WARPP DCWF-V1 User manual

1
Digital Cold Wire Feeder
Operating Manual
Model No - DCWF-V1.
Warpp Engineers Pvt Ltd.
Source of eliable welding and cutting equipment.
B-1005, 10th Floor, Western Edge 2, Near Metro Mall, Off western Express Highway, Borivali
(East). Pin code 400066.
TEL: 022-28542272 / 73 / 74.
E mail: sales@warpp.co.in Website: www.warpp.co.in

2
Thank you for selecting WARPP brand Digital cold wire feeder. In order to
keep you safe away from une pected accidents, and enjoy full benefits offered by our
quality products during welding, please read the instruction in details prior to
operation. Complying with procedures defined in this manual is always appreciated.
IMPO TANT
ead this manual carefully before installing, commissioning or operating this
product.
NOTICE :-
The installation, operation and maintenance guidelines set out in this manual will
enable you to maintain the equipment in peak condition and achieve ma imum
efficiency with your welding operation. Please read these instructions carefully to
become aware of every advantage.
CAUTION :-
Only e perienced personnel familiar with the operation and safe practice of welding
equipment should install and /or use this equipment.
Table of Contents
Section 1 .................................................................................................................. 3.
Safety Precautions ................................................................................................... 3.
A. Arc Welding ...................................................................................................... 3.
B. Electric Shock .................................................................................................... 3.
C. Arc Rays ............................................................................................................. 4.
D.Fume sand Gases ..................................................................................................4.
E. Cylinders .............................................................................................................. 5.
F. Welding ................................................................................................................. 5.
G. Moving Parts ........................................................................................................ 6.
H. EMF Information ................................................................................................. 6.
Section 2 ................................................................................................................... 7.
System Components ................................................................................................. 7.
Maintenance ............................................................................................................. 7.
Warning..................................................................................................................... 7.
Caution...................................................................................................................... 7.
Digital Cold Wire Feeder picture .............................................................................. 8.
Section 3 ................................................................................................................... 8.
A. Digital cold wire feeder Features ......................................................................... 8.
B. How to operate the digital key pad ....................................................................... 9.
C. SETTING ............................................................................................................ 10.
D. SPEED MODE SETTING .................................................................................. 10.

3
E. PULSE MODE SETTING .................................................................................. 10.
F. Important Note. ................................................................................................... 12.
Section 4 ................................................................................................................. 13.
1) Wire Feeder structure .......................................................................................... 13.
2) Wire Feeder Roller and Installation ..................................................................... 13.
Section 5 .................................................................................................................. 14.
Brake force of wire spool adjustment ...................................................................... 14.
Section 6 ................................................................................................................... 15.
Specifications ........................................................................................................... 15.
Appendi A ............................................................................................................... 16.
Section 1
Safety Precautions :-
WA NING
These Safety Precautions are for your protection. They summarize precautionary
information from the references listed in
Additional Safety Information section. Before performing any installation or
operating procedures, be sure to read and follow the safety precautions listed below as
well as all other manuals, material safety data sheets, labels, etc. Failure to observe
Safety Precautions can result in injury or death.
A. Arc Welding
Arc Welding can be hazardous. Protect yourself and others from possible serious
injury or death. Keep children away. In welding, as in most jobs, e posure to certain
hazards occurs. Welding is safe when precautions are taken. The safety information
given below is only a summary of the more complete safety information that will be
found in the Safety Standards listed at the end of this section. Read and follow all
Safety Standards. Have all installation, operation, maintenance and repair work
performed only by qualified people.
B. Electric Shock
Touching live electrical parts can cause fatal shocks or severe burns. The electrode
and work circuit is electrically live whenever the output is on. The input power circuit
and machine internal circuits are also live when power is on. When using mechanized
wire feed, the wire, wire reel, drive roll housing and all metal parts touching the
welding wire are electrically live. Incorrectly installed or improperly grounded
equipment is a hazard.
1. Do not touch live electrical parts.
2. Wear dry, hole-free insulating gloves and appropriate body protection.
3. Disconnect input power before installing or servicing this equipment.
4. Properly install and ground this equipment according to the operation manual.

4
5. Always verify the supply ground-check and be sure that input power cord ground
wire is properly connected to ground terminal in disconnect bo or that cord plug is
connected to a properly grounded receptacle outlet.
6. When making input connections, attach proper grounding conductor first - double
check connections.
7. Frequently inspect input power cord for damage or bare wiring. Replace cord
immediately if damaged - bare wiring can kill.
8. Turn off all equipment when not in use.
9. If earth grounding of the work-piece (JOB) is required, ground it directly with a
separate cable - do not use work clamp or work cable.
10. Do not touch electrode if you are in contact with the work, ground, or another
electrode from a different machine.
11. Use only well-maintained equipment. Repair or replace damaged parts at once.
Maintain unit according to manual.
12. Wear a safety harness if working above floor level.
13. Keep all panels and covers securely in place.
14. Clamp work cable with good metal to metal contact to work-piece or worktable as
near the weld as practical.
C. Arc ays
Arc rays can burn eyes and skin; noise can damage hearing; flying slag or sparks can
injure eyes.
Arc rays from the welding process produce intense visible and invisible (ultraviolet
and infrared) rays that can burn eyes and skin. Noise from some processes can
damage hearing. Chipping, grinding and weld cooling throw off pieces of metal or
slag.
1. Use approved ear plugs or ear muffs if noise level is high.
2. Use a welding helmet fitted with a proper shade of filter to protect your face and
eyes when welding or watching.
3. Wear approved safety glasses with side shields.
4. Use protective screens or barriers protect others from flash and glare; warn others
not to watch the arc.
5. Wear protective clothing made from durable, flame-resistant material (wool and
leather) and foot protection where necessary.
D. Fumes and Gases
Fumes and gases can be hazardous to your health. Welding produces fumes and gases.
Breathing these fumes and gases can be hazardous to your health.
1. Keep your head out of the fumes. Do not breathe the fumes.
2. If inside, ventilate the area and/or use e haust at the arc to remove welding fumes
and gases.
3. If ventilation is poor, use an approved air-supplied respirator.
4. Read the Material Safety Data Sheets (MSDS) and the suppliers instruction for
metals, consumables, coatings, cleaners, and degreasers.

