SESOTEC PRIMUS+ User manual

1PRIMUS-PLUS-BA-CU-EN-5136.docx
Operating Instructions
Control Unit
PRIMUS+
We reserve the right to change the contents
due to product innovation or technical im-
provement.
Please state type of equipment and serial
number when contacting us.
Please read these instructions and keep the
manual safe!
Please observe and follow the safety notes!
Sesotec GmbH
Regener Straße 130 * D-94513 Schönberg
Telephone: +49 (0) 8554 308-0 * Fax: +49 (0) 8554 2606
Internet: http://www.sesotec.com
Service: Telephone: +49 (0) 8554 308-180

2PRIMUS-PLUS-BA-CU-EN-5136.docx
Manufacturer:
Sesotec GmbH
D-94513 Schönberg, Germany
Contact:
Sesotec GmbH
Regener Straße 130
D-94513 Schönberg, Germany
Tel.: +49 (0) 8554 3080
Fax.: +49 (0) 8554 2606
Internet: www.sesotec.com
Represented by:

Contents
3
Contents
1General information 6
1.1 Introduction 6
1.2 Field of application 6
1.3 Application reasons 6
1.4 System identification 6
1.5 Symbols used 6
1.6 EC DECLARATION OF CONFORMITY 6
1.7 Overview 7
2Design and method of operation 8
2.1 Functional principle 8
2.2 Functional and control elements 9
2.2.1 Operating module with LCD graphic display 9
2.2.2 Cable glands 9
2.2.3 PRIMUS+ / IO electronics board 10
2.2.4 PRIMUS+ / CU electronics board 12
3Dimensions and technical data 13
3.1 Technical data sheet, see annex 13
3.2 Supply connections, see technical data sheet in the annex 13
3.3 Environmental conditions for operation, storage, and transport 13
3.4 Noise levels 13
4Safety 14
4.1 Intended use 14
4.2 Safety signs 14
4.3 Dangers arising from non-compliance with safety notes 14
4.4 Safety information for operators 14
4.5 Safety information for operation, maintenance and cleaning 15
4.6 Safety information for commissioning 15
4.7 Safety information for storage and transport 15
4.8 Notes on residual risks 15
4.9 Notes on stable standing requirements 15
4.10 Consequences of unauthorised modification 15
4.11 Improper use 16
5Commissioning 17
5.1 Mechanical mounting 17
5.2 Connection of the equipment 17
5.2.1 PRIMUS+ / IO electronics board (control electronics board) 18
5.2.2 Electrical connections 18
5.2.3 PRIMUS+ / CU electronics board (evaluation electronics board) 19
5.2.4 Electrical performance 20
5.2.5 Drawing of input / output connections 20
5.2.6 Electrical connection of the equipment 21
5.2.6.1 Mains supply via safety socket 21
5.2.6.2 Mains supply via terminal box 21
5.2.7 Behaviour of machine at start up 22
5.2.8 Relays –operating status 23
6Menu / Operation PRIMUS+ 24
6.1 General Operation 24

Contents
4
6.2 Quick Start 25
6.2.1 Language Selection 25
6.3 Menu Structure 26
6.3.1 Main menu 26
6.3.2 Function menu items 26
6.3.3 Settings menu items 26
6.3.4 Output menu 27
6.3.5 Setup menu 28
6.3.6 Operating mask 32
6.3.7 Change product 33
6.3.8 Auto-Set 34
6.3.9 Product parameter 35
6.3.10 Conveying speed 35
6.3.11 Output 36
6.3.11.1 Output adjust 36
6.3.11.2 Output lock 37
6.3.11.3 Monitoring 37
6.3.11.4 Output Level 37
6.3.11.5 Output options 38
6.3.12 Setup 38
6.3.12.1 Logbook 39
6.3.12.2 Clear logbook (Menu item requires login) 41
6.3.12.3 Show counter 41
6.3.12.4 Device-Info 42
6.3.12.5 Revision 42
6.3.12.6 Change password (menu item requires login) 43
6.3.12.7 Language 43
6.3.12.8 Clock/Date (menu item requires login) 43
6.3.12.9 Setup options (menu item requires login) 44
6.3.12.10 Units (menu item requires login) 44
6.3.12.11 Frequency deviation (menu item requires login) 44
6.3.12.12 Factory settings (menu item requires login) 45
6.3.12.13 Login 45
6.3.12.14 Logout 45
6.3.12.15 Air pressure monitoring (option) (menu item requires login) 45
6.3.12.16 Flap monitoring (option) (menu item requires login) 46
6.3.12.17 External error (option) (menu item requires login) 46
6.3.12.18 Ejection monitoring (option) (menu item requires login) 46
7Errors and error remedying 47
7.1 Error messages 47
7.1.1 Receiver voltage too high 47
7.1.2 Receiver faulty 47
7.1.3 Transmitter faulty 47
7.1.4 Transmitter over temperature 47
7.1.5 Hardware CU 48
7.1.6 Hardware IO 48
7.1.7 Communication IO 48
7.1.8 Watchdog 48
7.1.9 Memory error 48
7.1.10 Short circuit MV 48
7.1.11 Connection MV 48
7.1.12 Air pressure 49
7.1.13 Diverter position 49
7.1.14 Sensor 1 faulty 49
7.1.15 Sensor 2 faulty 49
7.1.16 Filling level 49
7.1.17 External error 50
7.2 Undefinable activation of the switching outputs 50
7.3 Replacing the backup battery 51

