SPX FLOW APV DELTA SW4 User manual

APV DELTA SW4
SINGLE SEAT AND CHANGE-OVER VALVE
FORM NO.: H170733 REVISION: UK-4 READ AND UNDERSTAND THIS MANUAL PRIOR TO OPERATING OR SERVICING THIS PRODUCT.
INSTRUCTION MANUAL
Scan for SW4 Valve
Maintenance Video


EU Declaration of Conformity
for Valves and Valve Manifolds
SPX FLOW TECHNOLOGY GERMANY GMBH
Gottlieb-Daimler-Str. 13, D-59439 Holzwickede
herewith declares that the
APV double seal and double seat valves of the series
SD4, SDT4, SDU4, SDMS4, SDMSU4, SDTMS4, SWcip4, DSV,
DA3, DA3SLD, DE3, DEU3, DET3, DKR2, DKRT2, DKRH2
in the nominal diameters DN 25 - 150, ISO 1“ – 6“ and 1 Sh5 - 6 Sh5
APV butterfly valves of the series SV1 and SVS1F, SVL and SVSL
in the nominal diameters DN 25 - 100, DN 125 - 250 and ISO 1“ – 4“
APV ball valves of the series KHI, KHV
in the nominal diameters DN 15 - 100
APV single seat, diaphragm and spring loaded valves of the series
S2, SW4, SWhp4, SW4DPF, SWmini4, SWT4, SWS4, MF4, MS4, MSP4, AP/T1, CPV,
RG4, RG4DPF, RGMS4, RGE4, RGE4DPF, RGEMS4, PR2, PRD2, SI2, UF/R3, VRA/H
in the nominal diameters DN 10 - 150, ISO 1/2“ – 4“ and 1 Sh5 - 6 Sh5
and the valve manifolds installed thereof
meet the requirements of the Directives 2006/42/EC (superseding 89/392/EEC
and 98/37/EC) and ProdSG (superseding GPSG - 9.GPSGV).
For official inspections, SPX FLOW presents
a technical documentation according to Appendix VII of the Machinery Directive,
this documentation consisting of documents of the development and construction,
description of measures taken to meet the conformity and to correspond with
the basic requirements on safety and health, incl. an analysis of the risks,
as well as an operating manual with safety instructions.
The conformity of the valves and valve manifolds is guaranteed.
Authorised person for the documentation:
Frank Baumbach
SPX FLOW TECHNOLOGY GERMANY GMBH
Gottlieb-Daimler-Str. 13, D-59439 Holzwickede, Germany
November 2017
Frank Baumbach
Regional Engineering Manager, F&B Components
UK


1
APV_SW4_UK-4_082017.indd
UK
Single seat and change-over valve
DELTA SW4
Instruction manual: UK - rev.4
APV
1. General Terms 2
2. Safety Instructions 2 - 3
3. Intended Use 3
4. Mode of Operation 4
4.1. General terms
5. Auxiliary Equipment 5 - 6
5.1. Valve position indicator
5.2. Control unit
5.3. Stroke limitation SW4 / M4
5.4. Oil dampening cylinder
5.5. SW4 variants
6. Cleaning 7
6.1. Cleaning recommendation
7. Installation 7 - 8
7.1. General terms
7.2. Connections
7.3. Welding instructions
8. Dimensions / Weights 9 - 10
8.1. Single seat valve
8.2. Change-over valve
9. Technical Data 11 - 14
9.1. General data
9.2. Compressed air quality
9.3. Closing times
9.4. Valve stroke
9.5. Pneumatic air consumption
9.6. Product pressures
9.7. Kvs values
10. Maintenance 15
11. Service Instructions - Single seat valve 16 - 17
12. Service Instructions - Actuator 18
13. Service Instructions - Change-over valve 19 - 20
14. Assembly Tool 21
15. Reconstruction of Actuator 22
16. Trouble Shooting 23
17. Spare Parts Lists 24
Spare parts lists - DN design & Inch design RN 01.054.805
RN 01.054.807
Table of Contents Page


