Tiger CSS User manual

www.tigerlifting.com
Instruction Guide Tiger CSS En 202201 v2.0
- PLEASE PASS ONTO OPERATOR
Sticker here

www.tigerlifting.com
Page 1 of 14
Instruction Guide Tiger CSS En 202201 v2.0
MUST READ BEFORE USE
1. It is important that this manual is read and fully understood and that all instructions are followed before
using the Tiger product.
2. Inspect the product for any damage or wear before use. Do not use the product if it is not in good working
order.
3. The product must be operated, inspected, maintained and repaired by a competently trained person in
accordance with applicable safety codes and regulations.
4. Do not use the machine to lift, support or transport people in any way.
5. Do not lift loads over or near people.
6. Never work under or near hoisted loads.
7. The product is for manual operation only. Do not attempt to use a motorized mechanical device to operate
the product.
8. Do not use the product in explosive environments unless an ATEX version has been supplied.
9. It is the responsibility of the operator to exercise caution, use good practice, common sense and be familiar
with proper rigging techniques.
10. Improper use could result in death or serious injury.
11. The supplier takes no responsibility for any form of consequential loss or damage as the result of
unauthorised repair or use of spare part other than those issued on behalf of the manufacturer/supplier.
Contents:
1.
Safety Information
1
6.
Manufacturer Testing and Verification
10
2.
Function/Operation
3
7.
Technical Data
10
3.
Inspection
5
8.
Exploded Diagram
11
4.
Maintenance
9
9.
Product Warranty and Warnings
12
5.
Transport, Storage, Decommissioning and
Disposal
9
For details of the full Tiger product range visit our website: www.tigerlifting.com
Due to our policy of continual product development, dimensions, weights and specifications may change without prior notice.
© Copyright Tiger Lifting UK Limited. No part of this manual shall be reproduced, transmitted, transcribed, translated into any language human or
electronic, stored in any electronic retrieval system, in any form without the written permission of Tiger Lifting UK Limited, Morpeth, UK
1. Safety Information
The operating company is responsible for the proper and professional instruction of the operating personnel. The personnel
responsible for operation, maintenance or repair of the product must read, understand and follow these operating
instructions. These instructions are intended to make the user familiar with the product and enable them to use it to the full
extent of its intended capabilities.
The operating instructions must always be available at the place where the product is operated. Apart from the operating
instructions and the accident prevention act valid for the respective country and area where the product is used, statutory
regulations and procedures along with the commonly accepted regulations for safe and professional work must also be
adhered to. The indicated protective measures will only provide the necessary safety if the product is operated correctly and
installed and/or maintained according to the instructions. The operating company must be committed to ensure safe and
trouble-free operation of the product.

www.tigerlifting.com
Page 2 of 14
Instruction Guide Tiger CSS En 202201 v2.0
Health and Safety at Work
All equipment must be maintained and tested to meet relevant statutory regulations. It is the responsibility of every company
to ensure that their employees have been fully and properly trained in the safe operation of their equipment.
Equipment Labelling
The identification stamping details the product type, model, manufacturer, year of manufacture, maximum working load limit
(WLL), serial number and the jaw range. The CE marking indicates compliance with the essential health and safety
requirements of the Machinery Directive 2006/42/EC. Other international standards that the unit conforms to may be shown.
Safety Instructions
Always select the correct size clamp for the job, determine the weight of the plate to be lifted. Plate thickness must be
within the grip range of the clamp.
Always use slings correctly. Pay special attention to the correlation between the lifting angle and the rated load. Use within
specified angles.
Always protect the surfaces of the cam and pad from weld spatters.
Always store and handle clamps correctly.
Always inspect clamps before use and before placing into storage.
Always remove dirt, rust, paint, grease, oil and any other foreign matter from the surface of the steel plate before clamping.
Always use genuine parts when repairing clamps.
Never allow the operator’s attention to be diverted when operating clamps and never leave the suspended load
unattended.
Never use a steel lifting clamp on material other than steel.
Never weld work pieces being lifted by clamp.
Never modify clamp by gas cutting or welding
Never use clamps for lifting high-tensile steel (over 300 HB) or soft steel (under 80 HB)
Never operate clamps unless the load is properly centred.
Never vertically lift material that tapers down to the edge.
Never exceed working load limit shown on clamp.
Never use defective clamps.
Never use the clamp with stainless steel, lead or copper material.
Never over torque the axle.
Never return damaged clamps to storage.
Never lift a plate/object that is not fully engaged with the clamping jaws.
Never lift loads that are not balanced, and the holding action is not secure.
Never lift more than one plate at a time.
Never Use the clamp in temperatures below -20oC or above 150oC
Never leave load supported by the clamp unattended unless specific precautions have been taken.
Never expose clamps to chemicals, particularly acids, without consulting the supplier.
Never use the clamp in areas containing flammable vapours, liquids, gasses or combustible dust or fibres.
Never expose a clamp directly to the elements, water spray, steam etc without consulting the supplier.
Never use clamps which are unidentified or uncertified for lifting applications.
Never throw or drop clamps or drag them along the ground.
Never allow a load attached to the clamp to swing or spin unintentionally.
Never work under suspended loads.

