Tritech TES-PU20V User manual

Page 1-1 Rev. 0
USERS’ MANUAL
Model TES-PU-20/26V
Uplift pressure measuring system
Doc. # WI 6002.14
Rev. 0
Printed 10/11/98

Page 1-1 Rev. 0
1. Introduction
TRITECH uplift pressure measurement is a precision instrumentation system designed to help civil engi-
neers in the measurement of uplift pressure in the foundation of a concrete dam. It forms an important
part of dam instrumentation. Seepage water from the reservoir area often seeps into the dam founda-
tion and the down stream side. The study of uplift pressure has the following main purposes:
To determine the magnitude of any hydraulic pressure that may be present at the base of a dam
due to percolation or seepage of water along underlying foundation seams or joint systems after
the reservoir is filled. To release this pressure, if necessary.
To monitor seepage water from the reservoir area into the dam foundation in view of the safety of
the dam structure.
To monitor the effectiveness of the drainage system below the dam.
To study the effectiveness of foundation grouting.
1.1. Typical installation in a concrete dam
Figure 1.1
1.2. Uplif t pressure measurement
The uplift pressure is measured mechanically by using a Bourden pressure gage or electronically by
using a vibrating wire uplift pressure meter and a digital vibrating wire indicator. The uplift pressure
measuring device consists of a perforated/non-perforated pipe of 50mm to 63mm φof adequate
strength. The pipe is inserted in a drilled hole in the foundation from the instrumentation gallery to a
depth upto the required location. The other end of the pipe is brought into the gallery where it is con-
nected to an uplift pressure meter or a Bourden pressure gage.
1.2.1. Mechanical method
The mechanical uplift pressure meter incorporating the Bourdon type pressure gage can be conven-
iently fixed to the uplift pressure pipe in the gallery. The installation of the mechanical system is very
easy and requires no cable jointing and special orientation.

Users’ Manual Uplift pressure measurement system
Page 1-2 Rev. 0
Mechanical measurement is economical. However, one has to go into the gallery to take the readings.
It should also be noted that the vibrating wire uplift pressure meter is a much more reliable device than
a Bourden type pressure gage and has a better resolution and accuracy.
1.2.2. Electronic met h o d
The development of vibrating wire sensor introduced a reliable and fast method of taking uplift pres-
sure readings electrically. This enables remote reading as well as data storing in case the output is
connected to a data acquisition system. The cable is carried from the sensor tip to the read-out unit or
data logger and is protected against any possible damage during construction. For details of vibrating
wire sensors and other vibrating wire instruments manufactured by TRITECH, refer to data sheet
1087-99w.
The electronic uplift pressure meter is installed with the necessary length of cable jointed with it. Prop-
er junction boxes are available to take the signals to any distant location through multi core cables. The
mounting is very simple as the meter is surface mounted and does not require to be embedded.
1.3. Conventio n s u sed in this manual
WARNING! Warning messages calls attention to a procedure or practice, that if not properly followed
could possibly cause personal injury.
CAUTION: Caution messages calls attention to a procedure or practice, that if not properly followed
may result in loss of data or damage to equipment.
NOTE: Note contains important information & is set off from regular text to draw users’ attention.
The user’s manual is intended to provide sufficient information for making optimum use of uplift pres-
sure measurement assembly in your applications. It covers description of the vibrating wire uplift pres-
sure meter and its accessories, procedure for installation & maintenance of the sensor, method of tak-
ing observations and recording data. The description of the mechanical system is also covered.
To make this manual more useful we invite your valuable comments and suggestions regarding any
additions or enhancements. We also request you to please let us know of any errors that you may find
while going through this manual.
1.4. How to use this manual
This manual is divided into a number of sections, each section containing a specific type of information.
The list given below tells you where to look for in this manual if you need some specific information. It is
however recommended that you read the manual from the beginning to the end to get a thorough grasp
of the subject. You will find lots of unexpected information in the sections you feel you may skip.
For measurement by Bourden gage: See § 2 ‘Mechanical measurement’
For understanding principle of vibrating wire uplift pressure meter: See § 3.2.2. ‘Operating principle’.
For installation of VW system: See § 5 ‘Installation of vibrating wire system’.

Page 2-1 Rev. 0
2. Mechanical Measurement
A system of piping is installed at several sta-
tions in the dam in the first lift just above the
contact between the foundation rock and the
base of the dam. The pipes extend into one
or more of the lower galleries in the dam. Al-
ternatively, holes may be drilled from the gal-
lery down to the level upto which the drain
pipes have to be installed. Drain pipes extend
below the dam, both on the upstream and
downstream side.
The mechanical assembly to be installed at
the top of these drain pipes is detailed in fig-
ure 2.1 and the following table:
Sl. Description Qty.
1 Reducer (2”x1”) 1
2 1” GI pipe (350 mm) 1
3 Reducer (1”x ½”) 1
4 ½” tee 1
5 ½” Male nipple (50 mm) 2
6 ½” Male nipple (150 mm) 1
7 ½” Wheel valve-10 kg/cm
2
(Zalota/Hawa)
1
8 ½” GI Socket 1
9 Brass hex. gage adopter 1
10 Teflon washer 1
11 Dial pressure gage 1
The installation is very simple and does not
need a detailed description.
2.1. Tools & accessories
The following tools and accessories are re-
quired for proper installation of the uplift
pressure measurement system:
2.1.1 Spanner 23/25 and 30/32 (Taparia)
2.1.2 Pipe wrench (30 cm)
2.1.3 Teflon tape (10 mm)
2.1.4 Thread sealant (Loctite 577)
2.1.5 Acetone (commercial)
2.1.6 Hacksaw with 300 mm blade
2.1.7 Pliers 160 mm (Taparia)
2.1.8 Waste paper basket
2.1.9 Cloth for cleaning (lintless)
Figure 2.1

