Toku TNB-08M User manual

Unsafe use of this machine may cause serious injury of death.
Operators and maintenance personnel must read this manual
before operating or maintaining this machine. This manual should
be kept near the machine for reference and periodically reviewed
by all personnel who will come into contact with it.
Hydraulic Breaker
TNB-08M
TNB-6M
TNB-27K/190LU2
TNB-1M
TNB-6E
TNB-230LU2
TNB-2M
TNB-7J
TNB-310LU1
TNB-3MB
TNB-16K/110
TNB-60K/400LU2
TNB-4M
TNB-141LU
TNB-5M
TNB-151LU2
M A N U A L
INSTRUCTION MANUAL
TOKU PNEUMATIC CO., LTD.
No.17
WARNING

●FOREWORD
Thank you very much for your purchasing of a Toku hydraulic breaker,
This instruction manual is a guidebook to the TOKU Hydraulic Breaker as well as helps deepen
your understanding of Toku hyd, breaker better for those who own a TNB breaker. Before
operating the Breaker, operators and maintenance personnel should read this manual carefully
making sure that they understand the contents. Keep this manual handy and ensure all
personnel read it periodically.
The TOKU Hydraulic Breaker is fitted to a hydraulic excavator as an attachment and this manual
is considered to be used together with an excavator manual. Therefore this must be kept together
with your hydraulic excavator manual.
WARNING
Improper operation can be hazardous and could result in serious injury or death.
Operators and maintenance personnel should read this manual carefully
before operating or maintaining this machine and always keep it near the
machine. All involved personnel should read it periodically.
●Do not operate the product unless you understand and comply with the contents of
the instruction manual.
●Operators and maintenance personnel should read this manual periodically
and always keep it handy.
● If this manual is lost or becomes damaged, ask for a manual at TOKU
Pneumatic Co., Ltd or a Toku distributor nearby by ordering.
●If you transfer the breaker to another source, make sure that you give this manual to
the new owners.
●When you rent this breaker, make sure that this manual must be handed over
to a user.

CONTENTS
●INTRODUCTION
0-1
Safety information
・・・・・・・・・・・・・・
1
0-2
Applying works
・・・・・・・・・・・・・・
2
0-3
Operation and qualifications
・・・・・・・・・・・・・・
2
●SAFETY
1-1
General precautions for safety
・・・・・・・・・・・・・・
3
1-2
Safety operation
・・・・・・・・・・・・・・
5
1-3
Precaution for maintenance
・・・・・・・・・・・・・・
7
1-4
Precautions for lifting the hydraulic breaker
・・・・・・・・・・・・・・
9
●OPERATION
2-1
Specifications
・・・・・・・・・・・・・・
10
2-2
Principle operation
・・・・・・・・・・・・・・
14
2-3
Structure
・・・・・・・・・・・・・・
16
2-4
Piping for the hydraulic breaker
・・・・・・・・・・・・・・
20
2-5
Grease selection and control
・・・・・・・・・・・・・・
22
2-6
Installation of the hydraulic breaker onto the
excavator
・・・・・・・・・・・・・・
24
2-7
Installation of chisel
・・・・・・・・・・・・・・
26
2-8
Replacement of chisel
・・・・・・・・・・・・・・
31
2-9
Lubrication of chisel
・・・・・・・・・・・・・・
36
2-10
Inspection prior to operation
・・・・・・・・・・・・・・
38
2-11
Test run
・・・・・・・・・・・・・・
39
2-12
Operation of hydraulic breaker
・・・・・・・・・・・・・・
41
2-13
Precautions during operation
・・・・・・・・・・・・・・
43
2-14
Dismantling the breaker
・・・・・・・・・・・・・・
46
2-15
Storage of the breaker
・・・・・・・・・・・・・・
49

●MAINTENANCE AND INSPECTION
3-1
Daily check ・ periodic inspection ・ regular
maintenance
・・・・・・・・・・・・・・
54
3-2
Inspection for looseness and retightening of
bolts and nuts
・・・・・・・・・・・・・・
58
3-3
Inspection of retainer pins
・・・・・・・・・・・・・・
75
3-4
Inspection of chisel bushing wear
・・・・・・・・・・・・・・
77
3-5
Inspection of chisel wear
・・・・・・・・・・・・・・
80
3-6
Inspection of chisel holder bushing wear
・・・・・・・・・・・・・・
85
3-7
Inspection of nitrogen gas pressure and
recharge
・・・・・・・・・・・・・・
87
3-8
Inspection and maintenance of the bracket
plastic and resin parts
・・・・・・・・・・・・・・
92
3-9
Replacement of oil filter element
・・・・・・・・・・・・・・
103
3-10
Change the hydraulic oil in the tank
・・・・・・・・・・・・・・
103
●SPECIAL APPLICATION
4-1
Under water application
・・・・・・・・・・・・・・
104
4-2
Tunnel application
・・・・・・・・・・・・・・
104
●TROUBLE SHOOTING GUIDE
5-1
Oil leakage
・・・・・・・・・・・・・・
105
5-2
Nitrogen gas leakage
・・・・・・・・・・・・・・
107
5-3
Poor operation of breaker
・・・・・・・・・・・・・・
108
●ACCESSORY TOOLS
6-1
Accessory tools
・・・・・・・・・・・・・・
109
6-2
Optional tools
・・・・・・・・・・・・・・
125
●AUTHORIZED DISTRIBUTOR’S RECORD
7-1
Manufacturing serial No. stamping location
・・・・・・・・・・・・・・
127
7-2
Authorized Distributor’s record
・・・・・・・・・・・・・・
127

