TrafFix Scorpion II METRO TL-2 PLUS User manual

P/N 13089 Rev A1 Dated 5/13/2020 1
Scorpion II® METRO Truck Mounted Aenuator
Assembly Manual and Mounng Instrucon Guide
(For Model: Scorpion II®METRO 10000 Series TMA)
160 Avenida La Pata
San Clemente, CA 92673
This Manual is Available at www.traxdevices.com

P/N 13089 Rev A1 Dated 5/13/2020 i
This Page is Intenonally Le Blank

P/N 13089 Rev A1 Dated 5/13/2020 ii
Scorpion II® METRO TMA
Introducon to Assembly and Mounng Instrucon Guide
Important: These instrucons pertain only to the assembly and mounng of the Scorpion II
Metro Truck Mounted Aenuator (TMA) TL-2 PLUS. These instrucons are only for the
assembly of the models and/or accessories cited in each secon. Any deviaon from the
models and accessories shown would require consultaon with the appropriate highway
authority engineer and/or cered TrafFix Devices, Inc. representaves. Contact informaon
of these representaves can be found on the last page of this manual (Pg.42).
Proper Installaon of the Scorpion II Metro TMA is essenal for proper performance of the system. For this
reason, contacng a TrafFix Devices, Inc. Cered Aenuator Installer for assistance in mounng the
system is recommended. Contact TrafFix Devices, Inc. to obtain a list of Cered Installers in the area.
Please read this manual in its enrety before assembling, installing, or operang the Scorpion II Metro
TMA. The informaon in this Manual supersedes all previous versions and manuals, with updated
illustraons and other informaon available at me of prinng; however; TrafFix Devices, Inc. reserves the
right to make changes at any me. For any quesons on proper Installaon and Operaon of the
Scorpion II Metro, please contact us at (949) 361-5663.
!Important: This manual applies to the Scorpion II® METRO TMA by TrafFix Devices, Inc. It
pertains only to the models referenced herein. It requires that all Assembly, Mounng, Service
and Repair parts be Genuine Scorpion II METRO parts that have not been modied or repaired
from the original in any way, unless with prior knowledge, consultaon and approval by TrafFix
Devices, Inc. Engineering.
!
160 Avenida La Pata
San Clemente, CA 92673
www.traffixdevices.com [email protected]

P/N 13089 Rev A1 Dated 5/13/2020 iii
Table of Contents
Secon 1 Limitaons and Warnings ………………………………………………………………………………………. 1
Operang Instrucons………………………………………………………………………………………….... 2-3
Safety Instrucons & Precauons…………………………………………………………………………… 4
Notes………………………………………...………………………………………………………………………….. 5
TMA Metro Parts List- Major Components…………………………………………………………….. 6-7
Secon 2 Assembly of Scorpion II Metro TMA.…………………………………………………………………….. 8
Recommended* Assembly Tools…………………..………………………………….……………… 9
Pre-Assembly Checklist/Scorpion II Metro Registraon……………………………………. 10
Remove Packaging/Tail Light & Side Marker Light Inspecon……….…………….….. 11-12
Metro TMA Assembly Overview ……………………...………………………………………..….. 13-14
Metro TMA Assembly…………………………………...………………………………………………. 15-18
Module C Installaon……………………………..……………………….…………………………….. 19
Module A Installaon……………………………..……………………….…………………………….. 20
Hydraulic Pump Assembly/Parts List…………………………….…………...…………………... 22-23
Secon 3 Standard Truck Mounng Installaon……………………….…………………………………….…… 24
Standard Flatbed Truck Mounng Installaon…………………………………………….…… 25-29
Dump Truck Mounng Installaon……………………………………………...………………….. 30-33
Installing the Fast-Trak SwiConnect™ to the TMA……………………………………….... 34
Fast-Trak SwiConnect™ Conguraon 1……………………………………………………..... 35-36
Fast-Trak SwiConnect™ Conguraon 2……………………………………………………..... 37
Fast-Trak SwiConnect™ Conguraon 3……………………………………………………..... 38-39
Secon 4 Limited TMA Warranty………...…………………………………………………….……………………..... 40
Metro TMA High Pivot…………………………..…………………………………………………………...... 41-44
Metro TMA Low Pivot…………………………..…………………………………………………………...... 45-48
TrafFix Devices, Inc. Contact Informaon…………………………………………………………...... 49
Page

