VPInstruments VPFlowScope User manual

VPFlowScope probe
VPINSTRUMENTS.COM
User manual
© 2019 VPInstruments
MAN-VP-SPRO-EN-1901 Date: 04-07-2019

All rights reserved. No parts of this document may be reproduced in any form or by any means - graphic,
electronic, or mechanical, including photocopying, recording, taping, or information storage and retrieval
systems - without the written permission of the publisher.
Products that are referred to in this document may be either trademarks and/or registered trademarks of the
respective owners. The publisher and the author make no claim to these trademarks.
While every precaution has been taken in the preparation of this document, the publisher and the author
assume no responsibility for errors or omissions, or for damages resulting from the use of information
contained in this document or from the use of programs and source code that may accompany it. In no event
shall the publisher and the author be liable for any loss of profit or any other commercial damage caused or
alleged to have been caused directly or indirectly by this document.
Creation date: 04-07-2019 in Delft
VPFlowScope probe
© 2019 VPInstruments
Publisher
Van Putten Instruments BV
Buitenwatersloot 335
2614 GS Delft
The Netherlands

3
Table of Contents
1Warning - Read this first 5
2Introduction 6
3Product overview 7
................................................................................................................................... 7
1 Configuration
................................................................................................................................... 8
2 VPFlowScope probe with connector cap
................................................................................................................................... 8
3 VPFlowScope probe with display
................................................................................................................................... 8
4 VPFlowScope probe with the VPFlowTerminal
4Quick start 9
5Measurement 10
................................................................................................................................... 10
1 Flow
................................................................................................................................... 10
2 Pressure
................................................................................................................................... 10
3 Temperature
................................................................................................................................... 11
4 Totalizer
6Mechanical installation 12
................................................................................................................................... 18
1 Piping table
................................................................................................................................... 19
2 Flow range table
7Display 20
................................................................................................................................... 20
1 Display status icons
................................................................................................................................... 20
2 LCD display
................................................................................................................................... 21
3 Data Logger
................................................................................................................................... 21
4 Keypad
................................................................................................................................... 22
5 Menu
8VPStudio software 24
9Electrical connections 25
................................................................................................................................... 25
1 4 .. 20 mA output
................................................................................................................................... 27
2 Pulse output
................................................................................................................................... 28
3 Modbus interface
10 Service 32
................................................................................................................................... 32
1 Software and firmware updates
................................................................................................................................... 32
2 Calibration interval
................................................................................................................................... 32
3 Service subscriptions
11 Specifications 33

© 2019 VPInstruments | MAN-VP-SPRO-EN | Revision: 1901 | Date: 04-07-2019
5
1 Warning - Read this first
Compressed gasses can be dangerous! Please familiarize yourself with
the forces under pressurized conditions. Respect the local guidelines and
regulations for working with pressurized equipment.
Gas flow through pipes follows certain physical laws. These physical
laws have serious consequences for the installation requirements. Familiarize
yourself with the basic physical laws of flow measurement, to make sure that
the product is installed correctly. Always make sure that upstream length,
downstream length, flow, pressure, temperature and humidity conditions are
within specifications.
Precision instruments need maintenance. Check your flow meter
regularly and make sure it remains clean. When polluted, gently clean the
sensor using demineralized water or cleaning alcohol.
Precision instruments need regular re-calibration. To keep your
VPFlowScope probe in best shape, it needs recalibration. We advice annual
recalibration.
Not intended for fiscal metering or billing. Our flow meters are not
certified for fiscal metering. Laws on fiscal metering and billing may vary per
country or state.
Do not overestimate the results. VPInstruments does not take any
responsibility for the correctness of measurement results under field
conditions. The practical measurement uncertainty of a flow meter in the
field may vary, depending on how well it is installed, due to the nature of gas
flow. The piping table provides guidelines on how to optimize the field
accuracy. Our products are not intended to be used as a single means to
determine compressor capacity.
Do not open the device. Our instruments are assembled with high
precision. Opening this device is dangerous and may destroy the
instruments. Warranty is voided when you open the instrument.
Feedback leads to product improvement. Please share your experience
with us, as we are continuously improving our products in our commitment to
quality, reliability and ease of use. Let us know via
sales@vpinstruments.com!