1
●INTRODUCTION
0-1. SAFETY INFORMATION
We use our safety messages and labels in following way in order for you to understand
the manual and the safety labels better.
TOKU cannot predict every circumstance that might involve a potential hazard in operation and
maintenance. Therefore the safety message in this manual and on the machine may not include
all possible safety precautions.
DANGER: If not avoided, result in death or serious injury.
WARNING: This word is used on safety messages and safety labels where there
is a potentially dangerous situation which could result in serious injury
or death if the hazard is not avoided. These safety messages or labels
usually describe precautions that must be taken to avoid the hazard.
Failure to avoid this hazard may also result in serious damage to the
machine
CAUTION: This word is used on safety messages and safety labels for hazards,
which could result in minor or moderate injury if the hazard is not avoid.
This word might also be word for hazards where the only result could
be damages to the machine
★NOTICE This word is used for precautions that must be taken to avoid
actions, which could shorten the life of the machine

2
Never use TNB breakers other than applying works
0-2. APPLYING WORKS
Mainly apply TNB breakers for following works.
・Demolition of Concrete and secondary breaking.
・Demolition of Asphalt and secondary breaking.
・Demolition of Rock.
・Quarry applications.
・Road Construction.
・
・Please consult us in case of tunnel work, under water works, works in extreme heat, cold
or dusty environment or any other ”special application.
0-3. OPERATION AND QUALIFICATIONS
Operators must be trained before operating TOKU BREAKER and must obey all rules at the
worksite and local regulations, which affect the operator and equipment.
WARNING

3
⚫It is essential to wear a hard hat, protective goggles, safety boots, a mask and
gloves.
Especially when operating a mini-excavator where a cabin is not installed on
the machine.
⚫Only trained and authorized personnel can operate and maintain the machine.
⚫Follow all safety rules, precautions and instructions when using the breaker.
⚫Follow the rules for group work when more than 2 people are working together.
●SAFETY
1-1. GENERAL PRECAUTIONS FOR SAFETY
When operating the hydraulic breaker, read the
instruction manual for the hydraulic excavator and
obey the safety requirements.
WARNING -SAFETY RULES AT THE WORK SITE-
WARNING
WARNING -CLOTHING AND PERSONAL PROTECTION ITEMS-
MANUAL

4
⚫When operating a hydraulic breaker, install a front guard on the windscreen. Also place
a laminate coating sheet over the windscreen.
⚫For work in mines, tunnel or other places where there is a danger of falling rocks, fit a
FOPS (falling object protective structure). Also place a laminate coating sheet over the
windscreen.
⚫When operating a breaker, make sure that you close the front window.
⚫During operation, make sure all personnel are out of range of materials, which may fly
up.
The hydraulic breaker contains a high volume of pressurized nitrogen gas. It can
therefore be dangerous if the breaker is not dismantled correctly. As a result, if the
breaker needs service, please contact TOKU or an authorized distributor/ service depot.
⚫Non-approved modifications can cause injury and damage.
⚫Consult your TOKU dealer for advice before making any modifications. TOKU will
not accept responsibility for any injury or damage caused by any unauthorized
modifications.
WARNING -PROTECTION AGAINST FALLING OR FLYING OBJECTS-
WARNING DON’T DISASSEMBLE
WARNING UNAUTHORIZED MODIFICATION
Top guard
Front guard
Laminate coating sheet
FOPS
FOPS ・・・Falling objects protection structure

5
When working on the structure, it may happen collapse
or floor. Check the strength of floor before operation.
Reinforce the floor if it’s necessary.
When working on embankments or near excavated
ditches, there is a hazard that the weight and vibration
of the machine will cause the soil to collapse. Before
starting operations, take steps to ensure that the
ground is safe and to prevent the machine from rolling
over falling.
Before starting operations, thoroughly check the area
for any unusual conditions that could be dangerous.
1-2. SAFETY OPERATION
⚫When carrying out operations near combustible
materials such as thatched roofs, dry leaves or dry grass,
there is a hazard of fire, so be careful when operating.
⚫Check the terrain and condition of the ground at the worksite, and determine the
safest method of operation. Do not operate where there is hazard of landslides
or falling rocks.
WARNING
Safety secure at work site
!
Do not raise up too high.
It may cause damage of excavator or falling accident
when excavator becomes unbalanced after breaking
an object.
WARNING
Do not lift materials with the breaker.
This may cause damage to the breaker and breaker
bracket and is a dangerous maneuver.
WARNING
×
×
WARNING Checking work site
×
WARNING –SAFETY AT JOBSITE-
×

