Vaporless ISM-4080 User manual

1
Quality Petroleum Equipment
Solutions for Over 30 Years
ISM-4080
Electro-Mechanical
Line Leak Detection
Installation & Operation Manual
Rev. 11/11/2020

2
I. System Concept:
The ISM-4080 Integrated Shutdown Module monitors pressure on multiple lines with multiple turbines
and ensures stable line pressure by monitoring line pressure through a switch attached to the LD-2000 or
LD-3000 MLLDs, starting the submersible turbine pump (STP) to check the line when low pressure is
detected in the line.
Line leak detection is needed for protecting assets and meeting regulatory compliance. The most common
and frustrating problem with any leak detection system is false alarm slow flow. At a station, when not
transferring fuel, the pressure in the underground piping system may fall due to thermal contraction of the
fuel within the line, causing vapor pockets to form, affecting all line leak detection systems. This condition
can create false alarm slow flow or missed line leaks. This condition is prevented in real time by the ISM-
4080. In the event of an actual leak, the device has alarm and shutdown capabilities.
In a manifold piping system, multiple turbines starting simultaneously overrides 3GPH line leak detection.
To alleviate this issue, the ISM-4080 will authorize one pump first, allow one leak detector to search for
a line leak, and then (after the line has been cleared/passed) start the additional submersibles at delayed
intervals.
The ISM-4080 includes the following features:
•Automatic fuel line re-pressurization
•Line leak monitoring
◦Up to (4) lines
•Sequence turbine control for manifold applications
◦Combinations up to (4) pumps
▪(1) line with (2, 3 or 4) pumps, (2) lines with (2) pumps
•Supports (2) control valves
◦Transition sump solenoids in marina applications
◦ Underground to aboveground transition solenoids in high head pressure applications
•Pressure failure alarm notification
•Sump sensor monitoring
◦May share the wire pair from single point sump sensor with a 100k resistor (such as Veeder
Root p/n: VR794380-208)
•Sump sensor alarm notification
•Full shutdown of the pump when an alarm condition is detected
•Pump contactor control in response to an authorization signal
•Ability to disable the re-pressurization cycle based on time-of-day if the tank test module of the
tank monitor needs extended quiet time
•Alarm output(s) can report to –
◦Standalone horn / light
◦ATG system
◦Building management system
•Remote Reset (optional)

3
II. Installation and Wiring:
A. High Voltage Wiring:
1. Must enter enclosure in the high voltage area –bottom of the enclosure on the left side.
2. High voltage wiring connects to the DIN rail terminal block strip.
3. All connections should be 14 –16 AWG.
4. Power Main
1. The enclosure requires one dedicated 120 VAC circuit at 15 or 20 amps
2. Max circuit draw could be 13 amps
3. HOT connects to terminal L1 –HOT.
4. Neutral connects to terminal N –NEUT.
5. Ground must be connected to GROUND. Ground must be connected to ensure
proper performance of the controller.
6. This system comes with advanced design characteristics that minimize the effects of
poor main grounds and transient noise. However, good design may not overcome all
of the problems of a poorly grounded site, or a site with a high amount of “noise”
transient voltage. If communication problems or excessive false alarms occur, first
have a qualified electrical contractor check the systems ground(s). Contact VMI for
trouble-shooting or the need for power line filtration.
B. AC Outputs
See B-1 for AC Outputs: Control Valve Applications
See B-2 for AC Outputs: Non-Control Valve Applications
B-1. AC Outputs: Control Valve Applications
1. (8) 120VAC Outputs
(4) Hook / Turbine Outputs
(2) Control Valve Outputs
(2) Alarm Outputs
2. All outputs provide a switched hot.
3. Each output can supply no more than 2 amperes of current.
4. Hook / Turbine Outputs

4
Hook / Turbine outputs cannot drive the pump directly. The turbine output should be wired to
the tank gauge’s Auth input or the turbine contactor coil. If the site has dispenser sump sensors
or submersible sump sensors the VMI controller is not monitoring, the VMI turbine outputs
should become the tank monitor’s authorizations. In this manner, the pump starting and
stopping is subject to the site sensors. Alternatively, Sump Alarms and E-stop can be wired to
break main power to the ISM.
B-2. AC Outputs: Non-Control Valve Applications
1. (8) 120VAC Outputs
(4) Hook / Turbine Outputs
(4) Alarm Outputs
2. All outputs provide a switched hot.
3. Each output can supply no more than 2 amperes of current.
4. Hook / Turbine Outputs
Hook / Turbine outputs cannot drive the pump directly. The turbine output should be wired to
the tank gauge’s Auth input or the turbine contactor. If the site has dispenser sump sensors or
submersible sump sensors the VMI controller is not monitoring, the VMI turbine outputs should
become the tank monitor’s authorizations. In this manner, the pump starting and stopping is
subject to the site sensors. Alternatively, Sump Alarms and E-stop can be wired to break main
power to the ISM.
C. Alarm Outputs:
1. Alarm outputs are provided per product or turbine. Alarm Outputs are dynamic depending upon
site configuration. Alarm Outputs can be wired to ATG alarm inputs, separate annunciators, or
building management systems.
D. AC Inputs:
1. Up to four 120 VAC Authorization inputs (require a switched hot).
Typically, one input per product. Different options are available per site configuration.
2. Each AC input draws only 20 mA.
E. Low Voltage Inputs/Outputs (5 VDC):
1. Must enter enclosure in the Intrinsically Safe area –bottom of the enclosure on the right side.
2. Low voltage intrinsically safe wiring only connects to the terminal blocks in the area on the
bottom right side of the enclosure labeled left to right 1 –4.
3. All low voltage wiring should be twisted pair 14 –22 AWG with shield.
4. Each piston switch pair connects to a single terminal block.
5. Shield should be connected to the provided terminal blocks grouped with each IS switch. Ground
(shield) should not be connected in the sump.

