Trane CSHD User manual

CSHD and CSHN/CSHL
Compressors
Installation and Service
Installation Instructions
January 2021 COM-SVN01D-EN
SAFETY WARNING
Only qualified personnel should install and service the equipment. The installation, starting up, and servicing of
heating, ventilating, and air-conditioning equipment can be hazardous and requires specific knowledge and training.
Improperly installed, adjusted or altered equipment by an unqualified person could result in death or serious injury.
When working on the equipment, observe all precautions in the literature and on the tags, stickers, and labels that are
attached to the equipment.

© 2021 Trane COM-SVN01D-EN
Introduction
Read this manual thoroughly before operating or servicing
this unit.
Warnings, Cautions, and Notices
Safety advisories appear throughout this manual as
required. Your personal safety and the proper operation of
this machine depend upon the strict observance of these
precautions.
The three types of advisories are defined as follows:
WARNING Indicates a potentially hazardous
situation which, if not avoided, could
result in death or serious injury.
CAUTIONsIndicates a potentially hazardous
situation which, if not avoided, could
result in minor or moderate injury. It
could also be used to alert against
unsafe practices.
NOTICE Indicates a situation that could result in
equipment or property-damage only
accidents.
Important Environmental Concerns
Scientific research has shown that certain man-made
chemicals can affect the earth’s naturally occurring
stratospheric ozone layer when released to the
atmosphere. In particular, several of the identified
chemicals that may affect the ozone layer are refrigerants
that contain Chlorine, Fluorine and Carbon (CFCs) and
those containing Hydrogen, Chlorine, Fluorine and
Carbon (HCFCs). Not all refrigerants containing these
compounds have the same potential impact to the
environment. Trane advocates the responsible handling of
all refrigerants-including industry replacements for CFCs
and HCFCs such as saturated or unsaturated HFCs and
HCFCs.
Important Responsible Refrigerant
Practices
Trane believes that responsible refrigerant practices are
important to the environment, our customers, and the air
conditioning industry. All technicians who handle
refrigerants must be certified according to local rules. For
the USA, the Federal Clean Air Act (Section 608) sets forth
the requirements for handling, reclaiming, recovering and
recycling of certain refrigerants and the equipment that is
used in these service procedures. In addition, some states
or municipalities may have additional requirements that
must also be adhered to for responsible management of
refrigerants. Know the applicable laws and follow them.
WARNING
Proper Field Wiring and Grounding
Required!
Failure to follow code could result in death or serious
injury. All field wiring MUST be performed by qualified
personnel. Improperly installed and grounded field
wiring poses FIRE and ELECTROCUTION hazards. To
avoid these hazards, you MUST follow requirements for
field wiring installation and grounding as described in
NEC and your local/state electrical codes.
WARNING
Personal Protective Equipment (PPE)
Required!
Failure to wear proper PPE for the job being undertaken
could result in death or serious injury. Technicians, in
order to protect themselves from potential electrical,
mechanical, and chemical hazards, MUST follow
precautions in this manual and on the tags, stickers,
and labels, as well as the instructions below:
• Before installing/servicing this unit, technicians
MUST put on all PPE required for the work being
undertaken (Examples; cut resistant gloves/sleeves,
butyl gloves, safety glasses, hard hat/bump cap, fall
protection, electrical PPE and arc flash clothing).
ALWAYS refer to appropriate Safety Data Sheets
(SDS) and OSHA guidelines for proper PPE.
• When working with or around hazardous chemicals,
ALWAYSrefertotheappropriateSDSandOSHA/GHS
(Global Harmonized System of Classification and
Labeling of Chemicals) guidelines for information on
allowable personal exposure levels, proper
respiratory protection and handling instructions.
• If there is a risk of energized electrical contact, arc, or
flash, technicians MUST put on all PPE in accordance
with OSHA, NFPA 70E, or other country-specific
requirements for arc flash protection, PRIOR to
servicing the unit. NEVER PERFORM ANY
SWITCHING, DISCONNECTING, OR VOLTAGE
TESTING WITHOUT PROPER ELECTRICAL PPE AND
ARC FLASH CLOTHING. ENSURE ELECTRICAL
METERS AND EQUIPMENT ARE PROPERLY RATED
FOR INTENDED VOLTAGE.

WARNING
Follow EHS Policies!
Failure to follow instructions below could result in
death or serious injury.
• All Trane personnel must follow the company’s
Environmental, Health and Safety (EHS) policies
when performing work such as hot work, electrical,
fall protection, lockout/tagout, refrigerant handling,
etc. Where local regulations are more stringent than
these policies, those regulations supersede these
policies.
• Non-Trane personnel should always follow local
regulations.
WARNING
R-410A Refrigerant under Higher Pressure
than R-22!
Failure to use proper equipment or components as
described below, could result in equipment failing and
possibly exploding, which could result in death, serious
injury, or equipment damage.
The units described in this manual use R-410A
refrigerant which operates at higher pressures than R-
22. Use ONLY R-410A rated service equipment or
components with these units. For specific handling
concerns with R- 410A, please contact your local Trane
representative.
WARNING
Explosion Hazard and Deadly Gases!
Failure to follow all proper safe refrigerant handling
practices could result in death or serious injury.
Never solder, braze or weld on refrigerant lines or any
unit components that are above atmospheric pressure
or where refrigerant may be present. Always remove
refrigerant by following the guidelines established by
the EPA Federal Clean Air Act or other state or local
codes as appropriate. After refrigerant removal, use dry
nitrogen to bring system back to atmospheric pressure
before opening system for repairs. Mixtures of
refrigerants and air under pressure may become
combustible in the presence of an ignition source
leading to an explosion. Excessive heat from soldering,
brazing or welding with refrigerant vapors present can
form highly toxic gases and extremely corrosive acids.
WARNING
Explosion Hazard!
Failure to follow these instructions could result in death
or serious injury or equipment or property-only
damage.
Use only dry nitrogen with a pressure regulator for
pressurizing unit. Do not use acetylene, oxygen or
compressed air or mixtures containing them for
pressure testing. Do not use mixtures of a hydrogen
containing refrigerant and air above atmospheric
pressure for pressure testing as they may become
flammable and could result in an explosion. Refrigerant,
when used as a trace gas should only be mixed with dry
nitrogen for pressurizing units.
WARNING
Hazardous Service Procedures!
Failure to follow all precautions in this manual and on
the tags, stickers, and labels could result in death or
serious injury.
Technicians, in order to protect themselves from
potential electrical, mechanical, and chemical hazards,
MUST follow precautions in this manual and on the
tags, stickers, and labels, as well as the following
instructions: Unless specified otherwise, disconnect all
electrical power including remote disconnect and
discharge all energy storing devices such as capacitors
before servicing. Follow proper lockout/tagout
procedures to ensure the power can not be
inadvertently energized.When necessary to work with
live electrical components, have a qualified licensed
electrician or other individual who has been trained in
handling live electrical components perform these
tasks.
WARNING
Hazardous Conditions!
Observe and follow the “Warning” and “Notices” labels
on the compressor. Failure to follow these instructions
could result in death or serious injury or damage to the
equipment.
NOTICE
Use Proper Charging and Crankcase
Heater Operation Procedures!
Failure to utilize proper charging and crankcase heater
procedure will result in compressor failure. Refer to unit
IOM or “Charging the System,” p. 19 and “Verification
Before Start-Up,” p. 19 in this manual for the proper
procedures.
Introduction
COM-SVN01D-EN 3

Introduction
4 COM-SVN01D-EN
Copyright
This document and the information in it are the property of
Trane, and may not be used or reproduced in whole or in
part without written permission. Trane reserves the right
to revise this publication at any time, and to make changes
to its content without obligation to notify any person of
such revision or change.
Trademarks
All trademarks referenced in this document are the
trademarks of their respective owners.
Revision History
• Updated Model Number Descriptions chapter.
• Updated Torque values table in General Information
chapter.
• Updated Oil change factory table in General
Information chapter.
• Updated Compressor weight with full oil charge table
in General Information chapter.
• The following figures are updated in General
information chapter:
•Figure 4. Model CSHD/CSHL
•Figure 5. Model CSHD
• The following figures are updated in Removal and
Installation chapter:
•Figure 11. CSHN wiring diagram
•Figure 12. CSHD wiring diagram
• Running edits.

