Econ DH860 User manual

Shenzhen ECON Technology Co.,Ltd
2
Contents
Introduction.................................................................................................................................3
Overview.................................................................................................................................3
Features...................................................................................................................................3
Applications............................................................................................................................3
Mounting the Drive....................................................................................................................4
Connecting the Power Supply....................................................................................................5
Transformer Selection...............................................................................................................5
Voltage..................................................................................................................................5
Current..................................................................................................................................6
Connecting the Motor...............................................................................................................6
Four Lead Motor .................................................................................................................6
Eight Lead Motor..................................................................................................................6
Connecting Input Signals.........................................................................................................7
Connector Pin Diagram.......................................................................................................7
Connection Examples: STEP & DIR..................................................................................7
Internal Circuit Diagram.....................................................................................................7
Connection Examples: EN..................................................................................................8
Configuring the Drive..............................................................................................................9
Step 1: Selecting a Motor....................................................................................................9
DH542 Motor Table..........................................................................................................9
Step 2: Setting the Current..................................................................................................10
Step 3: Setting Idle Current.................................................................................................10
Step 4: Step Size..................................................................................................................10
Reference Materials.................................................................................................................11
Drive Interface Description ................................................................................................11
Motor Outlines....................................................................................................................12
Torque-Speed Curves.........................................................................................................13

Shenzhen ECON Technology Co.,Ltd
3
DH860--Ultra low noise , high stability and smoothness digital stepper drive
Introduction
Overview
DH860 is the new generation high performance fully digital stepper drive which base on 32bit DSP with a advanced
algorithm .the power supply range is AC24~80V. it can drive frame 57---110mm 2 phase stepper motor .
Ultra low noise and high smoothness at middle/low speed ,and high torque at high speed, which can be applied to different
speed control applications. adopt smooth and accurate sinusoidal current vector control technology ,which make motor low
heat .
Features
New generation 32bit DSP
Good smoothness ,low noise ,low heat
Build-in micro step setting
Build-in current setting
The standstill current can be set to 50%
Opt-isolated differential pulse input
The response frequency is up to 300KHz
Over voltage , under voltage, over current protection
Operates from a 24 to 80 volt AC power supply
Running current up to 7.2 amps per phase
Applications
It can be used in various kinds of machines ,such as dispenser machine. floating machine
3D printer, labeling machine, medical machine, laser cut machine, and so on ,its unique features make it an ideal solution
for the applications which require low noise ,low vibration, low heat and high precision

Shenzhen ECON Technology Co.,Ltd
4
Mounting dimension(unit:mm)
You can mount the drive on the wide or the narrow side of the chassis using #2 screws.If possible,the drive should be
securely fastened to a smooth,flat metal surface that will help conduct heat away from the chassis. If this is not possible,then
force airflow from a fan may be required to prevent the drive from overheating. See below installation image:
Note:
•Never use the drive in a space where there is no air flow or where other devices cause the surrounding air to be more
than 50
℃
.
•Never use the drive in a space where the temperature is under -10
℃
•Never put the drive where it can get wet or where metal or other electrically conductive particles can get on the
circuitry.
•Always provide air flow around the drive.When mounting multiple drives near each other,maintain at least one half
inch of space between drives.

Shenzhen ECON Technology Co.,Ltd
5
Connecting the Power Supply
If you need information about choosing a power supply, please read the section Choosing a Power Supply
•Connect the power supply “+” terminal to the connector terminal labeled “AC1 or AC2”
•Connect power supply “-” to the connector terminal labeled “AC1 or AC2”
•The screw in the center of drive chassis should be connected to earth ground
•Use 18 or 20 gauge wire
Power Supply and Ground Connection
Transformer Selection
When choosing a transformer, there are many things to consider.You must decide what size of (in terms of voltage
and current) is needed for your application.
ECON Technology recommend HB500-60 transformer for drive:DH860
Voltage
Your motor can provide more torque at higher speeds if a higher power supply voltage is used. Please consult the
speed-torque curves later in this manual for guidance.
If you choose an unregulated power supply, make sure the no load voltage of the supply does not exceed the drive’s
maximum input voltage specification.
Current
The maximum supply current you could ever need is two times the motor current. However, you will generally need a
lot less than that, depending on the motor type, voltage, speed and load conditions. The more the power supply voltage
exceeds the motor voltage, the less current you’ll need from the power supply. A motor running from a 48 volt supply

