Technology Uncorked Robotic-Mech Instructions for use

© TU Technology Uncorked LLP. All Rights Reserved.
P a g e | 1
Learn about Robotics, Mechanical,
Electrical, Electronics and System
Design Concepts as you build this
Remote controlled Octamotion Pick
and Place Robot from bottoms-up
using a pre-programmed CPU
board!
Construction
Manual
Remote Controlled
Octamotion Pick and Place
Robot
From
Technology
Uncorked

© TU Technology Uncorked LLP. All Rights Reserved.
P a g e | 2
For any questions, concerns, or issues; submit them to support@tekuncorked.com
TU Technology Uncorked LLP provides the enclosed product(s) for use in Engineering development, demonstration, and education or evaluation. The kit contains
very small mechanical and electronic parts and hence is recommended for use by children above 10 years. For children below 6 years, the kit should be assembled
strictly under adult supervision.
Mailing address: Technology Uncorked LLP, D-125, Sushant Lok-3, Sector 57, Gurgaon, Haryana, India 122001
Reach out to us on phone at: 0124-2386436

© TU Technology Uncorked LLP. All Rights Reserved.
P a g e | 3
Contents
1Overview..............................................................................................................................................................................................5
2Key Features.........................................................................................................................................................................................5
3NUTS & BOLTS of the BOT...............................................................................................................................................................5
3.1 Mechanical Section.....................................................................................................................................................................5
3.2 Electrical and Electronics Section ..............................................................................................................................................7
3.2.1 TU050 Octamotion Robot Base-Board ..................................................................................................................................8
3.2.2 TU003 Renesas Microcontroller R8C1B Gumstrip V1.1.......................................................................................................9
3.2.3 TU048 DC Motor Driver Kit..................................................................................................................................................9
3.2.4 TU008 12 to 5V DC-DC Converter......................................................................................................................................10
3.2.5 TU043 IR Receiver Module.................................................................................................................................................10
3.2.6 Infrared (IR) Remote............................................................................................................................................................10
3.2.7 Re-chargeable Battery Pack..................................................................................................................................................11
3.2.8 Battery Charging Adapter.....................................................................................................................................................11
3.2.9 Connecting Wires.................................................................................................................................................................12
3.2.10 Spacers and Fasteners ......................................................................................................................................................12
3.2.11 Tools & Aids for Electronics Assembly...........................................................................................................................12
3.3 Constructing the BOT...............................................................................................................................................................13
3.3.1 Integrating the Base Board Electronics ................................................................................................................................13
List of Figures
Figure 1: TU050 Octamotion Robot Base-Board.........................................................................................................................................8
Figure 2: TU007 Micro-controller Gum-strip..............................................................................................................................................9
Figure 3: TU048 Dual DC Motor Driver Kit ...............................................................................................................................................9
Figure 4: TU008 12 to 5V DC-DC Converter............................................................................................................................................10
Figure 5: TU043 IR Receiver Module........................................................................................................................................................10
Figure 6: IR Remote...................................................................................................................................................................................11
Figure 7: Rechargeable Battery Pack .........................................................................................................................................................11
Figure 8: Battery Charging AC-DC Adapter..............................................................................................................................................11
Figure 9: Kit Mounting Holes ....................................................................................................................................................................13
Figure 10: Mounting DC Motor Drivers on Base Board............................................................................................................................13
Figure 11: Mounting 12V to 5V Converter Kit..........................................................................................................................................14
Figure 12: Mounting MCU Gumstrip.........................................................................................................................................................14
Figure 13: Mounting IR Recvr ...................................................................................................................................................................14
Figure 14: 12V/GND Connections.............................................................................................................................................................15
Figure 15: Motor Control Connections ......................................................................................................................................................15
Figure 16: Making 5V/GND Connections .................................................................................................................................................16
Figure 17: Mounting Baseboard on Chassis...............................................................................................................................................16
Figure 18: Battery Charging.......................................................................................................................................................................17
Figure 19: Fully Assembled Octamotion BOT...........................................................................................................................................18

