SunStar Fortuna 5 Series User manual

Version
1.0
USSR'S
MRNURL
PARTS
ROOK
es
5
ISO
9001
Certification
of
Quality
System
1)
FOR
AT
MOST
USE
VmH
EASINESS,
PLEASE
OBTTAINLY
READ
THIS
MANUAL
BEFORE
STARTtNG
2)
KEEP
THIS
MANUAL
IN
SAFE
PLACE
FOR
RffB)BICE
WHSI
THE
MACHINE
BREAKS
DOVm.

1.
Thank
you
for
purchasing
our
product.
Based
on
the
rich
expertise
and
experience
accumulated
in
industrial
sewing
machine
production,
SUNSTAR
wili
manufacture
industrial
sewing
machines,
which
deliver
more
diverse
functions,
high
performance,
powerful
operation,
enhanced
durability,
and
more
sophisticated
design
to
meet
a
number
of
user's
needs.
2.
Please
read
this
user's
manual
thoroughly
before
using
the
machine.
Make
sure
to
properly
use
the
machine
to
enjoy
its
full
performance.
3.
The
specifications
of
the
machine
are
subject
to
change,
aimed
to
enhance
product
performance,
without
prior
notice.
4.
This
product
is
designed,
manufactured,
and
sold
as
an
industrial
sewing
machine.
It
should
not
be
used
for
other
than
industrial
purpose.
SUNSTAR
CO.,
LTD.
From the library of Superior Sewing Machine & Supply LLC - www.supsew.com

DAS
Certification
Scope
of
Quality
Approval
The
following
Company
SUNSTAR
ELECTRIC
CO.,
LTD.
The
Company
has
been
approvedfor
the
following
scope
of
operation:
Manufacture,
Sale
and
Servicing
of
Motors
and
Controllers
for
Sewing
Machines
and
Embroidery
Machines
Scope
of
approval:
NACE
19,
Electrical
and
optical
equipment
Date
of
Certificate
Issue:
Certificate
Valid
until:
Certificate
Number:
26"^
November
2003
26**^
November
2006
KOl-1714
Date
03^^
December
2003
DAS
CERTIFICATION
Ltd.
Company
Number:
3384526
6
Amber
Court,
Crich
Lane,
Beiper,
Derbyshire
DE56
1
HG
Telephone
&
Fax:
+44
(0)
1773
828586
DAS
Certification
ISO
9001:
2000
Approval
From the library of Superior Sewing Machine & Supply LLC - www.supsew.com

iJiiMj.H-:
"«we?yi»-a-F-WTr"
US€R'
S
MRNURL
s^Wa
From the library of Superior Sewing Machine & Supply LLC - www.supsew.com

CONTENTS
1.
Safety
instruction
6
2.
Precautions
before
use
8
3.
Locating
and
using
parts
of
the
controller
box
10
4.
Installation
11
1)
Mounting
your
Servo
Motor
on
the
table
11
2)
Assembling
the
belt
cover
and
adjusting
the
belt
tension
12
3)
Mounting
and
adjusting
the
fbot-lift
solenoid
13
4)
Mounting
the
position
sensor
(Synchronizer)
and
setting
the
film
14
5)
How
to
equip
and
adjust
a
built-in
location
detector(synchronizer)
16
6)
Mounting
the
Program
Unit(P/U)
18
7)
An
example
of
installing
the
SunStar
sewing
machine
19
5.
Wiring
and
grounding
20
1)
Specification
of
the
power
plug
20
2)
Specification
of
electric
current
in
wiring
of
power
plug
20
3)
Name
and
description
on
the
outside
connector
of
control
box
21
4)
How
to
change
the
electric
voltage
supplied
for
solenoidfThe
factory
installed
setting
is;J2)
•
•
21
6.
Connection
the
earth
wire
of
the
sewing
machine
and
motor
23
7.
Things
to
be
checked
after
installation
23
8.
Program
unit
part
names
and
method
of
use
24
1)
Program
unit
part
names
24
2)
Program
Unit
Method
of
Use
24
3)
Start
and
End
Backtack
Stitch
Conection
Method
35
4)
Method
of
Use:
Inertia
Tuning
Function
38
5)
How
to
Use
Edge
Sensor
39
6)
Motor
Controller
Setting
42
7)
Advanced
Pattem
Sewing
Functions
46
8)
Automatic
Change
Function
ofTwin
Needles
(applicable
to
the
models
supporting
twin
needles)
•
-48
9.
Simple
operation
unit
part
names
and
method
of
use
50
1)
Names
of
Each
Part
in
the
Simple
Operation
Unit
50
2)
Simple
Program
Unit
Method
of
Use
50
10.
Fortune
series
5
full
function
software
method
of
use
55
1)
Basic
Functions
of
the
Fortune
Series
5
Full
Function
Software
55
2)
Fortune
Series
5
Full
Function
Software
Specific
Parameters
56
3)
Method
of
Use
and
Explanations
for
Specific
Items
of
the
Parameter
71
4)
Thread
Trimming
Sequence
Function
Method
of
Use
(Items
no.
54,55,56
of
Group
B)
• •
75
11.
Breakdown
and
troubleshooting
84
12.
How
to
place
for
controller
85
13.
Block
diagram
86
^
Parts
Book
87
From the library of Superior Sewing Machine & Supply LLC - www.supsew.com

