Weir SPM Flow Line User manual

SPM®Flow Line
Safety Restraint
System (FSR)
Installation Guide

2
Contents
WARNING 3
SAFETY INFORMATION 3
DUTY & PRESSURE RATINGS CHART 5
DUTY RATING & COLOR CODE CHART 6
CHEMICAL COMPATIBILITY CHART 7
DEFINITIONS 7
GENERAL INFORMATION 9
GENERAL INSTALLATION NOTES FOR FSR SYSTEM 13
INSTALLING FSR COMPONENTS
- “RIB” INSTALLATION 14
INSTALLING FSR COMPONENTS
- CORRECT RIB CONFIGURATION 18
INSTALLING FSR COMPONENTS
- REQUIRED RIB LOCATIONS 20
INSTALLING FSR COMPONENTS
– SPINE LINKING 23
ANCHOR CROSSOVER ASSEMBLY 26
INSTALLING FSR COMPONENTS
– ANCHOR CROSSOVER ASSEMBLY
(PRIMARY METHOD) 27
INSTALLING FSR COMPONENTS – NON-ANCHOR
CROSSOVER ASSEMBLY (ALTERNATIVE METHOD) 28
SECURING FSR SYSTEM ENDS 34
FINAL FSR SYSTEM INSPECTION 36
LINKED FSR MEASUREMENTS 37
RECOMMENDED SEQUENCE WHEN INSTALLING
SPM®FSR COMPONENTS 38
INSPECTION 39
LIMITED WARRANTY AND LIMITATIONS ON WARRANTY 40
NOTES 41

3
WARNING !
FAILURETO READ, UNDERSTAND AND FOLLOWTHIS
INSTRUCTION GUIDE MAY RESULT IN SEVERE PERSONAL
INJURY OR DEATH.
THE USE OF PRESSURIZED COMPONENTS IN OIL FIELD
OPERATIONS IS INHERENTLY DANGEROUS. PERSONNEL
WORKING AROUND ENERGIZED EQUIPMENT AND FLOW
LINES SHOULD USE EXTREME CARE AND OBSERVE ALL
APPLICABLE SAFETY PRECAUTIONS.
PROPER USE OFTHIS DEVICE CAN REDUCE BUT NOT
ELIMINATETHE RISK OF SEVERE PERSONAL INJURY OR
DEATH. EVEN WITH SPM®FSRs, SEVERE PERSONAL INJURY
OR DEATH CAN RESULT FROM DEBRIS AND SHRAPNEL
SHOULD A RUPTURE OCCUR.
THIS IS NOT A LIFTING DEVICE, NOR SHOULD IT BE
INSTALLED BY ANYONE OTHERTHAN PERSONNEL
SPECIFICALLYTRAINED IN WEIR OIL & GAS PROCEDURES.
SAFETY INFORMATION
Important! Read before attempting to use.
• It is critical that, since most SPM®products generate, control or
direct pressurized fluids, those who work with these products be
thoroughly trained in their proper application and safe handling.
It is also critical that these products be used and maintained
properly. Any components that show obvious signs of damage or
wear should be removed from service immediately.
• SPM®Flow Line Safety Restraint components are not intended
for individual use. SPM®FSR Ribs and Spines are not lifting
devices and should never be used as such. Any Ribs or Spines
that have been subjected to any loads should be immediately
taken out of service.

4
• SPM®FSRs are considered “single-use” items. This means that,
while these components can be installed multiple times out
in the field, if they are actually employed (that is, subjected to
trauma as in the event of a union failing or a pipe rupturing), then
the affected FSR components need to be replaced immediately.
• Always keep ALL personnel away from the flow line while under
pressure. This applies even when a restraint system such as
SPM®FSR is in place.
• Installation of individual SPM®FSR components as well as
the system itself should be done by Weir Oil & Gas personnel
or persons qualified by Weir Oil & Gas to do so. Training is
available from Weir Oil & Gas, contact 1-800-342-7458 for more
information.

5
DUTY & PRESSURE RATINGS CHART
Size & Pressure Ratings
Light Duty
Nominal Iron Size Max Working Pressure (PSI)
2” 15,000
3” 7,500
4” 5,000
Medium Duty
Nominal Iron Size Max Working Pressure (PSI)
2” 20,000
3” 15,000
4” 10,000
Heavy Duty
Nominal Iron Size Max Working Pressure (PSI)
2” 20,000
3” 15,000
4” 15,000
Above pressure ratings are valid for either gas or liquid frac media, and
apply to both non-waterproof and waterproof SPM®FSR models.
NOTE: SPM®FSR Ribs & Spines are rated for specific duty ratings.
Ribs should NEVER be substituted for Spines. Ribs & Spines from
different duty ratings should not be mixed.
NOTE: SPM’s Medium Duty FSR System is rated for use on 4”
treating iron up to 10,000 psi. In instances where the product
is required for 4” 1502 lines, a double wrapping technique may
be used that will provide acceptable load rating for the flow line.
Please contact Weir Oil & Gas Engineering at 1-800-342-7458 for
more details regarding the double wrap procedure or if you have
further questions.

