Sutter Instrument SOLO User manual

One Digital Drive
Novato, CA 94949
Voice: 415-883-0128 Web: www.sutter.com
Fax: 415-883-0572 Email: info@sutter.com
SOLO
Single-Axis Motorized
Micromanipulator System
With USB Interface for External Control
Operation Manual
Rev. 1.01b (20191002)

SOLO SINGLE-AXIS MICROMANIPULATOR SYSTEM OPERATION MANUAL – REV. 1.01B (20191002)
2
Copyright © 2019 Sutter Instrument Company. All Rights Reserved.



SOLO SINGLE-AXIS MICROMANIPULATOR SYSTEM OPERATION MANUAL – REV. 1.01B (20191002)
3
DISCLAIMER
The SOLO consists of one electromechanical micromanipulator device and one ROE (Rotary
Optical Encoder) with integrated controller. The purpose of the system is for the
manipulation at the micro level of micropipettes and probes used in conjunction with a
microscope. No other use is recommended.
This instrument is designed for use in a laboratory environment. It is not intended nor
should it be used in human experimentation or applied to humans in any way. This is not a
medical device.
Unless otherwise indicated in this manual or by Sutter Instrument Technical Support for
reconfiguration, do not open or attempt to repair the instrument.
Do not allow an unauthorized and/or untrained operative to use this device.
Any misuse will be the sole responsibility of the user/owner and Sutter Instrument Company
assumes no implied or inferred liability for direct or consequential damages from this
instrument if it is operated or used in any way other than for which it is designed.
SAFETY WARNINGS AND PRECAUTIONS
Electrical
Operate the SOLO using 110 – 240 VAC., 50-60 Hz line voltage. This instrument is
designed for use in a laboratory environment that has low electrical noise and mechanical
vibration. Surge suppression is always recommended
NOTE: There are no user-replaceable fuses in the SOLO system.
The SOLO system’s power supply consists of an external AC to DC switching
power adapter. If the external power adapter is damaged due to a mains over- or under-
voltage, it must be replaced.
GROUNDING/EARTHING: Proper grounding protects the ROE/controller
electronics, reduces/eliminates electromagnetic interference, and improves the safety of the
system operator. The ROE/controller provides a socket (labeled GROUND) that accepts a
banana plug attached to a suitably gauged insulated wire, the other end of which (alligator
clip) connects to a solid, proper ground.
Avoiding Electrical Shock and Fire-related Injury
Always use the grounded power cord provided to connect the system’s power adapter to a
grounded/earthed mains outlet (3-prong). This is required to protect you from injury if an
electrical hazard occurs.
Do not disassemble the system. Refer servicing to qualified personnel.
To prevent fire or shock hazard do not expose the unit to rain or moisture.
Electromagnetic Interference
To comply with FDA and CE/EU electromagnetic immunity and interference standards; and
to reduce the electromagnetic coupling between this and other equipment in your lab always
use the type and length of interconnect cables provided for interconnecting the electro-
mechanical devices and ROE/controller (refer to Technical Specifications for more details).
Operational
Failure to comply with any of the following precautions may damage this device.

SOLO SINGLE-AXIS MICROMANIPULATOR SYSTEM OPERATION MANUAL – REV. 1.01B (20191002)
4
This instrument is designed for operation in a laboratory environment (Pollution Degree I)
that is free from mechanical vibrations, electrical noise and transients.
DO NOT CONNECT OR DISCONNECT THE CABLES BETWEEN THE
CONTROLLER AND THE MECHANICAL UNITS WHILE POWER IS ON.
Please allow at least 20 seconds after turning the unit off before disconnecting the
mechanical units. Failure to do so may result in damage to the electronics.
Operate this instrument only according to the instructions included in this manual.
Do not operate if there is any obvious damage to any part of the instrument.
Do not operate this instrument near flammable materials. The use of any hazardous
materials with this instrument is not recommended and, if undertaken, is done so at the
users’ own risk.
Do not operate if there is any obvious damage to any part of the instrument. Do not
attempt to operate the instrument with the SOLO/M electromechanical manipulator
shipping tape in place or severe motor damage may result. When transporting the
mechanical manipulator, be sure to reinstall the shipping tape (using masking tape or
equivalent only) to the original locations. Failure to do this may result in damage to the
motors.
Never touch any part of the micromanipulator electromechanical device while it is in
operation and moving. Doing so can result in physical injury (e.g., fingers can be caught
and pinched between the moving parts of the micromanipulator).
If the SOLO system is used in a microinjection environment, please observe the
following. As with most micromanipulation devices, sharp micropipettes can fly out of their
holder unexpectedly. Always take precautions to prevent this from happening. Never
loosen the micropipette holder chuck when the tubing is pressurized, and never point
micropipette holders at yourself or others. Always wear safety glasses when using sharp
glass micropipettes with pressure tubing.
Take care to ensure no cables pass close to the SOLO/M electromechanical
micromanipulator within the spherical movement limits of all its axes combined.
Other
Retain the original packaging for future transport of the instrument.
Sutter Instrument reserves the right to change specifications without prior notice.
Use of this instrument is for research purposes only.
Handling Micropipettes
Failure to comply with any of the following precautions may result in injury to the users
of this device as well as those working in the general area near the device.
The micropipettes used with this instrument are very sharp and relatively fragile. Avoid
contact with micropipette tips to prevent accidentally impaling oneself.
Always dispose of micropipettes by placing them into a well-marked, spill-proof “sharps”
container.

