SYNTECHTRON TC6B Instruction manual

Page 1 of 12 TC6B IO&M Manual
TC6B Variable Rate
Electronic Controller Assembly
Installation, Operation &
Maintenance Manual

Page 2 of 12 TC6B IO&M Manual
Table of Contents
Page
1.0 Product Support after Sales. 3
1.1 Safety Instructions 4
2.0 Controller Instructions 5
Controller Installation*
2.1 Installing the Controller 5
2.2 Wiring the Feeder & Controller 5
2.3 Earthing 6
Controller Operation*
2.4 Controller Operation 6
Controller Maintenance*
2.5 Setting Up Procedure 6
2.6 Field Testing the Silicon Controlled Rectifier (SCR) Figure 2.1 – 2.2 7
3.0 Trouble Shooting 8
4.0 Recommended Spare Parts List 9
5.0 TC6B Controller Assembly Drawing 052D3825 A 10
6.0 Commissioning Record Sheets 11

Page 3 of 12 TC6B IO&M Manual
1.0 Product Support after Sales.
Urgent Breakdown Response & Assistance.
Our Service team consists of experienced “hands on” personnel.
Spare Parts.
We have a large inventory of critical spare parts – backed up by a highly responsive multi
disciplined manufacturing facility.
Preventative Maintenance.
On – site inspection and report to assist your Preventative Maintenance.
Refurbishment.
We provide full overhaul services for all sizes of Syntron, ICAL and Transfield feeding, screening
and vibratory conveying equipment.
Commissioning & Auditing.
Commissioning & Auditing are available for all equipment and systems supplied by Syntechtron.
Training.
Structured equipment training courses On / or Off / Site.

Page 4 of 12 TC6B IO&M Manual
1.1 Safety Instructions.
This manual highlights several safety hazards that may be encountered when working with this
equipment. A brief description of these symbols is shown below.
General Caution covering a broad spectrum of hazards.
Specific Danger restricting access to a hazard.
Specific Warning covering Live Circuitry hazards
General Warning covering a broad spectrum of hazards.
Specific Warning covering hazards in Explosive Environment.
Specific Warning covering Electromagnetism

Page 5 of 12 TC6B IO&M Manual
2.0 TC6B Controller Instructions – General Instructions
SAFETY FEATURES
Numerous safety precautions are mentioned through this Instruction Manual,
failure to follow these instructions or to heed these precautions may result in
serious personal injury or property damage.
Although components within the Controller enclosure are IP2X rated “finger
safe”, the operator must be aware of the potential hazards associated with
working around live equipment and circuits.
Installation*
2.1 Installing the Controller
The Controller assembly should be installed as close to the Feeder as possible, preferably on a wall in a
clean dry location, free from excessive vibration. The standard Controller is furnished in an enclosure with
a Degree of Protection rating of IP65 that is adequate for most applications. Controllers may be supplied
to meet a variety of environmental conditions or applications requiring a higher degree of protection.
If at all possible, the Controller should be installed at a location where it will receive good ventilation. The
life of most electrical components is reduced when operating in an atmosphere of intense heat. Good
ventilation in the area of the control enclosure will permit internal heat to be dissipated through the enclosure
external surfaces and into the outside atmosphere, thus prolonging component life. The Controller
should be installed at a location where it is easily seen and accessible to the operator and maintenance
technician.
2.2 Wiring the Feeder and Controller
The power supply voltage and frequency must be as stamped on the
equipment rating nameplate.
The supply conductors and the conductors between the Feeder and Controller must be of a size sufficient
to carry the current and voltage as stamped on the equipment nameplate. The distance between the
Controller and the Feeder is an important factor that must be taken into consideration when determining
the size of the conductor. The voltage drop through conductors of insufficient size for the distances involved
will result in a definite lack of Feeder stroke and performance during operation. The further the distance,
the larger is the required size of conductor.
Connection to the Feeder must be by flexible cable furnished with the machine which should be connected
to the fixed wiring by a junction box adjacent to, but not affixed to, the drive housing. A similar cable gland
to that by which the cable enters the housing should be used at the junction box. The flexible cable should
be quite slack between these two glands.