Table of Contents
COM-SVN01D-EN 5
Overview ............................... 6
Literature Referenced .................. 6
Model Number Descriptions .............. 7
General Information ..................... 8
POE Oil ............................... 8
Oil Handling ........................ 8
Oil Level ........................... 8
Operating Envelope .................... 8
Refrigerant Type ..................... 9
Transportation, Handling, and Storage ... 9
Pre-Installation Inspections ........... 10
Repair Recommendations ............. 11
Mechanical Failure .................. 11
Electrical Failure ...................... 12
Two Types of Motor Failures .......... 12
Removal and Installation ................ 13
Removal ............................. 13
Compressor Replacement—Tandem and Trio
Compressor Sets ................... 14
Installation ........................... 15
Electrical Connections ................. 16
Leak Detection ....................... 17
Vacuum Testing and Evacuation ........ 18
Charging the System .................. 19
Verification Before Start-Up ............ 19
Start-Up ............................... 20
Maintenance ........................... 21
Troubleshooting ........................ 22
CSHN Motor Protection Module Diagnosis 23

6 COM-SVN01D-EN
Overview
The purpose of this document is to provide installation and
service information for Trane CSHD and CSHN
compressors.
This document is not meant to be provide a step-by-step
procedure, but is intended to identify procedures or
precautions that may be unique to a Trane compressor and
should be taken into account to properly and safely
remove, install, and troubleshoot the compressor.
Each installation has its unique set of circumstances which
also must be taken into account by the service technician.
Literature Referenced
For additional information, this literature includes
references to “unit Installation, Operation, and
Maintenance (IOM) manuals”. The following table lists
these IOMs by unit type:
Unit Type IOM(a)
(a) Installation, Operation, and Maintenance (IOM) manuals listed here are
current as of Februaryl 2015. Check e-Library for the most recent ver-
sion.
Air-Cooled Scroll Chillers Model CGAM 20–130 Ton CG-SVX17*-EN
IntelliPak™ II Commercial Single-Zone Rooftop Air
Conditioners RT-SVX24*-EN
IntelliPak Single-Zone Rooftop Air Conditioners RT-SVX10*-EN
Voyager™ 12½–25 Ton Gas/Electric RT-SVX26*-EN
Voyager 12½–20 Ton Heat Pump RT-SVX33*-EN
Voyager 27½–50 Ton RT-SVX34*-EN
Split System Heat Pump Condensers, R-410 a 6-20
Tons SSP-SVX14*-EN
Split System Cooling Condensers, R-410a 6-25
Tons SS-SVX10*-EN
Remote Split System Units and Remote Chillers Air
Cooled Condensing Units SS-SVX11*-EN
IntelliPak Commercial Self-Contained Signature
Series 20-110 Tons SCXF-SVX01*-EN

COM-SVN01D-EN 7
Model Number Descriptions
CSHD125K0A0M
Digits 1, 2, 3, 4 — Model Type
CSHD = 6.2–15 Tons
CSHN = 15–30 Tons
CSHL = 30 Tons, LSPM motor
Digits 5, 6, 7 — Nominal Capacity
075 = 075 MBtu/h CSHD
089 = 089 MBtu/h CSHD1
092 = 092 MBtu/h CSHD1
103 = 103 MBtu/h CSHD
105 = 105 MBtu/h CSHD1
110 = 110 MBtu/h CSHD1
120 = 120 MBtu/h CSHD1
125 = 125 MBtu/h CSHD1
136 = 136 MBtu/h CSHD1
142 = 142 MBtu/h CSHD1
155 = 155 MBtu/h CSHD1
161 = 161 MBtu/h CSHD1
175 = 175 MBtu/h CSHD1
183 = 183 MBtu/h CSHD1
176 = 176 MBtu/h CSHN
184 = 184 MBtu/h CSHN1
240 = 240 MBtu/h CSHN
250 = 250 MBtu/h CSHN1
315 = 315 MBtu/h CSHN
374 = 374 MBtu/h CSHN/CSHL
Digit 8 — Voltage
J = 200–230/60/3
K = 460/60/3, 380–415/50/3
D = 575/60/3
X = 380/60/3
Digit 9 — Unloading
0 = No Unloading
Digit 10 — Design Sequence
Factory Assigned
Digit 11 — Motor Protection
Type
0 = Internal Line Break
H = 24 Vac
K = 115/230 Vac
Digit 12 — Basic Compressor Configuration
M = Standard volume ratio,
Suction and discharge tube
T = Standard volume ratio,
Suction and discharge Rotolock
R = Low volume ratio,
Suction and discharge tube
1These models also have low volume ratio optimized options, besides the standard volume ratio options. See digit 12.

8 COM-SVN01D-EN
General Information
Table 1. Torque values
Item Torque
CSHD Rotolock equalizer nut 1-3/4 133 ± 10 N·m; 98 ± 7 ft·lb
CSHN Rotolock equalizer nut 2-1/4 133 ± 5 N·m; 98± 7 ft·lb
CSHD Terminal screws #10-32 X 0.5 in 2.75 ± 0.25 N·m; 25 ± 2 in·lb
CSHN Terminal set screw and nut 3.4 ± 0.25 N·m; 30 ± 2 in·lb
Ground screw (CSHD and CSHN) 1.90 ± 0.25 N·m; 17 ± 2 in·lb
Terminal box cover 2.15 ± 0.25 N·m; 19 ± 2 in·lb
Note: With rotolock fittings, always use two wrenches:
one to back-up on the sleeve and one to tighten the
nut. Proper torquing of the rotolock nut is important
to insure a leak-free joint.
POE Oil
Table 2. Oil charge factory
Model Pints Liters Trane Part Number
CSHD103 5.0 2.4 OIL00078, OIL00080
CSHD075-092 6.3 3.1 OIL00078, OIL00080
CSHD105–161 7.0 3.3 OIL00078, OIL00080
CSHD 175, 183 7.6 3.6 OIL00078, OIL00080
CSHN176–315 14.2 6.7 OIL00078, OIL00080
CSHN374/CSHL374 15.2 7.2 OIL00078, OIL00080
Notes:
1. OIL00078—1 quart container
2. OIL00080—1 gallon container
3. Oil amount and type is also printed on the nameplate.
4. Use only Trane-approved oils and do not mix oils.
Oil Handling
POE oil is very hydroscopic, which means it absorbs
moisture very readily. Therefore, it is important to properly
handle the oil.
POE Oil handling guidelines
• Always use the smallest container size required for the
job requirements.
• Always leave the oil container tightly sealed until time
of use.
•Do not reuse oil that has been opened.
Oil Level
Figure 1. Compressor oil label
The oil should be visible through the oil sightglass both
during operation and when the compressor(s) is off. Oil
level slightly below the sightglass, but still visible is
acceptable.
Single compressor. The oil level should be stable in the
sightglass.
Tandem and trio compressors.
•Operation—The oil level will vary depending on the
operating condition.
•Unloaded condition—The running compressor will
have a higher oil level than the off compressor(s).
•Loaded condition—Oil should be visible through all
of the compressor sight glasses. Some may have a
higher level than others, but this is not abnormal.
•Off—After several minutes, the oil levels should be the
same in each compressor and should be visible in the
sightglass. This is the best method to determine if the
system has sufficient oil.
Units overcharged with oil will operate with degraded
performance and could lead to compressor damage.
Operating Envelope
The compressor must be operated within the published
operating envelope.

