Tecumseh FH2 Operating and maintenance manual

2
FH2Long Notice
03/2020
Please read this notice in full.
The implementation, operation, maintenance and end-of-life management of products involves following strict rules in accordance
with existing standards and best practices. Current standards and legislation should be respected in the country where the
compressor is installed, and the rules of good refrigeration and electrical installation practice should be applied.
These instructions cover the main points of the ISO Standards. The EN guidelines and standards described below prevail in the
European Union.
1. Statements of compliance and incorporation
These refrigeration compressors are designed to be incorporated into machines in accordance with the Machinery Directive
2006/42/EC. They comply with the Low voltage Directive 2014/35/EU and the PED Directive 2014/68/EU.
Their commissioning is only permitted if they have been assembled in accordance with the following instructions, and if the machines
comply with existing regulations.
In case of the use of A2L-classified refrigerants following ISO 817, follow the safety rules specific to flammable fluids. The compressors
will be installed, maintained in accordance with ISO 5149 or EN 378 or EN60335-2 safety standards. FH2 compressors with A2L
refrigerants requiring above compliance are with designation FH****N for R1234yf, FH**** P for R454C and R455A.
2. Safety and risks associated with the implementation and use of flammable refrigerants, classified as Category A2L
2.1. Flammable refrigerants:
R1234yf is a pure hydrofluoro olefin (HFO) fluid.
R455A is a non-azeotropic mixture of hydrofluoro olefin (HFO), hydrofluorocarbon (HFC) and natural fluid composed of R1234yf
(75.5%), R32 (21.5%) and R744 (3%)
R454C is a non-azeotropic mixture of hydrofluoro olefin (HFO) and hydrofluorocarbon (HFC) composed of R1234yf (78.5%) and R32
(21.5%)
R1234yf, R455A, and R454C fluids are heavier than air so they will naturally accumulate at the floor or bottom of the installation in
the absence of ventilation .
Their main features are:
Refrigerant R1234yf R455A R454C
Security class A2L A2L A2L
Lower flammability limit under
normal conditions in volume/volume
according to ISO 817
6.2% 11.8% 6.2%
Lower flammability limit under
normal conditions 0.289 kg/m30.431 kg/m3
0.293 kg/m3
Practical limit
20% LFL 57.8 g/m386 g/m3
59 g/m3
Self-inflammation temperature
(following ISO 817) 405°C ND (473°C supplier
data)
ND (> 400°C supplier
data)

3
FH2Long Notice
03/2020
Never use the product without referring to the Safety Data Sheet (S.D.S.) provided by refrigerant supplier/manufacturer.
2.2. Scope of application of standards for refrigeration systems using flammable fluids
Where authorised by local regulations and provided that the location is suitable, the maximum Refrigerant charge quantity for
hermetically sealed compressors running on R1234yf, R455A, R454C are defined in the table below:
Refrigerant
following EN 60335-2
series standards
(except EN 60335-2-40)
following
CEI 60335-2-89
standards
following
EN 378-1: 2017*
R1234yf 150g 1200g 1700g
R455A 150g 1200g 2500g
R454C 150g 1200g 1600g
*For higher refrigerant charge Quantities, please refer to the requirements of Standard EN 378-1
2.3. Preventing the formation of potentially explosive zones
The use of flammable fluids may present a risk of ignition in the event of a leak. It is therefore important to ensure that the refrigeration
system design and adequate compressor ventilation to avoid risk of formation of an explosive zone.
2.4. Staff Qualification
It is essential that Standard EN 378-3 is observed during installation and Standard EN 378-4 during maintenance works.
To maintain and repair the installations, staff must be authorised to handle refrigerants and correctly trained in the handling of
flammable refrigerants in order to avoid the risk of the formation of an explosive atmosphere.
Consequently, staff must know the tools, the transportation procedure for the compressor and refrigerant, and the safety precautions
and regulations that apply to maintenance and repair work. Do-not use ignition sources while handling flammable refrigerants.
2.5. Protection of the compressor's electric terminal
The disintegration of the insulation (glass bead) on a compressor electrical terminal due to physical shock or over heating can result
in terminal venting . Oil and refrigerant can spray out of the compressor if one of the terminal pins is ejected from the hermetic
terminal, this mixture can be ignited by electricity/ spark and produce flames that can lead to serious burns or death. Any accidental
damage to the electrical terminal during compressor’s installation or operation must be scrapped.
To reduce the risk of electrocution or serious burns or death from terminal venting with ignition never energize the system unless
the compressor’s protective terminal cover is securely fastened and the compressor is properly connected to ground.
Also, especially when using flammable refrigerants, Tecumseh advocates the use of a security system to protect users, installers and
installation. The system will be able to detect a spike in intensity that could melt the insulation (the phenomenon of "terminal
venting"), and will thereby cut off the compressor's power supply.
Since the compressor is not equipped with protection in the case of an external fire, it is appropriate for the equipment manufacturer
to secure the installation to prevent a fire. Adequate means of purging and protection against exceeding permissible limits (see
conditions on the PED label) must be provided. Compressors should not be installed in a corrosive or dusty environment.

4
FH2Long Notice
03/2020
3. Specifications - Marking compressors in the FH2range
3.1. Identification label and designation:
FH****N, FH****P compressors are CATEGORY II certified under the 2014/68/EU PED Pressure Equipment Directive.
