Tecfluid FLOMID Series User manual

R-MI-FIMX4 Rev.: 2 English version
Series FLOMID
Sensor FLOMID-FX
Converter MX4
Instructions manual
The art of measuring

2
Thank you for choosing a product from Tecfluid S.A.
This instruction manual allows the installation, configuration,
programming and maintenance. It is recommended to read it before
using the equipment.
• This document shall not be copied or disclosed in whole or in any
part by any means, without the written permission of Tecfluid S.A.
• Tecfluid S.A. reserve the right to make changes as deemed
necessary at any time and without notice, in order to improve the
quality and safety, with no obligation to update this manual.
• Make sure this manual goes to the end user.
• Keep this manual in a place where you can find it when you need
it.
• In case of loss, ask for a new manual or download it directly from
our website www.tecfluid.com Downloads section.
• Any deviation from the procedures described in this instruction
manual, may cause user safety risks, damage of the unit or cause
errors in the equipment performance.
• Do not modify the equipment without permission. Tecfluid S.A. are
not responsible for any problems caused by a change not
allowed. If you need to modify the equipment for any reason,
please contact us in advance.
PREFACE
WARNINGS

3
TABLE OF CONTENTS
FLOMID-FX SENSOR
1 WORKING PRINCIPLE ................................................................... 6
2 RECEPTION .................................................................................. 6
2.1 Unpacking .......................................................................... 6
2.2 Storage temperatures ......................................................... 6
3 HANDLING ................................................................................... 7
4 INSTALLATION ............................................................................. 7
4.1 Sensor position .................................................................. 8
4.2 Straight pipe sections .......................................................... 8
4.2.1 Mixtures ................................................................ 9
4.3 Valves ............................................................................... 9
4.4 Pumps ................................................................................ 9
4.5 Aeration ............................................................................. 10
4.6 Reduction of DN ................................................................. 10
4.7 Vibrations ............................................................................ 10
4.8 Magnetic fields ................................................................... 11
4.9 Temperature ...................................................................... 11
5 MOUNTING .................................................................................. 12
5.1 Parallelism .......................................................................... 12
5.2 Gasket position .................................................................. 12
5.3 Sensor earth connection ...................................................... 13
5.4 Tightening torque ................................................................ 14
6 MAINTENANCE ............................................................................ 14
MX4 CONVERTER
1 INTRODUCTION ........................................................................... 15
2 INSTALLATION .............................................................................. 15
2.1 Sensor connection .............................................................. 15
2.1.1 Compact converter ................................................ 15
2.1.2 Remote converter ................................................... 16
2.2 Electrical connection ............................................................ 16
2.2.1 Power supply wiring ................................................ 17
2.2.2 Relay output wiring ................................................. 17
2.2.3 Remote reset input wiring ....................................... 18

4
2.2.4 Analog output wiring ................................................ 19
2.2.5 Pulse output wiring ................................................. 20
3 REMOTE SENSOR ......................................................................... 21
3.1 Preparing the cable ............................................................ 21
3.2 Cable installation ................................................................. 23
3.3 Cable connection to sensor .................................................. 23
3.4 Cable connection to converter .............................................. 24
3.5 Cable specifications ............................................................ 25
4 CONVERTER INTERFACE .............................................................. 26
5 MAIN MENU .................................................................................. 27
5.1 Passwords to access the menus .......................................... 27
6 INSTALLATION PARAMETERS ....................................................... 29
6.1 Language ........................................................................... 30
6.2 Sensor factor ...................................................................... 30
6.3 Converter factor .................................................................. 30
6.4 Nominal diameter ................................................................ 30
6.5 Diagnosis ........................................................................... 30
6.5.1 Parameters ............................................................ 31
6.5.2 Simulator ............................................................... 31
6.5.3 Mains frequency .................................................... 32
6.5.4 Coil current ............................................................ 32
7 CONVERTER PROGRAMMING ...................................................... 33
7.1 Language ........................................................................... 33
7.2 Units .................................................................................. 34
7.3 Flow rate decimals .............................................................. 34
7.4 Flow rate ............................................................................. 35
7.4.1 Empty pipe ............................................................. 35
7.4.2 Cut off .................................................................... 35
7.4.3 Reversal flow rate ................................................... 36
7.4.4 Damping ............................................................... 36
7.4.5 Offset .................................................................... 37
7.5 Outputs ............................................................................. 37
7.5.1 Relay 1 and relay 2 ................................................ 37