www.tigerlifting.com
Page 3 of 14
Instruction Guide Tiger CSS En 202201 v2.0
2. Function/Operation
The Tiger CSS Safety Screw Cam Clamp is suitable for many applications. It is particularly useful for lifting and pulling sheet
metal, girders, and steel constructions. It is fitted with a moveable Cam on the thread spindle which provides a powerful
clamping force on the object being moved.
It can be used for lifting and transporting a large variety of different shaped steel, ranging from steel plates and structured
steel to curved and spherical shaped steel. As well as transporting plate, this clamp is well-suited to turning over steel
structures and welded constructions. It is also designed to be used in conjunction with a Tiger lever hoist to align steel
structures of fabrications and as an anchor point. These clamps are ideally suited for the construction industry.
Determine the weight of the object being lifted and make sure that it does not exceed the rated load of the clamp. The object
thickness must be within the grip range of the clamp (Chapter 7).
Before lifting the load, confirm that the clamps are in good condition and functioning properly. Inspect the clamp, if cam or
pad teeth are worn or if clamps are damaged, do not use! All personal must stand clear of load while it is being lifted or
moved.
See Chapter 8 for exploded diagram and part names.
The screw tightens when turned clockwise and loosens when turned counterclockwise).
1. Lower the clamp onto plate/object to be lifted., insert the load until it comes into contact with the deepest part of the jaw
opening of main body
2. Turn screw clockwise until the centre-ring on the Cam touches the plate. Tighten the screw further with the handle until
the clamp is fully tightened; The cam will turn back about 3mm after coming into contact with the steel plate when
tightening the forcing screw.
3. Continue to tighten Screw until it stops where the parallel Confirmation Lines align. After confirming the alignment,
tighten further until the force exceeds 25N.m (about 250Kgf. cm). Failure to match the parallel Confirmation Lines could
result in serious injury to person or damage to equipment.
4. The clamp has two shackle holes. Choose the appropriate hole depending on the application. Never use two holes
simultaneously for the same operation.
5. After the load has been lifted a short distance make sure it is well balanced before continuing. Lift slowly and smoothly at
all times.
6. During lifting operation, special attention must be given to prevent the Screw from loosening by an unintended contact
of the Clamp handle with wire rope or any other objects.
7. When loaded, the Cam swivels in proportion to the load applied and the teeth edges of the cam bite into the plate to
increase the clamping force, even when vibrations occur during operation.
8. If guiding a load by hand, place the palm of a gloved hand on top of the load, never grip the load with fingers on the side
or the underside.
9. When detaching the load, lower the plate/object to the ground slowly. To loosen load, turn the handle counterclockwise to
open the cam jaw.

www.tigerlifting.com
Page 4 of 14
Instruction Guide Tiger CSS En 202201 v2.0
Insert the load completely until it comes into contact
with the deepest part of the jaw opening
Methods of use
1. When lifting at two points, the lifting angle
must be within 60°
2. Always lift from three points when using the
clamps on complex shaped objects.
3. Clamps can also be used for positioning
steel structure for welding, pulling and/or
suspending.
Note - When clamps are used continuously
over long periods of time, check the
clamping force regularly and do not
overload the clamp.

