IMI NORGREN VM10 5 Series Installation and operating instructions

Operation & Service
Manual
Valve island VM10 with
EtherNet/IP Interface
8, 10, 12 or 16 stations

2
Operation & Service Manual
Valve islands VM10 EtherNet/IP
07/2018
Construction & Design is subject to change © 2018 Norgren GmbH
Change history:
The Change history reflects all changes of the Operation & Service Manual, which were done after
the initial release.
Index
Chapters
Change description
Date
Name
001
All
Set up initial version
08/02/2017
002
All
Modifications have been updated
28/02/2017
003
2
New chapter added
20/07/2017
004
3
Added chapter: static IP address setting
31/07/2017
005
All
Additional minor comments implemented
21/09/2017
006
All
Additional amendments made
19/07/2018
This Operation & Service Manual makes no claims of being complete as it doesn’t cover all
variants of the VM10 valve islands series at the moment.
Therefore this document is subject to extensions or changes.

3
Operation & Service Manual
Valve islands VM10 EtherNet/IP
07/2018
Construction & Design is subject to change © 2018 Norgren GmbH
Content
1. About this documentation.............................................................................................5
2. Important hints.............................................................................................................6
2.1 Grounding and equipotential bonding.....................................................................6
3. Electrical Connections of the VM10 valve islands........................................................7
3.1 EtherNet/IP - Bus connectors PORT 1 & PORT 2..................................................8
3.2 POWER supply connector......................................................................................8
4. Commisioning..............................................................................................................9
4.1 EDS File Installation...............................................................................................9
4.2 Hardware configuration: Select valve island.........................................................10
4.3 Set up IP Address.................................................................................................13
4.3.1 Using a DHCP Server....................................................................................13
4.3.2 Static IP Address assignment using TCP/IP Interface Object........................13
5. I/O connection via Assembly Object ..........................................................................15
5.1 Bit allocation valve stations ..................................................................................15
5.2 Input data (Assembly Object Instance: 101d).......................................................16
5.3 Output data (Assembly Object Instance: 100d)....................................................17
6. Solenoid Object..........................................................................................................18
7. Diagnostics and LEDs................................................................................................19
7.1 Status LEDs .........................................................................................................19
7.1.1 Status LEDs description.................................................................................19
7.1.2 Link states for Port P1 and Port P2................................................................19
7.1.3 Network Status LED (NS) .............................................................................19
7.1.4 Module Status LED (MS) ..............................................................................19
7.1.5 Electronics Power Supply Status, LED (VB)..................................................20
7.1.6 Valve Power Supply Status, LED (VA)...........................................................20
7.2 Valve slice Status LEDs .......................................................................................21
8. Output behavior in fault condition (Idle mode/Fault mode).........................................22
9. Properties EtherNet/IP Interface................................................................................23
10. Electrical data..........................................................................................................24
11. Technical data .........................................................................................................25

4
Operation & Service Manual
Valve islands VM10 EtherNet/IP
07/2018
Construction & Design is subject to change © 2018 Norgren GmbH
Contact information
Norgren GmbH
Site Fellbach
Stuttgarter Straße 120
70736 Fellbach
Tel: +49 711 5209-0

5
Operation & Service Manual
Valve islands VM10 EtherNet/IP
07/2018
Construction & Design is subject to change © 2018 Norgren GmbH
1. About this documentation
This Operation & Service Manual contains the information to set up and operate the VM10 valve
islands with EtherNet/IP interface and to detect and resolve problems.
Note
In addition to the specific information for the EtherNet/IP variants, all data sheets for the VM10 valve island series are
applicable and remain valid. No changes in valve size and flow. Diffence on connection and parameters.
Refer also to the datasheet on the following weblink:
http://cdn.norgren.com/pdf/en_5_1_100_VM10.pdf
Refer also to the installation video on the following weblink:
https://player.vimeo.com/video/256919223

