Stromag SIDEOS Box 2 Instruction Manual

SIME Brakes
Installation and maintenance
M10054-02
SIDEOS Box 2
Adapted to
interfaces up to
PL=e / CATEGORY 4
according to
ISO/IEC 13849-1
SPEED MONITORING UNIT
SIME Brakes
www.stromag.com - Customer service / Tel. : +33(0)1 49 90 32 20 / Fax : +33(0)1 49 89 06 38

SIME Brakes
13/05/16
M10054-02-A
Installation and maintenance
SIDEOS Box 2
1/17
Non contractual photographs.
Instructions of this manual must be adhered to, to obtain the performance and the safety of operation of the equipment.
Encoder and limit switch 51 questionnaire No. Q01390-01
Dimensions limit switch 51 No. T10003-01
Installation and maintenance SIDEOS One No. M10054-01
Limit switch 51 - Stromag
Catalog No. D142
Installation and maintenance No. 151-00004
EMC No. 900-00001
SUMMARY
Chapter Title Page
NOTES AND SYMBOLS 2
1 PRESENTATION 3
2 OUTPUTS CONTACTS USE 4
2-1 Use of overspeed outputs 4
2-2 Use of System Fault outputs 4
3 INPUTS CONTACTS CHARACTERISTICS 5
4 EXAMPLES OF APPLICATIONS 6
4-1 OVERSPEED (mechanical stop) SYSTEM FAULT (electrical stop) 6
4-2 OVERSPEED (mechanical stop) via safety relay and
SYSTEM FAULT (electrical stop) 7
5 TECHNICAL CHARACTERISTICS 8
5-1 Electrical connection terminal box 8
5-2 Electrical diagram 9
5-3 Encoders selection 10
5-3 Dimensions 11
6 INSTALLATION PARAMETERS SETTING 11
6-1 Parameters-setting mode 11
6-2 Parameters-setting according to the selected function (Dynamic Slipping
orKinematicLinkageBreaking)andmountingconguration 12
7 START-UP PROCEDURE 13
8 DIAGNOSIS 14
9 STARTING-UP REPORT 16
10 GARANTEE, LIABILITY AND TECHNICAL ASSISTANCE 17
SIME Brakes
www.stromag.com - Customer service / Tel. : +33(0)1 49 90 32 20 / Fax : +33(0)1 49 89 06 38

SIME Brakes
13/05/16
M10054-02-A
Installation and maintenance
SIDEOS Box 2
2/17
Non contractual photographs.
Instructions of this manual must be adhered to, to obtain the performance and the safety of operation of the equipment.
Encoder and limit switch 51 questionnaire No. Q01390-01
Dimensions limit switch 51 No. T10003-01
Installation and maintenance SIDEOS One No. M10054-01
Limit switch 51 - Stromag
Catalog No. D142
Installation and maintenance No. 151-00004
EMC No. 900-00001
NOTES AND SYMBOLS
According to EC regulations, we use, facing some paragraphs,
symbols dening hazards and informing the user about the
consequences of not following the instructions of this installa-
tionandmaintenanceleaet.
DANGER!
This symbol concerns people's safety. It points out
situations which could lead to death or serious in-
juries.
ATTENTION!
This symbol concerns the use of the equipment. It
points out situations which could lead to a dysfunc-
tioning of the equipment.
NOTE!
This symbol concerns information which can ease
the installation and the use of the equipment.
SIME Brakes
www.stromag.com - Customer service / Tel. : +33(0)1 49 90 32 20 / Fax : +33(0)1 49 89 06 38

SIME Brakes
13/05/16
M10054-02-A
Installation and maintenance
SIDEOS Box 2
3/17
Non contractual photographs.
Instructions of this manual must be adhered to, to obtain the performance and the safety of operation of the equipment.
Encoder and limit switch 51 questionnaire No. Q01390-01
Dimensions limit switch 51 No. T10003-01
Installation and maintenance SIDEOS One No. M10054-01
Limit switch 51 - Stromag
Catalog No. D142
Installation and maintenance No. 151-00004
EMC No. 900-00001
1 - PRESENTATION
The SIDEOS Box 2 unit is a secure monitoring system of the
speed. It includes 2 SIDEOS One to comply with the diagram
below.
The SIDEOS Box 2 unit monitors :
> the speed,
> the stop,
> the rotation direction,
> the kinematic linkage,
> the signals of the incremental encoder,
> the external speed signal 0-20mA ,
> the contacts of Ascent / Descent / HS-LS (High Speed - Low
Speed) control,
> the system fault and overspeed outputs and the taking into
account by the customer PLC.
It allows to obtain, when installation is correct, a speed moni-
toring system secured up to the category 4 with the perfor-
mance level of PL= e according to the standard ISO/IEC
13849-1. (see diagram examples in ch.4)
It provides :
> 2 secured outputs : System Fault
> 2 secured outputs : Overspeed
> 1 information output : System Fault
> 1 information output : Overspeed
It receives :
> 2 speed information (incremental encoders).
> Hoisting control information : Ascent - Descent - High Speed
-Low speed
> 2 loop feedback of the secured outputs : System Fault
> 2 loop feedback of the secured outputs : Overspeed
> 2 selection inputs of the functions : Dynamic Slipping or
Kinematic Linkage breaking
Signal
REDUCER
MOTOR
DRUM DRUM Encoder 1
Signal
Ascent
Descent
System Fault
outputs
Overspeed
outputs
High Speed
Encoder 2
Signal
REDUCER
MOTOR
DRUM Encoder 1
Signal
Ascent
Descent
System Fault
outputs
Overspeed
outputs
High Speed
Encoder 2
Conguration 1 : Drum / Motor
Conguration 2 : Drum / Drum
SIME Brakes
www.stromag.com - Customer service / Tel. : +33(0)1 49 90 32 20 / Fax : +33(0)1 49 89 06 38