P/N 13089 Rev A1 Dated 5/13/2020 1
Limitaon and Warnings
TrafFix Devices Inc. (TDI), in compliance with the Manual for Assessing Safety Hardware
(MASH) recommended procedures for the Safety Performance of Highway Features. TDI
contracts with ISO accredited testing facilities to conduct crash tests, evaluation of tests, and
submittal of results to the Federal Highway Administration for Eligibility for Federal-Aid
Reimbursement. The Scorpion II Metro Truck Mounted Attenuator (TMA) system was tested
to meet the safety evaluation guidelines of MASH. The Scorpion II Metro has been tested at
TL-2 PLUS (50 mph/80 km/hr) speed conditions. These tests are intended to evaluate product
performance by simulating those impacts outlined by MASH involving a range of vehicles on
the roadways. From cars with an approx. weight of 2425 lbs (1100 kg) to trucks with an
approx. weight of 5004 lbs (2270 kg). The Scorpion II Metro TMA is a TL-2 PLUS tested
device is capable of decelerating and stopping light and heavy weight vehicles 2425 lbs [1100
kg] and 5004 lbs [2270 kg] in accordance with the criteria of Tests 2-50, 2-51, 2-52, and 2-53
for FHWA Eligibility (Reference FHWA Eligibility Letter CC-158). TrafFix Devices does not
represent nor warrant that the results of these controlled tests show that vehicle impacts with
the products in other conditions would necessarily avoid injury to person(s) or property.
Impacts that exceed the system’s specifications may not result in acceptable crash performance
as outlined in MASH; relative to structural adequacy, occupant risk, and vehicle trajectory. TDI
expressly disclaims any warrant or liability for injury or damage to person(s) or property
resulting from any impact, collision, or harmful contact with products, other vehicles, or nearby
hazards or objects by any vehicle, object or person, whether or not the products were installed
by third parties. The Scorpion II Metro TMA system is intended to be assembled, and
maintained in accordance with specific State and Federal guidelines. TDI offers a reflective
delineator panel for its TMA line of products. However, the material is only intended to
supplement delineation required by the Department of Transportation’s “Manual on Uniform
Traffic Control Devices” (MUTCD). The appropriate highway authority approved engineer
should be careful to properly select, assemble, and maintain the product. Careful evaluation of
the speed, traffic direction, and visibility are some of the elements that require evaluation for
the proper selection of a safety appurtenance by the appropriate specifying highway authority.

P/N 13089 Rev A1 Dated 5/13/2020 2
Operang Instrucons
Proper Operaon includes knowledge of TMA use in Work Zones, both Moving and Staonary, including
the proper spacing, to allow for “roll-ahead”. Before use, the Operator should have prior knowledge/
discussion of the Work Zone in which the TMA will be deployed and that the TMA model used has been
tested and passed to Test Level 2 PLUS, 50 mph/80 kph. TMA’s should only be operated by individuals
properly trained in their use in work zones.
Pre-Use Inspecon
1. Walk around the unit inspecng for damaged, loose, or missing bolts, pins, coer pins and safety
snaps.
2. Inspect for damage to the energy absorbing modules and aluminum tubes, checking for deep
gouges, deep scratches, warping, or cracking.
3. Inspect the steel structure for damage, looking for warping, cracks, breaks or other damage.
4. Inspect all lights for proper operaon (including arrow/message board if applicable).
5. Cycle the unit from stowed to deployed and back to stowed posion (see direcons below),
ensuring proper sequence and funcon (including arrow/message board li system if aached) pay
close aenon for any binding or “slop” during operaon and that the alarm is funconing
properly.
6. Check road clearance of TMA in deployed mode, to ensure it is in specicaon (12 inches ±1 inch).
7. Ensure that retroreecve sheeng is in place and meets requirements for job.
8. Check visually for hydraulic leaks.
9. Check to ensure that there are no loose items on the truck that can become a projecle during an
impact.
10. Make sure items in the cab of the vehicle are secure and cannot come loose and become a
projecle should an impact occur.
11. Adjust the headrest properly for the driver of the vehicle.
12. Any deciencies should be corrected before use.
MUST BE FULLY
POWERED
DOWN FOR
TRAVEL
0 TO 60 MPH
MUST BE FULLY POWERED
DOWN FOR DEPLOYMENT
0 TO 30 MPH
WARNING:
ALWAYS SUPPORT
THE METRO TMA
WHEN PERFORMING
ANY TYPE OF WORK
ON THE UNIT