SOLO SINGLE-AXIS MICROMANIPULATOR SYSTEM OPERATION MANUAL – REV. 1.01B (20191002)
5
TABLE OF CONTENTS
DISCLAIMER .......................................................................................................................................3
SAFETY WARNINGS AND PRECAUTIONS....................................................................................3
Electrical ..................................................................................................................................................3
Avoiding Electrical Shock and Fire-related Injury..............................................................................3
Electromagnetic Interference ............................................................................................................3
Operational ..............................................................................................................................................3
Other.........................................................................................................................................................4
Handling Micropipettes..........................................................................................................................4
1. INTRODUCTION.............................................................................................................................9
1.1 Structure of the SOLO Documentation Package..........................................................................9
1.2 Components of the SOLO System ..................................................................................................9
1.3 Overview ..........................................................................................................................................10
1.3.1 Features.....................................................................................................................................10
1.3.2 Description................................................................................................................................10
2. INSTALLATION ............................................................................................................................11
2.1 Mounting Instructions ...................................................................................................................11
2.1.1 Mounting the SOLO/M to the Stand or Platform ................................................................11
2.2 Headstage Mounting ......................................................................................................................12
2.3 Other Accessories............................................................................................................................12
2.4 Electrical Connections and Initial Operating Instructions ........................................................12
2.5 ROE/Controller Rear Panel Controls and Configuration...........................................................13
2.5.1 Power Switch............................................................................................................................13
2.5.2 Configuration Switches ...........................................................................................................14
3. OPERATIONS ................................................................................................................................15
3.1 Main Controls and Indicators on the ROE/Controller ...............................................................15
3.2 Display..............................................................................................................................................15
3.2.1 Initial Startup...........................................................................................................................15
3.3 Control Operations .........................................................................................................................16
3.3.1 Maximum Positive Position Values: ......................................................................................16
3.3.2 Setting Position for HOME or WORK...................................................................................16
3.3.3 Moving to the Home Position .................................................................................................16
3.3.4 Moving to the Work Position ..................................................................................................17
3.3.5 Setting Absolute/Relative Coordinates Mode........................................................................17
3.3.6 Mode Indications ......................................................................................................................17
3.3.7 Speed Control and ROE Knob Movements (SPEED)..........................................................18
3.3.8 Pausing Home Movements .....................................................................................................18
3.3.9 Pausing Work Movements ......................................................................................................18
3.3.10 Pulse Mode..............................................................................................................................18
4. EXTERNAL CONTROL ................................................................................................................18
4.1 Virtual COM Port (VCP) Serial Port Settings.............................................................................18
4.2 Protocol and Handshaking ............................................................................................................19
4.3 Command Sequence Formatting ..................................................................................................19
4.4 Axis Position Command Parameters............................................................................................19

SOLO SINGLE-AXIS MICROMANIPULATOR SYSTEM OPERATION MANUAL – REV. 1.01B (20191002)
6
4.5 Microsteps and Microns (Micrometers)........................................................................................20
4.6 Ranges and Bounds: .......................................................................................................................20
4.7 Command Reference.......................................................................................................................20
4.8 Notes.................................................................................................................................................21
5. MAINTENANCE............................................................................................................................23
APPENDIX A. LIMITED WARRANTY............................................................................................24
APPENDIX B. ACCESSORIES .........................................................................................................25
APPENDIX C. TECHNICAL SPECIFICATIONS ...........................................................................26
C.1. SOLO/M..........................................................................................................................................26
C.2. SOLO ROE/Controller..................................................................................................................26
APPENDIX D. QUICK REFERENCE..............................................................................................28
Manual Operation...............................................................................................................................28
Configuration ......................................................................................................................................28
External Control .................................................................................................................................28
INDEX .................................................................................................................................................32
TABLE OF FIGURES
Figure 1-1. The SOLO system................................................................................................................... 9
Figure 2-1. Side view of SOLO/M showing mounting adapter plate and lock screws....................... 11
Figure 2-2. Mounting the SOLO/M on the Adapter Plate ................................................................... 12
Figure 2-3. Rear of SOLO ROE/Controller cabinet .............................................................................. 13
Figure 2-4. Configuration switches on rear of SOLO ROE/Controller unit (switch positions shown
are factory defaults)................................................................................................................ 14
Figure 3-1. Startup screen ....................................................................................................................... 15
Figure 3-2. Factory default startup calibrated position ....................................................................... 15
Figure 3-3. Maximum positive values..................................................................................................... 16
Figure 3-4. Moving to Home position (screen is amber while moving) .............................................. 16
Figure 3-5. Factory default Home position............................................................................................ 16
Figure 3-6. Example Home position defined and saved ....................................................................... 16
Figure 3-7. Example Work position ........................................................................................................ 17
Figure 3-8. Relative mode ........................................................................................................................ 17
TABLE OF TABLES
Table 2-1. Configuration DIP switch settings. ...................................................................................... 14
Table 3-1. Maximum positive position value of each axis .................................................................... 16

SOLO SINGLE-AXIS MICROMANIPULATOR SYSTEM OPERATION MANUAL – REV. 1.01B (20191002)
7
Table 3-2. Screen colors and modes........................................................................................................ 17
Table 4-1. USB-VCP interface serial port settings. .............................................................................. 18
Table 4-2. Microns/microsteps conversion............................................................................................. 20
Table 4-3. Ranges and bounds................................................................................................................. 20
Table 4-4. SOLO external control commands ....................................................................................... 21
Table C-1. SOLO cables and receptacles/connectors. ........................................................................... 27
Table D-1. Configuration Switches 1 – 4................................................................................................ 28
Table D-2. USB-VCP interface serial port settings............................................................................... 29
Table D-3. Microns Microns/microsteps conversion. ............................................................................ 29
Table D-4. Ranges and bounds................................................................................................................ 30
Table D-5. SOLO external control commands. ..................................................................................... 30

SOLO SINGLE-AXIS MICROMANIPULATOR SYSTEM OPERATION MANUAL – REV. 1.01B (20191002)
8
(This page intentionally left blank.)