(Reference free internal volume: 6.16L)
Labels contain the following information:
Information in agreement with EN 378-2:
Ref. Designation
a Voltage
b Frequency
c Number of phases
d Bill of Material
e Refrigerant
f Model Number
g Serial number
h Maximum allowable pressure (*)
i Min/max temperature (*)
j 1.1 * PS (*)
k Registration number of the notified body (*)
l Manufacturing and testing date (*)
m Free volume
FH****P compressors are qualified for R455A and R454C
FH **** N compressors are qualified for R134a and R1234yf.
The Identification label of these compressors has a yellow Flammable
warning logo as shown opposite:
In the case of multi-fluid compressors, the Printed PS pressure = at the pressure of the fluid + binding to TS maxi
Fluids PS (b) PED category
R-404A
20.1
I
R-452A
21
I
R-449A
20.4
I
R-448A
20.4
I
R-455A
21.5
II
R-454C
18.4
II
R-1234yf
10.8
II
R-513A
11.5
I
R-134a
10.9
I

5
FH2Long Notice
03/2020
3.2. Specifications
The housing of the compressors in the ‘FH2’ family is subject to the low pressure of the refrigeration system.
In line with the PED and in order to ensure the best level of quality of its products at all times, Tecumseh tests each compressor on an
assembly line at a pneumatic pressure which is greater than or equal to the requirement 1.1 x PS as per Annex C 1.3.2 of standard NF
EN 14276-1, irrespective of the refrigerant indicated on the identification label and based on the calculation of the most Critical
refrigerant,
For information: 1.1 * PS (46°C sat) = 24 bar rel for R455A.
Additional burst tests are also performed periodically.
4. Transport - handling:
The compressor is charged with oil and nitrogen (0.3 to 0.5 bar) at the final stage of assembly inside the factory. The compressors are
delivered with out refrigerant charged .
For information about compressor delivery, refer to your terms of sale. Check the condition of the equipment compressor at its
reception. (Good exterior appearance, no shock or deformation) especially on the connection terminal.
Do not hold or lift the compressor by the tubes, use its lifting ring intended for this purpose. Refer to our technical documentation to
find out which storage and transport positions are allowed.
The recommendations for transporting refrigeration systems/ appliances loaded with refrigerants are the responsibility of the
respective manufacturer of these refrigeration systems / appliances.
5. Recommendations related to the use and assembly of the compressor in a refrigeration system:
In the case of operating with flammable refrigerants, installation must be designed on the basis of a risk analysis to avoid refrigerant
accumulation in the event of leakage in areas that are potential ignition sources.
-It is recommended to provide a device capable of detecting current taken by compressor in order to prevent sudden surge
in currents that could melt the insulation (“pin venting” phenomenon) on electrical terminal pin of the compressor.
-Provide appropriate protections in line with local regulations to prevent the public, user or anyone with access to the
application from degrading the product.
-Also provide adequate signage for flammable refrigerants on the complete installation, so that the user or anyone with
access to the application is aware of the risks associated with their presence (putting in place standard pictograms preventing
the risk of flammability).
-Establish an appropriate way to alert the user that they need to call on a professional to manipulate the application.
5.1. Maximum allowable pressure
Tecumseh compressors are designed to operate at a maximum ambient temperature of +46°C. Observe and comply with the specific
regulations to optimise the quantity of refrigerant in the installation and never exceed the maximum discharge pressure corresponding
to the maximum condensation temperature of the compressor's operation. The compressor housing should not be subjected to a
temperature below -35°C; the materials used would not guarantee sufficient mechanical characteristics.

6
FH2Long Notice
03/2020
5.2. Expansion element
Tecumseh recommends the use of thermostatic expansion valves.
5.3. Installation for the first commissioning
Tecumseh cannot be held responsible if the installation and maintenance do not comply with the instructions provided in this manual.
Current guidelines and regulations in force in the country where the compressor is installed, and the rules of the art for refrigeration
and electrical connections, must be complied with.
5.4. Location of the compressor and definition of refrigerant charge
5.4.1. Defining the refrigerant charge
The refrigerant charge should not exceed the amount that can be stored under high pressure. To prevent migration of refrigerant
in to the compressor housing during the compressor’s off period/ thermal cycling, or when the refrigerant charge quantity is
greater than 1.5 Kg, Tecumseh recommends the use of a crank case Heater and/or an non-return valve (NRV)on the discharge
pipe line connected to condenser inlet( Scope of supply of NRV lies with the Refrigeration system/ appliance manufacturer) .
The return of liquid during transitional periods will be prevented by Accumulator.
The maximum charge quantity of flammable refrigerants is defined in Annex C of EN 378-1 based on the volume in which the
refrigeration system is installed, its location and its type of occupancy (non-exhaustive).
5.4.2. Location of electrical components that create sparks in the case of the use of A2L flammable fluids
They must be located in a non flammable area. Tecumseh recommends installing them high up, and in a adequately ventilated
area.
5.4.3. Replacing the compressor
Ensure that the compressor should not block the movement of people or opening of doors and shutters.
Ensure that the compressor is mounted on a base or structure that has enough strength to support it’s safe operation. Check that
the compressor level is horizontal and ensure silent blocks are assembled to the mounting leg . Be careful not to block the flow of
air around the electrical components and compressor, to ensure its cooling.
5.5. Brazing, refrigeration connections
As a reminder, Brazing can only be carried out on installations not loaded with refrigerants.
