Trio Avionics EZ Series Specification sheet

EZ Series
Altitude Control Systems
Operation and Installation Manual
Trio Avionics Corporation
Rev 1.8

2
Notice and Warnings
Warning: Any failure to comply with the following warnings can
lead to property damage, and serious injury including death.
Although Trio Avionics has taken reasonable steps to test its product, the final determination of safe
operation lies with you, the installer and pilot. Your workmanship in installing, cabling, and testing the
Altitude Hold system in your airplane is critical to safety. If you are not the original builder of your aircraft,
and do not hold a valid “Repairman’s Certificate” for your aircraft, you must have the installation done by a
qualified A&P aircraft mechanic or the original builder. You must comply with all current FAA regulations
regarding installation of this device in your airplane.
This product is to be used on homebuilt, experimental aircraft only. It is not approved for, nor is it legal to
install it in, certified aircraft. It is not approved by any governmental or non-governmental agency.
Prior to installing or flying this altitude hold system, read the manual completely. If you have any questions
about the installation or operation of the system, STOP and then call or email Trio Avionics for clarification.
The servo that is a part of this altitude hold system is attached directly to your elevator control system. It is
possible to install or adjust it in a manner that may result in improper or unexpected elevator movement that
could result in dangerous aircraft maneuvers. Install it only after you have read and understand the
installation instructions. You must thoroughly inspect and test your installation prior to flight. Mistakes in
any modification to your aircraft can be life threatening!
Each homebuilt aircraft is individual in its construction, maintenance and flying characteristics. Therefore,
while Trio Avionics has tested the product in a variety of aircraft, we do not represent or warrant that it is
appropriate or suitable for use in your particular aircraft. Only you can make that determination and
ultimately only you are responsible for its safe installation and use.
This product is designed for use as an en route navigation aid only, and only at safe altitudes in
unobstructed airspace. It must not be relied upon for any other purpose. It is not to be used for flight in
instrument meteorological conditions (IFR), or approaches into airports in either IFR or visual (VFR)
conditions. Power to the servo must be turned “off” for takeoffs and landings.
In operation, this product relies upon data provided by solid state sensors, gyros and electronic
components. Always keep in mind that such systems should never be thought of as totally reliable. They
may be disrupted by electromagnetic interference, close proximity of transmitting antennas and cables, and
other problems.
When flying an aircraft with this, or any, altitude hold system enabled, you must be constantly vigilant for
any sign of improper operation of the system. When there is even a suspicion that the altitude hold system
is not operating properly, you must immediately disable the altitude hold system by any of the various
methods detailed in this manual. Do not fly the altitude hold system without incorporating the remote servo
disconnect switch that is described in this manual.
There may be a tendency to concentrate on the instrument display when test flying this or any other new
system in your aircraft. Do not allow it to distract you from the need to “see and avoid” other aircraft.
The safe practice of aviation demands the consistent exercise of pilot skill, knowledge of
airmanship and weather, judgment and focused attention at a level which is appropriate to the
demands of each individual situation. Pilots who do not possess or exercise the required
knowledge, skills and judgment are frequently injured or killed. Therefore, although an altitude
hold system can serve as a useful navigation aid, no altitude hold system can be relied upon and
you must be at full attention at all times while flying any aircraft.
If you do not agree to comply with any of the warnings or notices above, do not
install or fly this altitude hold system in your aircraft. Call Trio Avionics for a
Return Material Authorization (RMA) and return the unused system for a full
refund.

3
Table of Contents Page
Notice and Warnings ....................................................................................................................2
1.0 Introduction...................................................................................................................................4
2.0 General Information......................................................................................................................4
3.0 Operation.......................................................................................................................................4
3.1 Startup....................................................................................................................................5
3.2 “Alt Hold” Mode.......................................................................................................................5
3.2.1 Fine Adjustments to Altitude .............................................................................6
3.2.2 ADJUST TRIM Annunciator ..............................................................................6
3.3 Pilot Command Steering (PCS) Mode....................................................................................7
3.4 System Gain, Brightness, Contrast, Servo Deadband & Trim settings...................................7
3.5 Safety Warning Features........................................................................................................8
3.5.1 Audible Warning................................................................................................8
3.5.2 G Force Limit.....................................................................................................8
3.5.3 Servo Clutch Slip...............................................................................................9
3.5.4 Servo CW (or CCW) Limit.................................................................................9
3.5.5 Servo Fault......................................................................................................10
4.0 System Safety Features .............................................................................................................10
4.1 Aircraft G-Load Sensing .......................................................................................................10
4.2 Servo Electronics Monitoring................................................................................................10
4.3 Clutch Slip Detection ............................................................................................................10
4.4 Rotation Limit Detection .......................................................................................................10
4.5 Supervisory Processor Monitoring........................................................................................10
4.6 Servo / Trim Driver Chip Fault Detection..............................................................................11
4.7 Disconnect Solenoid.............................................................................................................11
4.8 SMP and Supervisory Processor Watchdog Interrupts.........................................................11
5.0 Installing the Altitude Hold Control Module…… ………………...............……………………….11
5.1 Installing the LCD Switch......................................................................................................12
5.2 Installing the Encoder Switch................................................................................................12
5.3 Installing the Wiring Harness................................................................................................12
6.0 Servo Installation Setup...............................................................................................................13
6.1 Installing the Servo...............................................................................................................13
6.2 Servo Mounting Hardware....................................................................................................14
6.3 Selecting a Site for the Servo ...............................................................................................15
6.4 Install the Servo Pushrod......................................................................................................16
6.5 Setting Servo Override Force (Slip Clutch)...........................................................................16
6.6 Adjustment of Servo Rotation Direction and Servo Neutral..................................................17
6.6.1 Servo Direction Setting.....................................................................................17
6.6.2 Setting Trim Motor Direction.............................................................................18
6.6.3 Restore Factory Defaults..................................................................................18
7.0 SYSTEM GAIN and SERVO DEADBAND.....................................................................................18
7.1 System Gain ...........................................................................................................................18
7.2 Servo Deadband…..................................................................................................................19
8.0 The EZ-2 Altitude Hold System with Climb and Descent capability........................................19
8.1 EZ-2, EZ-3 Operation..............................................................................................................20
8.1.1 VS Mode...........................................................................................................20
8.1.2 Minimum and Maximum Airspeed Control........................................................21
8.1.3 Setting Minimum and Maximum Airspeed ........................................................22
8.1.4 Vertical Rate and Airspeed Track Pilot Command Steering (PCS) ..................23
9.0 The EZ-3 Altitude Control System with Altitude Pre-select......................................................24
9.1 EZ-3 Operation.....................................................................................................................25
9.1.1 Elevation (Baro) Set .........................................................................................25
9.1.2 EZ-3 Menu System...........................................................................................26
9.1.3 Enter Vertical Speed (VS) ................................................................................28
9.1.4 Enter a Destination Altitude..............................................................................28
10.0 Altitude Hold Wiring Diagram .....................................................................................................29
11.0 Automatic Trim.............................................................................................................................30
12.0 Glossary of Terms................................................................................. ……………………….…..32
13.0 Contact Information.....................................................................................................................32