5
7.5.1.1 Alarm ...................................................... 38
7.5.1.2 Empty pipe ............................................... 38
7.5.1.3 Negative flow ............................................ 38
7.5.2 Pulse output ........................................................... 38
7.5.2.1 Pulse output configuration ......................... 38
7.5.2.2 Units ....................................................... 39
7.5.2.3 Pulses ..................................................... 39
7.5.2.4 Duty cycle ............................................... 39
7.5.3 Analog output ......................................................... 39
7.5.3.1 4-20 mA output configuration ................... 40
7.5.3.2 Programming of the 4-20 mA output .......... 40
7.5.3.3 Current calibration for 4 and 20 mA .......... 40
7.6 Working screen ................................................................... 40
7.7 Totalizer ............................................................................. 41
7.8 Modbus ............................................................................. 42
8 SERIAL NUMBER ......................................................................... 42
9 SOFTWARE VERSION .................................................................... 42
10 WORKING SCREEN ....................................................................... 42
11 STARTING CURRENT ................................................................... 43
12 MAINTENANCE ............................................................................ 43
12.1 Fuse .................................................................................. 43
13 ASSOCIATED SOFTWARE WINSMETER MX4 ................................ 44
13.1 USB cable connection and drivers installation ...................... 44
13.2 Port connection ................................................................... 45
13.3 Access to installation and programming ................................ 46
13.4 Datalogger ......................................................................... 49
13.5 Visualization ....................................................................... 51
13.6 Firmware updates ............................................................... 52
14 TECHNICAL CHARACTERISTICS .................................................... 53
15 SAFETY INSTRUCTIONS ............................................................... 55
15.1 Pressure equipment directive .............................................. 55
15.2 Certificate of conformity TR CU (EAC marking) ..................... 55
16 DIMENSIONS ............................................................................... 56
17 TROUBLESHOOTING .................................................................... 69
ANNEX A Flow rate diagram ................................................................. 70

6
1 WORKING PRINCIPLE
The FLOMID electromagnetic flowmeters are based on Faraday’s induction law.
When an electrically conductive liquid flows through a magnetic field, perpendicular to the
flow direction, it induces a voltage Vm proportional to the liquid velocity.
Two electrodes in contact with the liquid and positioned perpendicularly to the magnetic
field, sense this voltage V.
2 RECEPTION
The FLOMID electromagnetic flowmeters are supplied conveniently packaged for
transportation together with their instruction manual for installation and operation.
All the flowmeters have been verified in our calibration rigs to obtain the Fc factor for each
sensor.
2.1 Unpacking
Unpack the instrument carefully, removing any remains of the packing from the inside of the
sensor. Do not remove the grease from the neck that couples to the electronics housing.
2.2 Storage temperatures
Sensors linings of : PTFE and PVDF -20ºC ...... +60ºC
PP and EBONITE -5ºC ...... +50ºC
V = B·vm·D
Where:
V = Measured voltage in the electrodes
B = Magnetic field
vm= Average liquid velocity
D = Pipe diameter

7
4 INSTALLATION
This should be made in a point that guarantees that the pipe is always completely full.
Avoid high points of the pipes where air pockets usually form, or pipes with falling flow where
vacuums can form.
Partially full pipes can produce important reading errors.
Flow rate measurement with open discharge makes it necessary to install the flowmeter in a
pipe section with a siphon which avoids stagnation of air in the sensor.
3 HANDLING
It should always be done with care and without knocks.
The large diameter sensors have rings for holding the elevation elements. If the flowmeter is
held using slings, these should hold on the sensor and not on the electronics housing (see
drawing).

8
4.2 Straight pipe sections
They are necessary before and after the sensor. The minimum distances are the following:
Upstream 5 DN
Downstream 3 DN
In installations with turbulent flow it may be necessary to increase these distances.
4.1 Sensor position
The most adequate position is with the electrodes in a horizontal plane. In this way,
deposits of particles on the electrodes are avoided.

9
4.2.1 Mixtures
If liquids of different conductivities are mixed it is necessary to install the sensor a minimum
of 30 DN from the point of mixture in order to obtain a uniform conductivity of the liquid and
stabilize the readings.
If this distance is shorter, readings may be unstable.
4.4 Pumps
Pumps should be mounted upstream from the sensor to avoid the suction of the pump
(vacuum) that could damage the sensor liner.
4.3 Valves
Control valves or shut-off valves should always be installed downstream from the sensor to
assure that the pipe is always full of liquid.

