Vexve BFS400W1 User manual

Butterfly valves
Installation, operation and maintenance manual

2 3
www.vexve.com
Contents
1. General 4
2. Valve identification 5
3. Unloading and storage 6
4. Valve installation 8
4.1 Valve location in the pipeline 10
4.2 Installation positions of the valve 11
4.2.1 Installation in a horizontal pipeline 12
4.3 Pipeline supports and pipeline reducers 13
4.4 Installation at end of pipeline 14
4.5 Welding procedures 15
4.5.1 Installation in a vertical pipeline 16
4.5.2 Welding with connection pipes (recommended method) 16
4.6 Installation of valve with flanged connections 17
4.7 Before commissioning 18
4.8 Flushing 18
4.9 Commissioning 19
4.10 Pressure test 19
5. Actuator disassembly and installation 20
5.1 Removing the actuator 20
5.2 Changing the actuator installation position 21
5.3 Actuator installation 21
5.4 Electric actuator 21
5.5 Hydraulic actuator 21
5.6 Actuator installation positions 22
6. Maintenance 24
6.1 Replacing the stem O-ring seal (BFS/BRS valves) 25
6.2 Replacing the stem graphite packing (BFC/BRC model) 26
7. Appendices 27
7.1 Parts list for BFS/BRS models 27
7.2 Parts list for BFC/BRC models 28
7.3 Type code 29
7.4 Coupling dimensions, BFS/BRS models 30
7.5 Coupling dimensions, BFC/BRC models 31

2 3
www.vexve.com www.vexve.com
NOTE:
This manual must be read and its instructions must be followed when installing,
operating and/or performing maintenance on the valve as well as its manual gear or
actuator.
These instructions are of general nature and do not cover all possible operating scenarios. For more spe-
cific guidance on the installation, operation and maintenance of the valve or its suitability for an intended
use, please contact the manufacturer.
Vexve Oy reserves the right to make alterations to these instructions.
Vexve Oy is not responsible for damages caused by incorrect transportation, handling, installation, opera-
tion or maintenance. Furthermore, Vexve Oy is not responsible for damage caused by foreign objects or
impurities.
Warranty
Warranty according to Vexve Oy’s “General terms and conditions of sale”.
The warranty covers manufacturing and material faults. The warranty does not apply to damages caused
by inappropriate installation, operation, maintenance, or storage ie. these instructions must be followed
for the warranty to apply. Vexve Oy requires that any faulty products under warranty are to be returned to
the factory for inspection. Only after the product has been found faulty, Vexve Oy can grant compensa-
tion.
Please refer to Vexve Oy’s “General terms and conditions of sale” for detailed warranty clauses.
The document is available from the manufacturer
Warnings and symbols
Ignoring the warnings and symbols may lead to serious injury or equipment damage. Persons
authorized to use the equipment must be familiar with the warnings and instructions.
Appropriate transportation, storage and installation as well as careful commissioning are essential to
ensure faultless and stable operation.
The following symbols are used in this manual to draw attention to actions essential to ensure the proper
use and safety of the device.
Meaning of the symbol: NOTE
The NOTE symbol is used for actions and functions that are essential for the proper use
of the device. Ignoring this symbol may have harmful consequences.
Meaning of the symbol: WARNING
The WARNING symbol is used for actions and functions that, if carried out incorrectly,
may lead to injury or equipment damage.
© 2020 Vexve Oy - All product names, trademarks and registered trademarks are property of Vexve Oy.

4 5
www.vexve.com
-40 ºC260230200170140110805020-10
MPa
3
2
1
0
BFC / BRC
BFS / BRS
1. General
Vexve Oy’s butterfly valves are high performance, metal seated, triple oset type butterfly valves designed
especially for district heating and district cooling applications. Vexve’s high quality butterfly valves with to-
tal bi-directional tightness can be used for shut-o (on/o) and control purposes. Vexve provides models
BFS and BRS for shut-o and models BFC and BRC for control purposes.
Vexve’s butterfly valve can be used within the following temperature-pressure range. Please note that the
maximum allowable working pressure is dependent on the operating temperature.
Chart 1. Pressure-temperature chart.
Note!
DN 1200–1600 temperature
range -20…+200 °C
The maximum allowable work-
ing pressure is dependent on
the operating temperature
NOTE:
When intending to use the valve for other media or applications please consult Vexve to
ensure its suitability.
The Parts list for Vexve’s butterfly valves is presented in Appendix 7.1. and 7.2.
For detailed technical information including dimensions and weights, torques, Kv-values etc please refer
to Vexve’s Product catalogue or data sheets (www.vexve.com) for the valve in question.