Page 6 of 12 TC6B IO&M Manual
2.3 Earthing
The Feeder drive unit is fitted with a three core flexible cable, the Green/Yellow conductor of which is
connected to the magnet core assembly and must be earthed. The Controller is provided with an earth
stud or terminal through which the Feeder earth connection is normally made.
Both the Feeder and its Controller must be properly connected to an efficient
earth, such as a water pipe, earth rod, etc, in accordance with Supply
Authority Regulations.
Operation*
2.4 Operation
Each SYNTRON Vibrator or Feeder requires a SYNTRON Controller for its operation. The Model
TC6B is the standard controller for a rectified current equipment rated up to 6 amperes at 240
Volts. This controller has a double pole single throw switch “OFF” and “ON”, which control the
starting and stopping of the vibrator or feeder.
A silicon rectifier (SCR) is used to control the voltage applied to the vibrator or feeder magnet coil.
The SCR and its control components, including a control potentiometer, are encapsulated in a
TC6B module. A potentiometer control the SCR and hence the voltage of the vibrator or feeder
magnet coil. The magnet coil, in turn controls the magnitude of vibration of the vibrator or feeder.
The controller also contains a terminal block for making electrical connections to the vibrator or
feeder and to the power supply.
The control box should be installed as close as possible to the vibrator or feeder, preferably on a
wall. It is most important that the controller is kept in a clean and dry a location as possible which
is free from excessive vibration.
Maintenance*
2.5 Setting-Up Procedure
During commissioning or for maintenance purposes, the following procedure should be carried out. This
will ensure the Controller functions correctly and the Feeder maximum stroke is as per the Specific Data
Section of this manual.
NOTE: Before proceeding to adjust the control potentiometer, check that the air gap is set as per the
Specific Data Sheet.
1. Before applying power, set the variable controls as follows: "Rate Set" potentiometer – midway.
2. Check the power supply voltage and frequency to see that it corresponds to the ratings shown on the
vibrator or feeder nameplates.
3. Check all of the connections.
4. Check the vibrator or feeder for shorted or open circuited magnet coil.

Page 7 of 12 TC6B IO&M Manual
2.6 Field Checking the Silicon Controlled Rectifier (SCR)
An SCR can be difficult to check in field, because its characteristics under load are somewhat different than
when in a cold state.
A simple and effective cold state check of an SCR to determine a complete open or short is outlined below:
Isolate equipment prior to commencement of any work.
1. Disconnect the SCR from the Controller circuit.
2. Referring to Figure 10.1, construct a simple DC circuit using two flashlight batteries and a flashlight
bulb.
3. Connect the positive (+) lead to the SCR anode.
4. Connect the negative (-) lead to the SCR cathode.
IF THE BULB LIGHTS AT THIS POINT, THE SCR IS SHORTED AND SHOULD BE REPLACED.
If the bulb does not light, continue with the test.
5. Connect one end of a jumper on the anode side of the SCR.
6. Momentarily touch the gate of the SCR with the other end of the jumper lead. The bulb should now
light and stay lit.
IF THE BULB DOES NOT STAY LIT AFTER THE GATE IS MOMENTARILY TOUCHED, THE SCR IS
OPEN AND SHOULD BE REPLACED.
As mentioned before, this test is effective only if the rectifier is completely open or shorted.
Any partial breakdown of an SCR under load conditions can be determined and remedied only by
replacement of the defective SCR.
NOTE: A portable SCR tester, Part No. 047C0001, is available to perform the above functions.
Figure 2.1

Page 8 of 12 TC6B IO&M Manual
3.0 Trouble Shooting
No. Problem Possible Cause Resolution
1 Reduced
Feed Rate
Build Up or Binding Clear all build up between the trough and
surrounding structure
Wide Air Gap
Refer to the Specific Data Section of this Manual
and reset in accordance with the Detailed Static
Air Gap Adjustment
Broken Springs Consult Syntechtron and order replacement
Springs.
2 Hammering
Narrow Air Gap
Refer to the Specific Data Section of this Manual
and reset in accordance with the Detailed Static
Air Gap Adjustment
Broken Springs Consult Syntechtron and order replacement
Springs.
3 High Current,
Blown SCR.
Wide Air Gap
Refer to the Specific Data Section of this Manual
and reset in accordance with the Detailed
Procedure for Air Gap Adjustment
Build Up or Binding Clear all build up between the trough and
surrounding structure
Shorted Turn in the Coil Consult Syntechtron and order replacement coil.
4 Feeder Will
Not Start
External Circuitry Measure Supply Line Voltage. If there is no
supply Ensure all external interlocks are removed
Blown Line Fuses Measure the Continuity of the Line Fuse

