Utile L95HP Guide

INSTALLATION
OPERATION
MAINTENANCE INSTRUCTIONS
MODELS
L95HP - 175HP
ROTARY BLOWERS,
VACUUM PUMPS
AND GAS BOOSTERS
THE UTILE ENGINEERING CO. LTD
IRTHLINGBOROUGH, NORTHAMPTONSHIRE NN9 5UG, ENGLAND
TEL: +44 (0) 1933 650216 FAX: +44 (0) 1933 652738
IC 153

This booklet has been written to enable you to obtain the best possible service from your
Rotary Pump. We ask you to give it to the person responsible for the installation and
operation of this machine and not just file it away.
The normal routine of running the machine is very simple. If it is carried out strictly at all times, many years
of trouble free service can be expected. We emphasise two points of paramount importance:
1: FILTRATION OF THE INCOMING GAS
2: LUBRICATION - use only SHELL RIMULA X 15W/40 oil or equivalent.
STORAGE:
If the unit is not used immediately, the pump and all adjoining equipment should be placed in a clean, dry
storage area protected from the weather. The intake and discharge connections must be kept covered at all
times, as foreign matter could enter the pump and cause serious damage.
INSTALLATION:
LOCATION:
The unit should be installed in a clean, dry, well ventilated area. Ample space and facilities should be
provided for ease of servicing and inspection.
FOUNDATION:
Simple slab type foundations, designed for static loadings only are satisfactory. The foundations should raise
the machine to a reasonable height above the floor for convenient service and inspection.
PIPEWORK:
If the machine is not required for immediate use, the intake and discharge connections must be covered.
Suction and discharge piping should incorporate flexible pipe couplings, be adequately supported and aligned
correctly to prevent strain being transmitted to the pump.
Connecting pipework on the intake side of the machine must be thoroughly cleaned to remove internal rust
and scale. Use PTFE tape for making joints since surplus from jointing compounds will damage the blades if
drawn into the pump.
The pipe diameter must not be smaller than the intake of the machine and for long runs we recommend
increasing this size. Long bends are preferable where changes in direction have to be made. Ample support
should be provided. Great care should be taken when making joints, especially on vacuum pumps and gas
boosters.
When the machine is delivering into or exhausting from a receiver, or working with a system having a large
storage capacity, a non-return valve must be fitted in the pipeline. In the majority of cases it is essential to fit a
vacuum line filter on the intake of vacuum pumps to prevent pipe scale, oil, water, dust and other harmful
matter from being drawn in.
PRE - START-UP CHECKS AND COMMISSIONING
Manually rotate the pump shaft through a few revolutions to ensure free running.
Remove drive belts and start the motor to ensure that direction of rotation is correct. Replace belts and re-
tension. Recommended procedure to set belt tension is as follows:
Measure span of belts between tangent points of
the two pulleys. For every 1" (25.4mm) between
these points the belt should deflect 1/64" (0.4mm)
when subjected to a central load of approximately
12lbs (5.5kgs).

Fill the lubricator reservoir with SHELL RIMULA X 15W/40 OIL or equivalent. Oil feed pipes should be
primed prior to initial start.
The lubricator pump is pre-set to the required drip rate and there should be no need to adjust.
If the system is to be pressure tested all gauges and pressure switches must be isolated or removed. Maximum
purge or pressure test is 2.0 bar g.
START-UP - GAS BOOSTERS ONLY
Some boosters are fitted with a manual bypass, which must be fully opened before start-up.
Start the drive motor.
When full speed is reached, slowly close the manual bypass valve.
OPERATING AND MAINTENANCE
Daily, check the oil feed through indicators. Fill oil tank.
Inspect the filter fitted to blowers and the inlet pipeline strainer fitted to gas boosters, renew the element after
the first 100 running hours, and then every 500 running hours clean and replace. Failure to carry out this
simple maintenance will result in loss of performance and overheating.
When a vacuum line filter is used in conjunction with a vacuum pump it is essential to regularly clean the
element and renew when necessary.
If the pressure or vacuum relief valve require altering then we recommend that you consult Utile Engineering
before proceeding.
