TQC Sheen PowderTAG User manual

PowderTAG
LD5860
Thickness Analysing Gauge
Operating Instructions (V1.4 0718)
IMPORTANT! Before taking this instrument in
use we strongly advise you to read this manual
carefully.

| 2 3 |
TQC Sheen will grant a warranty for a period of
12 months for the PowderTAG and 12 months for
all related equipment from the date of delivery in
respect of any evidence of faulty workmanship and
materials.
Should a delivered consignment prove to be
contrary to contract upon inspection, the customer
shall grant TQC Sheen the opportunity hereunder
of removing the fault, or else the customer may
demand replacement. Because of size and weight of
the instrument TQC Sheen will strive to give remote
support.
Should the supply or delivery of any improvement
or replacement not prove possible, the customer
may choose between having the purchase price
reduced or in demanding the contract of sale to
be rescinded (conversion). Damage resulting from
natural wear and tear, mechanical or chemical
damage, an act of God or non compliance with the
operating instructions shall be excluded from the
warranty as well as mechanical interference by the
customer or by third parties with the PowderTAG
and related equipment without TQC Sheen’s written
permission. No liability will be accepted for defects,
damage or injury caused due to use not carried
out in accordance with the manufacturer’s user
instructions.
To claim warranty, the rejected product has to
be sent to TQC Sheen together with the original
invoice, any exchange before the product has
been returned to TQC Sheen is not possible. TQC
Sheen reserve the right to repair, exchange or
supply an equivalent substitute. TQC Sheen is not
liable for handling or transport costs. Warranty
on the purchase price is limited, all liability for
consequential damages or changes in technology
is expelled.
This product complies to
- Low Voltage Directive 2006/95 / EC
- EMC Directive 2004/108 / EC
This product is RoHS 2 compliant
(2011/65/EU)
WARRANTY

| 4 5 |
1 Introduction
1.1 Information on the instructions
1.2 Safety
1.3 Copyright
1.4 Manufacturer’s / suppliers address
2 Safety instructions
2.1 Manual symbols
2.2 Instrument symbols
2.3 Designated purpose
2.4 Dangers from invisible optical
radiation
2.5 Dangers when handling Li-ion
batteries
2.6 Information for the use of the
battery charger
3 Transport and storage
3.1 Packing
3.2 User: check on receipt
3.3 Reporting transport damage and
documentation
3.4 Storage and protective measures
when not in use
4 Instrument data
4.1 Name / article
4.2 Scope of supply
4.3 Technical data
4.4 Power supply
5 Instrument controls
and functions
6 Do’s and don’ts
7 Getting started
7.1 Insert batteries and connect
sensor
7.2 Starting the PowderTAG and
perform measurements
8 User interface
8.1 Main menu
8.2 Measurement screen
8.3 Measure settings
8.4 Limit values
8.5 Instrument settings
8.6 Check instrument
9 Measuring mode
9.1 Notes for coating thickness measurement
9.2 Preparation for measurement
9.3 Performing measurements
10 Calibrations
10.1 General guide lines
10.2 Factory calibrations
10.3 User calibration
10.4 Calibration methods
10.4.1 Single point calibration - powder
10.4.2 Two-point calibration - powder
10.5 Loading calibrations
10.6 Editing user calibrations
10.7 Deleting user calibrations
11 Care and maintenance
11.1 Transport and storage
11.2 Maintenance
11.3 Cleaning
11.4 Batteries
11.5 Precautions - batteries in carry-on
baggage (aircraft cabin).
12 Disclaimer
615/17
18
19/21
22
23
7/8
9
10/11
12
13
14
INDEX