SAFETY
INSTRUCTION
Be
sure
to
read
and
keep
in
mind
the
following
instructions
before
you
install
and
use
thr
FORTUN
A
SERVO
MOTOR.
1)
Use
and
Purpose
This
product
is
designed,
manufactured,
and
sold
as
an
industrial
sewing
machine.
It
should
not
be
used
for
other
than
industrial
purpose.
2)
Working
Environment
®
Power
Source
•
It
is
desirable
that
voltage
of
the
power
source
be
kept
within
the
range
of
±
10%
of
the
rated
voltage.
•
It
is
desirable
that
fr
equency
of
die
power
source
be
kept
within
the
rage
of
±
10%
of
the
rated
fr
equency.
(50/60HZ)
•
The
SERVO
MOTOR
can
be
expected
to
work
normaly
only
in
case
the
foregoing
things
are
kept.
©
Electromagnetic
Noise
•
It
is
desirable
that
those
equipments
causing
strong
electromagnetic
fi
eld
or
high
fi
^quency
not
use
the
same
electrical
outlet
as
this
on
and
stay
away
fr
om
it.
@
Temperature
and
Humidity
•
Keep
the
ambient
temperature
above
5
degrees
and
below
40
degrees
Centigrade.
•
Never
use
it
outdoors
and
avoid
direct
ray
of
light
•
Keep
it
away
fr
om
an
hot
object
like
a
stove.
•
Keep
the
ambient
humidity
above
30%
and
below
95%.
®
Never
use
it
near
gases
and
explosives.
®
Do
not
use
it
at
a
spot
located
1,000m
or
higer
above
sea-level.
®
Keep
the
storage
temperature
higher
than
25
degrees
below
zero
and
lower
than
55
degrees
Centigrade
when
not
in
use.
3)
installation
Follow
the
instmction
carefully
when
installing
it.
®
Be
sure
to
start
installing
it
after
pulling
the
power
plug
off
the
outlet
®
Fbc
the
cable
so
that
it
may
not
move,
and
do
not
allow
the
moving
parts
like
belts
to
be
interfered
with.(keep
distance
of
at
least
25mm
fr
om
them.)
®
Be
sure
to
have
the
Controller,
the
Motor
and
the
sewing
Machine
grounded.
@
Be
sure
that
the
voltage
of
power
source
fi
ts
the
specification
of
the
Controller
before
the
power
is
on
®
Be
sure
to
use
Safety
Extra
Low
Voltage
when
an
extra
item
or
an
accessory
is
fi
tted
into
the
Controller.
4)
Disassembly
®
Indisassembling
it,
be
sure
to
wait
at
least
360
seconds
before
taking
any
action
after
pulling
the
plug
off
the
power
source
after
turning
it
off.
®
When
pulling
off
the
plug
fr
om
the
power
source,
be
sure
to
hole
the
plug
itself
instead
of
the
wire
connected
to
the
plug.
From the library of Superior Sewing Machine & Supply LLC - www.supsew.com

5)
Service
and
Maintenance
®
Make
sure
that
service
and
maintenance
are
carried
out
by
a
skilled
technician,
d)
Never
try
to
operate
with
the
Motor
and
the
Controller
open.
®
When
inserting
a
thread
into
or
touching
the
machine,
be
sure
to
turn
the
power
off
and
step
down
fr
om
the
platform.
®
Be
sure
to
use
standard
products
specified
for
replacement
of
parts.
6)
Other
Safety
Instructions
®
Tack
care
not
to
let
your
fi
ngers
touch
any
moving
parts
including
belts.
@
In
case
of
remodellhig
or
fi
tting
of
additional
device,
be
sure
to
follow
safety
standards
and
do
not
ever
try
to
go
ahead
based
on
your
own
judgments.
®
Do
not
try
to
operate
with
the
safely
device
removed.
®
Take
care
not
to
let
water
or
coffee
or
something
like
those
admitted
into
the
Controller
or
the
Motor.
®
Never
drop
the
Controller
or
the
Motor
to
the
ground.
^The
Inslrijc^ons
piBsented
above
are
ft
)r
the
sal^
and
more
proper
operation
of
the
Fcxtura
Motor.
Ignoring
such
instnictions
oould
cause
damage
to
the
machine
or
physical
injury
of
the
user.
FteasetbflowaB
the
Instructions
vvhen
operating
the
rnachine.
From the library of Superior Sewing Machine & Supply LLC - www.supsew.com