Shenzhen ECON Technology Co.,Ltd
6
can be expected to draw only half the supply current that it would with a 24 volt supply.
We recommend the following selection procedure:
1. If you plan to use only a few drives, get a power supply with at least twice “per phase” current rating of the step
motor. Example: for a motor that’s rated for 2 A/phase use a 4 A power supply..
2. If you are designing for mass production and must minimize cost, get one power supply with more than twice the
rated current of the motor. Install the motor in the application and monitor the current coming out of the power supply
and into the drive at various motor loads. This will tell you how much current you really need so you can design in a
lower cost power supply.
Motor Connecting
Never connect or disconnect the motor while the power is on.
Four Lead Motor
These motors can only be connected one way. Please follow the sketch below.
Eight Lead Motor
8 Leads Parallel Connected

Shenzhen ECON Technology Co.,Ltd
7
Connecting Input Signals
Remark:24V power need to series a 1.2k resistance
Connector Pin Diagram Internal Circuit Diagram
Connection Examples:STEP&DIR

Shenzhen ECON Technology Co.,Ltd
8
Connection Examples:EN
Connecting an input to a switch or relay
Connecting another drive to EN
Most PLC use NPN Proximity Sensor

Shenzhen ECON Technology Co.,Ltd
9
Configuring the Drive
Step 1: Selecting a Motor
The DH542 drive is optimized for use with carefully selected motors. To select a motor, simply move the rotary
switch to the letter or number that corresponds to the motor of your choice. You can do this while power is on, but it is
safer to select the motor before applying power to the drive so that you do not risk applying too much current to your
motor.
If your motor is not on the list, please set the switch to a selection whose rotor inertia, holding torque and current are
within 10% of your motor. Custom configurations can be added for qualifying applications.
DH860 Motor Table
Item
Motor
Wiring
Current
Holding Torque
Rotor Inertia
A
oz-in
g.cm²
1
QL86HB65-04A
8 leads
4
285.7
1000
2
QL86HB80-04A
8 leads
4
642.85
1400
3
QL86HB118-04A
8 leads
4.2
1157.14
2700
4
QL86HB156-06A
8 leads
4.5
1742.85
4000
5
QL110HB115-06A
4 leads
4.5
1714.28
7200
6
QL110HB150-06A
4 leads
5
2571.42
10900
7
QL110HB165-06A
4 leads
6
3142.85
15000
8
QL110HB201-06A
4 leads
6
4285.7
16200
Step 2: Setting the Current
The maximum current for the motor you have selected is set automatically when you set the rotary switch. But you
may want to reduce the current to save power or lower motor temperature. This is important if the motor is not
mounted to a surface that will help it dissipate heat or if the ambient temperature is expected to be high.
Step motors produce torque in direct proportion to current, but the amount of heat generated is roughly proportional to
the square of the current. If you operate the motor at 90% of rated current, you’ll get 90% of the rated torque. But the
motor will produce approximately 81% as much heat. At 70% current, the torque is reduced to 70% and the heating to
about 50%.
Three of the small switches on the front of the DH860 drive are used to set the percent of rated current that will be
applied to the motor: SW1,SW2 and SW3. Please set them according to the illustration below
Peak current(A)
RMS current (A)
SW1
SW2
SW3
2.40
2.00
ON
ON
ON
3.08
2.57
OFF
ON
ON
3.77
3.14
ON
OFF
ON

Shenzhen ECON Technology Co.,Ltd
10
4.45
3.71
OFF
OFF
ON
5.14
4.28
ON
ON
OFF
5.83
4.86
OFF
ON
OFF
6.52
5.43
ON
OFF
OFF
7.20
6.00
OFF
OFF
OFF
Step 3:Setting Idle Current
Motor heating and power consumption can also be reduced by lowering the motor current when it is not moving. One
small switch on the front of drive can set the idle current,SW4 is ON,then the current is 100%,when SW4 is OFF,the
current is 50%. The 50% idle current setting will lower the holding torque to 50%, which is enough to prevent the load
from moving in most applications. This reduces motor heating by 75%. In some applications, such as those supporting
a vertical load, it is necessary to provide a high holding torque. In such cases, the idle current can be set to 90% as
shown below.
SW4:OFF=Half Current
ON=Full Current
Step 4:Micro step setting
Pul/rev
SW5
SW6
SW7
SW8
200
ON
ON
ON
ON
400
OFF
ON
ON
ON
800
ON
OFF
ON
ON
1600
OFF
OFF
ON
ON
3200
ON
ON
OFF
ON
6400
OFF
ON
OFF
ON
12800
ON
OFF
OFF
ON
25600
OFF
OFF
OFF
ON
1000
ON
ON
ON
OFF
2000
OFF
ON
ON
OFF
4000
ON
OFF
ON
OFF
5000
OFF
OFF
ON
OFF
8000
ON
ON
OFF
OFF
10000
OFF
ON
OFF
OFF
20000
ON
OFF
OFF
OFF
25000
OFF
OFF
OFF
OFF