10
4.5 Aeration
If there is a point where the difference in level is higher than 5 m an air inlet valve should be
installed after the sensor to avoid a vacuum effect that could damage the sensor liner.
4.6 Reduction of DN
In installations where, due to reasons of the flow rate to be measured, a sensor of a smaller
DN than the pipe DN must be mounted, the reduction must be done with an angle smaller
than 4º to avoid turbulences that can give false readings.
If the angle cannot be so small, straight pipe sections indicated in point 4.2 must be kept.
4.7 Vibrations
Vibrations of the pipes should be avoided by anchoring the pipe before and after the sensor.
The vibration level should be less than 2.2 g in the range of 20-150 Hz according to IEC 068-
2-34.

11
4.8 Magnetic fields
Strong magnetic fields close to the sensor should be avoided.
4.9 Temperature
In open air installations it is recommended to install a protection to avoid direct sun light on
the flowmeter.
With thermally insulated pipes DO NOT insulate the sensor. High temperatures can damage
it.
The maximum liquid temperatures are shown on page 53.

12
5 MOUNTING
5.1 Parallelism
The maximum parallelism error must be less than 0.5 mm (Lmax—Lmin ≤ 0.5 mm).
5.2 Gasket position
In the wafer mounted sensors, in order to avoid leakage of the liquid into the sensor, it is
necessary to ensure that the rubber gasket (A) of the figure is well centered, so that it
presses directly on the plastic liner.
The standard gasket material supplied is NBR. Other materials can be supplied on demand.
The sensors with connections different to wafer are supplied without gaskets..

13
b) In the case of metallic pipes with internal lining or plastic pipes, connect the earth
cables to the earthing disks, supplied on request.
5.3 Sensor earth connection
To obtain correct operation the sensor should have its functional earth connected to a point
that is in direct contact with the liquid whose flow rate wants to be measured.
The earth cables should assure a good electrical contact. To obtain this, they should be well
screwed down and with a good contact on both sides of the sensor. It is important to
eliminate paint or coverings that act as insulation of the connection.
The functional earth connection should be used exclusively for the sensor given that parasitic
signals caused by other electrical equipment connected to this earth can cause malfunction
of the sensor.
In the case that there are high voltage differences between different earth points, this will
cause currents that may give problems in the readings (empty pipe indication). In these
cases, do not connect the functional earth to the protective earth of the mains.
The connection of the functional earth should be made as follows:
a) In the case of metallic pipes without internal lining connect the earth cables to the
counter flanges.
The earthing disks are necessary when the installation is with plastic pipes or metallic pipes
with an internal insulating lining (PTFE, PVDF, PP, EBONITE etc.).

14
Earthing disks are supplied in two versions:
Metallic, disk in stainless steel EN 1.4404 (AISI 316L), for liquids compatible with this
material.
Plastic, with an electrode to make the contact with the liquid. The materials (plastic and
metal) depend on the working liquid.
5.4 Tightening torque
The tightening torque for the flange bolts should not exceed 32 Nm for working pressures of
16 bar maximum.
This tightening torque should be applied to wafer mounting (Flomid-0FX) and also to flange
mounting sensors (FLOMID-2FX) for the same working pressure of 16 bar.
The maximum tightening torque varies in function of the nominal pressure (PN) of the sensor.
The tightening of the bolts should be uniform, following the sequence shown in the drawings
and depending on the number of flange bolts.
6 MAINTENANCE
It is recommended to clean the electrodes in installations where build ups or appreciable
sedimentations can occur.
Cleaning can be done using liquid detergents and medium hard brushes.
Dimensions in mm
PlasticMetallic

15
MX4 CONVERTER
1 INTRODUCTION
The MX4 converter unit can be used with the different FLOMID and FLOMAT series of
electromagnetic flow sensors. The electronic circuit is based on the most advanced
technology in digital signal processing, in order to obtain accurate and reliable
measurements.
The device provides the following features:
• Coil excitation by means of pulsed signal to obtain a negligible zero offset.
• Pulse and current output proportional to the flow rate and user programmable.
• Relay outputs user programmable as flow rate alarm or status.
• Local and remote mounting.
• Easy exchange with other sensors.
• Graphic display with intuitive menus.
• Adjustable front cover in order to make display reading easier, depending on
installation.
2 INSTALLATION
2.1 Sensor connection
2.1.1 Compact converter
The converter provides two
cables to be connected to the
sensor. Once connected, slide
the converter along the sensor
neck until the stop. Tight the
two fixing screws.
Fixing
screws
Connectors
Neck