5
F. Installation of IS Piston Switch(es):
1. Install provided O-ring on piston switch. Thread the piston switch into the vent port of the
mechanical line leak detector until hand-tight.
2. Apply a "UL Classified" (QLSR) pipe joint sealing compound (for use with petroleum products)
to the provided vent fitting and install in the open port on the side of the piston switch.
3. Install copper tube in the fitting and vent back to tank test port of the submersible pump.
4. Following the piston switch wiring diagram found on page 22 connect the IS wiring in the
junction box using the supplied wire nuts and di-electric grease. Use the wiring instructions
found on page 22 for the connection to the ISM-4080 control box.
5. If the Piston Switch is to share the wire pair with a sump sensor:
•Piston Switch and sump sensor must be installed in series
•The sump sensor must be single point with a 100k resistor (such as Veeder Root p/n
VR794380-208)
•Install per wiring diagram found on page 23
G. Wiring guides are located at end of this document. (Page 18)
Note: Before applying power to the system, it is recommended that you contact VMI. Be
prepared to email some pictures of your newly installed and wired ISM-4080 System.

6
III. Menu and Programming:
Caution: Before proceeding with the Set-up and Programming
ensure the breakers for the pumps connected to this system are OFF.
Preconfigured software may authorize pump(s).
GENERAL:
The ISM-4080 is an electronic interface that is a line leak detection monitor, a motor controller, and may
act as a sump sensor monitor. The ISM system can monitor and control up to (4) Products –(4)
Authorization Inputs, (4) Pump Outputs, (4) Alarm Outputs, (4) Sump Sensors Inputs, and (2) Control
Valve Outputs in various configurations.
The ISM-4080 series is able to identify line pressure through the ISM-4105\47 Piston Switch mounted on
the top of the LD-2000 MLLD (or ISM-4106\47 mounted on the LD-3000). The Piston Switch enables
the system to track when pressure falls to a determined level (switch opens). The ISM-4080 also
determines if the leak detector test that is run in response to low pressure completes with a pass. An Alarm
is initiated at a failure to pressurize the line (mechanical/electronic problem) or due to a 3 GPH line leak.
FRONT PANEL:
The ISM-4080 Controller protrudes through the front of the electrical box. In the center there is a 2-line
display. The displayed messages are listed below. There are 8 buttons or stick pins (4 on each side) that
may be used to program site specifics or initiate specific functions. The pin uses and functions follow.
DISPLAY:
The ISM-4080 2-line display presents system status:
•Line 1 reports 3 pieces of information
oProduct #, Turbine # (and which turbine is current lead on a manifolded line), and Pressure
oFor example, it may display
P=1 T=1L PRES=HI
oP= Product Number
▪P=1, 2, 3, or 4
oT= Turbine Number
▪T=1, 2, 3, or 4
oL= Lead Turbine Indicator
oPRES=Line Pressure
▪PRES = HI = High Line Pressure, LO = Low Line Pressure
•Line 2 displays State or Process and Alarm Status
oStates:
▪AUTHORIZE–There is a call or request for the product.
▪MONITOR–No Authorization, pump is off, line pressure is high.

7
▪DELAY–Line pressure is low –the system is waiting for the appropriate
time to repressurize/test the line.
▪PRESSURE–The system is testing the line.
▪PRES ALARM–The system has not been able to open the leak detector, or the
sensor response is not being detected by the ISM Controller.
▪SUMP ALARM- The sump sensor is reporting liquid in the sump.
▪DISABLE- Automatic repressurization is disabled for a programmed time
span.
▪SENSOR OUT- This piston switch is not connected, or the wire pair is open.
oAL= Alarm Status
▪AL States - N = No Alarm, P = Pressure Alarm, S = Sump Sensor Alarm
PUSH BUTTONS:
The buttons on the sides of the ISM are:
Left Side Right Side
MENU UP ARROW ▲
TEST CLEAR
PRINT ENTER
RESET DOWN ARROW ▼
•MENU- Used to enter and scroll through Categories, or to back out of a subcategory.
Each Category and their options will be discussed below.
•TEST- Test button not active on the ISM-4080 system.
•PRINT- Print button not active on the ISM-4080 system.
•RESET- This button is VERY IMPORTANT –WILL RESET ALARMS &
RESTART PUMP(S).
oEXAMPLE: If it appears Regular is not pumping, that Product should show:
P=1 T=1L PRES=LO
PRES ALARM AL=P
oFor the Product that is in Alarm - not pumping- it is important to have customers using the
product stop dispensing, no open nozzles. The line cannot be “cleared” if nozzles of the
fuel in question are still open. Customers using other products may continue to fuel.
oPush the RESET pin. Reset All is displayed, press ENTER to clear All Alarms. Thepump
will come on, trying to pressurize the line. The display will show MONITOR if pressure
returns. Allow customers to return to fueling.
oIf the Alarm returns such as
P=1 T=1L PRES=LO
PRES ALARM AL=P
▪Return nozzles to dispensers, push the RESET pin. Reset All is displayed, press
ENTER to clear All Alarms. If MONITOR does not return to the screen, contact VMI
for technical support.

