Vertex PureWaterMachine 3C Quick start guide

VERTEX
Water Products
PureWaterMachine
REVERSE OSMOSIS UNDERSINK
WATER FILTRATION SYSTEM
OWNERS INSTALLATION
MANUAL
™
VERTEX WATER PRODUCTS
Model 3C

The VERTEX PURE WATER MACHINE is made with quality components
to provide clean, safe drinking water. No chemicals are added or used
in this system. To preserve the filter capability, it is a must that the
filter replacement be made at the intervals and with replacement ele-
ments as specified in section 4.0 of this manual.
All filter elements are made in the USA and are NSF approved, includ-
ing the flow tubing and fittings.
Applicable Product Models
3C-4.0 (Standard model)
3C-4.0/P (With booster pump)
3C-4.0/UV (With Ultraviolet stage)
3C-14/P (With booster pump and 14 gallon tank)

Table of Contents
i.Notice . . . . . . . . . . . . . . . . . . . . . . . . . . . . . . . . . . . . . . . . . . . . . . . . pg. 1
ii.Parts List . . . . . . . . . . . . . . . . . . . . . . . . . . . . . . . . . . . . . . . . . . . . . pg. 1
1.0 Introduction . . . . . . . . . . . . . . . . . . . . . . . . . . . . . . . . . . . . . . . . . . pg. 1
2.0 Installation . . . . . . . . . . . . . . . . . . . . . . . . . . . . . . . . . . . . . . . . . . . . pg. 2
2.1 Location of RO Unit . . . . . . . . . . . . . . . . . . . . . . . . . . . . . . . . . pg. 2
2.2 Mounting the RO filter Unit Under a Sink . . . . . . . . . . . . . . . . pg. 2
2.3 RO Membrane Stage . . . . . . . . . . . . . . . . . . . . . . . . . . . . . . . . pg. 3
2.4 Connecting the Feed Water Supply . . . . . . . . . . . . . . . . . . . . . pg. 3
2.5 Installation of Drain Connection . . . . . . . . . . . . . . . . . . . . . . . pg. 5
2.6 Installation of Clean Water Faucet . . . . . . . . . . . . . . . . . . . . . . pg. 5
2.7 Porcelain/Enamel Over Steel or Cast Iron Sinks . . . . . . . . . . . pg. 6
2.8 Install Faucet . . . . . . . . . . . . . . . . . . . . . . . . . . . . . . . . . . . . . . . pg. 6
2.9 Tubing Connections . . . . . . . . . . . . . . . . . . . . . . . . . . . . . . . . . pg. 7
2.10 Air Gap Faucet Installation . . . . . . . . . . . . . . . . . . . . . . . . . . . . pg. 8
3.0 System Start Up . . . . . . . . . . . . . . . . . . . . . . . . . . . . . . . . . . . . . . . pg. 9
3.1 Start-Up . . . . . . . . . . . . . . . . . . . . . . . . . . . . . . . . . . . . . . . . . . pg. 9
3.2 Air Purge . . . . . . . . . . . . . . . . . . . . . . . . . . . . . . . . . . . . . . . . . pg. 9
4.0 Recommended Filter Changes . . . . . . . . . . . . . . . . . . . . . . . . . . . pg. 9
4.1 Filter Replacement, Pure Water Machine . . . . . . . . . . . . . . . . . pg. 9
4.2 Standard Filter Elements . . . . . . . . . . . . . . . . . . . . . . . . . . . . . pg. 10
5.0 Filter Replacement Procedure . . . . . . . . . . . . . . . . . . . . . . . . . . . . pg. 10
6.0 Installation Troubleshooting . . . . . . . . . . . . . . . . . . . . . . . . . . . . . pg. 11
7.0 Conditions of Use . . . . . . . . . . . . . . . . . . . . . . . . . . . . . . . . . . . . . . pg. 11
8.0 Product Warranty . . . . . . . . . . . . . . . . . . . . . . . . . . . . . . . . . . . . . pg. 11
9.0 Other Models . . . . . . . . . . . . . . . . . . . . . . . . . . . . . . . . . . . . . . . . . pg. 12
9.1 Pure Water Machine with booster pump . . . . . . . . . . . . . . . . . pg. 12
Appendix A: Theory of Operation . . . . . . . . . . . . . . . . . . . . . . . . . . . . pg. 13

iNOTICE
This instruction manual was written to guide a professional plumber to make an easy
installation of the VERTEX Pure Water Machine. The installation shall conform to local
plumbing codes.
It is imperitive to install a pressure regulator in front of the unit or at water point of entry
to prevent this system from experiencing pressure spikes above 90 psig.
This filter system can be installed by the homeowner who has sufficient tools and
skills. Be cautioned that an extra faucet for purified water will be installed . This requires
a 7/8-inch diameter hole in the sink top. If there is not an extra hole existing, a new one
must be drilled. For a porcelain sink, this requires a special drill (7/8" Relton cutter) which
costs about $100 and requires skill to use.
ii PARTS LIST
PARTS CONTAINED IN THE PURE WATER MACHINE CARTON
1-Box containing storage tank
1-Box with filter assemblies
1-Set of 1/4" plastic tubes, orange, black, 3/8” tubes, yellow, and white
1-clean water faucet and fittings
1-set of hardware consisting of:
Inlet water 1/4" ball valve and 1/2" feed line adapter
3/8" plastic ball valve for tank shutoff
Drain saddle clamp

