Stuart SC130 Manual

CUBE ICEMAKER MODELS
SC130 SC220 SC270 SC500
GENERATION 3 CONTROL BOARD
INSTALLATION
AND
SERVICE MANUAL
Revision 1
STUART MANUFACTURING
1 Jayelem Crescent
Padstow NSW 2211 Australia
Telephone (02) 9773 3711
Fax (02) 9773 4400
www.icemachines.com.au

PAGE
Specicaons 1
Installaon Instrucons 2
Operaon of Machine 3
Touch Panel 4
Adjustments 5
Trouble Shoong 6—8
Cleaning & Servicing 9
Control Board Flow Chart 10 - 12
Notes 13
Control Board Connecon Diagram 14
Parts List 15
TABLE OF CONTENTS

SPECIFICATIONS
MODEL
WATER
All Models Minimum: 140 kpa
OPERATING
All Models Minimum: 1 degree Celsius
FAN PRESSURE
CONTROL
WATER
CONNECTION
All Models 3/4” BSP male stop cock
DRAINAGE
All Models 25mm diameter PVC
SC130 SC270 SC500
ELECTRICAL
REFRIGERATION
240 volts
50 hz
5.6 amps
R404A
232kpa
240 volts
50 hz
8.6 amps
R404A
232kpa
240 volts
50 hz
12.0 amps
R404A
232kpa
ICE WEIGHT (Total both slabs)
PURGE AMOUNT
SC220
240 volts
50 hz
8.6amps
R404A
232kpa
SC130
1,500g
200ml
SC220
2,100g
300ml
SC270
2,700g
300ml
SC500
5,400g
400ml
1

LOCATION
Note! This icemaker must always be installed in a weatherproof environment
1. All models, allow a minimum of 250mm above for correct venlaon.
2. Machine must be LEVEL.
3. Incoming water temperature aects ice producon. Therefore, avoid above ground
plumbing and pipes exposed to direct sunlight.
4. Make sure drain hose has no kinks and has a fall to oor waste.
5. If water pressure is over 350kpa, a pressure reducon valve must be ed.
6. An approved back ow prevenon device must be ed.
START-UP PROCEDURE
1. ENSURE MACHINE IS LEVEL
2. Connect non return valve to tap, then water hose between valve and icemaker and turn
on water. Note! Non return valve must always be ed at the water supply point.
3. Remove front and side panels.
4. Turn on power.
5. Wait unl “Hi oat” light is illuminated, then press and hold RESET buon for about 5
seconds. The machine should now be in normal icemaking mode. i.e. the compressor and
water pump should both be running.
6. Set water purge (see water purge adjustment—Page 4).
7. Allow machine to complete two (2) cycles before making any adjustments (see
Page 3).
8. Replace all panels.
NOTE: On some models the top ice cubes may be slightly thinner than the boom ice
cubes. This is quite normal.
INSTALATION INSTRUCTIONS
2

OPERATION OF MACHINE
3
WARM UP CYCLE
In this mode the compressor is on, hot gas valve open, water pump and ll solenoid o.
(Defrost cycle) The compressor will run for two (2) minutes and will then switch o.
The pump will start and nothing else will happen for a further three (3) minutes.
At the end of this period the display will automacally switch to l__l and the ICE MAKE
CYCLE will commence
On inial start up the warm-up cycle can be cancelled by pushing the reset buon.
WHY A WARM UP CYCLE?
The warm up cycle has been designed in the soware to protect the machine from damage in
the event of a power failure during the freezing cycle. By using the WARM UP (defrost)
CYCLE No. 1 when power is restored, any ice which had formed on the icemaking plates
before the power failure will be fully removed before the ICE MAKE CYCLE recommences.
ICE MAKE CYCLE
The machine will remain in the icemaking cycle unl:
a) the ice storage bin is full, at which me the number is 7 displayed
As soon as ice is removed from the storage bin, allowing the aps to close, the
machine will go back to the start of the ICE MAKE CYCLE.
NOTE: The machine will only go into the ICE BIN FULL MODE aer a defrost and
both aps must be closed before it will return to the ICE MAKE CYCLE.
b) an error occurs and 3, 4, 5 or 9 ashes and the alarm sounds.
Aer a fault has been reced, press the reset buon to return the machine to the ICE
MAKE CYCLE.
ERROR CODES
There are four (4) error codes in the soware
3Did not ll with water in me
4Did not make ice in me
5Did not defrost in me
9Refrigerant high pressure fault
NOTE!
If an error 3 occurs, the machine will aempt to ll every hour unl the water supply is restored.Therefore, if
the water supply is interupted aer-hours, the machine may be funconing normally the next morning and
the only evidence of a problem may be a shortage of ice in the bin. If this becomes a regular occurrance, then
the cause of the interupon should be reced.
For more detailed informaon on the operaon of the machine, refer to the OPERATIONAL FLOW CHARTS on
pages 9 to 11.