8
•UP Arrow Increase a numeric value. If max value is reached, numbers will roll over to
lowest value. Holding down the button will speed up the counter.
•DOWN Arrow Decrease a numeric value. If min value is reached, numbers will roll over to
highest value. Holding down the button will speed up the counter.
•CLEAR- Resets a numeric value to original setting.
•ENTER- To choose a value or setting.
CONFIGURATION:
Before proceeding, it is important to determine if the ISM you are using is preconfigured or not.
When the ISM-4080 boots it will show the following screen:
ISM-4080
Version 3.XX
If the unit is not configured this message will stay on the screen after 10 seconds. If this is what shows
on your screen, follow from MENU next.
If the unit is configured, the boot screen will display for about 10 seconds and then move to the Home
Screen. The home screen will look something like this:
P=1 T=1L PRES=HI
MONITOR AL=N
This screen will rotate through all active products and channels showing the status of each. If the home
screen appears on the ISM-4080, Move down to 2nd MENU below.
MENU:
The MENU button is used to enter specific information about the station and how it is to operate. When
the MENU button is pushed, a Category will be displayed. Press ENTER to access the menu categories.
The first Category needed is SITE CONFIGURATION. The Category and responses are listed below.
Push MENU –RUN TIME SETUP
Push MENU –REPRESSURE
DISABLE TIME
Push MENU –SUMP SENSOR
SETUP
Push MENU –TEST SETUP
Push MENU –SET DATE/TIME?
Push MENU –SITE Facility Configuration
CONFIGURATION
Push ENTER –NUM OF TURBINES This is the Category, the 2nd line is the fill-in

9
PRODUCT 1 # Product = 1, Push the UP Arrow to enter the
number of pumps for Product 1 –1, 2, 3, or 4
Push ENTER –NUM OF LEAD TURB Define how many turbines can be lead
PRODUCT 1#
Push ENTER –NUM OF RUN TURB Max number of turbines (lead or not)
PRODUCT 1 # desired to run at a time
Push ENTER - ROTATE TURBINES? Select rotating or fixed lead turbine
PRODUCT 1 # Choose either YES/NO
Push ENTER - AUTO BASED Method of pump staging for manifolded
AUTHORIZATION applications. Use UP and DOWN ARROWS to set
correct option (AUTO/INPUT/PRESSURE)
Auto –Energizes additional pumps after MLLD on
lead pump has passed the line
Input –Not used for the ISM-4080 system
Pressure –Not used for the ISM-4080 system
Push ENTER –NUM SUCTION CV 0 is the default, only used for commercial suction
PRODUCT 1 0 pumps
Push ENTER –NUM PRESSURE CV 0 is the default. If controlling transition valves,
PRODUCT 1 0 enter appropriate value
Push ENTER –NUM DISPENSER CV 0 is the default, nearly always left at 0
PRODUCT 1 0
Push ENTER –NUM OF TURBINES This has moved back to get the same information on
PRODUCT 2 0 Product 2.
Push the UP Arrow to enter 1, 2, or 3 for the
number of pumps for Product 2
Pushing ENTER will cycle through subsequent Channels
Push MENU to return back to the Default screen, showing the normal scrolling screen such as:
PD=1 T=1L P=HI
MONITOR AL=N
If it is desired to temporarily disable scrolling to monitor a single channel, press the ENTER button on
the channel you wish to view. Pressing clear goes back to scrolling rotation, or the hold will timeout after
10 minutes.