2
APV_SW4_UK-4_082017.indd
UK
Single seat and change-over valve
DELTA SW4
Instruction manual: UK - rev.4
APV
1. General Terms
This instruction manual must be read carefully and observed by the
responsible operating and maintenance personnel.
We point out that we will not accept any liability for damage or
malfunctions resulting from the non-compliance with this instruction
manual.
Descriptions and data given herein are subject to technical changes.
2. Safety Instructions
This instruction manual must be read carefully and observed by the
responsible operating and maintenance personnel.
The valve must only be assembled, operated, disassembled,
serviced and repaired by persons who have been trained
accordingly.
Please contact your local SPX FLOW representative if necessary.
Danger!
This technical safety symbol draws your attention to important
directions for operating safety. You will find it wherever the activities
described are bearing health hazards or risks for persons or
material assets.
Do not touch the open valve.
Risk of injury by sudden valve operation.
In dismantled state there is the risk of crushing by sudden valve
operation!
- Schedule regular maintenance including replacement of all seals
and bearing bushes in order to prevent leakages and emersion of
liquids.
- Depressurize the line system before any maintenance work. Drain
the valve if possible.
- Separate electric and pneumatic connections.
- Observe Service Instructions to ensure safe maintenance of the
valve.

3
APV_SW4_UK-4_082017.indd
UK
Single seat and change-over valve
DELTA SW4
Instruction manual: UK - rev.4
APV
2. Safety Instructions
Danger!
Welded actuators are preloaded by spring force.
Opening of the actuators is strictly forbidden.
Danger to life!
Actuators which are no longer used or defective must be disposed
in professional manner.
Defective actuators must be returned to your SPX FLOW
representative for their professional disposal and free of charge for
you.
3. Intended Use
The intended use as field of application of the DELTA SW4 single
seat and change-over valves is the shut-off of line sections.
Arbitrary, constructive changes at the valve will influence safety
as well as the intended functionality of the valve and are not
permissible.
Authorizations
3-A Sanitary Standards, Inc.
ATEX (Directive 2014/34/EU)

4
APV_SW4_UK-4_082017.indd
UK
Single seat and change-over valve
DELTA SW4
Instruction manual: UK - rev.4
APV
4. Mode of Operation
4.1. General terms
Single seat and change-over valves DELTA SW4 have been
developed for use in the brewing and beverage, dairy and food
industries as well as for chemical and pharmaceutical applications.
The valves are designed for universal applications and stand out
for their increased mechanical reliability and absolute ease of
service.
The field of application of the DELTA SW4 valve is to shut off
and to change over line sections.
- Operation by pneumatic actuator with air connection, reset by spring
force.
- By different assembly of the actuator, the following designs are
possible:
NC: actuator normally closed / air-to-raise, spring-to-lower
NO: actuator normally open / air-to-lower, spring-to-raise
- The inner parts of the actuator need not be serviced.
- As standard design, the SW4 valve is equipped with a control unit
CU41 Direct Connect.
The luminous diodes in the control unit indicate the position of the
valve shaft.
control unit
actuator
actuator screw
yoke
housing
housing
upper housing
shaft
shaft
Single seat valve
Change-over valve