4

ADJUSTMENTS
There are only two (2) adustments which can be made to the machine, Water Purge and
Ice Thickness.
WATER PURGE (Parameter 4)
Water purge should be set at approximately 5-10% of the weight of ice per cycle (Check specicaons
chart on page 1 for recommended amount) As the water purge is me acvated, it will vary with water
pressure.
The purge drain is at the R/H rear of the icemaker
While the machine is in the normal ice make cycle (i.e. compressor and pump are running) Press and hold
the RESET buon, aer 3 seconds the display shows –
Release the RESET buon, display ashes 0. To change the number, press the MANUAL DEFROST buon
unl the number 4 is displayed.
Once the number 4 is displayed, press and hold the RESET buon (to conrm selecon) and the display will
change to —
Release the RESET buon.
Now press the “CLEAN BUTTON” to cycle through 1 to 0 with 1 being the minimum and 0 being the
maximum
To return to normal ice making mode, press and hold RESET buon unl display shows –
Note: This funcon only works during freezing cycle.
ICE THICKNESS
The recommended weight of ice per cycle has been factory set with the machine LEVEL and the correct
purge. If the machine is not installed level or there is insucient purge this can alter the weight of the ice
so it is recommended that the purge is set before adjusng the ice weight.
NOTE: Refer to specicaon chart on page 1 for correct ice weights.
Adjustments are made using the – and + buons on the front display board
There is a range of 0 to 9 with 0 being the minimum and 9 being the maximum
To make the ice thicker i.e. heavier, use the + buon
To make the ice thinner i.e. lighter, use the - buon
NOTE: All buons on the control panel have a built in three to ve (3-5) second delay except the ice
thickness adjustment..
i.e. each buon must be depressed for three to ve (3-5) seconds before the funcon will
be acvated
When the power is rst turned on 0 will appear in the window and 1 beep will be heard.
(The beep indicates the version number on the logic board i.e. 1 beep = Version 1) .
The machine will then go to No. 1 warm up cycle.
5

TROUBLE SHOOTING
MICROPROCESSOR DIAGNOSTICS
The 3rd generaon control board has a non volale memory which stores a fault history for the icemaker, plus
other diagnoscs such as total machine running hours, number of cleaning cycles performed and number of
icemaking cycles.
ACCESSING DIAGNOSTIC DISPLAY
While the machine is in the normal ice make cycle (i.e. compressor and pump are running) Press and hold the
RESET buon, aer 3 seconds the display shows a dash –
Release the RESET buon, display ashes 0. To change the number, press the MANUAL DEFROST buon unl the
desired diagnosc parameter is displayed
Available parameters are:
0Access last ve faults
1Number of hours since machine was last cleaned
2Number of cleaning cycles performed
3Number of ice harvests
4Purge adjustment
Once the desired diagnosc number has been selected, press and hold the RESET buon (to conrm selecon)
the display will change to a dash –
Release the RESET buon, display now shows the selected parameter
To adjust the purge press the CLEAN BUTTON to cycle through from 0 to 9
To return to normal ice making mode, press and hold RESET buon unl display shows a dash –
ERROR 3 DID NOT FILL WITH WATER IN TIME (3 Minutes)
If the water level oat does not see a high-water level within 3 minutes of calling for water the machine will stop,
indicate No3 and beep 3 mes every couple of minutes. This is the only fault that will try to restart every hour
unl the water is reinstated. If the reset buon is pressed the machine will try to restart.
Possible causes
(1) Water supply turned o
(2) Water supply line restricted or frozen
(3) Blocked strainer in water solenoid
(4) Faulty water solenoid
(5) Faulty water oat switch
(6) Blocked water lter
(7) Faulty water pump
(8) Faulty water oat switch
6

