Sterling Royal Series Specification sheet

-~
ARTISAN
®
~I
TECHNOLOGY
GROUP
Your definitive source
for
quality
pre-owned
equipment.
Artisan Technology
Group
Full-service,
independent
repair
center
with
experienced
engineers
and
technicians
on staff.
We
buy
your
excess,
underutilized,
and
idle
equipment
along
with
credit
for
buybacks
and
trade-ins
.
Custom
engineering
so
your
equipment
works
exactly as
you
specify.
•
Critical
and
expedited
services
•
Leasing
/
Rentals/
Demos
• In
stock/
Ready-to-ship
•
!TAR-certified
secure
asset
solutions
Expert
team
ITrust
guarantee
I
100%
satisfaction
All
tr
ademarks,
br
a
nd
names, a
nd
br
a
nd
s a
pp
earing here
in
are
th
e property of
th
e
ir
r
es
pecti
ve
ow
ner
s.
Find the Marathon Electric FVB 56T34D5825B P at our website: Click HERE

Operation and Installation Manual
Royal Series
Water Temperature
Control Units
Important! Read Carefully Before Attempting to Install or Operate Equipment
Part No. 682.88105.00 Revision G Bulletin No. SC1-610.7
Artisan Technology Group - Quality Instrumentation ... Guaranteed | (888) 88-SOURCE | www.artisantg.com

Page 2 Royal Series Water Temperature Control Units
Write down your unit serial number(s) ________________ ________________
here for future reference ________________ ________________
________________ ________________
________________ ________________
Sterling/Sterlco is committed
to a continuing program of product improvement.
Specifications, appearance, and dimensions described in this manual
are subject to change without notice.
© Copyright Sterling/Sterlco 2006
All rights reserved. Effective 3/15/06
Part No. 682.88105.00 Revision G Bulletin No. SC1-610.7
Artisan Technology Group - Quality Instrumentation ... Guaranteed | (888) 88-SOURCE | www.artisantg.com

Royal Series Water Temperature Control Units Page 3
Safety Considerations
Sterling Royal Series temperature control units are designed to
provide safe and reliable operation when installed and operated
within design specifications, following national and local safety
codes.
To avoid possible personnel injury or equipment damage when
installing, operating, or maintaining this equipment, use good
judgment and follow these safe practices:
;Only PROPERLY TRAINED personnel familiar with the
information within this manual should work on this equipment.
;Follow all local SAFETY CODES.
;Royal Series cabinets and piping are hot and are a BURN
HAZARD.
;Do not operate a Royal Series system without all outer panels
installed. Pressurized hot water leaks can cause serious injury.
;Wear SAFETY GLASSES and WORK GLOVES.
;Use care when LOADING, UNLOADING, RIGGING, or
MOVING this equipment.
;Operate this equipment within design specifications.
;OPEN, TAG, and LOCK ALL DISCONNECTS before
working on equipment. Sterling recommends following OSHA
Lock-Out/Tag-Out Standard 29 CFR 1910.147.
;Make sure the unit is properly GROUNDED before switching
power on.
;When welding or brazing in or around this equipment, be sure
VENTILATION is ADEQUATE. PROTECT adjacent
materials from flame or sparks by shielding with sheet metal.
An approved FIRE EXTINGUISHER should be close at hand
and ready for use if needed.
;Do not jump or bypass any electrical safety control.
;Do not restore power until all tools, test equipment, etc. have
been removed and the panels replaced.
Artisan Technology Group - Quality Instrumentation ... Guaranteed | (888) 88-SOURCE | www.artisantg.com

Page 4 Royal Series Water Temperature Control Units
Table of Contents
1General Information................................................6
1-1 Introduction.......................................................................................6
1-3 Models Covered ...............................................................................7
1-4 Standard Royal Series Features......................................................7
1-5 Available Options..............................................................................8
2Shipping Information.............................................12
2-1 Unpacking and Inspection..............................................................12
2-2 In the Event of Shipping Damages.................................................12
2-3 If the Shipment is Not Complete.....................................................13
2-4 If the Shipment is Not Correct........................................................13
2-5 Returns...........................................................................................13
2-6 Uncrating Your New Royal Series System.....................................14
3Installation..............................................................16
3-1 Installation Location Considerations...............................................16
3-2 Process Approach Temperature Considerations...........................16
3-3 External Piping Sizing Considerations ...........................................16
3-4 Piping Considerations for Permanent Installations ........................17
3-5 Piping Considerations for High Mobility Installations .....................18
3-6 Process Water Considerations.......................................................18
3-7 Making Process Water Connections..............................................19
3-8 Making Cooling Water Connections...............................................20
3-9 Making System Purge Connections...............................................21
3-10 Making Electrical Connections .......................................................24
4Identifying Controls and Features........................27
4-1 Identifying Mechanical Controls and Features...............................27
4-2 The Microprocessor Controller.......................................................31
4-3 Operating the Unit with the Controller............................................31
4-4 Communications.............................................................................32
5Startup and Operation ...........................................33
5-1 Introduction.....................................................................................33
5-2 Startup Checklist ............................................................................33
5-3 Starting the Temperature Control Unit ...........................................34
5-4 Sequence of Operation...................................................................35
5-5 Checking Motor Rotation Direction.................................................36
5-6 Shutting Down the Temperature Control Unit................................36
6Unit Maintenance....................................................38
6-1 Preventive Maintenance.................................................................38
Artisan Technology Group - Quality Instrumentation ... Guaranteed | (888) 88-SOURCE | www.artisantg.com