4
SYSTEM
TEST
EZ Altitude Control System
1.0 Introduction
Congratulations on choosing the EZ Altitude Control System. The EZ-1 System is designed to
hold a precise altitude of the aircraft. The EZ-2 system has all the features of the EZ-1 system
and adds additional safety features, vertical rate selection and vertical speed or airspeed capture
capabilities. The EZ-3 system builds on the capabilities of the EZ-1 and EZ-2 systems adding
airspeed management modes and altitude preselect and capture features. The following
paragraphs describe the EZ altitude control systems in detail. The EZ-2 system description
begins in paragraph 8 of this manual. The EZ-3 system is described in section 9.
The EZ-1 will precisely maintain a desired pressure altitude for your experimental aircraft up to an
altitude of 20,000 feet. In smooth air it will hold the aircraft altitude to within +/- 20 feet (generally
less). In turbulent air or turns of 15 to 20 degrees bank angle it will hold to within +/- 50 feet.
While the EZ-1 is simple to use, this manual is a guide to understanding its basic functions and
employing its many features. Operation is as simple as pressing the “ALT HOLD” button.
This causes the aircraft to maintain the current pressure altitude. The following sections illustrate
the built in safety measures, messages and the many features available in your new system.
2.0 General Information
The EZ altitude control system is comprised of 4 major hardware elements:
1Elevator Servo
2Electronics Module
3LCD push button switch
4Rotary encoder control
In addition, an external Sonalert or other warning device may be connected to provide an audible
warning prior to system disconnect. An audio tone is also available as an input to the aircraft
intercom system. An auxiliary small remote push button (momentary – normally open) switch
mounted to the stick or yoke will allow access to the many additional features of this system.
3.0 Operation
When power is applied, the amber SYSTEM TEST message will be
displayed for approximately 8 seconds. After this stabilization period
the unit will become fully functional. The LCD switch will display a
green READY message. The altitude hold function is activated by
pressing the LCD switch which will then annunciate the hold condition
1 2
3
4

5
READY
ALT
HOLD
with a green ALT HOLD message on the LCD display. (At this time servo activation should be
detected by resistance to manual yoke or stick movement forward or backward)
To disconnect the EZ altitude control system servo activation either the REMOTE AUTOPILOT
DISCONNECT switch or the LCD SWITCH may be momentarily pressed.
During normal operation in the altitude hold mode the ENCODER knob may be used to dial in
very fine corrections to the engaged altitude. Rotating the knob clockwise will cause an altitude
increase, rotating the knob counterclockwise will result in an altitude decrease.
In addition to the servo disconnect function the REMOTE AUTOPILOT DISCONNECT switch can
be used to “fly to” another altitude. This is accomplished by pressing and holding the REMOTE
AUTOPILOT DISCONNECT switch for a period of more than three seconds. When pressed, the
servo will immediately disengage so the airplane can be flown to a different altitude and will rearm
after the three second delay period. While in the armed mode the LCD switch will flash the
amber backlight and will display ALT HOLD. On the EZ-1 system, releasing the remote
disconnect switch (after the 3 second interval) will engage the servo, show a green LCD ALT
HOLD message and hold the aircraft at the proper altitude. The EZ-2 and EZ-3 systems add a
VS rate capture or an airspeed capture as additional options to this sequence (section 8.1.4)
3.1 Startup
It is strongly recommended that a 3 to 5 amp switch or circuit breaker be used to power
the EZ altitude control system. This switch or circuit breaker will provide absolute
emergency disconnect of the altitude hold servo should all other disconnect measures
fail. Once the aircraft engine is started, part of the pre-taxi checklist should be to apply
power to the system by engaging the switch or circuit breaker. Power should be applied
as soon as possible after engine start to ensure the inertial components within the
system are stabilized prior to takeoff.
After power is applied, the system will undergo a brief startup
sequence which will last approximately 8 seconds. During this
time the amber SYSTEM TEST message will be displayed.
After this short period the unit will become fully functional and
the LCD switch will display a green READY message.
3.2 “ALT HOLD” Mode
The altitude hold function is activated by momentarily pressing
the LCD switch which will then annunciate a green ALT HOLD
message on the LCD display. (During pre-taxi checks, servo
activation can be detected by resistance to manual yoke or
stick movement forward or backward).
IMPORTANT: Prior to taxi, momentarily press the remote
disconnect switch to disengage the servo. The LCD switch will
then display the READY message. A pre-flight checklist item
should be created to ensure the altitude hold system is disengaged (in the READY
mode). An additional safety feature available on the EZ-2 and EZ-3 systems is an
automatic servo disconnect on takeoff.
Once the aircraft is in flight, and the desired altitude has been reached, the aircraft should
be trimmed for stable, level flight. The pilot may then simply press the LCD switch and
the EZ altitude control system will enter the altitude hold mode and the LCD switch will
display ALT HOLD while it is employed. The servo will engage the elevator system and
control the elevators to maintain the desired altitude.
To disconnect the EZ altitude control system, the pilot may momentarily press either the
LCD switch or the REMOTE AUTOPILOT DISCONNECT switch on the stick or yoke.

6
ALT
UP
A
DJUST
ALT
DOWN
A
DJUST
The system will then immediately release the elevators from servo control and enter the
READY mode. Turning off power to the unit will also release the servo.
3.2.1 Fine Adjustments to Altitude - While flying with the ALT HOLD engaged,
the ENCODER knob may be used to dial in very fine corrections to the engaged
altitude. Rotating the knob clockwise will cause an altitude increase (and cause
the LCD to indicate “ALT UP ADJUST”), while rotating the knob
counterclockwise will result in an altitude decrease and corresponding display.
Each “click” of the rotating knob will change the altitude by approximately 5 feet,
up or down, depending on the direction of rotation. When the altitude change is
completed, the green ALT HOLD display will appear. Alternatively, the encoder
knob may be pressed at any time to stop the adjust feature.
3.2.2 ADJUST TRIM Annunciator – As the flight progresses the aircraft may
require occasional trim changes as the fuel burn lightens the aircraft, or if the
throttle setting is changed. The servo will hold the proper altitude in all but
extreme out-of-trim conditions, but it is prudent to keep the aircraft properly
trimmed to avoid sudden excursions when the servo is disengaged.
The EZ-1 will sense when the aircraft is out of trim. If
the out-of-trim condition is minor it will not alert the
pilot. However, when the out-of-trim forces on the
servo exceed a predetermined amount, it will present a
message (flashing up or down arrows) to the pilot
advising that the aircraft trim should be adjusted. The
arrows on the display indicate the required direction of
trim adjustment. The altitude will be maintained even
though this alert is present.
When a trim adjustment is sensed by the computer the
“Trim” message will be removed, and the normal ALT
HOLD message will return. Pressing the ENCODER
switch while the “Trim” message is present will erase
the message, remove the trim correction provided by
the system and replace it with the ALT HOLD
message. If the out of trim condition remains after a
correction has been made, or the message has been
cleared the message will return in a short period of time.
Probably the quickest way to eliminate the out-of-trim condition is to momentarily
disconnect the ALT HOLD function by pressing the LCD switch, re-trim the
aircraft for level flight, and then reengage the ALT HOLD.
The EZ altitude control system is available with an automatic trim option which
will automatically trim the aircraft to remove any trim errors. This feature will
control a separate trim motor (customer provided) such as the Ray Allen
Corporation model T3-12A or similar motor.
NOTE – If the ADJ TRIM arrows appear on the LCD, but when the ALT HOLD is released there is
very little trim correction required to the aircraft, the SYSTEM GAIN setting is probably too low, not
allowing the system to properly control the aircraft. See section 6.0 for proper adjustment of the
SYSTEM GAIN setting,
TRM
DWN
TRM
UP