Contents
5
7.4 Replacement of electronic boards 52
7.4.1 Replacing the CU electronics board PRIMUS+ 52
7.4.2 Replacing the IO electronics board PRIMUS+ 53
7.4.3 Replacing the display board 53
8Maintenance and cleaning 54
8.1 Maintenance 54
8.2 Cleaning 54
8.2.1 Hints for cleaning 54
8.2.2 Cleaning instructions 54
8.2.3 Care advice for stainless steel 54
9Spare parts 55
9.1 Spare parts view 55
9.2 Spare parts list 56
10 Shipping, preservation, waste disposal, transport, storage 57
10.1 Shipping, preservation, waste disposal 57
10.2 Transport 58
10.3 Storage 58
11 Annex 59

1. General information
6
1 General information
1.1 Introduction
The texts and illustrations in this instruction manual are for the exclusive purpose of explaining how to
operate and handle the control unit. The manufacturer accepts no responsibility for damage resulting
from the use or misuse of this equipment. All appropriate safety rules and regulations for the use of
this equipment must be adhered to. If you have any questions with regard to the installation and oper-
ation of this equipment please do not hesitate to contact us.
This instruction manual may not be copied, saved on computer or otherwise reproduced without the
prior permission of the manufacturer. Nor may any extract of this instruction manual be similarly repro-
duced.
1.2 Field of application
The PRIMUS+ control unit is used in combination with Sesotec metal detectors and separators in the
plastics, wood, food, chemical, and in a special version also in the pharmaceutical industry. Depending
on the respective version, these systems inspect packed, unpacked, or piece products, and bulk mate-
rials for magnetic and non-magnetic metal contaminations.
Of course they also are suitable for similar applications in other branches of industry.
1.3 Application reasons
Product liability
ISO 9000
TQM (Total Quality Management)
Protection of machines and quality assurance
1.4 System identification
The information in this instruction manual only applies to the PRIMUS+ control unit. A label with the
respective data is attached at every system.
1.5 Symbols used
Symbol
Signal word
Meaning
Danger
Warning: Possibility of severe or even fatal personal injuries.
Danger
The lightning symbol is an explicit warning that there is danger from
electric current.
Warning
Warning: Possibility of minor personal injuries or property damage.
Caution
Warning: Possibility of defects or destruction of the equipment.
Important in-
formation
Indicates an important information for the function.
Important
hint
Indicates an important hint for the function.
1.6 EC DECLARATION OF CONFORMITY
(See annex –EC DECLARATION OF CONFORMITY)

1. General information
7
1.7 Overview
PRIMUS+ Control Unit
Graphic display

2. Design and method of operation
8
2 Design and method of operation
2.1 Functional principle
Receiver
Transmitter
Receiver
Detection coil
Signal amplifier Analog/digital
converter
LCD graphic
display
Memory for
10 products
CU electronics IO electronics
Power
supply
CPU
Relay
I/O interface
Oscillator
Control Unit PRIMUS+
Control panel
Logbook
real time clock
CPU
Monitoring
The metal detector works with the so-called "balanced coil" principle:
The transmitter winding in the search coil creates a high-frequency electromagnetic field, which is re-
ceived by symmetrical placed receiver windings. The windings are connected against each other;
when undisturbed, the system is in balance.
An electrically conductible object within the detection area disrupts this balance and the electronic cre-
ates a switch signal.
A "teach in process” allows to suppress the conductivity of the product itself. Deviations from the
taught-in product are usually caused by metal contaminants, which are detected by the device with
high precision.
The metal detector is equipped with comprehensive test and analysis software to ensure fault-free op-
eration and retracing of product errors.
For reasons of the employed technology it is not possible to guarantee 100% metal
detection.