P/N 13089 Rev A1 Dated 5/13/2020 3
To Raise (“Store”) the Unit for Transport
1. Ensure that both the truck bed and area above the rear of the host vehicle is clear.
2. Locate the desired controller, either the in-cab controller (if installed) or the rear plug-in. If using
the rear plug-in, and it is not already plugged in, plug it into the socket on the TMA near the rear
passenger side of the truck.
3. If the unit is to be transported, ensure that the drop jacks are fully retracted and pinned and that
the swivel jacks are fully retracted and rotated to the stored and locked posion.
4. If using the rear plug-in controller unplug and store in the cab.
To Lower (“Deploy”) the Unit for removal or Use
1. Ensure that both the area above and to the rear of the host vehicle is clear.
2. Plug in the controller (see #2 above) or locate the in-cab controller (if installed).
3. If the unit is being removed, the swivel jacks should be rotated to the deployed posion and the
drop jacks lowered and pinned to the correct height. If the unit is being deployed for use, all
jacks should remain in the stored posion.
4. Being careful to avoid the pinch points, push the “Down” buon unl the TMA is fully deployed
to a horizontal posion.
5. Connue to hold the Down buon for 4 more seconds aer the Arrow/Message Board Li System
(if aached) or the TMA has stopped moving. This will ensure the TMA is fully deployed and the
hydraulic system is at the proper pressure to hold it in posion.
6. Make sure the Arrow/Message Board is displaying the proper message.
Note: TMA must be in the stowed posion for travel to and from the Work Zone

P/N 13089 Rev A1 Dated 5/13/2020 4
SAFETY INSTRUCTIONS & PRECAUTIONS
A. Before aempng to install or operate the Scorpion II Metro TMA this manual should be read and
understood. Those areas with warnings or cauons should be carefully followed.
B. Before raising or lowering the TMA the operator should check that the area around the TMA is clear and
that personnel are not in or near the area.
C. Before operaon on the roadway, check all 1” diameter pins and bolts at the back-up and hinge areas for
ghtness and excessive wear. Also, check that all coer pins are in place.
D. Check that the two drop jacks are fully retracted and that the safety pins are in place. Also, check that the
crank jacks are fully retracted and rotated to the up and locked posion.
E. For correct operaon of the TMA in the deployed posion (horizontal posion), the TMA should be 12" ±
1” above the ground and horizontal to the roadway.
F. The responsible agency for the support vehicle should check that the following specicaons are met:
The support vehicle should weigh a minimum of 7,300 lbs (3,300 kg). If the support vehicle is ballasted,
the ballast should be properly anchored to the support vehicle frame to prevent movement during an
impact. The support vehicle should be equipped with proper operator safety equipment such as seat
belts, headrest, etc.
G. The support vehicle should have a straight frame design. An over axle (bent) frame design is not
appropriate for use on a TMA support vehicle.
H. Before disconnecng the TMA from the support vehicle, make sure the TMA is in the horizontal posion
with all jack fully deployed
Special Warnings
1. Aer a vehicle impacts the TMA, do not drive the support vehicle with the damaged TMA. Remove the
TMA at the backup and have the TMA transported back to the maintenance yard.
2. Check the TMA model to make sure that the posted speed matches the TMA capacity.
Scorpion II Metro = TL-2 PLUS, 50 mph (80 kph).

