Tri-Tronics DFS21 User manual

1. Establish one of the following conditions:
Beam Make/Proximity - Reflect light off object.
Beam Break - Remove object from light beam path.
OBJECT
Beam Make
Beam Break
DETECTION PATH
OBJECT
REFLECTOR
RECEIVER
LIGHT SOURCE
RECEIVER
LIGHT SOURCE
DETECTION PATH
OBJECT
RECEIVER
LIGHT SOURCE
Proximity Mode
Retroreflective Mode
Opposed Mode
DFS21 - Instructions
Features
The Digital Fiber Optic Sensor is designed to provide reliable detection using fiber optic light guides. Sensor is adjusted by
a single push of a button; there is no guess work on the part of the operator. The sensor default settings* (Channel 1, Light State) will work
for most applications.
Follow the three step procedure below:
WIDE VARIETY OF FIBERS
Visit www.ttco.com for full listing.
AUTOSET (l)
1. Push to perform AUTOSET.
2. Instantly optimizes when in Health Monitor Mode
3-WAY ROCKER SWITCH (qp )
1. Manually adjusts the threshold.+/-
2. Alters programming parameters.+/-
Hold to scroll for numeric values.
3. Press down on center to switch channels.
MODE (n)
Tap to access parameters.
FIBER RELEASE CLAMP
Locks fibers in place.
DUAL CHANNEL OUTPUT LEDS
1. Channel 1 or 2 each illuminates solid when
output is ON.
2. Flashes when output is overloaded.
ADVANCED DIAGNOSTIC OLED DISPLAY
See next page for complete listing.
CONNECTION
5-Pin M8 connector or built-in cable.
• Intuitive numerical/percentage diagnostic
OLED display
• Attractive 10mm wide housing
• Low power & wide operating voltage
• Advanced remote programming
• Six AUTOSET modes including window
• Crosstalk rejection between two sensors
without a wire
• Programmable output/input configurations
• High-speed, High-resolution, and Long-range
modes
• Combinable dual timers, and counters
• CE approved
www.ttco.com • 800-237-0946 1
How To Specify
1.Select Sensor: DFS21
Dual Channel Digital
Fiber Optic Sensor
2.Select Light Source:
R = Red
I = Infrared
3.Select Connection:
Blank = 6ft cable (1.8m)
C = 5-pin M8 connector DFS21
Digital Fiber Optic Sensor
Light Source
Connection
Example: DFS21 R C
2.Tap AUTOSET (l) button:
3. Verify setup on advanced diagnostic OLED display. If needed, the
threshold can be altered by tapping up or down on the threshold
adjust rocker.
Signal Level Threshold
* Note: Consult all default settings on page 6.
Pressing the AUTOSET button
sets the sensors threshold to
the desired level.
Advanced Diagnostic OLED Display
Channel 1 &
Channel 2
• Two Individual Thresholds
• Two Individual Outputs
Channel 1 &
Health Monitor
• Health Monitoring System
and Display
• Auto Signal Tracking
Additional Features:
OR
Quick Start
Current
Channel
DFS Dual Channel Sensor

2 www.ttco.com • 800-237-0946
Dynamic
Press the AUTOSET button to start the
Dynamic AUTOSET. Now move the
object through the beam at least once
and press the AUTOSET button again
to complete the Dynamic AUTOSET.
The threshold is set between the
highest and lowest received light levels
caused by the object being passed
through. The threshold can be altered by tapping up or down on the
threshold adjust rocker (see Figure 5).
Sensing Distance
after Autoset
ON
Background
OFF
Object in Motion
Threshold
Using AUTOSET
The DFS threshold is set automatically by
pressing the AUTOSET button. There are six
different ways the sensor determines the
threshold. The user first must determine which
type of setup mode is appropriate for the
application. The simplest and most common mode
we recommend is Light State (LS) setup. It is used
in both beam make and beam break sensing.
When using this mode, the sensor will provide the
best sensitivity to fine changes in light level or contrast. This is
useful for small part detection and precise leading-edge triggering.
Please consult our website at
https://www.ttco.com/sensors/fundamentals or contact one of our
worldwide distributors for application help. We look forward to
providing any assistance you may need.
Note: OLED display will provide intuitive visual feedback during
autosetting. Paying close attention to the display is important.
Midpoint
Place object to be detected in position
at which you want the threshold to be
set and press the AUTOSET button.
The threshold can be altered by
tapping up or down on the threshold
adjust rocker (see Figure 3).
Object Position
@Autoset
Sensing
Distance
ON
Background
OFF
Threshold
Window
Window mode is a unique type of
AUTOSET mode. Window mode
creates two thresholds and can be
used in a similar manor as a dual
channel fiber optic sensor. Place the
object in the position at which you
want to be reliably detect it and press
the AUTOSET button. The DFS will
place two thresholds 10%(default) higher and 10%(default) lower
than the returned light level. Now when the object is passed in view
or through the fiber optic the object will be detected in the same
position +/- 10%. The threshold offset (both thresholds) can be
altered by tapping up or down on the threshold adjust rocker (see
Figure 6).
10% Window Span
OFF
ON
Background
OFF
10%
Object Position
@Autoset
Figure 6
Figure 5
Figure 3
Two-Point
Place object to be detected in the light-
state condition and press the
AUTOSET button. Then remove or
place the object in the dark-state
condition and press the AUTOSET
button again. The threshold will be set
between the two light-beam intensities.
The threshold can be altered by
tapping up or down on the threshold adjust rocker (see Figure 4).
1/2
Sensing
Distance
2nd Autoset
Point
1st Autoset
Point
ON
Background
OFF
1/2
Threshold
Figure 4
Dark State
Place object to be detected in the
worst-case dark-state condition and
press the AUTOSET button. The
threshold will be set 10%(default)
above the received light-beam
intensity. The threshold can be altered
by tapping up or down on the
threshold adjust rocker (see Figure 2).