16
2.1.2 Remote converter
One of the ends of the cable has a header and two wires, to connect them to the sensor.
The connection is as explained in point 2.1.1.
The other end has to be connected to the converter, and has five wires. The cable must be
passed through the cable gland and the connection for each wire is explained in chapter 3.
2.2 Electrical connection
For the electrical installation, the MX4 converter has two terminal strips. To help in the wiring
of the equipment, the description of the terminals is marked on a label in the rear cover of
the device.
For the electrical installation it is recommended to use multiple conductor cables with
individual cable sections in the order of 0.25 to 0.5 mm2in order to make it easier to
connect. It is better to maintain the cables with mains voltage (power supply) separated from
the cables with low level signals (4-20 mA, etc.).
Before starting the installation, check that the cable glands are the right size for the cables to
be used. This will guarantee the instrument will stay watertight. The cable glands used are
for cables with outside diameters between 3.5 mm and 10 mm
To connect the cables, peel the outside insulation to free the inner cables. It is
recommended to put a terminal at the ends of the wires to avoid loose ends. Pass the
cables through the cable glands and screw down in the corresponding positions of the
terminal strip. Once the wiring is finished make sure that the cables are well gripped by the
cable glands to maintain the degree of protection.
Incorrect installation of the cable gland or inadequate cable placement can cause irreparable
damage to the converter.
IMPORTANT NOTE: In order to comply with the electrical safety requirements as per EN-
61010-1 (IEC 1010-1), the installation of the equipment must take into account the following:
• A mains switch must be provided to disconnect the equipment. This switch must
be marked as the disconnecting device for the equipment and be within easy reach
of the operator.
• The mains supply must have an earth line.
• The housing must not be opened when the instrument has mains supply
connected.
IMPORTANT NOTE: To ensure smooth operation of the equipment, it is recommended to
make the connection paying attention to the following points:
• For the output signals, use shielded cable when possible.
• Keep the cables away from strong sources of noise.

17
2.2.1 Power supply wiring
Before starting the installation of the equipment, check that the supply voltage available is
the same as marked on the label of the converter.
Terminal Power supply AC Power supply DC
8Earth NC
9 Neutral -
10 Phase +
It is very important to connect the mains earth to the instruments with AC power supply due
to the presence of a mains filter inside the converter that uses this connection.
2.2.2 Relay output wiring

18
Terminal Description Relay
6Normally Open Relay 1
5Common Relay 1
4Normally Open Relay 2
3Common Relay 2
The relay outputs provide relays with potential free contacts (see characteristics in page 53).
The status of the relay contacts corresponds to the relay at rest.
The relay contacts are not protected in any way, and therefore they must be installed
externally as required in the application, taking into account the limitations of the
characteristics of such contacts. In the case of having inductive loads, and to extend the
working life of the relay contacts, it is recommended to use overvoltage protection (VDR for
AC and diodes for DC loads). In all cases a fuse or some kind of protection against short
circuits, should always be provided according to the needs of the intended load.
2.2.3 Remote reset input wiring

19
Terminal
1Contact
2Contact
These terminals correspond to an input that resets the value of the totalizer. A potential free
normally open push button can be connected. The push button contact must be a good
quality snap action switch to guarantee correct working at low voltages and reduce contact
bounce effects.
2.2.4 Analog output wiring
Terminal
11 mA (positive, active output)
12 mA
13 mA (negative, passive output)
The analog output is galvanically isolated. It can be either active (which means that the
receiving device must be passive) or passive (which means that the receiver must supply the
power for the current loop). It is recommended to use a receptor with an input resistance of
less than 700 Ω to guarantee correct operation.
The configuration of the analog output mode (active or passive) is done by means of the
connection to the terminal strip. For active mode, terminals 11 and 12 are connected. For
passive mode, terminals 12 and 13 are connected.
NOTE: The analog output has protection against reversed polarity. Due to another
protection against over voltages, if a loop supply voltage of more than 32 V is connected the
converter may be damaged.

20
2.2.5 Pulse output wiring
Terminal
14 Collector
15 Emitter
The pulse output is opto-isolated. The terminals are the collector and emitter of a NPN
bipolar transistor.
In the case of using inductive loads, in order to protect the output transistor, the use of free
wheeling diodes is required.
Active output
Passive output
Coil
Other manuals for FLOMID Series
2
This manual suits for next models
2
Table of contents
Other Tecfluid Measuring Instrument manuals