Page 3-1 Rev. 0
3. Electronic measurement
3.1. General system description
The uplift pressure meter is designed to measure uplift
pressure in the foundation of the dam. The vibrating wire
uplift pressure meter is fitted on the pipe coming in to the
instrumentation gallery from the foundation rock. Refer to
figure 3.1 and the table on this page.
The uplift pressure measuring device consists of a vibrat-
ing wire uplift pressure meter and a perforated/non-
perforated pipe of 50mm to 63mm φwith adequate
strength and connecting accessories. A system of piping is
installed at several stations in the dam in the first lift just
above the contact between the foundation rock and the
base of the dam. The pipes extend into one or more of the
lower galleries in the dam. Alternatively, holes may be
drilled from the gallery down to the level upto which the
drain pipes have to be installed. Drain pipes extend below
the dam, both on the upstream and downstream side. The
other end of the pipe is brought into the gallery where it is
connected to an uplift pressure meter through other acces-
sories listed below.
Sl. Description Qty.
1 Reducer (2”x1”) 1
2 1” GI pipe (350 mm) 1
3 Reducer (1”x ½”) 1
4 ½” Tee 1
5 ½” Male nipple (50 mm) 2
6 ½” Male nipple (150 mm) 1
7 ½” wheel valve-10 kg/cm
2
(Zalota/Hawa)
1
8 ½” socket (GI) 1
9 VW sensor 1
10 Adopter 1
11 Cable gland NG 16 1
12 Cable joint holder 1
The uplift pressure meter helps to accurately measure the
uplift pressure at various locations in the foundation of the
dam. Sharp increase in uplift pressure is interpreted as
failure of the foundation grouting or improper drainage sys-
tem. Being surface mounted, it is easy to install and re-
quires no special orientation.
NOTE: The ½” Tee (sl. # 4) may be repositioned if it is convenient to install the sensor horizontally.
Figure 3.1

Users’ Manual Uplift pressure measurement system
Page 3-2 Rev. 0
3.2. Vib rating wire pressure senso r
The heart of the electronic measurement is the TRITECH model TES-PU-20/26V vibrating wire pressure
sensor. The TRITECH vibrating wire sensor is the electrical sensor of choice as its frequency output is
immune to external noise & the output signal can be transmitted to long distances. It is able to tolerate wet
wiring common in geotechnical applications.
3.2.1. Manufactu ring range
ITEM MODEL CAPACITY
DESCRIPTION
Uplift pressure
meter
TES-PU-
20V
TES-PU-
21V
TES-PU-
22V
TES-PU-
23V
TES-PU-
24V
TES-PU-
25V
TES-PU-
26V
kg/cm
2
3
5
10
20
35
50
specify
The uplift pressure meter is suitable for monitoring the
uplift pressure of water in the found
ation of the dam and
the stability of foundations of embankments in dams,
tunnels and other underground works. The pres
sure
gage is fitted on the pipe coming into the instrumenta-
tion gallery from foundation rock. A ½” BSP adopter is
provided for the pipe connection. The adopter is in-
stalled on top of an uplift pressure meter. The height
from the bottom of the uplift pipe to where the meter is
mounted, should be added to the reading of the meter
to get the correct pressure at the bottom of the uplift
pipe.
3.2.2. Operating princip le
The vibrating wire pressure sensor basically consists of a magnetic, high tensile strength stretched wire,
one end of which is anchored and the other end fixed to a diaphragm which deflects in some proportion to
the applied pressure. Any change in hydrostatic pressure, deflects the diaphragm proportionally and this in
turn affects the tension in the stretched wire. Thus any change in uplift pressure, directly affects the ten-
sion in the wire.
The wire is plucked by a coil magnet. Proportionate to the tension in the wire, it resonates at a frequency
‘f’, which can be determined as follows:
f = [σ
σσ
σg/ρ
ρρ
ρ]
1/2
/ 2l Hz
where:
σ = tension of wire in kg/cm
2
g = 980 cm/sec
2
ρ= density of wire in kg/cm
3
l = length of wire in cm
The length of the wire in the uplift pressure meter is 5.5 cm. Consequently the formula can
be reduced to:
f = 32 [σ
σσ
σ]
1/2
Hz
The resonant frequency with which the wire vibrates, induces an alternating current in the coil magnet.
This is read by the read out unit.