P/N 13089 Rev A1 Dated 5/13/2020 5
Notes:

P/N 13089 Rev A1 Dated 5/13/2020 6
Scorpion II Metro TL-2 Plus
Major Components

P/N 13089 Rev A1 Dated 5/13/2020 7
Scorpion II Metro TMA Parts List - Major Components
Item # Part # Item Description QTY/TMA
110100L-Metro-HPP-KIT Cartridge Tube Assy, LH, Includes: C-Tape, Warning Labels, Side Marker Bracket
Installed 1
210100R-Metro-HPP-KIT Cartridge Tube Assy, RH, Includes: C-Tape, Warning Labels, Side Marker Bracket
Installed 1
311400E Module E, Absorbing Scorpion II Metro 1
411325 Angle, Module E Mounting 2
510300 Backup, Powder Coated Black 1
610352 Hydraulic Bracket, LH 2
710351 Hydraulic Bracket, RH 2
810750L Drop Jack Bracket, LH 1
910750R Drop Jack Bracket, RH 1
10 10725 Drop Jack w/ 6” Caster 2
11 10701 Swivel Jack w/ 6” Caster
2
10701MNJ Heavy Duty Swivel Jack w/ 6” Caster
12 10600TL2 Hydraulic Hose Kit, Scorpion II TL2 1
13 11010 Hydraulic Power Unit, 12V, Field Service Replacement
1
11011 Hydraulic Power Unit, 24V, Field Service Replacement
14 11200A Hydraulic Cylinder, 3” Bore, 8” Stroke, Fittings Installed 2
15
10508E-LED Tail Light Assy, LH, 10-30 Volt LED, Color Pattern: Red/Red/White
1
10504E-LED-RYR Tail Light Assy, LH, 10-30 Volt LED, Color Pattern: Red/Amber/Red
10504E-LED-YRW Tail Light Assy, LH, 10-30 Volt LED, Color Pattern: Amber/Red/White
16
10516E-LED Tail Light Assy, RH, 10-30 Volt LED, Color Pattern: Red/Red/White
1
10505E-LED-RYR Tail Light Assy, RH, 10-30 Volt LED, Color Pattern: Red/Amber/Red
10505E-LED-YRW Tail Light Assy, RH, 10-30 Volt LED, Color Pattern: Amber/Red/White
17 10518 Junction Block 1
18 10507C Motion Alarm, 10-30 Volt 1
19 10573 Side Marker Light, Amber, 10-30 Volt LED 2
20 10520 Housing, Side Marker Light 2
21 11400C-Metro Module C, Energy Absorbing, Scorpion II 1
22 10400A Module A, Energy Absorbing, 4” Yellow Avery MVP Sheeting 1
23 11300H Rear Diaphragm, Cartridge, Powder Coated Black 1
24 11327 Bottom Angle, Cartridge, Powder Coated Black 1
25 10465 Top Angle, Cartridge, Powder Coated Black 1
26
10508A-LED Cartridge Tail Light Assy, LH, 10-30 Volt LED, Color Pattern: Red/Red/White
1
10504A-LED-RYR Cartridge Tail Light Assy, LH, 10-30 Volt LED, Color Pattern: Red/Amber/Red
10504A-LED-YRW Cartridge Tail Light Assy, LH, 10-30 Volt LED, Color Pattern: Amber/Red/White
27
10516A-LED Cartridge Tail Light Assy, RH, 10-30 Volt LED, Color Pattern: Red/Red/White
110505A-LED-RYR Cartridge Tail Light Assy, RH, 10-30 Volt LED, Color Pattern: Red/Amber/Red
10505A-LED-YRW Cartridge Tail Light Assy, RH, 10-30 Volt LED, Color Pattern: Amber/Red/White
28 10557 ICC Bar Light Assy 1

