SRS Labs SR430 User manual

Multichannel
Scaler/Averager
Model SR430
1290 D Reamwood Avenue
Sunnyvale, CA 94089 USA
Phone: (408) 744-9040 • Fax: (408) 744-9049
Copyright©1999
All Rights Reserved
Revision 1.5• 8/2007
Stanford Research Systems


1
CONDENSED INFORMATION
Safety and Preparation for Use 3
Symbols 4
Specifications 5
Quick Performance Check 8
Abridged Command List 9
INSTRUMENT OVERVIEW
SR430 Overview 11
Trigger and Sync/Busy 11
Bin Clock Output 12
Ext Bin Clk Input 12
Signal Input and Discriminator 12
Timing 13
Data Acquisition 13
Add, Subtract, Toggle, and Inhibit 13
Aux, Test, Disk, and Interfaces 14
OPERATION
Front Panel Overview 15
Power 15
Video Display 15
Soft Keys 15
Keypad 16
Spin Knob 16
Disk Drive 16
BNC Connectors 16
Screen Display 17
Data Display 17
Cursor Display 18
Menu Display 18
Data Acquisition Status 18
Status Indicators 19
Keypad 21
Normal and Alternate Keys 21
START and STOP/RESET 21
Menu Keys 22
Entry Keys 22
CURSOR 22
AUTOSCALE 22
PEAK 23
CENTER 23
NORM 23
PRINT 23
HELP 23
LOCAL23
Rear Panel 25
Power Entry Module 25
IEEE-488 Connector 25
RS232 Connector 25
Parallel Printer Connector 25
PC Keyboard Connector 26
BNC Connectors 26
MENUS
Levels Menu 27
Mode Menu 29
Display Menu 35
Setup Menu 37
Save Menu 47
Recall Menu 53
Math Menu 59
Plot Menu 67
Test Menu 69
Info Menu 73
INSTRUMENT SETUPS
Default Setup / Power On Clear 75
Choosing Bin Width & Record Length 76
Accumulation 76
Using the Trigger Offset 76
Using SYNC/BUSY76
REMOTE PROGRAMMING
GPIB Communications 79
RS232 Communications 79
Status Indicators and Queues 79
Command Syntax 79
Interface Ready and Status 80
Detailed Command List 81
Level Control Commands 81
Mode Control Commands 82
Display Control Commands 83
Setup Commands 85
Save and Recall Commands 86
Math Operation Commands 87
Print and Plot Commands 89
Data Acquisition Control Commands 89
Data Transfer Commands 90
Interface Control Commands 91
Status Reporting Commands 91
Status Byte Definitions 92
Serial Poll Status Byte 92
Standard Event Status Byte 92
MCS Status Byte 93
Error Status Byte 94
TABLE OF CONTENTS

2
File Formats
Trace File 95
Settings File 95
Program Examples 97
IBM PC BASIC, RS232 97
Microsoft C, Nat'l Instruments GPIB 99
IBM PC BASIC, Nat'l Instruments
GPIB 101
TEST AND CALIBRATION
Power 103
Screen Brightness 103
Fan 103
Front Panel Tests 103
Power On Reset 103
Testing Data Acquisition Hardware 103
Counting Problems 104
Calibration 105
Signal Inputs 105
USING PHOTOMULTIPLIER TUBES
PMT Selection for Photon Counting 107
Geometry 107
Spectral Response 107
Gain and Risetime 107
Dark Counts 107
PMT Base Design 108
Dynode Biasing 108
Snubbing 109
Cathode Shielding 110
Magnetic Shielding 110
Preamplifiers 110
Gain Requirement 111
Plateauing a PMT 111
The 'Fast and Pretty Good' Way 111
TYPICAL EXPERIMENT
Energy Levels of Ruby 113
Apparatus 113
Operation 113
Instrument Configuration 114
Data Acquisition 114
CIRCUIT DESCRIPTION
Circuit Boards 115
Video Driver and CRT 116
CPU Board 116
Microprocessor System 116
Keypad Interface 116
Keyboard Interface 116
Spin Knob 117
Speaker 117
Clock/Calendar 117
Printer Interface 117
Video Graphics Interface 117
Disk Controller 117
GPIB Interface 117
RS232 Interface 117
Expansion Connector 117
Power Supply Board 118
Unregulated Power Supplies 118
Power Supply Regulators 118
ECL Logic Board 119
Signal Input 119
Discriminators 119
200 MHz Clock and Trigger Sync 119
Bin Clock Generator 119
Pulse Sorter 120
Counters 120
Shift Register Inputs 120
Control Signals 121
TTL Logic Board 121
Fast Record Buffers 121
Fast Buffer Address Counter 121
Accumulator 122
Copy Buffer Address Counter 122
Status and IO 122
Digital to Analog Converter 123
PARTS LISTS 125
Control Board 125
Power Supply Board 129
ECL Logic Board 132
TTL Logic Board 138
Hardware 142
Miscellaneous 144
ADDENDUM 145
SCHEMATIC DIAGRAMS
CPU Board
Power Supply Board
ECL Logic Board
TTL Logic Board

3
SAFETY AND PREPARATION FOR USE
CAUTION
This instrument may be damaged if operated
with the LINE VOLTAGE SELECTOR set for the
wrong ac line voltage or if the wrong fuse is in-
stalled.
LINE VOLTAGE SELECTION
The SR430 operates from a 100V, 120V, 220V, or
240V nominal ac power source having a line fre-
quency of 50 or 60 Hz. Before connecting the pow-
er cord to a power source, verify that the LINE
VOLTAGE SELECTOR card, located in the rear
panel fuse holder, is set so that the correct ac in-
put voltage value is visible.
Conversion to other ac input voltages requires a
change in the fuse holder voltage card position
and fuse value. Disconnect the power cord, open
the fuse holder cover door and rotate the fuse-pull
lever to remove the fuse. Remove the small print-
ed circuit board and select the operating voltage
by orienting the printed circuit board to position the
desired voltage to be visible when pushed firmly
into its slot. Rotate the fuse-pull lever back into its
normal position and insert the correct fuse into the
fuse holder.
LINE FUSE
Verify that the correct line fuse is installed before
connecting the line cord. For 100V/120V, use a 1
Amp fuse and for 220V/240V, use a 1/2 Amp fuse.
LINE CORD
The SR430 has a detachable, three-wire power
cord for connection to the power source and to a
protective ground. The exposed metal parts of the
instrument are connected to the outlet ground to
protect against electrical shock. Always use an
outlet which has a properly connected protective
ground.
WARNING REGARDING USE WITH
PHOTOMULTIPLIERS
The signal inputs may be damaged if a photomulti-
plier is used improperly with the photon counter.
When left completely unterminated, a PMT will
charge a cable to a few hundred Volts in a very
short time. If this cable is connected to a signal in-
put, the stored charge may damage the front-end
transistors. To avoid this problem, provide a leak-
age path of about 100 KΩ to ground inside the
base of the PMT to prevent charge accumulation.
CONNECTION TO OTHER INSTRUMENTS
All front panel BNC shields are connected to the
chassis ground and to the power outlet ground via
the power cord. Do not apply any voltage to either
the shields or to the outputs. The outputs are not
protected against connection to any potential other
than ground.
FURNISHED ACCESSORIES
- Power Cord
- Operating Manual
ENVIRONMENTAL CONDITIONS
OPERATING
Temperature: +10°C to +40°C
(Specifications apply over +18°C to +28°C)
Relative Humidity: <90% Non-condensing
NON-OPERATING
Temperature: -25°C to +65°C
Humidty: <95% Non-condensing
WARNING: Dangerous voltages, capable of causing injury or death, are
present in this instrument. Use extreme caution whenever the instru-
ment covers are removed. Do not remove the covers while the unit is
plugged into a live outlet.