10%
Sensing
Distance Object Position
@Autoset
ON
Background
OFF
Threshold
Figure 2
Light State (Default)
Place object to be detected in the
worst-case light-state condition and
press the AUTOSET button. The
threshold will be set 10%(default)
below the received light-beam
intensity. The threshold can be altered
by tapping up or down on the
threshold adjust rocker (see Figure 1).
10%
Sensing
Distance
Object Position
@Autoset
ON
Background
OFF
Threshold
Figure 1
Tap MODE (n) to show status screen.
Status Screen shows a quick overview of sensor’s settings.
n
AUTOSET
Mode
Resonse
Time
Lock
Active
LED
Power
AUTOSET
Percentage
Anti-Crosstalk
Channel
(Status Screen)
Note: Programming will time out after 60 seconds if no action is taken.
Tap and hold MODE (n) to exit status screen.
Hysteresis
Detect
Mode
Current
Channel
System-wide SettingsUnique Channel Settings
Timer
Light-State Set (LS): Sets threshold below received light
beam intensity.
Dark-State Set (DS): Sets threshold above received light
beam intensity.
Midpoint Set (MP): Sets threshold at received light beam
intensity.
Two-point Set (2P): Sets threshold between received light
beam intensity two point.
Dynamic Set (DY): Sets threshold between received light
beam high and low intensity.
Window Set (WN): Sets two thresholds equally spaced
above and below received light beam intensity. Received
light beam intensity within the window is a valid detect.
Outside the window is not a valid detect.
AUTOSET Modes
The sensor’s automatic threshold adjustment is controlled by the AUTOSET mode. Each
AUTOSET mode sets the threshold differently. Select the mode that works best for your
specific application. See details at the left.
AUTOSET Percent
For Light State (LS), Dark State (DS), and Window AUTOSET Modes (WN), the offset
percentage is adjustable. AUTOSET Percent determines threshold placement during
AUTOSET. Placement is a percentage of received light beam intensity.
1% - 50% (Hold to scroll)
AUTOSET Mode:
Light State LS
AUTOSET Mode:
Dark State DS
AUTOSET Mode:
Midpoint MP
AUTOSET Mode:
Two-Point 2P
AUTOSET Mode:
Dynamic DY
AUTOSET Mode:
Window WN
Select
p
q
n
Tap MODE (n) again to access first parameter. Continue tapping to select desired
parameter. Use the threshold/value ADJUST ROCKER (qp) to select or adjust a
specific parameter.
AUTOSET Pct:
10%
n
ADJUST
p
q
Signal
Returned Light
Display
MP
Threshold
Returned
light level
when
AUTOSET is
pressed
MP Setup
Signal
Returned Light
Display
Detect
No
Detect
AUTOSET
%
(10%)
AUTOSET
%
(10%)
Returned
light level
when
Autoset
is pressed
Signal
Returned Light
Display
Autoset Pt 1
Threshold
Autoset Pt 2
Signal
Returned Light
Display
DS
Threshold
LS
Threshold
AUTOSET
%
(10%)
AUTOSET
%
(10%)
Returned
light level
when
Autoset
is pressed
LS / DS Setup
2P or DY Setup WN Setup
In Light-On Mode,
a detect occurs
when signal is
within the window.
Programming
When using DUAL CHANNEL: Each channel has three
paramaters (AUTOSET, Detect Mode, and Timers) that can be tailored to your unique
application. System wide parameters are changed in Channel 1. Follow the
programming procedure contained in this section for Channels 1 and 2.
When using SINGLE / HEALTH MONITOR:
Channel 1 has three paramaters AUTOSET, Detect Mode, and Timers that
can be tailored to your unique application as well as several system
parameters. Follow the programming procedure contained in this section
for Channels 1, and see page 6 for detailed instructions pertaining to
Health Monitor.
Switch between Screens 1 and 2
by pressing straight down on the
3-way toggle switch.

www.ttco.com • 800-237-0946 3
Light On (LO): Output activates when received light intensity is over the
threshold. Note: In window mode (WN) output activates when received light
intensity is inside the window thresholds.
Dark On (DO): Output deactivates when received light intensity is over the
threshold. Note: In window mode (WN) output activates when received light
intensity is outside the window thresholds.
Detect Mode
Sensor output activates or deactivated when received light intensity is over the threshold. Not available when
input function is set to Remote Dark On.
OBJECTS
DARK ON
SENSOR
OBJECTS
LIGHT ON
SENSOR
Detect Mode:
Light On LO
Detect Mode:
Dark On DO
n
Select
p
q
Timer/Counter Function #:
Choose from 19 pre-configured timer/counter control functions.
Each one represents a function such as on-delay, off-delay,
etc. Once a function is selected, adjustable parameters of that
function appear such as delay time.
PRESS
n
On Delay:
10ms
Timer Duration
0.1 - 9.9, 10 - 9999ms
Hold up or down to scroll.
n
ADJUST
p
q
“ON” Delay
OFF
Events
Output
"ON"
Delay
Auto
ON
Input
One-Shot
ON
Input OFF
Events
Output
One-
Shot
One-
Shot
One-
Shot
Motion Detection One ShotOne Shot TriggeredTriggered
Input
ON
OFF
Events
Output
Retriggered
Latching, Edge Triggered
Input
Events
Output
ON
OFF
Reset Required
“ON” Delay then “OFF” Delay
Input
Events
Output
ON
OFF
"ON" "OFF"
Delay Delay
“ON” Delay, then One-Shot
ON
OFFInput
Events
Output
"ON" One-Shot
Delay
“ON” Delay then Latch
Input
ON
OFF
Events
Output
"ON"
Delay Latched
Reset Required
“OFF” Delay then Latch
ON
Input
Events
OFF
Output Reset Required
"OFF"
Delay Latched
10
Blind One-Shot
ON
OFF
11
One-Shot Delay, then One-Shot
ON
OFF
Input
Events
Output
One-
Shot
Delay
12
One-Shot Delay, then Latch
Input
Events
ON
OFF
Output
Delay Latched
Reset Required
13
Stop Motion, then One-Shot
ON
OFF
Input
Events
Output
Retriggerable
One-Shot
One-
Shot
14
Stop Motion, then Latch
ON
OFF
Input
Events
Output
Retriggerable
One-Shot
Requires Reset
Latched
15
Latch then “ON” Delay
Input
Events
Output
ON
OFF
"ON"
Delay
16
Latch, then One-Shot
17
One-
Shot
Delay
One-
Shot
Delay
Input
Events
Output
One-
Shot Note:
Output will not occur again
until Reset applied to Latch
ON
OFF
01
03
04
05
06
07
08
00
“OFF” Delay Pulse Stretcher
ON
Input OFF
Events
Output
"OFF"
Delay
"OFF"
Delay
"OFF"
Delay
02
Timer not used.
