VST S-810 User manual

VST FUEL S-810
INSTALLATION INSTRUCTIONS
VST 002.001
# 09805988
Revised 6/10
This document contains information proprietary to VST Fuel Management, Inc. and shall not be disclosed,
duplicated, or used for procurement, design, or manufacture, without the expressed written consent of VST Fuel
Management, Inc..
Copyright 2008 by VST Fuel Management, Inc.
All rights reserved
VST, 2010 1

VST FUEL MANAGEMENT, INC. PHOENIX, ARIZONA
CONFIDENTIAL
THE SYSTEM VALIDITY CODE FOR THIS UNIT IS _____ _____ _____
PLEASE USE THIS SYSTEM VALIDITY CODE WHEN PROFILING THE SYSTEM. INPUT DEVICES ARE
CHECKED AGAINST THE SYSTEM VALIDITY CODE AND WILL BE REJECTED IF THE
SYSTEM VALIDITY CODE AND THE INPUT DEVICE VALIDITY CODE DO NOT MATCH.
REFER TO THE STARTUP INSTRUCTIONS FOR MORE INFORMATION ON PROFILING
THE SYSTEM VALIDITY CODE.
READ THIS IMPORTANT SAFETY INFORMATION BEFORE INSTALLING THE
VST FUEL MANAGEMENT S-810 SYSTEM.
Parts of this product are installed and operated in the environment surrounding a gasoline service station. It is
important that you, the installer, take every precaution to prevent possible hazards which could result in serious
bodily injury and property damage.
You are responsible for installing this product according to the instructions and warnings contained within this
manual and found in the appropriate federal, state and local regulations and safety codes. Failure to install this
product in accordance with these instructions will void all warranties connected with this product and could create
hazards which might result in death, injury, and property damage.
Please keep the unit locked whenever possible to prevent its misuse. Present the front panel key only to an
authorized user.
WARNING:
READ ALL OF THE INSTALLATION INSTRUCTIONS AND WARNINGS FOUND IN THIS MANUAL
CAREFULLY. FAILURE TO DO SO COULD RESULT IN DEATH,SERIOUS
PERSONAL INJURY,PROPERTY DAMAGE,OR UNDETECTED POTENTIAL
ENVIRONMENTAL AND HEALTH HAZARDS.
VST, 2010 2

TABLE OF CONTENTS
1. INTRODUCTION 4
1.1 General 4
Figure 1. Typical Installation of VST Fuel S-810 4
1.2 Product Description 5
1.3 Specifications 5
2. GETTING STARTED 6
2.1 Inspection/Damage Claims 6
2.2 Parts Verification 6
2.3 Return Shipping 6
3. SITE PREPARATION 6
3.1 Mounting the VST Fuel S-810 7
Figure 2. VST Fuel S-810 Dimensions 7
Figure 3. VST Fuel S-810 Pedestal Mounting 8
3.2 Conduit installation 9
4. VST FUEL S-810 INSTALLATION 9
4.1 Wiring Requirements 9
4.2 Wire Manufacturers 9
4.3 Dispensers/Pumps 9
Table 1. Size of Dispenser Junction Box 10
b. Interface wiring 11
c. Dispenser wiring 11
Figure 4. Typical Wiring for 115Vac or 230 Vac VST Fuel S-810 12
Wiring Diagram 13
4.4 Communications 14
5. VST FUEL S-810 WIRING VERIFICATION 14
5.1 General 14
5.2 Diagnostics check 14
5.2 Diagnostics check 15
5.3 Dispensers/Pump Control 16
Figure 11. Pump Interface Board Jumper Settings 16
5.4 Handle Switch/Run circuit 17
5.5 Pulse Transmitters 16
6. WARRANTY CONDITIONS AND LIMITATIONS 16
6.1 Warranty 16
6.2 Limitation of Damages 17
6.3 Inspection and Limitation of Actions 17
6.4 Interpretation 17
VST, 2010 3

INTRODUCTION
1.1 General
This instruction manual is intended to assist the user with the installation of the VST Fuel S-810 Fuel Management
System. Due to wide variations in dispenser/pump wiring and fueling site layout, it is virtually impossible
to provide detailed instructions for each individual installation. This manual provides a general description
of various types of installations applicable to VST Fuel S-810 systems. Installation shall be in accordance
with National Electric Code (NFPA-70), the Automotive and Marine Service Station Code (NFPA-30A),
the Flammable and Combustible Liquids Code (NFPA-30) and applicable local codes. See Figure 1 for a
general diagram of a typical station layout and mounting restrictions for VST Fuel S-810 location.
THE VST FUEL S-810 IS CAPABLE OF MANAGING UP TO FOUR HOSES
VST, 2010 4

