TMG TMG-MVR50 User manual


CONTENTS
1.Foreword........................................................................................................................................................................... 1
2. Safety Information ...........................................................................................................................................................1
2.1 Operating Safety ............................................................................................................................................................ 2
2.2 Operator Safety While Using Internal Combustion Engines ...........................................................................................3
2.3 Service Safety ................................................................................................................................................................ 4
2.4 Safety Labels..................................................................................................................................................................5
3. Technical Data .................................................................................................................................................................6
3.1 Roller..............................................................................................................................................................................6
3.2 Engine ............................................................................................................................................................................ 7
3.3 Lubrication ..................................................................................................................................................................... 7
4. Operation.......................................................................................................................................................................... 8
4.1 Operation and Service Locations ...................................................................................................................................8
4.2 Application............................................................................................................................................................. …..9
4.3 Recommended Fuel ....................................................................................................................................................... 9
4.4 Before Starting............................................................................................................................................................... 9
4.5 Starting........................................................................................................................................................................ ..9
4.6Use of control instrument ............................................................................................................................................ 10
4.7 Stopping/Parking ..........................................................................................................................................................11
4.8 Direction and Speed.................................................................................................................................................... 12
4.9 Braking Machine ......................................................................................................................................................... 12
4.10 Vibration.................................................................................................................................................................... 12
4.11 Vibration.................................................................................................................................................................... 13

4.12 Watering System....................................................................................................................................................... 13
4.13 Articulation Joint Lockarm..........................................................................................................................................13
4.14 Adding Ballast to Rear Dru ........................................................................................................................................ 13
4.15 Hour Meter / Tachometer ......................................................................................................................................... 14
4.16 Operation on Slopes.................................................................................................................................................. 14
4.17 Battery Disconnect.................................................................................................................................................... 14
5. Maintenance ................................................................................................................................................................. 14
5.1 Engine Maintenance.................................................................................................................................................... 14
5.2 Maintenance Schedule................................................................................................................................................ 16
5.3 Fuel Filter .................................................................................................................................................................... 16
5.4 Engine Oil Drain........................................................................................................................................................... 17
5.5 Engine Oil .................................................................................................................................................................... 17
5.6 Spark Plug................................................................................................................................................................... 18
5.7 Air Cleaner (Honda)..................................................................................................................................................... 18
5.8 Carburetor................................................................................................................................................................... 19
5.9 Scraper Bars................................................................................................................................................................ 19
5.10 Grease Fittings.......................................................................................................................................................... 20
5.11 Hydraulic System Cleanliness................................................................................................................................... 20
5.12 Hydraulic Oil Requirements....................................................................................................................................... 21
5.13 Hydraulic Oil Level .................................................................................................................................................... 21
5.14 Suction Filter............................................................................................................................................................. 22
5.15 Changing Hydraulic Oil & Filter ................................................................................................................................. 22

5.16 Bleeding the Hydraulic System ................................................................................................................................. 22
5.17 Parking Brake Adjustment ........................................................................................................................................ 23
5.18 Throttle Solenoid Adjustment ................................................................................................................................... 23
5.19 Lifting Machine ......................................................................................................................................................... 24
5.20 Transporting Machine............................................................................................................................................... 24
5.21 Storage...................................................................................................................................................................... 24
5.22 Towing ...................................................................................................................................................................... 25
5.23 Electrical Schematic.................................................................................................................................................. 25
5.24 Wire Colors................................................................................................................................................................ 25
6. Front-wheel assembly................................................................................................................................................... 22
7. Control parts ................................................................................................................................................................. 23
8.Fuel tank assembly and other accessory....................................................................................................................... 23
9.Water tank assembly...................................................................................................................................................... 24
10.Rear frame assembly ................................................................................................................................................... 24
11.Steering system assembly........................................................................................................................................... 24
12.Front frame assembly .................................................................................................................................................. 25
13. Hydraulic tube............................................................................................................................................................. 25
14. Hydraulic tube............................................................................................................................................................. 25
15. Hydraulic tube............................................................................................................................................................. 24
16.Hydraulic tube.............................................................................................................................................................. 24