www.tigerlifting.com
Page 5 of 14
Instruction Guide Tiger CSS En 202201 v2.0
4. Inner angle for loading of lever hoists or
chain blocks should be less than 30°.
5. The clamps can be used for lifting pipe
shaped objects and for turning over
material.
Clamps should NOT be used on the following structures
3. Inspection
According to national and international accident prevention and safety regulations, lifting equipment must be inspected:
•in accordance with the risk assessment of the operating company
•prior to initial operation
•before the unit is put into service for any subsequent use
•after substantial changes
•however, at least once every 6 months, by a competent person.
The intervals of inspection must be determined by the individual application and are based upon the type of service to which
the clamp will be subjected. In the event of any defects refer the clamp to a Competent Person for thorough examination.

www.tigerlifting.com
Page 6 of 14
Instruction Guide Tiger CSS En 202201 v2.0
Disassembling the unit
1. Turn the Screw counterclockwise to pull it out of Main Body. (Screw and
Handle cannot be disassembled.)
2. Loosen Hex. Hole Head Screw, and pull out and remove Spherical Based
Cam, Cam Holder and Collar.
3. Pull out Guide Pins and Collar.
4. Pull out two Stopper Pins from Cam Holder and remove Spherical Based
Cam.
5. Remove Hex. Hole Head Screw and pull out Sleeve.
Assembling the unit
1. Fit and match the hole of the Sleeve into the body hole of Hex.
Hole Head Screw and fix it.
2. Place the spherical part of Spherical Based Cam in the Cam
Holder and fix it with two Stopper Pins.
3. Place the Collar in the Cam Holder, and fit and match the groove
(chase) of the spherical part of Spherical Based Cam, the Guide
Pin hole of Cam Holder and the groove (chase) of the Collar, and
when they are all lined up insert the Guide Pin.
4. As shown in the figure, assemble and attach the five Disc
Springs (or four for the 6.3t capacity unit).
5. Put the Steel Ball and Spring in order at the bottom of Cam
Holder.
6. Place the assembled Spherical Based Cam, Cam Holder, and
Collar in the main body, and fix them with Hex. Hole Head Screw.
7. Insert and turn Screw into the screw part of the main body.

www.tigerlifting.com
Page 7 of 14
Instruction Guide Tiger CSS En 202201 v2.0
Examinations should include the following:
Category
Inspection method
Limit of use
Remedy
Body
Visually check or use
colour dyes to find
cracks.
Check for wear or
deformation of
shackle and screw
holes.
Measure the jaw
opening.
When found visually.
When the diameter of any one part of circumference of
any hole exceeds the size in the table below:
Rated capacity (t)
0.5
1.0
2.0
3.2
6.3
D1(mm)
27.5
32.5
36.5
45.5
51.0
D2(mm)
27.5
32.5
32.5
35.5
41.5
D3(mm)
34.5
42.5
44.5
46.5
58.5
When the difference of “A” and “B” exceeds 5% (5mm or
more against 100mm in depth.)
When the displacement of the centre of the screw and
cam exceed 2 mm.
Discard
Screw
Visually check or use
colour dyes to find
cracks.
Visually check for
bending.
Visually check for
wear or damage.
Visually check or
measure the degree of
wear.
Visually check or use
colour dyes to find
cracks at the teeth
bottom.
Visually check for
broken teeth
When found visually.
When the movement is not smooth, or when the
displacement of the Screw centre exceeds 2mm.
When thread part on circumference exceeds the size in
the below table.
Rated capacity (t)
0.5
1.0
2.0
3.2
6.3
Diameter (mm)
23.3
29.3
29.3
34.2
37.3
When the degree of wear exceeds 0.5mm.
When found visually.
When any broken tooth is found.
Replace