5
5. Work in a confined space only if it is well ventilated, or while wearing an
air-supplied respirator. Always have a trained watch person nearby.
6. Do not weld in locations near cleaning, or spraying operations. The heat and rays of
the arc can react with vapors to form highly to ic and irritating gases.
7. Do not weld on coated metals, such as galvanized, lead or cadmium plated steel,
unless the coating is removed from the weld area, the area is well ventilated, and if
necessary, while wearing an air-supplied respirator. The coatings and any metals
containing these elements can give off to ic fumes if welded.
E. Cylinders
Cylinders can e plode if damaged. Shielding gas cylinders contain gas under high
pressure. If damaged, a cylinder can e plode. Since gas cylinders are normally part of
the welding process, be sure to treat them carefully.
1. Protect compressed gas cylinders from e cessive heat, mechanical shocks, slag,
open flames, sparks, and arcs.
2. Install cylinders in an upright position by securing to a stationary support or
cylinder rack to prevent falling or tipping.
3. Keep cylinders away from any welding or other electrical circuits.
4. Never weld on a pressurized cylinder - e plosion will result.
5. Use only correct shielding gas cylinders, regulators, hoses and fittings designed for
the specific application; maintain them and associated parts in good condition.
6. Turn face away from valve outlet when opening cylinder valve.
7. Keep protective cap in place over valve e cept when cylinder is in use or connected
for use.
8. Read and follow instructions on compressed gas cylinders, associated equipment
as per applicable Standards.
F. Welding
Welding can cause fire or e plosion. Welding on closed containers, such as tanks,
drums, or pipes, can cause them to blow up. Sparks can fly off from the welding arc.
The flying sparks, hot work-piece (JOB), and hot equipment can cause fires and burns.
Accidental contact of electrode to metal objects can cause sparks, e plosion,
overheating, or fire. Check and be sure the area is safe before doing any welding.
1. Protect yourself and others from flying sparks and hot metal.
2. Do not weld where flying sparks can strike flammable material.
3. Remove all flammables within 35 ft. (10.7 m) of the welding arc. If this is not
possible, tightly cover them with approved covers.
4. Be alert that welding sparks and hot materials from welding can easily go through
small cracks and openings to adjacent areas.
5. Watch for fire, and keep a fire e tinguisher nearby.
6. Do not weld on closed containers such as tanks, drums, or pipes, unless they are
properly prepared.
7. Connect work cable to the work as close to the welding area as practical to prevent
welding current traveling long, possibly unknown paths and causing electric shock
and fire hazards.

6
8. Wear oil-free protective garments such as leather gloves, heavy shirt, cuffless
trousers, high shoes, and a cap.
G. Moving Parts
Moving parts, such as fans, rotors, and belts can cut fingers and hands and catch loose
clothing.
1. Keep all doors, panels, covers, and guards closed and securely in place.
2. Have only qualified people remove guards or covers for maintenance and
troubleshooting as necessary.
H.To reduce magnetic fields in the work place, use the following procedures:
ELECT IC AND MAGNETIC FIELDS : -
May be dangerous. Electric current flowing through any conductor causes localized Electric and Magnetic Fields
(EMF). Welding and cutting current creates
EMF around welding cables and welding machines. Therefore:
1. Keep cables close together by twisting or taping them.
2. Arrange cables to one side and away from the operator.
3. Do not coil or drape cables around the body.
4. Keep welding power source and cables as far away as practical.
5. Connect work clamp to work-piece (JOB) as close to the weld as possible.
6.Welders having pacemakers should consult their physician
before welding. EMF may interfere with some pacemakers.
7. E posure to EMF may have other health effects which are
unknown.
8. Welders should use the following procedures to minimize
e posure to EMF:
A. Route the electrode and work cables together. Secure
them with tape when possible.
B. Never coil the torch or work cable around your body.
C. Do not place your body between the torch and work
cables. Route cables on the same side of your body.
The following definitions apply to DANGE , WA NING,
CAUTION found throughout this manual:
DANGE
Used to call attention to immediate hazards which, if not avoided, will result in immediate,
serious personal injury or loss of life.
WA NING
Used to call attention to potential hazards which could result in personal injury or loss of life.
CAUTION
Used to call attention to hazards which could result in minor personal injury.

7
Section 2
System Components
The Warpp Digital cold wire feeder will accurately feed 0.8 mm,1.0 mm, 1.2 mm, 1.6
mm (0.8 to 1.6 mm) hard and soft wires for mechanized TIG or plasma welding. The
system consists of a D.C. motor-driven four feed roll assembly, spool adapter, and a
wire guide positioner. The positioner incorporates X-Y-Z movements of the wire tip.
The basic components of the wire feeder are:
Wire drive unit: consists of motor, drive housing, wire spool assembly, spool holder
to feed wire.
Wire Feed Accessory : feed rolls, inlet guides, outlet guides, and tips for 0.8 mm,1.0
mm, 1.2 mm, 1.6 mm (0.8 to 1.6 mm) hard and soft wire. Order kits separately for
desired wire size.
Maintenance
Periodically clean the drive rolls of dirt and chips. Occasionally check the wear of
liners, tips and guides.
Always replace fuse with one of equal value 5 amp fast blow. If this equipment dos
not operate properly stops work immediately and investigate the cause of the
malfunction.Maintenance work must be performed by an e perience person, and
electrical work by a trained electrician. Do not permit untrained person to inspect, or
clean, or repair this equipment. Use only recommended replacement parts.
Warning
Maintenance and electrical work must be
performed by e perienced and trained personnel.
Caution
Whenever repairs are required, always turn
all power controls off and disconnect all electrical
cables from power supply.

8
Figure 1: - Digital Cold Wire Feeder.
Section 3
A. Digital cold wire feeder Features: -
1) 4 Seven segment display.
2) Saves all the set parameter in the internal EEP OM.
3) Compact and lightweight design.
4) Equipped with plastic spool holder and cover.

9
B. How to operate the digital key pad.
COLD WI E FEEDE .
DEC
PULSE
SELECT
INT
PULSE
MOTO
SPEED
ON TIME
OFF TIME
Figure 2 :- Digital Key pad with display.
The digital keypad includes two parts: The Display panel and keypad. The display panel provides
the parameter display and shows the operation status of the Digital Cold Wire Feeder and the
keypad provides programming and control interfacing.
Digital key pad Description : -
S.No Digital Key pad Function Key Pressed.
1 Increment Switch can be used to increment speed,
on time and off time.
INT is Increment
switch. ▲
2 Decrement Switch can be used to decrement speed,
on time and off time.
DEC is Decrement
switch. ▼
3 PULSE switch is for turning the pulse mode ON or
OFF.
PULSE mode
ON/OFF switch.
4 SELECT switch is for selecting SPEED setting
mode, ON TIME setting mode and the OFF TIME
setting mode.
SELECT switch.
C. SETTING : -
Display Page 1
Figure 3 :- In screen 1 the display shows the set SPEED.