WWW.TMGINDUSTRIAL.COM 1 /48 Toll Free:1-877-761-2819
1. FOREWORD
Thanks for purchasing our product!
This manual provides information and procedures to safely operateand maintain this TMG model. For your own safety
and protectionfrom injury, carefully read, understand and observe the safetyinstructions described in this manual.
Keep this manual or a copy of it with the machine. If you lose thismanual or need an additional copy, please contact TMG
Corporation. This machine is built with user safety in mind; however,it can present hazards if improperly operated and
serviced. Followoperating instructions carefully! If you have questions about operatingor servicing this equipment,
please contact TMG Corporation.The information contained in this manual was based on machines inproduction at the
time of publication. TMG Corporation reserves theright to change any portion of this information without notice.All rights,
especially copying and distribution rights are reserved.No part of this publication may be reproduced in any form or by
anymeans, electronic or mechanical, including photocopying, withoutexpress written permission from TMG
Corporation.Any type of reproduction or distribution not authorized by TMG Corporation represents an infringement of
valid copyrights and will beprosecuted. We expressly reserve the right to make technicalmodifications, even without due
notice, which aim at improving ourmachines or their safety standards.
2. SAFETY INFORMATION
This manual contains DANGER, WARNING, CAUTION, and NOTEcallouts which must be followed to reduce the possibility
of personalinjury, damage to the equipment, or improper service.
NOTE is the safety alert symbol. It is used to alert you to potential
NOTE personal injury hazards. Obey all safety messages that followthissymbol to avoid possible injury
or death.
DANGER indicates a hazardous situation which, if not avoided.
DANGER will result in death or serious injury.
WARNING indicates a hazardous situation which, if not avoided.
WARNINGcould result in death or serious injury.
CAUTION indicates a hazardous situation which, if not avoided,
CAUTION could result in minor or moderate injury.
CAUTION indicates a hazardous situation which, if not avoided,
CAUTION could result in minor or moderate injury.
CAUTION: Used without the safety alert symbol, CAUTION indicates potentially hazardous situation
which, if not avoided, may result in property damage.
Note: Contains additional information important to a procedure

WWW.TMGINDUSTRIAL.COM 2 /48 Toll Free:1-877-761-2819
2.1 Operating Safety
FAMILIARITY AND PROPER TRAINING ARE REQUIRED FOR THE SAFE OPERATION OF EQUIPMENT.
WARNING Equipment operated improperly or by untrained personnelcan be dangerous. Read the
operating instructions contained in boththis manual and the engine manual and familiarize yourself with
thelocation and proper use of all controls. Inexperienced operators shouldreceive instruction from
someone familiar with the equipment beforebeing allowed to operate the machine.
2.1.1 ALWAYS read, understand, and follow procedures in the Operator’s Manual before attempting to operate the
equipment.
ALWAYS disengage and stow the locking bar for the articulated steering joint before operating the machine. The
machine cannot be steered when the locking bar is engaged.
2.1.2 ALWAYS check that all controls are functioning properly immediately after start-up!
DO NOT operates the machine unless all controls operate correctly.
2.1.3 ALWAYS remain aware of changing positions and the movement of other equipment and personnel on the job site.
2.1.4 ALWAYS remain seated at all times while operating the machine
2.1.5 ALWAYS remain aware of changing surface conditions and use extra care when operating over uneven ground, on
hills, or over soft or coarse material. The machine could shift or slide unexpectedly.
2.1.6 ALWAYS use caution when operating near the edges of pits, trenches or platforms. Check to be sure that the
ground surface is stable enough to support the weight of the machine with the operator and that there is no danger of the
roller sliding, falling, or tipping.
2.1.7 ALWAYS wear protective clothing appropriate to the job site when operating equipment.
2.1.8 ALWAYS keep hands, feet, and loose clothing away from moving parts of the machine.
2.1.9 ALWAYS read, understand, and follow procedures in the Operator’s manual before attempting to operate the
equipment.
2.1.10 ALWAYS stores the equipment properly when it is not being used. Equipment should be stored in a clean, dry
location out of the reach of children.
2.1.11ALWAYS operates the machine with all safety devices and guards in place and in working order.
2.1.12 NEVER allows anyone to operate this equipment without proper training. People operating this equipment must be
familiar with the manual.