SIME Brakes
13/05/16
M10054-02-A
Installation and maintenance
SIDEOS Box 2
4/17
Non contractual photographs.
Instructions of this manual must be adhered to, to obtain the performance and the safety of operation of the equipment.
Encoder and limit switch 51 questionnaire No. Q01390-01
Dimensions limit switch 51 No. T10003-01
Installation and maintenance SIDEOS One No. M10054-01
Limit switch 51 - Stromag
Catalog No. D142
Installation and maintenance No. 151-00004
EMC No. 900-00001
2 - OUTPUTS CONTACTS USE
2-1 Use of overspeed outputs
Triggering of the secured contacts outputs : Overspeed C4
(terminals : 25-26) and C5 (terminals : 27-28), indicates an
emergency situation and must drive, directly or via a safety
relay, the redundant contactors of the safety brakes supply
(mechanical stop of type 0).
See diagram examples on chapter : 4.
The information output : Overspeed C6 (terminals : 29-30) can
be used to give triggering information signal to the customer
PLC, the stop control being processed otherwise via the secured
Overspeed contacts.
2-2 Use of System Fault outputs
Triggering of the secured outputs : System fault C1 (terminals:
19-20) and C2 (terminals : 21-22), indicates an operation fault
of the monitoring system :
Those signals must be processed in order to maintain the ma-
chinery in a safe state.
> Mechanical stop (stop of type 0): the secured contacts out-
puts must drive directly or via a safety relay the redundant
contactors of the service brakes supply.
> Electrical stop (stop of type 1) : the secured contacts out-
puts must drive the electrical stop of the hoidting motion, the
customer PLC giving back the signal that the System Fault
information is taken into account by 2 loops feedbacks.
See diagram examples on chapter : 4.
The information output System Fault C3 (terminals : 23-24) can
be used to give the triggering information signal to the customer
PLC, the stop control being processed otherwise via the secured
Overspeed contacts.
Restart :
As indicated in the diagram examples in ch.4, restart of SIDEOS
Box 2 (reset) must not restart the installation, but only allows
the restart of the machinery from a control position with good
visibilityofthehazardousarea.
Periodical checking :
When activation of SIDEOS Box 2 outputs is not frequent (hois-
ting normal application), a procedure of switching off / switching
on of the SIDEOS Box 2 mustbedenedbytheintegratorof
the SIDEOS One system, to carry out periodically the automatic
and global TEST of the SIDEOS box 2 unit.
3 - INPUTS CONTACTS CHARACTERISTICS
> Ascent order (terminals 13-14)
Ascent contact is closed during a hoisting Ascent working order.
> Descent order (terminals 15-16)
Descent contact is closed during a hoisting Descent working
order.
> High Speed order (terminals 17-18)
High Speed contact is closed during a hoisting High Speed
working order.
ATTENTION !
The High Speed connection cable is imperatively
shielded to avoid the risk of short-circuit in the
connection cable.
Otherwise, connect the High Speed contact
between terminals 15 and 18, and this contact
must imperatively be open (Low Speed order)
when a Hoisting Stop order is present (Ascent
and Descent order absent).
> Loop feedback : System Fault (terminals 31-32 + 33-34)
- Output contacts C1 and C2 are used to drive directly
2 internal relays of the customer PLC, which contacts drive
a mechanical stop through the service brakes or an electri-
cal stop through the controller.
- A NC contact of each of these relays is inserted in the res-
pective System Fault feedback loop. Those contacts must
imperatively close, when the contacts C1 and C2 open, to
indicate a System Fault. This allows to the SIDEOS Box
2to check the opening of the associated relays and the
customer PLC taking into account.
- Reminder of EN ISO 13849-2 standard :
Short-circuits between conductors are excluded in an elec-
trical enclosure (enclosure and connection must comply
with the requirements of CEI/EN 60204-1standard).
- If this exclusion is not possible, it will then be necessary to
include a contact indicating the service brakes closing or
the electrical stop in each feedback loop.
- In case of C1 and C2 contacts use in an input loop of a
safety relay, those loop feedbacks can be shunted.
ATTENTION !
In this case, taking into account of the System
Fault triggering by the customer PLC and pos-
sible short-circuits in the connection cables of C1
and C2 contacts are no more controlled by the
SIDEOS box 2 unit.
The customer will make sure that all these faults
will be detected by its system (for example : sa-
fety relay with input loops control).
The achieved performance level will then de-
pend on the performance level achieved by the
safety relay.
SIME Brakes
www.stromag.com - Customer service / Tel. : +33(0)1 49 90 32 20 / Fax : +33(0)1 49 89 06 38

SIME Brakes
13/05/16
M10054-02-A
Installation and maintenance
SIDEOS Box 2
5/17
Non contractual photographs.
Instructions of this manual must be adhered to, to obtain the performance and the safety of operation of the equipment.
Encoder and limit switch 51 questionnaire No. Q01390-01
Dimensions limit switch 51 No. T10003-01
Installation and maintenance SIDEOS One No. M10054-01
Limit switch 51 - Stromag
Catalog No. D142
Installation and maintenance No. 151-00004
EMC No. 900-00001
> Overspeed loop feedback terminals 35-36 and 37-38
- C4 and C5 contacts are used to drive directly 2 contactors
inserted on the feed line of the safety brakes.
- The NC contact of each contactor is inserted into the res-
pective overspeed feedback loop. This contact must impe-
ratively close when the C4 et C5 contacts open to indicate
an Overspeed, this allowing the SIDEOS Box 2 to check
the opening of the associated contactors.
- In case of a direct use of C4 and C5 contacts in an input
loop of a safety relay, these loop feedbacks can be shun-
ted. (see diagram ch. 4-2).
ATTENTION !
In this case, taking into account of KFS1 and
KFS2 contactors triggering and possible short-
circuits in the connection cables of C4 and
C5 contacts are no more controlled by the
SIDEOS box 2 unit.
The customer will make sure that all these faults
will be detected by its system (for example : sa-
fety relay with input loops control).
The achieved performance level will then de-
pend on the performance level achieved by the
safety relay
> Dynamic Slipping selection on SIDEOS One N°1
terminals 39-40
- Terminals 39-40 are dircetly linked to the terminal box to
select the Dynamic Slipping on the SIDEOS One N°1.
- TS parameter on the SIDEOS N°1 will be put on CW or
CCW according to the rotation direction of the encoder 1
during a Descent order.
- CW = clockwise, watching the encoder axis in front view.
- CCW = counter-clockwise, watching the encoder axis in
front view.
> Dynamic Slipping selection on SIDEOS One N°1
terminals 41-42
- Terminals 41-42 are dircetly linked to the terminal box to
select the Dynamic Slipping on the SIDEOS One N°2
- TS parameter on the SIDEOS N°2 will be put on CW or
CCW according to the rotation direction of the encoder 2
during a Descent order.
- CW = clockwise, watching the encoder axis in front view.
- CCW = counter-clockwise, watching the encoder axis in
front view.
SIME Brakes
www.stromag.com - Customer service / Tel. : +33(0)1 49 90 32 20 / Fax : +33(0)1 49 89 06 38