6
DUTY RATING & COLOR CODE CHART
Color Codes:
Light Duty
SPM®FSR Ribs Yellow
SPM®FSR Spines White
Medium Duty
SPM®FSR Ribs Red
SPM®FSR Spines Blue
Heavy Duty
SPM®FSR Ribs Orange
SPM®FSR Spines Grey

7
CHEMICAL COMPATIBILITY CHART
Chemical FSRs
Acids *See note
Alcohols OK
Strong Alkalis OK
Ethers OK
Hydro-Carbons OK
Ketones OK
Oils – Crude OK
Oils – Lubricating OK
Soaps / Seawater OK
Water / Seawater OK
Weak Alkalis OK
*Acid Compatibility – Hydrochloric Acid (HCl): Concentrations
up to 36% acceptable for up to 8 hours. Hydrofluoric Acid (HF):
Concentrations up to 10% acceptable for up to 8 hours. (Note that
all chemical exposures are assumed to be at ambient temperature.)
For other acids or chemicals not stated, please contact Weir Oil &
Gas Engineering at 1-800-342-7458.
DEFINITIONS
Anchor Line – Anchor lines are similar to main lines; however,
instead of being continuously installed along the flow line like main
lines, anchor lines are attached to a single point on the flow line,
such as an anchor crossover, and run to a properly rated object
away from the flow line. (Refer to Securing SPM®FSR System
Ends later in this document) Only appropriately rated Spines
should ever be used to make up anchor lines. Reference the
previous product rating color code chart for more information.

8
Anchor Crossover Assemblies – Special crossovers, similar to
standard integral crossovers, but designed with anchor clamps/
shackles that link SPM®FSR main lines together. Anchor crossover
assemblies should be installed on either end of a group of
swivels/swivel assemblies when using the primary installation
method. They are designed to reduce the movement of the swivel
assemblies in the event of a failure. Anchor crossovers should also
be used as the connection point of the anchor line to the flow line
when using the primary method of installation. Reference primary
and secondary installation methods found later in this document.
SPM®FSR – Abbreviation for SPM®Flow Line Safety Restraints.
SPM®FSR Rib – SPM®FSR Ribs are engineered synthetic loops
that are always 4’ long in Light Duty and Medium Duty, and 5’ long
in Heavy Duty. They are designed to be installed at each union
connection on a flow line, on swivel elbows, and mid-way through
long lengths of pipe. They are looped around the union connection,
and then the main SPM®FSR line, comprised of appropriately
rated Spines, is threaded through the Ribs in order to create a
continuous safety line (main line). Reference the previous product
rating color code chart for more information.
SPM®FSR Spine – SPM®FSR Spines are engineered synthetic
loops that can range from 4’ to 20’ in length. They make up the
main line of the SPM®FSR system as well as the anchor lines.
Spines are linked together to create the main line, and then both
ends should always be secured to immovable anchor points at
each end of the SPM®FSR installation. Reference the previous
product rating color code chart for more information. Available in
the following lengths: 4’, 6’, 8’, 10’, 15’, and 20’.
Main Line – Comprised of multiple SPM®FSR Spines, this is
the safety restraint line that is installed along the flow line. Ribs
are looped around the union connection, and then the main line,
comprised of appropriately rated Spines, is threaded through the
Ribs in order to create a continuous main line. The main line should
run perpendicular along side the flow line, never wrapping around
it. Reference the previous product rating color code chart for more
information.

9
GENERAL INFORMATION
Note: It is critical that, since most SPM®products generate,
control or direct pressurized fluids, those who work with these
products be thoroughly trained in their proper application and
safe handling. It is also critical that these products be used and
maintained properly.
GENERAL:
SPM®FSRs are intended to help contain high-pressure piping
and flow line components in case of rupture or excessive impulse
during the pumping process. When flow lines fail, whether it is
due to excessive pressure, faulty connections, worn components,
trauma to the piping connections, or otherwise, the results can be
devastating and catastrophic to both equipment and people. The
metal components that were previously being subjected to up to
20,000 psi of internal pressure are suddenly and instantly forced
to relieve themselves of the stored energy. In a failure there could
be hundreds or even thousands of pounds of iron pipe flailing
about in an unrestrained condition. In that scenario, there is a high
likelihood of severe personal injury or death. SPM®FSRs were
designed to reduce, but do not eliminate, that risk.
SPM®FSR is available in two different application configurations:
non-waterproof and waterproof. The waterproof version may be
desired in applications where increase in weight due to absorption
of water from the surrounding environment is a concern.
Waterproof and non-waterproof SPM®FSR components are both
rated to their listed duty rating.
IDENTIFICATION:
SPM®Safety Restraints are permanently identified on each of the
individual components. All metal components have full traceability.
The restraint components are identified with their VENDOR
ID (Weir SPM), PART NUMBER, SIZE, SERIAL NUMBER and
WATERPROOF (if applicable) recorded on the label permanently
attached to each restraint. NOTE: If this tag becomes removed
from component part or is no longer legible, discard restraint.