ERROR 4 DID NOT MAKE ICE IN TIME (40 Minutes)
If the low oat does not drop within 40 minutes from the beginning of the ice making cycle the machine will
shut down and indicate No4 and beep 4 mes every couple of minutes. The machine can be restarted by
pressing the reset buon or turning the power o and on at the power point.
Possible causes
(1) Paral loss of refrigerant
(2) Faulty fan motor
(3) Dirty condenser
(4) Faulty compressor
(5) Hot gas solenoid stuck open
(6) Faulty expansion valve
ERROR 5 DID NOT DEFROST IN TIME (7 Minutes)
If both water curtain switches do not send a signal that harvest is completed aer 7 minutes the machine will
shut down, indicate No 5 and beep 5 mes every couple of minutes. The machine can be restarted by press-
ing the reset buon or turning the power o and on at the power point.
Possible causes
(1) Faulty hot gas solenoid
(2) Dirty icemaking plate
(3) Faulty curtain ap switch
(4) Paral loss of refrigerant
(5) Ice too thin - will not open water curtain
ERROR 9 HIGH PRESSURE FAULT
If refrigerant pressure exceeds 3100kpa the machine will shut down and indicate No9
Possible causes
(1) Dirty condenser
(2) Failed fan motor
(3) Faulty pressure sensor
(4) Faulty compressor
(5) Very high ambient temperature at locaon
TROUBLE SHOOTING CONTINUED
7

CHECKING OPERATION OF REED SWITCHES
The curtain ap switches and the high and low oats have indicator (red LED) lights on the main control board.
To check the operaon of these switches, set the machine in the WARM UP CYCLE with no water in the water
trough.
CURTAIN FLAP SWITCHES
By moving the water curtains ,the lights marked FLAP 1 and FLAP 2 should be on when the curtain is closed and
o when the curtain is about 10 to 15mm open.
LOW FLOAT
With the low oat all the way down, the indicator light should be o, but by moving the oat up the indicator
light should come on.
NOTE: If the reverse is happening, rotate the whole oat switch assembly 180degrees
HIGH FLOAT
With the high oat in down posion, the light should be o, but by moving the oat up, the light should come
on.
NOTE: If the reverse is happening, rotate the whole oat switch assembly 180degrees
ELECTRONIC CONTROL BOARD FUSE - MAIN CONTROL BOARD
The main control board is protected by a fuse. If this fuse should blow it will isolate the whole machine. The
correct replacement fuse is a slow blow 3.15 amp HRC Ceramic.
DO NOT USE GLASS TYPE FUSES
When changing the control board ensure that the incoming acve goes to the relay tab marked COM.
Curtain ap switches
High oat switch
Low oat switch
8

SERVICE MODE 8
Aer 3000 hours of ice making me there will be 10 beeps and number 8 will ash 10 mes indicang that
the machine requires servicing. This will occur every hour unl the machine has been put through a clean
cycle. Once the clean cycle has been carried out the machine starts counng the hours again. Note: Ice
making me does not include bin full me.
CLEAN CYCLE 6
Cleaning of the icemaker is recommended on a regular basis, at least three mes a year.
1. Turn o water and t new water lter and purge water supply line.
2. Empty the remaining ice in storage bin into a clean hygienic sealed receptacle and seal to prevent
contaminaon. (Always dispose the boom 20% of ice in bin as it will most likely be dust
contaminated).
3. Remove front, top and right side panels, visually check all components are in sasfactory condion and
do not require replacement due to mechanical or electrical breakdown.
4. With the machine in ICE MAKE CYCLE press & hold the clean buon unl the machine goes into clean
mode 6, wait for the water trough to ll and the ll light goes o then remove the drain cap from the
trough and allow all the water to drain away and replace the drain cap.
5. Mix the specied quanty of cleaning medium as per manufacturers specicaons in a separate
container and pour into water trough and allow to circulate for 25 minutes maximum or unl plate is
clean. Then drain the water trough and replace drain cap.
6. Mix up sanizer in a container as per manufacturers specicaon and pour into water trough and allow
to circulate for 5 minutes. Remove drain cap and drain water trough then replace drain cap.
7. Press the ll buon unl the water overows the trough, remove the drain cap and allow all the water
to drain away, replace cap, press ll buon again, when full let circulate for 5 minutes before draining
trough.
8. Replace drain cap and PRESS RESET. When display returns to NORMAL ICE MAKER CYCLE switch o
power.
9. Vacuum or blow out condenser ensuring dust does not contaminate the surrounding area.
10. Wipe out Compressor secon removing dust and grime around fan motor. Spin fan and check for noisy
bearings.
11. Remove pump from trough and drain out and clean out any sludge remaining in trough. Dismantle
water distributor and clean with bole brush taking note that all water holes are clean and
unobstructed. Reassemble and ret distributor and water pump.
12. Sanize storage bin as per manufacturers specicaons.
13. Start machine & check all machine signal funcons, ensuring board lights operate when curtains, high /
low switches are acvated.
14. Check purge on ll cycle and adjust if required. (See Page 3)
15. Aer second ice drop check thickness and adjust if required. (See Page 3)
16. Replace machine panels.
17. Clean down all external surfaces.
18. Replace ice into storage bin.
Note: Using none-approved cleaning medium may void ice making plate warranty
9

