TRAXX SC250X User manual

Unit 4/1 Rocklea Drive
Port Melbourne Vic 3207
1300 109 108
www.traxxcp.com.au
SC250X FLOOR GRINDER
OPERATIONS MANUAL

SC250X FLOOR GRINDER | OPERATIONS MANUAL 2
Traxx Constructions Products Operations Manual –SC250X Floor Grinder 2
The contents of this Operations Manual are the copyright of the publisher and may not be reproduced (even extract)
unless permission is granted. Traxx Construction Products has composed this manual with accuracy. However, mistakes
may occur or articles may be changed. Traxx Construction Products is not responsible for mistakes or deviations of
figures, graphics or any other information found in this instruction manual.
1. CONTENTS …………….…….………………..….………………………………………………………………….……………………..2
2. INTRODUCTION & DESCRIPTION ……………….………………………………………………………………………………...3
3. TECHNICAL DATA ……………..…..……………………………………………………………………………….………………….…3
4. OPERATION …………..………...………..…………………………………………………………………………….…………..….….4
5. SAFETY PRECAUTIONS …………………………………..…………………………………………………….……………………….4
6. FAULT DIAGNOSIS ………………..…………………………………………………………………….……………………..…………5
7. MAINTENANCE ……………...……………………………………………….……………………………………….…………………..5
8. PARTS DIAGRAM …………………………………………………………………………………………………………………………..6
9. PARTS LIST …………………………………………………………………………………………………………………………………….7
Dec 2017

SC250X FLOOR GRINDER | OPERATIONS MANUAL 3
Traxx Constructions Products Operations Manual –SC250X Floor Grinder 3
1. INTRODUCTION & DESCRIPTION
This manual is intended to provide operation and service information necessary for the Nsafe and efficient use of the
Floor Grinder.
Operating or servicing the unit other than in accordance with the instructions given may subject the machine to
conditions beyond its capability, which may result in machine failure or personal injury.
IMPORTANT
1. Read the entire operating manual carefully before attempting to use the floor grinder. Special attention
should be paid to the section entitled ‘Safety Precautions’.
The Floor Grinder is a sturdy, reliable and easy to use machine.
The Floor Grinder is fitted with 2.2kW single phase motor. This motor offers a direct drive to the grinding plate with the
incorporation of a flexible coupling between the motor and the plate.
The shroud system is unique in design, automatically adjusting to suit segment height and floor angle. This shroud
system, when used in conjunction with an appropriate industrial vacuum unit, eliminates dust loss during grinding. The
shroud has 2 removable sections to enable the operator to grind close up to the wall etc. Please note that dust loss is
possible when this section is removed.
The floor grinder comes complete with a water connection for wet grinding should this be required. This incorporates a
ball valve allowing the operator to regulate the water supply to obtain the best grinding results.
The floor grinder has a foldable handle which enables it to be easily transported in the trunk of most small vehicles. The
rear wheels can also be extended outward should the operator want more stability from the grinder. This requires the
use of a 10mm wrench. The operator can also raise or lower the height of the handle to maximize their comfort when
using the grinder.
And the new designed lifter system makes operator handy to use.
2. TECHNICAL DATA
Motor HP 3hp
Motor KW Rating 2.2kW
Motor RPM 1410rpm
Unit Weight 48kg
Plate Type Standard 250mm plate or Cub Shoe
Plate Bolt Types M12 x 25 Countersunk socket head
Main Construction Powder Coated Steel
Ensure all re-tipped and new grinding plates are properly balanced.
Dec 2017
1. INTRODUCTION AND DESCRIPTION
2. TECHNICAL DATA

