Triton Electronics AMV3500 User manual

© Triton Electronics Ltd 2022 Doc. AMV35003_1.doc June 22
AMV3500 Operating Manual

© Triton Electronics Ltd 2022 Doc. AMV35003_1.doc v1.04 PAGE 2 OF 52
Contents
1. Starting and connecting the AMV3500...........................................................................................4
1.1 Connecting the sensors...........................................................................................................4
1.1.1 Current sensor.................................................................................................................4
1.1.2 Voltage connections........................................................................................................5
1.1.3 Wire Feed Sensor............................................................................................................5
1.1.4 Temperature Sensor .......................................................................................................5
1.1.5 Gas Flow Sensor..............................................................................................................6
1.1.6 Travel Speed Sensor........................................................................................................6
1.1.7 Voltage breakout box (P316) ..........................................................................................6
1.1.8 4-20mA Breakout box (P362)..........................................................................................6
1.2 Charging the AMV3500...........................................................................................................7
1.3 Starting the AMV3500.............................................................................................................7
2 Main Operating Screens and Menus...............................................................................................7
2.1 AMV3500 configuration menu................................................................................................7
2.2 Set Alarms ...............................................................................................................................8
2.3 Calibrate..................................................................................................................................8
2.4 Configure.................................................................................................................................9
2.4.1 Main ................................................................................................................................9
2.4.2 Heat Input .....................................................................................................................10
2.4.3 Trigger ...........................................................................................................................11
2.4.4 Maintenance .................................................................................................................12
2.5 Additional..............................................................................................................................12
2.6 Resume..................................................................................................................................13
2.7 New Procedure .....................................................................................................................13
2.8 About.....................................................................................................................................14
2.9 Stud Welding.........................................................................................................................15
2.10 Load Configuration................................................................................................................15
2.11 Save Configuration................................................................................................................15
2.12 Data export ...........................................................................................................................16
2.13 Monitor Screen .....................................................................................................................17
2.13.1 Oscilloscope Mode........................................................................................................18
2.13.2 Printer options ..............................................................................................................19
2.14 Pass Complete.......................................................................................................................21
2.14.1 Arc values......................................................................................................................21
2.14.2 Enter Pass Length..........................................................................................................22

© Triton Electronics Ltd 2022 Doc. AMV35003_1.doc v1.04 PAGE 3 OF 52
2.14.3 Pass summary values ....................................................................................................22
2.14.4 Graph.............................................................................................................................23
2.14.5 Procedure......................................................................................................................23
2.14.6 Summary PDF................................................................................................................23
2.15 Procedure Complete .............................................................................................................25
2.16 Printer Controls.....................................................................................................................26
2.16.1 Configure Screen...........................................................................................................26
2.16.2 Monitor screen..............................................................................................................27
2.16.3 To print an average at a specific second interval..........................................................28
2.16.4 Saving the values...........................................................................................................29
2.16.5 Suggested setting..........................................................................................................29
2.17 AMV Final File Uploader .......................................................................................................30
3 How to guides ...............................................................................................................................32
3.1 Monitor a GTAW, GMAW or MMAW procedure..................................................................32
3.2 Setup to monitor an AC SAW procedure ..............................................................................40
3.3 Use F1 and F2 Function buttons. ..........................................................................................48
3.3.1 Start a new procedure: .................................................................................................48
3.3.2 Record Welding –F1 .....................................................................................................49
3.3.3 Record Welding F2........................................................................................................50
3.3.4 Summary .......................................................................................................................52

© Triton Electronics Ltd 2022 Doc. AMV35003_1.doc v1.04 PAGE 4 OF 52
1. Starting and connecting the AMV3500
1.1 Connecting the sensors
1.1.1 Current sensor
There are two current sensing devices for the AMV3500. A clamp system is mostly used as it is a
convenient and simple way to attach to the welding cable. Secondly an inline sensor, this offers
greater accuracy and repeatability but is less flexible.
1.1.1.1 Clamp Sensor
The current sensor (P332) is clamped around either the torch
or earth return. Practically both sides should measure the
same values.
The clamp will determine a positive and negative flow of
current. The AMV3500 will show only the magnitude of
current on the digital display the direction is shown in the
OSCILLOSCOPE mode.
The clamp meters are iron based and will take an offset as
they become magnetised. Check that the current channel
reads zero, or close to, before monitoring a weld.
Check the clamp has not been mechanically damaged, the
clamp arms should be fully closed and aligned with each
other.
1.1.1.2 Inline sensor
The inline current sensor (P360) fits inline
with the welding cables, either torch or
earth return. The inline sensor uses Dinse
connectors.