© 2019 VPInstruments | MAN-VP-SPRO-EN | Revision: 1901 | Date: 04-07-2019
6
2 Introduction
Congratulations! You purchased the easiest to use and most complete compressed air
measurement tool in the world. With the VPFlowScope probe, you can monitor and record flow,
pressure, temperature, and total air consumption, simultaneously.
Great products deserve great user manuals. We have done our best to make this user manual as
complete as possible. New users, please read it carefully to familiarize yourself with our products.
Experienced users can check out the Quick start chapter.
Check the packaging box for any inconsistencies. Should there be any shipping damage, notify the
local carrier. At the same time a report should be submitted to Van Putten Instruments BV,
Buitenwatersloot 335, 2614 GS DELFT, The Netherlands.
This manual is dedicated to:
VPS.R150.P400
For latest VPStudio software and overview of latest firmware versions, please visit
www.vpinstruments.com.
Older software features may not be covered by the contents of this user manual. Please contact us
for a service subscription program, which includes software and firmware updates!

© 2019 VPInstruments | MAN-VP-SPRO-EN | Revision: 1901 | Date: 04-07-2019
7
3 Product overview
The VPFlowScope probe measures mass flow, temperature and pressure simultaneously. All these
parameters are key to proper compressed gas measurement and are therefore included in all
models. With the insertion probe you are flexible in pipe diameter. All data can be accessed by
Modbus RTU, 4 .. 20 mA and pulse.
The VPFlowScope probe is available in three configurations to fit every application. Use the
connector cap for sensor features only, ideal for integration into a central management system. Use
the display module for central read out and data logging. Use the VPFlowTerminal for central read out
and data logging on location where a standard display can not be read out. For all models, all
parameters and outputs are available.
The VPFlowScope probe is available in 2 lengths. Additional options are available for both types:
Order Code
Flow range
Option
Length
Option
Display
VPS.R150
150 mn/sec
P300
300 mm length
D0
No display, No connector
cap
P400
400 mm length
D10
Display
P600
600 mm length
D11
Display + 2M point logger
D2
Connector cap
Order the VPFlowScope KIT to receive the complete start kit with all required accessories, everything
you need to get started right away.
3.1 Configuration
The instrument needs only one step to be ready for operation. It needs to know the exact inner pipe
diameter for accurate measurement, wrong inner diameter will lead to very significant errors. The pipe
diameter can be programmed with the keypad on the display module or with the VPStudio
configuration software. This software suite is also used for configuration of the outputs and data
logger. This software can be downloaded from our website. www.vpinstruments.com/downloads.

© 2019 VPInstruments | MAN-VP-SPRO-EN | Revision: 1901 | Date: 04-07-2019
8
3.2 VPFlowScope probe with connector cap
The VPFlowScope probe with connector cap can be used in applications where local read-out and
data logging is not required. With it's various outputs the VPFlowScope probe can be connected to
remote data loggers.
3.3 VPFlowScope probe with display
The display module adds a 3 row display with keypad and an optional 2 Million point data
logger(optional) to the VPFlowScope probe. All parameters will be shown on the display in real time.
The keypad can be used to start a data log session or to change the key parameters of the
VPFlowScope probe. All output parameters for remote connection remain available on the M12
connector.
3.4 VPFlowScope probe with the VPFlowTerminal
The VPFlowTerminal can be used as a remote display for situations where the local display can't be
read. All display features will be available on the remote display.
The VPFlowTerminal is equipped with a 10 m / 32.8 ft. cable and connector cap with a M12 8pin
connector. The standard connector cap with M12 5pin connector can not be used for connection with
the VPFlowTerminal. The VPFlowTerminal features a 2 Million point data logger which can record
both the flow meter and the analog inputs.