Tecfluid
Tecfluid LS Series User manual
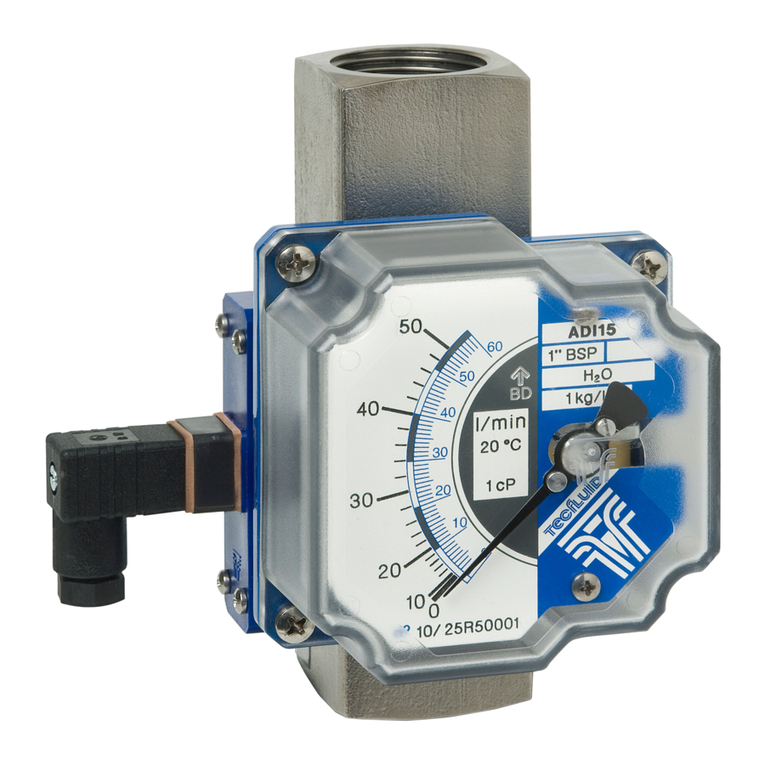
Tecfluid
Tecfluid AD Series User manual
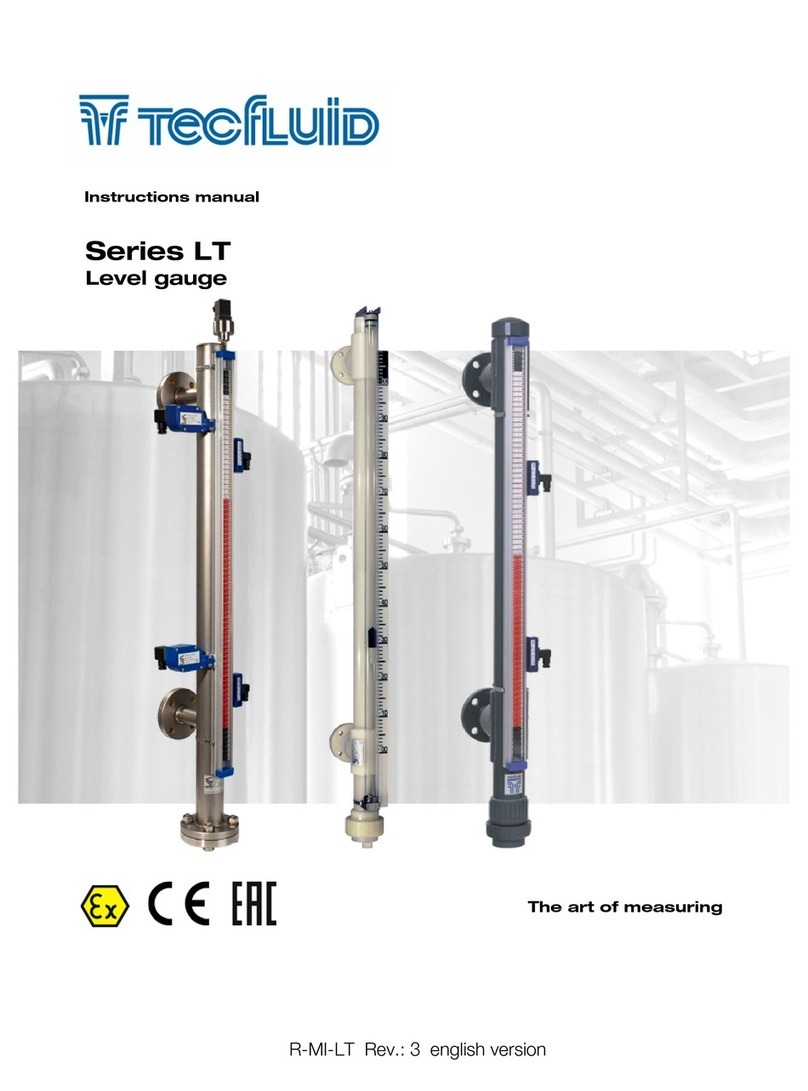