4

SR430 MULTICHANNEL SCALER / AVERAGER
GENERAL INFORMATION
The SR430 Multichannel Scaler / Averager counts incoming pulses in successive time bins. A trigger starts a
record of up to 32,704 time bins. The duration of the time bins is programmable from 5 ns to 10.5 ms. The
number of signal pulses counted during each time bin is stored in memory. There is no dead time between
bins. Each new trigger starts a record whose data is added to the bin by bin accumulation of all of the previ-
ous records. The result is a record of the sum (or average) of all counts in each time bin.
The trigger starts each record. The SYNC/BUSY output signals the beginning of the first time bin of the
record. The BIN CLOCK output signals the boundaries of each time bin. During each time bin, input signal
pulses are counted. At the end of the time bin, the counter data is stored in memory and the counter is reset.
The double buffered design ensures that there is no dead time between bins and no pulses are missed at the
bin boundaries.
After the record is complete, the data is added to the accumulation of all previous records. This only occurs
after the record of data is acquired and results in a accumulation dead time of 250 ns X number of bins in the
record (8 ms for 32k bins). After the accumulation is complete, the memory is re-armed for the next trigger.
The number of records accumulated is programmable 1 to 65,535 (or free run). The count capacity is 32,767
per bin per trigger. The total accumulation capacity per bin is also 32,767. The SYNC/BUSY output for each
record remains high from the trigger until the end of accumulation. When SYNC/BUSY returns low, another
trigger can be received.
The SR430 offers advanced functions such as Autoscale, Smoothing, Curve Fitting, non-volatile setup mem-
ories, data storage to disk, push button hardcopy to graphics printers and plotters, and GPIB and RS-232 in-
terfaces. The SR430 is also easy to use. It has a menu based user interface which makes front-panel adjust-
ments intuitive and straightforward. Entries are made with the front-panel knob or numeric keypad. On screen
help is available at all times.
SPECIFICATIONS
SIGNAL INPUT
Bandwidth dc to 250 MHz
Input impedance
50 Ω
Linear range ±300 mV (at input)
Input protection ±5 VDC, 50 V for 1 µs
Overload recovery 5 ns for <10 µs duration overload
DISCRIMINATOR
Referred to the signal input:
Discriminator range -300 mV to +300 mV
Resolution 0.2 mV
Slope Positive or Negative
Accuracy 2 mV + 1%
Minimum pulse input amplitude 10 mV
Pulse pair resolution 10 ns (typical)
DISC view output
NIM level into 50 Ω
There is a 20 ns insertion delay from signal input to discriminator out-
put.
TRIGGER INPUT
Impedance
10 kΩ
Threshold -2.000 V to +2.000 V in 1 mV steps
Slope Rising or Falling
5

6
SR430 Multichannel Scaler
Protection
15 VDC, 100 V for 1 µs
INTERNAL TIME BINS
Bin width
5 ns, 40 ns, 80 ns, 160 ns, 320 ns, 640 ns, 1.28 µs, 2.56 µs, ...
10.486 ms. (10 ns or 20 ns bins are not available)
Accuracy
1 ns + 20 ppm of bin width
Jitter (rms)
100 ps + 10 ppm of delay from SYNC/BUSY output (Time bins are
synchronous with the SYNC/BUSY output).
Indeterminacy
2.5 ns pk-pk with respect to the TRIGGER input
Insertion delay
45 ns from trigger to first bin. Rising edge of SYNC/BUSY output oc-
curs at the beginning of the first bin. However, signal pulses arriving
25 ns after the trigger will be counted in the first bin.
EXTERNALLY CLOCKED TIME BINS
EXT BIN CLK Input
Rising edge triggers next time bin.
Maximum frequency
4 MHz (250 ns minimum bin width)
Minimum pulse width high
100 ns
Minimum pulse width low
100 ns
Insertion delay
Rising edge of SYNC/BUSY output occurs at first rising edge of EXT
BIN CLK after TRIGGER. The beginning of the first bin occurs at the
same time. (Time bins are synchronous with the SYNC/BUSY out-
put).
COUNTERS/ACCUMULATION
Bins per record
1k to 16k in 1k increments (1024 to 32,704 including Trigger Offset)
Maximum count rate
100 MHz
Maximum count
32,767 per bin per trigger
Records per accumulation
1 to 64k (or free run)
Maximum accumulation
32,767 per bin in Add mode, ±16,383 per bin in Toggle, or External
mode.
Add/Subtract
Records may be added or added an subtracted (Toggle between add
and subtract every N triggers where N is programmable). External
subtract input may also control the toggle.
TRIGGER RATE
Minimum period between triggers
Tp=Record time + Accumulation time + Overhead
=(Number of Bins X Bin Width)+(Number of Bins X 250 ns)+150
µs
SYNC/BUSY output is high for Tp after each trigger. When
SYNC/BUSY returns low, the next record may be triggered. Triggers
received while SYNC/BUSY is high are ignored.
OUTPUTS
DISC
Nim level into 50 Ω. Low whenever the signal input exceeds the dis-
criminator level with the correct slope.
SYNC/BUSY
TTL level. Rising edge is synchronous with the first time bin of each
record. Use this edge to trigger the experiment. Remains high until
re-armed for next trigger.
BIN CLK OUTPUT
Nim level into 50 Ω. Each transition is a bin boundary. Active only
while a record is being acquired. Timing skew relative to the DISC
output is less than 2 ns.
TOGGLE
TTL level. Indicates whether the next record will be added to or sub-
tracted from the accumulation. (Internal toggle mode)
TEST
50 MHz Nim output into 50 Ω. Use to test counters.
AUX1, AUX2
General purpose analog outputs
Full scale
±10 VDC
Resolution
12 bits (5 mV)

7
SR430 Multichannel Scaler
Output current rating
10 mA
Output impedance
<1 Ω
Accuracy
0.1% + 10 mV
INPUTS
SIGNAL
Analog 50 Ω input.
TRIGGER
10 kΩ input.
BIN CLK INPUT
TTL input. Rising edge triggers next time bin
ACCUMULATOR INHIBIT
TTL input, sampled each trigger. If high, causes the current record to
be ignored (not accumulated)
SUBTRACT
TTL input, sampled each trigger. If high, causes the current record to
be subtracted from the accumulation ( in external toggle mode).
GENERAL
Interfaces
IEEE-488 , RS-232, and Centronics Printer standard. All instrument
functions can be controlled and read through the IEEE-488 and RS-
232 interfaces.
Hardcopy
Screen dumps to Epson compatible dot matrix or HP LaserJet print-
ers (parallel). Plots to HPGL compatible plotters (serial or IEEE-488).
Disk
3.5" MSDOS compatible format, 720kbyte capacity. Storage of data
and setups.
Power
60 Watts, 100/120/220/240 VAC, 50/60 Hz
Dimensions
17"W X 6.25"H X 16.5"L
Weight
30 lbs
Warranty
One year parts and labor on materials and workmanship