© 2019 VPInstruments | MAN-VP-SPRO-EN | Revision: 1901 | Date: 04-07-2019
9
4 Quick start
This chapter contains the basic steps to start using your VPFlowScope probe flow meter. Additional
information on all subjects can be found in the next chapters.
1. Unpack
Unpack the meter and check if all items are there and in good shape. A checklist with all items is
available on the box.
2. Program the settings
·
The inner pipe diameter needs to be programmed into the sensor. This can be done via the display
or with the VPStudio software (www.vpinstruments.com/downloads)
·
If required, set the output parameters for the Modbus, pulse and current output.
3. Mechanical installation
·
Find the best point of installation for this product. Make sure that all specifications are met.
·
For installation of the VPFlowScope probe, an insertion point needs to be created. You can weld a
tap with minimum internal 1/2 inch thread or use a hot tap saddle.
·
Place a ball valve (minimal 1/2 inch full bore) and compression fitting on the insertion point.
·
Connect the safety chain and insert the probe into the pipe.
·
The sensor needs to be in the middle of the pipe.
·
Tighten the compression fitting.
See chapter mechanical installation for more detailed information.
3. Electrical installation
3.1 Permanent installation
Connect a cable with 5 Pin M12 connector to the VPFlowScope probe. Use the power supply
module for permanent installation. The cable can be connected to a central data acquisition /
building management system or data logger via Modbus, 4 .. 20 mA or pulse. See chapter
electrical connections for more information.
Apply 12 .. 24 VDC to power up the device. Use a Class II power supply (less than 2 Amps). If a
display is available, it will light up when power is applied.
3.2 Temporary installation
Use a 12 .. 24 VDC power supply with M12 connector to power the VPFlowScope probe. This
quick method is ideal for audits.
4. Data recording
When the data logger option is available a data log session can be started by pressing the esc/rec
button and then enter. All parameters will be logged with the default logging intervals (5 seconds for
all parameters). These logging intervals can be changed with the VPStudio software. This software
tool is also used to retrieve the recorded sessions.

© 2019 VPInstruments | MAN-VP-SPRO-EN | Revision: 1901 | Date: 04-07-2019
10
5 Measurement
For all parameters the update interval is 1 second. Within this second, multiple samples are taken
and averaged to provide a stable and reliable output.
5.1 Flow
The VPFlowScope probe uses our proprietary insertion type thermal mass flow sensor. There is no
bypass flow, which results in a high robustness and less sensitivity for dirt or particles. The flow
sensor is directly temperature compensated.
The sensor response signal is directly related to
the mass flow rate and can be described by the
following formula:
Vout = k *λ* ρ * v * (Ts-Tg)
Vout = output voltage
k = sensor (geometrical) constant
λ = thermal conductivity of the gas
ρ = density of the gas
v = actual velocity in m / sec
Ts = sensor temperature
Tg = gas temperature
The optional bi-directional sensitivity is shown in
the picture on the right. In bi-directional mode the
negative flow value will show up as a minus sign.
The 4 .. 20 mA value needs to be adapted to suit
the application. See chapter 9.1 for details.
5.2 Pressure
The VPFlowScope probe features a built-in gauge pressure sensor. The sensor range is 0 .. 16 bar |
0 .. 250 psi gauge. The sensor cannot measure vacuum, please contact us if you have a vacuum
application. The sensor membrane can handle media which are compatible with glass, silicon,
stainless steel, Sn/Ni, plating and An/Ag solder.
The sensor signal is sampled with 16 bits. The practical resolution is 0.24 mbar on the 0 .. 16 bar
scale, which is equal to 0.004 psi on the 250 psi scale
5.3 Temperature
The built in temperature sensor measures the compressed air/ gas temperature. The signal is
sampled with 16 bits. The resolution is less than 0.1 °C.
In a vertical pipe, with flow going down, the temperature sensor may heat up at zero flow conditions,
due to the heated flow sensor element. This effect will disappear as soon as there is consumption.
For optimal measurement performance, the VPFlowScope probe needs to be in a stable temperature
environment. When exposed to quick temperature changes or large temperature changes (for
example taking the unit from outdoor to indoor during winter time, or when mounted downstream of a
heat regenerated drier) the temperature compensation may lag behind, which may result in
significant measurement errors.