WWW.TMGINDUSTRIAL.COM 3 /48 Toll Free:1-877-761-2819
2.1.13 NEVER touches the engine or muffler while the engine is on or immediately after it has been turned off. These
areas get hot and may cause burns.
2.1.14 NEVER uses parts or accessories not recommended by TMG as this may result in damage to the equipment and
injury to the user.
2.1.15 NEVER leave machine running unattended.
2.1.16 NEVER operate the machine with the fuel cap loose or missing.
2.2 Operator safety while using internal combustion engines
Internal combustion engines present special hazards during
DANGER operation and fueling. Read and follow the warning instructions in the engineowner’s manual
and the safety guidelines below. Failure to follow thewarnings and safety guidelines could result in
severe injury or death.
2.2.1 DO NOT smoke while operating the machine.
2.2.2 DO NOT smoke when refueling the engine.
2.2.3 DO NOT refuel a hot or running engine.
2.2.4 DO NOT refuel the engine near an open flame.
2.2.5 DO NOT spill fuel when refueling the engine.
2.2.6 DO NOT run the engine near open flames.
2.2.7 DO NOT run the machine indoors or in an enclosed area such as deep trench unless adequate ventilation, through
such items as exhaust fans or hoses, is provided. Exhaust gas from the engine contains poisonous carbon monoxide gas;
exposure to carbon monoxide can cause loss of consciousness and may lead to death.
2.2.8 ALWAYS refill the fuel tank in a well-ventilated area.
2.2.9 ALWAYS replace the fuel tank cap after refueling.
2.2.10ALWAYS keep the area around a hot exhaust pipe free of debris toreduce the chance of an accidental fire.
2.3 Service safety
Poorly maintained equipment can become a safety hazard! In
WARNING order for the equipment to operate safely and properlyover long period of time, periodic
maintenance and occasional repairs are necessary.

WWW.TMGINDUSTRIAL.COM 4 /48 Toll Free:1-877-761-2819
2.3.1DO NOT attempt to clean or service the machine while it is running. rotating parts can cause severe injury.
2.3.2DO NOT cranks a flooded engine with the spark plug removed on gasoline-powered engines. Fuel trapped in the
cylinder will squirt out the spark plug opening.
2.3.3 DO NOT test for spark on gasoline-powered engines if the engine is flooded or the smell of gasoline is present. A
stray spark could ignite the fumes.
2.3.4 DO NOT use gasoline or other types of fuels or flammable solvents to clean parts, especially in enclosed areas.
Fumes from fuels and solvents can become explosive.
2.3.5 DO NOT modify the equipment without the express written approval of the manufacturer.
2.3.6 ALWAYS check all external fasteners at regular intervals.
2.3.6ALWAYS replace worn or damaged components with spare parts designed and recommended by OUR Corporation.
2.3.7 ALWAYS keep the area around the muffler free of debris such as leaves, paper, cartons, etc. A hot muffler could
ignite the debris and start a fire.
2.3.8 ALWAYS replace worn or damaged components with spare parts designed and recommended by TMG Corporation.
2.3.9 ALWAYS disconnect the spark plug on machines equipped with gasoline engines, before servicing, to avoid
accidental start-up.
2.3.10ALWAYS keeps the machine clean and labels legible. Replace all missing and hard-to-read labels. Labels provide
important operating instructions and warn of dangers and hazards.
2.3.11 ALWAYS switch off the power supply at the battery disconnect before adjusting or maintaining the electrical
equipment.
2.3.12ALWAYS do Periodic Maintenance as recommended in the Operator’s Manual.

WWW.TMGINDUSTRIAL.COM 5 /48 Toll Free:1-877-761-2819
2.4 Safety Labels
TMG machines use international pictorial labels where needed.
These labels are described below:
Ref.
Label
Meaning
A
CAUTION!
Lifting point
B
CAUTION!
Lifting point
C
Hydraulic oil reservoir fill tube
D
Hydraulic oil drain
E
Hydraulic oil reservoir level

WWW.TMGINDUSTRIAL.COM 6 /48 Toll Free:1-877-761-2819
3. TECHNICAL DATA
3.1 Roller
Item No.
TMG-MVR50
Roller
Weight kg
1500
Water Tank Capacity L
150
Outside Turning Radius m
2.7
Forward /Reversem /S
0–126
Gradeability%
25
Vibration Frequency Hz (vpm)
60 (3600)
Exciting force
30KN
3.2 Engine
Item No.
TMG-MVR50
Engine
Engine Type
4-stroke, 2 cylinder, air cooled
Engine Make
Honda
Engine Model
GX 630
Rated Power kW (hp)
13.4 (18)
Displacement cm³(in³)
614 (37.5)
Spark Plug
(NGK) BPR6ES / (NGK) BPR6ESHigh Heat
Electrode Gapmm (in)
0.71–0.79 (0.028–0.031)
Engine Speed—full loadrpm
Engine Speed—idlerpm
3200
1800
Valve Clearance (cold)
intake:mm (in.)
exhaust: mm (in.)
0.10–0.16 (0.004–0.006)
0.10–0.16 (0.004–0.006)
Battery V
12 VDC
Air Cleaner type
Dual Element
Fuel type
Regular Unleaded Gasoline
Fuel Tank Capacity L
28
Fuel Consumption L/hr.
4.6