10
CARE:
Maintenance & Storage –
SPM®Safety Restraints generally do not require any special
maintenance to keep them in service. Even though they are water
resistant, the components should NOT be used underwater or
submersed in water. If they are in an environment where they get
wet, it is recommended that they are wiped dry after each use
with a clean, dry cloth.
It is recommended to store SPM®Safety Restraints and associated
equipment in a dry place. However, exposure to water will not
reduce the load capacity of the components; it only will make them
slightly heavier. This does not apply to waterproof SPM®FSRs.
TEMPERATURE RATING (Standard*):
Minimum: -30˚ C / -22˚ F
Maximum: 100˚ C / 212˚ F
*For higher temperature applications contact Weir Oil & Gas
Engineering at 1-800-342-7458.
APPLICATION:
SPM®Safety Restraint assemblies are designed to help reduce
the effect of failures on pressure pumping jobs running energized
fluid. This system has completed simulated field test at 15,000 psi
with nitrogen, utilizing approximately 125 linear feet of 3”- 1502
components, and has effectively performed in multiple flow line
ruptures. The SPM®Safety Restraint assemblies are effective
when used with either gas or liquid frac media.
Because non-energized systems are considerably less volatile,
SPM®FSR will also work with any flow line running non-energized
fluids provided they are within the previously mentioned duty
rating guidelines.

11
INSPECTING SPM®FSR COMPONENTS:
Inspect each component before every use. Also, to ensure safety,
qualified personnel should inspect the complete installation before
every use.
a) SPM®Safety Restraints (Spines & Ribs) –
The SPM®FSR Spines and Ribs are designed so failures are
normally visible. If there are any signs of damage, the affected
components should be replaced. Remove SPM® Safety Restraints
from service if inspection indicates the following damage:
1) Any damage to the SPM®FSR cover where internal red-
striped white core yarns are exposed.
(This includes cuts, holes, tears, snags, abrasions or other
damage to cover).
2) The SPM®Safety Restraint ID tag is missing or has become
illegible.
3) Knots or other modifications to any part of the SPM®FSR.
4) Melting, charring, or other indications of excessive heat to
any part of the SPM®FSR.
5) Acid, caustic burns or other signs of chemical deterioration
to the SPM® FSR.
6) Any SPM® FSR that has been stretched beyond its original
design length, deformed, or otherwise misshapen, is
visually noticeable by the outer cover being frayed and
discolored.
7) Any other visible damage which causes doubt as to the
strength of the SPM® FSR.
Note: Upon removal, note the serial number for your records, cut
the restraint in half, remove the tag, and discard.

12
b) Anchor Crossover Assembly –
Remove Anchor Crossovers from service if inspection indicates the
following damage:
1) Excessive rust or corrosion prevents the crossover
from operating properly.
2) Excessive wear on the OD or ID of crossover.
3) Any damage to integral female threads that would
prevent proper installation.
c) Anchor-“C”-type & “D”-type Shackles – Remove shackles from
service if inspection indicates the following damage:
1) Visible signs of damage or galling on screw threads
that would prevent proper operation.
2) The metal shackles show excessive wear.
3) The shackle’s screw pin is damaged and cannot be
fully installed into the mating threads.

13
GENERAL INSTALLATION NOTES FOR
SPM®FLOW LINE SAFETY RESTRAINT
SYSTEM (FSR)
Installation of individual SPM® FSR components as well as the
system itself should be done by Weir Oil & Gas personnel or
persons qualified by Weir Oil & Gas to do so. Training is available
from Weir Oil & Gas. Contact us at 1-800-342-7458 for more
information.
Any misuse of the SPM® FSRs such as lifting or towing, or
improper installation shall void any and all warranties and may
cause injury or death. Further, any mishandling of the SPM® FSRs
such as not following the maintenance and care instructions
contained in this guide, including but not limited to exposing the
SPM® FSRs to excessive heat, shall void all warranties.
Prior to installation, verify that the tag indicates its recent
inspection date. For most efficient setup, install SPM® FSR Ribs
and Spines in unison with the flow line rig-up. After SPM® FSR is
installed, check every connection, every link, and every SPM® FSR
component to ensure that there is a continuous connection from
anchor point to anchor point.
• As a note for standardization the annual inspection and tag
punch represents when the inspection is done.
After the complete SPM® FSR system is installed, make sure:
a) All SPM® FSR Ribs are installed as tight as possible around
flow line components.
b) All main line and anchor line SPM® FSR Spines are as tight as
possible from anchor point to anchor point.
Always keep ALL personnel away from the flow line while under
pressure. This applies whether or not a restraint system is
installed.

14
INSTALLING SPM®FSR COMPONENTS
- "RIB" INSTALLATION
STEP 1
Begin by positioning the Rib beneath flow line as shown. The Rib
profile should straddle the union assembly.
NOTE THAT PIPING MIGHT REQUIRE ELEVATION IN ORDER
TO FIT THE RIB BENEATH - SEE PAGE 22 “RECOMMENDED
ASSEMBLY AID” FOR COMPLETE DETAILS.
STEP 2
Next, bring end “A” up and over piping and union assembly. Insert
end “A” down through end “B” opening. Pull “A” back through to
original side as shown.
END “A”
END “B”
At this point keep
END “B” stationary
Piping
Union Assembly
SPM®FSR™Rib
END “A”
END “B”

