Weidmüller UC20-SL2000-EC-CAN User manual

UC20-WL2000-AC 1334950000
UC20-WL2000-IOT 1334990000
UC20-SL2000-EC 2674520000
UC20-SL2000-EC-CAN 2674620000
Controllers u-control
Manual (Original)
Letʼs connect.

22604080000/03/08.2020Manual u-control
Manufacturer
Weidmüller Interface GmbH & Co. KG
Klingenbergstraße 26
32758 Detmold, Germany
T +49 5231 14-0
F +49 5231 14-292083
www.weidmueller.com
Document No. 2604080000
Revision 03/August 2020
Content
1 About this documentation 3
1.1 Symbols and notes 3
1.2 Complete documentation 3
1.3 Hardware versions described 4
2 Safety 5
2.1 General safety notice 5
2.2 Intended use 6
2.3 Use in a potentially explosive atmosphere 6
2.4 Legal notice 7
3 System overview 9
3.1 General description of the controller 11
3.2 General technical data 12
3.3 Connectable u-remote I/O modules 13
3.4 Connector PG 1.5mm 13
3.5 Mechanical xing elements 13
3.6 Type plate 14
3.7 Battery 14
3.8 Memory card 14
4 Conguration 15
4.1 Order and arrangement of the modules 15
4.2 Orientation of the station 15
4.3 Installation distances 16
4.4 Use in a potentially explosive atmosphere 17
4.5 “PUSH IN” system cabling 17
4.6 Current demand and power supply 18
4.7 Example calculation for the power supply 19
4.8 Calculation of power loss 21
4.9 Feedback energy in DO modules 21
5 Detail description of controllers 23
5.1 UC20-WL2000-AC 23
5.2 UC20-WL2000-IOT 27
5.3 UC20-SL2000-EC 31
5.4 UC20-SL2000-EC-CAN 35
6 Installation 39
6.1 Preparations for assembly 39
6.2 Assembling the u-control station 42
6.3 Wiring 44
6.4 Inserting the battery 45
6.5 Inserting the SD card 46
6.6 Insulation test 46
7 Earthing and shielding 47
7.1 Earthing of shielded cables 48
7.2 Potential ratios 52
7.3 Electromagnetic compatibility (EMC) 54
7.4 Shielding of cables 56
8 Commissioning using u-create web 59
8.1 Requirements 59
8.2 Starting u-create web 59
8.3 Accessing u-create online help 60
8.4 Updating the rmware 60
8.5 Resetting the controller to default settings 61
8.6 Resetting the control to default settings without password 61
9 Commissioning using u-create studio 63
9.1 Requirements 63
9.2 Installing the rmware on the controller 63
9.3 Starting „DevAdmin“ 63
10 Replacing components 65
10.1 Removing/replacing the plug-in unit 65
10.2 Removing/replacing connectors 66
10.3 Removing/replacing cables 67
10.4 Replacing the battery 68
10.5 Replacing the SD card 69
11 Disassembly and disposal 71
11.1 Disassembling the u-remote station 71
11.2 Disposing of the u-control station 71
12 LED indicators and troubleshooting 73
13 Accessories and replacement parts 77
13.1 Accessories 77
13.2 Replacement parts 78
ANNEX A-1

1 Aboutthisdocumentation | Symbols and notes
3Manual u-control2604080000/03/08.2020
1 About this documentation
1.1 Symbols and notes
The safety notices in this documentation are designed
according to the severity of the danger.
DANGER
Imminent risk to life!
Notes with the signal word “Danger” warn
you of situations which will result in serious
injury or death if you do not follow the in-
structions given in this manual.
WARNING
Possible danger to life!
Notes with the signal word “Warning” warn
you of situations which may result in serious
injury or death if you do not follow the in-
structions given in this manual.
CAUTION
Risk of injury!
Notes with the signal word “Caution” warn
you of situations which may result in injury
if you do not follow the instructions given in
this manual.
ATTENTION
Material damage!
Notes with the signal word “Attention” warn you of hazards
which may result in material damage.
Text next to this arrow are notes which are not rel-
evant to safety, but provide important information
about proper and effective work procedures.
The situation-dependent safety notices may contain the fol-
lowing warning symbols:
Symbol Meaning
Warning against hazardous electrical
voltage
Warning against explosive atmospheres
Warning against electrostatically charged
components
Warning against automatic startups
Instruction: observe the documentation
▶All instructions can be identified by the black triangle
next to the text.
–Lists are marked with a tick.
1.2 Complete documentation
–When using UC20-SL2000 controllers, please
also observe the u-create studio system
manual.
–When using I/O modules, please also observe
the Remote-I/O-System u-remote Manual.
–When using safe I/O modules or safe feed-in
modules, please also observe the Modules
for Functional Safety Manual.
–The u-create web and u-create studio enginee-
ring tools contain an integrated online help.
All documents are available to download from the
Weidmüller website.