SIME Brakes
13/05/16
M10054-02-A
Installation and maintenance
SIDEOS Box 2
6/17
Non contractual photographs.
Instructions of this manual must be adhered to, to obtain the performance and the safety of operation of the equipment.
Encoder and limit switch 51 questionnaire No. Q01390-01
Dimensions limit switch 51 No. T10003-01
Installation and maintenance SIDEOS One No. M10054-01
Limit switch 51 - Stromag
Catalog No. D142
Installation and maintenance No. 151-00004
EMC No. 900-00001
4 - EXAMPLES OF APPLICATIONS
4-1 OVERSPEED (mechanical stop ) SYSTEM FAULT (electrical stop)
WIRING DIAGRAM
K1 and K2 relays, and K3 and K4 contactors have force-guided
contacts according to IEC 609947-5-1 standard. (NO and NC
contacts cannot close in the same time).
OVERSPEED :
> Overspeed / secured contacts outputs (C4 and C5) drive di-
rectly two redundant contactors (K3 and K4) inserted on the
feed line of the safety brakes (Mechanical stop of type 0).
> A NC contact of K3 and K4 contactors is inserted in the res-
pective feedback loop to check the good operation of the
contactors.
> If a feedback loop remains open during an overspeed trig-
gering, SIDEOS box 2 unit triggers a System Fault (Contac-
tor 2 fault). SIDEOS Box restart will not be possible before
the installation reconditioning.
SYSTEM FAULT :
> System Fault / secured contacts outputs (C1 and C2) drive
directly two redundant relays (K1 and K2) of the customer
PLC, they are inserted on the hoisting control line and
control the hoisting electrical stop
> A NC contact of K1 and K2 relays is inserted in the respec-
tive feedback loop to check that the System Fault is taken
into account by the customer PLC.
> If a feedback loop remains open during a System Fault trig-
gering, SIDEOS Box 2 unit triggers a mechanical stop by
switching off the contactors K3 and K4. Restart is no allowed
before the installation reconditioning.
CATEGORY AND PERFORMANCE LEVEL
Category 4, and overall performance level obtained : PLe
Supply
Secured output 1 System Fault
Secured output 2 System Fault
Output 3 System Fault
Secured output 1 Overspeed
High Speed
Descent
Ascent
Feedback 1 System Fault
Feedback 2 System Fault
Feedback 1 Overspeed
Secured output 2 Overspeed
Output 3 Overspeed
Feedback 2 Overspeed
ENCODER N°2 ENCODER N°1
Customer PLC
Start-up cde
Start-up cde
STOP
cde
STOP
cde
SAFETY BRAKE
AU = emergency stop
CED = external condition of start-up
CO = brake opening switch
FDC = hoisting limit switch stop
K1 = contactor 1 / System Fault
K2 = contactor 2 / System Fault
K3 = contactor 1 / Overspeed
K4 = contactor 2 / Overspeed
KFS = contactor of safety brake control
KL = contactor of hoisting control
SIME Brakes
www.stromag.com - Customer service / Tel. : +33(0)1 49 90 32 20 / Fax : +33(0)1 49 89 06 38

SIME Brakes
13/05/16
M10054-02-A
Installation and maintenance
SIDEOS Box 2
7/17
Non contractual photographs.
Instructions of this manual must be adhered to, to obtain the performance and the safety of operation of the equipment.
Encoder and limit switch 51 questionnaire No. Q01390-01
Dimensions limit switch 51 No. T10003-01
Installation and maintenance SIDEOS One No. M10054-01
Limit switch 51 - Stromag
Catalog No. D142
Installation and maintenance No. 151-00004
EMC No. 900-00001
4-2 OVERSPEED (mechanical stop ) via safety relay and SYSTEM FAULT (electrical stop)
WIRING DIAGRAM
K1 and K2 relays, and KFS1 and KFS2 contactors have force-
guided contacts according to IEC 609947-5-1 standard. (NO
and NC contacts cannot close in the same time).
OVERSPEED :
> Overspeed / secured contacts outputs (C4 and C5) are in-
serted in the input loops of a safety relay, the contactors
KFS1 and KFS2 are inserted on the feed line of the emer-
gency brakes (Mechanical stop of type 0).
> The loops feedbacks are inactive (terminals 35-36 and 37-
38 linked), the safety relay checking the input loops and
monitoring the contactors KFS1 and KFS2.
SYSTEM FAULT :
> Secured contacts outputs of System Fault (C1 and C2) drive
directly two redundant relays (K1 and K2) of the customer
PLC, they are inserted on the hoisting control line and drive
the hoisting electrical stop.
> A NC contact of K1 and K2 relays is inserted in the respec-
tive feedback loop to check that the System Fault is taken
into account by the customer PLC.
> If a feedback loop remains open during a System Fault trig-
gering, SIDEOS Box 2 unit triggers a mechanical stop by
switching off the contactors K3 and K4. Restart is no allowed
before the installation reconditioning.
CATEGORY AND PERFORMANCE LEVEL
> Category 3 or4, and overall performance level obtained:
PLd or e.
> Selection of the safety relay and its checkings will determine
the achieved performance level.
As indicated in this diagram, connection in series of the
emergency stop contacts and the contacts of the SIDEOS
Box 2 unit will limit the category to 3 and the maximal attai-
nable level to PLd.
Supply
Output 1 System Fault
Output 2 System Fault
Output 3 System Fault
Output 1 Overspeed
High Speed
Descent
Ascent
Feedback 1 System Fault
Feedback 2 System Fault
Feedback 1 Overspeed
Output 2 Overspeed
Output 3 Overspeed
Feedback 2 Overspeed
= Inactive feedback loop
ENCODER N°2 ENCODER N°1
Customer PLC
Start-up cde
Start-up cde
Start-up cde
STOP
cde
STOP
cde
Safety module
SAFETY BRAKE
AU = emergency stop
CED = external condition of start-up
CO = brake opening switch
FDC = hoisting limit switch stop
K1 = contactor 1 / System Fault
K2 = contactor 2 / System Fault
K3 = contactor 1 / Overspeed
K4 = contactor 2 / Overspeed
KFS = contactor of brake control
KL = contactor of hoisting control
SIME Brakes
www.stromag.com - Customer service / Tel. : +33(0)1 49 90 32 20 / Fax : +33(0)1 49 89 06 38