www.tigerlifting.com
Page 8 of 14
Instruction Guide Tiger CSS En 202201 v2.0
Category
Inspection method
Limit of use
Remedy
Sleeve
Visually check or use
colour dyes to find
cracks
Measure the screw
teeth for wear
Visually check the
adequacy of
installation
When found visually.
When rattling exceeds 2 mm between Screw and Sleeve.
When the Hex. Hole Head Screw is found to be loose or
falls out.
Replace
Adjust by tightening
Spherical
Based Cam
Visually check and
measure the degree of
wear.
Visually check or use
colour dyes to find
cracks at the bottom
cam teeth.
Visually check for
broken cam teeth
Inspect each section
for wear.
When the degree of wear exceeds 0.5mm.
When found visually.
When any broken tooth is found.
When the clearance between Spherical Based
Cam and Cam Holder exceeds 0.5mm
Replace
Cam Holder
Measure each section
for wear.
When the clearance between the Cam Holder, Collar and
Spherical Based Cam exceeds 0.5 mm resulting in
rattling.
Replace
Collar
Inspect each section
for wear.
Visually check for the
state of attachment.
When the clearance between Collar, Body, and Cam
Holder exceeds 0.3mm resulting in rattling.
When extreme low head hexagon bolt with hole
disconnects or loosen
Replace
Adjust by tightening
Guide pin
Measure each section
for wear.
Visually check or
measure for
deformation.
When the clearance in the hole exceeds 0.1mm resulting
in rattling.
When bending or deformation exceeds 0.1mm.
Replace
Stopper pin
Measure each section
for wear.
Visually check or
measure for
deformation.
When the space with the hole of the Cam Holder exceeds
0.2mm resulting in rattling.
When deformation exceeds 0.2mm.
When the movement of the Spherical Based Cam is not
smooth.
Replace

www.tigerlifting.com
Page 9 of 14
Instruction Guide Tiger CSS En 202201 v2.0
Category
Inspection method
Limit of use
Remedy
Steel ball
Measure for wear, or
deformation.
When any part of Ball diameter becomes smaller than
the size in the table below:
Rated capacity (t)
0.5
1.0
2.0
3.2
6.3
Diameter (mm)
4.8
6.8
6.8
6.8
7.8
When the movement of the spherical based cam is not
smooth.
Replace
Spring
Visually check if cam
returns automatically
to original position
when moved by hand.
Visually check the
clearance of spring
coils.
When the Cam does not return to its original position
due to the loss of adequate repulsive power from
deformation.
Replace when the spring becomes more than 5% shorter
than its original length.
Replace
Disc spring
Check for adequate
repulsive power when
cam pushed
When normal repulsive power lost from deformation and
lack of movement of Spherical Based Cam.
Replace
4. Maintenance
The equipment should not be dismantled for cleaning or maintenance, except by an authorised competent person. Clean the
clamp. Lubricate any moving parts. Correctly secure all fastenings.
5. Transport, Storage, Decommissioning and Disposal
Transporting the unit:
•Do not drop or throw the unit, always deposit it carefully.
•Use suitable transport means. These depend on the local conditions.
Storing or temporarily taking the unit out of service:
To ensure the continuing integrity of the unit you should store the unit in conditions that do not lead to damage or
deterioration. Therefore:
•Inspect clamps and accessories before placing into storage.
•Never return damaged clamps to storage.
•The unit should be secured against unauthorised and unwarranted use.
•Store the unit in a clean and dry place.
•Wipe off all dirt and water.
•A light oil film should be applied to moving parts.
•Protect the unit including all accessories against contamination, humidity and damage by means of a suitable cover.
•Protect against corrosion.
•If the unit is to be used again after it has been taken out of service, it must first be inspected again by a competent
person.
Disposal
When the product comes to the end of its lifecycle, after taking the unit out of service, recycle or dispose of the parts of the
unit respecting local and national environmental regulations.