42604080000/03/08.2020Manual u-control
1.3 Hardware versions described
The present manual describes the following hardware ver-
sions of the controllers:
Order No. Controller Hardware version
1334950000 UC20-WL2000-AC 01.22.00
1334990000 UC20-WL2000-IOT 01.22.00
2674520000 UC20-SL2000-EC 01.22.00
2674620000 UC20-SL2000-EC-CAN 01.22.00

2 Safety | General safety notice
5Manual u-control2604080000/03/08.2020
2 Safety
This section includes general safety instructions for handling
the u-control system. Specic warning notices for specic
tasks and situations are given at the appropriate places in
the documentation. Failure to observe the safety and warn-
ing notices can result in damage to persons and material.
–When using I/O modules modules, please
also observe the Remote-I/O-System
u-remote Manual.
–When using safe I/O modules or safe feed-
in modules, please also observe the
Modules for Functional Safety Manual.
All manuals are available to download from the
Weidmüller website.
2.1 General safety notice
Work on the u-control products may only be performed by
qualied electricians with the support of trained persons.
As a result of their professional training and experience, an
electrician is qualied to perform the necessary work and
identify any potential risks.
Before any work is carried out on the products (installa-
tion, maintenance, retrotting), the power supply must be
switched off and secured against being switched on again.
Work may be carried out with safety extra-low voltage (SELV/
PELV). When working during continued operations, the
emergency stop mechanisms must not be made ineffective.
The u-control products do not comprehend any components
or parts that can be maintained by the operator. If a malfunc-
tion on a u-control product cannot be xed after following
the recommended measures (see Chapter 11), the product
in question must be sent back to Weidmüller. Weidmüller
does not assume any liability if the product has been tam-
pered with!
Electrostatic discharge
u-remote products can be damaged or destroyed by electro-
static discharge. When handling the products, the neces-
sary safety measures against electrostatic discharge (ESD)
according to IEC61340-5-1 and IEC61340-5-2 must be
observed.
All devices are supplied in ESD-protected packaging. The
packing and unpacking as well as the installation and di-
sassembly of a device may only be carried out by qualied
personnel and in accordance with the ESD information.
Open equipment
u-remote products are open equipment that may only be in-
stalled and operated in lockable housings, cabinets or electri-
cal operations rooms. Only trained and authorised personnel
may access the equipment.
For applications requiring functional safety, the surrounding
housing must meet at least IP54. The standards and guide-
lines applicable for the assembly of switch cabinets and the
arrangement of data and supply lines must be complied
with.
Fuse protection
The operator must set up the equipment so that it is pro-
tected against overloading. The 24VDC power supply units
used must fulll the SELV category, no matter whether they
supply the system or feed-in modules. The output voltage of
the feed-in power supply has to fulll overvoltage category1
according to IEC61010. When connecting to outer current
circuits the respective overload category has to be regarded
for each single module of the u-control station (see technical
data).
The main switch, the switches of the subsequent circuits, the
cable cross sections and the fuse protection have to be con-
gured according to IEC61010. The current demand must
be caluclated separately for each single u-control station as
described in section 4.6.
In the case of modules without fused sensor/actuator power
supplies, all lines to the connected sensors/actuators must
be fused corresponding to their conductor cross-section (as
per DIN VDE0298 Part 4).
To meet UL-specications in accordance with UL248-14,
a UL-certied automatic fuse (e.g. ABB Type S201-B16)
or a 10A fuse with a medium time-lag (e.g. ESKA Part No.
522.227) must be used.
All connections of the u-control components are protected
against voltage pulses and overcurrent in accordance with
IEC61131-2, ZoneB. The operator has to decide whether
additional overvoltage protection according to IEC62305
is required. Voltages that exceed +/-30V may cause the de-
struction of couplers and modules.
Earthing
Via an FE spring on its underside each controller and each
module is electrically connected to the DIN rail. This connec-
tion is only established certainly if the assembly is carried
out carefully and in accordance with the instructions (see
section6.2). In order to ensure the earthing of the station
the DIN rail must be connected to the protective earth via the
earth terminals (PE).
Several modules have connections with green pushers. An
FE potential is also provided at these connections. They
must not be used as a PE!
Shielding
Shielded lines are to be connected with shielded plugs and
xed on a shield bus in compliance with the relevant stand-
ard (see Chapter7).