6
When carrying out maintenance of the breaker and you are exposed to noise for long
periods of time, wear ear covers or ear plugs while working.
If the noise from the machine is too loud, it may cause temporary or permanent hearing
problems.
Do not travel or operate the machine near electric cables.There is a hazard of electric shock, which
may cause seriousinjury or property damage. On jobsites where the machine maygo close to electric
cables, always do as follows.Before starting work near electric cables, inform the localpower
company of the work to be performed, and ask them totake the necessary action. Even going close
to high-voltage cables can cause electricshock, which may cause serious burns or even death.
Always maintain a safe distance (see the table on the right) between the machine and the electric
cable. Check with the local powercompany about safe operating procedure before
startingoperations.To prepare for any possible emergencies, wear rubber shoesand gloves. Lay a
rubber sheet on top of the seat, and becareful not to touch the chassis with any exposed part of
yourbody. Use a signalman to give warning if the machine approachestoo close to the electric
cables.When carrying out operations near high voltage cables, donot let anyone near the machine.If
the machine should come too close or touch the electric cable, to prevent electric shock, the
operator shouldnot leave
The operator's compartment until it has been confirmed
That the electricity has been shut off. Also, do not let
anyone near the machine.
Safety distance to high voltage cables
Voltage of cables Safety distance
0 - 60,000V more than 3m
66,000V more than 4m
154,000V more than 5m
500,000V more than 11m
WARNING –DISTANCE TO HIGH VOLTAGE CABLES-
If you find any abnormality in the machine during operation or maintenance (noise, vibration,
smell, incorrect gauges, smoke, oil leakage, etc., or any abnormal display on the warning
devices or monitor), report to the person in charge and have the necessary action taken. Do
not operate the machine until the abnormality has been corrected.
WARNING –IF ABNORMALITIES ARE FOUND-
WARNING –NOISE-

7
It is very dangerous to use worn and broken tools and to misuse tools. Use the proper tools
for maintenance.
Place the hydraulic breaker in a stable and flat place so as to prevent from over turning
Do not remove the hydraulic hose immediately after stopping the hydraulic breaker. The oil
reaches a very high temperature during operation and may possibly cause burns. Remove hose
only when the temperature has dropped. When you leave an abnormal on the hydraulic breaker,
it may cause serious injury. Repair immediately when an abnormal is found.
1-3. PRECAUTION FOR MAINTENANCE
WARNING
WARNING
WARNING Using suitable tools
WARNING Position of the hydraulic breaker
WARNING High temperature oil
×
WARNING
WARNING
The hydraulic breaker is an attachment for the hydraulic excavator. Before maintaining the
hydraulic breaker, read and understand the manual for the hydraulic excavator.
Always wear protection such as hard hat, safety glasses, safety shoes and mask, and
gloves. When tightening the bolt and nut by an impact spanner, debris of metal may fly out
or be scattered. It may cause serious injury for eyes.
When you leave an abnormal on the hydraulic breaker, it may cause serious injury. Repair
immediately when an abnormal is found.
Do not carry out when the hydraulic oil
temperature is high. After operating the breaker
many parts are still hot. If the hose is removed
immediately, it may cause serious burn injury.

8
⚫Carry out maintenance on a flat and solid ground surface.
⚫When the operation is carried out by two or more workers, choose the leader and follow
leaders instructions.
⚫A crane should be used for handling heavy material (over 25 kg)
⚫When using a crane, make sure that the material is well balanced.
⚫Do not work on materials that are being lifted. Put them on a worktable.
⚫
When assembling and disassembling the hydraulic breaker, make sure that the breaker is balanced.
⚫Never remain under material which is being lifted by crane. Keep away from material.
Do not touch the chisel right after operating the hydraulic breaker.
The chisel becomes very hot during operation and you may get burnt.
WARNING
Do not use any other gas except nitrogen gas. If other gases are used, it may explode
and is dangerous.
When filling nitrogen gas, the chisel may suddenly come out. Therefore, keep away from the
chisel when refilling with nitrogen gas.
WARNING
Various parts will be very hot after operation of the engine. Do not change the filter element immediately.
Change the element after the hydraulic oil and various parts have cooled off.
WARNING
Various parts will be very hot after operation of the engine. Do not change the hydraulic oil immediately.
Change the hydraulic oil after the oil and various parts have cooled off.
WARNING
WARNING Use a crane when handling heavy materials
When aligning the pin, do not put your finger or hand into the pin hole. The arm or hydraulic
breaker can move and this may lead to loosing your finger or hand.
WARNING
When hammering the pin, always wear protective goggles, hard hat, gloves, mask and safety boots due
to the possibility that metal chips will fly off and may enter your eye causing serious injury.
WARNING

9
1-4. PRECAUTIONS FOR LIFTING THE HYDRAULIC BREAKER
WARNING
・Crane operation qualification is necessary to do lifting work.
・Do not lift if person is still working on/around the breaker.
・Use appropriate size/diameter/strength of wire rope per breaker weight/model.
・Lift slowly and keep the breaker level & horizontally as shown below.
・Keep away from the lifting area, and Never go underneath the breaker.
Lift the breaker properly & safely as shown below.
There is a risk of losing the balance of the breaker.
CAUTION
Lift the breaker properly & safely as shown below.
Hydraulic hose can be damaged, if breaker is not properly lifted.

