Titan TOx-5810XTR2-10-54 Programming manual

OWNER’S MANUAL & INSTALLATION GUIDE
TITAN-Ox™ Arsenic and Heavy Me al Reduc ion Fil ers
highly effec ive and economical rea men for he removal of arsenic,
uranium, lead, and o her heavy me als!
APPLICABLE MODELS: TOx-5810XTR2 Series
PLEASE READ THIS MANUAL CAREFULLY BEFORE
ATTEMPTING INSTALLATION. FAILURE TO FOLLOW THESE
INSTRUCTIONS MAY AFFECT THE PERFORMANCE OF YOUR
SYSTEM, VOID YOUR WARRANTY, AND RESULT IN
PROPERTY DAMAGE.

2
Congra ula ions on he purchase of your TITAN-Ox™ Series arsenic and heavy me al
fil ra ion sys em.
You have purchased one of the finest arsenic treatment systems on the market today. All
TITAN-Ox™ Series ater treatment systems utilize the orld's most advanced titanium
dioxide media to remove arsenic (both arsenic III and arsenic V), uranium, lead, cadmium,
copper, chromium +6, selenium, zinc and other heavy metals. Our titanium dioxide out-
performs iron and alumina-based removal systems – it has a high adsorbent capacity and
reacts quickly. It is long lasting and more environmentally-friendly. When the media has
reached exhaustion, it is non-hazardous and may be landfilled ithout concern about
leaching trapped contaminants back into the ecosystem. No chemical regeneration of the
media is required and back ash requirements are minimal so ater is not asted.
The brain of your TITAN-Ox™ system is the Fleck 5810XTR2 control valve. It is manufactured
by one of the orld’s premier ater treatment companies. The Fleck 5810 control valve is
ell respected for its reliability, serviceability, simple operation, and value. The integrated
Fleck XTR2 touch screen valve controller offers unsurpassed simplicity of operation, yet
complete control over all important valve operations. The Fleck 5810 XTR2 Water Softener of
Filter Control Valve Service Manual is also included ith your system. It includes additional
information regarding the operation of your valve, replacement parts lists, and more.
Your TITAN-Ox™ ater treatment system is designed to offer lo maintenance operation.
The control valve ill perform regular back ash functions automatically. For your
convenience, your system has been pre-programmed for you at our factory. Should you
need to change any of the settings, simply follo the instructions provided in this manual.
IMPORTANT SAFETY SYMBOLS
Hazards or unsafe practices that may result in personal injury
and/or severe property damage.
Hazards or unsafe practices that may cause operational
problems ith your ater treatment system.

3
Table of Con en s:
GENERAL WARNINGS ……………………………………………………………………………………………...….. …….. 4
OPERATING CONDITIONS …………………………………………………………………………………………….…... 5
INSTALLATION ………………………………………………………………………………………………………….…..…..….. 7
Step 1 – Pre-Installation Inspection ……………………………………………………………..……… 7
Step 2 – Selecting an Installation Location ………………………………………………..…..... 8
Step 3 – Prepare Treatment Tank ………………………………………………………………..……… 9
Step 4 – Turn off the Water & Electric Water Heaters ………………………………….… 12
Step 5 – Prepare and Install Inlet and Outlet Plumbing Connection …….…… 12
Step 6 – Drain Line Installation …………………………………………………………………………..… 15
Step 7 – Control Valve Set-up ………………………………………………….……………………….….. 16
Step 8 – Initial Start-up and Leak Testing …………………………………………………......…. 20
PERFORMANCE MONITORING …………………………………………………………………………….…..……. 21
BACKWASH ………………………………………………………………………………………………………………….…..……. 22
CHANGING TIME OF DAY ………………………………………………………………..…………………………..…… 24
CHANGING BASIC SETTINGS ……………………………………………………………………………………..…. 25
DIAGNOSTICS ………………………………………….…………………………………………………………………….…… 26
MASTER SETTINGS MODE …………………………………………………………………………………….……..… 27
OPERATION DURING A POWER FAILURE ………………………………………………………….…..…… 29
MAINTENANCE & TROUBLESHOOTING ……………………………………………………….…..….……. 30
WARRANTY INFORMATION ………………………………………………………………………………………..…… 31

4
GENERAL WARNINGS
Do not allo children or pets to play on or around the ater filter.
Do not install or store this filter system here it ill be exposed to freezing temperatures.
Do not tamper ith controls.
Do not repair, replace, or attempt to service any part of the system unless specifically
instructed to in this manual and you have the understanding, tools, and skills necessary to
carry out the procedure.
Packing materials can be dangerous to children. Keep all packing material (plastic bags,
polystyrene, boxes, etc.) ell out of children’s reach.
Individual components of this ater treatment system, and the installed system, are heavy.
Precautions should be taken to prevent personal injury or strain. Do not move heavy
components ithout assistance if you are not physically capable of safely carrying out the
procedure.
If the ater treatment system is to be left unattended for an extended period of time
(vacation, etc.), e strongly recommend that you turn off the ater supply to the system, or
the hole house, hile you are a ay.
If your ater pipes are metal (galvanized or copper), they may be used to ground electrical
systems, appliances, or your phone line. If this is the case, be sure to install regulation
ground clamps to the metal pipe on each side of the control valve and connect a jumper
ire bet een the 2 clamps (#4 gauge solid copper ire recommended). Consult a certified
electrician or plumber if you are unsure.
CRITICAL NOTE: THE CONTAMINANTS TARGETED BY THIS WATER TREATMENT
EQUIPMENT HAVE THE POTENTIAL TO CAUSE SERIOUS ADVERSE HEALTH EFFECTS.
WE STRONGLY RECOMMEND AN ONGOING REGIMEN OF FOLLOW-UP WATER TESTING
TO CONFIRM THE PERFORMANCE OF THE SYSTEM AND THE MAINTENANCE OF
CONTAMINANT LEVELS BELOW THE U.S. EPA AND HEALTH CANADA GUIDELINES.

