TQC Sheen LD7015 User manual

1
ULTRASONIC THICKNESS
ULTRASCHALL-WANDDICKENMESSER
ULTRASONE WANDDIKTEMETER
LD7015 / LD7016
User Guide
Bedienungsanleitung
Gebruiksaanwijzing
V1.2 0121

2
CONTENT / INHALT / INHOUD
English - User Guide - LD7015 3 - 8
English - User Guide - LD7016 9 - 18
Deutsch - Bedienungsanleitung - LD7015 19 - 24
Deutsch - Bedienungsanleitung - LD7016 25 - 31
Nederlands - Gebruiksaanwijzing - LD7015 32 - 37
Nederlands - Gebruiksaanwijzing - LD7016 38 - 47
This product complies to
- Machinery Directive 2006/42 / EC
- Low Voltage Directive 2006/95 / EC
- EMC Directive 2004/108 / EC
This product is RoHS 2 compliant (2011/65/EU)
Das Produkt erfüllt:
- Maschinenrichtlinie 2006/42 / EC
- Niederspannungsrichtlinie 2006/95 / EC
- EMC-Richtlinie 2004/108 / EC
Dieses Produkt ist RoHS2 konform (2011/65/EU)
Dit product voldoet aan:
- Machinerichtlijn 2006/42 / EC
- Laagspanningsrichtlijn 2006/95 / EC
- EMC richtlijn 2004/108 / E
Dit product is conform RoHS 2 (2011/65/EU)
ENDE
NL

3
EN - LD7015
1 ULTRASONIC THICKNESS GAUGE BASIC LD7015
Ultrasonic thickness gauge specically designed to measure the thickness of metallic and non-
metallic materials e.g. aluminium, titanium, plastics, ceramics, glass and plastics. It can also be
used to monitor all types of pipes and pressure vessels for loss of thickness due to corrosion or
erosion. The gauge is easy to use and will give accurate readings to an accuracy of 1%. This unit is
not suitable for cast iron due to its big crystalloid composition.
1.1 Specications
Measuring method : Ultrasonic pulse echo
Measuring frequency : 5MHz
Measuring range : 1.20 - 220 mm (steel); (deviation possible with use of
other materials)
Measuring range (tubes) : 20x3mm (steel)
Nauwkeurigheid : +/- (1%H + 0.1) mm
Display : LCD
Resolution : 0.1mm
Operation temperature : 0 ºC ~ 40 ºC
Batteries : 3x AAA alkaline batteries (total 5V)
Size : 70x135x38mm
1.2 Details
Receiving socket
Transmitting socket
Ultrasonic probe
LCD screen
Calibration block

4
EN - LD7015
2 WHAT’S IN THE BOX?
• Ultrasonic thickness gauge basic
• Ultrasonic gel 60ml
• Transducer 10mm - 5.0MHz
• Calibration block
3 OPERATION INSTRUCTIONS
• Operation area condition: This gauge can measure all samples which are equal to or bigger
than the transducers surface area.
• Curved surface condition: When materials have a curved surfaces like a boiler wall or tubing,
the curvature radius must be equal to or more than 10mm and the wall thickness must be
equal to or more than 3mm.
• Roughness condition: This gauge is applicable for a wide range of materials. In most cases
the supplied transducer makes very accurate readings. However if the roughness is too big
due to rust etc. an error may occur. In this case please try to minimise the roughness or select
the 2.5MHz transducer. If the transducer is worn-out, please contact your local distributor for a
replacement transducer
• Working temperature condition: Material and sound velocity will change along with
temperature. In normal measurement conditions environment temperature impact can be
ignored. The transducer is made of propylene material. Considering the protection of the
transducer and its precision we recommend a surface temperature of the work piece should
not be over 60oC otherwise the transducer could be damaged.
• Operation temperature: 0 - 40oC
• Relative humidity: <90% RH
• Hardware / Work piece/ Material temperature: < 60oC
• Do not apply on vibrating or erosive material
• Avoid impact and moisture