“OFF” Delay then One-Shot
ON
Input OFF
Events
Output
"OFF"
Delay One-
Shot
09
Count, One-Shot
18 Input
Events
Output
1234012
One-Shot
One-Shot output occurs on the Nth
detection. For this example N = 5.
Input
Events
Output
19
Count, Latch
Events
Output
1234567
Reset Required
Latch occurs on Nth detection.
For this example N = 5. Latched
Latched
One Shot One ShotBlind Blind
Reset Required
Input
Timer Func: 00
Bypass
Timer Func: 01
On-Delay
Timer Func: 02
Off-Delay
Timer Func: 03
One-Shot
Timer Func: 04
Motion
Timer Func: 05
Latch
Timer Func: 06
On, Off-Delay
Timer Func: 07
On, One-Shot
Timer Func: 08
On, Latch
Timer Func: 09
Off, One-Shot
Timer Func: 10
Off, Latch
Timer Func: 11
Blind One-Shot
Timer Func: 12
Delayed One-Shot
Timer Func: 13
Delayed Latch
Timer Func: 14
Stop, One-Shot
Timer Func: 15
Stop, Latch
Timer Func: 16
Latch, On-Delay
Timer Func: 17
Latch, One-Shot
Timer Func: 18
Count, One-Shot
Timer Func: 00
Count, Latch
Select
p
q
Count:
0005
Counter
0001-9999
Hold up or down to scroll.
n
ADJUST
p
q

4 www.ttco.com • 800-237-0946
Output Mode
Outputs can be set one of three ways:
Output Mode:
PNP - Source
Output Mode:
NPN - Sink
Output Mode:
Push/Pull
n
Select
p
q
B
A
Asynchronous Crosstalk
Ultra-High-Speed (UHS): Fastest response time (50us).
Not available in Asynchronous Anti-Crosstalk Mode.
High-Speed (HS): Fast response time with higher sensitivity (125us). Not
available in Asynchronous Anti-Crosstalk Mode.
Standard (STD): Good balance of response time and range for general
purpose sensing (250us).
High-Resolution (HR): Improved resolution for general purpose sensing (1ms).
Long-Range (LR): General purpose sensing with improved range (4ms).
Ultra-Long-Range (ULR): Special purpose sensing with maximum sensitivity
and range (16ms).
Best
Resolution
Fastest
Speed
Response Time:
Ultra-High-Speed
Response Time
Select which mode that best fits the performance need of your application. Sensor speed, range, and sensitivity
are optimized for best performance.
Response Time:
High-Speed
Response Time:
Standard
Response Time:
High-Resolution
Response Time:
Long-Range
Response Time:
Ultra-Lon-Range
Hysteresis:
Low H0
Hysteresis
To avoid false triggers for example due to object vibration. Adjusts the span between the operate point and the
release point of the sensor output. Low hysteresis increases sensitivity and high hysteresis increases sensing
stability.
Hysteresis:
Standard H1
Hysteresis:
High H2
n
Select
p
q
n
Select
p
q
Anti-Crosstalk
Turns on Asynchronous Anti-Crosstalk rejection for two sensors. Note: Channels 1 and 2 cannot be set as
Channels A and B; anti-crosstalk is for use of two seperate sensors.
Not available for UHS and HS modes.
Anti-Crosstalk:
Disabled
Async Crosstalk:
Channel A xA
Async Crosstalk:
Channel B xB
n
Select
p
q
Hysteresis
Distance
Sensing
Distance
OFF
ON
OFF
ON
Most Sensitve
Hysteresis
Distance
Sensing
Distance
OFF
ON
Hysteresis
Distance
Sensing
Distance
Most Stable
OFF
ON
Disabled: Turns off Anti-Crosstalk rejection.
Assign one sensor to channel A and the
other to channel B.
}
A
B
The following are system wide perameters that can only be adjusted in Channel 1.
(Change channels by pressing straight down on the rocker switch if necessary).
Low (H0): Reduced hysteresis for increased sensitivity.
Standard (H1): Automatic adjustment depending on signal level.
High (H2): Increased hysteresis for increased stability.
PNP - Source: PNP transistor open
collector output.
NPN - Sink: NPN transistor open
collector output.
Push/Pull: NPN and PNP transistor
connected in a push/pull configuration.
LED Power
Emitter LED power set for Channel 1 will override Channel 2 (both will
always be the same), so use Low or High only to prevent invalid
Channel 2 setting.
LED Power:
AUTO 1A
LED Power:
Low 0P
LED Power:
High 1P
n
Select
p
q
Auto: automatically determined during
Channel 1 AUTOSET.
Low: Cuts power to prevent saturation.
Example: short range.
High: Boosts power when signal level is
low. Example: long range.
Channel Configuration
Choice of a Channel 1 and 2, or Channel 1
with Health Monitor:
Channel Config:
Dual Channel
Channel Config:
Single / Health
n
Select
p
q
Dual Channel: Channels 1 and 2 are
independent.
Single / Health: Reconfigures
Channel 2 to be used as the Health
Monitor. See page 6 for Health
Monitor information.
Mounting on a
DIN Rail
1.Hook the DIN rail clip
on the bottom of the
sensor under the
edge of the DIN rail.
2.Gently push and pivot
the sensor onto the
DIN rail, pressing until
it snaps into place.
Fiber Emitter
Fiber Receiver
Fiber Clamp
Move Fiber Clamp forward,
insert fibers, and move clamp
back to secure in place.
