WEISS WSG 32 Technical document

Mounting and Operating Manual
Electrical Compact Gripper WSG 32
Firmware Version: 4.0.0
Hardware Version: 1
July 2015


- 1 -
Contents
1Introduction ...................................................................................................... 3
2About this manual ............................................................................................. 4
2.1 Applicable documents ..................................................................................................4
2.2 Target audience............................................................................................................4
2.3 Notation and symbols...................................................................................................4
3Basic safety notes ..............................................................................................6
3.1 Intended use ................................................................................................................6
3.2 Environmental and operating conditions.......................................................................6
3.3 Product safety ..............................................................................................................6
3.3.1 Protective equipment............................................................................................................ 6
3.3.2 Constructional changes, attachments, or modifications....................................................... 7
3.3.3 Special standards................................................................................................................... 7
3.4 Personnel qualification .................................................................................................7
3.5 Safety Considerations ...................................................................................................7
3.6 Notes on particular risks ...............................................................................................7
4Warranty ........................................................................................................... 9
5Scope of delivery ............................................................................................. 10
6Accessories ...................................................................................................... 11
7Technical Data ................................................................................................. 12
7.1 Outer dimensions .......................................................................................................12
7.2 Nominal mechanical data ...........................................................................................13
7.2.1 Mechanical Finger Load....................................................................................................... 14
7.2.2 Gripping force...................................................................................................................... 15
7.3 Nominal electrical data...............................................................................................17
7.3.1 Fuse...................................................................................................................................... 18
7.3.2 Power supply and CAN-Bus (optional) ................................................................................ 18
7.3.3 Ethernet............................................................................................................................... 18
7.3.4 CAN-Bus (optional) .............................................................................................................. 19
7.3.5 Base jaw with sensor port ................................................................................................... 20
7.4 Name plate ................................................................................................................22
8Installation ...................................................................................................... 23
8.1 Installation instructions ..............................................................................................23
8.2 Mechanical connection...............................................................................................23

- 2 -
8.3 Electrical connection...................................................................................................24
8.4 Installation of the fingers............................................................................................26
8.5 Initial startup..............................................................................................................26
8.6 Changing the IP address and using DHCP .....................................................................29
9Operation ........................................................................................................ 30
9.1 Operating software ....................................................................................................30
9.2 Memory card..............................................................................................................30
9.3 Boot process ..............................................................................................................31
9.4 Display of operating state...........................................................................................31
9.5 Status word and gripper state.....................................................................................33
9.5.1 Status word.......................................................................................................................... 33
9.5.2 Gripper state........................................................................................................................ 34
9.6 Homing the module....................................................................................................36
9.7 Gripping, part detection and grip monitoring ..............................................................36
9.8 Software limit switch..................................................................................................37
9.9 Fast Stops requiring acknowledgment.........................................................................38
9.10 Log memory ...............................................................................................................39
9.11 Thermal monitor ........................................................................................................39
9.12 Monitoring the drive current ......................................................................................40
9.13 Monitoring the supply voltage ....................................................................................40
9.14 Configuration and diagnosis via the web interface.......................................................41
9.15 Access restrictions for the web user interface..............................................................42
9.16 Command interface ....................................................................................................43
9.17 Scripting.....................................................................................................................44
9.18 Resetting the configuration.........................................................................................44
9.19 Implementing the gripping process .............................................................................44
10 Maintenance and cleaning ............................................................................... 47
11 Troubleshooting .............................................................................................. 48
11.1 The gripper jaws don’t move.......................................................................................48
11.2 Module stops abruptly................................................................................................48
11.3 No connection to the web interface ............................................................................49
12 EC Declaration of Incorporation ....................................................................... 50

- 3 -
1Introduction
The WSG 32 is an electrical 2-Finger Compact Gripper. It has an integrated control unit supporting the Inter-
faces: Ethernet TCP/IP, CAN-Bus (optional), PROFINET (optional) and Modbus/TCP (optional). Figure 1
shows the components and connectors of the module. The configuration of the module is done via a Web-
Interface supporting almost every common web browser. Furthermore, the WSG 32 comes standard with a
sensor port in the base jaws. Here gripper fingers can be connected with integrated sensors, which are
evaluated directly from the gripper control. Weiss Robotics and authorized distributors provide standard-
ized finger as accessories, which work directly with the gripper control. For more information, please con-
tact Weiss Robotics.
Figure 1: Components and connectors of the WSG 32