5
EN - LD7015
4 PREPARATIONS
1. Switching on the instrument
Connect the probe to the main unit, press ON/OFF to
turn on the instrument. All display signs will light up for
0.5 sec on the LCD screen. Then it will show a value of
0.0mm and 5900 VEL and after that the last registered
sound velocity with selected memory unit. The instru-
ment is now ready for use.
2. Material selection
To select a material please press the VEL button several times to your needed material sign
appears as per below schedule:
Code Material Sound Velocity (VEL)
FS Iron/Steel 5900
AL Aluminium 6320
CP Copper 4700
bR Brass 4430
Zn Zinc 4170
TIN Tin 3320
Pb Lead (Pb) 2400
GL Glass / Stainless Steel 5800
PVC Polyvinylchloride 2390
PMM Acrylic 2730
3. Calibration
If necessary this step should be repeated; Press the“ZERO” key for 2 seconds, after a short time
“CAL”will appear on the display, this indicates the unit is in calibration mode. Put a small amount
of coupling gel on the sample block and then place the probe on the sample block. When the
display shows 4.0mm the calibration is completed. After calibration the sound velocity will
remain the same as previous selected. A calibration should be made the every time the probe or
batteries are replaced. This is very important to make sure measurements will be accurate.
Start screen

6
5 PERFORM A MEASUREMENT
5.1 Thickness measurement
Put some coupling gel on the material surface, press the ultrasonic probe on the material surface
to measure. Please make sure there is good coupling, which will be indicated with this symbol
appearing on the display.
If this symbol does not appear or ashes it means there is not a good coupling. The reading on
the display is the measured value. After removing the probe, the reading will be held.
5.2 LCD backlight
By pressing this button you will activate the LCD backlight. With each operation the light
will switch on for about 7 seconds. When switching o the gauge the light will also automatically
switch o.
Calibration status Calibration accomplished
Correct coupling Measurement completed
Backlight
on
Backlight
o
EN - LD7015

7
5.3 Automatic power shut down
If the instrument is not operated for over 2 minutes it will automatically switch o.
6 CALIBRATIONS
We recommend annual calibration. For calibration, send the instrument, together with a RMA
form* to TQC Sheen, Molenbaan 19, 2908 LL Capelle aan den IJssel, NL.
*You can download the RMA form here: https://www.tqc.eu/en/service/repairs-calibrations/
6 REPLACING BATTERIES
When the icon ashes, please replace the batteries before taking any new measurements.
Turn the instrument o by pressing the ON/OFF button. Open the battery lid and replace them
with 3 pcs of AAA alkaline batteries.
7 MAINTENANCE
• Though robust in design, this instrument is precision-machined. Never drop it or knock it over
• Always clean the instrument after use.
• Clean the instrument using a soft dry cloth. Never clean the instrument by any mechanical
means such as a wire brush or abrasive paper. This may cause, just like the use of aggressive
cleaning agents, permanent damage.
• Do not use compressed air to clean the instrument.
• Always keep the instrument in its case when not in use.
• We recommend annual calibration
Backlight
o
EN - LD7015

8
8 DISCLAIMER
The right of technical modications is reserved.
The information given in this manual is not intended to be exhaustive and any person using
the product for any purpose other than that specically recommended in this manual without
rst obtaining written conrmation from us as to the suitability of the product for the intended
purpose does so at his own risk. Whilst we endeavour to ensure that all advice we give about
the product (whether in this manual or otherwise) is correct we have no control over either the
quality or condition of the product or the many factors aecting the use and application of the
product. Therefore, unless we specically agree in writing to do so, we do not accept any liability
whatsoever or howsoever arising for the performance of the product or for any loss or damage
(other than death or personal injury resulting from our negligence) arising out of the use of the
product. The information contained in this manual is liable to modication from time to time in
the light of experience and our policy of continuous product development.
EN - LD7015

9
Receiving socket
Transmitting socket
Ultrasonic probe
LCD screen
Calibration block
EN - LD7016
1 ULTRASONIC THICKNESS GAUGE PRO LD7016
Ultrasonic thickness gauge specically designed to measure the thickness of metallic and non-
metallic materials e.g. aluminium, titanium, plastics, ceramics, glass and plastics. It can also be
used to monitor all types of pipes and pressure vessels for loss of thickness due to corrosion or
erosion. The gauge is easy to use and, after a simple calibration to a known thickness or sound
velocity, the gauge will give accurate readings to an accuracy of 1%. This unit is not suitable for
cast iron due to its big crystalloid composition.
1.1 Specications
Measuring method : Ultrasonic pulse echo
Measuring frequency : 5MHz / 2.5MHz
Measuring range : 1.20 - 220 mm (steel);
Actual range varies with the type of material measured
Accuracy : +/- (1%H + 0.1) mm, H denotes the measured thickness
Sound velocity : 1000 - 9999 m/s.
Display : LCD
Resolution : 0.1mm
Working temperature : 0 ºC ~ 40 ºC
Power Supply : 3x AAA alkaline batteries (total 5V)
Size : 70x135x38mm
Measuring sound velocity with a given thickness: Measuring range: 1000 to 9999 m/s. When
the given thickness is over 20mm, the accuracy is +/-5%; when the given thickness is less than
20mm, the accuracy is +/- 1 mm/H*100%
1.2 Details