www.tigerlifting.com
Page 10 of 14
Instruction Guide Tiger CSS En 202201 v2.0
6. Manufacturer Testing and Verification
This product was manufactured under our single-unit control of quality and was passed with strict inspection in accordance
with our inspection standards.
Declaration of Conformity
Tiger CSS Clamps have a 4:1 factor of safety. They are tested in line with the requirements within applicable
EN13155:2003+A1:2009. All items comply with the essential health and safety requirements of the Machinery Directive
2006/42/EC.
7. Technical Data
Product
code
Capacity
(t)
Clamping
Range
(mm)
L
L2
H
H1
H2
D1
D2
T1
T2
S
Weight
(kg)
(mm)
CSS-005
0.5
0-25
158
89
121
72
30
27
27
46
13
17
1.9
CSS-010
1.0
0-40
208
121
161
94
45
32
32
54
14
21
3.6
CSS-020
2.0
0-40
227
121
177
105
45
36
32
60
18
21
4.8
CSS-032
3.2
0-40
252
136
196
119
50
45
35
64
20
21
7.0
CSS-063
6.3
0-50
291
151
225
132
55
50
41
90
43
21
17.0
The minimum WLL. is 10 % of the maximum WLL.
Due to our policy of continual product development, dimensions, weights and specifications may change without prior notice.
Product code
Capacity (tonne)
WLL (kg)
Test Load (kg)
CSS-005
0.5
500
1,000
CSS-010
1.0
1,000
2,000
CSS-020
2.0
2,000
4,000
CSS-032
3.2
3,200
6,400
CSS-063
6.3
6,300
12,600

www.tigerlifting.com
Page 11 of 14
Instruction Guide Tiger CSS En 202201 v2.0
4 Disk Springs for
6.3t, 5 for all other
capacities
8. Exploded Diagram
Part
Number
Name
Assembly Name
Quantity
1
Screw
Screw
1
2
Handle
1
3
Sleeve
Sleeve
1
4
Hex. Hole Head Screw
1
5
Spherical Based Cam
Cam
1
6
Stopper Pin
2
7
Cam Holder
1
8
Pin
1
9
Steel Ball
1
10
Guide Pin
1
11
Collar
1
12
Disk Spring
5 (4 for 6.3t)
13
Hex. Hole Head Bolt
1
14
Spring Washer
1

www.tigerlifting.com
Page 12 of 14
Instruction Guide Tiger CSS En 202201 v2.0
9. Product Warranty and Warnings
Definitions
'Customer' means the individual, firm, company or other party with whom the Company contracts;
'Company' means Tiger Lifting UK Limited or Woo Sing Industrial Co., Ltd;
‘Contract’ the contract between the Company and the Customer for the sale and purchase of this product;
‘Defective Goods’ goods, parts or materials, which by reason of fault or incorrect design or workmanship, are found to be defective or fail or are
unable to perform in accordance with a Contract;
One Year Limited Warranty
The Company makes every effort to assure that its products meet high quality and durability standards and extends the following warranty to the
Customer of new products manufactured by the Company:
1. The Company warrants that this product, when shipped, shall be free from defects in materials and workmanship under normal use and
service and the Company shall, at its election, repair or replace free of charge any Defective Goods, provided that all claims for defects
under this warranty shall be made in writing immediately upon discovery and, in any event, within one (1) year from the date of purchase
of this product by the Customer and provided, further, that Defective Goods shall be kept for examination by the Company or its authorised
agents or returned to the Company or an authorised service centre upon request by the Company.
2. The Company does not warrant components of products provided by other manufacturers. However to the extent possible, the Company
will assign to the "Purchaser" applicable warranties of such other manufacturers.
3. Except for the repair or replacement mentioned in (1.) above, which is the Company’s sole liability and Customer's exclusive remedy under
this warranty, the Company shall not be responsible for any other claims arising out of the purchase and use of this product, regardless of
whether the Customer's claims are based on breach of contract, tort (including negligence), breach of statutory duty, or otherwise,
including claims for any loss of profit, goodwill or business opportunity or any indirect or consequential loss arising under or in connection
with the Contract.
4. This one year limited warranty is conditional upon the installation, maintenance and use of this product pursuant to the product manuals
prepared in accordance with content instructions by the Company. The warranty on this product does not apply to defects due directly or
indirectly to misuse, abuse, negligence or accidents. This warranty does not apply if the product has been subjected to improper fittings,
alignment or maintenance.
5. The Company shall not be responsible for any loss or damage caused by transportation, prolonged or improper storage or normal wear and
tear of this product or for loss of operating time.
6. This warranty shall not apply to this product if it has been fitted with or repaired with parts, components or items not supplied or approved
by the Company or which have been modified or altered.
7. The Company limits all implied warranties to the period specified above from the date the product was purchased by the Customer.
8. Except as stated herein, any implied warranties or merchantability and fitness are excluded.
If our inspection discloses a defect, the Company will repair, replace the product or refund the purchase price, if we cannot readily or quickly
provide a repair or replacement and if you are willing to accept such refund. The Company will return repaired or replacement products at The
Company’s expense, but if it is determined there is no defect, or that the defect resulted from causes not within the scope of Tiger Lifting’s
warranty, then the Customer must bear the cost of storing and retrieving the product.
Disclaimer
We believe that the information in this document, including technical information and any advice, is reliable although we give no guarantee as
to its accuracy or completeness. The user of our products must determine if the product, either used alone or conjunction with other products, is
suitable for their purpose and assumes all risk and liability in connection with those decisions. We have made every effort to make sure this
document is accurate. The information contained in this document does not form part of any contract.
Please also refer to our terms and conditions which can be found at: www.tigerlifting.com/terms-conditions/
The use of this product is beyond the control of Tiger Lifting. The warranty of this product is limited to the replacement
cost of this product should it be found to be defective in material and/or workmanship. The warranty is void if the product
is damaged, worn or used improperly. Normal wear and tear is not considered grounds for replacement. The Tiger Lifting
product warranty does not apply where there has been excessive overloading of the product.
! WARNING