62604080000/03/08.2020Manual u-control
2 Safety | Intended use
2.2 Intended use
The products of the UC20 series are intended for use in in-
dustrial automation. A u-control station comprising a control-
ler and connected u-remote I/O modules is intended for the
control of systems or sub-systems.
The UC20-WL2000 controllers are congured and pro-
grammed using the integrated web application u-create web.
The UC20-SL2000 controllers are congured and pro-
grammed using the separate engineering tool u-create stu-
dio.
The UC20 products conform to protection class IP20 (in ac-
cordance with IEC60529).
The observance of the documentation is part of the intended
use. The products described in this manual may only be used
for the intended applications and only in connection with
certied third-party devices or components. The product-
specic protective measures can become ineffective in the
event of deviating use.
2.3 Use in a potentially explosive atmosphere
Unless otherwise noted, the u-control products can be used
in potentially explosive atmospheres rated as Zone2 (as per
Directive 2014/34/EU). The u-remote products are suitable
for use in ClassI, Division2, Groups A to D according to
NFPA publication70.
If u-remote products are used in potentially explosive atmos-
pheres, the following notes are also applicable:
–Staff involved in assembly, installation and operation must
be qualified to perform safe work on electrical systems
protected against potentially explosive atmospheres.
–The requirements according to IEC 60079-14 must be
observed.
–The substitution of any components may impair suitability
for ClassI, Divsion2.
–The equipment shall be installed in an enclosure that pro-
vides a degree of protection not less than IP54 in accord-
ance with IEC60079-15, accessible only by the use of a
tool.
–The housing enclosing must meet the requirements of
explosion protection type Exn or Exe.
–The u-control station may only be installed in horizontal
orientation.
–The controller may only be used without battery.
–Sensors and actuators that are located in Zone 2 or in a
safe zone can be connected to the u-control station.
–If the ambient temperature under rated conditions exeeds
55°C, the cables used for feed-in (on the fieldbus coupler
and on power-feed modules) must be specified for at
least 90°C.
–If the temperature under rated conditions exceeds 70°C
at the cable or conduit entry point, or 80°C at the
branching point of the conductors, the temperature speci-
fication of the selected cable shall be in compliance with
the actual measured temperature values.
–The equipment shall only be used in an area of not more
than pollution degree2, as defined in IEC60664-1.
–A stabilized 24V DC power supply with double or rein-
forced insulation shall be used.
–A visual inspection of the u-control station is to be per-
formed once per year.
–When using relais modules UR20-4RO-CO-255, solid
state relais modules UR20-4RO-SSR-255 or
UR20-4DI-2W-230V-AC modules in explosive atmos-
phere:
–The device shall be installed in an environment free of
condensation, corrosives and conducting dusts.
–If the switching or input voltage exceeds 63V, a tran-
sient protection device shall be provided that limits the
transients to a peak voltage of 500V or less.
–When using relais modules UR20-4RO-CO-255 in explo-
sive atmosphere:
–Make sure that the module will not be exposed to
chemicals, which may degrade the sealing properties
of materials used in the relay.
–Due to the fact that relays are subject to wear, it must
be ensured, by appropriate maintenance intervals, that
the temperature do not exceed the limits of tempera-
ture class T4. A contact resistance of more than
110mΩ will be considered as a fault.
–The modules may only be charged with resistive loads.
–While explosive atmosphere is present:
–No electrical connection shall be separated in ener-
gized condition.
–The USB interface shall not be used.
–Dip-switches, binary-switches and potentiometers shall
not be actuated.

2 Safety | Legal notice
7Manual u-control2604080000/03/08.2020
2.4 Legal notice
The u-control series products are CE-compliant in accor-
dance with Directive 2014/30/EU (EMC Directive) and
Directive 2014/35/EU (Low Voltage Directive). They also
meet the requirements of the ATEX Directive 2014/34/EU
unless otherwise noted.
The results of the measurements according to CISPR16-2-3
should also be suitable to demonstrate the compliance of
the u-control devices to the limits for radiated emissions as
dened by CFR47Part15, SubpartB, §15.109, ClassA
(2010) and ICES-003, Issue5, ClassA (2012).
Components of the free software products are integrated
into the u-control products. The licensing terms are available
in the program.

82604080000/03/08.2020Manual u-control

3 Systemoverview
9Manual u-control2604080000/03/08.2020
3 System overview
Example arrangement of a u-control station
The products of the u-control series are programmable logic
controllers. The UC20-WL2000 controllers are congured,
parameterised and programmed using the integrated en-
gineering tool u-create web via a web browser. The UC20-
SL2000 controllers are congured, parameterised and
programmed using the separate engineering tool u-create
studio.
Up to 64 active u-remote I/O modules can be connected to a
controller. The controller and the I/O module of a u-control-
station communicate over the u-remote-system bus.
The following components belong to a u-control-station:
–Controller: head station for production and execution of
control programs and for integration into the existing net-
work architecture or into HMIs
–Active I/O modules:
–Modules with digital input (DI) or digital output (DO)
with 4, 8 or 16 channels
–Modules with analogue input (AI) or analogue output
(AO) with up to 8 channels
–Safety-related supply terminals (PF-O-xDI-SIL) 24 V for
output current with either one or two dual channel
inputs for safety circuits
–Passive I/O modules (no fieldbus communication)
–24-V power-feed modules (PF) for input or output cur-
rent
–Potential distribution modules (AUX)
–Empty modules acting as placeholders (ES)
–Mechanical fixing elements
–End brackets
–End plate
D
W
Height (H) Width (W) Depth (D)
Controller 120.0 / 4.72 52.0 / 2.05 76.0 / 2.99
I/O module 120.0 / 4.72 11.5 / 0.451) 76.0 / 2.99
End plate 120.0 / 4.72 3.5 / 0.14 76.0 / 2.99
End bracket 120.0 / 4.72 8.0 / 0.32 36.0 / 1.42
Dimensions of the u-control station components (mm / inch)
“Double-click” installation
The u-control station modules can be installed quickly and
simply. When attaching the module to the DIN rail, a clear
clicking noise can be heard, which means that the module
has clicked into place. In the second step, which involves
pushing the module being installed together with the neigh-
bouring module, a further clicking noise indicates that the
modules have been correctly connected to each other.