10
D. SPEED : -
1) Use INT ▲as an increment switch or use DEC ▼as an decrement switch to set the
desired speed from 0.1 meter per minute minimum to 10 meter per minute
maximum.
2) While setting if the speed is set to 0000 the motor will turn stop and it will stop
feeding the filler wire.
3) While setting the SPEED the speed LED will turned ON and the display will show the
set SPEED in screen 1 as shown in the figure 3.
E. PULSE MODE SETTING : -
1) Pulse mode can be turned on by just pressing pulse switch. After the pulse mode has
been turned on the motor will start feeding the filler wire in pulse mode and the pulse
mode LED indicator will also turned on.
2) In pulse mode the motor indicator will start blinking indicating the status of the
motor.
Display Page 2
Figure 4 :- In screen 2 the display shows the set ON TIME in pulse mode.
3) The ON TIME and the OFF TIME of the motor in pulse mode can be set by turning
on the pulse mode and then pressing the SELECT switch to get into the ON TIME
setting mode and use INT as an increment switch or use DEC as an decrement switch to
set the desired ON TIME from 0.1 second minimum to 9 seconds maximum.
4) While setting the ON TIME the ON TIME LED will turned ON and the display will
show the set ON TIME in screen 2 as shown in the figure 4.

11
Display Page 3
Figure 5 :- In screen 3 the display shows the set OFF TIME in pulse mode.
5) To set the OFF TIME once again press SELECT switch to get into the OFF TIME
setting mode and use INT as an increment switch or use DEC as an decrement switch to
set the desired OFF TIME from 0.1 second minimum to 9 seconds maximum.
6) While setting the OFF TIME the OFF TIME LED will turned ON and the display will
show the set OFF TIME in screen 3 as shown in the figure 5.
7) After the setting is Complete if the Digital cold wire feeder machine is turned off all
the parameter’s which were set will be saved in the internal Microcontroller EEP OM
or the memory and will be saved until it has been changed and turned off again.
8) The setting of SPEED , ON TIME and the OFF TIME will only be saved when Digital
cold wire feeder machine is turned off will be saved until it has been changed and turned
off again.
F. Please Note : -
1) The wire from the job connector to the job is compulsory to isolate the machine from
unwanted high frequency (HF) noise.
2) The earthing to the machine through the three pin mains cord supply is compulsory
to avoid shock and to ground unwanted high frequency (HF) noise.
3) The setting of the ON TIME and the OFF TIME can be done only when the pulse
mode has been turned on.

12
Section 4
1) Wire Feeder structure:
Wire Feeder structure, as Figure 6:
Figure 6 :-
(1) Pressing Handle
(2) Wire Pressing oller
(3) Driving Gear
(4) Wire Feed oller
2) Wire Feeder oller and Installation
There is a scale for wire feeding pressure on the Pressing Handle, Different materials and
sizes of the wires are corresponding to different pressures value, refer to Table 1 and
Figure 6 and Figure 7 for detail. The data in the table is only for reference, the actual
pressure regulator
norms must be adjusted based on torch model, cable length, type of welding torch,
welding wire type and size.
• Type 1 for hard wire, such as carbon steel wire, stainless steel wire.
• Type 2 for soft wire, such as Aluminum wire and AL alloys wire, copper wire and
cooper Alloy wire.
• Type 3 for flu cored wire.
Regulating the pressure of feeding rollers with the pressure handle, ensure the wire go
through the guiding tube smoothly, and there should be a bit brake force where the wire
come out from the conductive tip to avoid the wire feed rollers skidding.
Note: Too much pressure will cause wire crushed, and the wire coating will be damaged,
and it will cause feed rollers wear out, and increase the wire feeding resistance

13
Table 1:-
Figure 7: Wire Feeder Operating Instruction.
Section 5
Brake force of wire spool adjustment
Use screw wrench to turn the Brake Force Control Screw (#1) as shown in Figure 8. The brake force
must be appropriate, ensure the wire round the wire spool will not become too loose and prevent the
wire scattering. If the brake force is too large, it will increase the wire-feeding load. Generally the
faster the wire is feeding, the greater is the brake force.

14
Figure 8 :- Filler wire Spool holder.
Section 6
Specifications : -
AC Auxiliary supply: - 230V AC to 250V AC.
Frequency: - 50 Hz
Wire size :- 0.8 mm,1.0 mm,1.2 mm, 1.6 mm (0.8 to 1.6 mm) hard and soft wire.
Wire Type :- 1.Carbon steel, 2. Alternate steel, 3. Aluminum, 4. Stainless steel, 5. Silicon
bronze.
Approx Weight : - 20 Kg .
Dimension : -
Length : - 70 Centimeter.
Breath : - 35 Centimeter.
Height : - 46 Centimeter.
(Specification subject to change as development is a continuous process.)
Appendix A
1. General
The user is responsible for installing and using the arc welding equipment according to
the manufacturer’s instructions. If electromagnetic disturbances are detected, then it shall
be the responsibility of the user of the arc welding equipment to resolve the situation with
the technical assistance of the manufacturer. In some cases this remedial action may be as
simple as earthling the welding circuit, see note. In other cases it could involve
constructing an electromagnetic screen enclosing the welding power source and the word