2. Design and method of operation
9
2.2 Functional and control elements
2.2.1 Operating module with LCD graphic display
1
Graphic display
LCD module
Display of operating and input masks
2
Operator keys
+ , - , , Esc
For operation and machine setting
3
Function key
Reset
Reset to restore the unit after metal or fault signal
4
Function key
Test
Test function for metal detectors
5
Metal LED
Metal
Lights red when metal detected
6
Operating / Fault LED
Operating
Lights green in normal operating mode, metal detec-
tion active
6
Operating / Fault LED
Fault
Lights red in case of fault and error
2.2.2 Cable glands
11
98 10 127
O pe ra ting/ Fau lt M eta l
Esc Test Reset
(7) Cable gland for the mains cable
(8), (9), (11) Cable gland for option
(10) Cable gland for free use
(12) Cable gland for connecting the detector coil

2. Design and method of operation
10
2.2.3 PRIMUS+ / IO electronics board
Connectors and termi-
nals:
(1) "Mains/Option" L/N: Control unit power supply
O1/O2: Optional 24V module power supply
(2) "Relay metal" Potential free change over contact
(3) "Relay fault" Potential free change over contact
(4) "Switching outputs" J5, connector, magnetic valves, signal combi., etc.
(5) "Switching inputs" J6, connector, sensors, switches, etc.
(12)"MV voltage external" J13, connector 24V external (option)
(18)"CU connection" J10, plug connection to CU electronics
Elements connected to
mains voltage:
(1) "Connector, Mains/Option"
(10)"Mains fuses
Elements connected to
external voltage:
(2) "Connector, relay metal"
(3) "Connector, relay fault"
Vorsicht
Fremd-
spannung
Light diodes:
(7) "Monitor LED, MV1-3" LD 10, magnetic valve (MV1)
LD 9, magnetic valve (MV2)
LD 8, magnetic valve (MV3)
(9) "Monitor LED, relay" LD 11, relay fault (84, 81, 82)
LD 12, relay metal (74, 71, 72)
(17) "Monitor LED, Vcc” LD 1, +24V
LD 2, +10V
LD 3, +3.3V
925 26 27 28 29 30 31 32
117 18 19 20 21 22 23 24
10
2
11
3
12
4
13
5
14
6
15
7
16
8
8171N8474L8272O1 O2
TP2
JP9
F1 JP10
LD10
LD9 LD8
LD11
LD12
J8
J10
J14
J13
LD1
LD2
LD3
TP1
1
J5 J6
JP33
2
1
3
8
14
6
2
5
7
J11
11 3 5
246
2345
6
7
8
9
14
13
3
11
15
(GND)
(GND_24V)
2
17
10
16
12
18

2. Design and method of operation
11
Jumper:
(6) "MV connection monitor" JP10, 1-2, MV1
JP10, 3-4, MV2
JP10, 5-6, MV3
(11)"MV voltage supply" JP3, 2-1external 24V (connector J13 +/-)
JP3, 2-3 internal, 24V (default)
(15)"Service jumper" J8, 5-6, plugged, enable, program update
Test points:
(8) "GND_24V” TP2, magnetic valves (MV1- MV3)
(16)"GND" TP1, IO electronics
Interface/plug connectors:
(14)"Program update" J11, mini USB, (only for trained staff)
JP9, USB selection (jumper plugged)
(13)"Data backup" J14, USB interface (system / product data)
JP9, USB selection (jumper open)
Fuse
Description
Type
F1
Mains supply
1.6A slow-blowing 1500A @ 250VAC 5x20mm

2. Design and method of operation
12
2.2.4 PRIMUS+ / CU electronics board
Connectors and terminals:
(1) "Receiver" J10, input signal from the detection coil
(2) "Transmitter" J7, output signal to the detection coil
(9) "Service interface" J11, diagnostics interface
(11) "FFC connector" J5, ribbon cable connector to the display module
(12) "Memory" J4, system / product data
Test points:
(3) "Transmitter signal" TP7, sine signal ( 25Vss) to the detection coil
(6) "GND" TP8, TP19, reference ground for all signals
Jumper:
(8) "Service jumper" J2, 5-6, plugged, enable, program update
Interface/plug connectors:
(10) "Program update" J9, mini USB, (only for trained staff)
(JP2, observe jumper position)
Light diodes:
(5) "Monitor LED,s, Vcc" LD 5, +24V
LD 6, +5V
LD 7, -5V
LD 8, +15V
LD 9, -15V
LD 10, 3.3V
(4) "Monitor LED’s" LD 4, green, operating status
LD 3, red, fault status
Memory:
(12) "Memory devices" J4, device and product data
(7) "Battery" BT1, for real-time clock