10 2604080000/03/08.2020Manual u-control
3 Systemoverview
Power supply concept
The u-control controllers and the u-remote modules use three
internal current paths as described in following chapter4. In-
put and output paths are supplied seperately, therefore a cus-
tom-t refreshing by power-feed modules is easyly feasible.
The gure shows the general supply concept. For detailed
description and calculation of the current demand please
regard sections 4.6 and 4.7.
X1
X2
DI DI DO PF-IDODO DI DIDI DODO DO
PF-OUC20 PF-OAO DO
UOUT 24V
UOUT Power supply of the output paths
UIN Power supply of the intput paths
PF-X Power feed-in
Surge protection on each power feed-in
UIN 24V
24V Power feed-in outputs 24V Power feed-in inputs
24V
Power supply of a u-control station in general

3 Systemoverview | General description of the controller
11Manual u-control2604080000/03/08.2020
3.1 General description of the controller
1
2
4
5
6
12
10
11
9
8
7
14
13
13
15
16
18
17
3
Controller (example: UC20-SL2000-EC-CAN)
1 Release lever for the DIN rail fixing
2 Data line connection (RJ45)
3 CAN interface (only UC20-SL2000-EC-CAN)
4 Seats for module markers
5 Type designation
6 Swivel marker for labelling modules and channels (optional)
7 Connector frame unlocking device
8 LED power supply controller
9 Controller status LEDs
10 Power supply connector for the system and input modules
11 Power supply connector for output modules
12 Service flap (access USB port)
13 Latching hook for latching onto module sides
14 System bus
15 System current path
16 Input current path
17 Type plate
18 Output current path

12 2604080000/03/08.2020Manual u-control
3 Systemoverview | General technical data
3.2 General technical data
Type of connection "PUSH IN" solid, ne-wired
Wire cross-section 0.14 ... 1.5mm2 (AWG 16 – 26)
Configuration interface USB 2.0
Dimensions Height 120.0 mm / 4.72"
(with release lever: 128.0 mm / 5.04")
Width 52.0mm / 2.05"
Depth 76.0 mm / 2.99"
Protection class (IEC 60529) IP20
FlammabilityratingUL94 V-0
Temperature data Operation (horizontal installation) for 24VDC +20%/-15% -20°C to +55°C (2×5A power supply)
Operation (vertical installation) at 24VDC +20%/-15% -20°C to +50°C (2×5A power supply)
Storage, transport -40°C to +85°C
Humidity Operations 95%, non-condensing according to IEC 61131-2
Storage, transport 95%, non-condensing according to IEC 61131-2
Air pressure Operations ≥ 795 hPa (altitude ≤ 2000 m) according to IEC 61131-2
Storage, transport ≥ 700 hPa (altitude ≤ 3000 m) according to IEC 61131-2
Vibration resistance 5 Hz ≤ f ≤ 8.4 Hz: 3.5 mm amplitude as per IEC 60068-2-6
8.4 Hz ≤ f ≤ 150 Hz: 1 g acceleration as per IEC 60068-2-6
Shock resistance 15g over 11ms, half sine wave, as per IEC 60068-2-27
Potential isolation Test voltage max. 28.8V inside a channel
500VDC eld/system (according to EN60079-15:2010)
Pollution degree 2 (according to DINEN60664-1:2008)
Overvoltage category II (according to DINEN50178)
Approvals and standards cULus UL61010
Maritime und offshore applications pending
EX zone 2 ATEX Directive 2014/34/EU
EMC IEC 61000 (partial standards according to the requirements of IEC
61131-2)
Explosion protection IEC60079-0:2012, IEC60079-15:2010, EN60079-0:2012,
EN60079-15:2010
PLC IEC61131-2
You can nd all product-specic technical data in the corresponding product description in Chapter5.

3 Systemoverview | Connectable u-remote I/O modules
13Manual u-control2604080000/03/08.2020
3.3 Connectable u-remote I/O modules
The release notes concerning the controllers
describe which u-remote modules at which rm-
ware version are supported. The release notes
are available to download from the Weidmüller
website.
▶Please regard the information in the release notes.
3.4 ConnectorPG1.5mm
A connector frame can take up to four connectors, and four
conductors can be connected to each connector. “PUSH IN”
technology allows for ne-wired conductors with crimped
wire-end ferrules or ultrasonically welded conductors, each
with a maximum cross-section of 1.5mm², to be inserted
easily through the opening in the clamping terminal without
having to use tools. To insert ne-wired conductors without
wire-end ferrules, the pusher must be pressed in with a
screwdriver (wiring see section 6.3).
ConnectorPG1.5mmwithfourconductorconnections
–conductor cross-section 0.14 to 1.5 mm² (AWG 16 – 26)
–max. ampacity: 10A
–4-pole
The pushers are colour-coded for the following connections:
White Signal DC or AC
Blue GND
Red 24VDC
Green Functional earth (FE)
Black SignalAC
3.5 Mechanicalxingelements
The station is xed in the installation position by an end
bracket at either side. The last I/O module is protected
against dust by a cover plate. Into this cover plate the second
end bracket is inserted and screwed to the mounting rail.
Every u-control controller is supplied with a termination kit.
1 2
u-control station fixing elements
1 End bracket (left end, on the controller side)
2 Termination kit with end plate and end bracket (right end)
For vertical installation, a special end bracket (Order No.
1805610000 MEW 35/1) must also be installed below the
station.

14 2604080000/03/08.2020Manual u-control
3 Systemoverview | Type plate
3.6 Type plate
Each controller features a type plate, which includes iden-
tication information and the key technical specications.
In addition, a QR code allows for direct online access to the
associated documentation. The software for reading the QR
code must support inverted QR codes. A breakdown of the
serial numbers can be found in the table provided in the an-
nex.
3
17
6
8
5
4
2
Type plate (example)
1 Product number (Order No.)
2 Serial number
3 Manufacturing code
4 ATEX marking
5 Logos of certification bodies
6 Replacement part order number
7 Hardware version
8 Notice documentation
3.7 Battery
The controller can be equipped with a battery (for specica-
tion see technical data). The battery continues to supply the
integrated real-time clock if the power supply is interrupted.
3.8 Memory card
The controller can be equipped with an SD card (for speci-
cation see technical data).
For the UC20-SL2000 controllers, you need the SD card to
install the rmware on the controller.
You can insert an SD card into the UC20-WL2000 control-
lers, if you want to access the SD card via Node-RED.