15
STEP 3
Continue to bring end “A” back around to form a second loop. Rib
profile should still evenly straddle union assembly as shown.
STEP 4
Draw end “A” even with “B” end as shown. Ensure that the Rib
profile fits snugly around union assembly (or other applicable
connection). This Rib is now ready for Spine installation. See Page
10-13 for correct spine installation.
NOTES:
a) Rib profiles must always STRADDLE each side of wing union
connection. This configuration provides the most purchase to
contain flow line components on either side if the union fails.
END “A”
END “B”
END “A”
END “B”

16
b) SPM® FSR Ribs can NEVER be substituted for SPM® FSR
Spines.
c) No SPM® FSR Ribs are required, or should be used, on anchor
lines (Anchor lines are the separate SPM® FSR lines that secure
the entire SPM® FSR system to separate anchor points).
d) SPM®FSR Ribs should be installed as tightly as possible.
Excessive play in the overall SPM® FSR System could allow
components to release during line failure.
e) In the limited instance where a single SPM® FSR Rib is not long
enough to fit around a large component, SPM® FSR Ribs can
be “linked” if necessary, but never tied together. For complete
information on linking, see linking instructions on pages 23-25 of
this Installation Guide.

17
RECOMMENDED ASSEMBLY AID
It is typically necessary to raise the flow line piping in order to
insert Ribs between union connections and the ground. Never
attempt to lift piping manually. The suggested method is to use
a “pipe jack”. A secondary method is to use a lever and fulcrum.
Place lever under flow line as shown and temporarily lift piping to a
minimal height using the following guidelines for reference:
a) Do not lift piping more than 6-8 inches. More than this increases
the potential of loosening the union seal connection.
b) Never extend any part of your body underneath the piping while
it is elevated.
c) Sometimes an opposing force is required from the side opposite
the lever. A second lever may be used.
d) Make sure that piping is still in straight line after lowering back
to ground. If piping or components are askew, there is potential
of leakage through union assemblies.
e) Do not lift piping while flow line is under pressure.
Lever
Fulcrum
6”- 8” Max Lift
Preferred Method-
“Pipe Jack”
Downward Force

18
INSTALLING SPM®FSR COMPONENTS
- CORRECT RIB CONFIGURATION
(Shown with SPM®FSR Spine installed)
PRIMARY Method
This is the recommended method of installing SPM®FSR Ribs.
ROTATE “A” and “B” ends 270° from flat before installing SPM®
FSR Spine.
• This takes up extra slack
• Makes connection more secure
Rotate 270°
(Common on 2” Pipe)
SPM®FSR Rib
SPM®FSR Spine

19
SECONDARY Method
Use this method only when there is not enough slack in the RIB
material to allow for an additional twist. ROTATE “A” and “B” ends
only 90° - 180° from flat before installing SPM®FSR Spine.
SPM®FSR Ribs should be installed as tight as possible.
Excessive play in the overall system could allow components
to release during failure.
SPM®FSR Rib
SPM®FSR Spine
Rotate 90°-180°
(Common on 3” & 4” Pipe)