3. Dimensions and technical data
13
3 Dimensions and technical data
3.1 Technical data sheet, see annex
3.2 Supply connections, see technical data sheet in the annex
3.3 Environmental conditions for operation, storage, and transport
The environment of the control unit should be free of any chemical vapours such as softeners, chlo-
rine, or similar substances. The control unit must not be exposed to direct sunlight or to other envi-
ronmental influences (rain, snow and storm). For ambient temperature conditions for operation,
storage, and transport please refer to the technical data sheet in the annex.
3.4 Noise levels
Sound pressure level measurements (in acc. with DIN 45 635)
Peak value of sound pressure level at a distance of 1m from the machine surface and 1.60m above
the floor, LpA, 1m, max.
Result:
Idling: < 70 dB(A)
Activated: < 90 dB(A)
We reserve the right to change the contents due to product innovation or technical improve-
ment.

4. Safety
14
4 Safety
Our equipment conforms to all official technical safety regulations. However, as a manufacturer we be-
lieve it is our duty to make you aware of the following information.
The following safety and danger notes are intended for your protection, for the protection
of third parties, and for the protection of the equipment. The safety notes therefore should
always be observed!
4.1 Intended use
The equipment is intended for use in the following fields of application and only in combi-
nation with a corresponding detection coil of series GLS, C-SCAN DLS, P-SCAN RP: Suc-
tion/pressure conveyor applications, free-fall applications, and applications at a conveyor
belt. The equipment can be used in the plastics, food, animal feed, recycling, and chemical
industry. Basically it is possible to also use the system in other applications than the in-
tended use stated herein, but such applications always require the prior consultation and
approval of Sesotec GmbH.
4.2 Safety signs
Symbol
Signal word
Location
Meaning
Mains volt-
age
Cover of
the elec-
tronics
housing
This symbol indicates that mains voltage is used in the elec-
tronics housing, and that any connected external circuits
(e.g. at the metal relay) also may be energised. There is
danger of electric shocks due to the presence of mains volt-
age.
Connection symbols:
"Mains" (1)
"Metal" (2) und "Fault" (3)
4.3 Dangers arising from non-compliance with safety notes
Any non-observance of safety notes constitutes a danger for life and health.
4.4 Safety information for operators
The control unit PRIMUS+ may only be operated in the intended purpose and in a perfect func-
tioning condition, especially the cover of the electronic housing has to be closed during opera-
tion. Entered moisture has to be removed! All fixed warning signs on the equipment may not be
removed and have to be in a well recognizable condition. The operating instructions always
have to be in a legible condition and complete available. Prior to commissioning always make
sure that the applicable accident prevention regulations are observed. If the control unit is
not mounted at the detection coil, it must be properly and firmly fastened by means of the
four screws. The operator must make sure that the equipment is mounted at an ergonomic
height for operation. The operator may only appoint qualified personnel for operation, mainte-
nance and repair work. If potentially explosive materials are examined, the pertinent regula-
tions must be observed.
Emitted interference
Test report according to the provisions of:
BGV B11:2001-06
Regulations of the professional association for safety and
health at work.
Accident prevention regulations for electromagnetic fields.
E DIN VDE 0848-3-1: 05-2002
Safety in electrical, magnetic, and electromagnetic fields,
part 3-1: Protection of persons with active implants in the
frequency range of 0Hz to 300 GHz.
In the area where the operating personnel is working the electromagnetic field of the metal