10
EN - LD7016
2 WHAT’S IN THE BOX?
• Ultrasonic wall thickness gauge
• Coupling gel 60ml
• Probe 10mm - 2.5MHz
• Probe 10mm - 5.0MHz
• Calibration plate
3 OPERATION INSTRUCTIONS
• Operation area condition: This gauge can measure all samples which are equal to or bigger
than the probes surface area.
• Curved surface condition: When materials have a curved surfaces like a boiler wall or tubing,
the curvature radius must be equal to or more than 10mm and the wall thickness must be
equal to or more than 3mm.
• Roughness condition: This gauge is applicable for a wide range of materials. In most cases the
supplied probe makes very accurate readings. However if the roughness is too big due to rust
etc. an error may occur. In this case please try to minimise the roughness or select the 2.5MHz
probe. If the probe is worn-out, please contact your local distributor for a replacement probe.
• Working temperature condition: Material and sound velocity will change along with
temperature. In normal measurement conditions environment temperature impact can be
ignored. The probe is made of propylene material. Considering the protection of the probe
and its precision we recommend a surface temperature of the work piece should not be over
60oC otherwise the probe could be damaged.
• Operation temperature: 0 - 40oC
• Relative humidity: <90% RH
• Hardware / Work piece/ Material temperature: < 60oC
• Do not apply on heavily vibrating / erosive material
• Avoid impact and moisture

11
EN - LD7016
4 PREPARATIONS
1. Turning on your instrument
Connect the probe with the main unit, press ON/OFF to turn on the instrument. The display
shows a full screen for 0.5 sec with backlight, then a vertical bar is displayed twice circularly,
meanwhile the main display area shows 0000 to 9999 progressively. After that the LCD displays
the last applied sound velocity with registered memory.
2. Sound velocity selection and adjustment
Press“VEL”key to enter the sound velocity interface, press again, you can now select the velocity
data by pressing or the word“VEL”will be blinking on the display. If you need to adjust
the sound velocity, press the“VEL” key once more, the“VEL” and “m/s”will keep blinking. Then
increase or decrease the sound velocity to the number you want by pressing or again. The
data will be automatically stored into the current sound velocity memory unit. After this, press to
conrm new sound velocity and the icons will stop blinking.
3. Calibration
If necessary this step should be repeated; Press the“ZERO” key for 2 seconds, after a short time
“CAL”will appear on the display, this indicates the unit is in calibration mode. Put a small amount
of coupling gel on the sample block and then place the probe on the sample block. When the
Full screen Last applied sound velocity & unit no.
velocity adjustment velocity revision

12
display shows 4.0mm the calibration is completed. After calibration the sound velocity will
remain the same as previous selected. A calibration should be made the each time the probe or
batteries are replaced. This is very important to make sure measurements will be accurate.
5 PERFORM A MEASUREMENT
5.1 Thickness measurement
Put some coupling gel on the material surface, press the ultrasonic probe on the material surface
to measure. Please make sure there is good coupling, which will be indicated with this symbol
appearing on the display.
If this symbol does not appear or ashes it means there is not a good coupling. The reading on
the display is the measured value. After removing the probe, the reading will be held.
5.2 Sound velocity measurement
To get a read out of sound velocity of the material with a known thickness: Obtain the thickness
of the material by using a micrometer or calliper, then put the probe on the material until a value
appears on the display. Remove the probe and press or to adjust the value to match the
same thickness as measured with the micrometer/calliper. Then press VEL to display the sound
velocity and save the current velocity in the memory unit.
EN - LD7016
Good coupling measurement Measurement accomplished
Calibration status Calibration accomplished