Royal Series Water Temperature Control Units Page 5
6-2 Corrective Maintenance..................................................................39
6-3 Restoring the Controller to Factory Setup......................................41
6-4 Electrical Connections....................................................................41
6-5 Safety Devices................................................................................42
6-6 Cleaning and Storage.....................................................................44
7Troubleshooting.....................................................45
IIndex........................................................................48
Artisan Technology Group - Quality Instrumentation ... Guaranteed | (888) 88-SOURCE | www.artisantg.com

Page 6 Royal Series Water Temperature Control Units
1 General Information
1-1 Introduction
Sterling/Sterlco Royal Series water temperature control units are
reliable, accurate, and easy-to-use process temperature control
units. They are self-contained, portable, and shipped ready to use.
The Royal Series water temperature control unit is designed to
circulate water through your process and to precisely,
automatically, and reliably maintain it at a specified temperature.
Standard unit operating range is from 0ºF (-17ºC) to 250°F
(121°C), or up to 300°F (149°C) as an option. The unit is suited for
use with city water, water from portable or central chillers or
towers, or well water.
These units are designed for rapid recirculation of a relatively
small amount of water to provide close and uniform temperature
relation between To Process and From Process lines. This
performance, of course, depends on the configuration of your
process and any restrictions within the mold. The recirculation,
combined with the large immersion heater and cooling capability,
gives fast and accurate response to bring the water up to
temperature or to changes in the settings when needed.
The 2010 Series water temperature control unit is a self-contained
system consisting of a centrifugal pump, electric immersion heater,
cool/vent solenoid valve, and electrical control, including a PID
microprocessor controller and thermocouple. It is designed for use
in process temperature control applications using water or a
water/glycol mix. Any other use or fluid is prohibited.
Some standard safety devices include a mechanical
overtemperature safety thermostat, a pressure relief valve, motor
overload protection, a low pressure cutout switch, branch fusing,
and non-fused lockable rotary disconnect.
A properly installed, operated, and maintained Royal Series system
provides years of reliable operation. Please read and follow the
instructions in this manual to get the most satisfaction from your
Royal Series system.
Artisan Technology Group - Quality Instrumentation ... Guaranteed | (888) 88-SOURCE | www.artisantg.com

Royal Series Water Temperature Control Units Page 7
1-2 Necessary Documents
The following documents are necessary for the operation,
installation, and maintenance of Sterling/Sterlco Royal Series
water temperature control units. Additional copies are available
from Sterling.
Familiarize the appropriate personnel with these documents:
;This manual.
;The controller operation manual.
;The electrical schematic and connection diagram placed inside
the control enclosure.
;The operation and installation manuals for accessories and
options selected by the customer.
;The Customer Parts List included in the information packet.
1-3 Models Covered
This manual provides operation, installation, and maintenance
instructions for the Royal Series water temperature control unit.
Model numbers are listed on the serial tag. A model number
followed by Qindicates a specially constructed unit, and not all
information in this manual may apply. Make sure that you know
the model number, serial number, and operating voltage of your
temperature control unit if you contact Sterling.
1-4 Standard Royal Series Features
•Compact, rugged cabinet with easy-access side panels
•Cast-and-flange design to reduce connection points
•Half- and full-heat automatic switching capability
•Dual stage Incoloy™ immersion heater with IEC contactors
•NEMA 12 electrical enclosure
•Microprocessor controller with fuzzy logic; includes
diagnostics features with indicator and warning status lights;
CE and CUL
Artisan Technology Group - Quality Instrumentation ... Guaranteed | (888) 88-SOURCE | www.artisantg.com

Page 8 Royal Series Water Temperature Control Units
•Forward-facing liquid-filled To and From Process pressure
gauges
•Independent high temperature safety thermostat
•Non-fused lockable rotary disconnect
•Branch fusing
•¼” cooling solenoid valve on ¾ to 3 hp (0.56 to 2.24 kW)
models; ½” slow-close cooling solenoid valve on 5, 7½, & 10
hp (3.73, 5.60, & 7.46 kW) models
•EPDM/NI-Resist pump seal
•Adjustable low supply water pressure switch; factory-set at
16 psig (110 kPa/1.1 bars)
•150 psig (1,034 kPa/10.3 bars) pressure relief valve
•Choice of 230 or 460 operating voltages
•¾” water supply and drain connections; 1½” process
connections
•Automatic vent sequence
•3” (76 mm) casters
•Operating range of 0ºF to 250ºF (-17ºC to 121ºC)
•Three (3) -year parts and labor warranty at the factory; five
(5) -year controller warranty, and limited lifetime warranty
on wetted pump components and pump seal; subject to
factory review
1-5 Available Options
Royal Series systems are available with options to tailor the unit to
your requirements. Some are factory installed; some can be retro-
fitted in the field. Consult your Sterling sales representative for
more information. Available Royal Series options include:
•Controller with integral flow meter; with:
Up to 30 gpm (114 lpm) flow indicator
- or -
30 to 75 gpm (114 to 284 lpm) flow indicator
0-20 mA and 4-20 mA current control output
Artisan Technology Group - Quality Instrumentation ... Guaranteed | (888) 88-SOURCE | www.artisantg.com