1.0 INTRODUCTION
The VERTEX Pure Water Machine is a 4-stage water cleansing system. The princi-
pal cleansing of the water of its dissolved solids is by the Reverse Osmosis membrane fil-
ter (stage 3).
Stage One is a sediment filter which removes particles of rust, sand and other trash
in the water line down to 5-microns in size.
Stage Two is an activated carbon block filter which removes odors, chlorine and for-
eign tastes.
Stage Three is an advanced reverse osmosis membrane for removal of dissolved
solids. This is the heart of the system. The reverse osmosis technology removes 95% of
the dissolved solids on average. Dissolved solids are not removed by municipal water
treatment. That is why the Vertex Pure Water Machine is an important safety factor for the
water you drink and use in your cooking. Chemical contaminants such as mercury, lead,
nitrates, pesticides and others not yet identified which seep into municipal water systems
are removed. Bacteria such as cryptosporidium and giardia lamblia and others yet
unknown are removed. The RO system works differently than standard mechanical filters,
such as the two pre-filters in this system. The RO splits the incoming water into two
streams-clean water and brine water. The brine water carries away the contaminants. The
water pressure against the reverse osmosis membrane forces the water molecules through
the membrane, but the larger contaminant molecules and bacteria are kept behind and are
flushed to the sewer. The clean water goes to the storage tank and is held there ready to
use. When the faucet is opened, clean water from the storage tank flows through the final
polishing filter (Stage Four) of activated carbon and into the faucet for your use. The tank
is prepressurized with a bladder which pushes the water out through Stage Four.
On your sink, a special faucet is installed which is your safe, good tasting drinking
water, and especially good for coffee, tea and drinks. By extending a line to your refrig-
erator, it can be used to make ice cubes.
LIFE. The filter life is specified by the number of gallons of water flowing through
the system. Normal household will use two to three gallons of purified water daily. The
filters are good for 1500 to 3000 gallons total usage. Therefore, to be safe, the filters, that
is, Stage 1, 2, and 4, should be changed once per year. The reverse osmosis membrane has
a 5-year shelf life and a 3 to 4-year working life. It is recommended this membrane be
changed once each four years. See section 4.0
– 1 –

– 2 –
2.0 INSTALLATION
Before starting the installation, you should measure the water pressure that is avail-
able under the sink to power the Pure Water machine RO. If the pressure is less than 40-
PSIG, it is too low; and if it is 90-PSIG, it may be too high. The solution if the pressure
is too low is to use a model with a booster pump. The solution for high water pressure, is
to put a pressure regulator in the inlet water line to the house. A pressure of 60-75 PSIG
is normal.
2.1 Location of RO unit
The RO unit may be located under the kitchen sink or in the basement. A cold
water supply line must be close by. When locating the system under a sink make sure
there is adequate room for the filter module assembly as well as the storage tank. For
best performance the tank should be located as close to the clean water faucet (sup-
plied) as possible (within 20 feet).
2.2 Mounting the RO filter unit under a sink (Fig. 1.)
Mount the unit to the wall of the sink cabinet. Pre-fit the unit by positioning the
bottom of the pre-filter cartridges 2 inches off the floor of the cabinet. This clearance
is necessary to make room to remove the housings when replacing the filter car-
tridges. Mark the location of the 2 mounting holes in the mounting bracket. Install 2
mounting screws leaving 1/8 inch clearance under the screw head. Check fit the
mounting of the RO filter unit but don’t install yet.

– 3 –
Figure 1
To Clean Water Tank
RO SYSTEM TOP VIEW
CHECKVALVE
ASSEMBLY
3/8”
1/4”
3/8”
FLOW
RESTRICTER
INSIDE
DRAIN TUBE
Existing Water Supply

2.3 RO Stage
Note that the RO housing on the bracket in Figure 1 (horizontal element on top
of the bracket) already contains a pre-installed 75 GPD (gallon per day) membrane.
There is no need to install the membrane, and when it is time to replace the membrane,
the whole element including the housing is discarded. Note that the fittings are the
"push-type" (John Guest type) to seal, and are easily disconnected from the tubing.
The tubing is color coded. Orange for feed water through the 2-pre-filters to the
auto-valve "IN" connection and from auto-valve "OUT" connection to the inlet of the
membrane housing. Then the clean water from the from the RO is a white line to the
auto-valve and from the auto-valve to the tank (yellow tubing is provided). The reject
or brine line from the RO is colored black and connects to the sewer line under the sink.
2.4 Connecting the feed water supply (Fig. 2)
The feed water assembly consists of 1/2” brass slip joint adapter, a black wash-
er, and a 1/4” x 1/4” ball valve. Locate these parts in the installation kit.
Locate the cold water shut off valve under the sink and turn it off. Open the cold
water faucet to release the pressure. On single handled faucets, the hot water may
have to be turned off to prevent any hot water cross-over. If water continues to come
out of the faucet with the under-sink valves turned off, the house main valve will have
to be turned off.
Now that the water has been turned off, disconnect the cold water riser tube (flex
line) from the valve. Install the slip joint connector with the black washer. Loosen the
nut and separate the cold riser tube from the faucet shank. Gently bend the riser tube
so that the slip joint adapter fits onto the faucet shank. Reinstall the cold riser tube on
the slip joint connector using the existing cone washer. For Solid copper tube the pro-
cedure is the same except you must cut a piece of the riser tube about 3/4” to 1” so
the slip joint adapter can fit between the valve and the riser tube. Wrap several turns
of teflon tape on the ball valve and install on the slip joint connector.
In some cases the Pure Water Machine is supplied with a saddle Valve which can
clamp over a copper pipe and make the hole and seal at once. (See figure 3).
Figure 2 Figure 3
– 4 –
Existing Cold Water
Line to Sink
1/4”Tubing
(orange)
Ball Valve
Rubber
Grommet
1/2”Slip Joint
Adapter
Black Washer
Existing Cold Water
Supply Valve
Nut
Valve with
Piercing Point
1/4” Feed
Clamp
Copper
Water
Line