6
Operation & Service Manual
Valve islands VM10 EtherNet/IP
07/2018
Construction & Design is subject to change © 2018 Norgren GmbH
2. Important hints
2.1 Grounding and equipotential bonding
Proper grounding and equipotential bonding are very important to protect against electromagnetic
interferences in Ethernet networks. In order to reduce potential impact, grounding of the Ethernet
cable screen should be done at both ends of every cable (i.e. at each device). Equipotential
bonding ensures that the ground potential is identical throughout the entire Ethernet network and is
essential to avoid equipotential bonding currents, which could otherwise flow through the Ethernet
cable screen.
For proper grounding please use the terminal for functional earth (M4) on the upper side of the
valve island. For easy reference see position 4 in chapter 3.

7
Operation & Service Manual
Valve islands VM10 EtherNet/IP
07/2018
Construction & Design is subject to change © 2018 Norgren GmbH
3. Electrical Connections of the VM10 valve islands
1. Port 1 bus connector for EtherNet/IP
(4 pins M12 D-coded female connector)
2. Port 2 bus connector for EtherNet/IP
(4 pins M12 D-coded female connector)
3. Power supply connector
(5-pins M12 A-coded male connector)
4. Terminal for functional earth (M4)
5. Status LEDs
6. Valve status LEDs

8
Operation & Service Manual
Valve islands VM10 EtherNet/IP
07/2018
Construction & Design is subject to change © 2018 Norgren GmbH
3.1 EtherNet/IP - Bus connectors PORT 1 & PORT 2
M12 / 4 pins / female connector / D-coded
Pin no.
Function
1
Transmission Data + (TD+)
2
Receive Data + (RD+)
3
Transmission Data - (TD -)
4
Receive Data - (RD -)
Earth screw
FE (functional earth)
3.2 POWER supply connector
M12 / 5 pins / male connector / A-coded
Pin no.
Function
1
L1 (VB+) 24V electronics power supply
2
N2 (VA-) 0V valves power supply
3
N1 (VB-) 0V electronics power supply
4
L2 (VA+) 24V valves power supply
5
FE (functional earth)

9
Operation & Service Manual
Valve islands VM10 EtherNet/IP
07/2018
Construction & Design is subject to change © 2018 Norgren GmbH
4. Commisioning
The configuration of the EtherNet/IP valve island is done via inclusion of the device description file
(EDS file) „002A002B1XXXX0100.EDS“. The device description file is required to be included for
the configuration of the corresponding EtherNet/IP - Controller.
The following steps are necessary.
Note:
XXXX = ‘1000’ -> VM10 with 8 Stations, ‘1100’ -> VM10 with 10 Stations,‘1200’ -> VM10 with 12 Stations, ‘1300’ ->
VM10 with 16 Stations.
Note: All explanations in this manual are based on Rockwell Automations “Studio 5000”.
4.1 EDS File Installation
The EDS file is required to configure the VM10 valve island. A symbol file is necessary to display
an icon in the engineering tool.
EDS files are provided by the module vendor and can be downloaded from:
https://www.imi-precision.com/us/en/technical-support/software
Note: The method of module installation strongly depends on the configuration software. Please refer to the
configuration software manual.
The following picture shows Startup image of Rockwell Automations “Logix Designer”.
In menu “Tool -> EDS Hardware Installation Tool” start the Installation Wizard. Follow the
installation steps described in the wizard.

10
Operation & Service Manual
Valve islands VM10 EtherNet/IP
07/2018
Construction & Design is subject to change © 2018 Norgren GmbH
After the installation the new module is shown in the catalogue.
4.2 Hardware configuration: Select valve island
After the successful installation of the EDS file, the module configuration is needed. In context
menu choose “New Module” after right-clicking on “Ethernet”.

11
Operation & Service Manual
Valve islands VM10 EtherNet/IP
07/2018
Construction & Design is subject to change © 2018 Norgren GmbH
In the module catalog choose the corresponding VM10 valve island and click on „Create“.
The picture bellow shows “Select Module Type” – Dialog
In the following dialogue tab “General” set the “Name” and the correct “IP Address” of the module.