Uplift pressure measuring system Users’ Manual
Rev. 0 Page 3-3
Summarizing, any variation in hydraulic pressure causes the diaphragm to deflect. This changes the ten-
sion in the wire thus affecting the frequency of vibration. Uplift pressure is proportional to the square of the
frequency and the read out unit is able to display this directly in engineering units.
3.2.3. Specificatio n s
Type: Vibrating wire
Model: TES-PU-20/21/22/23/24/25/26V
Range (kg/cm
2
): 3, 5,10,20,35,50, specify
Accuracy: ±1 % fs; (non linearity + hysteresis + repeatability)
Temperature limit
Operational: -20 to 70
o
C
Compensated: 0 to 55
o
C
Over range limit: 150 % of range
Over range effect: ±0.1% fs upto 150%
Enclosure: Stainless steel, IP-68 enclosure
Read out: Portable vibrating wire indicator
Thermistor: YSI 44005 or equivalent (3,000 Ohm at 25
o
C)
3.2.4. Description
The uplift pressure meter is manufactured in various capacities. Each transducer is provided with a ther-
mistor for making correction due to temperature induced frequency changes and the correlating data for
this is provided in the test report (see § 3.5). Thermistor may also be used to monitor the temperature.
A tripolar plasma surge arrestor inside the transducer housing protects the vibrating wire pluck and read
coils from electrical transients such as may be induced by direct or indirect lightning strikes.
3.2.4.1. Stainless steel body
The vibrating wire and coil magnet assembly is enclosed in a stainless steel body which is electron beam
welded to the diaphragm. This results in a vacuum of 1/1000 torr inside the sensor resulting in it becoming
immune to the effect of any ingress of water. As the uplift pressure meter is of stainless steel construction,
it is not affected by normal chemical corrosion at locations in which it is used. Once properly installed, it is
almost maintenance free.
Figure 3.2
3.2.4.2. Adopter
A ½” BSP adopter is provided for the pipe connection. The water oozing through internal pores or seams
in rock formations of dam foundations, mass concrete of structures, foundation soil of structures, re-
claimed land soil etc. percolates upward through the pipe to actuate the diaphragm.

Users’ Manual Uplift pressure measurement system
Page 3-4 Rev. 0
3.2.4.3. Cable connection:
The leads from the coil magnet are terminated on a glass to metal seal which is integrally electron beam
welded to the stainless steel body of the uplift pressure meter. The two pins marked red and black are
connected to the coil magnet. The other two pins are free and may be used in case a thermister is re-
quired for measurement of temperature. A cable joint housing and cable gland is provided for the cable
connection. For cable jointing, refer to Users Manual 6002.11/Rev 03/98.
3.3. Taking readings with the model TES-DI- 51V vibratin g wire indicator
The model TES-DI-51V vibrating wire indicator is a microprocessor based read-out unit for use with
TRITECH’s range of vibrating wire transducers. It can display the measured frequency in terms of time
period, frequency, frequency squared or the value of the measured parameter directly in proper engineer-
ing units.
The TES-DI-51V indicator can store calibration coefficients of up to 100 vibrating wire transducers so that
the value of the measured parameter from these transducers can be shown directly in proper engineering
units.
The indicator has an internal non-volatile memory with sufficient capacity to store about 720 readings from
any of the 100 programmed transducers in any combination. You can store either 720 readings from any
one transducer or 7 sets of readings from all 100 transducers. Each reading is stamped with the date and
time the measurement was taken.
The calibration coefficients are given in the individual TEST CERTIFICATE provided with each trans-
ducer. Refer to the model TES-DI-51V instruction manual WI-6002.26 for entering the transducer calibra-
tion coefficients. The gage factor and the factory zero reading (frequency) can directly be taken from the
test certificate for setting up transducer coefficients in the read-out unit.
The test certificate also gives the factory zero reading in frequency
2
for use with transducers provided with
polynomial linearity correction. For polynomial linearity correction pressure is calculated by the following
equation:
P = A(R1)² + B(R1)² + C (kg/cm²)
P = pressure in engineering unit
R1 = current reading in digits during observation
A, B, C = polynomial constants
The polynomial constants are stored in the model TES-DI-51V memory to give linearity corrected data of
the parameter in engineering units. For more details refer to the instruction manual WI-6002.26 of the
model TES-DI-51V
For transducers with a built in interchangeable thermistor, the model TES-DI-51V can also display and
record the temperature of the transducer directly in degree Centigrade. All TRITECH vibrating wire sen-
sors, excepting the temperature sensors have a thermistor incorporated in them for temperature meas-
urement.
The stored readings can either be uploaded to a host computer using the serial interface or can be printed
out on any text printer equipped with a RS-232C serial communications interface. The setup information
(calibration coefficients) for all the channels can also be printed out for verification.
An internal 6V rechargeable sealed maintenance free battery is used to provide power to the indicator. A
fully charged new battery provides nearly 60 hours of operation on a single charge. A separate battery
charger is provided with the TES-DI-51V indicator to charge the internal battery from 230 V AC mains.

Uplift pressure measuring system Users’ Manual
Rev. 0 Page 3-5
The TES-DI- 51V indicator is housed in a splash proof resin molded enclosure with weatherproof con-
nectors for making connections to the vibrating wire transducer and the battery charger.