– 5 –
2.5 Installation of drain connection (Fig. 4)
Place the drain outlet saddle on the drain pipe. Allow proper space for the
drilling operation. Tighten the saddle bolts evenly on both sides. Using the opening
in the drain outlet saddle as a guide, drill a 1/4”hole in the drain pipe. Clean any
debris out of the drain saddle connection.
Figure 4
2.6 Installation of clean water faucet (Fig. 5.)
The faucet should be positioned
with aesthetics, function, and con-
venience in mind. An ample flat
area is required for the faucet base
so that it can be drawn down tight.
The space under the sink below
where the faucet will be mounted
must be clear of any obstructions.
Some conditions may eliminate
the need to drill a hole in the sink
such as a faucet previously
installed in the sink, a hole cov-
ered by a chrome hole cover, or
an unused spray handle. If any of
these situations are present, you
may mount the faucet in one of
these holes. continued...
Vertical
Mount
Foam
Sealing
Washer
Compression
Fitting
1/4”tube
(black)
Horizontal
Mount
Do Not
Mount Here
Disposal
Sink Sink
Maximum Displacement
from Top Center –30˚
RO Drain Line
Step 2.
Spring Loaded
Porcelain Saw
(Relton Cutter)
Step 1.
Pilot Drill

– 6 –
The sink drilling process is not
complicated, but requires a cer-
tain amount of caution and fore-
thought. Porcelain sinks can be
chipped if care is not exercised
when drilling the hole for the
faucet.
[NOTE: This procedure is for the non air gap faucet provided.]
2.7 Porcelain/Enamel over Steel or Cast Iron Sinks
Using a small diameter carbide tipped drill, drill a pilot hole completely through
the porcelain and the material underneath. Remove any metal chips that fall into the
sink to prevent rust stains. Place the spring-loaded porcelain cutter bit in to the drill
chuck. Make sure the pilot guide is inserted tightly. Insert the pilot guide onto the
pilot hole. Push down gently on the drill motor to apply light pressure to the porce-
lain surface. Start the drill motor, turning as slowly as possible. After the initial cut
has started, motor speed may be gradually increased. The cut may require three to
four minutes to complete. Going faster could result in excessive chipping. Be sure a
complete ring has been cut through the porcelain to the metal underneath.
Place the finish hole saw into the drill chuck. Make sure the pilot guide is insert-
ed tightly. Insert the pilot guide into the pilot hole. Begin cut using a slow speed and
light pressure until the porcelain has been penetrated to the material underneath.
Remove the saw from the hole and clean all debris from the porcelain surface.
Reinsert saw into the hole and cut through the remaining material.
2.8 Install Faucet (Fig. 6)
Figure 6
Disassemble the hard-
ware from the threaded
stud except for the top base
plate and sealing gasket.
Install the faucet in the sink
hole. From below the sink
assemble the mounting
hardware. Use a deep sock-
et to tighten the nut.
Step 3.
Finish Hole Saw
Small Rubber Washe
r
Counter Top
Lock Washe
r
Nut
Black Locating Washer
(used where a 1/2”hole is
available, reverse when
mounting on stainless steel
or when using drilled hole)
Escutcheon Plate
Black Rubber Washer
Push-in Fitting, 7/16" X 3/8" Tube.
3/8”Tubing (White)