10
●OPERATION
2-1. SPECIFICATIONS
Model TNB-
08M
1M
2M
3MB
4M
Working Weight
Side Mount
Bracket
kg
65
85
105
175
235
Top Mount
Bracket 1PC
kg
75
85
110
190
220
Top Mount
Bracket 2PC
kg
75
100
140
210
255
BOX Bracket
kg
85
125
170
250
340
Side Mount
Silenced Bracket
kg
-
-
160
235
285
O i l F l o w
L/min
18~25
20~30
20~35
25~45
30~55
Operating Pressure
MPa
6~13
7~14
8~15
10~15
10~16
Line Relief Pressure
MPa
18
19
20
20
21
C r a c k i n g
P r e s s u r e ( * 1)
MPa
14
at minimum
15
at minimum
16
at minimum
16
at minimum
17
at minimum
I m p a c t R a t e
bpm
930~1300
700~1200
600~1150
550~1000
580~1060
T o o l D i a m e t e r
mm
φ40
φ45
φ50
φ58
φ64
H o s e S i z e
inch
3/8
1/2
1/2
1/2
1/2
Gas Pressure(*2)
MPa
0.8
0.8
0.8
0.8
0.8
B a s e M a c h i n e
ton
0.7~1.5
1~2
1.5~2.5
2.4~4
3~4.5
NOTE) Working Weight does not include bracket bushings and bracket pins.
Always operate the breaker with proper oil flow and working pressure shown above.
*1) Cracking pressure means a pressure observed constant flow after the relief valve starts
opening by the pressure increased at the inlet port of the relief valve.
*2) When the Breaker body temperature is 40℃(104F).

11
SPECIFICATIONS
Model TNB-
5M
6M
6E
7J
Working Weight
Side Mount
Bracket
kg
300
350
430
820
Top Mount
Bracket 1PC
kg
305
365
420
-
Top Mount
Bracket 2PC
kg
315
350
465
-
BOX Bracket
kg
400
440
585
940
Side Mount
Silenced Bracket
kg
-
415
-
910
O i l F l o w
L/min
35~60
40~70
45~80
80~120
Operating Pressure
MPa
10~16
10~16
10~16
14~18
Line Relief Pressure
MPa
21
21
21
23
C r a c k i n g
P r e s s u r e ( * 1)
MPa
17
at munimum
17
at minimum
17
at munimum
19
at minimum
I m p a c t R a t e
bpm
550~1000
600~1050
550~1000
450~720
T o o l D i a m e t e r
mm
φ75
φ75
φ95
φ105
H o s e S i z e
inch
1/2
3/4
3/4
3/4
Gas Pressure(*2)
MPa
0.8
1
0.8
0.9
B a s e M a c h i n e
ton
3.8~6
5.5~8
6~11
8~14
NOTE) Working Weight does not include bracket bushings and bracket pins.
Always operate the breaker with proper oil flow and working pressure shown above.
*1) Cracking pressure means a pressure observed constant flow after the relief valve starts
opening by the pressure increased at the inlet port of the relief valve.
*2) When the Breaker body temperature is 40℃(104F).

12
SPECIFICATIONS
Model TNB-
16K
110
141LU
151LU2
27K
190LU2
Working Weight
Side Mount
Bracket
(Short Skirt)
kg
-
1530
1710
(1680)
-
Top Mount
Bracket 1PC
kg
-
1600
1650
-
Top Mount
Bracket 2PC
kg
1120
1700
1880
-
BOX Bracket
kg
1240
1900
1780
2250
Side Mount
Silenced Bracket
kg
-
-
1810
-
O i l F l o w
L/min
100~140
130~170
160~200
160~210
Operating Pressure
MPa
12~17
13~17
14~18
14~18
Line Relief Pressure
MPa
22
22
23
23
C r a c k i n g
P r e s s u r e ( * 1)
MPa
18
at minimum
18
at minimum
19
at minimum
19
at minimum
I m p a c t R a t e
bpm
430~600
490~650
450~630
370~490
T o o l D i a m e t e r
mm
φ115
φ135
φ135
φ140
H o s e S i z e
inch
3/4
1”(*1)
1"
1"
1"
Gas Pressure(*2)
MPa
0.8
0.8
1.1
0.8
B a s e M a c h i n e
ton
14~20
18~25
18~25
20~30
NOTE) Working Weight does not include bracket bushings and bracket pins.
Always operate the breaker with proper oil flow and working pressure shown above.
(*1) For North American market
*1) Cracking pressure means a pressure observed constant flow after the relief valve starts
opening by the pressure increased at the inlet port of the relief valve.
*2) When the Breaker body temperature is 40℃(104F).