13
EN - LD7016
5.3 Data storage
Press“MODE”key to enter the data save mode. The display will show the “Thickness and mm”
icons with the rst memory unit (M 1) If the rst memory unit wasn’t registered, the display will
show 0. 0.
Press or to select your desired memory unit(1-10) and press “MODE” again to store.
After selecting your memory unit you can start measuring again. While measuring, the memory
unit will ash and the new measurement will delete the stored value. When your measurement is
completed the last reading will be held again in the selected memory unit automatically. After-
wards the memory unit no. will stop blinking.
5.4 Review the saved data
Press“MODE”, then memory unit no. and stored data will be displayed. You can review the saved
data in unit 1-10 by pressing or , they are read only. By pressing“MODE” again you will
return to the measuring mode.
5.5 Low battery indication
When the following icon ashes, please replace the batteries before taking any new mea-
surements.
Thickness measurement Adjusting the thickness Velocity read out
Review saved data

14
5.6 LCD backlight and automatic power shut-down
Hold the“ZERO” button pressed for a second and then also simultaneously press the ON/OFF
button. This way the backlight will be activated. Every operation the backlight will turn on for
7sec. until the gauge is switched o again. If the gauge is not operated for over 2 minutes, it will
automatically switch o and the backlight function will be cancelled.
5.7 Measurement tips
1. Cleaning the surfaces
Before making a measurement please make sure dust, dirt rust and grease are removed from the
surface.
2. Decreasing the surface roughness
Too rough surfaces may result in measuring faults or error readings. Please try to smooth the
surface by milling, polishing, lling or a use a high viscosity coupling gel.
3. Rough machined surfaces
The regular tiny texture/slots resulting from rough machining processes may cause errors. Please
follow the method as mentioned at paragraph 3 Operating Instructions “Roughness condition”.
Adjusting the angle between the crosstalk segregating board of the probe (a metal membrane
crossing the detector bottom centre) and linear texture slots (parallel or vertical) may also get
better results.
4. Measuring cylindrical surfaces
When measuring cylindrical surfaces like pipes, oil tubes etc. it is critical to select an angle
between the crosstalk segregating board of the probe and axis of the material to be measured. In
simple terms; couple the probe and material, keep the crosstalk segregating board of the probe
right-angled to the axis of the pipe to be measured. For small pipes two measurements should
be performed, one with the axis of the pipe perpendicular, the other one parallel. The smallest of
the 2 values displayed, should then be taken as the thickness at that point.
5. Complex shaped materials
For complex shaped material measurements please check paragraph 4.7.3., the smallest of the
two readings should in this case be used as the thickness.
6. Non-parallel surfaces
To get a satisfying ultrasonic response, the surface must have got one measuring side parallel to
another side, otherwise the results will be faulty.
7. Material surface temperature inuences
The size and sound velocity of material will change at dierent temperatures. When precision is
critical please make 2 dierent measurements under the same temperature conditions to deter-
mine the correct thickness reading. When making steel measurements with high temperatures,
this method may be used also to get a correct reading.
EN - LD7016

15
EN - LD7016
8. High acoustic reduction materials
For materials such as ber, poriferous or big granular, acoustic dispersion will cause energy at-
tenuation which may result in abnormal readings (the reading is less than the actual thickness) In
this case, the material is not suitable for the gauge.
9. Reference sample block
Calibrating the gauge, a given thickness or sound velocity of the material is very important. Cali-
bration needs at least one standard reference sample block. This gauge is provided with a 4.0mm
sample block on the front of the casing. Please check the calibration procedure.
With dierent materials and situations, only one sample block may not be enough to get the
most exact calibration. The more similar sample blocks, the more exact readings will be obtained.
Ideally reference blocks are a group of dierent thicknesses of the same material. When calibra-
tion the gauge with dierent blocks, the variation of sound velocity will be minimised. To get a
most exact measurement, a set of reference blocks is very important.
In most situations using only one reference block will result in a proper measurement. This refe-
rence block must be the same material and thickness as the parts to be tested. The thickness of
the reference block should be read out in micrometers.
When measuring thin materials of which the thickness is close to the minimum limit range of
the gauge, please use a reference block to dene the exact limit of the material (1.2mm for steel
material) Do not measure material from which the thickness is under the minimum limit.
When material consist of a complex alloy in a large size, a block which has a similar material thick-
ness, should be used for calibration.
Forged or casted hardware mostly have dierent inner structures which results in slightly dif-
ferent sound velocities. To reach the exact reading, the reference block most have a similar struc-
ture as the hardware. With common measurements you have to check the sound velocity table
stated in this manual instead of calibrating the gauge with a reference block. However this table
is just for reference, sometimes the sound velocity will be dierent caused by dierent physical/
chemical factors. The sound velocity of mild steel is mentioned in the reference table.
5.8 Accuracy precautions
1. Thin material
When the thickness of the material is less than the minimum limit, any ultrasonic thickness
gauge will give faulty measurements. Use the sample block comparing method to get a mini-
mum limit of a material. When measuring thin material, an error may occur (the thickness reading
is two times the actual thickness) To prevent wrong readings with thin material, double check the
minimum limit of the material.