– 7 –
2.9 Tubing Connections
a.
The model 3C-4.0 has the quick-connect “push-in”fittings. These fittings have
a collet to grip the tube and an “o”ring to provide the seal to the tubing. The col-
let has steel teeth in it to grasp the tubing to prevent it from backing out.
b.
Making a connection. To make a connection, first cut the tubing so it has a square
end. The tube must be clean and the surface smooth. Push the tube into the col-
let as far as it will go. See the diagrams below
c.
Disconnecting
d. Feed Water Line
Connect the orange colored 1/4”inlet tubing to the ball valve installed in step 2.4
above. To connect, remove compression nut and ferrule and slide on to tube. Insert
tube over the ball valve tube as shown in Fig. 2. Slide nut over threads and tighten.
e. Drain Line
Find the black colored 1/4”tubing. Connect the tube to the drain saddle clamp
from step 2.5. Push tube into fitting about 1/2 inch. Tighten plastic nut.
f. Faucet Line
Find the push-on fitting that screws on the faucet. Thread onto the faucet stem.
Find the white colored 3/8”tubing and push the tube into the fitting until it stops.
g. Tank Line
Install the plastic ball valve on the storage tank. Find the yellow colored 3/8”
tubing. Connect the tube to the plastic ball valve on the tank. Push tube into fit-
ting until it stops. Turn the valve to the on position. The tank comes pre-charged
from the factory at 5-7 psi. Double check the pressure with a tire gage (the air
fitting is on the opposite end of the tank from the ball valve). If it is less than 5
psi add 2psi with a compressor or bicycle pump. Note: Putting more pressure
than 7 psi does not help to increase water flow through the faucet.
Cut the tube square. It is essential that the outside diameter is free of score
marks and that burrs and sharp edges be removed before inserting into fitting
Fitting grips before it seals. Ensure tube is pushed into the tube stop
Push the tube into the fitting, to the tube stop. The collet (gripper) has stain-
less steel teeth which hold the tube firmly in position while the “O” ring pro-
vides a permanent leak proof seal
Pull on the tube to check it is secure. It is good practice to test the system
prior to leaving site and/or before use.
To disconnect ensure the system is depressurized before removing fitting.
Push in collet squarely against face of fitting. With the collect held in this
position, the tube can be removed. The fitting can then be re-used.
Cut the tube square.
Insert tube
Push in collet and remove tube
Pull to check secure
Push up to tube stop
“O” Ring Collet
Stainless Steel Teeth

– 8 –
2.10 Air-Gap Faucet Installation (Fig. 9)
Air-Gap Faucets are sometimes required by municipal code. The faucet is designed
to take the waste water from the membrane to the top of the sink and then let it flow by
gravity to the drain saddle. The objective is to prevent possible backup of drain water
from the sink to the membrane in the event of a sink clog. A drain saddle with 3/8" instead
of 1/4" is used. An extra section of 3/8" tubing (black) is used from the faucet to the drain.
Sink Preparation
Drill the appropriate size hole in the kitchen sink to accommodate the air-gap faucet.
Drain Connection
Follow instructions of section 2.5 except drill a 3/8" hole in the drain pipe.
Tubing Connections
Find the black colored 1/4" drain line from the membrane. Remove from mem-
brane housing. Connect this tube to the 1/4" barbed fitting on the air-gap faucet.
Find the 3/8" black tubing in the parts kit. Connect this tube to the 3/8" barbed
fitting on the air-gap faucet. Install the faucet assembly (with tubes attached)
into the sink hole. Secure the faucet per instructions in section 2.8. Re-attach the
1/4" black tubing to the drain side of the RO membrane housing. Be sure to
tighten the fitting nut securely. Attach the 3/8" tube to the drain connector.
Tighten the fitting nut securely. Attach the pure water line to the faucet per the
instructions in section 2.9-f.
Small Rubber Washe
r
Counter Top
Lock Washe
r
Nut
Black Locating Washer
Escutcheon Plate
Black Rubber Washer
3/8”Tubing (White)
Drain line 1/4" from RO
to Airgap (Black)
Push-in Fitting, 7/16" X 3/8" Tube.
3/8 drain line from Airgap
to drainsaddle (Blue)
Figure 9
Escutcheon Plate
Black Rubber Washer
Black Locatin
g
Washer
3/8 drain line from Airgap
to drainsaddle (Blue)
Drain line 1/4" from RO
to Airgap (Black) 3/8”Tubing (White)
N
ut
Lock Washe
r
Counter Top
S
mall Rubber Washe
r
P
ush-in Fitting, 7/16" X 3/8" Tube.

– 9 –
3.0 System Start Up
3.1 Start-Up
Start the system by opening the feed water ball valve. Make sure the ball valve on
the storage tank is in the closed position. Check for leaks for at least 10 minutes. If water
leaks from a fitting, retighten the fitting nut. Open the product water faucet and let the
water flow until all the air has been expelled from the system. This will take about 30 min-
utes. Close the product water faucet. Make sure drain water has stopped flowing within one
minute.
Open the tank ball valve and let the system run about 2-hours to get a complete tank-
ful. Then open the clean water faucet on the sink and empty the tank. This is to flush the
system and remove the preservative from the RO membrane, as well as flush carbon
"fines" from the post filter
If the waste continues to run after the tank is full, it may mean there is air binding the
autovalve. Empty the tank again by opening the faucet. This will help to clear more air
from the system. If the waste water running persists, remove the connection and the stain-
less steel checkvalve at the outlet of the RO stage (fig. 1). Clean the check valve, reassem-
ble and start the system again.
3.2 Air Purge
The water moves slowly through the PureWaterMachine™. Small amounts of
air therefore tend to hang up in corners and accumulate over a period of time. This
can cause the autovalve to malfunction (not close properly), letting water run contin-
uously to the drain. The instructions in 3.1 “startup”should be rigidly followed.
4.0 Recommended Filter Changes
4.1 Filter Replacement, Pure Water Machine
Filter element replacements of Stage 1, Stage 2, and Stage 4 are mandatory once
a year to maintain water purity.
The recommended replacement frequency is listed below:
Part Number Replacement Frequency
Sediment Filter Element, Stage 1 SF-4001 6-12 Months
Pre-Carbon Filter Element, Stage 2 CF-4000 6-12 Months
RO Membrane Assembly, Stage 3 MH-4206 3-5 Years
Post Carbon Filter Element, Stage 4 CF-4008 6-12 Months
These filter replacement elements are available from your dealer. When you buy
or install your Pure Water Machine, we recommend that you buy the first year filter
replacement kit. This includes Stage 1, 2 and 4 filter elements.
This kit comes in a plastic satchel which can be attached to the installed Pure