4 Conguration | Order and arrangement of the modules
15Manual u-control2604080000/03/08.2020
4 Conguration
4.1 Order and arrangement of the modules
The u-control station is designed to be installed on a DINrail
(35 × 7.5mm or 35 x 15mm) made from steel or galvanised
steel according to EN 60715.
–A u-remote station may be built up to a maxi-
mum length of 1m. Therefore at most
82modules (including max. 64 active mod-
ules) can be aligned on a controller.
A u-control station may only be installed in this sequence
(starting from the left/bottom):
–End bracket
–Controller
–Up to 82 modules (including max. 64 active modules)
–End plate and end bracket
ATTENTION
A maximum of three passive modules (potential distribu-
tion module, power-feed module or blank module) may be
placed in successive positions. Then at least one active
module must follow.
Arrangement of safe power-feed modules
A safe power-feed module PF-O-xDI-SIL module can be
positioned anywhere in the u-control station. All of the fol-
lowing output modules (except for the UR20-4RO-CO-255
and UR20-4RO-SSR-255 relay modules) up to the next PF-O
module will be safely disconnected (safety segment). Multi-
ple PF-O-xDI-SIL modules/safety segments can be arranged
within a station.
When using safe power-feed modules, please
also observe the Modules for Functional Safe-
ty Manual.
The manual is available to download from the
Weidmüller website.
4.2 Orientation of the station
The u-control station is usually installed on a horizontally
positioned DIN rail.
42 mm
1.65"
42 mm
1.65"
X1
X2
Installation position of the u-control station on the DIN rail (horizontal installation)
Installation on vertically positioned DIN rails is also possible.
In this case however, the heat dissipation is reduced such
that the derating values change (seeSection 4.6).
In the case of vertical mounting, the controller must always
be arranged as the rst module at the bottom and secured
with a MEW35/1 end bracket for vertical mounting (Order
No. 1805610000).
42 mm 42 mm
1.65" 1.65"
X1
X2
Installation position of the u-control station on the DIN rail (vertical installation)

16 2604080000/03/08.2020Manual u-control
4 Conguration | Installation distances
4.3 Installation distances
In order to be able to carry out the installation and subse-
quent maintenance work and to ensure sufcient ventilation,
the u-control station must be installed while observing the
following minimum distances (see the following gures).
ATTENTION
Depending on how the station shielding is implemented,
the specied distances may have to be made larger, where
necessary.
The minimum permissible conductor bending radii must also
be observed. Earth terminals already installed can be ignored
when calculating the distance.
40 mm
1.57"
35 mm
1.38"
40 mm
1.57"
20 mm
0.79"
20 mm
0.79"
X1
X2
Minimum distances for horizontal installation
35 mm
1.38"
40 mm
1.57"
40 mm
1.57"
20 mm
0.97"
20 mm
0.97"
X1
X2
Minimum distances for vertical installation
1.18"
30 mm
10
mm
0.39"
Minimum distance for electrical cabinet door (without/with swivel marker)
Calculation of space requirements
The space requirements for a u-control station with n mod-
ules (horizontal installation) is calculated as follows:
D
W
Height: 120mm (4.72")
+ 2 x 40mm (1.57") distances at top and bottom
=200mm (7.87")
Width: 8mm (1.57" ) end bracket
+ 52mm (2.05") controller
+ nx11.5mm (0.45") nmodules
+ 11.5mm (0.45") end plate and end bracket
+ 2x20mm (0.79") distances to the sides
=111.5mm (4.39") + nx11.5mm (0.45")
For vertical installation please interchange height and
width. When calculating the width, 12.5mm / 0.49"
must be added for the end bracket MEW35/1 (OrderNo.
1805610000).