8
SR430 Multichannel Scaler
SR430 Quick Performance Check
Be sure to read the Overview and Operations sections of the manual to familiarize yourself with the instru-
ment.
This setup requires a 1 Hz to 2 kHz TTL trigger source. A simple function generator will suffice.
Hold down the CLR key while turning the unit on. This resets the SR430 to its default state.
Connect the trigger source to the TRIGGER input on the front panel. Set the Trigger Level and Slope in the
LEVELS menu appropriately for the trigger source. Use a 5 foot length or longer BNC cable to connect the
TEST output on the rear panel to the SIGNAL input on the front panel. Set the Disc Level to -300 mV and the
Disc Slope to Falling.
Set the trigger rate to 1 kHz. Press the START key. Data acquisition should begin. The default bin width is 5
ns and the record length is 1k. 1000 records will be accumulated. When the scan is done, press AUTOSCALE
to scale the display. The TEST output is a 50 MHz signal so a pulse occurs every 20 ns or every 4 bins. The
data should have 1000 counts in every 4th bin.
Use the Mode menu to select different bin widths and records per scan. Records with longer bin widths trigger
at lower rates so the trigger rate needs to be lowered to avoid RATE errors. Use the formula for Tbusy in the
Specifications section of the manual to calculate the maximum trigger rate for each bin width and record
length. Longer bin widths also require a smaller number of records per scan to avoid overflow. This is be-
cause each bin acquires a larger number of counts per trigger.
Bin widths of 40 ns and longer will collect data in every bin. The first bin may have 1 less count per trigger
than the other bins. For longer bin widths 163 µs or longer, the data may vary up to ±7 counts per bin per trig-
ger. This is due to the jitter in the longer bin widths.
After acquiring data, use the other menus to scale the data, smooth or perform calculations with the data,
save and recall data to disk, etc.

9
SR430 Multichannel Scaler
COMMAND LIST
LEVELS
TRLV(?) {x}
Set the Trigger Level to -2.000 <= x <= 2.000 V.
TRSL(?) {i}
Set the Trigger Slope to Positive (0) or Negative (1).
DCLV(?) {x}
Set the Discriminator Level to -0.3000 <= x <= 0.3000 V.
DCSL(?) {i}
Set the Discriminator Slope to Positive (0) or Negative (1).
AUX1(?) {x}
Set the AUX1 Level to -10.000 <= x <= 10.000 V.
AUX2(?) {x}
Set the AUX2 Level to -10.000 <= x <= 10.000 V.
MODE
BCLK(?) {i}
Set the Bin Clock Source to Internal (0) or External (1).
BWTH(?) {i}
Set the internal Bin Width to 5 ns (0) through 10.486 ms (19).
BREC(?) {i}
Set the number of Bins Per Record to 1 ≤ i ≤ 16 times 1024.
RSCN(?) {i}
Set the number of Records Per Scan to 0 ≤ i ≤ 65535.
BOFF(?) {i}
Set the Trigger Offset to 0 ≤ i ≤ 16320 in increments of 16.
ACMD(?) {i}
Set the Accumulate Mode to Add (0), Toggle (1), or External (2).
TCNT(?) {i}
Set the Toggle Count to 1 ≤ i ≤ 16384.
PTOG(?) {i}
Set the Pause At Toggle mode Off (0) or On (1).
REAC
ReAcquire count data from data acquisition memory.
ROFF(?) {i}
Set the ReAcquire From Offset to 0 ≤ i ≤ Trigger Offset in increments of 16.
DISPLAY
AUTS
AutoScale the graph. Same as [AUTOSCALE] key.
CRPK
Move the cursor to the on screen peak. Same as [PEAK] key.
BUGP?
Query the Cursor Marker bin number.
CNTR
Translate the graph to center the cursor. Same as [CENTER] key.
LEFT(?) {i}
Set the Left edge of the graph to bin #i.
BOTM(?) {i} {x}
Set the Bottom of the graph to i counts or x value.
HSCL(?) {i}
Set the Horizontal Screen Width to 8 bins (0) through 16k bins (22).
VSCL(?) {i} {x}
Set the Vertical Scale to i counts/division or x/division in a 1-2-5-10 sequence.
CURS(?) {i}
Turn the Cursor Off (0) or On (1).
CURW(?) {i}
Set the Cursor Width to Normal (0), Wide (1), or Spot (2).
CURM(?) {i}
Set the Cursor Seek Mode to Maximum (0), Minimum (1), or Mean (2).
GRID(?) {i}
Turn the Grid Off (0) or On (1).
SETUP
OUTP(?) {i}
Set the Output Interface to RS232 (0) or GPIB (1).
KCLK(?) {i}
Turn the Key Click Off (0) or On (1).
ALRM(?) {i}
Turn the Alarms Off (0) or On (1).
THRS(?) {i}
Set the Hours to 0 ≤ i ≤ 23.
TMIN(?) {i}
Set the Minutes to 0 ≤ i ≤ 59.
TSEC(?) {i}
Set the Seconds to 0 ≤ i ≤ 59.
DMTH(?) {i}
Set the Month to 1 ≤ i ≤ 12.
DDAY(?) {i}
Set the Day to 1 ≤ i ≤ 31.
DYRS(?) {i}
Set the Year to 0 ≤ i ≤ 99.
PLTM(?) {i}
Set the Plotter Mode to RS232 (0) or GPIB (1).
PLTB(?) {i}
Set the Plotter Baud Rate to 300 (0), 1200 (1), 2400 (2), 4800 (3), 9600 (4).
PLTA(?) {i}
Set the Plotter GPIB Address to 0 ≤ i ≤ 30.
PLTS(?) {i}
Set the Plot Speed to Fast (0) or Slow (1).
PNTR(?) {i}
Set the Trace Pen Number to 1 ≤ i ≤ 6.
PNGD(?) {i}
Set the Grid Pen Number to 1 ≤ i ≤ 6.
PNAP(?) {i}
Set the Alphanumeric Pen Number to 1 ≤ i ≤ 6.
PNCR(?) {i}
Set the Cursor Pen Number to 1 ≤ i ≤ 6.
PNFT(?) {i}
Set the Fit Pen Number to 1 ≤ i ≤ 6.
PRNT(?) {i}
Set the Printer Type to Epson (0) or HP (1).
SAVE AND RECALL
FNAM(?) {string}
Set the current
File Name to

