TX Testing Instruments PHB-3000 User manual

PHB-3000
HYDRAULIC BRINELL
HARDNESS TESTER
www.txinstruments.com

1. Introduction……………………………………………………………1
2. Features…………………………………………………………………1
3. Technical Parameters………………………………………………3
4. Principle & Structures………………………………………………3
5. Operations……………………………………………………………4
5.1 Preparation…………………………………………………………4
5.2 Operation……………………………………………………………4
6. Introduction of Main Parts…………………………………………5
6.1 Indenter……………………………………………………………5
6.2 Gauge………………………………………………………………6
6.3 Pressure Lever……………………………………………………6
6.4 Pressure Release Lever…………………………………………6
6.5 Control Valve………………………………………………………7
6.6 Oil Cylinder…………………………………………………………7
6.7 Test Head Carriage………………………………………………7
7. Standard Package……………………………………………………8
8. Optional Accessories………………………………………………8
Appendix 1: Maintenance Manual
Table 1: Brinell Hardness Table
Table 2: Testing Accuracy of Brinell Hardness Testers
Table 3: Testing Conditions for Brinell Hardness Testers
Table 4: Selection of Testing Conditions for Brinell Hardness Testers
Table 5: Conversion of Brinell Hardness and Tensile Strength
5.3 Usage Method of the reading microscope… … …………… … ……5
Appendix 2: Packing & Transportation
Appendix 3: Warranty
Contents

1. Introduction
PHB-3000 portable Brinell hardness tester has the same structure as King Brinell
hardness tester. It is the unique portable hardness tester in the world which applies
test condition with 3000kg test force on a 10mm carbide indenter. The large
indentation resulted by the tester can reflect the average value of combined influence
affected by all the compositions of large materials. It is unaffected by certain
composition of materials or partial nonuniform distribution and very suitable for
testing nonuniform materials made of large crystal particle. The testing result of this
instrument is true and accurate with good repeatability and it has a good
correspondence with tensile strength. It is the best mechanical property tester which
can be used on site. The test condition and accuracy meet the requirements of ISO
6506 and ASTM E110 and can be used to test rough castings, forgings, nonferrous
metals and semi-finished products after tempering heat treatment.
2. Features
2.1 On-site testing, without sampling
It is a portable instrument suitable to use in the plant. It is easy to operate and
convenient to carry. So it can be used to test the large workpiece, fixed workpiece
without sampling and to test the large workpiece in any direction (like upside,
underside, side face or inversion) on site.
2.2 Permanent indentation, easy reinspection
By applying 3000kg
test force and 10mm ball indenter, the permanent indentation
can be reinspected at any time after testing. In addition, the existence of the
indention shows that the workpiece has been tested .
2.3 Accurate testing, real result
Testing according to the real principle of Brinell hardness testing, PHB-3000
applies the same principle as the bench type Brinell hardness tester. Thus the result
is totally different from the inaccurate conversion value that other portable hardness
testers (eg. Leeb hardness tester) get. The calibration accuracy of the test force is
0.5%. The accuracy of hardness testing is the same as bench type hardness tester.
2.4 Optional test condition, wide testing range
The tester has various testing forces and indenters so that it can test all kinds of
materials and its testing range can be up to 16-650HBW.
2.5 High technique, high cost performance
The parts machining and assembling quality of this instrument are much better
than King Brinell hardness tester. It is free of the problem of oil leak of the hydraulic
system and gear jamming of the jacking system, so it has a higher cost performance.
1
PHB-3000 Hydraulic Brinell Hardness Tester
www.txinstruments.com

3. Technical Parameters
Test Force: 3000kg (500kg, 750kg, 1000kg, and 1500kg optional)
Indenter: 10mm carbide ball indenter (5mm ball optional)
Testing Range: 16-650HBW
Max. Specimen Height: 350mm
Throat Depth: 100mm
Repeatability: comply with ISO 6506
Error Indication: comply with ISO 6506
Net Weight: 13.8kg
4. Principle & Structures
It adopts hydraumatic principle which functions the hand-operated way to apply
3000kg test force. The central part of PHB-3000 is a small hydraulic system in which
a release valve is used to control the test force. When the force reaches 3000kg, the
release valve will open and the pressure will fall down. As specified in the operation
manual, the tester needed to be forced to make the indicator of the dial point at
3000kg test force for 3-5 times. Thus it is equivalent to the test condition of Brinell
hardness testing method to hold 3000kg test force for 10-15 seconds with 10mm
steel ball, which complies with ASTM E110.
The structure of the instrument is shown as Fig .1.
The instrument consists of carriage and test head.
The carriage is composed of base, anvil, anvil holder, throat, handle, jacking
system and test head pallet. The base with anvil applies the extended structure in
front , which is easy to clamp workpieces or to test tubes. The test head installed
between the two pallets and the throat is responsible for holding the tester and
keeping the 3000kg test force. The screw jacking system controlled bythe crank can
be up and, down from the throat in order to make the test head move.
The test head is composed of gauge, pressure lever, indenter, oil cylinder,
pressure release lever and operating lever.
The test head is a small hydraulic system. By giving the small cylinder a little
force, the large cylinder (indenter) will produce a huge force. The function of the dial
gauge is to show the value of test force the pressure lever is used to apply the force;
the indenter is to apply the force onto the workpiece and result in a standard Brinell
indentation on it. The job of the oil cylinder is to store oil, pressure release lever is
used to control the test force releasing or keeping, and operating lever is used to
accurately control the largest 3000kg test force.
The test head is installed on the carriage in order to move the test head up and
down by means of screw jacking system.
3
PHB-3000 Hydraulic Brinell Hardness Tester
2PHB-3000 Hydraulic Brinell Hardness Tester
Fig. 1 Instrument Structure
Jacking system
Pressure release valve
Control valve
Cylinder cap
Hydraulic pump
Crank
Handle
Screw rod
Handle
Gauge
Operating lever
Carriage
Test head
Screw
Indenter body
Indenter holder
Ball
Anvil cap
Anvil
Base
Jacking system
Pressure release valve
Control valve
Cylinder cap
Hydraulic pump
Crank
Handle
Gauge
Handle
Screw rod
Operating lever
Carriage
Test head
Screw
Indenter body
Indenter holder
Ball
Anvil cap
Anvil
Base
www.txinstruments.com
www.txinstruments.com