Installing the Fibers
1. Open the dust cover.
2. Move the fiber clamp
forward to unlock it.
3. Insert the fiber(s) into the
fiber port(s) until they stop.
4. Move the fiber clamp
backward to secure the
fiber(s).
5. Close the dust cover.

www.ttco.com • 800-237-0946 5
n
Lock Mode Locks buttons. Note: Input wire remains unlocked.
Display Mode Selects between numeric and percentage modes and flips orientation.
Display Mode:
Numeric
Display Mode:
Percentage
Button Lock:
Disabled
Button Lock:
Enabled
n
Select
p
q
Select
p
q
01.0% 99.9%
Sensor Locked
04095 00016
00016 04095
Displayed when sensor is
locked.
Display Mode:
Numeric
Display Mode:
Percentage
99.9% 01.0%
FIBER CABLE
FIBER CABLE
04095
00016
9 9.0 %
01.0%
Display flips 180 degrees.
FIBER
CABLE
FIBER
CABLE
00016
04095
01.0%
9 9.0 %
Display flips 180 degrees.
Factory Reset Hold down MODE (n) on power up, then hit up or down (pq).
Sensor will return to all settings to factory default (see chart above).
Default Setting Chart
Default Other Options
Light-State Dark-State, Midpoint,Two-point, Dynamic, Window
10% 1% - 50%
Light On Dark On
Bypass Timer 1-19
10ms 0001 - 9999ms
Standard Ultra-High-Speed, High-Speed, High-Resolution, Long-Range, Ultra-Long-Range
Standard Low, High
Disabled Asynchronous Channel A, Asynchronous Channel B
Auto Low, High
Dual Channel Single / Health
PNP - Source NPN - Sink, Push/Pull
Remote Set Remote Command, Interrogate, Gate, Remote Dark On, Remote Lockout
Active High Active High, Active Low
Numeric Percentage, Numeric Flipped, Percentage Flipped
Unlocked Enabled
Disabled Automatic
Good Great, Low
Active High Active Low
Input Polarity
Select the active state of the input.
Input Functions
Select input to be performed:
Input Function:
Remote Set
Input Function:
Remote Command
Input Function:
Interrogate
Input Function:
Gate
Input Function:
Remote Dark On
Input Polarity:
Active High
Input Polarity:
Active Low
Input Function:
Remote Lockout
n
Select
p
q
n
Select
p
q
Remote set: An AUTOSET function is performed when input wire is transitioned from idle to
active and returned. Note: input wire can be used in addition to the AUTOSET button.
Remote command: Sensor parameters can be adjusted via defined pulses. See chart on
page 7.
Interrogate: Sensor output is latched when input wire is transitioned from idle to active.
Gate: Sensing is gated. Detection is enabled when input is active.
Remote Dark On: Detect Mode is determined by input state. Dark On mode is used when
input is active.
Remote Lockout: Remote lock of the AUTOSET, up and down adjust and most mode
functions.
Disabled: To ignore unwanted signals.
Active High: Selects active High.
Active Low: Selects active Low.
Disabled: Adjustments made by anyone.
Enabled: Prevents unauthorized tampering.
To unlock, tap MODE to scroll through menu to
Button Lock and select Disabled to unlock.
Input Function:
Disabled
CHANNEL 1
AUTOSET MODE
AUTOSET PERCENT
DETECT MODE
TIMER
TIMER DURATION
RESPONSE TIME
HYSTERESIS
ANTI-CROSSTALK
LED POWER
CHANNEL CONFIG.
OUTPUT MODE
INPUT FUNCTIONS
INPUT MODE
DISPLAY MODE
LOCK MODE
CHANNEL 2
AUTOSET MODE
AUTOSET PERCENT
DETECT MODE
TIMER
TIMER DURATION
HEALTH MONITOR
MARGIN TRACKING
REQUIRED MARGIN
ALERT MODE

6 www.ttco.com • 800-237-0946
IMPORTANT:
To use the Health Monitor the sensor
must be put in Single / Health mode.
Margin Tracking
When enabled, automatic adjustments will be made to the threshold if the
margin gets too low.
Margin Tracking:
Automatic
Margin Tracking:
Disabled
n
Select
p
q
Automatic: The sensor will automatically
make small adjustments to the threshold
setting.
Disabled: Adjustments will need to be made
manually.
Required Margin
Choose how sensitive to set the alarm.
Required Margin:
Low
Required Margin:
Good
n
Select
p
q
Low: Alarms when the margin is less than
Low (less than 25% filled).
Good: Alarms when the margin is less than
Good (less than 50% filled).
Great: Alarms when the margin is less than
Great (less than 100% filled).
Required Margin:
Great
Alert Mode
Select the active state of the output.
Alert Mode:
Active High
Alert Mode:
Active Low
n
Select
p
q
Active High: Selects active High.
Active Low: Selects active Low.
ThresholdAUTO
Margin Tracking
Current
Margin
Threshold
25%
50%
100%
Signal
Time
Real Time Status
25%
50%
100%
Margin
Margin
Percent
Filled
The term contrast is commonly used when characterizing fiber-optic sensor
performance. Contrast is the light difference between the light-state
and dark-state conditions of a sensing task. The sensors
switching threshold is placed between these two conditions via
the AUTOSET button during a setup. When the setup is
complete the sensors diagnostic screen is used to determine if
enough margin is present above and below the threshold for
stable operation. This is done by passing an object through the
light beam while watching the screen.
This is most useful when the object moves slowly past the fiber-optics. In general,
numerical displays are ineffective for monitoring sensor performance at fast and
even moderate production line speeds. The DFS21 includes a new feature to
address this issue. We use a unique algorithm to track how far above (+Margin)
and how far below (-Margin) the signal goes relative to the threshold over multiple
events.
We then turn the second channel output into a health channel output and the
second channel display into a health monitor meter to display the tracked margin.