5
OPERATING CONDITIONS
The follo ing chart provides guidance on the conditions required for successful operation of
your TITAN-Ox™ system.
Dissolved iron and manganese have a significant negative impact on the life of the Titanium
dioxide treatment media used in the TITAN-Ox™ system. Pre-treatment to remove iron is
strongly recommended here iron levels exceed 0.3 ppm (mg/l), and/or if manganese levels
exceed 0.05 ppm (mg/l), and may be desirable to extend media life even here the iron and
manganese in your ra ater do not exceed these levels. Media life and performance is
significantly reduced hen the pH exceeds 8.3. If pH exceeds this level, pH correction
should be undertaken prior to the TITAN-Ox™ system. Elevated levels of silica and/or sulfate
may reduce media life depending on other ater chemistry conditions (particularly if the
ater is soft). Pre-filtration to remove sediment and particulates ill reduce required
back ash frequency.
FOR IDEAL CONTAMINANT REDUCTION RATES, THE OPTIMAL FLOW RATE SHOULD
NOT BE EXCEEDED. THE LOWER THE FLOW RATE, THE HIGHER THE CONTAMINANT
REDUCTION RATES WILL BE. SATISFACTORY PERFORMANCE CAN GENERALLY BE
ACHIEVED UP TO THE RECOMMENDED PEAK FLOW RATE AS LONG AS THIS LEVEL OF
FLOW RATE IS NOT SUSTAINED CONTINUOUSLY.
USE OF THIS EQUIPMENT OUTSIDE OF THESE OPERATING CONDITIONS MAY
ADVERSELY AFFECT THE PERFORMANCE OF YOUR SYSTEM, RESULT IN SYSTEM
DAMAGE INCLUDING WATER LEAKS AND CORRESPONDING PROPERTY DAMAGE, AND
MAY VOID YOUR WARRANTY.
Minimum Water Pressure 20 PSI
Maximum Water Pressure 90 PSI*
Recommended Water Pressure 40-70 PSI
Water Temperature 36F to 100F (2 to 38C)
Minimum Air Temperature 32°F (0°C)**
pH Range 5.0*** to 8.3
Maximum Iron 0.3 ppm (mg/l)
Maximum Manganese 0.05 ppm (mg/l)
Maximum Arsenic See note belo

6
* While the TITAN-Ox™ system is built to ithstand pressures exceeding 90 PSI, if your ater
pressure is greater than 70 PSI, e recommend that you have a certified plumber install a
pressure reducing valve ahead of the TITAN-Ox™ system.
** The system cannot be subjected to freezing conditions or severe damage to the system
and your property could occur.
*** pH correction is strongly recommended here pH levels are less than 6.5 to prevent
damage to your control valve and plumbing system, and to prevent leaching of metals from
copper and brass plumbing components and solder in your home. Contact your dealer for
recommendations.
IF YOUR TOTAL ARSENIC LEVEL IS GREATER THAN 60 PARTS PER BILLION (0.060 MG/L),
PLEASE CONTACT ONE OF OUR CERTIFIED WATER TECHNICIANS FOR SIZING
ASSISTANCE (PHONE TOLL FREE 1-866-376-2690). A LEAD/LAG CONFIGURATION OR
LARGER MEDIA VOLUME MAY BE REQUIRED FOR DESIRED TREATMENT.
TITAN-Ox™ Series Flow Ra es & Backwash Requiremen s:
Model
Op imal
Service Flow
Ra e* (GPM)
Maximum
Service Flow
Ra e* (GPM)
Backwash Flow Ra e
a 40F Wa er Temp
(GPM)
Backwash Flow Ra e
a 70F Wa er Temp
(GPM)
TOx-5810XTR2-10-54
2.7 5.5 4.5 6
TOx-5810XTR2-12-52
3.9 7.9 7 8
TOx-5810XTR2-13-54
4.6 9.2 8 10
TOx-5810XTR2-14-65
5.3 10.7 9 12
CONFIRM THAT YOUR WATER CONDITIONS, SERVICE FLOW RATE NEEDS, AND
AVAILABLE BACKWASH FLOW RATES MEET THE ABOVE SPECIFICATIONS FOR THE
MODEL YOU ARE INSTALLING BEFORE COMMENCING THE INSTALLATION PROCESS.
IF IN DOUBT, CALL YOUR DEALER FOR ADVICE. INSTALLED UNITS CANNOT BE
RETURNED.