2
PRECAUTIONS
BEFORE
USE
1.
Do
not
turn
on
the
power
while
stepping
on
the
pedal.
2.
Turn
off
the
power
when
leaving
the
servomotor
overnight
S[i
3.
Tum
off
the
power
when
servicing
the
servomotor
or
changing
4.
Be
sure
to
keep
the
servomotor
securely
grouned.
the
needle.
E
5.
Do
not
connect
multiple
servomotor
power
plugs
to
the
same
6.
Install
the
servomotor
away
from
noise
sources,
such
as
high-
power
strip.
frequency
equipments
and
welding
machines.
♦-rf
Noise}^-*
7.
Avoid
electrical
shock
when
servicing
the
controller
box.
(Wait
for
6
8.
When
an
error
message
"Er"
appears
on
the
digital
display,
minutes
before
opening
the
cover
after
turning
off
the
power.)
take
a
note
of
the
"Er"
code,
and
then
tum
on
and
off
before
resuming
operation(Contact
the
local
dealer
if
"Er"
message
persists
on
the
display)
From the library of Superior Sewing Machine & Supply LLC - www.supsew.com

(Sun^a^
9.
Adjust
the
t)elt
tension
to
the
optimum
level.
Beit-tension
acfustment
stiould
t)e
peribrmed
after
ttw
motor
is
mounted
on
ttie
table:
First,
loosen
botti
the
upper
and
loMer
anchoring
bolt^0,®).
The
belt
tension
will
then
be
adjusted
by
the
weight
of
servo
motor
Itself.
Fasten
both
anchoring
bolts.
10.
Clean
it
every
two
or
three
weeks
so
that
no
dirt
or
a
dirty
substance
may
be
piled
up.
11.
When
repladng
the
fuse,
use
a
standard
item,
opening
the
12.
Make
the
length
of
the
cable
connected
with
an
outside
parts
cover
as
shown
in
the
diagram.
like
stand-up
pedal
as
short
as
possible.
F1
250V/15A
F2
250V/15A
F3
250V/6.3A
F4
250V/1A
From the library of Superior Sewing Machine & Supply LLC - www.supsew.com

3
LOCATING
AND
USING
PARTS
OF
THE
CONTROLIS
BOX
1)
Left
and
ri
ght
side
of
control
box
Motor
Power
Cable
AG
Power
switch
Standard
Solenoid
Connector
Switch
and
Lamp
Foot^
SoIenokltGreen]
Right
InlSolenotdTBlue)
Tenson-reteaseand
AuxSaiy
sdenoidrwhite)
Encoder
Connector
(Green)
OPTION
Connector
for
Position
Sensor(BIack)
Program
Unit
Connector(VVhite)
2)
Rear
panel
©Caution
WARNING
a
n
A
Hazardous
voltage
will
cause
in^ry.
Be
sure
to
wait
at
least
360
seconds
Isefore
opening
this
cover
after
turn
off
main
switcfi
and
unplug
power
cord.
Hgf
Em
2lofl
^
Em
lhbiji
e^
^
o\mQ.
^
212E5
mm
%
aa
iBini
UM
saoszf
©Motor
©ACINPUT
10
From the library of Superior Sewing Machine & Supply LLC - www.supsew.com

4
INSTALLATION
1)
Mounting
your
Servo
Motor
on
the
table
(D
Make
sure
that
the
holes
are
bored
on
the
table
as
shown
in
the
figure.
L
Table
3-0
9
Hole
MlCabte^tde
BeHHcle
®
Insert
three
motor-fbcing
bolts
through
the
thiee
holes
on
the
table.
Attach
the
motor
base
padded
with
vibration-ptoof
rubber,
and
slide
flat
and
spring
washers
over
the
bolt
stems,
and
then
fasten
the
bolts
with
nuts.
\
Motv-FDdng
Bolts
Table
Motor-Fodng
Bo(ts(3ea)
Vibn^Ptoofnifaber
Flatvy^
SpringWaser
=}=
NutofD
a
Motor-Fixing
Bo!ts(3ea)
mp
Controller
Box
®
Make
sure
that
the
center
of
motor
pulley
is
matched
to
diat
of
die
sewing
machine
before
tightening
the
motor-fixing
bolts
and
nuts.
11
From the library of Superior Sewing Machine & Supply LLC - www.supsew.com