20
INSTALLING SPM®FSR COMPONENTS
- REQUIRED RIB LOCATIONS
UNION CONNECTIONS
SPM®FSR Ribs should be installed on EVERY union connection
on the flow line (one Rib per union). The Rib envelope must always
straddle both sides of the union in order to help contain each end
of the adjoining pipes/components.
FLOW LINE COMPONENTS
Virtually all flow line components utilize two wing union
connections – usually male x female. Therefore, most flow line
components (check valves, plug valves, etc.) require SPM®FSR
Ribs installed at each end as shown
Table of contents
Popular Security Sensor manuals by other brands
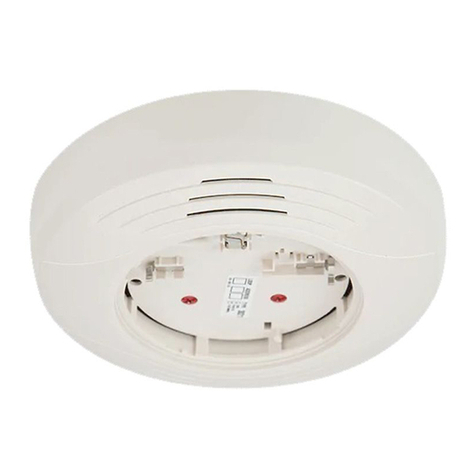
System Sensor
System Sensor B224RB Installation and maintenance instructions
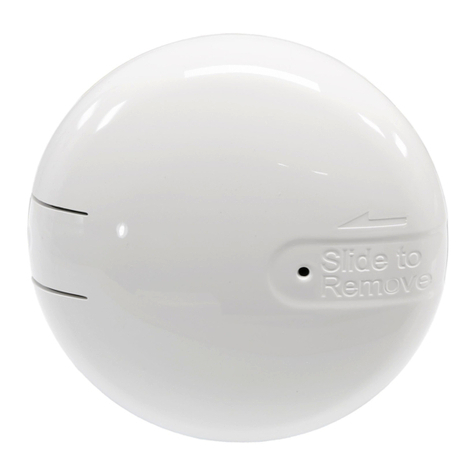
Nortek Security & Control
Nortek Security & Control 2GIG e Series quick start guide
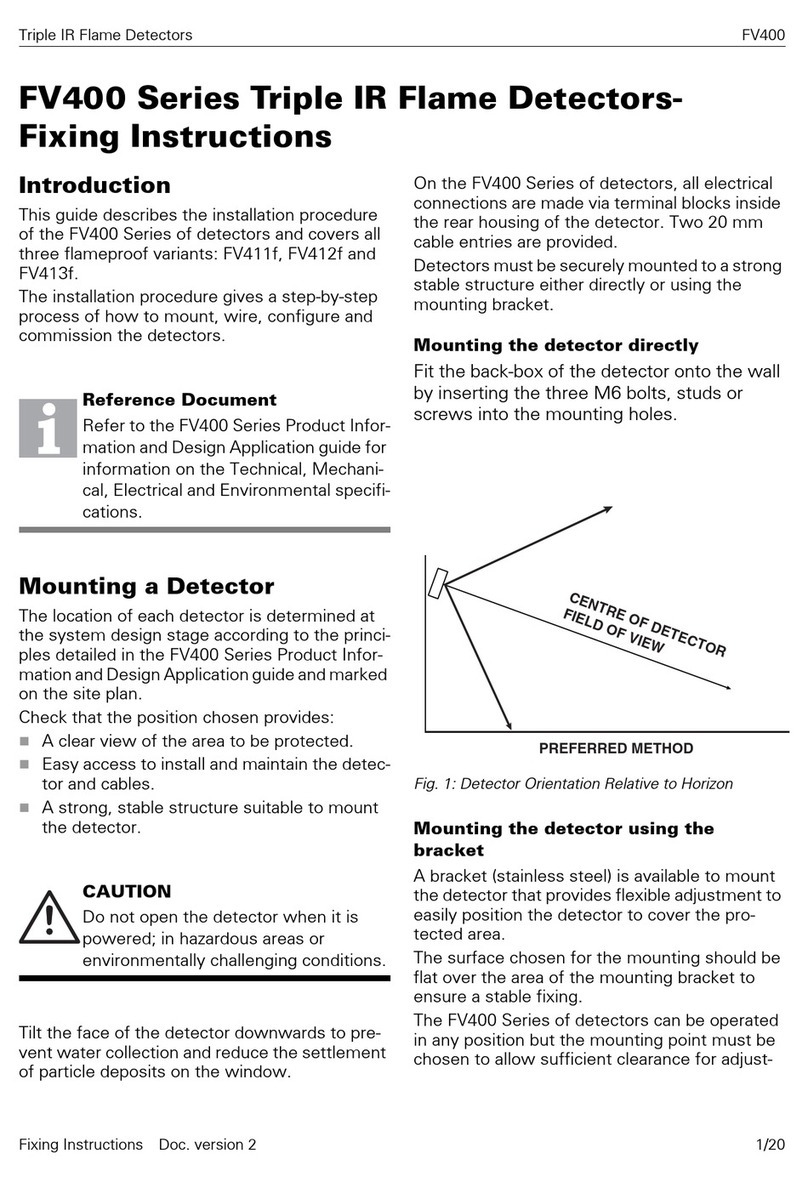
ZETTLER
ZETTLER FLAMEVision FV400 Series Fixing instructions
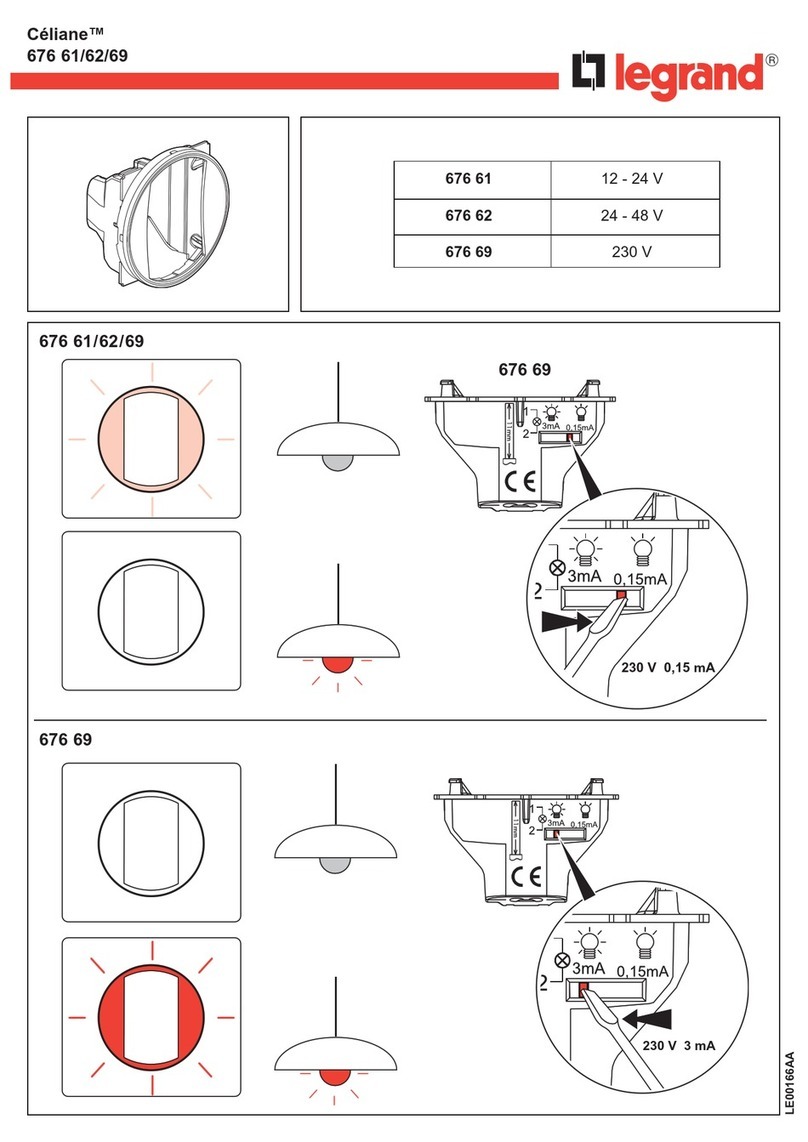
LEGRAND
LEGRAND Celiane 676 61 instructions