P/N 13089 Rev A1 Dated 5/13/2020 8
Assembly of Scorpion II Metro TMA

P/N 13089 Rev A1 Dated 5/13/2020 9
1. IMPORTANT: Before beginning Assembly, please read and review the Installaon Secon of this
manual, paying close aenon to the checklist at the beginning of the secon.
2. Inspect the two pallets containing the Metro and Module A, shown in Figure 1, inspect for shipping
damage and completeness against the packing list. If there is anything missing or not complete,
contact a TrafFix Devices representave as soon as possible.
3. WARNING: TOP HEAVY– Indicates to move pallets with extreme cauon. The use of a forkli is
preferred when handling pallets. All personnel should be kept clear when the pallets are being moved.
4. Remove the shrink-wrap from the pallets using a ulity knife. Cauon: Be careful not to cut any wires
or parts!
Figure 1
Metro TMA (TL-2) Assembly
Recommended* Assembly Tools
1. Hammer
2. Tapered Pry Bar
3. Tape Measure
4. 12” Crescent Wrench
5. 1/2” Drive Socket Wrench
6. 1/2” Drive Socket (1-7/16”)
7. Open End Wrenches (1-7/16”, 3/4”, 7/16”)
8. 3/8” Drive Socket Wrench
9. 3/8” Drive Socket (7/16”, 3/4”)
10. Allen Wrench
11. Wire Cuer/Crimper
12. Floor Jacks or Stands (2 Ea.)
13. Forkli
*More or less tools may be needed.
MODULE A
PALLETIZED
METRO
PALLETIZED
When Cutting Bands,
Pieces from Top will Fall
M01589

P/N 13089 Rev A1 Dated 5/13/2020 10
Sample of
Module Serial Number
All Serial Numbers must coincide with each other
Idenfy Serial Number for Scorpion II Metro Truck Mounted Aenuator (TMA):
Strut
Cartridge
M01589
TMA
Module A
Pre-Assembly Checklist
Inial Inspecon: Compare the Packing List with the original order to ensure all items have been delivered.
Should any damage be found, or any items missing, contact the freight company as well as a TrafFix Devices
representave as soon as possible.
Scorpion II Metro Registraon
1. Once unpacked, ensure that the Scorpion II Metro TMA Serial Number matches with the number shown
on the Packing List and the pallet. Once conrmed that they are the same, record the Serial Number below
with all the serialized components to retain for personal records. TrafFix Devices, Inc. will require this Serial
Number for any possible repairs, warranty claims, and maintenance records.
Module A Serial Number
Module C
Serial Number
Module E
Serial Number
Module A Serial Number:_______________
Module C Serial Number:_______________
Module E Serial Number:_______________
Metro Pallezed Module A Pallezed

P/N 13089 Rev A1 Dated 5/13/2020 11
Removing Packaging for Inspecon
• Remove plasc wrap and cardboard with ulity knife.
*Be careful not to cut any wires or parts.
2. Observe the warning signs before unwrapping.
Module A TMA

P/N 13089 Rev A1 Dated 5/13/2020 12
Unwrap and Inspect: Tail Lighng and Side Marker Lights
Side Marker:
Tail Lighng:
3. Remove all cardboard from lights and inspect for damage.
TMA

P/N 13089 Rev A1 Dated 5/13/2020 13
Metro TMA Assembly Overview
1. Cut and remove Steel bands and cardboard from the
TMA.
2. Remove Module A from the pallet and open the box.
3. Remove Module C from the TMA.
4. Open parts and accessory box, conrm contents.
5. Place a piece of cardboard on the forkli to prevent
damage to the TMA diaphragm.

P/N 13089 Rev A1 Dated 5/13/2020 14
Metro TMA Assembly Overview
6. Li the TMA o the pallet using a forkli.
7. Remove mounng brackets from the pallet.
8. Reposion the TMA on the edge of the pallet.
9. Lower drop jacks so that the yellow paint is not showing.
10. Move the liing straps towards the Back-up of the TMA
and li, using a forkli, unl the unit is level.
11. Lower the swivel jacks so the TMA is no longer
supported by the forkli.