4 5
www.vexve.com www.vexve.com
BRS1000W
0101001 2015
25 200
-40
25
1 2 3 4 567 8
9 10 11 12 13 14
2. Valve identification
The type code for Vexve’s butterly valves is presented in Appendix 7.3.
The valve-specific serial number can be found on the identification plate
on the side of the actuator connection (see Figure 1).
Figure 1. Identification plate.
The markings on the identification plate are as follows:
1. Valve manufacturer
2. Valve product number, which is individual
valve number
3. Valve type:
B = butterfly valve
4. Product group:
F = full bore
R = reduced bore
5. Valve use
S = shut-o valve
C = control valve
6. Valve size (DN)
7. Connection to the pipeline:
W = welding ends
F = flanged ends
8. Manufacturing year
9. Eurasian Conformity Valve Certification
10. CE marking and ID of the notified body
11. Pressure class
12. Maximum pressure dierence when
the valve is closed
13. Minimum operating temperature
14. Maximum operating temperature

6 7
www.vexve.com
3. Unloading and storage
Check that the contents of the delivery is as
ordered. Check that the valve and related equip-
ment have not been damaged during transpor-
tation.
Store the valve carefully before installation, pref-
erably in a well-ventilated, dry space,
on a shelf or a wooden grid to protect it from
rising damp (see figure 5).
Protect bare metal surfaces, shaft parts,
and flange surfaces with anti-corrosive agent
before storage.
The valve must be transported to the installation
site in a sturdy package. Do not remove the flow
port protectors before installation. Protect the
valve from sand, dust, and other impurities.
The valve must always be lifted by its lifting lugs
and upper neck (see Figures 3 and 4). The valve
or valve assembly must not be lifted from the
actuator (see Figure 2). Even light knocks may
damage the actuator or aect the actuator and
valve adjustments.
NOTE:
Take the weight of the valve into
account when handling it.
When delivered, the valve will be in the closed
position. During storage, the valve must be
lightly closed.
Maximum recommended storage time is two
years. If the valve is stored for more than two
years, it should be operated and cleaned yearly.
Packaging:
Vexve’s products are protected during transpor-
tation with special packaging. The packaging
consists of environmentally friendly materials that
are easy to sort and recycle.
Recycling the packaging materials at designated
waste collection points is recommended.
The following packaging materials are used:
wood, cardboard, paper, and polyethylene
sheets.
Recycling and disposal
Nearly all parts of the valve are made of recy-
clable material. The material type is marked on
most parts. The valve is delivered with a material
list, and separate recycling and disposal instruc-
tions are available from the manufacturer. The
valve can also be returned to the manufacturer
for recycling and disposal against a fee.
Figure 2. Do not lift the valve by the actuator.

6 7
www.vexve.com www.vexve.com
Figure 4. Lifting a valve equipped with 4 lifting lugs.
Figure 3. Lifting a valve equipped with 2 lifting lugs.
Figure 5. Storage.

8 9
www.vexve.com
WARNING:
Incorrect installation may result in serious personal injury and it may damage or cause
malfunction of the equipment. These instructions must therefore be followed carefully
when installing the valve.
These general instructions do not cover all possible operating scenarios. For more
specific guidance on the use of the valve or its suitability for an intended use, please
contact the manufacturer.
· Do not remove the flow port protectors before installation. Keep the valve protected from sand,
dust and other impurities.
· If the valve was delivered with the actuator installed, avoid removing the actuator during installation.
· Incorrect re-installation or adjustment of the actuator will result in a high risk of damage and leakage.
· Exercise extreme caution when testing the valve before installation in the pipeline.
· The valve or valve assembly must not be lifted by the actuator. If the valve is equipped with lifting lugs,
use the lugs (see Figures 3 and 4). Dropping or incorrect lifting of the valve can result in personal injury
or equipment damage.
· Use one of the allowed lifting methods shown in Figures 3 and 4.
4. Valve installation
Figure 6. Do not remove the actuator. Figure 7. Do not change factory settings.