10
2ND MENU:
All must complete 2nd Menu
The MENU button is used to enter specific information about the facility and how it is to operate. When
the MENU button is pushed, a Category will be displayed.
Push MENU –RUN TIME SETUP
Push ENTER –RESILIENCY VALUE Then enter the Resiliency Value, up to 9999 ml
PRODUCT 1 #### Push and hold the UP Arrow or the DOWN Arrow to
Write down the Line Resiliency Value here: increase or decrease the value. Read Line Resiliency
and Testing in the LDT-890 installation instructions
___________________ ml and read Bleed-Back Measurement: Page 13.
If the Resiliency is non-zero, then the Repressure and Delay times will automatically be calculated. The
next two screens will allow you to view the calculated values. WRITE DOWN the REPRESSURE and
DELAY VALUES BELOW on this sheet. Do not change the values displayed below unless you have
consulted with VMI.
Push ENTER –REPRESS TIME MIN Use the UP and DOWN ARROWS to adjust the
PRODUCT 1 __._ value between 0 and 20 minutes.
Push ENTER –DELAY TIME MIN Use the UP and DOWN ARROWS to adjust the
PRODUCT 1 ___._ value between 0 and 150 minutes.
Pushing ENTER will cycle back through for subsequent Channels
After all Channels have been programmed:
Push MENU - REPRESSURE Used to program a time period when repress-
DISABLE TIME urization is disabled for tank test quiet time. Only set
this up if the tank monitor is unable to complete a tank
test during normal operation quiet time.
Push ENTER –DIS START HOUR Use the UP and DOWN ARROWS to adjust the
PRODUCT 1 ## disable start time hour (24 hour clock)
Push ENTER –DIS END HOURUse the UP and DOWN ARROWS to adjust the
PRODUCT 1 ## disable end time hour (24 hour clock)
Pushing ENTER will cycle back through subsequent Channels. After all Channels have been
programmed:
Push MENU –SUMP SENSOR Sump Sensor Menu
SETUP

11
Push ENTER –SUMP SENSOR Use the UP and DOWN ARROWS to adjust the
TYPE type of sump sensor (NORMALLY OPEN/
NORMALLY CLOSED/NO SUMP SENSOR).
Push ENTER –SUMP SHUTDOWN Use the UP and DOWN ARROWS to adjust the
shutdown action (PRODUCT/CHANNEL/ALARM
ONLY).
Push MENU –TEST SETUP Test Setup Menu
Push ENTER –REPRESS RETRIES Use the UP and DOWN ARROWS to adjust the
number of repressurization attempts before alarm
output. Factory default is 1.
Push ENTER –3GPH RETRIES Use the UP and DOWN ARROWS to adjust the
number of repressurization attempts before alarm
output. Factory default is 1.
Push ENTER –ALARM ACTION CONFIGURED AT THE FACTORY. DO NOT
MODIFY.
Push MENU –SET DATE/TIME
Push ENTER –SET DATE Use the UP and DOWN ARROWS to adjust the
current year
YEAR = ####
Push ENTER –SET DATE Use the UP and DOWN ARROWS to adjust the
current month
MONTH = ##
Push ENTER –SET DATE Use the UP and DOWN ARROWS to adjust the
current day
DAY = ##
Push ENTER –SET TIME Use the UP and DOWN ARROWS to adjust the
current hour (24-hour clock)
HOUR = ##
Push ENTER –SET TIME Use the UP and DOWN ARROWS to adjust the
current minute
MINUTE = ##
Push MENU –SITE Facility configuration needs to be entered here
CONFIGURATION (See Above).

12
Push MENU P=1 T=1L PRES=HI
MONITOR AL=N
This concludes the setup of the ISM-4080. The above screen should rotate through the active products.
GENERAL ALARM STATUS DETAILS:
When an alarm condition is recognized by the ISM-4080 it is an indication of failure to build line pressure
/ failure to detect flow. This may be due to many mechanical or electrical problems including:
•Line leak
•Pump motor failure
•Motor starter contactor failure
•Low Fuel
SUMP SENSOR ALARM DETAILS:
If your site has (optional) sump sensors integrated into the ISM-4080 System. When the presence of liquid
is detected by the sump sensor, the system will not allow the turbine to operate in the sump where the
liquid is detected until the fault condition is corrected. In other words, you must remove the liquid from
the sump with the sump alarm in order to enable operation for the turbine in the affected sump.
If you wish to retrofit sump sensors into the ISM-4080 system at a later date, please consult VMI so that
we can ensure proper configuration of the ISM-4080 system.
Please feel free to contact VMI for additional diagnostic/programming assistance.

13
IV. Calibration and Testing:
MEASURING SYSTEM RESILIENCY / BLEED-BACK
When under pressure all closed piping systems exhibit an elastic response that will force fuel from the
line if an opening is provided. The volume of fuel forced from the line is dependent on a number of factors
and must be measured for each installation.
The following statements outline a procedure for measuring the expelled volume, which is referred to as
resiliency or bleed-back. This procedure assumes the use of the Vaporless Model LDT-890 Leak Detector
Tester to perform this task.
The following procedure assumes no knowledge of the operation of the LDT-890 and therefore details
each step of the process. The operation manual supplied with the LDT-890 provides additional information
and should be consulted by the technician.
The following procedure measures the bleed-back for a single product. If the site contains multiple
products, this procedure must be repeated for each product.
CAUTION: Eye protection required during the calibration and testing process.
1. Disable ISM Repressure Cycle
With power applied to the ISM, disable repressurization function by setting REPRESSURE DISABLE
TIME from 00 to 23.
2. Power Off
Turn off the circuit breaker providing power to the product under test. This is done to prevent the
accidental starting of the pump while the line is open in the following steps. Power may remain on the
ISM-4080. However, it is acceptable if power is also disconnected from the module.
3. Install LDT-890 Test Unit
WARNING – THE FOLLOWING ASSUMES THE LINE HAS BEEN PURGED BEFORE THE
LDT-890 IS INSTALLED! IF THE LINE HAS NOT BEEN PURGED, DO SO FIRST BEFORE
INSTALLING THE LDT-890.
Select the dispenser at the highest point of the delivery system for the selected product. If there is no
elevation difference, select the dispenser furthest from the pump.
4. Set the test unit selector to the PRESSURE STEP TEST position.
5. Power On
Turn on the circuit breaker for the product under test. If power had been disconnected from the ISM,
restore power to the module.