WWW.TMGINDUSTRIAL.COM 7 /48 Toll Free:1-877-761-2819
3.3 Lubrication
Item No.
TMG-MVR50
Lubrication
Engine Lubrication type
SAE 10W30 Class SG, SF, or SE rated
Hydraulic System type
Premium grade, Anti-wear hydraulic fluid 10W30
Exciter type
Wheel Bearing Grease Filmed EMB type
Rear Drum Drive type Bearing
qty
Shell alvania RL2 Grease (1 grease fitting)
2–3 shots with hand-held grease gun
Front Drum Drive type
Bearing
Sealed Bearings—No lubrication required
Articulated Joint type
qty
Shell Alvania RL2 Grease
2–3 shots with hand-held grease gun
4. OPERATION
4.1 Operation and Service Locations
Ref.
Description
Ref.
Description
1
Front wheel
15
Mud scraping board
2
Motor
16
Fixed pin of Mud scraping board
3
Mud scraping board
17
Hinge assembly

WWW.TMGINDUSTRIAL.COM 8 /48 Toll Free:1-877-761-2819
4
Front frame
18
Cleaning hole
5
Machine cover
19
Fixed pin of Mud scraping board
6
Air door
20
Mud scraping board
7
Direction assembly
21
Working lamp
8
Spraying time setting
22
Key
9
Forward/reverse
23
Rain cover
10
ROPS
24
Accelerator
11
Water tank
25
Rear wheel vibration motor
12
Rear frame
26
Connect plate of front/rear frame
13
Fixed pin of Mud scraping board
27
Seat
14
Mud scraping board
28
Vibration switch
4.2 Application
This machine is designed as a lightweight roller to be used in the compaction of sublayers and finish layers of asphalt on
roads, driveways, parking lots, and other types of asphalt-covered surfaces. Do not use this machine for any other
purpose.
4.3 Recommended Fuel
The engine requires regular grade unleaded gasoline. Use only fresh,cleangasoline.Gasoline containing water or dirt will
damage fuelsystem.
Consult engine Owner’s Manual for complete fuelspecifications.
4.4 Before Starting
Before starting the machine check the following:
• Engine oil level
• Hydraulic fluid level
• Condition of fuel lines
• Condition of air cleaner
• Operation of the brake system
• Fuel level
• Scraper bars are clean and properly adjusted
• Water level
Note: All fluid levels should be checked with the machine on a levelsurface.that regular maintenance has been carried
out.hat the driver's platform is clean.
Always use the steps and handrails when climbing on and off themachine.
4.5 Starting

WWW.TMGINDUSTRIAL.COM 9 /48 Toll Free:1-877-761-2819
4.5.1 If the engine is cold, place the choke lever in the closed position.If the engine is warm, place the choke control in
the open position.
4.5.2 Set the forward/reverse control in the neutral position.
Note: The roller will not start unless the forward/reverse control is inneutral.
4.5.3 Check the parking brake.
4.5.4 Turn the ignition switch to start the engine. Turn off vibration.
4.6 Use of control instrument
4.6.1 Integration functions of instrument panel
See the follow picture, the function: Battery voltage alarm, work time, fuel display, water spray switch, working lamp
switch, e-stop button, etc.
4.6.2 Explanation of function
1) Low voltage warning
If the system voltage is lower than standard voltage,the red warning will light on continuity.
2) Timer
After engine starting, the machine starts to timing, and engine stop, the timing stop.

WWW.TMGINDUSTRIAL.COM 10 /48 Toll Free:1-877-761-2819
3) Fuel level gauge
Show the fuel level real-time
4) Charge fault warning
Before engine start, the light is on. And after engine start, the light is off. When charging line is fault, the light is on.
5) Neutral position warning
When the light is on, the forward/ backward handle is not in neutral position, and can’t start engine. When the light is
off, and then can start the engine.
6) Seat indicator light
When the light is off, and then can start the engine. Operator can’t leave the seat, or the engine will shut down.
7) Cooling indicator light
When the hydraulic oil temperature is over 65 °, cooling fan open. When the oil temperature is less than 55 °, cooling
fan shut. Cooling fan open, the indicator light is on.
8) Rotate speed meter
Show the rotate speed of engine
9) Time of spray on/off
Set the time of spray on and off, and can come true interval spray water.
This machine is with function of spray time and interval adjustment at random. Double time is controlled by panel spray
on and off. The time can be adjusted according to the construction requirements. Meet the construction requirements
and save water.
Note: Press the “Menu key”, “Time of spray on” start to flash, then press “Adjust key” to adjust time. Then press again the
“Menu key”,“Time of spray on” set up and stored in the system.
At same time, “Time of spray off” start to flash, and then press the “Menu key” third time, “Time of spray off”
set up and stored in the system. The light flash 10 seconds, if don’t operate within 10 seconds, will store to
system automatically and stop flash.
If any fault lights on, the buzzer will ring. Please check the machine faults.
10) Spray water switch
11) Working lamp switch
It controls the on/off of working lamp. Open the working lamp when night construction.
12) E-stop button
When press down the e-stop button, forward/backward stop, vibration stop, and engine stops
4.7 Stopping/Parking
4.7.1 Turn vibration off.
4.7.2 Close both watering valves.