7
INSTALLATION
WE RECOMMEND THAT YOU READ THIS ENTIRE MANUAL BEFORE STARTING THE
ACTUAL INSTALLATION. WHILE WE STRONGLY RECOMMEND THAT A LICENSED
PLUMBER PERFORM ALL INSTALLATION WORK, A MECHANICALLY-INCLINED
HOMEOWNER WITH SUITABLE PLUMBING KNOWLEDGE CAN INSTALL THIS SYSTEM.
IN ALL CASES, IT IS CRITICAL THAT THE INSTALLATION BE DONE IN ACCORDANCE
WITH THESE INSTRUCTIONS AND ALL APPLICABLE PLUMBING AND ELECTRICAL
CODES. BE SURE TO OBTAIN ALL REQUIRED PERMITS. IF THESE INSTRUCTIONS AND
THE APPLICABLE CODES ARE IN CONFLICT, THE RELEVANT PLUMBING/ELECTRICAL
CODE SHALL BE FOLLOWED. EQUIPMENT FAILURE, PERSONAL INJURY, OR PROPERTY
DAMAGE CAN RESULT IF THIS EQUIPMENT IS NOT INSTALLED PROPERLY.
S ep 1. – Pre-Ins alla ion Inspec ion
Inspect all of the components that you
received ith your unit. You should have
received the follo ing:
1. Fleck 5810 XTR2 Control Valve
2. Media Tank
3. Upper Screen
4. Bypass Assembly / Bypass Valve and
1” NPT Connector Yokes (2) and Flo
Restrictor (attached to outlet yoke)
5. Riser tube and Lo er Distributor
6. Bag or Box of Gravel
7. Bag(s) or Box(es) of MetSorb media
8. Funnel
9. Drain Line Flo Control - DLFC
(attached to #1)
10. Arsenic Test Kit

8
S ep 2. – Selec ing an Ins alla ion Loca ion
While exterior installation in arm climate areas is possible, e strongly recommend interior
installation only. The system cannot be allo ed to freeze or severe system damage could
occur. The system should not be exposed to rain and it should not be installed in direct
sunlight, as long-term exposure to UV light could damage components of the system.
Furthermore, direct sunlight could raise the internal ater temperature in the treatment tank
and reduce back ash effectiveness.
In most cases, the system should be located AFTER your ater pump and pressure tank(s)
and BEFORE all other ater treatment equipment and your hot ater heater.
IF YOU HAVE OTHER WATER TREATMENT EQUIPMENT, YOU SHOULD DISCUSS THE
ORDER OF YOUR TREATMENT EQUIPMENT WITH YOUR DEALER PRIOR TO
INSTALLATION.
Select a location for installation of your ater filter that is ithin close proximity to the main
incoming ater line of the home. The location should have a firm, level surface ith enough
space for the unit itself and sufficient space surrounding the unit to facilitate maintenance.
WHILE WATER LEAKS ARE VERY RARE AND UNEXPECTED, YOUR WATER FILTER
SYSTEM SHOULD BE LOCATED NEXT TO A FLOOR DRAIN OR PROTECTED BY A WATER
LEAK DETECTION SYSTEM WITH AUTOMATIC SHUT-OFF VALVE TO PREVENT WATER
DAMAGE TO YOUR PROPERTY IN THE UNLIKELY EVENT OF A WATER LEAK.
RECOMMENDED WATER LEAK DETECTION SYSTEMS ARE AVAILABLE AT WWW.A-LEAK-
DETECTOR.COM.
You ill also require a suitable drain to discharge aste ater from the back ash cycle. A
drain standpipe for a ashing machine, floor drain, or sump pump are excellent drain
options. We recommend that the drain line be connected to a minimum 1½" drain
standpipe or floor drain located ideally belo the top of the head of your ater filter. If
possible, the drain should be no farther than 20 feet from the system.

9
NOTE: NEVER CONNECT THE DRAIN LINE DIRECTLY INTO A DRAIN PIPE. ALLOW AN AIR
GAP BETWEEN THE DRAIN TUBING AND WASTE LINE TO PREVENT THE POSSIBILITY
OF BACK-SIPHONING. WE DO NOT RECOMMEND USE OF A CHECK VALVE AS IT MAY
BECOME CLOGGED WITH CONTAMINANTS EJECTED FROM THE SYSTEM DURING
BACKWASH.
You ill also need access to a standard, non-s itched, grounded 120 volt (60 Hz) electrical
outlet. An extension cord may be used to reach a suitable electrical outlet. If this option is
used, ensure that the extension cord is UL/CSA certified and of an appropriate ire gauge
for the application.
S ep 3. – Prepare Trea men Tank
T o types of media are supplied ith your TITAN-Ox™ system: gravel hich forms the base
layer (underbedding) in your treatment tank, and a specialized ater treatment media called
MetSorb.
Place the tank in the location here it ill sit hen the installation is complete. Note that the
black base of your tank is not permanently attached to the rest of the tank. If your tank
appears to be crooked, the base has likely been knocked out of alignment during shipping.
This can be correct by picking the tank up and tapping it on a hard surface hile holding it
perpendicular to the floor. A fe light taps ill generally straighten it out.
Temporarily remove the distributor and riser tube assembly from the treatment tank. Hand
tighten the Fleck 5810XTR2 control valve on the tank and mark here the front of the tank
ill be. Turn the tank so that the front of the tank is here you ant it hen it is full – once it
is full of media and ater, it becomes very heavy and difficult to move!
Remove the control valve and re-insert the distributor and riser tube assembly into the tank.
The distributor, hich looks like a cone-shaped plastic screen, is pre-connected to the end of
the long plastic riser tube hich extends from the bottom of the tank to the top of the tank
here the control valve is attached. At the bottom of the tank, there is a recess in the center
of the tank to accept the distributor to keep it properly aligned. The riser tube has been pre-
cut to the correct height for you. When the distributor is correctly positioned, the top of the
riser tube ill be approximately 1/8 to 1/4 of an inch belo the top of the tank. If the tube is