14
6. System Purge
Authorize the dispenser. The pump should start running. On the right-hand pressure gauge of the LDT-
890, watch for the pump to achieve operating pressure.
7. Check all connections for leaks. Correct any fault conditions.
8. With the large beaker (1000 ml) under the LDT-890 discharge port, set the selector to the DISPENSER
NOZZLE position. Purge the tester of air by allowing 800 to 1000 ml of fuel to flow into the beaker.
Continue until air spitting has stopped. After purging the LDT-890, set the selector back to the
PRESSURE STEP TEST position.
9. Bleed-Back Measurement
Remove the dispenser authorization. The pump should stop running. Unless there are fault conditions
such as a leak or significant thermal contraction, the line pressure should stabilize at 20 – 30 PSI for
fractional horsepower pumps, or 20 – 50 PSI for higher pressure pumps.
10. With the large beaker under the LDT-890’s discharge port, carefully move the selector
counterclockwise until fuel begins to flow. Monitor the line pressure and when it falls to 14 PSI rapidly
return the selector to the PRESSURE STEP TEST position. For a more precise measurement, have
one tech monitor ISM display while another tech drains line pressure, when the display changes from
MONITOR to DELAY, stop flow.
11. With the flow of fuel stopped, empty the collection beaker.
12. With the small (250 ml) beaker under the LDT-890 discharge port, carefully move the selector to the
DISPENSER NOZZLE position. Fuel will begin to flow into the beaker. When fuel stops flowing,
return the selector to the PRESSURE STEP TEST position.
13. Note the volume of fuel collected. This volume is referred to as bleed-back. Repeat the collection
process several times to confirm the bleed-back volume.
Note: Depending upon the measured volume, the use of the large beaker may be needed. When
possible, the small beaker provides more accurate measurements. The averaging of several
consecutive samples is necessary to accurately determine the bleed-back volume. Enter resiliency
value into ISM-4080 controller (see page 10).
This completes the bleed-back measurement procedure and set-up of the ISM repressure cycle. To ensure
proper installation and system calibration, a 3 GPH leak test must be performed.
LEAK DETECTOR TEST AT 3 GPH
Whether the ISM is fitted to a new installation or retrofit to an existing site, a test of the leak detector must
be performed. This is done to ensure that the VMI Leak Detector is operating normally and that the
selected ISM delay time is long enough for the VMI Leak Detector to return to its reset position.
The following statements outline a procedure for testing the operation of the VMI Leak Detector. This
procedure assumes the use of the Vaporless Model LDT-890 Leak Detector Tester to perform this task.

15
The following procedure assumes no knowledge of the operation of the LDT-890 and therefore details
each step of the process. The operation manual supplied with the LDT-890 provides additional information
and should be consulted by the technician.
1. Install LDT-890 Test Unit
If the LDT-890 has not been installed, follow steps 1 through 8 in the procedure outlined under Measuring
System Resiliency / Bleed-Back. This procedure should result in the dispenser being authorized, the pump
running, and the repressure cycle being disabled.
2. Leak Calibration
With the large beaker (1000 ml) under the LDT-890 discharge port, set the selector to the CALIBRATE
GPH position. Fuel will begin to flow into the beaker.
3. The object of the next step is to calibrate the fuel flow from the test unit to the rate of 3 gallons per hour
at 10 psi pressure at the discharge. This specification meets the requirements of the EPA regarding leak
rate testing.
NOTE:
Turn the ORIFICE knob counterclockwise to increase flow and clockwise to decrease flow.
Turn the PRESSURE knob counterclockwise to reduce pressure and clockwise to increase pressure.
4. The procedure is performed as follows:
FOR THIS FIRST TEST adjust the fuel flow using the Right-hand knob labeled CALIBRATE
PRESSURE. Adjust the pressure on the left-hand pressure gauge to 10 psi.
5. Using the small beaker (250 ml), collect a sample of fuel over a 30 second interval. If the volume is not
95 ml on the first test, the volume will need to be increased or decreased to create a 95 ml flow in 30
seconds. FOR THIS PORTION OF THE TEST: First adjust the flow using the left-hand CALIBRATE
ORIFICE knob and then adjust the left-hand gauge pressure using the right-hand CALIBRATE
PRESSURE knob to bring the pressure back to 10 psi on the left-hand gauge.
Adjust the ORIFICE knob first, turn counterclockwise to increase flow and clockwise to decrease flow.
Adjust the PRESSURE knob second, turn counterclockwise to reduce pressure and clockwise to increase
pressure.
It is important to perform the procedure in the above order.
The flow is properly adjusted when 95 ml are collected in 30 seconds. This volume is equivalent to a rate
of 3 gallons per hour at 10 psi. Repeat the procedure until the correct volume of fuel is collected in the
specified time.
6. Set the selector to the PRESSURE STEP TEST position and remove the dispenser authorization.
7. Reduce Line Pressure to Zero
With the large beaker under the LDT-890 discharge port, set the selector to the DISPENSER NOZZLE
position. Fuel will begin to flow into the beaker. After the reading on the right-hand pressure gauge falls
to zero, set the selector to the PRESSURE STEP TEST position.