Users’ Manual Uplift pressure measurement system
Page 3-6 Rev. 0
3.4. Sam p le test cert ificate
TEST CERTIFICATE
DWT Traceable to standard no.: NPL 1285/09/138/93
Instrument Uplift pressure meter Date January 1, 1998
S. no. 1722
Temperature 14
o
C
Capacity 5.0 kg/cm
2
Atm. Pressure 75.5 cm Hg
Input f ²
Pressure Observed value Average End point fit Deviation
kg/cm² UP I UP II
x 10
3
x 10
3
x 10
3
x 10
3
0.0 6925 6925 6925 6925 0
1.0 6625 6625 6625 6630 5
2.0 6335 6335 6335 6336 0
3.0 6037 6037 6037 6041 4
4.0 5743 5743 5743 5746 4
5.0 5451 5451 5451 5451 0
Non linearity: 0.34 % fs
Gage factor: 2.375E-02 kg/cm² /f
2
Temperature
zero shift (C)
+ 0.023 %/°C fsd
Read ings at the time of shipmen t
Date
Mar 7,1998
Factory zero reading f
f
2
2630 Hz
6917 x 10
3
Hz
2
Temperature
32°C
Thermistor
2190 Ohm
Atm. Pressure
74.1cm Hg
Coil resistance
130 Ohm
(The user is advised to establish zero conditions in the field by recording the reading at a known tem-
perature and barometric pressure)
Pin configuration/wiring code:
Red & black: signal
Green & white: thermistor
Checked by
Tested by

Uplift pressure measuring system Users’ Manual
Rev. 0 Page 3-7
3.5. Thermist or - t emperature resist ance correlation
Thermist or type: Dale 1C3001-B3
Temperature resistance equat ion
T = 1/[A + B(LnR) + C(LnR)
3
] - 273.2
o
C
T = temperature in
o
C
LnR = Natural log of thermistor resistance
A = 1.4051 x 10
-3
B = 2.369 x 10
-4
C = 1.019 x 10
-7
Ohm Temp.
o
C Ohm Temp.
o
C Ohm Temp.
o
C
201.1k -50 16.60K -10 2417 +30
187.3K -49 15.72K -9 2317 31
174.5K -48 14.90K -8 2221 32
162.7K -47 14.12K -7 2130 33
151.7K -46 13.39k -6 2042 34
141.6K -45 12.70K -5 1959 35
132.2K -44 12.05K -4 1880 36
123.5K -43 11.44K -3 1805 37
115.4K -12 10.86K -2 1733 38
107.9K -41 10.31K -1 1664 39
101.0K -40 9796 0 1598 40
94.48K -39 9310 +1 1535 41
88.46K -38 8851 2 1475 42
82.87K -37 8417 3 1418 43
77.66K -36 8006 4 1363 44
72.81K -35 7618 5 1310 45
68.30K -34 7252 6 1260 46
64.09K -33 6905 7 1212 47
60.17K -32 6576 8 1167 48
56.51K -31 6265 9 1123 49
53.10K -30 5971 10 1081 50
49.91K -29 5692 11 1040 51
46.94K -28 5427 12 1002 52
44.16K -27 5177 13 965.0 53
41.56k -26 4939 14 929. 6 54
39.13K -25 4714 15 895.8 55
36.86K -24 4500 16 863.3 56
34.73K -23 4297 17 832.2 57
32.74K -22 4105 18 802.3 58
30.87K -21 3922 19 773.7 59
29.13K -20 3748 20 746.3 60
27.49K -19 3583 21 719.9 61
25.95K -18 3426 22 694.7 62
24.51K -17 3277 23 670.4 63
23.16K -16 3135 24 647.1 64
21.89K -15 3000 25 624.7 65
20.70K -14 2872 26 603.3 66
19.58K -13 2750 27 582.6 67
18.52K -12 2633 28 562.8 68
17.53K -11 2523 29 525.4 70

Page 4-1 Rev. 0
4. Tools & accessories required for installation of vw system
The following tools and accessories are required for proper cable jointing and installation of the vibrat-
ing wire uplift pressure meter (also refer users manual on cable jointing - 6002.11/Rev02/96):
4.1 Soldering iron 25 watt (Solder on 5102 - Vimla Engineering, Bombay)
4.2 Rosin 63/37 solder wire RF-3C, 30 swg (Arrow, Delhi)
4.3 Thread sealant (Loctite 577).
4.4 Cable jointing compound (MS 853 and hardener MSH 283 - Mahendra Engineering & Chemi-
cal Products Ltd.)
4.5 Acetone (commercial).
4.6 Spanner 23/25 and 30/32 (Taparia)
4.7 Cable joint housing (refer figure 3.2)
4.8 Hacksaw with 300 mm blade
4.9 Cable Cutter
4.10 Surgical blade with holder
4.11 Wire Stripper (Taparia).
4.12 Pliers 160 mm (Taparia).
4.13 Locking nut spanner
4.14 Pouring funnel.
4.15 Stainless steel rod 6 mm φ150 mm length
4.16 Spatula
4.17 Rotary tin cutter
4.18 Fixture for jointing upto six uplift pressure meters (refer figure 4.1)
4.19 Tooth brush
4.20 Waste paper basket
4.21 Cloth for cleaning (lintless)
4.22 Wooden cable spacer
4.23 Wooden cable rake
4.24 Cotton cloth bag (200 mm x 250 mm) with integral tying string to contain the piezometer
4.25 Coarse brass wire mesh and tie wire
4.26 Digital multimeter
4.27 Portable pressure indicator (TES-DI-51V)
4.28 Pipe wrench (30 cm)
Figure 4.1