SOLO SINGLE-AXIS MICROMANIPULATOR SYSTEM OPERATION MANUAL – REV. 1.01B (20191002)
9
1. INTRODUCTION
1.1 Structure of the SOLO Documentation Package
The SOLO 1-Axis Micromanipulator System is comprised of a ROE/controller, a power
adapter, and a SOLO-25 or SOLO-50 stepper-motor-based electromechanical
micromanipulator. This manual consists of four parts: This chapter, Introduction, which
provides an overview and general description of the SOLO system; Chapter 2, Installation,
which describes how to install, set up, and configure all components of the system; Chapter 3,
Operations, which describes how to operate the SOLO; Chapter 4, Maintenance, describes
how to perform routine and other maintenance of the SOLO; and Chapter 5,
Reconfiguration, describes the reconfiguration possibilities of the SOLO system.
Figure 1-1. The SOLO system
1.2 Components of the SOLO System
Carefully remove all components from the shipping container. In addition to this manual, the
following should be included:
SOLO ROE Rotary Optical Encoder input device with built-in controller and external
power adapter.
SOLO-25 or SOLO-50 electromechanical micromanipulator
9-pin DSUB cable (connects the ROE/controller to the SOLO/M electromechanical
micromanipulator).
Power adapter
Power adapter AC mains cable appropriate for your location
Ground/Earth cable
USB Cable
IMPORTANT
Once the SOLO system has been unpacked, remove the shipping tape from the various
locations on the SOLO/M electromechanical micromanipulator. The shipping tape must be
removed before operating the SOLO system. If you need to transport the SOLO/M in the
SOLO/E ROE/CONTROLLER
SOLO/M
ELECTROMECHANICAL
MICROMANIPULATOR

SOLO SINGLE-AXIS MICROMANIPULATOR SYSTEM OPERATION MANUAL – REV. 1.01B (20191002)
10
future, reapply 2 to 3-inch pieces of masking tape to the same locations. Once the tape has
been removed, handle the SOLO/M with care. The mechanisms can be damaged if any of the
axes are inadvertently moved without the tape in place.
1.3 Overview
1.3.1 Features
Three independent axes (X, Y, and Z) each with 25mm travel with a virtual fourth axis
(D) for coaxial pipette movement utilizing a tangent function factoring the holder’s angle
and the X and Z axes.
Sub-micron 100nm resolution
Digital display indicates coordinates in relative or absolute
User-f r i e n d l y, f a nless compact controller with ROE preserves bench space
Push button control of multiple functions – work, home, Lock, pulse and relative
Robotic home- and work-position moves for easy automated pipette exchange
1.3.2 Description
The SOLO, the newest Sutter Instrument motorized manipulator, is easy to use and has
three independent axes. The X, Y, and Z axes provide 25mm range of motion. D-axis
movement is accomplished virtually using a tangent function of the chosen angle of the
holder and simultaneously moving X and Z. The ROE controller has a digital display and
keys for Home, Work, Pulse, Lock, and Relative. The compact, intuitive controller takes up
minimal bench space, is fan-free, and easy to use.
While the axes provide X and Y orthogonal motion typical of most motorized manipulators,
Sutter has introduced a diagonal axis with the SOLO so one can move the electrode coaxially
at the exact desired angle of approach.
The SOLO’s ROE provides fine control of electrode position and the rate of rotation of ROE
dials for each axis determines the speed of travel. The finest step size is less than 100nm.
Five conveniently located buttons on the ROE provide control of all the basic functions you
will need in normal operation (Work, Home, Lock, Relative, and Pulse).
Press and hold WORK (for 3 seconds) to quickly store a work position, tap HOME to move all
axes to an initial location that is useful for changing electrodes, or press and hold the HOME
button (for 3 seconds) to memorize a new HOME position.
When ready to record data, the motor drive electronics can be suppressed by pressing the
LOCK button. In the LOCK mode, the display turns red and ROE input is locked out to avoid
any accidental motion.
Pressing and holding the RELATIVE button for three seconds at any location causes the
display coordinates to all zeroes. When activating relative mode, the display turns blue.
To return to viewing the absolute coordinates, tap the RELATIVE button to toggle back.
Finally, tapping the PULSE button causes a 3μm advance in the diagonal. This rapid burst of
forward motion can assist in sharp electrode cell penetration.
All the electronics, except for a small power supply, are housed within the SOLO ROE and no
separate controller or computer is required.

SOLO SINGLE-AXIS MICROMANIPULATOR SYSTEM OPERATION MANUAL – REV. 1.01B (20191002)
11
In keeping with the compact and simple design, the SOLO has no need of computer
connectors. If the user desires a computer connection, a USB port is provided on the rear of
the SOLO ROE.
2. INSTALLATION
When installing the SOLO system for the first time, it is recommended that the components
of the system be installed in the following order: SOLO/M electromechanical
micromanipulator first, followed by the SOLO/E ROE/Controller.
2.1 Mounting Instructions
The following sections describe how to mount the SOLO/M manipulator to a stand using the
mounting adapter plate, how to adjust the pipette angle and how to mount different
headstages.
2.1.1 Mounting the SOLO/M to the Stand or Platform
The SOLO/M attaches to the mounting adapter plate using four M3X0.5 hex head locking
screws.
Figure 2-1. Side view of SOLO/M showing mounting adapter plate and lock screws.
The SOLO/M is shipped with the adapter plate in place. It is attached using four tapered
pegs, along with four locking screws.
To remove it, first loosen the four hex screws that secure the manipulator to the pegs in the
adapter plate. The rear pair is in a similar location in the back of the manipulator. Once the
locking screws are sufficiently loosened, lift the SOLO/M upwards from the adapter plate.
Before attaching the adapter plate to the SOLO/M, you need to decide where to position the
manipulator on your stand/platform. The stand can be any flat surface carrying ¼-20, 10-32,
or M6 holes on one-inch centers (such as a Sutter Instrument MT-series stand or MD series
platform).
Examine the space of the platform onto which installation is to take place. Attach the control
cable to SOLO/M and move the entire unit around on the platform until the precise desired
Locking Screws
Locking Screws