10
flush or protruding above the top of the tank, the distributor tube is not nested correctly in the
recess at the bottom of the tank.
Add enough ater to the tank to cover the lo er distributor ith a minimum of 6 inches of
ater. This ill prevent damage to the lo er distributor as gravel is loaded. Place the funnel
into the tank so that the riser tube is in the middle. Place tape over the open end of the riser
tube. This ill prevent gravel or media from accidentally going do n the tube during the
follo ing steps.
For the follo ing steps, e recommend that you ear a dust mask. Take the bag/box of
gravel and, using a small scoop, add the gravel to the tank through the funnel to completely
cover the lo er distributor. Use all of the gravel. Be sure to provide some do n ard
pressure on the riser tube hile adding the gravel to ensure that the distributor does not shift
out of its recess or rise up. Ensure that you create an even layer of gravel across the bottom
of the tank. A rigid piece of thin all tubing (conduit, copper pipe, etc.), approximately 1”
longer than the tank height orks ell as a leveling tool if you need it. Ensure that the riser
tube remains centered in the opening at the top of the tank.

11
Once this is complete, add the MetSorb media in the same manner. Use all of the media
provided. Depending on the capacity of the system, there ill only be enough media to fill
the tank to about 1/2 to 3/4 full. This is normal. The media tank should never be filled to the
top of the tank as the remaining space, kno n as the “freeboard,” is necessary for the media
to have room to expand during the back ash cycle.
Once you have finished adding the media to the tank, remove the tape from the distributor
tube. Be careful not to pull up ards on the riser tube hile doing this as it is important that
the distributor remain in its recess at the bottom of the tank.
Fill the media tank ith ater up to ithin a couple of inches of the top of the tank. This ill
allo the media to pre-soak, thereby preventing media loss during the initial back ash.
DO NOT INITIATE A REGENERTION OF THIS SYSTEM
FOR A MINIMUM OF 2 HOURS AFTER ADDING THE
WATER TO ALLOW ADEQUATE PRE-SOAKING.
BACKWASHING BEFORE THE MEDIA IS SATURATED
MAY CAUSE A LOSS OF MEDIA AND POTENTIAL
DAMAGE TO THE CONTROL VALVE.
Attach the upper screen to the underside of the control
valve. Be sure to t ist clock ise and lock it into place.
Apply a small amount of lubricant to the top inch of the
outside of the riser tube and to the tank o-ring seal.
No e: Only use food-grade silicone lubrican . A small bag of
lubrican is provided in he small par s bag. Do NOT use pe roleum jelly.
The control valve can no be secured to the top of the tank. Before attaching the valve,
check to make sure that there is no debris such as gravel or media in the tank threads.
Scre the control valve onto the tank. Make sure that the riser tube inserts into the center
hole in the upper screen and the control valve as you scre do n the valve. The control
valve should be hand-tightened (clock ise). Do NOT use the control valve's timer assembly

12
for leverage and do not use tools. A firm grasp ith both hands at the base of the valve ill
ork. Do NOT use pipe cement (“pipe dope”) or Teflon® tape on the threads.
S ep 4. – Turn off he Wa er & Elec ric Wa er Hea ers
FAILURE TO FOLLOW THIS PROCEDURE COULD RESULT IN SERIOUS, PERMANENT
DAMAGE TO THE HEATING ELEMENTS IN YOUR WATER HEATER.
If you have a conventional electric ater heater or an on-demand (tankless) electric ater
heater, e highly recommend that you turn off the po er to the heater hile installing any
ater treatment equipment. Turn off po er to your ater heater no .
Turn off the household main ater shutoff valve. Open several plumbing fixtures inside the
home as ell as the outside faucets to drain as much ater out of the plumbing system as
possible.
Follo ing completion of the entire installation, restore the ater flo by turning on the
household main ater valve and allo all air to be purged from the plumbing system before
turning the po er back on to your ater heater.
S ep 5. – Prepare and Ins all Inle and Ou le Plumbing Connec ions
IF YOU WISH TO USE COPPER PIPING FOR YOUR INSTALLATION AND WILL BE
SOLDERING THE JOINTS, DO NOT APPLY HEAT NEAR YOUR CONTROL VALVE, BYPASS
ASSEMBLY, 1” NPT CONNECTOR YOKES, FLOW RESTRICTOR, OR THE DRAIN FITTINGS;
OTHERWISE SERIOUS DAMAGE TO THESE PARTS COULD OCCUR. ALWAYS SOLDER
JOINTS WITH THESE COMPONENTS DETACHED. IF YOU ARE USING COPPER
ADAPTERS TO CONNECT TO THE 1” NPT CONNECTOR YOKES, IT IS RECOMMENDED
THAT YOU SOLDER A 6 INCH PIECE OF COPPER PIPE INTO EACH OF THE CONNECTION
ADAPTERS AWAY FROM THE VALVE, THEN LET THEM COOL OFF BEFORE THREADING
THEM ONTO THE 1” NPT CONNECTORS.