15
complete with associated input filters. In all cases electromagnetic disturbances shall be
reduced to the point, where they are no longer troublesome.
NOTE: The welding circuit may not be earthed for safety reasons. Changing the
earthling arrangements should only be authorized by a person who is competent to
assess whether the changes will increase the risk of injury.
2. Assessment of area
Before installing arc welding equipment the user shall make an assessment of potential
electromagnetic problems in the surrounding area. The following shall be taken into
account:
1) Other supply cables, control cables, signaling and telephone cables, above, below and
adjacent to the arc welding equipment;
2) Radio and television transmitters and receivers;
3) Computer and other control equipment;
4) Safety critical equipment, for e ample guarding of industrial equipment;
5) The health of the people around, for e ample the use of pacemakers and hearing aids;
6) Equipment used for calibration or measurement;
7) The immunity of other equipment in the environment is compatible. The user shall
ensure that other equipment being used in the environment is compatible. This may
require additional protection measures;
8) The time of day that welding or other activities are to be carried out.
3. Methods of reducing emissions
1) Public supply system
Arc welding equipment should be connected to the public supply system according to the
manufacturer’s recommendations. If interference occurs, it may be necessary to take
additional precautions such as filtering of the public supply system. Consideration should
be given to shielding the supply cable of permanently installed arc welding equipment, in
metallic conduit or equivalent. Shielding should be electrically continuous its length. The
shielding should be connected to the welding power source so that good electrical contact
is maintained between the conduit and the welding power source enclosure.
2) Maintenance of the arc welding equipment
The arc welding equipment should be routinely maintained according to the
manufacturer’s recommendations. All access and service doors and covers should be
closed and properly fastened when the arc welding equipment is in operation. The arc
welding equipment should not be modified in any way, e cept for those changes and
adjustments covered in the manufacturer’s instructions. In particular, the spark gaps of arc
striking and stabilizing devices should be adjusted and maintained according to the
manufacturer’s recommendations.
3) Welding cables
The welding cables should be kept as short as possible and should be positioned close
together, running at or close to the floor level.
4) Equipotent bonding
Bonding of all metallic components in the welding installation and adjacent to it should
be considered. However, metallic components bonded to the word piece will increase the
risk that the operator could receive an electric shock by touching these metallic

16
components and the electrode at the same time. The operator should be insulated from all
such bonded metallic components.
5) Earthling of the work piece
Where the work piece is nor bonded to earth for electrical safety, nor connected to earth
because of its size and position, for e ample ships hull or building steel work, a
connection bonding the work piece to earth may reduce emissions in some, but not all
instances. Care should be taken to prevent the earthling of the work piece increasing the
risk of injury to users, or damage to other electrical equipment. Where necessary, the
connection of the work piece to earth should be made by a direct connection to the work
piece, but in some countries where direct connection is not permitted, the bonding should
be achieved by suitable capacitance, selected according to national regulations.
6) Screening and shielding
Selective screening and shielding of other cables and equipment in the surrounding area
may alleviate problems of interference. Screening of the entire welding installation may
be considered for special applications.
Thank you for selecting WA PP brand Digital Cold Wire Feeder.
Head Office : -
Warpp Engineers Pvt Ltd.
Manufacturers of Welding And elated Plasma Products.
B-1005, 10th Floor, Western Edge 2, Near Metro Mall,
Off western Express Highway, Borivali (East).
Pin code 400066.
TEL: 022-28542272 / 73 / 74.
E mail: sales@warpp.co.in Website: www.warpp.co.in
Table of contents
Other WARPP Welding System manuals
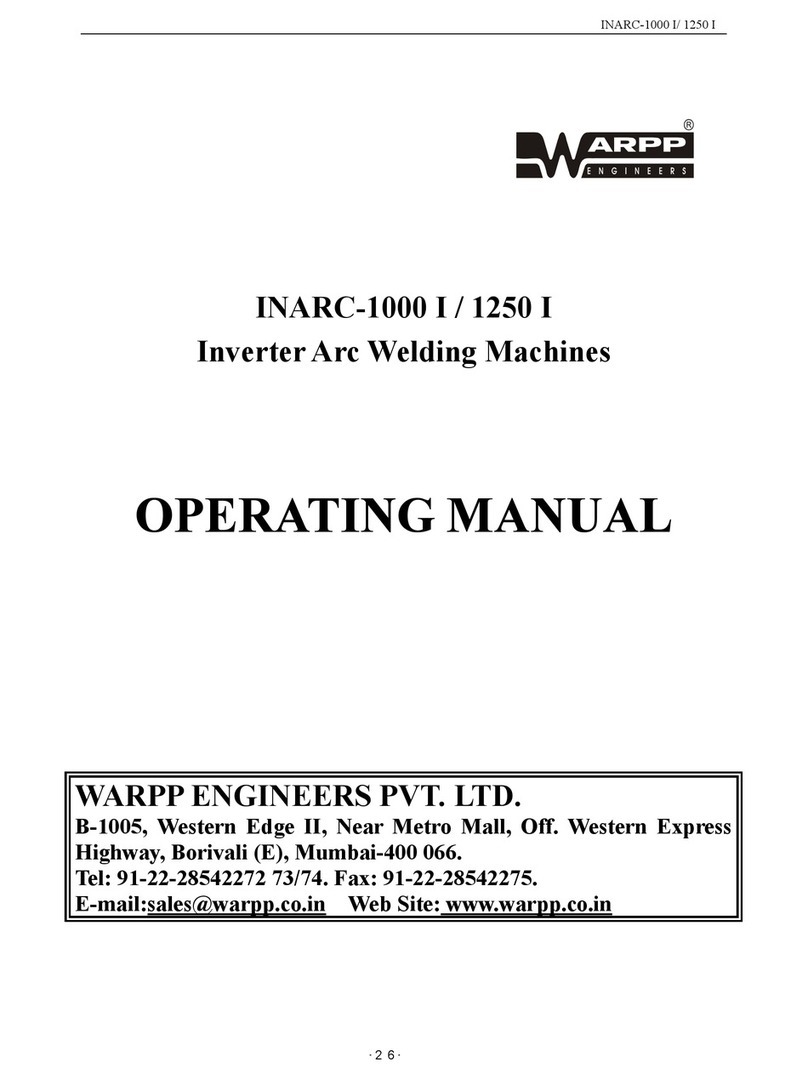
WARPP
WARPP INARC-1000 I User manual

