to provide a
convenient tie-off point for workers when entering/exiting at
the top of Vi-Go Vertical Cable Lifeline Systems. The Vi-
Go Anchorage Connector is designed for one person only
with a capacity of 310 lbs. (140.6kg).
Model Compatible Top Bracket Assembly
TRS-AC1 Compatible with the 5ft. (1.5m) top bracket
assembly (with 1.5” x 1.5” tube)
TRS-AC2 Compatible with the 7 ft. (2m) and 10 ft. (3m) top
bracket assemblies (with 2” x 2” tube)
Vi-Go Anchorage Connector
WARNING: All instructions and warnings pro-
vided with the anchorage connector must be
read and understood before using the equip-
ment.
TRS-AC2

15
User Instructions - English
Cleaning and Storage
Basic care of all Miller Fall Protection equipment will prolong the life of the unit and will contribute toward the
performance of its vital safety function. Proper storage and maintenance after use are as important as cleansing
the equipment of dirt, corrosives, or contaminants. Clean system components using a cloth dampened with water
and mild soap or detergent and towel dry. Storage areas should be clean, dry and free of exposure to fumes or
corrosive elements.
Servicing
Servicing must only be carried out by a qualied person trained in the inspection and replacement of the system.
A record log of all servicing and inspection dates for this system must be maintained. This system and all its
components and devices must be withdrawn from service if subjected to fall arresting forces. Only original
Miller Fall Protection replacement parts are approved for use in this system. Contact Miller Technical Services at
800.873.5242 if you have any questions.
8.0 Inspection and Maintenance
Inspection
The Vi-Go System is designed for today’s rugged work environments. To maintain its service life and high
performance, all components should be inspected frequently. Visually inspect before each use. Regular
inspection by a competent person for wear, damage or corrosion should be a part of your safety program.
Replace equipment if any of the defective conditions explained in this manual are found.
System Inspection
Before each use, visually inspect for the following:
Inspect all components for physical damages, cracks, wear and corrosion.• Check fasteners, bolts and pins for damages, cracks, wear and corrosion.• Inspect the cable lifeline for cuts, frays, kinks, broken strands or other signs of unusual wearing patterns.• [CAUTION: Always wear gloves when inspecting wire rope!]
Check cable tension ensuring there is no slack. Retension cable to specications as per section 5.5 of this • manual.
Inspect for malfunctioning components, broken or missing springs and fasteners.• [For replacement parts call: 800.873.5242]
Inspect cable sleeve, connector and full-body harness according to the manufacturer’s instructions.•
Labels
LB1019 REV. A
WARNING
Manufacturer's instructions supplied with this product
at the time of shipment must be followed. Failure to
do so may result in serious injury or death.
Climbing System
3
42
1
TO SYSTEM MUST NOT EXCEED
NUMBER OF USERS ATTACHED
SYSTEM CAPACITY RATING
1
2
4
3
DJYR FM JJAM NOAS
PUNCH DATE OF INSTALLATION/INSPECTION
6
5
Sperian Fall Protection, Inc.
Franklin, PA. U.S.A.
Call: 800-873-5242
Vi-Go
200%
OSHA 1926.502,
1910.27, ANSI A14.3,
CSA Z259.2.1-98
(Class AS)

16
INSPECTION DATE
DATE D’INSPECTION
FECHA DE INSPECCIÓN
INSPECTION
ITEMS NOTED
POINTS NOTÉS
LORS DE L’INSPECTION
PUNTOS DE INSPECCIÓN
RELEVANTES
CORRECTIVE
ACTION
ACTION CORRECTIVE
MEDIDA CORRECTIVA
MAINTENANCE
PERFORMED
ENTRETIEN EFFECTUÉ
MANTENIMIENTO
REALIZADO
Approved by:
Approuvé par:
Aprobado por:
Approved by:
Approuvé par:
Aprobado por:
Approved by:
Approuvé par:
Aprobado por:
Approved by:
Approuvé par:
Aprobado por:
Approved by:
Approuvé par:
Aprobado por:
Approved by:
Approuvé par:
Aprobado por:
Approved by:
Approuvé par:
Aprobado por:
Approved by:
Approuvé par:
Aprobado por:
Approved by:
Approuvé par:
Aprobado por:
Approved by:
Approuvé par:
Aprobado por:
DATE OF MANUFACTURE:_________________________________________________
DATE DE FABRICATION / FECHA DE FABRICACIÓN
MODEL NUMBER:________________________________________________________
NUMÉRO DE MODÈLE / NÚM. DE MODELO
DATE PURCHASED:______________________________________________________
DATE D’ACHAT / FECHA DE COMPRA
Inspection and Maintenance Log
Registre D'inspection et D'entretien
Registro de Inspección y Mantenimiento

17
MILLER® FALL PROTECTION PRODUCTS
TOTAL SATISFACTION ASSURANCE
At Miller Fall Protection, we have been providing quality Miller brand fall protection
equipment to millions of workers worldwide since 1945.