Page 5-1 Rev. 0
5. Installation of vibrating w ire system
The typical layout for the uplift pressure pipe with its connecting fixtures and vibrating wire uplift pres-
sure meter is illustrated in figures 1.1 and figure 3.1 respectively.
A system of piping is installed at several stations in the dam in the first lift just above the contact be-
tween the foundation rock and the base of the dam. Drill holes with installed drainpipes extend below
the dam, both upstream and downstream of the grout curtain. The pipes extend into one or more of
the lower galleries in the dam.
The pipes are fitted with a tee-section and a vibrating wire uplift pressure meter for observing water
pressure. A shutoff valve is included on one leg of the tee. Although readings may be taken at any
time, it is common practice to leave the shut-off valve open and to close the system the day before
readings are to be taken. Then after readings are taken, the valve is reopened. Therefore in addition
to the existing uplift pressures, readings taken in this manner indicate the uplift pressure that may be
achieved if one or more systems of drains should become inoperative through blockage. The shut-off
valve may also be kept closed and opened only when the uplift pressure builds up.
5.1. Preparation of the senso r before installation
5.1.1 Remove the cable joint housing from the sensor. This gives access to the four pin terminal.
Two of the terminals are marked with red and black colors. These are internally wired to the
coil of the magnet assembly inside the sensor. The other two terminals are utilized in case a
thermistor is used for temperature measurement. Clean the terminals with a tooth brush.
NOTE: Do not use any acetone for cleaning the terminals as it may damage the glass to metal
seal. Acetone should be used to clean the other portions of the sensor.
5.1.2 Check the working of the sensor as follows:
The coil resistance measured by a digital multimeter between the red and black pins, should lie
between 120-140 Ohm. In case thermistor is used, determine resistance at the room temperature
from thermistor temperature resistance chart in § 3.5. This resistance should be equal to that be-
tween pins marked green and white. For example, in case the room temperature is 25
o
C, this re-
sistance would be 3,000 Ohm.
The resistance between any lead and the protective armour should be > 500 m Ohm.
Connect the sensor to the TRITECH model TES-DI-51V portable readout unit and switch it on. The
display will show something like:
Freq: 2629.8 Hz
where the actual figure will vary depending on the transducer connected to the indicator.
For the uplift pressure meter, the initial reading (offset) in frequency should lie between 2,250 -
2,650 Hz. This initial reading on the portable readout unit should be stable.
Check whether sensor is responding to changes in pressure. A crude but a simple and very effec-
tive method of checking whether the sensor is responding to changes in pressure is as follows:
•Connect sensor to the portable readout unit and remove ½” BSP adapter from the meter.
•Press diaphragm with thumb and verify that frequency reading on the indicator decreases.
•This change in reading ensures that the deformation produced by the pressure of the
thumb on the diaphragm is transmitted to the vibrating wire sensing element.
Shift the read-out unit display to the frequency
2
mode. Each sensor is provided with a test certifi-
cate giving relationship between applied pressure and output. The zero reading in frequency
2
given
in the test certificate should not differ from the current zero reading by more than 50 (x 10
3
) divi-

Users’ Manual Uplift pressure measurement system
Page 5-2 Rev. 0
sions after due regard to corrections made for difference in temperature, barometric pressure,
height above sea level and actual cell position (whether standing up or lying down).
For example in test certificate (see § 3.4), the zero reading in frequency
2
at the time of dispatch is
6917 (x 10
3
Hz
2
). In case the temperature and the barometric pressure is the same at the place
and time of installation and the sensor is placed lying down, the reading in frequency
2
should be be-
tween 6867 and 6967 (x 10
3
Hz
2
).
5.1.3 Connect the required length of cable to the sensor as suggested in the operating manual on
cable jointing - 6002.11/Rev 03/98.
WARNING! Take precautions while handling the epoxy system so that skin contact is minimal. The
epoxy components should never come in contact with eyes or other sensitive body parts.
Wash hands very thoroughly with soap immediately after work is over.
5.1.4 Check the working of the sensor again following the procedure described in § 5.1.2.
NOTE: Remember to add the cable resistance when checking the resistance between the leads
after the cable jointing. For the model ERC-10/11 cable, the resistance is 26 Ohm/km and
for the model ERC-12-15 cable, the resistance is 84 Ohm/km. (x 2 for both leads). In
case any other cable is used, make the necessary addition in the resistance value.
5.1.5 Record the initial readings including offset, barometric pressure and temperature in the field
book in the format provided in § 6.
5.1.6 Cable should be carefully marked. Cable should be marked with permanent markers every 5m
by the use of stainless steel tags tied by stainless steel wire stamped with appropriate con-
crete pressure cell numbers. Alternatively, plastic tabs are also available. Temporary identifi-
cation is possible by writing serial number of the sensor, its code number and the location at
which it is installed, on a strip of paper, placing the strip on the cable and covering it with a
transparent plastic cello tape. Permanent identification is necessary for proper connections in
the junction box and to insure correct splicing if cable is cut or broken.
CAUTION: The single most important factor leading to loss of worthwhile data from sensors is
losing track of identification of the cable ends. Proper identification and marking of the
cables is generally taken most casually. Care should also be taken to put an identifi-
cation tag at the point where the cable comes out of the structure such that cable
identity is not lost if the cable gets accidentally cut.
5.2. Installing the uplift pressure met er
The installation procedure comprises of the following steps:
5.2.1 A system of piping is installed at several stations in the dam with the top of any uplift pressure
measuring pipe ending in the gallery.
5.2.2 Remove the plug on the pipe coming into the gallery from foundation and check the threads.
5.2.3 Ensure before starting the installation that the pipes are not choked. If so clean them.
5.2.4 Make the connections as illustrated in figure 3.1. Use Loctite or the teflon tape to make them
water tight.
5.2.5 Connect the leads of the jelly filled cable to the respective connector pins in the junction box.
NOTE: For transmitting the signals to the observation room from the junction box, 10 core (5
pairs) or 20 cores (10 pairs) jelly filled cable, standardized by TRITECH may be used.

