WAYCOM MXAX SERIES User manual

INSTALLATION GUIDE
Magnetic Scale Series MXAX and MXAZ
For more information please see the data sheet at
www.waycon.biz/products/digital-rulers/
FIRST STEPS
WayCon Positionsmesstechnik GmbH would like to thank you for the trust you have placed in us and
our products. This manual will make you familiar with the installation and operation of our magnetic
scale sensors. Please read this manual carefully before initial operation!
Unpacking and checking:
Carefully lift the device out of the box by grabbing the housing. After unpacking the device, check
it for any visible damage as a result of rough handling during the shipment. Check the delivery for
completeness.
If necessary consult the transportation company, or contact WayCon directly for further assistance.
SAFETY
• Installation and maintenance have to be carried out by qualied personnel only.
• During installation and maintenance make sure that the machine is not running and the power
supply is OFF.
• The encoder must be used only for the purpose appropriate to its design. The use for purposes
other than those for which it has been designed could result in serious personal and/or environment
damages.
• High current, voltage and moving mechanical parts can cause serious or fatal injury.
• Warning! Do not use in explosive or ammable areas.
• Failure to comply with these precautions or with specic warnings elsewhere in this manual violates
safety standards of design, manufacture and intended use of the equipment.
• WayCon assumes no liability for the customer‘s failure to comply with these requirements.
MECHANICAL SAFETY
• For the installation of the device strictly follow the information in the section “Mounting the sensor”.
• Mechanical installation has to be carried out only when the machine is switched o.
• Do not disassemble the device, do not tool the device.
• Protect the unit against acid solutions or chemicals that may damage it.
• Sensitive electronic equipment: handle with care. Do not shock or drop the device.
• During installation we suggest protecting the device against pollution, like chips, lings or liquids.
Should this be impossible, please make sure that adequate cleaning measures (as for instance
brushes, scrapers, jets of compressed air, etc.) are in place in order to prevent the sensor and the
magnetic scale from jamming.

MOUNTING THE SENSOR
• Fix the sensor by means of two M4x25 mm cylinder head screws.
• Always comply with the mounting tolerances indicated in the gures below.
• Use the WBAX type magnetic scale for the MXAX reading head or the WBAZ for the MXAZ reading
head (refer to specic technical instructions). The arrow indicates the standard counting direction
(count up information).
• Recommended minimum bend radius of the cable: R ≥ 25 mm.
Overall dimensions
Mounting direction
Mounting
direction
M4x25 mm cylinder head
screws (2 x)
Recommended mounting tolerances
Distance from the scale
Tilt
< 1°
Distance (D) between the centre of the screw
xing holes and the magnetic tape
without cover strip with cover strip
31.7 mm to 33.2 mm 31.3 mm to 32.8 mm
Yaw
< 3°
Lateral deviation
1 mm
Roll
< 3°

ELECTRICAL SAFETY
• Turn OFF the power supply before connecting the device.
• Unconnected wires must be cut at dierent lengths and insulated singularly.
• Do not stretch the cable. Do not pull or carry by cable. Do not use the cable as a handle.
• In compliance with 2004/108/EC norm on electromagnetic compatibility, following precautions
must be taken:
• Before handling and installing the equipment, discharge electrostatic charges from your body
and tools which may come in touch with the device.
• Power supply must be stabilized without electronic noise. Install EMC lters on device power
supply if needed.
• Always use shielded cables (twisted pair cables whenever possible) and avoid cables longer
than necessary.
• Avoid placing the signal cable near high voltage power cables.
• Mount the device as far as possible from any capacitive or inductive noise source. Shield the
device from electronic noise source if needed.
• To guarantee a correct working of the device, avoid using strong magnets on or near by the
unit.
• Minimize electronic noise by connecting the cable shield and/or the connector housing and/or
the sensor to ground. Make sure that ground is not aected by electronic noise.
ELECTRICAL CONNECTION
Signals 0...20 mA Signals 0...10 V cable output connector output
0 VDC Power Supply BK 1
13...30 VDC RD 2
0 VDC analog YE 3
START BU 4
+I out +V out GN 5
STOP OG 6
not connected WH 7
FAULT not connected GY 8
Shielding Shield Case
Cable specications
Type HI-FLEX M8
Wires 2 x 0.22 mm2 + 6 x 0.14 mm2
Shield Tinned copper braid
External Ø 5.3 up to 5.6 mm
Impedance <90 Ω/Km (0.22 mm2), <148 Ω/Km (0.14 mm2)
Min. bend radius ≥ 25 mm
12
5
4
3 7
6
8
connector output,
M12, male