12
Operation & Service Manual
Valve islands VM10 EtherNet/IP
07/2018
Construction & Design is subject to change © 2018 Norgren GmbH
In dialogue tab “Connection” change “Requested Packet Interval (RPI)” greater than or equal to 10
ms and click “OK”. The RPI times has a direct impact to the busload.
Note: The lower the cycle times, the higher the busload.
The picture bellow shows module tree with the new added module.
After successful configuration please perform download by clicking „Download“ in the menu item
„Communication“.

13
Operation & Service Manual
Valve islands VM10 EtherNet/IP
07/2018
Construction & Design is subject to change © 2018 Norgren GmbH
4.3 Set up IP Address
4.3.1 Using a DHCP Server
As default the VM10 valve island is set up as a DHCP client. In this mode IP Address has to be
assigned using a DHCP server or a similar tool. This has to be repeated after each power cycle.
The following example shows the IP Address assignment using Rockwell Automations
BOOTP_DHCP Tool.
It is important to ensure that the network adapter set up in the “Network Settings” of the tool is the
one, which is connected physically to the VM10 valve island.
Menu: “Tools” -> “Network Settings”
The VM10 valve island should then appear in the “Discovery History” list. Double clicking the MAC
Address opens the dialog used to set up the IP Address.
The IP Address settings are transferred into the “Discovery History” if they are valid and confirmed
with the “OK” button. Pushing the “Enable BOOTP/DHCP” Button enables the IP Address
assignment for the chosen entry. The VM10 valve island will appear with assigned IP Address in
“Discovery History” list if address assignment was successful.
4.3.2 Static IP Address assignment using TCP/IP Interface Object
Configuration method of the IP Address could also to be set up as a static value. The interface
configuration is saved to NV storage. This has to be done once and is valid after a power cycle.
The Read/Write access to the TCP/IP Interface Object is done via the Explicit Messages
communication method.
The configuration method is set up with the bits0-3 in attribute 3. Please use the statically-assigned
IP configuration set up value “0” for those bits.
Attribute 3 of TCP/IP Interface Object: Configuration Method

14
Operation & Service Manual
Valve islands VM10 EtherNet/IP
07/2018
Construction & Design is subject to change © 2018 Norgren GmbH
Attribute 5 contains the configuration parameters required to operate as a TCP/IP node. At least
network address and network mask needs to be configured.
Attribute 5 of TCP/IP Interface Object: Interface Configuration
Next table shows the structure of the interface configuration attribute
Structure of Attribute 5: Interface Configuration

15
Operation & Service Manual
Valve islands VM10 EtherNet/IP
07/2018
Construction & Design is subject to change © 2018 Norgren GmbH
5. I/O connection via Assembly Object
The Assembly Object is used to bundle attributes of different objects, to use only one connection
exchanging I/O data. One instance is used for input data and one for output data.
5.1 Bit allocation valve stations
The following picture shows exemplarily a VM10 with 12 valve stations.
Valves are numbered ascending from left to right.
The following acronym is used to identify the valves and their solenoids.
Vn-s
n: Valve number [1, 16]
s: Solenoid [12, 14]
Example: V3-12 is used to describe solenoid 12 of the third valve