After the initial running in period, check the belt tension. Belt squeal denotes a loose belt that requires re-
tensioning.
Check the pump internally for wear every 10,000 running hours. (See INSPECTION AND SERVICE)
The blade depth should be checked every 5,000 for wear and renewed if the rubbing tips have worn so as to
reduce the depth to 2 5/8" (67mm). (See CHECK BLADE WEAR).
If adjustment of oil pump is necessary then refer to LUBRICATOR MAINTENANCE.
MAINTENANCE OF ANCILLARY EQUIPMENT
Drain valve should be opened at weekly intervals, when the system is not pressurised.
OIL/MOISTURE SEPARATOR
The only maintenance required with this type of separator is to clean the filter element with a suitable solvent
to remove any build up of solids or grease.
Also, the drain valve should be cleaned at monthly intervals when the system is not pressurised.
CENTRIFUGAL SEPARATOR
Due to the design of the separator the amount of maintenance required is minimal. At regular intervals, drain
the separator, when the system is not pressurised.
VALVES
Keep all intake and discharge valves clean and check that they function correctly, close tightly and do not
stick.
To keep in line with the above recommendations the following maintenance guide should be adhered to:
Daily Checks Weekly checks
Check the lubricator drip rate. Check belt tension and wear.
Check oil tank level. Fill if necessary If applicable, run the standby pump for a few minutes.
Regular checks Yearly checks
Inspect the blades for wear (every 5000 running hours) Clean the lubricator, oil lines and all valves.
Drain all ancillary equipment. Clean internally filters and elements.
Check valves are functioning correctly.

1: TO CHECK BLADE WEAR
1.1 Carry out the following procedure after the first 2,000 running hours and repeat very 5,000-hour interval.
Record all measurements.
1.2 With the pump stationary and without pressure in the system, remove the eyebolt (44) and insert into the
hole beneath a pointed measuring rod 6mm dia x 150mm long or alternatively a pencil until contact is
made with the rotor. Slowly rotate the shaft by hand until the rod drops onto the tip of a blade. Measure
the amount of movement and renew the blades if this exceeds 6mm. Replace the eyebolt.
2: INSPECTION AND SERVICE
Inspection commences with the dismantling of the drive end, after removal of drive belts and oil pipes.
2.1 Take off the drive pulley (45), oil pump guard (13), drive belt (48) and drive pulley (46). Slacken clamp
screw (33) in oil pump support plate (12) and remove complete with oil pump from locating boss on
drive end coverplate (2).
2.2 Undo four bolts (31) and remove end cap (4) complete with shaft seal (21). Remove six bolts (29) and
withdraw coverplate (2) complete with outer race of roller bearing (23) and seal (22).
2.3 Measure and note the thickness of the gaskets (41) fitted between the coverplate (2) and the cylinder (1).
2.4 The blades (7) can now be withdrawn for inspection.
Check the blades for lamination, chipping or charring on their rubbing edges and for concave side wear.
For any wear other than polished surfaces or if the blade depth has reduced to 67mm or below then
replace the blades.
When fitting new blades, make sure they slide freely in their slots and if necessary remove high spots
with fine emery cloth. Lightly smear the blade surfaces with oil before re-assembly.
2.5 Inspect the visible part of the cylinder bore and rotor for any signs of excessive wear or scuffing and for
excessive slot wear. If there is any sign of cylinder rubbing completely dismantle the machine. Factory
reconditioning is recommended, but if the work has to be carried out on site, we advise you most strongly
to consult our Service Department for advice.
During the inspection, determine if the correct oil is being used. Bearings, cylinder wall, rotor/shaft
assembly and blades should show a polished surface with a light film of oil. Hard baked deposits indicate
inferior oil, dirt or excessive temperature.
3: RE-ASSEMBLY AFTER BLADE INSPECTION/RENEWAL
Re-assemble in reverse order taking note of the following points:
3.1 If coverplate gaskets have been replaced it is essential that they are the same thickness as the originals,
otherwise clearances will be affected and could cause serious damage. Lightly smear with oil before
replacing.
