Vanair Goodall CAP-START User manual

Vanair Manufacturing, Inc.
10896 West 300 North
Michigan City, IN 46360
Telephone (toll free): (800) 526-8817
Service (toll free): (844) VAN-SERV
(844) 826-7378
Telephone: (219) 879-5100
Service Fax: (219) 879-5335
Parts Fax: (219) 879-5340
Sales Fax: (219) 879-5800
www.vanair.com
©2022 Vanair Manufacturing, Inc.
All rights reserved
KEEP THE MANUAL
WITH THE VEHICLE
P/N: 090189-OP_r0
Effective Date:
JUNE 2022
HYDRAULIC-DRIVEN • 12V/24V BATTERY
STARTER • CHARGER
OPERATION MANUAL AND PARTS LIST
Read this manual before install-
ing, operating or servicing this
equipment. Failure to comply
with the operation and mainte-
nance instructions in this man-
ual will VOID THE EQUIPMENT
WARRANTY.
NOTE
This publication contains the
latest information available at
the time of preparation. Every
effort has been made to ensure
accuracy.
Vanair Manufacturing, Inc.
reserves the right to make
design change modifications
or improvements without prior
notification.
NOTE
Use only Vanair Van-
guard™Premium Synthetic
Compressor Oil and Genuine
Vanair Parts. Inspect and
replace damaged components
before operation. Substituting
non-Vanair oil or non-genuine
Vanair filter components WILL
VOID THE COMPRESSOR
WARRANTY!
NOTE
Making unauthorized modifica-
tions to the system components
WILL VOID THE WARRANTY!
Always inform Vanair Manufac-
turing, Inc., before beginning
any changes to the Cap•Start
Hydraulic-Driven Package.

MOBILE POWER SOLUTIONS
AIR N ARC®
ALL-IN-ONE POWER-SYSTEMS®
RELIANT™ SERIES
POWERFLEX™ SERIES
PRO SERIES
VIPER™ SERIES
ALL WARRANTY OR
RETURNS MUST BE
PRE-AUTHORIZED PRIOR
TO PERFORMING
ANY WARRANTY WORK.
(844) VAN - SERV
SERVICE@VANAIR.COM
PARTS@VANAIR.COM
10896 W. 300 N.
MICHIGAN CITY, IN 46360
(800) 526-8817
VANAIR.COM
EFFECTIVE: JUNE 15, 2020
This limited warranty supersedes all previous Vanair warranties
and is exclusive with no other guarantees or warranties ex-
pressed or implied.
LIMITED WARRANTY—Subject to the expressed terms and con-
ditions set forth below, Vanair Mfg., Inc. (“Vanair”), of Michigan
City, Indiana (USA), warrants to the original retail purchaser of
new Vanair equipment that such equipment is free from defects
in materials and workmanship when shipped by Vanair.
For warranty claims received by Vanair within the applicable
warranty periods described below, Vanair will repair or replace
any warranted equipment, parts or components that fail due to
defects in material or workmanship or refund the purchase price
for the equipment, at Vanair’s discretion. Vanair is not responsi-
ble for time or labor to gain access to the machine to perform
work. WARRANTY WILL BE VOID IF GENUINE VANAIR PARTS AND
FLUIDS ARE NOT USED.
Vanair must be notied in writing within thirty (30) days of any
such defect or failure. All warranty or returns must be pre-autho-
rized in writing prior to performing warranty work. Call Vanair
for process and forms. Vanair will provide instructions on the
warranty claim procedures to be followed.
Warranty will commence upon receipt of the Warranty Regis-
tration Card. If the Warranty Registration Card is not received
within six (6) months of shipment from Vanair, the warranty
commencement date shall be thirty (30) days from the date of
shipment from Vanair. Records of warranty adherence are the
responsibility of the end user.
1. Lifetime Warranty Parts – 3 Years Labor
• Rotary Screw Air Compressor Air End
2. 6 Years Parts – 3 Years Labor
• Vanair Super Capacitor (VSC)
3. 3 Years Parts – 1 Year Labor
• Reciprocating Compressor Air End
• Generators
• Welders
4. 2 Years Parts – 1 Year Labor
• Hydraulic Motors
• Hydraulic Pumps
5. 1 Year Parts – 1 Year Labor
• All electronics including, but not limited to:
I) I/O Boards
II) Modules
III) Panel Boxes
IV) Instrumentation
V) Clutches
VI) Solenoids
VII) Running Gear/Trailers
VIII) Compressor/Hydraulic Coolers, including Fan
and Radiator Core
This Limited Warranty shall not apply to:
1. Consumable components, such as shaft seals, valves, belts,
lters, capacitors, contactors, relays, brushes or parts that fail
due to normal wear and use.
2. Items furnished by Vanair, but manufactured by others, such
as engines and trade accessories (these items are covered by
the manufacturer’s warranty, if any).
3. Equipment that has been modied by any party other than
Vanair or equipment which has not been used and main-
tained in accordance with Vanair’s specications.
4. Equipment which has been improperly installed and/or
improperly operated, based upon Vanair’s specications for
the equipment or industry standards.
5. Equipment installed by non-authorized or third party per-
sonnel. Vanair products are intended for purchase and
use by commercial/industrial users and persons trained
and experienced in the use and maintenance of industrial
equipment.
In the event of a warranty claim covered by this Limited War-
ranty, the exclusive remedies shall be, at Vanair’s sole discretion:
(i) repair; or (ii) replacement; (iii) where authorized in writing
by Vanair in appropriate cases, the reasonable cost of repair
or replacement at an authorized Vanair service facility ; or (iv)
payment of (or credit for) the purchase price (less reasonable
depreciation based upon actual use) upon return of the equip-
ment at the warranty claimant’s risk and expense. Vanair will pay
standard ground freight for any warranty item shipped to and
from Vanair or (Vanair designated facility) within the rst year of
the applicable warranty period. Any additional expedited freight
cost is the responsibility of the purchaser.
TO THE GREAT EXTENT PERMITTED BY APPLICABLE LAW, THE
REMEDIES PROVIDED HEREIN ARE THE SOLE AND EXCLUSIVE
REMEDIES APPLICABLE TO THE VANAIR EQUIPMENT. IN NO
EVENT SHALL VANAIR BECOME LIABLE FOR DIRECT, INDIRECT,
SPECIAL, PUNITIVE, INCIDENTAL OR CONSEQUENTIAL DAMAGES
(INCLUDING LOSS OF PROFIT OR LOST BUSINESS OPPORTUNI-
TY), WHETHER BASED ON CONTRACT, TORT OR ANY OTHER LE-
GAL THEORY. IN NO EVENT SHALL VANAIR BECOME OBLIGATED
TO PAY MORE ON ANY WARRANTY CLAIM THAN THE PURCHASE
PRICE ACTUALLY PAID BY THE ORIGINAL RETAIL PURCHASER.
THIS LIMITED WARRANTY IS MADE IN LIEU OF ALL OTHER WAR-
RANTIES, EXPRESS OR IMPLIED, INCLUDING THE WARRANTIES
OF MERCHANTABILITY AND/OR FITNESS FOR A PARTICULAR
PURPOSE, OR ANY OTHER WARRANTY OR GUARANTY ARIS-
ING BY OPERATION OF LAW. ANY WARRANTY NOT EXPRESSLY
PROVIDED HEREIN, IMPLIED WARRANTY, GUARANTY AND ANY
REPRESENTATION REGARDING THE PERFORMANCE OF THE
EQUIPMENT, AND ANY REMEDY FOR BREACH OF CONTRACT,
IN TORT, OR ANY OTHER LEGAL THEORY WHICH, BUT FOR THIS
PROVISION, MIGHT ARISE BY IMPLICATION, OPERATION OF LAW,
CUSTOM OF TRADE, OR COURSE OF DEALING ARE EXCLUDED
AND DISCLAIMED BY VANAIR.
Some states in the United States of America do not allow lim-
itations of how long an implied warranty lasts, or the exclusion
of incidental, indirect, special or consequential damages, and as
such, the above limitations and exclusions may not apply to you.
This warranty provides specic legal rights. Other rights may be
available to you, but may vary from state to state.
In Canada, legislation in some provinces provides for certain
additional warranties or remedies other than as stated herein,
and to the extent that they may not be saved, the limitations
and exclusions set out forth above may not apply. This Limited
Warranty provides specic legal rights, and other rights may be
available, but may vary from province to province.