© TU Technology Uncorked LLP. All Rights Reserved.
P a g e | 4

© TU Technology Uncorked LLP. All Rights Reserved.
P a g e | 5
Construction Manual for Remote Controlled
Octamotion Pick and Place Robot
1OverviewCPU board!
Remote Controlled Octamotion Pick and Place Robot is Do-It-Yourself Kit which is available with a Pre-
programmed CPU Board. Learn the nuances of Robotics, Mechanical, Electrical, Electronics and System
Design as you build this Robot from bottoms-up.
2Key Features
Learn as You Build : Do-It-Yourself Kit
4-wheel Chassis with Robotic ARM and Gripper
Eight Movements: FWD,BWD,RIGHT,LEFT,ARM UP,ARM DWN,GRIPPER OPEN,GRIPPER CLOSE
Fine Controls for FWD & BACKWARD: Slight FWD, Slight BWD
Differential gear mechanism for turning
Supports Infrared Remote Control Operation
Load bearing capacity of the arm up to 500g
12V Rechargeable Battery Operated
Integrated Battery Charging Pod and Adapter
So, are you ready for this adventure?
3NUTS & BOLTS of the BOT
The entire BOT is constructed part by part and comprises of two primary sections:
Mechanical and Electro-Mechanical Section or the Robot Chassis
Electronics Section or the Robot Controller
Let us spend some time understanding each section before we start the actual integration.
3.1 Mechanical Section
This section comprises of mechanical components which shall be used to construct the mechanical
structure of your BOT.
Identify following components and tools in your Kit:

© TU Technology Uncorked LLP. All Rights Reserved.
P a g e | 6
250x130mm Jumbo Metal
Chassis | Quantity: 1
Use: Base Chassis for the
Robot
95 x 20 mm Robot
Wheel and Tyre for
6mm shaft | Quantity:
4
150 RPM DC
Geared Motor |
Quantity: 4
Use: Locomotion
45 RPM DC Geared
Motor 6mm Dia |
Quantity: 2
Use: Gripper
Movements
Clamping Block |
Quantity: 4
Use: To Clamp Gripper
Base Plate
Worm Gear | Quantity: 2
Use: Gripper Movements
Gripper Base Plate |
Quantity: 4
Worm Wheel Gear |
Quantity: 3
Use: Gripper Movements
Metal Shaft | Quantity: 1
Use: Gear Mount
Gripper Plate
Spacers 30mm|
Quantity: 4
Gripper Plate
| Quantity: 2
Double Hole Plate
| Quantity: 4
Lever Plate |
Quantity: 2
M4 Fastener
10mm | Quantity:
15
M4 Fastener
8mm | Quantity:
15
M4 Hex Nut |
Quantity: 10
Also Included:
Gripper Mounting Plate: 1
Gripper Clip: 2
Locking Key: 1
Taparia 712 |
Quantity: 1
Taparia 932 |
Quantity: 1
M4 Nut Spanner
| Quantity: 1

© TU Technology Uncorked LLP. All Rights Reserved.
P a g e | 7
Construction of the mechanical section or the Robot Chassis involves
Assembly of base 4-wheel drive chassis
Arm & Gripper
Integration of the Base Chassis with the Arm and Gripper
For details about assembly of the Mechanical structure of the BOT, please follow the given
links: Product: https://www.tu-eshop.com/Octamotion-Pick-and-Place-Robotic-Arm-DIY-Kit
YouTube Video: https://www.youtube.com/watch?v=oWJuhIX7fiM
3.2 Electrical and Electronics Section
This is the section which allows you to operate and control the Robot remotely. This section consists of
the following parts:
TU050 Octamotion Robot Base-Board
TU003 Renesas Microcontroller R8C1B Gumstrip V1.1
TU048 DC Motor Driver Kit
TU008 12 to 5V DC-DC Converter Kit
TU043 IR Receiver Module
IR Remote
Re-chargeable Battery Pack
Battery Charging Adapter
Connecting Wires
Spacers and Fasteners
Tools for Electronics Assembly

© TU Technology Uncorked LLP. All Rights Reserved.
P a g e | 8
Know Your Electronic Kits
3.2.1 TU050 Octamotion Robot Base-Board
All the electronic kits are mounted and inter-connected on the Base board. Base board is mounted
on the chassis using nuts and spacers. The battery charging POD is also integrated on the
Base Board.
Rear Side of the Base Board
Front Side of the Base Board (Near Pick and Place Arm)
Figure 1: TU050 Octamotion Robot Base-Board