16
8. Read Operating Pressure
Authorize the dispenser. The pump will start running. Watch for the pump to achieve operating pressure
as seen on the right-hand pressure gauge. Note this pressure reading on the LDT-890 Test form and then
remove the authorization from the dispenser.
9. Reduce Line Pressure to Zero
With the large beaker under the discharge port, set the test unit’s selector to the DISPENSER NOZZLE
position. Fuel will begin to flow into the beaker. After the reading on the right-hand pressure gauge falls
to zero, set the test unit’s selector to the GPH TEST position and authorize the dispenser.
10. 3 GPH Leak Detector Test
With the dispenser authorized, the pump will start running. With the selector in the GPH TEST position a
3 GPH leak has been introduced to the system. On the right-hand pressure gauge watch for the pump to
build pressure. If the mechanical leak detector is properly calibrated this pressure should not reach the
normal operating pressure previously observed. Note this lower pressure value here. Remove the
authorization from the dispenser.
11. Reduce Line Pressure to Zero
Set the test unit’s selector to the DISPENSER NOZZLE position. Fuel will continue to flow into the
beaker. After the reading on the right-hand pressure gauge falls to zero, set the selector to the GPH TEST
position and again authorize the dispenser.
12. Leak Test Confirmation
With the dispenser authorized, the pump will start running. Again, note that with the selector in the GPH
TEST position a 3 gph leak has been introduced to the system. Watch the right-hand pressure gauge as the
pump builds pressure. The pressure should build to the value noted in Step 10.
TECHNICAL NOTE — If on either test, the pressure indicated on the right-hand pressure gauge does
not stabilize at the lower pressure, but rather steps through to the higher normal operating value, the leak
detector has failed the leak test. Adjust the LD-2000 or LD-3000 to detect a leak consistently. The VMI
Piston Switch will have to be removed to complete this adjustment. Contact VMI for LD-2000 or LD-
3000 adjustment instructions if needed.
After the LD-2000 or LD-3000 has been properly adjusted to detect the leak, and the Piston Switch has
been reinstalled, turn the selector to the PRESSURE STEP TEST position. Reauthorize the pump.
Following a short delay, the pressure should step up to the value noted in Step 8. This is the indication that
the mechanical leak detector has properly transferred from its leak test position to its full flow position.
13. Auto-Repressure Test
Remove the dispenser authorization. With the large beaker under the discharge port, set the selector to the
DISPENSER NOZZLE position. Fuel will flow into the beaker. After the reading on the right-hand
pressure gauge falls to zero, set the selector to the PRESSURE STEP TEST position.
14. Re-Enable Repressurization Feature by adjusting REPRESSURE DISABLE END TIME from 23 to
00, the original time setting (reference page 10 above).

17
Reset the ISM using the RESET> ENTER push-buttons to initialize the repressure cycle. The pump will
start running. Immediately return to the dispenser.
On the right-hand pressure gauge of the LDT-890, verify that normal operating pressure has been achieved.
If the REPRESS RETRIES has been set to 2 or more cycles, the system may cycle 2 or more times to
reach the normal operating pressure (full pump pressure).
15. At the end of the pump REPRESS cycle, the ISM will automatically turn off the pump.
IMMEDIATELY AFTER THE PUMP SHUTS OFF, set the selector on the LDT-890 to the GPH TEST
position. This will introduce a 3 GPH leak to the system. This leak may be introduced with the pump
running during the REPRESS CYCLE AS LONG AS THE LEAK DETETOR HAS STEPPED
THROUGH TO FULL FLOW.
On the right-hand pressure gauge of the LDT-890, verify that the pressure falls due to the 3 GPH leak. If
the proper delay has been entered, the pressure should fall to zero before the next Repressurization Cycle
is started.
16. At the end of the delay timing cycle, the ISM will automatically turn on the pump. Pressure will begin
to build but will stop at the value observed in Step 10 indicating that the leak detector has found the 3
GPH leak. If the 3GPH RETRIES is set to two or more cycles, the ISM Controller may retest 2 or more
times. The ISM-4080 controller should recognize the line leak after the cycles are completed, shutdown
the STP, and Alarm. This successfully completes the ISM test.
17. Disconnect LDT-890 Test Unit
Turn off the pump’s power breaker. Reprogram the repressurization disable time or turn off power to the
ISM to disable the repressure cycle.
18. With the large beaker under the LDT-890 discharge port, set the selector to the DISPENSER NOZZLE
position and bleed off fuel until the reading on the right-hand pressure gauge is zero.
19. Remove the LDT-890. Before re-energizing pump, ensure system is returned to tight status.
20. Full System Operation
Turn on the power breaker. If required, restore power to the ISM. Press the RESET > ENTER push-
buttons to reset all channels. This completes the test procedure. The system including the ISM-4080
Integrated Shutdown Module is now fully functional.