2)
Assembling
the
belt
cover
and
adjusting
the
belt
tension
(1)
Belt
cover
assembling
procedure
®
Upon
the
completion
of
the
motor
mounting,
bring
the
two
pulleys
of
motor
and
sewing
machine
closer
to
each
other,
by
pulling
back
the
sewing
machine.
You
can
then
mount
the
belt
easily
as
shown
in
the
figure.
A
Wamlhd
Make
sure
that
the
power
is
off
before
assembly.
(2)
Place
the
belt
cover
'B',
making
sure
that
the
bell
cover
does
not
contact
the
bell,
and
Ihen
fasten
the
cover
with
the
fixing
A
Warning
Do
not
remove
the
belt
cover.
If
a
finger
slips
into
the
belt
it
might
be
broken
or
cutoff.
BeK
Guide
FDdng
Screw
Belt
Cover
RoigSoew
(2)
Adjusting
the
belt
tension
iD
Optimum
Tension
Level
:
The
optimum
lention
level
is
achieved
when
the
bell
is
pushed
by
5-lOmm
when
the
top
surface
portion
of
the
belt
at
about
30-50mm
above
the
tabletip
Ispressedby
afingerwilhaforceof-Ikgm/sec^or
1
Newton.
©
Adjusting
the
Tension
Level
:
If
the
tension
level
is
out
of
the
optimum
range,
adjust
the
tension
as
follows.
First,
loosen
both
the
upper
and
lower
nuts
for
the
anchor
boll,
letting
the
belt
be
stretched
by
the
motor
weight
itself.
Second,
tighten
the
upper
nut
only
to
the
extent
that
the
motor
does
not
move.
Third,
fasten
the
bottom
nut
tightly
so
that
the
motor
is
securely
fixed.
5-10mm
^
1kg
Upper
Nut
for
Ihe
Anchor
Bolt
lower
Nut
fo
r
the
Anchor
Bolt
From the library of Superior Sewing Machine & Supply LLC - www.supsew.com

3)
Mounting
and
adjusting
the
foot-lift
solenoid
(1)SunStarKM-235
Model
0
Attach
the
main
power
switch
fi
rst
since
the
power
switch
is
located
normally
in
between
the
solenoid
brackets.
(2)
By
referring
to
the
figure
on
the
right
and
the
mounting
instmctions
enclosed
in
the
padcaging
box,
locate
the
insertion
surface
of
the
oil
pan,
and
then
attach
the
foot-lift
solenoid.
No.
Solenoid
No.
Applicable
Models
1
SPF-2
KM-235A
B
(2)SunStarKM-250Model
(D
First,
assemble
a
panel
for
the
attachment
of
presser
foot
solenoid
on
the
backof
ICM-2S0.
(D
Attach
the
presser
foot
solenoid
to
a
bracket
"A".
©Attach
the
bracket
"A"with
the
presser
foot
solenoid
to
the
panel
above.
0
Attch
a
crank
to
a
solenoid
shaft
and
then
connect
it
to
a
sewing
machine.
(5)
Place
a
cover
on
the
solenoid.
(3)
SunStar
Special-specification
models
The
same
mounting
procedure
fi
ir
KM-235
model
is
q)plicable
for
other
models
listed
below.
No.
Sdenotd
No.
Applicable
Models
1
KM-750-7.
KM-750BL-7
2
SPF-3
KM-790-7.
KM-790BL-7
3
KM-857-7.KM-867-7
4
SPF-4
KM-560-7
5
SPF-6
KM-957-7.KM-967-7
6
SPF-8
KM-757-7
7
SPF-9
KM-640BL-7
(4)
Adjusting
the
stroke(Gap)
of
the
automatic
foot-lift
solenoid
0
Check
point
Check
to
make
sure
that
the
stroke-adjusting
screw
is
located
at
the
center
of
the
solenoid
axis,
i.e.,
the
solenoid
should
be
assembled
in
parallel
with
the
bottom
surface
of
the
table.
If
the
solenoid
is
not
in
paralle,
make
an
adjustment
so
that
the
screw
is
in
parallel
with
the
center
of
the
solenoid
axis
using
the
connection
link-fixing
screw.
(2)
Adjusting
Procedure
The
verical
travel
distance
of
the
presser
foot
can
be
adjusted
by
the
stroke-adjusting
saew.
First,
Loosen
the
two
fi
xing
screws,
and
adjsut
the
vertical
stroke
using
the
stroke-adjusting
screw,
loosening
and
tightening
the
stroke-adjusting
screw
will
decrease
and
increase
the
verical
stroke
of
die
presser
foot
respectively.
After
the
adjustment,
fasten
the
fixing
screw
tighdy.
03
Pan
tnseftion
Sur^
Mounting
Positjcn(4)
for
Automatic
Foot-UflSoIenotd
Belt
Holes
128
■
o
h'-
168
Mounting
PosiBon
fofl£BS(4)
65
(44.5)
Solenoid
Bracket
A
«
Specification
viewed
from
the
table
bottom
Cover
for
Foot-Lift
Solenoid
r
■■
[fer-
*
«KM-250
Rear
Panel
T
03
Par
Insertion
Surface
Mount'ng
Position(4)
for
Automatic
Foot4JftSoteno(d
Beft
Holes
168
110
"h'
i
.l.
i
!
(60)
»
SpecHication
viewed
from
the
table
bottom
Connection
Unk-
Fixing
Screw
Oil
Pan
Stroke^justing
Screw
FodngNuts
Solenoid
Axis
@
0
13
From the library of Superior Sewing Machine & Supply LLC - www.supsew.com