SIME Brakes
13/05/16
M10054-02-A
Installation and maintenance
SIDEOS Box 2
8/17
Non contractual photographs.
Instructions of this manual must be adhered to, to obtain the performance and the safety of operation of the equipment.
Encoder and limit switch 51 questionnaire No. Q01390-01
Dimensions limit switch 51 No. T10003-01
Installation and maintenance SIDEOS One No. M10054-01
Limit switch 51 - Stromag
Catalog No. D142
Installation and maintenance No. 151-00004
EMC No. 900-00001
5 - TECHNICAL CHARACTERISTICS
5-1 Electrical connection terminal box
Terminals Function Characteristics
1Input 115/230VAC 50/60HZ +/-10% Consumption maxi 60VA – internal protection by fuse -
Micro-power cut : 250ms
2
3 + Input 24VDC +/-10%
- Input 0VDC
Consumption 25W - internal protection by fuse
Micro-power cut : 20ms
4
5UB
Encoder input 1
Type push-pull HTL with inverted signal, no-load consumption maxi = 160mA
Supply voltage delivered by SIDEOS One UB/GND = 12V
Maxi.inputfrequencyetnominalspeed=1000Hz
Linkage by standard shielded cable (Length maxi : 250m)
Input voltage maxi = 12.5V / mini = 7V
6A+
7B+
8O+
9A-
10 B-
11 O-
12 GND
13 Ascent contact input Potential-free contact / voltage and breaking current : 24V/120mA
14
15 Descent contact input Potential-free contact / voltage and breaking current : 24V/150mA
16
17 High Speed contact input Potential-free contact / voltage and breaking current : 24V/60mA
18
19 C1 : Output 1 secured System Fault
Fail-safe NO contact output, the NO contact is maintained closed and opens in case
of fault or absence of supply voltage.
Breaking capacity Maxi : AC15 : 500VA (230VAC)
DC13 : 50W
Breaking capacity Mini : 50mW (5V/2mA)
Themaximumcurrentowinginthecontactswillbelimitedbyafuse:2A
Using an arc suppressing device at the coil terminals of the output contactor allows
toensurethespeciedlifespan.
20
21 C2 : Output 2 secured System Fault
22
23 C3 : Output 3 System Fault
24
25 C4 : Output 1 secured Overspeed
26
27 C5 : Output 2 secured Overspeed
28
29 C6 : Output 3 Overspeed
30
31 Loop feedback 1 System Fault
NC potential-free contact / voltage and breaking current : 24V/30mA
32
33 Loop feedback 2 System Fault
34
35 Loop feedback 1 Overspeed
36
37 Loop feedback 2 Overspeed
38
39 SIDEOS One N°1
Input of dynamic slipping selection
To select the function, link terminals 39-40 and set SIDEOS ONE N°1
parameter TS = CW or CCW
40
41 SIDEOS One N°2
Input of dynamic slipping selection
To select the function, link terminals 41-42 and set SIDEOS ONE N°2
parameter TS = CW or CCW
42
43 UB
Encoder input 2
Type push-pull HTL with inverted signal, no-load consumption maxi = 160mA
Supply voltage delivered by SIDEOS One UB/GND = 12V
Maxi.inputfrequencyetnominalspeed=1000Hz
Linkage by standard shielded cable (Length maxi : 250m)
Input voltage maxi = 12.5V / mini = 7V
44 A+
45 B+
46 O+
47 A-
48 B-
49 O-
50 GND
terminal linked to + 24VDC
We recommend to connect the inputs and outputs contacts of the
SIDEOS Box 2 to the customer PLC with one or several shielded
cable(s) to prevent any short-circuits in the connection cables.
Connection on terminals Wire
Maxi. 6mm² without end ferrule
4mm² with end ferrule.
Mini. 0.5mm² without end ferrule
0.25mm² with end ferrule.
SIME Brakes
www.stromag.com - Customer service / Tel. : +33(0)1 49 90 32 20 / Fax : +33(0)1 49 89 06 38

SIME Brakes
13/05/16
M10054-02-A
Installation and maintenance
SIDEOS Box 2
9/17
Non contractual photographs.
Instructions of this manual must be adhered to, to obtain the performance and the safety of operation of the equipment.
Encoder and limit switch 51 questionnaire No. Q01390-01
Dimensions limit switch 51 No. T10003-01
Installation and maintenance SIDEOS One No. M10054-01
Limit switch 51 - Stromag
Catalog No. D142
Installation and maintenance No. 151-00004
EMC No. 900-00001
5-2 Electrical diagram
1 2
Mains
line
protection
Customer
115V or 230V
1613 14 15 1817 19 20 23 24
Ascent
Command
Descent
Command Command
Incremental encoder
High Speed
AL1
OV
24VL
N
3 4
Direct mains supply
24VDC +/-15%
50/60Hz
N°1
4039 4241
Dynamic Slipping
25 26 27 28
Dynamic
Slipping
SIDEOS One
N°1
Dynamic
Slipping
SIDEOS One
N°2
POWER SUPPLY INFORMATION CONTACTS INPUTS FUNCTIONS SELECTION
FAIL-SAFE NO CONTACTS OUTPUTS
System Fault and overspeed
In normal operation, the NO contact is maintained closed,
Output 1
secured
System
Fault
Output 1
secured
Over-
-speed
Output 2
secured
Over-
-speed
Output 3
info
Over-
-speed
Output 2
secured
System
Fault
Output 3
info
System
Fault
Incremental encoder
N°2
60W
of the hoisting command
UDC
0V
UDC
0V
UDC
0V
31 32 33 34
Feedback 1
System
Fault
Feedback 1
Overspeed
Feedback 2
Overspeed
Feedback 2
System
Fault
Ascent Stop\Descent High Speed DD N°1 DD N°2
SYSTEM FAULT OVERSPED
SYSTEM FAULT \ OVERSPEED \ SYSTEM FAULT \ OVERSPEED \
Terminals are linked to select
When the input contact is closed, it indicates:
the dynamic slipping function
it opens in the event of fault
37 38
POWER ON Loop feedback
System Fault
Loop feedback
System Fault
Loop feedback Loop feedback
Overspeed
Descent
Overspeed
+ -
OV
linked to
ground
Consistency control RLS3 / RLS4
Ascent or Descent command control
21 22 35 3629 30
NC FEEDBACK LOOPS
Outputs
System Fault
NC FEEDBACK LOOPS
Outputs
Overspeed
Consistency control RLS5 / RLS6
Contact
Potential-free
LOOP
FEEDBACK
21
= 24VDC ContactInput voltage maxi 12.5V
Frenquency maxi 1000 Hz
SIDEOS One 24VDC N°1
11
ENCODER
Coil voltage KDS-KSV
SYSTEM
FAULT
321 4 5
SPEED
OVER
876 9 10
Potential-free
SPEED LEVELS
141312 15 16 191817 20
Nominal Speed
15mA at
26
SPEED SIGNALS
242322 25 27
24VDC
Out In
B+
+UB
A+
O-
B-
A-
O+
0V
RL1
A2
A1
RL3
A2
A1
RLS1
A2
A1
A2
RLS8
A1
RLS9
A1
A2
56 7 8 9 10 11 12
UB A+ B+ O+ A- B- O- GND
H1
D2
D1 F1
Contact
Potential-free
LOOP
FEEDBACK
21
=24VDC Contact
Input voltage maxi 12.5V
Frenquency maxi 1000 Hz
SIDEOS One 24VDC N°2
11
ENCODER
Coil voltage KDS-KSV
SYSTEM
FAULT
321 4 5
SPEED
OVER
876 9 10
Potential-free
SPEED LEVELS
14
13
12 15 16 191817 20
Nominal Speed
15mA at
26
SPEED SIGNALS
242322 25 27
24VDC
Out In
B+
+UB
A+
O-
B-
A-
O+
0V
A2
RLS12
A1
RLS13
A1
A2
0.5A F
RL5
A2
A1
RL6
A2
A1
11
12 14
RL6
11
12 14
RLS9
RLS10
43 45 46 47 48 49 50
UB A+ B+ O+ A- B- O- GND
RLS14
A1
A2
RLS10
A1
A2
R2
1K
RL4
7
6
R1
1K
RL3
7
6
RL5
RLS13
RLS14
H2 H3
RL7
RL9
RL8
RL10
F2
F3
0.5A F
0.5A F
RL2
A2
A1
D4
RLS9RLS10
D3
RL2 RLS1
RL1
RL3
RSL2
A2
A1
RLS4
A2
A1
A1
A2
RL7
A1
A2
RLS11
RL8
A1
A2
RL110
A1
A2
RLS3
A2
A1
RLS3
RLS4
RL2 RLS2
RL1
RL4
RL4
A2
A1
44
RL7RL9
RLS6
A2
A1
RLS8
RLS5
A2
A1
RLS11
RLS12
RLS7
A2
RLS7
A1 A1
A2
RL9
RL8RL10
RLS5
RLS7RLS8
RLS3
RLS13RLS14
RLS6
RLS11RLS12
RLS4
RLS5
RLS6
SIME Brakes
www.stromag.com - Customer service / Tel. : +33(0)1 49 90 32 20 / Fax : +33(0)1 49 89 06 38