© Triton Electronics Ltd 2022 Doc. AMV35003_1.doc v1.04 PAGE 5 OF 52
1.1.2 Voltage connections
It is important to remember that unless measuring the voltage at the welding head or torch, all
measured voltage will include the voltage drop across the cables. So, if a procedure is qualified using
3m cables but in production uses 6m cables the voltage measured at the power source will be
different.
AMV3500 will display the voltage magnitude when displaying digital values, it is only in
OSCILLOSCOPE mode that polarity of voltage is shown. For all calculations the magnitude is used.
1.1.2.1 Voltage clips
These are the simplest way to connect to any power source. Generally, one side on the earth clamp
and, if MIG/ MAG welding the other on the wire feed unit.
1.1.2.2 Dinse connectors
Dinse connectors provide a convenient way to measure
welding voltage. These are particularly applicable to TIG and
MMAW welding.
1.1.3 Wire Feed Sensor
Clip the wire feed sensor around the welding wire and
connect to the AMV3500.
1.1.4 Temperature Sensor

© Triton Electronics Ltd 2022 Doc. AMV35003_1.doc v1.04 PAGE 6 OF 52
1.1.5 Gas Flow Sensor
The gas flow sensor is plumbed into the gas flow line. The
direction of flow is marked on the sensor.
1.1.6 Travel Speed Sensor
The travel sensor is a surface contact sensor for monitoring table or
welding torch speeds. The mounting of the sensor is dependent on the
application, it can be by surface wheel or through the gear train. Output
pulses are calibrated by the AMV to give results in speed (units can be
specified at calibration) or RPM as the application dictates.
1.1.7 Voltage breakout box (P316)
The voltage breakout board provides an easy way to integrate additional sensors to the AMV weld
monitors. The P316 is intended for a device that outputs voltage that can feed into the +/- 3V input
stage on the AMV.
In addition, it can also power device from the internal 12V AMV power bus. Max drain 20mA.
Connections are made by screw terminal.
1.1.8 4-20mA Breakout box (P362)
The voltage breakout board provides an easy way to integrate additional sensors to the AMV weld
monitors. The P362 is intended for a device that outputs a 4-20mA signal that can feed into the +/-
3V input stage on the AMV.
In addition, it can also power device from the internal 12V AMV power bus. Max drain 20mA.
Connections are made by screw terminal.

© Triton Electronics Ltd 2022 Doc. AMV35003_1.doc v1.04 PAGE 7 OF 52
1.2 Charging the AMV3500
The AMV3500 is charged using the 18V 3.3A DC Jack at the back of the unit. The bayonet is centre
positive. The charger will time out after approximately 4 hours, to ensure the battery is fully charged
from empty two 4 hours cycles are required.
A full charge should run the AMV3500 for 3-4 hours depending on the printer setting. When the low
battery alarm goes off there is about 15 minutes of charge left.
With regular charging cycles the battery will last for a few years.
1.3 Starting the AMV3500
To start the AMV press the ON/OFF button at the back of the unit. It takes 2 minutes to boot to the
AMV3500 Configuration menu
2Main Operating Screens and Menus
2.1 AMV3500 configuration menu
This is the main screen to setup and record a new procedure. The main sections are:
1. Procedure information –this section displays the current procedure name and details. To
change the entries, press NEW PROCEDURE or EDIT
2. Channels to monitor, select the channels Voltage and Current these must be selected.
Temperature can be set to IP (InterPass). In this mode the temperature is taken at the start
of the weld.
2
1
3
4
5

© Triton Electronics Ltd 2022 Doc. AMV35003_1.doc v1.04 PAGE 8 OF 52
3. Select the welding process. This has most effect when calculating heat input using process
efficiency –see CONFIGURE.
4. These are the main control features and are discussed in more detail later.
5. Options for saving configuration files and exporting the recorded data.
The next sections go through the individual screens and options, there are also examples for how to
run through a setup in the How to Guides.
2.2 Set Alarms
The alarms show on the main screen. There are two levels an amber warning level and a red out of
tolerance level. To turn on the channel’s alarm press the channel button and the state changes to
ENABLED:
To set the values, enter the target values in the central column. Click in the box and a numeric entry
pad will be displayed. Once the values have been entered press the Set AMBER and Set RED buttons
to automatically set the limits. By default these are 10% and 12.5% respectively, but this can be
changed, by clicking inside the red and amber value boxes. Individual boxes can also be changed as
required.
The alarms are saved with the configuration file.
2.3 Calibrate
To access the calibration menu please contact Triton Electronics Ltd.