– 10 –
Water Machine under your sink. There is a space to write in the date of replacement,
which is one year from date of installation. In this way you will have your reminder
date for replacement and the parts to do it at hand. Kit part number is FK-102
In the replacement kit are instructions for replacement and cleaning, and a handy
wrench to unscrew the Stage 1 and Stage 2 filter bodies. A post card order form for
the next replacement kit is included, ready for you to send in for the new replacement
kit for the next year.
At year 4 (or sooner if you have severe water problems),we recommend that the
Stage 3 reverse osmosis assembly be changed also. When you order your fourth year
kit from your Vertex dealer, this will be included, along with the other three elements.
Kit part number is FK-102/75
4.2 Standard Filter Elements
The Stage 1, 2 and 4 elements are standard and are available in many large hard-
ware stores. The descriptions below may be used to get comparable elements for the
Vertex model 3C-4.0 Pure Water Machine.
Stage 1 Sediment filter, standard size, 2-3/4”dia. by 9-3/4”long, polyspun fiber,
5 micron, made by Osmonics, "Purtrex". Vertex P/N S-4001
Stage 2 Activated Carbon block filter, 2-3/4”dia. by 9-3/4”long (10”nominal),
10 micron, made by KX, "CTO"/2. Vertex P/N CB-4000
Stage 4 Activated carbon post-filter, 2 3/4”dia by 9 3/4”long, granulated carbon fill.
Vertex P/N P/N CF-4008
Stage 3 This is the reverse osmosis element. It may be obtained from your deal-
er or ordered direct from Vertex Water Products, 909-626-2100. It is des-
ignated as a TFC (thin film composite).
Vertex P/N MH-4206
5.0 Filter Replacement Procedure
Turn off the feed water at the feed water ball valve. Empty at least 2.0 gallons
from the storage tank to take any back pressure off the system. Put a shallow pan
under the RO system to catch any water that may spill during the operation.
Unscrew the filter housing and carefully lift it to the sink to drain or empty the
water remaining in it. Remove the spent filter cartridge. Sanitize by adding 4 table-
spoons of chlorine bleach to the empty housing and then filling with tap water. Let stand
for 10 minutes. Empty the solution and rinse with clear water and dry. Install new car-
tridge in housing. Reinstall housing being careful to make sure o-ring is properly seat-
ed. Tighten housing securely. Re-start the system by opening the feed water ball valve.
The filter canisters, sediment and carbon, including the the caps must be replaced
every 5 years. Order Vertex part number FH-1000 to obtain original equipment replace-
ment part.

– 11 –
6.0 Installation Troubleshooting
7.0 Conditions Of Use
Water must be microbiologically safe. System pressure, 40 to 100 PSIG.
Temperature, 40 to 100 degrees F. PH Range, 3 to 10. Maximum TDS, 1500 PPM.
Turbidity, less than 1.0 NTU. Max iron content, 0.3 ppm
8.0 Product Warranty
The VERTEX Pure Water Machine components, specifically the bracket, the filter
housings, the filter elements, tank and valves are warranted to be free of defects. Any
defect arising in these items within one year from date of purchase will be replaced at no
cost. Example - if the filter housing is cracked and leaks during the warranty period, we
will replace it at no cost. Procedures in the manual must be followed during installation
and maintenance.
There is no liability assumed by the company for damage due to water leakage
or other secondary effects from the component defects. Labor for installation is not
covered in this warranty.
Problem
•No or low water production.
•Leak at filter housing.
•Leak at threaded connection.
•Bad-tasting water.
Possible Cause
•Feed water shut off.
•Tank valve closed or
partially closed.
•Low feed pressure.
Feed pressure must by at
least 40 PSI.
•Defective or misaligned
O-ring.
•Not properly tightened.
•Post-filter cartridge not
flushed completely.
Solution
•Turn on feed water.
•Open tank valve.
•Increase inlet water pressure
or install booster pump if
feed water pressure is less
than 40 PSI.
•Shut off feed valve and tank
valve. Turn on faucet.
Change or realign O-ring.
•Tighten compression fitting.
•Flush one or two tanks of
pure water through system.
•Water runs to drain all the
time.
•Auto-valve not closing prop-
erly.
•Purge the system again.
Lock the clean water valve
open and turn the inlet
water on for thirty minutes
•RO Production good at first
but falls off in months or
weeks.
•High TDS and/or Iron and
Manganese.
•Consult your dealer or
Factory and provide water
analysis.