SIME Brakes
13/05/16
M10054-02-A
Installation and maintenance
SIDEOS Box 2
10/17
Non contractual photographs.
Instructions of this manual must be adhered to, to obtain the performance and the safety of operation of the equipment.
Encoder and limit switch 51 questionnaire No. Q01390-01
Dimensions limit switch 51 No. T10003-01
Installation and maintenance SIDEOS One No. M10054-01
Limit switch 51 - Stromag
Catalog No. D142
Installation and maintenance No. 151-00004
EMC No. 900-00001
5-3 Encoders selection
a) Electrical characteristics
Supply voltage range = 10…. 30V
Push-pull output with inverted signals
Maxi no-load consumption = 160mA
Standard shielded cable : 0.25 to 0.5mm²
The cable ways and connection should respect the safety
EMC-regulations.
b) SIDEOS One encoder resolution
Encoder
NS =
Nominal speed maxi
(NC < 60000 / NS)
Rotation control
threshold
Encoder : RC = On
rpm rpm
20 3000 0,6
40 1500 0,3
360 166 0,04
600 100 0,02
1024 58 0,012
1500 40 0,008
3600 16 0,004
c) Option : Encoder frequency divider
Ifthemotorencoderdeliversafrequency>1000Hzwithout
the possibility to install an other encoder on the motor shaft,
the option of an encoder frequency divider can be selected.
SIME Brakes
www.stromag.com - Customer service / Tel. : +33(0)1 49 90 32 20 / Fax : +33(0)1 49 89 06 38

SIME Brakes
13/05/16
M10054-02-A
Installation and maintenance
SIDEOS Box 2
11/17
Non contractual photographs.
Instructions of this manual must be adhered to, to obtain the performance and the safety of operation of the equipment.
Encoder and limit switch 51 questionnaire No. Q01390-01
Dimensions limit switch 51 No. T10003-01
Installation and maintenance SIDEOS One No. M10054-01
Limit switch 51 - Stromag
Catalog No. D142
Installation and maintenance No. 151-00004
EMC No. 900-00001
5-4 Dimensions
General characteristics
Temperature range -20°C to + 60°C
Casing material Steel
Protection rating of the casing IP66
Impact resistance IK10
Weight 25Kg
Dimension 600x600x200
Fastening 555x555
600
600 75
200
555
40
ISO16 ISO25
ISO20
ISO16ISO25
ISO20 ISO16
REFERENCE
REFERENCEREFERENCE
REFERENCEREFERENCE
SIME Brakes
N°desérie-Serial N°-Serien Nr
ARMOIREDE SURVEILLANCE VITESSE - SPEEDMONITORING ENCLOSURE
Avenuede l'Europe BP24 18150 La Guerche/L'Aubois FRANCE
SIDEOS Box
2
Indice: B
Stromag
GKN LANDS SYSTEM
Power on
H1 H2 H3
Overspeed
fault
System
Screw M8x10
+ nut HU8
+ washers
6 - INSTALLATION PARAMETERS SETTING
6-1 Parameters-setting mode
1. Unlock the access to the parameters (function Loc) :
press simultaneously on 1and 2during 3 seconds
2. Brieypresson3to access to the parameter-setting mode
3. By means of the buttons 1and 2select the parameter to modify
4. Brieypresson3toswitchtothemodicationmode
5. By means of the buttons 1and 2adjust the parameter as required
6. Press and hold 3to validate the parameter
7. Repeat steps 3 to 6 to adjust an other parameter
8. To leave the parameter-setting mode and return to the display mode
press and hold 3or wait 5s
9. Toleavethemodicationmodeandreturntotheparameter-settingmode,
brieypresson3or wait 5s
10. From the display mode to lock the access to the parameters (Loc):
press simultaneously on 1and 2during 3 seconds
1
Button UP
2
Button DOWN
3
Button VALID
SIME Brakes
www.stromag.com - Customer service / Tel. : +33(0)1 49 90 32 20 / Fax : +33(0)1 49 89 06 38