TABLE OF
CONTENTS
TABLE OF CONTENTS
090189-OP_r0 (JUNE-2022) TOC - I
VANAIR MANUFACTURING, INC.
(844) VAN-SERV • www.vanair.com
Cap•Start Hydraulic-Driven
12V/24V • Battery Starter • Charger
WARRANTY.................................................................. BEHIND COVER
TABLE OF CONTENTS ................................................................ TOC - I
WARRANTY CLAIMS PROCEDURE ..............................WARRANTY - I
CLAIMS PROCESS FOR WARRANTED PARTS ................................................WARRANTY - I
PROCEDURE ......................................................................................................WARRANTY - I
Figure W-1: Machine Serial Plate / Serial Number Location .........................WARRANTY - I
SECTION 1: SAFETY ................................................................. 1 - 1
1.1 GENERAL INFORMATION ..................................................................................... 1 - 1
1.2 DANGERS, WARNINGS, CAUTIONS AND NOTES ............................................... 1 - 1
1.3 SUMMARY OF DANGERS, WARNINGS AND CAUTIONS .................................... 1 - 1
1.3.1 DANGERS....................................................................................................... 1 - 1
1.3.2 WARNINGS..................................................................................................... 1 - 1
1.3.3 CAUTIONS...................................................................................................... 1 - 2
1.4 SAFETY DECALS.................................................................................................... 1 - 2
1.5 CALIFORNIA PROPOSITION 65 WARNINGS ........................................................ 1 - 3
1.6 DISPOSING OF MACHINE FLUIDS........................................................................ 1 - 3
SECTION 2: SPECIFICATIONS ....................................................... 2 - 1
2.1 GENERAL INTRODUCTION ........................................................................................ 2 - 1
TABLE 2A: SPECIFICATIONS FOR CAP•START HYDRAULIC MACHINE ......................... 2 - 1
TABLE 2B: CAPSCREW TIGHTENING TORQUE VALUES................................................. 2 - 1
Figure 2-1: Machine Main Component Locations........................................................... 2 - 2
SECTION 3: INSTALLATION ........................................................... 3 - 1
3.1 MACHINE PACKAGE RECEIPT/INSPECTION ........................................................... 3 - 1
3.2 GENERAL INSTRUCTIONS......................................................................................... 3 - 1
3.3 DETERMINING THE MACHINE MOUNTING LOCATION ........................................... 3 - 2
Continued on next page...

TOC - II 090189-OP_r0 (JUNE-2022)
TABLE OF CONTENTS
VANAIR MANUFACTURING, INC.
(844) VAN-SERV • www.vanair.com
Cap•Start Hydraulic-Driven
12V/24V • Battery Starter • Charger
SECTION 3: INSTALLATION (CONTINUED)
3.4 HYDRAULIC SYSTEM OVERVIEW............................................................................. 3 - 2
Figure 3-2: Identification and Dimension Diagram.......................................................... 3 - 3
3.4.1 HYDRAULIC SYSTEM FILTRATION................................................................. 3 -4
3.4.2 HYDRAULIC OIL RESERVOIR ......................................................................... 3 -4
3.4.2.1 DETERMINING RESERVOIR SIZE........................................................... 3 - 4
3.4.2.2 DETERMINING RESERVOIR SHAPE....................................................... 3 - 4
3.4.2.3 MANDATORY RESERVOIR FEATURES................................................... 3 - 5
3.4.2.4 RECOMMENDED RESERVOIR OPTIONS............................................... 3 - 5
3.4.2.5 RESERVOIR FEATURES TO AVOID......................................................... 3 - 5
3.4.2.6 RECOMMENDED HYDRAULIC SYSTEM SPECIFICATIONS .................. 3 - 6
3.4.3 STANDARDS GUIDELINES ............................................................................. 3 - 6
3.5 INSTALLATION............................................................................................................. 3 - 6
3.5.1 MACHINE LOCATION ...................................................................................... 3 - 6
3.5.2 CLEARANCES ................................................................................................. 3 - 6
3.5.3 MACHINE STABILIZATION AND GROUNDING .............................................. 3 - 6
3.5.4 SERVICE CONNECTIONS .............................................................................. 3 - 6
3.5.5 ELECTRICAL CONNECTIONS........................................................................ 3 - 6
3.5.6 HYDRAULIC SUPPLY CIRCUIT ...................................................................... 3 - 6
3.5.7 ROUTING ......................................................................................................... 3 - 7
3.5.8 HYDRAULIC SYSTEM REQUIREMENTS ....................................................... 3 - 7
3.6 CONNECTING THE HYDRAULIC SUPPLY AND RETURN ........................................ 3 - 7
SECTION 4: OPERATION ................................................................ 4 - 1
4.1 GENERAL INFORMATION........................................................................................... 4 - 1
4.2 OPERATING CONDITIONS ......................................................................................... 4 - 1
4.3 INITIAL (FIRST-TIME) START-UP................................................................................ 4 - 1
4.3.1 ROUTINE START-UP PROCEDURE .............................................................. 4 - 1
4.4 ROUTINE SHUTDOWN PROCEDURE (FIRST AND ROUTINE) ................................ 4 - 2
4.5 EXTREME CONDITION OPERATION ......................................................................... 4 - 3
Continued on next page...

090189-OP_r0 (JUNE-2022) TOC - III
TABLE OF CONTENTS
VANAIR MANUFACTURING, INC.
(844) VAN-SERV • www.vanair.com
Cap•Start Hydraulic-Driven
12V/24V • Battery Starter • Charger
SECTION 4: OPERATION (CONTINUED)
Figure 4-2: Controller Screen Identification and Navigation.................................................. 4 - 4
SECTION 5: MAINTENANCE........................................................... 5 - 1
5.1 GENERAL INFORMATION........................................................................................... 5 - 1
5.2 REPLACEMENT PARTS .............................................................................................. 5 - 1
5.3 PARTS REPLACEMENT AND ADJUSTMENT PROCEDURES .................................. 5 - 2
5.3.1 ADJUSTING THE BELT TENSION .................................................................. 5 - 2
5.3.2 REPLACING THE BELT ................................................................................... 5 - 2
5.4 STORAGE AND INTERMITTENT USE ........................................................................ 5 - 3
5.4.1 INTERMITTENT USE....................................................................................... 5 - 3
5.4.2 LONG TERM STORAGE.................................................................................. 5 - 3
SECTION 6: TROUBLESHOOTING................................................. 6 - 1
6.1 GENERAL INFORMATION........................................................................................... 6 - 1
6.2 TROUBLESHOOTING GUIDE - HYDRAULICS........................................................... 6 - 2
SECTION 7: ILLUSTRATED PARTS LIST....................................... 7 - 1
7.1 PARTS ORDERING INFORMATION............................................................................ 7 - 1
Figure 7-1: Machine Serial Plate/Serial Number Location.............................................. 7 - 1
TABLE 7A: RECOMMENDED SPARE PARTS LIST............................................................. 7 - 2
7.2 FINISHED ASSEMBLY - 1 OF 3................................................................................... 7 - 4
7.2 FINISHED ASSEMBLY - 2 OF 3................................................................................... 7 - 6
7.2 FINISHED ASSEMBLY - 3 OF 3................................................................................... 7 - 8
7.3 ELECTRICAL ASSEMBLY, FRAME, CAPACITOR AND RELAY - 1 OF 2.................... 7 - 9
7.3 ELECTRICAL ASSEMBLY, FRAME, CAPACITOR AND RELAY - 2 OF 2.................. 7 - 10
7.4 ALTERNATOR ASSEMBLY ........................................................................................ 7 - 12
7.5 MOTOR ASSEMBLY .................................................................................................. 7 - 14
7.6 MANIFOLD ASSEMBLY ............................................................................................. 7 - 16
7.7 CONTROL MODULE ASSEMBLY.............................................................................. 7 - 17
7.8 CANOPY AND PARTS ............................................................................................... 7 - 18
7.9 DECAL IDENTIFICATION/LOCATION - 1 OF 2 ......................................................... 7 - 20
7.9 DECAL IDENTIFICATION/LOCATION - 2 OF 2 ......................................................... 7 - 21
Continued on next page...