SC250X FLOOR GRINDER | OPERATIONS MANUAL 4
Traxx Constructions Products Operations Manual –SC250X Floor Grinder 4
3. OPERATION
The floor grinder is designed to be used either wet or dry. If the floor is being ground dry, ensure a suitable industrial
vacuum is connected and that operator is wearing suitable breathing respiratory equipment. Contact your local work
place health authority to ensure that their requirements regarding respiratory equipment are being met.
Starting the Grinder
1. Check the grinding plate being used is suitable for the material being ground AND THAT THEY ARE CORRECTLY
BALANCED.
2. Check that the grinding plates being used are in good order and properly attached, with all countersunk bolts firmly in
place. Check this occasionally during use, as they can work loose during operation.
3. Check that the grinding plate is adjusted so that it sits level on the ground.
4. Check that all nuts and bolts on the folding handle latch are tight and firm.
5. Raise the grinding plates from the floor.
6. Start the motor by pressing the black switch on the starter box.
7. Lower the grinding plate and commence grinding.
Stopping the Grinder
1. Press the red stop button on the starter box.
Note:
1. By turning and pushing the handles, you can fix vertical grinding position (photo 1).
2. You can adjust the axle’s width for your need (photo 2).
4. SAFETY PRECAUTIONS
The Floor Grinder has been designed to minimize noise and vibration levels and to provide maximum operator safety.
However, incorrect use of the grinder may cause serious injury and therefore the following precautions must be taken:
1. Do not use the grinder for longer than prescribed in your local environmental working regulations, as the noise load
from extensive daily use may result in hearing defects.
2. Always use protective earplugs or earmuffs, goggles, gloves and correct footwear.
3. Do not modify the grinder in any manner, or use a machine that has been modified by anyone other than the
manufacturer or authorised dealer.
4. Do not add weight to the machine to make the grinder work harder. Instead reduce the number of segments on the
grinding plate to increase performance.
5. Be sure that re-tipped and new grinding plates are properly balanced.
6. Do not run the grinder with grinding head raised any higher than necessary, i.e tipped back on handle.
7. Always be sure that folding handle latch is secure and has not vibrated loose after use.
8. When grinding, the machine is exposed to high vibration. Occasionally check machine for bolts/nuts which may have
vibrated loose.
9. Do not allow water or cotton to enter the interior of the motor.
Dec 2017
3. OPERATION
4. SAFETY PRECAUTIONS

SC250X FLOOR GRINDER | OPERATIONS MANUAL 5
Traxx Constructions Products Operations Manual –SC250X Floor Grinder 5
5. FAULT DIAGNOSIS
Symptom
Possible Cause
Action
Grinder runs for 5-
15 minutes, then
stops
The current screw is not adjustable
Adjust the current screw to the
suitable area
Extension cable
too long and/or not
made from heavy enough cable
Get electrician to check extension lead
compatibility
Grinder runs but does not perform
adequately
Motor defective Repair or replace
Grinder vibrates during use
Grinding plates not correctly placed
Replace or re-balance grinding plates
Grinding noise coming from grinding
head when up on jockey wheel
Excessively worn motor bearings Have motor serviced
Symptom Possible Cause Ac
6. MAINTENANCE
Daily cleaning: The motor in use should always be kept clean. No water drops, cotton etc should be allowed to get into
the interior of the motors.
Check on load current: While the motor is in operation, constant care should be taken to keep the load current below
the rated value.
Operational sounds: During operation of the motor there must be no rubbing sounds, shrieks or other random noises.
Stop the motor immediately and restart after inspection and corrections have been made.
Check folding handle latch periodically. This is adjustable.
To adjust, loosen adjusting handle and adjust handle height until a satisfactory tension
has been achieved.
The wheel bearings use sealed bearings and require no regular greasing.
Dec 2017
6. MAINTENANCE
5. FAULT DIAGNOSIS

SC250X FLOOR GRINDER | OPERATIONS MANUAL 6
Traxx Constructions Products Operations Manual –SC250X Floor Grinder 6
7. PARTS DIAGRAM
Traxx Constructions Products Operations Manual –SC250X Floor Grinder 6
7. PARTS DIAGRAM
Dec 2017
7. PARTS DIAGRAM