Figure 2. Operating envelope
R410A Operating Map - Superheat
50
60
70
80
90
100
110
120
130
140
150
160
170
180
190
-30 -20 -10 0 10 20 30 40 50 60 70
R410A Operating Map - Superheat 20
°
F
Evaporating temperature (°F)
Condensing temperature (°F)
General Information
COM-SVN01D-EN 9
Refrigerant Type
CSHD and CSHN/CSHL compressors are approved for use
with R-410A refrigerant only. Any use of hydrocarbon
refrigerants or air is strictly prohibited!
Transportation, Handling, and
Storage
The compressor must be handled in the vertical position
(maximum 15-degree offset from vertical). Should the
compressor be handled in an upside down position, its
suitability for its use can not be guaranteed.
NOTICE
Improper Handling!
Improper handling of the compressor resulting from
being handled or transported in the upside position,
dropped or tipped over could result in internal damage to
the compressor and it is recommended that the
compressor not be put into service.
Damage to compressor or packaging should be reported
to the shipper immediately.
Use a proper method of lifting the compressor, both lifting
ears must be used with a spreader bar.
WARNING
Heavy Object!
Failure to follow instructions below could result in unit
dropping which could result in death or serious injury,
and equipment or property-only damage. Ensure that all
the lifting equipment used is properly rated for the
weight of the unit being lifted. Each of the cables (chains
or slings), hooks, and shackles used to lift the unit must
be capable of supporting the entire weight of the unit.
Lifting cables (chains or slings) may not be of the same
length. Adjust as necessary for even unit lift.
For approximate compressor weight, see Table 3.
Spreader bar use is recommended to better balance the
compressor.

Figure 3. Lifting compressor with spreader bar
General Information
10 COM-SVN01D-EN
Use lifting hooks with close clasps.
Table 3. Compressor weight with full oil charge
Model Weight (lb)
CSHD 075 - 092 128
CSHD 103 - 125 142
CSHD 136 - 161 150
CSHD 175/183 160
CSHN 176 - 250 236
CSHN315 337
CSHN374/CSHL374 362
The compressor and its packaging must not be exposed to
rain and/or corrosive, flammable atmosphere.
The compressor must not be stored in an environment less
than -31°F (-35°C) or to exceed +160°F (+71°C).
Pre-Installation Inspections
Check the following before using the compressor:
• Compressor for visible shipping damage.
• Compressor is the correct model/part number.
• Compressor is the correct voltage.
• Compressor ship-with items:
– Restrictors for use with tandem and trio
compressors.
– Oil equalizer Teflon®gaskets.
WARNING
R-410A Refrigerant under Higher Pressure
than R-22!
Failure to use proper equipment or components as
described below, could result in equipment failing and
possibly exploding, which could result in death, serious
injury, or equipment damage.
The units described in this manual use R-410A
refrigerant which operates at higher pressures than R-
22. Use ONLY R-410A rated service equipment or
components with these units. For specific handling
concerns with R- 410A, please contact your local Trane
representative.
Figure 4. Model CSHN/CSHL
Oil equalizer rotolock
connection fitting
Oil valve with
dip tube
Figure 5. Model CSHD
Oil equalizer rotolock
connection fitting
1/4 Schrader port

Figure 6. Tandem and Trio
Oil equalizer rotolock
connection fitting
Oil equalizer lines
TANDEM
TRIO
General Information
COM-SVN01D-EN 11
Repair Recommendations
WARNING
Explosion Hazard and Deadly Gases!
Failure to follow all proper safe refrigerant handling
practices could result in death or serious injury.
Never solder, braze or weld on refrigerant lines or any
unit components that are above atmospheric pressure
or where refrigerant may be present. Always remove
refrigerant by following the guidelines established by
the EPA Federal Clean Air Act or other state or local
codes as appropriate. After refrigerant removal, use dry
nitrogen to bring system back to atmospheric pressure
before opening system for repairs. Mixtures of
refrigerants and air under pressure may become
combustible in the presence of an ignition source
leading to an explosion. Excessive heat from soldering,
brazing or welding with refrigerant vapors present can
form highly toxic gases and extremely corrosive acids.
Mechanical Failure
Replace only the failed compressor in a tandem or trio set.
Important: On tandem or trio assemblies, the suction
and discharge lines must NOT be modified,
except for the use of slip joint couplings.
Other modification may cause oil return
issues and lead to compressor failure. Cut
the lines in a convenient place, remove the
compressor, and then unbraze the lines
from the compressor. On reinstallation,
reinstall lines to compressor and
reassemble the cut lines utilizing a slip
coupling. See Figure 7, p. 11 for suggested
area to cut the discharge and suction line.
Figure 7. Suggested areas to cut refrigerant lines
Suggested area to cut the
refrigerant lines so that
they can be reinstalled
Minimize system and compressor open times to avoid
excessive moisture absorption by the POE oil. Maximum
suggested open time is 15 minutes.
Drain and replace oil in all the non-failed compressors.
Note: For CSHD compressors, this requires removing oil
using a suction device through the oil equalizer
rotolock fitting (see Figure 5, p. 10). Use a
dedicated device for removing oil. It is good
practice to flush the suction device with clean oil
prior to use.
The CSHN compressor has an oil drain with a Schrader®
valve that can be used to remove the oil (see Figure 4,
p. 10).
Replace unit liquid line filter-drier. This is a very important
part of controlling moisture in R-410A POE oil systems.

General Information
12 COM-SVN01D-EN
Reuse the compressors mounting isolators or mounting
spacers that are used with the existing compressor
assembly.
Braze the compressor into the system. Compressor
connections are copper-plated steel. Use BAg-28, 40%
silver, with paste flux to make the copper tube connections
to the compressor.
Proceed with the following as described in the following
sections:
•“Leak Detection,” p. 17
•“Vacuum Testing and Evacuation,” p. 18
•“Verification Before Start-Up,” p. 19
Electrical Failure
Replace only the failed compressor in a tandem or trio set.
Drain and replace the oil in all the non-failed compressors.
Reuse the compressors mounting isolators or mounting
spacers that are used with the existing compressor
assembly.
Braze compressor into the system. Compressor
connections are copper-plated steel. Use BAg-28, 40%
silver, with paste flux to make the copper tube connections
to the compressor.
Important: On tandem or trio assemblies, the suction
and discharge lines must not be modified,
except for the use of slip joint couplings.
Other modification may cause oil return
issues and lead to compressor failure. Cut
the lines in a convenient place, remove the
compressor then unbraze the lines from the
compressor. On reinstallation, reinstall
lines to compressor and reassemble the cut
lines with a slip coupling. See Figure 7, p. 11
for suggested area to cut the discharge and
suction line.
Minimize system and compressor open times to avoid
excessive moisture absorption by the POE oil. Maximum
suggested open time is 15 minutes.
Test the acid condition of the oil in the compressors using
an acid test kit. Use Trane Part Numbers KIT06815,
CHM00414, and KIT06754.
Two Types of Motor Failures
Light. If oil test kit is negative and oil is only slightly
discolored, treat in the same manner as a mechanical
failure.
Severe. If oil test kit is positive with strong pungent odor
and dark oil, drain and replace oil in all of the non-failed
compressors.
Reuse the compressor mounting isolators or mounting
spacers that are used with the existing compressor
assembly.
This type of failure requires changing both the suction and
liquid line filter-driers. Use replaceable filter-drier cores to
facilitate changing filter-driers, if required.
Install the suction filters no closer than the distance listed
in the following table. The distance is measured from the
centerline of the suction inlet tee (see Figure 7, p. 11).
Braze compressor into the system. Compressor
connections are copper-plated steel. Use BAg-28, 40%
silver, with paste flux to make the copper tube connections
to the compressor.
Proceed with the following as described in previous
sections:
•“Leak Detection,” p. 17
•“Vacuum Testing and Evacuation,” p. 18
•“Charging the System,” p. 19
•“Verification Before Start-Up,” p. 19
Figure 8. Minimum distance before installation of
suction line filter
X Minimum Distance
Compressor Model “X” Distance
CSHD 10 inches
CSHN tandem 16 inches
CSHN trio 25 inches
1. Use acid removal type filter-drier cores in both the
suction filter and liquid line filter drier.
2. Change when the pressure drop exceeds 4 psig.
CSHN/CSHL models
Test oil after 24 hours of operation. Change filter-drier
again if required. If oil is still acid, drain and replace oil in
all the non-failed compressors.
After system is clean, test kit indicates okay, remove the
suction clean up filter-drier and replace the liquid line drier
with standard filter drier cores.
CSHD models
Since CSHD compressors do not have an oil drain valve
that allows complete oil charge removal, it is
recommended that after 24 hours of operation, the filter-
drier cores be replaced with acid removal filter-drier cores.
Operate the system for another 24 hours before changing
to remove the suction filter-drier and install a standard
filter-drier in the liquid line.