LIMITED LIFETIME WARRANTY
BACKED BY OVER 60 YEARS IN THE FALL PROTECTION BUSINESS
We sincerely believe that our fall protection equipment is the best in the world.
Our products endure rigorous tests to ensure that the fall protection equipment you trust is manufactured
to the highest standards. Miller fall protection products are tested to withstand normal wear and tear,
but are not indestructible and can be damaged by misuse.
Our Limited Lifetime Warranty does not apply to normal wear and tear or abusive treatment of the product.
In the unlikely event that you should discover defects in either workmanship or materials,
under our Limited Lifetime Warranty, we will repair or replace the product at our expense.
If a replacement is necessary and your product is no longer available, a comparable product will be substituted.
Should a product issue surface, contact us at 800.873.5242.
Manufacturing specications are subject to change without notice.
PRODUITS MILLER® FALL PROTECTION
ASSURANCE DE SATISFACTION TOTALE
Chez Miller Fall Protection, nous fournissons des équipements de protection contre les chutes de marque
Miller de qualité à des millions de travailleurs dans le monde entier depuis 1945.
GARANTIE LIMITÉE À VIE
ASSURÉE GRÂCE À PLUS DE 60 ANS PASSÉS DANS LE DOMAINE DE LA PROTECTION CONTRE LES CHUTES
Nous croyons sincèrement que notre équipement de protection contre les chutes est le meilleur au monde. Nos
produits sont soumis à des tests rigoureux, an d’assurer que les équipements de protection contre
les chutes dans lesquels vous avez conance sont fabriqués selon les normes les plus exigeantes.
Les produits de protection contre les chutes Miller sont soumis à des essais pour vérier qu’ils résistent à une usure
normale; ils ne sont cependant pas indestructibles et peuvent s’endommager en cas de mauvaise utilisation. Notre
garantie limitée à vie ne s’applique pas à l’usure normale ou à un usage abusif du produit.
Dans le cas peu probable où vous découvririez des défauts, soit de fabrication, soit de matériau,
dans le cadre de notre garantie à vie, nous réparerons ou remplacerons le produit à nos frais.
En cas de remplacement, si votre produit n’est plus offert, vous recevrez un produit comparable.
En cas de problème sur un produit, nous contacter au 800-873-5242.
Les caractéristiques de fabrication peuvent être modiées sans préavis.
PRODUCTOS ANTICAÍDAS MILLER®
GARANTÍA DE SATISFACCIÓN TOTAL
En Miller Fall Protection, venimos suministrando desde 1945 los equipos de protección anticaídas
con la calidad Miller a millones de trabajadores en todo el mundo.
GARANTÍA LIMITADA DE POR VIDA
NOS RESPALDAN MÁS DE 60 AÑOS EN LA FABRICACIÓN DE EQUIPO ANTICAÍDAS
Sinceramente creemos que su equipo de protección contra caídas es el mejor del mundo. Nuestros productos resisten
rigurosas pruebas para garantizar que el equipo de protección contra caídas en el que usted confía está fabricado de
conformidad con las normas más elevadas. Los productos anticaídas Miller son sometidos a pruebas para que resistan el
desgaste normal, pero no son indestructibles y su incorrecta utilización puede dañarlos.