18
WIRING GUIDE –CONTROL VALVE APPLICATIONS
The wiring diagram on the following page represents the two terminal block groups located on the bottom
DIN rail of the ISM-4080 System. The right-side connections will need to be wired onsite. Please note
that not all sites will use all of the terminals. Note: Alarm Output #2 becomes a dedicated Sump Alarm
Output if CV Output #2 is not used.
It is the responsibility of the installer to determine which terminals will be used based upon the individual
site configuration. Only a qualified electrician familiar with the site should make the electrical connections
outlined below. Please contact VMI if you have any questions or concerns.
HIGH VOLTAGE TERMINAL
Main Power Supply:
(BLACK) 120 VAC (Hot) from a dedicated
15- 20-amp circuit breaker
(GREEN) Ground Connection
(WHITE) Neutral Connection
Authorization (Hook Signal) Inputs:
(BROWN) Authorization Input #1
(RED) Authorization Input #2
(ORANGE) Authorization Input #3
(YELLOW) Authorization Input #4
Turbine (Pump) Outputs:
(BROWN) Turbine Output #1
(RED) Turbine Output #2
(ORANGE) Turbine Output #3
(YELLOW) Turbine Output #4
Control Valve Outputs:
(BROWN) Control Valve Output #1
(RED) Control Valve Output #2
Alarm Outputs:
(YELLOW) Alarm Output #1
(ORANGE) Alarm Output #2
IS SWITCH I/O TERMINALS:
IS switch wiring connections are to be made using low capacitance data cable, 1 twisted pair, 24 AWG.
Please note that VMI recommends a high-quality shielded cable rated for data communication when
wiring the IS switches. Automation Direct Part Number L19827-1 is an ideal cable for this application.
If using another cable, please ensure that the cable specifications meet or exceed the ratings of this cable.
Properly landing the cable shield line(s) to the designated terminals is imperative for proper system
operation. Do not connect the cable shield line to a chassis ground. Doing so will likely cause system
instability and/or false alarms.
IS Switch #1
(BROWN) Output to IS Switch #1
(GREEN) Shield Line for IS Switch #1
(BROWN) Input (or Return) from IS
Switch #1
IS Switch #2
(RED) Output to IS Switch #2
(GREEN) Shield Line for IS Switch #2
(RED) Input (or Return) from IS Switch #2
IS Switch #3
(ORANGE) Output to IS Switch #3
(GREEN) Shield Line for IS Switch #3
(ORANGE) Input (or Return) from IS
Switch #3
IS Switch #4
(YELLOW) Output to IS Switch #4
(GREEN) Shield Line for IS Switch #4
(YELLOW) Input (or Return) from IS
Switch

19

20
WIRING GUIDE –NON-CONTROL VALVE APPLICATIONS
The wiring diagram on the following page represents the two terminal block groups located on the bottom
DIN rail of the ISM-4080 System. The right-side connections will need to be wired onsite. Please note
that not all sites will use all of the terminals. It is the responsibility of the installer to determine which
terminals will be used based upon the individual site configuration.
Only a qualified electrician familiar with the site should make the electrical connections outlined below.
Please contact VMI if you have any questions or concerns.
HIGH VOLTAGE TERMINALS
Main Power Supply:
(BLACK) 120 VAC (Hot) from a dedicated
15- 20-amp circuit breaker
(GREEN) Ground Connection
(WHITE) Neutral Connection
Authorization (Hook Signal) Inputs:
(BROWN) Authorization Input #1
(RED) Authorization Input #2
(ORANGE) Authorization Input #3
(YELLOW) Authorization Input #4
Turbine (Pump) Outputs:
(BROWN) Turbine Output #1
(RED) Turbine Output #2
(ORANGE) Turbine Output #3
(YELLOW) Turbine Output #4
Alarm Outputs:
(BROWN) Alarm/Sump Alarm Output #1
(RED) Alarm/Sump Alarm Output #2
(ORANGE) Alarm/Sump Alarm Output #3
(YELLOW) Alarm/Sump Alarm Output #4
IS SWITCH I/O TERMINALS:
IS switch wiring connections are to be made using low capacitance data cable, 1 twisted pair, 24 AWG.
Please note that VMI recommends a high-quality shielded cable rated for data communication when
wiring the IS switches. Automation Direct Part Number L19827-1 is an ideal cable for this application.
If using another cable, please ensure that the cable specifications meet or exceed the ratings of this cable.
Properly landing the cable shield line(s) to the designated terminals is imperative for proper system
operation. Do not connect the cable shield line to a chassis ground. Doing so will likely cause system
instability and/or false alarms.
IS Switch #1
(BROWN) Output to IS Switch #1
(GREEN) Shield Line for IS Switch #1
(BROWN) Input (or Return) from IS
Switch #1
IS Switch #2
(RED) Output to IS Switch #2
(GREEN) Shield Line for IS Switch #2
(RED) Input, (or Return) from IS Switch #2
IS Switch #3
(ORANGE) Output to IS Switch #3
(GREEN) Shield Line for IS Switch #3
(ORANGE) Input (or Return) from IS
Switch #3
IS Switch #4
(YELLOW) Output to IS Switch #4
(GREEN) Shield Line for IS Switch #4
(YELLOW) Input (or Return) from IS
Switch
Table of contents
Popular Security Sensor manuals by other brands