4: CYLINDER RENEWAL
With the drive end coverplate (2) already removed the next stage is to withdraw the rotor complete with the
rear end coverplate.
4.1 Remove fancowl (10) and fan (9).
4.2 Undo four bolts (31) and remove end cap (5) complete with shaft seal (21).
4.3 Remove six bolts (29) and withdraw coverplate (2) complete with rotor. Measure and record the
thickness of the rear end coverplate gaskets.
The cylinder can now be replaced or rebored.
4.4 When reboring the cylinder the maximum allowable increase in diameter is 0.8mm to give a final bore of
185.0mm. CONTACT WORKS FOR APPROPRIATE ASSEMBLY INSTRUCTIONS IN THIS
CASE.

5: REMOVAL OF BEARINGS AND SEALS
5.1 Withdraw the outer race of the roller bearing from the drive end coverplate, renew if the bearing shows
any signs of wear or pitting. To remove the inner race of the bearing, first remove the circlip (25)
from its groove then slip off the retaining washer (28), then use a two leg pulley drawer to pull the inner
race off the shaft.
5.2 At the rear end undo four bolts (31) and remove end cap (5) complete with shaft seal (21). Pull coverplate
(2) complete with ball bearing (55) and seal (22) from shaft using a two-leg pulley drawer.
5.3 The ball bearing can now be removed for inspection.
5.4 Examine the bearing seals (22) and renew if the wiping lips are worn or damaged.
5.5 Also examine the seal sleeves (11) for wear and replace if necessary. Using a depth gauge accurately
measure and record the width of each seal ring. These are retained on the shaft by an adhesive and are
removed by machining in a lathe with the shaft between centres.
6: RE-ASSEMBLY PROCEDURE
This section only applies when using original bore size or replacement cylinder. Before commencing re-
assembly ensure that all components are perfectly clean and oilways are clear.
The correct clearances for this machine are:
Total combined clearance -
Drive end coverplate/rotor
Rear end coverplate/rotor - 0.25mm / 0.31mm
Rotor/cylinder - 0.10mm / 0.13mm
6.1 Grind replacement seal sleeves to the width of the originals and locate firmly against the rotor side faces
using Loctite 648 adhesive or equivalent.
Commence at rear (ball bearing) end.
6.2 Press seal and ball bearing into coverplate.
6.3 Lay the rotor/shaft assembly on the bottom of the cylinder.
6.4 Fit coverplate assembly onto rotor/shaft, secure in place with retaining washer and circlip.
6.5 Fit new 'O' rings in the coverplate grooves.
Lightly smear coverplate gaskets with grease and fit over coverplate spigot.
6.6 Assemble coverplate to the cylinder ensuring location dowels are replaced.
6.7 Replace endcap, shaft seal and endcap gasket.
6.9 Refit fan and fancowl.
6.10Refit sliding blades after lightly smearing with oil and removing any high spots with fine emery cloth.
Re-assemble drive (roller bearing) end.
6.11Press inner race of roller bearing onto shaft.
6.12Refit outer race and seal in coverplate.
6.13Assemble onto cylinder ensuring correct thickness of gaskets and location dowels are replaced.
6.14Secure in place with retaining washer and circlip.
6.15With gasket in position fit endcap onto coverplate.
Check that the shaft rotates freely by hand before refitting oil pump assembly and pipes.

7: LUBRICATOR MAINTENANCE
Prime all oil pipes prior to initial start and every time compressor is dismantled for service.
At least every year, or if the machine has been out of use for a long period, the oil pump must be thoroughly
flushed out with petrol/kerosene to clear any oil residues that may have solidified in the control ducts.
8: OIL PUMP ADJUSTMENT
The pump is adjusted to the correct flow rate when
despatched from our works. If it is found necessary to
alter the oil feed then proceed as follows:
1: Remove the cover (1) to expose the
two pistons (2).
2: Slacken off the locknuts (3) and adjust
the feed as required.
To increase the flow, turn the two
adjusting screws (4) clockwise, or
anti-clockwise to decrease.