10
SR430 Multichannel Scaler
string.
SVTR
Save the Trace Data to the file specified by FNAM.
SVST
Save the Settings to the file specified by FNAM.
SVSS
Save the System Configuration to the file specified by FNAM.
RCTR
Recall the Trace Data from the file specified by FNAM.
RCST
Recall the Settings from the file specified by FNAM.
RCSS
Recall the System Configuration from the file specified by FNAM.
MATH
SMTH i
Smooth the data using 5 pts (0), 11 pts (1), 17 pts (2), 21 pts (3), or 25 pts (4).
FTYP(?) {i}
Set the Fit Type to Line (0), Exponential (1), or Gaussian (2).
FITS
Start the Fit Calculation.
PARS? i
Query Fit Parameter t0 (0), a (1), b (2), or c (3).
LLIM(?) {i}
Set the Left Limit of the curve fit region to bin #i where 0 ≤ i < Right Limit.
RLIM(?) {i}
Set the Right Limit of the curve fit region to bin #i where Left Limit < i ≤ Last bin in record.
CALC
Start a Calculation
ARGT(?) {i}
Set the calculation Argument type to Constant (0), or File (1).
ARGM(?) {i}
Set the Constant Argument to x.
STAT
Start the Statistical Calculations.
SPAR? i
Query Statistical Parameter mean (0), deviation (1), area (2), baseline area (3).
PRINT AND PLOT
PRSC
Print the screen. Same as [PRINT] key.
PALL
Plot the entire screen.
PTRC
Plot the trace only.
PCUR
Plot the cursor only.
DATA ACQUISITION CONTROL
SSCN
Start data acquisition. Same as [START] key.
PAUS
Pause a scan in progress. Same as [STOP] key while BUSY.
CLRS
Reset the data memory. Same as [STOP] key while DONE.
SCAN?
Query the number of records which have been accumulated so far.
DATA TRANSFER
BINA? {i}
Read the entire data record in ASCII format. If i included, read only bin #i data.
BINB?
Read the entire data record in binary format.
INTERFACE
*RST
Reset the unit to its default configurations.
*IDN?
Read the SR430 device identification string.
LOCL(?) {i}
Set the Local/Remote state to LOCAL (0), REMOTE (1), or LOCAL LOCKOUT (2).
STATUS
*CLS
Clear all status registers.
*ESE(?) {i}
Set the Standard Status Byte Enable Register to the decimal value i (0-255).
*ESR? {i}
Query the value of the Standard Status Byte. If i is included, only bit i is queried.
*SRE(?) {i}
Set the Serial Poll Enable Register to the decimal value i (0-255).
*STB? {i}
Query the value of the Serial Poll Status Byte. If i is included, only bit i is queried.
*PSC(?) {i}
Set the value of the Power-On Status Clear bit to Set (1) or Clear (0).
ERRE(?) {i}
Set the Error Status Enable Register to the decimal value i (0-255).
ERRS? {i}
Query the value of the Error Status Byte. If i is included, only bit i is queried.
MCSE(?) {i}
Set the MCS Status Enable Register to the decimal value i (0-255).
MCSS? {i}
Query the value of the MCS Status Byte. If i is included, only bit i is queried.

INSTRUMENT OVERVIEW
record can only acquire 4 counts per bin maximum
(4 * 10 ns = 40 ns). If the bins width is 5 ns, then
the maximum number of counts per bin is 1. The
maximum count capacity of each bin is 32,767.
When the bin width is large and the count rate is
high, it is possible to exceed the count capacity of
a bin in a single record. In this case, the data will
overflow and be stored as the maximum count
(32,767).
A single record can capture a transient counting
signal if there are enough counts to be statistically
significant in a single shot. If the count rate is very
low but the signal is repetitive, then multiple
records may be accumulated. Accumulation of
records means simply taking each new record and
adding it to the sum of all previous records on a
bin by bin basis, i.e. data from T1of each record is
summed together, data from T2of each record is
summed together, etc. Accumulation reduces sta-
tistical noise since the accumulated counts in each
bin will be larger than the data from a single
record. Each bin can accumulate counts up to
32,767. Additional counts will cause an overflow
and the data will be stored as 32,767. If this limit is
reached, then the bin width should be reduced and
the bins per record increased (to keep the same
record time). This will divide the bins which over-
flowed, into 2 or more smaller bins, each capable
of 32,767 counts. Thus, more total counts may be
accumulated for the same record time.
A scan is an accumulation of a number of records.
The number of records in a scan may be pro-
grammed from 1 to 65,535.
SR430 OVERVIEW
The SR430 data acquisition timing is diagrammed
below. A trigger starts a record of up to 32,704
time bins (T1, T2, ... TN). Each time bin is of equal
duration and is programmable from 5 ns to 10 ms.
There is no dead time between time bins. During
each time bin, signal pulses are counted. At the
end of each time bin, the counter data is stored in
memory. The memory address is then increment-
ed and the counter is reset for the next time bin.
Thus, a record is a list of counter data points cor-
responding to counts received in successive time
bins. Counts which arrive at a bin boundary are
not missed but either fall in the bin just ending or
in the bin just starting.
The number of bins per record is set in 1k incre-
ments from 1k (1024) to 16k (16,384). This repre-
sents the maximum number of bins which can be
displayed and analyzed at one time. This limitation
is due to the data display buffer having a maxi-
mum capacity of 16k data points. The data acqui-
sition memory, however, can store up to 32k data
points. Up to 32,704 bins may actually be acquired
and accumulated, of which, up to 16k bins may be
displayed at a time. The Trigger Offset determines
how many bins are skipped at the beginning of the
total record before data is transferred to the dis-
play buffer.
The maximum count rate is 100 MHz or one count
every 10 ns. Thus, short bins can only acquire a
small number of counts per bin in a single record.
For example, if the bin width is 40 ns, then a single
TIMING DIAGRAM
TRIG
BIN CLK TT
1
SYNC/
BUSY
T2ACCUMULATION AND
PROCESSING TIME
TBUSY
N
T3
20 ns
SIGNAL
INPUT
DISC
OUT
BIN WIDTH
45 ns
11