COM-SVN01D-EN 13
Removal and Installation
WARNING
Refrigerant under High Pressure!
Failure to follow instructions below could result in an
explosion which could result in death or serious injury
or equipment damage.
System contains refrigerant under high pressure.
Recover refrigerant to relieve pressure before opening
the system. See unit nameplate for refrigerant type. Do
not use non-approved refrigerants, refrigerant
substitutes, or refrigerant additives.
WARNING
Explosion Hazard and Deadly Gases!
Failure to follow all proper safe refrigerant handling
practices could result in death or serious injury.
Never solder, braze or weld on refrigerant lines or any
unit components that are above atmospheric pressure
or where refrigerant may be present. Always remove
refrigerant by following the guidelines established by
the EPA Federal Clean Air Act or other state or local
codes as appropriate. After refrigerant removal, use dry
nitrogen to bring system back to atmospheric pressure
before opening system for repairs. Mixtures of
refrigerants and air under pressure may become
combustible in the presence of an ignition source
leading to an explosion. Excessive heat from soldering,
brazing or welding with refrigerant vapors present can
form highly toxic gases and extremely corrosive acids.
Only qualified personnel should install or repair
refrigeration systems. If you are not qualified, seek the
services of qualified personnel. The steps listed below are
not meant to be an exact step-by-step procedure, but are
intended to identify procedures or precautions that may
be unique to a Trane compressor and should be taken into
account to properly and safely remove and install the
compressor. Each installation has its unique set of
circumstances which must be considered by the service
technician to perform a safe and successful compressor
replacement.
Removal
WARNING
Pressurized Burning Fluid
Failure to follow these instructions could result in death
or serious injury.
Before opening a system, you must remove refrigerant
from both the high and low sides of the system. If the
pressure is not removed from both sides of the system,
pressure could still exist in the system. If a torch is used
to unbraze the tubing the refrigerant and oil mixture
could ignite.
WARNING
Hazardous Voltage w/Capacitors!
Failure to disconnect power and discharge capacitors
before servicing could result in death or serious injury.
Disconnect all electric power, including remote
disconnects and discharge all motor start/run
capacitors before servicing. Follow proper lockout/
tagout procedures to ensure the power cannot be
inadvertently energized. Verify with a CAT III or IV
voltmeter rated per NFPA 70E that all capacitors have
discharged.
For additional information regarding the safe discharge of
capacitors, see PROD-SVB06*-EN.
•Prior to removing the compressor, open the unit
disconnect and place a lock on the disconnect to
prevent someone else from accidentally applying
power to the unit while it is under repair.
• Completely recover the refrigerant from the refrigerant
circuit being repaired. Do not release refrigerant to the
atmosphere! Use Responsible Refrigerant Practices. If
adding or removing refrigerant, the service technician
must comply with all Federal, State, and local laws.
Before removing the electrical connections on the
compressor use a voltmeter to check for the absence of
power on:
• Compressor power terminals.
• Compressor motor protection module.
• After confirming the absence of power, remove the
electrical connections.
–Mark the electrical wires so they can be placed back
on the same terminal on the replacement
compressor to prevent improper phasing.
– CSHD compressor terminal blocks are marked: T1 is
marked red, T2 is marked blue, and T3 has no mark
(see Figure 12, p. 17).

Removal and Installation
14 COM-SVN01D-EN
• Remove oil prior to compressor removal:
– CSHN/CSHL Compressors
•CSHN and CSHL compressors have an oil valve
(see Figure 4, p. 10) that allows oil to be
completely drained out of the compressor due to
an internal dip tube. After the refrigerant has
been recovered, pressurize the system with
nitrogen to help remove oil from the
compressor.
•If the compressor is in a tandem or trio set, place
acatch pan under the oil equalizer rotolock
connection on the compressor to catch the oil
from the oil equalizer tube or compressor when
the oil equalizer tube is removed.
– CSHD Compressors
•For CSHD compressors complete, oil removal
requires using a suction or pump device through
the oil equalizer rotolock fitting, see Figure 6,
p. 11. Flush the suction device with clean oil prior
to use.
•If the compressor is in a tandem set, place a
catch pan under the oil equalizer rotolock
connection fitting on the compressor to catch the
oil from the compressor when the oil equalizer
tube is removed. Refer to Figure 6, p. 11 for the
location of the oil equalizer rotolock connection
fitting.
Tip: Before removing the existing tubing from the
compressor, apply flux to the joint. This will aid in
the flow of the braze material and help keep the
joint clean for rebrazing. After fluxing, heat the joint
evenly to slightly higher temperature than the
melting temperature of the filler material. At this
point, the two parts of the assembly should be
easily separated.
• Refrigerant Connection Removal
– Single compressor—Cut the refrigerant lines in a
convenient location that allows reassembly with
slip couplings. Then, unbraze the line from the
compressor and reuse it when the replacement is
installed.
•When removing the compressor use both hooks
on the cap of the compressor with a spreader bar
(see Figure 3, p. 10).
•The lifting device must be rated to handle the
weight compressor as listed in Table 3, p. 10.
Compressor Replacement—Tandem and
Trio Compressor Sets
Definitions:
•Tandem—Two compressors on a single refrigerant
circuit.
•Trio—Three compressors on a single refrigerant
circuit.
There are special considerations that are unique to
replacing compressors in a tandem or trio set:
1. Only replace the failed compressor.
2. On tandem or trio assemblies, the suction and
discharge lines must not be modified, except for the
use of slip-joint couplings. Other modifications may
cause oil return issues and lead to compressor failure.
Cut the lines in a convenient place, remove the
compressor, and then unbraze the lines from the
compressor. On re-installation, reinstall lines to
compressor and reassemble the cut lines using a slip
coupling. Refer to Figure 7, p. 11 for suggested area to
cut the discharge and suction line.
Tip: Before removing the existing tubing from the
compressor, apply flux to the joint. This will aid in
the flow of the braze material and help keep the
joint clean for re-brazing. After fluxing, heat the
joint evenly to slightly higher temperature than the
melting temperature of the filler material. At this
point, the two parts of the assembly should be
easily separated.
3. Change oil in all compressors in the tandem or trio
compressors whenever there is a failure.
a. CSHN/CSHL—Use the oil valve on the compressor.
b. CSHD—Remove the oil equalizer fitting and use a
suction or pump device to remove the oil from the
compressor through the oil equalizer tube opening.
A suction type device should be used to remove oil
from the compressor.
Important: Some compressor tandem configurations
require a restrictor be placed in the suction
inlet to balance the oil levels. Each service
replacement compressor ships with all the
restrictors that can be used with that
compressor. The restrictors are packaged in
a bag with a label with the part number and
diameter required (see Figure 9). The part
number is X17311028010 and the internal
diameter in millimeters is Ø31. The
restrictor is also marked on the face with
both the extension number, last three digits
of the part number, and diameter. For the
previous example, the restrictor would be
marked 010-31. Without the proper
restrictor installed the compressor oil level
balance will not be correct. Refer to the
instruction sheet included with the service
replacement compressor for the correct size
and location of the restrictor.
NOTICE
Incorrect Restrictor Size and Location!
Failure to install the correct size restrictor or in the
correct position will lead to improper oil levels in the
compressor. This could result in a compressor failure
due to low oil level.