The more filled the health monitor meter the better the margin. At the bottom left of
the screen, sensor performance is categorized as Poor, Low, Good, or Great. The
bargraph display has steps to
indicate the difference between
the 4 levels. Fully filled is
“Great”, 50% is “Good”, 25%
filled is “Low” and less than that is Poor. The system requires ongoing events to
evaluate margin. This screen can be left active. When the health monitor meter is
underfilled, tapping the appropriate manual adjust – or + can increase margin.
Health Monitor System
Setting up Health Monitor Parameters:
Dual Channel
Mode
Single Channel / Health Monitor
Mode
Switch between
Screens 1 & 2
by pressing
straight down
on the 3-way
toggle switch.
Change between Dual Channel and
Single Channel with Health Monitor by
changing Channel Configuration
parameter. See page 4 for details.
Pressing the AUTOSET button with
the health channel selected will
instantly optimize the threshold-
maximizing margin.
Tap Minus (-) to move
threshold.
Tap Plus (+) to move
threshold.
Optimized
Tracking Optimizer
When Margin Tracking System is enabled, automatic adjustments will be
made to the threshold to maintain margin over time. This optimizes the sensing
application, and manual adjustment won’t be needed.
Health Channel Alarm and “Required Margin” Parameter
If the health monitor detects a problem, an alarm is sent via the health channel
output. You can choose how sensitive to set the alarm via the Required Margin
parameter. If you set the parameter to “Good” you will get an alarm when the
margin is less than “Good”. The alarm is self-resetting when the monitor detects
that margins have returned to a “Good” level.
About: Health Monitor System

www.ttco.com • 800-237-0946 7
Delay
D
Delay
D
P
Active
Idle
P
Pulse width (P) is 40ms - 400ms.
The delay between sets of pulses (D) is 0.75 - 5 seconds.
Remote Command
Programming
In Remote Command Mode a limited set of options
can be configured via the input wire. This is
accomplished by sending a simple sequence of
pulses on Q2 (white wire). For example, sending a
sequence of three pulses followed by three pulse
followed by two pulses selects dark on mode.
Example of 2 - 3 - 2 pulse command
Setting Option Icon Pulse Notes
Sequence
AUTOSET Channel 1 1 - - -
Channel 2 2 - - -
PER CHANNEL
AUTOSET Mode Light-State LS 3 - 1 - 1
Dark-State DS 3 - 1 - 2
Midpoint MP 3 - 1 - 3
Two-Point 2P 3 - 1 - 4
Dynamic Set DY 3 - 1 - 5
Window WN 3 - 1 - 6
AUTOSET Percent 1% 01% 3 - 2 - 1
2% 02% 3 - 2 - 2
5% 05% 3 - 2 - 3
10% 10% 3 - 2 - 4
20% 20% 3 - 2 - 5
50% 50% 3 - 2 - 6
Detect Mode Light On LO 3 - 3 - 1
Dark On DO 3 - 3 - 2
Timer Function Bypass 3 - 4 - 1
On-Delay 3 - 4 - 2
Off-Delay 3 - 4 - 3
One-Shot 3 - 4 - 4
Motion 3 - 4 - 5
On, Off-Delay 3 - 4 - 6
On, One-Shot 3 - 4 - 7
Off, One-Shot 3 - 4 - 8
Blind One-Shot 3 - 4 - 9
Delayed One-Shot 3 - 4 - 10
Stop, One-Shot 3 - 4 - 11
Timer 1 Duration 1ms 3 - 5 - 1
2ms 3 - 5 - 2
5ms 3 - 5 - 3
10ms 3 - 5 - 4
20ms 3 - 5 - 5
50ms 3 - 5 - 6
Timer 2 Duration 1ms 3 - 6 - 1
2ms 3 - 6 - 2
5ms 3 - 6 - 3
10ms 3 - 6 - 4
20ms 3 - 6 - 5
50ms 3 - 6 - 6
SHARED
Button Lock Disabled 4 - 1 - 1
Enabled 4 - 1 - 2
Display Mode Numeric 4 - 2 - 1
Percentage 4 - 2 - 2
Numeric (Flipped) 4 - 2 - 3
Percentage (Flipped) 4 - 2 - 4
Response Time Ultra-High-Speed UHS 4 - 3 - 1 Anti-Crosstalk Disabled
High-Speed HS 4 - 3 - 2 Anti-Crosstalk Disabled
Standard STD 4 - 3 - 3
High Resolution HR 4 - 3 - 4
Long-Range LR 4 - 3 - 5
Ultra-Long-Range ULR 4 - 3 - 6
Hysteresis Low H0 4 - 4 - 1
Standard H1 4 - 4 - 2
High H2 4 - 4 - 3
Anti-Crosstalk Disabled 4 - 5 - 1
Async-Channel A xA 4 - 5 - 2 Changed but ignored in UHS & HS
Async-Channel B xB 4 - 5 - 3 Changed but ignored in UHS & HS
LED Power Auto #A 4 - 6 - 3
High Power IP 4 - 6 - 3
Low Power OP 4 - 6 - 3
HEALTH MONITOR
Channel Config. Dual Channel 5 - 1 - 1
Single / Health 5 - 1 - 2
Margin Tracking Disabled 5 - 2 - 1
Enabled A 5 - 2 - 2
Required Margin Low 5 - 3 - 1
Good 5 - 3 - 2
Great 5 - 3 - 3
Alert Mode Normally Open 5 - 4 - 1 Active High in Push/Pull Mode
Normally Closed 5 - 4 - 2 Active Low in Push/Pull Mode
Active Channel Channel 1 6 - 1 - Invalid with Health enabled
Channel 2 6 - 2 -
Percentage will affect the next
Light, Dark AUTOSET.
Immediate effect on Window Size
A single pulse initiates AUTOSET. An
additional pulse command is required
to complete AUTOSET for two-point
and dynamic modes.
Pulses are displayed while being received. Valid
commands are executed immediately. Holding the
input active will cancel a partial command.
AUTOSET
A single pulse command initiates an AUTOSET.
A second single pulse command is required to
complete Two-Point and Dynamic AUTOSETs.