5
APV_SW4_UK-4_082017.indd
UK
Single seat and change-over valve
DELTA SW4
Instruction manual: UK - rev.4
APV
5. Auxiliary Equipment
5.1. Valve position indication (fig. 5.1.)
Proximity swith holders (PSH) for the valve position indication can
be mounted direct on the actuator. Proximity switches to signal
the limit position of the valve seat can be installed at the proximity
switch holder.
We recommend to use our APV standard types:
Operating distance: 5 mm / Diameter: 11 mm.
Operating voltage: 10 - 30 VDC
Outlet: operating voltage pnp positive switching
Connection: moulded cable 5 m length
Protective type: IP 67
Reference number: 08 - 60 - 011/93; H16223
Using a valve position idicator other than APV, we cannot accept
any liability for a faultless function.
5.2. Control unit (fig. 5.2.)
For the start-up as well as assembly and disassembly of the
different designs, please use the respective manual.
The following different designs are available:
Direct Connect
reference number; ID-No.
CU41-S-Direct Connect
08-45-100/93; H320460
Profibus
reference number; ID-No.
CU31-Profibus
08 - 45 - 001/93; H315495
DeviceNet
reference number; ID-No.
CU31-DeviceNet
16 - 31 - 240/93; H209422
AS-interface extended
reference number; ID-No.
CU41-S-AS-i extended
08 - 45 - 110/93; H320467
An adapter is required to install the control unit on the SW4 valve.
Designation:
reference number; ID-No.
CU3 adapter SW4/M4
08 - 48 - 480/93; H315806
Designation:
reference number; ID-No.
CU4 - S adapter
DN25 - 100 / 1” - 4”
08 - 46 - 600/93; H320474
fig. 5.2.
fig. 5.1.

6
APV_SW4_UK-4_082017.indd
UK
Single seat and change-over valve
DELTA SW4
Instruction manual: UK - rev.4
APV
5. Auxiliary Equipment
5.3. Stroke limitation SW4 / M4 (fig. 5.3.)
The pneumatic stroke limitation provides for the continuous
adjustment of the total valve stroke of 0 - 100%.
The pneumatic stroke limitation is installed on the actuator.
The valve disc can be in the three different positions:
open, throttled and closed.
The stroke limitation can only be applied with valve design
NC (FS) = normally closed.
To operate the pneumatic stroke limitation a separate control is
required.
The control unit CU43-S-2 Hall sensors-Direct Connect
can be used for this purpose.
control unit + adapter
Designation:
reference No.;
ID-No.
CU43-S-2 Hall sensors-Direct Connect
000 08-45-106/93;
H320466
Designation:
reference No.;
ID-No.
CU4-S-Adapter
000 08-48-600/93;
H320474
5.4. Oil dampening cylinder (fig. 5.4.)
The oil dampening cylinder provides for a slow opening and closing
of the valve (to prevent pressure hammers in the line system). The
oil dampener is installed between the actuator and the control unit.
Function:
During valve switching, a throttling valve presses the oil from one
chamber of the dampening cylinder into the second chamber of the
cylinder. By adjustment of the throttling screw, the required delay
can be variably adjusted.
5.5. SW4 variants
The SW4 range contains the following designs:
- DELTA SW4 - DN125-150
- DELTA SW4 with manual actuation
- DELTA SWT4 - tank outlet valve
- DELTA SW4 - long stroke version
- DELTA SW4 -DPF (with steam chamber)
- DELTA SWR4 (with modulating cone)
- DELTA SW4 - ATEX DN 25-100, Inch 1"-4"
Corresponding manuals are available for the different designs.
fig. 5.3.
fig. 5.4.

7
APV_SW4_UK-4_082017.indd
UK
Single seat and change-over valve
DELTA SW4
Instruction manual: UK - rev.4
APV
6. Cleaning
6.1. Cleaning recommendation
-Flow passages
The passages of the valve are cleaned by the cleaning liquid during
cleaning of the connected pipelines.
Depending on the degree and substances of soiling, cleaning
liquids, times and processes must be scheduled for the individual
application.
The compatibility of the individually selected cleaning processes
and liquids with the respective seal material must be veried.
7. Installation
7.1. General terms
- Installation must be undertaken in such a way that liquids can drain
off and should preferably be carried out in vertical position.
-Single seat valve:
The valve housing can be welded direct into the pipeline system
(completely dismantable valve insert).
-Change-over valve:
The upper housing is connected with the pipeline via a ange or
clamp connection in detachable manner (see g. 7.).
Attention! Observe Welding Instructions 7.3.
7.2. Connections
Besides the basic version with weld ends, the valve housing are
also available with threaded, flange and clamp connection.
fig. 7.
change-over valve
separate connection