ELECTRICAL CONNECTION
Connection of the shield
For signal transmission always use shielded cables. The cable shielding must be connected properly
to the metal ring nut of the connector in order to ensure a good earthing through the frame of the
device.
Ground connection
Minimize electronic noise by connecting the shield and/or the connector housing and/or the sensor
to ground. Make sure that ground is not aected by electronic noise. The connection point to ground
can be situated both on the device side and/or on user’s side. The best solution to minimize the inter-
ference must be carried out by the user.
SIGNAL DESCRIPTION
0 VDC
0 VDC Power Supply and 0 VDC analog are internally connected.
START input
START input is used to execute the TEACH-IN procedure. It is active at HIGH logic level (voltage greater
than 10 V must be applied). For any further information on using the START and STOP inputs please
refer to the “TEACH-IN procedure” section.
+I out current analog output
+I out provides the current analog signal. AI1 output range is: min. quote = 4 mA, max. quote = 20 mA.
The increment at each step is as follows: 10-bit DAC 4...20 mA: 16000/1024 = 15.625 μA
+V out voltage analog output
+V out provides the voltage analog signal. AV2 output range is: min. quote = 0 V, max. quote = 10 V
The increment at each step is as follows: 10-bit DAC 0...10 V: 10000/1024 = 9.765 mV
STOP input
STOP input is used to execute the TEACH-IN procedure. It is active at HIGH logic level (voltage greater
than 10 V must be applied). For any further information on using the START and STOP inputs please
refer to the “TEACH-IN procedure” section.
Fault output
This Fault output is only available for AI1 current analog output. It is intended to show an error
condition such as a circuit break.
Please pay attention to the value of the R2 resistor.
Imax = 50 mA R1 = 47 Ω R2 = (VDC/I) - R1
No encoder error = transistor ON (conducting)
Encoder error = transistor OFF (open)

TEACH-IN PROCEDURE
The TEACH-IN function allows to set a start and end position by means of two external signals. The
analog signal will automatically adapted to the teached range.
The set output range (the overall information
to be output) is defined over the travel of
the specific application and is comprised
between the ends of the axis: the origin of
the axis, i.e. the point where you activate
either the START or the STOP input, and
the end of the axis, i.e. the point where you
activate the other input. For the positions
beyond the travel limits the current / voltage
signal level will be kept at the minimum /
maximum value of the selected range.
With ascending ramp, before the initial
position of the travel the encoder will
provide the minimum current / voltage
signal level of the output range (4
mA for AI1; 0 V for AV2). After the last
position of the travel the encoder will
provide the maximum current / voltage
signal level of the output range (20 mA
for AI1; 10 V for AV2).
On the contrary, with descending
ramp, before the initial position of the
travel the encoder will provide the
maximum current / voltage signal level
of the output range (20 mA for AI1; 10
V for AV2). After the last position of
the travel the encoder will provide the
minimum current / voltage signal level
of the output range (4 mA for AI1; 0 V
for AV2).
WARNING: It is mandatory to activate
the START input first and then the STOP
input.
mA / V
STOP
End position
START
Start position
Adjustable range
START STOP
Axis travel
Analog signal
value
Max.
value
Min.
value
STARTSTOP
Axis travel
Analog signal
value
Max.
value
Min.
value

TEACH-IN PROCEDURE
To programme the encoder using the TEACH-IN procedure act as described below. The following steps
dene a ramp with increasing output values:
• Move the axis to the origin of the physical travel of the application you want to measure and control.
In other words, move it to the point where the travel starts.
• Switch the START input to HIGH logic level +VDC for 3 seconds at least; the LED in the sensor switches
o. This way you set the point where the encoder will provide the minimum current / voltage signal
level available in the output range (4 mA for AI1; 0 V for AV2).
• Now move the axis to the end of the physical travel of the application you want to measure and
control. In other words, move it to the point where the travel stops.
• Switch the STOP input to HIGH logic level +VDC for 3 seconds at least; the LED in the sensor switches
on again. This way you set the point where the encoder will provide the maximum current / voltage
signal level available in the output range (20 mA for AI1; 10 V for AV2).
For a descending ramp (as shown in the gure on the previous page) activate the START input and
then move backward the axis in reverse of the standard direction before activating the STOP input (in
other words you activate the START input when the axis is in the nal position of its travel and then
activate the STOP input when the axis is in the rst position of its travel). The maximum value of the
output range precedes the initial point of the ramp (i.e. the beginning of the axis travel). The minimum
value of the output range follows the nal point of the ramp (i.e. the end limit of the axis travel).
WARNING: If you set a wrong point for the initial position of the travel by activating the START input,
you have to turn o and then on again the power supply to reset the sensor. Then repeat the procedure
from the rst step.
Otherwise, if you set a wrong point for the nal position of the travel by activating the STOP input (this
means that you have already set the initial position of the travel by activating the START input), you
have to switch the STOP input to 0 VDC. Then move the axis to the right nal position and activate the
STOP input.
RECOMMENDED CIRCUIT
Current output
Voltage output