© 2019 VPInstruments | MAN-VP-SPRO-EN | Revision: 1901 | Date: 04-07-2019
11
5.4 Totalizer
The totalizer keeps track of the total consumed amount of compressed air in normal cubic meters, or
in scf depending on which unit you choose to read out. The refresh interval is 1 second, actual
measurement data will be available on the display and by Modbus. For back up reasons, the totalizer
value is written to it's internal memory with an interval of 15 minutes. A power down might result in
maximum 15 minutes of totalizer data loss.
In bi-directional operation, negative flow is subtracted from the totalizer. The totalizer will count
backwards as the compressed air is delivered back to the supply side. The totalizer can only be
reset to zero. It's not possible to set it to a different value.
The display will show totalizer values up to 999.999,9 and will then become 0,0 independent of the
taken unit. This will not clear the internal totalizer.

© 2019 VPInstruments | MAN-VP-SPRO-EN | Revision: 1901 | Date: 04-07-2019
12
6 Mechanical installation
Put together the VPFlowScope probe
Connect the display or connector cap on the VPFlowScope probe sensor module. Make sure that it
slides completely over the O-ring seal. Position the O-ring in the upper position for the connector
cap. Use the lower position for the display. Apply some O-ring grease if required. Gently fix the
screw on top.
Install the VPFlowScope probe in the pipe
First select the right installation point. The installation point is crucial for the right measurements.
Sources of error can be: installation effects, unknown flow profiles, swirls, pressure and temperature
effects, humidity effects, oscillations in the flow. To ensure the highest possible accuracy of flow
measurement, the installation and piping instructions must be followed carefully. Therefore read this
paragraph carefully.
Take into account:
·
Choose a site which is accessible, which allows ease of wiring and maintenance, and which allows
you to still read and access the display when needed.
·
Meet the specifications of the VPFlowScope probe. When the specifications are not met, for
instance the pressure or temperature level is too high; this will cause inaccurate flow measurement
and can even damage your flow meter.
·
Do not apply mechanical stress to the flow meter.
Avoid:
·
Excessive heat, check the temperature range of your VPFlowScope probe.
·
Potential water damage on the outside. Avoid areas of high humidity and avoid dripping. Be aware
that the VPFlowScope probe is not watertight, it is only splash proof.
·
Corrosive atmosphere where possible.
·
Electrical problems (high voltage/ high power).
·
Mechanical vibration and danger (walking bridges, fork lift trucks).
Stop: These devices are only for use with Air, Nitrogen and other non hazardous and
non combustible gases. The maximum working pressure is 16 bar (250 psi)
Arrêt: Ces dispositifs sont uniquement destinés à être utilisés avec de l'air, de l'azote et
d'autres gaz non dangereux et non combustibles. La pression opérationnelle maximale
est de 16 bar (250 psi)
Prepare the installation
The VPFlowScope probe can be inserted through a welding tap with internal 1/2 inch thread or
through a hot tap saddle. A hot tap saddle can be installed under pressurized conditions, so there is
no need to shut down production.
Use a ball valve to insert and retract the VPFlowScope probe when you want. Use a 1/2 inch full bore
ball valve or a 3/4 inch ball valve. The VPInstruments hot tap drill has a 1” drill size. In that case,
place a 1” ball valve and use, after drilling, a reducer to go back to 1/2” for the compression fitting.
Warning: Make sure that the hole is at least 16 mm | 0.63 inch inner diameter, and
completely clear for insertion. A too small hole will damage the probe or your
measurement value will be very low.