13
Key Con rol Valve Componen s:
1. Control Valve Body
2. Bypass Valve
3. 1” NPT (Male) Connector Yokes
4. Drain Line Flo Control (DLFC)
5. Valve Cover
6. DLFC Retention Clip
7. Flo Restrictor
TEFLON® TAPE IS THE ONLY SEALANT TO BE
USED ON THE 1” NPT CONNECTOR YOKES AND
DRAIN FITTINGS.
The system’s control valve is connected to your
incoming and outgoing ater lines by ay of a
bypass assembly ith 1”NPT threaded fittings.
This assembly is composed of the bypass valve and t o 1”NPT connector yokes. A flo
restrictor is attached to the outlet connector yoke. Locate the inlet and outlet ports on the
back of the control valve. Note that the inlet and outlet are marked ith arro s indicating
the correct direction of ater flo . When you are looking at the back of the control valve, the
inlet is on the left and the outlet is on the right. Check the corresponding markings on the
bypass to ensure the correct direction of ater flo and attach the bypass valve to the
control valve. The in and out arro s on the bypass should be pointing the same direction as
the in and out arro s on the outside of the control valve.
BE VERY CAREFUL TO MAKE SURE YOU PLUMB THE SYSTEM IN THE RIGHT DIRECTION.
The bypass assembly is secured to the control valve using threaded fittings. Thread sealant
tape should not be used on these threads. The seal is made by ay of o-rings. To attach
the bypass to the control valve, simply thread the 2 nuts on the bypass onto the valve until
the nuts bottom out on the valve body. Do not overtighten - it is normal for some “play” to
exist hen the bypass assembly is properly seated. This allo s for minor misalignment of

14
the piping connections and relieves stress on the valve. The 1” NPT connector yokes are
connected to the bypass in the same manner (they are normally shipped to you pre-
connected to the bypass, but you can separate them to make the plumbing to your main
ater lines easier if you ant). Make sure that the connector yoke ith the attached flo
restrictor is attached to the outlet of the bypass.
WE HIGHLY RECOMMEND THAT YOU REMOVE THE BYPASS ASSEMBLY FROM THE
CONTROL VALVE BEFORE MAKING THESE FINAL CONNECTIONS AS YOU MAY
INADVERTENTLY APPLY TOO MUCH PRESSURE ON THE VALVE WHILE SECURING THE
ADAPTERS, CAUSING DAMAGE TO THE VALVE BODY.
You ill need to purchase the appropriate NPT threaded fittings to connect the connector
yokes to the material and size of your main inlet and outlet ater lines.
Plumb your main incoming and outgoing ater lines using suitable pipe, fittings, elbo s, etc.
as necessary to create a tidy, secure installation up to the back of the bypass valve
(including the correct connection adapters to mate ith the threaded fittings on the bypass
assembly’s connection yoke and flo restrictor. Be sure to follo all local plumbing codes.
Place the bypass in the “bypass” position as pictured:

15
S ep 6. – Drain Line Ins alla ion
NOTE: NEVER CONNECT THE DRAIN LINE DIRECTLY INTO A DRAIN. ALLOW AN AIR-GAP
OF A MINIMUM OF 1 INCH (CHECK LOCAL CODES) BETWEEN THE DRAIN LINE AND
WASTE LINE TO PREVENT THE POSSIBILITY OF BACK-SIPHONING. ALWAYS FOLLOW
LOCAL CODES. THE DRAIN LINE SHOULD NOT BE EXPOSED TO FREEZING
TEMPERATURES.
During the back ash cycle, your TITAN-Ox™ ill send captured contaminants out the drain
port. This port needs to be connected to a suitable household drain, ideally ithin 20 feet of
your media tank. A nearby floor drain, sump pump, or a standpipe for a ashing machine is
an excellent option. We recommend that the drain line be connected to a minimum 1 1/2"
drain standpipe or floor drain located ideally belo the top of the head of your ater filter.
Locate the drain port on the back of your control valve. The drain line flo control assembly
(DLFC) is pre-attached to the control valve. For back ash flo rates of 7 GPM or less, the
DLFC ill be a black plastic elbo housing ith 3/4 inch male NPT threads. This housing
contains a flo control asher that limits the back ash flo rate. For back ash flo rates
exceeding 7 GPM, the DLFC ill be a black plastic straight housing ith 1 inch male NPT
threads.
You ill need to purchase suitable pipe or tubing for the drain line, either in 3/4 or 1 inch
diameter, to match the connection points on the drain line flo control assembly (DLFC). To
determine your MINIMUM drain line diameter, look up your model and incoming ater
temperature using the chart belo . If in doub , ma ch he size of your drain line o he
hread size of he DLFC on your con rol valve.

16
MINIMUM Drain Line Diame er:
Model 40F Wa er Temp 70F Wa er Temp
TOx-5810XTR2-10-54 1/2" 1/2"
TOx-5810XTR2-12-52 1/2" 3/4"
TOx-5810XTR2-13-54 3/4" 3/4"
TOx-5810XTR2-14-65 3/4" 3/4"
Polyethylene tubing, PEX, PVC, CPVC, or copper pipe are all acceptable material choices for
the drain line. If you are using flexible tubing, be sure that there are no “kinks” or “crimps” in
the tubing after installation that may cause a flo restriction. If used, overhead drain lines
are not to exceed a height of 5 feet above the control valve and should be not more than 50
feet in length. Should an overhead drain line be utilized, it is recommended that the drain
line be increased in size (diameter), and that it not be fastened flush to the bottom of a floor
joist to minimize noise transfer to the upstairs of the building during regeneration.
Using an appropriate fitting, connect the drain line flo control to your drain line tubing/pipe.
The DLFC can be removed from the control valve to facilitate easier plumbing if desired. To
remove the drain line flo control, pull on the retaining clip to remove it and then grasp the
drain line flo control and pull out ard. You may ish to dry-fit the fitting first to make sure
you line up the drain line properly ith the drain port on the control valve if you are using
rigid pipe.
Re-insert the DLFC into the control valve and securely lock into place ith the retaining clip
hen done.
Ensure that the drain line is thoroughly secured along its route to the drain. The drain line
ill be under pressure hen the back ash cycle is orking. If not adequately secured, the
drain line could vibrate during back ash causing excessive noise. If this is experienced, use
additional fixtures to better secure the drain line.
S ep 7 – Con rol Valve Se -up
During cold eather, the installer should arm the control valve to room temperature before
operating. Note: All electrical connections must be done according to local codes.
Plug the control valve into a standard, grounded 120 volt (60 Hz) electrical outlet. Be certain
that the outlet is uninterrupted and not controlled by a s itch. An extension cord may be
used to reach a suitable electrical outlet. Ensure that the extension cord is UL/CSA certified