TOC - IV 090189-OP_r0 (JUNE-2022)
TABLE OF CONTENTS
VANAIR MANUFACTURING, INC.
(844) VAN-SERV • www.vanair.com
Cap•Start Hydraulic-Driven
12V/24V • Battery Starter • Charger
SECTION 7: ILLUSTRATED PARTS LIST (CONTINUED)
7.10 WIRING DIAGRAM - 1 OF 2 ....................................................................................... 7 - 22
7.11 HOSE INSTALLATION GUIDE ................................................................................... 7 - 23
TABLE 7B: MAINTENANCE TRACKING LOG.................................................................... 7 - 24

WARRANTY
CLAIMS PROCEDURE
WARRANTY CLAIMS PROCEDURE
090189-OP_r0 (JUNE-2022) WARRANTY - I
VANAIR MANUFACTURING, INC.
(844) VAN-SERV • www.vanair.com
Cap•Start Hydraulic-Driven
12V/24V • Battery Starter • Charger
CLAIMS PROCESS FOR WARRANTED
VANAIR PARTS
This process must be used by owners of Vanair®
equipment in situations where a warranted item
needs repair or replacement under the terms of
the purchase warranty. Do not return items to
Vanair without prior authorization from the Vanair
Warranty Administrator.
PROCEDURE:
When a customer needs assistance in trouble-
shooting a system and/or returning parts, follow
the steps below.
1. Locate the machine’s serial number:
The machine package serial number plate is
located inside the machine compartment on
the wall of the enclosure near the hydraulic
motor unit (see Figure W-1).
The machine and the alternator also have
individual serial numbers respectively (see
Figure W-1). Have a list of the symptoms/
condition/malfunctions along with any ap-
plicable temperature and pressure read-
ings, and also the number of operational
hours available:
Note that the above information will also
need to be included on the Return Material
Authorization Form (per Step #6); this form
is necessary for warranty processing if the
warranty claim is deemed valid by the service
case review.
2. Contact the Vanair Service Department by
phone (1-219-879-5100) to speak with a
Service Technician.
3. Vanair Service will troubleshoot the prob-
A
B
KEY DESCRIPTION KEY DESCRIPTION
AMACHINE SERIAL PLATE / SERIAL NUMBER BALTERNATOR SERIAL PLATE / SERIAL NUMBER
Figure W-1: Machine Serial Plate / Serial Number Location

WARRANTY PROCEDURE
WARRANTY - II 090189-OP_r0 (JUNE-2022) VANAIR MANUFACTURING, INC.
(844) VAN-SERV • www.vanair.com
Cap•Start Hydraulic-Driven
12V/24V • Battery Starter • Charger
lem based on the information provided by
the customer, and attempt to return the
unit to service as quickly as possible.
4. If the unit cannot be returned to service,
and Vanair determines this matter is a
warranty issue, the Service Technician
will assign an RMA (Return Material Au-
thorization) number that will provide for
the return of the item to Vanair for anal-
ysis and a final determination as to the
item’s warranty status.
NOTE
The RMA number must be placed on the outside
of the package being returned.
5. Warranty Claims are solicited via a Return
Material Authorization (RMA) Form. This
form can be obtained via download from
the web site, or requested directly from
the Vanair Service Department:
Once a current form has been obtained, fol-
low the instructions given on the form to fill in
the information needed. This form is used for
the purpose of soliciting a warranty case. All
of the field information except for the bottom
section block fields, which includes Dispo-
sition of Goods, Notifications and Additional
Notes, will be required.
Customers have 30 days after the RMA num-
ber is issued to return the item. If the part is
not returned within this period, the RMA is
void and any claims will be denied.
NOTE
All labor claims or invoices must be approved
by the Vanair Warranty Administrator prior
to starting repair work along with the cost of
the repair. All paper work associated with the
returned item and warranty repair cost must
reference the RMA number issued against the
part, and be forwarded to Vanair within 30 days
of the completion of work.
Before sending a warranty part to a customer,
Vanair will need a P.O. or credit card number to
cover the cost of the part and shipping. After the
part is analyzed and deemed to be covered under
warranty, Vanair will issue credit to the customer.
All parts eligible for warranty must have the RMA
number on the invoice at the time of purchase.
No items can be returned “freight collect”. Freight
costs will be addressed at the time the claim is
closed. The customer pays any additional costs
for warranty parts delivered through expedited
services (i.e., Next Day, Second Day).
IMPORTANT
VANAIR WILL NEVER ACCEPT ANY INVOICES
FOR PARTS RETURNED: ANY PARTS RE-
TURNED VIA INVOICE WILL BE RETURNED
FREIGHT COLLECT: NO PARTS ARE TO BE
RETURNED FREIGHT COLLECT!
Vanair Mfg., Inc. strives to continuously improve
its customer service. Please forward any ques-
tions, comments, or suggestions to Vanair Ser-
vice:
Vanair Manufacturing, Inc.
10896 West 300 North
Michigan City, IN 46360
Telephone (toll free): (800) 526-8817
Service (toll free): (844) VAN-SERV
(844) 826-7378
Telephone: (219) 879-5100
Service Fax: (219) 879-5335
Parts Fax: (219) 879-5340
Sales Fax: (219) 879-5800
www.vanair.com