12
Instrument Overview
TRIGGER and SYNC/BUSY
Data acquisition is started by a trigger. The TRIG-
GER input is on the front panel. The trigger thresh-
old is adjustable from -2V to +2V and the slope
may be either RISE or FALL.
The SYNC/BUSY output is a TTL level signal
which serves two purposes. First, it can be used to
synchronize the experiment timing with the actual
time bins of each record. Second, it indicates
when the unit is busy acquiring data and cannot
be triggered.
After a trigger is recognized, the SYNC/BUSY out-
put will go high indicating the start of the first time
bin. The insertion delay from TRIGGER to SYNC/
BUSY is 45 ns. SYNC/BUSY will have 2.5 ns of in-
determinacy with respect to the trigger. As a re-
sult, the entire record starts with 2.5 ns of uncer-
tainty with respect to the trigger. This is not a
problem if the bin width is much longer than 2.5 ns
but may be a problem for shorter bin widths. In
these cases, the SYNC/BUSY output should be
used to trigger the experiment. Since the record is
synchronized to SYNC/BUSY, there will be no in-
determinacy of the time bins with respect to the
experiment. One way to accomplish this is to trig-
ger the SR430 with the experiment's master rate
generator and use the SYNC/BUSY (which is de-
layed from trigger by only 45 ns) to trigger the ac-
tual experiment.
After a trigger, the unit is busy acquiring and accu-
mulating data. During this busy time, no new trig-
gers will be recognized. After SYNC/BUSY returns
low, a new trigger may occur. The busy time is
T
busy
= (N*T
bin
) + (N*250 ns) + 150 µs
where T
bin
is the bin width (5 ns to 10.5 ms) and
N is the number of bins per record (1024 to
32704). The first term is the actual record length
and equals the real time duration of the data ac-
quisition. Counts received during the time N¥T
bin
after the trigger are captured. The second term is
the time needed to accumulate the record, i.e. add
the data to the sum of all previous data. Accumula-
tion takes 250 ns per bin. The last term is a fixed
overhead for processing. For example, if N=1k
bins and T
bin
= 5 ns, then T
busy
= 411 µs. The
maximum trigger rate would then be 2400 Hz.
When the bin width is programmed to be much
larger than 250 ns, then the busy time is almost to-
tally due to the real time data acquisition and virtu-
ally no time is lost processing or accumulating.
SYNC/BUSY is only output during actual data ac-
quisition. Triggers that arrive when the unit is not
acquiring data will not cause a SYNC/BUSY out-
put.
BIN CLOCK OUTPUT
The front panel BIN CLK output is a 50 ½, NIM lev-
el signal showing the bin boundaries. The first
bin,T
1
, is the time period when the BIN CLK is
first low following a trigger. Each rising and falling
transition of the BIN CLK marks the boundary of a
bin. Thus, the second bin, T
2
, is when BIN CLK is
next high, T
3
is when BIN CLK is low again, etc.
The first bin starts synchronously with the SYNC/
BUSY output. BIN CLK may be used with the
DISC OUT signal to determine the exact timing of
the counts with respect to the time bins.
BIN CLK is only output during actual data acquisi-
tion. Triggers that arrive when the unit is not ac-
quiring data will not cause a BIN CLK output.
EXT BIN CLK INPUT
The front panel EXT BIN CLK input is a TTL input
which allows an external source to determine the
bin boundaries. When the bin width mode is pro-
grammed to EXTERNAL, the EXT BIN CLK will
clock the bins. After a trigger, the first rising edge
of the EXT BIN CLK will start the first bin. SYNC/
BUSY goes high at the same time. Each new ris-
ing edge of the EXT BIN CLK will clock the start of
a new bin. The maximum external clock rate is 4
MHz or a 250 ns minimum external bin width. The
EXT BIN CLK is useful if bins longer than 10.5 ms
are required, or when the bins must be synchron-
ized to external events.
SIGNAL INPUT AND DISCRIMINATOR
The analog signal input is labelled SIGNAL INPUT
on the front panel. This input is internally terminat-
ed into 50 ½. The input can accept signals of ei-
ther polarity up to ±300 mV and is protected to
±5V dc. The input is followed by a dc to 250 MHz
amplifier. This allows detection of pulses as small
as 10 mV. If greater sensitivity is required, the
SR440 remote pre-amplifier can be used. The
SR440 can provide gains from 5 to 125 at band-
widths exceeding 200 MHz.
Following the input amplifier is a discriminator.
The discriminator has selectable slope and a
threshold programmable from -300 mV to +300
mV in 0.2 mV steps (referred to the inputs). Pulse-
pair resolution is 10 ns and pulses of either

13
Instrument Overview
polarity may be detected.
The discriminator output is labelled DISC OUT on
the front panel. The DISC OUT is a 50 ½, NIM lev-
el signal showing the actual input to the counter.
The output is active low (-0.7 V) and counting oc-
curs on the falling edge. The output is low when
the signal input exceeds the threshold level with
the correct slope, i.e. the signal is higher than the
threshold with positive slope or the signal is lower
than the threshold with negative slope.The DISC
outputs are very useful when adjusting discrimina-
tor thresholds or determining the exact timing of
the counts relative to the time bins.
The DISC OUT is active at all times. Whenever a
signal pulse exceeds threshold with the correct
slope, a pulse is output at DISC OUT. The unit
does not have to be actively acquiring data. This
enables setting the discriminator threshold without
triggering the unit.
TIMING
The DISC OUT signal is delayed internally by 20
ns so that the DISC OUT and the BIN CLK output
are correct relative to each other. In other words, a
DISC OUT pulse which falls in the first BIN CLK
will be counted in the first bin. However, a DISC
OUT pulse is actually due to a signal pulse arriving
20 ns earlier at the SIGNAL INPUT. This means
that BIN CLK and DISC OUT, when viewed on a
scope using equal length cables terminated into
50 ½, are accurately timed. However, for timing
purposes, each output viewed by itself is 20 ns
late relative to the trigger. Since the insertion delay
for the BIN CLK is 45 ns, signal pulses arriving 25
ns after the trigger will be output at the DISC OUT
45 ns after the trigger and counted in the first bin.
For accurate timing, it is best to use DISC OUT
and BIN CLK, rather than SIGNAL INPUT and BIN
CLK since the latter pair are skewed by 20 ns.
Thus, even though the BIN CLK is output with a 45
ns insertion delay relative to the TRIGGER, the ac-
tual insertion delay is 25 ns (20 ns less). Signal
pulses arriving 25 ns after the TRIGGER will be
counted.
Note that SYNC/BUSY and BIN CLK are only out-
put only during actual data acquisition while the
DISC OUT is active all of the time.
DATA ACQUISITION
To begin acquiring data, the number of bins per
record and the number of records per scan must
be programmed. The record length, N, is the num-
ber of time bins in a single record. Each trigger will
take N data points corresponding to N sequential
time bins. N may be programmed from1024 to
32704 (including Trigger Offset).
Records are accumulated until the number of
records per scan, R, have been acquired. R may
be programmed from 1 to 65536. If R is set to 0
(free run), then accumulation continues without
end. This mode is convenient when timing an ex-
periment since BIN CLK and SYNC/BUSY are out-
put only when data is being acquired. When R is
0, every trigger will output SYNC/BUSY and BIN
CLK without stopping after a programmed number
of triggers.
After the record length and scan length have been
programmed, data acquisition can be started.
When the [START] key is pressed or a START
command is received from the computer interface,
data acquisition begins. The next TRIGGER will
start the first record and count data will be stored.
Successive triggers will acquire records which are
accumulated until the number of records per scan
have been taken. During this time, the unit is
BUSY and the SYNC/BUSY and BIN CLK outputs
are active. After the number of records per scan
have been accumulated, data acquisition is halted.
The unit is now in the DONE state. Triggers which
arrive while the unit is DONE are ignored and
SYNC/BUSY and BIN CLK are inactive.
When the data acquisition is DONE, the final accu-
mulated data is displayed on the screen and may
be analyzed and manipulated. Before taking data
again, the current data must be cleared by press-
ing the [STOP/RESET] key or sending the RESET
command via the computer interface. This will
clear the count memory and the display. The unit
will now be in the CLEAR state. While in the
CLEAR state, the data acquisition setup may be
altered. A new record length or bin width may be
programmed, etc. The [START] key will start data
acquisition once again and put the unit in the
BUSY state.
ADD, SUBTRACT, TOGGLE, and INHIBIT
Normally, records are accumulated by summing
corresponding bin data from successive records.
Records may also be subtracted from the accumu-
lation. The accumulation mode may be set to
ADD, SUBTRACT, TOGGLE, or EXTERNAL.
ADD will sum new records to the accumulation.
SUBTRACT will subtract new records from the ac-
cumulation.