8
APV_SW4_UK-4_082017.indd
UK
Single seat and change-over valve
DELTA SW4
Instruction manual: UK - rev.4
APV
7. Installation
7.3. Welding Instructions
Shut-off valve
- Before welding of the valve, the valve insert must be dismantled
from the housing. Careful handling to avoid damage to the parts
is necessary.
Change-over valve:
- Before welding of the valves, the valve insert must be dismantled
from the housing. The lower housing seal must be removed.
Careful handling to avoid damage to the parts is necessary.
- Welding should only be carried out by certified welders (DIN EN ISO
9606-1) (seam quality DIN EN ISO 5817).
- The welding of the valve housings must be undertaken in such a
way that the valve body is not deformed.
- The preparation of the weld seam up to 3 mm thickness must be
carried out as a square butt joint without air.
(Consider shrinkage!)
- TIG orbital welding is best!
- After welding of the valve housings or of the mating flanges
and after work at the pipelines, the corresponding parts of the
installation or pipelines must be cleaned from welding residues
and soiling.
If these cleaning instructions are not observed, welding residues
and dirt particles can settle in the valve and cause damage.
- Any damage resulting from the non-observance of these welding
instructions is not subject to our guarantee.
- Welding directives for aseptic applications shall be drawn from the
AWS/ANSI Directives and EHEDG Guidelines.

A1 / L1
∅Di
∅Di
∅Di
Ø 134
Ø K
F
F
H
A / A1H
G
F
F
F
F A
L
200
9
APV_SW4_UK-4_082017.indd
UK
Single seat and change-over valve
DELTA SW4
Instruction manual: UK - rev.4
APV
8. Dimenions/Weights
Dimensions in mm Weight
in kg
DN A L ∅Di F ∅G H ∅K A1 L1
25 410 460 26 50 18 54 86 338 388 5
40 414 481 38 67 24 66 86 342 409 5
50 451 523 50 72 32 78 126 379 451 7
65 459 544 66 85 40 94 126 387 472 7
80 512 610 81 98 47,5 109 189 440 438 13
100 522 633 100 111 57 128 189 450 561 15
Inch
1" 408 458 22,6 50 16,3 50,6 86 336 386 5
1,5" 412 479 34,9 67 22,4 62,9 86 340 407 5
2" 450 522 47,6 72 30,8 75,6 126 378 450 7
2,5" 456 541 60,3 85 37,2 88,3 126 384 469 7
3" 507 597 72,9 90 43,5 100,9 189 435 525 13
4" 520 631 97,6 111 55,8 125,6 189 448 559 15
8.1. Single seat valve
housing variants
SW 41
SW 42
SWE 43
SWE 44
SWE 42 SWE 41
Single seat valve
with CU4 control unit Valve position indicator
SWE 43/44
SWE 41/42

10
APV_SW4_UK-4_082017.indd
UK
Single seat and change-over valve
DELTA SW4
Instruction manual: UK - rev.4
APV
8. Dimensions/Weights
Dimensions in mm Weight
in kg
DN A L ∅Di F ∅G H ∅K A1 L1
25 410 514 26 50 18 54 86 338 442 6
40 414 547 38 67 24 66 86 342 475 6
50 451 601 50 72 32 78 126 379 529 8
65 459 638 66 85 40 94 126 387 566 8
80 512 719 81 98 47,5 109 189 440 647 15
100 522 761 100 111 57 128 189 450 689 17
Inch
1" 408 509 22,6 50 16,3 50,6 86 336 437 6
1,5" 412 542 34,9 67 22,4 62,9 86 340 470 6
2" 450 598 47,6 72 30,8 75,6 126 378 526 8
2,5" 456 629 60,3 85 37,2 88,3 126 384 557 8
3" 507 698 72,9 90 43,5 100,9 189 435 626 15
4" 520 757 97,6 111 55,8 125,6 189 448 685 17
A1 / L1
∅Di
∅Di
Ø 134
Ø K
F
A / A1H H
G
F
FF
F H A
L200
8.2. Change-over valve
housing variants
Change-over valve
with CU4 control unit Valve position indicator
SWE 45/46
SWE 45
SWE 46
SW 47
SW 48
SW 43
SW 44