SIME Brakes
13/05/16
M10054-02-A
Installation and maintenance
SIDEOS Box 2
12/17
Non contractual photographs.
Instructions of this manual must be adhered to, to obtain the performance and the safety of operation of the equipment.
Encoder and limit switch 51 questionnaire No. Q01390-01
Dimensions limit switch 51 No. T10003-01
Installation and maintenance SIDEOS One No. M10054-01
Limit switch 51 - Stromag
Catalog No. D142
Installation and maintenance No. 151-00004
EMC No. 900-00001
6-2 Parameter-setting according to the selected function (Dynamic Slipping or Kinematic Linkage Breaking)
and mounting conguration :
SIDEOS N°1 SIDEOS N°2 Conguration
Encoder N°1 Encoder N°2
Kinematic linkage breaking Kinematic linkage breaking Drum Drum
Drum Motor
Kinematic linkage breaking Dynamic Slipping Drum Motor
Dynamic Slipping Dynamic Slipping Drum Drum
PARAMETERS
KINEMATIC LINKAGE BREAKING DYNAMIC SLIPPING
Setting Setting
VER N/A
CL French / English
NC Pulses number / encoder N°1 Pulses number / encoder N°2
NS Nominal speed detected by encoder N°1 in rpm Nominal speed detected by encoder N°2 in rpm
DT Deceleration time of the installation to pass from the nominal speed to the stop
VS Necessarynumberofencoderpulsestoconrmtheoverspeedoutputtriggering
SP1 0
SP2
Hoisting Low Speed detected by encoder N°1 +10% (rpm) Hoisting Low Speed detected by encoder N°2 +10% (rpm)
SP3 Hoisting High Speed
detected by encoder N°1 +10% (rpm)
Hoisting High Speed
detected by encoder N°2 +10% (rpm)
RC Off : Inactive Off : Inactive
DS 10 % 0%
TS Speed : Input of a speed signal. CW : Encoder rotation = clockwise
CCW : Encoder rotation = counter-clockwise
PARAMETERS DETAILS FOR SETTING
NC Theselectedencoderwilldeliverafrequency<1000Hzatnominalspeedotherwisetheoptionofencoderfrequency
divider will be selected.
VS
Thecorrespondingangleoftheconguredpulsesnumberwillbe>mechanicalclearance
The validation angle will be = VS x (360/NC) (Slipping).
The validation time will be = (60xVS) / (NC x Triggering speed)
SP2 Will be = SP3 if no hoisting Low Speed, KGV input will not be wired
RC Will be set on ON if the 2 SIDEOS One monitor the Dynamic Slipping
TheminimumspeedallowedduringaStartorderwillbe>0.2Hzattheencoder
DS Setting of the maximum speed difference in % of the nominal speed (NS)
for the Kinematic Linkage Breaking function
CW/CCW Rotation direction by watching the encoder axis from the front during the hoisting descent
SIME Brakes
www.stromag.com - Customer service / Tel. : +33(0)1 49 90 32 20 / Fax : +33(0)1 49 89 06 38

SIME Brakes
13/05/16
M10054-02-A
Installation and maintenance
SIDEOS Box 2
13/17
Non contractual photographs.
Instructions of this manual must be adhered to, to obtain the performance and the safety of operation of the equipment.
Encoder and limit switch 51 questionnaire No. Q01390-01
Dimensions limit switch 51 No. T10003-01
Installation and maintenance SIDEOS One No. M10054-01
Limit switch 51 - Stromag
Catalog No. D142
Installation and maintenance No. 151-00004
EMC No. 900-00001
7 - START-UP PROCEDURE
> Switch on the SIDEOS Box 2.
> The 2 internal SIDEOS One launch automatically an
AUTOTEST or actuate the RESTART button (Actuated du-
ring 1s).
> Check the autotest result on each SIDEOS One :
TEST FAULT
- Light : Test (red)
- LCD display :
Autotest Fault èFeedback loop open
(31-32 / 33-34 / 35-36 / 37-38).
- Correct the fault and launch again the test with the
RESTART button (Actuated during 1s).
TEST OK and System Fault
- Light : Test (Green) and System Fault (Orange).
- LCD display :
Encoder fault 1 èencoder supply short-circuit
Encoder fault 2 èencoder not connected or
encoder wiring fault
Speed contact fault èwiring fault or wrong speed
contacts information (ch. 2-2).
- Correct the fault and launch again the test with the
RESTART button (Actuated during 1s).
TEST OK
- Light : Test (green).
- LCD display : Parameter SPx active
èConnections are correct
èSet the SIDEOS One parameters - see ch.6
èCheck the command operation and the setting by
following the instructions below :
HOISTING WITH MONITORING OF 3 SPEED THRESHOLDS
Step Point
to check Command Possible
fault Causes
1
Normal
operation and
accordance of
the speed read
on the LCD
display with the
required speed
HS (High Speed)
speed active :
make lifting operate
at nominal and
minimum speed in
ascent then if the
dynamic slipping
function is active
make lifting operate
in descent.
Different
speed Customer data mistake or parameter-setting mistake : NC
zerospeed Coupling not mounted or untighten (encoder 3 fault if function RC=On)
Overspeed
Parameter-setting mistake NC
Parameter-setting mistake : SPx
Speed control mistake
Wrong alignment of the encoder coupling
Wrong parameter-setting of the variable speed drive
Diff speed Parameter-setting mistake, NS, DS
Parameter-setting mistake of the external speed signal
Dynamic
Slipping
Parameter-setting mistake, CW, CCW
External signal mistake
Speed
contact fault Command mistake : See speed contact input
Encoder 3
fault Parameter-setting mistake of the variable speed drive : F mini motor too low
2
LS (Low Speed)
speed active :
make the lifting
operate at nominal
and minimum
speed
Different
speed Customer data mistake
Overspeed
Parameter-setting mistake : DT too short relatively to the real deceleration ramp
Parameter-setting mistake : SPx
Speed control mistake
Wrong alignment of the encoder coupling
Speed
contact fault Command mistake : See speed contact input
3Stop the lifting Static
Slipping
Parameter-setting mistake : DT too short relatively to the real deceleration ramp
Parameter-setting mistake : VS too low relatively to the mechanical slacks
SIME Brakes
www.stromag.com - Customer service / Tel. : +33(0)1 49 90 32 20 / Fax : +33(0)1 49 89 06 38