13
SPECIFICATIONS
Model TNB-
230LU2
310LU1
60K
400LU2
Working Weight
Side Mount
Bracket
kg
2530
3370
-
Top Mount
Bracket 1PC
kg
-
-
-
Top Mount
Bracket 2PC
kg
2800
3400
4450
BOX Bracket
kg
2720
3650
5000
Side Mount
Silenced Bracket
kg
-
-
-
O i l F l o w
L/min
180~230
240~300
280~390
Operating Pressure
MPa
13~18
14~18
14~18
Line Relief Pressure
MPa
23
23
23
C r a c k i n g
P r e s s u r e ( * 1)
MPa
19
at minimum
19
at minimum
19
at minimum
I m p a c t R a t e
bpm
350~450
340~470
310~470
T o o l D i a m e t e r
mm
φ146
φ160
φ178
H o s e S i z e
inch
1"
1"-1/4
1"-1/4
Gas Pressure(*2)
MPa
0.8
0.8
0.8
B a s e M a c h i n e
ton
27~40
38~50
45~70
NOTE) Working Weight does not include bracket bushings and bracket pins.
Always operate the breaker with proper oil flow and working pressure shown above.
*1) Cracking pressure means a pressure observed constant flow after the relief valve starts
opening by the pressure increased at the inlet port of the relief valve.
*2) When the Breaker body temperature is 40℃(104F).

14
2-2. PRINCIPLE OPERATION
(1) Upward movement (2) Reversing (3) Downward movement (4) Impact
(1) Upward movement
Oil flows into chambers 1 and 9: the control valve is pressed in the downward direction.
The piston moves in the upward direction toward the cushion chamber 5.
Oil in the opposite chamber 4 is discharged through chamber 6 and 7.
(2) Reversing direction
When the lower flange fills with oil, it reaches chamber 2. At this point both chamber 8 and
9 exert the same pressure on the flange but the control valve moves in the upward direction
due to the area difference between the flanges.
(3) Downward movement
When the control valve rises and reaches chamber 9, the flow moves through chamber 6 then
4.
Due to the difference in area between the piston flange and the force from the cushion
chamber 5 pressures, the piston accelerates downwards.
(4) Impact
The piston hits the chisel. At this point the mid-section of the piston reaches chamber 2 and
as a result chamber 8 releases the pressure through chamber 2 and 3.
When chamber 8 is empty, as chamber 9 is constantly pressurized, the valve moves in the
downward direction.
Repetition of the cycle mentioned above results in continuous blows.
TNB-08M, 1M, 2M, 3MB, 4M, 5M

15
(1) Upward movement (2) Reversing (3) Downward movement (4) Impact
(1) Upward movement
Oil flows into chambers 1 and 8: the control valve is pressed in the downward direction.
The piston moves in the upward direction toward the cushion chamber 5.
Oil in the opposite chamber 4 is discharged through the control valve into chamber 7.
(2) Reversing direction
When the lower flange fills with oil, it reaches camber 2. At this point both chamber 6 and 8
exert the same pressure on the flange but the control valve moves in the upward direction
due to the area difference between the flanges.
(3) Downward movement
When the control valve rises and reaches chamber 8, the flow moves through control valve
and reaches chamber 4.
Due to the difference in area between the piston flange and the force from the cushion
chamber pressure, the piston accelerates downwards.
(4) Impact
The piston hits the chisel. At this point the mid-section of the piston reaches chamber 2 and
as a result chamber 6 releases the pressure through chamber 2 and 3.
When chamber 6 is empty, as chamber 8 is constantly pressurized, the valve moves in the
downward direction.
Repetition of the cycle mentioned above results in continuous blows.
TNB-6M, 6E, 7J, 16K/110, 141LU, 151LU2,
27K/190LU2, 230LU2, 310LU1, 60K/400LU2