16
EN - LD7016
2. Stained/rusted material:
Stained or rusted surfaces on the contra side will result usually in wrong readings. Sometimes a
small stained spot is hard to nd. Be careful while measuring known rust spots/suspicious areas
or use sound insulation board-celotex to locate the spots in dierent test angles.
3. How to determine velocity of various materials
A faulty reading will be obtained, when measuring the material with a velocity calibrated with
a previous material. So a correct velocity should be obtained. The faulty reading may also result
from the dierence between the actual velocity of the calibrated value.
4. Wearing of the probe
Because the probe is made of propylene, long term use will cause the surface to roughen, this
will result eventually in wrong readings. Please polish the surface with sand paper or whetstone
to assure the smoothness. If the readings are still unsteady, the probe should be replaced by a
new one.
5. Multilayer-composite material
It is impossible to read out the thickness of uncoupled multilayers as the ultrasonic wave cannot
go through into the uncoupled space. Furthermore, the sonic wave cannot go through in to the
composite material at an even speed. So ultrasonic reect principles cannot be applied for mea-
suring multilayers and composite material.
6. Inuences from oxidized materials
For some metals such as aluminium, a layer of oxide can be generated on the surface. Although
the oxidised layer combines with the substrate tightly, the sonic wave does need to travel
through 2 dierent materials so it will lead to incorrect readings. With a thicker oxidised layer,
more deviation will occur. Please calibrate the instrument with a reference block of the same
material as the sample. Obtain the thickness of the sample block by using a micrometer/calliper.
7. Any abnormal readings
An operator should be capable to distinguish any abnormal readings as a result of erosive, recess
surface, incorrect calibration sample blocks or the inner aw of materials.
8. Coupling gel
Coupling gel causes the high frequency ultrasonic waves transmitting between the probe and
material. Choosing incorrect coupling or wrong operation may cause errors or pour coupling
which results in failure to measure. The coupling gel should be used in a proper way, normally,
a small drop of gel is sucient. It is important to use proper coupling gel, low viscosity gel (as
supplied) is suitable for smooth surfaces. For rough, vertical, aluminium surfaces, high viscosity
liquids like glycerine and lubrication grease is applicable. These kinds of agents are normally
available in the local market but you can buy them also from a local distributor.

17
EN - LD7016
Sound Velocity table:
Material Velocity m/s Material Velocity m/s
Aluminium 6320 Acetate resin 2670
Zinc 4170 Phosphor 3530
Silver 3600 Turpentine 4430
Gold 3240 Glass 5440
Tin 3230 Incoloy alloy 5720
Iron/steel 5900 Magnesium 6310
Brass 4640 Monel alloy 6020
Copper 4700 Nickel 5630
SUS 5790 Steel 4330 (mid) 5850
Acrylic resin 2730 Steel 330 5660
Water (20°C) 1480 Titanium 6070
Glycerin 1920 Zirconium 4650
Soluble glass 2350 Nylon 2620
6 CALIBRATIONS
We recommend annual calibration. For calibration, send the instrument, together with a RMA
form* to TQC Sheen, Molenbaan 19, 2908 LL Capelle aan den IJssel, NL.
*You can download the RMA form here: https://www.tqc.eu/en/service/repairs-calibrations/
7 REPLACING BATTERIES
When the batteries are low the battery icon will appear on the display. Turn the instrument of by
pressing the ON/OFF button. Open the battery lid and replace them with 3 pcs of AAA alkaline
batteries.