Page 9 of 12 TC6B IO&M Manual
4.0 Recommended Spare Parts List
Equipment: TC6B Controller Assembly
Part No Description Qty
048E0710 Pot & Switch Label 1
048E0711 Connection Diagram Sticker 1
052D3830 TC6B 240 Volts Control Module 1
102E0257 Terminal Block 4
103E0058 Cable Gland 2
116E0189 500 ΩControl knob 1
118E0310 2 pole 20 Amps Isolator Switch 1


Page 11 of 12 TC6B IO&M Manual
6.0 Commissioning Record Sheets
1. It is important that before Commissioning the Engineer should be familiar with all aspects of Feeder
operation as contained in the Manual.
2. All items to be recorded.
3. Boxes are for checks and need only be ticked.
Model: Plant No:
Serial No: Current Rating: 6 Amps
Controller Model: TC6B Serial No:
Workshop Test Report Details:
Natural Frequency: cpm Static Air Gap: mm
Maximum Stroke: mm
Remarks:
Our Ref:
Isolation Spring Heights: (each set of springs must be equally loaded i.e. Front LHS equals to Front RHS)
Front Springs Unloaded mm Loaded mm
Rear Springs Unloaded mm Loaded mm
Trough Angles: Down slope Deg Level Transversely
Hopper Outlet Details:
Gate Height (H) mm Between Skirts (W) mm
Throat (T) mm
Skirt Divergence Skirt Clearance
Natural Frequency: Static Air Gap:
Cabling: Supply Cable size mm² Approx run length m
Drive Cable size mm² Approx run length m
Flexible Cable clearance from structure
Feeder: Suspension Slings Safety Slings
Transducer: Fitting Wiring
Controller: Supply Connections Interlocks
Wiring: Magnet Cable