| 6 7 |
The PowderTAG is a photo-thermal gauge which
measures film thickness non -contact and non-
destructive. It complies with standard: DIN EN
15042-2. The small and robust instrument is suitable
for fast and precise coating thickness measurement
of powder coatings on metallic substrates before
and after cure. The measurement system consists
of a sensor and a display device. The sensor is
connected to the display device with a cable.
Please note that the performance-, range- and
accuracy of the PowderTAG is depending on the
structure and specific colour of the powder coating.
The majority of powder coatings can be measured
without any problems. In rare occasions the
coating is not compatible with the photo thermal
technology or special settings are required.
Special settings always relate to a specific powder
from a specific manufacturer and NOT to a specific
colour.
Because heat disturbs the photo-thermal
measuring principle, the measurement object
needs to be cooled down to approx 40°C when the
measurement is performed.
1.1 Information on the instructions
This manual allows for the safe and efficient use of
the instrument. The manual is part of a measuring
instrument and must at all times be kept accessible
and nearby the gauge for the staff.
The personnel must have read and understood
this manual carefully before starting work. Basic
requirement for safe working is the observance of
all specified safety and handling instructions in this
manual.
Moreover, the local work safety regulations and
general safety regulations for the application of the
PowderTAG shall apply.
Illustrations in this manual are provided for basic
understanding and may differ from the actual
design.
1.2 Safety
All warnings must be read and observed in order
to work safely and securely with the gauge. Never
make the warning labels on the instrument
unrecognizable. Keep these instructions in a safe
place and pass them with the instrument.
Observe the detailed safety instructions in section 2!
1.3 Copyright
The copyright of this operating manual remains
with TQC Sheen.
This operating manual is intended solely for the user
and his personnel. Its instructions and guidelines
may not be duplicated, circulated or otherwise
passed on to others, neither fully, nor partly.
Infringement of these restrictions may lead to legal
action may be taken if this restrictions are infringed
upon.
1.4 Manufacturer’s / supplier’s address
TQC Sheen B.V.
Molenbaan 19
2908 LL Capelle aan den IJssel
The Netherlands,
T +31(0)10-79 00 10 0
1 INTRODUCTION
2.1 Manual symbols
The following symbols for dangers are used in this
instruction manual.
2.2 Instrument symbols
WARNING! Danger of illegible signs!
Over time stickers and signs can become dirty
or unrecognizable in any other way, so that risks
are not recognized and necessary operating
instructions are not followed. This may result in
injury. All safety, warning and operating instructions
should be kept clearly legible. Replace damaged
signs or labels immediately.
2.3 Designated purpose
The photo-thermal meter “PowderTAG” is
exclusively designed to determine the thickness of
wet and dry organic coatings for quality assurance
and production-related testing in the laboratory
environment as described within the specifications.
Other applications will be considered improper
use. TQC Sheen will not be held liable for damage
resulting from improper use. Designated purpose
also includes proper observing all instructions in the
operation manual, and adhere to inspection and
maintenance schedules.
WARNING! Misuse of PowderTAG can lead to
dangerous situations.
• Never Use PowderTAG for medical purposes.
• Never immerse PowderTAG in liquids.
Possible immediate danger to the
life or health of personnel.
If this guideline is not noted it can lead
to severe danger to health, up to fatal
injury.
A dangerous situation could be
caused.
Non observance of this guideline
can lead to injury or to damage to
equipment.
Special tips and particular
information.
Guidelines to make optimal use of the
instrument.
2 SAFETY INSTRUCTIONS
Position:
On the sensor
Position:
On the back of the equipment

| 8 9 |
2.4 Dangers from invisible optical radiation
WARNING! Danger to health from invisible optical
radiation! Irradiation of the skin close to the exit
hole can lead to light burns.
• The red light spots are only an aid and serve to
focus the measuring point. They light up when the
equipment is configured and ready to measure.
The excitation beam itself is slightly blue!
• Never point the excitation beam directly at eyes
and skin.
• Never observe the excitation beam with optical
instruments such as lenses and microscopes.
• Long time exposure to radiation (over 60s daily)
may lead to skin damages. When working in the
path of the beam the use of protective gloves is
recommended.
• Only switch on the equipment if the sensor’s beam
exit hole has been tested for external damage.
• If the sensor is damaged, do not continue to use
the measuring equipment and send it immediately
to TQC Sheen.
WARNING! Danger to life from re caused by heat
generated by the excitation beam!The excitation
beam can set ammable solids, liquids and gases
on re and cause severe to fatal injuries.
• Never use the excitation beam in areas where
there is a risk of explosion.
• Never point the measuring equipment at
flammable materials.
2.5 Dangers when handling Li-ion batteries
WARNING! The accompanying 14500 Lithium
ion batteries are impermeable to gases and
non-harmful as long as the manufacturers’
requirements for use and handling are obeyed.
Improper handling of the rechargeable battery,
especially mechanical damage or charging with
an unsuitable battery charger can lead to it
catching re or exploding.
• Avoid mechanical and thermal stresses. Mechanical
damage can lead to internal short-circuits. Fire risk!
• Protect batteries from damp. In case of fire, do not
extinguish it with with water, but with sand, say.
• Electrolyte solution is highly flammable. Leaked
electrolyte solution from a Li-ion battery can be
washed away from the battery with water.
• Do not short-circuit Li-ion batteries. Take care
when using tools and wearing metal jewellery.
• Fire risk! Excess voltage and overcharging are to be
avoided in all situations. The batteries should not
be charged close to combustible materials!
• Avoid external sources of heat such as sun, heaters
and fire. There is a risk of explosion.
2.6 Information for the use of the battery
charger
The battery charger is only to be used with
rechargeable 14500 batteries. It is recommended
that the batteries be inserted in pairs (in 2s or 4s)
in slots 1 and 3 and/or 2 and 4. The battery charger
is only designed for use indoors. The operating
temperature of the battery charger is in the range of
0°C –40°C; heat and humidity are to be avoided.
3.1 Packing
• Please take note of pictorial symbols on the
packing.
3.2 User: check on receipt
• Check packing for damage
• After unpacking check complete supply.
3.3 Reporting transport damage and
documentation
• Any damage should be documented as accurately
as possible (possibly photographed) and reported
to the relevant insurers or, in the case of sales
“delivered to customers works”, to the supplier.
3.4 Storage and protective measures
when not in use
• The instrument must be stored in a dry place at a
temperature between 10 - 40˚C.
• If packing is damaged upon receipt immediately
inform the forwarder and make a note on the
packing list and have it signed by the forwarder.
Ideally make some pictures of the damage as well.
• Store instrument in the original packing if possible.
3 TRANSPORT AND STORAGE