Figure 1. Typical Installation of VST Fuel S-810
VST, 2010 5

1.2 Product Description
The VST Fuel S-810 Fuel Management System is a self- contained, micro-processor based, control and data
acquisition system designed to authorize, monitor, and record fuel dispensing operations. The VST Fuel
S-810 consists of an Island Mounted Data Entry Terminal (DET) which has the capability of simultaneous
control and monitoring of from one to four dispensers. Access input device options for the VST Fuel S-810
are available for magnetic cards, optical cards, touch buttons, or keys. Models are also available which use
keypad entry only and do not require an input device.
Operating the VST Fuel S-810 is straightforward. The user inserts his input device or “keypad entry only” into the
VST Fuel S-810 and enters the required information on the keypad; usually a PIN number and odometer
reading, etc.. If the input device and the entered information are valid, the VST Fuel S-810 applies power
to the requested pump, allowing the user to dispense fuel. At the completion of fueling, the VST Fuel
S-810 transmits transaction information to its output devices and stores the information in its transaction
memory for later recall. The VST Fuel S-810 will hold up to 1000 transactions in memory for
downloading.
The VST Fuel S-810 Fuel Management System has the capability of operating with a wide range of output devices,
which include printers, modems, personal computers, and other devices which are RS-232 or RS-485
compatible.
The various system operations for control of the VST Fuel S-810 and the generation of reports from the VST Fuel
S-810 are thru priority VST Fuel Management, Inc. software. These commands may be issued locally from
a personal computer or remotely by dial-up communications from a personal computer, , or other serial
communication device. Refer to the Operators Manuals and Reference Manuals for additional information.
1.3 Specifications
Power Requirements: 115 VAC, 50/60 HZ, 1/2 A or
Dimensions: 15.5 inches wide x 10.5 inches high x 13.5 inches deep
Weight: Approximately 25 Pounds
Operating Temperature: -30 to 140 Degrees Fahrenheit
Environment : Weatherproof, suitable for outdoor mounting in a
non-classified area in a service station. Not suitable
for direct connection to intrinsically safe wiring.
Pump Controls/Monitors: 1 Control Relay: 115 VAC, 6 A, 1/3 HP or
(Per pump, four pumps max.) 230 VAC, 3 A, 1/3 HP
1 Pulser Input: 12 VDC, 10 ma Minimum,
50% duty cycle, pulse rates
up to 500 pulses per minute
1 Handle Switch Input: 115 VAC, 20 MA Maximum or
230 VAC, 20 MA Maximum
Communications: 3 RS-232/RS-485 Asynchronous Communication Ports
VST, 2010 6

2. GETTING STARTED
2.1 Inspection/Damage Claims
a) Examine all components thoroughly as soon as received. If damaged, write a complete and detailed description of
the damage on the face of the freight bill. Have the carrier's agent sign the description.
b) Notify the delivering carrier of damage or loss immediately. This may be done either in person or by telephone.
Written confirmation must be mailed within 48 hours.
c) Risk of loss or damage to merchandise remains with the buyer. It is the buyer's responsibility to file a claim with
the carrier involved.
d) If you need assistance contact your distributor or the VST factory representative.
2.2 Parts Verification
Prior to starting work, make sure that all of the correct parts have been received.
You will also need the following partial list of parts to complete the installation:
1. Pulsers for each dispenser - 1, 10 , 100 or 500 pulses/gallon
2. A Single Pole Double Throw (SPDT) or Double Pole Double Throw (DPDT) switch
activated by the dispenser handle.
3. An Electric Reset (optional).
4. A Junction box of sufficient volume for each dispenser.
2.3 Return Shipping
All return shipments of VST products must be prepaid. Return items in their original shipping containers. VST will
accept no liability for damage caused by improper packing. Address the shipment to:
Service Department
VST Fuel Management, Inc.
2238 N. Los Alamos
Mesa, Arizona 85213
3. SITE PREPARATION
3.1 Mounting the VST Fuel S-810
VST, 2010 7

First, a spot must be selected that is convenient for the users of the system and is appropriate from a wiring point of
view. Refer to Figure 1 for mounting location restrictions. Also refer to the National Electrical Code for
specific information on the location of classified areas in and around service stations and fuel dispensing
equipment. Pay particular attention to the layout of conduit runs and the placement of ac conduit and low
voltage conduit. Care should be taken to provide as much isolation as possible between these wire/conduit
runs and any sources of electrical noise.
The VST Fuel S-810 (DET) may be mounted using either of two methods. The first method is mounting the DET
on the top of a 2 inch pipe x 55” (approx.) height. The DET is simply screwed onto the pipe and after
being positioned for operation the two set screws in the mounting hub are tightened to prevent the DET
from turning during normal operation. The second method consists of removing the mounting hub
normally supplied with the DET and using the gasket and bolts to fasten the DET to the VST Pedestal. The
VST Pedestal must be anchored to the island using six 1/4 inch bolts and appropriate concrete anchors.
Refer to Figures 2 and 3 for detailed information on the space requirements and the bolt pattern required for
mounting the pedestal. Note that the suggested clearance requirements in Figure 2 are for operation and
service of the VST Fuel S-810.
VST, 2010 8