18
8 MAINTENANCE
• Though robust in design, this instrument is precision-machined. Never drop it or knock it over
• Always clean the instrument after use.
• Clean the instrument using a soft dry cloth. Never clean the instrument by any mechanical
means such as a wire brush or abrasive paper. This may cause, just like the use of aggressive
cleaning agents, permanent damage.
• Do not use compressed air to clean the instrument.
• Always keep the instrument in its case when not in use.
• We recommend annual calibration
9 DISCLAIMER
The right of technical modications is reserved.
The information given in this manual is not intended to be exhaustive and any person using
the product for any purpose other than that specically recommended in this manual without
rst obtaining written conrmation from us as to the suitability of the product for the intended
purpose does so at his own risk. Whilst we endeavour to ensure that all advice we give about
the product (whether in this manual or otherwise) is correct we have no control over either the
quality or condition of the product or the many factors aecting the use and application of the
product. Therefore, unless we specically agree in writing to do so, we do not accept any liability
whatsoever or howsoever arising for the performance of the product or for any loss or damage
(other than death or personal injury resulting from our negligence) arising out of the use of the
product. The information contained in this manual is liable to modication from time to time in
the light of experience and our policy of continuous product development.
EN - LD7016

19
DE - LD7015
1 ULTRASCHALL-WANDDICKENMESSGERÄT - LD7015
Das Ultraschall-Wanddickenmessgerät wurde speziell für die Dickenmessung von metallischen
und nicht metallischen Materialien wie z. B. Aluminium, Titan, Kunststo, Keramik und Glas ent-
worfen. Es kann des Weiteren zur Überwachung des Wandstärkenverlustes aller Arten von Rohr-
leitungen und Druckkörpern aufgrund von Korrosions- oder Erosionserscheinungen eingesetzt
werden. Das Messgerät ist einfach zu handhaben und liefert, nach einer einfachen Kalibrierung,
anhand einer bekannten Schichtdicke oder Schallgeschwindigkeit akkurate Messwerte mit einer
Genauigkeit von 1%.
Eine Messung auf Gusseisen ist aufgrund dessen Zusammensetzung nicht möglich.
1.1 Spezikationen
Messmethode : Ultraschall-Pulsecho
Messfrequenz : 5MHz
Messbereich : 1,2 – 220mm (Stahl) – eektive Reichweite variiert mit
dem Material
Genauigkeit : ± 1%
Auösung : 0,1mm
Stromversorgung : 3 x AAA Alkali Batterien
Display : LCD
Betriebstemperatur : 0 – 40°C
Abmessung : 135 x 70 x 38mm
1.2 Details Eingangsstecker
Ausgangsstecker
Ultraschall-Sonde
LCD Display
Kalibrier-Block