| 10 11 |
4.1 Name / article
PowderTAG Thickness Analysing Gauge / LD5860
4.2 Scope of supply
4 INSTRUMENT DATA
Rugged hard carrying case
4 x Li-Ion batteries + extra
set of 4 Li-Ion batteries
Display unit
Varification tool
Photo-thermal coating
thickness sensor + cable
Quad charger for Li-Ion
batteries
Rubber protection harness
for display un
Manual
4.3 Technical data
Environmental conditions data value unit
Altitude <2000 m
Relative humidity 5 - 80%
Relative humidity (32˚C) 5 - 50%
Temperature (operating) 5 - 40˚C
Temperature (storage) 0 - 55˚C
Estimated operating time approx 5000 h
Display unit
Depth 42.5 mm
Width 80 mm
Height 180 mm
Weight approx 700 g
Power 4 Li-Ion batteries type 14500
Sensor
Length 160 mm
Diameter 50 mm
Weight approx 225 g
Measurement period 64 - 1024 ms
Risk Group 3
Optical power max. 0.45 W
Wavelength 365 nm
Measuring field size 1 mm
Measuring distance 35 mm
Distance tolerance ± 3 mm
Angle tolerance ± 15˚
The following values are dependent on the material
properties. Indicated are exemplary, typical values.
Resolution about 1% *
Accuracy about 3% *
Layer thickness typ. * 50 - 300 microns
* Depending on the material properties
4.4 Power supply
The PowderTAG is powered by four Li-Ion batteries
3.7V type (included). It is not suitable for operation
with conventional 1.5V AA batteries.
To charge the batteries, an external battery charger
(included) must be used. This charger is exclusively
designed for Li-ion batteries.
For safe handling of the batteries please refer to
section 11.
• Remove the batteries from the unit when
the instrument will not be used for an extended
period. The battery level indicator in the
measurement menu shows the battery level in 4
steps.
• A blinking empty battery icon indicates that the
batteries are nearly discharged.
• When the battery level drops below a critical
voltage, the meter turns off to prevent itself from a
deep discharging of the batteries.
• Even though the meter is designed for long
operating times, we suggest to take a set of fully
loaded spare batteries with you in case you want
to perform on-site measurements.
• Measurement errors due to discharged batteries
are not possible because the meter shuts down
upfront or cannot be turned on.
• Defective batteries are hazardous waste and must
be disposed of in accordance with the statutory
provisions.

| 12 13 |
5 INSTRUMENT CONTROLS AND FUNCTIONS
Display unit
Sensor with LED pointers
Sensor plug
On/off button
Context-sensitive function buttons
Measurement button
4
5
6
1
2
3
2
1
3
4
5
6
6 DO’S AND DON’TS
• Bright colours may need extra calibration!
• Probe distance is important, measuring angle NOT
• User calibration settings always relate to a specific
powder from specific manufacturer and NOT to a
specific colour.
• The measurement object needs to be cooled
down when the measurement is performed.
• The cured setting is not meant for QC applications
as per formed by a regular coating thickness
gauge. It mainly comes in handy on curved objects
and corners that cannot be measured with a
regular coating film thickness gauge
• In case of new combinations of materials check
measured PowderTAG values against a regular
coating thickness gauge.
• When a second layer of coating is applied the
PowderTAG will add 25% of the layer thickness of
the first (cured) layer to the measured value of
the second layer. To calculate the actual layer
thickness of the second layer this 25% has to
be substracted from the measured value.