9: OIL FEED RATES
The oil feed rates per sight glass are as follows:
1: Coverplates - 6 Drops/min - L95HP - L130HP
2: Coverplates - 8 Drops/min - L175HP
When ordering spares always quote the machine serial number.

PART NUMBER
ITEM DESCRIPTION L 95HP L 130HP L 175HP QTY
1 CYLINDER S 8500/1 S 8500/1 S 8501/1 1
2 COVERPLATE - DRIVE END S 8502/2 S 8502/2 S 8502/2 1
3 COVERPLATE - REAR END S 8502/1 S 8502/1 S 8502/1 1
4 END CAP - DRIVE END S 8503 S 8503 S 8503 1
5 END CAP - REAR END S 8503 S 8503 S 8503 1
6 ROTOR AND SHAFT ASSEMBLY S 13026/1 S 13026/2 S 13026/3 1
7 BLADE S 8797/1 S 8797/2 S 8797/3 5
8 FLANGE S 1186/2 S 1186/2 S 8506 2
9 FAN S 8185/3 S 8185/3 S 8185/3 1
10 FANCOWL S 8505 S 8505 S 8505 1
11 SEAL SLEEVE S 8511 S 8511 S 8511 2
12 SUPPORT PLATE S 8680 S 8680 S 8680 1
13 GUARD S 8681 S 8681 S 8681 1
14 HOUSING - BEKA OIL PUMP S 8687 S 8687 S 8687 1
15 SHAFT - BEKA OIL PUMP S 8683 S 8683 S 8683 1
16 END CAP - BEKA OIL PUMP S 8688 S 8688 S 8688 1
17 GUARD SUPPORT - BEKA OIL PUMP S 7061 S 7061 S 7061 1
18 SUPPORT BAR S 8689 S 8689 S 8689 1