www.tigerlifting.com
Page 13 of 14
Instruction Guide Tiger CSS En 202201 v2.0
Owner’s Notes

www.tigerlifting.com
Page 14 of 14
Instruction Guide Tiger CSS En 202201 v2.0
Owner’s Notes

www.tigerlifting.com
Instruction Guide Tiger CSS En 202201 v2.0
Tiger HQ Taiwan
Woo Sing Industrial Co., Ltd
6F, No. 118-1,
ZhongZheng Road
Shilin Dist.,
Taipei City
11145
Taiwan
+886-2-2831 3035
+886-2-2834 0188
Tiger UK and Europe
Tiger Lifting
Coquet Enterprise Park
Amble
Morpeth
Northumberland
NE65 0PE
United Kingdom
+44 1665 605130
+44 1665 603185
Representative in Europe
Tiger North America
Tiger Lifting NA
38381 N. Robert Wilson Rd.
Gonzales, Louisiana
70737
USA
+1 225-647-1312
+1 833-681-3057
sales@tigerliftingna.com
Tiger SEA Warehouse (Singapore)
Blk 18, Boon Lay Way #05-147
Tradehub 21
Singapore
609966
+65 9365 7207
+65 6250 0661
www.tigerlifting.com
© Copyright Tiger Lifting UK Limited. No part of this manual shall be reproduced, transmitted, transcribed, translated into any
language human or electronic, stored in any electronic retrieval system, in any form without the written permission of Tiger
Lifting UK Limited, Morpeth, UK
This manual suits for next models
5
Table of contents
Other Tiger Lifting System manuals
Popular Lifting System manuals by other brands