© TU Technology Uncorked LLP. All Rights Reserved.
P a g e | 9
3.2.2 TU003 Renesas Microcontroller R8C1B Gumstrip V1.1
This microcontroller kit is the brain of the BOT and has a powerful micro-controller R8C1B from
Renesas Inc. It is a 16-bit microcontroller which can operate at maximum frequency of 20MHz. It
can access memory size of 64K Bytes. Connector J1 on the Base Board is the main power
connector for this Kit. Reset switch (S1) on the Gumstrip can be used to reset the microcontroller.
Use it, if the BOT misbehaves. The micro-controller kit that you have in the box is pre-programmed
for the BoT operation.
3.2.3 TU048 DC Motor Driver Kit
Each DC Motor driver kit can drive two independent DC motors in Clockwise or Anti-clockwise directions.
The Motor Driver receives signals from the micro-controller which is operating at 5V. The MCU commands
are decoded and converted to 12V Motor signals with adequate current to drive the motors.
Octamotion Robot Base Board has two DC Motor Driver Kits. One kit is dedicated to the Robot Locomotion
in Forward, Reverse, Right and Left directions. Other kit is dedicated for the Robot Arm and Gripper
motions.
Figure 2: TU007 Micro-controller Gum-strip
Figure 3: TU048 Dual DC Motor
Driver Kit

© TU Technology Uncorked LLP. All Rights Reserved.
P a g e | 10
3.2.4 TU008 12 to 5V DC-DC Converter
Octamotion Robot requires two DC supplies for it’s operation – 12V for driving the six motors and 5V for
operating the entire electronics kits and circuits. This kit draws power from the 12V battery and converts it to
regulated 5V DC which powers all the electronics kits. !2V battery supply is also fed to the Motor Drivers
which use this supply to derive motor signals.
3.2.5 TU043 IR Receiver Module
This module receives infrared signals from the IR Remote, converts them to
electrical signals and sends them to the Microcontroller. Microcontroller decodes
the commands embedded in these signals and initiates actions on the BoT
accordingly. Make sure that IR Remote and Infrared Receiver Module are in
Line of Sight and not farther apart than few meters.
3.2.6 Infrared (IR) Remote
We control the movement of the Robot with the help of this remote. IR works on line of sight. Hence
always position the IR remote in line of sight of IR Receiver Module TU043 that is mounted on the
Octamotion Base Board. Here are the commands that you can send to the BoT:
Figure 4: TU008 12 to 5V
DC-DC Converter
Figure 5: TU043 IR Receiver Module

© TU Technology Uncorked LLP. All Rights Reserved.
P a g e | 11
3.2.7 Re-chargeable Battery Pack
12V Re-chargeable Li-ion Battery Pack is used to power up and operate the BoT.
Charging POD on the Base Board can be used to charge the battery using the AC-DC
Adapter included in the box.
3.2.8 Battery Charging Adapter
220V AC to 12V DC Charging Adapter is provided in the box to
charge the battery. Plug the Adapter into AC MAINS and plug the
DC Jack in to the charging pod provided on the Octamotion Base
Board. Connect the battery to the charging pod connector. Charge a
fully depleted battery for 3 Hours to re-charge it again.
KEY
Control
2
FORWARD
4
LEFT
6
RIGHT
8
REVERSE
1
GRIP CLOSE
3
GRIP OPEN
7
ARM UP
9
ARM DOWN
VOL+
MOVE FORWARD SLIGHTLY
VOL-
MOVE BACKWARD SLIGHTLY
5
HALT
PWR
HALT
Figure 6: IR Remote
Figure 7: Rechargeable
Battery Pack
Figure 8: Battery Charging AC-DC Adapter

© TU Technology Uncorked LLP. All Rights Reserved.
P a g e | 12
3.2.9 Connecting Wires
3.2.10 Spacers and Fasteners
3.2.11 Tools & Aids for Electronics Assembly
Multi-strand Wires –Red &
Black | Quantity: 1.5 m Each
Use: Electronics Assembly
Connections
Female to Female
Connectors | Quantity: 30
Use: Electronics Assembly
Connections
Mini Jumpers | Quantity: 6
Use: DC Motor Driver
Jumpers
M3x55mm Spacers
Quantity: 4
Use: For mounting Base
Board on BOT Chassis
M3x12mm Spacers
Quantity: 12
Use: For mounting Kits on
the Base Board
3x8mm Screws
Quantity: 32
Use: Mounting Screws
Wire Cutter
Quantity: 1
Use: For Nipping and Stripping
Wires
Electrical tape
Quantity: 1
Use: For Wiring Insulation
Double Sided tape
Quantity: 1
Use: For mounting IR Receiver