SOLO SINGLE-AXIS MICROMANIPULATOR SYSTEM OPERATION MANUAL – REV. 1.01B (20191002)
12
position is determined. A small bag containing the necessary hardware to attach the SOLO
to the stand is included.
Figure 2-2. Mounting the SOLO/M on the Adapter Plate
Once the plate is mounted, align the pegs on top of the plate with the holes in the
manipulator, push the X-axis firmly onto the plate, and re-tighten the locking hex set
screws.
2.2 Headstage Mounting
Sutter IPA headstage, Axon headstages 203B or CV-7, and the Heka EPC-10 headstage have
an integral dovetail that fits directly into the rotary dovetail slide bracket on the SOLO/M.
The dovetail slide bracket on the SOLO/M also supports older Axon and Heka headstages
when using the 4’’ dovetail extension.
Rod-mounted headstages and micro tools are accommodated using a rod clamp that fits into
the dovetail (not shown). All the headstage adapters and mounting hardware are included
with the manipulator and are shipped in a zip lock plastic bag.
2.3 Other Accessories
One or more accessories may have been ordered and received for mounting the SOLO/M
and/or modifying the headstage mount to the manipulator (i.e., rotating base, microscope
stage mount, gantry, dovetail extension, etc.). Setup of these accessories is normally covered
in documentation accompanying the accessory.
2.4 Electrical Connections and Initial Operating Instructions
Initially, you may want to simply connect the SOLO/M micromanipulator and the
ROE/Controller together and try some gross movements in order to get a feel for the controls
and how to make simple movements. It is perfectly acceptable to set the manipulators in the
middle of a bench top, make all electrical connections and then observe each unit’s
movement by eye.
CAUTION: Unless the SOLO/M micromanipulator electromechanical baseplate is firmly
bolted down to a breadboard or solidly to a firm surface, the SOLO/M is likely to tip over

SOLO SINGLE-AXIS MICROMANIPULATOR SYSTEM OPERATION MANUAL – REV. 1.01B (20191002)
13
when fully extending its axis, especially if it is loaded with a headstage that extends beyond
the SOLO/M’s current center of gravity.
Upon deciding to directly install the SOLO system in your rig, it is useful to follow the initial
setup procedure to learn how to move the units to allow easy access to the mounting screws.
1. With the power switch on the back of the ROE in the OFF (0) position, connect the power
adapter’s 24VDC cable to the POWER receptacle.
Figure 2-3. Rear of SOLO ROE/Controller cabinet
2. With the power OFF (rear panel switch in the “0” position), connect a well-
grounded/earthed wire to the GROUND post/banana plug socket.
3. With the power OFF, connect the male end of the DB-9 cable to the MANIPULATOR
connector on the ROE, the other end of which is connected to the SOLO/M
micromanipulator electromechanical. (See cautionary note below.)
4. Verify that the four switches on the rear of the ROE are set as desired.
5. Power up the system by moving the power switch on the rear of the ROE to the “1”
position.
*CAUTION: NEVER CONNECT OR DISCONNECT THE ROE/CONTROLLER
FROM THE SOLO/M WHILE THE POWER IS ON!
2.5 ROE/Controller Rear Panel Controls and Configuration
2.5.1 Power Switch
The power switch for the SOLO system is located on the rear panel of the ROE/controller. At
power up, the microprocessor in the ROE/controller scans the attached equipment and
configures the system accordingly.
POWER
SWITCH
POWER
RECEPTACLE
MANIPULATOR
CONNECTOR
GROUND
POST

SOLO SINGLE-AXIS MICROMANIPULATOR SYSTEM OPERATION MANUAL – REV. 1.01B (20191002)
14
2.5.2 Configuration Switches
Figure 2-4. Configuration switches on rear of SOLO ROE/Controller unit (switch positions shown are factory
defaults).
Switches 1, 2, 3 and 4 set the operating characteristics of the SOLO at power-up.
Table 2-1. Configuration DIP switch settings.
* Factory default (typical setting for right-hand-mounted manipulator).
Switch #
Function
Setting
Description
1
Knob Rotation Directionality
for Forward (+) Manipulator
Movement
OFF* (UP)*
Clockwise
ON (DOWN) Counterclockwise
2
Length of Travel of Connected
Electromechanical Device
OFF* (UP)
25mm
ON (DOWN) 50mm
3
Electromechanical device
compatibility
OFF* (UP)
SOLO/M
ON (DOWN) MP-285/M series
4
Calibration Homing on Power
On
OFF* (UP)
Enabled. Moves to position 0 (physical
beginning of travel), then advances to 1,000
microns.
ON (DOWN))
Disabled. Point of Origin stays at physical
position of attached eletromechanical. All
positions forward of Point of Origin are
positive, and negative in opposite direction.