7
BRITE
SET
GAIN
SET
45
SERVO
DBAND
6
CONTR
SET
If the pilot wishes to re-trim the aircraft without disconnecting the ALT HOLD,
trim adjustments should be made in small increments. When each adjustment is
made, the pilot should wait for approximately 30 seconds to allow the system to
sense the change. If the “Trim” message remains, continue further adjustments
until the ALT HOLD message returns.
3.3 Pilot Command Steering (PCS) Mode
In addition to the servo disconnect function, the REMOTE DISCONNECT switch can be
used to “fly to” another altitude. This is accomplished by pressing and holding the
REMOTE DISCONNECT switch for a period of more than three seconds. The servo will
immediately disengage so the airplane can be flown to a different altitude manually and
will “re-arm” after the three second interval. While in the “armed” mode the LCD switch
will flash an amber backlight and will display ALT HOLD. Releasing the remote
disconnect switch will engage the servo and cause the LCD switch to present a solid
green color while displaying the ALT HOLD message. The aircraft will then hold the
selected altitude.
3.4 System Gain, Brightness, Contrast, Servo Deadband and (optional)
Trim Speed settings
The SYSTEM GAIN, BRIGHTNESS, CONTRAST, SERVO DEADBAND and
(optionally) the TRIM SPEED settings are adjustable with the system in the ALT HOLD
mode. The same settings are available in the READY mode with the exception of the
SYSTEM GAIN setting. This menu mode is entered from either the READY mode or the
ALT HOLD mode by pressing in and holding the encoder switch knob for at least 3
seconds.
To activate this feature, perform the following steps when either READY or ALT HOLD
message is displayed on the LCD switch:
1. Press and hold the encoder switch knob until the GAIN SET message
appears on the LCD switch
2. Press (click) the encoder switch knob repeatedly
until the desired selection is displayed.
3. Rotate the encoder switch knob to change the
setting.
The GAIN setting (ALT HOLD only) controls
the response characteristics of the system.
The proper adjustment of the GAIN setting is
fully discussed in paragraph 6.0.
The BRIGHTNESS setting controls the
illumination level of the LCD background. This
setting is best done in subdued light.
The CONTRAST adjustment will allow
setting the optimum contrast for the pilots
viewing angle.
The SERVO DEADBAND setting controls
the “deadband” width of the servo. The
proper adjustment of this parameter is fully
discussed in paragraph 6.0.

8
G
FORCE
L
IMIT
TRIM
SPEED
10
The TRIM SPEED setting is only available if
the AUTO TRIM option is installed. The TRIM
SPEED setting allows the pilot to tailor the
speed of the trim correction for the particular
airplane and trim drive motor.
4. Press and hold the encoder switch knob for 3
seconds to exit back to READY or ALT HOLD display
mode
3.5 Safety Warning Features
3.5.1 Audible Warning
Whenever the servo disconnects from the elevator control system, an audio tone
is generated, consisting of 3 beeps. This tone may be routed into the aircraft
audio system, as shown on the wiring diagram on page 19. Alternatively, an
sequential DC voltage is also provided on the connector to allow use of an
external warning device, such as a Sonalerttm or other warning instrument.
3.5.2 G Force Limit
When giving elevator control over to a servo, the pilot
must be constantly vigilant to assure that any
unexpected system activity such as that caused by
extreme turbulence or meteorological wave activity
cannot impose excessive acceleration forces on the
aircraft. To assist in this endeavor, the EZ altitude
control system incorporates an accelerometer system
that continually monitors the G forces being experienced by the aircraft.
In the event the aircraft experiences abnormal G forces, the EZ altitude control
system is designed to automatically disconnect from the control system before
structural damage can occur. The software is designed to detect acceleration
(G) forces that can cause structural damage due to system activity (or pilot
override action). The system will monitor, but not react to, accelerations due to
moderate turbulence. However, the system may automatically disconnect in
high end moderate or severe turbulence. The pilot is always cautioned to use
proper judgment as to whether to engage the EZ altitude control system in these
types of conditions. The pilot should always follow the aircraft designer’s
recommendations with regard to autopilot engagement, maneuvering speed
limitations, etc.
System Response – When the EZ altitude control system detects an
excessive G force condition it will immediately issue a servo disconnect
tone and disconnect the servo from the control system. The LCD switch
will illuminate red while displaying “G FORCE LIMIT”.
Pilot Action – Determine the cause of the excessive G force problem.
If the disconnect was due to turbulence or pilot action, the alarm may be
cleared by pressing the LCD switch, which will put the system back in the
READY condition. Altitude hold may then be re-engaged by pressing the
LCD switch. Pilot judgment should be exercised in accordance with the
NOTE: Even when the Contrast / Brightness / Gain / or Servo Deadband is selected, the LCD switch or the
REMOTE DISCONNECT switch can be pressed to disengage the servo and return to the
READY mode. Likewise, if the selection was entered from the READY mode, pressing the LCD
switch will terminate the SETUP mode and activate the ALT HOLD mode

9
SERVO
CLTCH
SLIP
S
ERVO
CW
L
IMIT
SERVO
CCW
L
IMIT
airframe designer’s limitation regarding use of an autopilot system in
turbulent conditions. If an EZ altitude control system control problem is
suspected, turn off power to the system and contact Trio Avionics for
direction before further use.
3.5.5 Servo Clutch Slip
The EZ altitude control system incorporates an
important special safety feature: a clutch within the
servo that can be overridden when actived by moderate
manual stick or yoke pressure. Sensors are provided
in the servo to detect slippage of the mechanical clutch
assembly. The message “SERVO CLTCH SLIP” will
appear as a flashing amber message if the condition is
sensed.
The clutch adjustment should be set during installation so that the system can
drive the elevator control system under normal conditions but be easily
overridden by a manual pilot input. Pilot override will force the clutch to slip,
allowing the pilot to take positive control away from the EZ-1 system in
emergency situations such as unexpected traffic. On the other hand, a clutch
slip message that appears for no apparent reason is probably due to the clutch
not being adjusted properly or by extreme out-of-trim conditions, thereby not
allowing the control system to be driven correctly.
System Response – the message “CLUTCH SLIP” will flash with amber
illumination. The message is advisory in nature and will not cause a
servo disconnect.
Pilot Action – If this message occurs under conditions other than a
manual servo override, the clutch adjustment should be checked to
ensure it is tight enough to drive the control system under normal
conditions including light to moderate turbulence and normal out of trim
conditions. However, you must assure that it is set loose enough that
the pilot can easily overcome it in an emergency.
3.5.4 Servo CW (or CCW) Limit
This red message indicates the servo crank arm has been
moved to a clockwise or counterclockwise position outside of
its normal range of operation. This error will result in an
immediate servo disconnect. The cause of this error is most
likely a manual system override by the pilot.
System response – immediate servo disconnect
and servo power down. Red SERVO CW (or CCW)
LIMIT message displayed.
Pilot Action – Determine the cause of the SERVO
CW (or CCW) LIMIT message. If not due to pilot
manual override, tighten the servo slip clutch to allow
greater servo control of the elevator system.