20
DE - LD7015
Ein/Aus-Schalter
Kalibrierung
Schallgeschwindigkeit Auswahl-Taste
Hintergrundbeleuchtung
Batterieanzeige
Kupplungsanzeige
Schallgeschwindigkeit
Dicke
Schallgeschwindigkeitsanzeige
Hintergrundlichtanzeige
Materialanzeige
2 LIEFERUMFANG
• Ultraschallwanddickenmessgerät
• Ultraschallgel 60ml
• 10mm Sonde – 5,0MHz
• Kalibrierblock
• Bedienungsanleitung
3 HINWEISE
• Messbereich: Die zu messende Oberäche muss mindestens gleichgroß (oder größer) sein,
als der Sondenkopf.
• Gewölbte Oberäche: Soll eine gewölbte Oberäche gemessen werden (z. B. Rohrleitungen),
sollte der Krümmungsradius 10mm und die Wandstärke 3mm nicht unterschreiten.
• Rauheit: Dieses Gerät zeichnet sich durch seine hohe Genauigkeit der Messwerten aus. Weist
die Oberäche jedoch eine starke Rauheit auf (z. B. durch Rost), kann es dennoch zu Fehl
messungen kommen. In diesem Fall versuchen Sie die Rauheit zu minimieren.
• Oberächentemperatur: Die Oberächentemperatur der Probe darf eine Temperatur von 60°C