SOLO SINGLE-AXIS MICROMANIPULATOR SYSTEM OPERATION MANUAL – REV. 1.01B (20191002)
15
3. OPERATIONS
3.1 Main Controls and Indicators on the ROE/Controller
Figure 3-1. Front view of the SOLO ROE/Controller
3.2 Display
3.2.1 Initial Startup
Figure 3-1. Startup screen
Figure 3-2. Factory default startup calibrated position
When starting the SOLO system for the first time, the value for the single axis will be 1,000
micrometers (microns) for both
Absolute
and
Relative
. Absolute always indicates the
absolute number of microns from beginning of travel (absolute position 0). Relative always
indicates the number of microns away from the last-set absolute position (absolute position 0
on startup).
DISPLAY
AXIS
CONTROL
RELATIVE
POS. RESET
PULSE
FORWARD
WORK
POSITION
HOME
POSITION
SPEED
Sutter
Instrument R2.6
(Text in
Green)
Absolute = 1000
Relative = 1000
(Text in
Green)

SOLO SINGLE-AXIS MICROMANIPULATOR SYSTEM OPERATION MANUAL – REV. 1.01B (20191002)
16
3.3 Control Operations
3.3.1 Maximum Positive Position Values:
Move the dial of an axis clockwise until its position value stops incrementing. The following
table lists the maximum position value (in microns) for each axis.
Table 3-1. Maximum positive position value of each axis
Maximum Positio n Value (in microns)
25mm
50mm
25,000
50,000
Figure 3-3. Maximum positive values
3.3.2 Setting Position for HOME or WORK
To set position, hold down HOME or WORK button for 3 seconds until beep sounds.
3.3.3 Moving to the Home Position
Figure 3-4. Moving to Home position (screen is amber while moving)
If the Home position has not yet been defined and saved, the Home position value for the
single axis will default to 1,000 microns, as shown in the following figure.
Figure 3-5. Factory default Home position
If the Home position has been previously defined (saved), pressing HOME will make a move
to the defined home position (see example in the following figure).
Figure 3-6. Example Home position defined and saved
Absolute = 25000
Relative = 25000
(Text in
Green)
Absolute = 2602
Relative = 2602
(Text in
Red)
Absolute = 1000
Relative = 1000
(Text in
Green)
Absolute = 2602
Relative = 2602
(Text in
Green)

SOLO SINGLE-AXIS MICROMANIPULATOR SYSTEM OPERATION MANUAL – REV. 1.01B (20191002)
17
3.3.4 Moving to the Work Position
Figure 3-7. Example Work position
To move to the Work position, press the WORK button.
3.3.5 Setting Absolute/Relative Coordinates Mode
The RELATIVE button toggles between Relative and Absolute coordinate systems. The
default coordinate system on power up is Absolute, with the coordinates on the screen shown
in green. To switch to relative coordinates, press the RELATIVE button once. To reset the
current position to all zeroes, depress the RELATIVE for 3 seconds or until a beep is heard,
and then release the button. This resets the current position to all zeroes.
Depress RELATIVE for 3 sec. or until beep sounds
Figure 3-8. Relative mode
3.3.6 Mode Indications
The SOLO system has two modes of operation: Absolute/relative coordinates status and
while moving with the rotary knob, and when moving to HOME/WORK or when commanded
to move by an external-control command. The display turns color for each specific mode, as
shown in the following table.
Table 3-2. Screen colors and modes
Screen Color
Mode
Example
Green
Absolute & relative
coordinates and while moving
with the rotary knob.
Red
Move to Home or Work
position, or when commanded
by external computer control
(knob is disabled during the
move)
Absolute = 2602
Relative = 2602
Absolute = 3264
Relative = 3264
Absolute = 3264
Relative = 3264
(Text in red while
moving, then green)
Absolute = 3321
Relative = 0
(Text in green)