11
APV_SW4_UK-4_082017.indd
UK
Single seat and change-over valve
DELTA SW4
Instruction manual: UK - rev.4
APV
9. Technical Data
9.1. General data
- Product-wetted parts: 316 L, 1.4404 (DIN EN
10088)
- Other parts: 1.4301 (DIN EN 10088)
- Seals: standard design: EPDM
- Option: HNBR, VMQ, HNBR
- Max. line pressure: 10 bar
- Operating pressure: depending on actuator
- see 9.6
- Max. operating temperature: 135°C EPDM, HNBR
*FPM, *VMQ
- Short-term load: 140°C EPDM, HNBR
*FPM, *VMQ
*(no steam)
- Air connection (for hose): 6 x 1mm
- Max. pneumatic air pressure: 8 bar
- Min. pneumatic air pressure: 6 bar
Use dry and clean air, only.
9.2. Compressed air quality
- Compressed air quality: quality class according to ISO 8573-1
- Content of solid particles: quality class 3,
max. number of particles per m³
10000 of 0,5 μm < d ≤ 1,0 μm
500 of 1,0 μm < d ≤ 5,0 μm
- Content of water: quality class 3,
max. dew point temperature - 20 °C
For installations at lower temperatures
or at higher altitudes, additional
measures must be considered to reduce
the pressure dew point accordingly.
- Content of oil: quality class 1,
max. 0,01 mg/m³
The oil applied must be compatible with Polyurethane elastomer
materials.

12
APV_SW4_UK-4_082017.indd
UK
Single seat and change-over valve
DELTA SW4
Instruction manual: UK - rev.4
APV
9. Technical Data
9.3. Closing times for single seat and change-over valves
The opening and closing times of the valves which are equipped
with a control unit, can be fixed through adjustment of the
throttling screws at the solenoid valve.
Closing times in sec
Pneumatic air pressure 6bar
hose length 1 m
DN Inch 1m 10m
25 1" 1 sec. 1,5 sec.
40 1,5" 1 sec. 1,5 sec.
50 2" 1 sec. 1,5 sec..
65 2,5" 1 sec. 2,5 sec.
80 3" 1 sec. 3,0 sec.
100 4" 1.2 sec. 3,5 sec.
Times mentioned are only approximate values from sample measurements.
9.4. Valve stroke SW4
DN Inch
Single seat valve
SW 41, SW 42
SWE41, 42, 43, 44
Change-over valve
SW43, SW44
SWE45, 46
25 1" 12 9
40 1,5" 25 22
50 2" 28 25
65 2,5" 28 25
80 3" 28 25
100 4" 28 25
9.5. Pneumatic air consumption
at 6 bar control pressure
Actuator per stroke NL
Ø74mm 1,0
Ø110mm 2,1
Ø165mm 4,5