9.0 Other Models
9.1 Pure Water Machine with booster pump; Configuration and operation Model 3C 4.0/P
The 4 stage RO system with pump is used when the city water pressure is below
40 psi. The booster pump allows the RO system to run at peak efficiency by provid-
ing a pressure of about 80 psi to the RO membrane.
The model 3C-4.0/P, 4 stage RO system with booster pump includes these addi-
tional components: A 24 volt DC diaphragm pump powered by a step down trans-
former, (115 VAC/24 VDC 60 hz) a high pressure switch to monitor the pressure in
the storage tank and turn the pump off when the tank is full.
Installation and Operation
Install the RO system per the instructions in the previous section of this manual.
To start the RO system operating, turn on the water supply. But before plugging
in pump transformer, perform the air-purge procedure outlined in section 3.1. After
airpurge has been completed plug in pump transformer to an electrical outlet. The
pump will start running. From this point on follow the rest of the start-up procedure.
The pump will now operate automatically. The pump will start running. From this
point on follow the normal start up procedure for the RO system. The pump will now
operate automatically.
12

– 13 –
Appendix A: Theory of Operation
Figure A-1: Flow Schematic
A.1 Pre-Filters:
The pre-filters have two purposes, one is to clean the water for better consumption,
and the second is to prevent the RO membrane from being fouled. The RO membrane is
at the heart of this system, taking out dissolved materials from the water. The first stage fil-
ter removes sediment, that is materials such sand, rust, pipe scale, and dirt. This is accom-
plished with spun polypropylene material that will take out particles down to 5 -microns.
The water then goes to the carbon block filter, which is there for two reasons; first to
take out 90% of the chlorine in the water- this protects the RO membrane which would be
damaged by prolonged presence of chlorine. The carbon block also takes out the taste of
chlorine, and other tastes and odors too, which affect the drinking water, and changes the
flavor of tea, coffee or other mixed drinks. The carbon accomplishes this by adsorption on
its surface. This is a chemical/mechanical process unique to carbon that is activated, that
is, made to have high surface area.
The second reason is the carbon block also takes out VOC’s (volatile organic chem-
icals) which are contaminants from industrial pollution.
AUTO
VA LV E
CLEAN
WATER
TANK
BLADDER
AIR PRESSURE
AIR VALVE
CARBON
BLOCK
FILTER
SEDIMENT
FILTER
ORIFICE
FLOW CONTROL
CHECK VALVE
FEED
WATER
DISCARDED WATER
RO MEMBRANE
CLEAN WATER
POST FILTER
PURE WATER
FAUCET

A.2 The Reverse Osmosis Membrane:
This is the heart of the Machine, and is the great protector. The membrane is a replica-
tion of human or animal stomach tissue, which permits the water molecule to pass through,
and holds dissolved molecules back. This is done naturally by osmotic pressure developed
because of the content of dissolved solids. To make this happen with the RO membrane, we
apply pressure to the water (reversing the process of generating pressure) and this pushes the
water molecules through, keeping most of the dissolved solid molecules behind. “Most”
means about 70% of nitrates are kept behind, and 99% of Copper and Lead, and high mol-
ecular weight material. The reverse osmosis technology will, on average, reject 95% of the
total dissolved solids in the incoming water. Over time, the RO membrane will foul with a
very thin layer of materials, and the efficiency drops, so that the TDS content of the clean
water will rise. When it rises from 10% of the inlet TDS value, it is an indicator that the RO
membrane should be replaced. In large units, the RO can be cleaned periodically by back
wash, but for home units, the cost of replacement is low and usually only needs to be made
every 3 years. About 4 gallons of water is discarded for every gallon of pure water made. In
Figure A-1, the discard is shown with a flow control orifice at the outlet of the RO stage.
This is designed to hold back the discard water to the above ratio, and maintain pressure on
the water in the membrane. For a 75-gallon per day membrane, approximately 788 milliliters
per minute of water are discarded. Note there is a check valve on the clean water outlet from
the RO. The purpose is to prevent backflow of water to the membrane from the tank or
faucet or because of autovalve failure. In the average household, 3 gallons of drinking water
are used a day.
A.3 Auto Control:
As water is produced , the pressure in the storage tank increases. To stop production of
water when the tank is full, an auto control valve is used in the system, as shown in Figure
A-1. The pressure in the tank is set nominally at 2/3 of the incoming line pressure. Normal
U.S. city water pressure is 60-psi, therefore the tank pressure when full and when water flow
stops is at a tank pressure of 40-psi.
The purified water goes to the tank where it is stored at pressure as described above.
The tank has a bladder in it, and on one side is air at 6-psi, initially. The initial volume of the
storage tank is 4.0 gallons. As the water fills the tank, it pushes against the bladder, and rais-
es the pressure as it takes space in the tank. When the pressure increases to 40-psi, water flow
stops. The net amount of water in the tank when full, less the space taken by the air at 40-
psi is approximately 2.5 gallons. When water is drawn by opening the clean water faucet on
the sink, water flows through the final post filter, another activated carbon filter, which pol-
ishes, or take out staleness of the water which has set in the tank, and the last few molecules
of taste or odor. When water is supplied to the refrigerator, the line should be therefore taken
after the post filter.
When the raw water pressure available is 40-psi or less, the RO membrane will not
operate efficiently or produce water at a reasonable rate. This is overcome by using a boost-
er pump which raises the water pressure to 80-psi.
14

Notes
Water Disinfection
with chlorine bleach (5.25%)
Clean Water
2 drops
8 drops
1/2 tsp.
Cloudy Water
4 drops
16 drops
1 tsp.
Quantity
1 quart
1 gallon
5 gallons
15