WARPP
WARPP INTIG-315 AC/DC User manual
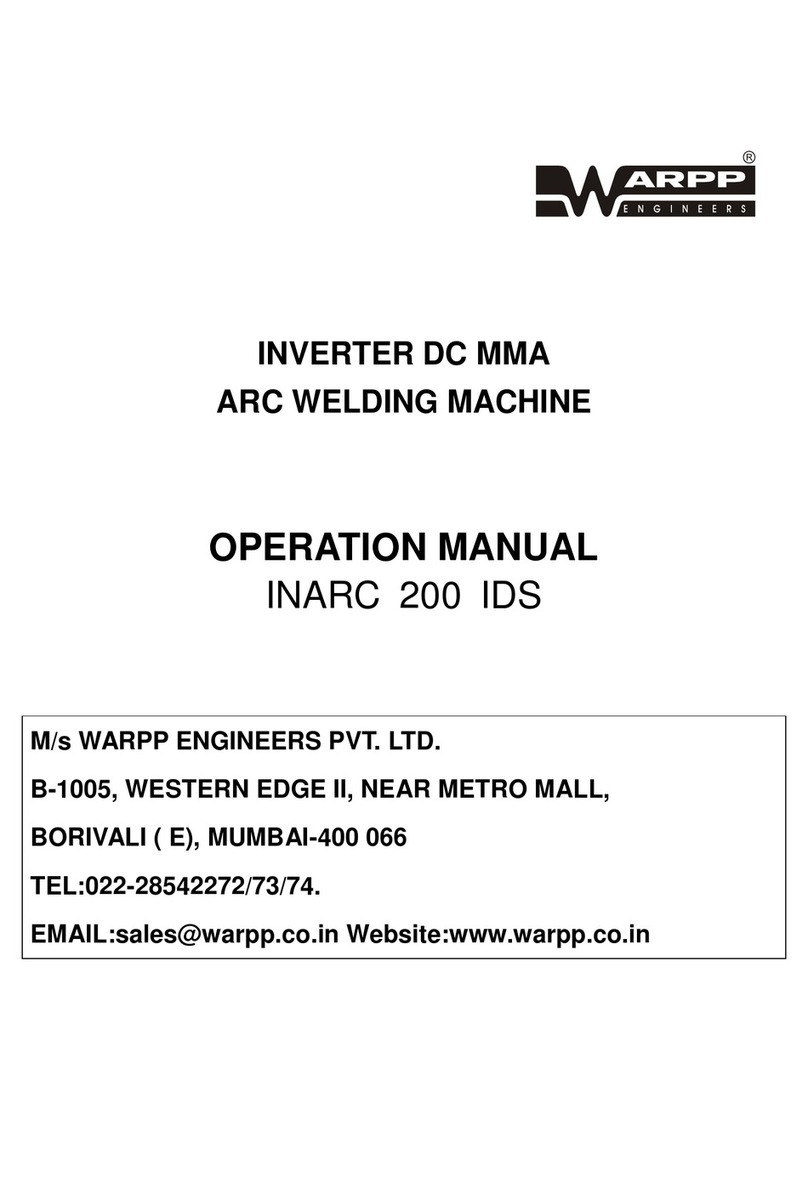
WARPP
WARPP INARC 200 IDS User manual
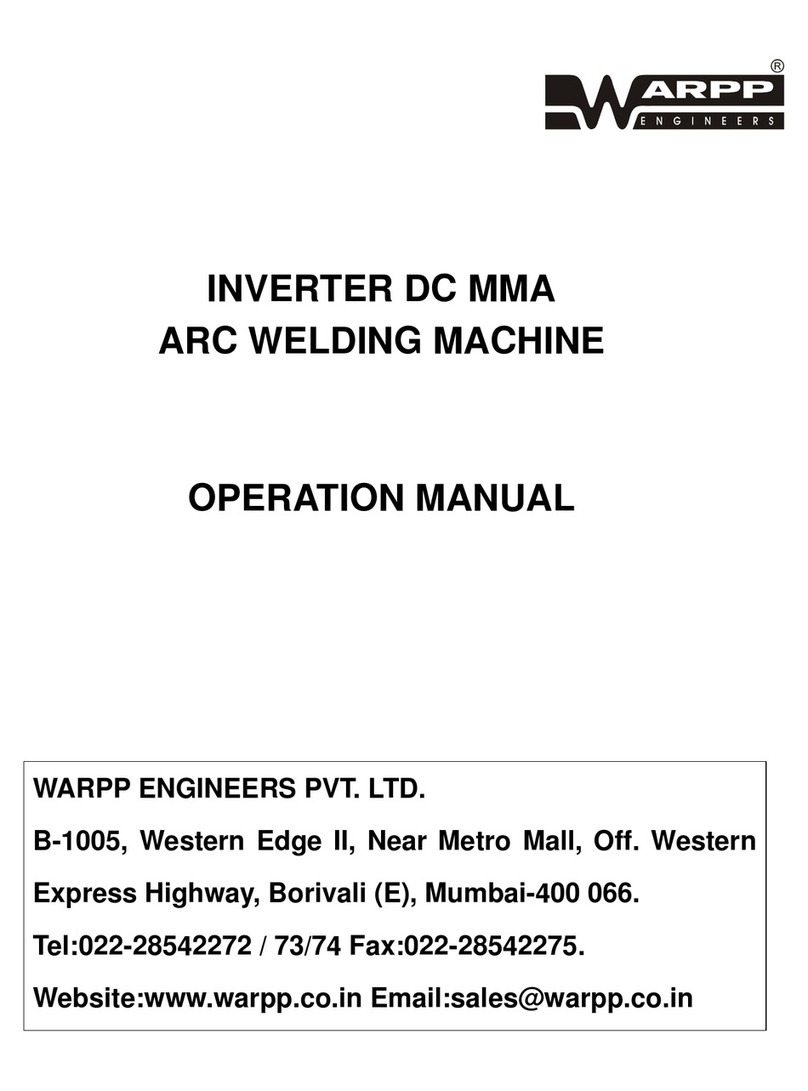
WARPP
WARPP INARC IH SERIES User manual
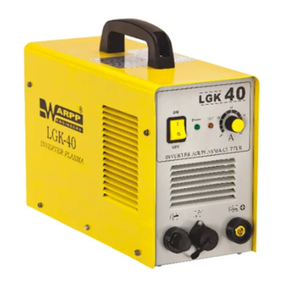
WARPP
WARPP LGK-40 User manual
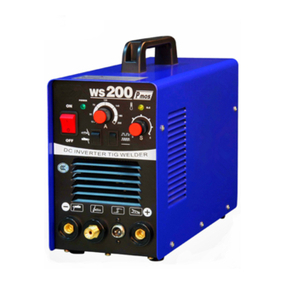
WARPP
WARPP WS-200 User manual