8 9
www.vexve.com www.vexve.com
Prior to installation:
· Remove the flow port protectors
· Clean the pipes and the valve, see Figure 8
· Close the valve fully before welding or installing it in the pipeline.
The valve must remain closed for the entire installation procedure!
WARNING:
Pipeline and valve shall be carefully cleaned prior to installation as any welding debris or
other impurities can damage the valve.
Valve installation:
· Check the instructions for the correct location of valve in the pipeline, see chapter 4.1
· Install the valve in an allowed position, see chapter 4.2
· See chapter 4.5 for installation instructions of valve with welding ends
· See chapter 4.6 for installation instructions of valve with flanges
NOTE:
The valve must be used only in applications for which it is intended.
Figure 8. Clean the pipes and the valve before installation.

10 11
www.vexve.com
5D
3D
3D
1
2
2
3
4.1 Valve location in the pipeline
Valve should be installed as far as possible from
the components causing turbulence, such as
pumps, pipe bends and pipe connections.
Minimum installation distances shown in figure 9
should be followed.
1Pipe bend axis
2Stem axis
3Pump shaft axis
Figure 9. Minimum distances, D = pipeline diameter
Figure 10. Valve location
NOTE:
Valve should not be installed
in such sections in the pipeline
where impurities can easily be
piled. For example lowest sections
of the pipeline should be avoided
(see figure 10).

10 11
www.vexve.com www.vexve.com
Y
1 2 3
X
4.2 Installation positions of the valve
Valve can be installed in a vertical (see figure 11, section 1), horizontal (2) or diagonal (3) pipeline.
NOTE:
See chapter “4.2.1 Installation in a horizontal pipeline” for more specific instructions for
installation in a horizontal (2) or diagonal (3) pipeline.
After a pipe bend valve should be installed so that the stem axis is perpendicular to the pipe bend axis,
see figure 9.
Especially a control butterfly valve should be installed after a centrifugal pump so that stem axis is at 90°
angle in relation to the pump shaft axis, see figure 9. However, if two valves are installed one after the
other, the stems must be perpendicular to each other.
When installed this way, the loading on the valves is more even and vibration that may otherwise be
present will not be generated.
Figure 11. Possible installation positions of the valve.

12 13
www.vexve.com
Figure 12. Installation in a horzontal position. Figure 13. Installation at an angle.
Figure 14. Not recommended positions.
4.2.1 Installation in a horizontal pipeline
The most recommendable installation position is in a horizontal pipeline with the valve stem horizontal
(see Figure 12). The valve can alternately be installed at an angle of max 45°(see Figure 13).

12 13
www.vexve.com www.vexve.com
Figure 15. Pipeline supports.
4.3 Pipeline supports and pipeline reducers
Pipeline supports should not be installed under the valve!
If pipeline reducers are used in connection with the valve, additional pipeline supports must be used
because of the higher mechanical load on the valve (see figure 15).

14 15
www.vexve.com
min 450 mm
NOTE:
Do not use the valve at the end of the pipeline – a blank flange must always be installed
after the valve (see Figures 16 and 17.).
When the valve is installed at the end of the pipeline, there is a risk of corrosion-causing oxygen-rich
water or air collecting in the empty rear side of the valve. To prevent corrosion, the space after the valve
must be filled with oxygen-free water.
NOTE:
If the valve is located near to the blind flange at the end of the pipeline, valve must not be
fully closed. Instead the valve must remain slightly open to prevent a closed space from
forming between the valve and blind flange. If water in the closed space expands
(for example due to temperature), it may damage the valve.
Figure 17. Blank flange.
Min. 450 mm pipe must be installed between
the valve and the blank flange.
Figure 16. Do not use the valve at the end
of the pipeline.
4.4 Installation at end of pipeline