4. Safety
15
detector or separator does not exceed the limits stated in the provisions. Therefore there
are no health impairments due to electromagnetic fields in this area for persons and for
wearers of medical implants such as cardiac pacemakers. Inside the coil of round or
closed tunnel coils, or on the surface of flat coils, the limits may be exceeded depending
on design and system version. If work is to be performed inside or at the search coil, per-
sons and wearers of medical implants such as cardiac pacemakers may only enter the
equipment when it is turned off, provided that size and design allow this.
4.5 Safety information for operation, maintenance and cleaning
Because of energised components in the electronics housing there is a risk of injuries due
to electric shock or burns. During operation the cover of the electronics housing must be
kept closed. Only qualified personnel may operate and clean the equipment.
If the electronics housing must be opened for maintenance or cleaning purposes, remove
any dirt and moisture from the electronics housing, so that no larger amounts may get into
the interior. Always disconnect the power supply and any connected external circuits be-
fore opening the cover. Any moisture that has penetrated into the interior must be re-
moved from the electronics housing. If any maintenance work must be performed in
energised condition, e.g. battery replacement, such work may only be performed by a
qualified electrician under strict observation of the attached warning labels and with due
regard to standard approved rules of electrical engineering.
No safe condition is established when outputs are switched "inactive" (with "Disable Out-
puts", "Bypass", or "Output level inactive".
For any maintenance work the compressed-air and power supply of the machine must al-
ways be disconnected, and any existing pneumatic cylinders must be vented.
4.6 Safety information for commissioning
To avoid any injuries due to energised parts in the electronics housing, the information in
5.1 and 5.2 must always be observed.
4.7 Safety information for storage and transport
Always observe the information in paragraph 10 to avoid any transport damage and per-
sonal injuries.
4.8 Notes on residual risks
Electrical circuits may still be live even after having been isolated from the mains. Switch
off immediately if a fault occurs.
4.9 Notes on stable standing requirements
To avoid any loss of stable standing, the information for transport, commissioning and op-
eration must always be observed. Always make sure that the fastening screws of the con-
trol unit are tight during operation. When storing or transporting the control unit, place it on
the closed rear panel of the housing.
4.10 Consequences of unauthorised modification
Unauthorised modification or repair will invalidate all manufacturer declarations and guar-
antees.

4. Safety
16
4.11 Improper use
For other applications as enumerated in 4.1 the control unit PRIMUS+ intended for –that
is regarded as inadmissible operation. Improper use also includes operating the equip-
ment with excessive mechanical, static or dynamic loads (e.g. heavy machine parts or
strong vibration). It is furthermore not permitted to inspect any aggressive materials on the
conveyor, such as materials containing lyes, acids, and solvents, or materials that react to
electromagnetic fields, or living persons or animals, and to operate the system in an Ex
protection area.

5. Commissioning
17
5 Commissioning
5.1 Mechanical mounting
Ensure stable and non-vibrating installation! In house mounting and operation. Do not install the
system in an explosion proof zone.
Do not install the detection coil and the electronic unit in the vicinity of interference fields (large
electric motors and frequency converters!) The distance depends on the power consumption of the
motor or of the frequency converter (value for orientation: 5 m).
Mount the control cabinet by using the provided bores. I.e. at a wall or frame (dimensions are shown in
the outline drawings). Pay attention to good stability, as the weight of the control unit is approx. 4 kg.
Never install the electronic unit in other switchgear cabinets, because this may lead to interference
effects. (E.g. from contactor controls)!
Cable lengths may only be modified after consultation with "Sesotec". Use only original cables. Lay
the connecting cable in fixed installation apart from other cables (e.g. fix it with nailing clips or lay it
in a cable duct).
If several metal detector systems are used, the distance of the detection coils must not be less than
2m, if these coils stand side by side. If the coils are arranged opposite to each other, the distance
must not be less than 10 m. These values apply to large systems; for smaller systems the distanc-
es may be reduced to 50 cm. If, for reasons of space, these distances cannot be observed, please
contact Sesotec service!
Do not install the equipment in such a way that operation of the mains cut-off switch is hindered in
any way!
5.2 Connection of the equipment
In order to meet CE conformity all cable outside of the housing has
to be shielded. The shields must be grounded immediately after the
cable gland.
Housing
Shield
Cable