SOLO SINGLE-AXIS MICROMANIPULATOR SYSTEM OPERATION MANUAL – REV. 1.01B (20191002)
18
3.3.7 Speed Control and ROE Knob Movements (SPEED)
The rate at which the ROE axis knob moves the manipulator can be adjusted with the
SPEED button. Each press of the button cycles through four speeds: 0 (normal) through 3
(fastest).
3.3.8 Pausing Home Movements
After Move to Home has been initiated, and while the move is in progress, pressing HOME a
second time pauses the manipulator. Pressing HOME again resumes movement.
3.3.9 Pausing Work Movements
After Move to Work has been initiated, and while the move is in progress, pressing WORK a
second time pauses the manipulator. Pressing WORK again resumes movement.
3.3.10 Pulse Mode
Pulse mode advances the single axis in 2.85 µm steps. Each press of the PULSE button
increments by one 2.85-µm step beyond the current position. This feature can be used to
penetrate tough or resistant tissue.
4. EXTERNAL CONTROL
Controlling the SOLO externally via computer is accomplished by sending commands over
the USB interface between the computer and the USB connector on the rear panel of the
SOLO controller/ROE. The USB device driver for Windows is downloadable from Sutter
Instrument’s web site (www.sutter.com). The SOLO requires Sutter Instrument’s USB CDM
(Combined Driver Model) Version 2.10.00 or higher. The CDM device driver consists of two
device drivers: 1) USB device driver, and 2) VCP (Virtual COM Port) device driver. Install the
USB device driver first, followed by the VCP device driver. The VCP device driver provides a
serial RS-232 I/O interface between a Windows application and the SOLO. Although the VCP