Homematic IP
Homematic IP HmIPW-SCTHD Installation instructions and operating manual
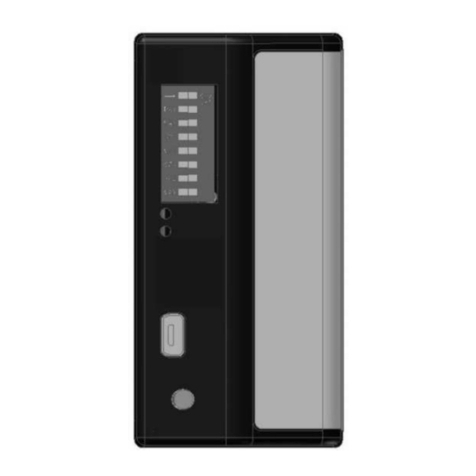
Feig Electronic
Feig Electronic VEK MNE1-R24-A operating instructions

PHYWE
PHYWE Cobra4 operating instructions

SELS
SELS AIRD-2730 user manual
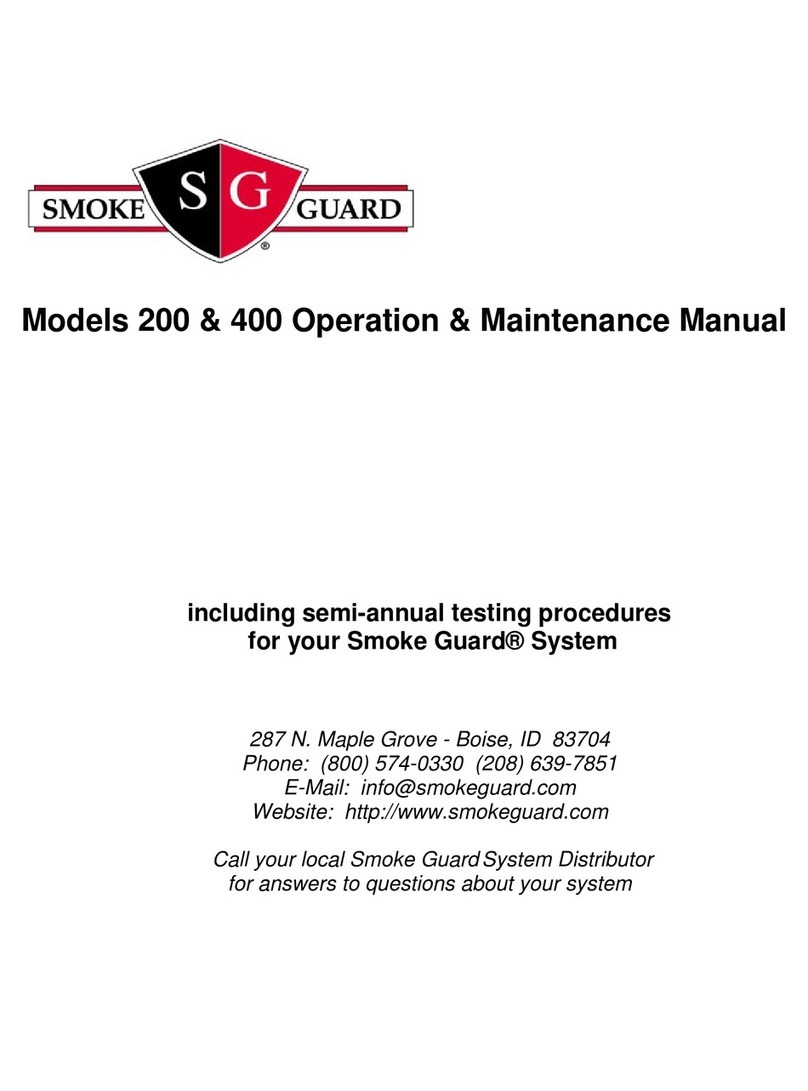
Smoke Guard
Smoke Guard 200 Operation & maintenance manual

Jäger Direkt
Jäger Direkt OPUS operating instructions