5. Commissioning
18
5.2.1 PRIMUS+ / IO electronics board (control electronics board)
5.2.2 Electrical connections
Pos.
Connection
Type of connection
Function
(1)
"Mains/Option"
Connector for mains
supply
L/N: Electronics power supply
O1/O2: Optional 24V module power supply connector
(2)
"Relay metal"
Voltage free
relay contact
Normal operation: Contacts 71 and 72 closed
On metal detected Contacts 71 and 74 closed
(3)
"Relay fault"
Voltage free
relay contact
Normal operation: Contacts 81 and 84 closed
In case of fault: Contacts 81 and 82 closed
(4)
"Outputs"
Switching outputs
24V
J5
Switching functions
MV = magnetic valve connection
(=24V to GND or = 0V to 24V)
1–9
, FU: Not assigned
2 –10
, LM: Lamp metal
3 –11
, LB: Lamp operation
4 –12
, LF: Lamp fault
5 –13
, Mz: Ext. metal counter
6–14
or , MV1, (after system setup)
7–15
or , MV2, (after system setup)
8–16
or , MV3, (after system setup)
(5)
"Inputs"
Switching inputs 24V
J6
Switching functions
24V, NPN or PNP switching
17 –18 –25
KÜ: Flap monitoring
PNP or NPN (dep. on application)
19 –26 –27
FEX: Fault external
PNP or NPN (dep. on application)
20 –28
DÜ: Compressed-air monitoring
NPN
21 –29
TEX: Test external
NPN
22 –30
REX: Reset external
NPN
23 –31
MAN:Manual separation
NPN
24 –32
MD: Deactivate metal detection
NPN
J5J5
J6

5. Commissioning
19
Pos.
Connection
Type of connection
Function
(6)
"Jumper JP10"
Placement,
connection monitor-
ing MV1 –MV3
active / inactive
JP10
Functions
Jumper plugged, monitoring inactive
Jumper open, monitoring active
1 –2
MV1 connection monitoring
3 –4
MV2 connection monitoring
5 –6
MV3 connection monitoring
Remove jumper when valve is connected
(12)
"+24V external"
+24V, external sup-
ply of magnet valve
connection
Supply MV1 / MV2 / MV3 with external 24V.
Necessary when high-power valves are used, if total valve
power >6W
JP3
Function
Selection, supply of magnet valve connec-
tion
2 –3
MV supply 24V internal
2 –1
MV supply 24V external through connector J13
5.2.3 PRIMUS+ / CU electronics board (evaluation electronics board)
Pos.
Connection
Type of connection
Function
(1)
"Receiver"
Connection for de-
tection coil:
Receiver
JP10
Functions
1
Receiver signal
2
Receiver signal
3
Reference ground for receiver signal
4
- 5V
5
+ 5V
(2)
"Transmitter"
Connection for de-
tection coil:
Transmitter
JP7
Functions
1
Transmitter voltage
2
Reference ground for transmitter voltage
3
Not assigned
4
Transmitter switch-over signal