| 14 15 |
This chapter is intended for first-time users of the
instrument. It is a quick introduction to the use
of the instrument and highlights the essential
functions shortly.
7.1 Insert batteries and connect sensor
1. Take the instrument and the batteries out of the
storage case.
2. Take the instrument from the rubber harness and
remove the screws on the battery compartment
lid manually or, for example, using a coin.
3. Insert the batteries into the battery compartment.
Pay attention to the correct polarity (see battery
compartment).
4. Close the battery compartment lid and secure it
with the screws.
5. Slide the display unit back into the rubber
harness.
6. Take the sensor out of the case and push the
plug on the cable end into the corresponding
socket at the top of the display unit. There is only
one correct way: the red spot on the plug and the
red spot on the socket should face each other.
7.2 Starting the PowderTAG and perform
measurements
1. Press the on-off button for 2 seconds to turn the
PowderTAG on. The instrument is immediately
ready for operation. The display shows the
selected application.
2. In the initial start-up the factory calibration
is preselected. This is suitable for simple, fast
measurements. It should however be noted
that, depending on the measurement task, larger
measurement inaccuracies may occur.
3. Activate the sensor by pressing the measurement
button once. An active sensor is acoustically
confirmed and indicated by a steady light of
the led pointers; do not stare in it directly.
The instrument is now ready to measure.
4. Point the sensor to the object. Make sure the
three LED pointers combine into one point on the
object. This is the correct measuring distance.
5. Press the measurement button to trigger the
measurement. Start and end of the measurement
are indicated by a brief flash of the positioning
LEDs and an acoustic signal.
6. The measurement result is shown on the display.
The meter is ready for the next measurement.
7. If you want to delete the measurement
press delete shortly. If you want to start
over with the statistics, press delete long and all
measurements will be deleted.
7 GETTING STARTED
The measuring equipment will switch automatically
to the menu for measurement operation. This
means measurement can start straight away.
In the measurement menu, essential information on
the measurement such as current reading, statistical
indices etc. are collected. An overview of the
corresponding symbols and their meaning is shown
in the following table.
Mean
Minimum
Upper limit exceeded
Limits met
Number of the measurement series
Standard deviation
Maximum
Lower limit not met
Reading offset
Number of the meaurement
You read the current calibration used and the
battery level in the top status bar. The central field
displays all information on the current measurement
series. You press the left function button to switch
statistical values between minimum, maximum,
standard deviation and mean.
Tapping the central context button Delete, deletes
the current reading from the series. To delete all
readings, you must hold the Delete button down for
approx. 5s. Pressing the right button Back opens the
measuring equipment main menu
8 USER INTERFACE

| 16 17 |
8.1 Main menu
After turning the unit on the measurement screen
appears. The context sensitive function but-ton on
the right has the function ‘back’. This can be read in
the display. It takes you back to the main menu.
The context sensitive function buttons should be
used to navigate through the menu:
Measure:
Opens the measurement screen with the recently
used calibration and the last recorded values.
Previously commenced measurements can be
continued immediately.
Measure settings:
Opens the menu to select a new calibration.
The following applications (calibrations) are
available:
Powder:
Measures the expected dry film thickness after cure
of powders with an expected dry film thickness
under 200 µm. This function probably will be used
mainly.
Powder thick:
Measures the expected dry film thickness after cure
of powders with an expected dry film thickness of
200 µm and up.
If the expected coating thickness is more than
150µm or 200µm and errors occur during
measurements, we advise to choose this setting and
continue with the measurements.
Cured:
Measures the dry film thickness after cure. The
cured setting is not meant for QC applications as
performed by a regular coating thickness gauge.
It mainly comes in handy on curved objects and
corners that cannot be measured with a regular
coating film thickness gauge
User calibration:
See chapter 10.
Limits:
Activate and set min max limits.
Instrument settings:
Opens the menu for basic settings and provides
access to language, statistics, units, precision mode,
sound, power saving, check instrument, factory
reset and information.
8.2 Measurement screen
The measurement screen shows layer thickness
measurements and statistical information can be
read.
By pressing the left context sensitive function
button the display of statistical values (if enabled)
can be switched between the following statistic
functions:
Mean value
Max deviation
Highest value
Lowest value
When coating thickness limits are defined (see
section 8.4), the left context sensitive function
button description shows compliance or higher
( ) is - or lower ( )
Pressing the center function button shortly, deletes
the last recorded measured value. Pressing it long
deletes all recorded values. Pressing the right
function button opens the main menu.
8.3 Measure settings
The Measure Settings menu allows you to load,
edit, create and delete calibrations, and set limits.
Use the arrow keys to highlight the corresponding
calibration and press OK. You will immediately be
redirected to the measurement screen. The desired
calibration appears in the display and you can start
a measurement immediately. For more information
on creating and editing calibrations, see Chapter 10.
It is not possible to delete or edit factory
calibrations.
8.4 Limit values
• Selecting the function ‘limit values’ (at the end
of the measure settings menu list) opens a
cor-responding menu for selecting and activating
limit values.
• You can switch the limit values on or off by
pressing the OK button when the desired function
is selected.
• To change the Min and Max values, press the arrow
function button until the cursor is at the position
you want to change. Press the arrow function
button again to change the value (position) and
confirm with the OK function button. The cursor
jumps to the next digit. Repeat this for each digit.
• Use the arrow button to change or confirm with
the OK button.
• Compliance with or under-/overshoot of activated
limit values are indicated symbolically in the
measurement screen.
• Selecting the Back button saves the settings
you have made and returns you to the Measure
Settings menu.
8.5 Instrument settings
The following functions can be changed in the
Instrument Settings menu:
Language: English, German, Dutch*
Statistics: On or Off* When on is
selected the display shows
the statistics while measuring
Units: Micron (μm) or mils*
Precision mode: On or Off*
Sound: On or Off*
Power saving: Always 0n, 3, 6, or 10 min*
Check instrument: Checks the UV source. If the
result is“not okay’ for five
times in a row, even after
changing batteries, the
instrument needs
to be returned to TQC Sheen.
Factory reset: Deletes all measured values,
user calibrations, and user
settings
Information: Displays the version and date
* To change the settings, select the correct setting
and press the OK button.
8.6 Check instrument
1. Go to the instrument settings menu and choose
Check instrument
2. Take the reference socket / verification tool out of
the case
3. Place the sensor on the reference socket
verification tool
4. Press the OK button to start the check
5. The displays shows if the test function (UV source)
is OK or not (NOK)
6. If the result is “not okay’for five times in a row,
even after changing batteries, the instrument
needs to be returned to TQC Sheen.