(Window) Invalid when Health
Monitor enabled

SUPPLY VOLTAGE & CURRENT
• 8-30 Vdc
• 28ma @ 24Vdc, 49ma @ 12Vdc
• Reverse polarity protected
• Transient spike protected
OUTPUT
• Configurable NPN, PNP or Push-Pull
• 150mA output current
• Short circuit & transient spike protected
• Saturation voltage: < 0.3Vdc @ 10mA
< 2Vdc @150mA
INPUT
• Configurable active high/low
• Transient spike protected
• Configurable function: Remote setting or
commands, Interrogate, Gate, Dark-On, Lockout,
and Latch Reset.
POWER-UP DELAY
• 300ms. No output pulse on power-up.
RESPONSE TIME (Dependent on Mode)
• Ultra-High-Speed (UHS) 50µs
• High-Speed (HS) 125µs
• Standard (STD) 250µs
• High-Resolution (HR) 1ms
• Long-Range (LR) 4ms
• Ultra-Long-Range (ULR) 16ms
REPEATABILITY (Dependent on Mode)
• UHS 12µs.
• HS, STD, HR, LR, ULR (15.635µs)
• Asynchronous crosstalk enabled (31.25µs)
MAXIMUM RANGE
(RED) (INFRARED)
Opposed Mode
• UHS 20in (508mm) 34in (878mm)
• HS 28in (711mm) 48in (1219mm)
• STD 32in (813mm) 57in (1463mm)
• HR 47in (1193mm) 69in (1756mm)
• LR 60in (1524mm) 83in (2121mm)
• ULR 75in (1905mm) 118in (3000mm)
Proximity Mode
• UHS 8in (203mm) 10in (254mm)
• HS 11in (279mm) 14in (355mm)
• STD 13in (330mm) 15in (381mm)
• HR 16in (406mm) 20in (508mm)
• LR 21in (533mm) 23in (584mm)
• ULR 28in (711mm) 28in (707mm)
When anti-crosstalk is enabled maximum range
specifications are reduced 30%.
Note: Opposed tests utilized: PF-Z-78TL (Red)
Proximity tests utilized: PFD-Z-78M64 (Red)