To keep the installation running smoothly, it is advisable to:
- Braze using dry nitrogen and keep any flames away from electrical equipment.
- Insulate the suction line up to the compressor entrance, to avoid condensation.
Cut and shape the tubes carefully, to prevent dust and metal particles from entering the system. Never use a saw. Use a bending tool
adapted to the diameter of the tube to avoid excessive restrictions.
Tecumseh recommends brazed connections instead of Flare and Nut fittings to limit the likelihood of leakage over time. Screwed
fittings on a flat surface using a gasket are acceptable. A leakage check is mandatory before commissioning.

7
FH2Long Notice
03/2020
5.6. Suction and Discharge valve tightening torques
1- SAE tips 1/4'': 7 to 11 Nm
A – Process connection
B – Pressure gauge connection
2- setting needle square 1/4’’ : 6 à 13 Nm
setting needle square 5/16’’ : 30 à 34,5 Nm
3- packing gland nut: 5 à 13 Nm
4- Rotalock connection 1’’1/4- 12UNF : 114 Nm à 126 Nm.
Rotalock connection 1’’-14 UNS : 70 Nm à 85 Nm
Unlock the packing nut before handling the float valve. Then tighten the
packing nut.
5.7. Suspensions
An external suspension set including Silent blocks (Grommets) and spacers (sleeves) come as standard with all Tecumseh compressors.
The role of these silent blocks is to reduce the transmission of vibrations generated by the compressor to the base on which it is
mounted. In order to ensure this function properly, silent blocks should not be constrained. For this, the washer pressing on the spacer
must leave a clearance of 1 to 4 mm from the top of the silent block. In order to not distort the spacer, apply a tightening torque of
between 8 to 13 Nm for the M8 screws.
5.8. Electrical connections
Electrical connections will be made before the refrigeration system is charged with refrigerant.
To preserve the quality of the Tecumseh compressor and the safety of the installation and ensure their proper operation, it is
imperative to:
- Always wire the compressor when it is switched off.
- Validate the compatibility of the installation's power voltage with that of the compressor (see the nameplate).
- Validate the compatibility of the compressor's electrical drawing with that of the installation.
- Size the connecting cables (power, control) according to the characteristics of the installed compressor (see nameplate).
- Protect the power line and install a grounding line.
- Make electrical connections in accordance with the country's current regulations.
- Use the electrical components that come with the compressor, even if others seem acceptable.

8
FH2Long Notice
03/2020
The electric box must always be fixed vertically.
Dimensions
JUNIOR box
SENIOR box
L
125
180
H
206
232
P
82
90
X
91
130
Y
60
65
A
91
154
B
12
12
Assembly drawing for Protective cover for FH2Compressors
5.9. Circuit sealing
Before Charging with refrigerant, systematically search for leaks on all fittings, and seal them if necessary.
5.10. Evacuation

9
FH2Long Notice
03/2020
Evacuate the installation to reach a residual pressure of about 200 micrometres of mercury (0.27 mbar), guaranteeing a good quality
of vacuum. It is advisable to drain the HP and BP circuits simultaneously in order to reduce the operation time and ensure an identical
level of vacuum throughout the circuit.
6. Refrigerant charge, powering up and maintenance:
If the following manipulations are performed in potentially explosive atmospheres, Tecumseh recommends referring to Standard EN
378. Part 4 prescribes the general safety guidelines, Annex E provides guidelines for interventions in equipment using flammable
refrigerants.
General recommendations:
The electrical boxes will be properly installed and closed before charging the refrigerant and switching on installation.
HFO levels in the air will be monitored throughout the whole refrigerant charge and maintenance period.
Leak detection equipment will be calibrated to 20% of the LFL of the refrigerant in accordance with the EN 378-4 standard.
The work area will be ventilated throughout the procedure.
6.1. Coolant charge
The provisions in Parts 2, 3 and 4 of EN 378 must apply to prevent the risk of refrigerant emission during refrigeration system filling
and emptying operations.
Limit the refrigerant load so that the pressures are in the operating window defined by Tecumseh.
Never start the compressor if the vacuum is not broken in HP and BP.
The components will be grounded before starting the refrigerant charge.
Load the installation only with the refrigerant or one of the refrigerants for which the compressor was designed (see nameplate).
The refrigerant charge will always be in liquid form, to keep the mixture in the right place.
- Do not add any additives or dyes.
6.2. Risk of refrigerant Over Charge
If the main parts of the compressor are submerged due to excess refrigerant charge, this can cause the compressor housing to burst.
Immersion of the crank case, connecting rod, piston and cylinder in the liquid creates a hydraulic blockage preventing the compressor
from starting: this is therefore a blocked rotor situation. If, for some reason, the compressor protector does not intervene quickly
enough, a high current in the motor winding will create a rapid rise in temperature. This will cause the liquid to vaporise and the
pressure in the compressor housing to increase rapidly.
As an example of what not to do when charging a system with refrigerant, never leave the charging cylinder connected to the system,
even if the valve of the cylinder or that of the "manifold" is closed. If one of these valves leaks slightly, the system will be Over Charged
with the risks mentioned above.
6.3. Checks when commissioning
- Calibrate electrical protective devices, adjust the set/cut points of the regulatory and safety devices.
- Fully open the service valves.
- Check the operation of the oil heater, if present.