Figure 2. VST Fuel S-810 Dimensions
VST, 2010 9

Figure 3. VST Fuel S-810 Pedestal Mounting
VST, 2010 10

3.2 Conduit installation
Conduit must be installed for the VST Fuel S-810 wiring. Refer to the National Electric Code and applicable local
codes for specific requirements. Generally, rigid metallic conduit is recommended for all wiring due to its
electrical noise shielding and durability characteristics. Other types of conduit may be used as allowed by
the National Electric Code and applicable local codes if proper precautions are taken in its application.
Separate conduits are required for the ac circuits and for the low voltage circuits. Shielded cable is
recommended for all low voltage circuits.
4. VST FUEL S-810 INSTALLATION
4.1 Wiring Requirements
The wire insulation must be oil and moisture proof, using THW, THWN, or equivalent insulation as defined in the
National Electrical Code. All VST Fuel S-810 low-voltage wire size is to be minimum AWG #18 stranded
shielded cable with the shield grounded at one end only. AC wire size is to be minimum AWG #14.
All wiring should be either color coded or numbered to facilitate connection of the wire ends.
CAUTION:
Do not use non moisture, non oil-proof, or standard house grade wire.
4.2 Wire Manufacturers
There are several manufacturers of wiring, any of which produce wire and cable that will work satisfactorily, The
following wire manufacturers' products have been used in conduit on previous systems with good results.
Alpha Wire Corporation; Elizabeth, New Jersey
Belden Electronic Wire and Cable; Richmond, Indiana
Chester Cable Company; Chester, New York
Coleman Wire and Cable Company; Chicago, Illinois
General Electric Vulkene Wire
4.3 Dispensers/Pumps
A. GENERAL
VST Fuel S-810 systems are designed to operate with most commercial type fuel dispensers or pumps. The
dispensers and/or pumps are normally provided by the user or qualified contractor.
For most efficient system operation, dispensers/pumps should be equipped with electric resets. This feature
simplifies control interfacing and, also, helps eliminate false counts during the dispenser computer reset
cycle.
VST, 2010 11

The dispensers/pumps must contain a 1, 10, 100 or 500 count/gallon pulse transmitter and a Single Pole Double
Throw (SPDT) or Double Pole Double Throw (DPDT) switch that operates when the dispenser/pump is
turned on and off. This switch is used to generate a fueling-complete signal when turned off.
Each dispenser must have a junction box of sufficient volume. See Table 1.
Table 1. Size of Dispenser Junction Box
Size of Conductor
Free Space within Box for Each
Conductor, Cubic Inches
AWG
Box with Hubs
Box without Hubs
16 or smaller
1.3
1.5
14
1.8
2.0
12
2.0
2.25
10
2.2
2.5
8
2.7
3.0
.
Note: A conductor passing through the box and each conductor terminating in the box is counted as
one conductor. No unplugged openings are permitted
WARNING:
IN INSTALLATION AND USE OF THIS PRODUCT, COMPLY WITH THE NATIONAL ELECTRICAL CODE;
FEDERAL, STATE, AND LOCAL CODES; AND ANY OTHER APPLICABLE SAFETY CODES. IN
ADDITION, TURN OFF POWER AND TAKE OTHER NECESSARY PRECAUTIONS DURING
INSTALLATION, SERVICE, AND REPAIR TO PREVENT PERSONAL INJURY, PROPERTY LOSS,
AND EQUIPMENT DAMAGE.
THIS EQUIPMENT IS TO BE INSTALLED IN ACCORDANCE WITH THE NATIONAL ELECTRICAL CODE
(NFPA-70) ,THE AUTOMOTIVE AND MARINE SERVICE STATION CODE (NFPA-30A), AND THE
FLAMMABLE AND COMBUSTIBLE LIQUIDS CODE (NFPA-3O) .
CAUTION:
THIS EQUIPMENT IS NOT SUITABLE FOR DIRECT CONNECTION TO
INTRINSICALLY SAFE CIRCUITS.
This equipment is intended for self-service type dispensing devices containing equipment suitable for that purpose.
The wiring diagrams contained here typify installation circuits for dispensers containing:
Computer electric reset actuator (when provided)
Pulse transmitter with appropriate ratings
VST, 2010 12