Tecfluid
Tecfluid Series LT User manual
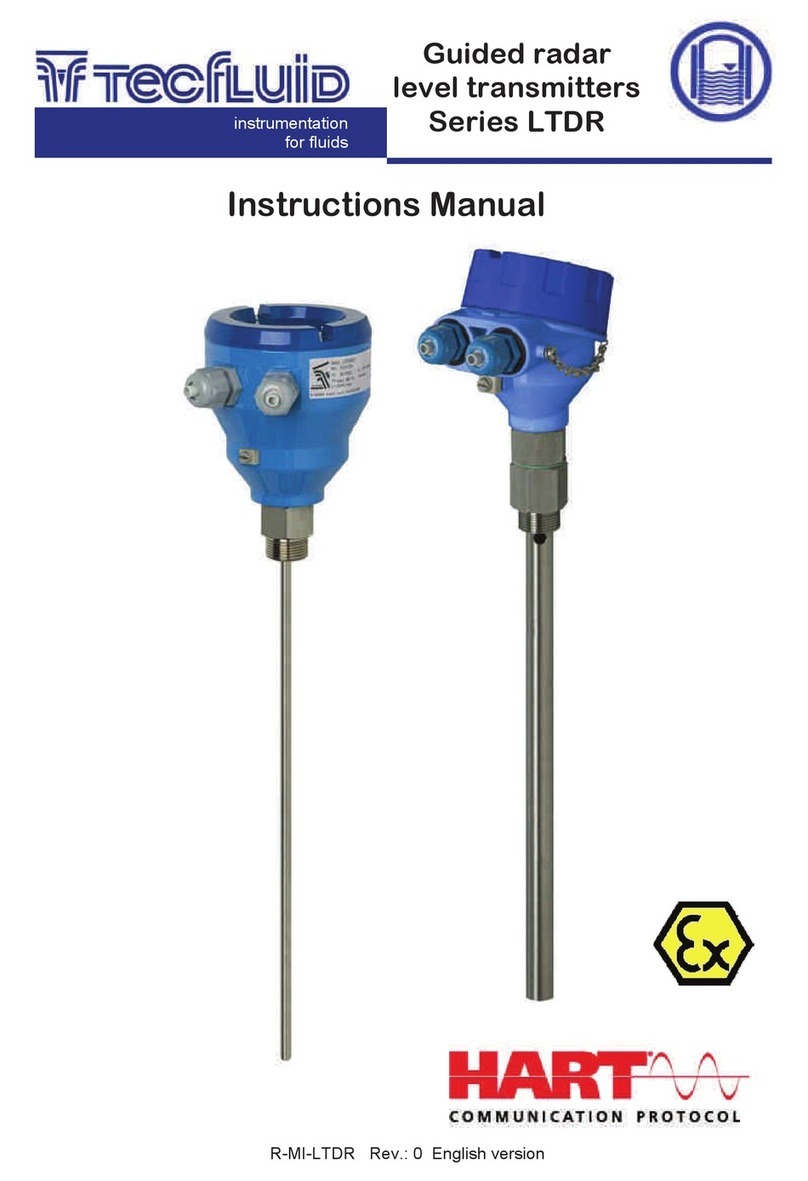
Tecfluid
Tecfluid LTDR series User manual