SECTION 1:
SAFETY
SECTION 1: SAFETY
090189-OP_r0 (JUNE-2022) 1 - 1
VANAIR MANUFACTURING, INC.
(844) VAN-SERV • www.vanair.com
Cap•Start Hydraulic-Driven
12V/24V • Battery Starter • Charger
1.1 GENERAL INFORMATION
IMPORTANT
Read this manual before operating
or servicing the Cap•Start Hydrau-
lic-Driven Package. Failure to do
could result in damage equipment,
bodily injury, or death.
The products provided by Vanair®Manufacturing,
Inc., are designed and manufactured for safe op-
eration and maintenance. But it is ultimately the
responsibility of the users and maintainers for
safe use of this equipment. Part of this responsi-
bility is to read and be familiar with the contents of
this manual before operation or performing main-
tenance actions.
1.2 DANGERS, WARNINGS,
CAUTIONS AND NOTES
These boxes are labeled clearly with the title
block listing either Danger, Warning, Caution, or
other non-safety issue. They draw attention to
specific issues that are pertinent to the safe and
correct operation of the machine.
The symbols shown and defined in Section 1:
Safety are used throughout this manual and on
the machine to call attention to, and identify, pos-
sible hazards.
The international warning symbol [ ] is used on
all decals, labels and signs that concern informa-
tion pertaining to bodily harm. When you see
the international warning symbol, pay extremely
careful attention, and follow the given instructions
or indications to avoid any possible hazard.
1.3 SUMMARY OF DANGERS,
WARNINGS AND CAUTIONS
These boxed inserts are placed throughout this
manual in the sections where they apply. This
subsection is a general summary of their con-
tents.
1.3.1 DANGERS
• Keep tools or other conductive objects away
from live electrical parts.
• Never touch electrical wires or components
while the machine is operating. They can be
sources of electrical shock.
1.3.2 WARNINGS
• DO NOT perform any modifications to this
equipment without prior factory approval.
• DO NOT install this Cap•Start in a confined
space that lacks proper ventilation and airflow;
breathing and cooling air circulation must not
be compromised.
• DO NOT operate the Cap•Start or any of its
systems if there is a known unsafe condition.
Disable the equipment by disconnecting it
from its power source. Install a lock-out tag to
identify the equipment as inoperable to other
personnel.
• DO NOT operate the machine with any by-pass
or other safety systems disconnected or ren-
dered inoperative.
• DO NOT operate the equipment while you are
under the influence of alcohol or drugs.
• DO NOT operate the equipment while you are
feeling ill.
• DO NOT attempt to service the equipment
while it is operating.
• Before performing maintenance or replacing
parts remove all electrical power.
• DO NOT use flammable solvents or cleaners
for cleaning the machine or it parts.
• DO NOT operate the Cap•Start in areas where
flammable, toxic, or corrosive fumes, or other
damaging substance can be ingested by the
Cap•Start intakes.
• Keep arms, hands, hair and other body parts,

1 - 2 090189-OP_r0 (JUNE-2022)
SECTION 1: SAFETY
VANAIR MANUFACTURING, INC.
(844) VAN-SERV • www.vanair.com
Cap•Start Hydraulic-Driven
12V/24V • Battery Starter • Charger
and clothing away from fans, drive shafts, and
other moving parts.
• DO NOT wear jewelry, unbuttoned cuffs, ties,
or loose-fitting clothing when you are working
near moving/rotating parts.
• ALWAYS confine long hair when working near
moving/rotating parts.
• NEVER operate the equipment while wearing a
headset to listen to music or the radio.
• Wear personal protective equipment such as
gloves, work shoes, and eye and hearing pro-
tection as required for the task at hand.
• DO NOT operate the Cap•Start with any guards
removed or damaged, or other safety devices
inoperative.
• DO NOT operate the Cap•Start in enclosed or
confined spaces where ventilation is restricted
or closed-off.
• Ensure that hoses connected to service valves
are fitted with correctly sized and rated flow
limiting devices which comply with applicable
codes. Pressurized broken or disconnected
hoses can whip causing injuries or damage.
• Over speed is hazardous! NEVER tamper with
the governor components or settings to in-
crease the maximum speed. Severe personal
injury and equipment damage can result if op-
erated at speeds above the maximum.
• DO NOT use tools, hoses, or equipment that
have maximum ratings below that of this ma-
chine.
• Keep metal tools, and other conductive objects
away from live electrical components.
• Before performing maintenance or repair oper-
ations on the Cap•Start, ensure that all pow-
er has been removed and been locked out to
prevent accidental application.
• DO NOT assume that because the Cap•Start is
in a STOPPED condition that power has been
removed.
• Install, operate, and maintain this equipment in
full compliance with all applicable OSHA, oth-
er Federal, state, local codes, standards, and
regulations.
• When lifting objects, be aware of proper lifting
techniques to avoid injury.
• ALWAYS read and follow safety related pre-
cautions found on containers of hazardous
substances.
1.3.3 CAUTIONS
• Check all safety devices for proper operation
on a routine basis.
• Ensure that no tools, rags, or other objects are
left on machine drive systems or near intakes.
• Keep the equipment clean when performing
maintenance or service actions. Cover open-
ings to prevent contamination.
• DO NOT operate the Cap•Start if cooling air is
not available (fan/cooler not operating) or if
lubricant levels are below their specified min-
imum levels.
• Ensure all plugs, hoses, connectors, covers,
and other parts removed for maintenance ac-
tions are replaced before applying power to
the Cap•Start.
• Avoid touching hot surfaces and components.
• Ensure that electrical wiring, terminals; hoses
and fittings are kept in serviceable condition
through routine inspections and maintenance.
Replace any damaged or worn components.
• DO NOT install safety devices and/or replace-
ment parts other than authorized Vanair®re-
placement parts.
• Keep personnel out of line with, and away from
discharge opening of valves, hoses and tools.
• Immediately clean up any lubricant or spills.
1.4 SAFETY DECALS
Safety decals are placed onto, or located near,
system components that can present a hazard to
operators or service personnel. All pertinent de-
cals listed in Section 7.9, Decal Identification/
Location are located near a component, which is
subject to respect in terms of safety precautions.
Always heed the information noted on the safety
decals.

090189-OP_r0 (JUNE-2022) 1 - 3
SECTION 1: SAFETY
VANAIR MANUFACTURING, INC.
(844) VAN-SERV • www.vanair.com
Cap•Start Hydraulic-Driven
12V/24V • Battery Starter • Charger
WARNING
DO NOT REMOVE OR COVER ANY SAFETY
DECAL. Replace any safety decal that becomes
damaged or illegible.
1.5 CALIFORNIA PROPOSITION
65 WARNINGS
WARNING
Discharge from this machine may cause cancer
and/or reproductive harm.
Proposition 65 requires businesses to provide
warnings to Californians about significant expo-
sures to chemicals that cause cancer, birth de-
fects or other reproductive harm. Exposure to
these chemicals may take place when products
are acquired or used. Exposure may also occur
in homes, workplaces, or other environments in
California. By requiring that this information be
provided, Proposition 65 enables Californians to
make informed decisions about their exposures
to these chemicals.
Proposition 65 also prohibits California busi-
nesses from knowingly discharging significant
amounts of listed chemicals into sources of drink-
ing water.
1.6 DISPOSING OF MACHINE
FLUIDS
Always dispose of machine fluids under the guid-
ance of all applicable local, regional and/or fed-
eral law.
Vanair encourages recycling when allowed. For
additional information, consult the container label
of the fluid in question.