WWW.TMGINDUSTRIAL.COM 11 /48 Toll Free:1-877-761-2819
4.7.3Return the engine throttle to idle by pressing the throttle switch,and allowthe engine to cool down.
4.7.4Stop the engine by turning the ignition switch to OFF.
4.7.5 Set the parking brake. Alwaysset the parking brake before leaving the machine.
Note:
The parking brake engages the rear drum only
.
CAUTION: Avoid parking the roller on a hill or an incline. If the rollermust be parked on a hill, block the drums in addition
to setting thebrake to prevent the roller from moving.
4.8 Direction and Speed
The forward/reverse lever controls both the direction and speed of theroller. Use the control lever, rather than the throttle,
to control thespeed of the machine while compacting.Daily, before operating, check the machine for
drift
(movement
with theforward/reverse control in the NEUTRAL position) and adjust asneeded. See section
Adjusting the Drive Control
Cable
.
Speed is controlled by the amount the lever is moved in the directionof travel—forward or reverse.
While operating the machine, run it at full throttle. To run the machineat full throttle, press and release the throttle switch.
This ensuresmaximum travel speeds and will produce the best compaction results.Operating the machine at slower
engine speeds will reducecompaction, slow down machine functions, and damage hydrauliccomponents.
4.9 Braking Machine
The machine will brake automatically when the control lever is returnedto neutral. If the machine continues to drift, shift
the control leverslightly in the opposite direction to stop movement and then return thelever to neutral. If the machine will
not remain stationary in neutral,adjust it.
Emergency stop pushbutton
When pushed, the emergency stop pushbutton not only stops all travel(either forward or reverse) and applies the brake,
but also stops excitervibration.
4.10 Vibration
CAUTION: If the machine has been turned off with the vibration on, thevibration will come on as soon as the machine is
restarted. Therefore,for easier starting and to keep the surface finish smooth, be ready toswitch vibration off should it
come on while cranking the engine.
4.11 Watering System
The watering system is controlled by two valves, one for each drum.
The valve handles are located to the right of the operator. Rotatethe valve handles to control the amount of water being
applied to thedrum.
4.12 Articulation Joint Lockarm
A lockarm, located above the articulated joint, is provided to securethe front and rear halves of the roller together. Once
secured, thelockarm prevents the two halves from swinging together.
To avoid being pinched by machine halves, set the lockarm

WWW.TMGINDUSTRIAL.COM 12 /48 Toll Free:1-877-761-2819
WARNINGbefore lifting the machine for transport or repairs!
To set lockarm, release it from its holder and swing it out from its storedposition. Place theforward
end of the arm into the hole provided in thefront frame of the machine. Secure it in this position using
the largehairpin cotter provided.
4.13 Adding Ballast to Rear Drum
The rear drum can be filled with ballast to provide additional weight.Add ballast through plug opening.If water is used as
ballast, add antifreeze or drain drum after use, inareas where temperatures are below freezing.
4.14 Roll Over Protection Structure (ROPS)
The machine is fitted with a Roll Over Protection Structure (ROPS).
The machine is normally delivered to the customer with the ROPSfolded forward to facilitate transport.
Before using the machine, position the ROPS in the fully uprightposition as follows:
4.14.1Support the ROPSusing a crane and suitable rigging capable of
supporting 48 kg. (105 lbs.), or two individuals capable of supportingthe ROPS.
4.14.2 Loosen the screws(one on each side) without removing them.
4.14.3 Raise the ROPS to the upright position.
4.14.4 Insert the screws into the holesand torque all screws to 120 Nm
(88 ft.lbs.).
4.14.5 Remove the rigging from the ROPS.
CAUTION: Do not use the ROPS to lift the machine.
WARNING Each month, check that the screws holding the ROPS in place aretight. Check that the ROPS
frame is not rusty, cracked, broken ordamaged in any way.
If the frame has been removed from the machine, it must be reinstalledbefore the machine is used. When reinstalling a
safety frame, use theoriginal nuts and bolts.
Keep the safety frame upright when working with the roller, and
WARNING use the safety belt provided.
4.15 Hour Meter / Tachometer
The hour meter/tachometeris located on the steering column.When the engine is running, it acts as a tachometer. When
the engineis shut down, it records the actual running time of the engine. Use then hour meter when planning scheduled
maintenance.
4.16 Operation on Slopes
When operating on slopes or hills special care must be taken to reducethe risk of personal injury or damage to the
equipment. Alwaysoperate the machine up and down hills rather than from side to side.For safe operation and for
protection of the engine, continuous dutyuse should be restricted to front/rear slopes of 17°(30% grade) or less.