13
APV_SW4_UK-4_082017.indd
UK
Single seat and change-over valve
DELTA SW4
Instruction manual: UK - rev.4
APV
9.6. DELTA SW4 calculatory product pressures in (bar) at 6 bar pneumatic air pressure
Single seat valve
SW41 FS
Single seat valve
SW41 NO with
6 bar air pressure
Change-over valve
SW43 NC
lower seat
Change-over valve
SW43 NO with
6 bar air pressure
Change-over valve
SW43 NC upper seat
with 6 bar air pressure
Change-over valve
SW43 NO
upper seat
Ø Actuator in mm Ø Actuator in mm Ø Actuator in mm Ø Actuator in mm
DN Inch Ø 74 Ø 110 Ø 165 Ø 74 Ø 110 Ø 165 Ø 74 Ø 110 Ø 165 Ø 74 Ø 110 Ø 165
25 1" 11,7 11,2 20,3 21,2
40 1,5" 5,0 12,5 5,4 11,2 6,9 14,4 6,0 16,0
50 2 2,8 7,6 19,6 3,4 7,1 16,8 4,0 8,3 19,5 3,3 8,8 22,8
2,5" 2,0 5,4 13,8 2,4 5,0 11,9 2,7 5,5 13,1 2,2 6,0 15,3
65 1,7 5,0 11,7 2,0 5,0 10,0 2,2 5,0 10,9 1,8 5,0 12,7
3" 3,8 9,9 3,6 8,5 3,8 9,1 4,1 10,6
80 3,1 7,9 2,9 6,8 3,0 7,2 3,3 8,4
100 4" 2,1 5,3 1,9 5,0 2,0 5,0 2,1 5,5
standard actuator
9. Technical Data
p
pp
pp
p

14
APV_SW4_UK-4_082017.indd
UK
Single seat and change-over valve
DELTA SW4
Instruction manual: UK - rev.4
APV
9. Technical Data
9.7. DELTA SW4 kvs values in m³/h
SW41, 42
SWE41, 42
SWE43, 44
SW41, 42
SWE41, 42
SWE43, 44
SW42
SWE42
SW44
SW43, 44
SW47, 48
SW43, 44
SW47, 48
DN
25 20 21 28 14 13
40 45 53 60 33 31
50 92 85 120 58 51
65 159 159 215 100 89
80 201 209 650 160 137
100 302 325 540 245 212
Inch
1" 16 18 26 10 10
1,5" 38 45 57 30 28
2" 83 77 118 54 49
2,5" 133 133 185 87 76
3" 176 176 300 137 114
4" 292 310 530 225 210