Tecumseh compressors are protected by an external or internal over load protector , the principle of which is based on a
temperature/current combination. Like any protective device, it is normal for the compressor to trip on overload protector when it is
operating outside the Tecumseh’s recommended application window.

10
FH2Long Notice
03/2020
When operating conditions are stabilised, do the following checks:
-Tension(Voltage) and intensity ( Current) absorbed by the compressor;
-HP and BP pressures from the installation;
-Overheating, undercooling, return gas temperature, discharge temperature;
-Search for leaks;
-Carry out a general inspection of the installation (cleanliness of installation, abnormal noise, etc.). Visually inspect the
refrigeration system (for example, according to the list listed in Annex G of EN378-2).
For installations operating with a flammable refrigerant, check if the leak detection equipment is working properly.
Do not add oil unless the pipes exceed 20 m; in this case, use the oil recommended by Tecumseh.
6.4. Maintenance
Tecumseh recommends securing the maintenance area in accordance with EN 378 Part 4
Below is a non-exhaustive list of recommendations:
-Obtain a permit for high-temperature work (if necessary);
-Ensure that no flammable material is stored in the work area and that there are no sparks in the work area;
-Switch off electrical appliances;
-Keep heat sources away to avoid explosions;
-If a heat source is present in the workplace, make sure a fire extinguisher is available;
-Ensure that the work area is properly ventilated, before intervening on the refrigeration system or before welding or tender
brazing work;
-Mark the work area to prevent entry of unqualified people;
-Ensure that the leak detection system used is spark-proof, secured appropriately or inherently safe
-Ensure that all maintenance personnel have been trained.
Wherever possible, the refrigeration system operating with a refrigerant classified as an A2L category will be transported to a
workshop authorized and compliant to do its maintenance.
Check that the pressure of the refrigeration system will not be a danger factor during the intervention (projection of parts, refrigerant
etc.). The compressor can reach temperatures above 120°C in operation. Do not intervene in the compressor without protection.
IMPORTANT : If the detection system preventing sudden surge in current that could melt the insulation (pin venting) has tripped,
do not reset it. Replace the compressor following installation and commissioning recommendations (see Section 5).
6.4.1. Recovery of flammable refrigerants
-Use a recovery plant suitable for flammable refrigerants
-Identify the refrigerant in the cylinder and affix the flammability logo
-Do not mix refrigerants together.
6.4.2. Inerting the refrigeration system and precautions before soldering
-Ensure that a fire extinguisher is present nearby,
-Inert the system with nitrogen without oxygen (or air),
-The flow will be ventilated preferably outdoors.
6.4.3. Opening of the refrigeration system and replacement of components
IMPORTANT : Soldering operation is prohibited on installations / refrigeration system charged with a flammable refrigerant .
More generally, it is imperative to prohibit any source of ignition (sparks, flames, hot springs) near the circuit.

11
FH2Long Notice
03/2020
After replacing components, crimped connections are an alternative to soldering.
6.4.4. Evacuation
For flammable refrigerants, check that the vacuum pump contactor is the only source of ignition.
Make sure the vacuum pump does not blow near an ignition source (empty pump switch, etc.).
An evacuation outside is recommended.
6.4.5. Replacing electrical components
-The electrical cabinets will be properly closed before refrigerant charging and restarting installation.
-Replace defective electrical components with the same parts as recommended by the manufacturer to ensure
continuity of installation safety. For electrical components of compressors please use Tecumseh’s original spare parts.
-Do not move electrical components.
Check regularly
-security and regulatory bodies;
-the states of the electrical and refrigeration connections (retightening, oxidation, etc.);
-the operating conditions;
-the compressor attachments on its support;
-how the oil heater works.
Look for leaks once a year, or according to local regulations.
Signage
The refrigerant used and its mass must be labelled, whatever they may be.
In the case of a fluid classified A2L, the flammability logo will be visible and readable.
6.5. End of life of the product
Fluorinated refrigerants will be recovered as imposed by the F-Gas regulation in the European Union.
Tecumseh also advises recycling the compressor oil and the compressor itself.
7. Warranty
For information on the compressor warranty, refer to the terms and conditions of sale.
In order to be able to continuously improve these products, Tecumseh reserves the right to modify these instructions without notice.