SIME Brakes
13/05/16
M10054-02-A
Installation and maintenance
SIDEOS Box 2
14/17
Non contractual photographs.
Instructions of this manual must be adhered to, to obtain the performance and the safety of operation of the equipment.
Encoder and limit switch 51 questionnaire No. Q01390-01
Dimensions limit switch 51 No. T10003-01
Installation and maintenance SIDEOS One No. M10054-01
Limit switch 51 - Stromag
Catalog No. D142
Installation and maintenance No. 151-00004
EMC No. 900-00001
èCheck of triggering and reaction mode of the PLC for each SIDEOS One :
SIDEOS function SIDEOS modication Hoisting
control Action expected from the customer
System Fault Disconnect a wire on the encoder input
Make hoisting
operate to the
nominal speed
Check that the customer PLC
reaction is in conformity
for ex :
closing of the emergency brakes.
Overspeed Decrease the active parameter SPx
Differential speed
if parameter setting
Disconnect the wire A on the encoder input
of the other SIDEOS One
Static slipping Disconnect the Descent command and
make hoisting operate in Descent mode.
Dynamic slipping
if parameter setting Reverse the parameter-setting CW / CCW
After each test restore the SIDEOS Oneinitspreviousconguration,makeaRESTARTandproceedwiththefollowingtest.
8 - DIAGNOSIS
The following indicators provide access to diagnosis information
for a quick troubleshooting of your application :
LED lights and LCD display are placed on the front of the SIDEOS
One
When the correct voltage is applied, the LEDs POWER ON light up.
When a SIDEOS One makes an Autotest :
-TheLEDTESTashesOrange.
- Contacts C1-C2-C3-C4-C5-C6 are open.
- The LCD display indicates Autotest.
When a SIDEOS One validated its Autotest :
- The LED TEST lights up in green.
- Contacts C1-C2-C3-C4-C5-C6 are closed.
- The LCD display indicates the active speed parameter and its
value.
When a Test Fault occurs :
- The LED TEST lights up in red.
- Contacts C1-C2-C3-C4-C5-C6 remain open.
- The LCD display indicates a Autotest Fault
When a System Fault occurs :
- The LED SYSTEM FAULT lights up.
- Contacts C1-C2-C3 open
- The LCD display indicates the Fault which caused the triggering.
When an Overspeed occurs :
- The LED OVERSPEED lights up.
- Contacts C4-C5-C6 open
- The LCD display indicates the Overspeed type which caused the
triggering.
SIME Brakes
www.stromag.com - Customer service / Tel. : +33(0)1 49 90 32 20 / Fax : +33(0)1 49 89 06 38

SIME Brakes
13/05/16
M10054-02-A
Installation and maintenance
SIDEOS Box 2
15/17
Non contractual photographs.
Instructions of this manual must be adhered to, to obtain the performance and the safety of operation of the equipment.
Encoder and limit switch 51 questionnaire No. Q01390-01
Dimensions limit switch 51 No. T10003-01
Installation and maintenance SIDEOS One No. M10054-01
Limit switch 51 - Stromag
Catalog No. D142
Installation and maintenance No. 151-00004
EMC No. 900-00001
MISTAKES OF INSTALLATION OR APPLICATION : Light off ÅÅÅ: Light on
LCD
display
POWER
ON
TEST
SYSTEM
OVER-
SPEED
Mistake types Possible causes Solutions
no 24VDC
supply on
terminals 2
and 3 of the
SIDEOS One
Lack of mains voltage Check the wiring, the mains voltage
and correct the fault.
Restart the SIDEOS One.
Mains Protection Triggering :
Fuse F2- F3 out of order
Internal supply failure Return the SIDEOS One for repair
Encoder 1 Fault Å/ÅÅ
Encoder
supply
short-circuit
External fault of wiring : Short-circuit
1of terminal UB to ground (OV)
Check the wiring and correct the fault.
Restart the SIDEOS One.
Encoder internal fault Replace the encoder
Encoder 2 Fault Å/ÅÅEncoder
signals fault
External fault of wiring : Short-circuit -
cut wire - wire wrongly connected on
terminals 9 to 14
Check the wiring and correct the fault.
Restart the SIDEOS One.
Encoder internal fault Replace the encoder
Encoder 3 Fault Å/ÅÅEncoder
rotation fault
Encoder coupling fault Check the encoder coupling
mini speed during operation at speed 2
orspeed3<0.2Hz(encoder)
Modicationoftheparameter-settingof
the variable speed drive
Speed
contact fault Å/ÅÅWrong speed
information
Control fault
Ascent and Descent information
overlap
High Speed order in stop position.
Discrepancy of relays RLS3/RLS4 or
RLS5/RLS6
Relays RL1-RL2-RL3 or RL4 stuck
Check the wiring
Check the relays operation
Correct the fault.
Restart the SIDEOS One.
Contactor fault Å/ÅÅ/Å
Mistake in a
feedback loop
During a triggering System Fault or
Overspeed, the feedback loop remains
open
Check the feedback loops wiring
Check the wiring of KDS (4-5).
Check the relays :
RLS7-8-9-10-11-12-13-14
Restart the SIDEOS One.
Autotest fault ÅÅÅÅDuring the test or a reset demand, the
feedback loop remains open
Overspeed 2 (Low
Speed)
Overspeed 3 (High
Speed)
Diff speed
Static Slipping
Dynamic
slipping
Å/ÅÅOverspeed
Real Overspeed, see procedure of
start-up to know the causes of wrong
detection.
Check the parameter-setting
Check the encoder mounting
Check the variable speed drive
After carrying out all the indicated checkings, restart the SIDEOS One, if the fault persists consult us.
SIDEOS One INTERNAL FAULT
Internal fault Å/ÅÅInternal
signals fault Overspeed function internal fault Restart and check the programming of
the SIDEOS One.
If the fault comes back, return the
SIDEOS One for repair
Autotest fault ÅÅÅÅInternal
signals fault
Welding, short-circuit, faulty internal
component.
For each SIDEOS One :
SIME Brakes
www.stromag.com - Customer service / Tel. : +33(0)1 49 90 32 20 / Fax : +33(0)1 49 89 06 38

SIME Brakes
13/05/16
M10054-02-A
Installation and maintenance
SIDEOS Box 2
16/17
9 - STARTING-UP REPORT
APPLICATION…………………………….............. CRANE N° ………………………....…. Place :………………......................
SIDEOS Box 2 N° …………… LIMIT SWITCH 51 Type :..………………................................. N° ……………
Reminder :
The frequency provided by the
encoder at nominal speed of the
machinery must be lower than
1000Hz.
SIDEOS One PARAMETERS SETTING see ch.8
Customer data SIDEOS One parameters
Number of encoder pulses pulses NC = pulses
Nominal speed rpm NS = rpm
Deceleration time s DT = s
Mechanical slacks ° VS = pulses
Speed 1 rpm SP1 = rpm
Speed 2 rpm SP2 = rpm
Speed 3 rpm SP3 = rpm
Encoder rotation checking Y/N RC =
% Differential speed % DS = %
Differential speed Y/N TS =
Dynamic slipping Y/N
ELECTRICAL CONNECTION OK
Protection and connection of mains input
Mounting and connection of the encoder
Speed contact
Connection of the feedback loop : NC contact
Periodic test
ACTION OF THE OUTPUT CONTACTS TOWARDS è
Alarm Electrical Stop Service brakes Emergency brakes Connection
System Fault Required
Overspeed Forbidden Forbidden Required
STARTING UP OK
Autotest
Lifting operation without fault
System fault triggering : Encoder fault
System fault triggering : Speed contact fault
System Fault triggering : Contactor 1 and 2 fault
Overspeed triggering
Differential Speed triggering
Static Slipping triggering
Dynamic Slipping triggering
TEST made by : ……………………………………..……………., on ……………………… Signature :
DocumenttobekeptwithnotimelimitintheequipmentleandprovidedtoGKNStromag
France for all request of technical assistance.
SIME Brakes
www.stromag.com - Customer service / Tel. : +33(0)1 49 90 32 20 / Fax : +33(0)1 49 89 06 38