Teledata
Teledata SF2000E quick start guide
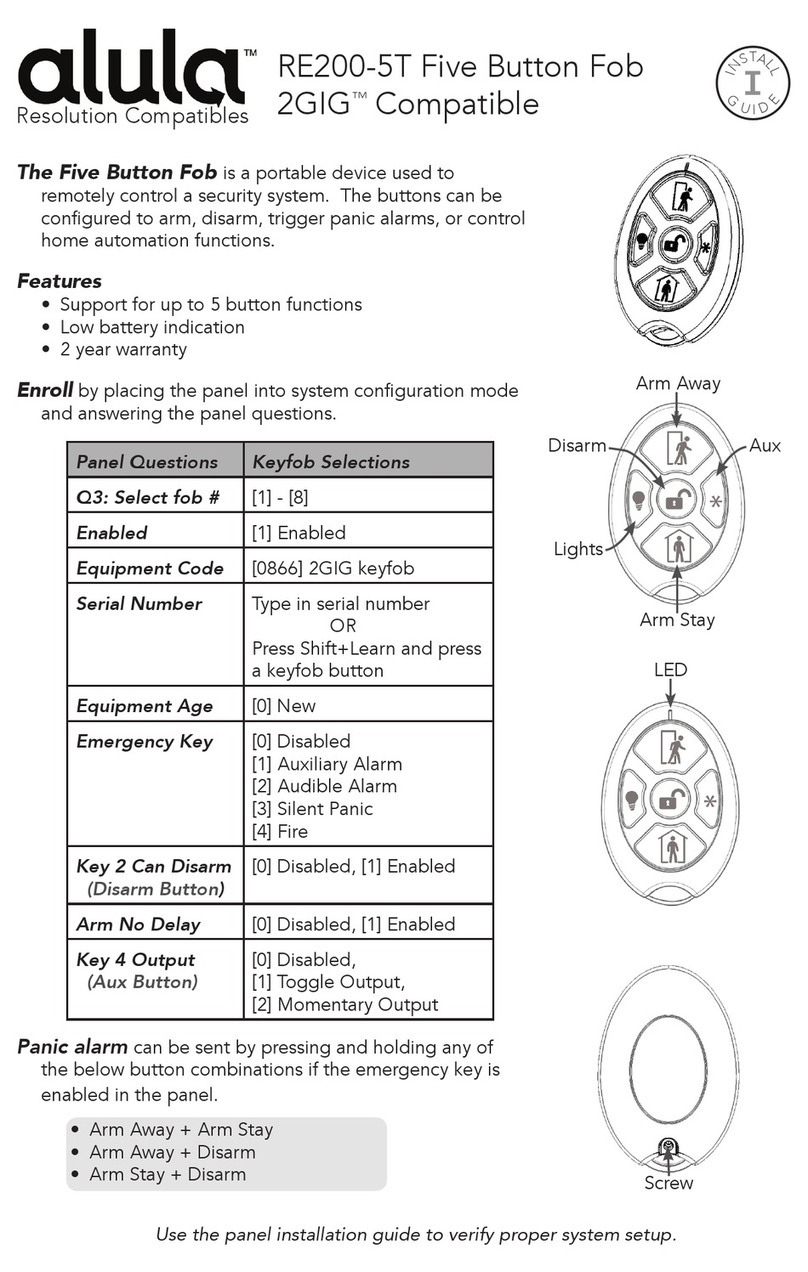
Alula
Alula RE200-5T quick start guide
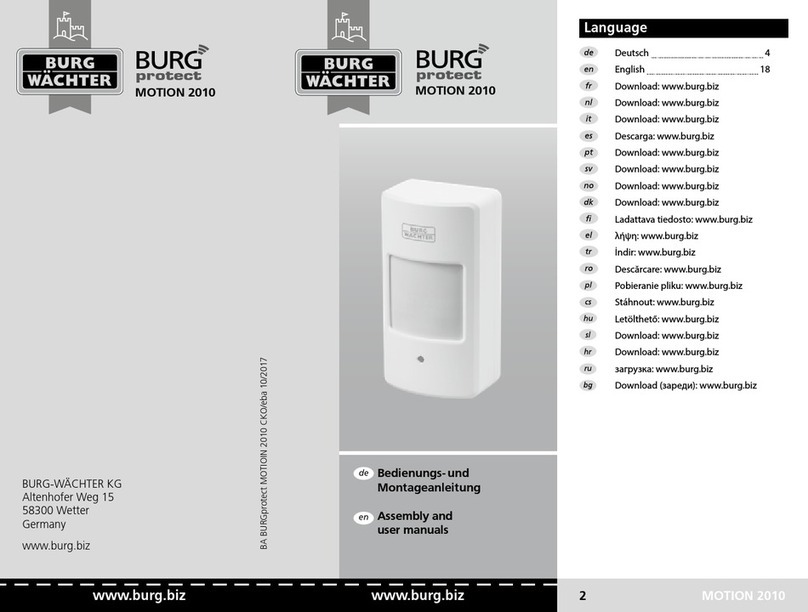
Burg Wächter
Burg Wächter MOTION 2010 Assembly and user's manual