VERTEX WATER PRODUCTS, Montclair, Calif.
M-2 Rev B • 10/02
Copyright 2002
VERTEX Industrials, Inc.
This manual suits for next models
4
Table of contents
Other Vertex Water Filtration System manuals
Popular Water Filtration System manuals by other brands
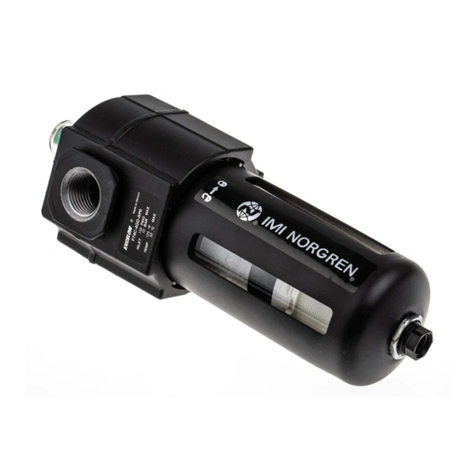
Norgren
Norgren F74C Series Installation & maintenance instructions
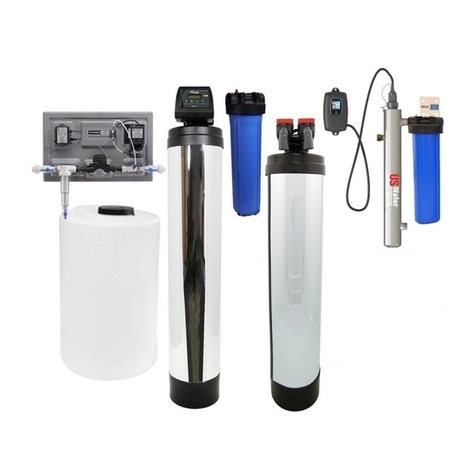
US Water Systems