© Triton Electronics Ltd 2022 Doc. AMV35003_1.doc v1.04 PAGE 9 OF 52
2.4 Configure
There are 4 main tabs of configurations
•Main –these are most of the user configurations
•Heat Input –special options for heat input calculation
•Trigger –where to set the arc on / arc off condition
•Maintenance –mainly for Triton engineers to help diagnose any system issues
Company name can be set (needs a USB keyboard to be used) –this is printed at the top of all
reports.
CLOSE returns the programme to the main AMV3500 Configuration Screen and saves the values.
2.4.1 Main

© Triton Electronics Ltd 2022 Doc. AMV35003_1.doc v1.04 PAGE 10 OF 52
2.4.1.1 Store Transient Data
This will store the welding waveform data. The data can be analysed using our AMV_Desktop
software. This is available to all purchasers of the AMV3500.
Generally, this is not set as transient data files can be large.
2.4.1.2 WFS pulse
Sets the wire feed speed sensor to a frequency type. The option to use a voltage input sensor is for
legacy compatibility –all new sensors are frequency base.
2.4.1.3 RMS Values
If RMS values are preferred this should be turned on. By default if the process is set to AC the RMS
option is activated, otherwise it is off.
2.4.1.4 PICO temp
For compatibility with a TC-08 Pico Data logger, please ask if you are interested in using this option.
2.4.1.5 AutoPassUp
This is for surfacing type applications. In normal operation the pass complete button is blocked
when an arc is recording. This stops an operator accidentally completing a recording before the weld
has completed. However, for a surfacing application the welding arc is maintained during the
completion of the pass. Activating this function allows a pass up to be completed while the AMV
continues to “see” a welding arc. It can result in a few seconds of data loss (approx. 5 seconds) as
the files are saved and the next pass started.
2.4.1.6 Multi-power source
Voltage and current are set as data channels 1 and 2, but the remaining channels can be configured
as needed. In this case up to 4 current channels can be summed for heat input. For instance, a SAW
system with 4 wires feeding the same weld pool, the assumption is that the voltage is common. Of
course, this is rarely the case, but it can be used as an approximate control.
2.4.1.7 Arc Cancel Option
If this is selected the user has an option to cancel the last recorded arc.
2.4.2 Heat Input
2.4.2.1 Heat Input Calculation
Changes calculation from instantaneous to average.

© Triton Electronics Ltd 2022 Doc. AMV35003_1.doc v1.04 PAGE 11 OF 52
2.4.2.2 Use BS EN Process Efficiency
Adds the process efficiency to the overall heat input calculation
2.4.2.3 Arc Heat Input
If turned on a weld length is entered at the end of an arc so heat input can be calculated, this is
aimed at automated applications.
2.4.2.4 Use Segment Control
If you are using the strip welding technique you can use segment control to calculate heat input as
the pipe is welded. At the completion of an arc you can complete a section, enter a weld length so
the heat input is calculated. Once the last segment is welded all segments are included in the pass
data.
2.4.2.5 Resistance
Practically it is not possible to monitor the welding voltage across the welding arc. This allows for an
adjustment to be made if the resistance of the power cables is known.
2.4.3 Trigger
2.4.3.1 Trigger values
Once the voltage and current values are ‘seen’ by the AMV it considers a welding arc is on. If either
drops below the value the arc is considered off. One or both can be set to zero (if both are set to
zero the AMV will always see a welding arc –this condition is to be avoided)
Slope up and Slope down times can be set –these are removed from the arc time and heat input
calculations. If the welding arc is shorter than both the slope up plus slope down value an error is
detected, and the arc discarded.
Min arc time is the shortest arc time needed for an arc to be considered “real”. Particularly for
manual metal arc welding if the electrode is struck to just prove there is contact or “warm” the
electrode this is ignored if below the min arc time.

© Triton Electronics Ltd 2022 Doc. AMV35003_1.doc v1.04 PAGE 12 OF 52
2.4.4 Maintenance
These settings are just for basic setup or fault finding only and should not be altered.
2.5 Additional
This screen can be used to store additional procedure information. Please speak to Triton Electronics
Ltd.