Nuestra Garantía limitada de por vida no se aplica al desgaste normal ni al maltrato del producto.
En el poco probable caso de que usted descubriera defectos de mano de obra o materiales, por nuestra Garantía limi-
tada de por vida, repararemos o sustituiremos el producto por cuenta nuestra. Si un reemplazo es necesario y nuestro
producto ya no está disponible, se lo sustituiremos por otro comparable.
En caso de que surja un problema con el producto, contáctenos al 800.873.5242.
Las especicaciones de fabricación están sujetas a modicaciones sin previo aviso.

Sperian Fall Protection, Inc.
P.O. Box 271, 1345 15th Street
Franklin, PA 16323 USA
Toll Free: 800.873.5242
Fax: 800.892.4078
Download this manual at: www.millerfallprotection.com
Téléchargez ce manuel à l’adresse: www.millerfallprotection.com
Puede bajar por Internet este manual en: www.millerfallprotection.com
Table of contents
Popular Ladder manuals by other brands
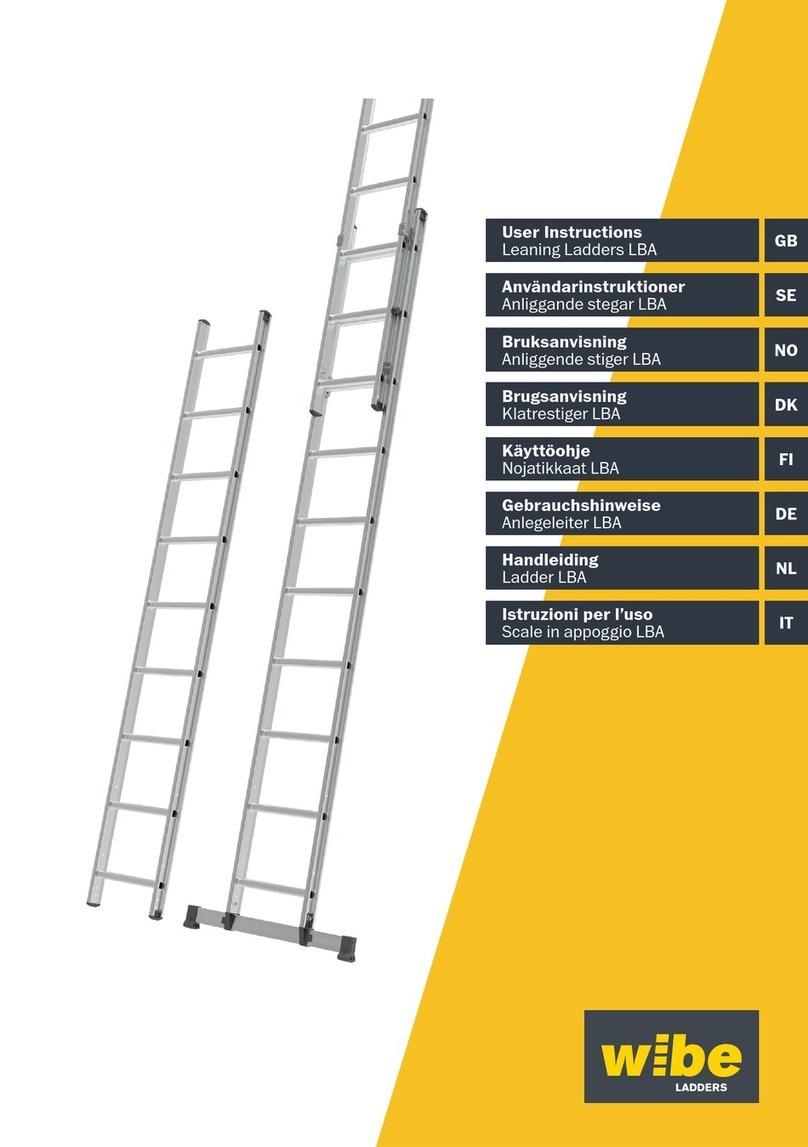
wibe
wibe LBA User instructions
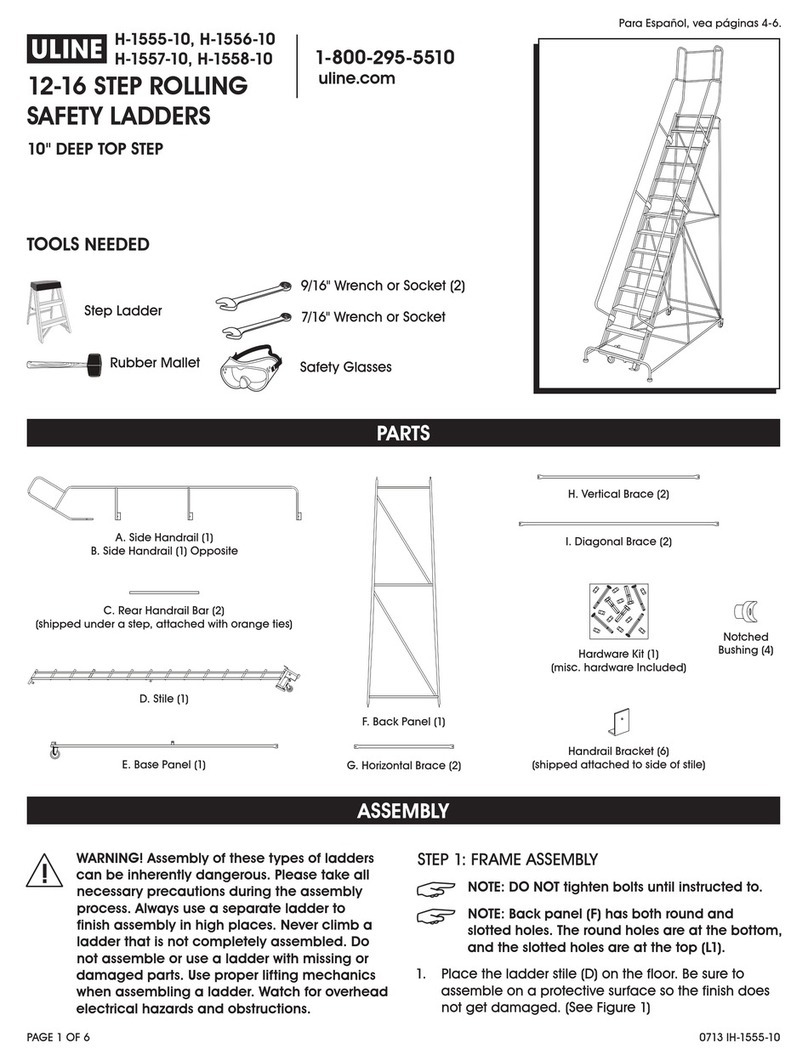
U-Line
U-Line H-1555-10 Assembly
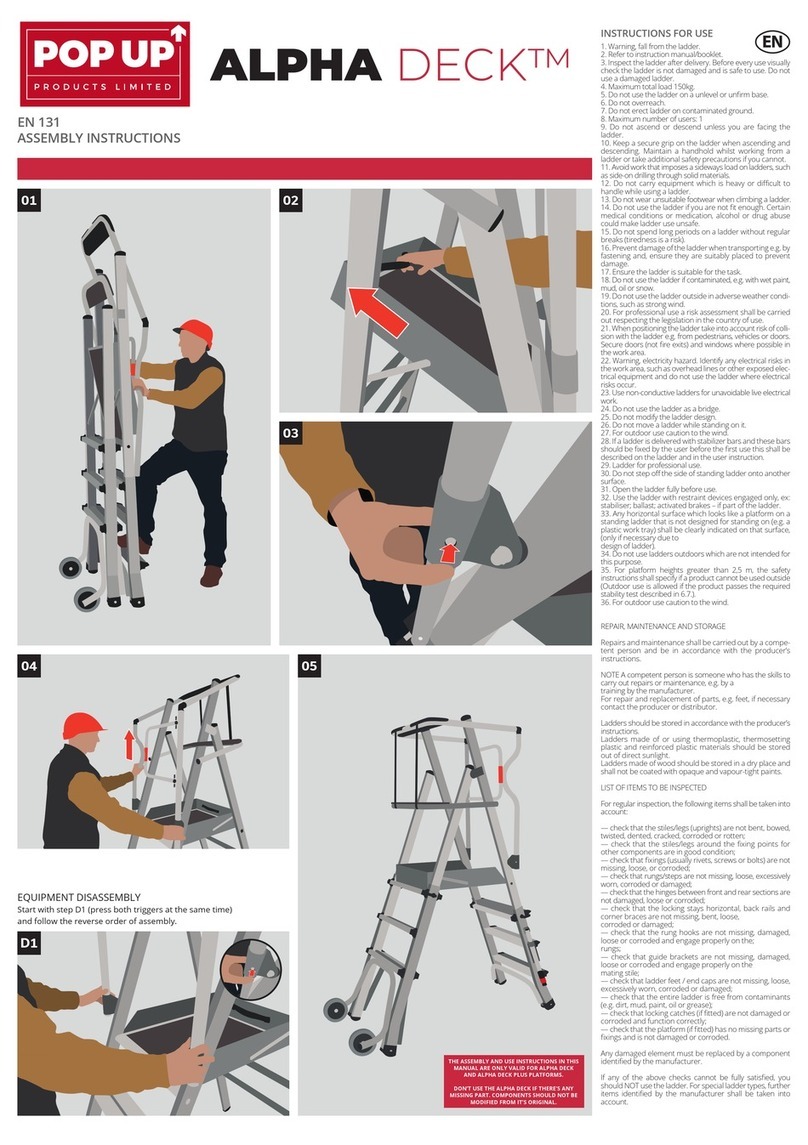