Other manuals for FH2
1
Other Tecumseh Compressor manuals
Popular Compressor manuals by other brands
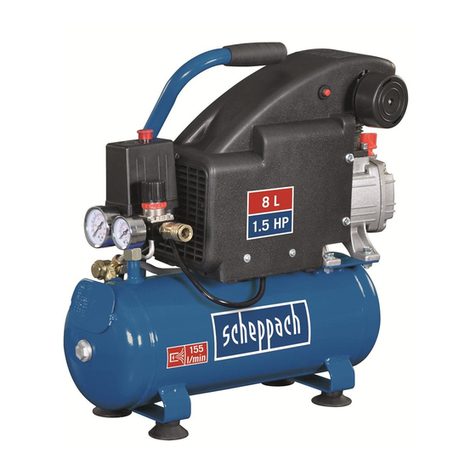
Scheppach
Scheppach HC08 Translation of original instruction manual
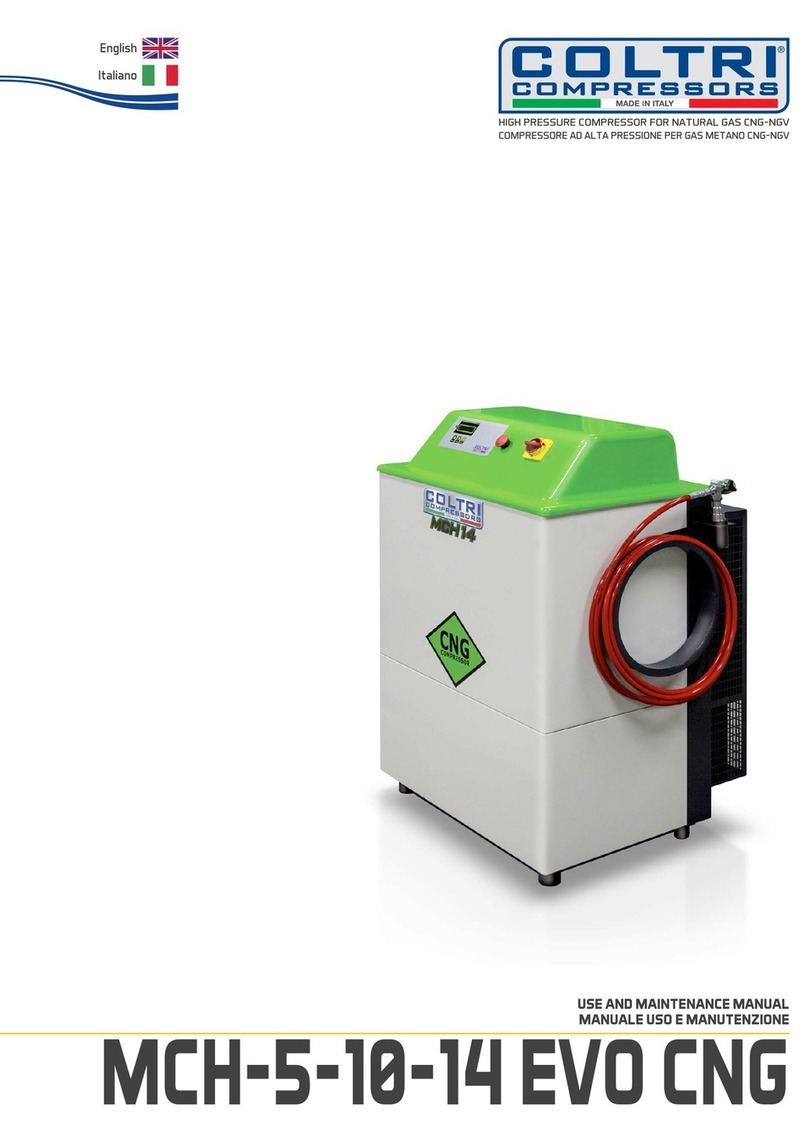
COLTRI
COLTRI MCH-5-10-14 EVO CNG Use and maintenance manual
