Westlock Controls Corporation Intellis 7604 User manual

IInntteelllliiss
DDeevviicceeNNeett NNeettwwoorrkk MMoonniittoorr
MMooddeellss 77660044,, 77664444 && 77667799
Installation and Operation Manual

Revision History
Revision 1.0
1 June, 2004
Initial Version
Revision 1.1
10 February, 2005
Document was updated to reflect new PCB design, addition of pneumatic section, misc.
corrections and changes in IOM format.
Revision 1.2
7 August, 2006
Changed note 9 in Class Code 9 of Appendix B
Tech-309

1 Introduction
Scope of Manual 1-2
Symbols Used in this Document 1-2
About DeviceNet 1-2
Westlock Intellis DeviceNet Module EL-40092 1-3
Module Bit Map 1-4
Watchdog Timer 1-4
LED Status Indicators 1-5
EL-40092 Module Layout 1-7
Device Specifications 1-7
Specifications 1-7
DeviceNet Features 1-8
EL-40092 Current Consumption 1-8
Tech-309 1-1

1.1 Scope of Manual
This manual contains installation, configuration and specification data for the DPAC
DeviceNet valve controller.
This manual assumes a basic level of familiarity and competence with DeviceNet
terminology and technology. Only qualified personnel should install, operate and
maintain this equipment.
1.2 Symbols Used in this Document
This symbol warns the user of possible danger. Failure to heed this warning
may lead to personal injury or death and/or severe damage to equipment.
o
connected equ
This symbol identifies information about operating the equipment in a
particular manner that may damage it or result in a system failure. Failure t
heed this warning can lead to total failure of the equipment or any other
ipment.
This symbol draws attention to information that is essential for understanding
the operation and/or features of the equipment.
1.3 About DeviceNet
DeviceNet is an open network standard originally developed by Allen-Bradley and based
on a broadcast oriented, communications protocol - the Controller Area Network (CAN).
The CAN protocol was originally developed by BOSCH the European automotive market
for replacing expensive, wire harnesses with a low-cost network.
In 1995 Allen-Bradley released the protocol to the open DeviceNet Vendors Association
(ODVA). ODVA oversees the development of the DeviceNet specification and the
conformance testing of DeviceNet products. ODVA is open to any manufacturer or user
of this protocol with a worldwide membership of over 250 companies.
DeviceNet is a simple networking solution that reduces the cost and time required to
install and wire industrial automation devices. A single DeviceNet Intellis System will
accommodate up to 63 valves and 1008 discrete I/O points. Although a simple system to
Tech-309 1-2

design and implement, DeviceNet has the capability to interconnect complex as well as
simple devices to the same network, easily accommodating both analog and discrete I/O.
Westlock Controls is a member of ODVA and our DeviceNet products are conformance
tested and certified.
1.4 Westlock Intellis DeviceNet Module EL-40092
The EL-40092 module is a 4 input, two output network monitor. Inputs 0 and 1 are
internal Hall Effect sensors that are activated by the field of a magnet (south pole). Inputs
2 and 3 are active high/low (activated by pulling the input up to +24V or activated by
pulling the input down to ground). The outputs are open drain active low FETs, fused
(solid state self resetting) at 0.2A with diode protection to 24Vdc. For current
consumption see Table 6, page 1-8. Minimum power supply input voltage is 19Vdc to
insure proper solenoid operation.
Connection to the network is via DeviceNet specific cable. There are both Round and
Flat Media Refer to the Allen-Bradley document “DeviceNet Cable System”’ (Cat. No.
DN-6.72) for a detailed treatment of this topic.
For data exchange to occur each network monitor connected to the DeviceNet network
must be programmed with a unique address, numbered between 0 and 63 and all nodes
must be set to the same Baud rate as the scanner. This may be accomplished via setting
the DIP switch, S1, on the electronics module.
The address and Baud rate may also be set via explicit Messaging if positions 7 and 8 on
S1 are set to the “On” position. Refer to Section 3.1, page 3-2 for additional information.
It is possible to exchange or add slaves during normal operation without interfering with
communications to other nodes.
The Westlock Controls Corp. DeviceNet Module, EL-40092, operates as a GROUP 2
Only Slave on a DeviceNet network. The unit supports Explicit Messages and Polled I/O
Messages of the Predefined Master/ Slave Connection Set. The device does not support
the Explicit Unconnected Message Manager (UCMM).
Refer to Section 1.5 Device Specifications, page 1-7, for a summary of features.
Tech-309 1-3