WWW.TMGINDUSTRIAL.COM 13 /48 Toll Free:1-877-761-2819
NEVER operate machine on side slopes. The machine may roll
WARNING over,even on stable ground.
4.17Battery Disconnect
Isolate the battery using this switch before performing any
WARNING maintenance operations on electrical equipment.
5. Maintenance
5.1 Engine Maintenance
•The chart below lists basic engine maintenance.Refer to the enginemanufacturer’sOperation Manual for additional
information on enginemaintenance.
Honda
Daily
before
starting
After
first
20 hrs.
Every
50
hrs.
Every
100
hrs.
Every
300
hrs.
Check fuel level.
●
Check engine oil level.
●
Inspect air filter. Replace as needed
●*
Change engine oil and filter.
●
●
Clean air cleaner.
●*
Check and clean spark plug.
●
Clean sediment cup.
●
Check and adjust idle speed
●**
Check and adjust valve clearances
●**
Replace fuel filter.
●**
•Service more frequently in dusty conditions.
•These items should be serviced by an authorized Honda dealer, unless the owner has the proper tools and is
mechanically proficient. See Honda shop manual.
Vanguard
Daily
before
starting
After
first
20 hrs.
Every
50
hrs.
Every
100
hrs.
Every
300
hrs.
Check fuel level.
●
Check engine oil level.
●

WWW.TMGINDUSTRIAL.COM 14 /48 Toll Free:1-877-761-2819
Change engine oil.
●
●
Change oil filter.
●
Clean air cleaner.
●
Check and clean spark plug.
●
Check and adjust valve clearances.
●
Replace fuel filter.
●
5.2 Maintenance Schedule
TMG-MVR50
Daily
before
starting
Every
100
hrs.
Every
600
hrs.
Every
1200
hrs.
Check external hardware.
●
Check level of hydraulic fluid.
●
Grease articulated joint.
●
Grease rear drum drive bearing.
●
Grease exciter bearing.
●
Change hydraulic system return line filter.
●
Check and adjust scraper bars.
●
Clean battery terminals.
●
Change hydraulic oil.
●
Periodically:
• Check operation of the parking brake, making sure it engages.
• Check for leaks around hydraulic hoses and connections.
• Clean engine exterior, cooling fins, and blower housing.
• Check electrical wiring and connections.
New machines:
• Change the engine oil per engine schedule.
• Replace the hydraulic system return line filter after the firstmonth or 100
hours of operation.
5.3 Fuel Filter

WWW.TMGINDUSTRIAL.COM 15 /48 Toll Free:1-877-761-2819
Change the in-line fuel filteronce per year. Check the fuel lines andfittings daily for cracks or leaks. Replace as needed.
Gasoline is extremely flammable! Turn the engine off and allow theengine to cool before replacing the fuel filter.
Note: The fuel filter is located under the floor panel of the
WARNINGoperatingplatform.Replace the oil filter after every 200
hours of operation.
To change the filter:
5.3.1Drain the engine oil. See Engine Oil. Remove the used filter.
5.3.2 Before installing a new filter, lightly oil the filter gasket with fresh,clean
engine oil. Screw the filter on by hand until gasket makescontact; then
tighten an additional 7/8 turn.
5.3.3 Fill the engine with the recommended oil. See Engine Oil.
5.3.4 Start and run the engine to check for leaks. Stop the engine. Recheck
the oil level and add oil if required. Refer to the engine owner’s manual.
5.4 Engine Oil Drain
The engine oil drain has been routed to the outside of the front halfof the
TMG-MVR50. This is to make draining easier and to help keep theengine
compartment clean.
5.5 Engine Oil
5.5.1Drain the oil while the engine is still warm. To drain the oil:
Remove the filler cap drain screw, and washer. Drain the oil into asuitable
container.
Note: In the interests of environmental protection, place a plastic sheet and a
container under the machine to collect any liquid which drains off. Dispose
of this liquid in accordance with environmental protection legislation.
5.5.2 Re-insert the drain screw and washer and tighten the screw securely.
5.5.3 Fill the engine with the recommended oil to the upper limit mark on the
dipstick. See Technical Data for correct oil type and amount.
Burn hazard! Care must be taken when draining hot engine oil.