14 15
www.vexve.com www.vexve.com
1
3
2
4
1
3
2
4max 45º
NOTE:
Electric welding must be used to
weld the valve in place.
· Recommended welding method is manual
metal arc welding. Recommended welding
rod is ESAB OK 48.00 or equal (standard: EN
ISO 2560-A; classification: E 42 4 B 42 H5).
· Valve may be welded only by an authorized
mechanic, following valid norms and
standards.
· The valve must remain closed during
installation and welding to ensure that welding
residue does not damage the seal surfaces.
· The ends of the pipes must be parallel to the
valve and correctly aligned.
· The length of the valve must be the same as
the distance between the pipe ends, taking
into consideration the welding gaps.
· Diameter and wall thickness of the pipes must
be compatible with the welding ends of the
valve
· It is recommended to install the valve so
that the main flow direction is same as the
recommended flow direction for the valve.
· The recommended installation position for the
valve is at an angle (see Figure 19.) or with the
shafts in the horizontal position
(see Figure 18.). Avoid installation with the
shafts fully upright.
NOTE:
The greatest angle between stem
axis and horizontal axis is 45
degrees (see Figure 19.).
· The valve must first be bridged to the
pipeline using spot welding, with 4–8 seams
alternately on opposite sides of the valve.
· Then the seams between the bridges are
welded as shown in Figures 18. and 19.
Welding order: 1-2-3-4.
· Any lid welding must be carried out at a
minimum of 200 mm from the valve seam.
· During welding the ground must be
connected to the pipe of the valve body or the
pipeline. Ground cable should be connected
to the pipe on the same side as the welding
seam. Otherwise the current may damage the
valve seal. Never connect the ground to the
valve neck, actuator flange or actuator.
Figure 18. Welding the seams. Figure 19. Welding the seams.
4.5 Welding procedures

16 17
www.vexve.com
Ls ≥ L Ls ≥ L
L mm
Figure 20. Cover the seal and disc with a water
cushion of minimum 40 mm.
If the valve is welded to a vertical pipeline,
close the valve and cover the seal and disc
with a water cushion of at least 40 mm
(see Figure 20.).
The water protects from welding spatters that
may damage the seal and disc surfaces during
welding.
· The recommended method of welding
the valve to the pipeline is welding with
connection pipes (see Figure 21.). Tack
welding and the welding order for the seams
are the same as in Figures 18. and 19.
Welding order: 1-2-3-4.
· The valve must remain closed during
installation and welding to ensure that welding
residue does not damage the seal surfaces.
· This also facilitates cleaning of the inner
surfaces from welding residue and impurities.
Figure 21. The recommended method.
4.5.2 Welding with connection pipes (recommended method)
4.5.1 Installation in a vertical pipeline

16 17
www.vexve.com www.vexve.com
· The gasket used on installation must be
selected to match operating conditions,
temperature, pressure and medium. Gasket
dimensions must be compatible with sealing
faces of the flanges. For detailed information
please refer to the standard EN1514.
· It is recommended to install the valve so
that the main flow direction is same as the
recommended flow direction for the valve.
· The recommended installation position for the
valve is at an angle (see Figure 13.) or with the
shafts in the horizontal position
(see Figures 12 and 22). Avoid installation with
the shafts fully upright.
· Valve may be installed only by an authorized
mechanic, following valid norms and
standards.
· The valve must remain closed during
installation to ensure that any residue or dirt
does not damage the sealing faces.
· The sealing faces of the pipe flanges must be
parallel to the valve sealing faces and correctly
aligned.
· The length of the valve must be the same as
the distance between the flanges in the pipe
line, taking into consideration the gasket.
· The flanges in the pipeline must be
compatible with valve flanges. For detailed
information please refer to the standard
EN1092-1.
· The bolts and nuts used on installation must
be selected to match operating conditions
on installation location. Bolts and nuts must
also fulfill requirements of the pressure,
temperature, flange material and gasket.
For detailed information please refer to the
standards EN 1515-1, EN1515-2 and
1515-4.
Figure 22. The recommended method.
4.6 Installation of valve with flanged connections