device driver is optional, its installation is recommended even if it is not going to be used.
Once installed, the VCP can be enabled or disabled.
The CDM device driver package provides two I/O methodologies over which communications
with the controller over USB can be conducted: 1) USB Direct (D2XX mode), or 2) Serial RS-
232 asynchronous via the VCP device driver (VCP mode). The first method requires that the
VCP device driver not be installed, or if installed, that it be disabled. The second method
requires that the VCP be installed and enabled.
4.1 Virtual COM Port (VCP) Serial Port Settings
The following table lists the required RS-232 serial settings for the COM port (COM3,
COM5, etc.) generated by the installation or enabling of the VCP device driver.
Table 4-1. USB-VCP interface serial port settings.
Property
Setting
Data (“Baud”) Rate (bits per second (bps)) 57600
Data Bits 8
Table of contents
Other Sutter Instrument Controllers manuals
Popular Controllers manuals by other brands
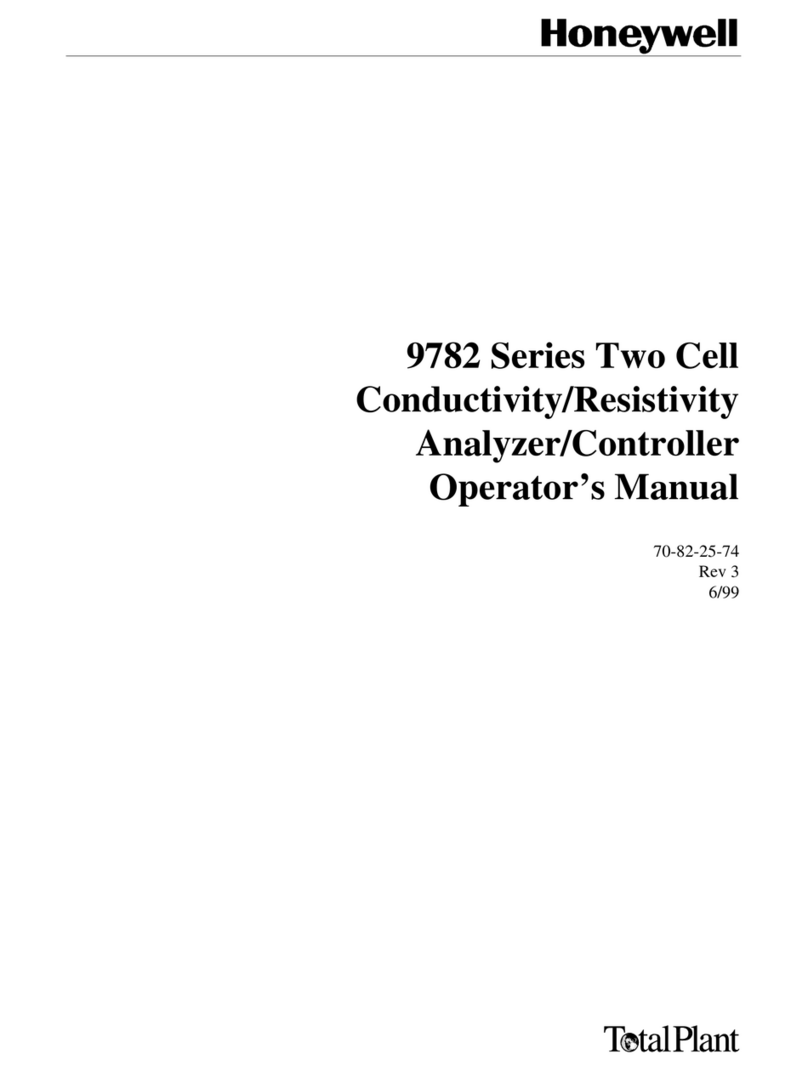
Honeywell
Honeywell 9782 Series Operator's manual
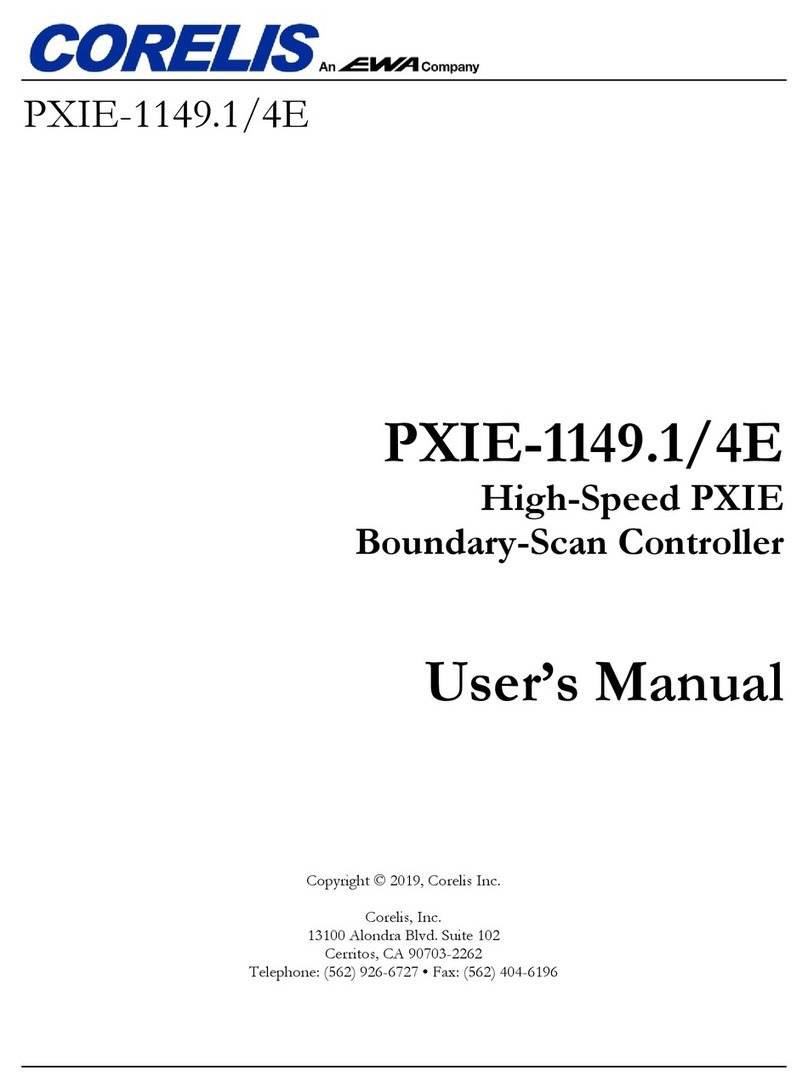
EWA
EWA CORELIS PXIE-1149.1/4E user manual
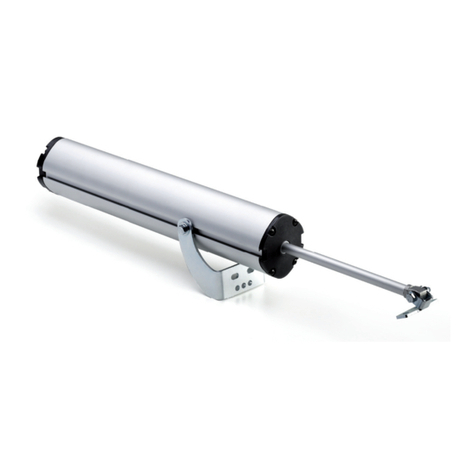
Comunello
Comunello MOWIN FAST 50/160 instruction manual
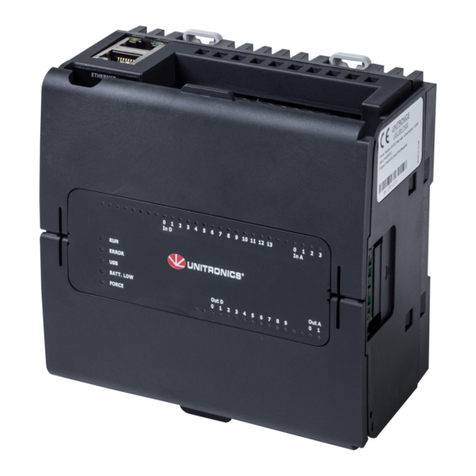
Unitronics
Unitronics UniStream PLC Series installation guide
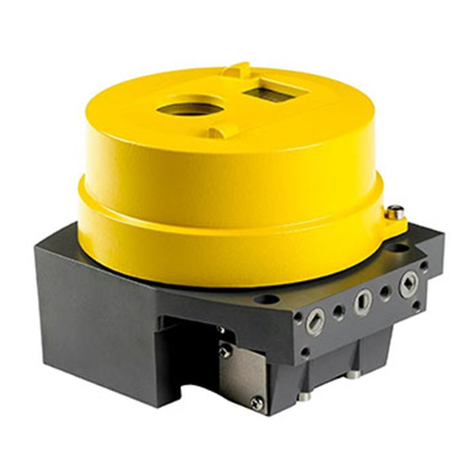
Metso
Metso Neles SwitchGuard SG9200H Installation maintenance and operating instructions
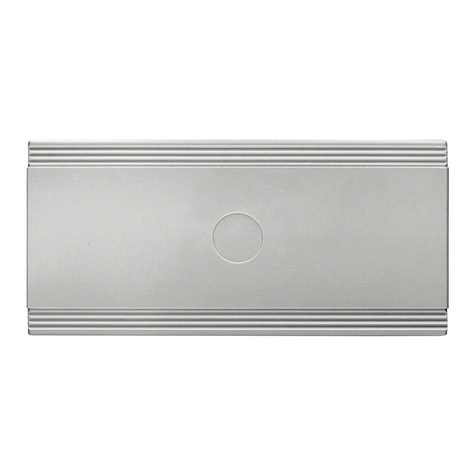
Vimar
Vimar BY-ALARM PLUS 03823 quick start guide
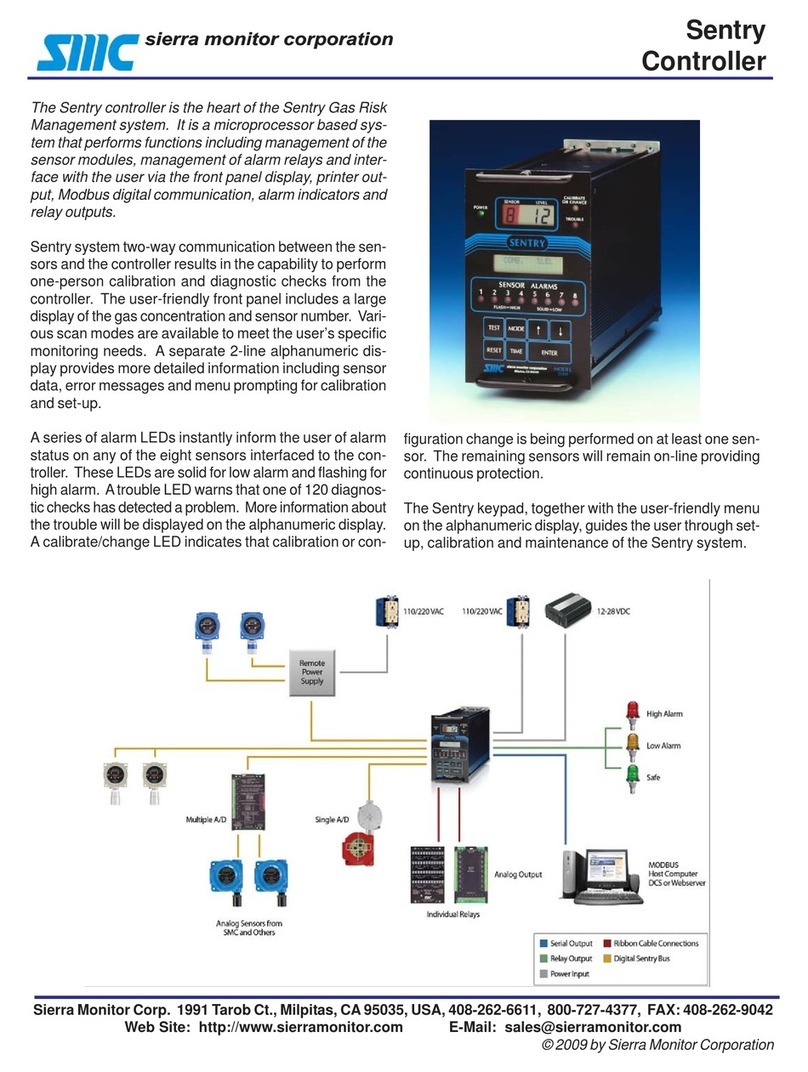
Sierra Monitor Corporation
Sierra Monitor Corporation Sentry 5000 Specification sheet