19 OIL DRIP INDICATOR S 8899 S 8899 S 8899 2
20 BEKA OIL PUMP T 1013 T 1013 T 1013 1
21 SHAFT SEAL F 1073 F 1073 F 1073 2
22 BEARING SEAL F 1074 F 1074 F 1074 2
23 ROLLER BEARING H 1030 H 1030 H 1030 2
24 'O' RING F 1070 F 1070 F 1070 2
25 CIRCLIP B 1013 B 1013 B 1013 2
26 THRUST WASHER B 1066 B 1066 B 1066 1
27 SEALED BALL BEARING H 1052 H 1052 H 1052 2
28 BEARING RETAINING WASHER S 8512 S 8512 S 8512 2
29 HEX HEAD SCREW G 1083 G 1083 G 1083 12
30 HEX HEAD SCREW G 1072 G 1072 G 1072 2
31 HEX HEAD SCREW G 1068 G 1068 G 1068 8
32 HEX HEAD SCREW G 1071 G 1071 G 1071 8
33 SOCKET HEAD CAP SCREW G 1059 G 1059 G 1059 2
34 CSK SCREW G 1052 G 1052 G 1052 3
35 SPRING WASHER B 1022 B 1022 B 1022 2
36 STEM ADAPTOR S 8957 S 8957 S 8957 2
37 BANJO CONNECTOR/N.R.V. R 1085 R 1085 R 1085 2
38 REDUCING CONNECTOR R 1086 R 1086 R 1086 2
39 PLASTIC WASHER R 1082 R 1082 R 1082 2
40 ELBOW R 1089 R 1089 R 1089 5
41 GASKET - COVERPLATE K 1032 K 1032 K 1032 TO SUIT
42 GASKET - END CAP S 8544/1 S 8544/1 S 8544/1 2
43 GASKET - FLANGE S 1170/1 S 1170/1 S 1170/1 2
44 EYE BOLT A 1013 A 1013 A 1013 1