Page 12 of 12 TC6B IO&M Manual
Company: Plant No.
Our Ref: Serial No.
Setting Up No Load
Signal Loss Trough Stroke mm
Rate set at Max. Trough Stroke mm Base Stroke mm
Coil Volts Volts Coil Current Amps
Rate set at Min. Trough Stroke mm Base Stroke mm
Coil Volts Volts Coil Current Amps
Maximum Current Amps @ Trough Stroke of mm
Dynamic Air Gap @ Maximum Stroke
Running Fully Loaded:
Rate set at Max. Trough Stroke mm Base Stroke mm
Coil Volts Volts Coil Current Amps
Rate set at Min. Trough Stroke mm Base Stroke mm
Coil Volts Volts Coil Current Amps
Maximum Current Amps @ Trough Stroke of mm
Supply Voltage: Prior to Feeder running Volts
Running loaded at maximum current with Volts
maximum gate opening
Tonnes per Hour: Minimum tph Maximum tph
Commissioning Remarks:
Commissioned by: Date:
NOTE: All voltage and current measurements must be measured with a true R.M.S. meter
Table of contents
Popular Controllers manuals by other brands
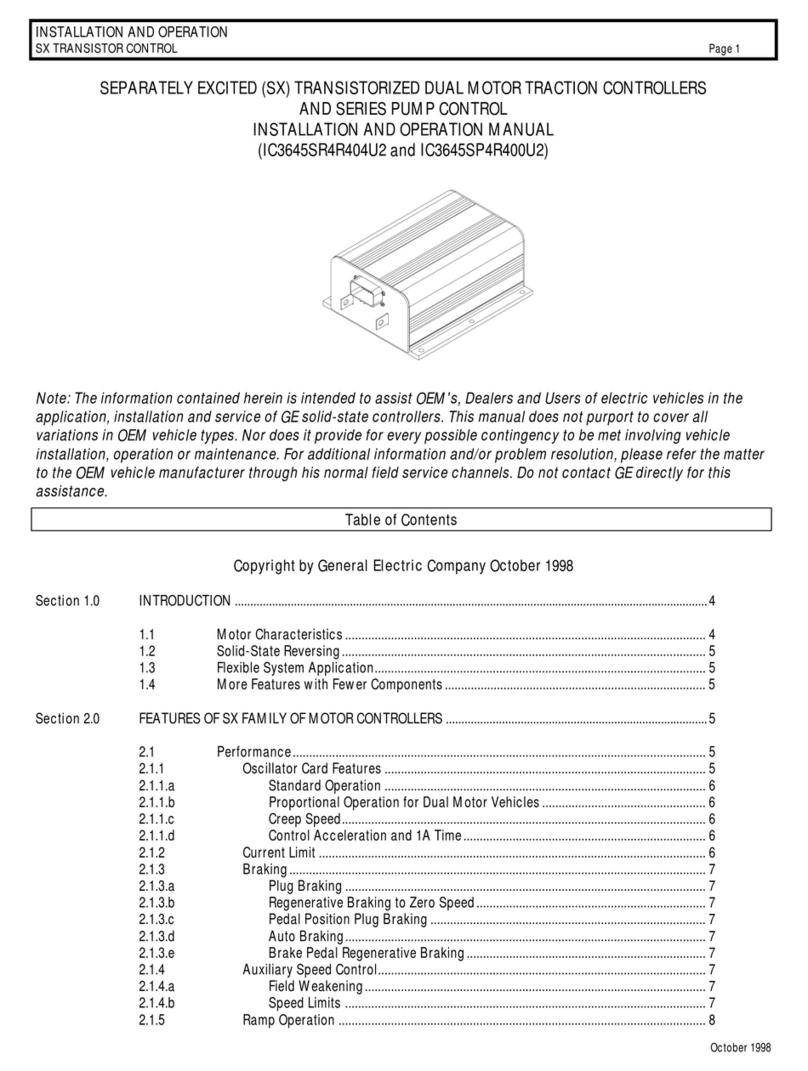
GE
GE IC3645SR4R404U2 Installation and operation manual
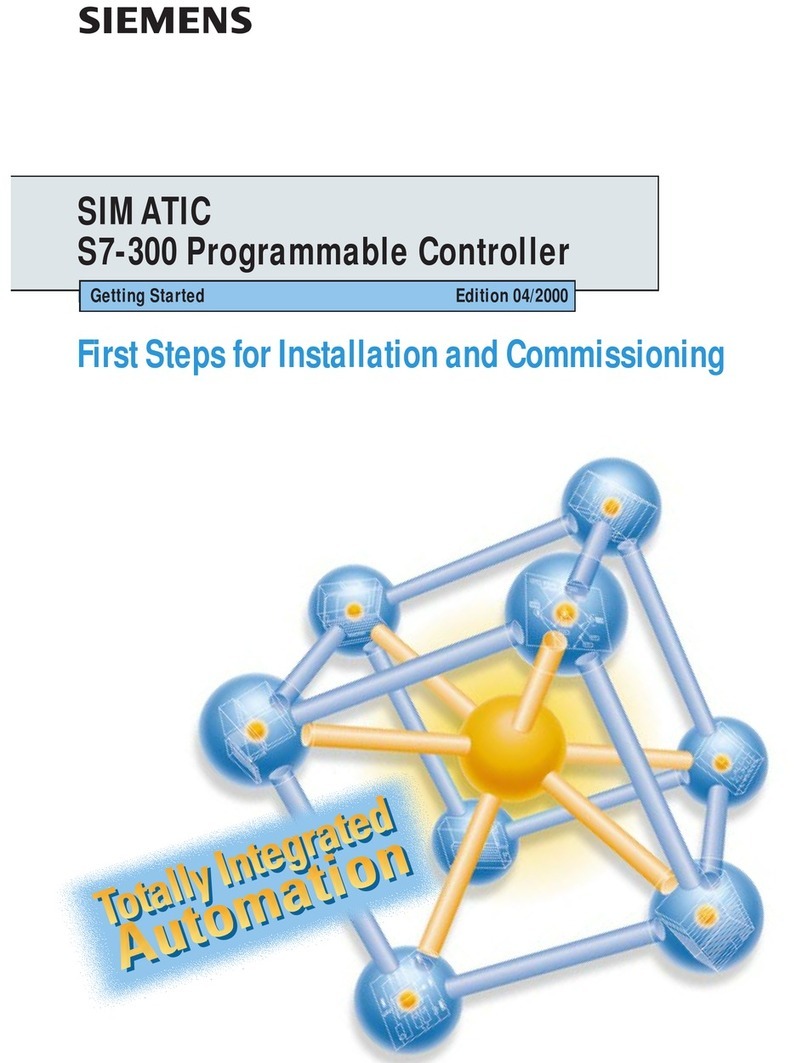
Siemens
Siemens Simatic S7-300 Getting started