P/N 13089 Rev A1 Dated 5/13/2020 15
Steel Bands
1. Cut the Steel bands that are holding the components to the TMA. One person should be holding the components in
place, while another person cuts the bands. WARNING: Watch for falling components when cung the Steel Bands.
Remove the components and the cardboard from the TMA.
Metro TMA Assembly
2. Remove Module C from the TMA.
Module E
Module C

P/N 13089 Rev A1 Dated 5/13/2020 16
Metro TMA Assembly
1. Cut and remove the steel bands that hold the TMA to the pallet.
Steel Bands
3. Using a forkli, li the TMA o the pallet. CAUTION: Be sure the drop jacks are facing the forkli before liing the
TMA. Once the TMA is safely o the pallet, remove the mounng brackets that are on the pallet.
Mounng Brackets
2. To prevent paint from geng damaged, place a piece of cardboard on the blades of the forkli. Use the forkli to li
the TMA diaphragm o the pallet.
Table of contents
Popular Control Unit manuals by other brands
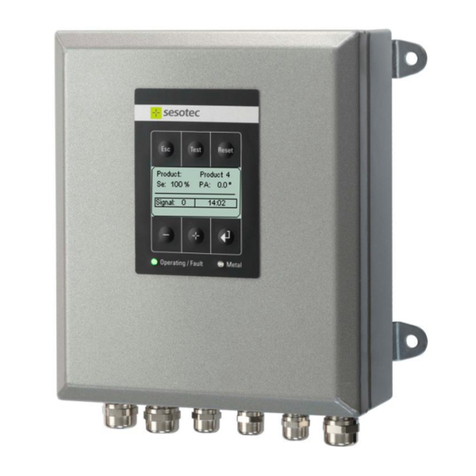
SESOTEC
SESOTEC PRIMUS+ operating instructions
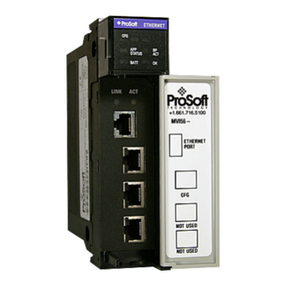
ProSoft Technology
ProSoft Technology inRax MVI56-DNPSNET user manual

Kohler
Kohler K-528-K1 Installation and care guide

Newhaven Display International
Newhaven Display International NHD-0420D3Z-FL-GBW-V3 manual
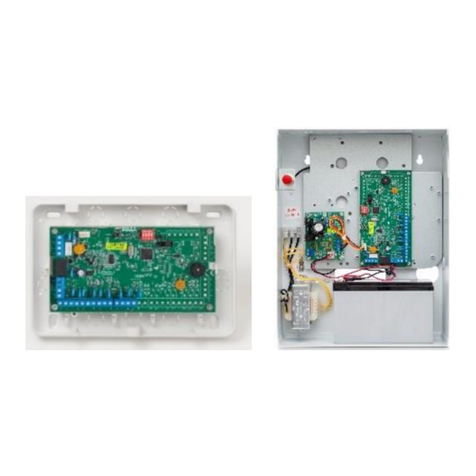
Pima
Pima ZEX508 installation instructions
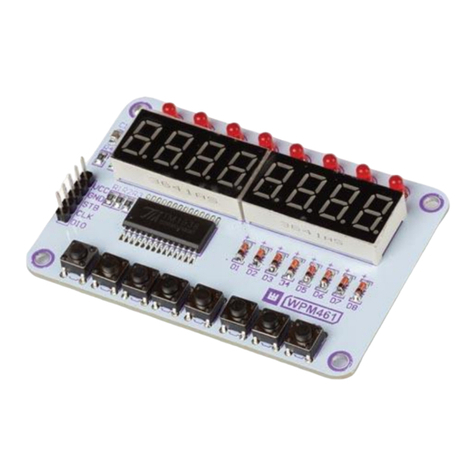
Velleman
Velleman Whadda WPM461 manual
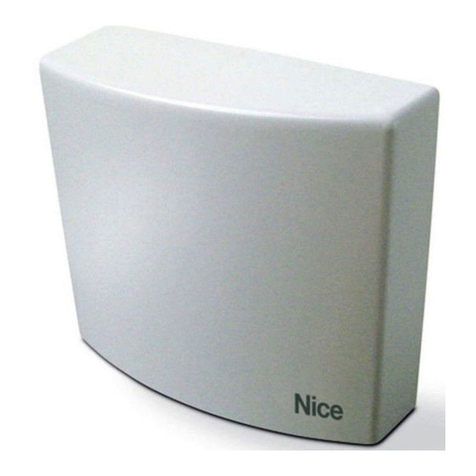
Nice
Nice MC200 Instructions and warnings for installation and use