pressure lever; load the test force on the specimen and watch the gauge. The dial
begins to move to 3000kg scale. Continue to move the pressure lever. When the dial
reaches 3000kg, the control valve will work and the pressure will fall down. Repeat
this procedure 2-4 times and make the dial point reach 3000kg for 2-4 times ( totally
reaches 3000kg for 3-5 times ). Then the progress of loading force is finished. Open
the pressure release lever, raise the test head and move the tester away from the
specimen. The indenter will leave an indentation on the surface of the specimen. Use
the reading microscope to measure the diameter of the indentation. Check the
,
tables in the appendix for Brinell hardness test result s If there is provisionally no
need of testing, do as the following processes to protect the tester:
a. Install the anvil cap.
b. Lower the test head and make the indenter reach the anvil cap.
c. Remove the pressure lever.
5.3 Usage Method of the reading microscope
5.3.1 Look into the ocular and turn the rotational barrel dial to make the vertical lens
line aligned with the 0 scale of the horizontal line, Meanwhile look at the barrel
outside, the long black scale mark should rest on 0 scale of the rotational drum dial
5.3.2 Put the reading microscope on the test piece to locate the indentation in the
centre of the viewing field of the microscope. Move the microscope to make the
vertical line tangential to the left edge of the indentation. Press the bottom of the
reading microscope firmly, turn the rotational drum dial and make the vertical line
tangential to the right edge of the indentation.
5.3.3 Read the integer part (mm) of the indentation diameter from the horizontal scale
mark, then read the 2-digit decimal part of the indentation diameter from the
rotational drum, accurate to 0.01mm.
5.3.4 In routine use, when you look into the ocular, let the vertical line is aligned with
the 0 scale mark of the horizontal line, but in the outside barrel if the 0 scale
mark of the rotational drum dial does not align with the long black scale mark, it
means the microscope is inaccurate. Adjustment should be made as follow:
a. Make the vertical lens line aligned with the 0 scale mark of the horizontal line.
b. Loosen the three screws on the rotational drum dial.
c. Make the 0 scale mark on rotational drum dial exactly aligned with the long
reading mark.
d. Fasten the three screws.
6. Introduction of Main Parts
6.1 Indenter
The indenter is composed of indenter body, indenter ball and indenter holder.
" "
" "
" " " "
" "
" "
5. Operations
5.1 Preparation
5.1.1 Prepare the workpiece
Choose an appropriate part of the sample and clean the rust and dirt around the
test point before testing. If the surface of the sample is rough or has the coating,
hardened layer, and decarburized layer, the operator need to polish the surface
of the workpiece properly until the substrate part of the workpiece exposes. The
high quality rechargeable grinder can be bought from the manufacturer.
5.1.2 Calibration of the tester
The c al ibration accuracy of the tester has been verified before deli very.
A calibration certificate is attached to the tester. Because of the w rong operation
or delivery accident, the accuracy of the tester w ill be impacted so that it w ill
influence t h e testing result. Before using the tester, inspect the accuracy of th e
tester w i t h the test block. In order to assure the accuracy of t he tester, it is
nec ess a r y to inspect the tester regularly with test blocks.
According to the rule,the loading force time is 3-5 times when test the steel
workpiece.Decrease the loading time when test the hard metal;Add the loading
time when test the soft metal.Determine the most correct loading time before test
the standard hardness block,this data can be used for reference when test similar
speciman in the future.
5.1.3 Select and install t h e anvil
The standard package of the tester includes 3 anvils. Each anvil fits for certain
specimens.
The flat anvil fits for most specimens and test blocks; the V anvil is used to test
cylinder and convex sp e cimens; the dome anvil is used to test te concave
surfaces and tubes.
Selecting the correct anvil can avoid unstable force loading and assure the
accuracy and reliability of the test.
5.1.4 Check the indenter
Check the indenter before testing and make sure the indenter holder is fastened
tightly, otherwise it may damage the indenter ball or make it lost.
5.1.5 Operation preparation
Install the pressure lever and open the pressure release lever, then raise the test
head in enough height, remove the anvil cap
5.2 Operation
Put the specimen in the opening of the tester; turn the crank in order to make the
test head move down and clamp the specimen between the test head and the
anvil.Keep turning the crank with big loading force in order to make the indenter body
come into the test head body. Then close the pressure release lever and move the
5
PHB-3000 Hydraulic Brinell Hardness Tester
PHB-3000 Hydraulic Brinell Hardness Tester
4
www.txinstruments.com
www.txinstruments.com

7
PHB-3000 Hydraulic Brinell Hardness TesterPHB-3000 Hydraulic Brinell Hardness Tester
6
tighten on the Workpiece and the test force is prepared to be loaded, the
pressure release lever can be closed.
c. After testing, open the pressure release lever and raise the test head
Immediately.
6.5 Control Valve
The control valve is the autocontrol pressure switch of hydraulic system. Before
leaving factory, the work point of the control lever is calibrated accurately to 3000kg
scale, and the tolerance is less than 0.5%. When the pressure in the cylinder reaches
at full scale 3000kg, the control valve will instantly open and close immediately, and
then the pressure in cylinder will fall down. Repeat these processes for 3-5 times,
and a Brinell test is finished.
The control valve has been calibrated accurately before leaving factory, so do not
remove the screw of the control valve optionally, otherwise the tester will lose accuracy.
6.6 Oil cylinder
The oil cylinder is composed of oil cover, locking nut of oil sac, oil sac, and sump.
When the indenter extends or retracts under the effect of test force and crank, the
oil volume in oil cylinder will change. This changing will be adjusted by oil sac
pressing or releasing, so that it can ensure there is no negative pressure and cavity
in the sump and also no oil slopping over. The oil will leak a little during the operation.
This instrument is improved on the indenter seal which makes the oil do not leak as
much as like products. The indenter cannot make a standard Brinell indentation
because of not enough movement dues to oil volume reducing. The typical effect of
that is no matter how to operate the pressure lever, the test force can not point at
3000kg full scale.
If this happens , add or change the oil.
Generally, changing oil should be done by the manufacturer or the reseller who has
,
been trained. Operators who try to do this by themselves should under manufacturer s
guide. The process of replacing the oil in sump is complicated, any carelessness will
result in mistake and the tester has to be sent back to the manufacturer.
6.7 Test Head Carriage
The test head holder is composed of base, throat, and gear jacking system,
crank, and test head pallet.
The base shape is extended forward, which makes it easy to test the edge of
specimen and tubes. There is no limitation for testing no matter to test the whole body
or the extended part of the specimen. The tester can test most of the specimens except
some thick ones. If the part of the specimen can be clamped between the indenter and
the anvil, it just can be tested. Even the tester is upside down, it can get the accurate
results.
The indenter body is a large cylinder obtained test force of hydraulic system. It
uses its larger area to get the huge test force from hydraulic system and can transfer
the test force into the specimen through at most several millimeters movement, so
that the indenter is impressed into the specimen.Turn the crank and force the
indenter retract into the test head body before loading force.
The instrument adopts the carbide ball indenter which is suitable for the latest
standard of Brinell hardness testing. The advantage of the carbide ball indenter is
hard, long-life, wearing resistant, and high accuracy. However it can not test the
chilled steel whose hardness is more than 60HRC, otherwise the indenter will be
damaged.
The carbide ball indenter can be bought from the manufacturer.
The indenter holder is used to fix the ball. Make sure the indenter is fixed well
before each testing.
6.2 Gauge
The gauge is used to show the value of test force and let operators see directly
the whole processes of the test force going up and down.
The gauge only can show the test force. It can not control the 3000kg test force.
In theory, experienced operators can test accurately without the gauge.
When the test force is less than 3000kg, the accuracy will depend on the gauge
accurate indication and the operator' s careful operation.
Protect the gauge from crashing and never tear it down.
6.3 Pressure Lever
The function of the pressure lever is to make the hydraulic system produce test
force.
The reciprocating motion of the pressure lever can make the small valve in hydraulic
system pressing the cylinder, and then the pressure will transfer into the large valve-
indenter body by oil. After suffering the large press, the indenter will move and output
the test force.
Make the indenter pressing on the workpiece when testing, then operate the
pressure lever.
6.4 Pressure Release Lever
The pressure release lever is the switch of the hydraulic system. Open the pressure
release lever, then the pressure will take off and close the pressure release lever, the
hydraulic cylinder will keep closed. At this time, the operator should operates the pressure
lever; the hydraulic cylinder will make force on the indenter.
The operator should follow the rules:
a. W hen not using the tester, keep the pressure release lever open.
b. O nly when the test head falls down, the indenter should be pressed
www.txinstruments.com
www.txinstruments.com