Royal Series Water Temperature Control Units Page 9
Remote set point and retransmission; 0-20 mA and 4-20
mA
RS-232 or RS-485 communications
Remote sensor; 10 ft. (3 m)
•Remote controller enclosure
•Heaters available in 12 kW, 18 kW, 24 kW, 36 kW, and 48
kW on direct-injection compact models; 36 kW and 48 kW
heaters available on direct-injection upright models
•Closed-loop heat exchanger available in 3.7 sq. ft. (0.344 sq.
m) on compact models; 3.7, 7.4, 11.2, 18.1, and 27.0 sq. ft.
(0.135, 0.688, 1.042, 1.683, and 2.511 sq. m) on upright
models
•Quick Cool function
•Auto system water purge (mold purge)
•Y-strainer
•Hammer arrestor (water hammer shock stop)
•Remote start/stop control
•Rubber feet; available in lieu of casters
•Non-ferrous brass construction
•Slow-close cooling solenoid valves available in 1/2” x 9/16”
(CV= 3.5) and 3/4” x 3/4” (CV= 5.5)
•Modulating valves available in 1/2” (CV= 0.4, 1.3, 2.2,
or 4.4), 3/4” (CV= 5.5 or 7.5), 1” (CV= 10 or 14),
and 11/4” (CV= 20)
•Two-zone stack rack with casters, common wiring and piping
available; compact units only
•300ºF (149ºC) operation; includes graphite-impregnated
silicon carbide seal
•Audible and visual general fault alarm
•Electrical operation available in 208, 230, 460, and 575 volts,
60 Hz; 200, 380, and 415 volts, 50 Hz
•UL/CUL-listed electrical subpanel
Artisan Technology Group - Quality Instrumentation ... Guaranteed | (888) 88-SOURCE | www.artisantg.com