© Triton Electronics Ltd 2022 Doc. AMV35003_1.doc v1.04 PAGE 13 OF 52
2.6 Resume
The resume screen shows the available data files that can be resumed. Press the file name and the
data should be loaded into the display boxes along with the next pass number.
Press LOAD to return to the configuration screen. This returns to the Configuration Screen.
2.7 New Procedure

© Triton Electronics Ltd 2022 Doc. AMV35003_1.doc v1.04 PAGE 14 OF 52
To clear the current flashing text box press the CLEAR button. Then start to type in the new
information.
The other buttons on the screen are:
NEXT –use this button to move to the next text box.
DELETE –deletes the last entry in the current box being edited.
UPDATE –When the new data has been entered press the UPDATE button to return to the
configuration screen. This will return to the Configuration Screen.
2.8 About
The about screen shows the current software version. When connected to a network the IP address
is also displayed.

© Triton Electronics Ltd 2022 Doc. AMV35003_1.doc v1.04 PAGE 15 OF 52
2.9 Stud Welding
2.10 Load Configuration
To use this screen, select the configuration name and press LOAD. Configurations include alarms
settings, welding process and logging channels.
Return the configuration details to the Configuration Screen.
2.11 Save Configuration

© Triton Electronics Ltd 2022 Doc. AMV35003_1.doc v1.04 PAGE 16 OF 52
To store the current configuration use the Save Configuration screen. Use the screen keypad to
enter a file name and description.
Press UPDATE to save the configuration and return to Configuration Screen
2.12 Data export
1. Select the procedure to be either copied or moved to a USB.
2. Make sure the USB has been detected and that the correct drive letter is selected.
3. Decide if TEXT or ALL data is required
4. Select to wither MOVE files or SAVE files. SAVE files copies the files to the USB stick,
MOVE removes them from the AMV and onto the USB stick.
5. To DELETE a folder ALL files must first have been moved to the USB stick.
6. Press CLOSE to complete and return to the Configuration Screen.

© Triton Electronics Ltd 2022 Doc. AMV35003_1.doc v1.04 PAGE 17 OF 52
2.13 Monitor Screen
The main monitoring screen shows the values recorded during welding. If a pulse process has been
chosen the pulse values are displayed along the bottom of the screen.
The options are:
•CONFIGURE –takes the software back to the Configuration Screen.
•PASS COMPLETE –finishes this pass (collection of arcs) and moves to the PASS COMPLETE
screen
•OSCILLOSCOPE –changes the display to a graph of the welding waveforms.
•PRINTER –sets the printer options.
•QUIT –close the software and the AMV3500

© Triton Electronics Ltd 2022 Doc. AMV35003_1.doc v1.04 PAGE 18 OF 52
2.13.1 Oscilloscope Mode
This changes the main display so that the welding waveform can be analysed. Use the button at the
top right-hand side of the screen to view current and voltage values:
If the transient file option has been set in the CONFIGURE screen the transient file will be recorded
for future examination. However, please note these files will become large very quickly.

© Triton Electronics Ltd 2022 Doc. AMV35003_1.doc v1.04 PAGE 19 OF 52
2.13.2 Printer options
The AMV prints out the recorded data as the weld progresses. It simultaneously saves a text file
containing the same information.
The options are:
OFF turns the printer off completely
for this run only. Resets to ON after
pass complete. This also stops a text
file being saved.
ARC/PASS prints out the averages of
the pass and every arc.
If a time is selected the AMV prints
out averages at these second
intervals and the average arc and
pass values
PRINTER OFF turns the printer off
but allows a printer text file to be
generated as if the printer was on.
This option is remembered and once
set it is the default value.
Print Arc. If this option is selected
the AMV prints Arc averages, if
unticked they are stored in the text
file, similarly second averages are
saved but not physically printed
(need to select the period).