10
SERVO
FAULT
3.5.5 Servo Fault
This red message can be due to several factors
based on sensors within the servo and will always
cause an immediate disconnect and power down of
the servo.
System Response - In all cases the servo will be
immediately disconnected from the system, servo
power will be automatically removed and a red error message will be
displayed
Pilot Action - If the SERVO FAULT closely followed an extreme out of
trim condition, CLUTCH SLIP or G FORCE LIMIT alarm , press LCD
switch and continue normal operation. If the cause is unknown, or
occurs in conditions other than described above, perform ground tests of
the system paying particular attention to the wiring from the servo to the
electronics module and the mechanical linkage. If the problem persists,
contact Trio Avionics for assistance.
4.0 System Safety Features
The EZ altitude control system incorporates many safety features to ensure the system
cannot force the airplane into an un-commanded, unsafe flight regime. The following items
are implemented to ensure flight safety.
4.1 Aircraft G-load sensing.The AH module contains an accelerometer interfaced to
the main processor that is used to detect unusual positive or negative flight loads.
Software algorithms prevent unnecessary detection due to turbulence, but allow
shutdown of the servo if the flight loads exceed preset g-force limits. The intent of this
implementation is to prevent aircraft structural failure caused by an un-commanded
excursion of the servo or trim actuators. The fault condition is annunciated on the LCD
switch with the G FORCE LIMIT message
4.2 Servo Electronics monitoring. The servo and trim motor drive circuits are
instrumented and monitored by the servo main processor (SMP). The SMP commands
the magnitude and direction of the servo motor drive output. Any error in the
commanded state of these signals is reported back to the AH module via a digital data
link and results in a SERVO FAULT message on the LCD.
4.3 Clutch Slip Detection.Circuitry and software is provided that detects any slipping of
the safety clutch in the servo. Normally, this condition would only exist in the event the
pilot manually forced the control system into a position that exceeded the commanded
drive position of the servo. This event is reported to the AH module for resolution. The
amber CLUTCH SLIP message is displayed for a momentary slip condition.
4.4 Rotation Limit Detection. Under normal conditions the servo arm moves less than
20 degrees in either direction from the neutral (servo zero) position. If, for any reason
(commanded, un-commanded or pilot manual override), the crank arm transitions
approximately + / - 10 degrees outside of this range servo power is disconnected and a
red error message (CW or CCW LIMIT) is displayed.
4.5 Supervisory processor monitoring. The Servo Main Processor (SMP) is
continuously monitored by an independent supervisory processor to ensure it is
executing its program as designed. This is implemented via a “heartbeat” signal from
the SMP each 10 milliseconds. If for any reason the processor does not provide a

11
“heartbeat” signal to the supervisory processor for a period of 65 milliseconds, the
supervisory processor will unilaterally cut power to the safety disconnect solenoid and
the trim and servo motor drive circuits. The problem will be reported to the pilot with the
red SERVO FAULT message being displayed on the LCD switch
4.6 Servo / Trim Driver Chip Fault Detection. The integrated circuits used to drive
the servo and trim motors are internally equipped to detect and report to the SMP a
variety of fault conditions including:
•High side (supply side) short to ground (low side)
•Low side short to high side
•Under voltage lockout
•Over temperature shutdown
When any of these faults are detected a red SERVO FAULT message is displayed
4.7 Disconnect Solenoid. The servo contains a solenoid that disconnects the servo
gear train whenever power is removed from the solenoid. Power can be removed under
program control of the Servo Main Processor (SMP), the supervisory processor or
whenever power is interrupted by the Electronics Module. With the gear train
disconnected, the elevators are free to move.
4.8 SMP and Supervisory Processor Watchdog Interrupts. Both the SMP and
Electronics Module processors have built in peripherals for detecting an improper cycle
of the software program. If either of these processors enter this condition a watchdog
interrupt will occur which will automatically reset the processor software. This condition
is conveyed to the pilot with the red SERVO FAULT or the amber SYSTEM TEST
message displayed on the LCD switch.
4.9 EZ-2 / EZ-3 additional safety features. The EZ-2 and EZ-3 systems incorporate
an airspeed sensor which adds the capability to disengage the servo if left on during
takeoff and to sense minimum and maximum airspeeds during all phases of flight.
Section 8 describes these features in more detail
5.0 Installing the Altitude Hold Control Module
The control module is embossed with
lettering indicating TOP and RIGHT (looking
forward). It is important to install this module
in this orientation because the gyro uses this
orientation for pitch recognition. Although the
controller may be installed at any convenient
place and need not be in the panel or close
to it, it must be installed in its proper
orientation. Each face of the module has
tapped holes that allow the long rectangular
mounting plate to be attached to any side of
the unit. This will allow for maximum
flexibility in locating and mounting it in the
aircraft.
A static port is provided to allow the control module to access an accurate pressure source.
While it is possible to operate the altitude hold system with the port open to cockpit pressure,
it is highly recommended that it be connected to the aircraft static pressure system or an
independent static port for most reliable operation.

12
If you have an EZ-2 or EZ-3 altitude hold
system, you will also be required to
connect the electronics control module to
your pitot system. This allows the system
to sense airspeed so that it can limit
Minimum Airspeed and Maximum
Airspeed, allow Climb-on-Airspeed, and
enable Pilot Command Steering (PCS) with
airspeed control (see section 8). Note that
the pitot port is closest to the 25 pin DIN
connector.
5.1 Installing the LCD Switch
The LCD switch is mounted in the control panel by cutting a square
hole the size of the LCD switch bezel. The LCD switch is positioned
behind the control panel, with the LCD screen protruding through the
control panel. Several optional bezels are available from Trio to
facilitate this installation. The switch is secured to the control
panel using the two Philips head screws that are inserted
into the switch housing.
5.2 Installing the Encoder Switch
The encoder switch is attached to the control panel by means of a
threaded mounting shaft that protrudes from the front of the switch
housing. Mounting nuts are included that allow the switch to be
mounted in panels of varying thickness. When placing the switch in
the panel, it is important that the shaft extends out sufficiently to
space the knob away from the panel so that the switch can be fully
activated when pressing in on the knob. If the knob is flush with the
panel, it will not operate properly. Allow at least 1/16 inch clearance.
5.4 Installing the Wiring Harness
A quick check of the schematic at the back of this manual will show that the connectors to
both the LCD switch and the ENCODER module are DB9 connectors. It is important to
assure that the DB9 connector that has TWO cables coming into it is connected to the
LCD module, and that the DB9 connector that has one cable connected to it is attached
to the ENCODER module.