Page 10 Royal Series Water Temperature Control Units
Figure 1
Typical Royal Series Water Temperature Control Unit and Specifications
Direct Injection
Closed Circuit
Model Dimensions Shipping
number Pump H W D weight
460 / 230 hp kW gpm lpm psig kPa in. cm in. cm in. cm lbs. Kg
¾ 0.56 30 113.6 25 172.4
1 0.75 35 132.5 30 206.9
2 1.50 50 189.3 30 206.9
3 2.24 60 227.1 35 241.3
210 96
5 3.73 75 283.9 54 372.3
2010,
9 kW heater
7½ 5.60 90 454.2 63 434.4
28¾” 73.0 13” 33 28” 71.1
240 109
28"
28 3/4"
3 3/4"
13"
PARTN O. 522-00205-00
EQUIPMENT.
OR DANGERTOOPERATINGPERSONNEL.
BESHUTOFFBEFORE DISCONNECTING ORSERVICINGTHIS
5.THISEQUIPMENT MUST NOT BE USED W HILE UNATTENDED.
6.VENT ANDDRAIN PROVISIONS MUST NOTBE RESTRICTED.
7.AIRAN DFLUIDSUPPLY SERVICEPROVISIONS MUSTALWAYS
WO RKINGCONDITION TO AVOIDACCI DENTALOVERHEATING
4.ALL CONTROLDEVICES MUST BE MAINTAINED IN PROPER
THISSIGNMUSTNOTBE REMOVEDORCAMOUFLAGED
DURINGUSEOFTHISEQUIPMENT.
OFTHISEQUIPMENT.
RECOGNITIONOF ANDCOMPLIANCE WITH THEFOLLOWING
THISEQUIPMENTCONTAINSFLU ID, PIPINGA ND CONNECTIONS
WHICHMAYBEEXT REMELY HOT ANDCOULDCAUSESERIOUS
PRECAUTIONSARETHESOLE RESPONSIBILITY OF THEUSER
T HISEQ UIPMENT,AND ALLAPPLICABLECODES.
PROPERLY FUSED A NDSIZED TOMEETREQUIREMENTSOF
T OO PENINGA NY EL ECTRIC ENCLOSURE ORW ORKINGON
1.EQUIPMENT MUST BE PROPERLY GROUNDED.
2.ELECTRICPOWER SUPPLYW IRINGAND DEVICESMUSTBE
3.ELECT RI C PO WER SO URCE MUSTBEDISCONNECT ED PRIOR
ANY ELECTRIC COMPONENTS.
BURNSANDP E RSONA L I NJURY.
4.LOS DISPOSITIVOS DE MANDOD EBENM ANTENERSEEN PER-
PERSONAL QUE ATEINDE EL EQ UIPO.
O TAPARSEMIENTRASSEUSAEL EQUIPO.
ESTAADVERTENCIAOSENAL NO DEBEQUITARSE
DEDESCONECTAROSERVIRELEQUIPO.
SOBRECALENTAMIEN TOACCIDENTALO EL DANOAL
O PURGANOESTANRESTRINGIDASUNICAMENTEAL FLUJO
DEFLUIDOYAIREDEBEN CERRARSE SIEMPREANTES
7.LAS DISPOSICIONES OCONEXIONESDESUMINISTRO
6.LASDI SPOSICIONESSOBRE ELSERVICIO DEDRENAJE
5.ESTE EQUIPO NO DEBESERUSADOCUANDONOHAY QUIEN
FECTO ESTADODE F UNCIONAMIENTOPARAE VITAREL
CO RRECT O D EL FLUIDO.
LO AT I ENDA.
PARTN O. 522-00205-01
T RABAJO ENLOS CO MPONENTESEL ECTRICOS.
QUECORRESPONDEAESTE EQUIPO.
PUEDENESTARPELIGROSAMENTECALIENTES!
PRECAUCION
DE ABRI RL AS CAJAS ELECTRICAS O HACER CUALQUIER
3.DEBEDESCONECTARSE LA F UERZAELEC TRICAANTES
T ENER S US FUSIBLESYSERDEL TAMANOO CAPACIDAD
ELECTRICAYDISPOSITIVOSCORRESPONDIENTESDEBEN
2.ELAL AMBRADOPA RA EL SUMINISTRO DE LA FUERZA
1.ELEQUIPO DEBE ESTARCONECTADO A TIERRAENFORMA
CIONESSONLARESPONSABILIDADEXCL USIVADEL USUARIODE
CONOCIMIENTOYCUMPLIMIENTOCONL AS SIGUIENTESPRECAU-
ESTE EQUIPOCONTIENE FLUIDO, TUBERIA Y CONEXIONESQUE
DEBIDA.
ESTEEQUIPO.
21 7/16"
15 1/8"
2 3/4"
11 3/4"
2 3/4"
6 7/16"
IN LEAKS OR DAMAGE TO UNIT.
FAILURE TO DO SO MAY RESULT
MAKING PIPING CONNECTIONS.
TO SUPPORT UNIT PIPING WHEN
ALWAYS USE A BACK−UP WRENCH
NOTICE
COOLING WATER IN
COOLING WATER OUT
FROM PROCESS TO PROCESS
28 3/4"
1.EQUIPMENTMUSTBE PROPERLYGROUNDED.
13"
3 3/4"
28"
3.ELECTRICPOWERSOURCE M UST BEDISCONNECTEDPRIOR
2.ELECTRICPOWERSUPPLYWIRINGANDDEVICESMUSTBE
PROPERLYFUSED ANDSIZED TO MEETREQUIREMENTSOF
T HISEQUIPMENT,ANDALL APPLICABLECODES.
DURING USEOF THIS EQUIPMENT.
THISSIGNMUSTNOTBEREMOVEDORCAMOUFLAGED
ANY ELECTRICCOMPONENTS.
4.ALLCONTROLDEVICESMUSTBEMAINTAINEDINPROPER
T O OP ENING ANY ELECTRICENCLOSURE OR W ORKING ON
W ORKINGCONDITIONTOA VOIDA CCIDENTAL O VERHEATING
7.AIRANDF LUIDSUPPLYSERVICEPROVISIONSMUSTALWAYS
6.VENT AND DRAIN PROVIS IONSMUSTNOTBERESTRICTED.
5.THIS EQ UIPMENT MUST NOT BE USE DW HILE UNATTENDED.
BE SHUT OFF B EFORE DISCONNECTING OR SERVICINGTHIS
OR DANGERTOOPERATINGPERSONNEL.
EQUIPMENT.
PARTNO.522-00 205- 00
2.ELALAMBRADOPARAEL SUMINISTRO DE LA FUERZA
ELECTRICAYDISPOSITIVOSCORRESPONDIENTESDEBEN
TENERSUS FUSIBLESY SER DEL TAMANOO CAPACIDAD
3.DEBEDESCONECTARSELAFUERZAELECTRICAANTES
DE A BRIRLAS CAJASEL ECTRICASOHACERCUALQUIER
4.LOS DISPOSITIVOSDEMANDO DEBEN MANT ENERSEENPER-
F ECTOESTADODEFUNCIONAMIENTOPAR A EVITARE L
5.ESTEEQUIPONODEBE S ER USADOCUANDONOHAY QUIEN
6.LASDISPOSICIONESSOBREELSERVICIO DEDRENAJE
7.LASDISPOSICIONESO CONEXIONESDESUMINISTRO
DE FLUIDO Y AIREDEBENCERRARSE SIEMPREANTES
O PURGANOESTAN RESTRINGIDASUNICAMENTEALFLUJO
SOBRECALENTAMIENTOACCIDENTALOEL DANOAL
ESTAADVERTENCIAOSENALNODEBEQUITARSE
TRABAJO ENLOSCOMPONENTESELECTRICOS.
CORRECTO DEL FLUIDO.
DE DESCONECTAROSERVIRELEQUIPO.
OTAPARSE MIENTRASSEUSAELEQUIPO.
QUECORRESPONDEAESTEEQUIPO.
LO ATIENDA.
PERSONALQUE ATEINDEEL EQUIPO.
PARTNO. 522-00205-01
OFTHISEQUIPMENT.
BURNSANDPERSONALINJURY.
PRECAUTIONSARETHESOLERESPONSIBILITYOF T HE USER
WHICHMAYBEEXT REMELY HOTANDCOULDCAUSESERIOUS
THISEQUIPMENTCONTAINSFLUID, PIPINGANDCONNECTIONS
RECOGNITIONOFA ND COMPLIANCE W IT H THE FOLLOWING
ESTEEQUIPOCONTIENEFLUIDO,TUBERIAYCONEXIONESQUE
CONOCIMIENTOYCUMP LIMIENTO CONL AS SIG UIENTES PRECAU-
CIONESSONLARESPONSABILIDADEXCLUSIVADELUSUARIODE
1.ELEQUIPODEBE ESTARCONECTADOA TIERRAENFORMA
PRECAUCION
PUEDENESTARPELIGROSAMENTECALIENTES!
ESTEEQUIPO.
DEBIDA.
27 1/8" 26 1/16" 21 7/16"
2 3/4"
11 3/4"
6 7/16"
15 1/8"
2 3/4"
IN LEAKS OR DAMAGE TO UNIT.
NOTICE
ALWAYS USE A BA CK−UP WRENCH
TO SUPPORT UNIT P IPING WHEN
MAKING PIPING CONNE CTIONS.
FAILURE TO DO SO MAY RE SULT PROCESS WATER IN
COOLING WATER IN
COOLING WATER OUT 1 15/16"
3 9/16"
PROCESS WATER VENT
TO PROCESS
FROM PROCESS
Artisan Technology Group - Quality Instrumentation ... Guaranteed | (888) 88-SOURCE | www.artisantg.com