Shenzhen ECON Technology Co.,Ltd
11
Reference Materials
Drive Interface Description
Name
Function
Description
PWR
Power light
When power on ,the green light is on
ALARM
Over current/under voltage/over
voltage displaying light
If the drive Over current/under voltage/over voltage, the red light is on
PU+
Pulse input positive
Pulse signal: In single pulse (pulse/direction) mode, this input represents
pulse signal, each falling edge active; 4-5V for High -level, 0-0.5V for
low-level
Series connect resistors for current-limiting when +12V or +24V
used.(should connect 1k resistor for +12V,2k for +24V)
PU-
Pulse input negative
Pulse signal: In single pulse (pulse/direction) mode, this input represents
pulse signal, each falling edge active; 4-5V for High -level, 0-0.5V for
low-level
DR+
Direction input positive
DIR signal: In single-pulse mode, this signal has low/high voltage levels,
representing two directions of motor rotation;
Series connect resistors for current-limiting when +12V or +24V
used.(should connect 1k resistor for +12V,2k for +24V)
DR-
Direction input negative
DIR signal: In single-pulse mode, this signal has low/high voltage levels,
representing two directions of motor rotation;
MF+
Enable input positive
Enable signal: This signal is used for enabling/disabling driver. High
level for enabling the driver and low level for disabling the driver.
Usually left UNCONNECTED (ENABLED).
Series connect resistors for current-limiting when +12V or +24V
used.(should connect 1k resistor for +12V,2k for +24V)
MF-
Enable input negative
Enable signal: This signal is used for enabling/disabling driver. High
level for enabling the driver and low level for disabling the driver.
Usually left UNCONNECTED (ENABLED).
AC1
AC Power input
AC24-80V
AC2
AC Power input
A+,A-
Motor A phase
Connect to Motor A phase
B+,B-
Motor B phase
Connect to Motor B phase
Note!
1: Connect power supply rightly ,can’t exceed 80VAC
2: If the control signal (PU, DR,MF ) is over 5V ,please connect resistors (at the PU+, DR+, MF+ terminals) for
current-limiting.
3:if the alarm light is on ,please check it after power off
A :Check the power supply range is lower than 20VAC or higher than 80VAC
B:Connect power supply after eliminate motor wiring and other circuit short problems

Shenzhen ECON Technology Co.,Ltd
12
Motor Drawing
Motor Length(L)
QL86HB65-04A 65±1mm
QL86HB80-04A 80±1mm
QL86HB118-04A 118±1mm
QL86HB156-06A 156±1mm
QL86 Outline Drawing
Motor Length(L)
QL110HB115-06A 115±1mm
QL110HB150-06A 150±1mm
QL110HB165-06A 165±1mm
QL110HB201-06A 201±1mm
QL110 Outline Drawing

Shenzhen ECON Technology Co.,Ltd
13
Torque-Speed Curve
QL86 with DH860
Connection:8 leads
48VDC Power supply
QL110 with DH860
Connection:4 leads
80VDC Power supply
Table of contents
Other Econ Control Unit manuals
Popular Control Unit manuals by other brands
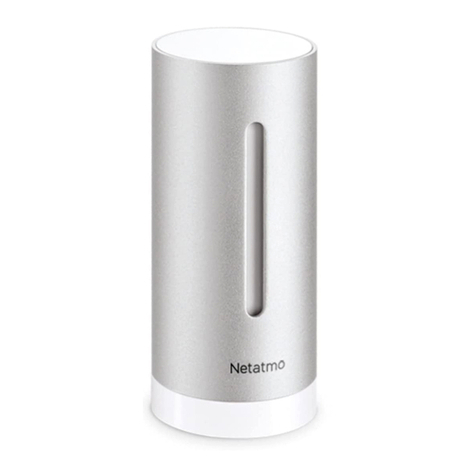
Netatmo
Netatmo Additional Smart Indoor Module manual