13
6.0 Servo Installation Setup
The servo unit incorporates important safety features:
•The internal gears are pulled into the engaged position by an electric solenoid.
When the gears are not engaged, the output crank arm rotates freely and the
elevator controls can be operated normally without friction. When the servo is
engaged, the solenoid pulls the gears into place so the servo has control of the
elevators. Disengaging the servo allows free movement of the elevator controls.
•The servo is engaged and disengaged by pressing the LCD push switch. The servo
is engaged in any mode other than the READY mode. There is also a recommended
remote SERVO DISCONNECT switch on the control stick (or other remote location).
Installation of a remote switch is highly recommended, as it allows an immediate way
to disengage the servo - even in heavy turbulence, when it may be difficult to operate
the LCD button. In addition, such a switch will allow for the PILOT COMMAND
STEERING feature (Section 3.3) and the VS and airspeed capture features (EZ-2 &
EZ-3, see section 8).
•The servo also employs a clutch, which allows the pilot to override the servo by
applying moderate force to the control stick. Even though the solenoid will hold the
gears in place, the clutch will then slip and allow the control surfaces to move. In the
event of strong turbulence, or an altitude anomaly, the pilot can thus override the
servo to control the airplane. In such an instance, the servo should be disengaged
as soon as possible.
NOTE: The clutch function does not rely on a shear pin failure mechanism as is employed on
some other popular autopilot servos. Activation of the “clutch” function in no way damages the
servo drive system although prolonged operation in this condition should be avoided.
6.1 Installing the Servo
Begin by looking for a point on your elevator bell crank, control pushrod or cable where
pushing or pulling the elevator control linkage a distance of 1.5 to 2.4 inches will do the
job. Then find a place to mount the servo nearby to accomplish this by means of the
pushrod. You will mount the servo and pushrod so that the elevator is in a neutral
position when the servo crank arm is at mid position. That’s it, aside from carefully

14
checking that the required range of elevator movement is available within the limits
of the servo travel range, and that no “over center” condition can exist.
The servo crank arm uses a pushrod terminated by rod end bearings to link the servo
arm to the aircraft elevator control system. The pushrod provided in the installation kit
should be trimmed to the correct length for your particular installation. The servo should
be mounted on a solid platform that will not buckle or “oilcan” and attached to a firm
existing support. It is recommended that the servo platform not be mounted to the
aircraft “skin” without a doubler or some other additional support. Rigidity of the servo
mount is critical to proper servo operation. If you do not have the experience
required to fabricate the required bracket please contact Trio Avionics for guidance.
In your installation, it may be more convenient to rotate the crank arm to a new
orientation that will give a neutral (servo center position) at +/- 90 degrees or 180
degrees from that as supplied from the factory. The servo crank arm is secured to a
flange by four machine screws that can be removed for indexing the crank arm in 90
degree increments.
If the screws need to be removed to reposition the crank arm, after repositioning,
LoctiteTM Number 222 must be reapplied (very sparingly) to prevent loosening of
the screws.
Choose an operating radius on the servo crank arm that allows full elevator movement
(elevator stop to elevator stop) without driving the servo crank arm into its limits. Most
aircraft get best performance in the outermost hole. In the event the servo rotation is
insufficient, the servo mechanical stops may be removed. Contact Trio Avionics if this
appears to be necessary.
6.2 Servo Mounting Hardware
Below is the provided electrical and mechanical installation kit. A pushrod is provided,
along with two rod end bearings. Typically, one of these connects to the servo crank arm
and the other is connected to the elevator bell crank. When the servo is connected to the
elevator control system it should be installed so that the servo crank arm is at a right
angle to the control rod. This mechanically centers the servo mechanism to the control
system so that there is equal displacement in either direction when the servo is actuated.
Fine zeroing checks conducted after the installation is complete will verify proper
positioning.
Note: It is important to assure that the proper direction of travel is preserved
when modifying the crank arm orientation. Changing the crank arm mounting by
180 degrees will essentially reverse the direction of travel for the servo arm. In
such a case the EZ1 must be programmed to reverse the drive signal. In the event
unusual pitch changes occur in the first flight, the first check on the ground should
be to be certain the servo direction of travel is correct.

15
Note: A longer elevator crank radius dictates a correspondingly longer radius at the drive end.
The elevators must travel from elevator stop to elevator stop within the range of
movement allowed by the servo stops which limit crank arm rotation.
When the above conditions are met, the system usually performs best when the pushrod is
attached to the outermost hole in the servo crank arm. If your aircraft employs an elevator bell
crank, you should ideally attach the pushrod to the bell crank at a distance from its pivot point
equal to that of the servo crank arm radius (distance from crank arm pivot point to pushrod
attach point).
Again, never allow the servo to limit elevator travel.
6.3 Selecting a Site for the Servo
For most aircraft, it’s relatively easy to find a suitable site for locating the crank arm
servo. The length of the pushrod and, to some extent, the angle it makes with the driven
element are user selectable.
The rod end bearing allows
some misalignment, usually
about 8 degrees, between the
servo pushrod and the plane of
rotation of the crank arm. This
limit on angular displacement
often determines the minimum
pushrod length. Any side-to-
side movement must not jam
the rod end bearing. A suitable
hard point must be found, or
built, for mounting the servo.
The mounting place needs to be
as accessible as possible, and
there must be a means of
linking to the elevator control
system. RV-6 Installation
The mounting place must be strong and rigid. If, for example, you need to mount the
servo on the skin of an airplane, it will be necessary to use additional bracing or a
“doubler” to provide appropriate rigidity. You do not want the push-pull of the servo to
fatigue the metal that holds it.
When mounting the servo, be careful not to drill
mounting holes into critical load bearing members.
It may be best to construct a mounting plate, place
and bond machine screws so that they will
interface with the case mounting holes, and then
secure the assembly into place. For a composite
aircraft installation, the bottom of the plate (shown
above) should be floxed and the holes in the plate
filled with flox before applying fiberglass layers
over it to secure it to the fiberglass structure.
NOTE - It is important that the servo mounting plate surface be flat and smooth. If it is not, this can
distort the servo frame when the servo is secured to the mounting plate.
Usually the servo pushrod will terminate on a control pushrod or a bell crank. If you are
connecting to a pushrod care should be taken to keep the pushrod from being free to
rotate. (To repeat, the pushrod should NOT rotate.) The reasoning for this is that as the
pushrod rotates there is “lost motion” in the system, i.e., movement of the crank arm does
not result in movement of the control system.