| 18 19 |
9.1 Notes for coating thickness measurement
To carry out the correct film thickness
measurements not only a proper handling of
the measuring instrument are an advantage, but
also a basic knowledge of general handling of
coating thickness gauges and the corresponding
metrological requirements.
This mainly concerns the following topics:
- Selecting the suitable measuring method
- Statistical evaluation methods of measurement
series
- Interpretation of measured values
We recommend in case of new (and random
sample-based) combinations of materials, to check
measured values of the PowderTAG against values
obtained by other layer thickness measurement
methods (such as a regular coating thickness
gauge). If necessary the PowderTAG values can be
corrected via a user calibration. (See section 10.3)
9.2 Preparation for measurement
Select the calibration that suits the measurement
task. Depending on the application, you can
select an existing factory calibration (powder,
powder thick, cured). Measurements with
maximum measuring accuracy can be achieved
with calibrations that have been created from the
combination of materials to be examined (see
Chapter 10).
When a second layer of coating is applied the
PowderTAG will add 25% of the layer thickness of
the first (cured) layer to the measured value of the
second layer. To calculate the actual layer thickness
of the second layer this 25% has to be substracted
from the measured value.
E.G.: the first layer (cured) is 100 µm. The PowderTAG
measures 85 µm on the second layer. Then the
actual thickness of the second layer is 60 µm. (25%
of 100 µm = 25 µm. 85µ - 25 µm = 60 µm)
9.3 Performing measurements
Freehand measurements
Photo-thermal measuring processes are non-
contact thus non-destructive.
While performing a freehand thickness
measurement it is important to keep the correct
working distance to the object. The LED-pointer
helps to achieve this. The pointer consists of three
on the sensor positioned LEDs. When the three LED
pointers combine into one point on the object the
correct distance is achieved and a measurement
can be performed.
Measurements with distance cap
Generally, the use of a distance cap (Art. No LD5852,
to be ordered separately) is recommended for
touch-sensitive materials. This makes it possible to
maintain an accurate working distance without the
risk of touching an object.
Measurements with Tripod
For the contactless measurement of small parts and
geometries, we recommend using a tripod.
10.1 General guide lines
Measure settings menu of the PowderTAG shows all
the Calibration options. Three factory calibrations
are available: Powder, Powder Thick and Cured.
It is possible to create user calibrations based on the
factory calibrations. The PowderTAG has the option
of single-point or two-point calibration.
To ensure an optimum calibration the following
should be observed:
The quality of a calibration influences how precisely
the layer thicknesses of a material system can
be determined. A careful approach is therefore
essential.
Please note that the powder coatings may vary
greatly in nature and composition. Since the color
in the photo-thermal layer thickness measurement
also plays an important role, under cer-tain
circumstances, despite calibration it occasionally
may come to unsatisfactory measurement results in
the color range of bright yellow, orange and red!
Calibration should be performed on a calibration
object. The material properties of this calibrati-on
object should match the material properties of the
object to be measured as closely as possible. The
better both objects match the better the calibration,
thus the accuracy of measurement.
The results of a film thickness measurement
only covers the measured positions of an object.
It is therefore important to ensure that the
measurement position matches the created
calibration and the measurement position of the
reference method. Moreover, it should in certain
circumstances be ensured (by means of statistical
methods), that the layer thickness information of
the reference measurement and the calibration
measurement are obtained from the same
measurement area. This is particularly important
with rough objects.
10.2 Factory calibrations
The PowderTAG has three factory calibrations
(powder, powder thick and cured)
Powder:
Measures the expected dry film thickness after cure
of powders with an expected dry film thickness
under 50 - 150 µm.
Powder thick:
Measures the expected dry film thickness after cure
of powders with an expected dry film thickness of
50 - 250 µm and up.
Cured:
Measures the dry film thickness after cure of 50 -150
µm.
The “Check Instrument”function in the “Instrument
Settings”menu is no calibration tool. It only checks
the UV-source (see section 8.5).
10.3 User calibration
The PowderTAG allows the use of up to 20
calibrations. You can create a new calibration by
selecting New Calibration (Measurement Settings>
User Calibration> New Calibration). In the field type
a factory calibration (powder, cured, powder thick)
suitable for the material system to be examined
can be selected. It contains basic information like
measuring times and measuring method. After
saving the new calibration, the menu for single-
point calibration or two-point calibration pops up.
This allows for rapid calibration.
10.4 Calibration methods
10.4.1 Single point calibration - Powder
After confirming Powder and single-point
calibration, you end up in the measured value recor-
ding of the calibration menu. Here you can make
measurements, and adjust the measurement value
manually.
9 MEASURING MODE 10 CALIBRATIONS