Bühler technologies
Bühler technologies Thermotronik T77 Brief instructions
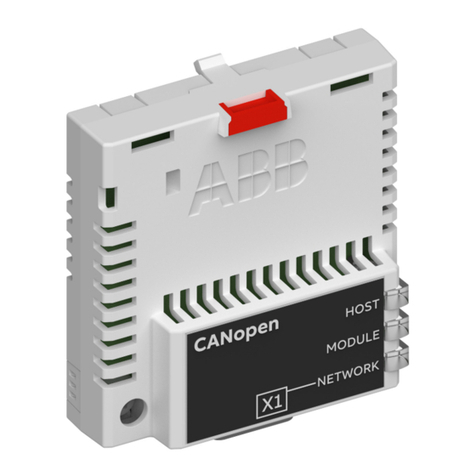
ABB
ABB FCAN-01 Quick installation and start-up guide

Pentair
Pentair AUTOTROL 363 Service manual

SOMFY
SOMFY MATIC Series Installation and operation instructions

Vintage Air
Vintage Air 46115-VUH manual
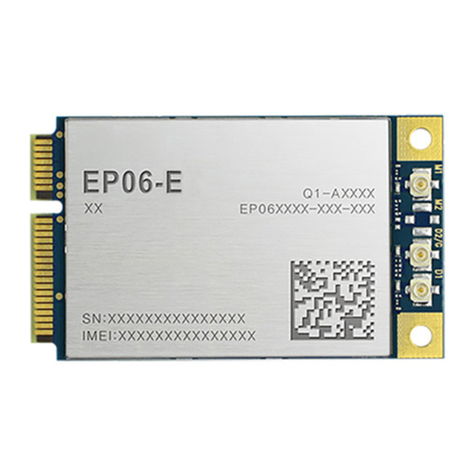
Quectel
Quectel EP06 Hardware design