© 2019 VPInstruments | MAN-VP-SPRO-EN | Revision: 1901 | Date: 04-07-2019
13
The installation
Insertion depth
Generally the insertion depth of the VPFlowScope probe is
0.5 times the inner pipe diameter, where the bottom of the
sensor tip must be in the middle of the pipe (see picture).
Position
Install the VPFlowScope probe upwards in an angle of 30
degrees (see picture). Never install the instruments upside
down.
When mated to a display, the VPFlowScope DP is shaped to make alignment with the flow direction
easy. The display should point downstream of the flow. With a connector cap, the M12 connector
points downstream of the flow. Alignment “by the eye” is sufficient.
The flow direction is indicated on the product label.

© 2019 VPInstruments | MAN-VP-SPRO-EN | Revision: 1901 | Date: 04-07-2019
14
Measurement point/ hot tap installation: make it smooth
It is important to create a smooth pipe all the way, before and after the insertion probe. This fact is
often overlooked, resulting in poor measurement results. When welding a stub, and drilling the hole,
make sure it is as small as possible.
Rules of thumb:
·
Keep it smooth
·
Avoid welding rims on the inside
·
Avoid seals (from flanges) to block the flow path
·
Avoid large dead spaces around the probe
Good practice
Bad practice
The pipe is smooth and the hole is relatively
small, leaving a small gap around the sensor tip.
A standard T-piece is used. This causes
turbulence around the sensor. Furthermore, the
diameter changes in the measurement section,
leading to unpredicted behavior of the flow meter
over the measurement range. Especially in small
pipes < 3 inch this is a very unwanted situation.
Exception
Between pipe sizes of 25 mm and 55 mm | 1
inch and 2 inch: be aware that the field
accuracy is +/- 10%; installation errors are
bigger. The insertion depth between 25 mm
and 65 mm | 1 inch and 2.5 inch is also
different. The VPFlowScope probe needs to
installed 5 mm | 0.2 inch from the bottom or
else the temperature sensor of the
VPFlowScope probe itself is outside the flow
path. The sensor tip will not be in the middle
of the pipe any more. The measurement
value is automatically corrected for small
diameters.
SAFETY FIRST: START WITH MOUNTING THE SAFETY LINE!
The VPFlowScope probe is mounted with a 1/2 inch compression fitting. The probe is
sealed with a Teflon ferrule instead of a stainless steel ferrule. Teflon may become
slippery. The safety line will keep the sensor secure when it accidentally moves out of
the compression fitting. NEVER over-tight the fitting, because it might damage the
sensor tube.

© 2019 VPInstruments | MAN-VP-SPRO-EN | Revision: 1901 | Date: 04-07-2019
15
Installation with standard safety line
Step 1.
1. Keep the ball valve closed!
2. Insert the compression fitting in ball valve. Use
Teflon tape or liquid sealant.
Step 2.
1. Insert the VPFlowScope probe until it hits the
ball valve. The probe remains in the compression
fitting.
2. Attach the safety line to the pipe.
3. Hook the safety line to the ring of the
VPFlowScope probe. Make sure that the line is
tight.
Step 3.
1. Keep your hand on top of the VPFlowScope
probe. When you install the VPFlowScope
probe into a pressurized system you are about
to experience temporary leakage and force trying
to push out the VPFlowScope probe from the
compression fitting. When the safety system is
correctly installed this is part of the normal
installation procedure.
2. Open the ball valve slowly and push the
VPFlowScope probe gently downwards.
3. The probe tip should be in the center of the
pipe
4. Tighten the compression fitting
Step 4.
Optionally pull tight the safety line. When
adjusting the safety line, make sure you secure
the VPFlowScope otherwise during adjustment.
This can fox example be done by applying force
by hand on top of the instruments or with a
secondary safety line
1. Unlock the safety line
2. Pull tight the safety line and lock the safety
line again
3. Align the flow direction. Alignment by the eye
is sufficient

© 2019 VPInstruments | MAN-VP-SPRO-EN | Revision: 1901 | Date: 04-07-2019
16
Installation with adjustable safety system
Step 1.
1. Remove the compression fitting's parts on the
long threaded end side
2. Place the safety plate over the compression
fitting long threaded end
Step 2.
1. Mount the nut, and close tight. Then mount
the compression fitting's Teflon rings and nut
Step 3.
1. Keep the ball valve closed!
2. Insert the compression fitting in the ball valve.
Use Teflon tape or liquid sealant.
Step 4.
1. Insert the VPFlowScope probe until it hits the
ball valve. The probe remains in the compression
fitting.
2. Hook the safety line to the ring of the
VPFlowScope probe.