WWW.TMGINDUSTRIAL.COM 16 /48 Toll Free:1-877-761-2819
WARNING Hot oil can burn!
5.6 Spark Plug
•Clean or replace the spark plug as needed to ensure proper operation. Refer
to the engine owner’s manual.
The muffler becomes very hot during operation and remains hot
WARNING for a while after stopping the engine. Do not touch the
muffler while it is hot.
Note: Refer to the Technical Data for the recommended spark plug type and the
electrode gap setting.
5.6.1 Remove the spark plug and inspect it.
5.6.2 Replace the spark plug if the insulator is cracked or chipped.
5.6.3 Clean the spark plug electrodes with a wire brush.
5.6.4 Set the electrode gap .
5.6.5 Tighten the spark plug securely.
CAUTION: A loose spark plug can become very hot and may cause engine
damage.
5.7 Air Cleaner (Honda)
The Honda engine is equipped with a dual-element air cleaner.
To service:
5.7.1 Remove the wing bolt and cover。
5.7.2 Remove the 5 mm screws from the cover and remove paperelement from
the cover.
5.7.3To clean the paper element, tap it lightly on a flat surface. Replace thepaper
element if it is damaged or heavily soiled. Reassemble the paperelement
to the cover. Include the gaskets .
5.7.4 To clean the foam element, wash it in liquid detergent and water.
Table of contents
Other TMG Construction Equipment manuals
Popular Construction Equipment manuals by other brands