4)
Mounting the
position
sensor
(Synchronizer)
and
setting
the
film
(1)
Mounting
the
position
sensor(Synchronizer)
(D
SunStar
thread-cutting
sewing
machine.
All
SunStar
thread-cutting
sewing
machines
are
equipped
with
a
position
sensor.
Users,
therefore,
are
required
to
the
adjust
the
fi
lm
position,
if
necessary,
as
shown
in
the
fi
gure.
,
LWency
^
/
Puliey
1?
\
ill
Synchro
shafl-fbdng
screw(2)
.
\
jlj
/.Synchroshaft
1
Iw^//
Pbotofilm
J'ji^
(Adjusted
left
and
right)
_
_upp^
"n
ni
irlri
,U
y
P'"'®
INTERRUPT
fSh^i
*-]—
I
/
^
\
COVER
P.C.B
Holder
®
All
other
sewing
machines(including
other
manufacturers'
brands)
First,
attach
ti
ie
position
sensor-mounting
adapter
to
the
upper
shaft
of
the
sewing
machine.
Second,
attach
the
position
sensor-fixing
plate
to
the
bocfy
of
ti
te
sewing
machine
as
shown
below
in
the
fi
gure.
Third,
secure
the
position
sensor
to
the
ad^ter
witii
the
fi
xing
screws.
Sewing
machine
screw
adopter
Dimension
Screw
A
TYPE
SM
11/32n=28
Screw
B
TYPE
SM
5/16n=24
Adapter
A-TYPE
B-TYPE
Position
Sensor-Fixing
Bolts
Sewing
Machine
t:--
Position
Sensor-
Fixing
PiateCTypeA)
Position
Sensor
Position
Sensor-Fixing
Plate(Type
8)
Nylon
Cable
Tie'
Fixing
Bolt
tor
Position
Sensor-Fixing
Plate
14
From the library of Superior Sewing Machine & Supply LLC - www.supsew.com

Sviiilntar
(2)
Adjusting
the
film
of
the
position
sensor
(D
Assemble
the
films
and
position
sensor
in
the
order
as
shown
in
the
figure.
FExingVl^sher
Fixing
Bushing
Position
Sensor
Shaft
Film-Fixing
Screw
©
Upon
the
completion
of
the
assembling,
position
the
needle
shaft
tight
at
the
rising
point
from
the
lowest
needle
position
by
manually
rotating
the
pulley.
Loosen
the
film-fixing
screw,
and
adjust
the
DOWN
film
so
that
the
film-adjsting
line
and
the
sensor
housing
calibration
line
are
matched.
Tighten
the
film-fixing
screw
just
to
the
extent
that
the
fi
lm
can
not
be
ro
tated.
Likewise,
position
the
thread
take-up
at
the
highest
position.
Loosen
the
fi
lm-fixing
screw,
and
adjust
the
UP
fi
lm
as
shown
in
the
fi
gure,
while
using
caution
not
to
move
die
DOWN
fi
lm
\^ich
is
already
adjusted
earlier.
Tighten
the
adjusted
fi
lm
with
the
fixing
screw.
Fixing
Nut
Fixing
Nut
Setting
Position
\Sensor
Calibration
Une
t
Film-Adjusting
Une
Down
Rim
Adjustment
Up
Rim
Adjustment
The
highest
positlcffi
position
of
needle
bar
take-up
lever
Sensor
Housing
(3)
Adjustlon
the
films
of
reverse
rotation
sewing
machines
For
reverse-rotation
sewing
machines,
the
film-adjusting
lines
located
at
right
e<^e
of
the
"UP"
and
"DOWN"
film
should
be
matched
to
the
center
line
of
die
sensor.
Fixing
Nut
Fixing
Nut
Setting
Position
Sensor
Calibration
Une
vj
Rim-Adjusting
Une(Reverse
Rotation)
Down
Film
Adjustment
2mm
tuming
around
Up
Film
Adjustment
The
highest
position
from
the lowest
of
take-up
lever
position
of
needle
bar
Sensor
Housing
A
Cautioif
After
adjustment
the
film
of
the
position
detector,
be
sure
to
rotate
the
motor
fo
r
S-^S
seconds
by
pedalling
so
that
the
Controller
may
rememtier
location
of
the
film.
From the library of Superior Sewing Machine & Supply LLC - www.supsew.com