16
The control movements are so small that it takes very little slop in the system to
make the airplane not track properly.
It will simplify installation adjustments if there is enough overhead clearance to allow
removal and replacement of the servo lid with the servo remaining in place (for instance,
you will possibly want to adjust the slip clutch). The servo lid is secured by two screws on
the top of the servo.
6.4 Install the Servo Pushrod
Cut the pushrod to the proper length so that, when the servo is at neutral, or centered in
its full rotation stop to stop, the elevator is also neutral (see note).
Choose the longest possible crank arm radius that accommodates a pushrod range of
movement equal to or exceeding that required for full elevator travel. Be sure that the
rod end bearings never jam due to misalignment as the pushrod angle is varied by
different combinations of control system input. Put the control stick (or control
wheel) in all four corners to test this.
When attaching the servo pushrod to an elevator bell crank, it is important to keep the
two lever arms equal. Measure the distance from the servo crank arm pivot point to the
outermost hole in the crank arm. Then drill an attach point in the elevator bell crank that
is the same distance from its pivot point. This will assure proper servo operation.
6.5 Setting Servo Override Force (Slip Clutch)
t
Note: The crank arm neutral position for your elevator control system will be dependent on
the particular aircraft design. Many designs require more throw of the control system from the
neutral elevator position to the full stick back position (elevator up) than the other direction.
In this case when the elevators are positioned at their neutral position , the crank arm will not
be at it’s centered (exact vertical or horizontal) position. This is not of concern during
operation of the system as the servo design compensates for this offset automatically during
operation. Again, the important thing to remember is that the elevator control system must
contact its mechanical sto
p
s before the servo contacts it’s mechanical sto
p
s

17
The servo Torque Control nut (the adjustment nut inside the servo on the output shaft)
sets the override force - the force you will feel at the stick when the servo clutch begins to
slip.
Engage the servo by pressing the LCD switch. You should hear the solenoid operate
inside the servo housing and the servo crank arm should become firmly held in place by
the gear train. Then push the control stick hard enough to override the servo. Using an
11/16 “ or 17mm open end wrench set the override force to a value that seems strong
enough to give a fairly good pitch authority, but not so strong as to be difficult to override
with the control stick. Work toward setting the servo slip clutch to the minimum torque
necessary to give enough elevator authority to handle a reasonable amount of turbulence
or trim error.
6.6 Adjustment of Servo Rotation Direction, Trim Rotation Direction
(optional) and Factor Default Setting restore.
After installation wiring is complete the system servo direction check must be
accomplished.
IMPORTANT – Prior to performing step 6.6.1 the system must be powered up and
placed in the READY mode for a full 5 minute period to allow the gyro and
accelerometers to bias to their zero position. During this time the aircraft must remain
perfectly still. After the 5 minute period has elapsed secure power to the EZ altitude
control system and perform step 6.6.1
6.6.1 Servo Direction Setting - The servo direction must be set so that the
system knows which way to drive the controls for an increase or decrease in
altitude. This is a one time ground setting and should never be attempted in
flight.
Do the following to enter the servo direction setting mode:
Turn on power to the system.
While the SYSTEM TEST message is being displayed, simultaneously press and
release both the LCD switch and the ENCODER switch – The LCD switch will
now display the amber SERVO DIR NORM or SERVO DIR REV message.
a. Rotate the ENCODER knob clockwise while observing the elevator
travel direction. The elevators should move in a direction that would
cause an increase in altitude.
b. If the elevators drive in the opposite direction momentarily press the
ENCODER switch. The LCD message will now read SERVO DIR REV.
Repeat step “a” above and verify correct elevator directional control is
achieved.
NOTE: At this point the servo will engage and drive the servo to its mechanical zero
position.
NOTE: This is a CRITICAL setting and MUST be verified before flight. If the
command to the servo motor is not correct the aircraft will be forced into a divergent
climb or dive when the system is engaged.

18
GAIN
SET
40
Pressing the LCD switch will advance to the TRIM DIRECTION screen if
the system has the AUTO TRIM option installed
6.6.2 Setting the Trim Motor Direction – This procedure is only available
on models equipped with the auto-trim option.
When in this mode, the LCD message will be amber and read “TRIM DIR NORM”
or “TRIM DIR REV”. You should verify that when the ENCODER is rotated in a
CLOCKWISE direction the trim system is moved so as to make the airplane
CLIMB. If this is not the case, momentarily press the ENCODER switch to
reverse the sense of the command to the trim motor.
Pressing the LCD switch will advance to the RESTORE FACTORY DEFAULTS
screen.
6.6.3 Restore Factory Defaults Procedure - The display will now be
amber and display “RESTOR DEFLTS”. If you want to return all internal gains
and variables to the factory settings perform the following steps, otherwise press
the LCD switch momentarily an proceed to step 7.0
The display will now be amber and display “RESTOR DEFLTS”. To activate the
restoration, once again press and hold the ENCODER switch followed by
pressing and holding the LCD switch. The display will change from a steady
amber color to a flashing green color. Continue to hold the two switches for
approximately 10 seconds until the flashing green screen turns to a steady green
screen. Once this has occurred restoration of the factory settings is complete.
To advance to step 7.0, press the LCD switch momentarily.
NOTE. Releasing either switch during the flashing green display will cause the
restoration to be inhibited. If this occurs, simply recycle power to the system and
start the procedure again at step 6.6.1
7.0 SYSTEM GAIN and SERVO DEADBAND Adjustment
The System Gain and Servo Deadband Settings optimize the EZ altitude control system
tracking performance for your individual airplane
7.1 SYSTEM GAIN
The system gain adjustment allows the EZ altitude control system to be tailored to your
individual airplane. The factory setting is a nominal value which should give good
performance in most airplanes. However, to achieve best performance in your airplane
the SYSTEM GAIN adjustment should be optimized.
To optimize the gain setting in your airplane, perform the following steps:
a. Enter the ALTITUDE HOLD mode in smooth air at
your normal cruise speed after verifying the pitch
trim is properly adjusted for level flight.
b. Press the ENCODER knob for more than 3 seconds
until the SYSTEM GAIN setting is displayed.
c. Execute a turn at a bank angle of approximately 15

19
SERVO
DBAND
6
degrees. If the altitude sags more than 30 feet after entering the turn the
system gain needs to be increased. Perform step d.
d. Increase the SYSTEM GAIN by 5 units, then repeat step c.
7.2 SERVO DEADBAND
The SERVO DEADBAND adjustment optimizes servo performance for your particular
installation. The “deadband” is an area in the servo rotation where drive signals are
momentarily nulled to prevent unnecessary hunting and / or oscillation of the servo
mechanism. The lowest setting that gives satisfactory performance is the optimum
setting. The factory setting is a nominal value which should give good performance in
most airplanes. However, to achieve best performance in your airplane the SERVO
DEADBAND adjustment should be optimized.
To optimize the servo deadband setting in your airplane perform the following
steps:
a. Enter the ALTITUDE HOLD mode in smooth air
at your normal cruise speed after verifying the
pitch trim is properly adjusted for level flight.
b. Press the ENCODER knob for more than 3
seconds until the SYSTEM GAIN setting is
displayed.
c. Press the ENCODER knob several more times until the SERVO DBAND
message is displayed
d. Decrease the deadband setting by slowly rotating the ENCODER knob
counterclockwise until jitter or bumping is experienced in the control stick.
e. Rotate the encoder clockwise until the jitter or bumping just stops. This is the
optimum gain setting for your installation.
NOTE – A SERVO DEADBAND setting of between 3 and 6 has proven to be optimum in
several aircraft used for flight evaluation. Your settings should be similar
NOTE: This gain setting is for smooth air tracking. If you enter turbulent conditions and the
altitude excursions are more than what you will accept, you may increase the gain (clockwise
rotation) to limit the altitude excursion. A setting of between 40 and 60 has been shown to
be optimum for most aircraft tested during flight evaluation. Your settings should be similar.