MAINTENANCE
The magnetic measurement system does not need any particular maintenance. Please always consider
it is a sensitive electronic equipment and therefore it must be handled with care. From time to time we
recommend the following operations:
• Periodically check the proper assembly of the sensor system and make sure that there are no loose
screws, tighten them if necessary.
• Check the mounting tolerances between the sensor and the magnetic scale all along the measuring
length. Wear of the machine may increase the tolerances.
• The surface of the magnetic scale should be cleaned periodically by using a soft cloth to remove
dust, chips, moisture etc.
TROUBLESHOOTING
The following list shows some typical faults that may occur during installation and operation of the
magnetic measurement system.
Fault: The system does not work (no pulse output).
Possible cause:
• The tape or the sensor has been mounted incorrectly (the active part of the tape does not match the
active side of the sensor).
• A magnetic part or a protection surface is interposed between the sensor and the tape. Only non-
magnetic materials are allowed between the sensor and the tape.
• Installation does not comply with the tolerance gap between the sensor and the scale indicated
in this guide. The sensor hits the surface of the scale or is too far from it. Check whether the sensor
sensitive part is damaged.
• The sensor has been damaged by a short circuit or a wrong connection.
Fault: The measured values are either inaccurate or not provided in the whole length.
Possible cause:
• The mounting tolerances between the sensor and the tape are not met all along the whole
measurement length.
• The connection cable is located next to a high voltage cable. or the shielding is not connected
correctly. Check the earthing point.
• A section of the magnetic scale has been damaged mechanically or magnetically along the
measuring length.
• The measuring error is caused by torsion of the machine structure. Check parallelism and symmetry
of machine movement.