5. Commissioning
20
5.2.4 Electrical performance
Potential-free relay contacts
250V 3A with alternating voltage
120V 3A with direct voltage
For the potential-free relay circuits fusing must be provided outside the equipment.
Switching outputs (MV1, MV2, MV3)
Switching outputs (LM, LB, LF, Mz)
Maximum current load: 250 mA
Maximum current load: 150 mA
Switching inputs
Connection of make contacts against+24 V,
connection of sensors (PNP, NPN)
total max. permissible current load 24V / 150 mA
5.2.5 Drawing of input / output connections
Switching outputs
J5
910 11 12 13 14 15 16
1 2 3 4 5 6 78
NC
Not
used
LM
Light
metal
LB
Light
oper-
ating
LF
Light
error
1
2
3
MZ
Metal
counter
MV1 MV2 MV3
Switching inputs
J6
Sensor1
25 26 27 28 29 30 31 32
Sensor2
17 18 19 20 21 22 23 24
P
Pressure
switches
External
test External
Reset
Manual
separation
Disable
metal
detection
At J5, J6 only circuits that are isolated from the mains supply by way of double insulation
(SELV circuits) may be connected.
Table of contents
Popular Control Unit manuals by other brands
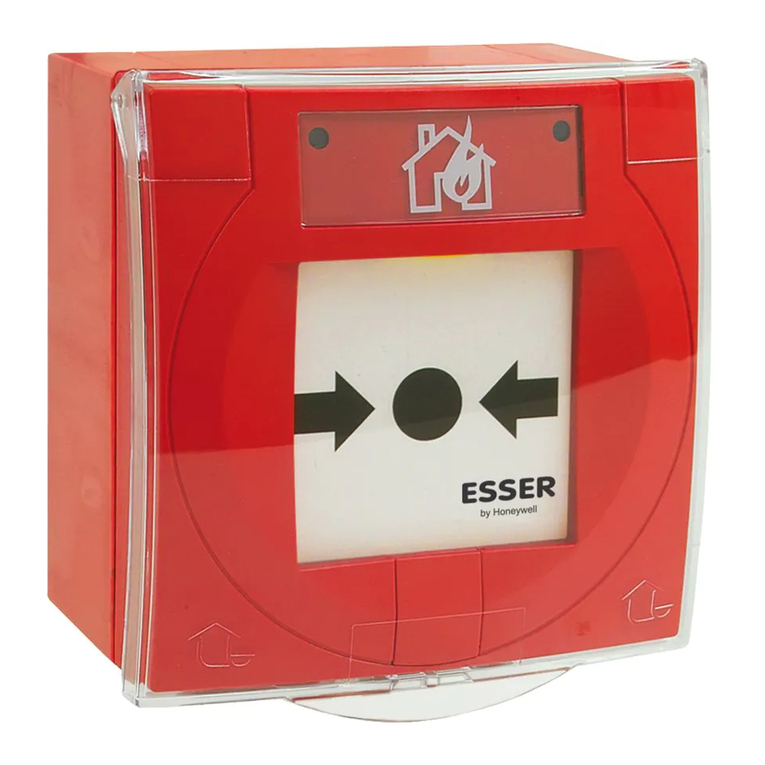
Honeywell
Honeywell ESSER IQ8MCP Installation instruction
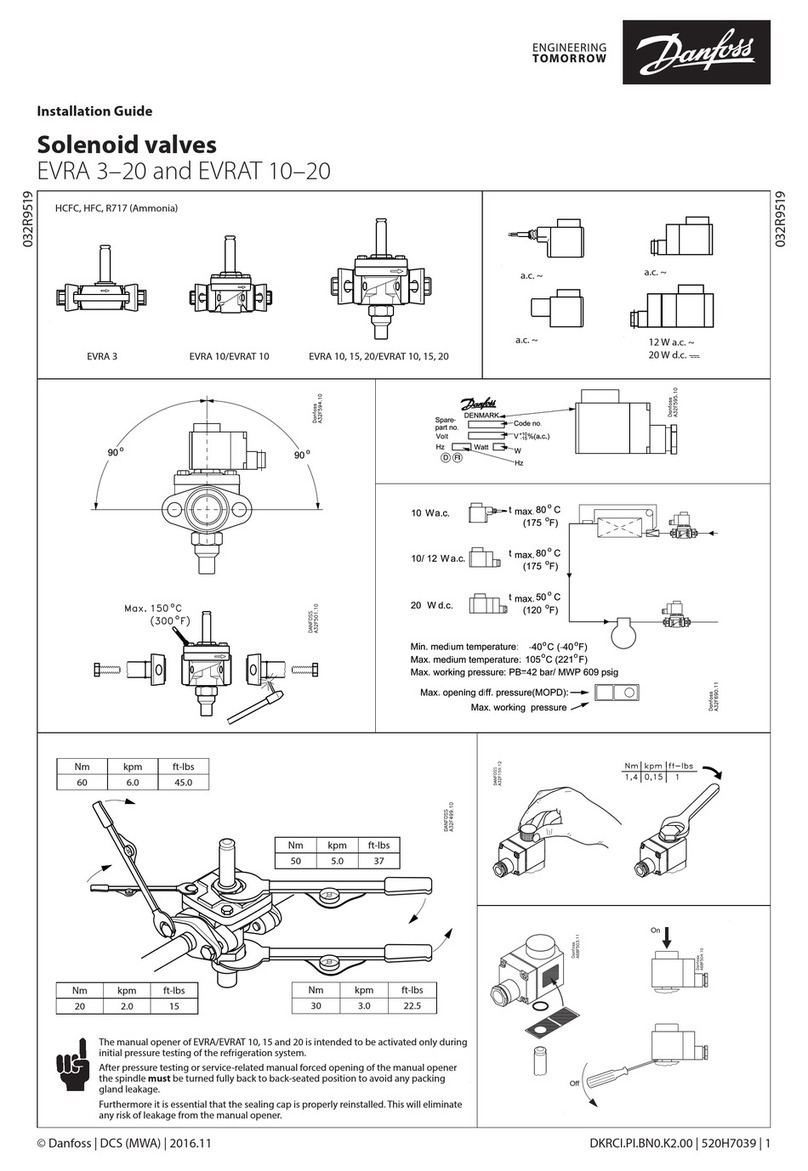
Danfoss
Danfoss EVRA 10 installation guide
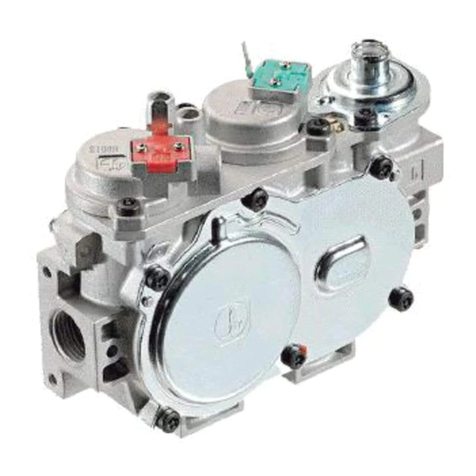
Sit
Sit PROFLAME 880 Use and Installation Instructions
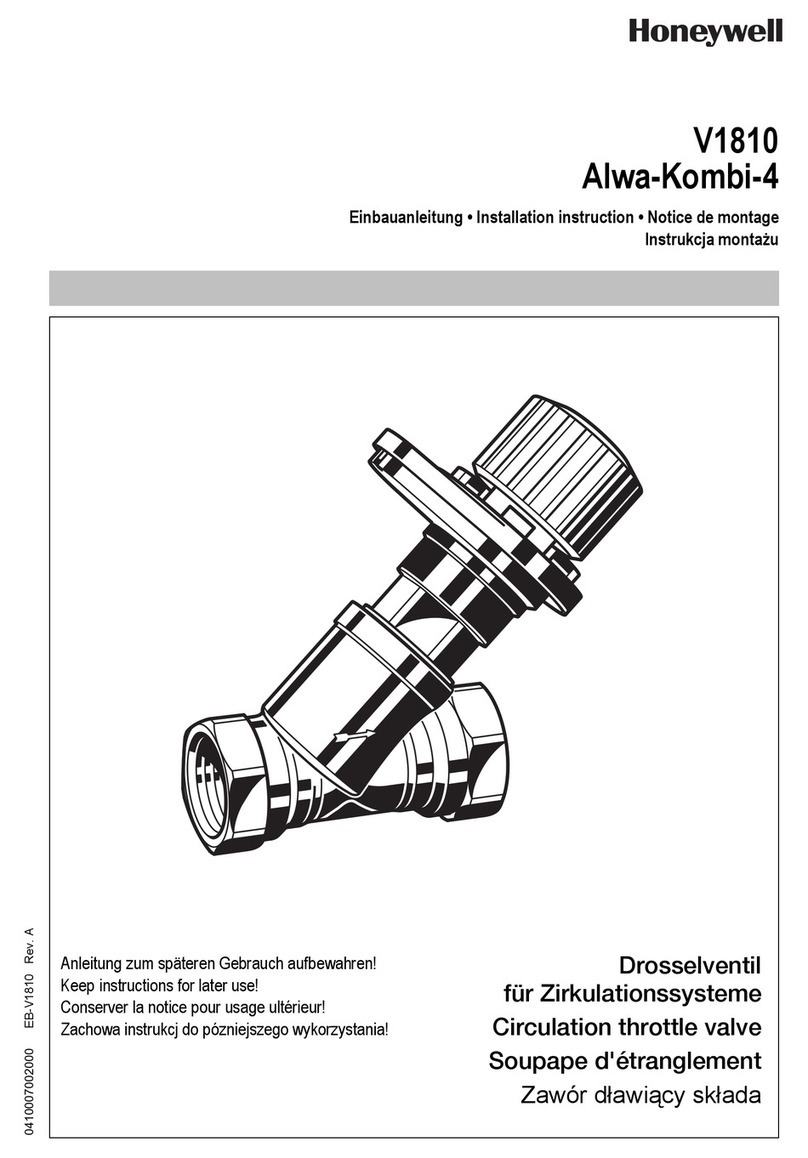
Honeywell
Honeywell V1810 Alwa-Kombi-4 Installation instruction
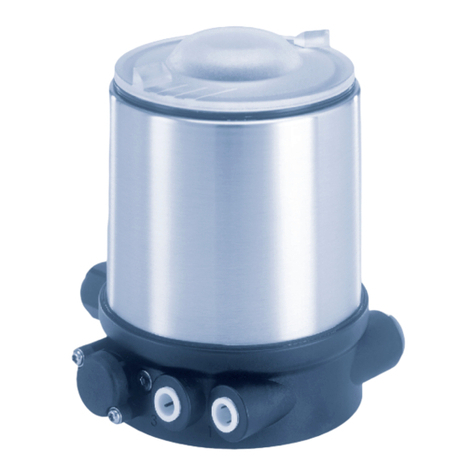
Burkert
Burkert 8691 quick start

Baker Hughes
Baker Hughes Consolidated Generation II 2900 Series instruction manual