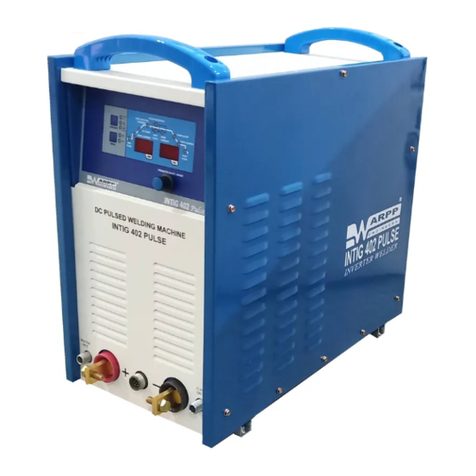
WARPP
WARPP INTIG 402 PULSE User manual
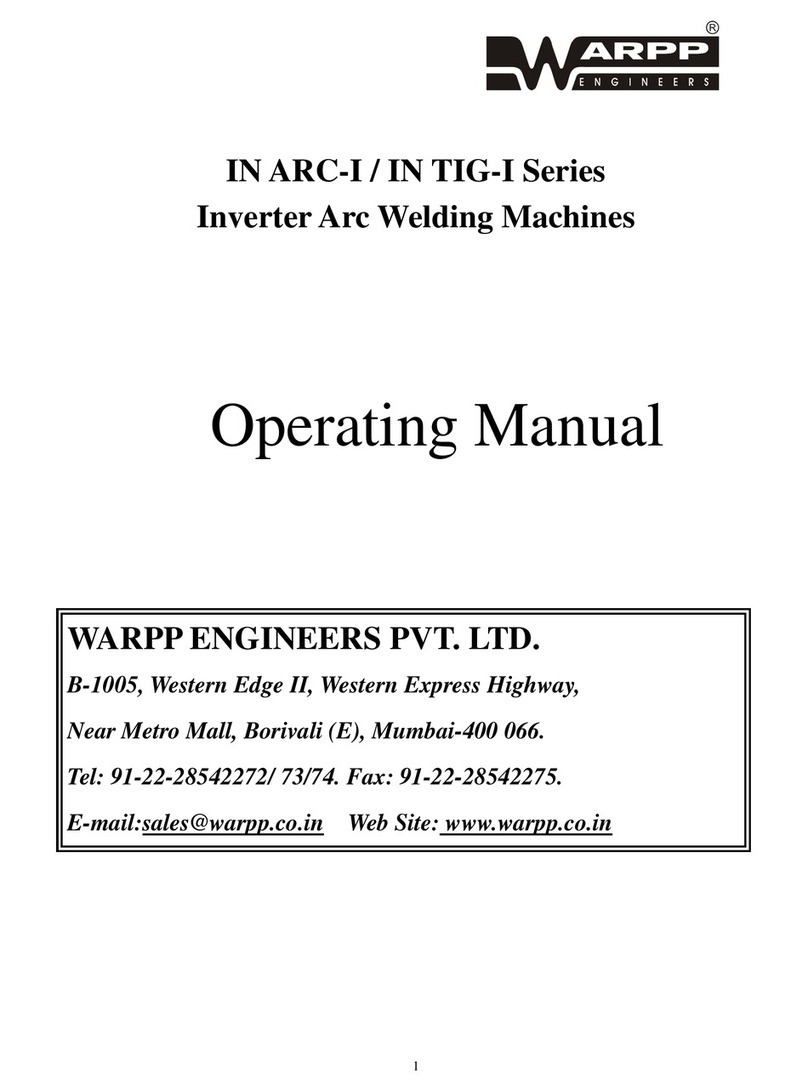
WARPP
WARPP IN ARC-I series User manual
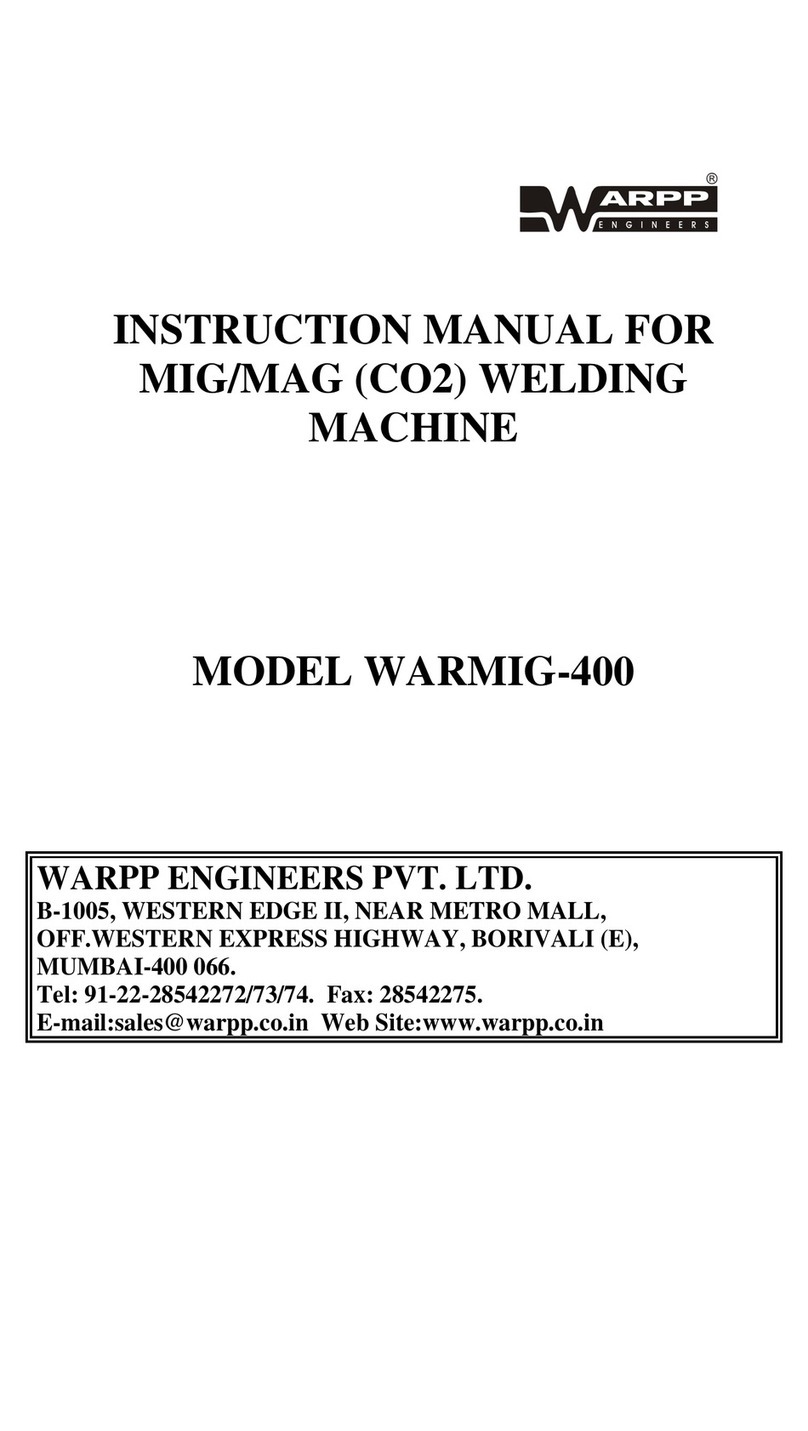
WARPP
WARPP WARMIG-400 User manual
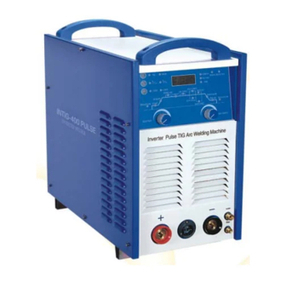
WARPP
WARPP INTIG-PULSE series User manual