SC250X FLOOR GRINDER | OPERATIONS MANUAL 7
Traxx Constructions Products Operations Manual –SC250X Floor Grinder 7
8. PARTS LIST
Item No. Part No. Description Qty
1 100663 Millstones 1
2 100279 hexagon socket countersunk head cap head screw 2
3 100664 Dowel disc 1
4 100272 flex coupling 1
5 100253 Spring lock washers 4
6 100275 hexagon nut 2
7 100274 Hexagon head bolts 1
8 100266 Big plain washers 3
9 100276 driving sleeve 1
10 100277 Hexagon head bolts 2
11 100210 hexagon nut M12 2
12
100207
shroud plastic wear strip set
1
13
100206
Hexagon socket button head screws
9
14
100208
Detachable shroud
1
15 100665 hexagon socket countersunk head cap head screw,M8x16 5
16 100270 Enclosure 1
17
100211
location Case
1
18 100216 electrical motor 1
19 100269 shroud plastic wear strip set 1
20 100109 washer 8-2/2 4
21 100086 spring washer 8-6/2 4
22 100268 Hexagon head bolts 4
23 100066 cable tie-in 2
24 100267 pipe joint 1
25 100222 flexible conduit L=480 1
26 100263 big clip 2
27 100222 flexible conduit L=245 1
100264 small clip 2
28 100249 crossover coupling 1
29 100249 crossover coupling 1
30 100666 Frame body part 1
31 100245 Inner hexagon spanner 1
32 100307 flat washer 12 2
33 100667 Hexagon jam nuts 2
34 100668 Big plain washers 2
35 100669 power cord 1
36 100670 Cross recessed pan head screw M4X16 3
37 100223 breaker,GV2-ME16C 1
100224 breaker crust,GV2-MC02 1
100225 UVT assemble 1
38 100671 Upper arm 1
39 100217 Grip 2
40 100672 Plain washers 3
41 100673 hex. Lock nut M4 3
42 100674 lock twist spring 2
43
100675
Positioning clamping claw buckle
1
100676
Adjustale handle M10x25
1
44 100252 Hexagon socket button head screws head screws 2
45 100251 Wheel 2
46
100250
adjustale handle M12*25
1
47
100246
quick joint
1
48 100247 o-ring 1
49 100678 Eccentric shaft 1
50 100679 lift lever 1
51 100654 spring washer 2
52 100262 hexagon bolt 2
53 100273 Hexagon head bolts 2
54 100303 flat washer 8 2
55 100680 Hexagon socket button head screws 2
56 100681 hex flat round head screws 2
57 100271 Key 2
Handle holder
Front Handle 1
100651 Level bubble
1
1
58
59
60
100042
100041
Dec 2017
8. PARTS LIST