4 Conguration | Use in a potentially explosive atmosphere
17Manual u-control2604080000/03/08.2020
4.4 Use in a potentially explosive atmosphere
Please regard the safety notes in section 2.3.
If the u-remote station is used in a potentially explosive
atmosphere rated as Zone 2, the housing must meet the re-
quirements of explosion protection type Exn or Exe and pro-
tection class IP54. Sensors and actuators that are located in
Zone 2 or in a safe zone can be connected. All cable glands
on the housing must be approved for Exe.
IP54
Zone 2
safe area no ex-approval
u-remote
II 3G Ex nA
II 3G Ex nA nC
Use in a potentially explosive atmosphere
ATEXmarking(internalcertication)
II 3 G Ex nA IIC T4 Gc
WI 13ATEX0002X
Ta: -20°C … +60°C
ATEXmarking(externalcertication)
II 3 G Ex nA IIC T4 Gc
DEMKO 15ATEX1525X
Ta: -20°C … +60°C
II 3 G Ex nA nC IIC T4 Gc (relay modules)
DEMKO 15ATEX1525X
Ta: -20°C … +60°C
IECEx marking
Ex nA IIC T4 Gc
IECEx ULD 15.0013X
Ex nA nC IIC T4 Gc (relay modules)
IECEx ULD 15.0013X
Calculation of power loss for the use in a potentially explo-
sive atmosphere
You will nd the module specic data needed for calculation
in the document "WI13ATEX0002_Power_Calc.pdf" which
you can download from the Weidmüller website.
4.5 “PUSH IN” system cabling
Controllers are equipped with the “PUSH IN” connector sys-
tem. Single-strand and ne-strand lines with wire-end ferrules
can be inserted without the need for a tool. Copper wires
with a cross-section measuring between 0.14 mm2 and
1.5mm2can be connected.
We recommend using the following wire-end ferrules:
Cross-section
AWG
Weidmüller order no.
Weidmüller colour code
Weidmüller order no.
DIN colour code
0.14 mm² 26 9028240000
0.25 mm² 24 9025760000
0.34 mm² 22 9025770000
0.50 mm² 20 9025870000 9019020000
0.75 mm² 18 9025860000 9019050000
1.00 mm² 17 9025950000 9019100000
1.50 mm² 16 0635100000 9019130000
Wire-end ferrules for the wiring
The external dimensions of the crimped wire-end ferrules
must conform with IEC-60947-1. For crimping, we recom-
mend crimp shape A and the following tools:
–Crimping tool for wire-end ferrules from 0.25mm² to
1.5mm² (AWG 24 to 16) with a trapezoidal indentation
crimp, type: PZ6/5 ZERT (Order No. 9017900000)
–Crimping tool for wire-end ferrules from 0.14mm² to
0.75mm² (AWG 26 to 18) with a trapezoidal crimp, type:
PZ 1.5 ZERT (Order No. 9017310000)

18 2604080000/03/08.2020Manual u-control
4 Conguration | Current demand and power supply
4.6 Current demand and power supply
The u-control controllers use three internal current paths:
The ISYS system current path supplies the communication
part of the I/O modules; it is fed from the controller input
supply and cannot be interrupted by any module. The maxi-
mum current-carrying capacity of ISYS allows a u-control sta-
tion to be expanded with a maximum of 64 active modules
without having to refresh the power.
The IIN input current path supplies the input circuit of the
input modules as well as the connected ISsensors. The cur-
rent must be refreshed with UR20-PF-I (power feed in) mod-
ules as required. These UR20-PF-I modules isolate the input
current path towards the left (towards the controller), and as
a result start a new electricity segment towards the right.
The IOUT output current path supplies the output circuit
of the output modules with power, as well as the connect-
ed ILactuators. The current must be refreshed with the
UR20-PF-O (power feed-out), as required. These UR20-PF-O
modules isolate the output current path to the left (towards
the controller), and as a result start a new electricity segment
to the right.
The design of the power supply being used must
take start-up peaks into account.
Power supply derating
The power supply is restricted according to the temperature.
The following values apply for the horizontal and vertical po-
sitioning of the u-remote station:
Temperature-dependent values for the power supply
horizontal vertical
Controller power
supply 55°C / 2 x 5A 50°C / 2 x 5A
Power-feed mod-
ule power supply 55°C / 1 x 10A 50°C / 1 x 10A
ATTENTION
Equipment may become damaged if improperly rat-
ed circuit protection is used!
▶In order to achieve spezification according to UL248-14
use a UL-approved Type-B automatic circuit breaker
(e.g. ABB Typ S201-B16) or use a fuse with a maxi-
mum of 10A protection (e.g. ESKA Art. Nr. 522.227).
ATTENTION
Equipment may become damaged by overcurrent!
▶Auxiliary supplies as well as signal inputs and outputs
may not be used for supplying the station.
Current demand
Product ISYS IIN IOUT
UC20-WL2000-AC < 116mA –
UC20-WL2000-IOT < 116mA –
UC20-SL2000-EC < 116mA –
UC20-SL2000-EC-CAN < 116mA –
The current demand of the u-remote I/O-modules
can be found in the Remote-I/O-System
u-remote Manual.
All manuals are available to download from the
Weidmüller website.
Voltage interruption
The controllers meet severity level PS1 (maximum inter-
ruption time 1ms) according to IEC61131-2. If you want
to achieve severity level PS2 (maximum interruption time
10ms), you must use a power supply that meets the require-
ments of severity level PS2.