Pump motor control relay (when provided)
Solenoid valve (when provided)
Pump motor (when applicable).
The following paragraphs in this section provide guidelines for wiring dispensers to VST Fuel S-810 systems. These
instructions should be followed as closely as possible for proper system operation. Functional descriptions
and drawings are provided in this section to assist installers with wiring data.
B. VST FUEL S-810 INTERFACE WIRING
1. Typical dispenser-to-VST Fuel S-810 field wiring diagrams are included in this section (see drawing). The VST
Fuel S-810 connections are shown in the drawing as they appear on the back of the VST Fuel S-810 with
the cover removed. (Installations may vary from this concept due to wiring codes and other circumstances.)
Wiring diagrams of dispensers are used as examples only and in no way imply that the units used with the
system must be rewired to conform with the drawings. Dispensers are shown in all drawings at the end of
fueling with the operating handle in the off position.
2. Install all interconnecting wiring using the most applicable local wiring codes and reliable installation methods.
Wire should be installed in rigid conduit buried in a trench. When planning wire runs, the following
specifications apply:
a. Use Table 1 and the National Electrical Code to determine size of conduit required for the number
of conductors.
b. When possible, install at least 25 percent spares for expansion and maintenance.
CAUTION:
NEVER RUN AC OR OTHER EQUIPMENT WIRING WITH VST FUEL S-810 LOW-VOLTAGE WIRING
UNLESS IT IS IMPOSSIBLE TO AVOID SUCH WIRE RUNS. FAILURE TO COMPLY MAY CAUSE
MALFUNCTION OR POSSIBLE EQUIPMENT DAMAGE.
c. Never run ac or other manufacturers' equipment wiring with VST Fuel S-810 wiring unless it is
impossible to avoid such wire runs. In these cases, shielded cable with outside insulating sheath
must be used for low-voltage wiring. The shield must be grounded at one end only. Insulate the
ungrounded end to prevent shorting to conduit or other wiring.
Note: Shielded wire should be used only if authorized by the applicable electrical codes.
C. DISPENSER WIRING
1. One single-pole interpose relay is provided for each dispenser. Interpose relays are located inside at the rear of
the VST Fuel S-810 housing. (See Figures 4-8 for interpose relay wiring) Relay contacts are rated at 1/3 hp
(115 Vac @ 6 amperes, 230 Vac @ 3 amperes).
2. Terminals are provided at the rear of the VST Fuel S-810 for wiring connections to the control interpose relays,
for wiring connections to the pulse transmitters, and for wiring connections to the handle switches. A
three-wire 115/230 Vac, 50/60 Hz. line input is required for ac power to the VST Fuel S-810. Screw
terminals are located at the rear of the VST Fuel S-810 for the ac line connections.
VST, 2010 13

3. The interpose relay contacts are normally wired in series with the operating handle switch, reset motor switch, or
similar control circuit of the dispenser. Take care to ensure that the dispenser is shut off and no product can
be withdrawn whenever the interpose relay contacts are open.
4. Submersible Pump System. When controlling submersible pump systems, attention must be given to pump
control and the dispenser control . The submerged pump is turned on by the first dispenser that is enabled
for a given product. This control is accomplished typically through a relay network that is normally not
associated with the VST Fuel S-810 system. Once the pump is running, fuel can be withdrawn from any
one or all of the dispensers associated with that pump unless each dispenser hose is provided with
individual control. This control may be implemented through the use of electrically operated solenoid
valves.
5. Pulser Wiring. Each dispenser, pump, or hose to be controlled and monitored by the VST Fuel S-810 system
requires a pulse transmitter (pulser). The pulser should be a 1, 10, 100 or 500 pulses per gallon resettable
type.
6. Run Circuit or Fueling-Complete Switch. This switch is used for product count enable and for a fueling complete
signal. This switch normally is part of the electric reset. If the proper switch is not available, a relay may be
used. The switch or relay contact allows the pulser to count into the VST Fuel S-810 input only after the
dispenser computer has been reset to zero. This prevents false counts from the pulser into the meter input
during the reset cycle. The switch, in the off position, provides a contact closure to the VST Fuel S-810 to
indicate that fueling has been completed.
Figure 4. See Drawing
Typical Wiring for a “relay control” of 115 Vac pump or 220Vac Submerged
Pump
VST, 2010 14