17
and of an appropriate ire gauge for the application. Plug the other end of the po er cord
into the electrical port on the control valve.
Note: The electrical port on the control valve is
located on the right side of the valve ( hen you are
facing the control panel), just behind the tab used
to remove the valve cover. It is a bit tricky to find.
Once plugged in, the touch screen on the control
valve ill illuminate. The control valve may need
to reset to the home position hen it is po ered
up. If it does, the motor ill run for a fe seconds.
Optional: The touch screen is shipped ith a protective plastic film that can be peeled off.
The follo ing is the primary “Home Screen” or Main Menu:
Items displayed in blue or grey can be touched to edit or obtain more information. Items
displayed in black are for information purposes only and cannot be selected.
In the top left corner of the screen, you ill find the current day of the eek and time.
In the top right corner, there is an indicator that ill tell you hen the next “regeneration” or
back ash cycle is scheduled to occur.

18
In the middle of the screen is the regeneration cycle heel hich indicates the current valve
cycle (indicated in green), and other applicable cycles (in black).
The bottom menu bar provides the follo ing options:
Vacation: Select this icon to set your ater filter system to vacation mode. This mode can
be used if you ill be a ay for an extended period of time and ill not be using ater.
When vacation mode is selected, the system ill temporarily cease flush cycles. Upon
returning from vacation, it is important to remember to end the vacation mode by pressing
the same icon. When in vacation mode, “Vacation Mode” ill be displayed in the top right
corner of the screen.
Assistance: Select this icon to display the name and phone number of your dealer.
Diagnostics: Select this icon to enter the Diagnostics Mode - see Diagnostics Mode belo
for more details.
Settings: Select this icon to edit the time of day that the flush cycle ill occur. Other
programming functions can be accessed using this icon, ho ever, it is strongly
recommended that you do not change any settings ithout first discussing ith your dealer.
Regeneration: Select this icon to schedule a flush cycle to occur immediately or the next
time that time of day equals the regeneration (flush) time.
The touch screen has an energy-saving feature that ill turn the display off (sleep mode) if
no user input has been made for 5 minutes. To turn the screen back on, just touch it.
We ill first set the time of day to the correct time. The current day of the eek and time is
displayed in the top left corner of the home screen. It is important that the day and time be
accurate so that the back ash cycle ill occur at the correct time of the day and so that the
diagnostic and data gathering functions of the control valve ill be accurate.
If the day and time are flashing, it means that there has been a po er failure and the day
and time need to be checked.
To change the time of day, touch the day and time display in the top left corner of the home
screen and the follo ing screen ill appear:

19
Touch the grey box associated ith the year. 2 blue arro s ill appear. Touch the blue
arro on the left to decrease the year. Touch the blue arro on the right to increase in the
year. Adjust the year by touching the arro s until it is correct.
Similarly, touch the grey boxes associated ith the month and day and use the arro s to
adjust the month and day settings until they are correct
Set the hour, minutes, and pm/am in the same manner.
When you are satisfied that all of the settings are correct, press the checkmark icon on the
bottom right corner of the screen. To cancel your changes and return to the home screen,
press the “X” icon at any time.
Your TITAN-Ox™ has been pre-programmed to back ash every 10 days or 3,000 gallons
( hichever occurs first) and to perform the back ash process at 12:30am in the morning
hen it is very unlikely that ater ill be required in the building. If ater is required during
the back ash process, untreated ater ill be permitted to flo to meet your service needs.
You may edit the frequency and duration of the back ash based on your ater conditions.
You may also alter the time of day that the back ash process occurs if 12:30am is not ideal
for you. If you have a ater softener or other automatic back ashing ater treatment
systems, make sure that they are not set to regenerate at the same time. We recommend
that they back ash/regenerate at least 2 hours apart. Follo the instructions under
“Changing Basic Settings” to change the frequency or back ash time if desired. If you ant
to change the duration of the back ash or final rinse cycles, these settings must be edited in
the “Master Settings Mode” – see belo for details.