TABLE OF CONTENTS
1.
INTRODUCTION .........................................................................................................................1-1
1.1.
T
YPICAL INSTALLATION IN A CONCRETE DAM
...........................................................................1-1
1.2.
U
PLIFT PRESSURE MEASUREMENT
.........................................................................................1-1
1.2.1.
Mechanical method.........................................................................................................1-1
1.2.2.
Electronic method...........................................................................................................1-2
1.3.
C
ONVENTIONS USED IN THIS MANUAL
.....................................................................................1-2
1.4.
H
OW TO USE THIS MANUAL
....................................................................................................1-2
2.
MECHANICAL MEASUREMENT ...............................................................................................2-1
2.1.
T
OOLS
&
ACCESSORIES
.........................................................................................................2-1
3.
ELECTRONIC MEASUREMENT ................................................................................................3-1
3.1.
G
ENERAL SYSTEM DESCRIPTION
............................................................................................3-1
3.2.
V
IBRATING WIRE PRESSURE SENSOR
.....................................................................................3-2
3.2.1.
Manufacturing range.......................................................................................................3-2
3.2.2.
Operating principle .........................................................................................................3-2
3.2.3.
Specifications .................................................................................................................3-3
3.2.4.
Description......................................................................................................................3-3
3.3.
T
AKING READINGS WITH THE MODEL
TES-DI-51V
VIBRATING WIRE INDICATOR
........................3-4
3.4.
S
AMPLE TEST CERTIFICATE
....................................................................................................3-6
3.5.
T
HERMISTOR
-
TEMPERATURE RESISTANCE CORRELATION