4.4 Communications
VST Fuel S-810 systems are designed to interface to serial communication devices. Generally the serial device is a
printer, a modem, or a personal computer. Connection to these devices are at the removable terminal strip
on the RS 232 or RS 485 boards mounted on the MotherBoard inside the VT-Fuel 810
(See Figure 15). Low voltage wiring is used to make these connections. A communications grade of shielded cable
suitable for RS 232 or RS 485 is recommended (#24 AWG minimum, twisted pair, low capacitance). Be
sure to ground the shield at one end only.
The following figures (Figures 9-14) show typical installation connections for several devices. Specific devices may
require jumpers on some of the control signals that are not required for the operation of the VST Fuel
S-810. Usually connecting the communication device's DTR signal back to the DSR, DCD, and CTS
signals will satisfy any protocol requirements for printers and personal computers. Modems need to be
configured in the answer mode with the appropriate baud rate. The configuration should be stored as the
default mode of the modem on power up to insure that it will operate without intervention. Figure 12 shows
the minimum field wiring required for a modem. The additional control signals (CTS, DCD, RTS, and
DTR) may be connected on a one-for-one basis if desired (See Figure 13). The support of these signals is
limited to providing the correct signal level for operation of the modem.
WARNING:
LOOSE CABLES,OR CABLES ROUTED ON FLOORS OR PASSAGE AREAS,CREATE HAZARDOUS CONDITIONS TO PERSONNEL
AND POSSIBLE DAMAGE TO EQUIPMENT. PROPERLY SECURE ALL CABLING TO FLAT SURFACES,SUCH AS
WALLS OR TABLE SIDES TO AVOID PERSONAL INJURY, PROPERTY LOSS, AND EQUIPMENT DAMAGE
5. VST FUEL S-810 WIRING VERIFICATION
5.1 General
In order to verify the wiring it is convenient to have the VST Fuel S-810 operational (ac power applied) and be
familiar with some of the basic built-in diagnostic tools. This section is a brief explanation of the built-in
diagnostics. These diagnostics may vary for specific systems, but will generally contain at least those
shown below. The Configuration switch definitions may also vary for specific systems. If there are
differences from those shown, refer to the applicable reference manuals for each specific system.
DIAGNOSTICS CHECK: To access the diagnostics feature of the VST Fuel S-810, the configuration switches
located on the Motherboard must be set as follows (See Figure 15):
Switch # 8 set to ON
After making the necessary switch changes, press the RESET button on the Motherboard, close and lock the front
panel of the VST Fuel S-810 (See Figure 15). The display on the front panel should be as follows:
ENTER DIAG #
VST, 2010 15

You can now perform the diagnostic tests from the keypad on the front panel of the VST Fuel S-810. Each of the
following diagnostic tests are engaged by keying in the number of the desired diagnostic routine. To go to
the next diagnostic routine or to terminate the current one, press CLEAR ENTRY.
DIAG # 1 DISPLAY DIAGNOSTIC: This test is performed to insure that all the elements of the display are
functioning correctly . When this diagnostic routine is engaged, the display will start scrolling the complete
character set and will continue until the CLEAR ENTRY key is pressed.
DIAG # 2 KEYPAD TEST: The keypad test is used to check the functions of all the keys on the keypad. The
test is performed by pressing each key and checking the corresponding display. To exit this diagnostic
routine, press CLEAR ENTRY.
DIAG # 3 READER TEST: The reader diagnostics checks the reader to insure accurate reading of the input
devices (cards, keys, or touch memories). An input device is inserted into the reader, and the display will
show the information from the device. The information on the device is then compared against the
displayed information to test for accuracy. To exit this diagnostic routine press CLEAR ENTRY
DIAG # 4 PUMP CONTROL RELAY TEST: This diagnostic is used to check the pump control relays, to
insure that they will energize upon command from the system and will control the correct pump. When
Diagnostic # four is selected, the display will change to the following:
SELECT PUMP
When you press key 1 the display will change to the following:
1 2 3 4 PUMPS <---- The four pumps.
1 0 0 0 <---- The 1 indicates ON,
the 0's indicate OFF
You could have pressed a 2, 3, or 4, instead of the 1. The number of the pump you press indicates which pump you
are trying to energize. As each pump is energized, the 0's under the pump number will change to 1's. To go
to the next diagnostic press CLEAR ENTRY.
DIAG # 5 PULSER DIAGNOSTICS: The pulser diagnostic is used to check the interface of the system to
the pulsers on the pumps. The pump BYPASS/NORMAL switch must be in the BYPASS position to
perform this test. Pressing key 5, ENTER will cause the display to change to the following:
1 2 3 4 PULSERS <---- Pulser numbers.
0 0 0 0 <---- 0 = OFF, 1 = ON
As each pulser is operated (by pumping fuel), the 0 under that pulser number will alternate between 0 and 1,
indicating that the pulser is working. To exit this diagnostic routine press CLEAR ENTRY.
DIAG # 6 HANDLE SWITCH DIAGNOSTIC: The Handle Switch Diagnostic is used to test the operation
of the dispensers' handle switch, and the interface to the ESI-FUEL 810.. The pump BYPASS/NORMAL
switch must be in the BYPASS position to perform this test. Press 6, ENTER and the display should
change to the following:
1 2 3 4 PUMP SWITCHES
0 0 0 0 0 = SWITCH OPEN, 1 = SWITCH CLOSED
The 0 indicates an open circuit. As each pump switch handle is turned on the 0 for that number pump will change to
a 1. To exit this diagnostic press CLEAR ENTRY.
VST, 2010 16