© 2019 VPInstruments | MAN-VP-SPRO-EN | Revision: 1901 | Date: 04-07-2019
17
Step 5.
1. Keep your hand on top of the VPFlowScope
probe
When you install the VPFlowScope probe
into a pressurized system you are about to
experience temporary leakage around the
compression fitting and force trying to push out
the VPFlowScope probe from the compression
fitting. When the safety system is correctly
installed this is part of the normal installation
procedure.
2. Open the ball valve slowly and push the
VPFlowScope probe gently downwards.
3. The probe tip should be in the center of the
pipe
4. Tighten the compression fitting
Step 6.
1. Unscrew the safety lock and pull the safety
line tight
2. Tighten the safety lock
3. Align the flow direction. Alignment by the eye
is sufficient

© 2019 VPInstruments | MAN-VP-SPRO-EN | Revision: 1901 | Date: 04-07-2019
18
6.1 Piping table
Check the piping table below and match it for your application. The table shows the amount of
upstream and downstream length depending on the installation. If applicable in front of the meter, use
given upstream length. If applicable in behind the meter, use given downstream length. Gas flow in
pipes follows certain rules, which must be observed for optimal measurement results. In some cases
the upstream length needs to be longer, in other cases it can be shorter.
If possible choose a longer upstream length, as these are minimum values. The up- and
downstream lengths are used industry wide as guidelines, but will never be a guarantee
for obtaining the “true value”. So always be careful and try to build up your own
experience from practical measurements
Piping table
The following table provides a guideline for proper distances between upstream or downstream
objects and the VPFlowScope probe. The upstream length is the length between the last non-straight
object and the VPFlowScope probe. If the upstream length is straight, and the distortion is
downstream of the VPFlowScope probe, you can use the column "downstream length" as a
guideline. In very complex situations, with multiple up- and downstream objects, you should consider
another location. This table is a practical guideline and is not exact science. Practical situations can
have multiple sources of distortion, therefore VPInstruments does not take any responsibility for the
correctness.
Picture
Description
Upstream
length2
Downstream
length2
Effect
Single elbow
30 * D1
10 * D1
Distorted flow profile
Complex feed-in situation
(header)
40 * D1
10 * D1
Flow profile will be
distorted
Double elbow, multiple
elbows following each
other
40 * D1
10 * D1
Distorted profile +
swirl
Diameter change from
small to large (gradual or
instant)
40 * D1
5 *D1
Jet shaped flow
Diameter change from
large to small (gradual
change, between 7 and
15 degrees)
10 * D1
5 * D1
Flattened flow profile
1 = inner diameter; 2 = minimumlength

© 2019 VPInstruments | MAN-VP-SPRO-EN | Revision: 1901 | Date: 04-07-2019
19
6.2 Flow range table
Schedule 40 standard seamless carbon steel pipe
ID
Flow
Size (inch)
DN
Inch
mm
Min (scfm)
Max (scfm)
Min (m3n/hr)
Max (m3n/hr)
2
50
2.1
52.5
2
688
4
1,169
3
80
3.1
77.9
5
1,516
9
2,576
4
100
4.0
102.3
9
2,610
15
4,435
6
150
6.1
154.1
20
5,924
34
10,065
8
200
8.0
202.7
34
10,259
58
17,429
10
250
10.2
259.1
56
16,756
95
28,468
12
300
11.9
303.2
77
22,953
130
38,995
16
400
15.0
381.0
121
36,237
205
61,565
20
500
18.8
477.8
190
56,996
323
96,832
The ranges apply only to compressed air and nitrogen
Schedule 10 standard seamless carbon steel pipe
ID
Flow
Size (inch)
DN
Inch
mm
Min scfm
Max scfm
Min m3n/hr
Max m3n/hr
2
50
2.2
54.8
2
749
4
1,273
3
80
3.3
82.8
6
1,712
10
2,908
4
100
4.3
108.2
10
2,923
17
4,966
6
150
6.4
161.5
22
6,508
37
11,057
8
200
8.3
211.6
37
11,173
63
18,982
10
250
10.4
264.7
58
17,487
99
29,709
12
300
12.4
314.7
82
24,724
140
42,004
16
400
15.6
396.8
131
39,315
223
66,794
20
500
19.6
496.9
205
61,643
349
104,729
The ranges apply only to compressed air and nitrogen