1 - 4 090189-OP_r0 (JUNE-2022)
SECTION 1: SAFETY
VANAIR MANUFACTURING, INC.
(844) VAN-SERV • www.vanair.com
Cap•Start Hydraulic-Driven
12V/24V • Battery Starter • Charger
BLANK PAGE

SECTION 2:
SPECIFICATIONS
SECTION 2: SPECIFICATIONS
090189-OP_r0 (JUNE-2022) 2 - 1
VANAIR MANUFACTURING, INC.
(844) VAN-SERV • www.vanair.com
Cap•Start Hydraulic-Driven
12V/24V • Battery Starter • Charger
2.1 GENERAL INTRODUCTION
The tables and figures in this section list the
specifications (including operational, output and
dimensional) of the overall machine. Contact the
Vanair®Service Department if additional specifi-
cations are needed that cannot be found in this
manual.
Refer to Figure 2-1 for general machine compo-
nent locations. For additional information, includ-
ing measurement specifications, refer to Figure
3-1 (machine and identification and dimensions)
in Section 3, Installation.
TABLE 2A: SPECIFICATIONS FOR CAP•START HYDRAULIC MACHINE
GENERAL SYSTEM INFORMATION SPECIFICATION
HYDRAULIC MOTOR
Motor Speed: 2600 RPM
Motor GPM: 8 - 12 @ 3000 PSI
Pump Size Required: 8 - 25 GPM
Operating Temperature Limits: -40° - 140°F
TABLE 2B: CAPSCREW TIGHTENING TORQUE VALUES
SIZE GRADE LUBRICATED
1/4 - 20 UNC 5 6 ft-bs
5/16 - 18 UNC 5 13 ft-lbs
3/8 - 16 UNC 5 23 ft-lbs
1/2 - 13 UNC 5 55 ft-lbs
3/4 - 10 UNC 5 200 ft-lbs

2 - 2 090189-OP_r0 (JUNE-2022)
SECTION 2: SPECIFICATIONS
VANAIR MANUFACTURING, INC.
(844) VAN-SERV • www.vanair.com
Cap•Start Hydraulic-Driven
12V/24V • Battery Starter • Charger
F
G
H
J
K
L
A
B
C
D
E
RS
T
U
Q
M
P
N
KEY DESCRIPTION KEY DESCRIPTION
AULTRACAPACITOR LMANIFOLD
B500 AMP RELAY (X 5) MINSTRUMENT PANEL MODULE
CDRIVE BELT NPRESSURE
DHYDRAULIC MOTOR PRETURN
EOUTPUT CABLE CONNECTOR QCONTROL MODULE
FAC GEN FAN RPOWER CONNECTION
GAC GENERATOR SCASE DRAIN
HSOLENOID THYDRAULIC RETURN
JPRESSURE RELIEF VALVE UHYDRAULIC SUPPLY
KPOWER CONNECTOR
Figure 2-1: Machine Main Component Locations

SECTION 3:
INSTALLATION
SECTION 3: INSTALLATION
. 090189-OP_r0 (JUNE-2022) 3 - 1
VANAIR MANUFACTURING, INC.
(844) VAN-SERV • www.vanair.com
Cap•Start Hydraulic-Driven
12V/24V • Battery Starter • Charger
3.1 MACHINE PACKAGE
RECEIPT/INSPECTION
Upon receipt of the machine package, inspect the
exterior of the shipping crate for signs of shipping/
transit damage. Any damage should be reported
immediately to the shipping company.
NOTE
Before fully unpacking the unit, inspect the
component parts, supports and loose-packed
parts to ensure that there have been no inter-
nal movements of assemblies or components,
which may have been damaged during ship-
ment.
Should any damage be discovered during pack-
age inspection, contact the shipping company
immediately.
VANAIR MANUFACTURING, INC.
(219) 879-5100 / (800) 526-8817
Service (toll free): (844) VAN-SERV
(844) 826-7378
Service Fax: (219) 879-5335
www.vanair.com
3.2 GENERAL INSTRUCTIONS
This section provides general guidance for locat-
ing and preparing the Cap•Start Hydraulic ma-
chine package for operation. Each installation
is unique and can be affected by location, ven-
tilation, and other factors such as electrical and
hydraulic power supply availability and location.
DISCLAIMER
DO NOT install in any enclosed space without
first contacting Vanair.
WARNING
Install, operate, and maintain this equipment in
full compliance with all applicable OSHA, other
Federal, state, local codes, standards, and regu-
lations.
WARNING
Before performing maintenance or repair op-
erations on the machine, ensure that all power
has been removed and locked out to prevent
accidental start-up.
DO NOT assume that because the machine is
in a STOPPED condition that power has been
removed.
WARNING
DO NOT perform any modifications to this
equipment without prior factory approval.
WARNING
DO NOT use plastic pipe, or incorrectly rated
piping or hose. Incorrectly rated connection
material can fail and cause injury or equipment
damage.
WARNING
DO NOT operate the machine in enclosed or
confined spaces where ventilation is restricted
or closed off.
NOTE
Install electrical components (circuit breakers,
pressure switches, toggle switches, etc.) in
locations where exposure to water or moisture
will be most minimized.
NOTE
In order to prevent accidental damage to vehi-
cle components (fuel tanks, lines, brake lines,
wiring harnesses), note their location before
drilling any holes.

SECTION 3: INSTALLATION
3 - 2 090189-OP_r0 (JUNE-2022) VANAIR MANUFACTURING, INC.
(844) VAN-SERV • www.vanair.com
Cap•Start Hydraulic-Driven
12V/24V • Battery Starter • Charger
3.3 DETERMINING THE MACHINE
MOUNTING LOCATION
When determining the location to mount the
Cap•Start Hydraulic unit, the following criteria
must be taken into consideration:
• The mounting surface must be level and able to
accommodate the four (4) mounting bolts and
isolators of the base frame. Refer to Figure
3-1 or Figure 3-2 for clearance room and lay-
out of mounting hole slots’ locations.
IMPORTANT
Mounting surface must be able to bear the
weight of the machine (245 lbs).
• Mount the machine with a minimum of four (4)
mounting locations.
• The location must allow for the machine dimen-
sions, and additional space requirements for
minimum cooling, maintenance and access.
Refer to Figure 3-3 to determine the additional
minimum space requirement measurements.
• The external gauges/display must be easily vis-
ible to the operator.
It is recommended, for most installations, to
mount the machine on the driver’s side of the ve-
hicle. The unit should be situated in such a man-
ner that the fan (rear) and hydraulic cooler (front)
are not obstructed. Do not place the machine in
any location where it can ingest exhaust fumes,
dust or debris.
NOTE
When considering external system layout hoses
refer to Section 7.12, Hose Guide for proper
routing and mounting practices.
3.4 HYDRAULIC SYSTEM
OVERVIEW
IMPORTANT
Vanair®highly recommends consulting a hy-
draulic supply expert for specifying the correct
hydraulic supply components for vehicle-side
integration (including oil reservoir size, hy-
draulic pressure relief, hose size, etc.) for your
application.
A
B
B
C
C
Figure 3-1: Machine Minimum Operational Clearance
KEY DESCRIPTION
AMINIMUM CLEARANCE: 8"
BMINIMUM CLEARANCE: 8"
CMINIMUM CLEARANCE: 8"
DMINIMUM CLEARANCE: 8"

SECTION 3: INSTALLATION
090189-OP_r0 (JUNE-2022) 3 - 3
VANAIR MANUFACTURING, INC.
(844) VAN-SERV • www.vanair.com
Cap•Start Hydraulic-Driven
12V/24V • Battery Starter • Charger
20.83
24.00
11.2 5
18.00
5.34
12.11
Ø0.55
(4X)
16.00
14.43 14.73
5.30
8.23
15.31
DECAL AREA
AIR FLOW
DECAL AREA
DECAL AREA
DECAL AREA
AIR
FLOW
IN
AIR FLOW OUT
24.92
HYDRAULIC RETURN
#12 MJIC 37°
HYDRAULIC SUPPLY
#8 MJIC 37°
0.98
0.95 22.00
Figure 3-2: Identification and Dimension Diagram
DISCLAIMER
If machine package is to be
mounted within a confined
space such as beneath a can-
opy, the area must be deter-
mined to allow for adequate air
flow to take place for cooling
purposes. Consult factory for
assistance in ensuring ade-
quate air flow before mounting
the machine.
NOTE
The dimensions listed in this
diagram are the minimum required
clearance distances needed for
properly cooling the machine.
Additional clearance room may be
desired for easier access for control
and/or maintenance functions.
050211ID_r0