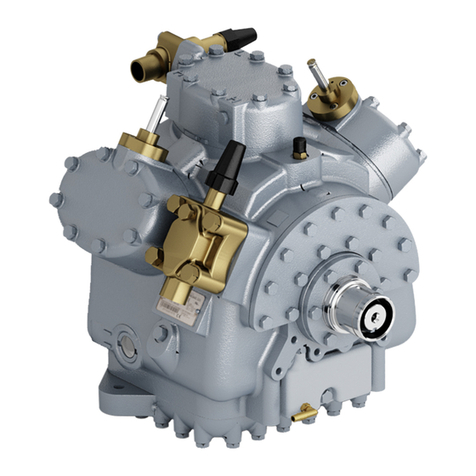
Carrier
Carrier TRANSICOLD 05G Operation and service
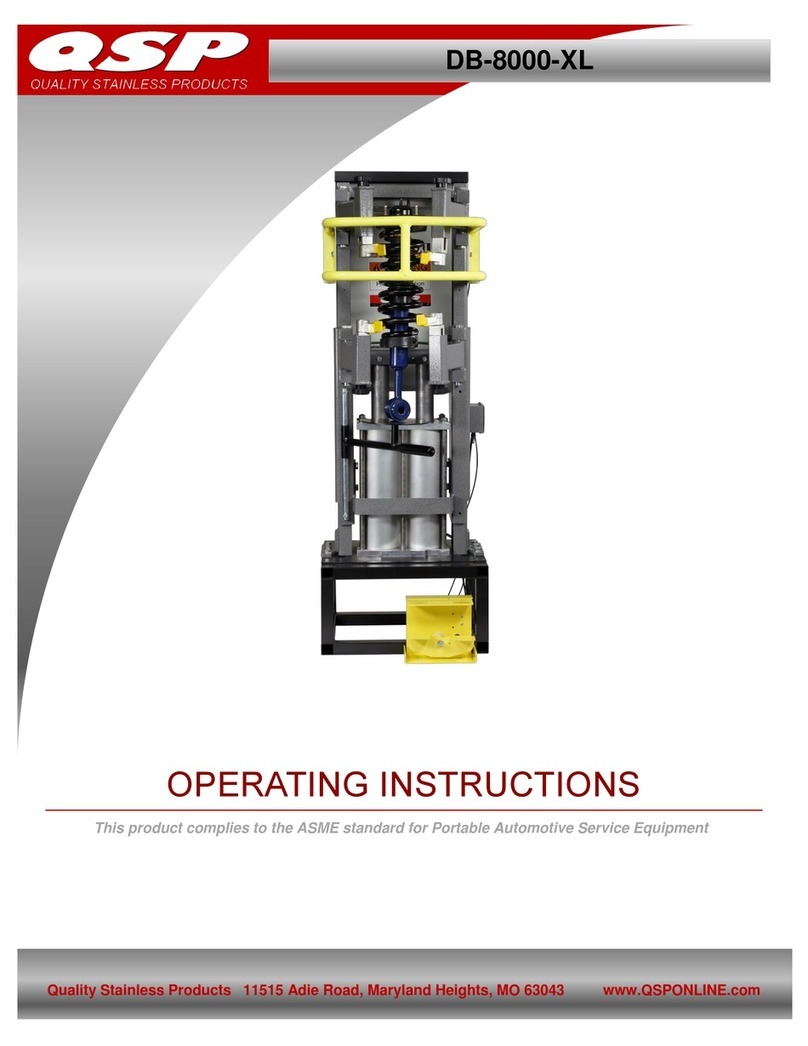
QSP
QSP DB-8000-XL operating instructions

Panasonic
Panasonic Matsushita SD43C77JBU6 Specification sheet
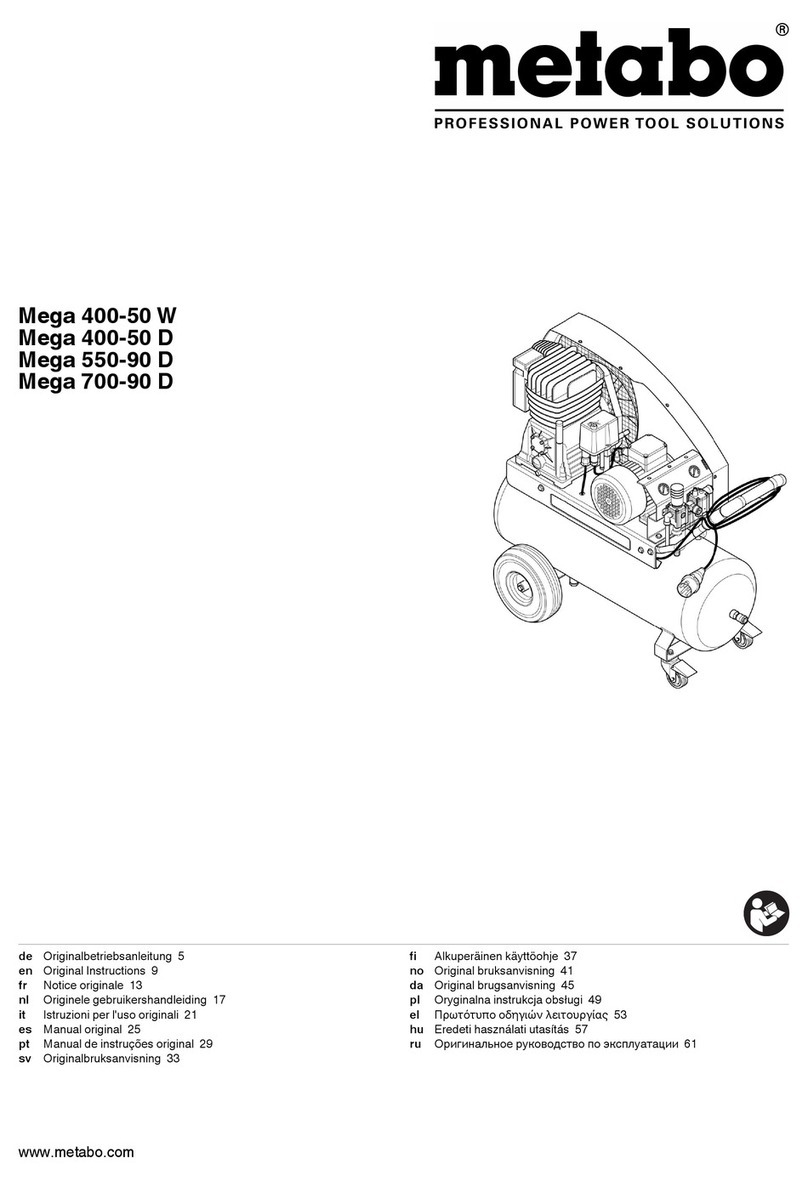