45 DRIVE PULLEY P 1020 P 1020 P 1020 1
46 DRIVEN PULLEY P1021 P1021 P1021 1
47 BUSH P 1022 P 1022 P 1022 1
48 TIMING BELT P 1023 P 1023 P 1023 1
49 NUT B 1044 B 1044 B 1044 1
50 WASHER W 1027 W 1027 W 1027 1
51 ADAPTOR R 1055 R 1055 R 1055 2
52 OIL FEED PIPE X 1072/1 X 1072/1 X 1072/1 1
53 OIL DELIVERY PIPE X 1073/1 X 1073/1 X 1073/1 1
54 OIL DELIVERY PIPE X 1074/1 X 1074/1 X 1074/1 1
55 BALL BEARING H 1034 H 1034 H 1034 1
56 TUBING NUT R 1040 R 1040 R 1040 10
Other manuals for L95HP
1
This manual suits for next models
1
Table of contents
Other Utile Blower manuals
Popular Blower manuals by other brands
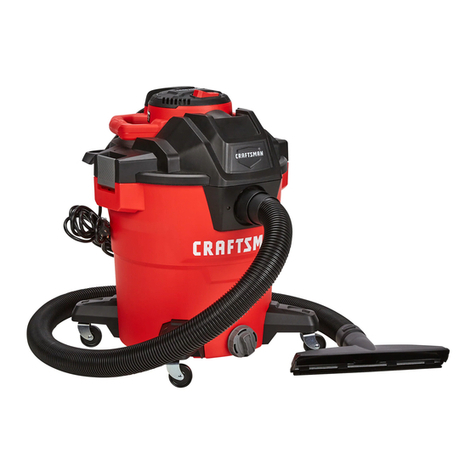
Craftsman
Craftsman CMXEVBCB1260L instruction manual
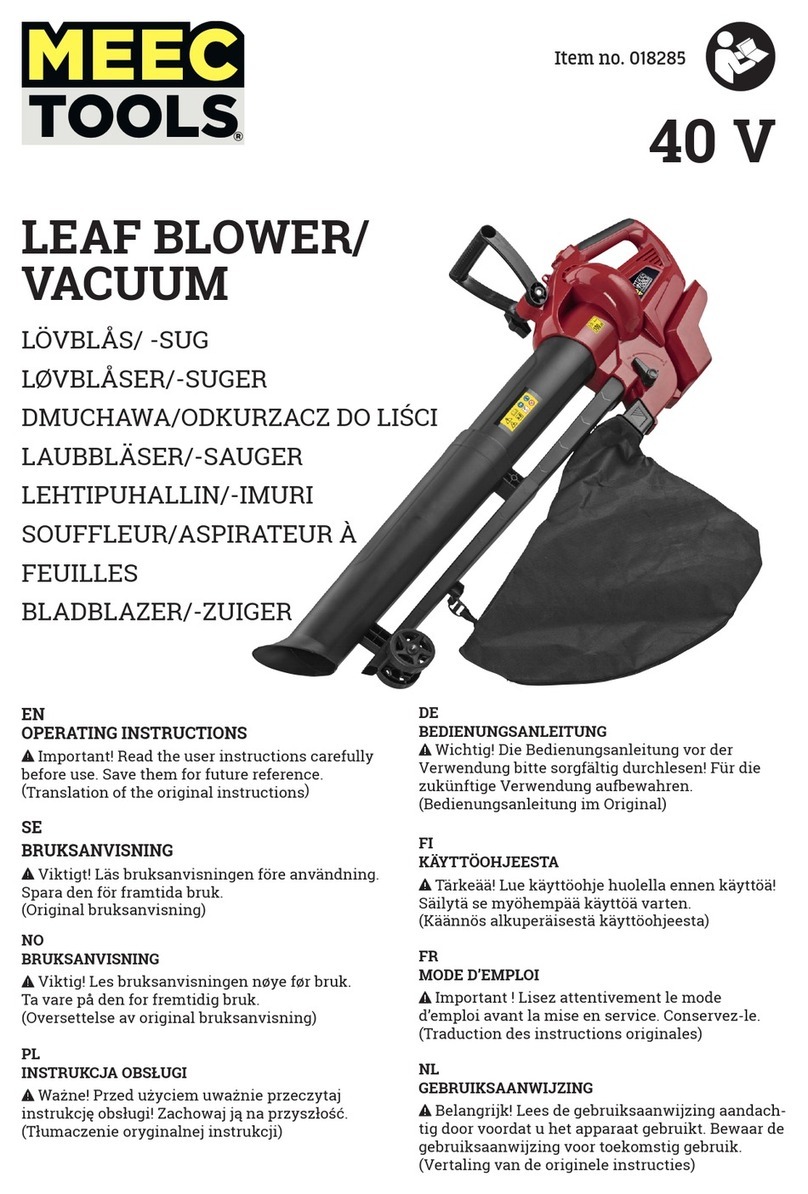
Meec tools
Meec tools 018285 operating instructions

Scag Power Equipment
Scag Power Equipment CLASSIC LBC15-BS950 Operator's manual

Black & Decker
Black & Decker BL1200 Series instruction manual
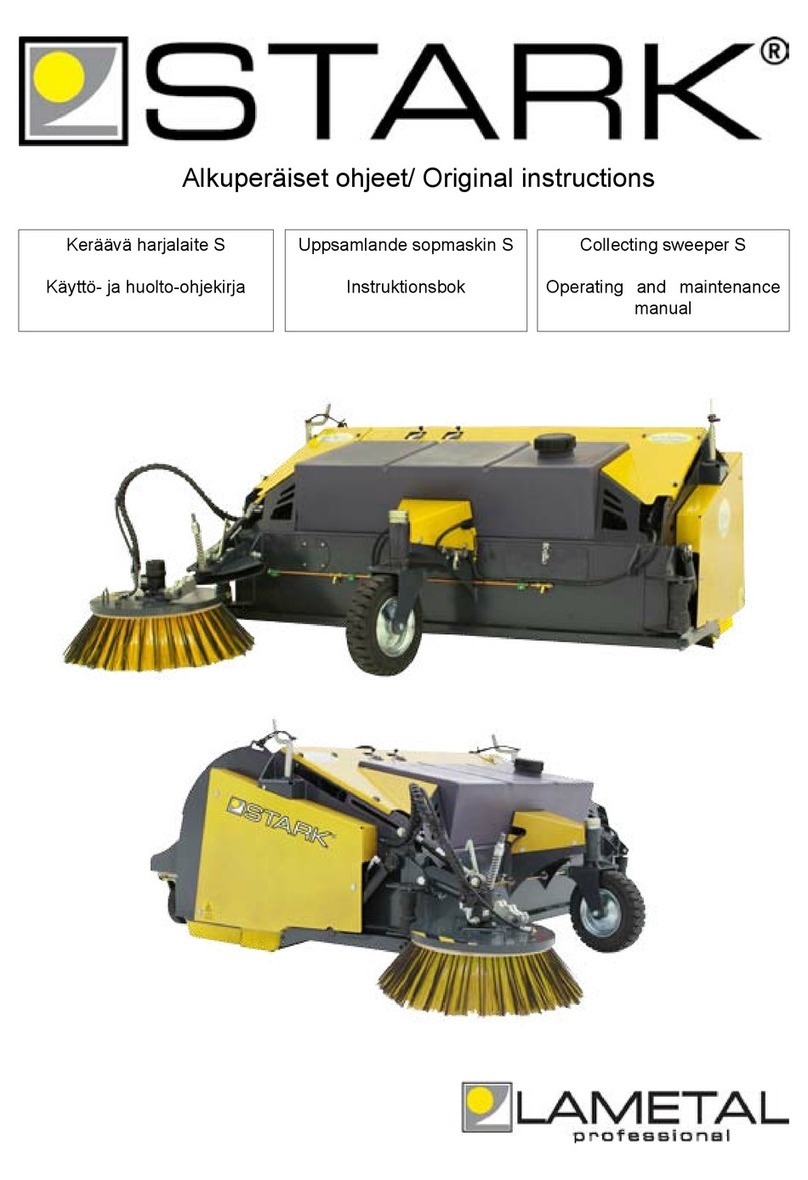
LAMETAL
LAMETAL STARK S Original instructions

Tennant
Tennant S6 NA Operator's manual