16
2-3. STRUCTURE
(13) Piston
(14) Oil Seal
(15) Dust Seal
(16) Air Port for Air Supply (TNB-2M, 3MB, 4M, 5M)
(17) Chisel Holder
(18) Retainer Pin
(19) Retainer Pin Stopper Pin
(20) Grease Nipple
(21) Chisel Holder Bushing
(22) Chisel Bushing
(23) Chisel
(01) Side Bolt
(02) Side Bolt Nut
(03) Gas Valve
(04) Cylinder Cover
(05) Control Valve Cap
(06) Control Valve
(07) Hose Adapter
(08) Cylinder
(09) Gas Seal
(10) Oil Seal
(11) Slide Ring
(12) Packing Bushing
01
02
21
19
18
14
15
17
13
16
08
07
06
05
04
12
11
10
03
09
20
22
23
TNB-08M, 1M, 2M, 3MB, 4M, 5M
Other manuals for TNB-08M
1
This manual suits for next models
15
Table of contents
Other Toku Power Tools manuals
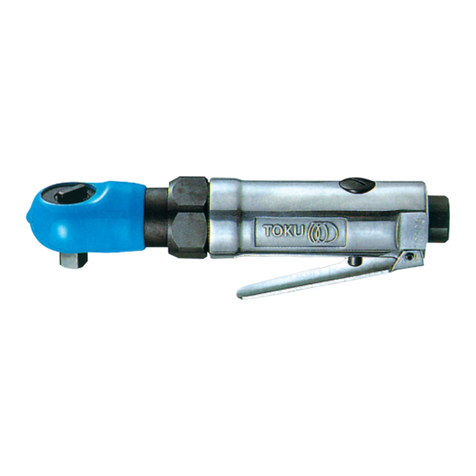
Toku
Toku MR-2207C User manual
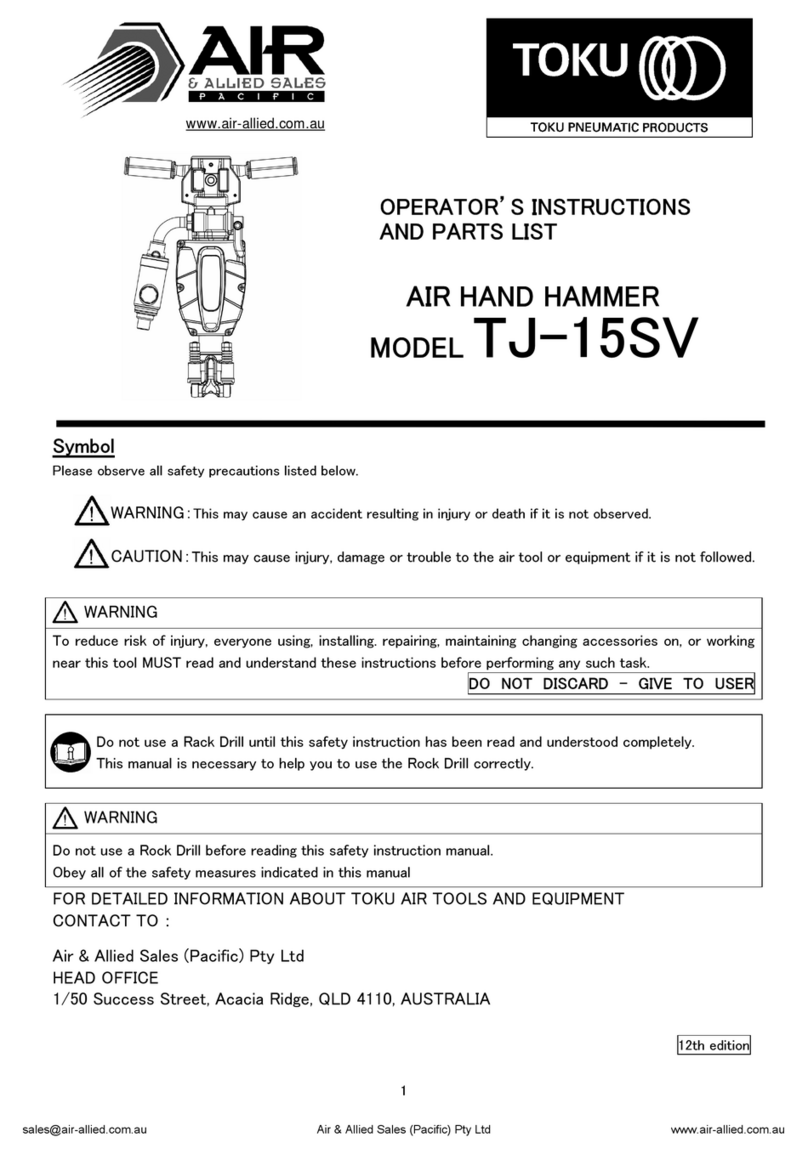
Toku
Toku Air & Allied Sales TJ-15SV User manual

Toku
Toku MI-3800PR User manual
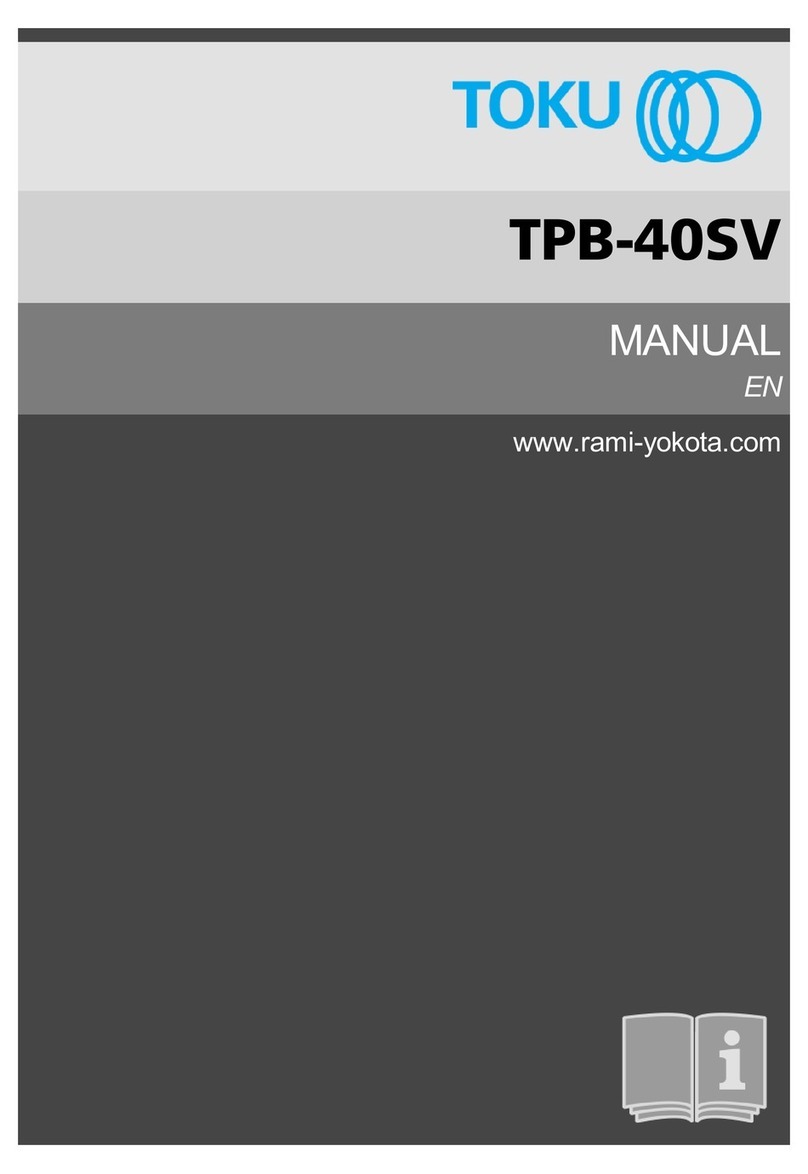
Toku
Toku TPB-40SV User manual
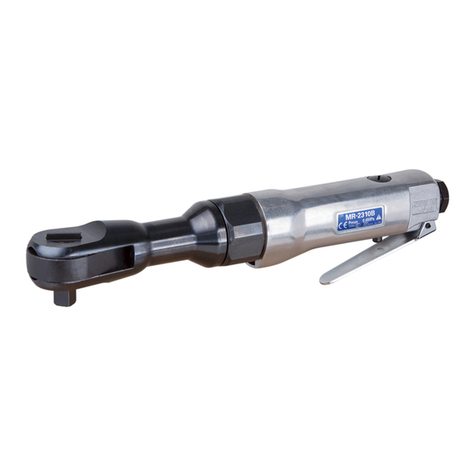
Toku
Toku MR-2310B User manual