16
Operation & Service Manual
Valve islands VM10 EtherNet/IP
07/2018
Construction & Design is subject to change © 2018 Norgren GmbH
5.2 Input data (Assembly Object Instance: 101d)
The following table shows the bit allocation of the input data for VM10 with 8, 10, 12 and 16 valve
stations.
Valve stations
Bit
Function
16
12
10
8
7
6
5
4
3
2
1
0
Byte#
Byte#
Byte#
Byte#
0
0
0
0
Res
Res
Res
Res
UV-VB
OV-VB
UV-VA
OV-VA
Module status
1
V04-12
V04-14
V03-12
V03-14
V02-12
V02-14
V01-12
V01-14
Short Circuit/Overload
2
V08-12
V08-14
V07-12
V07-14
V06-12
V06-14
V05-12
V05-14
Short Circuit/Overload
3
V04-12
V04-14
V03-12
V03-14
V02-12
V02-14
V01-12
V01-14
Open Load
4
V08-12
V08-14
V07-12
V07-14
V06-12
V06-14
V05-12
V05-14
Open Load
1
V04-12
V04-14
V03-12
V03-14
V02-12
V02-14
V01-12
V01-14
Short Circuit/Overload
2
V08-12
V08-14
V07-12
V07-14
V06-12
V06-14
V05-12
V05-14
Short Circuit/Overload
3
N/A
N/A
N/A
N/A
V10-12
V10-14
V09-12
V09-14
Short Circuit/Overload
4
V04-12
V04-14
V03-12
V03-14
V02-12
V02-14
V01-12
V01-14
Open Load
5
V08-12
V08-14
V07-12
V07-14
V06-12
V06-14
V05-12
V05-14
Open Load
6
N/A
N/A
N/A
N/A
V10-12
V10-14
V09-12
V09-14
Open Load
1
V04-12
V04-14
V03-12
V03-14
V02-12
V02-14
V01-12
V01-14
Short Circuit/Overload
2
V08-12
V08-14
V07-12
V07-14
V06-12
V06-14
V05-12
V05-14
Short Circuit/Overload
3
V12-12
V12-14
V11-12
V11-14
V10-12
V10-14
V09-12
V09-14
Short Circuit/Overload
4
V04-12
V04-14
V03-12
V03-14
V02-12
V02-14
V01-12
V01-14
Open Load
5
V08-12
V08-14
V07-12
V07-14
V06-12
V06-14
V05-12
V05-14
Open Load
6
V12-12
V12-14
V11-12
V11-14
V10-12
V10-14
V09-12
V09-14
Open Load
1
V04-12
V04-14
V03-12
V03-14
V02-12
V02-14
V01-12
V01-14
Short Circuit/Overload
2
V08-12
V08-14
V07-12
V07-14
V06-12
V06-14
V05-12
V05-14
Short Circuit/Overload
3
V12-12
V12-14
V11-12
V11-14
V10-12
V10-14
V09-12
V09-14
Short Circuit/Overload
4
V16-12
V16-14
V15-12
V15-14
V14-12
V14-14
V13-12
V13-14
Short Circuit/Overload
5
V04-12
V04-14
V03-12
V03-14
V02-12
V02-14
V01-12
V01-14
Open Load
6
V08-12
V08-14
V07-12
V07-14
V06-12
V06-14
V05-12
V05-14
Open Load
7
V12-12
V12-14
V11-12
V11-14
V10-12
V10-14
V09-12
V09-14
Open Load
8
V16-12
V16-14
V15-12
V15-14
V14-12
V14-14
V13-12
V13-14
Open Load

17
Operation & Service Manual
Valve islands VM10 EtherNet/IP
07/2018
Construction & Design is subject to change © 2018 Norgren GmbH
5.3 Output data (Assembly Object Instance: 100d)
The following table shows the bit allocation of the output data for VM10 with 8, 10, 12 and 16 valve
stations.
Valve stations
Bit
16
12
10
8
7
6
5
4
3
2
1
0
Byte#
Byte#
Byte#
Byte#
0
V04-12
V04-14
V03-12
V03-14
V02-12
V02-14
V01-12
V01-14
1
V08-12
V08-14
V07-12
V07-14
V06-12
V06-14
V05-12
V05-14
0
V04-12
V04-14
V03-12
V03-14
V02-12
V02-14
V01-12
V01-14
1
V08-12
V08-14
V07-12
V07-14
V06-12
V06-14
V05-12
V05-14
2
N/A
N/A
N/A
N/A
V10-12
V10-14
V09-12
V09-14
0
V04-12
V04-14
V03-12
V03-14
V02-12
V02-14
V01-12
V01-14
1
V08-12
V08-14
V07-12
V07-14
V06-12
V06-14
V05-12
V05-14
2
V12-12
V12-14
V11-12
V11-14
V10-12
V10-14
V09-12
V09-14
0
V04-12
V04-14
V03-12
V03-14
V02-12
V02-14
V01-12
V01-14
1
V08-12
V08-14
V07-12
V07-14
V06-12
V06-14
V05-12
V05-14
2
V12-12
V12-14
V11-12
V11-14
V10-12
V10-14
V09-12
V09-14
3
V16-12
V16-14
V15-12
V15-15
V14-12
V14-14
V13-12
V13-14