WARPP
WARPP WTR-600 User manual
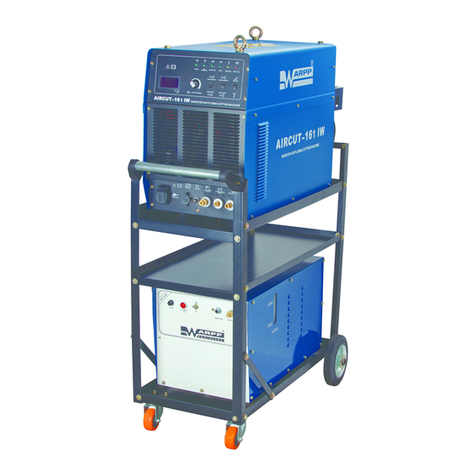
WARPP
WARPP AIRCUT 100I User manual

WARPP
WARPP WTR-400 User manual

WARPP
WARPP INTIG 200 IDS User manual
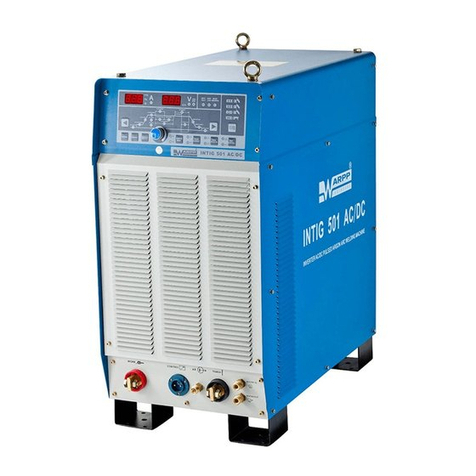
WARPP
WARPP INTIG 316 AC/DC User manual
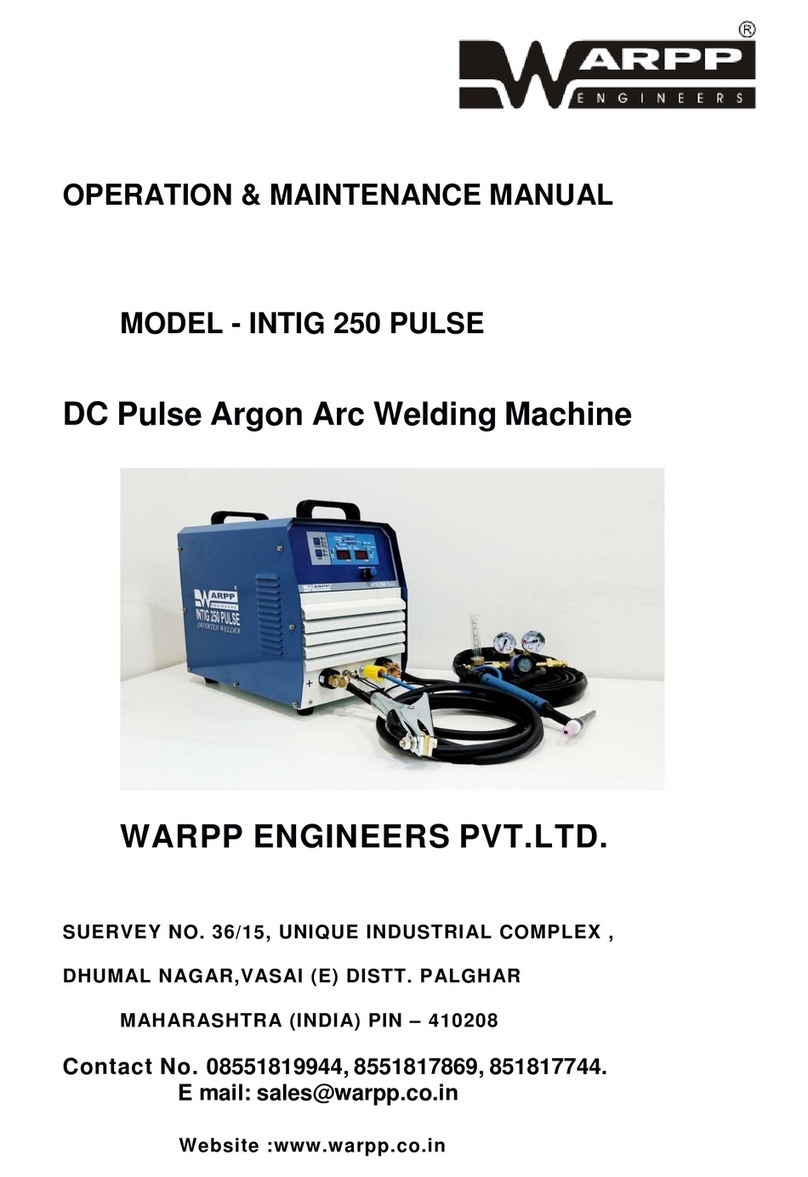
WARPP
WARPP INTIG 250 PULSE Manual