Removal and Installation
COM-SVN01D-EN 15
4. It will be necessary to use an oil catch pan under the oil
equalizer connection to catch the oil when the
connection is loosened and removed.
Figure 9.
Installation
WARNING
Hazardous Voltage w/Capacitors!
Failure to disconnect power and discharge capacitors
before servicing could result in death or serious injury.
Disconnect all electric power, including remote
disconnects and discharge all motor start/run
capacitors before servicing. Follow proper lockout/
tagout procedures to ensure the power cannot be
inadvertently energized. Verify with a CAT III or IV
voltmeter rated per NFPA 70E that all capacitors have
discharged.
For additional information regarding the safe discharge of
capacitors, see PROD-SVB06*-EN.
WARNING
Explosion Hazard and Deadly Gases!
Failure to follow all proper safe refrigerant handling
practices could result in death or serious injury.
Never solder, braze or weld on refrigerant lines or any
unit components that are above atmospheric pressure
or where refrigerant may be present. Always remove
refrigerant by following the guidelines established by
the EPA Federal Clean Air Act or other state or local
codes as appropriate. After refrigerant removal, use dry
nitrogen to bring system back to atmospheric pressure
before opening system for repairs. Mixtures of
refrigerants and air under pressure may become
combustible in the presence of an ignition source
leading to an explosion. Excessive heat from soldering,
brazing or welding with refrigerant vapors present can
form highly toxic gases and extremely corrosive acids.
• Only qualified personnel should install or repair
refrigeration systems. If you are not qualified, seek the
services of qualified personnel.
• Pressure tests must be performed by qualified
personnel.
• The replacement compressor contains a nitrogen
charge of 5 psig.
• Remove the suction plug before the discharge plug to
avoid oil spray while opening the compressor.
• Keep exposure to the atmosphere at a minimum due to
POE oil. Remove the rubber plugs only when ready to
install the compressor. Plug other compressor on
tandem or trio compressors.
•Before removing the oil equalizer connection cap,
place a can pan under the rotolock fitting as the
compressor oil level is above the rotolock connection.
Oil must be added to the compressors after
installation.
a. Removal Instructions
Tip: Before removing the existing tubing from the
compressor, apply flux to the joint. This will aid in
the flow of the braze material and help keep the
joint clean for rebrazing. After fluxing, heat the joint
evenly to slightly higher temperature than the
melting temperature of the filler material. At this
point, the two parts of the assembly should be
easily separated.
b. Installation
c. Preparation:
i. For proper capillary action to occur, the tube and
the fitting must be free of oil, grease, burrs, and
oxide contamination. To remove the oil and
grease a commercial solvent or denatured
alcohol can be used. The surface may be
properly cleaned by brushing with a stainless
shell brush or by a stiff rubbing with emery cloth.
Wipe the joint clean to remove small foreign
particles such as emery dust, by wiping the
surface with a clean cloth. Once the surfaces are
clean, be careful not to touch them as oil from
the skin will contaminate the surfaces.
ii. Pre-fit the existing tubing into the compressor to
check that it has full insertion into the
compressor fitting. For compressors that have a
suction restrictor located in the suction inlet,
ensure that the tube is inserted completely such
that the suction restrictor fits tightly against the
end of the compressor suction connection.
iii. Apply flux with a brush to the outside of the
compressor connecting tubing, taking care to
evenly apply the flux around the entire diameter.
Care must also be taken not to get the flux inside
of the tubing as this may result in contamination
of the refrigerant system.
iv. Reinsert the tube into the compressor
connection. If the tubing does not stay fully
inserted, it must be restrained to prevent it from
backing out of the compressor connection
during the brazing process.
d. Brazing Technique
i. If possible, use a double-side torch while
brazing.

Removal and Installation
16 COM-SVN01D-EN
ii. Use 40% silver brazing alloy with flux.
iii. Start heating the tube first. Evenly heat the tube,
location 1 (see Figure 10), until it reaches a dull
red color. When using flux, this color is also a
good indicator of when the proper brazing
temperature has been reached. Continue
heating the tube until the flux passes the
“bubbling” temperature range and becomes
quiet, completely fluid, and transparent—it
should have the appearance of clear water.
iv. Direct the flame from the tube to the fitting,
evenly heating it until the flux that may be
remaining in the fitting is also completely fluid.
v. Sweep the torch between the fitting and the
tube, locations 1 and 2 (see Figure 10), with most
of the heat being applied to the heavier and
slower-heating fitting until the tube and fitting
reach and maintain a uniform heat in both parts.
Figure 10. Brazing locations 1 and 2
vi. Pull the flame slightly back and feed the brazing
material in between the fitting and the tube. If the
joint has been properly heated, the braze
material should flow around and into the joint.
Important: The heated base metal should melt the
filler; the heat from the torch flame should
not be what melts the filler.
vii.Once the braze material has flowed around and
into the joint, briefly move the torch around the
fitting to ensure complete capillary action into
the joint.
viii.Check the joint to visually ensure that the braze
material is completely around the joint.
e. Post-Braze
NOTICE
NOTICE
Clean Flux From Joint!
Quench the joint with water or a wet rag while the joint
is still hot—but below 900°F—to shock off the flux. If
not cleaned off, flux could hide leaks. Flux is also
corrosive and could lead to long-term problems and
equipment damage if not properly removed.
• Tandem (two compressors) and trio combinations
(three compressors) with uneven compressor
combinations requires the use of restrictor(s) to
balance the oil level in the compressor. Refer to
COM-SVN02*-EN, Installation: Restrictor (or the most
recent version) for proper size and location of the
restrictor.
• When brazing refrigerant connections, protect
compressor body and terminal box from torch heat
damage.
• When brazing, always use a nitrogen purge to prevent
the formation of copper oxide contamination that can
damage the compressor.
• CSHN/CSHL compressors have an internal check valve.
When pressurizing the system, it is important to never
allow the low-side pressure to exceed the high-side
pressure by more than 5 bar (72 psig). Such a pressure
differential could result in pressure compressor
damage. Also, slowly raise the pressure over a
two-minute time period to allow sufficient time for the
internal pressures in the compressor to equalize.
Electrical Connections
WARNING
Hazardous Service Procedures!
Failure to follow all precautions in this manual and on
the tags, stickers, and labels could result in death or
serious injury.
Technicians, in order to protect themselves from
potential electrical, mechanical, and chemical hazards,
MUST follow precautions in this manual and on the
tags, stickers, and labels, as well as the following
instructions: Unless specified otherwise, disconnect all
electrical power including remote disconnect and
discharge all energy storing devices such as capacitors
before servicing. Follow proper lockout/tagout
procedures to ensure the power can not be
inadvertently energized.When necessary to work with
live electrical components, have a qualified licensed
electrician or other individual who has been trained in
handling live electrical components perform these
tasks.
2

Removal and Installation
COM-SVN01D-EN 17
CSHN/CSHL
•Before removing wires, mark them so that they can be
put back on the same terminal when the new
compressor is installed.
• Insure that the compressor model terminals are
installed on the correct terminals (see Figure 11, p. 17).
• If the compressor is not wired properly, it will shut off
within five seconds.
•Proper torque for the terminal set screws and nuts is 30
in-lb.
•Before starting the compressor, check the electrical
phasing with a phase sequence meter similar to an
Ideal-Sperry Model 61-520.
Figure 11. CSHN/CSHL wiring diagram
CSHD
The terminal blocks have red and blue marks for phase
identification. Compressor terminal T1 is red, compressor
terminal T2 is blue, and compressor terminal T3 is
unmarked. Depending on the unit type, several methods
of marking the wires may be used, colored wires, wire
color marks on the wire or wire numbers to indicated the
proper location of the wire on the compressor terminal
block.
If the wires are not marked, ensure that you mark them
prior to removing them so that they can be reinstalled in
the same position.
Figure 12. CSHD wiring diagram
• Ensure that the compressor model terminals are
installed on the correct terminals (see Figure 12).
• Proper torque for the terminal screws is 25 in·lb.
• Before starting the compressor, check the electrical
phasing with a phase sequence meter similar to an
Ideal-Sperry Model 61-520.
NOTICE
Improper Power Phasing!
Check phasing before starting compressor. Operating
the compressor with improper phasing could cause
compressor failure.
Leak Detection
WARNING
Explosion Hazard!
Failure to follow these instructions could result in death
or serious injury or equipment or property-only
damage.
Use only dry nitrogen with a pressure regulator for
pressurizing unit. Do not use acetylene, oxygen or
compressed air or mixtures containing them for
pressure testing. Do not use mixtures of a hydrogen
containing refrigerant and air above atmospheric
pressure for pressure testing as they may become
flammable and could result in an explosion. Refrigerant,
when used as a trace gas should only be mixed with dry
nitrogen for pressurizing units.
PHASING TO BE CONNECTED AS SHOWN TO
PREVENT REVERSE ROTATION
MODULE INPUT
VOLTAGE
POWER
SUPPLY
CONTROL
CIRCUIT
L1 L3 L2
BLACK
BLUE
RED
L1
L3
L2
A
B
C
L1 L3L2
M1
NO
M2
COM
CONTROL
VOLTAGE
TH-
S1
TH+
S2 N
L
Blue mark
indicating T2
(Phase B)
Red mark
indicating T1
(Phase A)
Unmarked
T3
(Phase C)