Some parts of the tester may wear after long time use, for example, seals leakage,
difficulty in loading full scales force, inaccurate test result, and difficulty in retracting the
indenter, deformed or worn indenter, loose support frame, being out of gauge and so on.
If these problems occur, the tester needs to be repaired.
Some of the maintenance tasks must to be done by the manufacturer. If the tester is
damaged or broken, send it back to the manufacturer.
Some of the maintenance tasks should be done by the resellers. The manufacturer
will have training for the technical team of main resellers to make them professional to
calibrate the tester, change oil or accomplish some of the maintenance work. The user
can repair their testers at the nearest retailer.
Other maintenance tasks can be accomplished by the user. Because of location or
transportation limitation, some end users can not send the tester back to manufacturer or
distributor. The user who has professional technicist can do by himself to change oil,
calibrate tester and repair the seals according to the maintenance manual. If there is any
difficulty during the repairing, contact the manufacturer for support. Parts and tools for
changing oil can be bought from the manufacturer.
As a general rule, the parts taken off during repairing should be changed to new
ones. The repeated use of the old ones will affect the performance of the tester,
especially for the O ring, washer and screw.
Problems and handling:
1. Hard to load test force
If it is hard for the test force to reach full scale of 3000kg, the probable cause and
handling is as following:
1.1 Indenter over-extending
When the indenter is extending too long, the pressure lever will take effect; the
movement distance of the indenter can not be long enough to apply 3000kg test force on
the specimen.
The handling method is:
Open the release valve, turn the crank and force the indenter to retract into the test
head body.
1.2 Oil shortage
After long time use, the hydraulic oil will lose and the remaining volume is not
enough to produce proper movement of indenter, so that it can not apply full scale of
3000kg test force on the specimen.
1.2.1 Checking the hydraulic sump
Take off the pressure lever and check if there is oil near the bronze bushing. If there
Appendix 1:
Maintenance Manual
Standard hardness block (high value)
Standard hardness block (low value)
10mm carbide ball indenter
5mm carbide ball indenter
Indenter holder
V anvil
Flat anvil
Dome anvil
Anvil cap
20X reading microscope (with LED light)
40X reading microscope (with LED light)
Rechargeable angle grinder
Automatic Brinell indentation
reading instrument
Maintenance tools and accessories
Pressure gauge
Oil (for two changes)
Injector (for oil injecting)
Sac
Sac nut
Cylinder cap
Pressure lever
O ring
Sump bronze bushing
Pop-off copper gasket
Sac nut wrench
Control valve wrench
Release valve wrench
Sump bronze bushing wrench
1 Tester
1 Pressure lever
1 Standard Brinell hardness block
(high value)
1 Standard Brinell hardness block
(low value)
1 V anvil
1 Flat anvil
1 Dome anvil
1 Anvil cap
1 20X reading microscope
(With LED light)
1 Spare carbide ball indenter
1 Allen wrench
1 Warranty certificate
7. Standard Package 8. Optional Accessories
9
PHB-3000 Hydraulic Brinell Hardness TesterPHB-3000 Hydraulic Brinell Hardness Tester
8
The throat is made of high grade alloy steel with high hardness, which gives the
testing reliable support. It will not be d eformed or bent under 3000kg test force.
The high advanced gear jacking system consists of crank, big nut, gear seat and
several gears. Turn the crank and the big nut will move up and down through the throat
by means of gears in order to control the test head up and down. The segments of the
gear jacking system are very precise. By accurate installation, the gears, big nut and
throat will get into the best interaction and it can quickly, portably move the test head up
and down.
The test head pallet is used to fix test head.
www.txinstruments.com
www.txinstruments.com

11
PHB-3000 Hydraulic Brinell Hardness TesterPHB-3000 Hydraulic Brinell Hardness Tester
10
is, it means the O-ring in the bronze bushing is worn. Both of the O ring and the
bushing need to be changed for new ones. The operation process of it is as following:
Take off the test head from the carriage, make the sump upside and put it on the
desk. During this process, take care to avoid oil leakage.
Use the special wrench for bronze bushing to take the bronze bushing off. The
bronze bushing has a left-hand thread which is different from other threads, so turn it
clockwise. An O ring will be found in the bronze bushing. If the O ring wears, some
oil will leak from bronze bushing. Fill the hydraulic sump with oil, take off the worn O
ring, insert a new one and screw tightly. There will be some hydraulic oil overflowing
around the bronze bushing. Clean the test head with soft cloth and cleaning fluid and
install back the test head.
Other parts of the hydraulic sump can not be taken down or changed except for
bronze bushing and o ring.
1.2.2 Changing hydraulic oil
To use oil of correct type and viscosity is vital important. Mobile oil BB is the best
(Saybolt 956 Secs at 100 F) and it can be bought locally. The spare hydraulic oil
and the tools for changing the oil can be bought from manufacturer or retailer.
The procedures of changing oil are a little complicated, change the oil strictly following
the instruction. Any disoperation may result in permanent damage of the parts.
Procedures are as following:
Close the pressure release lever,move the handle and push the indenter out to
10-12mm.
Screw off the cap and use the special wrench to take off the sac nut under the cap,
and then take out the sac.
Open the pressure release valve. Turn the crank in order to make the whole indenter
come into the test head body.
Close the pressure release lever.
Remove the screws which are fixed on the carriage.
Remove the test head, dump the old oil from the cylinder and then put the test head
back on the carriage.
Fix the test head in the carriage and tighten the screws.
Fill sump with oil, align the oil level with the step of the cylinder.
Turn the pressure lever and push the indenter out. At this moment, the oil level will
fall down. During the operation, keep the oil level and the step at the same level all
the time. Add the oil while pushing out the indenter until the exposing part of indenter
is 10-12mm.
Pump the 1/2 oil out of the sump with the injector.
Put back the sac. If there is some oil spilling from the sac, it means that the cylinder
is full. If there is no spilling oil, take out the sac and add more oil again.
º
Screw
Handle
Adjust nut
Sealing ring
Valve screw
Pin valve
Cap
Sac nut
Pressure lever
O ring
Bronze bushing (left screw)
Gear shaft
1
2
3
4
5
6
Note:The parts displayed in gray zone can not be removed by the user.
13
14
15
16
Spring
10
Sac
17
18
19
Bronze gasket
Calibrating nut
Ejector rob
Valve ball
7
8
9
11
12
Control valve cap
Fig. 2 Test Head
www.txinstruments.com
www.txinstruments.com

Quickly insert and fasten the sac nut tightly. Cover the cap and fasten it.
Open the pressure release lever.
Turn the crank and push in the indenter totally come into the test body
Close the pressure release lever. Load test force to 3000kg. Open the pressure
release lever.
Repeat the above processes for 5-10 times. It can get rid of the air which gets inside
during changing oil in hydraulic system.
Clean the test head and carriage with soft cloth cleaning fluid and then reassemble
test head.
1.2.3 Verification of test head
If it is difficult to load test force during a short time after changing oil, that indicates
X ring may wear. X ring can not be changed by the user.
They must be sent back to the manufacturer for maintenance.
2. Instrument misalignment
The tester may be inaccurate after long time use. It shows that the readings will be
out of specified range when testing on the standard test block. See Table 2.
Probable reasons and handling:
2.1 Incorrect numbers of loadings
To be equivalent to the condition for Brinell hardness test method of holding 3000kg
test force for 10-15 seconds with 10mm indenter. The tester is ruled to be forced for 3-5
times to make 3000kg. If the tester is a little out of tolerance, add 1 or 2 more times for
loading force so that it can make readings approaching to the real readings.
Add the loading times when test the soft metal. For example, when applying 500kg
test force with 10mm ball, the loading force times need to be added to 10-15 times.
2.2 Expired block
The block has been inspected before leaving factory and the hardness value marks
on the front face of block as well as its inspection date is on the certificate. The valid
period of blocks is one year and it should be rechecked after one year otherwise the
hardness value is not reliable, and the tester calibrated with the expired block will be
inaccurate. New test blocks can be bought from the manufacturer.
2.3 Deformed and worn ball
The carbide ball is durable and hard with high accurate dimension. After a long time
use and the wrong operation or testing on hard materials, the ball may become deformed
or worn.
When the tester is inaccurate and the block is verified to be not the reason, remove
the ball and twirl the ball in order to change its testing surface, then reinstall it on the test
head and fasten the ball cover.
It may take several times to renew the testing surface in one ball. After too many
PHB-3000 Hydraulic Brinell Hardness TesterPHB-3000 Hydraulic Brinell Hardness Tester 1312
times of the renewal, the ball cannot be used again and needs to be changed for a new
one. New balls can be bought from the manufacturer.
2.4 Inaccurate test force
After eliminating the reasons of blocks and balls, the accuracy of 3000kg test force
can be the probable reason.
The 3000kg test force has been calibrated before leaving factory and its tolerance is
less than ±0.5% of 3000kg。
The 3000kg test force is controlled by the control valve. If the 3000kg test force
needs to be recalibrated, follow the steps bellow. First, turn the pressure lever in order to
make the indenter extending as far as possible. Second, use an Allen wrench to remove
the control valve cover and take off the copper gasket, then oil will be seen through the
hole of control lever, and a calibrating screw is underneath. Use straight screwdriver to
search for the calibrating screw under the oil and turn it a little (any direction is ok). If the
hardness is a litter higher, turn the calibrating screw clockwise; otherwise, turn the
calibrating screw anticlockwise. Make sure the angle turned is not too big otherwise it is
hard to find the original calibrating point and the test force may be out of the secure
range and the tester may be damaged.
After adjusting the screw for control valve, verify the tester with the test block. If it is
out of tolerance, repeat the processes above until it is accurate.
After adjustment, fill the hole with oil. Replace the copper gasket with a new one and
screw the cover tightly.
The screw for control valve can be adjusted only a little. Too much adjustment and
taking it off are not allowed.
Other reasons for being out of tolerance, please contact manufacturer.
3. Leakage of pressure release valve
There are three sac rings in the pressure release valve for sealing. The sealing rings
will be damaged after long time use which makes the sealing effect worse, and oil will
leak slightly. Check the pressure release lever during the testing. If there is a little oil
leaking from the lever, do as the following processes:
Firstly, turn the pressure lever to make the indenter extending as far as possible.
Secondly, remove the screws of the pressure release lever with a screwdriver and take
off the crank. There will be a nut beneath it. Use the wrench for pressure release lever to
screw the nut, turn clockwise 1/6-1/8 round. Fill the hole with oil and reinstall the
pressure release handle and fasten it with screw.
The maintenances of pressure release valve are limited to the above procedures. The
release nut can not be removed by the user.
www.txinstruments.com
www.txinstruments.com