© 2019 VPInstruments | MAN-VP-SPRO-EN | Revision: 1901 | Date: 04-07-2019
20
7 Display
The display provide some additional features:
·
LCD display with 3 rows of real time data, refreshed every second
·
Key pad with menu to configure the main settings
·
Data logger with adjustable logging intervals (option)
·
5 custom units (multiply an existing unit with a factor and show it on the LCD display).
Configuration can be done with VPStudio.
By default, the display will show 3 rows of measurement data in the factory default units: mn/sec,
deg C and bar (g). The menu can be entered to change the configuration. See section menu for all
configuration options.
The VPFlowScope display can be powered up without a sensor being connected. In this case a "no
sensor" message will be shown when the device. Always connect a sensor to ensure proper
operation.
7.1 Display status icons
Some status icons show feedback on the meters' status. Below is a list with explanation
Icons
Description
Sensor module is properly connected and supplied with power
No communication with the sensor [Check external power when disconnected]
A blinking dot will indicate that a data session is active
2 rotating arrows indicate that there is communication with the computer
The display is locked. The menu can not be accessed
Memory indication. Each block indicates 20% of memory usage. The blocks start to
blink if the memory is more then 95% full
7.2 LCD display
The LCD display provides 3 rows for real time data. Each row can be configured in the display menu
by selecting the desired parameter for this row.
Available options are listed in menu -> display.
Other manuals for VPFlowScope
1
This manual suits for next models
1
Table of contents
Popular Analytical Instrument manuals by other brands
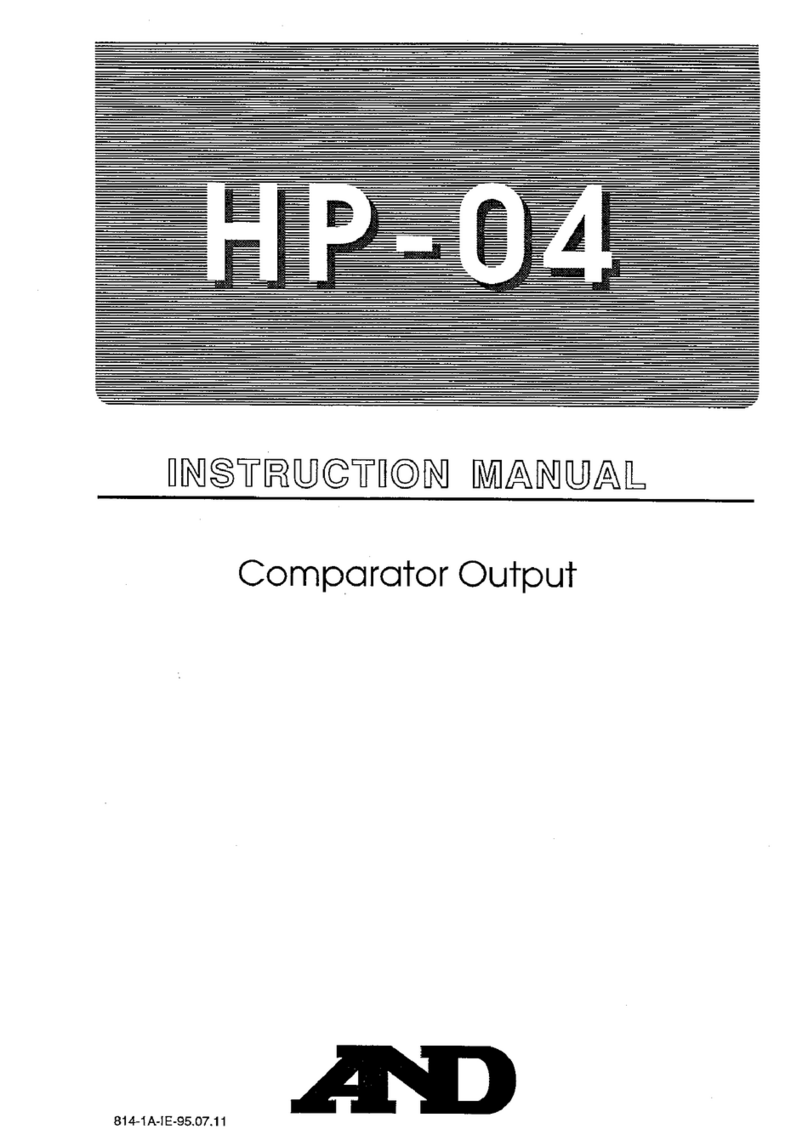
A&D
A&D HP-04 instruction manual
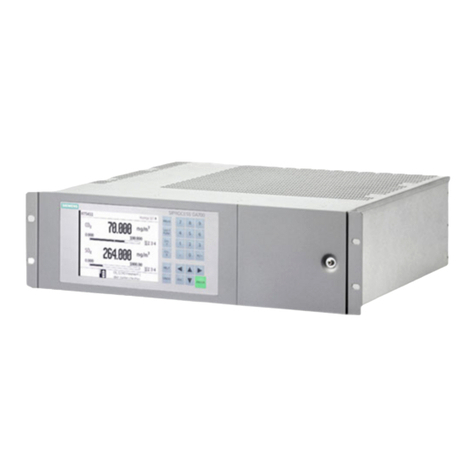
Siemens
Siemens SIPROCESS GA700 quick start
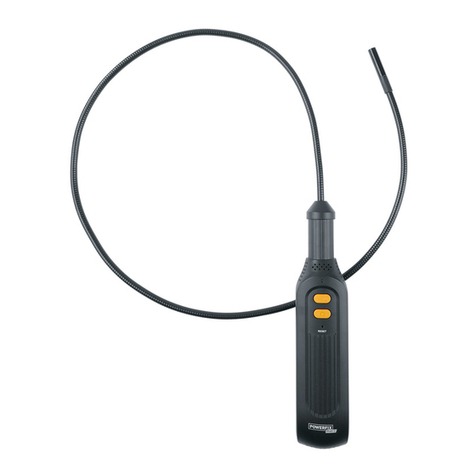
Powerfix Profi
Powerfix Profi PEKW 8 A1 Operating instructions and safety instructions

Swan Analytical Instruments
Swan Analytical Instruments AMI Hydrazine Operator's manual
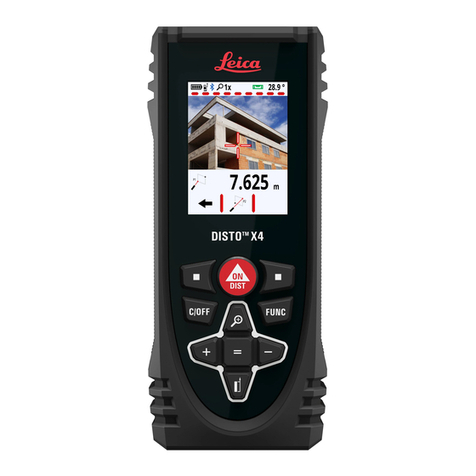
Leica
Leica DISTO X4 instruction manual

Swann
Swann AMI Trides Operator's manual