4 Conguration | Example calculation for the power supply
19Manual u-control2604080000/03/08.2020
4.7 Example calculation for the power supply
The power supply must be calculated individually for each
station installation. Therefore the simultaneity factor g and
the current demand of each module, as well as the devices
to be connected must be established (see the example calcu-
lation table).
In the example station, a UC20-WL2000-AC controller
is congured with four UR20-4DI-P modules and eight
UR20-8DO-P modules. The cumulative current demand for
each module is now calculated to determine whether and at
which point a UR20-PF-I power-feed module must be posi-
tioned to refresh the current path. A power-feed module must
always be used where the current demand exceeds 10 A.
The power refresh must be separately calculated
for the input and output current paths. The sys-
tem voltage need not be considered during this
step.
Calculation of the current demand for the input current
The current consumption of the controller must be consid-
ered for the main power supply, and the sum of consump-
tion values is multiplied by the simultaneity factor g for each
following module:
ISYS controller
+ (ISYS + IIN )+ (IS x g) module 1
+ (ISYS + IIN )+ (IS x g) module 2
+ ∑((ISYS + IIN )+ (IS x g)) modules 3 to 4
= Cumulative current demand
ISYS Current consumption from the system current path
IIN Current consumption from the input current path
IS Power supplies for the connected sensors
In the case of an additional power supply (power refresh)
with a UR20-PF-I power-feed module, only the sensor power
supplies and the module current consumption have to be
considered:
((IIN + IS module x) x g)
+ ((IIN + IS module y) x g)
+ ∑((IIN + IS) x g) n modules
= Cumulative current demand
Calculation of current demand for the output current
The current consumption of each module and the current
demand of the connected actuators must be considered for
the output current. There is no difference in the calculation
of the main power supply and power refresh:
(IOUT + (IL x g) module 1
+ (IOUT + (IL x g) module 2
+ ∑(IOUT + (IL x g)) n modules
= Cumulative current demand
IOUT module current consumption from the output current path
IL Current demand of the connected actuators
Example:
The values in the following table are used to calculate the
current demand of the example station (cumulative for each
module). The input current is:
Module1:
I=0.116 A + (0.008 A + 0.012 A) + (0.06 Ax1)= 0.196A
Module2:
I=0.196 A+ (0.008 A + 0.012 A) + (0.06 Ax1)= 0.276A
The values for the other modules are calculated accordingly.
The result shows that the accumulated value for up to 12
modules remains under 10 A, and therefore a power-feed
module need not be used for the input current path.
Results for the output current path:
Module 5:
I=0.015 A+(2A x 0.5)=1.015A
Modul6 6:
I=1.015 A+(0.015 A+(4A x 0.5)=3.03A
Module10:
I=6.175A +(0.015A +(4A x 0.5)=8.19A
Module11 (without power refresh):
I=8.19 A+(0.015 A+(4A x 0.5)=10.205A
Therefore the available 10 A would be exceeded. As a result,
a PF-O power-feed module must be positioned e 11th mod-
ule, which will supply anocalculation of current consumption
is repeated for each power-feed module. Unused current
values may not be included.
Module11 (as per PF-O):
I=(0.015 A+(4A x 0.5)=2.015A
Module 12 (as per PF-O):
I = 2.015A (0.015 A + (4A x 0.5) = 4.030A

20 2604080000/03/08.2020Manual u-control
4 Conguration | Example calculation for the power supply
Example calculation for the current demand (all current values in A)
Module
no.
Product ISYS IIN IOUT ISILSimultaneity
factor
g
Cumulative
current demand
of the input cur-
rent path
Cumulative
current demand
of the controller
output power
path
Cumulative cur-
rent demand of
the PF-O output
power path
UC20-WL2000-AC 0.116 0.116 0
1UR20-4DI-P 0.008 0.012 0.06 10.196 0
2UR20-4DI-P 0.008 0.012 0.06 10.276 0
3UR20-4DI-P 0.008 0.012 0.12 10.416 0
4UR20-4DI-P 0.008 0.012 0.18 10.616 0
5 UR20-8DO-P 0.008 0.015 20.5 0.624 1.015
6UR20-8DO-P 0.008 0.015 40.5 0.632 3.03
7 UR20-8DO-P 0.008 0.015 30.5 0.64 4.545
8UR20-8DO-P 0.008 0.015 20.5 0.648 5.56
9 UR20-8DO-P 0.008 0.015 1.2 0.5 0.656 6.175
10 UR20-8DO-P 0.008 0.015 40.5 0.664 8.19
UR20-PF-O
11 UR20-8DO-P 0.008 0.015 40.5 0.672 2.015
12 UR20-8DO-P 0.008 0.015 40.5 0.68 4.030
ISYS Current consumption from the system power supply
IIN Power consumption from input current path
IOUT Power consumption from output current path
IS Current demand of the connected sensors
IL Current demand of the connected actuators
The current demand is just under 10A! The output
current path must therefore be refreshed before the
11th module.
10A is supplied by the UR20-PF-O module. The
1.81A calculated as remaining after the 10th module
must not be added to the 10 A after the UR20-PF-O
module!
This manual suits for next models
8
Table of contents
Other Weidmüller Controllers manuals
Popular Controllers manuals by other brands