PHB-3000 Hydraulic Brinell Hardness Tester
14
Appendix 2:
PHB-3000 is a totally mechanical instrument which will be damaged by any
carelessness caused by packing and transportation.
The user should check carefully if the packing of the instrument is in good condition
when receiving it. If not, claim to the forwarder.
The packing of this instrument when it leaves factory is safe enough and can not be
substituted. The user should keep the packing materials for maintenance.
The warranty will be void if the tester is returned to the manufacturer without the
original packing.
Refer to the pictures of the original packing as follow:
Packing & Transportation Fig.3 Original Packing of the Tester
Caution:
Only the maintenance tasks listed in this manual can be carried out by
users. Any other maintenance tasks and disassembling of the tester do not
listed in this manual are forbidden. The parts are forbidden to disassembling in
gray area is shown as Fig.2 More maintenance fees may cost if the instrument
is damaged by forbidden operations. The parts even the whole instrument will
be scrapped.
PHB-3000 Hydraulic Brinell Hardness Tester 15
PHB-3000 Hydraulic Brinell Hardness Tester
www.txinstruments.com
www.txinstruments.com

PHB-3000 Hydraulic Brinell Hardness Tester 17
10 9
10 8
10 7
10 6
10 5
10 4
10 4
10 3
10 2
10 1
10 0
99.4
98.6
97.8
97.1
96.3
95.5
94.8
94.0
93.3
92.6
91.8
91.1
90.4
89.7
89.0
88.4
87.7
87.0
86.4
85.7
85.1
84.4
83.8
83.2
82.6
81.9
81.3
80.8
80.2
79.6
79.0
78.4
77.9
77.3
218
216
214
212
211
209
207
205
204
202
200
199
197
196
194
193
191
190
188
187
185
184
182
181
179
178
177
175
174
173
171
170
169
168
166
165
164
163
162
160
159
158
157
156
155
327
324
321
319
316
313
311
308
306
303
301
298
296
294
294
289
287
284
282
280
278
276
273
271
269
267
265
263
261
259
257
255
253
251
250
248
246
244
242
240
239
237
235
234
232
653
648
643
637
632
627
621
616
611
606
601
597
592
587
582
578
573
569
564
560
555
551
547
543
538
534
530
526
522
518
514
510
507
503
499
495
492
488
485
481
477
474
471
467
464
2. 40
2. 41
2. 42
2. 23
2. 44
2. 45
2. 46
2. 47
2. 48
2. 49
2. 50
2. 51
2. 52
2. 53
2. 54
2. 55
2. 56
2. 57
2. 58
2. 59
2. 60
2. 61
2. 62
2. 63
2. 64
2. 65
2. 66
2. 67
2. 68
2. 69
2. 70
2. 71
2. 72
2. 73
2. 74
2. 75
2. 76
2. 77
2. 78
2. 79
2. 80
2. 81
2. 82
2. 83
2. 84
1.200
1.205
1.210
1.215
1.220
1.225
1.230
1.235
1.240
1.245
1.250
1.255
1.260
1.265
1.270
1.275
1.280
1.285
1.290
1.295
1.300
1.305
1.310
1.315
1.320
1.325
1.330
1.335
1.340
1.345
1.350
1.355
1.360
1.365
1.370
1.375
1.380
1.385
1.390
1.395
1.400
1.405
1.410
1.415
1.420
30
15
10
Ball Diameter D/mm
29.42kN 3000
7.355kN 750
( )
( ) 14.71kN 1500( ) 9.807kN 1000( ) 4.903kN 500( )
5
2
0.102xF/D
Test Force F/N kg( )
5
Indentation Diameter D/mm
10
Brinell Hardness (HBW)
Table 1: Brinell Hardness Table
PHB-3000 Hydraulic Brinell Hardness Tester
Appendix 3:
1. The warranty period of this instrument is 15 months after it leaves the factory
(regardless the operation time).
2. Users should describe the problem in writing and send it to the agent or service
department of the manufacturer.
3. If the instrument is still in warranty period and the problem described is confirmed,
the manufacturer will repair it for free and the users do not have to pay any
maintenance cost. The instrument should be delivered to the manufacturer or its
authorized agent. The user is responsible for the freight.
4. The following situations are not included in the warranty range:
Inappropriate operation, natural losses, operation carelessness, chemical corrosion
and force majeure which go again to the rules presented in the operation manual,
packing and transportation notice operated by unauthorized users or other parties are
not included in the warranty range.
Warranty
PHB-3000 Hydraulic Brinell Hardness Tester
16
www.txinstruments.com
www.txinstruments.com