SECTION 3: INSTALLATION
3 - 4 090189-OP_r0 (JUNE-2022) VANAIR MANUFACTURING, INC.
(844) VAN-SERV • www.vanair.com
Cap•Start Hydraulic-Driven
12V/24V • Battery Starter • Charger
IMPORTANT
Contaminated hydraulic fluid allowed to enter
the pump will cause malfunction of the pump
controls. Hydraulic system hoses must be
flushed and cleaned prior to being connected to
the unit.
Refer to Figure 3-2 for hydraulic pump system
connections.
Please take into consideration the following:
• The hydraulic flow and pressure requirements
of the system.
• A continuous hydraulic load is necessary when
machine is running.
• The duty cycle and ambient operating tempera-
tures.
• Other hydraulic equipment which may share
that same hydraulic supply system (Vanair
recommends a dedicated pump and hydraulic
circuit).
WARNING
Follow all applicable safety recommendations
as outlined in Section 1: Safety of this manual.
WARNING
Improperly, or non-connected lines may cause
harm, and will damage the equipment.
The hydraulic hoses must be run to the machine.
Verify that hoses are hooked up properly to en-
sure proper flow. Also, verify that the hoses are
laid out properly so that no chafing or kinking
of the hoses is possible. Refer to Section 7.12,
Hose Installation Guide, for assistance with
proper hose layout and connecting functions.
NOTE
The temperature of the hydraulic oil should not
exceed 160°F due to the rating of the Vanair-
supplied hydraulic motor.
3.4.1 HYDRAULIC SYSTEM
FILTRATION
Vanair recommends using a 10 micron oil filter on
the hydraulic oil return line. Flow rating of the filter
must be equal to, or greater than, the maximum
GPM at which the system will be operated.
IMPORTANT
Use only a filter that is specifically intended for
hydraulic systems.
3.4.2 HYDRAULIC OIL RESERVOIR
3.4.2.1 DETERMINING RESERVOIR
SIZE
In a conventional hydraulic system, minimum
tank size, in gallons, should be equal to the max-
imum GPM flow rate, times two (x 2).
3.4.2.2 DETERMINING
RESERVOIR SHAPE
The reservoir structure should be tall and narrow
rather than shallow and broad (Figure 3-3). A tall,
narrow tank is recommended because:
1. The oil level is well above suction line open-
ing, avoiding the possibility of drawing air into
the pump due to a vortex or “whirlpool” effect
within the tank during operation flow.
A
B
KEY DESCRIPTION
A PREFERRED SHAPE: TALL AND NARROW
B SHAPE TO AVOID: BROAD AND SHALLOW
Figure 3-3: Reservoir Design Shape

SECTION 3: INSTALLATION
090189-OP_r0 (JUNE-2022) 3 - 5
VANAIR MANUFACTURING, INC.
(844) VAN-SERV • www.vanair.com
Cap•Start Hydraulic-Driven
12V/24V • Battery Starter • Charger
2. Allows for better oil level tolerance level of
the system if vehicle operates at an unusual
(slightly offlevel) vehicle angle.
3. To keep return flow well below the surface so
it does not break the surface and cause aer-
ation (cavitation) of the oil.
3.4.2.3 MANDATORY RESERVOIR
FEATURES
• The reservoir should incorporate the following
design features:
• In terms of location of the reservoir tank within
the hydraulic system, note that the hydraulic
pump’s inlet line (suction line out from the res-
ervoir to the pump) should be located near the
bottom of the tank, well below the oil level. The
suction line should protrude a minimum of two
(2”) inches into the reservoir to keep it away
from potential contaminant surface buildup.
• A baffle or baffles should be included to pre-
vent sloshing, or centrifugal motion of the oil;
the goal is to break up direct flow of the oil
from the return point to the suction point. This
allows for the cooling action contact with the
tanks’ inner surfaces, and promote separation
of any air or contaminants that interact with
the flowing oil.
• An ideal baffle design would position several
(but not too many) baffles to promote an ‘S’
shape flow within the reservoir, as viewed
from above. The area of the end gaps should
be at least twice the area of the suction line
diameter.
• A drain port with plug, situated at the lowest
point of the reservoir, is needed to assure
complete draining. It should be installed using
an adapter or housing which does not pro-
trude above the inner surface of the floor of
the tank. It should be visible and accessible
for removal, with sufficient space available for
catching the waste oil.
• If the return line entrance to the tank is located
near the top, it should be extended downward
within the tank to minimize foaming and aer-
ation of the circulating oil. This extends oil in-
tegrity, which in turn helps to maintain system
performance and reliability.
• An in-line filter on the return line is needed to
protect the system against contaminants be-
ing introduced into the oil. The filter should be
mounted externally from the reservoir in a lo-
cation that allows for easy of service access.
• A breather and fill cap is needed at the oil fill
port, which needs to be located above the
system oil level. The breather cap acts to both
filter air that is drawn into the reservoir as the
oil level diminishes, and bleeds air out as the
level is regained. This maintains constant at-
mospheric pressure in the air volume within
the reservoir.
• A sight-glass provides a direct visual indication
of the oil level without having to open, or oth-
erwise access, the reservoir.
3.4.2.4 RECOMMENDED RESERVOIR
OPTIONS
Although not essential for an adequately func-
tioning reservoir, the following components will
contribute to maximize the hydraulic system’s ef-
ficiency and maintain a quality operational level.
• Magnetic drain plug: Attracts and concentrates
ferrous contaminants at the drain plug source
for easier accessibility and removal when
cleaning tank interior.
• A temperature gauge: Located in approxima-
tion to, or built in to, the sight glass assembly
allows for temperature reading at a glance.
• Filler port strainer: Prevents large contaminant
particles from blending with system oil when
adding new oil.
• Return line diffuser (splash) plate reduces ve-
locity of oil flow before return oil stream merg-
es with the main reservoir oil volume.
• A reservoir heater: For those systems that are
exposed to cold climate ambients, having the
ability to preheat the hydraulic oil prior to start
up will make for easier startups, and reduce
the strain of warming up the system under ad-
verse cold conditions.
3.4.2.5 RESERVOIR FEATURES TO
AVOID
A strainer used to screen the suction line is not
recommended for systems designed for mobile
equipment use. Having equipment that likely ex-
periences long suction lines, cold startups and
non-tracked or infrequent maintenance practic-
es may cause this strainer to potentially promote