Royal Series Water Temperature Control Units Page 11
Figure 2
Typical Royal Upright Series Water Temperature Control Unit and Specifications
PRECAUCION
IN LEAKS OR DAMAGE TO UNIT.
FAILURE TO DO SO MAY RESULT
MAKING PIPING CONNECTIONS.
TO SUPPORT UNIT PIPING WHEN
ALWAYS USE A BACK−UP WRENCH
NOTICE
48"
3 3/4"
28"
13"
Model Dimensions Shipping
number Pump H W D weight
460 230 letter hp kW gpm lpm psig kPa in. cm in. cm in. cm lbs. Kg
C ¾
0.56 30 113.6 25 172.4
D 1 0.75 35 132.5 30 206.9
F 2 1.50 50 189.3 30 206.9
G 3 2.24 60 227.1 35 241.3
210 96
H 5 3.73 75 283.9 54 372.3
J 7½ 5.60 90 340.7 63 434.4 240 109
2012,
9 kW heater
K 10 7.46 120 454.2 55 379.2
48 122 13 33 28 71.1
270 123
Figure 3
Royal Series Unit Full-Load Amps
Model Full-load amps at 460 volts
hp kW 9 kW heater 12 kW heater 18 kW heater 24 kW heater 36 kW heater 48 kW heater
0.75 hp 0.56 kW 12.7 amps 16.5 amps 24.0 amps 31.6 amps 47.4 amps 62.4 amps
1.00 hp 0.75 kW 13.1 amps 16.9 amps 24.4 amps 32.0 amps 47.8 amps 62.8 amps
2.00 hp 1.50 kW 14.7 amps 18.5 amps 26.0 amps 33.6 amps 49.4 amps 64.4 amps
3.00 hp 2.24 kW 16.1 amps 19.9 amps 27.4 amps 35.0 amps 50.8 amps 65.8 amps
5.00 hp 3.73 kW 18.9 amps 22.7 amps 30.2 amps 37.8 amps 56.6 amps 71.6 amps
7.50 hp 5.60 kW 22.3 amps 26.1 amps 33.6 amps 41.2 amps 57.0 amps 72.0 amps
10.00 hp 7.46 kW 26.0 amps 30.0 amps 37.0 amps 45.0 amps 60.0 amps 75.0 amps
497/8”
Artisan Technology Group - Quality Instrumentation ... Guaranteed | (888) 88-SOURCE | www.artisantg.com

Page 12 Royal Series Water Temperature Control Units
2 Shipping Information
2-1 Unpacking and Inspection
You should inspect your Sterling/Sterlco Royal Series temperature
control unit for possible shipping damage. If the container and
packing materials are in re-usable condition, save them for
reshipment if necessary.
Thoroughly check the equipment for any damage that might have
occurred in transit, such as broken or loose wiring and
components, loose hardware and mounting screws, etc. In case of
breakage, damage, shortage, or incorrect shipment, refer to the
following sections.
2-2 In the Event of Shipping Damages
Important!
According to the contract terms and conditions of the Carrier,
the responsibility of the Shipper ends at the time and place of shipment.
;Notify the transportation company’s local agent if you discover
damage.
;Hold the damaged goods and packing material for the
examining agent’s inspection. Do not return any goods to
Sterling before the transportation company inspection and
authorization.
;File a claim against the transportation company. Substantiate
the claim by referring to the agent’s report. A certified copy of
our invoice is available upon request. The original Bill of
Lading is attached to our original invoice. If the shipment was
prepaid, contact Sterling at (262) 641-8610 for a receipted
transportation bill.
;Advise Sterling regarding your request for assistance and
to obtain an RGA (return goods authorization) number.
Artisan Technology Group - Quality Instrumentation ... Guaranteed | (888) 88-SOURCE | www.artisantg.com

Royal Series Water Temperature Control Units Page 13
2-3 If the Shipment is Not Complete
Check the packing list. The apparent shortage may be intentional.
Back-ordered items are noted on the packing list. You should have:
;Sterling/Sterlco Royal Series water temperature control unit
;Bill of lading
;Packing list
;Operating and Installation packet
;Electrical schematic and panel layout drawings
;Component instruction manuals
Re-inspect the container and packing material to see if you missed
any smaller items during unpacking. Determine that the item was
not inadvertently taken from the area before you checked in the
shipment. Notify Sterling immediately of the shortage.
2-4 If the Shipment is Not Correct
If the shipment is not what you ordered, contact Sterling
immediately. Include the order number and item. Hold the items
until you receive shipping instructions.
2-5 Returns
Important!
Do not return any damaged or incorrect items
until you receive shipping instructions from Sterling.
Artisan Technology Group - Quality Instrumentation ... Guaranteed | (888) 88-SOURCE | www.artisantg.com

Page 14 Royal Series Water Temperature Control Units
2-6 Uncrating Your New Royal Series System
;Royal Series water temperature control units are shipped
fastened to a skid and covered with a cardboard box.
;Carefully remove the staples on the bottom of the box, lift off
the box, and remove the bolts holding the unit to the skid.
Caution!
Be careful when cutting straps.
Straps may spring back and cause injury!
;From the side, slip two lifting straps between the skid and
temperature control unit. Spread the straps from the center line
so it is balanced.
;Loop the straps over a fork truck fork. Lift slowly and only
high enough to clear the skid. Use a pry bar if necessary to
remove the skid from the unit.
;Carefully slide the skid from beneath the unit and lower the
unit. Lower slowly. The unit should land on its casters and can
be rolled into position.
;Retain the crating in case reshipment is necessary due to
hidden shipping damage.
Artisan Technology Group - Quality Instrumentation ... Guaranteed | (888) 88-SOURCE | www.artisantg.com