Unit 4/1 Rocklea Drive
Port Melbourne Vic 3207
1300 109 108
www.traxxcp.com.au
Table of contents
Popular Floor Machine manuals by other brands
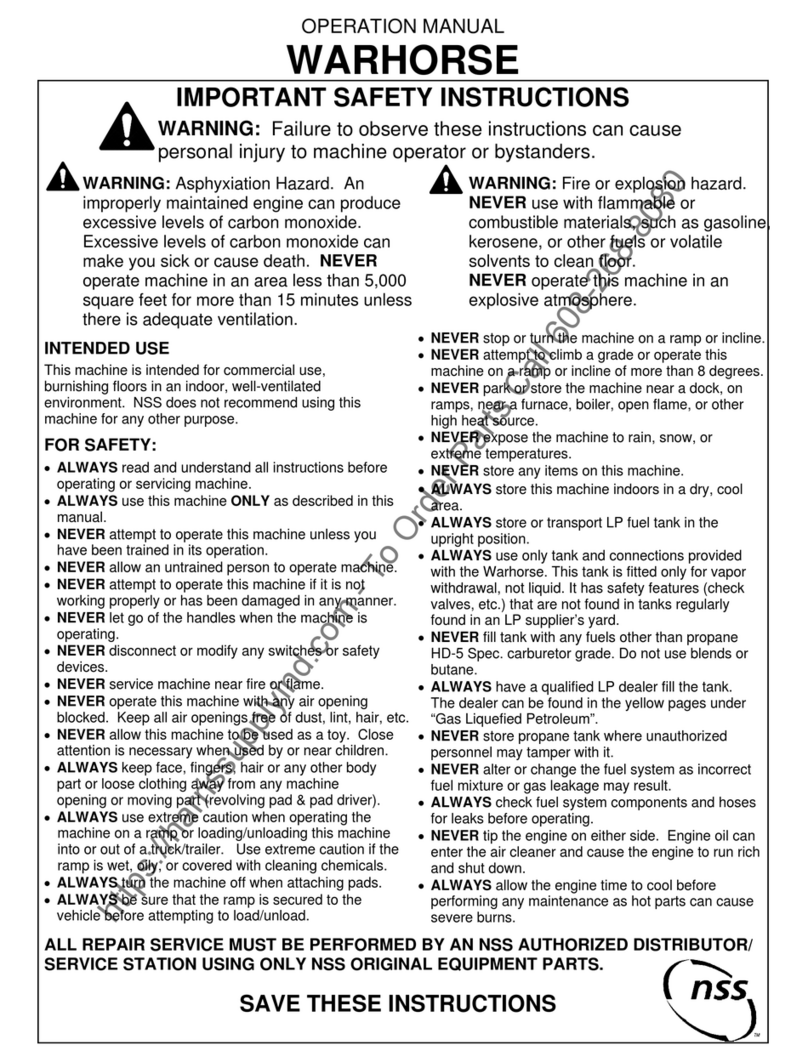
NSS
NSS WARHORSE Operation manual
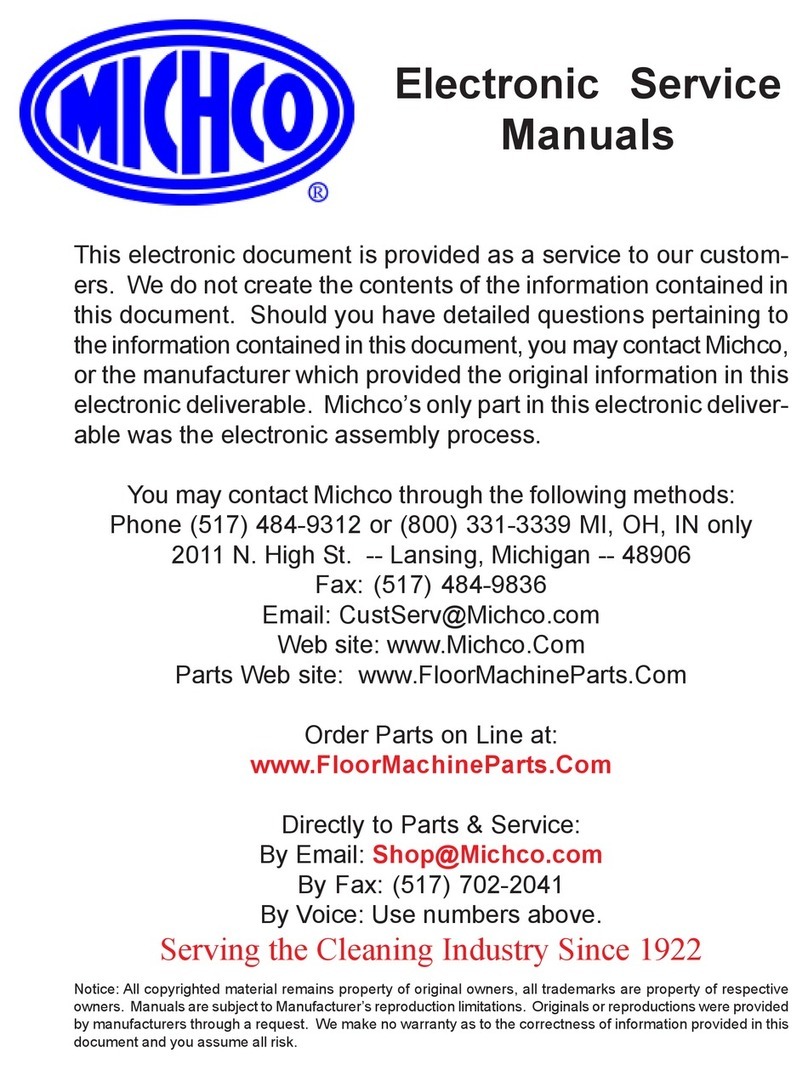
Nilfisk-Advance
Nilfisk-Advance Kent SelectLine 17TS Operator's manual