Run self test procedure
Compressor ON, Hot gas ON, fill to
Hi then run on hot gas for 2 minutes
Compressor OFF, pump ON
delay for 3 minutes
Is bin
Full ?
Fill ON, Compressor ON, Pump ON,
Hot Gas OFF, Start Fill timmer
Wait for correct quantity of water in
tray or fill
t im er t o t im e out
Reset button
pushed
Fill solenoid OFF Start Error Timer
for icemaker cycle
Error
Timer?
No
Go To
DEFROST
Go to Man.
Defrost
Go to
Clean
Didn't Fill In Time
No
Yes
Go to Bin
Full
Yes
No
Note: 5
See Note 1
Power Up
FILL ERROR
ICE MAKE ERROR
Ice Make Cycl e Starts
See Note 3
Start Up Defrost Stage 1
Start Up Defrost Stage 2
Didn't make Ice in Time
Manual
defrost
Clean
Button
Yes, Manual Defrost button
pushed
Yes, Clean Button pushed
Lo
Float?
Yes, the correct quantity of
Water has been used to make ice
No
No
See Note 2
See Note 2
Retry every 60 minutes
See Note 7
Clean
Timer?
No
error '8' & sound alarm
ten times , repeat every
hour
Yes
7
3
4
Display
Display
Display
Note: 4
Note 6
10

Fill & Pump On Compressor
Off
Water
Full?
(Hi Float)
No
Man Fill
Button
Pres sed
Reset
Button
Pushed
Fill Solenoid
Off
Fill
ON
Yes
Return To
Normal Ice
Make
Yes
No
No
Yes
Clean Cycle Processing
Clean Cycle
Reset Clean Hour Counter
6
Display
Note 6
11

Pump
OFF
Hot - gas solenoid
ON
Both
flaps
operated
Defrost
Timed
out
No
No Yes
Return
To
Make
ice Cycle
Yes
Did both
flaps close
after opening
Yes
Compressor,Pump,Fill
OFF
Hot Gas solenoid
On
No
Defrost
Is This
a
M anal
Defrost ?
No
Yes
Manual
Button
Pressed?
Yes
No
Bin Ful l
Defrost Error
Bin Ful l
BIN FULL and DEFROST Processing
5
Display
See Note 7
12

Note 1.
Self Test Procedure.
Fail = Buzzer sounds connuously.
Pass = Buzzer beeps several mes, the number of beeps indicates the control
board version number, e.g. 1 beep for version 1 etc.
Note 2.
The hot gas solenoid is always opened for 15 seconds before starng the compressor,
this allows the gas pressures to equalise before the compressor starts.
Note 3.
Pushing the reset buon during the inial start up defrost will cancel the defrost and place
the machine in normal ice making mode.
Note 4.
Bin Full is indicated by one or more of the ice curtains remaining open aer an ice drop.
Note 5.
The correct quanty of water during ll is signalled by the high oat switch, the water lls unl the
top oat switch operates. The water will connue to ll for a period of me aer reaching the high
oat. This is the purge me.
Note 6.
The clean mer is set for 3,000 hours, this mer is reset when the manual clean cycle
is acvated.
Note 7.
The rst me this error occurs the machine will restart at “Power Up” if the same error is detected
aer Power Up the machine will shut down and the appropriate error number will ash on the display.
13

Wiring harness idencaon numbers and colours
1. Brown HOT GAS
2. Red PUMP
3. Orange FAN
4. Yellow WATER INLET
5. Green LOW FLOAT
6. Blue HIGH FLOAT
7. Purple FLAP 1
8. Grey FLAP 2
9. White FAN CONTROL
0. Black HP CONTROL
15