- 4 -
2About this manual
This instruction is an integral part of the product and contains important information for a safe and proper
assembly, commissioning, operation, maintenance and helps for an easier trouble shooting.
Before using the product, read and note the instruction, especially chapter 3 "Basic safety notes". This
manual is exclusively valid for the gripper type WSG 32.
2.1 Applicable documents
For more detailed information about the operation of this module, please see the following documents
which are available in PDF format on both the accompanying CD as well as via the WSG web interface:
WSG Command Set Reference Manual - Description of the binary command protocol (TCP/IP, CAN-
Bus)
WSG GCL Reference Manual –Description of the text based command protocol (TCP/IP)
WSG Fieldbus Interface Manual - Description of the fieldbus interface (PROFINET, Modbus/TCP)
WSG Scripting Reference Manual - Description of the optional script interpreter for the gripper
control system
Please find additional information about the warranty in our general terms and conditions, available online
at www.weiss-robotics.com.
2.2 Target audience
Target audience for these instructions are plant manufacturers and operators who keep this and other
documents supplied to the personnel at all times and also ask to read and observe particularly the safety
instructions and warnings.
In addition, it is aimed at professionals and technicians who read this manual, while they should particularly
observe the safety and warning notes at all times.
2.3 Notation and symbols
For better clarity, the following symbols are used in this manual:
Functional or safety-related information. Failure to comply may jeopardize the safety of per-
sonnel and equipment, damage the device or impair the function of the device.
Additional information for a better understanding of the facts described.

- 5 -
Reference to further information.

- 6 -
3Basic safety notes
3.1 Intended use
The module was designed to grip and to temporarily and securely hold work pieces and objects.
The module is intended for installation in a machine/system. The requirements of the applicable
guidelines must be observed and complied with.
The module may be used only in the context of its defined application parameters.
To use this unit as intended, it is also essential to observe the technical data and installation and
operation notes in this manual and to comply with the maintenance intervals.
3.2 Environmental and operating conditions
The module may only be used within its defined application parameters.
It must be ensured that the module and the top jaws are sufficiently dimensioned according to the
use case.
It must be ensured that the environment is clean and the ambient temperature corresponds to the
specifications catalogue. Please observe the maintenance instructions (see chapter 10).
It must be ensured that the environment is free from splash and vapours as well as from abrasion
or process dust. Excepted are modules that are specifically designed for dirty environments.
3.3 Product safety
Dangers arise from the module, if e.g.:
The module is not used in accordance with its intended purpose.
The module is not installed or maintained properly.
The safety and installation notes are not observed.
Avoid any manner of working that may interfere with the function and operational safety of the module.
Wear protective equipment.
3.3.1 Protective equipment
Provide protective equipment per EC Machine Directive

- 7 -
3.3.2 Constructional changes, attachments, or modifications
Additional drill holes, threads, or attachments that are not offered as accessories by Weiss Robotics may be
attached only with permission of Weiss Robotics.
3.3.3 Special standards
The following standards are met:
Fast transients on supply and I/O lines (burst) to IEC / EN 61000-4-4
FH power supply to IEC/EN 61000-4-6
HF radiation according to IEC/EN 61000-4-3
Emissions according to EN 55011:2009 Class A (corresponds to EN 61000-6-4:2007)
Power frequency magnetic field according to EN 61000-4-8
3.4 Personnel qualification
The assembly, initial commissioning, maintenance, and repair of the module may be performed only by
trained specialist personnel. Every person called upon by the operator to work on the module must have
read and understood the complete assembly and operating manual especially the chapter 3 "Basic safety
notes”. This applies particularly to personnel only used occasionally, such as maintenance personnel.
3.5 Safety Considerations
Avoid any operation that affects the function and reliability of the module.
Observe applicable on site safety and accident prevention regulations.
3.6 Notes on particular risks
Generally valid:
Risk of injury from objects falling and being ejected
The danger zone must be surrounded by a safety fence during operation.
Risk of injury due to squeezing and bumping during movement of the gripper jaws and breaking or loosen-
ing of the gripper fingers
While disassembling uncontrollable moves of parts of the gripper possible!
Do not move parts by hand when the energy supply is connected.
Do not reach into the open mechanism or the movement area of the module.