Tornado
Tornado BATTERY GLAZER 17 user manual

Bona
Bona HD Belt Owner's operation manual

Royal Appliance
Royal Appliance Dirt Devil operating manual
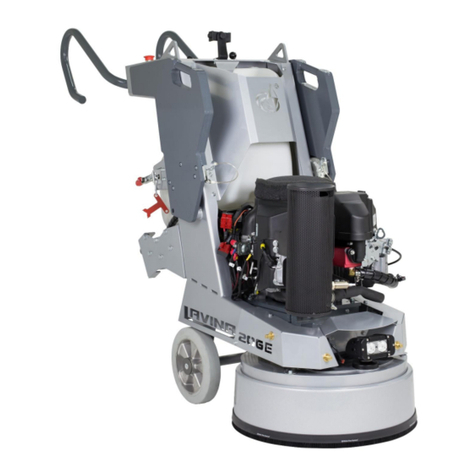
Superabrasive
Superabrasive LAVINA ELITE L20GE user manual

Bona
Bona FlexiSand AMO310000 Manual and safety instructions
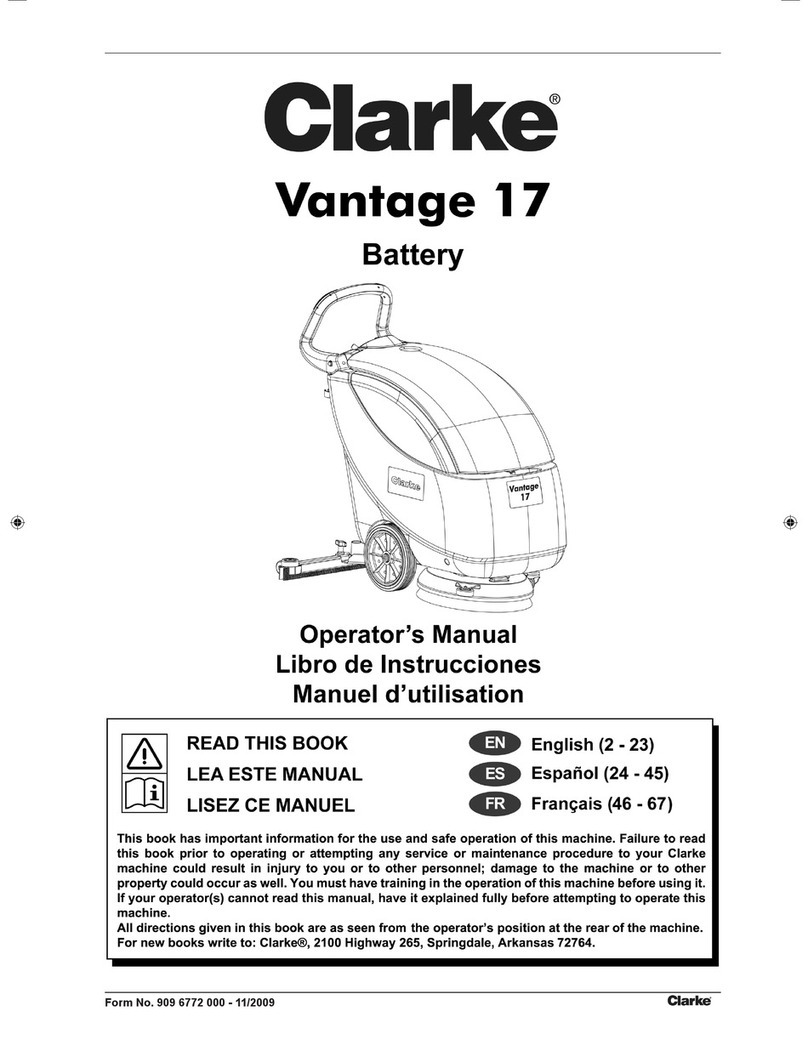
Clarke
Clarke Vantage 17 Battery Operator's manual
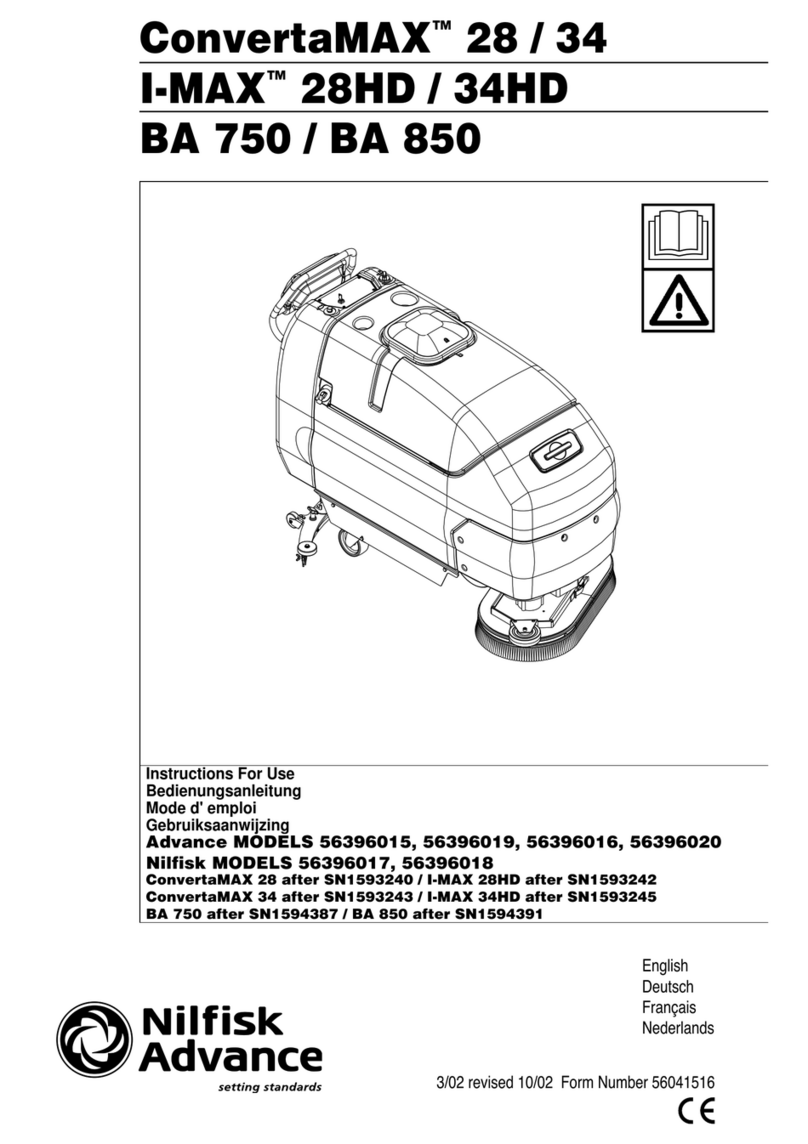
Nilfisk-Advance
Nilfisk-Advance ConvertaMAX 28 Instructions for use