LOTOS
LOTOS AR04 Assembly & operating instructions
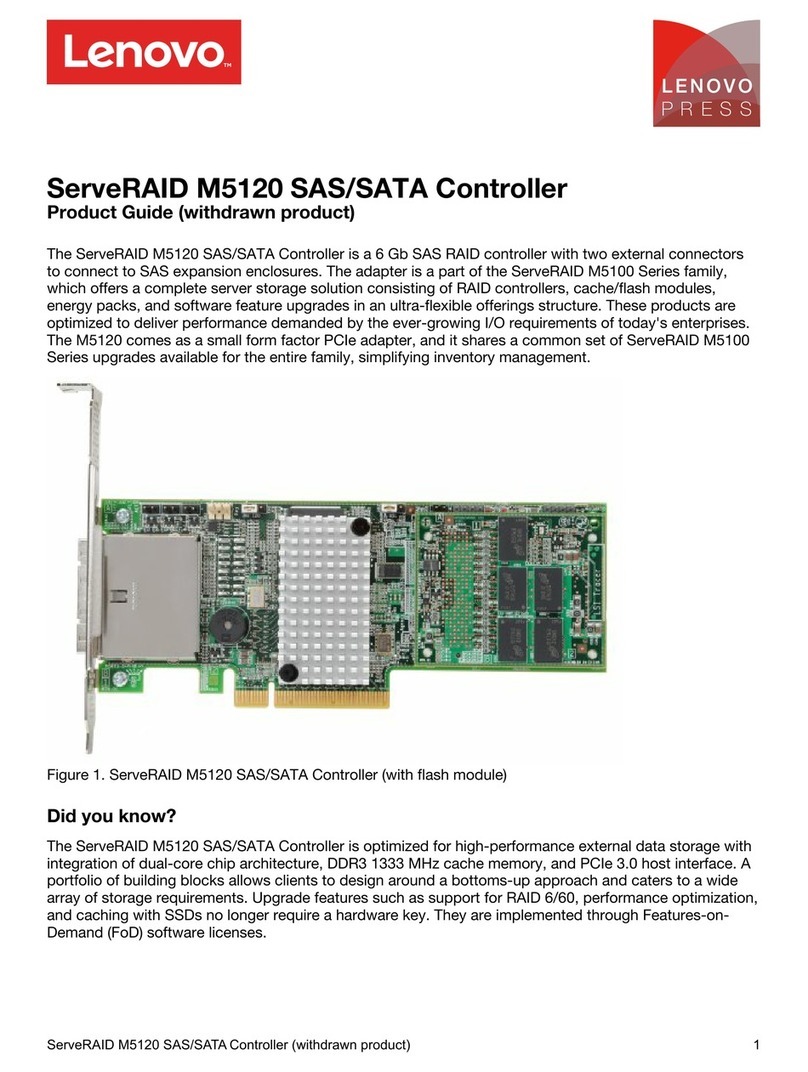
Lenovo
Lenovo ServeRAID M5120 Product guide
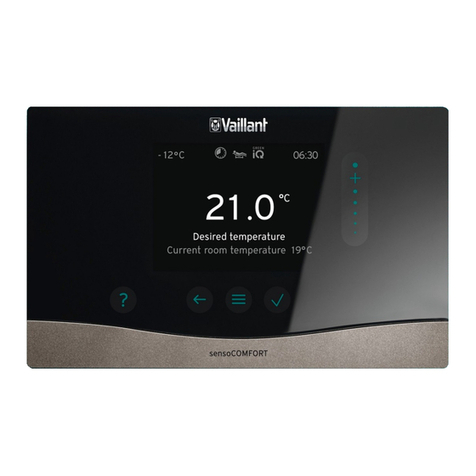
Vaillant
Vaillant sensoCOMFORT VRC 720 Operating and installation instructions
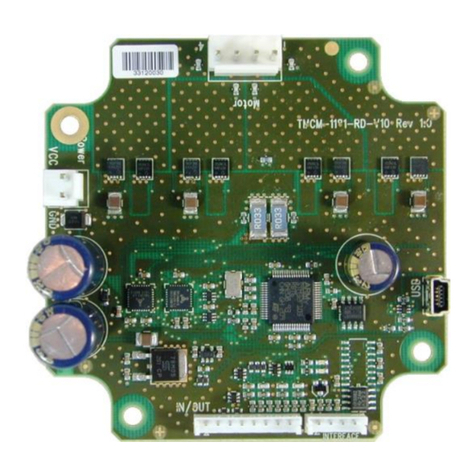
Trinamic
Trinamic TMCM-1181 manual
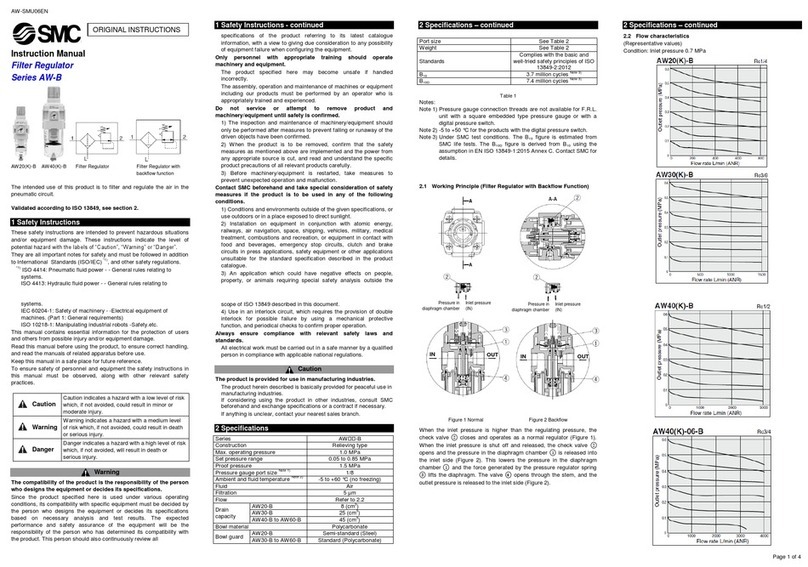
SMC Networks
SMC Networks AW20-B instruction manual
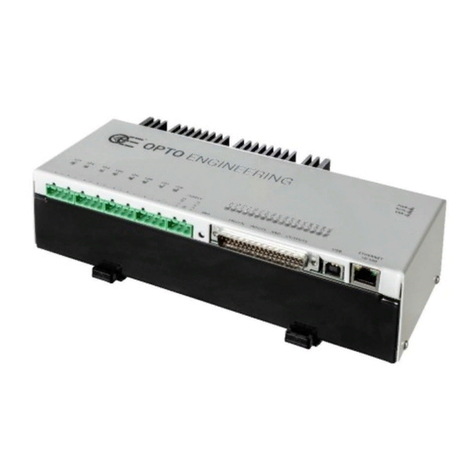
opto engineering
opto engineering LTDVE8CH-20 instruction manual