Audioplex
Audioplex VC300 installation manual

Beninca
Beninca START-I operating instructions
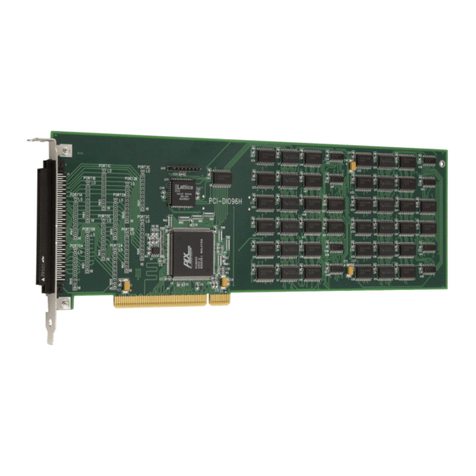
Measurement Computing
Measurement Computing PCI-DIO96H user guide
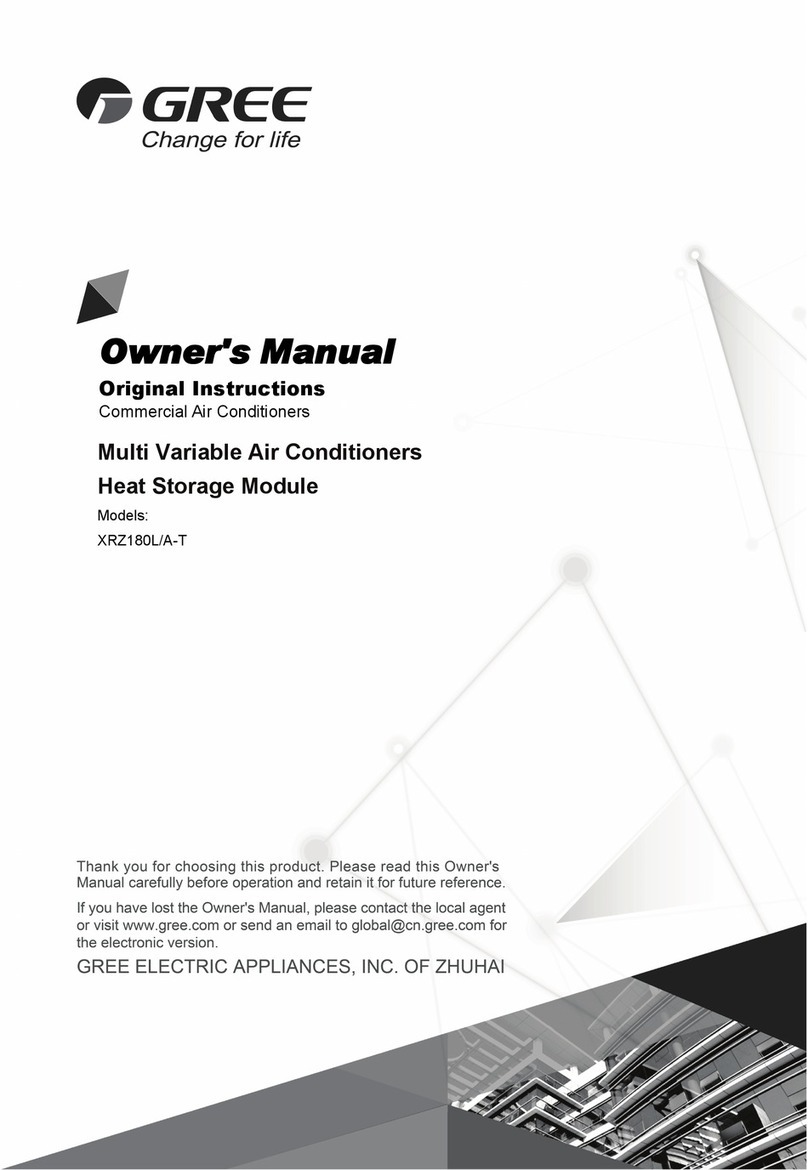
Gree
Gree XRZ180L/A-T owner's manual

Land Pride
Land Pride 380-168A installation instructions