WARNING
Explosion Hazard!
Failure to properly regulate pressure could result in a
violent explosion, which could result in death, serious
injury, or equipment or property-only-damage.
When using dry nitrogen cylinders for pressurizing units
for leak testing, always provide a pressure regulator on
the cylinder to prevent excessively high unit pressures.
Never pressurize unit above the maximum
recommended unit test pressure as specified in
applicable unit literature.
Removal and Installation
18 COM-SVN01D-EN
Pressure Testing
• Use industry-standard and EPA-accepted techniques
for testing.
• Pressure tests must be performed by qualified
personnel.
• Use tools especially designed for leak testing.
• Do not exceed the high-side and low-side pressures
listed on the unit nameplate.
• If no test pressure value is listed on the nameplate of
the unit, a pressure of no more than 150 psig is
acceptable.
• The CSHN compressor has an internal check valve.
When pressurizing the system, it is important to never
allow the low side pressure to exceed the high side
pressure by more than 5 bar (72 psig). Greater
pressure differential could result in compressor
damage. Also slowly raise the pressure over a
2-minute time period to allow sufficient time for
internal pressures in the compressor to equalize.
NOTICE
Overpressure Damage!
Do not pressurize the low side of the compressor by
more than 5 bar (72 psig) higher than the high side of
the compressor within less than two minutes. Failure to
follow these instructions could result in compressor
damage.
• Pressure decay testing can be used to check for gross
leaks but will not be able to detect the location of a leak.
• After pressurizing the system use an R-410A leak
detection device to detect and locate leaks.
Vacuum Testing and Evacuation
• Use the procedure as described in the unit Installation,
Operation, and Maintenance manual (see “Literature
Referenced,” p. 6).
• If no other information is available, use the following
information.
NOTICE
Compressor Motor Damage!
Never use the compressor as a vacuum pump. Never
meg-ohm test or apply power to the compressor while
it is in a vacuum. Failure to follow these instructions
could cause compressor motor damage.
WARNING
Hazardous Voltage w/Capacitors!
Disconnect all electric power, including remote
disconnects and discharge all motor start/run
capacitors before servicing. Follow proper lockout/tag
out procedures to ensure the power cannot be
inadvertently energized. Verify with an appropriate
voltmeter that all capacitors have discharged. Failure to
disconnect power and discharge capacitors before
servicing could result in death or serious injury.
• Ensure that there is no voltage being applied to the
compressor terminals.
•Evacuate the unit to 500 microns.
• Hold vacuum for 30 minutes.
• Rapid pressure rise indicates a leak; locate and repair
the leak.
•Slow pressure rise indicates one of two possibilities:
– A small leak, indicated by a continuous rise in
pressure.
– Moisture in the system, indicated by a slow rise in
pressure and leveling-out at a pressure equivalent
to the moisture level. If this occurs, break the
vacuum with dry nitrogen and repeat evacuation
process to 500 micron.
• Once system is leak-tight, connect compressor repeat
the vacuum procedure, break vacuum with dry
nitrogen and evacuate to 500 microns. The vacuum
should be able to be maintained for four hours. Isolate
the vacuum pump so that the vacuum gauge only
reads the system pressure.
• Vacuum must be measured in the refrigeration system
and not at the vacuum pump.

Removal and Installation
COM-SVN01D-EN 19
Charging the System
WARNING
Hazardous Pressures!
Failure to follow instructions below could result in a
violent explosion, which could result in death or serious
injury.
If a heat source is required to raise the tank pressure
during removal of refrigerant from cylinders, use only
warm water or heat blankets to raise the tank
temperature. Do not exceed a temperature of 150°F. Do
not under any circumstances apply direct flame to any
portion of the cylinder.
Use R-410A refrigerant only! Follow the instructions in the
unit Installation, Operation, and Maintenance manual (see
“Literature Referenced,” p. 6) for proper charging
methods.
If there are no instructions available, use these guidelines:
• Evacuate the unit as described in “Vacuum Testing and
Evacuation,” p. 18.
• Ensure that the oil level is at least 1/2-sight glass in the
compressor
• Do not use the compressor to pull refrigerant into the
system.
• Charge liquid refrigerant into the high-side of the
unit—either into the condenser or liquid receiver, if so
equipped.
• Charge as much of the unit refrigerant charge as
possible before starting the compressor.
• Do not charge liquid refrigerant into the low side of the
compressor without the compressor running. Small
amounts of liquid may be metered through refrigerant
gauges into the suction line while the compressor is
operating.
• If the unit is equipped with suction and discharge
service valves, close them during the charging
procedure.
•Water chiller units—Always operate the chilled water
pumps while charging the unit to prevent freezing the
evaporator.
Verification Before Start-Up
Follow the instructions in the unit Installation, Operation,
and Maintenance manual (see “Literature Referenced,”
p. 6). If there are no instructions available, use these
guidelines:
•Before starting the unit, verify that all service valves are
open.
•Energize the crankcase heater a minimum of 8 hours
before starting the compressor
NOTICE
Improper Crankcase Heater Operation!
Exception to the 8-hour minimum crankcase heater
operation time.
Apply power to the crankcase heater for a minimum of
8 hours prior to startup of the compressor! Failure to
follow this instruction could result in a compressor
failure.
If the compressor is a replacement for a failed compressor
and has been charged in accordance with either the
procedures in the unit IOM or “Charging the System,” p. 19
in this manual, the compressor could be immediately
started after charging the system. The reason for this is
that the refrigerant has not had sufficient time to migrate
to the compressor and cause potential damage upon
startup. The system should set for no more 8 hours or
overnight with a refrigerant charge without crankcase
heater operation. If the time exceeds 8 hours or the unit
sits overnight, the crankcase heater must be operational
for a minimum of 8 hours prior to starting the compressor.
If liquid refrigerant was charged into the suction or low
side during the charging procedure, damage could still
occur.