- 8 -
Remove the energy supplies before installation, modification, maintenance, or adjustment work.
Make sure, that no residual energy remains in the system.
Perform maintenance, modifications, and additions outside the danger zone.
For all work, secure the unit against accidental operation.
Take a precautionary approach by maintenance and disassembly.
Only special trained staff should disassemble the module.

- 9 -
4Warranty
The warranty is valid for 24 months from the delivery date to the production facility under the following
conditions:
Intended use in 1-shift operation
Observe the mandatory maintenance and lubrication intervals.
Observe the environmental and operating conditions.
Parts touching the work piece and wearing parts are not part of the warranty.
The module is considered defective if its basic function “gripping” is no longer given.

- 10 -
5Scope of delivery
The scope of delivery includes:
WSG 32-068 servo-electric 2-finger parallel gripper
Operating manual
CD with documentation and firmware

- 11 -
6Accessories
The following accessories that are required for the module must be ordered separately:
Ethernet data cable, length 5 m, 4-pole M8 to RJ-45, for WSG gripper modules and KMS 40,
Part No. AL-ETH-4P-5M (straight) and AL-ETH-4PW-5M (right angle)
Power supply cable, length 5 m, 6-pole M8 connector to free wire ends, shielded,
Part No. AL-M8-6P-5M (straight) and AL-M8-6PW-5M( right angle)
Centering sleeves, 06.0x5.35, outer diameter 6h6, item no. ZH-6.0-5.35
PROFINET RT (software license), OPT-WSG-PN
Universal Finger WSG-F
Force Measurement Finger WSG-FMF
Tactile Sensing Finger WSG-DSA
Please order accessories separately. More accessories can be found on our web site www.weiss-
robotics.com.

- 12 -
7Technical Data
7.1 Outer dimensions
Figure 2: Outer dimensions

- 13 -
7.2 Nominal mechanical data
Exceeding the specified nominal data can damage the module. If in doubt, please discuss your ap-
plication with our technical sales department.
Mechanical Data
Unit
Min.
Typ.
Max.
Remark
Stroke per finger
mm
34
Nominal gripping force
N
50
Minimum gripping force
N
5
Gripping speed 5 mm/s,
finger length 55 mm, steel
on steel
Maximum gripping force
N
50
Gripping speed 50 mm/s,
finger length 55 mm, steel
on steel
Weight
kg
0.55
Workpiece weight
kg
0.5
0.5
Finger length
mm
120
at nominal force, see
Figure 3
Mass per finger
kg
0.1
Tightness
IP
40
DIN EN 60529
Ambient temperature
°C
0
50
Air humidity
%
0
90
Non condensing
Repeatability
mm
±0.005
3σ-deviation
Gripping speed
mm/s
5
400
Finger acceleration
mm/s²
100
5000
Figure 3: Determining the clamping height

- 14 -
Figure 4: Typical finger acceleration, gripping force: 50 N, finger mass: 2x 0.1 kg
7.2.1 Mechanical Finger Load
The following table shows the maximum load of the finger. The specified load may be applied simultane-
ously and in addition to the gripping force.
Mechanical Load
Unit
Min.
Typ.
Max.
Remark
FZ
N
50
MX
Nm
1.6
MY
Nm
1.6
MZ
Nm
1
0
50
100
150
200
250
300
350
400
450
0 1 2 3 4 5 6
Gripping Speed (mm/s)
Finger position (mm)
Acceleration:
5000 mm/s²

- 15 -
7.2.2 Gripping force
The gripping force is defined as the effective force acting between the fingers multiplied by the number of
fingers in contact with the part to be grasped. To operate the gripping module without force measurement
fingers, the gripping force is calibrated during the manufacturing process. The actual gripping force de-
pends on gripping speed, finger length and temperature. Figure 6 shows the recommended gripping speed
according to the desired gripping force. The typical influence of the finger to the effective gripping force is
shown in Figure 7.
For a precise control of the gripping force use the Force Measurement Finger WSG-FMF (available
as an accessory)
Figure 5: Mechanical finger load