Tecfluid
Tecfluid 2100 Series User manual
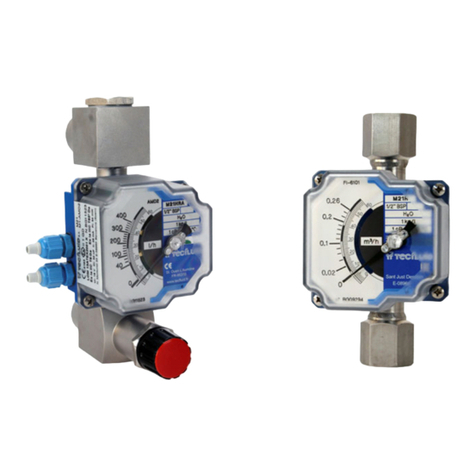
Tecfluid
Tecfluid M21 User manual

Tecfluid
Tecfluid CU Series User manual
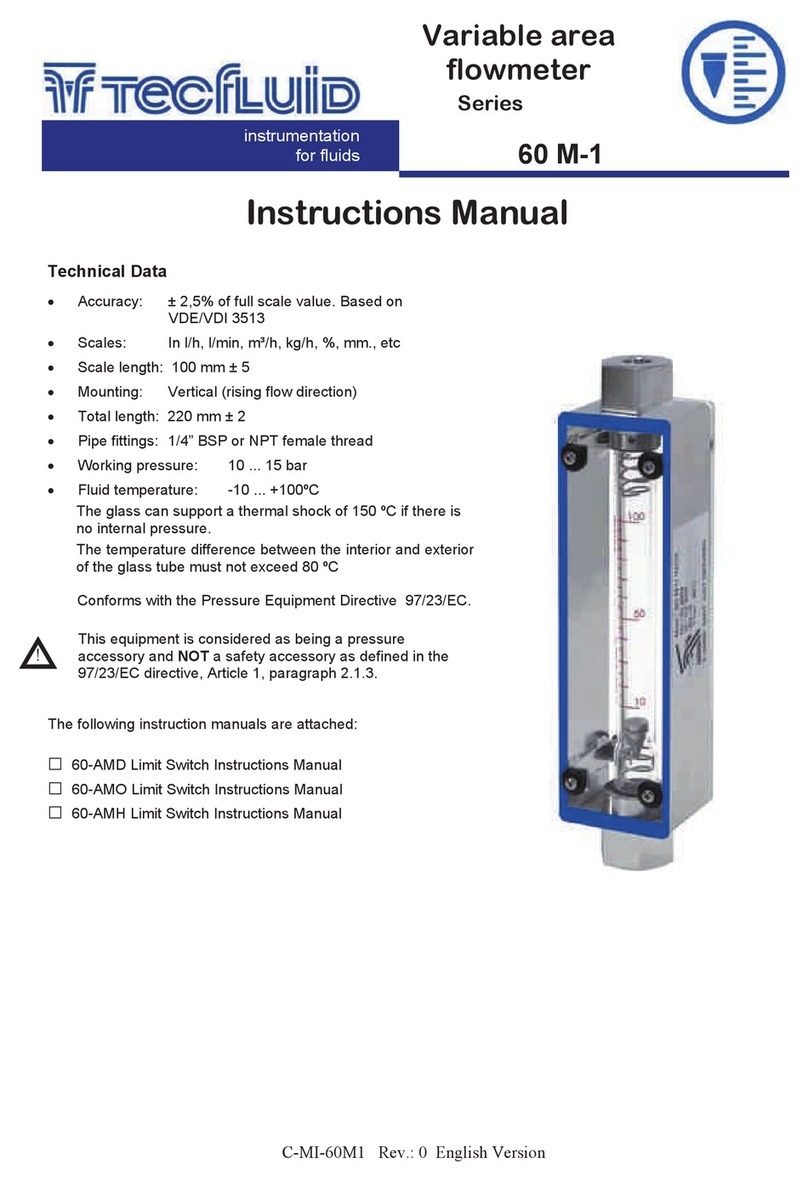
Tecfluid