DESCRIPTION
Compressor
Fan/motor assy.
Fan control
Curtain Assembly—Front
Curtain Assembly—Rear
Evaporator Assembly
Solenoid valve - water
Solenoid valve - hot gas
Capillary tube
Expansion valve body
Expansion valve orice
Control board
Display board
Fuse - 3.15 amp
SC130
050654
050348
050622
050774
050773
050478SP
050023
050704
1.62mm
2500mm
———
———
050844F
050877
050011
SC220
050766
050348
050622
050757
050756
050751
050023
050704
1.78mm
2600mm
———
———
050844F
050877
050011
SC270
050766
050348
050622
050776
050775
050523SP
050023
050704
1.78mm
2250mm
———
———
050844F
050877
050011
SC500
050841
050620
050622
050778
050777
050524SP
050023
050705
———
———
050850
050851
050844F
050877
050011
PARTS LIST
16

MANUFACTURER'S LIMITED LABOUR AND PARTS WARRANTY
STUART COMMERCIAL ICEMAKERS
Model SC130, SC220, SC270, SC500
CERISUN PTY. LTD. trading as STUART MANUFACTURING at 1 JAYELEM CRESCENT PADSTOW warrants to the original owner/user that any
STUART commercial icemaker manufactured on or aer January 1st 1997 shall be free of defects in material or workmanship under normal
and proper use and maintenance service as specied by STUART MANUFACTURING and upon proper installaon and start-up in accordance
with the instrucon manual supplied with the Product.
The obligaon under this warranty is limited to:
(1) associated and approved labour costs for a period of two years aer the date of original installaon;
(2) the repair and or replacement of parts or assemblies that in the opinion of STUART MANUFACTURING are
defecve, for a period of two years aer the date of original installaon;
(3) the supply or repair of the electronic control board(s) for a period of two years aer the date of original installaon.
The labour warranty shall include straight me labour charges at the product locaon only and shall exclude charges for travel me, mileage
or other premium charges.
Any labour required to full the warranty obligaon must be performed by a refrigeraon service company qualied and accepted by STU-
ART MANUFACTURING.
This warranty does not include parts or labour coverage for components failure or other damage resulng from:
*external electrical power failure or miswiring to the Product for any reason
*external water supply failure or plumbing problems to the Product for any reason
*external drain line malfuncon
*adverse operang condions as set forth in the owner/user manual for the Product.
All claims for labour or parts must be made through the original reseller. The defecve part for which reimbursement is claimed, together
with the service invoice, must be returned to STUART MANUFACTURING, freight pre-paid, within een days from date of service to be
eligible for labour and parts warranty coverage. All replacement parts must be approved STUART parts.
Incidents of failure that do not require the replacement of a part shall be explained in sucient detail on the service invoice to
idenfy the failure. All claims shall include the product model number, serial number, original date of installaon and customer idenca-
on.
The foregoing warranty shall not apply to:
(1) Faults caused by dirty water distribuon systems or icemaking plates
(2) Adjustments to ice thickness or purge levels caused by incorrect installaon.
(3) any part or assembly
(a) that has been altered, modied or changed
(b) that has been subjected to misuse, abuse, neglect or accidents or
(c) any Product or part on which the serial or model number has been removed or altered
(4) any Product that has been installed and/or maintained inconsistant with STUART technical publicaons
(5) any product that has been installed or is located outside Australia.
The two years compressor parts warranty shall not apply when the Product's refrigeraon system is modied with a condenser, heat re-
claim device, or parts and assemblies other than those manufactured by STUART MANUFACTURING unless STUART
MANUFACTURING has accepted modicaon for specic installaon in wring.
STUART MANUFACTURING assumes no liability for misuse or inadequate maintenance of the Product.
In no event shall the owner/user be entled to recover incidental or consequenal damages, including but not limited to damages for incon-
venience, ice purchase, rental or replacement equipment, loss of prots or other commercial loss.
Warranes stated above are the only warranes made in connecon with the sale and distribuon of the Products.
ANY AND ALL OTHER EXPRESSED, STATUTORY AND IMPLIED WARRANTIES APPLICABLE TO THE PRODUCT,
INCLUDING, WITHOUT LIMITATIONS, ALL IMPLIED WARRANTIES OF MERCHANTABILITY AND FITNESS FOR USE ARE EXPRESSLY DISCLAIMED.
The warranty informaon set forth above shall be governed by and construed in accordance with the laws of the state of NSW and, if appli-
cable the laws of Australia. The labour warranty, as stated is extended only to the original owner/user and is not assignable to any other
owner or user.