SpaGuts
SpaGuts VS510SZ installation instructions
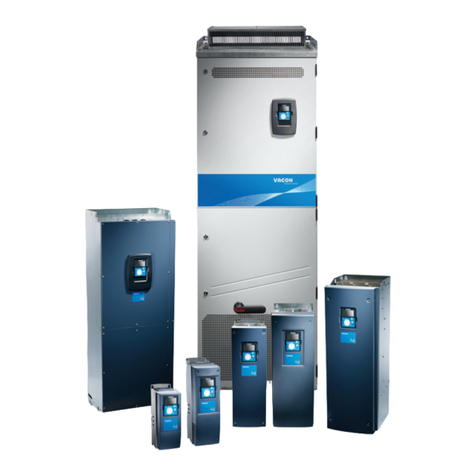
Danfoss
Danfoss Vacon NXP Series operating guide
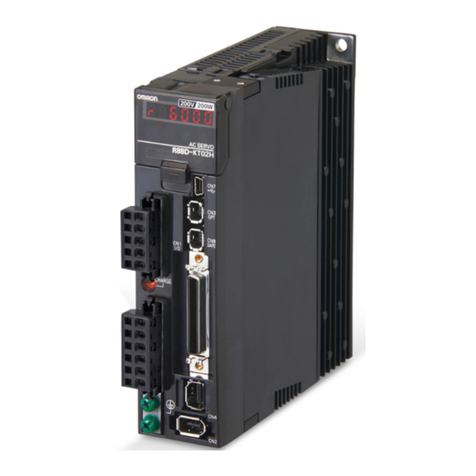
Omron
Omron OMNUC G5 R88M-K series user manual
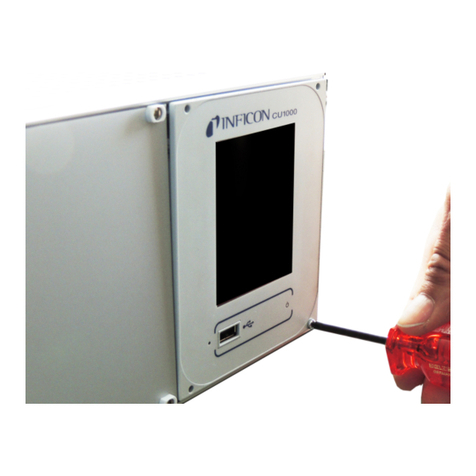
Inficon
Inficon CU1000 Translation of the original instructions
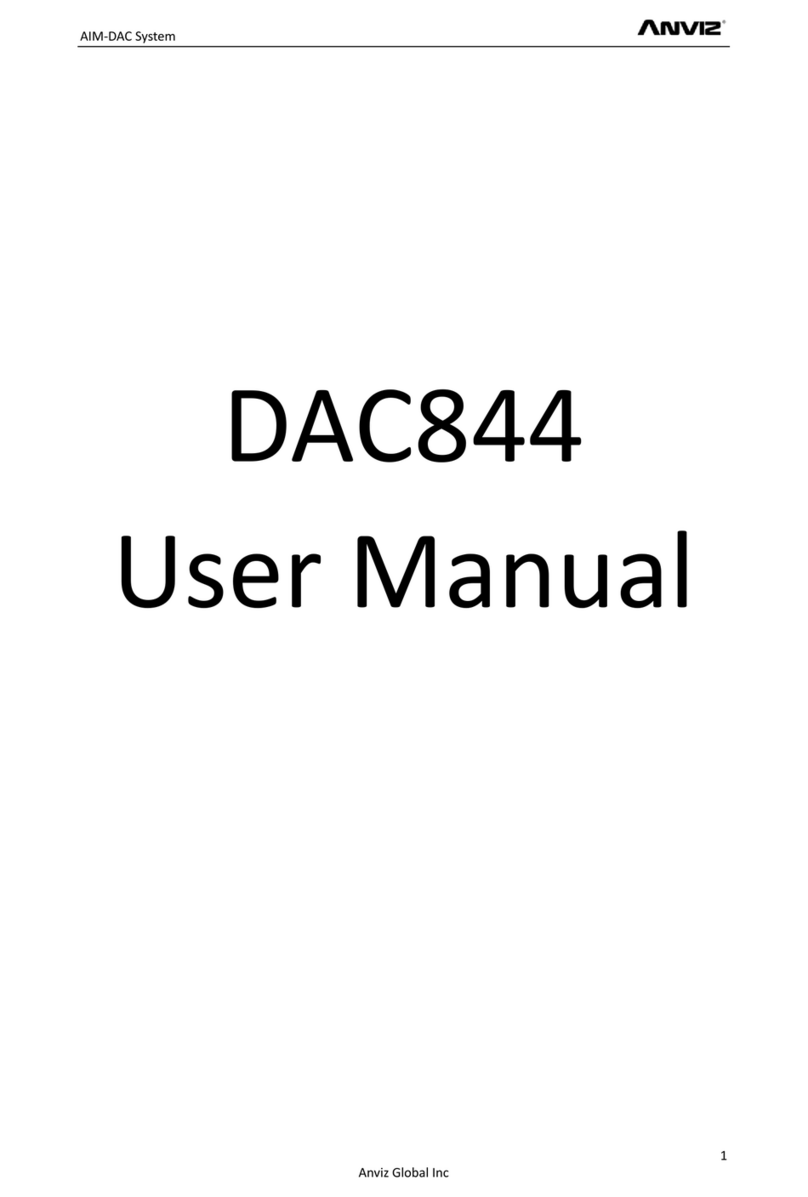
Anviz
Anviz DAC844 user manual