Royal Series Water Temperature Control Units Page 15
- Notes -
Artisan Technology Group - Quality Instrumentation ... Guaranteed | (888) 88-SOURCE | www.artisantg.com

Page 16 Royal Series Water Temperature Control Units
3 Installation
3-1 Installation Location Considerations
Royal Series systems are portable and can be installed almost
anywhere. As with all equipment installations, follow all
applicable codes and regulations.
;The recommended ambient temperature range for Royal Series
installations is from +14ºF (-10ºC) to a maximum operating
ambient temperature of 131°F (55ºC). Recommended ambient
storage temperature range is from -13ºF to 149ºF (-25ºC to
65ºC). If storing the unit below freezing temperatures, make
sure the unit has an antifreeze mixture circulated inside.
;Provide a minimum of twelve inches (12” or about 30 cm)
clearance on all sides of the cabinet to allow circulation of
cooling air.
;Locate the unit as close to the process as is practical.
3-2 Process Approach Temperature Considerations
If the differential (U) between COOLING WATER IN and TO
PROCESS temperatures is less than 10°F (7ºC), consult our Sales
Department for advice on how to control low approach
applications.
3-3 External Piping Sizing Considerations
;All external hose and piping should be adequately sized to
assure minimum external pressure drop.
;Low external piping pressure drop is needed for best operation.
Artisan Technology Group - Quality Instrumentation ... Guaranteed | (888) 88-SOURCE | www.artisantg.com

Royal Series Water Temperature Control Units Page 17
Note: Use a backup wrench to support Royal Series system
piping when making process piping connections.
!CAUTION
All external valves, fittings, and hoses must be rated at a minimum of
150 psig and 250°F (1,034.25 kPa/10.34 bars and 121ºC).
The exception is when the temperature control unit
is optionally rated for 300ºF (149ºC) operation;
external valves fittings and hoses must then be rated at a minimum of
150 psig and 300ºF (1,034.25 kPa/10.34 bars and 121ºC).
3-4 Piping Considerations for Permanent
Installations
Sterling recommends an optional (or customer-installed) strainer
on the COOLING WATER IN inlet.
The unit must have at least 16 psig (110.32 kPa/1.1 bars) water
supply pressure to prevent pump cavitation that can be caused by
the water “flashing” to steam. To avoid damage to the pump or
other components, make sure that maximum supply pressure does
not exceed 55 psig (379.2 kPa/3.79 bars).
Keep restrictions to a minimum by using proper inlet pipe sizing. If
the water supply piping is larger than ¾”, reduce the size at the
unit. The table below contains the pipe sizes that are used in the
unit.
Pipe sizes for ¾ hp to 10 hp (0.56 kW to 7.46 kW) units
Location Size in inches NPT
To Process 1½”
From Process 1½”
Cooling Water In ¾”
Cooling Water Out - depends on solenoid used -
Common black pipe is recommended for permanent installations.
Royal Series water circuit piping is primarily ferrous (iron) and
reacts electro-chemically with non-ferrous metallic materials such
as copper. Some water contains dissolved minerals that greatly
accelerates the reaction between dissimilar metals.
Artisan Technology Group - Quality Instrumentation ... Guaranteed | (888) 88-SOURCE | www.artisantg.com

Page 18 Royal Series Water Temperature Control Units
Ferrous piping is recommended to minimize galvanic action. If
piping must be copper, use dielectric unions at the unit.
3-5 Piping Considerations for High Mobility
Installations
Mobile Royal Series systems must use high quality hose rated for
at least 150 psig and 250°F (1,034.25 kPa/10.34 bars and 121ºC).
Special 300°F (149ºC) high temperature Royal Series systems
must use hosing rated at 150 psig and 300°F (1,034.25 kPa/10.34
bars and 149ºC) or greater.
Quick disconnects may be used for mobility, although they cause
a drop in pressure. If used, they must be sized carefully to
minimize pressure drop. Don’t use quick disconnects with check
valves unless absolutely necessary.
!CAUTION
Non-relieving quick connect fittings or check valves on the water supply
must have a pressure relief piped to the drain.
Failure to do so could result in a dangerous over-pressure condition!
3-6 Process Water Considerations
Raw Water
Water treatment is vital in any piping system. In some cases, raw
water may be used in the system without problems; in other cases,
it can result in large deposits of scale and corrosion.
Sterling offers a complete line of water treatment equipment.
Contact your Sterling sales representative for water testing and
treatment options.
Distilled Water
Non-ferrous (brass, copper, or high-temperature plastic) piping is
recommended for distilled water processes.
Artisan Technology Group - Quality Instrumentation ... Guaranteed | (888) 88-SOURCE | www.artisantg.com