teko
teko Astra-621 user guide
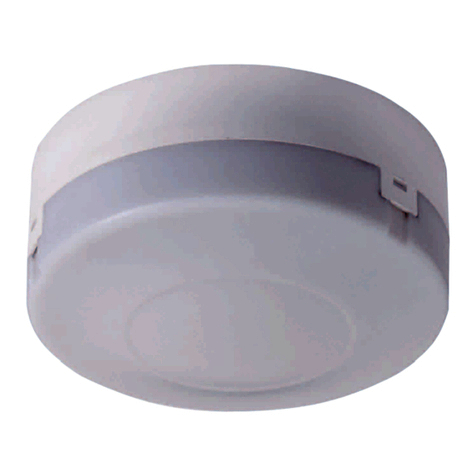
Lexing
Lexing LX-MV-360S10-A instructions
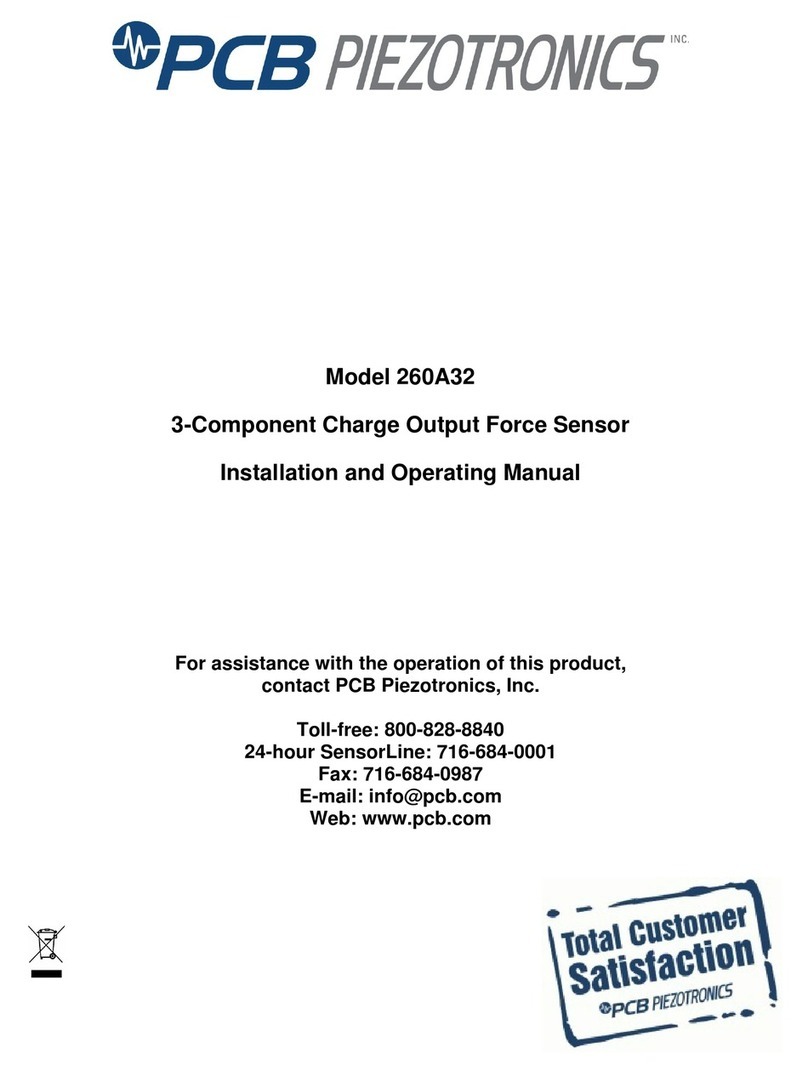
PCB Piezotronics
PCB Piezotronics 260A32 Installation and operating manual