Configuration Switch settings:
From the following descriptions of the switch functions, you will have to determine the correct position for each of
the eight switches. For the initial set-up all should be placed in the OFF position. The configuration switch
is located on the VST Fuel S-810 Motherboard (See Figure 15). Note that anytime the switch positions are
changed the RESET button will need to be pressed.
5.2 AC Power
Turn the On/Off switch inside the VST Fuel S-810 to the Off position. Turn on the breaker and measure the ac
voltage at the terminals labeled "L" and "N" on the back of the VST-Fuel 810 (TB-1). The measured
voltage should be approximately 115 Vac. (Or 230 Vac for the 230 Vac Model). Verify that the ground
terminal is connected to a low impedance ground. If the correct voltage is present, turn the Esi-Fuel 810
power switch to the on position. Put the VST Fuel S-810 into the keypad diagnostic mode as explained in
the previous section. Run the diagnostics for the display (DIAG #1) and keypad entry (DIAG #2) at this
time as a general check that the VST Fuel S-810 is functioning.
5.3 Dispensers/Pump Control
Before proceeding, verify that the jumper blocks on the pump interface boards are in the proper positions for each
board (See Figure 16). If they need to be changed, turn the power off and change the jumper blocks to the
correct positions.
For each pump interface board, place the BYPASS/NORMAL switch in the bypass position and verify that the
proper voltage is applied to the pump or dispenser. Do this one pump at a time to isolate and detect any
cross wiring. Verify that the level of voltages on the pulser circuits is approximately 10 Vdc and that the
voltage on the run circuit is 115 Vac only when the pump is authorized and the handle is in the on position.
Figure 16. Pump Interface Board Jumper Settings
VST, 2010 17

5.4 Handle Switch/Run circuit
Using the Handle Switch Diagnostic (DIAG #6) and the pump switches in the BYPASS position verify that the
handle switch is detected for each pump. Turn the handles on one at a time and check that only the
indicator for that pump is on. Do this for all pumps attached to the VST Fuel S-810.
5.5 Pulse Transmitters
Using the Pulser Diagnostic (DIAG #5) authorize each pump and dispense a small amount of fuel to verify that the
pulsers are counting properly. Do this for each pump one at a time. Also verify that the pulsers are
connected to their respective pumps.
5.6 Communications
Checking out the communications circuits require the communications boards addresses and jumpers to be in the
proper positions. Refer to the system documentation to verify that all jumpers are configured correctly (See
Figure 17). Refer to the Operators Manual for information on communicating with the VST Fuel S-810.
6. WARRANTY CONDITIONS AND LIMITATIONS
6.1 Warranty
VST Fuel Management, Inc. warrants this product, of VST manufacture, to be free from defects in material and
workmanship for a period of one (1) year from the date of invoice. If VST receives written notification and
determines that the equipment is defective within this period, VST (or its representative) will, at its option,
repair or replace the product. During the first ninety (90) days of the warranty period, the product will be
repaired at no cost to the user, at the location where the product is in use. After the first ninety (90) days of
the warranty period, VST will repair or replace the product only if it is returned to the VST factory (at the
Tempe facility), transportation prepaid. The foregoing warranty will not cover reimbursement for labor,
transportation, removal, installation or other expenses which may be incurred in connection with repair or
replacement.
This warranty shall not apply to any products which VST determines have, by the user or otherwise, been the subject
of misuse, misapplication, neglect, alteration, damage, or improper installation, operation, maintenance,
storage or repair. This warranty applies only when a valid Warranty Registration and Check-out Form has
been filed with VST Fuel Management, Inc.
Except as may be expressly provided in an authorized writing by VST, VST shall not be subject to any other
obligations or liabilities whatsoever, expressed or implied, with respect to equipment manufactured by VST
or services rendered by VST.
THE FOREGOING WARRANTIES ARE EXCLUSIVE AND IN LIEU OF ALL OTHER EXPRESS AND
IMPLIED WARRANTIES EXCEPT WARRANTIES OF TITLE, INCLUDING BUT NOT LIMITED TO
IMPLIED WARRANTIES OF MERCHANTABILITY AND FITNESS FOR A PARTICULAR
PURPOSE. VST further disclaims any responsibility whatsoever for injury to person or damage to or loss
of property or value caused by any product which has been subjected to misuse, negligence, or accident; or
misapplied; or used in violation of product manuals, instructions, or warning; or modified or repaired by
unauthorized persons; or improperly installed; or malfunctioning.
VST, 2010 18