- 16 -
The diagram above is considered as a recommendation. If in doubt, please try out and measure the
actual force for your application.
Figure 6: Recommended gripping speed (steel on steel, finger length 40 mm)
Figure 7: Gripping force over clamping height diagram
0
10
20
30
40
50
60
0 5 10 15 20 25 30 35 40 45 50
Gripping Speed (mm/s)
Gripping Force (N)
0
10
20
30
40
50
60
0 10 20 30 40 50 60 70 80 90 100 110 120
Gripping force [N]
Clamping height [mm]
F = 25N
F = 50N

- 17 -
Definition of the nominal gripping force
To determine the nominal gripping force, the module is non-positively mounted to an aluminum plate, see
Figure 8. The plate itself is thermally insulated from the underlying surface. With an ambient temperature
of 22° C the module can hold with the nominal gripping force for at least 5 hours.
For high gripping forces or long holding cycles, make sure that heat is well dissipated via the screw
contact surface. Damage to the module is possible!
7.3 Nominal electrical data
Exceeding the specified nominal data can damage the module. If in doubt, please discuss your ap-
plication with our technical sales department.
Parameter
Unit
Min.
Typical
Max.
Remark
Clamping voltage
V DC
22
24
28
Currend drawn when idle
A
0.05
Current drawn when hold-
ing
A
0.75
Gripping force = 50N
Positioning resolution
µm
1.3
Controller
Integrated
Field bus interface
Ethernet / CAN-Bus (optional) / PROFINET
(optional)
Configuration interface
web based
Figure 8: Arrangement for ascertaining the nominal gripping force