14
Instrument Overview
TOGGLE will switch between ADD and SUB-
TRACT every M records where M is programma-
ble. In this mode, the rear panel TOGGLE OUT-
PUT will be TTL high before the trigger of those
records which will be subtracted.
EXTERNAL will subtract records whenever the ex-
ternal SUBTRACT INPUT is TTL high. The SUB-
TRACT INPUT is sampled at the trigger and will
determine whether that record will be added or
subtracted.
The rear panel INHIBIT INPUT is used to ignore a
record. If INHIBIT is TTL high when the trigger is
received, that record is ignored and not accumulat-
ed. The record does count towards the number of
records accumulated.
AUX 1, AUX 2
The rear panel AUX 1 and AUX 2 outputs are pro-
grammable general purpose dc analog outputs.
The output voltages may be set from the front pan-
el or computer interface and can range from -10V
to +10V. These outputs may be used wherever an
external variable dc voltage is required
TEST
The rear panel TEST output is a 50Ω, NIM level
output. The output frequency is 50 MHz and is
synchronous with the BIN CLK. The TEST output
is used to test that the counter and accumulator
are working properly. By connecting the TEST out-
put to the SIGNAL input, a known number of
counts can be put into every time bin. This allows
the user to quickly check the functionality of the
unit.
DISK DRIVE
The 3.5" disk drive is used to save data, setups,
and configurations. The format is DOS compatible
and the capacity is 720k.
COMPUTER INTERFACES
RS232 and GPIB (IEEE-488) interfaces are stan-
dard on the SR430. All settings of the instrument
may be controlled via the computer interfaces.
Data may also be transmitted to a computer.
PLOTTING
An HPGL compatible plotter may also be connect-
ed directly connected to the RS232 or GPIB inter-
face. Data will be plotted directly from the SR430
without a computer.
PRINTER
A parallel printer port is standard on the SR430.
Any EPSON compatible dot matrix graphics printer
or HP LaserJet printer may be used. Full screen
printouts may be generated by pressing the
[PRINT] key on the front panel.
KEYBOARD
An IBM PC compatible keyboard may connected
to the keyboard connector. The keyboard must op-
erate in the PC or XT mode. This is often called
the 8088 mode. The keyboard may be used to en-
ter data instead of the keypad. This is most useful
with disk file names.

GUIDE TO OPERATION
FRONT PANEL OVERVIEW
POWER BUTTON
The SR430 is turned on by pushing in the POWER
button. The video display may take a few seconds
to warm up and become visible. Adjust the bright-
ness until the screen is easily readable.The model,
firmware version, and serial number of the unit will
be displayed briefly when the power is turned on.
The memory status is also displayed. All instru-
ment settings are stored in nonvolatile memory
and are retained when the power is turned off. If
the memory check passes, then the instrument re-
turns to the settings in effect when the power was
last turned off. If there is a memory error, then the
stored settings are lost and the default settings are
used. To reset the unit into the default state, hold
down the [CLR] key while the power is turned on.
The default setup is listed in a later chapter.
VIDEO DISPLAY
The monochrome video display is the user inter-
face for data display and front panel programming
operations. The resolution of the display is 640H
by 480V. The brightness is adjusted using the
brightness control knob located at the upper left
corner. As with most video displays, do not set the
brightness higher than necessary. The display
may be adjusted left and right using the Setup
Screen function in the SETUP menu.
The main area of the display is occupied by the
data display. Data is graphed as accumulated
counts per bin on the vertical axis and bin # or
time from trigger on the horizontal axis. The graph
is continuously updated during data acquisition.
When data acquisition is DONE, the total accumu-
lated data is displayed.
A complete description of the screen display fol-
lows in the next section.
SOFT KEYS
The SR430 has a menu driven user interface. The
6 soft keys to the right of the video display have
different functions depending upon the information
displayed in the menu boxes at the right of the vid-
eo display. In general, the soft keys have two
uses. The first is to toggle a feature on and off or
to choose between 2 settings. The second is to
highlight a parameter which is then changed using
the spin knob or numeric keypad. In both cases,
the soft keys affect the parameters which are dis-
played adjacent to them.
Power Button
Brightness Control Soft Keys Spin Knob Key Pad Disk Drive
Front Panel BNC Connectors
15
Video Display

16
Guide To Operation
KEYPAD
The keypad consists of four groups of keys. The
ENTRY keys are used to enter numeric parame-
ters which have been highlighted by a soft key.
The MENU keys select a menu of soft keys.
Pressing a menu key will change the menu boxes
which are displayed next to the soft keys. Each
menu groups together similar parameters and
functions. The CONTROL keys start and stop ac-
tual data acquisition, select the cursor and auto-
scale the display. These keys are not in a menu
since they are used frequently and while display-
ing any menu. The SYSTEM keys print the screen
to a printer and display help messages. Once
again, these keys can be accessed from any
menu.
A complete description of the keys follows in the
next section.
SPIN KNOB
The spin knob is used to adjust parameters which
have been highlighted using the soft keys. Any nu-
meric entry field may be adjusted using the knob.
In addition, functions such as display zooming and
scrolling use the knob as well. In these cases, the
knob function is selected by the soft keys. The
[CURSOR] key, which can be pressed at any time,
will set the knob function to scrolling the cursor.
DISK DRIVE
The 3.5" disk drive is used to store data and instru-
ment settings. Double sided, double density disks
should be used. The disk capacity is 720k bytes
formatted. The disk format is DOS compatible.
Disks written by the SR430 may be read by PC
compatible computers equipped with a 3.5" drive
and DOS 3.0 or higher.
BNC CONNECTORS
TRIGGER
The rising or falling edge of the TRIGGER input
triggers a record. The input impedance is 10 KΩ
and the minimum pulse width is 10 ns. The trigger
level is adjustable from -2V to +2V with either
slope. The minimum pulse amplitude is 100 mV.
SYNC/BUSY
TTL output high whenever the SR430 is acquiring
or accumulating a record. Triggers received during
this time are ignored. The rising edge of SYNC/
BUSY is synchronous with the start of the first bin
and may be used to trigger the experiment to re-
move the 2.5 ns uncertainty between trigger and
SYNC/BUSY. This output is active only when the
SR430 is in the BUSY state actively accumulating
records.
SIGNAL INPUT
The SIGNAL INPUT is a 50 Ω analog input. A pho-
tomultiplier or preamplifier output is connected to
this input. The input is linear between -300 mV to
+300 mV and protected to ± 5 Vdc.
DISC OUT
The DISC output is a 50 Ω, NIM level output is ac-
tive low (-0.7 V) when the signal input exceeds the
threshold level with the correct slope. Counting oc-
curs on the falling edge.
BIN CLK OUT
The BIN CLK output is a 50 Ω, NIM level output
showing the position of the time bins. Each transi-
tion of this output is a bin boundary. This output is
active only when SYNC/BUSY is active.
EXT BIN CLK INPUT
The EXT BIN CLK is a TTL input whose rising
edges mark the bin boundaries. The maximum
clock rate is 4 MHZ. This input is active if the bin
width has been programmed to EXTERNAL.
OPTION
This connector is unused.