POP UP
POP UP ALPHA DECK Assembly instructions
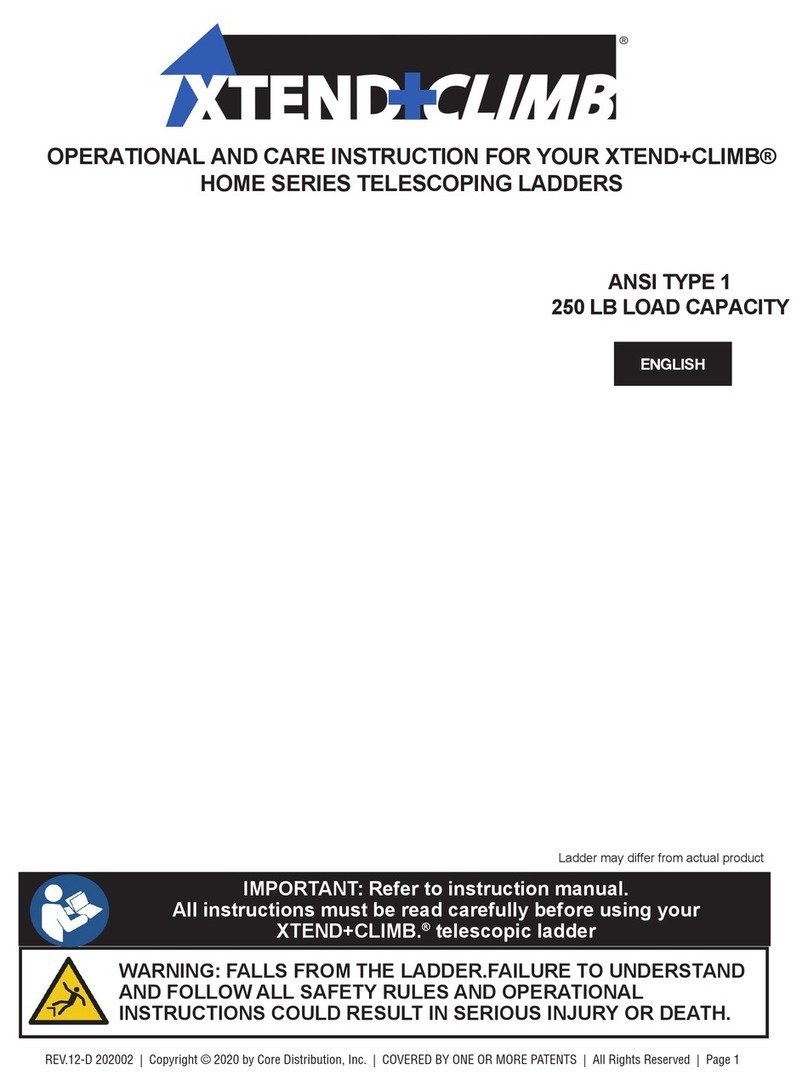
Xtend+Climb
Xtend+Climb HOME 750P PLUS Operational and care instructions
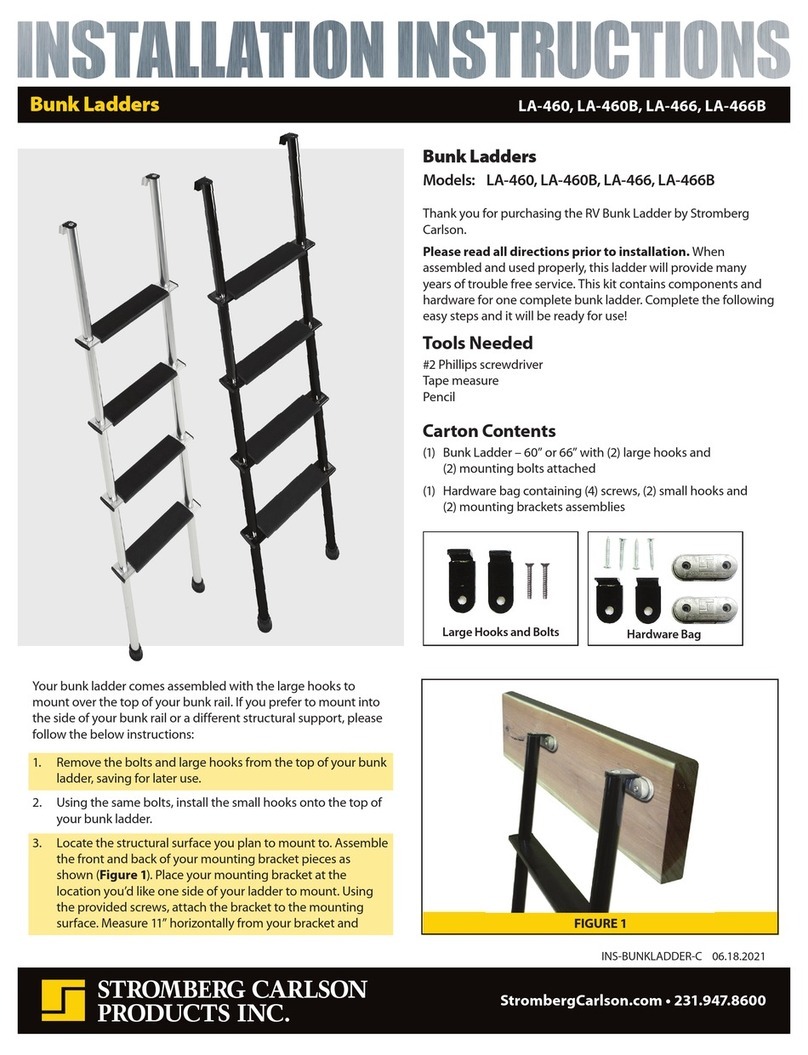
Stromberg Carlson Products
Stromberg Carlson Products LA-460 installation instructions
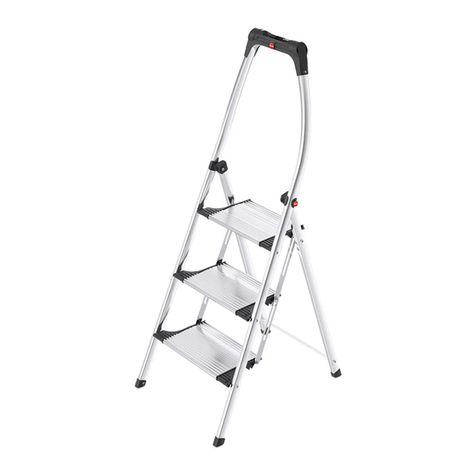
Hailo
Hailo K100 TopLine Instructions for use