18
Operation & Service Manual
Valve islands VM10 EtherNet/IP
07/2018
Construction & Design is subject to change © 2018 Norgren GmbH
6. Solenoid Object
Object Class: 100d
Instances: 8 stations 1…16
10 stations 1…20
12 stations 1…24
16 stations 1…32
Each solenoid is a separate instance of the Solenoid Object. The allocation between Instance ID
and solenoid is shown in the following table:
Valve 1…4
V04-12
V04-14
V03-12
V03-14
V02-12
V02-14
V01-12
V01-14
Instance ID
8
7
6
5
4
3
2
1
Valve 5…8
V08-12
V08-14
V07-12
V07-14
V06-12
V06-14
V05-12
V05-14
Instance ID
16
15
14
13
12
11
10
9
Valve 12…9
V12-12
V12-14
V11-12
V11-14
V10-12
V10-14
V09-12
V09-14
Instance ID
24
23
22
21
20
19
18
17
Valve 13…16
V16-12
V16-14
V15-12
V15-14
V14-12
V14-14
V13-12
V13-14
Instance ID
32
31
30
29
28
27
26
25
Following table shows all Instance Attributes of the Solenoid Object:
Attr.
ID
Acces
Rule
Name
Data
Type
Description
Schematic of
Values
1
Get/Set
Solenoid Value
Bool
Output point value
0=Off
1=On
3
Get/Set
Enable Diagnostics
Bool
Enables/Disables Diagnostics
(Channel diagnostics)
0=Disabled
1=Enabled
4
Get
Open load
Bool
Diagnostics Open Load
0=OK
1=Open Load
5
Get
Short Circuit / Overload
Bool
Diagnostics Short Circuit
0=OK
1=Short Circuit
6
Get/Set
Fault Action
Bool
Action taken on outputs value in
recoverable fault state
0=Fault Value Attribute
1=hold last state
7
Get/Set
Fault Value
Bool
Value for use with Fault Action
attribute
0=Off
1=On
8
Get/Set
Idle Action
Bool
Action taken on outputs value in idle
state
0=Idle Value Attribute
1=hold last state
9
Get/Set
Idle Value
Bool
Value for use with Idle Action
attribute
0=Off
1=On

19
Operation & Service Manual
Valve islands VM10 EtherNet/IP
07/2018
Construction & Design is subject to change © 2018 Norgren GmbH
7. Diagnostics and LEDs
7.1 Status LEDs
7.1.1 Status LEDs description
7.1.2 Link states for Port P1 and Port P2
7.1.3 Network Status LED (NS)
7.1.4 Module Status LED (MS)
LED type
Description
P1
Link Port 1 (TX/RX & Link)
P2
Link Port 2 (TX/RX & Link)
NS
Network Status
MS
Module Status
VA
Valves Power Supply Status
VB
Electronic Power Supply Status
Link Status
LED State
Link Connection Established
yellow
Link Communication Active
flashing yellow / green
Link Connection Not Established
off
Module Status
LED State
No Power
off
Connected
green
Not Connected
flashing green
Connection Timeout
flashing red
Duplicate IP n/a
red
Network Status
LED State
No Power
off
Device Operational
green
Standby n/a
flashing green
Recoverable fault
flashing red
Non-recoverable fault
red