DIAGNOSTIC LED
Diagnostic LED
ON The sensor is running properly, there are no active errors
Blinking at high frequency
(100 ms ON / 100 ms OFF) Machine data parameters error
Blinking slowly
(500 ms ON / 500 ms OFF) Flash memory error
Blinking very slowly
(1 s ON / 1 s OFF) Error of the sensors while reading the magnetic tape
Single ash
(200 ms ON / 1 s OFF)
The sensor is installed too far from the magnetic tape, the installation does not
comply with the tolerance values between the sensor and the tape
Double ash
(200 ms ON twice / 1 s OFF) Several errors are active in the same time
Note: When you execute the TEACH-IN, as soon as you activate the START input the LED switches o. As soon as you
activate the STOP input it switches on again.
DECLARATION OF EC-CONFORMITY
WayCon Positionsmesstechnik GmbH
Mehlbeerenstrasse 4
82024 Taufkirchen / Germany
This is to certify that the products
Classication Magnetic scales
Series MXAX and MXAZ
fulll the current request of the following EC-directives:
EMV-directive 2014/30/EU
2011/65/EU
applied harmonized standards:
CEI EN 61000-6-4, CEI EN 61000-6-2
The declaration of conformity loses its validity if the product is misused or modied without proper
authorisation.
Taufkirchen, 02.10.2017 Andreas Täger
CEO
This manual suits for next models
1
Table of contents
Popular Scale manuals by other brands
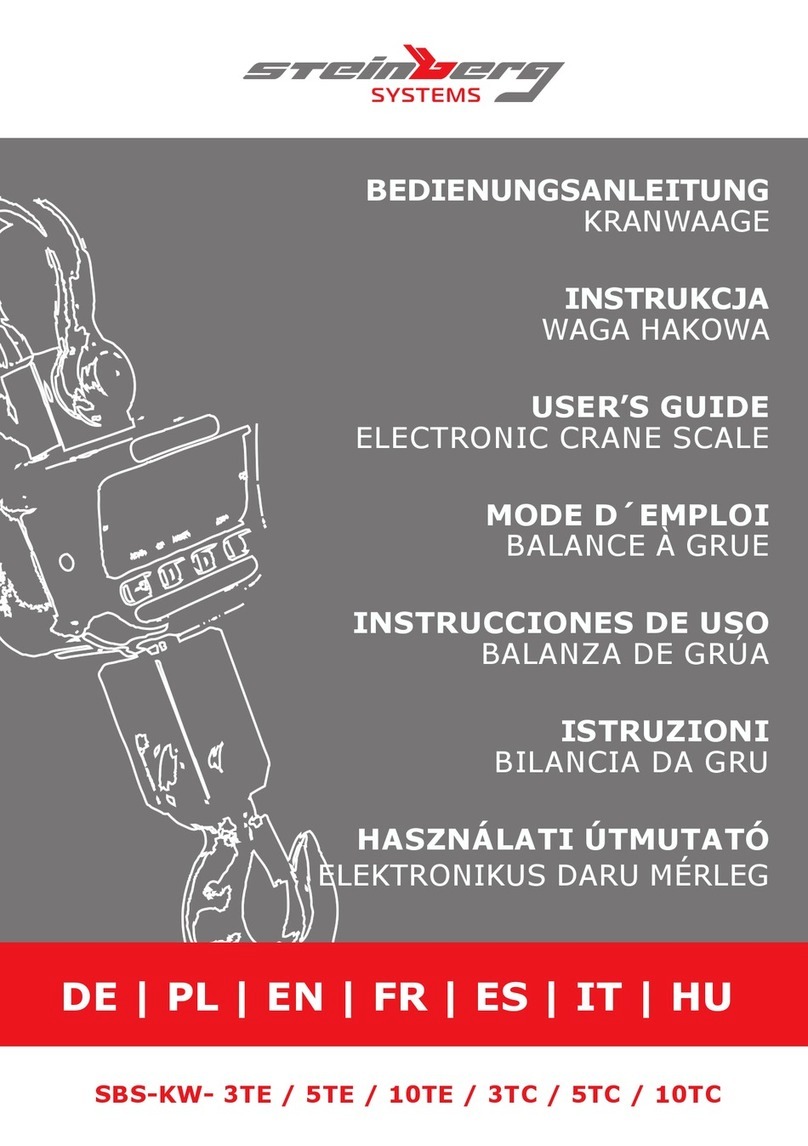
Steinberg Systems
Steinberg Systems SBS-KW-3TE user guide