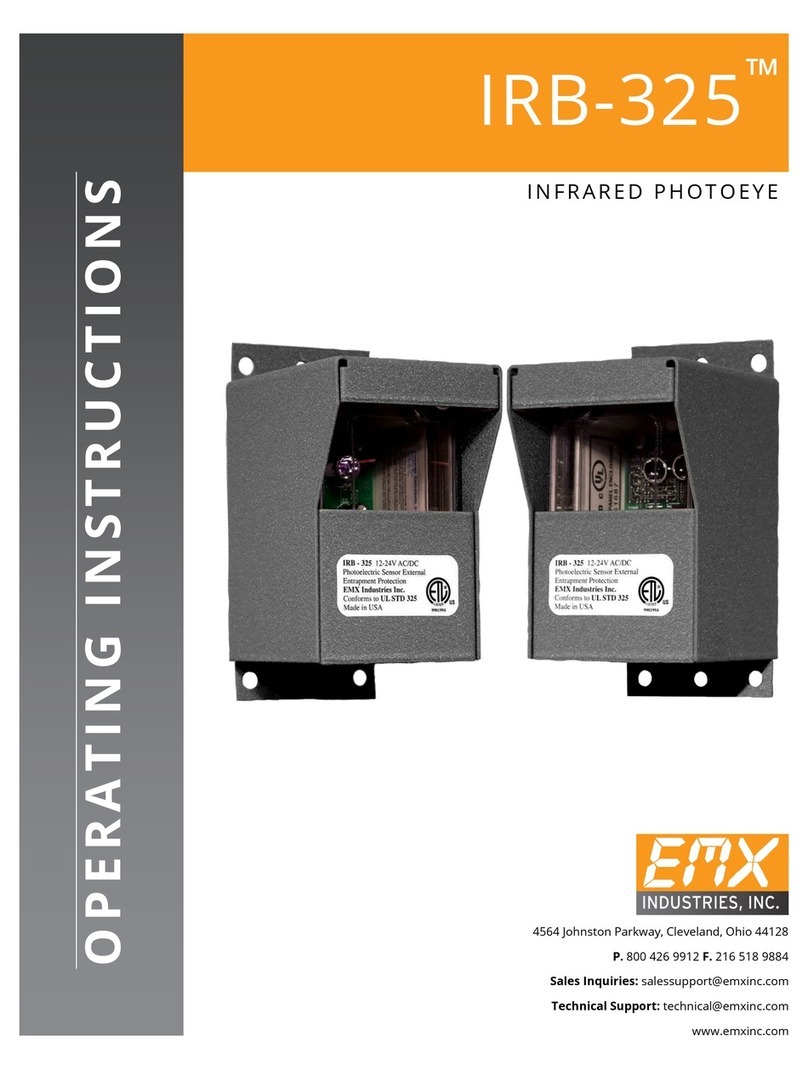
EMX
EMX IRB-325 operating instructions
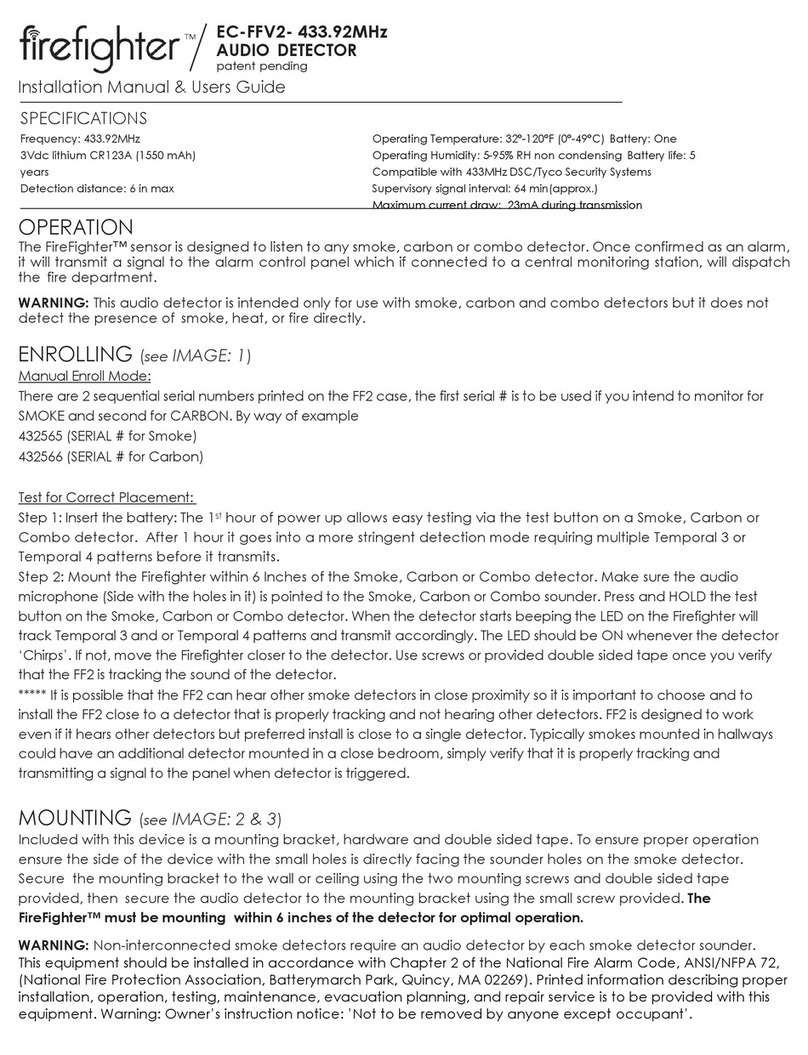
Firefighter
Firefighter EC-FFV2 Installation manual & users guide