nicht übersteigen. Eine höhere Temperatur würde die Sonde beschädigen.
• Betriebstemperatur: 0 – 40°C
• Relative Luftfeuchtigkeit: <90%RH
• Nicht auf vibrierenden oder erodierenden Materialien anwenden.
• Vermeiden Sie Erschütterungen und Feuchtigkeit.
This manual suits for next models
1
Table of contents
Languages:
Other TQC Sheen Measuring Instrument manuals
Popular Measuring Instrument manuals by other brands
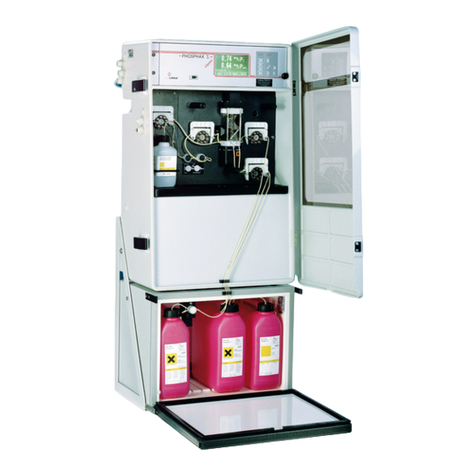
Hach
Hach PHOSPHAX sigma High Range Basic user manual
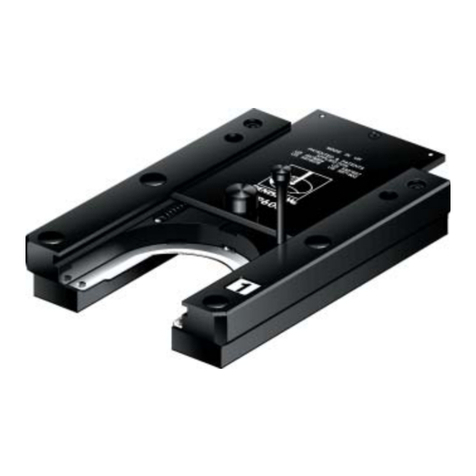
Renishaw
Renishaw SCP600 manual
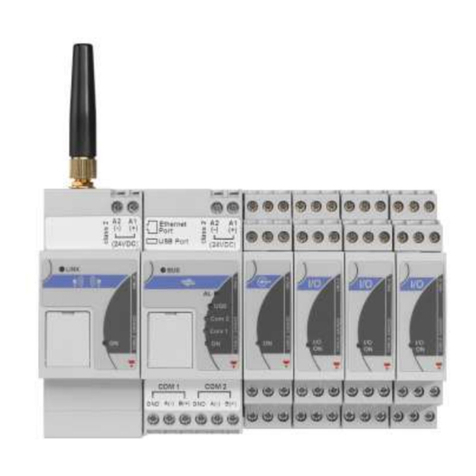
CARLO GAVAZZI
CARLO GAVAZZI VMU-C EM instruction manual
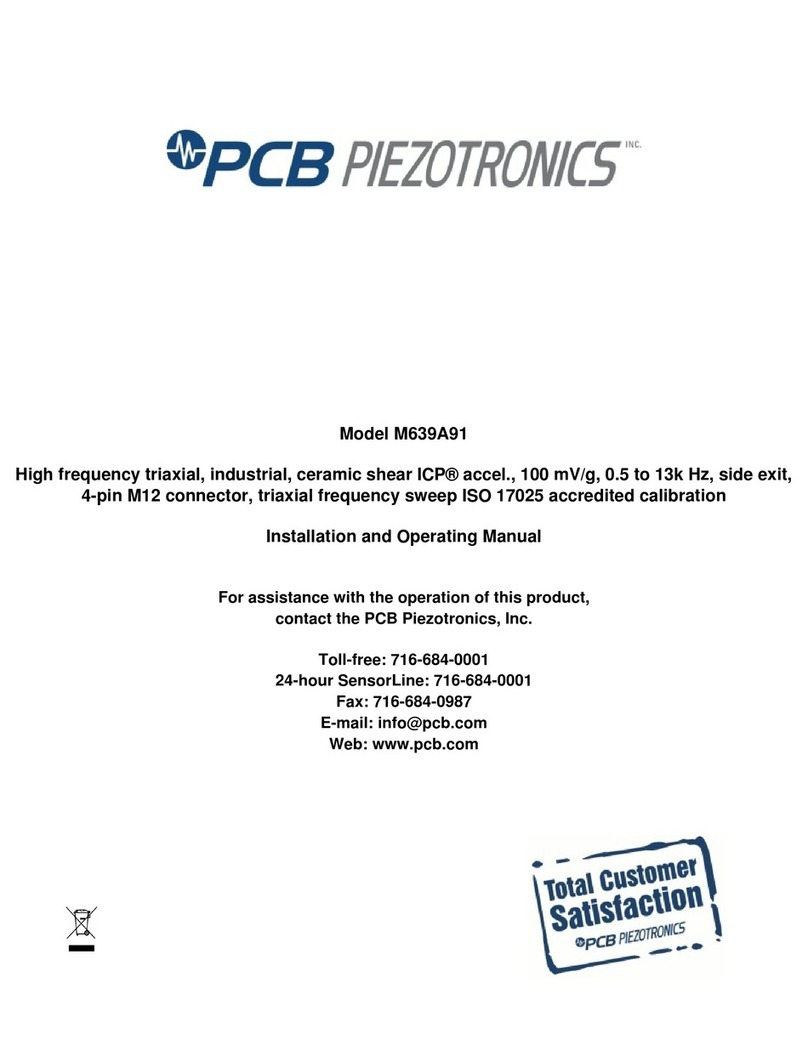
PCB Piezotronics
PCB Piezotronics M639A91 Installation and operating manual
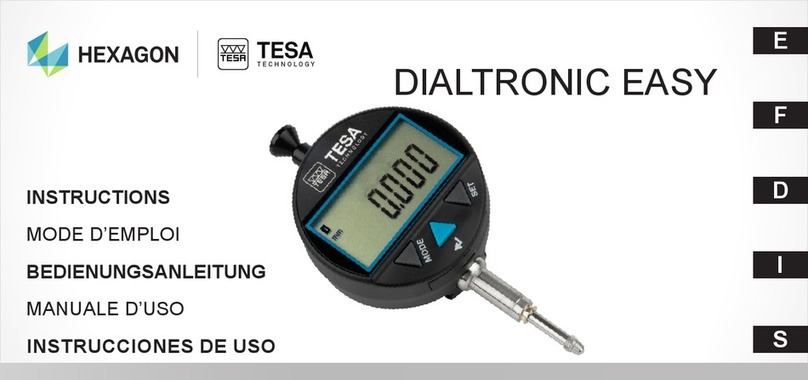
TESA
TESA HEXAGON DIALTRONIC EASY instructions
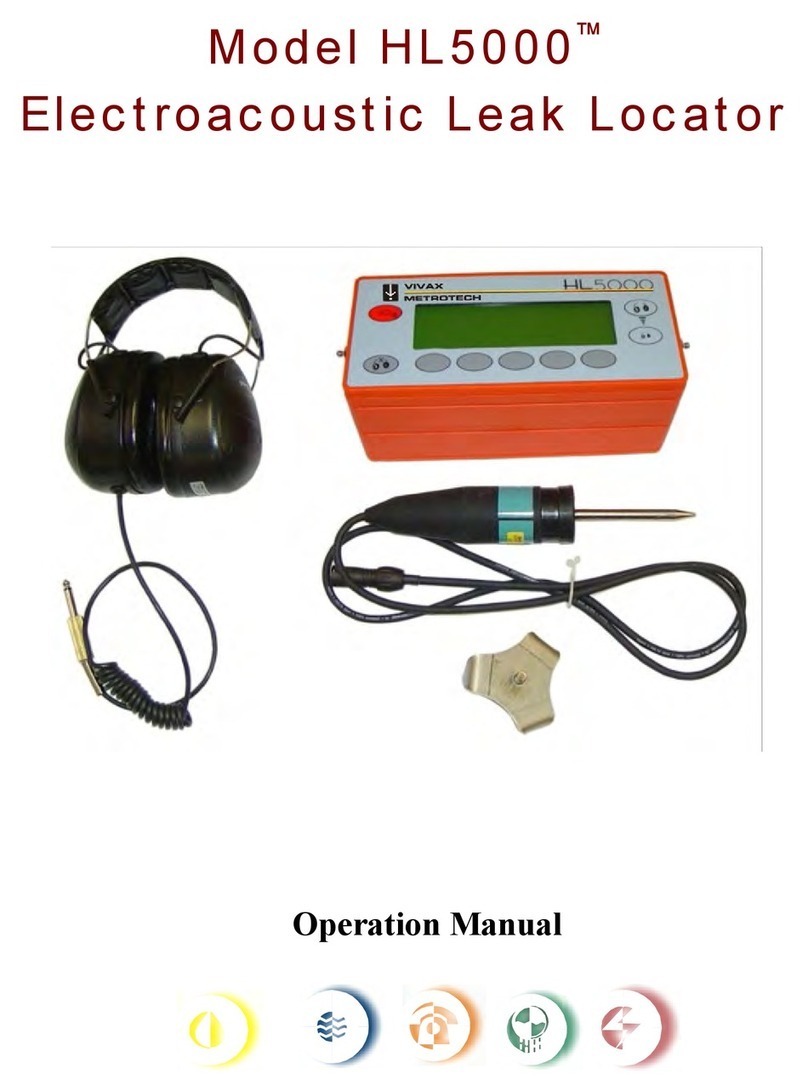
Vivax Metrotech
Vivax Metrotech HL5000 Operation manuals