- 18 -
7.3.1 Fuse
The module has an integrated fuse to protect against short circuits and incorrect polarity.
To have the fuse changed, please contact an authorized sales partner.
7.3.2 Power supply and CAN-Bus (optional)
Power is supplied via a 6-way M8 connector on the modules housing, which also carries the optional CAN-
Bus interface. CAN-Bus can be used for commands as well as for configuration and diagnosis via the web
server (cf. chapter ). The CAN-Bus interface is not electrically isolated and uses the module’s GND pin as
reference potential. Figure 9 shows the pin assignments.
Requirement for the power supply:
Power supply: 24 V DC ±10%
Ripple < 150mVPP
Available output current: at least 3 A
7.3.3 Ethernet
The Ethernet interface can be used both for commands as well as for configuration via the integrated web
server. It is presented via a 4-way M8 connector (socket). Figure 10 shows the pin assignments.
Wire colorPin position Signal
Brown1 +24V MOTOR
White2 +24V LOGIC
Blue3 GND
Black4 CAN-L*
ShieldShielding
1
+24V
MOTOR
2
+24V
LOGIC
5
CAN-H*
3
GND
Grey5 CAN-H*
Rose6 not used
4
CAN-L*
6
*) only with option CAN-BusView on device plug
Figure 9: Terminal assignment of the power supply and CAN-Bus connector
Table of contents
Popular Control Unit manuals by other brands
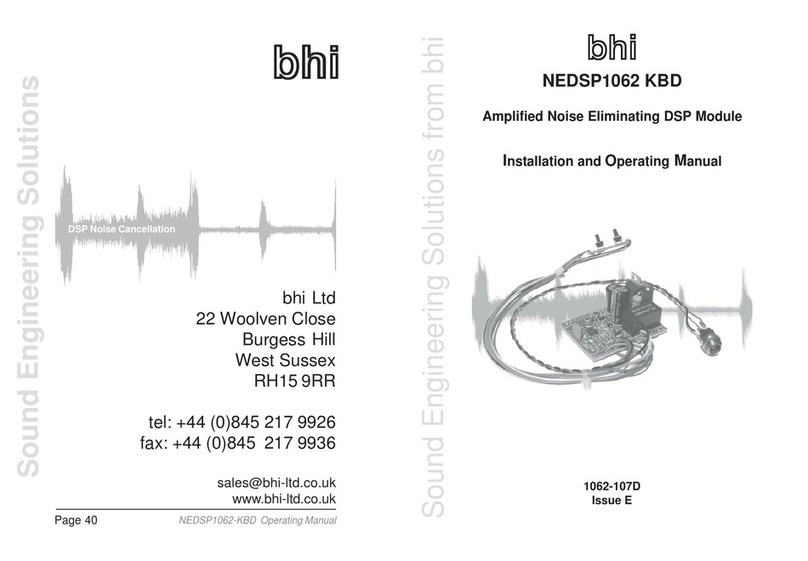
BHI
BHI NEDSP1062 KBD Installation and operating manual
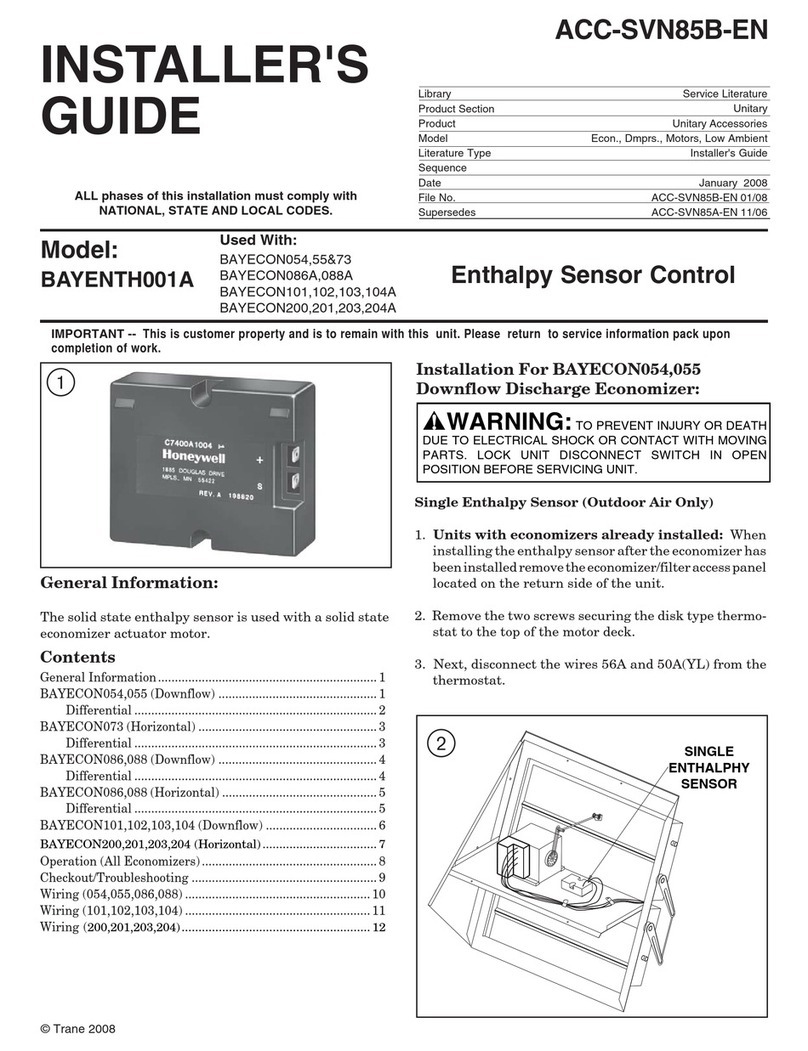
Trane
Trane BAYENTH001A Installer's guide
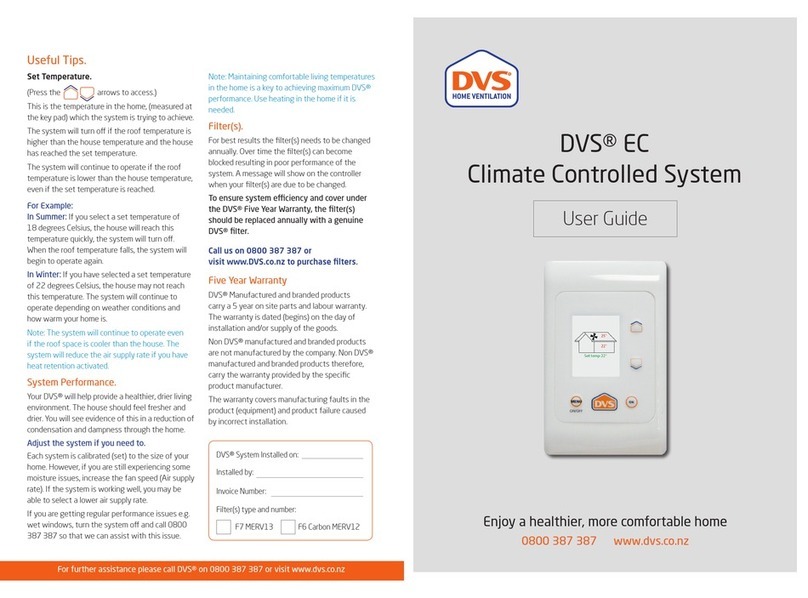
DVS
DVS EC Climate Controlled System user guide