SECTION 3: INSTALLATION
3 - 6 090189-OP_r0 (JUNE-2022) VANAIR MANUFACTURING, INC.
(844) VAN-SERV • www.vanair.com
Cap•Start Hydraulic-Driven
12V/24V • Battery Starter • Charger
system strain (cavitation) than prolong fluid integ-
rity through filtration.
A pressurized reservoir is not recommended for
vehicles, as its complexity invites too much po-
tential for loss of system reliability if it is not prop-
erly maintained.
3.4.2.6 RECOMMENDED HYDRAULIC
SYSTEM SPECIFICATIONS
WARNING
Do not operate machine without hydraulic sys-
tem completely assembled.
Refer to Figure 3-1 or Figure 3-2.
Flow controller is optional to reduce flow if neces-
sary. Consult Vanair®.
HYDRAULIC LINES
The following is a minimum requirement and NO
quick disconnects may be used. Lines are to be
kept as straight and short as possible.
• Pressure port = Standard, #12, 3/4” hose (lo-
cated at manifold block)
• Load sense = #4 JIC = 1/4” hose (Used for
closed center system only)
• Pressure relief/case drain = #6 JIC = 3/8” hose
• Hydraulic suction = Standard, #16, 1” hose
3.4.3 STANDARDS GUIDELINES
• Hydraulic pressure relief factory set at 3200
PSI.
3.5 INSTALLATION
3.5.1 MACHINE LOCATION
It is vital to locate the machine so that there is
no restriction of cooling air through the enclosure
(Refer to Figure 3-1). Cooling air enters the en-
closure at the rear (cooler) package end of the
machine, passes through the cooler and exits
through vents in the upper sides and the front.
3.5.2 CLEARANCES
Refer to Figure 3-1. Ensure that adequate sur-
rounding clearance space exists around the ma-
chine to allow for adequate cooling ventilation
through the canopy shroud, unobstructed service
access, and a clear view of the control panel. An
approximate recommendation of ten (10) inches
clearance, minimum, is needed for proper cool-
ing circulation, plus any additional service access
room included where needed.
3.5.3 MACHINE STABILIZATION AND
GROUNDING
Machine should be mounted to vehicle using a