TBEI
TBEI CRYSTEEL STINGRAY manual
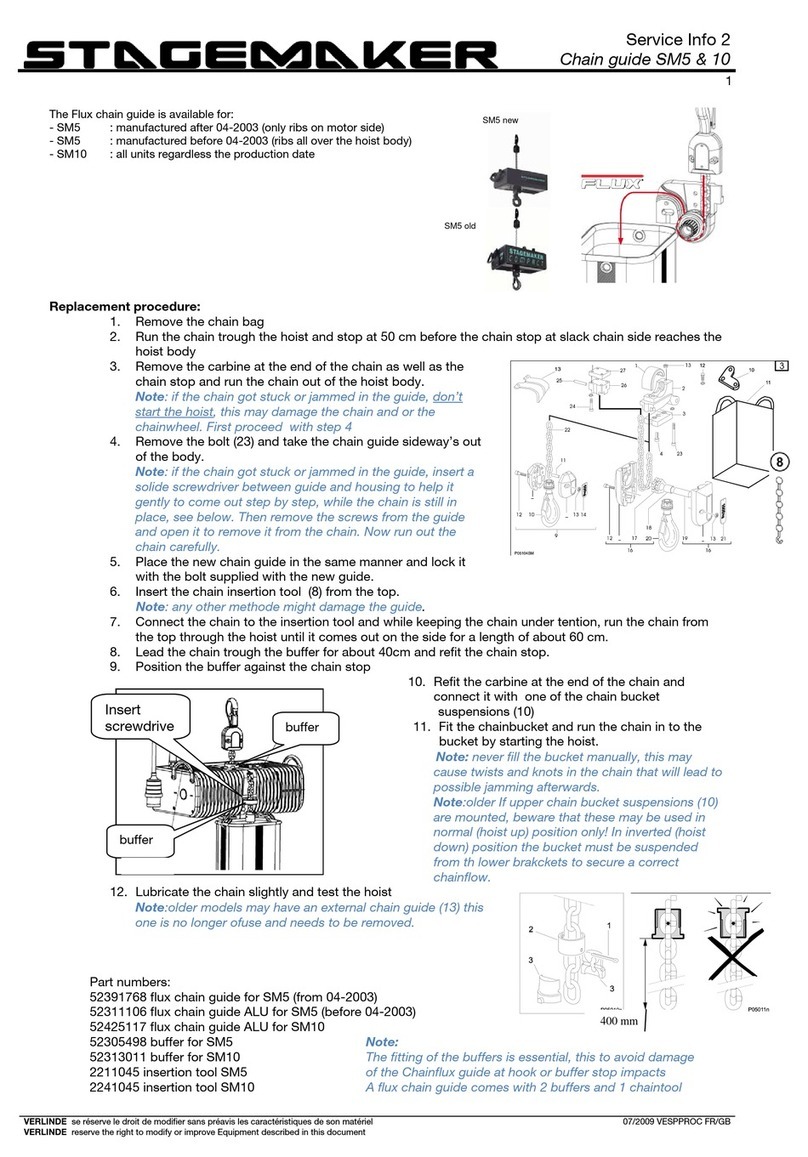
Stagemaker
Stagemaker SM5 Service Info
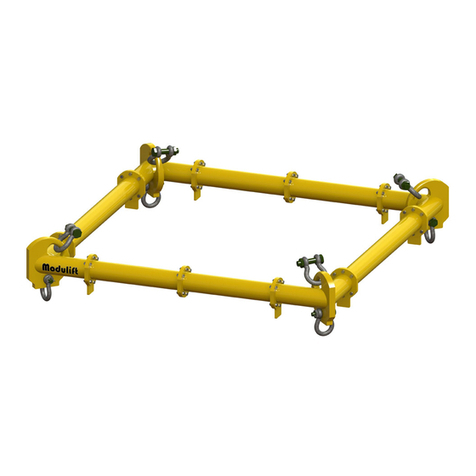
Modulift
Modulift CMOD 50 quick start guide
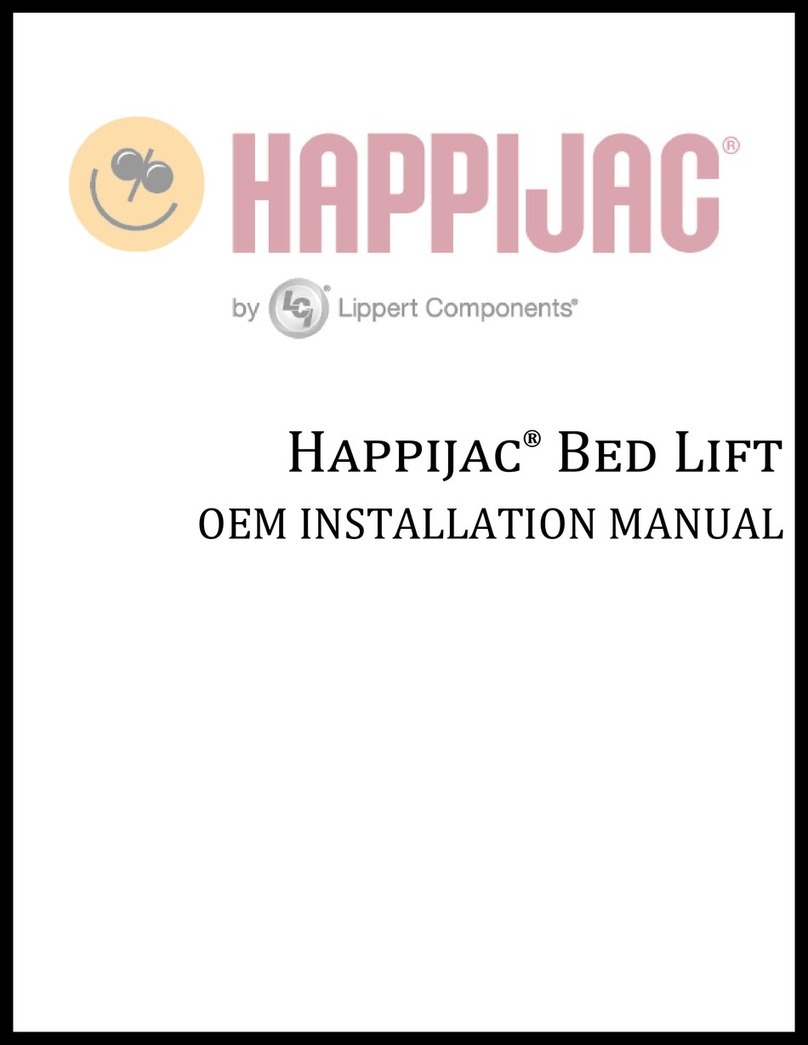
Lippert Components
Lippert Components Happijac OEM INSTALLATION MANUAL