20 COM-SVN01D-EN
Start-Up
Follow the instructions in the unit Installation, Operation,
and Maintenance manual (see “Literature Referenced,”
p. 6). If there are no instructions available, use these
guidelines:
NOTICE
Equipment Damage!
Failure to follow guidelines below could result in
equipment damage.
• Never start the compressor without refrigerant in the
system.
• Never bypass the low pressure switch to start the unit.
• Monitor oil level for 60 minutes to ensure that oil
returns from the system.
• Check system pressures and temperatures to ensure
they are in line with unit design pressures. Refer to the
unit Installation, Operation, and Maintenance manual
(see “Literature Referenced,” p. 6) for this information.
• To top off the unit, charge liquid refrigerant may added
by slowly throttling it into the suction line. This must be
done only when the compressor is operating.
• Do not overcharge the unit.
• Recommended system full load superheats—unless
specified differently in the unit Installation, Operation,
andMaintenancemanual(see“LiteratureReferenced,”
p. 6)—is 16°F–20°F.
• Measure the oil sump superheat. Oil sump superheat
should be greater than 20°F. Oil sump superheat is
calculated as follows:
Oil Sump Superheat = Oil Sump Temperature –
Saturated Suction Temperature
• Measure the oil sump temperature by placing a
thermocouple on the bottom of the compressor,
preferably in the center, and insulate it. Calculate sump
superheat. If less than 20°F, recheck the expansion
valve superheat and increase it. Low sump superheat
is indicated by foaming compressor oil.
• After fully charging the unit, recheck all pressure,
temperatures, and electrical readings.
• Ensure that the compressor protection module and
power supply wires are installed on the correct
terminals (see Figure 11, p. 17 and Figure 12, p. 17).
• CSHD: Proper torque for the terminal set screws is 25
in-lb.
• CSHN/CSHL: Proper torque for the terminal set screws
is 30 in-lb.
This manual suits for next models
2
Table of contents
Other Trane Air Compressor manuals
Popular Air Compressor manuals by other brands
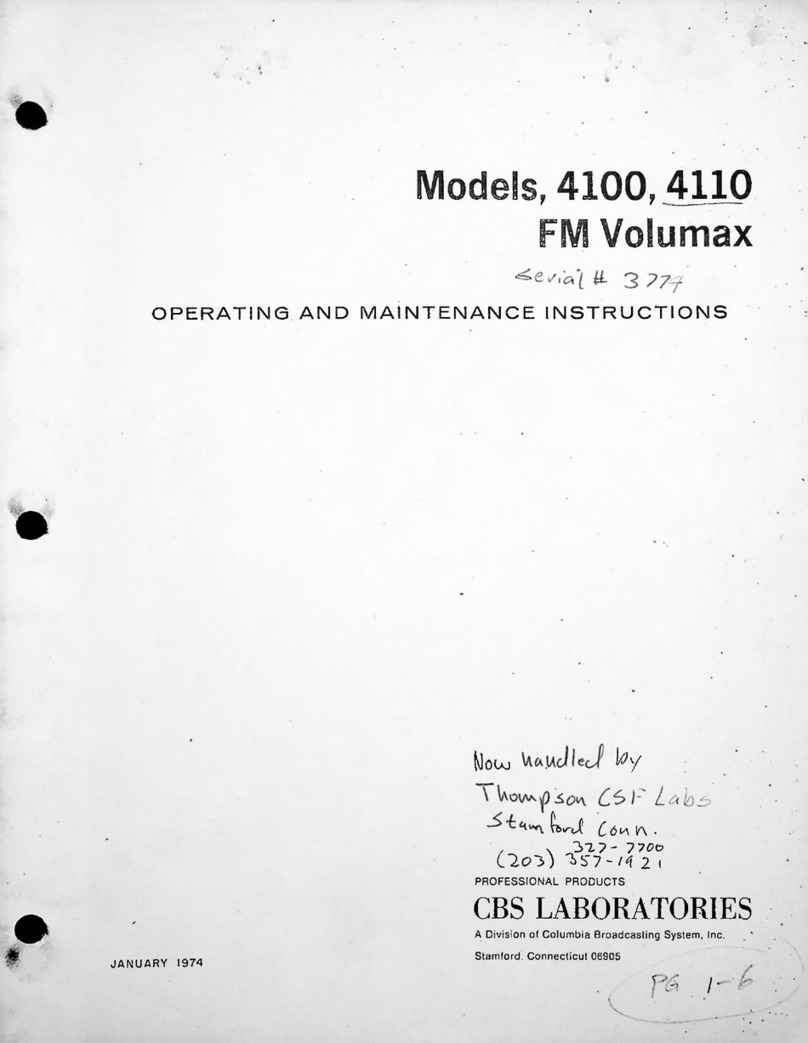
CBS laboratories
CBS laboratories 4100 Operating and maintenance instructions

Hamron
Hamron 604-193 User instructions
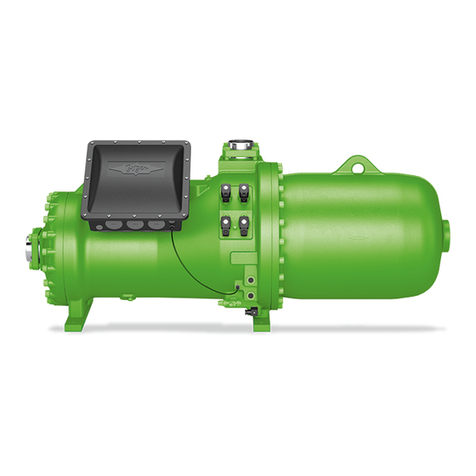
Bitzer
Bitzer CSH Series manual
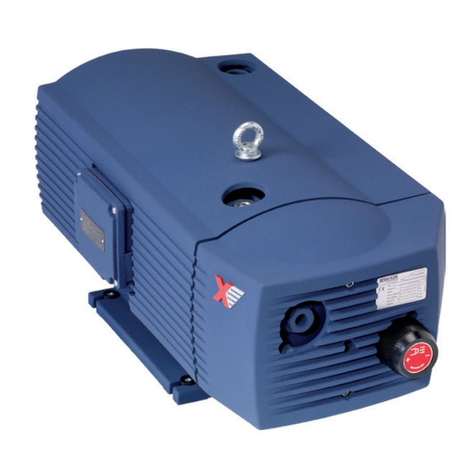
Becker
Becker DX 4.25K operating instructions
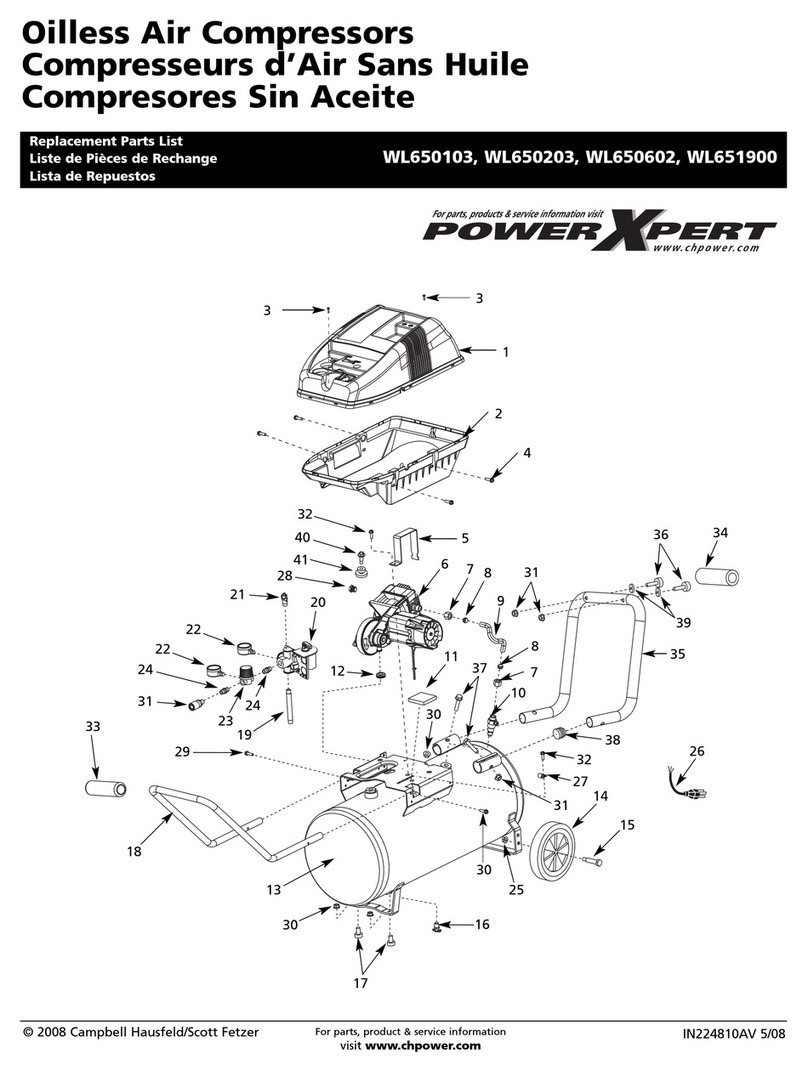
Campbell Hausfeld
Campbell Hausfeld WL650103 Replacement parts list
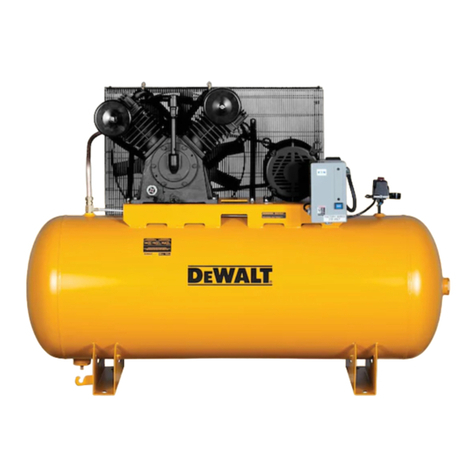
DeWalt
DeWalt DXCMH9919910-CA instruction manual
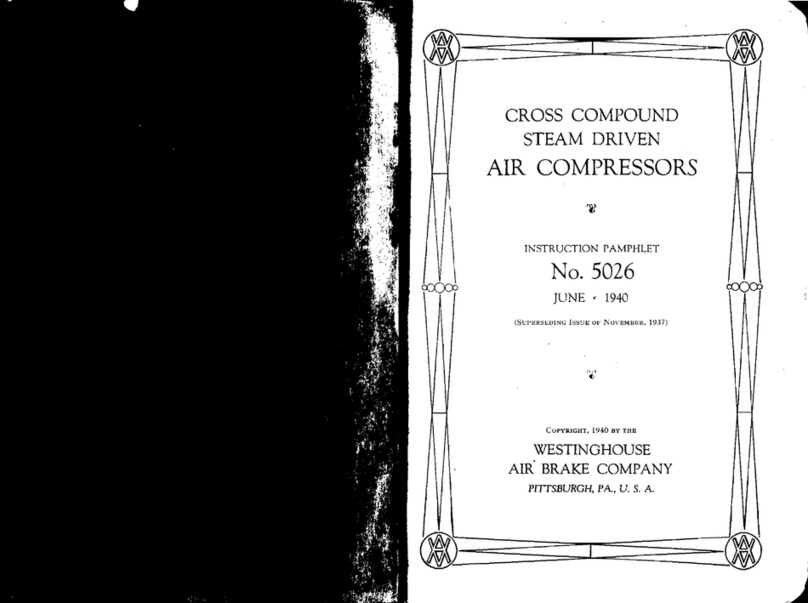
Westinghouse
Westinghouse 5026 Instruction Pamphlet
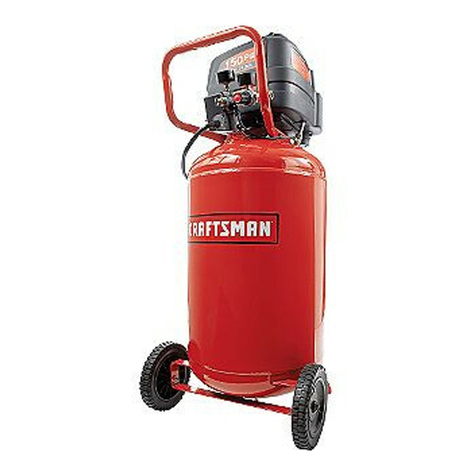
Craftsman
Craftsman 919.168700 owner's manual