Tecfluid 60 M-1 Series User manual
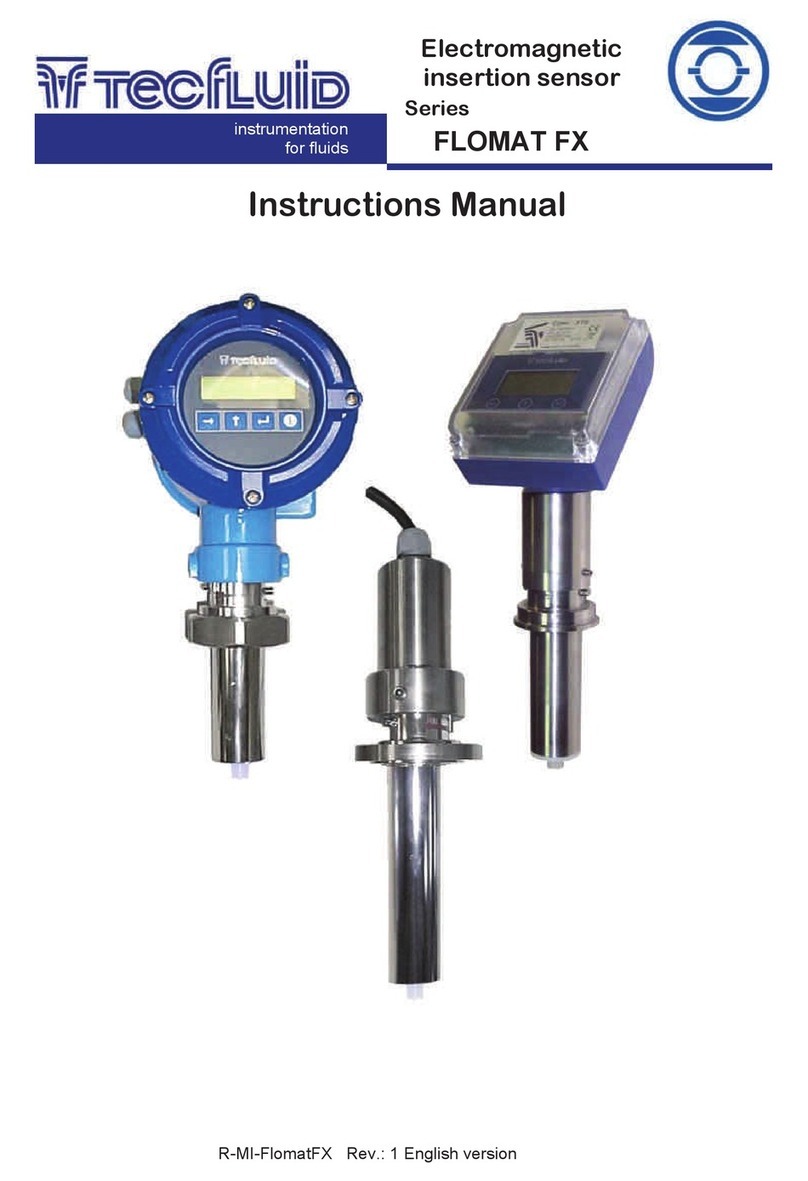
Tecfluid
Tecfluid FLOMAT FX FlomatFX User manual
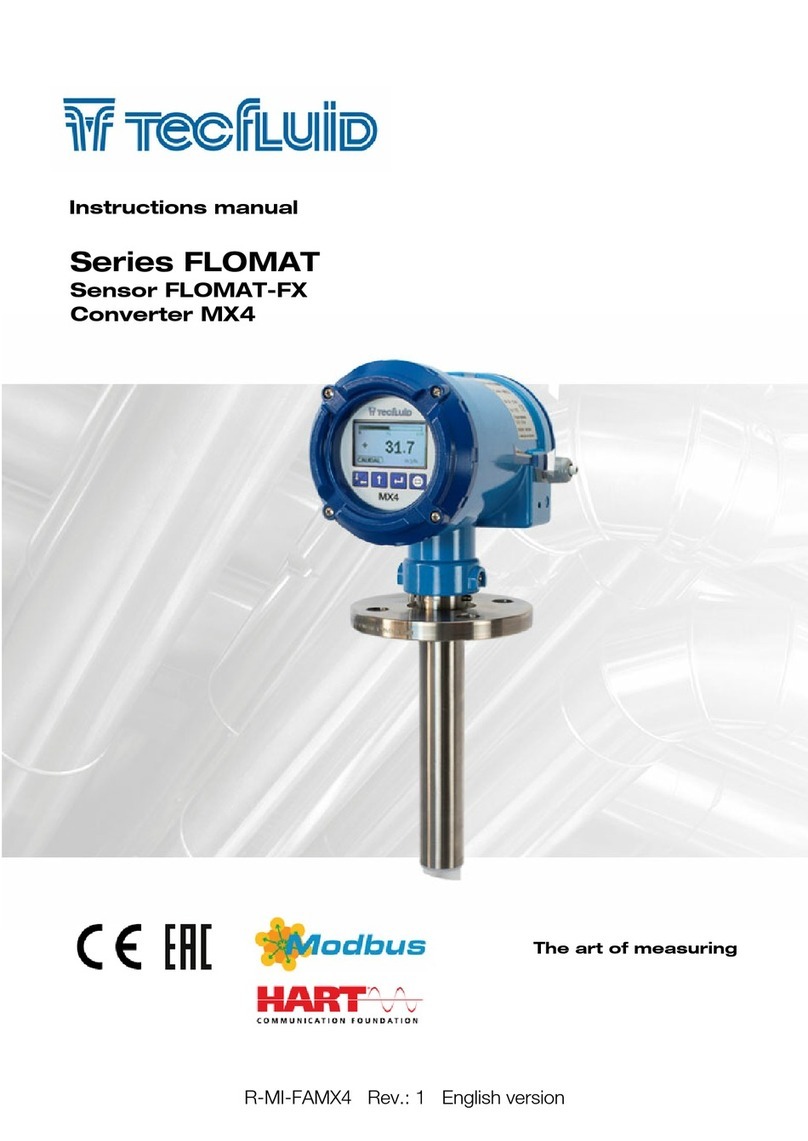
Tecfluid
Tecfluid FLOMAT Series User manual