© TU Technology Uncorked LLP. All Rights Reserved.
P a g e | 13
3.3 Constructing the BOT
Build the mechanical structure of your BOT using the YouTube Construction video:
https://www.youtube.com/watch?v=oWJuhIX7fiM
Integrate the electronics structure of your BOT using the YouTube Construction video:
https://www.youtube.com/watch?v=HEN6-qMkf6c
3.3.1 Integrating the Base Board Electronics
The steps involved in the assembling of kits on base board are as follows:
STEP 1: Mount the M3x12mm spacers on the base-board using 3x8mm screws. Use the small and
handy screwdriver Taparia 932 for this task.
STEP 2: Mount the two DC Motor Driver kits on the Base Board over their designated areas such that
J1 and J2 PBT connectors on the kit face the ARM AND GRIPPER SIDE of the Baseboard. Screw
the kits using spacer screws.
Kit Mounting Holes
Mount M3x12mm Spacers
on These Holes
Figure 9: Kit Mounting Holes
TU048 DC Motor Driver Kit
Orient & Mount as Shown
TU048 DC Motor Driver Kit
Orient & Mount as Shown
Figure 10: Mounting DC Motor
Drivers on Base Board

© TU Technology Uncorked LLP. All Rights Reserved.
P a g e | 14
STEP 3: Mount the 12V to 5V converter Kit on the baseboard over its designated space such that 12V
DC Terminal Connector on the kit is mounted over Wire Slot WS1 on the Base Board. The Heat Sink
should be facing the DC Motor Driver kits. Screw the kit using spacer screws.
STEP 4: Align the Micro-controller Gum-strip R8C/1B connector and the respective slots on the
Baseboard and press fit the kit.
STEP 5: Place the IR receiver on the space provided on the board facing towards the rear side using
double-sided tape such that J7 Connector Slot on the IR kit face the REAR SIDE of the Baseboard.
Figure 11: Mounting 12V to 5V Converter Kit
TU003 R8C1B Gumstrip
Orient & Mount as Shown
Figure 12: Mounting MCU Gumstrip
Figure 13: Mounting IR Recvr

© TU Technology Uncorked LLP. All Rights Reserved.
P a g e | 15
STEP 6: With all the kits mounted, we are now ready to make physical connections between the kits.
Starting with 12V connections: The battery supply is fed to J18 from where it is fed to connectors J15,
J16 and J17. Connect 12v, GND terminals of J15 (near WS1) with +V, GND terminals of 12V to 5V
Converter Kit. Use wire slots WS1 and WS2 to route the wiring from under the baseboard and avoid
the clutter on baseboard top. Connect 12v, GND terminals of J16 to respective terminals of J3
connector of Left side DC Motor Driver Kit. Repeat the same connections between J17 and J3
connector of Right side DC Motor Driver Kit. For ease of debugging and identification use RED wire for
12V and BLACK for GND connections.
STEP 7: Making Motor Control connections: The motor control signals for FORWARD and REVERSE
locomotion of the Robot are routed through MCU Gumstrip and made available on connector J13 on
the Baseboard. Use the 4-wire Female to Female connector cable to connect the 2BI, 1BI, 2AI, 2BI
terminals to the corresponding terminals of connector J7 on the Left Side DC Motor Driver.
Similarly, motor control signals for the Robot ARM and Gripper are routed through MCU Gumstrip and
made available on connector J14 on the Baseboard. Use the 4-wire Female to Female connector
cable to connect the 2BI, 1BI, 2AI, 2BI terminals to the corresponding terminals of connector J7 on the
Right Side DC Motor Driver.
12V
GND
Figure 14: 12V/GND Connections
Figure 15: Motor Control Connections