| 20 21 |
We suggest the following calibration procedure for
Powder application:
• Create a reference object and choose the area you
want to measure.
• Take a series of 5 measurements of this area with
the PowderTAG. Use the measurement button to
perform the measurement. The PowderTAG
displays the mean of all measurements.
• Remember the area you have measured.
• Cure the reference object.
• Take a series of 5 measurements of the
cured reference object on the same area,
but with another layer thickness measurement
method (such as a regular dry film thickness
gauge). The mean of this measurements is the
desired value.
• Use the cursor and the arrow key to correct the
recorded (average) PowderTAG value to the
desired value. The value consist of 3 digits that
has to be adjusted and confirmed separately. Use
Function button 6a to change each digit. Use
function button 6b to confirm each digit and to
confirm the final value.
Example:
With a regular coating thickness gauge you have
determined that the average layer thickness of
a certain spot is 80µm. On this same spot the
PowderTAG averagely measures 60µm. This way you
have determined that a specific powder deviates
+20μ to the actual layer thickness. By correcting
the value to 80μm (and store it), the deviation is
compensated.
If no reference values are available during the
calibration (for example, because these must
be determined by a destructive procedure after
calibration), the calibration can be saved and
corrected at a later time after a repeated call.
10.4.2 Two-point calibration - Powder
Two-point calibration provides better accuracy
than single-point calibration. The results are
optimal for layer thicknesses between the reference
thicknesses used. It is therefore recommended to
use calibration objects which layer thicknesses are
at the outer limits of the expected measuring range
(for example, components which are at the upper or
lower limit of the tolerance range).
To set the calibration, simply follow the procedure
described in section 10.4.1 twice. Once with a low
layer thickness and once with a high layer thickness.
Example:
With a regular coating thickness gauge you have
determined that the lower layer thickness averagely
is 60µm. On this same area the PowderTAG
measured a mean of 53µm. The average higher
layer thickness of another area is 100µm, measured
with a regular coating thickness gauge, whereas the
PowderTAG measures 85µm on this area.
This way you have determined that a specific
powder deviates +7μ to the low layer thickness and
+ 15 µm to the higher layer thickness. This offset is
calculated throug hout the range, as shown in the
chart below.
If no reference values are available during the
calibration (for example, because these must
be determined by a destructive procedure after
calibration), the calibration can be saved and
corrected at a later time after a repeated call.
10.5 Loading calibrations
Both factory set calibrations and user calibrations
can be loaded in the measurement settings menu.
Factory set calibrations are powder, powder thick
and cured. User calibrations are listed s eparately in
measure settings > user calibration>load.
After selecting the appropriate calibration the
calibration is activated and the PowderTAG switches
to the Measurement display.
10.6 Editing user calibrations
Factory calibrations cannot be deleted or changed!
Go to measure settings > user calibration>edit.
select the desired user calibration and press OK.
Now you are back in the registered measured value
for the calibration. For instance the value of the
example as described in section 10.4.1 will be Offset
+20µm.
Use the cursor and the arrow key to correct the
offset. The value consist of 3 digits that has to be
adjusted and confirmed separately. Use function
button 6b to confirm each digit. By changing the
first digit you can also change the + - offset. The
new offset is automatically stored when you touch
the back button.
In the edit menu it is also possible to delete the user
calibration. When the sentence“delete Calibration”
is marked black, and the OK button is pushed the
user calibration will be deleted.
10.7 Deleting user calibrations
All measured values and user calibrations can be
deleted immediately via the menu Instrument
settings >> Factory reset. The PowderTAG returns to
the measurement screen. All User settings will be
reset as well.