Optima Home Scales
Optima Home Scales LUNA user manual

Steinberg
Steinberg SBS-KW-1000/10O user guide
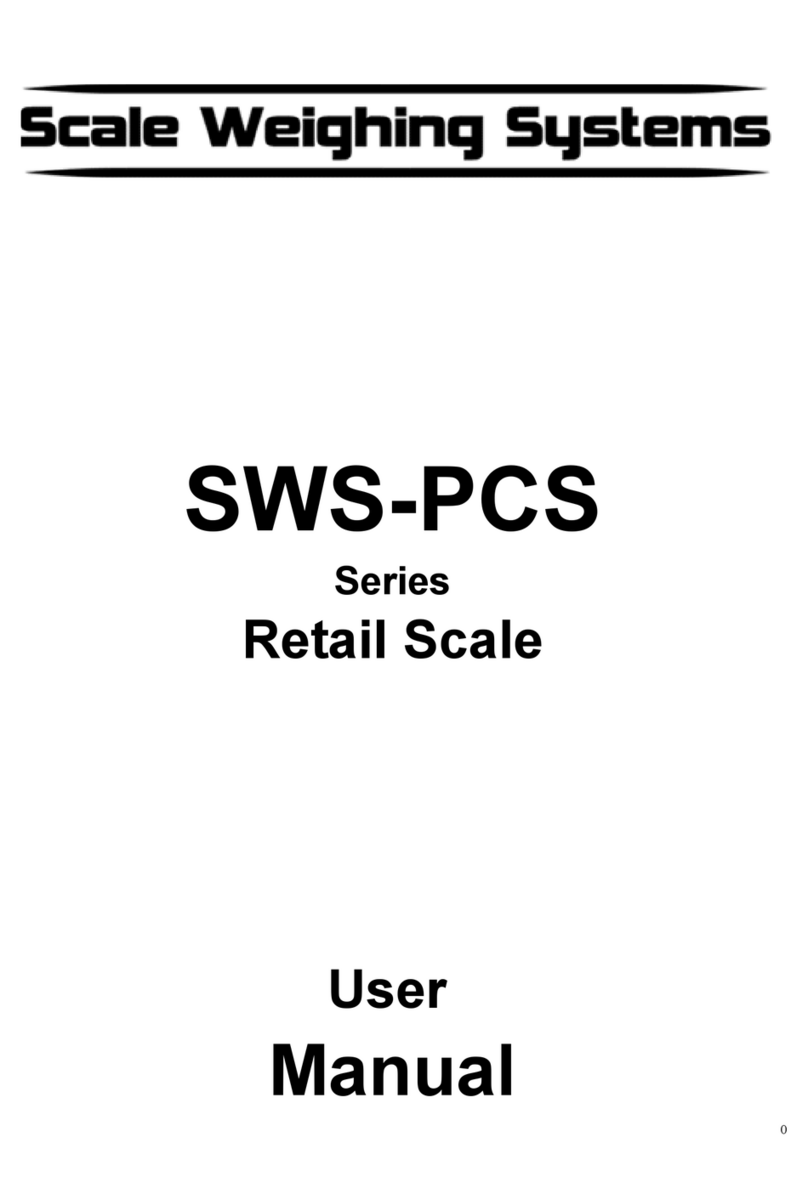
Scale Weighing Systems
Scale Weighing Systems SWS-PCS-60 user manual
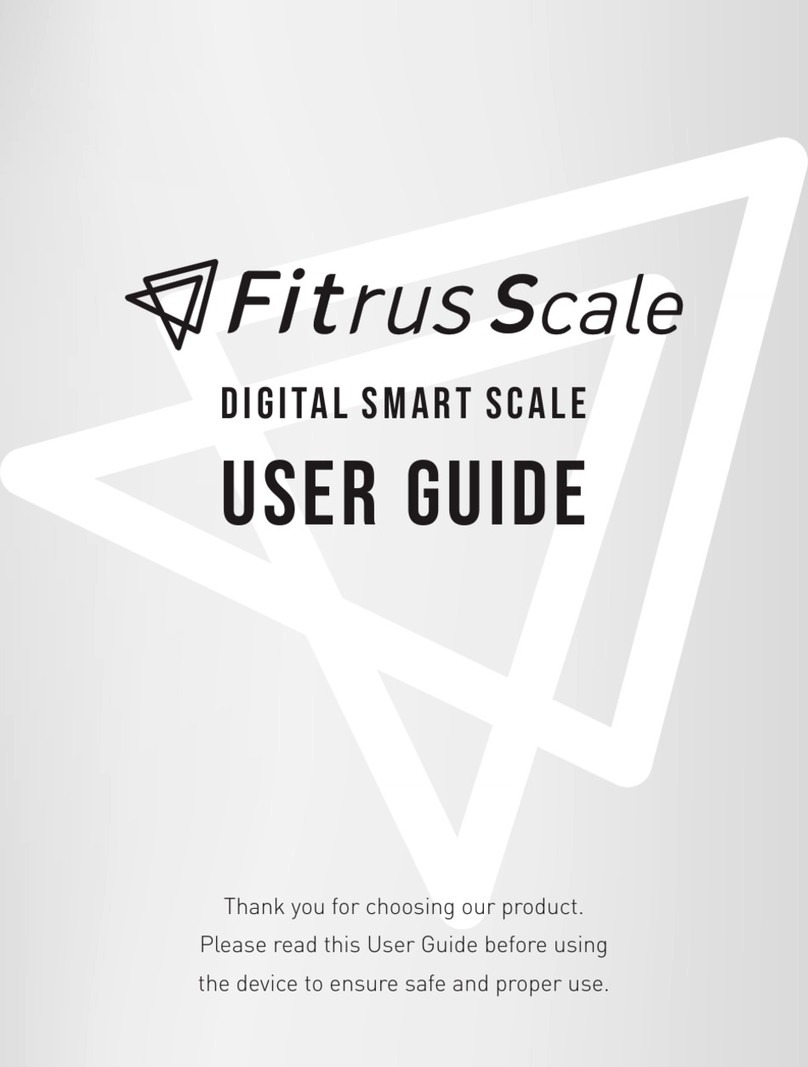
Fitrus Scale
Fitrus Scale FRS-W10 user guide

Adam Equipment
Adam Equipment HIGHLAND SERIES user manual