1. 65 0
1. 65 5
1. 66 0
1. 66 5
1. 67 0
1. 67 5
1. 68 0
1. 68 5
1. 69 0
1. 69 5
1. 70 0
1. 70 5
1. 71 0
1. 71 5
1. 72 0
1. 72 5
1. 73 0
1. 73 5
1. 74 0
1. 74 5
1. 75 0
1. 75 5
1. 76 0
1. 76 5
1. 77 0
1. 77 5
1. 78 0
1. 78 5
1. 79 0
1. 79 5
1. 80 0
1. 80 5
1. 81 0
1. 81 5
1. 82 0
1. 82 5
1. 83 0
1. 83 5
1. 84 0
1. 84 5
1. 85 0
1. 85 5
1. 86 0
1. 86 5
1. 87 0
3. 30
3. 31
3. 32
3. 33
3. 34
3. 35
3. 36
3. 37
3. 38
3. 39
3. 40
3. 41
3. 42
3. 43
3. 44
3. 45
3. 46
3. 47
3. 48
3. 49
3. 50
3. 51
3. 52
3. 53
3. 54
3. 55
3. 56
3. 57
3. 58
3. 59
3. 60
3. 61
3. 62
3. 63
3. 64
3. 65
3. 66
3. 67
3. 68
3. 69
3. 70
3. 71
3. 72
3. 73
3. 74
56 .8
56 .5
56 .1
55 .8
55 .4
55 .1
54 .8
54 .4
54 .1
53 .8
53 .4
53 .1
52 .8
52 .5
52 .2
51 .8
51 .5
51 .2
50 .9
50 .6
50 .3
50 .0
49 .7
49 .4
49 .2
48 .9
48 .6
48 .3
48 .0
47 .7
47 .5
47 .2
46 .9
46 .7
46 .4
46 .1
45 .9
45 .6
45 .4
45 .1
44 .9
44 .6
44 .4
44 .1
43 .9
11 4
11 3
11 2
11 2
11 1
11 0
11 0
10 9
10 8
10 8
10 7
10 6
10 6
10 5
10 4
10 4
10 3
10 2
10 2
10 1
10 1
10 0
99 .5
98 .9
98 .3
97 .7
97 .2
96 .6
96 .1
95 .5
95 .0
94 .4
93 .9
93 .3
92 .8
92 .3
91 .8
91 .2
90 .7
90 .2
89 .7
89 .2
88 .7
88 .2
87 .7
17 0
16 9
16 8
16 7
16 6
16 5
16 4
16 3
16 2
16 1
16 0
15 9
15 8
15 7
15 6
15 6
15 5
15 4
15 3
15 2
15 1
15 0
14 9
14 8
14 7
14 7
14 6
14 5
14 4
14 3
14 2
14 2
14 1
14 0
13 9
13 8
13 8
13 7
13 6
13 5
13 5
13 4
13 3
13 2
13 2
34 1
33 9
33 7
33 5
33 3
33 1
32 9
32 6
32 5
32 3
32 1
31 9
31 7
31 5
31 3
31 1
30 9
30 7
30 6
30 4
30 2
30 0
29 8
29 7
29 5
29 3
29 2
29 0
28 8
28 6
28 5
28 3
28 2
28 0
27 8
27 7
27 5
27 4
27 2
27 1
26 9
26 8
26 6
26 5
26 3
30 15 10
Ball Diameter D/mm
29.42kN 3000
7.355kN 750
( )
( ) 14.71kN 1500( ) 9.807kN 1000( ) 4.903kN 500( )
5
2
0.102xF/D
Test Force F/N kg( )
5
Indentation Diameter D/mm
10
Brinell Hardness (HBW)
PHB-3000 Hydraulic Brinell Hardness TesterPHB-3000 Hydraulic Brinell Hardness Tester 1918
76 .8
76 .2
75 .7
75 .1
74 .6
74 .1
73 .6
73 .0
72 .5
72 .0
71 .5
71 .0
70 .5
70 .1
69 .6
69 .1
68 .6
68 .2
67 .7
67 .3
66 .8
66 .4
65 .9
65 .5
65 .0
64 .6
64 .2
63 .8
63 .3
62 .9
62 .5
62 .1
61 .7
61 .3
60 .9
60 .5
60 .1
59 .8
59 .4
59 .0
58 .6
58 .3
57 .9
57 .5
57 .2
154
152
151
150
149
148
147
146
145
144
143
142
141
140
139
138
137
136
135
135
134
133
132
131
130
129
128
128
127
126
125
124
123
123
122
121
120
120
119
118
117
117
116
115
114
23 0
22 9
22 7
22 5
22 4
22 2
22 1
21 9
21 8
21 6
21 5
21 3
21 2
21 0
20 9
20 7
20 6
20 5
20 3
20 2
20 0
19 9
19 8
19 6
19 5
19 4
19 3
19 1
19 0
18 9
18 8
18 6
18 5
18 4
18 3
18 2
18 0
17 9
17 8
17 7
17 6
17 5
17 4
17 3
17 2
461
457
454
451
448
444
441
438
435
432
429
426
423
420
417
415
412
409
406
404
401
398
395
393
390
388
385
383
380
378
375
373
370
368
366
363
360
359
356
354
352
350
347
345
343
1.425
1.430
1.435
1.440
1.445
1.450
1.455
1.460
1.465
1.470
1.475
1.480
1.485
1.490
1.495
1.500
1.505
1.510
1.515
1.520
1.525
1.530
1.535
1.540
1.545
1.550
1.555
1.560
1.565
1.570
1.575
1.580
1.585
1.590
1.595
1.600
1.605
1.610
1.615
1.620
1.625
1.630
1.635
1.640
1.645
2. 85
2. 86
2. 87
2. 88
2. 89
2. 90
2. 91
2. 92
2. 93
2. 94
2. 95
2. 96
2. 97
2. 98
2. 99
3. 00
3. 01
3. 02
3. 03
3. 04
3. 05
3. 06
3. 07
3. 08
3. 09
3. 10
3. 11
3. 12
3. 13
3. 14
3. 15
3. 16
3. 17
3. 18
3. 19
3. 20
3. 21
3. 22
3. 23
3. 24
3. 25
3. 26
3. 27
3. 28
3. 29
30 15 10
Ball Diameter D/mm
29.42kN 3000
7.355kN 750
( )
( ) 14.71kN 1500( ) 9.807kN 1000( ) 4.903kN 500( )
5
2
0.102xF/D
Test Force F/N kg( )
5
Indentation Diameter D/mm
10
Brinell Hardness (HBW)
www.txinstruments.com
www.txinstruments.com

34 .4
34 .2
34 .1
33 .9
33 .7
33 .6
33 .4
33 .2
33 .1
32 .9
32 .8
32 .6
32 .4
32 .3
32 .1
32 .0
31 .8
31 .7
31 .5
31 .4
31 .2
31 .1
30 .9
30 .8
30 .6
30 .5
30 .3
30 .2
30 .0
29 .9
29 .8
29 .6
29 .5
29 .3
29 .2
29 .1
28 .9
28 .8
28 .7
28 .5
28 .4
28 .3
28 .1
28 .0
27 .9
68 .8
68 .5
68 .2
67 .8
67 .5
67 .1
66 .8
66 .5
66 .2
65 .8
65 .5
65 .2
64 .9
64 .6
64 .2
63 .9
63 .6
63 .3
63 .0
62 .7
62 .4
62 .1
61 .8
61 .5
61 .2
60 .9
60 .6
60 .4
60 .1
59 .8
59 .5
59 .2
59 .0
58 .7
58 .4
58 .1
57 .9
57 .6
57 .3
57 .1
56 .8
56 .5
56 .3
56 .0
55 .8
103
103
102
102
101
101
100
99 .7
99 .2
98 .8
98 .3
97 .8
97 .3
96 .8
96 .4
95 .9
95 .4
95 .0
94 .5
94 .1
93 .6
93 .2
92 .7
92 .3
91 .8
91 .4
91 .0
90 .6
60 .1
89 .7
89 .3
88 .9
88 .4
88 .0
87 .6
87 .2
86 .8
86 .4
86 .0
85 .6
85 .2
84 .8
84 .4
84 .0
83 .6
207
205
204
203
202
201
200
199
198
198
197
196
195
194
193
192
191
190
189
188
187
186
185
185
184
183
182
181
180
179
179
178
177
176
175
174
174
173
172
171
170
170
169
168
167
2. 10 0
2. 10 5
2. 11 0
2. 11 5
2. 12 0
2. 12 5
2. 13 0
2. 13 5
2. 14 0
2. 14 5
2. 15 0
2. 15 5
2. 16 0
2. 16 5
2. 17 0
2. 17 5
2. 18 0
2. 18 5
2. 19 0
2. 19 5
2. 20 0
2. 20 5
2. 21 0
2. 21 5
2. 22 0
2. 22 5
2. 23 0
2. 23 5
2. 24 0
2. 24 5
2. 25 0
2. 25 5
2. 26 0
2. 26 5
2. 27 0
2. 27 5
2. 28 0
2. 28 5
2. 29 0
2. 29 5
2. 30 0
2. 30 5
2. 31 0
2. 31 5
2. 32 0
4. 20
4. 21
4. 22
4. 23
4. 24
4. 25
4. 26
4. 27
4. 28
4. 29
4. 30
4. 31
4. 32
4. 33
4. 34
4. 35
4. 36
4. 37
4. 38
4. 39
4. 40
4. 41
4. 42
4. 43
4. 44
4. 45
4. 46
4. 47
4. 48
4. 49
4. 50
4. 51
4. 52
4. 53
4. 54
4. 55
4. 56
4. 57
4. 58
4. 59
4. 60
4. 61
4. 62
4. 63
4. 64
30 15 10
Ball Diameter D/mm
29.42kN 3000
7.355kN 750
( )
( ) 14.71kN 1500( ) 9.807kN 1000( ) 4.903kN 500( )
5
2
0.102xF/D
Test Force F/N kg( )
5
Indentation Diameter D/mm
10
Brinell Hardness (HBW)
PHB-3000 Hydraulic Brinell Hardness TesterPHB-3000 Hydraulic Brinell Hardness Tester 2120
43 .6
43 .4
43 .1
42 .9
42 .7
42 .4
42 .2
42 .0
41 .7
41 .5
41 .3
41 .1
40 .9
40 .6
40 .4
40 .2
40 .0
39 .8
39 .6
39 .4
39 .1
38 .9
38 .7
38 .5
39 .3
38 .1
37 .9
37 .7
37 .5
37 .3
37 .1
37 .0
36 .8
36 .6
36 .4
36 .2
36 .0
35 .8
35 .7
35 .5
35 .3
35 .1
34 .9
34 .8
34 .6
87 .2
86 .8
86 .3
85 .8
85 .3
84 .9
84 .4
83 .9
83 .5
83 .0
82 .6
82 .1
81 .7
81 .3
80 .8
80 .4
80 .0
79 .5
79 .1
78 .7
78 .3
77 .9
77 .5
77 .1
76 .7
76 .3
75 .9
75 .5
75 .1
74 .7
74 .3
73 .9
73 .5
73 .2
72 .8
72 .4
72 .0
71 .7
71 .3
71 .0
70 .6
70 .2
69 .9
69 .5
69 .2
131
130
129
129
128
127
127
126
125
125
124
123
123
122
121
121
120
119
119
118
117
117
116
116
115
114
114
113
113
112
111
111
111
110
109
109
108
108
107
106
106
105
105
104
104
262
260
259
257
256
255
253
252
250
249
248
246
245
244
242
241
240
239
237
236
235
234
232
231
230
229
228
226
225
224
223
222
221
216
218
217
216
215
214
213
212
211
210
209
208
1.875
1.880
1.885
1.890
1.895
1.900
1.905
1.910
1.915
1.920
1.925
1.930
1.935
1.940
1.945
1.950
1.955
1.960
1.965
1.970
1.975
1.980
1.985
1.990
1.995
2.000
2.005
2.010
2.015
2.020
2.025
2.030
2.035
2.040
2.045
2.050
2.055
2.060
2.065
2.070
2.075
2.080
2.085
2.090
2.095
3. 75
3. 76
3. 77
3. 78
3. 79
3. 80
3. 81
3. 82
3. 83
3. 84
3. 85
3. 86
3. 87
3. 88
3. 89
3. 90
3. 91
3. 92
3. 93
3. 94
3. 95
3. 96
3. 97
3. 98
3. 99
4. 00
4. 01
4. 02
4. 03
4. 04
4. 05
4. 06
4. 07
4. 08
4. 09
4. 10
4. 11
4. 12
4. 13
4. 14
4. 15
4. 16
4. 17
4. 18
4. 19
30 15 10
Ball Diameter D/mm
29.42kN 3000
7.355kN 750
( )
( ) 14.71kN 1500( ) 9.807kN 1000( ) 4.903kN 500( )
5
2
0.102xF/D
Test Force F/N kg( )
5
Indentation Diameter D/mm
10
Brinell Hardness (HBW)
www.txinstruments.com www.txinstruments.com