20
VS
SET
500
VS
SET
400
VS
400
VS
SET
0
8.0 The EZ-2 / EZ-3 ALTITUDE CONTROL SYSTEMS with Climb and
Descent capability.
Section 8 describes the additional features of the EZ-2 systems. The EZ-2 and EZ-3 altitude
control system incorporates all of the features of the EZ-1 while adding several additional
capabilities and safety features.
•A major safety feature of the EZ-2 and EZ-3 system is its ability to prevent the system
from stalling or over speeding the aircraft. To facilitate this, the electronic module
contains an airspeed sensor, which must be connected to the aircraft pitot system.
•Another safety feature is autopilot disconnect on take off. The autopilot will automatically
disconnect at an airspeed below 50 kts IAS - if inadvertently left on during takeoff.
•Vertical climbs and descents may be performed by setting the desired vertical rate via the
encoder knob and LCD switch.
•Pilot Command Steering (PCS) allows the pilot to press the remote disconnect switch to
fly the aircraft manually to establish a desired climb or descent rate and (when the remote
disconnect button is released) the aircraft will hold that vertical rate.
•Alternatively, the pilot may choose– via a setup menu – to have the PCS mode climb and
descend on airspeed (instead of vertical speed). This will allow the ability to maintain a
specific airspeed during climb or descent to help maintain proper engine temperature.
8.1 EZ-2, EZ-3 Operation
8.1.1 VS Mode
To enter a vertical climb or descent rate, momentarily press the
encoder button until the VS set selection screen is present on the
LCD switch. The screen color will change to amber and display
the message shown. This screen may be used to set the desired
vertical speed regardless of whether the system is in the “ALT
HOLD” or in the “READY” mode.
If the LCD switch is pressed while the VS SET 0 screen is active,
or the vertical rate is set to zero while the VS mode is active, the
system will capture and hold the current altitude.
Rotating the encoder knob while the VS set selection screen is
active will change the vertical speed increment (VSI) on the
screen in 100 foot per minute intervals – to a maximum setting of
2,000 feet per minute. Rotating the knob clockwise will indicate
that a climb rate is being input. Rotating the knob
counterclockwise will indicate that a descent is being entered.
Once the desired vertical rate has been entered, the pilot must
press the LCD switch to begin the climb or descent. If the
display was in the “READY” mode (system not engaged),
pressing the LCD switch will engage the servo and the climb or
descent will begin. If the display is in the “ALT HOLD”mode
when vertical speed is selected, it will begin to execute the climb
or descent rate once the LCD switch is pressed. If the VS SET 0
screen is active when the LCD is pressed the system will hold the
current altitude.
When the LCD switch is pressed, the color of the screen changes to green and displays a
“VS ACT” (Vertical Speed Active) message. Once the aircraft is climbing or descending
Table of contents
Other Trio Avionics Avionic Display manuals
Popular Avionic Display manuals by other brands
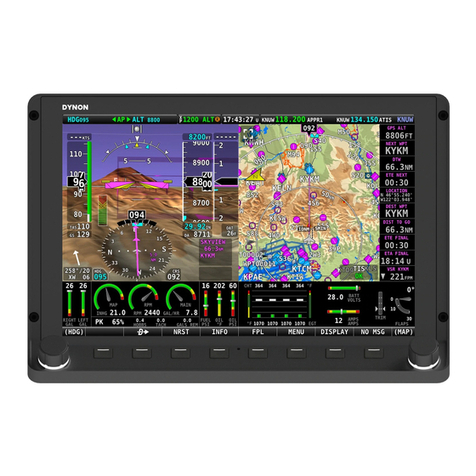
Dynon Avionics
Dynon Avionics SkyView HDX Configuration manual
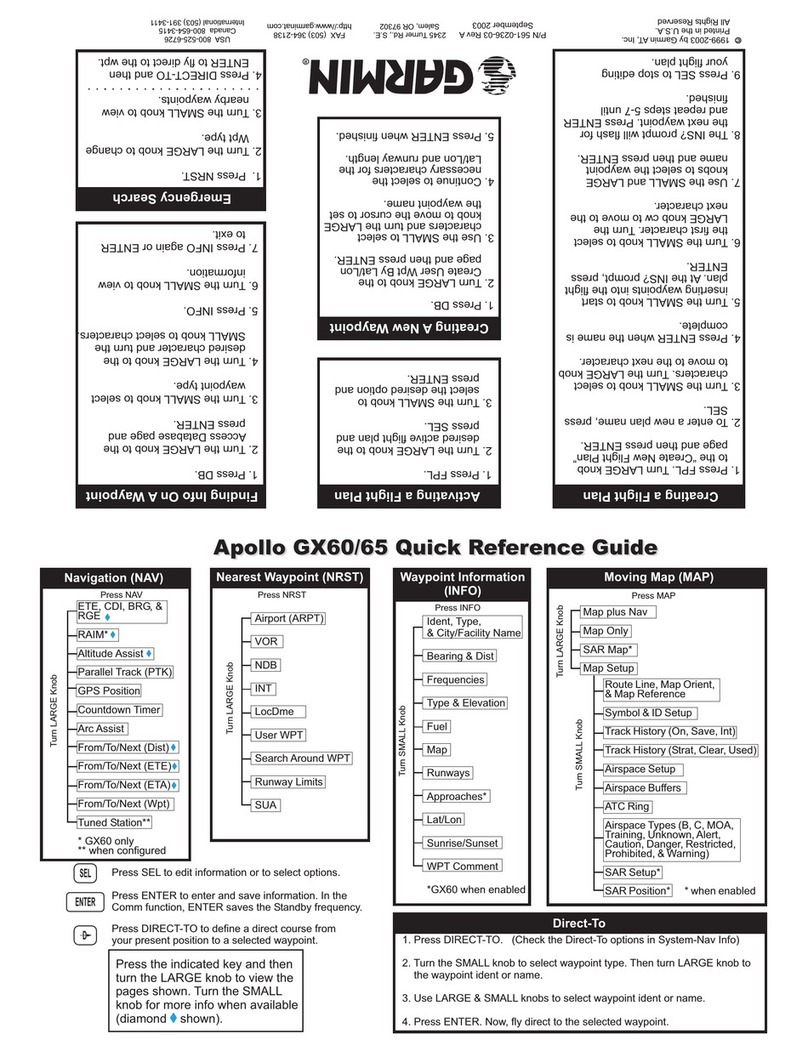
Garmin
Garmin APOLLO GX60 Quick reference guide
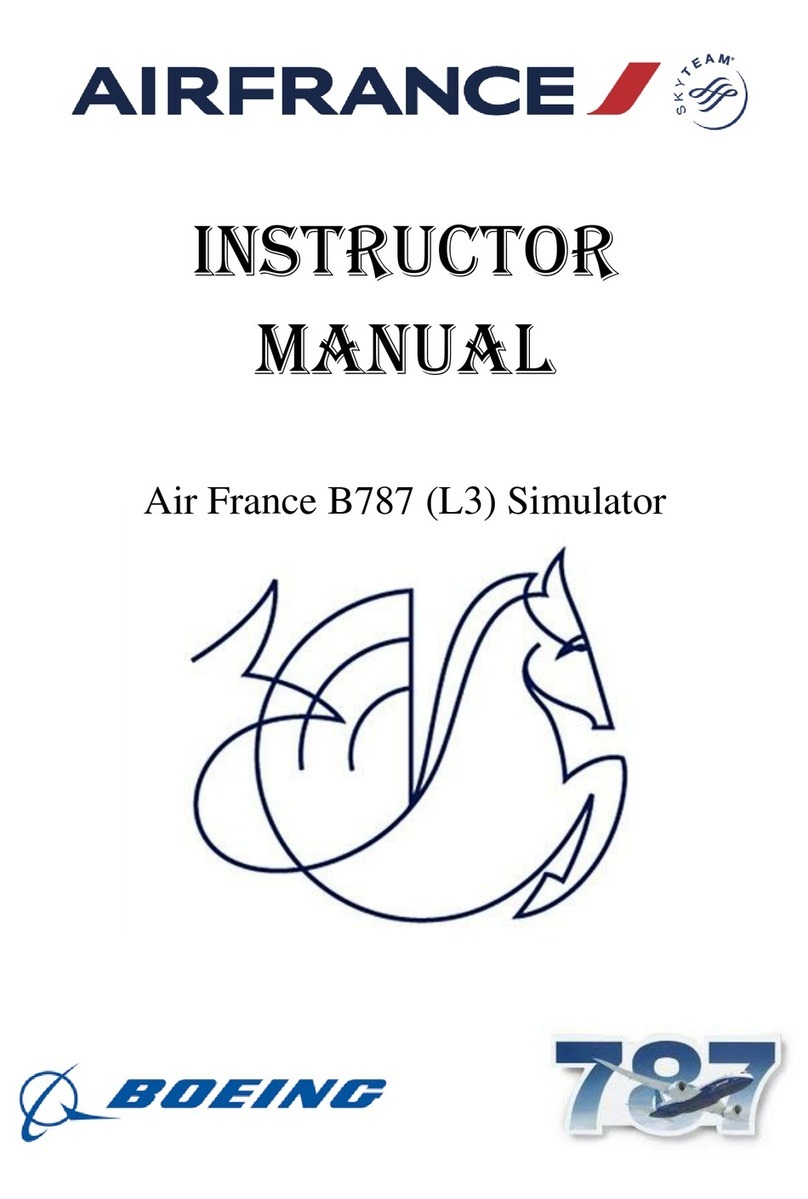
L3 Aviation Products
L3 Aviation Products B787 Flight Simulator Instructor's manual