US Water Systems 385-GWU-1000 owner's guide
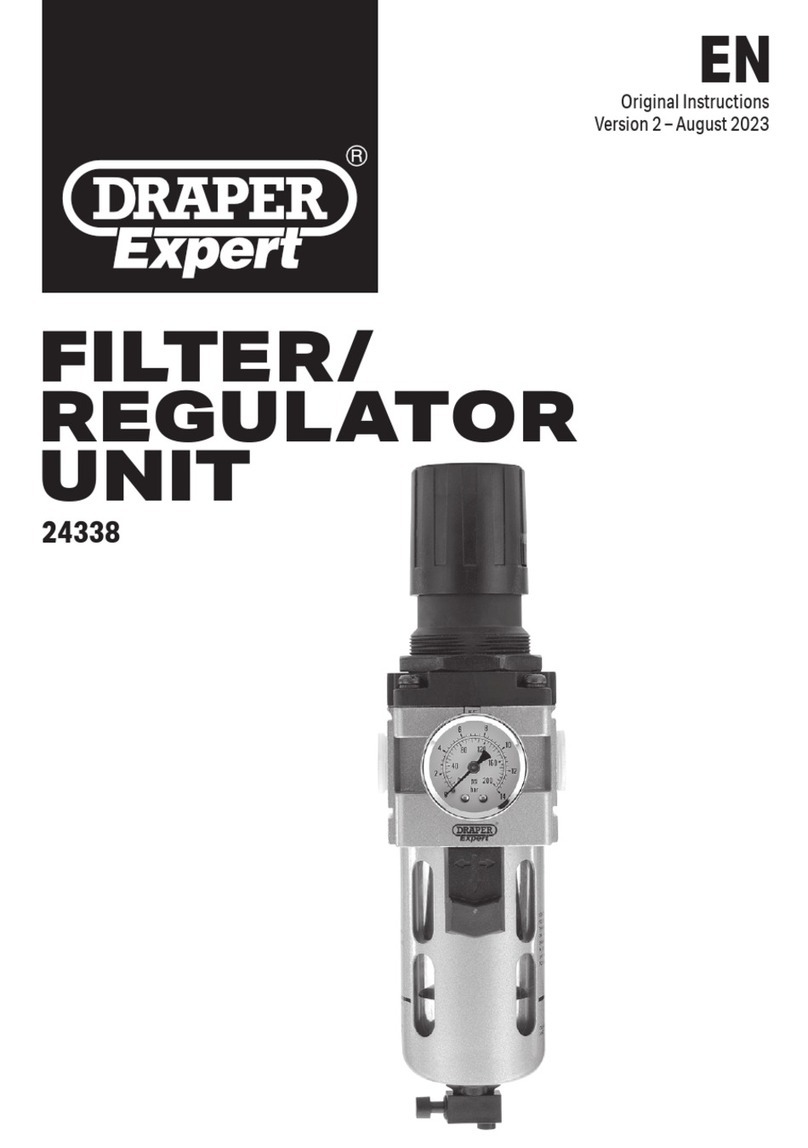
Draper
Draper Expert 24338 Original instructions
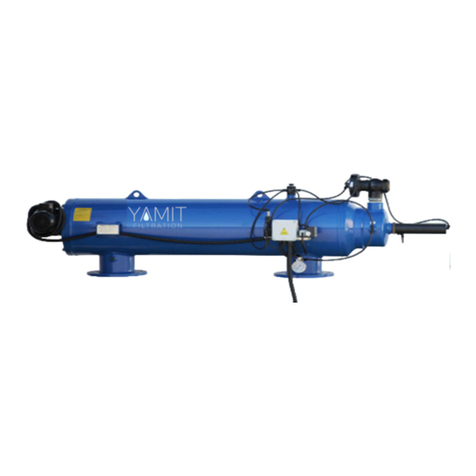
YAMIT
YAMIT AF-9800 Series Service maintenance manual
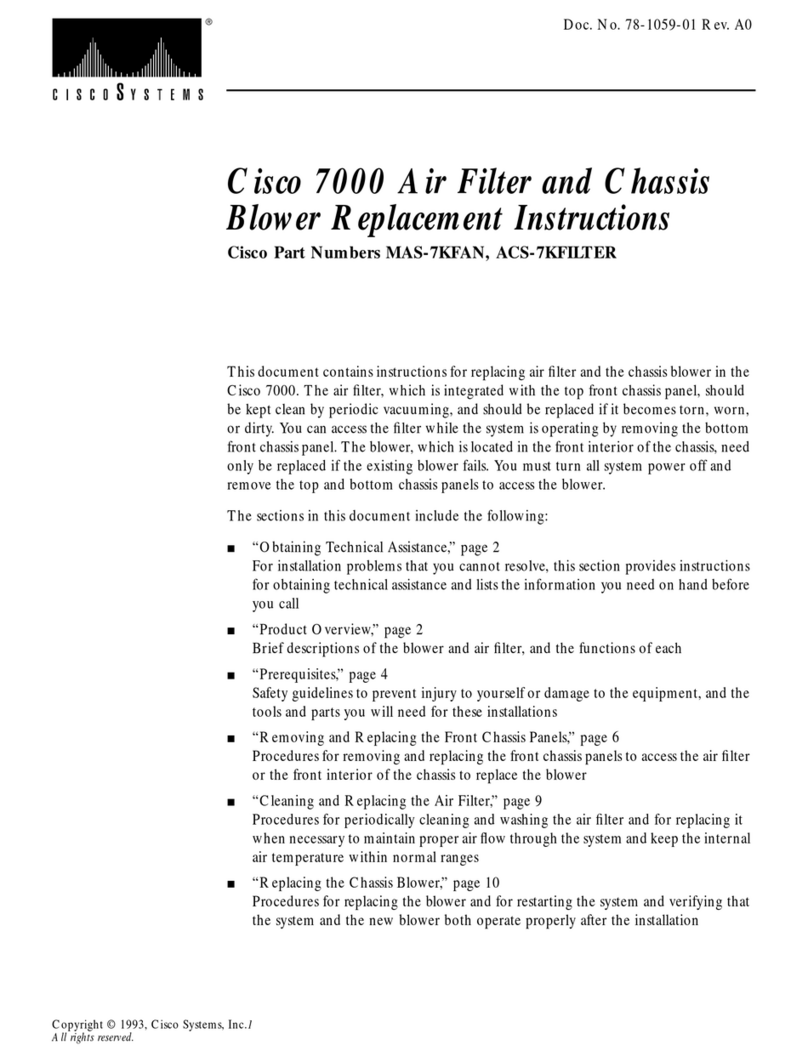
Cisco
Cisco Nexus 7000 Series Replacement instructions
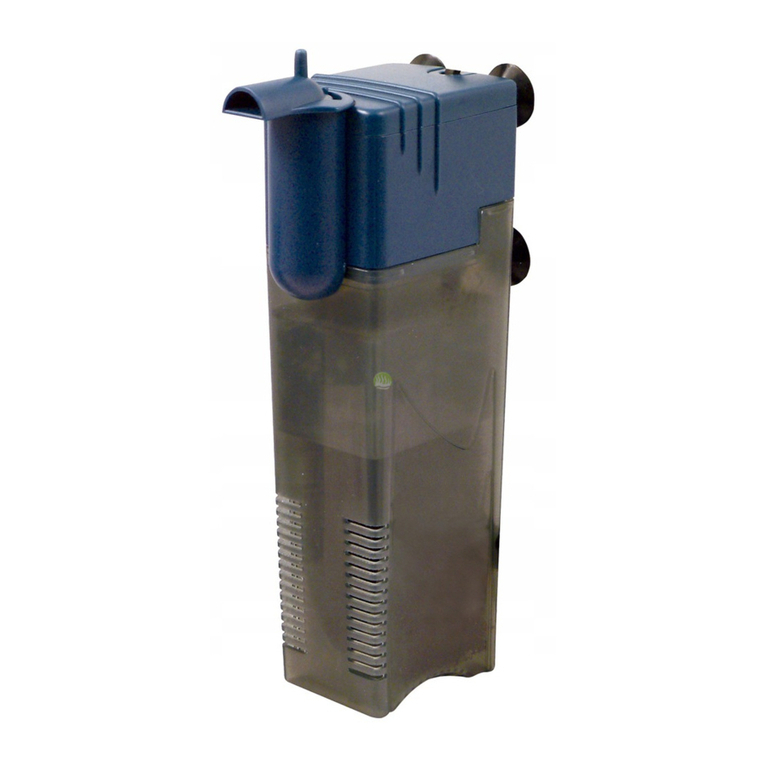
Hagen
Hagen ELITE JET-FLO 50 user manual