17
Guide To Operation
0.0 V
0.0 V
bin 0
0 msec
bottom = 0 cnts 10 cnts/Div
bin 127
1.300 msec
Record = 100
SRS bin 71
Y = 50 cnts
727.0 µsec
500 mV
Trigger Level
Trigger Slope
Disc. Level
Disc. Slope
Aux. 1 Level
Aux. 2 Level
SCREEN DISPLAY
Soft Key Definitions. Pressing the
corresponding soft key will either
highlight a field or select an option.
Data Acquisition
status (CLR, BUSY,
PAUSE, or DONE).
Cursor Region is
defined by these
dashed lines.
Cursor Marker is
located at the Min,
Max, or Mean of the
data within the
cursor region.
Left most
displayed bin and
time.
Minimum displayed Y value.
This Y value corresponds to
the bottom of the graph.
Vertical scale.
Number of records
accumulated so far.
Right most displayed
bin and time.
DATA DISPLAY
Data is graphed with accumulated counts per bin
on the Y axis and bin number or time on the X
axis. The physical size of the graph remains con-
stant while the vertical and horizontal scales may
be changed. The graph area has a dotted grid for
reference. There are 8 vertical divisions and 10
horizontal divisions. In addition to X and Y scaling,
the graph may also be translated in the X and Y di-
rections.
Data is shown in 2 modes depending upon the X
scaling. There are 496 pixels or X screen locations
across the graph. If the number of bins displayed
is less than the 496, then each data point is shown
as a horizontal line at the correct Y position. The
graph above shows data in this mode. When the
number of bins exceeds 496, then each X screen
location on the graph corresponds to multiple bins.
The data is then displayed as a vertical line at
each X screen location. The displayed line con-
nects the maximum and minimum values of the
data points at each X screen location.
The
Left
most displayed bin and time is the X val-
ue corresponding to the left edge of the graph.
Cursor Position and data
value. When surrounded by a
box, indicates that the knob
will move the cursor region.
Soft Keys
DONE
-10.0 mV