Embelin
Embelin Remuc-2-AC Installer's guide
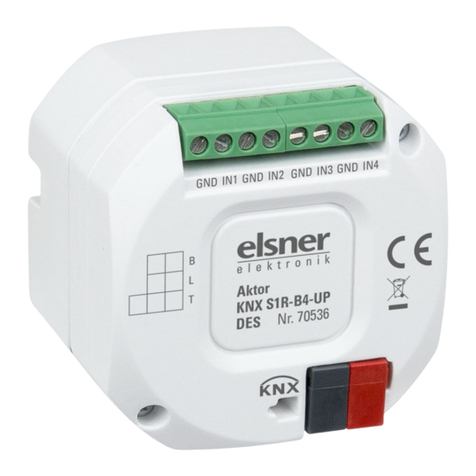
elsner elektronik
elsner elektronik KNX S1R-B4-UP DES Technical specifications and installation instructions
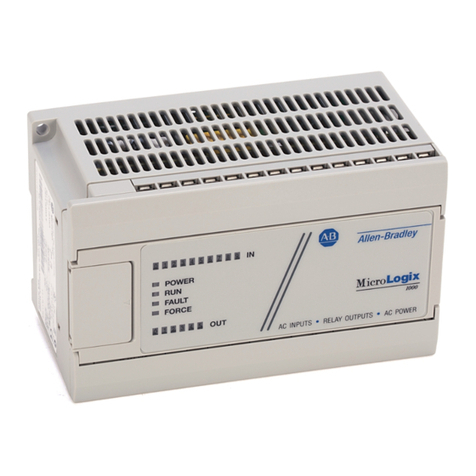
Rockwell Automation
Rockwell Automation MicroLogix 1000 installation instructions
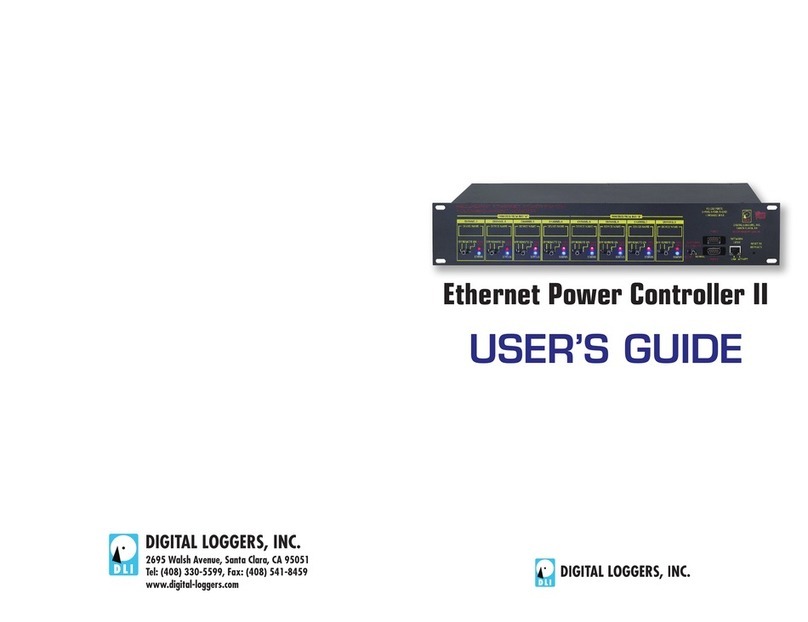
Digital Loggers
Digital Loggers Ethernet Power Controller II user guide