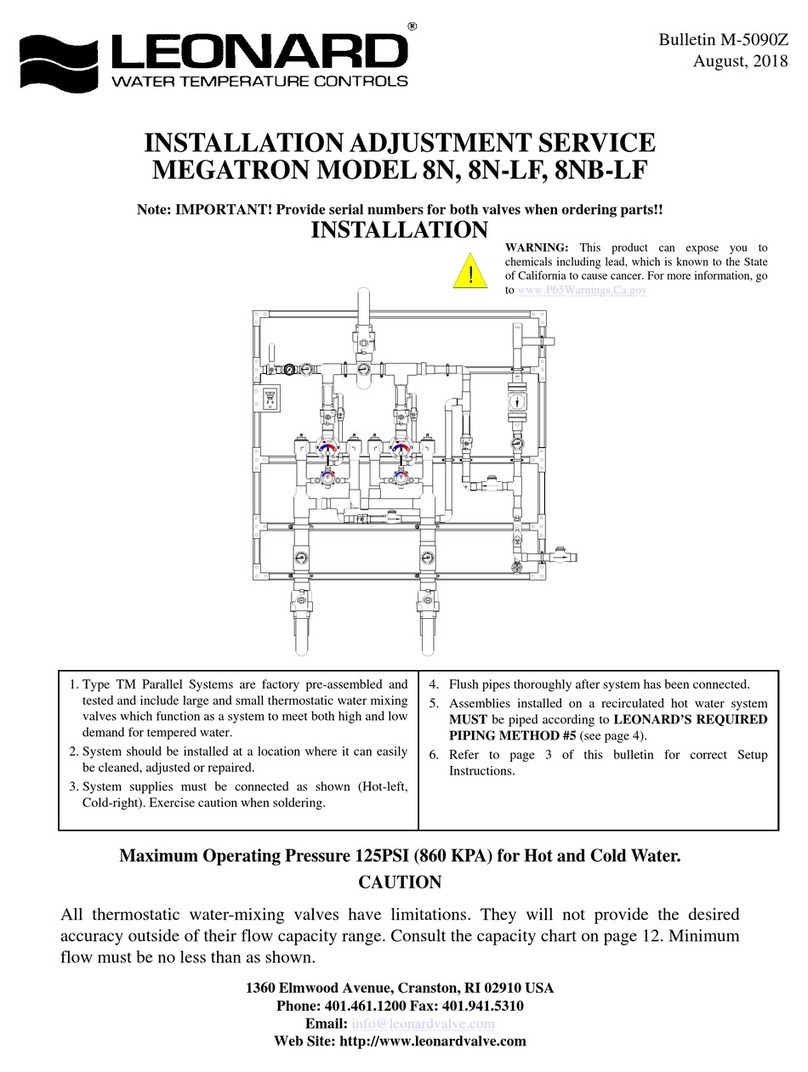
Leonard
Leonard MEGATRON 8N INSTALLATION ADJUSTMENT SERVICE
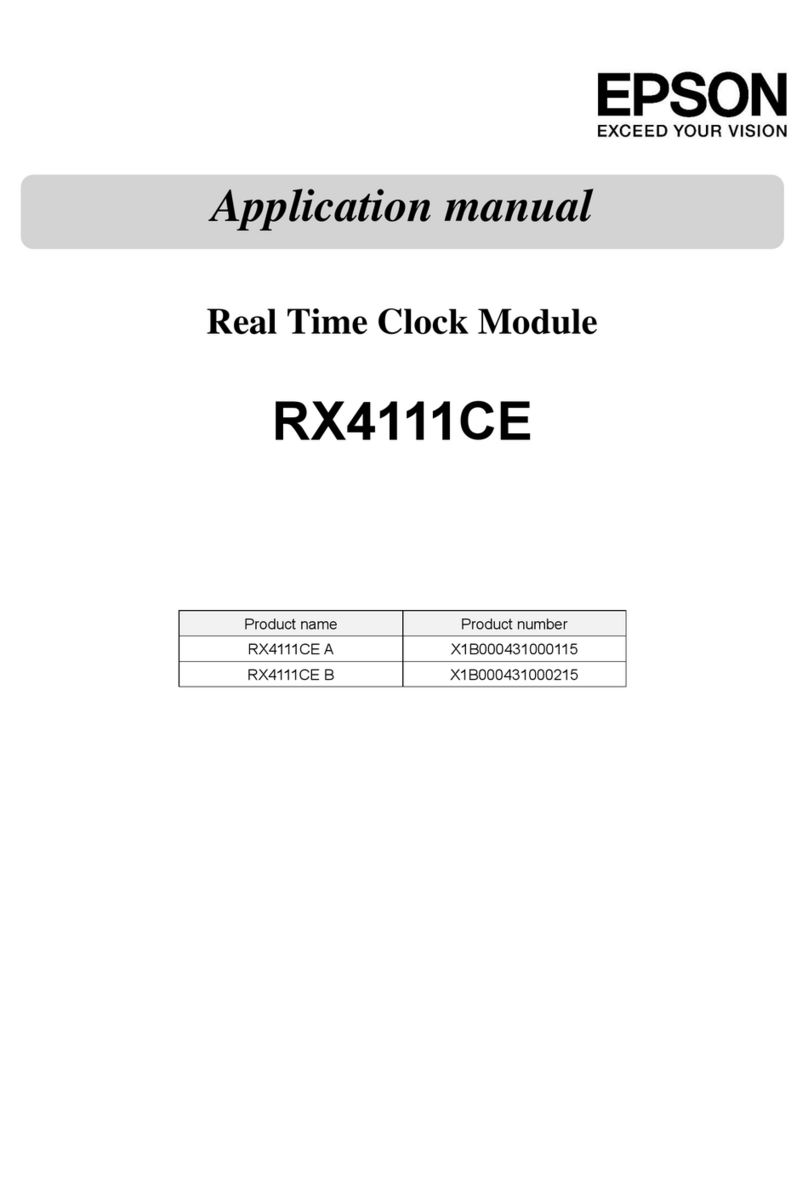
Epson
Epson RX4111CE Applications manual

HORNE
HORNE H-2501 Installation, operating, & maintenance instructions

Lincoln
Lincoln POWER-MASTER III 84981 Owner's/operator's manual

Water Specialist
Water Specialist WS1HR instruction manual