© TU Technology Uncorked LLP. All Rights Reserved.
P a g e | 16
Mounting Holes
Mount Base-Board on
Robot Chassis Through
These Holes
STEP 8: Making 5V connections: 5V and GND supply can be tapped through connectors J1, J2, J3,
and J4 on the baseboard. 5V is generated on the 12V to 5V Converter Kit. Connect the +5V, GND
terminals of this kit to any pair of VCC, GND terminals on J3 connector on the baseboard using
Female to Female Jumper wires. Similarly, use J1 VCC, GND terminals to feed 5V and GND to
connector J4 of Right Side DC Motor Driver Kit. Also connect VCC, GND (Connector J3) of IR Recvr
Module with corresponding terminals of connector J4 on Baseboard. For ease of debugging and
identification use Orange wire for 5V and BLACK for GND connections.
STEP 9: Connecting IR Receiver Module: Connect IR out terminal (Connector J3) of IR Recvr. Module
to any terminal of Baseboard Connector J5 using Female to Female Jumper wires. This completes all
the wiring connections on the Baseboard.
STEP 10:Mount the Base board on the mechanical chassis using four M3x55mm Spacers and 8
3x8mm screws. Use the small and handy screwdriver Taparia 932 for this task. Ensure that the side of
the board with legend ARM AND GRIPPER SIDE is placed adjacent to the Robot Arm.
GND
GND
5V
Figure 16: Making 5V/GND Connections
Figure 17: Mounting Baseboard on Chassis

© TU Technology Uncorked LLP. All Rights Reserved.
P a g e | 17
STEP 11: Connecting the Battery: Now place the battery below the baseboard using double sided
tape carefully.
Use a 2-wire male pin type connector with other ends stripped. Insert one pin to the negative terminal
of the battery (BLACK wire) and the stripped end to the GND terminal of baseboard connector J18.
Insert the other pin in the positive terminal of the battery connector and connect the stripped end to
any one of the wires attached to ON/OFF switch PS1 on the baseboard. Insulate and strengthen this
joint using insulation tape provided in the box.
Now connect the other open wire attached to PS1 switch to 12V terminal of connector J18 on the
baseboard. Now battery connections to the BOT are complete.
STEP 12: Connecting the ARM and GRIPPER Motors: Connect the RED wire attached to the
GRIPPER Motor to terminal 2A of connector J1 of right side DC motor driver kit. Similarly, connect
BLACK wire of this motor to terminal 1A of J1. Now, connect the RED wire attached to the ARM Motor
to terminal 2A of connector J2 of right side DC motor driver kit. Similarly, connect BLACK wire of this
motor to terminal 1A of J2.
STEP 13: Preparing the ROBOT LOCOMOTION Motors: Turn the BOT upside down so that you can
access the 4 motors mounted underneath the chassis. Join the RED wires of the Motors below the
Right Side Wheels. Add a multi-strand wire extender to this joint and secure the three wires with
insulation tape. Repeat the same procedure with BLACK wires of the motors. Similarly, prepare the
motors under the LEFT side wheels for connections.
STEP 14: Connecting the ROBOT LOCOMOTION Motors: Pass the RED and BLACK wire extenders
of the Right side motors from the central round hole in the chassis and connect them to terminals 1B
and 2B of connector J2 of right side Motor Driver respectively.
Now, Pass the RED and BLACK wire extenders of the Left side motors from the central round hole in
the chassis and connect them to terminals 1A and 2A of connector J1 of right side Motor Driver
respectively
STEP 15: Now do a final check of all the connections and make sure that they are secure and tight.
Switch the ON/OFF switch PS1 to check that the BOT is getting powered ON and OFF.
STEP 16: Connecting the Battery Charging POD: Take 2-wire Male pin header wire strip. Strip their
open ends and connect them to the RED and BLACK wires of the charging POD respectively. TAG the
male headers as Positive and Negative header. Whenever the battery needs to be charged, connect
the headers to the battery connector, ensuring that the positive header is connected to positive battery
terminal and vice versa. Whenever, the battery needs to be charged, connect the AC-DC adapter
provided in the box to the charging POD and plug in to AC mains. Charge the battery when it is fully
depleted. Charge it for typically 2- 3 hours.
ON/OFF SWITCH
BATTERY CHARGING POD
Figure 18: Battery
Charging