minimum of four (4) isolators. Isolators absorb vi-
bration. Isolators are included with the machine.
NOTE
An isolator replacement kit is available from
Vanair®; order bolt down isolator no. KIT1202-
001 (kit contains four [x4] isolators).
WARNING
GROUNDING STRAP: If the machine and/or
instrument panel respectively are isolated from
contacting the chassis (paint fiberglass body,
rubber mounts, etc.), then the machine must
be grounded to the truck chassis with a mini-
mum two (2) ga wire (reference Vanair ground
strap no. 267498).
If the machine is bonded by traditional hard
mounting (metal to metal contact with chas-
sis), then the grounding strap is not required.
3.5.4 SERVICE CONNECTIONS
Refer to Figure 3-2. Service connections are
conveniently grouped at the lower rear section of
the unit in the base frame.
3.5.5 ELECTRICAL CONNECTIONS
Refer to Figure 3-2. Connect the electrical supply
connector, located at the connection port panel
end of the unit. This system is offered with 12V
DC circuits.
3.5.6 HYDRAULIC SUPPLY CIRCUIT
Refer to the proper hydraulic flow schemat-
ic drawing (Sections 7.19 through 7.22) that
matches the machine model build. It is recom-
mended that the Cap•Start unit possesses a sep-
arate pump/flow/return hydraulic circuit to other
hydraulic equipment. This is to prevent the pos-
Table of contents
Popular Controllers manuals by other brands
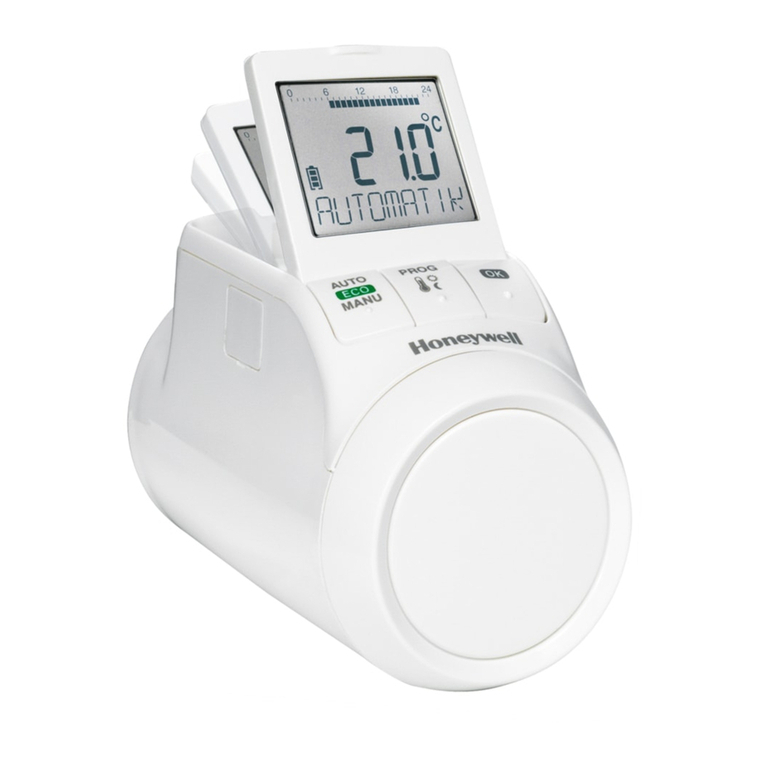
Honeywell Home
Honeywell Home TheraPro HR90 Quick start installation guide
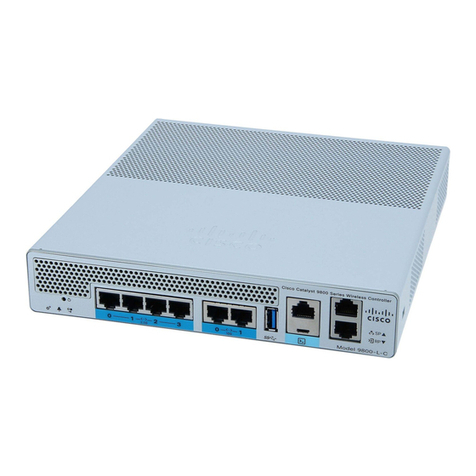
Cisco
Cisco Catalyst C9800-L Hardware installation guide
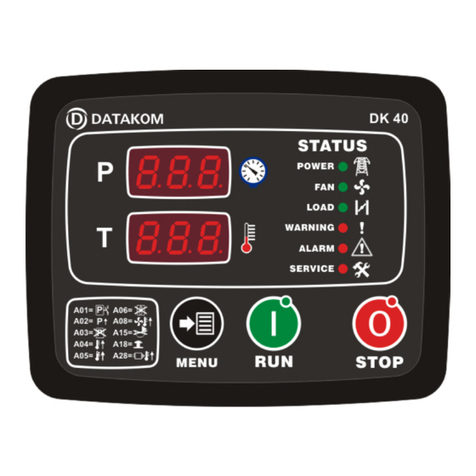
Datakom
Datakom DK-40 user manual
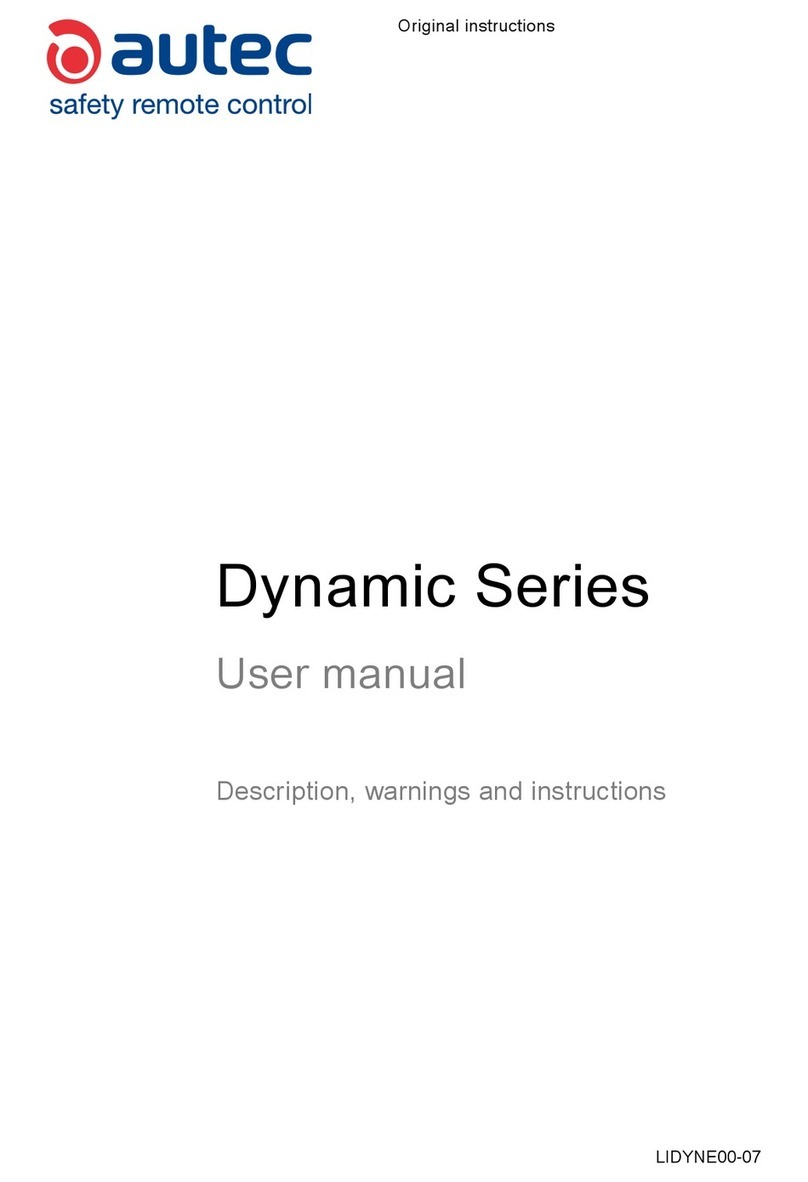
AUTEC
AUTEC Dynamic Series user manual
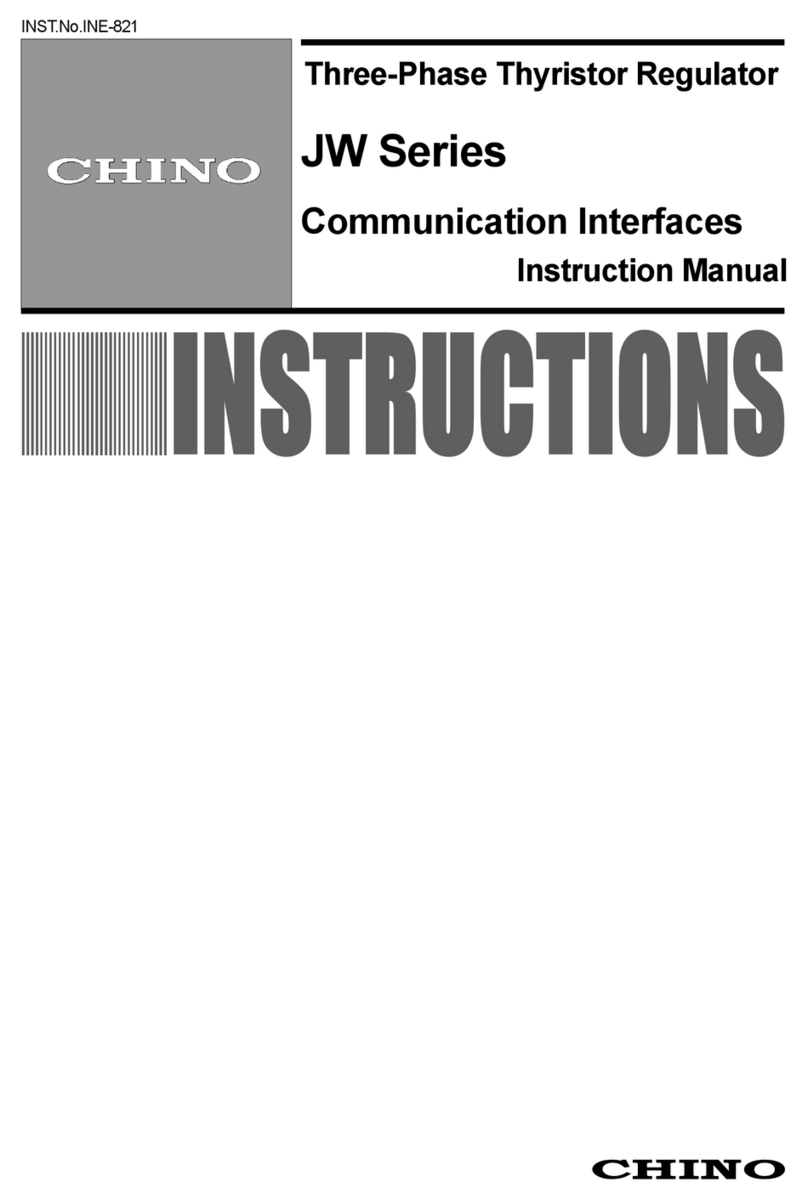
Chino
Chino JW Series instruction manual
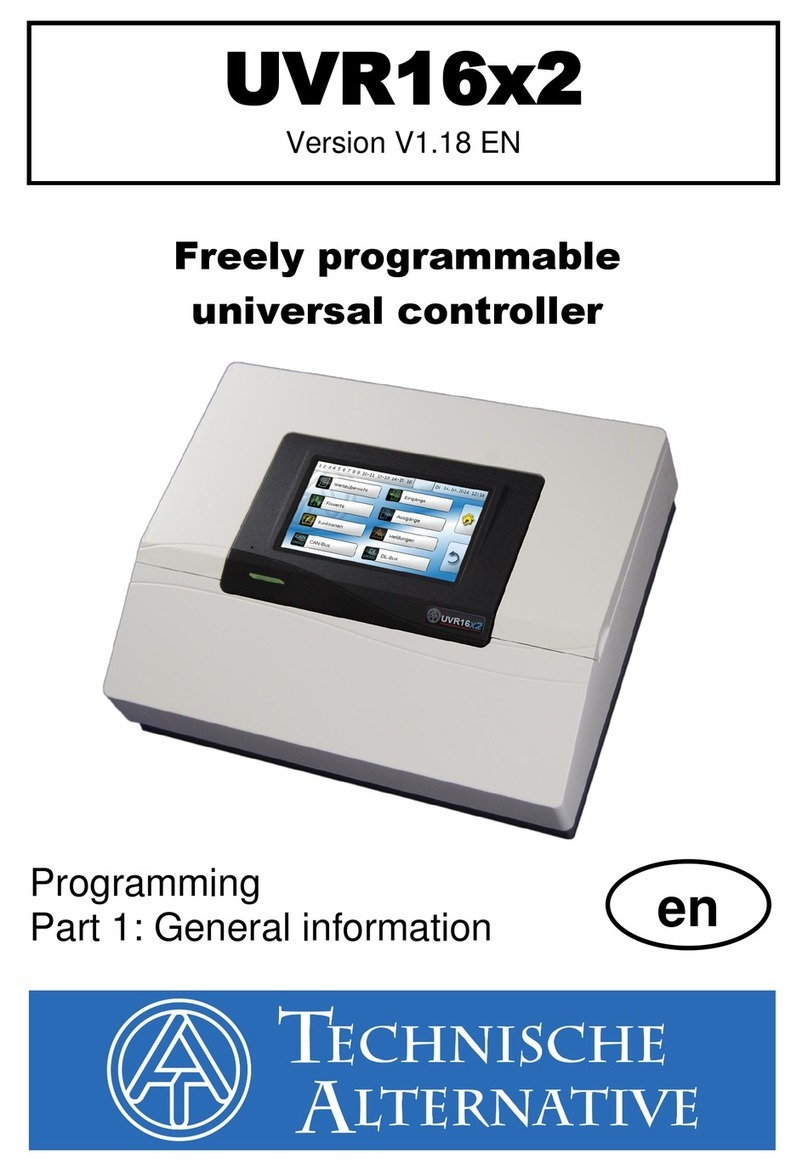
Technische Alternative
Technische Alternative UVR16x2***-D Programming guide