| 22 23 |
11.1 Transport and storage
The meter should always be stored and transported
in the supplied case. It should be noted that the
sensor and the display unit should always be placed
in the appropriate compartment.
Improper storage may cause damage to the
instrument.
Carrying case and instrument must be stored under
the following conditions
- Do not store outdoors
- Store in a dry and dust free
- Do not expose to aggressive media
- Protect from direct sunlight
- Avoid mechanical vibrations
- Storage temperature: 0 to 55 ° C
- Relative humidity: max. 80%, at temperatures of
32 °C max. 50%See also section 11.5 Batteries in
carry-on baggage (aircraft cabin).
11.2 Maintenance
All maintenance work must be carried out
exclusively by the company TQC Sheen. In
particular, the casing of the display unit must never
be opened. For accumulating maintenance the
company TQC Sheen must be consulted.
11.3 Cleaning
1. Turn off the monitor and unplug the mains plug
2. Wipe display unit and sensor gently with a slightly
damp, soft cloth.
Use of corrosive, abrasive and scratching cleaners
can cause considerable damage to the sensor and
the display unit.
- Never use solvents for cleaning.
- Always wipe display unit and sensor with a damp,
soft cloth.
11.4 batteries
The supplied Li-ion batteries may only be charged
with the supplied charger. The electronics of the
charger control the charge-dependent charging
current and monitores the correct maintenance-
charge voltage. Charging the battery should never
take place in the presence of flammable materials!
For optimum storage of Li-ion battery state of
charge should be 55-75%, cool storage is favorable.
The electrolytes in the cell must not freeze, which
corresponds to a minimum temperature of -25 ° C.
Recommended storage temperature is 15 ° C at a
charge level of 60%. A battery should be recharged
every six months to 55-75%.
11.5 Precautions - Batteries in carry-on
baggage (aircraft cabin)
The battery employed in PowderTAG is a generic
single cell Lithium-Ion battery, 3.7V 850mAh. The
battery employed in PowderTAG has a capacity of
3.11 Watt-hours, and is rated for low-power use
only. A protection circuitry has been applied to the
PowderTAG mainboard as per best practice.
- The battery is rated below 100 Watt-hours per
battery
- The battery is protected from damage and short
circuit
The battery is assembled into an end product and
classified to be freely transported on aircraft both
in carry-on and check-in luggage. When carried-on,
please keep the provided product documentation
with the instrument in order to be able to provide
regulatory agencies relevant information about your
instrument when requested.
The right of technical modifications is reserved.
The information given in this manual is not
intended to be exhaustive and any person using the
product for any purpose other than that specifically
recommended in this manual without first
obtaining written confirmation from us as to the
suitability of the product for the intended purpose
does so at his own risk. Whilst we endeavour to
ensure that all advice we give about the product
(whether in this manual or otherwise) is correct we
have no control over either the quality or condition
of the product or the many factors affecting the use
and application of the product. Therefore, unless
we specifically agree in writing to do so, we do not
accept any liability whatsoever or howsoever arising
for the performance of the product or for any loss
or damage (other than death or personal injury
resulting from our negligence) arising out of the use
of the product. The information contained in this
manual is liable to modification from time to time in
the light of experience and our policy of continuous
product development.
11 CARE AND MAINTENANCE 12 DISCLAIMER

www.tqcsheen.com
This manual suits for next models
1
Table of contents
Other TQC Sheen Measuring Instrument manuals
Popular Measuring Instrument manuals by other brands
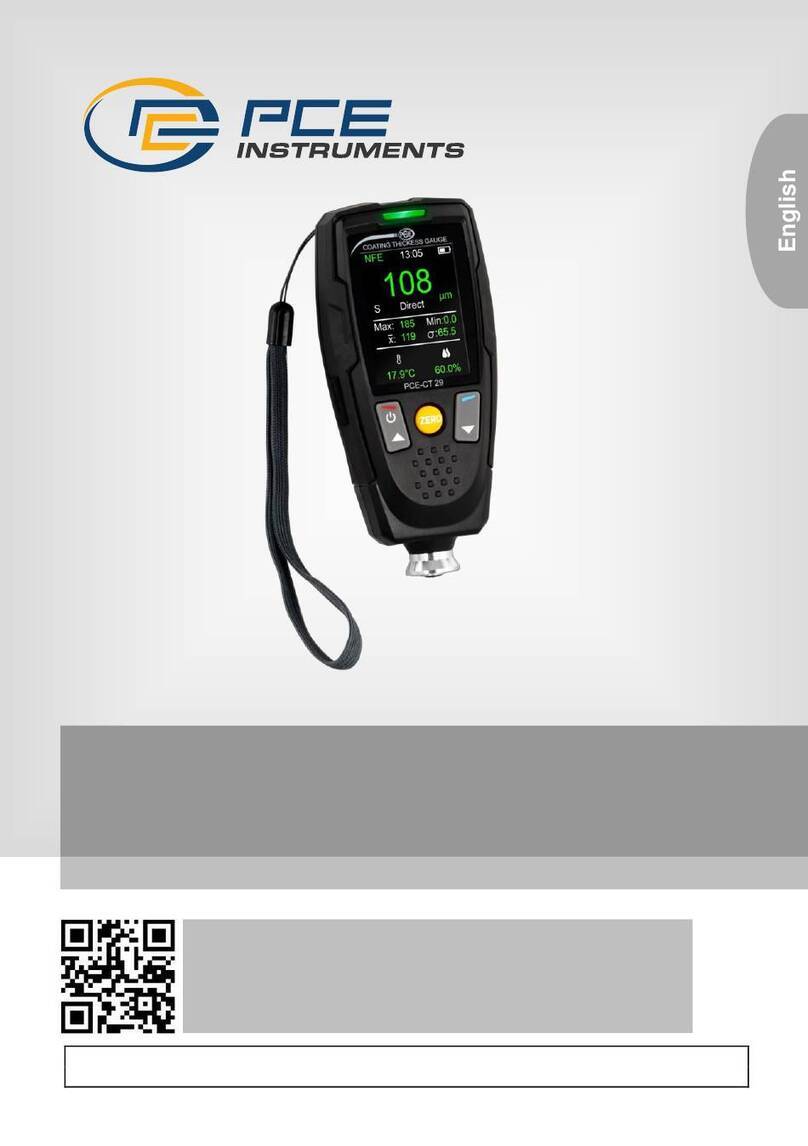
PCE Instruments
PCE Instruments PCE-CT 29 user manual