Honeywell
Honeywell Bendix/King KMD 550 Pilot's guide addendum
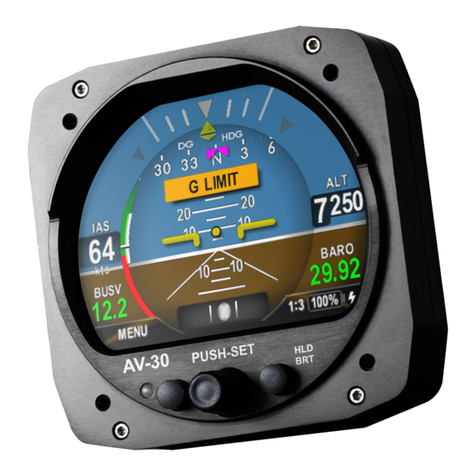
uAvionix
uAvionix AV-30 Service bulletin
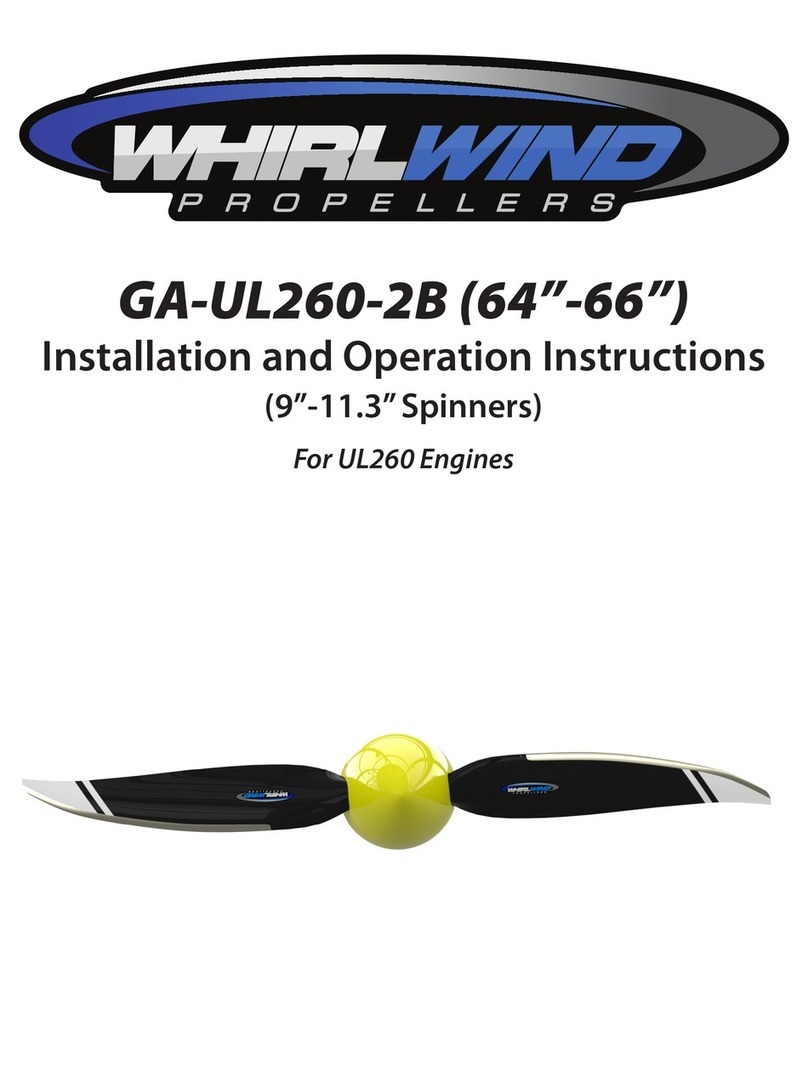
Whirlwind
Whirlwind GA-UL260-2B Installation and operation instructions