20
Operation & Service Manual
Valve islands VM10 EtherNet/IP
07/2018
Construction & Design is subject to change © 2018 Norgren GmbH
7.1.5 Electronics Power Supply Status, LED (VB)
7.1.6 Valve Power Supply Status, LED (VA)
Electronics Power Supply States
LED State
Voltage O.K.
green
Undervoltage
flashing red
Overvoltage
red
Valve Power Supply States
LED State
Voltage O.K.
green
Undervoltage
flashing red
Overvoltage
red
This manual suits for next models
2
Table of contents
Other IMI NORGREN Controllers manuals
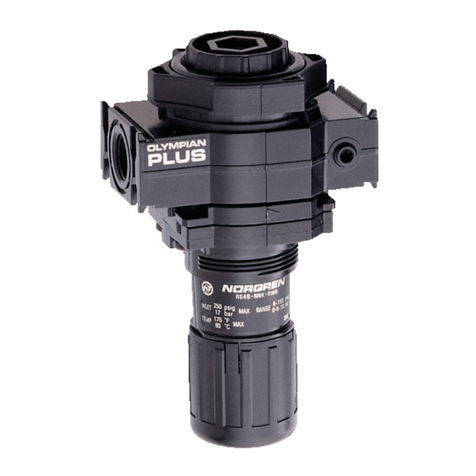
IMI NORGREN
IMI NORGREN R64G Series Installation and operating instructions
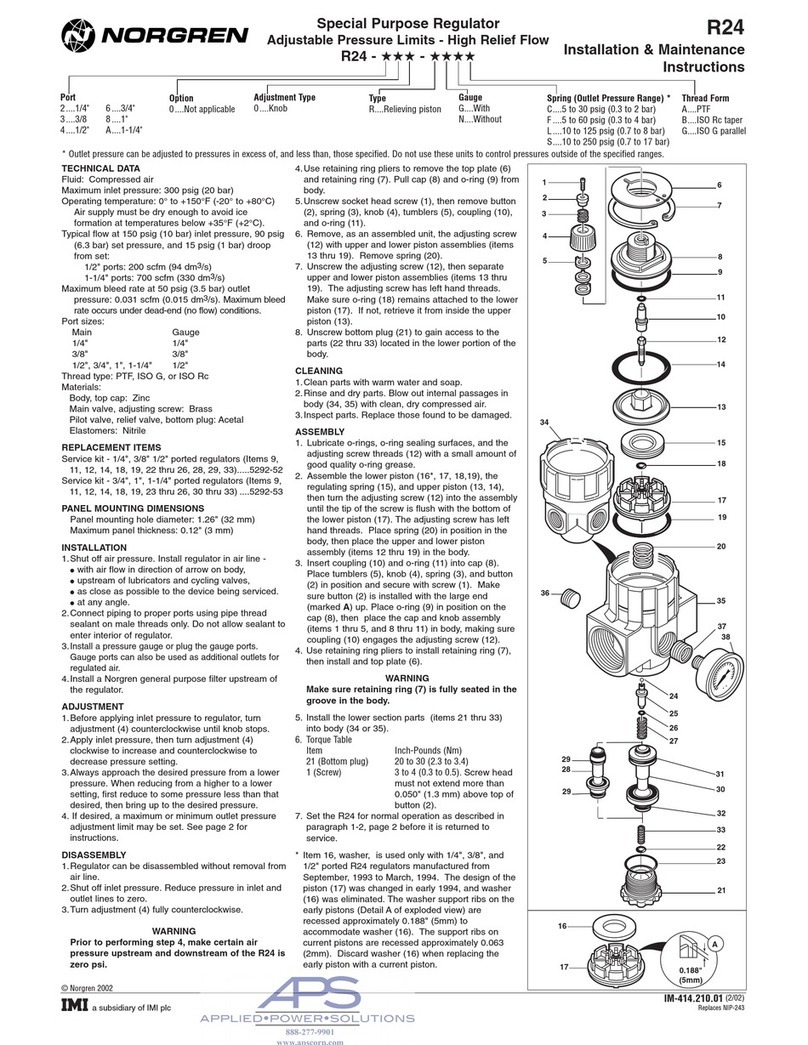
IMI NORGREN
IMI NORGREN R24 Installation and operating instructions
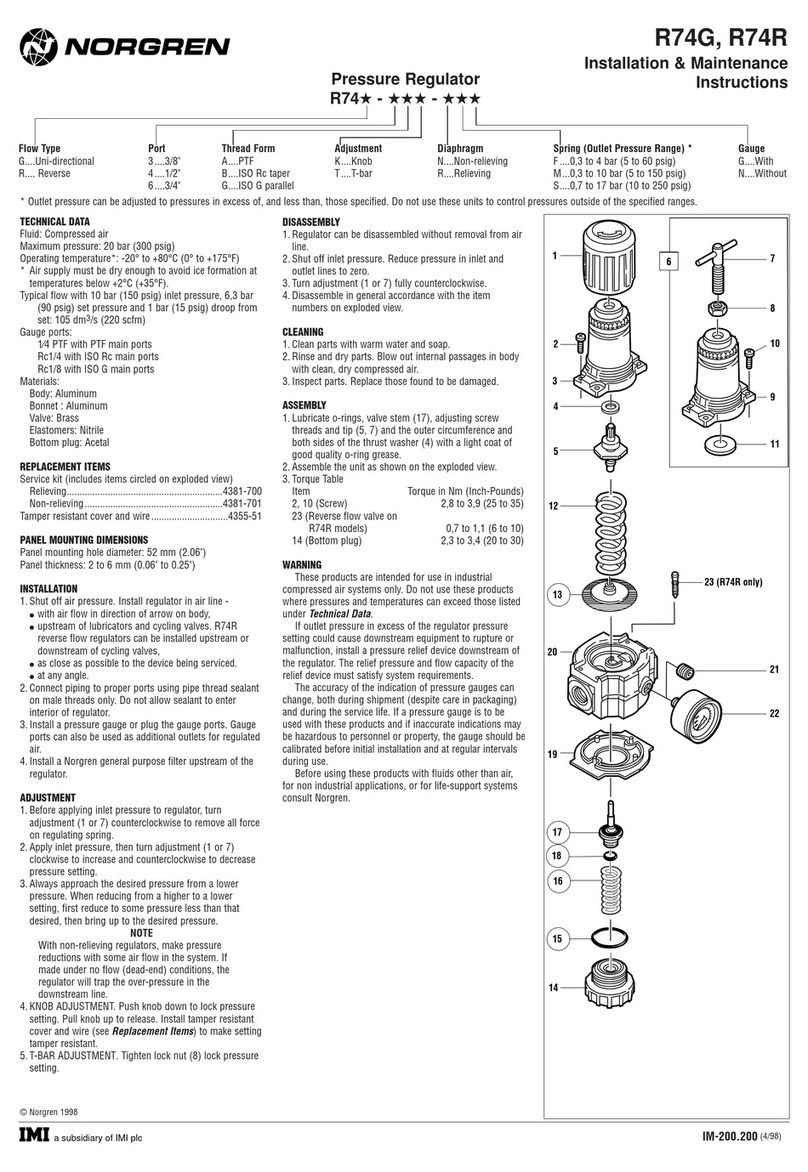
IMI NORGREN
IMI NORGREN R74G Installation and operating instructions

IMI NORGREN
IMI NORGREN B38 Installation and operating instructions
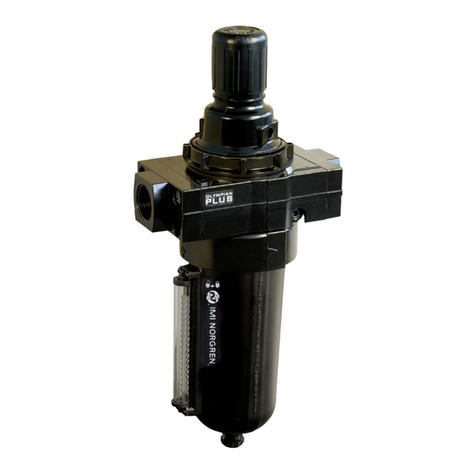
IMI NORGREN
IMI NORGREN B68G Installation and operating instructions