6.2 Limitation of Damages
Not withstanding any other provision contained herein. VST SHALL NOT BE LIABLE IN CONTRACT. IN TORT
(INCLUDING NEGLIGENCE OR STRICT LIABILITY) OR OTHERWISE FOR ANY SPECIAL,
INCIDENTAL OR CONSEQUENTIAL DAMAGES, LOSSES, OR EXPENSES ARISING FROM THIS
CONTRACT OR ITS PERFORMANCE IN CONNECTION WITH THE USE OF OR INABILITY TO
USE, THIS PRODUCT FOR ANY PURPOSE, WHATSOEVER.
6.3 Inspection and Limitation of Actions
The user must inspect the product promptly after receipt and notify VST Fuel Management, Inc., in writing, of any
claims, including claims of breach of warranty, within thirty days after the facts upon which the claim is
based are discovered or should have been discovered. Failure to give written notice of a claim within the
time period shall be deemed to be a waiver of such claim.
No action arising from this contract, regardless of form, may be commenced more than one (1) year after the cause
of action has accrued, except an action for nonpayment.
6.4 Interpretation
These conditions and any accompanying contract of sale shall be considered as made and performed in the state or
Arizona and governed by, interpreted, and construed according to the laws of Arizona.
VST, 2010 19
Table of contents
Popular Control System manuals by other brands
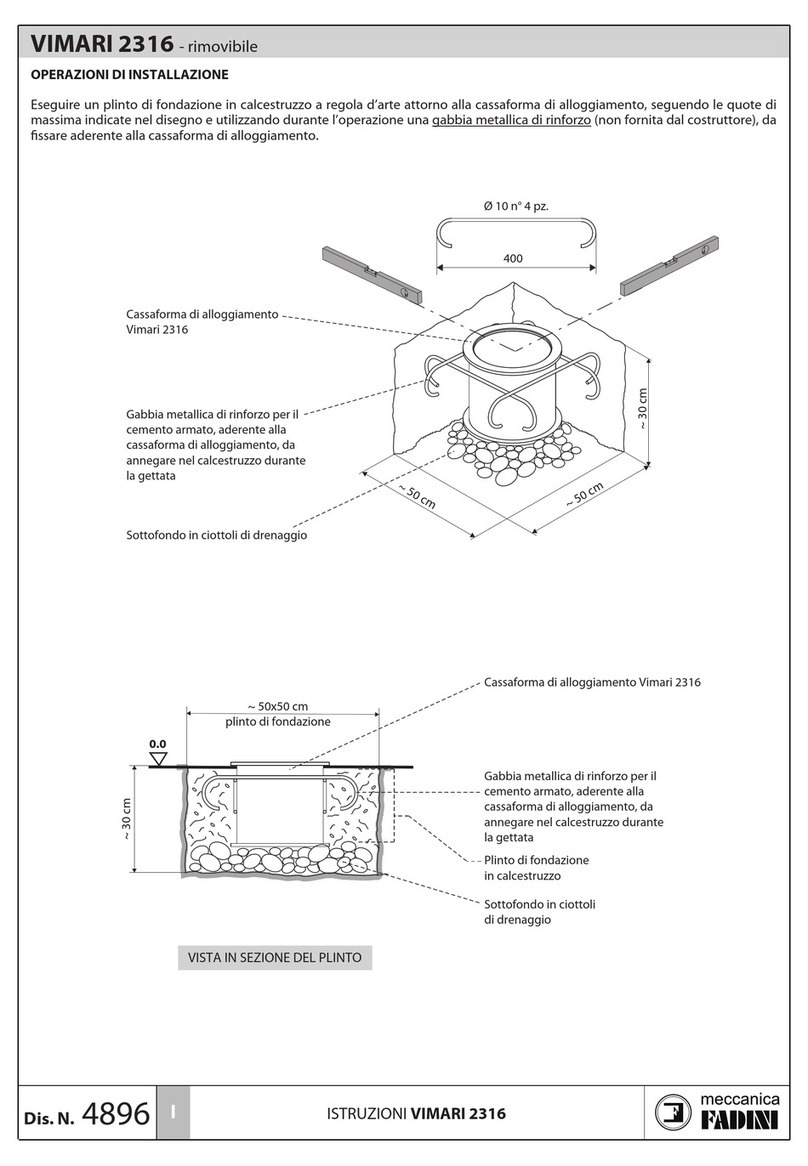
Meccanica Fadini
Meccanica Fadini VIMARI 2316 instructions