Toku
Toku TJ-20 Parts list manual
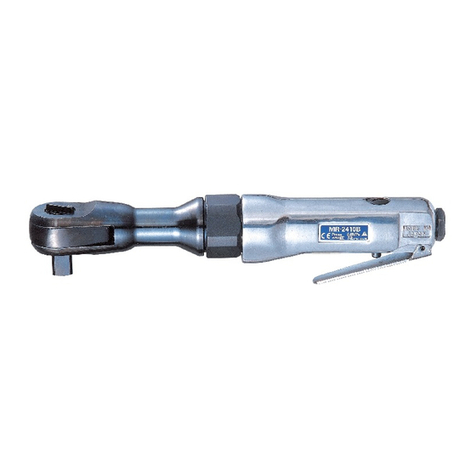
Toku
Toku MR-2410B User manual

Toku
Toku MR-2209C User manual
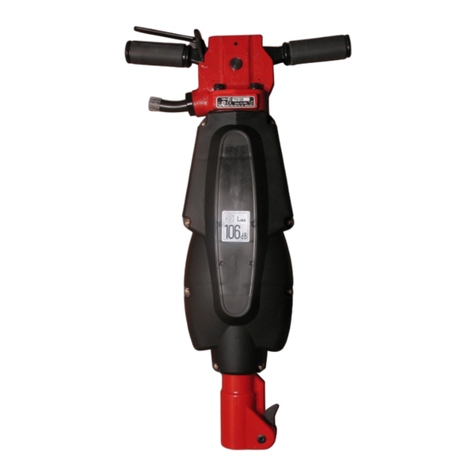
Toku
Toku TPB-501SV User manual
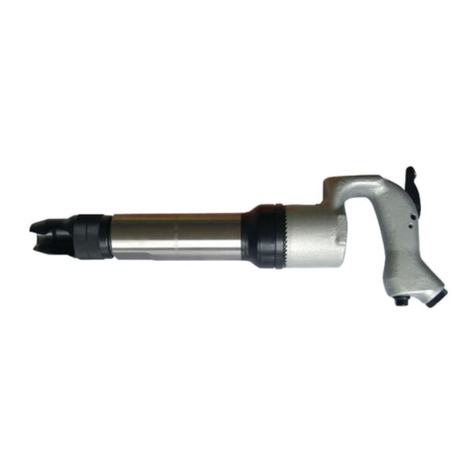
Toku
Toku THA-4BRH19X50 User manual
Popular Power Tools manuals by other brands
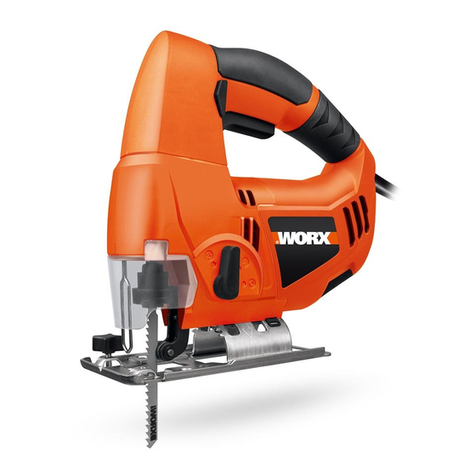
Worx
Worx WX472 manual