5.10
5.11
5.12
5.13
5.14
5.15
5.16
5.17
5.18
5.19
5.20
5.21
5.22
5.23
5.24
5.25
5.26
5.27
5.28
5.29
5.30
5.31
5.32
5.33
5.34
5.35
5.36
5.37
5.38
5.39
5.40
5.41
5.42
5.43
5.44
5.45
5.46
5.47
5.48
5.49
5.50
5.51
5.52
5.53
5.54
2.550
2.555
2.560
2.565
2.570
2.575
2.580
2.585
2.590
2.595
2.600
2.605
2.610
2.615
2.620
2.625
2.630
2.635
2.640
2.645
2.650
2.655
2.660
2.665
2.670
2.675
2.680
2.685
2.690
2.695
2.700
2.705
2.710
2.715
2.720
2.725
2.730
2.735
2.740
2.745
2.750
2.755
2.760
2.765
2.770
137
136
135
135
134
134
133
133
132
132
131
130
130
129
129
128
128
127
127
126
126
125
125
124
124
123
123
122
122
121
121
120
120
119
119
118
118
117
117
116
116
115
115
114
114
68.3
68.0
67.7
67.4
67.1
66.9
66.6
66.3
65.8
65.5
65.2
64.9
64.7
64.4
64.1
63.9
63.6
63.3
63.1
62.8
62.6
62.3
62.1
61.8
61.5
61.3
61.0
60.8
60.6
60.3
60.1
59.8
59.6
59.3
59.1
58.9
58.6
58.4
58.2
57.9
57.7
57.5
57.2
57.0
45 .5
45 .3
45 .1
45 .0
44 .8
44 .6
44 .4
44 .2
44 .0
43 .8
43 .7
43 .5
43 .3
43 .1
42 .9
42 .8
42 .6
42 .4
42 .2
42 .1
41 .9
41 .7
41 .5
41 .4
41 .2
41 .0
40 .9
40 .7
40 .5
40 .4
40 .2
40 .0
39 .9
39 .7
39 .6
39 .4
39 .2
39 .1
38 .9
38 .8
38 .6
38 .5
38 .3
38 .2
38 .0
22.8
22.7
22.6
22.5
22.4
22.3
22.2
22.1
22.0
21.9
21.8
21.7
21.6
21.6
21.5
21.4
21.3
21.2
21.1
21.0
20.9
20.9
20.8
20.7
20.6
20.5
20.4
20.3
20.3
20.2
20.1
20.0
19.9
19.9
19.8
19.7
19.6
19.5
19.5
19.4
19.3
19.2
19.2
19.1
19.0
30 15 10
Ball Diameter D/mm
29.42kN 3000
7.355kN 750
( )
( ) 14.71kN 1500( ) 9.807kN 1000( ) 4.903kN 500( )
5
2
0.102xF/D
Test Force F/N kg( )
5
Indentation Diameter D/mm
10
Brinell Hardness (HBW)
PHB-3000 Hydraulic Brinell Hardness TesterPHB-3000 Hydraulic Brinell Hardness Tester 23
22
27 .8
27 .6
27 .5
27 .4
27 .3
27 .1
27 .0
26 .9
26 .8
26 .6
26 .5
26 .4
26 .3
26 .2
26 .1
25 .9
25 .8
25 .7
25 .6
25 .5
25 .4
25 .3
25 .1
25 .0
24 .9
24 .8
24 .7
24 .6
24 .5
24 .4
24 .3
24 .2
24 .1
24 .0
23 .9
23 .8
23 .7
23 .6
23 .5
23 .4
23 .3
23 .2
23 .1
23 .0
22 .9
55 .5
55 .3
55 .0
54 .8
54 .5
54 .3
54 .3
53 .8
53 .5
53 .3
53 .0
52 .8
52 .6
52 .3
52 .1
51 .9
51 .6
51 .4
51 .2
51 .0
50 .7
50 .5
50 .3
50 .1
49 .8
49 .6
49 .4
49 .2
49 .0
48 .8
48 .6
48 .3
48 .1
47 .9
47 .7
47 .5
47 .3
47 .1
46 .9
46 .7
46 .5
46 .3
46 .1
45 .9
45 .7
83 .3
82 .9
82 .5
82 .1
81 .8
81 .4
81 .0
80 .7
80 .3
79 .9
79 .6
79 .2
78 .9
78 .5
78 .2
77 .8
77 .5
77 .1
76 .8
76 .4
76 .1
75 .8
75 .4
75 .1
74 .8
74 .4
74 .1
73 .8
73 .5
73 .2
72 .8
72 .5
72 .2
71 .9
71 .6
71 .3
71 .0
70 .7
70 .4
70 .1
69 .8
69 .5
69 .2
68 .9
69 .6
16 7
16 6
16 5
16 4
12 4
16 3
16 2
16 1
16 1
16 0
15 9
15 8
15 8
15 7
15 6
15 6
15 5
15 4
15 4
15 3
15 2
15 2
15 1
15 0
15 0
14 9
14 8
14 8
14 7
14 6
14 6
14 5
14 4
14 4
14 3
14 3
14 2
14 1
14 1
14 0
14 0
13 9
13 8
13 8
13 7
2. 32 5
2. 33 0
2. 33 5
2. 34 0
2. 34 5
2. 35 0
2. 35 5
2. 36 0
2. 36 5
2. 37 0
2. 37 5
2. 38 0
2. 38 5
2. 39 0
2. 39 5
2. 40 0
2. 40 5
2. 41 0
2. 41 5
2. 42 0
2. 42 5
2. 43 0
2. 43 5
2. 44 0
2. 44 5
2. 45 0
2. 45 5
2. 46 0
2. 46 5
2. 47 0
2. 47 5
2. 48 0
2. 48 5
2. 49 0
2. 49 5
2. 50 0
2. 50 5
2. 51 0
2. 51 5
2. 52 0
2. 52 5
2. 53 0
2. 53 5
2. 54 0
2. 54 5
4. 65
4. 66
4. 67
4. 68
4. 69
4. 70
4. 71
4. 72
4. 73
4. 74
4. 75
4. 76
4. 77
4. 78
4. 79
4. 80
4. 81
4. 82
4. 83
4. 84
4. 85
4. 86
4. 87
4. 88
4. 89
4. 90
4. 91
4. 92
4. 93
4. 94
4. 95
4. 96
4. 97
4. 98
4. 99
5. 00
5. 01
5. 02
5. 03
5. 04
5. 05
5. 06
5. 07
5. 08
5. 09
30 15 10
Ball Diameter D/mm
29.42kN 3000
7.355kN 750
( )
( ) 14.71kN 1500( ) 9.807kN 1000( ) 4.903kN 500( )
5
2
0.102xF/D
Test Force F/N kg( )
5
Indentation Diameter D/mm
10
Brinell Hardness (HBW)
www.txinstruments.com
www.txinstruments.com