Burk
Burk ARC Plus SL instruction manual

Compool
Compool Cp3810 Installation & operating instructions
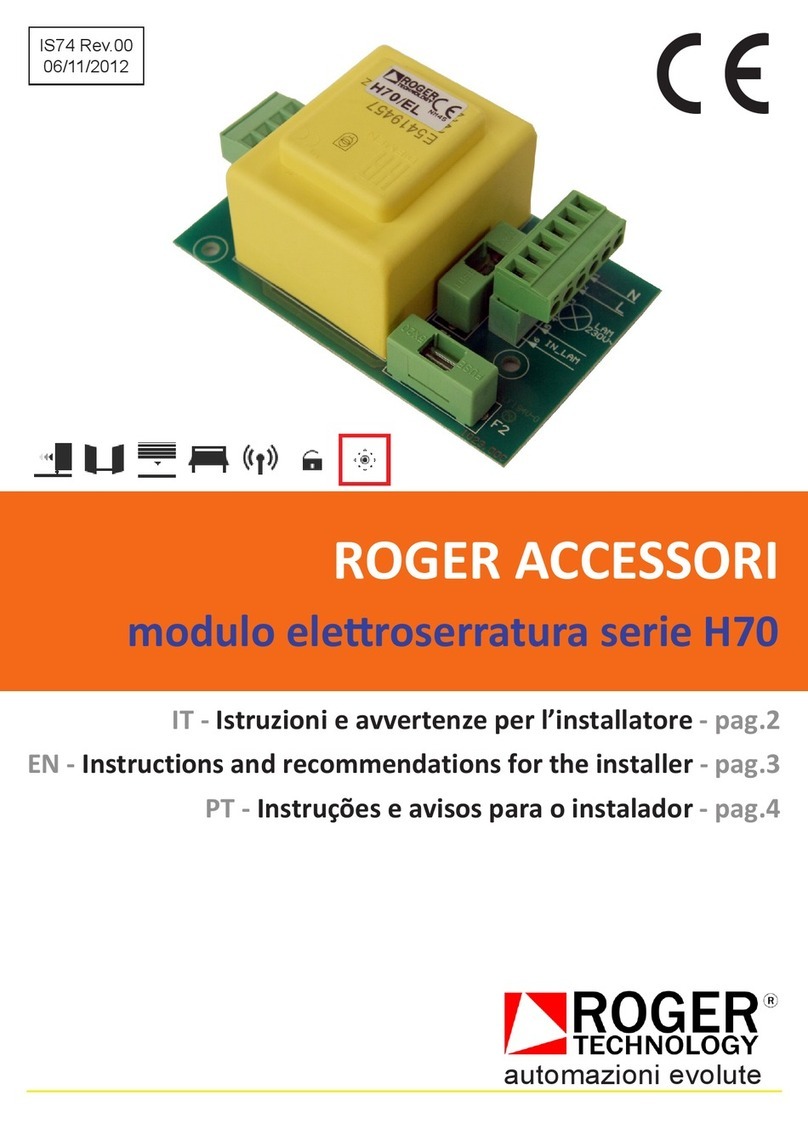
Roger Technology
Roger Technology H70 Series INSTRUCTIONS AND RECOMMENDATIONS FOR THE INSTALLER
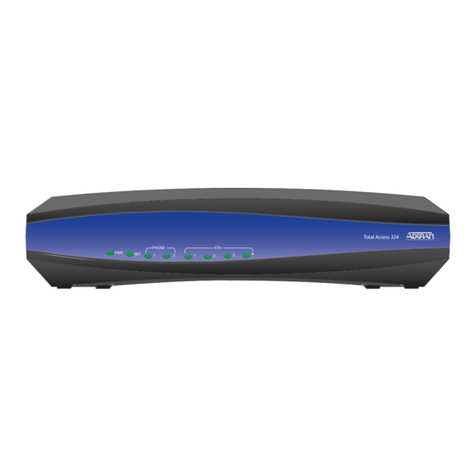
ADTRAN
ADTRAN Total Access 300 Series Installation and maintenance guide
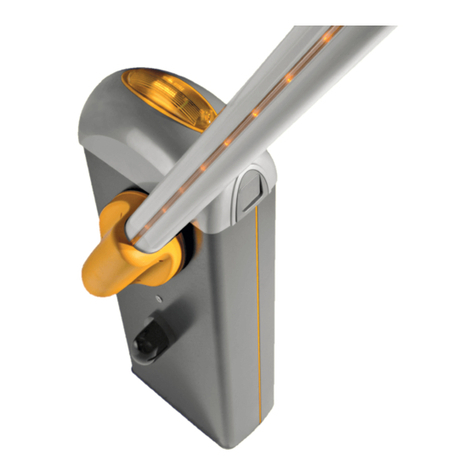
CAME
CAME Barriere GARD quick start guide