18
Guide To Operation
The
Right
most displayed bin and time is the X
value of the right edge of the graph. These values
represent the X scale and translation. The X scale
is (Right-Left)/10 per division. The horizontal scale
ranges from 16 bins to N bins across the graph.
The actual position of the displayed data within the
record is given by the Left and Right values. Bin
#0 is the first bin in the record and Bin #N-1 is the
last bin where N is the programmed number of
bins per record. The Left and Right values mark
the region of the record displayed on the graph.
The graph may be horizontally translated in incre-
ments of 1/100 of the screen or 1 bin, whichever is
larger.
The
Vertical
scale is the number of accumulated
counts per division displayed on the graph. This
value is changed whenever the vertical scale is
adjusted. The vertical scale ranges from 1 to 5000
counts per division. The
Minimum
displayed Y
value corresponds to the Y value of the bottom
edge of the graph. This value is changed whenev-
er the graph is translated up or down. The graph
may be translated in the vertical direction in incre-
ments of 1/80 of the screen or 1 count, whichever
is larger.
The
Number of Records
accumulated is dis-
played in the bottom right corner. While data is be-
ing acquired and accumulated, the graph is being
constantly updated to display the data accumulat-
ed so far. Each time the data is updated, the num-
ber of records is updated. When the scan is com-
plete, the graph will show the total accumulated
data and the number of records accumulated will
be equal to the programmed number of records
per scan. While data acquisition is in progress, the
graph shows the data accumulated and the num-
ber of records completed.
CURSOR DISPLAY
The
Cursor Region
is the graph region between
the vertical dashed lines. The cursor region may
be set to 1 division (wide), 1/2 division (norm), or a
single vertical line (spot). The cursor region does
not change with horizontal scaling. The
Cursor
Marker
is a small square which seeks the mini-
mum, maximum, or mean of the data within the
cursor region. When seeking min or max, the cur-
sor marker is located at the position of the data
point which is the min or max. This allows peaks
and valleys in the data to be easily read out. When
seeking the mean, the X position of the cursor
marker is at the center of the cursor region and the
Y position is the mean of the data within the re-
gion. When a spot cursor region is used, the cur-
sor marker is confined to a single X screen loca-
tion. However, depending upon the horizontal
scaling, each X screen location may represent
multiple data points. The cursor marker can still
seek the min, max, or mean of the data at a single
X screen location.
The
Cursor Position
displays the X position (bin
# and time) and the Y data of the cursor marker. In
the case where each X screen location represents
multiple data points, the actual bin# corresponding
to the min, max, or mean is displayed. Pressing
the [CURSOR] key will draw a box around the cur-
sor information. When the cursor readout is sur-
rounded by a box, the spin knob is to adjusts the
position of the cursor region. The cursor region
moves in increments of one X screen location or
pixel.
MENU DISPLAY
The
Soft Key
menu boxes define the functions of
the 6 soft keys at the right of the screen. The
menu boxes are grouped into menus. Pressing
each of the ten menu keys will display a different
menu of boxes. Related functions are grouped into
a single menu. In general, pressing a soft key
does one of two things. One is to toggle between 2
or 3 choices directly. An example is the Trigger
Slope box illustrated on the previous page. Press-
ing the second soft key toggles the slope between
rising and falling. The second soft key function is
to highlight an entry field and knob function. An ex-
ample would be the Trigger Level. Pressing the
first soft key will highlight the Trigger Level value.
The Trigger Level may then be adjusted with the
knob or programmed with a value using the nu-
meric entry keys. Each menu is described at
length in a following section.
DATA ACQUISITION STATUS
The
Data Acquisition
status is displayed in the
upper left corner. The acquisition status is always
displayed and is always in inverse video. CLR indi-
cates that the accumulation memory and counters
are reset. The data are all zeroes. All parameters
can be changed while in the CLR state. Pressing
the [START] key will start data acquisition and the
status will change to BUSY. While in the BUSY
state, data is graphed as it accumulates and pa-
rameters related to the data acquisition may not
be changed. When the programmed number of
records per scan has accumulated, then data ac-
quisition is DONE. The graph will show the final
accumulation. Acquisition may be paused during
BUSY by pressing the [STOP] key. The status is
then PAUSE. While in the PAUSE state, the
[START] key continues data acquisition and the
[STOP] key will reset to the CLR state. In general,
pressing the [STOP] key twice in succession will
Table of contents
Other SRS Labs Laboratory Equipment manuals
Popular Laboratory Equipment manuals by other brands
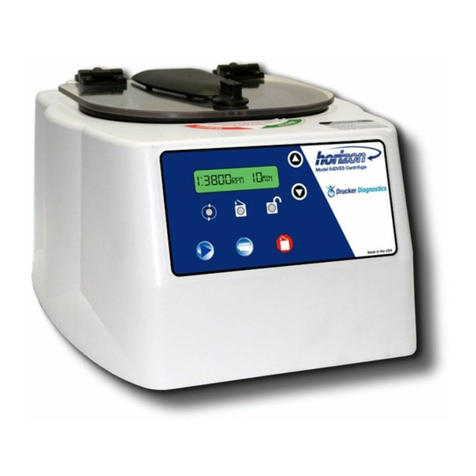
Drucker Diagnostics
Drucker Diagnostics 642VES Operator's manual
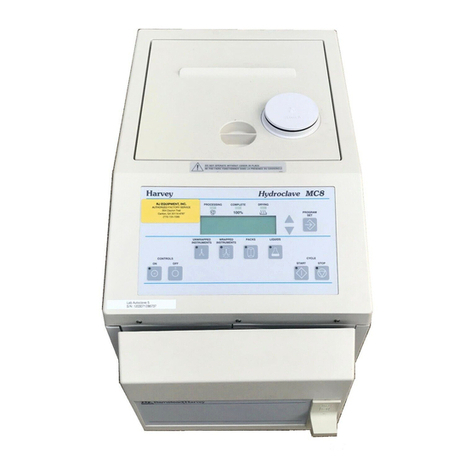
Barnstead International
Barnstead International Harvey Hydroclave MC8 Service manual
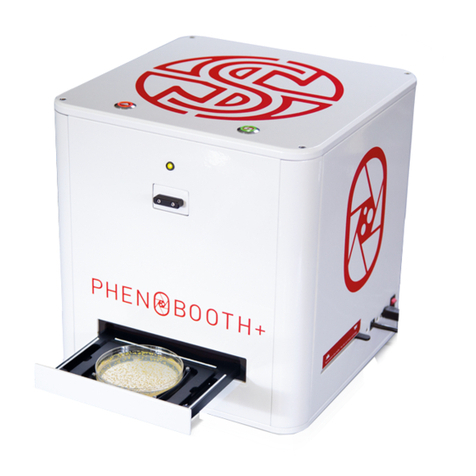
Singer Instruments
Singer Instruments PhenoBooth user guide
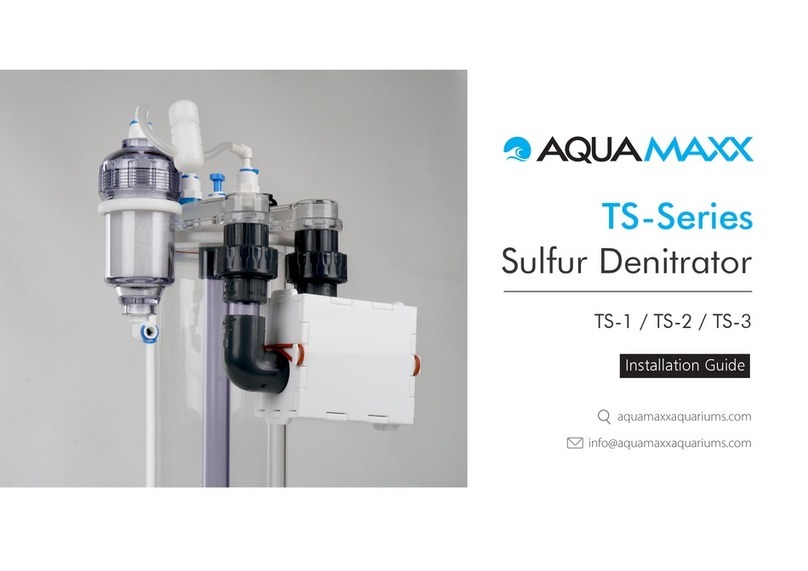
AQUAMAXX
AQUAMAXX TS Series installation guide
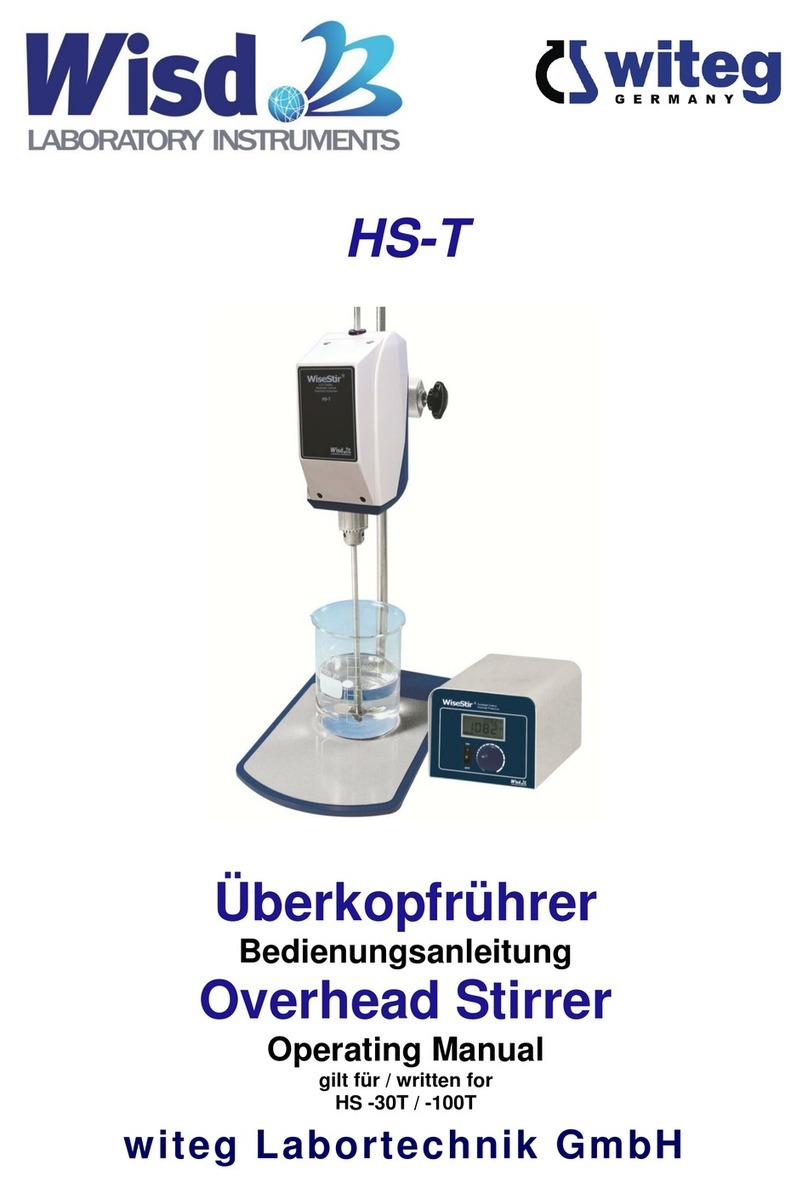
Witeg
Witeg Wisd HS-T Series operating manual

IKA
IKA HABITAT manual