© Triton Electronics Ltd 2022 Doc. AMV35003_1.doc v1.04 PAGE 20 OF 52
For example, this setting:
Means a text file will be generated, producing averages every second of the weld and at the end of
an arc and pass. However, physically all that will be printed is the pass summary.
This is a good starting point as the paper generated acts as a good physical summary of the welding
and the text file contains more detail, that if printed would use much of the paper roll.
For more information see the section on PRINTER CONTROLS
Table of contents
Popular Data Logger manuals by other brands
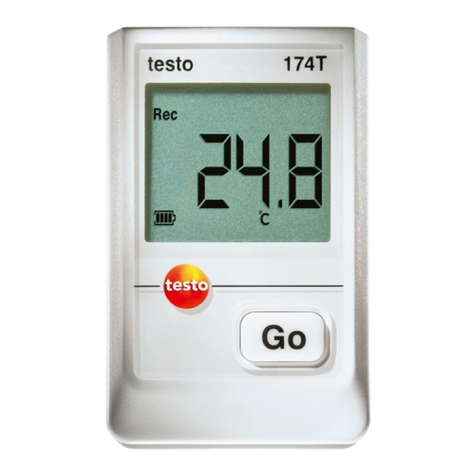
TESTO
TESTO 174 instruction manual
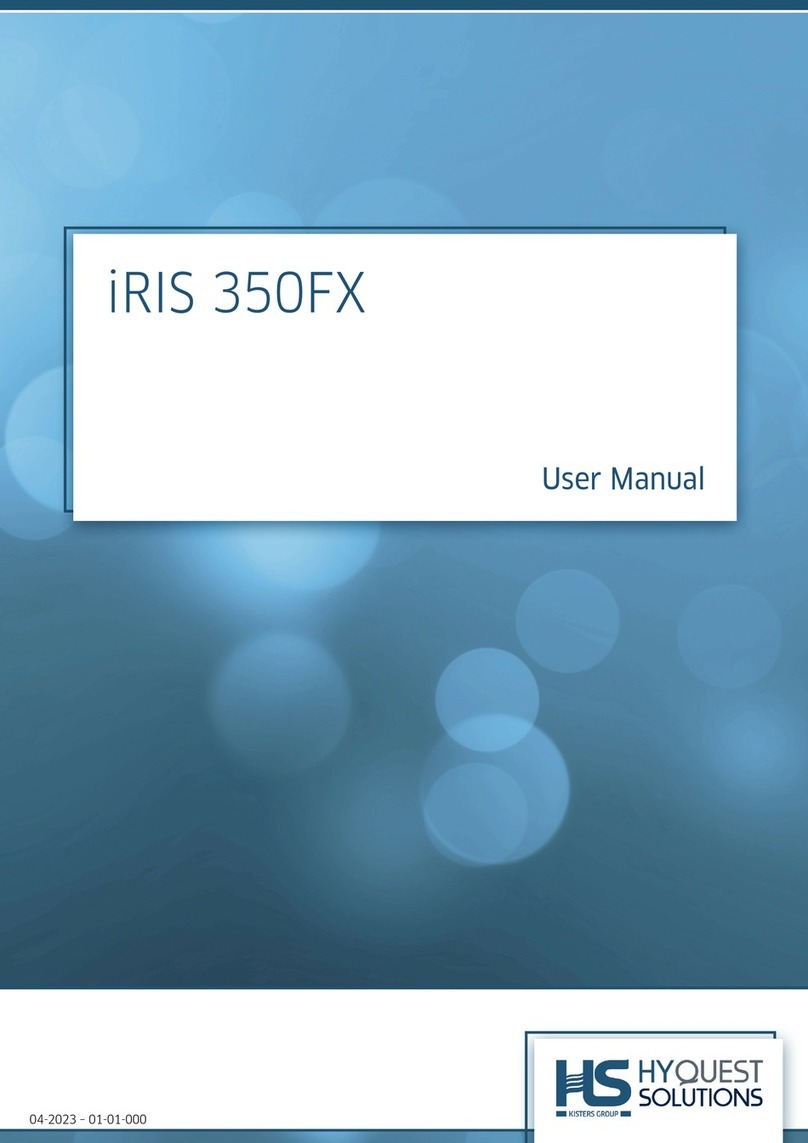
HyQuest Solutions
HyQuest Solutions iRIS 350FX user manual
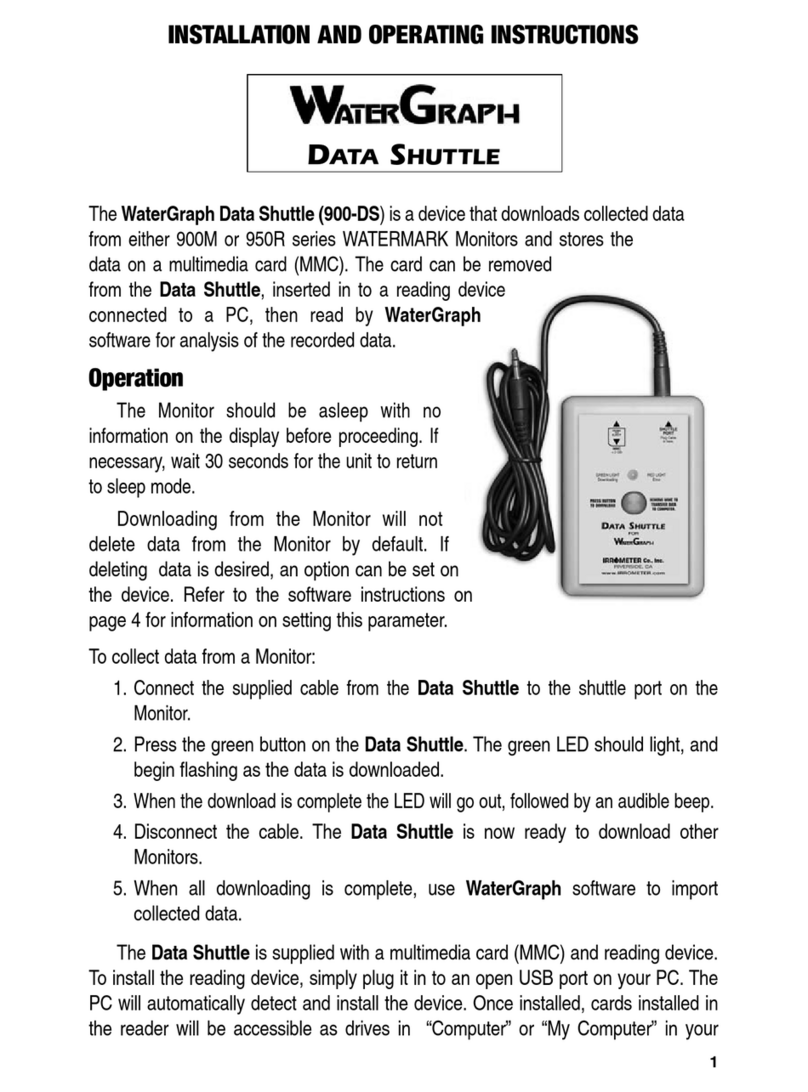
IRROMETER
IRROMETER WaterGraph Data Shuttle Installation and operating instructions