LIGHT IMMUNITY
• High immunity to most ambient light, including
high efficiency lighting and high intensity strobes.
MUTUAL INTERFERENCE REJECTION
• Asynchronous: Two sensor max. responds to
selected A or B Channel.
COMBINABLE DUAL TIMERS & COUNTERS
• On-Delay, Off-Delay, One-Shot, Motion
• Latching function
• Counters (counting range up to 9999)
• Each channel can use a unique timer/counter
• Timer range: 0.1 - 0.9ms, 1ms - 9,999ms
LED LIGHT SOURCE
• 4 element LED, Red = 660nm
• IR = 880nm (Use glass fibers with Ø2.2mm
connection only).
DISPLAY
• 96 X 16 white dot matrix OLED
• Display numerical range depended on processing
mode
• UHS - 1,023
• HS - 2,047
• STD - 4,095 (default setting)
• HR - 16,383
• LR - 32,767
• ULR - 65,535
LED INDICATORS
• Each channel has a seperate LED indicator,
Channel 1 and Channel 2.
Output: Red LED. Illuminates when output is ON.
Flashes when either output is overloaded.
CONNECTIONS
• M8, 5-pin
• Attached cable: 5-wire 6ft (1.8m)
OPERATING TEMPERATURE
• 5°C to 55°C (41°F to 131°F) - Electrical.
HOUSING CONSTRUCTION
• Chemical resistant, high-impact polycarbonate
RATINGS & CERTIFICATIONS
• IP50
• CE
• UL pending
Specifications
Dimensions DFS21 Digital Fiber Optic Sensor
0.39"
[10.0mm]
3.58" [90.9mm]
1.10" [27.8mm]
35mm DIN RAIL
MOUNTING
0.25"
[6.4mm]
0.28"
[7.0mm]
(ALTERNATE MOUNTING
WITH INCLUDED BRACKET -
SEE DETAIL)
CLEAR COVER
(SEE DETAIL)
5-PIN MALE M8
CONNECTOR (B CODE)
(ALSO AVAILABLE
WITH ATTACHED
6 FT CABLE)
(3)(1)
(4)(2)