Royal Series Water Temperature Control Units Page 19
Deionized Water
Stainless steel (316 SS minimum) or PVC plastic components must
be used with deionized water. Sterling recommends stainless steel
because of the temperature constraints with plastic.
3-7 Making Process Water Connections
Closed Circuit/Direct Injection
On the back of each unit, the connections are labeled appropriately.
For Direct Injection units connect the TO PROCESS hookup to the
entrance of the process and the FROM PROCESS hookup to
the exit of the process. Connect the COOLING WATER
IN to your plant water supply. Connect the COOLING WATER
OUT line to an open drain, or to the return line of
your central water system.
For Closed Circuit units make the connections as stated above, and
if there is a separate supply for the process and cooling make the
following connections. Connect the PROCESS WATER
SUPPLY hookup to the water source for the process. Connect the
PROCESS WATER VENT hookup to return the water back to
the process source.
Make sure you carefully select the connecting lines and
connectors between the temperature control unit and the
process to suit the needs and requirements of your application.
If your unit has a maximum operating temperature of 250ºF
(121ºC), the connecting lines and connectors should have a
service rating of at least 250ºF (121ºC) and 150 psig (1,034.25
kPa/10.34 bars). If it has a maximum temperature of 300ºF
(149ºC), the lines and connectors should have a service rating
of at least 300ºF (149ºC) and 150 psig (1,034.25 kPa/10.34
bars).
TO PROCESS — 1½” NPT
This is the outlet for the tempered water leading to the process
being controlled.
Artisan Technology Group - Quality Instrumentation ... Guaranteed | (888) 88-SOURCE | www.artisantg.com
This manual suits for next models
2
Table of contents
Other Sterling Control Unit manuals
Popular Control Unit manuals by other brands
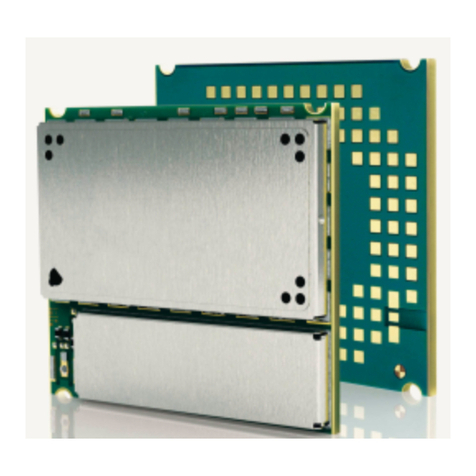
Cinterion
Cinterion BGS3 Hardware interface description
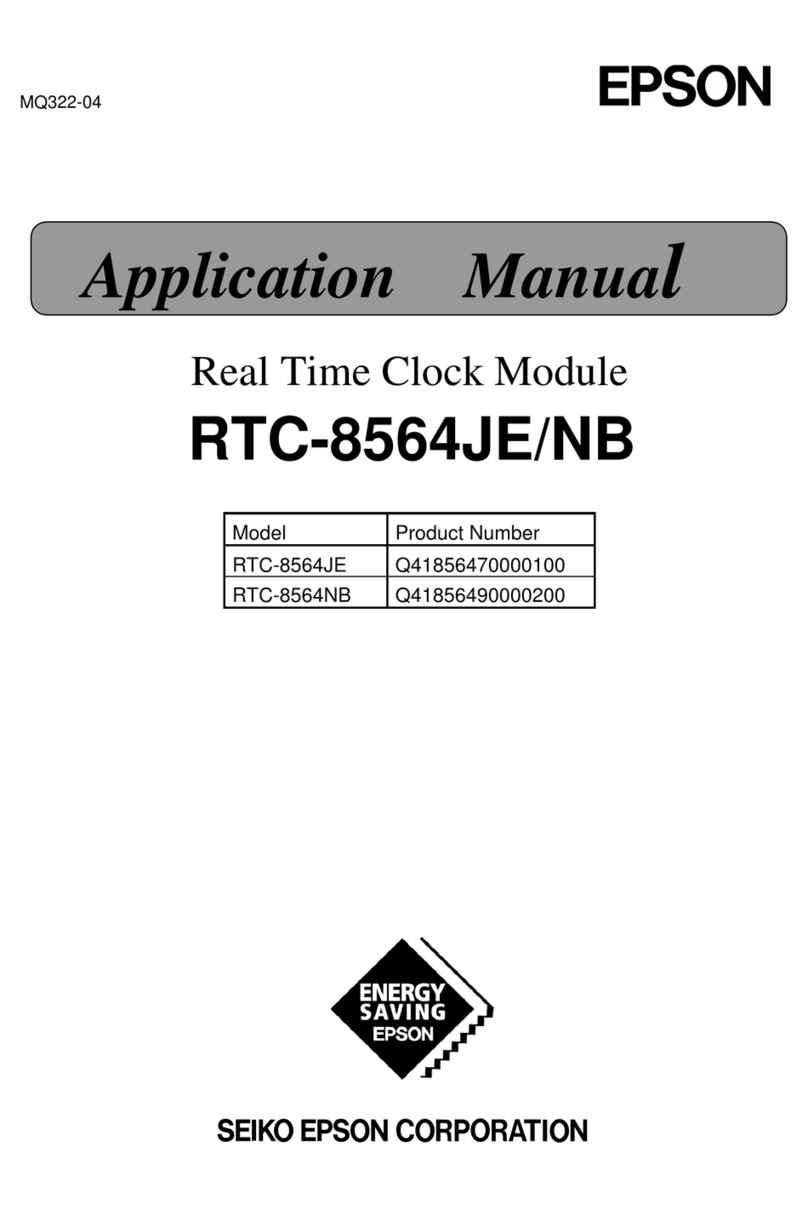
Epson
Epson RTC-8564JE Applications manual
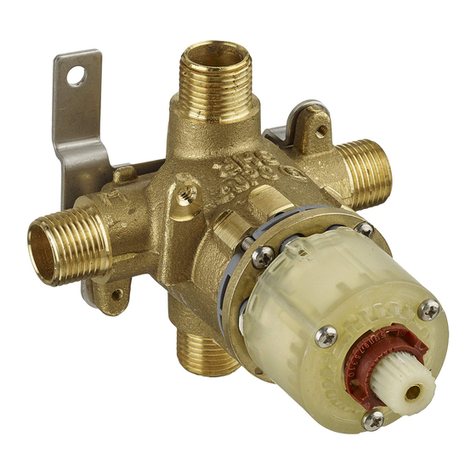
American Standard
American Standard R111 installation instructions
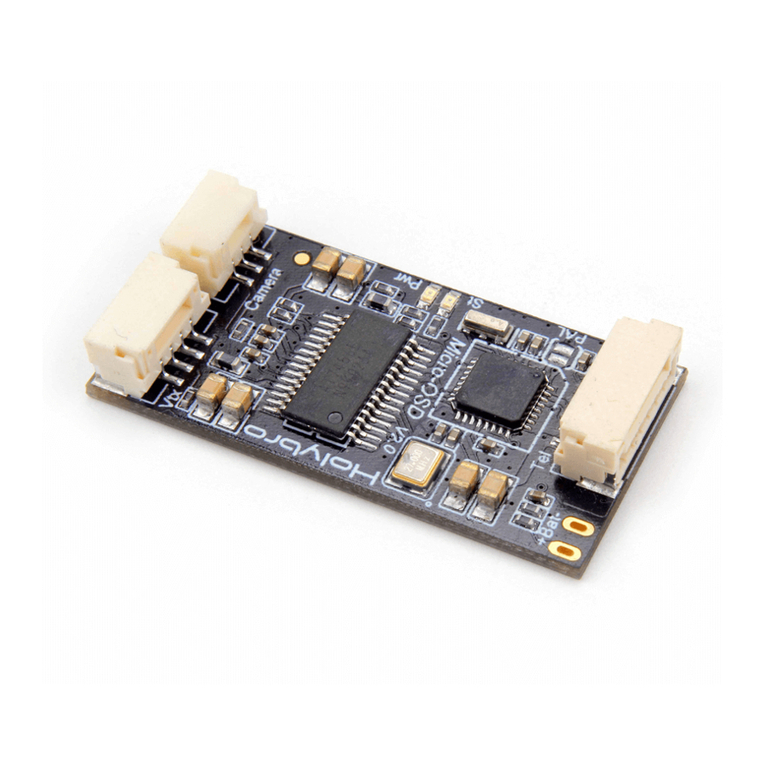
Holybro
Holybro Micro OSD V2 Full Manual & Installation Guide
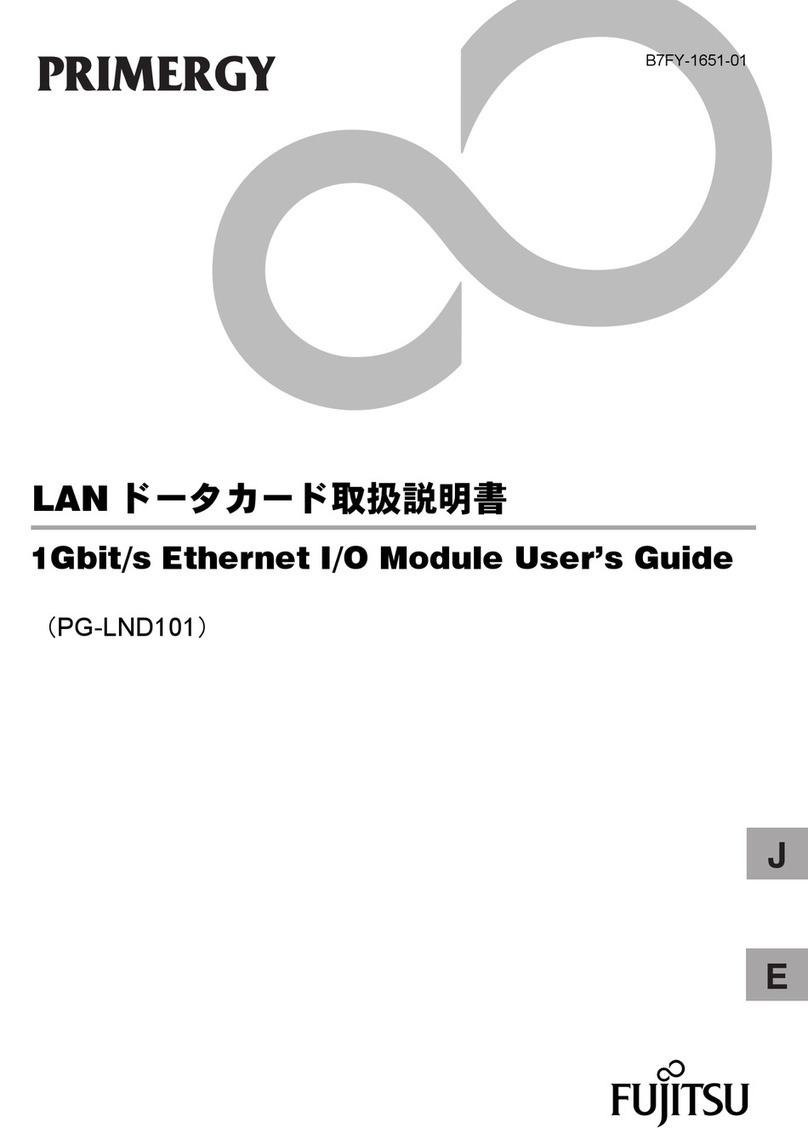
Fujitsu
Fujitsu PRIMERGY PG-LND101 user guide

Bosch
Bosch Rexroth 2THE5R instruction manual