Cirrus
Cirrus CK675 user manual
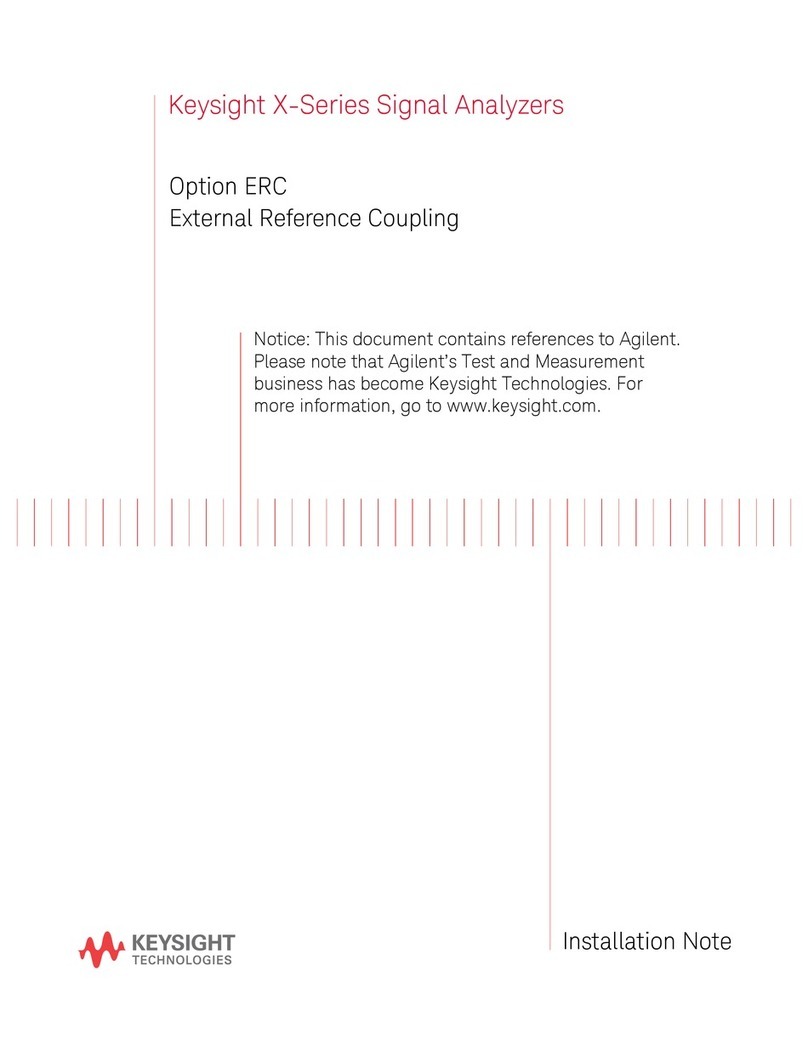
Keysight
Keysight x series Installation note

Radiodetection
Radiodetection RD4000T3F user manual
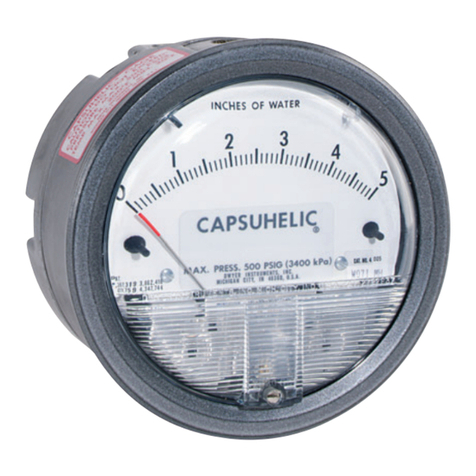
Dwyer Instruments
Dwyer Instruments Capsuhelic 4000-0 Installation and operating instructions

Gantner
Gantner Q.brixx quick start guide