© TU Technology Uncorked LLP. All Rights Reserved.
P a g e | 18
STEP 17: Keep the BOT in an open area. Pull out the plastic sheet from the IR Remote so that its
battery slides into the power slot. Now you are ready to operate your BoT.
Figure 19: Fully Assembled Octamotion BOT
Table of contents
Popular Robotics manuals by other brands
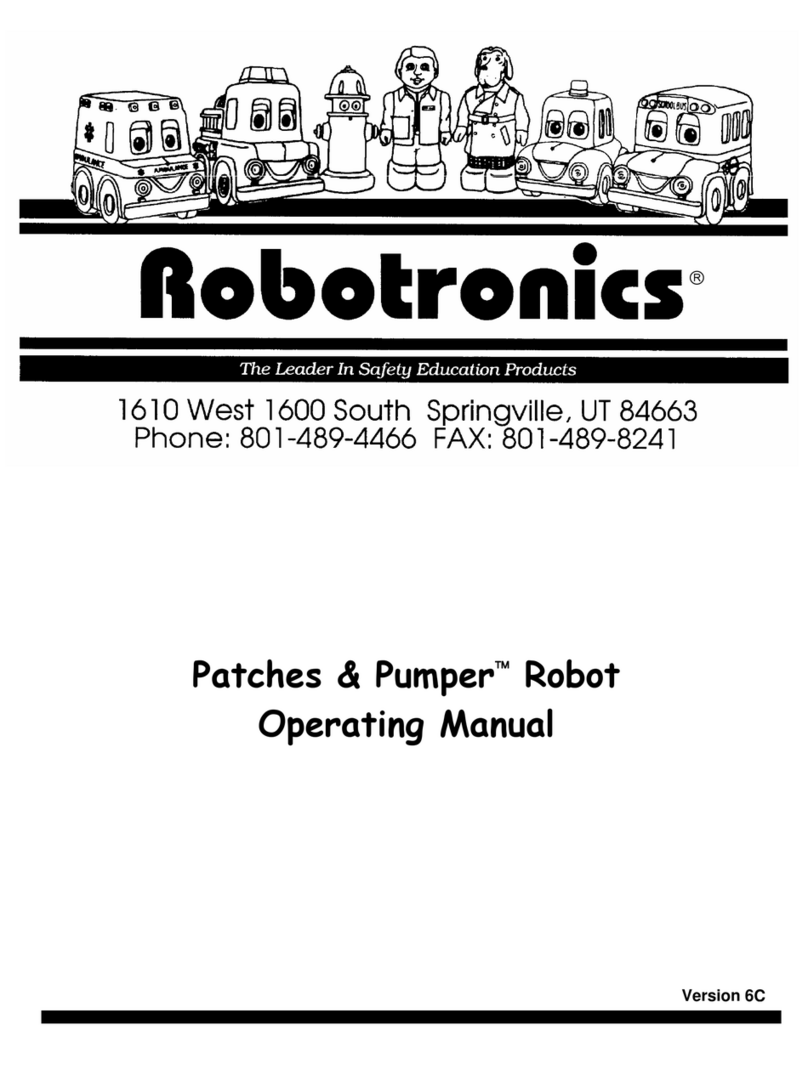
Robotronics
Robotronics Patches & Pumper operating manual