18 19
www.vexve.com
NOTE:
·It is recommended to fill the pipeline via by-pass valves.
·The pipeline must be flushed carefully, see chapter 4.8 for instructions
Figure 23. By-pass valve.
Figure 24. Pipeline needs to be flushed after
valve installation
It is recommended to fill the pipeline via by-pass valves in order to avoid pressure shocks and to reduce
forces caused by opening the butterfly valve under pressure (see Figure 23.).
To avoid pressure shocks and to reduce the
forces caused by opening the valve under pres-
sure, a by-pass valve must be used in
connection with butterfly valves
(see Figure 23.).
4.7 Before commissioning
4.8 Flushing
Pipeline needs to be flushed carefully after the
valve installation.
Before starting the flushing, turn the valve disc
so that the opening angle is 30–40°.
Close the valve gradually during the flushing until
the opening angle is approximately 5-10°.
Decreasing the opening angle increases the
velocity of the flow through the valve. This
produces ecient removing of impurities from
sealing surfaces of the valve.

18 19
www.vexve.com www.vexve.com
21 3
During commissioning the opening angle of the valve should be at least 15 degrees. This is to reduce the
eect of any pressure shocks on the valve.
Figure 25. If the opening angle is small, it is
recommended to perform flushing before
closing the valve
4.9 Commissioning
Exceeding the permitted values marked on the
valve may damage the valve and, in the worst
case, cause uncontrolled venting of the pres-
sure. This leads to equipment damage and
possibly also to personal injuries.
· The greatest permitted test pressure against
a closed valve is 1.1 x PN (PN = valve’s
max. trim ΔP). When carrying out a pipeline
pressure test (1.5 x PN), the valve must be
fully open. The tightness of the valve can be
ensured after this.
· If the stem is equipped with graphite packing
(BFC/BRC models), the tightness of the
packing should be checked. If required,
the graphite packings are tightened with the
hexagonal nuts until they no longer leak.
Do not over-tighten the packings as this
increases the valve torque.
4.10 Pressure test
NOTE:
It is recommended to perform the
flushing also before closing the
valve after it has been used for
control purposes so that the
opening angle has been small
(10° or less), see Figure 25.