MSW
MSW MSW-HCSC-02 user manual
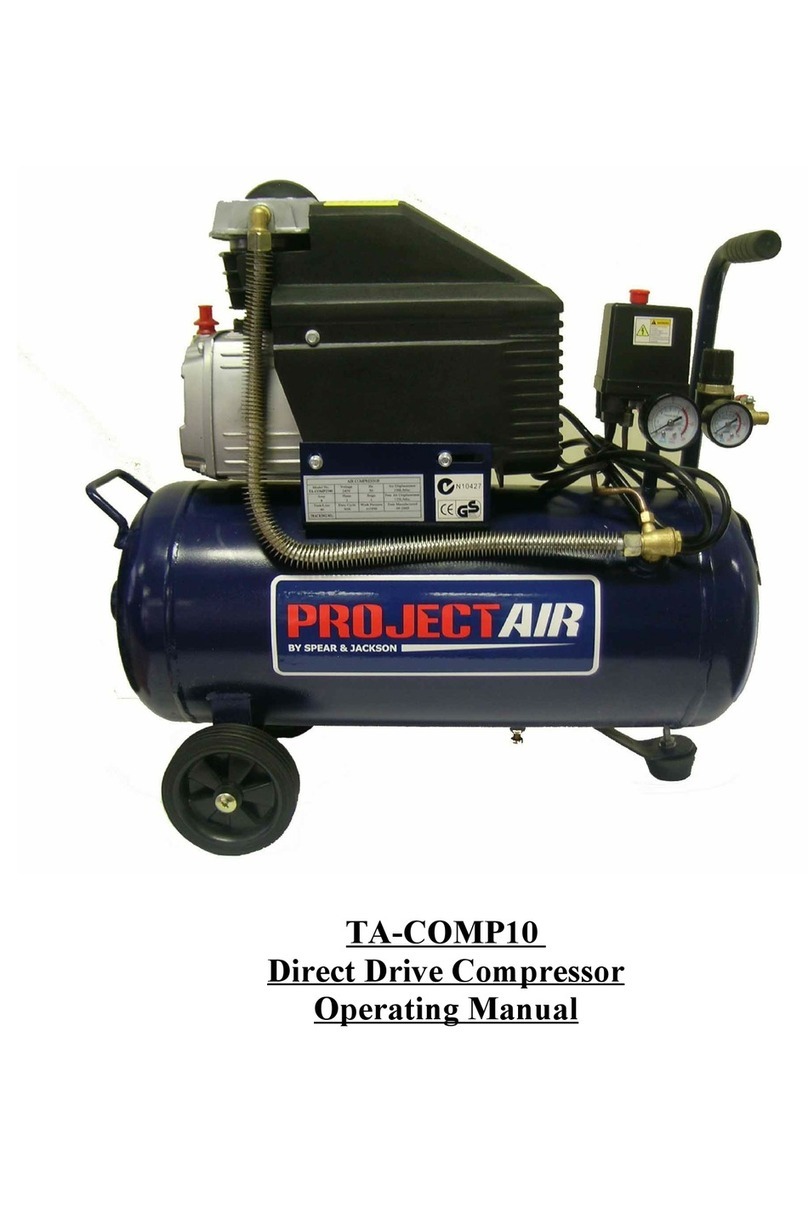
Spear & Jackson
Spear & Jackson ProjectAir TA-COMP10 operating manual
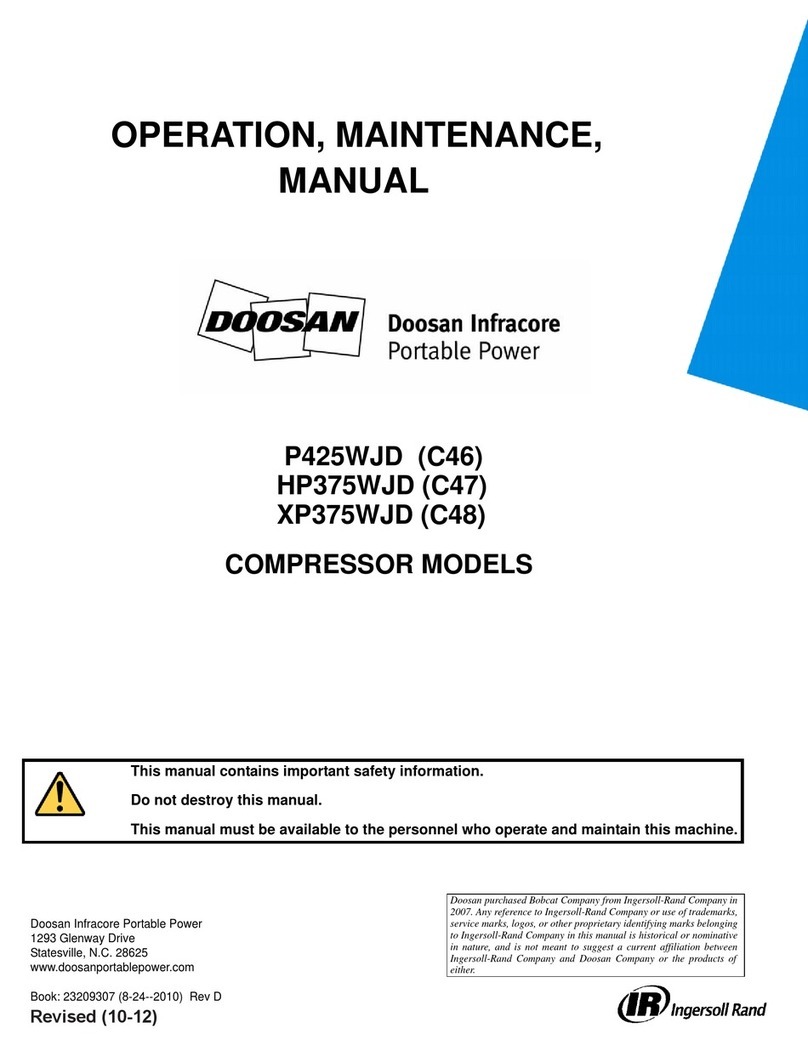
Doosan
Doosan P425WJD Operation & maintenance manual

Ingersoll-Rand
Ingersoll-Rand XF 20 Operator's instruction manual