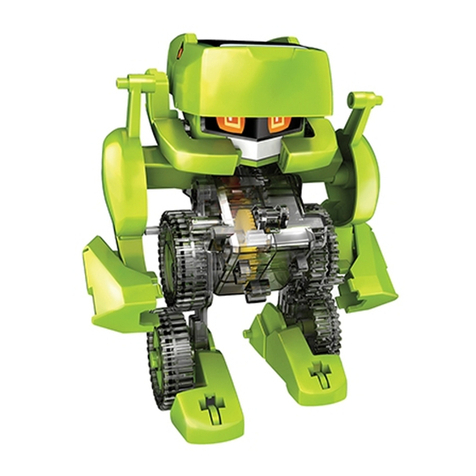
TEACH TECH
TEACH TECH TTG-617 Assembly & instruction manual
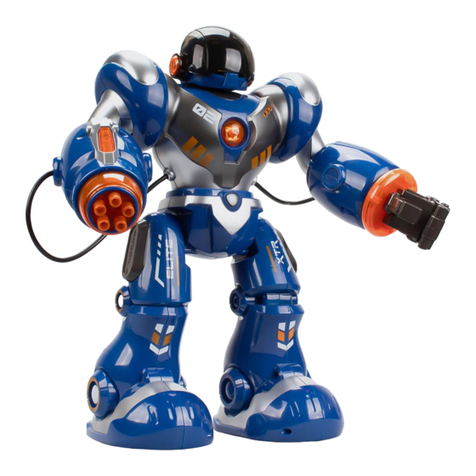
Xtrem Bots
Xtrem Bots ELITE TROOPER instruction manual
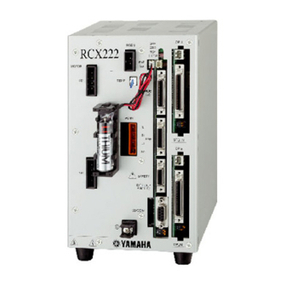
Yamaha
Yamaha RCX222 user manual
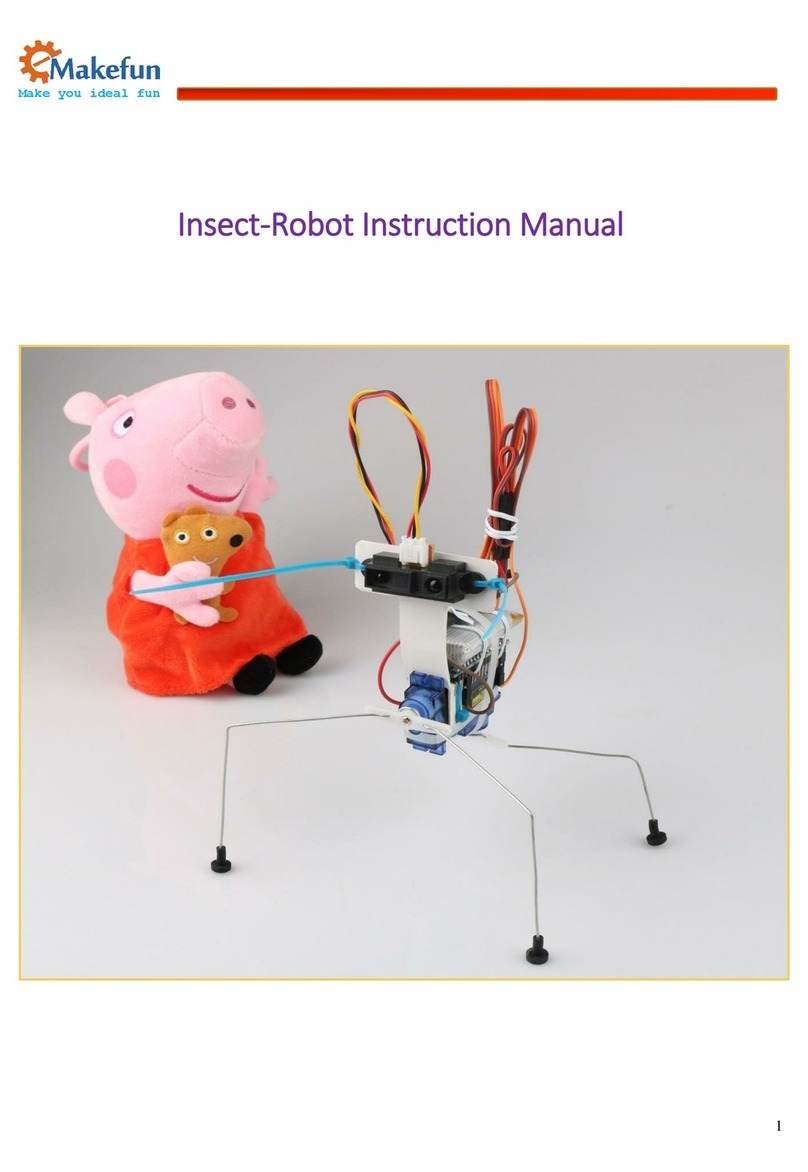
Makefun
Makefun Insect-Robot instruction manual

Innovati
Innovati Mini Hexapodinno 18-DOF instruction manual