Table 2: Testing Accuracy of Brinell Tester
Hardness Value of Standard
Block
(HBW)
Allowable Max.
Repeatability of Hardness
Testers (mm)
Allowable Max.
Error of Hardness Testers /%
(relative to H)
≤125
125<HBW≤225
>225
0.025
±3
±2.5
±2
0.030
0.020
d
d
d
d-
Hardness Symbol Ball Diameter D/mm Test Force F/kg 2
0.102ⅹF/D
HBW 10/3000
HBW 10/1500
HBW 10/1000
HBW 10/500
HBW 5/750
HBW 5/250
HBW 5/125
10
10
10
10
5
5
5
30 0 0
15 0 0
10 0 0
500
750
250
125
30
15
10
5
30
10
5
In accordance with Intemational Standard ISO6506-1999
Note: The hardness symbol HBW 10/3000 denotes using a carbide ball indenter with 10mm diameter
and applying 3000kg test force.
Table 3: Testing Conditions of Brinell Hardness
steel
Ca s t iro n
Bronze
Material
≥14 0
14 0<
20 0>
80-200
16-80
Hardness(HBW) Ball Diameter
D/mm
2
0.102F/D
Test Force F/kg
10
10
10
10
10
5
3000
1000
500
3000
750
3000
1000
30
10
5
30
30
10
In accordance with Intemational Standard ISO6506-1999
mean diameter of indentations
Table 4: Selection of Testing Conditions for Brinell Hardness Testers
Brass, red copper,
Aluminum alloy
Red copper, Aluminum
alloy, aluminum
PHB-3000 Hydraulic Brinell Hardness TesterPHB-3000 Hydraulic Brinell Hardness Tester 2524
5.55
5.56
5.57
5.58
5.59
5.60
5.61
5.62
5.63
5.64
5.65
5.66
5.67
5.68
5.69
5.70
5.71
5.72
5.73
5.74
5.75
5.76
5.77
5.78
5.79
5.80
5.81
5.82
5.83
5.84
5.85
5.86
5.87
5.88
5.89
5.90
5.91
5.92
5.93
5.94
5.95
5.96
5.97
5.98
5.99
6.00
2.775
2.780
2.785
2.790
2.795
2.800
2.805
2.810
2.815
2.820
2.825
2.830
2.835
2.840
2.845
2.850
2.855
2.860
2.865
2.870
2.875
2.880
2.885
2.890
2.895
2.900
2.905
2.910
2.915
2.920
2.925
2.930
2.935
2.940
2.945
2.950
2.955
2.960
2.965
2.970
2.975
2.980
2.985
2.990
2.995
3.000
56 .9
56 .6
56 .3
56 .1
55 .9
55 .7
55 .5
55 .2
55 .0
54 .8
54 .6
54 .4
54 .2
54 .0
53 .7
53 .5
53 .3
53 .1
52 .9
52 .7
52 .5
52 .3
52 .1
51 .9
51 .7
51 .5
51 .3
51 .1
50 .9
50 .7
50 .5
50 .3
50 .2
50 .0
49 .8
49 .6
49 .4
49 .2
49 .0
48 .8
48 .7
48 .5
48 .3
48 .1
47 .9
47 .7
37 .9
37 .7
37 .6
37 .4
37 .3
37 .1
37 .0
36 .8
36 .7
36 .5
36 .4
36 .3
36 .1
36 .0
35 .8
35 .7
35 .6
35 .4
35 .3
35 .1
35 .0
34 .9
34 .7
34 .6
34 .5
34 .3
34 .2
34 .1
33 .9
33 .8
33 .7
33 .6
33 .4
33 .3
33 .2
33 .1
32 .9
32 .8
32 .7
32 .6
32 .4
32 .3
32 .2
32 .1
32 .0
31 .8
18 .9
18 .9
18 .8
18 .7
18 .6
18 .6
18 .5
18 .4
18 .3
18 .3
18 .2
18 .1
18 .1
18 .0
17 .9
17 .8
17 .8
17 .7
17 .6
17 .6
17 .5
17 .4
17 .4
17 .3
17 .2
17 .2
17 .1
17 .0
17 .0
16 .9
16 .8
16 .8
16 .7
16 .7
16 .6
16 .5
16 .5
16 .4
16 .3
16 .3
16 .2
16 .2
16 .1
16 .0
16 .0
15 .9
11 4
11 3
11 3
11 2
11 2
11 1
11 1
11 0
11 0
11 0
10 9
10 9
10 8
10 8
10 7
10 7
10 7
10 6
10 6
10 5
10 5
10 5
10 4
10 4
10 3
10 3
10 3
10 2
10 2
10 1
10 1
10 1
10 0
99.9
99.5
99.2
98.8
98.4
98.0
97.7
97.3
96.9
96.6
96.2
95.9
95.5
30 15 10
Ball Diameter D/mm
29.42kN 3000
7.355kN 750
( )
( ) 14.71kN 1500( ) 9.807kN 1000( ) 4.903kN 500( )
5
2
0.102xF/D
Test Force F/N kg( )
5
Indentation Diameter D/mm
10
Brinell Hardness (HBW)
www.txinstruments.com
www.txinstruments.com

Material Brinell Hardness(HBW) 2
Tensile Strength(MN/m )
Steel
Quenched brass,
quenched bronze
σ≈0. 3 63H B W×10
b
σ≈0. 3 43H B W×10
b
σ≈0. 4 0HB W×1 0
b
σ≈0. 5 5HB W×1 0
b
σ≈0. 2 6HB W×1 0
b
>17 5
12 5 -17 5
Table 5: Conversion of Brinell Hardness and Tensile Strength
Annealed brass,
annealed bronze
Cast aluminum alloy
PHB-3000 Hydraulic Brinell Hardness Tester
26
www.txinstruments.com
Popular Test Equipment manuals by other brands