5)
How
to
equip
and
adjust
a
built-in
location
detector(synchronizer)
(1)
How
to
equip
the
built-in
location
detector
(synchronizer)
^
In
case
ofaSunStar
thread
trimmer
When
a
built-in
location
detector(synchronizer)
for
the
sewing
machine
with
the
SunStar
thread
trimmer
is
equipped,
all
that
the
users
need
to
do
is
to
simply
adjust
the
location
of
magnetic
for
detection
according
to
their
needs.
Locate
detector
(synchronizer)
Position
magnetic
up
■£
)
Position
magneto
d
Positon
magnetic
up
Sewing
machine
pulley
Locate
detector
(synchronize^
Sewing
machine
Position
magnetic
down
16
From the library of Superior Sewing Machine & Supply LLC - www.supsew.com

(2)
How
to
adjust
the
magnet
of
the
location
detector
0
Assemble
the
detector
in
order
following
the
pictures.
Locate
d6tector(synchronizer)
(2)
Once
assembling
is
completed,
power
the
controller
on
and
step
on
the
pedal.
At
this
time,
make
sure
that
the
needle
moves
up
and
down.
Stop
the
needle
at
a
desired
location
by
moving
the
magnet
back
and
forth
along
the
location
where
the
needle
stops.
The
highest
position
of
take-up
lever
Normal
rotation
direction
Nonnal
rotation
direction
Locate
detector
2mm
turning
around
(synchronizer)
ft
om
the
lowest
o
\J
\
V
r
(3)
How
to
adjust
a
location
detector
in
case
of
a
reverse
rotation
sewing
machine
^
It
is
the
same
as
diat
used
for
the
normal
rotation
direction
The
highest
position
of
take-up
lever
Reverse
rotation
direction
Reverse
rotation
direction
Locate
detector
2mm
tuming
around
(synchronizeO
(ix}m
the
lowest
J
\v
A
After
adjusting
a
location
detector,
rotate
the
motor
by
stepping
on
the
pedal
for
3~5
seconds
so
that
a
controller
can
remember
the
location.
17
From the library of Superior Sewing Machine & Supply LLC - www.supsew.com

6)
Mounting the
Program
Unit(P/U)
(1)
SunStar
KM-235
Sewing
Machine
First,
attach
the
P/U
bracket
to
the
P/U
using
three
fi
xing
screws
and
a
supporting
bolt
with
nut
attached
on
it
as
shown
in
the
fi
gure.
Second,
securely
attach
the
PAJ
to
the
head
of
the
sewing
machine
using
two
fi
xing
screws
and
washers,
keeping
a
3~4nun
distance
between
the
bottom
surface
of
the
nut
and
the
base
of
the
supporting
bolL
If
(2)
Other
SunStar
thread-machine
First,
attach
the
PAJ
bracket
to
the
PAJ
using
the
four
fi
xing
screws.
Second,
attach
the
PAJ
to
the
main
body
of
the
sewing
machine
using
the
three
bracket-fixing
screws
as
shown
in
the
fi
gure.
Program
Unit
P/U
Bracket
©©©
Program
Unit
PAJ
Bracket-Fixing
Screw(3)
A
Fix
die
cable
using
the
cable
tie
so
that
cable
is
not
in
the
way
of
the
belt
18
From the library of Superior Sewing Machine & Supply LLC - www.supsew.com

7)
An
example
of
installing
the
SunStar
sewing
machine
19
From the library of Superior Sewing Machine & Supply LLC - www.supsew.com