Upright
Upright SL-26 Service & parts manual
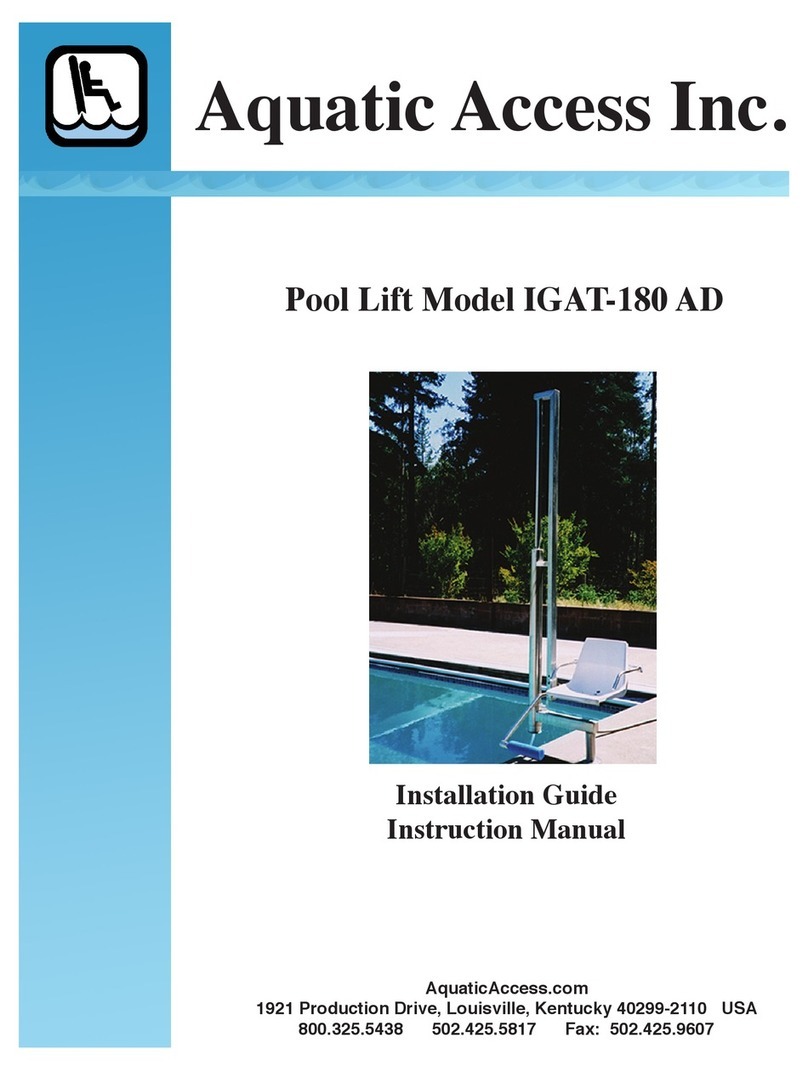
Aquatic Access
Aquatic Access IGAT-180 AD Installation guide / instruction manual