Hanna Instruments
Hanna Instruments HALO2 HI9810452 instruction manual
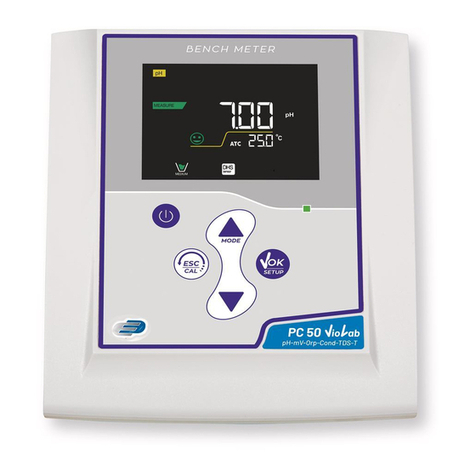
Carl Roth
Carl Roth VioLab 50 Series instruction manual
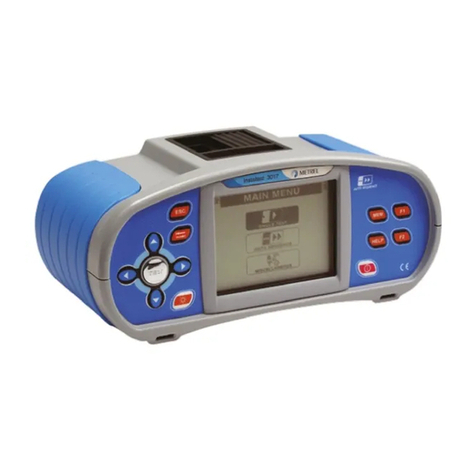
METREL
METREL Instaltest 3017 Short instructions
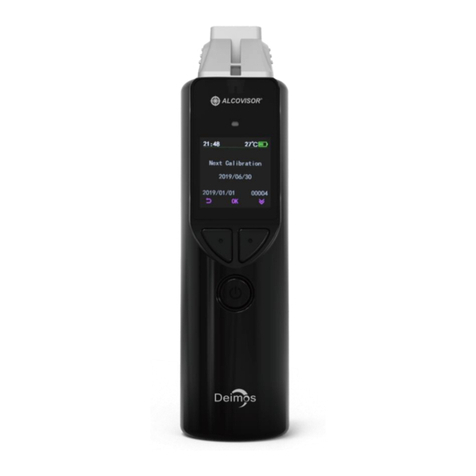
Alcovisor
Alcovisor Deimos instruction manual
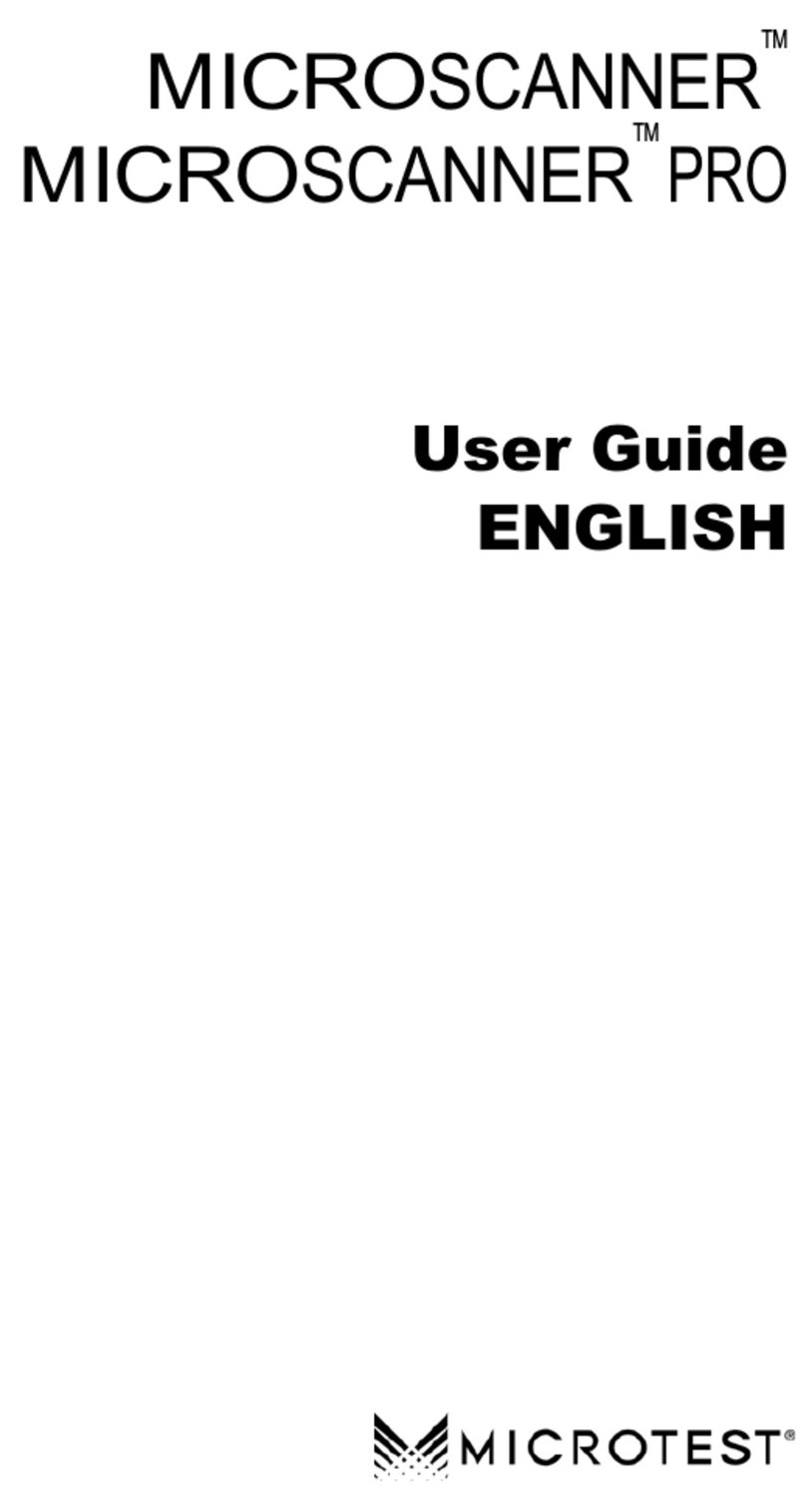
Microtest
Microtest MICROSCANNER user guide
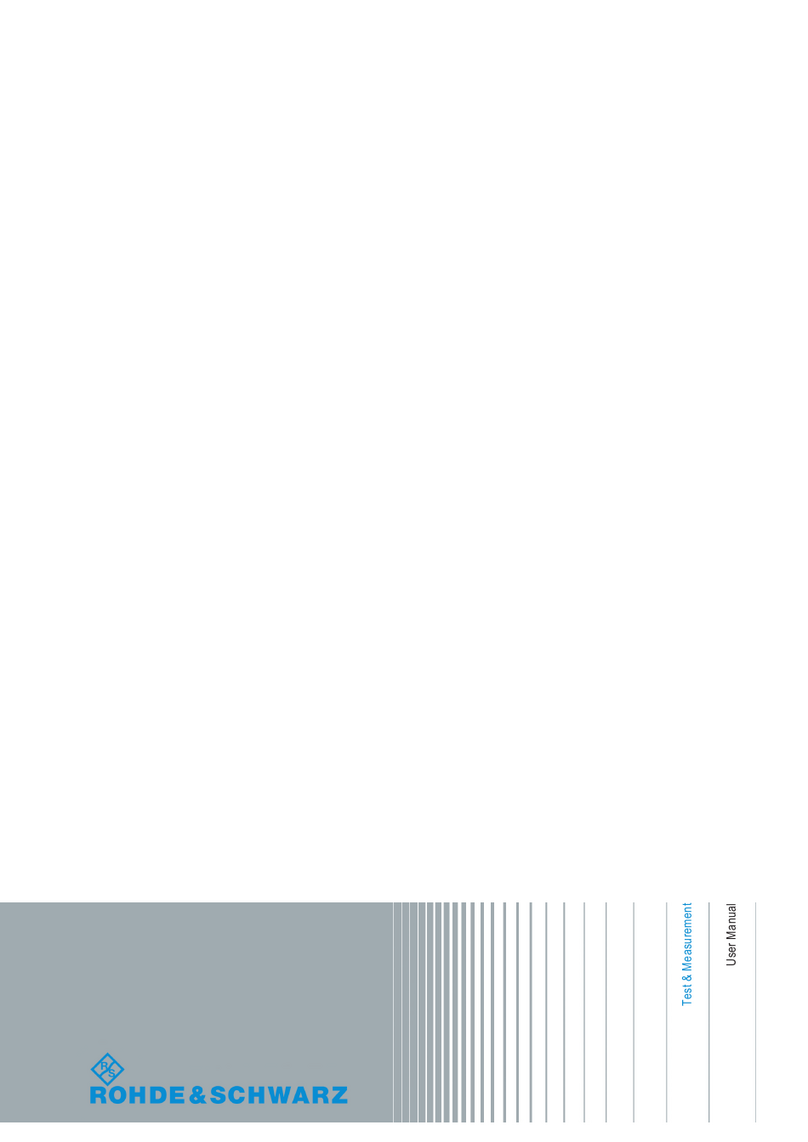
Rohde & Schwarz
Rohde & Schwarz CMW-KM8 Series user manual