20
S ep 8 – Ini ial S ar -up and Leak Tes ing
Ensure that the bypass is in the bypass position. Turn on the main ater supply. Open a
cold ater tap nearby and let the ater run for a fe minutes or until the system is free of
foreign material (usually solder) and air that may have resulted from the installation. Once
the ater is running clear and free of air, close the ater tap.
INSPECT YOUR PLUMBING CONNECTIONS AND CONTROL VALVE FOR LEAKS AND
REPAIR ANY LEAKS FOUND BEFORE PROCEEDING.
DO NOT INITIATE A REGENERTION OF THIS SYSTEM FOR A MINIMUM OF 2 HOURS
AFTER ADDING WATER TO THE MEDIA TANK TO ALLOW ADEQUATE PRE-SOAKING.
BACKWASHING BEFORE THE MEDIA IS SATURATED COULD CAUSE A LOSS OF MEDIA
AND POTENTIAL DAMAGE TO THE CONTROL VALVE.
Once the media has been adequately pre-soaked for 2 hours:
WITH THE BYPASS STILL IN THE BYPASS POSITION, touch the REGENERATION ICON. You
ill be given a choice to regenerate “no ” or “at regen time” - select “no .” You ill hear the
valve motor change the position of the valve piston, “back ash” ill be indicated on the
regeneration heel on the touch screen display, and the back ash time ill begin counting
do n in the top right corner of the display. Once the motor has stopped moving (no more
noise), press the REGENERATION ICON again to advance to the rinse stage of the
regeneration cycle.
Without delay, immediately begin to slo ly open the bypass to the service position, allo ing
ater to flo into the system. Water and air ill begin to flo to the drain line and ill
continue for 3 minutes. At the end of this time, the valve ill re-position and the filter ill
return to normal service mode.
INSPECT YOUR DRAIN LINE PLUMBING CONNECTIONS AND REPAIR ANY LEAKS
IMMEDIATELY BEFORE PROCEEDING. IF THE PLUMBING PIPE RATTLED OR VIBRATED
This manual suits for next models
3
Table of contents
Other Titan Water Filtration System manuals
Popular Water Filtration System manuals by other brands

Oase
Oase ProfiClear Premium L operating instructions
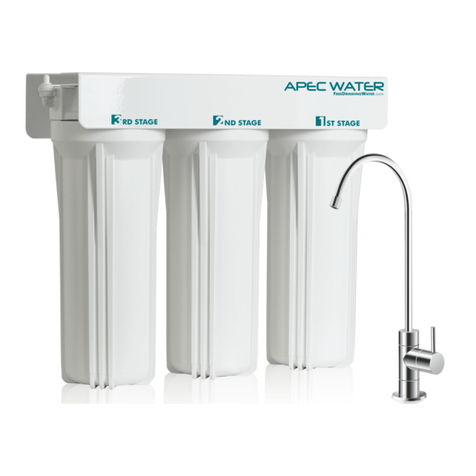
Apec Water
Apec Water WFS-1000 Installation instructions & owner's manual