5
WIRING
AND
GROUNDING
1)
Specification
of
the
power
plug
(1)
Single
phase
100V~120V
Switch
Box
Control
Box
o
o
&■
dte"
n
D
D
o
PH
10
AC
110V
>'(Prat*<tivt
E«
EARTHV
(2)
Single
phase
200V~240V
Control
Box
Switch
Box
fi
r
o
o
-o
r
a
o
o
110
AC
220V
Eatttv
EARTHV
(3)
Three
phase
200V~240V
Control
Box
Switch
Box
-o
o-
u
o-x—o-
[fe"
30
AC
220V
PE
(Pfottctlw
EiittO
EARTHV
^Be
sure
to
connect
Protective
Eaitii
2)
Specification
of
electric
current
in
wiring
of
power
plug
Be
sure
to
use
wiring
materials
which
can
stand
electric
current
of
higher
than
15A.
20
From the library of Superior Sewing Machine & Supply LLC - www.supsew.com
Other manuals for Fortuna 5 Series
1
Table of contents
Other SunStar Servo Drive manuals
Popular Servo Drive manuals by other brands
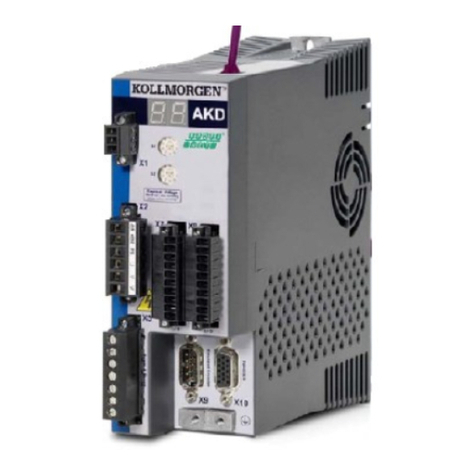
Kollmorgen
Kollmorgen AKD PROFINET RT Communication manual
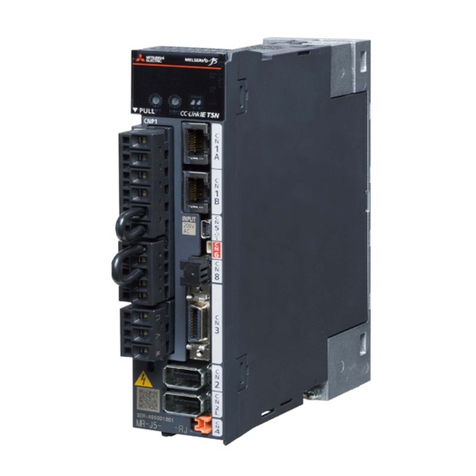
Mitsubishi Electric
Mitsubishi Electric MR-J5 Series user manual
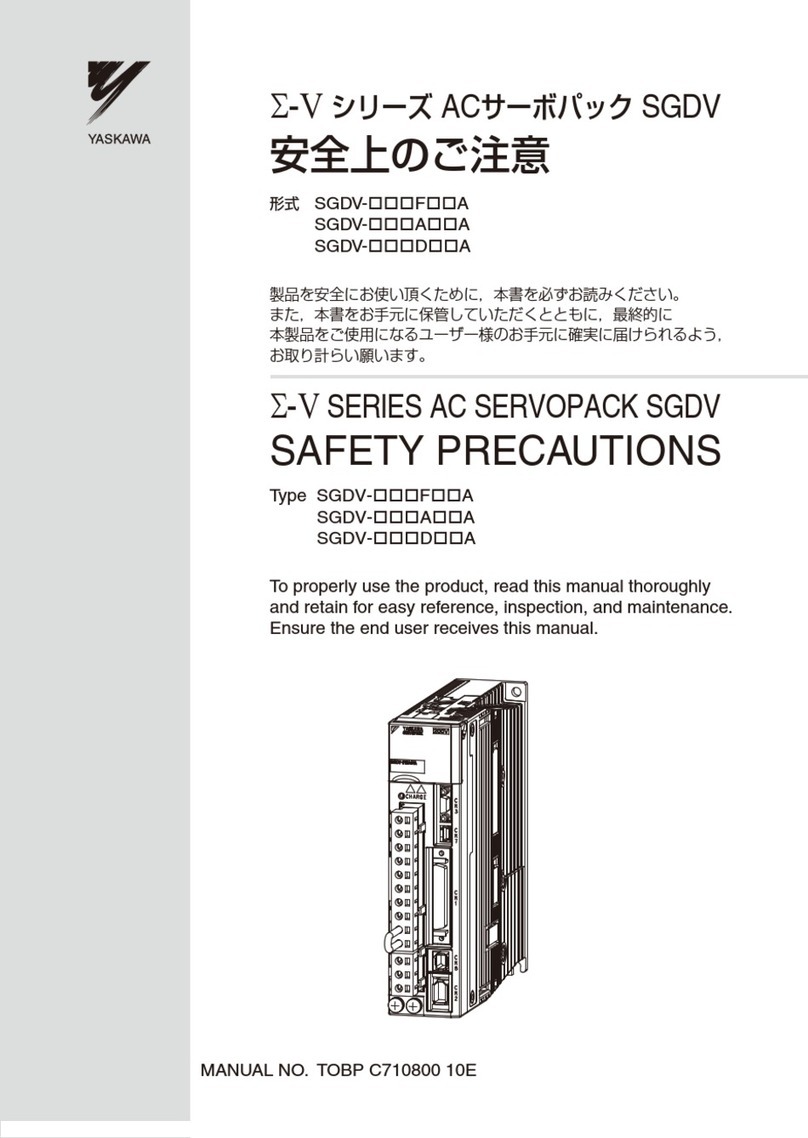
YASKAWA
YASKAWA S-V Series Safety precautions
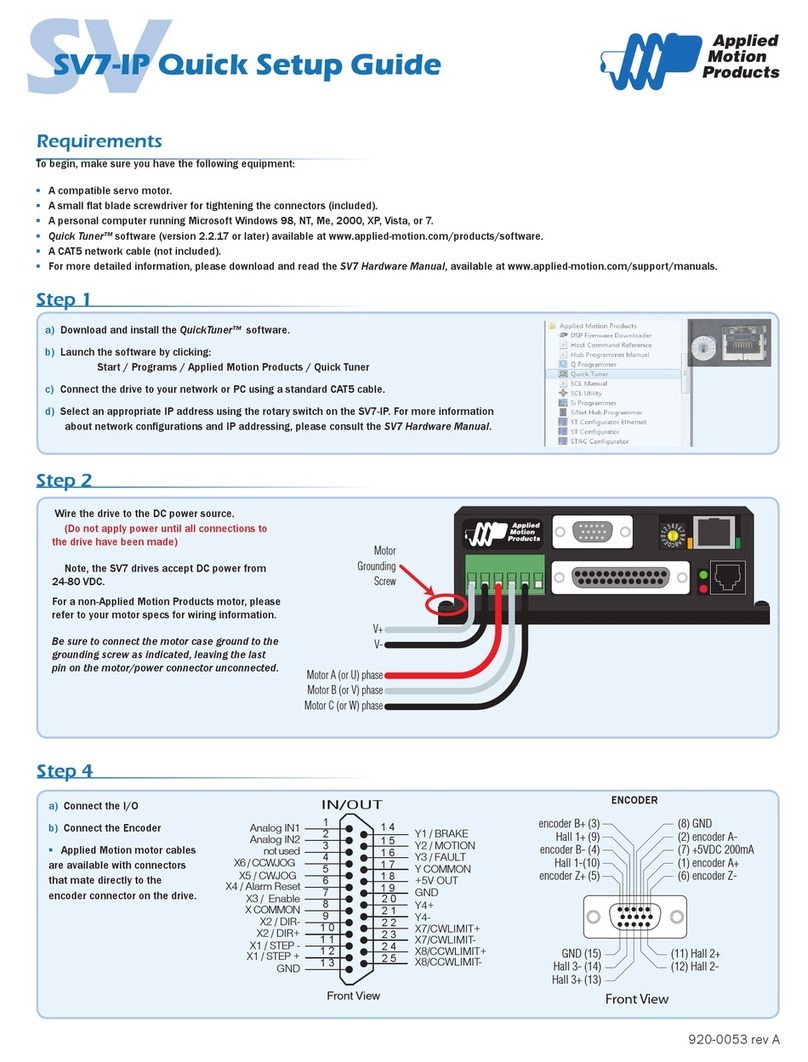
Applied Motion Products
Applied Motion Products SV7-IP Quick setup guide