VonHaus
VonHaus 0518 Care & use instructions
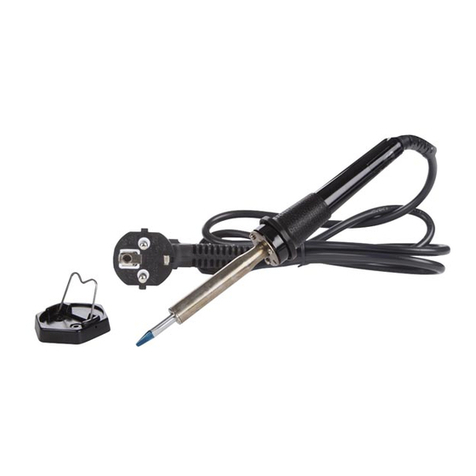
Velleman
Velleman VTS60 user manual
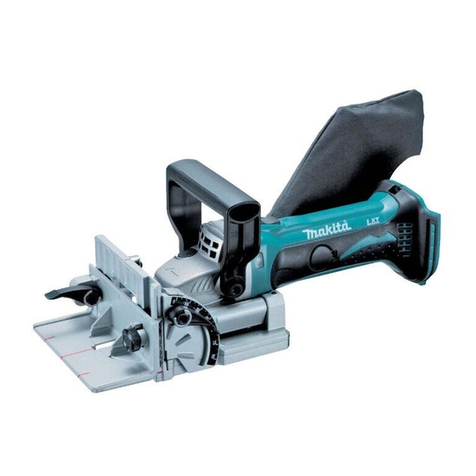
Makita
Makita DPJ180Z instruction manual
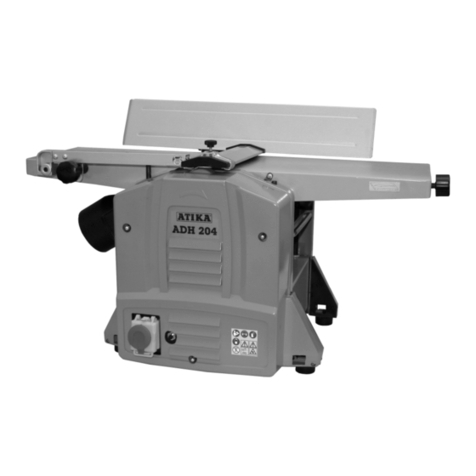
ATI Technologies
ATI Technologies ADH 204 Original instructions, safety instructions, spare parts
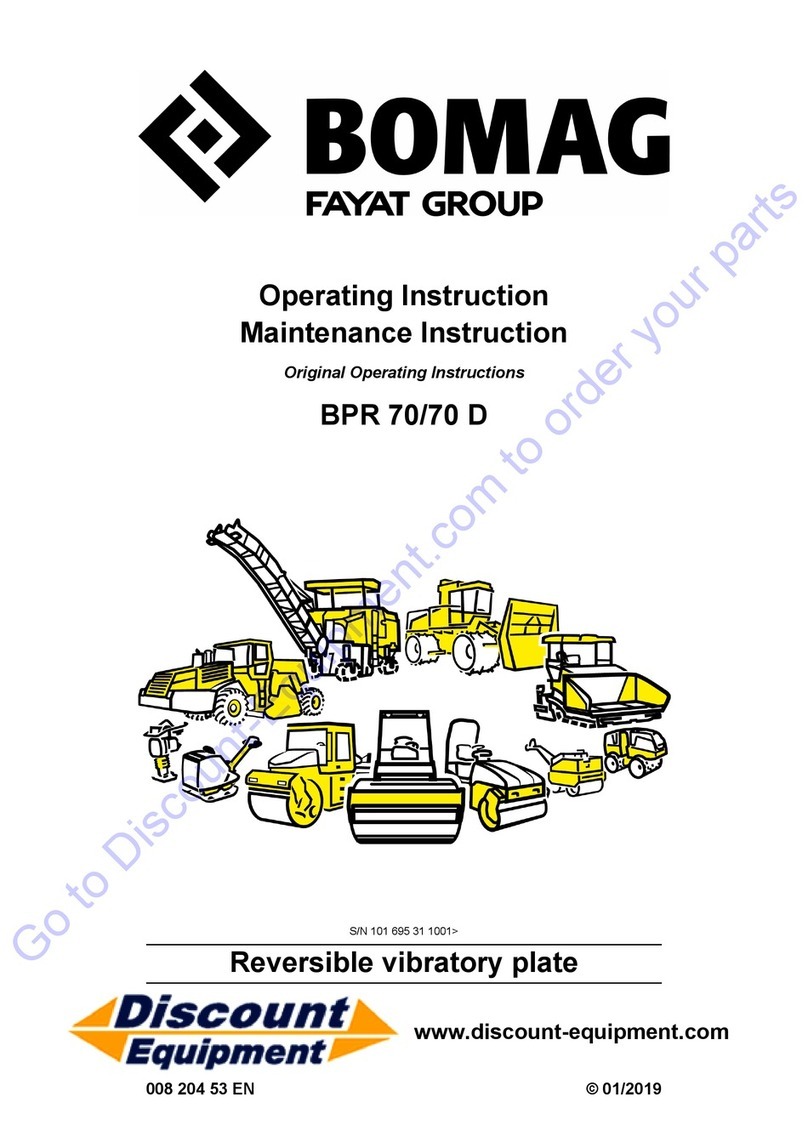
Fayat
Fayat BOMAG BPR 70 Operating Instruction, Maintenance Instruction