20 21
www.vexve.com
NOTE:
Avoid removing the actuator from the valve. The actuator has been calibrated at the
factory to ensure that the valve is tight. If the actuator is removed, the actuator may have
to be re-calibrated.
Vexve Oy accepts responsibility only for actuators installed by Vexve.
Refer to the separate adjustment instructions, available from the manufacturer.
WARNING:
Due to dynamic torque, the actuator must not be disconnected from the valve in
a pressurised pipeline.
Incorrect disconnection may cause serious personal injuries as well as malfunction and
damage to the equipment. Extreme caution must be exercised during disconnection.
Do not turn the disc more than 90° as this may damage the seal. Due to the valve
structure, the disc can only be turned within its original range of 0–90 degrees.
5.1 Removing the actuator
· Keep the valve and the pipeline non-pressurised whenever the gearing is not connected.
· In a butterfly valve, the gear functions as a limiter for the open and close positions. The valve itself is
not equipped with limiters. The manual gears used with butterfly valves are self-locking manual gears.
· Close the valve fully with the handwheel when the manual actuator is being disconnected.
(The valve is closed by turning the actuator handwheel clockwise.)
· Turn the actuator handwheel slightly anti-clockwise to reduce the force of the actuator and the valve.
Now the handwheel will turn easily.
· Remove the actuator bolts and pull the actuator out. Use an extractor, if required.
5. Actuator disassembly and installation
This manual suits for next models
23
Table of contents
Other Vexve Control Unit manuals
Popular Control Unit manuals by other brands
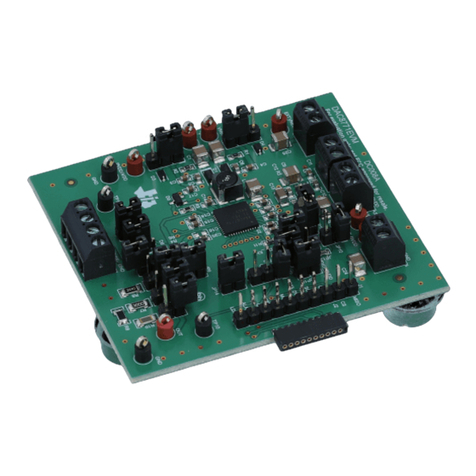
Texas Instruments
Texas Instruments DAC8771EVM user guide
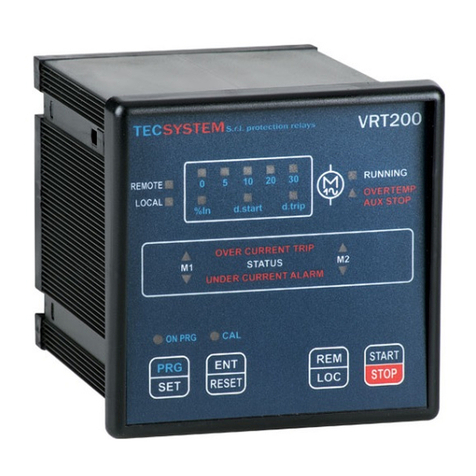
TECSYSTEM
TECSYSTEM VRT200 instruction manual
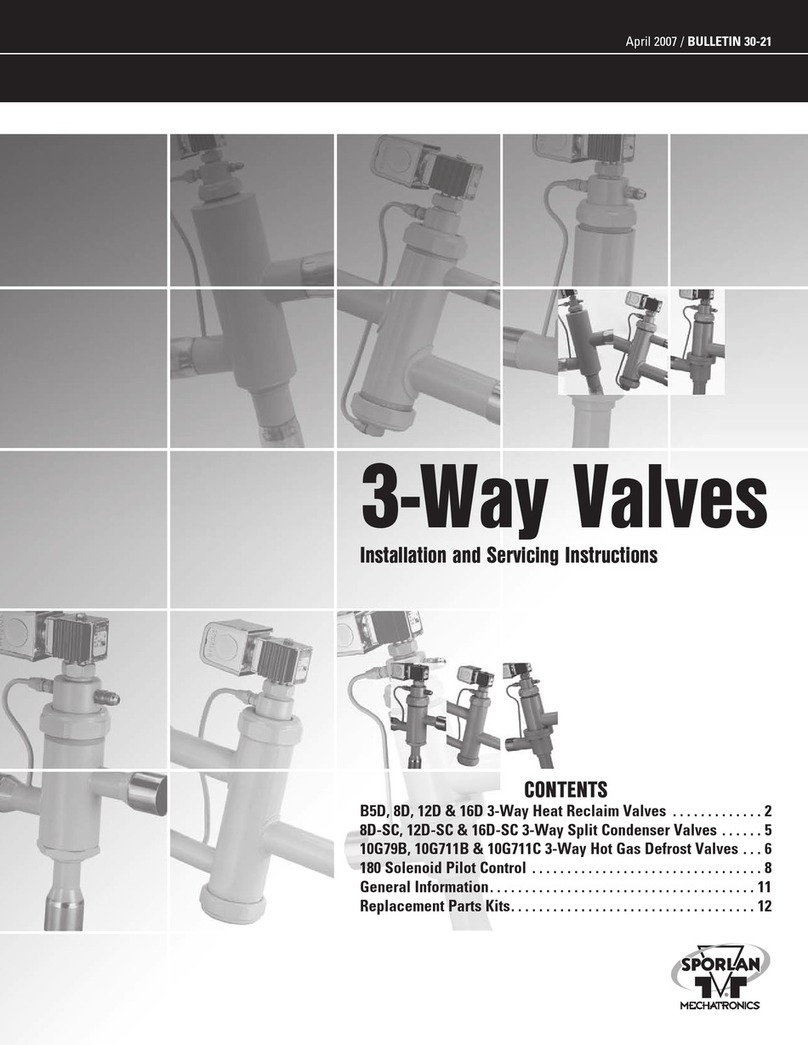
Sporlan
Sporlan B5D Installation and servicing instructions
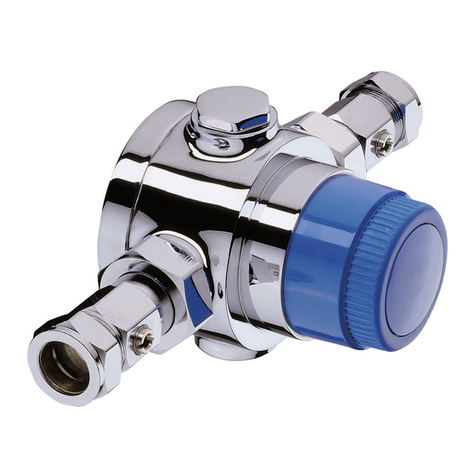
Bristan
Bristan TS4753ECP Installation instructions and user guide
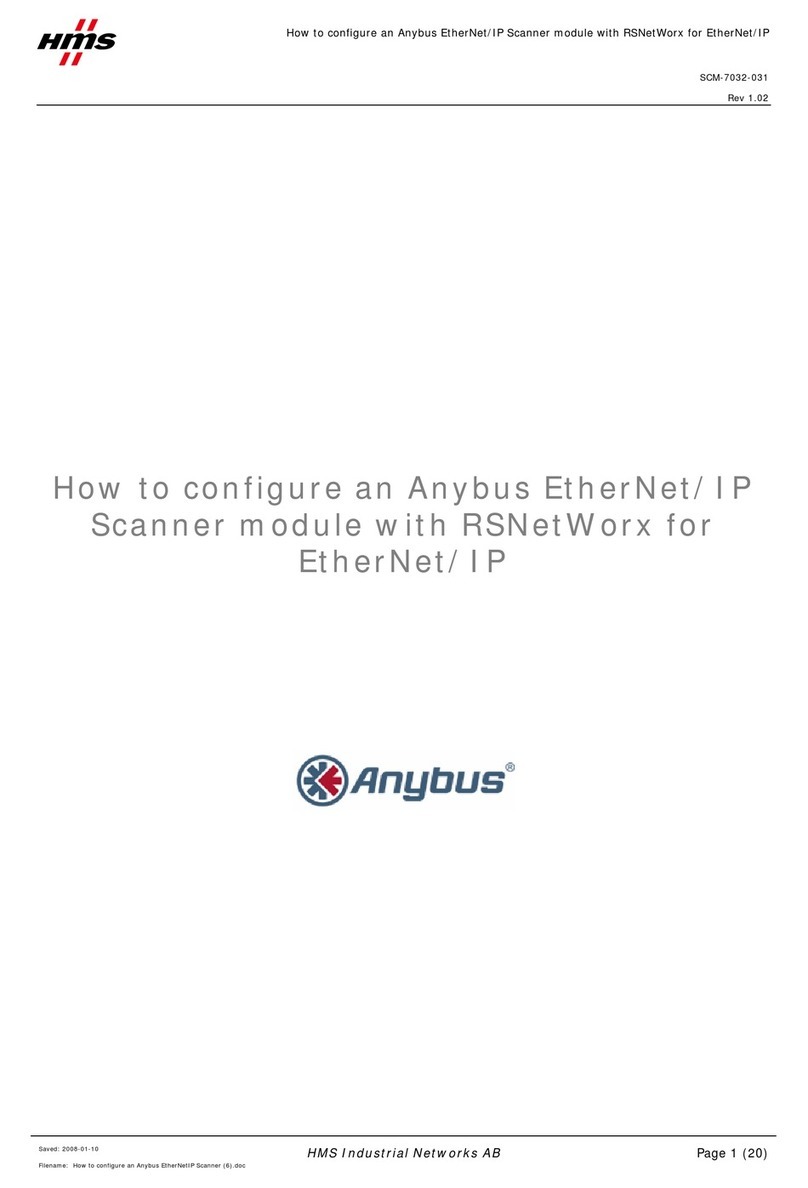
HMS
HMS Anybus manual
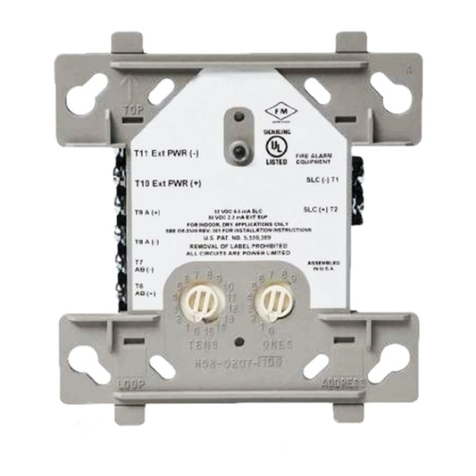
Honeywell
Honeywell Notifier FCM-1 Installation and maintenance instructions