Emerson
Emerson Epsilon EP Drive 400518-01 installation manual
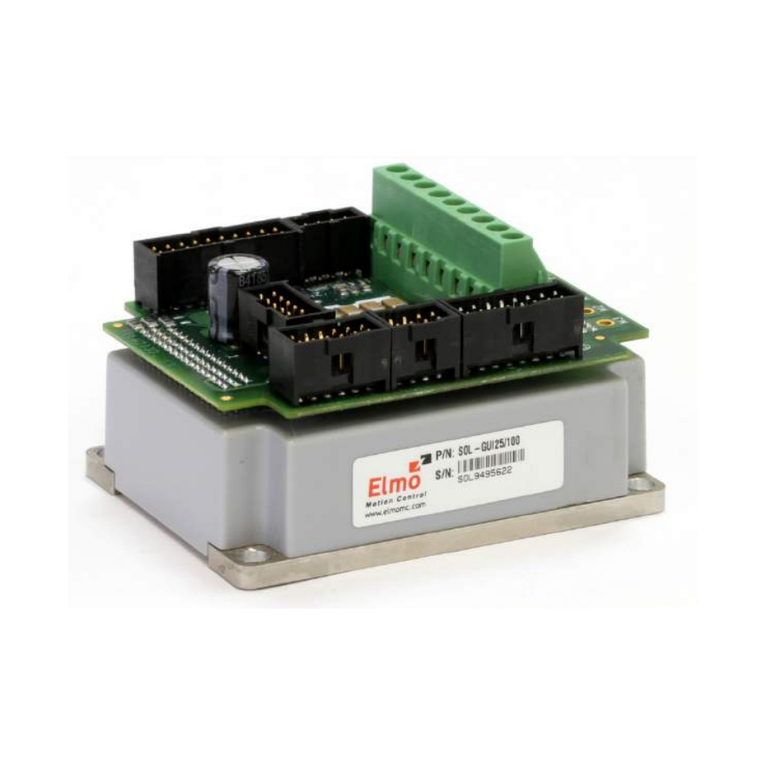
Elmo
Elmo SimplIQ Series installation guide