WARRANTY CLAIM GUIDELINES
Model SC130, SC220, SC270, SC500, SC1000, SC2000
As from January 1st 1993 all STUART ICEMAKERS will carry a standard two years warranty. This covers two years labour, two years on parts
and two years on compressor failure, provided warranty condions are met and installaon is in accordance with published standards.
All dates are from the original date of installaon. This date is assumed to be a maximum of eight (8) weeks from the date of invoice to the
dealer.
Warranty claims are condional on the following:
(1) All claims for labour or parts must be made through the original reseller.
(2) The defecve part must be returned with the service invoice to STUART MANUFACTURING, freight pre-paid, within 15 days of date of
service. Details of End User, Model, Serial Number and Date of Installaon of the product must be provided with the claim.
(3) All replacement parts must be detailed and be approved STUART parts.
(4) All labour only claims must be explained in sucient detail on the service invoice to properly idenfy the nature of the failure.
(5) The labour warranty includes standard straight me charges at the installaon locaon only and does not include charges for travel
ling me, mileage or other premium charges.
(6) When consumables such as driers,refrigerant etc. are supplied by the service agent, the cost allowed will be the
Refrigeraon Wholesalers list price only.
(7) If a compressor is faulty and requires replacement, the service agent MUST contact Stuart Manufacturing before obtaining a replace
ment.
The warranty will not apply in the following circumstances:
(1) When any part, assembly or ice machine:
(a) has been altered, modied or changed
(b) has been subject to misuse, neglect or accident
(c) where the serial number or other idencaon has been removed or altered.
(2) When the product has been installed and or maintained in a manner inconsistant with the approved procedure or STUART technical
publicaons.
(3) The two years compressor warranty will not apply where the refrigeraon system has been modied with a condenser, heat reclaim
device or part or assembly not approved by STUART MANUFACTURING.
GENERAL
As from 1st January, 1993 the following warranty will apply to all spare parts:
(a) Replacement parts exchanged while the original equipment is sll under manufacturers warranty will be covered on a pro-rata
basis up to the warranty expiraon of equipment in which they are installed.
(b) Warranty on spare parts other than the above is three (3) months from the date of installaon as evidenced by suitable docu-
mentaon or eight (8) weeks from the invoice date of sale to the dealer.
Other manuals for SC130
1
This manual suits for next models
3
Table of contents
Other Stuart Ice Maker manuals
Popular Ice Maker manuals by other brands
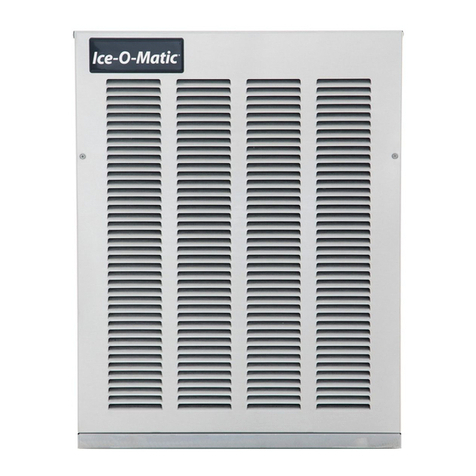
Ice-O-Matic
Ice-O-Matic MFI Series Cleaning and Sanitizing Instructions
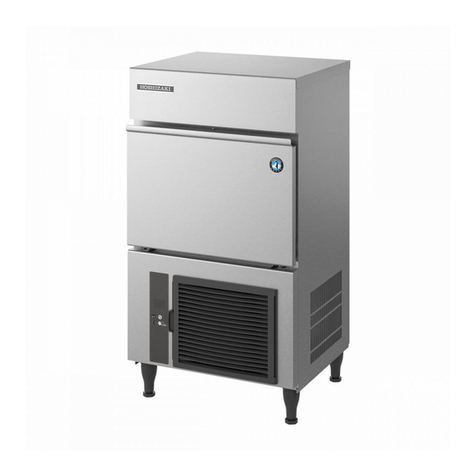
Hoshizaki
Hoshizaki IM-30CNE-HC instruction manual
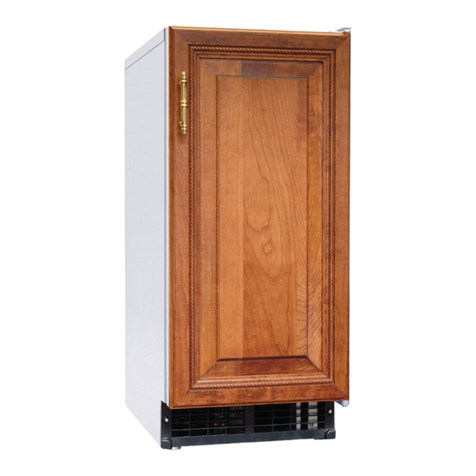
Hoshizaki
Hoshizaki C101BAHA Service manual
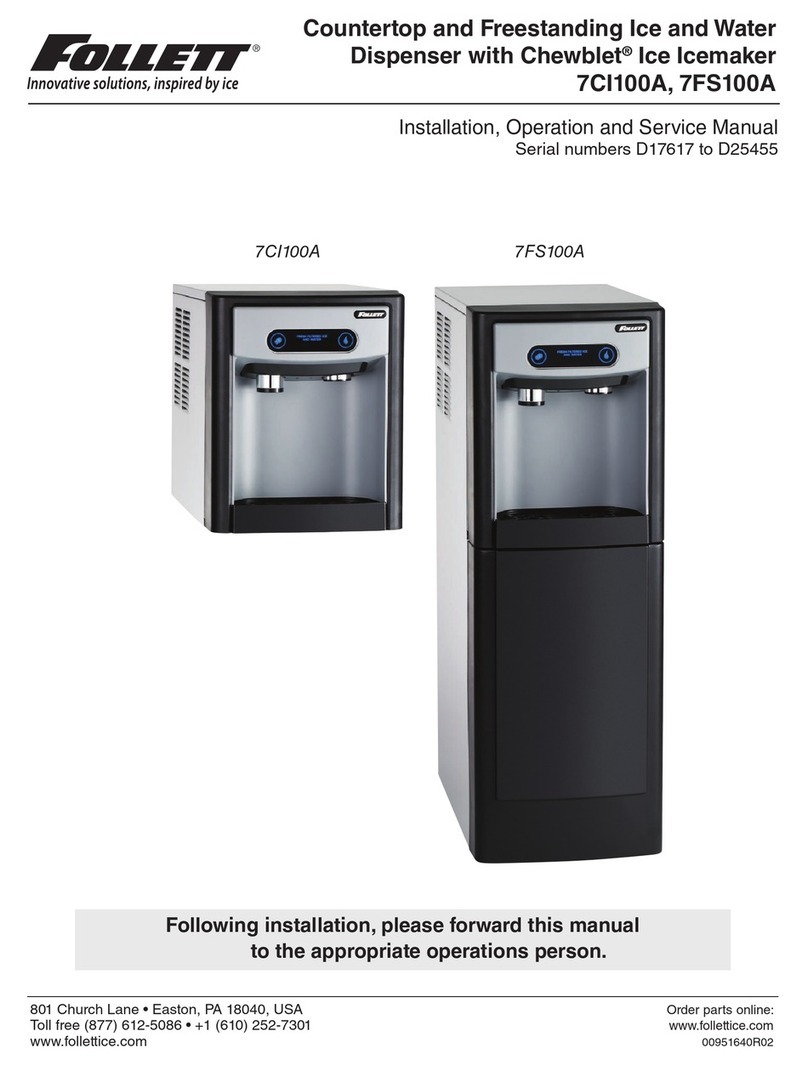
Follett
Follett D17617 Installation, operation and service manual
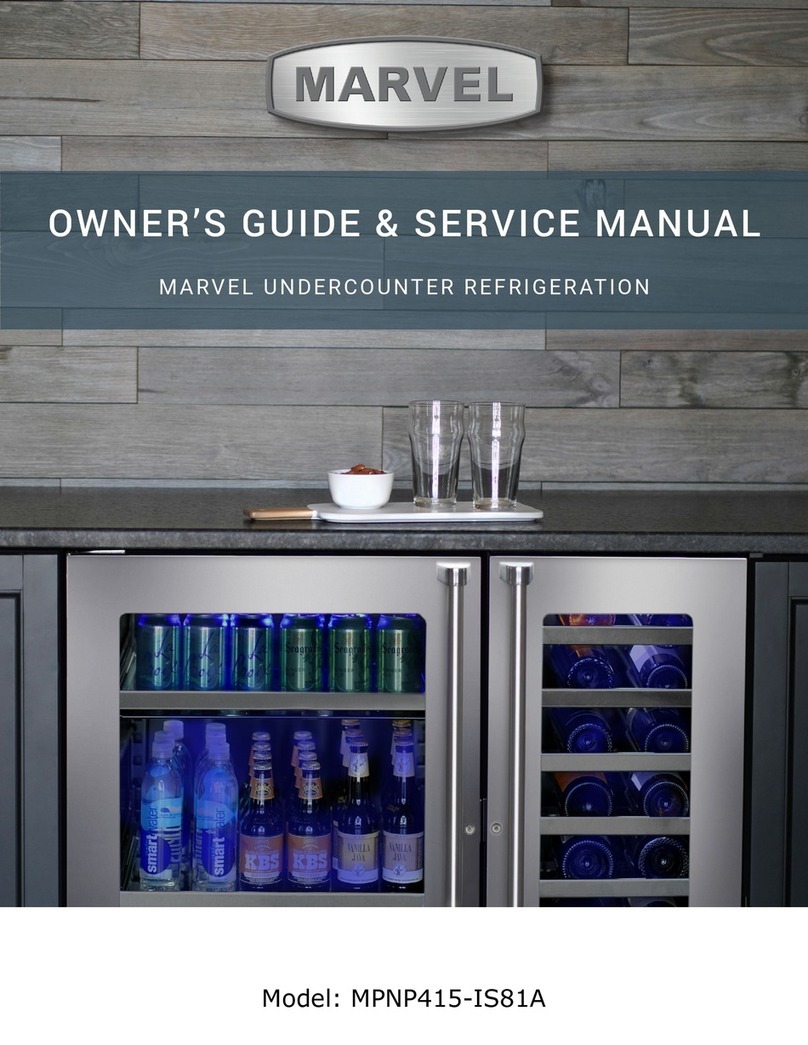
Marvel
Marvel MPNP415-IS81A owner's guide
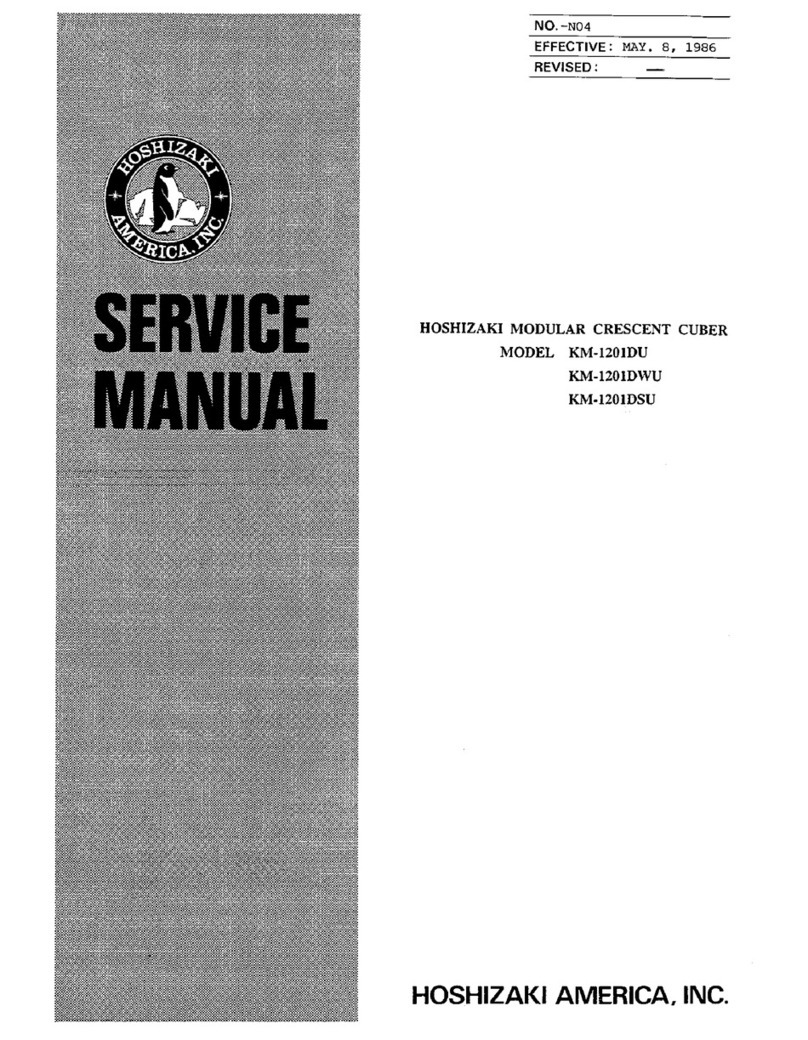
Hoshizaki
Hoshizaki KM-1201DSU Service manual