Metabo
Metabo Mega 400-50 D Original instructions

UK Sound
UK Sound 176 user manual
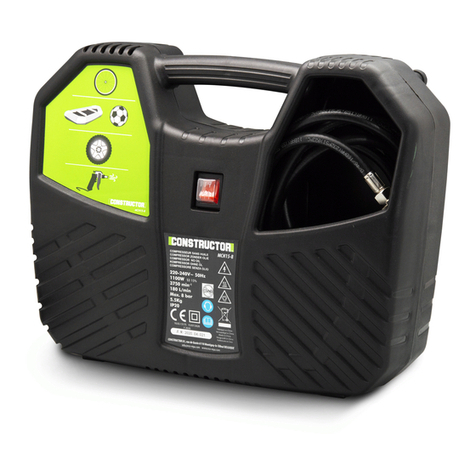
Constructor
Constructor MCH15-8 Operation and safety notes
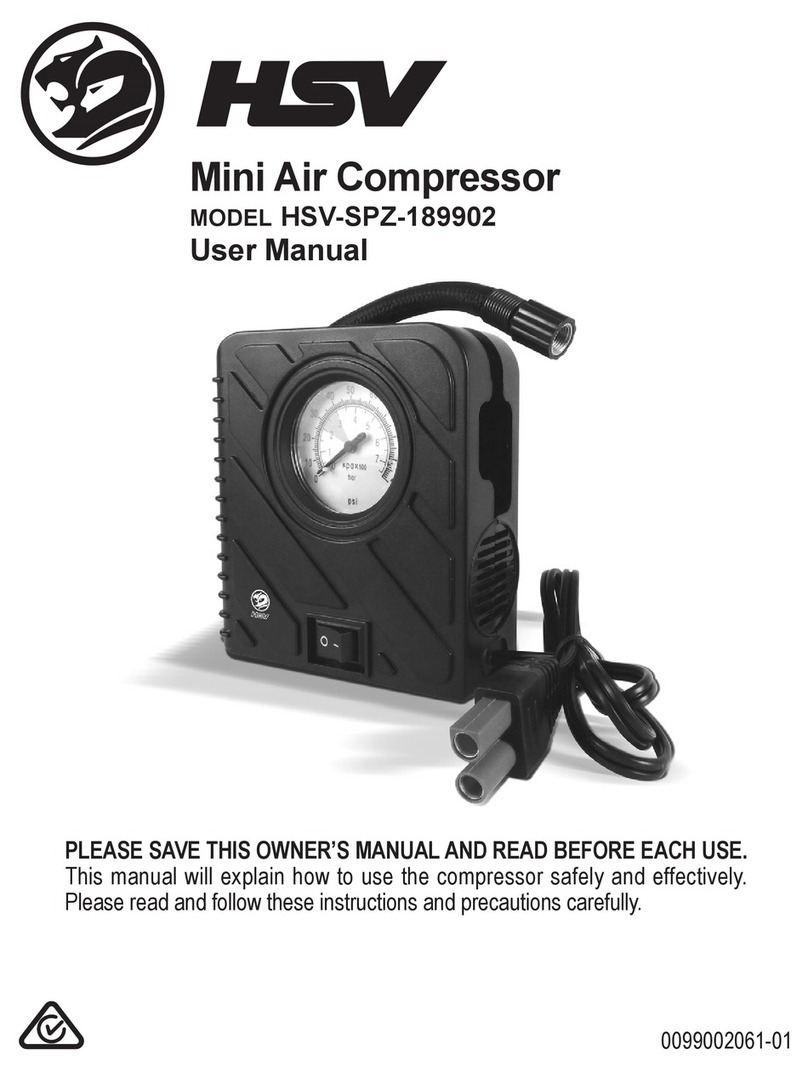
HSV
HSV HSV-SPZ-189902 user manual