......................................................3-7
4.
TOOLS & ACCESSORIES REQUIRED FOR INSTALLATION OF VW SYSTEM.....................4-1
5.
INSTALLATION OF VIBRATING WIRE SYSTEM .....................................................................5-1
5.1.
P
REPARATION OF THE SENSOR BEFORE INSTALLATION
............................................................5-1
5.2.
I
NSTALLING THE UPLIFT PRESSURE METER
.............................................................................5-2
This manual suits for next models
6
Table of contents
Other Tritech Measuring Instrument manuals
Popular Measuring Instrument manuals by other brands
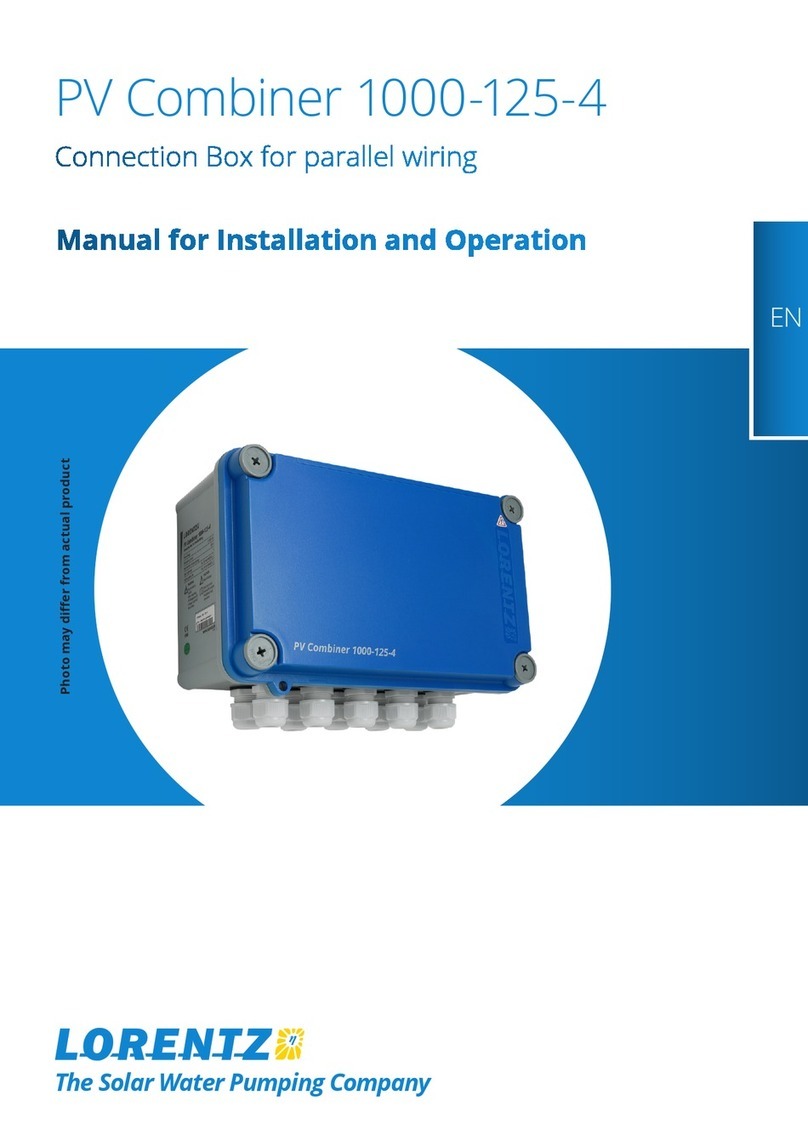
Lorentz
Lorentz PV Combiner 1000-125-4 Manual for installation and operation
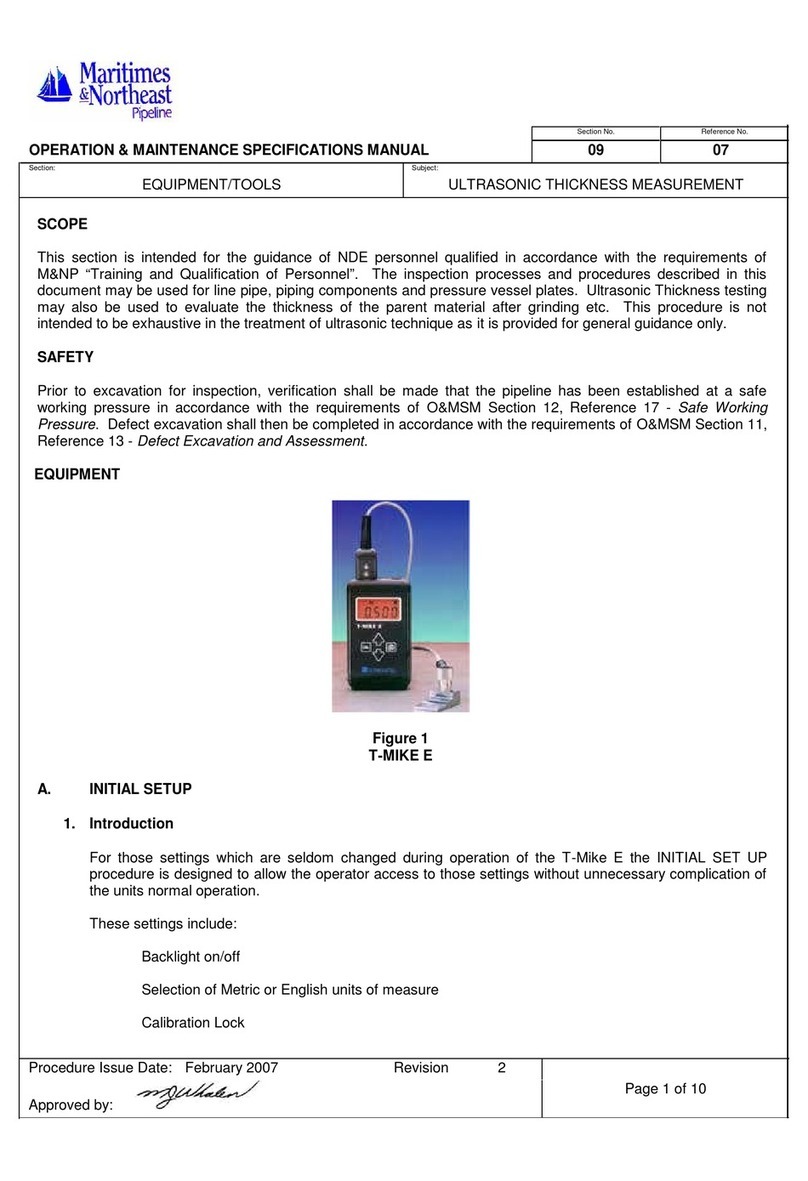
GE
GE StressTel T-MIKE E Operation & Maintenance Specifications Manual
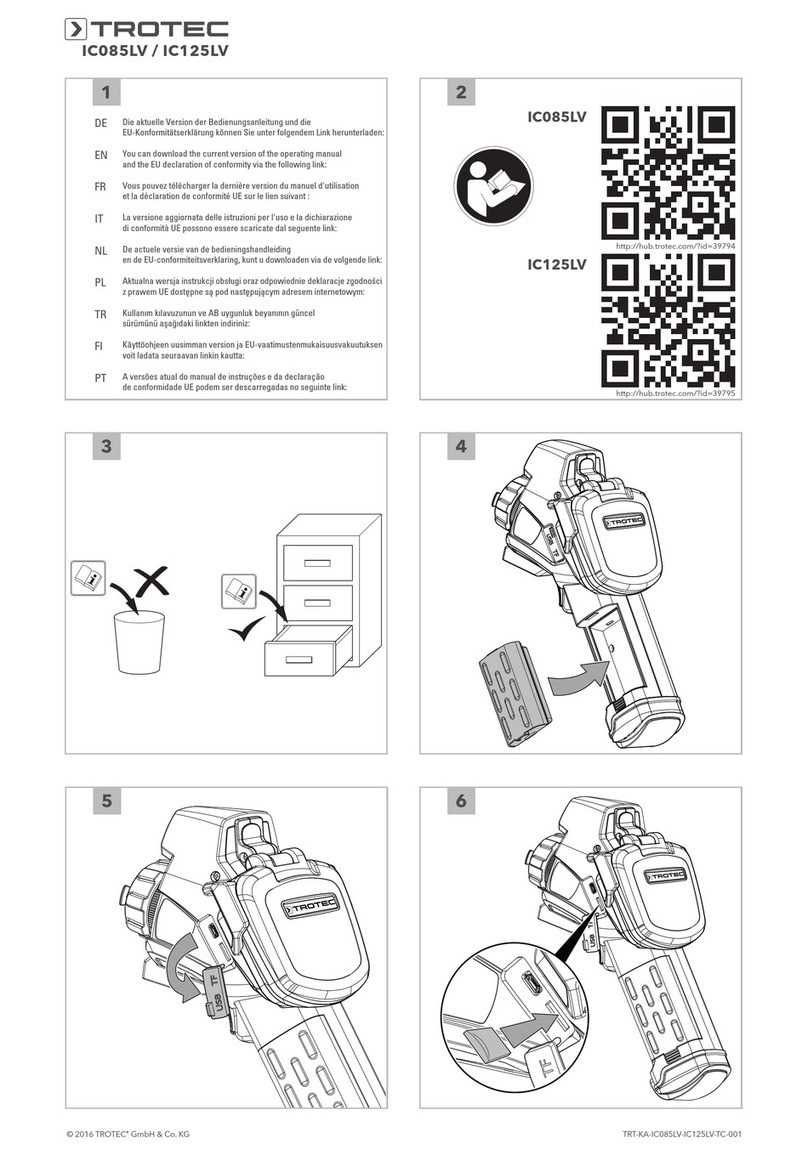
Trotec
Trotec IC085LV operating manual
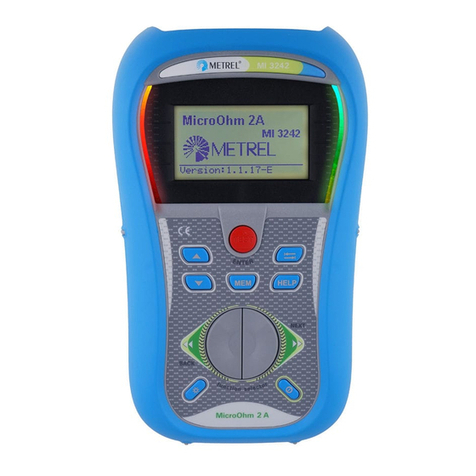
METREL
METREL MicroOhm 2A MI 3242 instruction manual
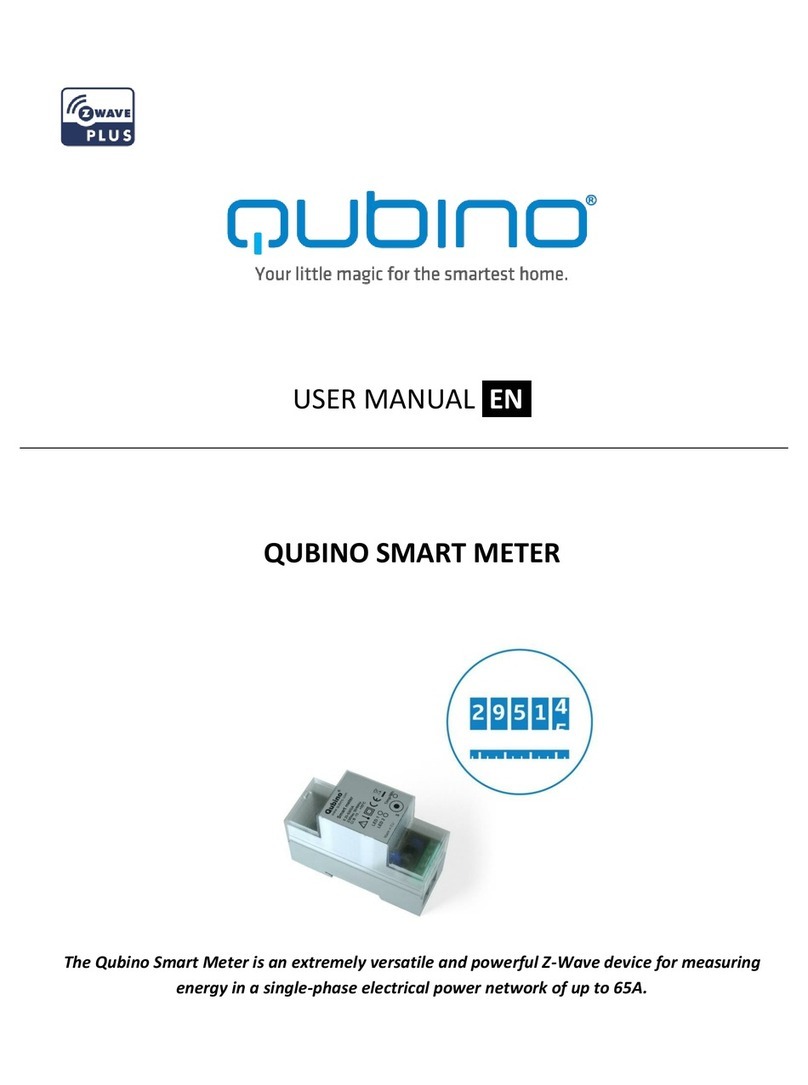
QUBINO
QUBINO Smart meter user manual
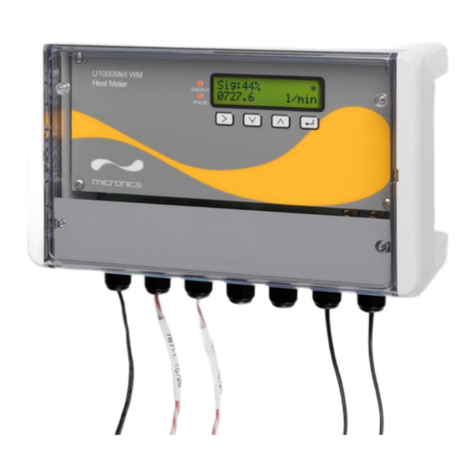
Micronics
Micronics U1000MkII WM user manual