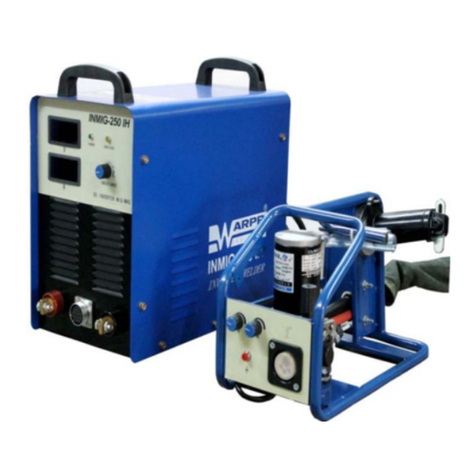
WARPP
WARPP INMIG 250 IH User manual
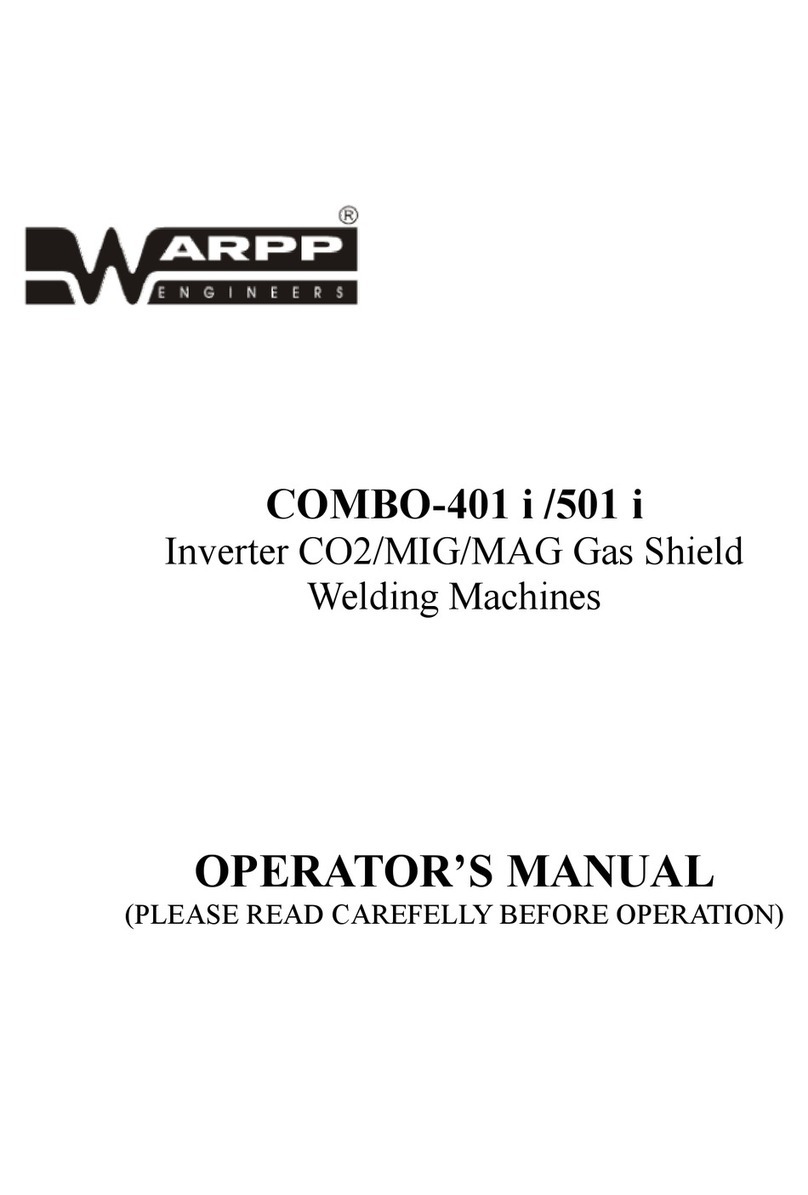
WARPP
WARPP COMBO-401 i User manual
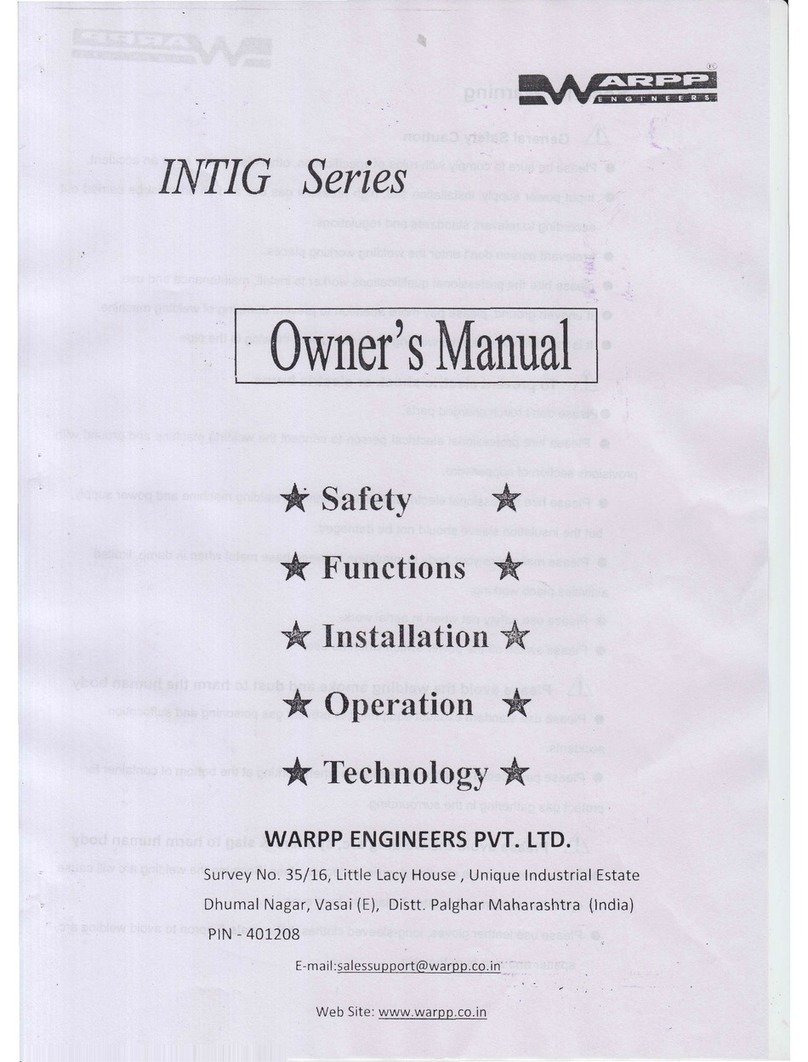
WARPP
WARPP INTIG-200IDS User manual
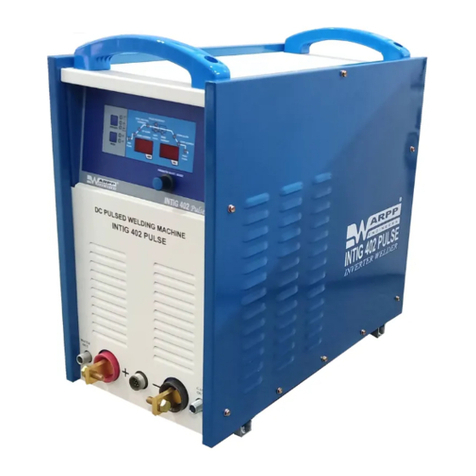
WARPP
WARPP INTIG 402 PULSE User manual