SIME Brakes
13/05/16
M10054-02-A
Installation and maintenance
SIDEOS Box 2
17/17
Non contractual photographs.
Instructions of this manual must be adhered to, to obtain the performance and the safety of operation of the equipment.
Encoder and limit switch 51 questionnaire No. Q01390-01
Dimensions limit switch 51 No. T10003-01
Installation and maintenance SIDEOS One No. M10054-01
Limit switch 51 - Stromag
Catalog No. D142
Installation and maintenance No. 151-00004
EMC No. 900-00001
10 -
GUARANTEE, LIABILITY, TECHNICAL ASSISTANCE
Obtaining the installation safety level targeted by the designer,
is conditioned by a correct integration of the SIDEOS One in
the control system.
For this, it is necessary to take into account the operating cha-
racteristics of the SIDEOS One,describedinthisleaetandin
theleaetsquotedbelow,atthedesignstageinordertoensure
the compatibility of the characteristics, connections, parame-
ters of the others components of the control chain such as the
frequency converter, the controller, …
It is important to check that the assumptions used for the se-
lection stated in the commercial offer match the real operating
conditions of the crane.
Installation, start-up and maintenance will imperatively be car-
ried out by skilled personnel, reading and understanding the
recommendationsoftheGKNStromagleaetsanddocumen-
tation.
GKN Stromag France remains at the disposal of their custo-
mers for assistance provision during start-up. Contact your
GKN Stromag sales representative.
Although we provide assistance for the applications, in an in-
dividual way or in our literature, it is the responsability of the
customer to determine the suitability of the product for the ap-
plication.
Specications can change at any time and without previous
notice. Information we provide is presumed to be accurate and
reliable at the time of publication. However, we decline all res-
ponsability for its use.
SIME Brakes
www.stromag.com - Customer service / Tel. : +33(0)1 49 90 32 20 / Fax : +33(0)1 49 89 06 38

SALES HEADQUARTERS
20, allée des Erables - BP 40004
ZI Paris Nord II
95911 ROISSY Charles de Gaulle Cedex
France
Tél. Export: +33 (0)1 49 90 32 20
Tél. France: +33 (0)1 49 90 32 22
Fax: +33 (0)1 49 89 06 38
E-mail: [email protected]
PRODUCTION CENTER
AFTER SALES DEPARTMENT
Avenue de l’Europe - BP 24
18150 La Guerche sur l’Aubois
France
Tél. : +33 (0)2 48 80 72 72
web: www.stromagfrance.com
SIME Brakes
SIME Brakes
www.stromag.com - Customer service / Tel. : +33(0)1 49 90 32 20 / Fax : +33(0)1 49 89 06 38
Table of contents
Popular Measuring Instrument manuals by other brands
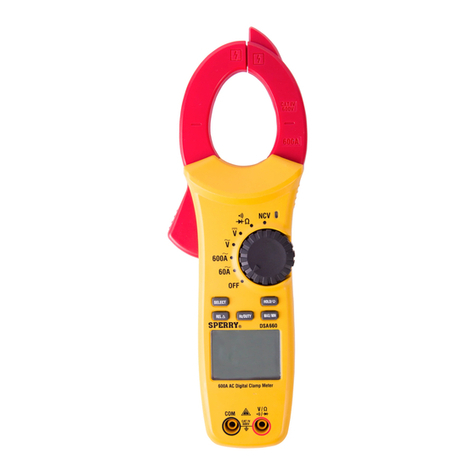
Sperry instruments
Sperry instruments DSA660 operating instructions
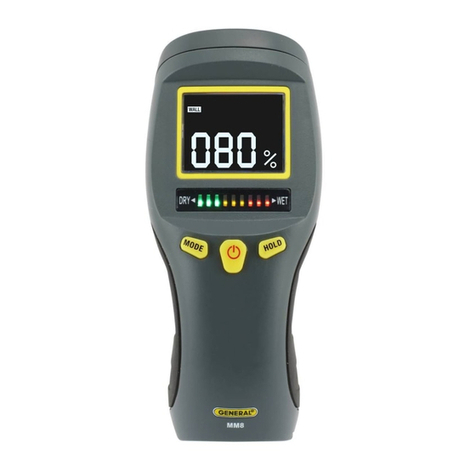
General
General MM8 user manual

Meters UK
Meters UK 3MB100 user manual
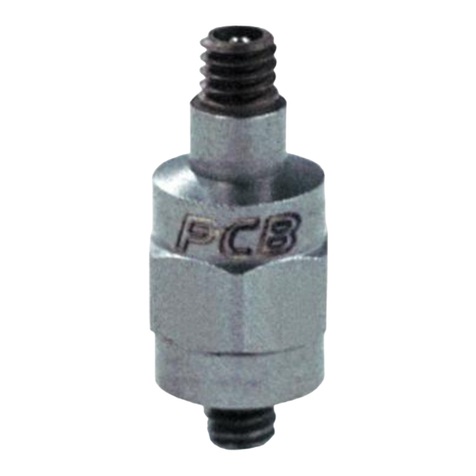
PCB Piezotronics
PCB Piezotronics M353B16 Installation and operating manual
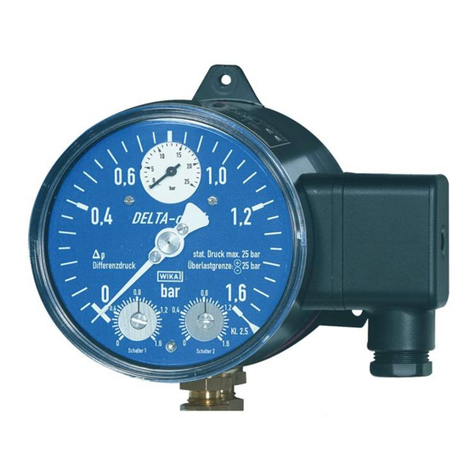
WIKA
WIKA Delta-comb operating instructions

EternalArts
EternalArts Universal Tape Stage operating instructions