Allmatic
Allmatic ACTION Instructions for installation
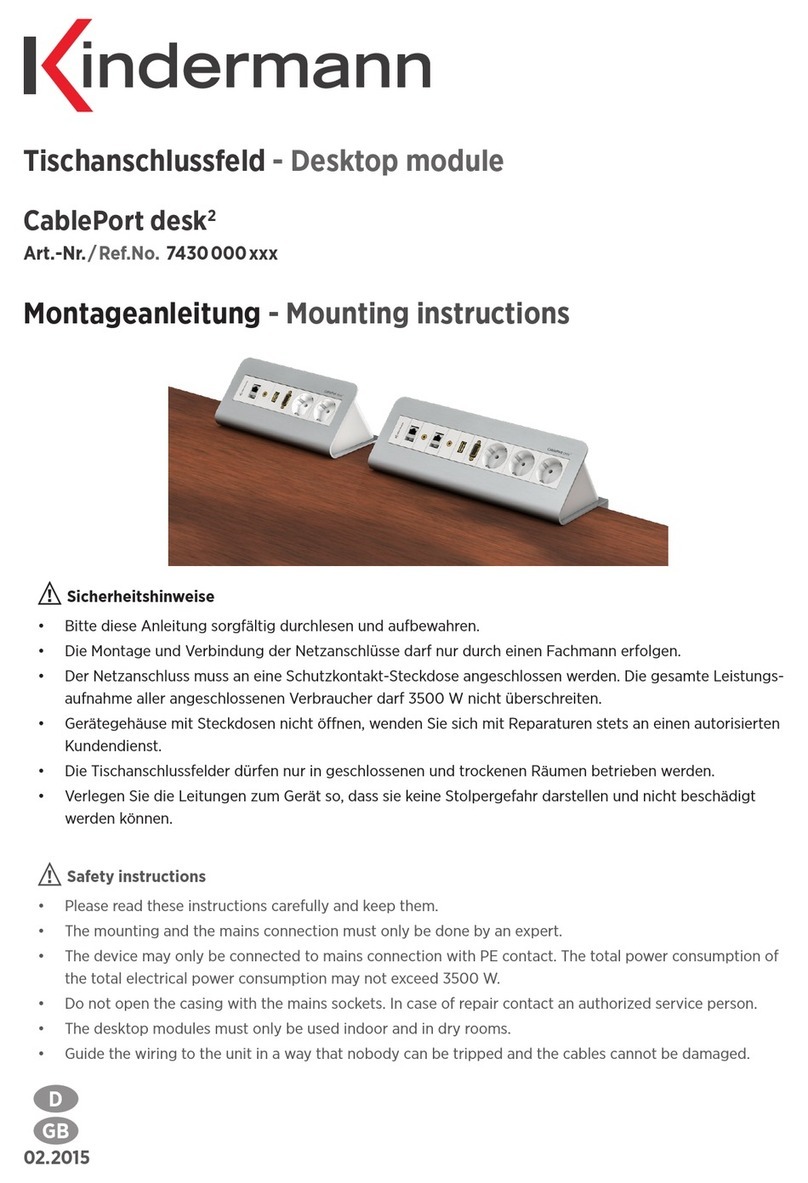
Kindermann
Kindermann CablePort desk2 Mounting instructions

Imtex-Controls
Imtex-Controls VSD-IOM-002 Installation, Operating, Maintenance