(5)
Pin 1 = Pos (Brown*)
Pin 2 = Q2 (White*)
Pin 3 = Neg (Blue*)
Pin 4 = Q1 (Black*)
Pin 5 = IN (Grey*)
* - wire colors are identical for
sensors with built in 6ft cables
4.06" [103.0mm]
5.84" [148.3mm]
1.00"
[25.4mm]
0.63"
[16.0mm]
4X Ø0.13"
[Ø3.2mm]
0.10" [2.5mm]
1.35" [34.3mm]
0.25" [6.4mm]
AUTOSET
MODE
8 www.ttco.com • 800-237-0946 070-0664, Rev. 2
RoHS Compliant
Product subject to change without notice
Table of contents
Other Tri-Tronics Measuring Instrument manuals
Popular Measuring Instrument manuals by other brands
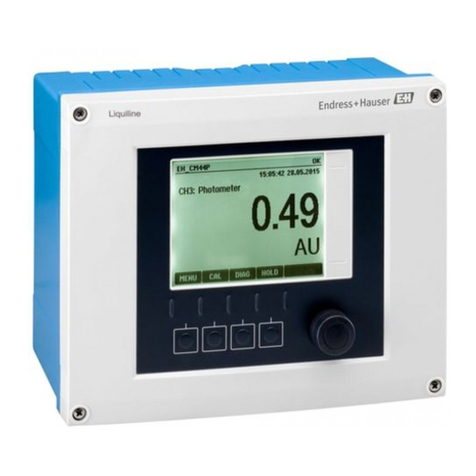
Endress+Hauser
Endress+Hauser Liquiline CM44P Brief operating instructions
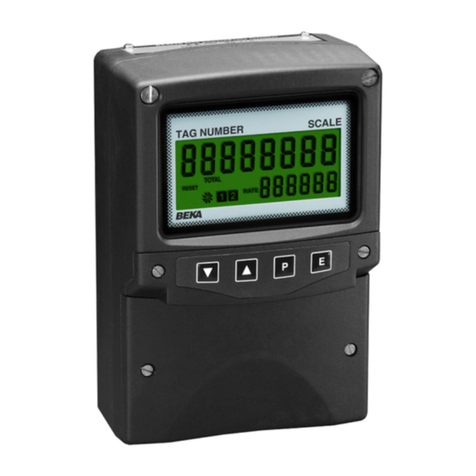
BEKA
BEKA BA334ND manual
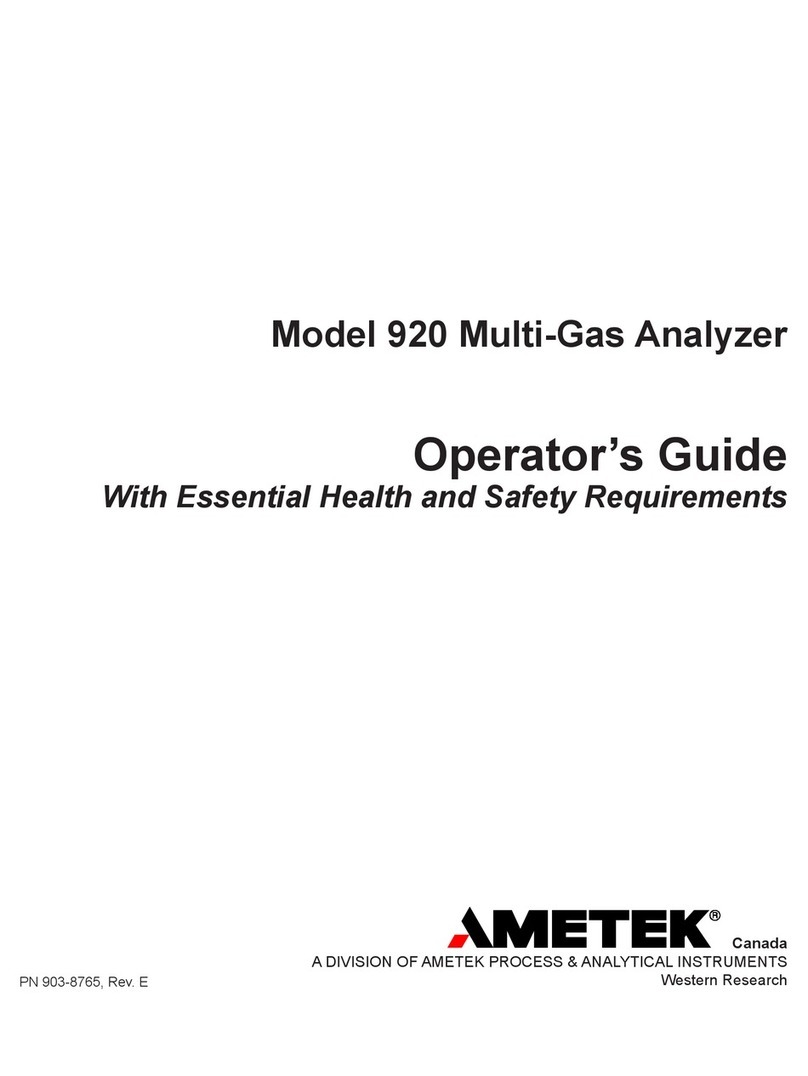
Metek
Metek 920 Operator's Guide With Essential Health and Safety Requirements
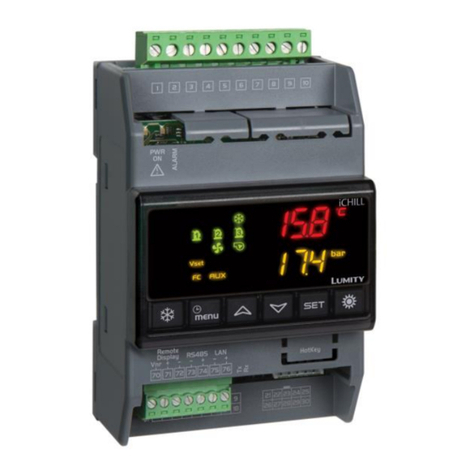
Emerson
Emerson Lumity IC100D EVO Quick reference guide
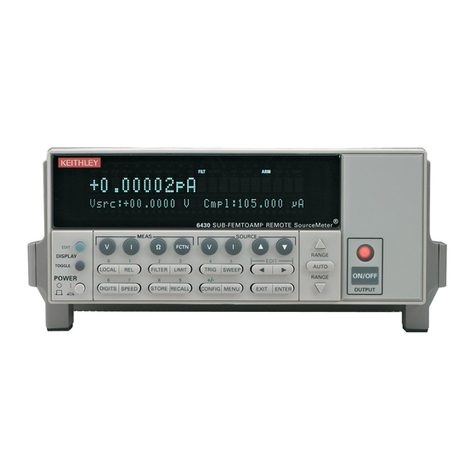
Keithley
Keithley 6430 Quick results guide
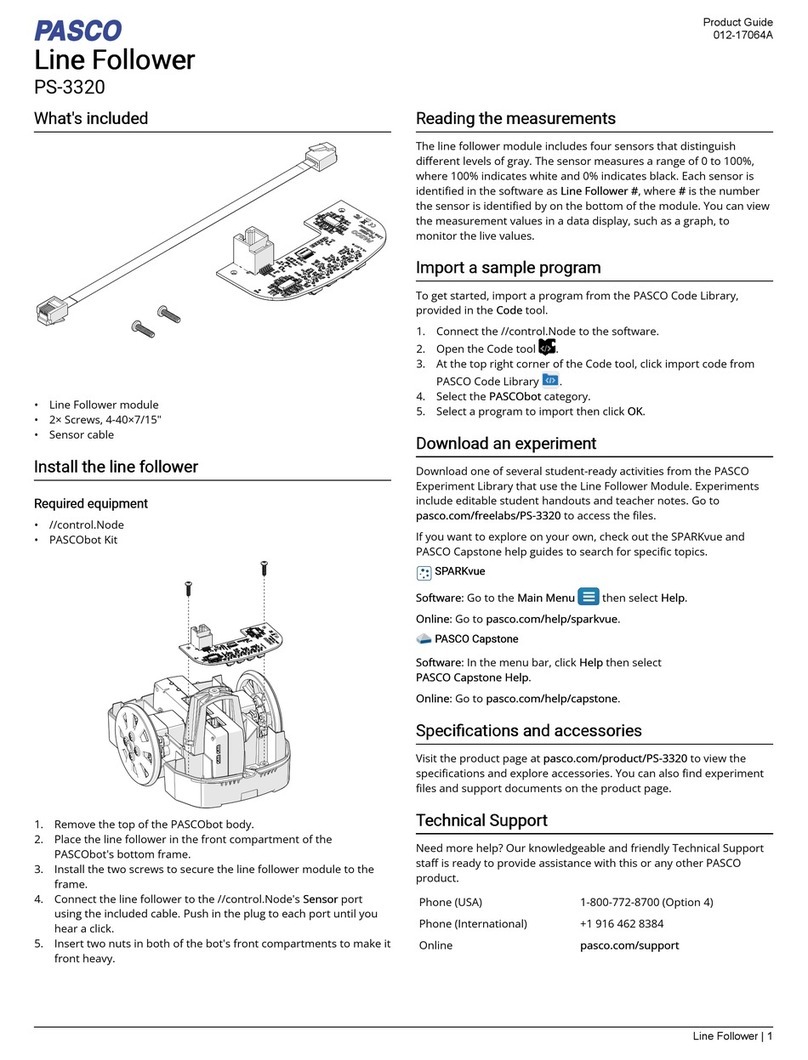
PASCO
PASCO PS-3320 Product guide

Unipulse
Unipulse F370 Operation manual

KROHNE
KROHNE M-PHASE 5000 Supplementary instructions
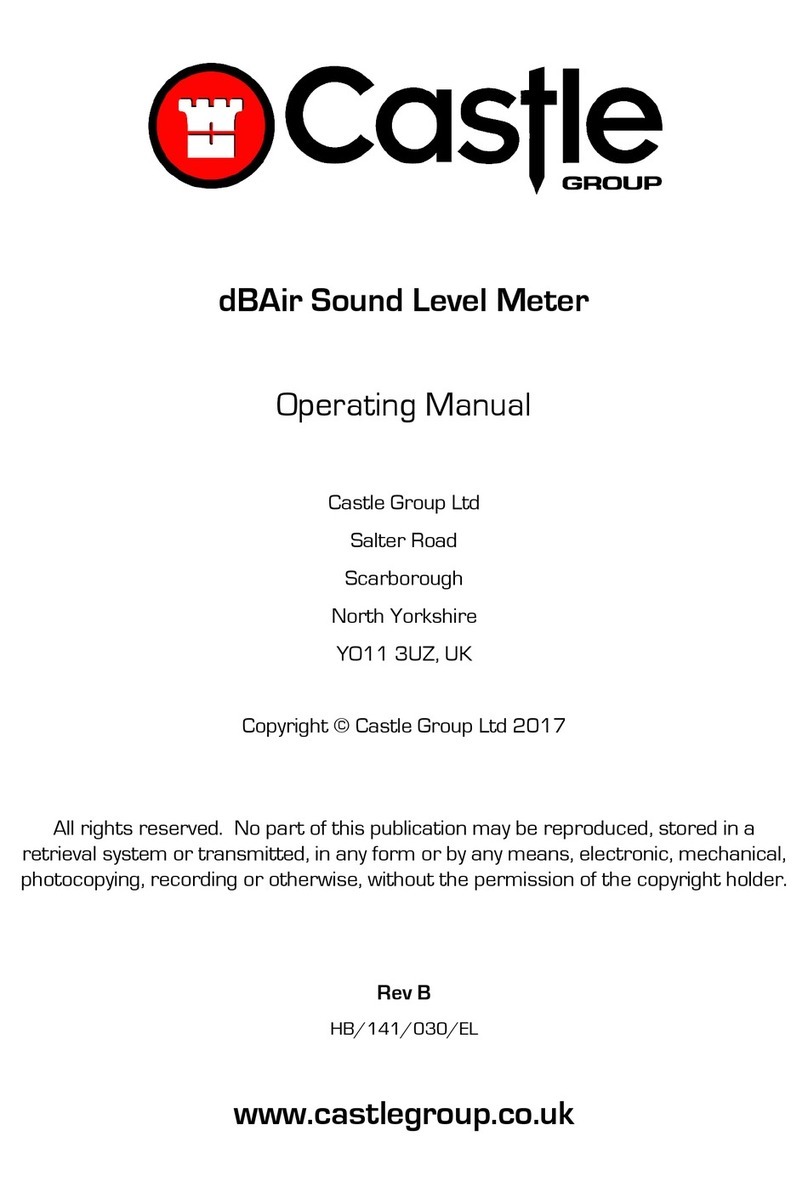
Castle group
Castle group dBAir operating manual

Keller
Keller CellaTemp PA 4 Series quick guide

Leica Geosystems
Leica Geosystems Rugby 640 quick start
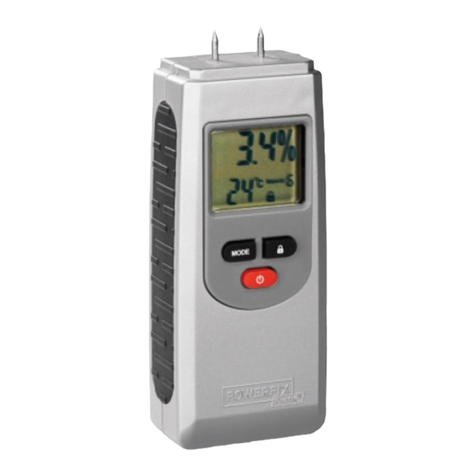
Powerfix Profi
Powerfix Profi HG00384C Operation and safety notes