COMAC
COMAC CS50 B-BT Use and maintenance manual
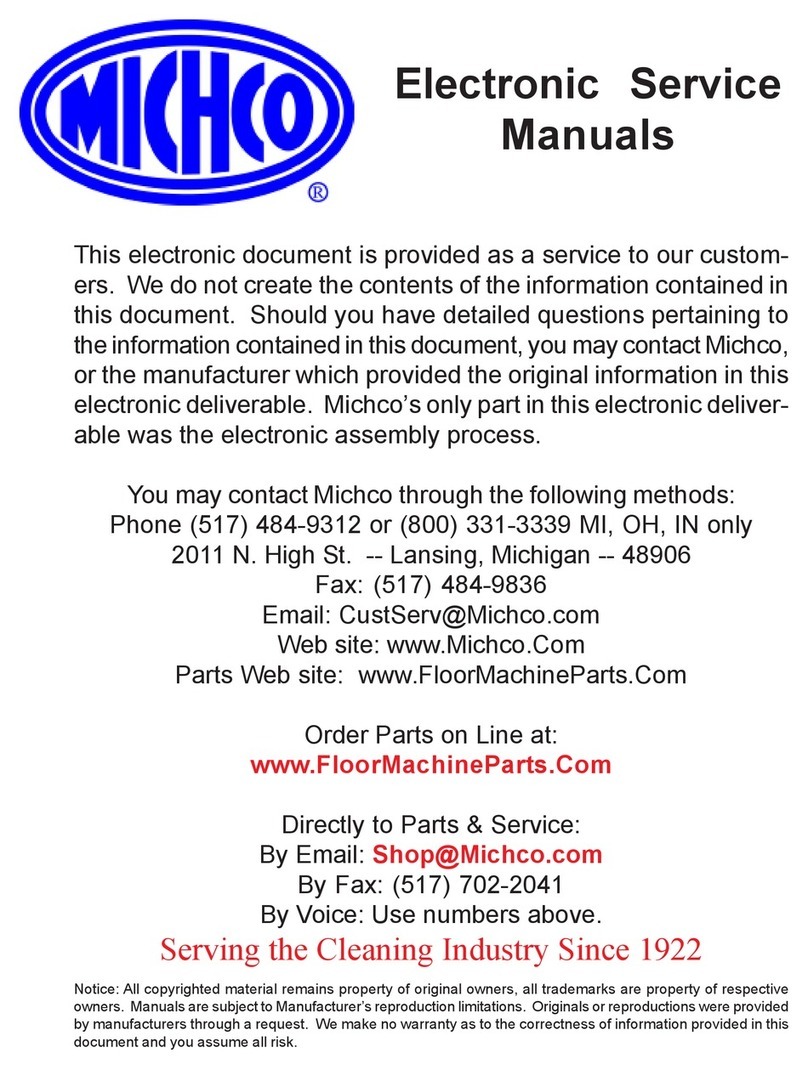
Kent Euroclean
Kent Euroclean SelectGloss 21PH Operator's manual and parts list
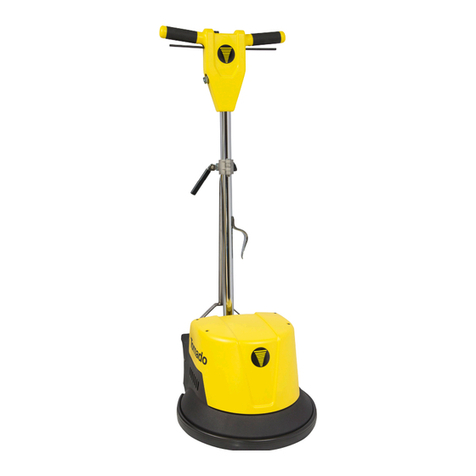
Tornado
Tornado 97561 Operation & maintenance manual