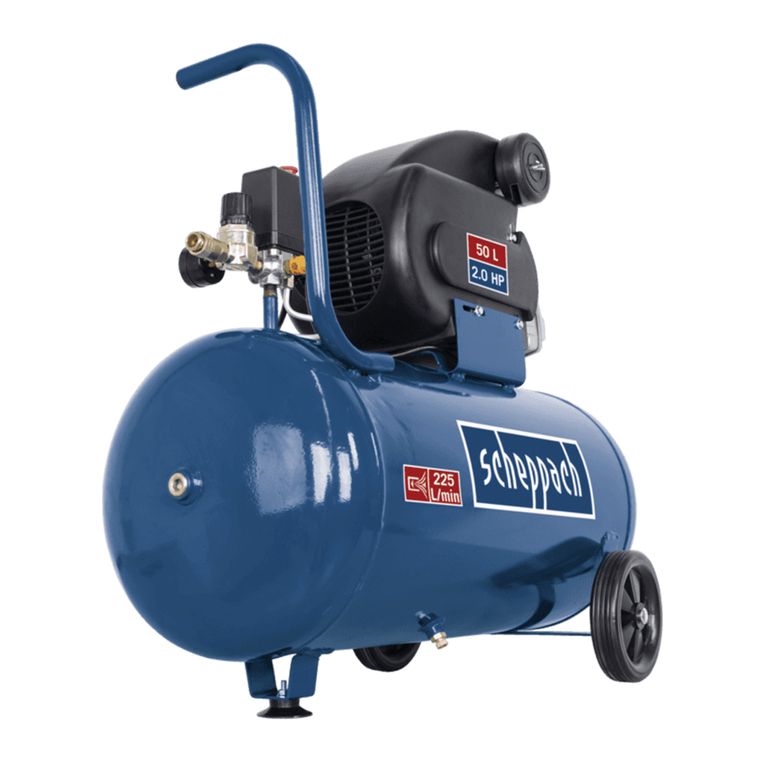
Scheppach
Scheppach HC60 instruction manual
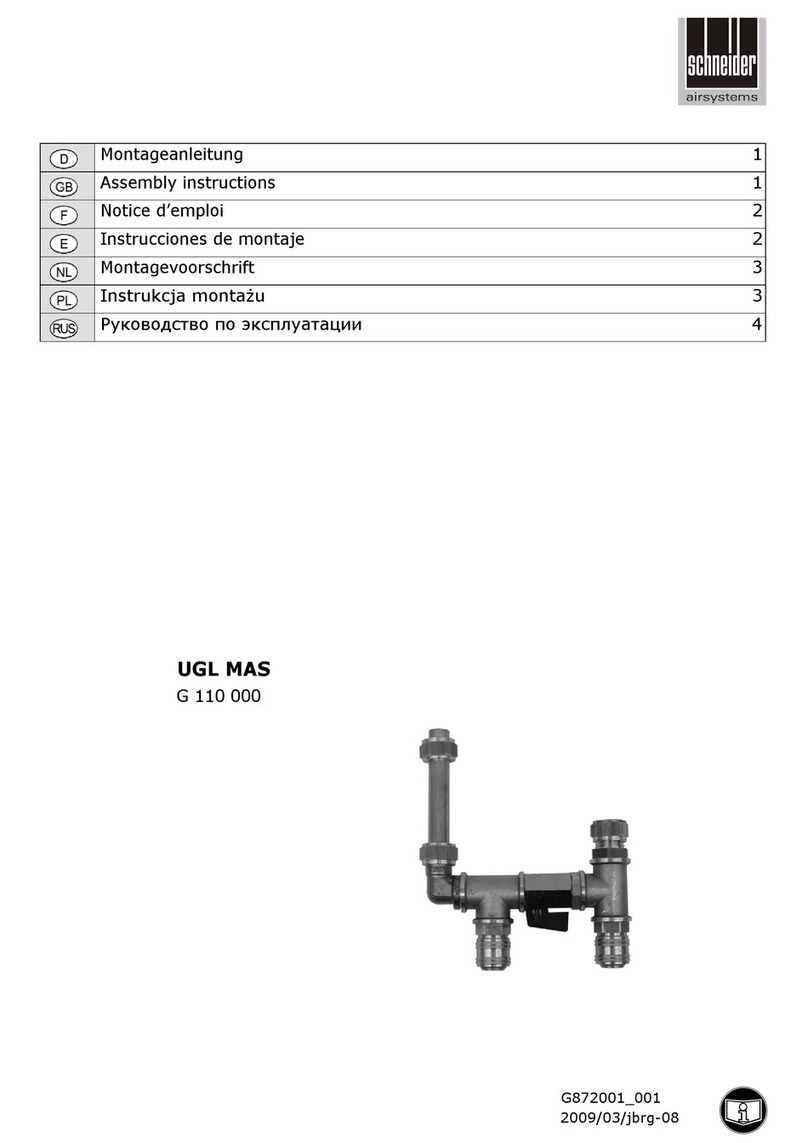
Schneider Airsystems
Schneider Airsystems UGL MAS Assembly instructions
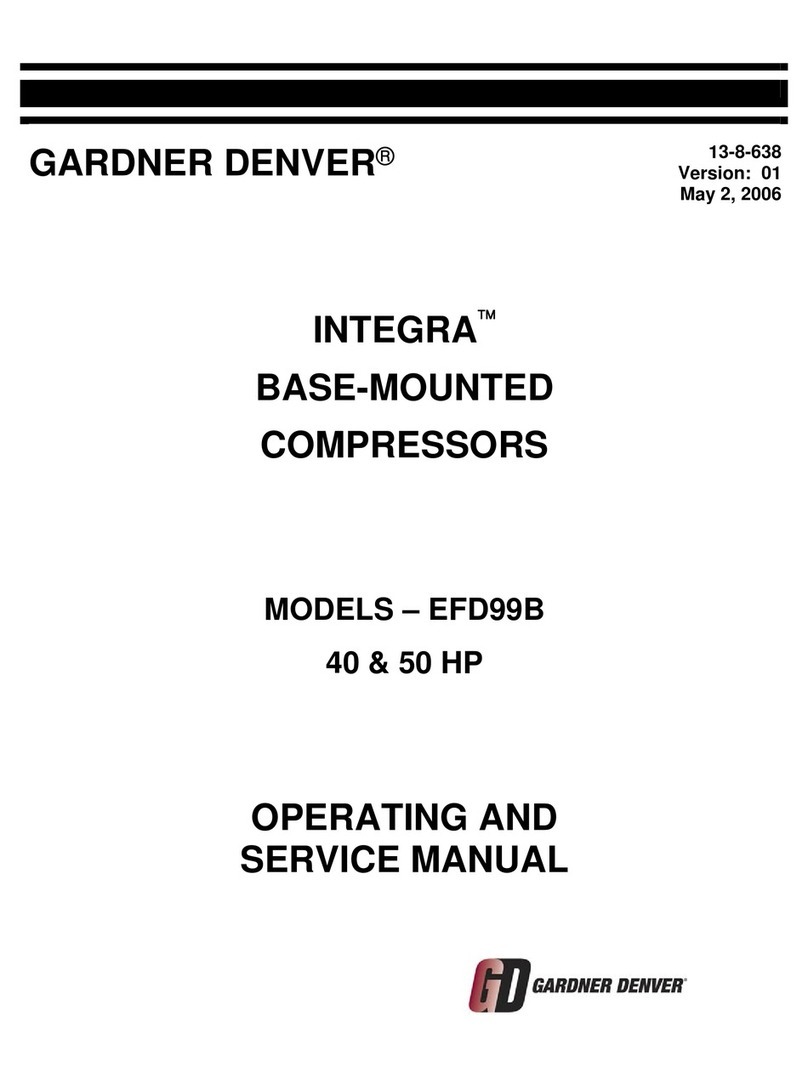
Gardner Denver
Gardner Denver INTEGRA EFD99B Operating and service manual