Biomark
Biomark IS1001 user manual
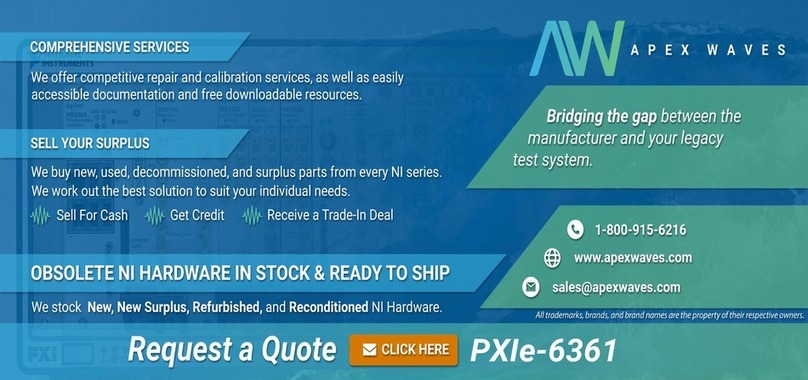
National Instruments
National Instruments 636 Series user manual
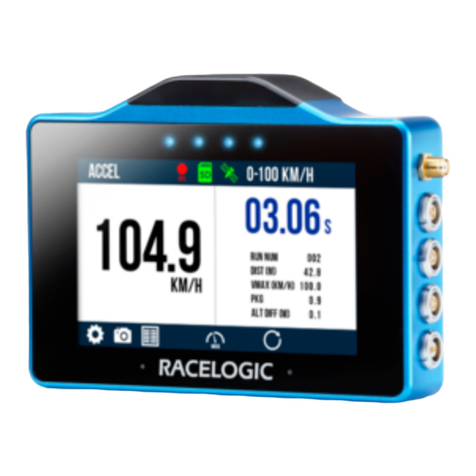
Racelogic
Racelogic VBOX Touch V2 quick start guide