Broderson
Broderson IC-250-3E Operation and maintenance manual
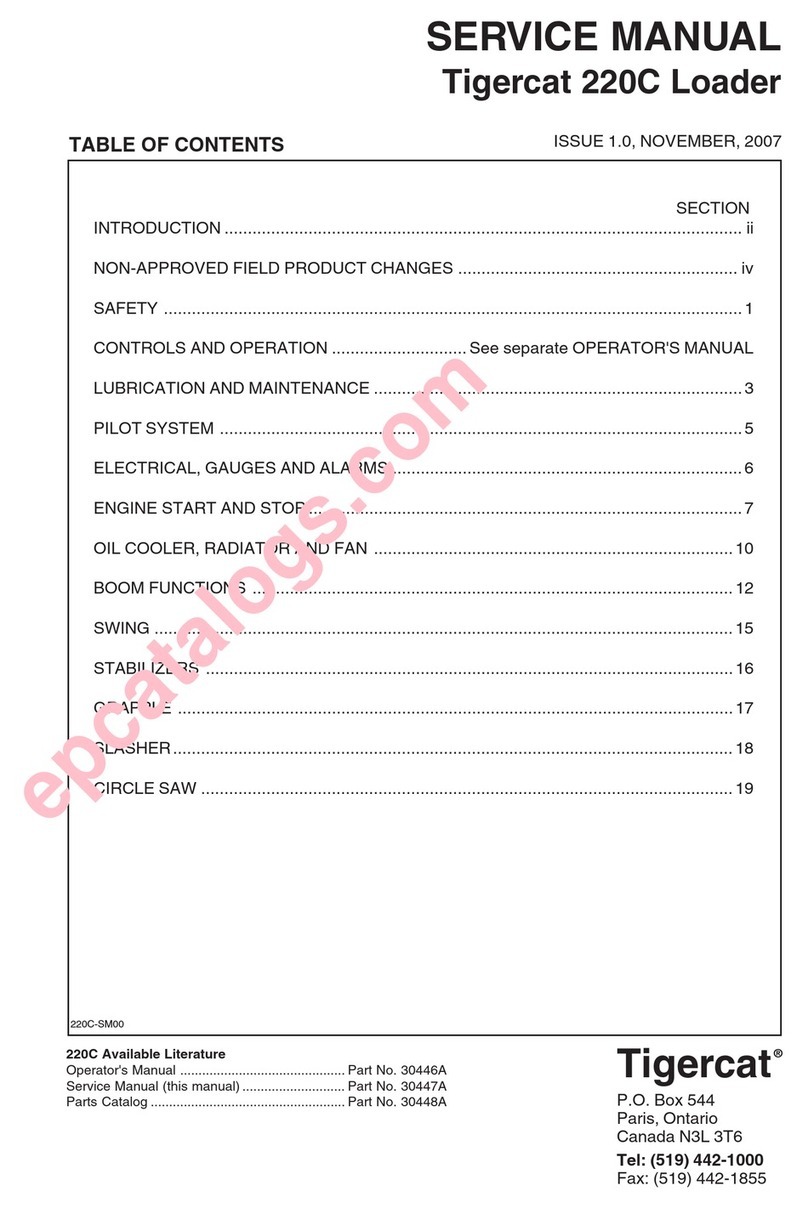
Tigercat
Tigercat 220C Service manual
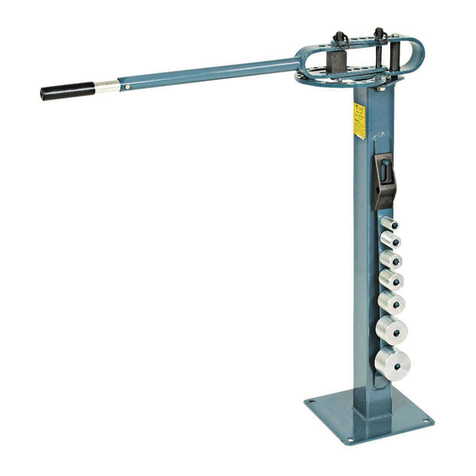
Central Machinery
Central Machinery 38470 Owner's manual & safety instructions
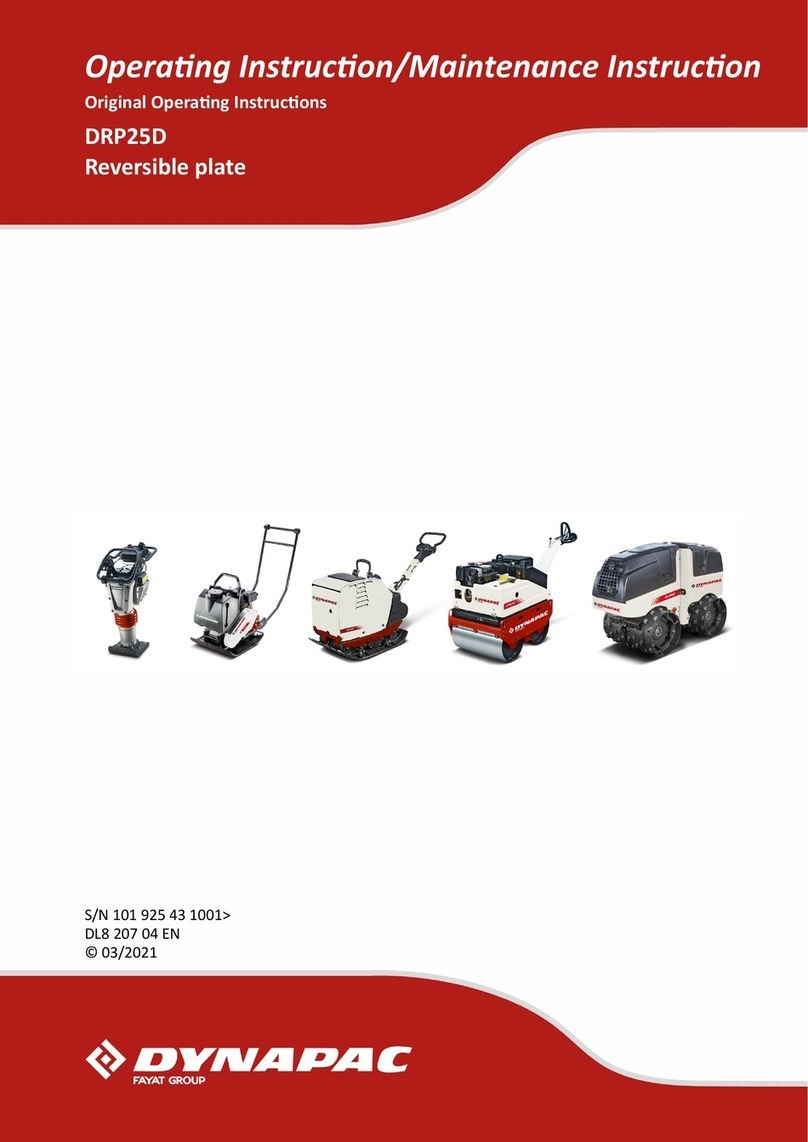
Fayat Group
Fayat Group DYNAPAC DRP25D Original operating instructions

MULTIQUIP
MULTIQUIP Stow MS-93 Operation and parts manual

Fayat Group
Fayat Group Dynapac SD2500C operation & maintenance