Waterway
Waterway Crystal Water owner's guide
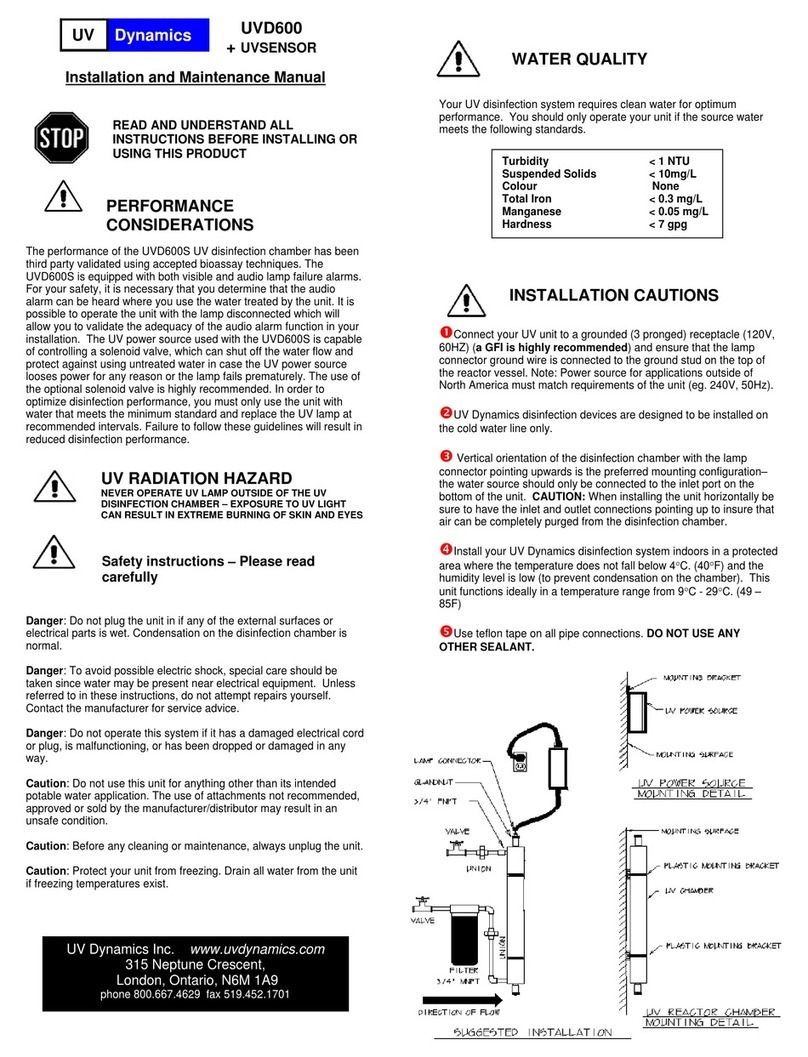
UV Dynamics
UV Dynamics UVD600/S Installation and maintenance manual
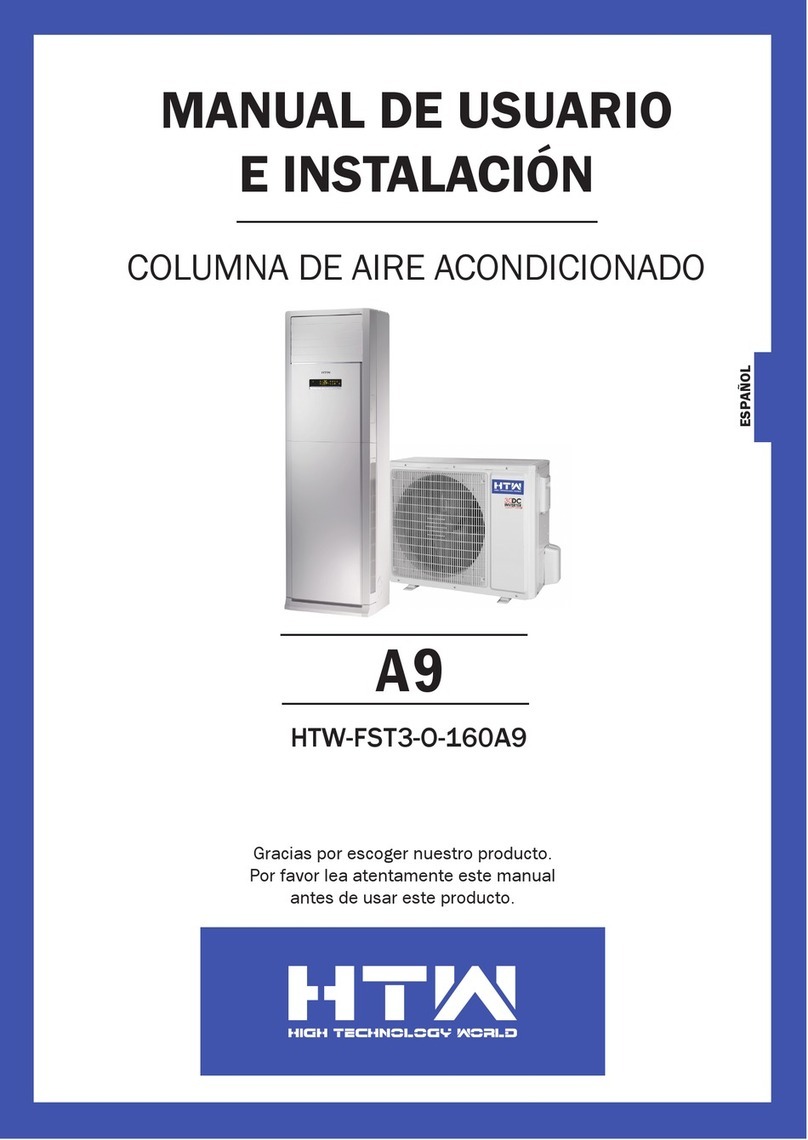
HTW
HTW HTW-FST3-O-160A9 manual
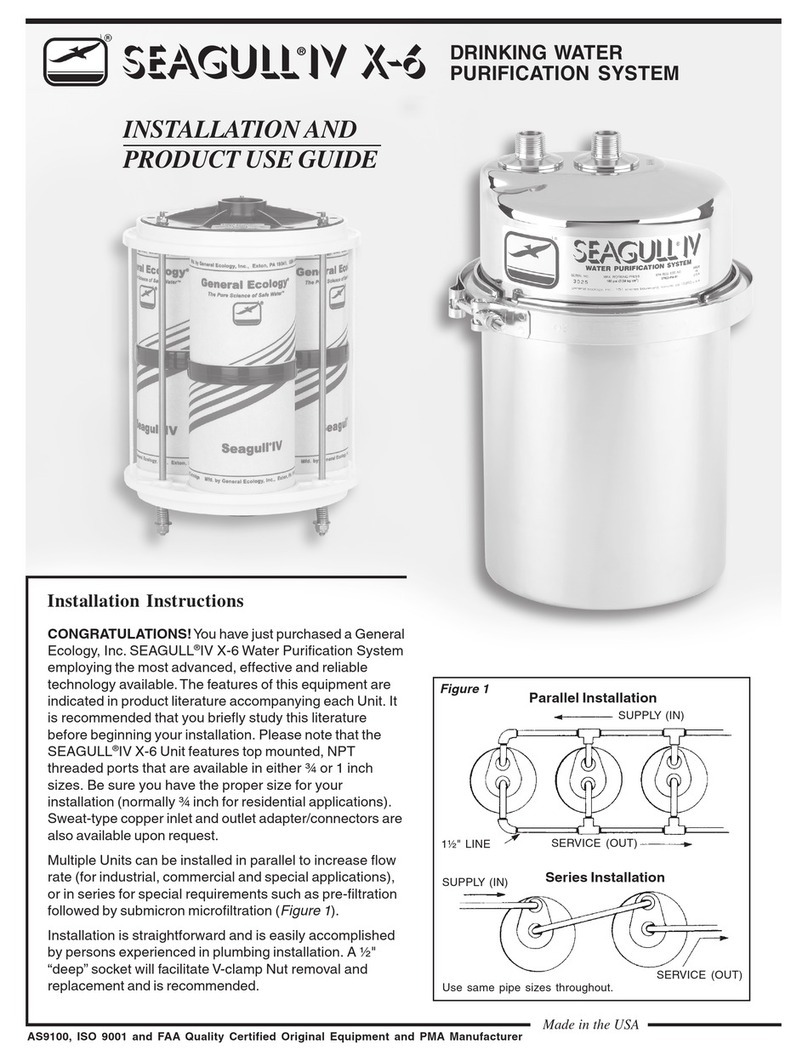
GENERAL ECOLOGY
GENERAL ECOLOGY SEAGULL IV X-6 Installation and product use guide