15
APV_SW4_UK-4_082017.indd
UK
Single seat and change-over valve
DELTA SW4
Instruction manual: UK - rev.4
APV
10. Maintenance
The maintenance intervals depend on the corresponding
application and are to be determined by the operator himself
carrying out temporary checks.
The valve must not be cleaned with products containing abrasive
or polishing material. Especially the valve shaft must not, under
any circumstances, be cleaned with such agents. Damage of the
valve shaft can lead to leakages.
- Required tools:
- 1x wrench SW13
- 1x wrench SW17
- 1x wrench SW19
- 1x wrench SW30
- assembly tool for seat seal (see chapter 14.)
- Exchange of seals is done according to Service Instructions.
Customer stock keeping of spare seals is recommended.
For valve service actions we supply complete seal kits
including seal grease (see spare parts lists).
Assembly of the valve and change of the valve design NC
or NO according to Service Instructions.
Attention! Use food-grade grease and special greases being
suited for the respective seal material, only!
Recommendation:
APV assembly grease for EPDM, FPM, HNBR and NBR
(0,75 kg/tin - ref.-No. 000 70-01-019/93 ; H147382)
(60 g/tube - ref.-No. 000 70-01-018/93 ; H147381)
or
APV assembly grease for VMQ (Silicone)
(0,6 kg/tin - ref.-No. 000 70-01-017/93; H147380)
(60 g/tube - ref.-No. 000 70-01-016/93; H147379)
! Do not use grease containing mineral oil for EPDM seals.
! Do not use Silicone-based grease for VMQ seals.
Less suited grease types can influence function and service life.
Scan for SW4 Valve
Maintenance Video
Table of contents
Popular Measuring Instrument manuals by other brands
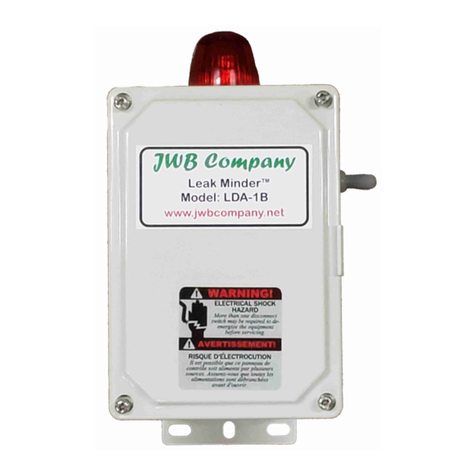
JWB Company
JWB Company Leak Minder LDA-1B instruction manual
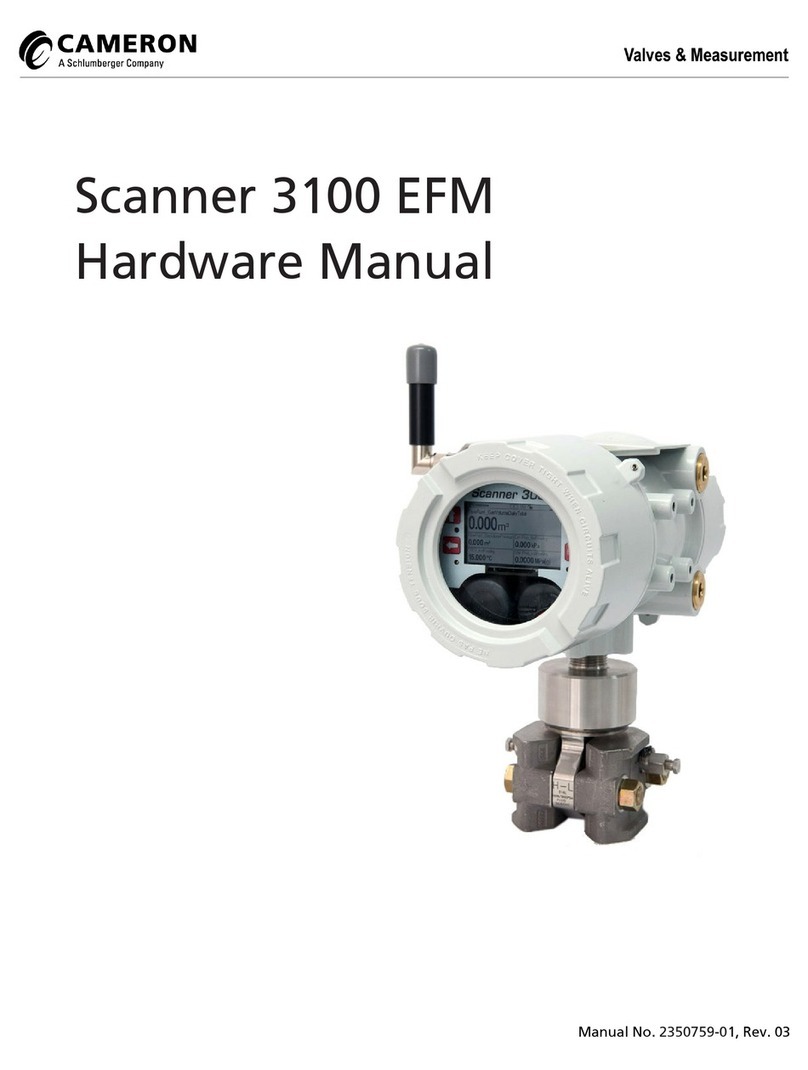
Cameron
Cameron Scanner 3100 EFM Hardware manual
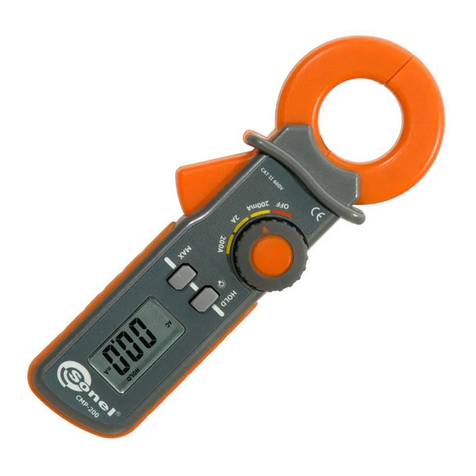
Sonel
Sonel CMP-200 operating manual
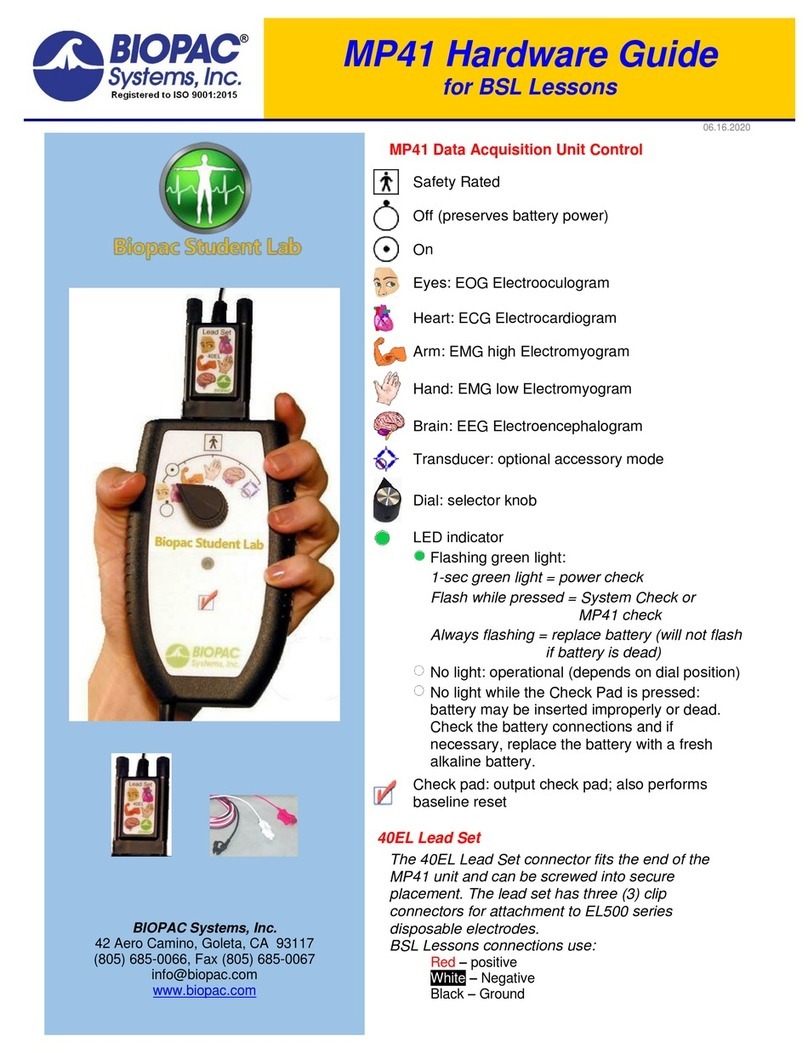
BIOPAC Systems
BIOPAC Systems MP41 Hardware guide

Endress+Hauser
Endress+Hauser Proline Promass F 500 operating instructions
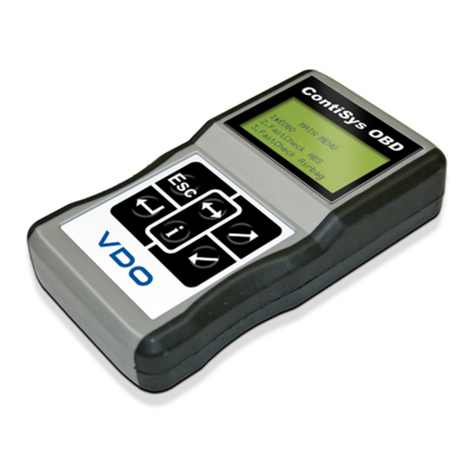
VDO
VDO CONTISYS OBD - Quick reference guide