1.4.1 Module Bit Map
Table 1
I/O TYPE MODULE REFERENCE
BITMAP OF DATA
INSTANCE #4 (8-POINT INPUT WITH
NO STATUS) ATTRIBUTE #3 (DATA)
INPUT 0 Hall Effect Internal Sensor BYTE 0, BIT 0 Valve Closed
(Bottom L.S.)
INPUT 1 Hall Effect Internal Sensor BYTE 0, BIT 1 Valve Open
(Top L.S.)
INPUT 2 Active High/Low* J2-1 (In Hi/Low) to J2-2 (Ground) BYTE 0 BIT 2 Aux. Input
INPUT 3 Active High/Low* J2-3 (In Hi/Low) to J2-4 (Ground) BYTE 0, BIT 3 Aux. Input
*Active High/Low indicates that pulling the input pin up to +U or down to ground activates the input.
I/O TYPE MODULE REFERENCE
BITMAP OF DATA
INSTANCE #33 (STATIC OUTPUT)
ATTRIBUTE #3 (DATA)
OUTPUT 0 Active Low* J4-1 (+24V) to J4-2 (Out) BYTE 0, BIT 0 “A” Solenoid
OUTPUT 1 Active Low* J4-3 (+24V) to J4-4 (Out) BYTE 0, BIT 1 “B” Solenoid or
Aux. Output
*Active Low indicates that when the output is activated it pulls the pin down to GND drawing current through the load from the +24V
1.4.2 Watchdog Timer
The DeviceNet Connection Object (Class Code 05) of the DPAC firmware has an
integral inactivity/watchdog timer (IWT). The behavior of the IWT is defined by the
DeviceNet Specification.
There are two types of message connections, Explicit and I/O, each with their own IWT.
There are also different configurable attributes that effect device behavior in the event of
an IWT timeout.
The initial timeout value is the expected_packet_rate attribute multiplied by 4 or by 10
seconds, which ever is greater (Configuring state). All subsequent activations of the IWT
use the expected_packet_rate attribute multiplied by 4 as the number of milliseconds to
load into the IWT (Established state).
The default configuration of the DPAC will cause the outputs of the DPAC to go to
the de-energized state when either IWT times out.
The IWT attribute for the Explicit message connection is configurable via explicit
messaging. There are two values for this attribute supported by the DPAC; Auto Delete
(the factory default setting) and Deferred Delete. Refer to Table 2 for definitions of these
values and refer to Appendix B for the Device Specification to obtain Class, Instance,
Attribute codes for explicit messaging the device.
The DeviceNet Discrete Output Point Object (Class Code 09) controls the behavior of the
DPAC outputs. There are four attributes that specify the behavior of the device when
either a Fault state (IWT timeout) or Idle state (Poll message without data) is entered. The
DPAC may be configured to execute the Fault Value, outputs “ON” or “OFF”, or to keep
at last value. Refer to Appendix B for the Device Specification for additional
information.
Tech-309 1-4

Table 2
Value Meaning
1 Auto Delete: The Connection Class automatically deletes the Connection if it
experiences an IWT timeout. This is the default value for this attribute with respect to
Explicit Messaging Connections
3
Deferred Delete: The Connection transitions to the Deferred state if any child
connection instances are in the Established state. If no child connection instances are
in the Established state the connection is deleted. This value is invalid for I/O
Messaging Connections.
1.4.3 LED Status Indicators
The LEDs provide information concerning the status of inputs, outputs, the
module and/or the network. The LEDs provide visual indication whether any
inputs or outputs are active and whether the module or network is in a fault
condition. The I/O Status LEDs are intended to indicate the state of the inputs
and outputs only.
Refer to Table 3, page 1-6, for more information.
Tech-309 1-5

Table 3
Module
p/n LED State Indicates
Off There is no power applied to the device.
Green Device is operating in a normal condition.
Flashing Green The device Needs commissioning due to
configuration missing, incomplete or incorrect.
Red Unrecoverable fault, device may need replacing.
Module
Status
LED 1
Flashing Red Recoverable fault.
Off Not powered/ Not online
Green For a Group 2 Only device: Device is allocated to
Master
Flashing Green Online, not connected. For a Group 2 Only device:
Device is not allocated to a Master
Red
Failed communication device. The device has
detected an error that has rendered it incapable of
communication on the network (Duplicate MAC ID
or Bus-off).
Network
Status
LED 2
Flashing Red One or more I/O connections are in the Time-out
state.
Closed LS
IN_0 LED Yellow
Input 0, Bottom L.S. Closed: Valve is in the
closed position as determined by the triggering of
the Internal Hall Effect sensor by the travel of the
trigger mechanism on the shaft assembly.
Open LS
IN_1 LED Yellow
Input 1, Top L.S. Closed: Valve is in the open
position as determined by the triggering of the
Internal Hall Effect sensor by the travel of the
trigger mechanism on the shaft assembly.
Aux. Input
IN_2 LED Yellow Input 2, Active: Dry contact type switch attached
to this input is closed.
Aux. Input
IN_3 LED Yellow Input 3, Active: Dry contact type switch attached
to this input is closed.
Output
OUT_0
LED Yellow Output 0. “A” Solenoid is energized.
EL-
40092
Output
OUT_1
LED Yellow Output 1. “B” Solenoid is energized.
Tech-309 1-6

1.4.4 Module Layout
J1
Figure 1- EL-40092
1.5 Device Specifications
1.5.1 Specifications
Table 4
Round Physical Media Shielded 2 twisted pairs for communication and power
Flat Physical Media Unshielded 4 parallel conductors for communications
and power
Supported Topology Trunk and drop
Maximum Trunk Distance Round Media: 500m (1640’) @ 125 kbd
Flat Media: 420m (1378’) @ 125 kbd
Maximum Nodes/Network 64, one being the master
Maximum I/O Points/Network 378, 4 inputs and 2 outputs/DPAC
Typical Current
Consumption/Network Monitor 75 mA with single Falcon NI solenoid energized
80 mA with single Falcon XP solenoid energized
Host System’s Interface Allen-Bradley, Omron, Emerson and many others
Communications Method Group 2 only slave
Error Checking CRC
Redundancy No
Valve Specific Diagnostics No
Tech-309 1-7

1.5.2 DeviceNet Features
Table 5
DeviceNet Features
Device Type Generic
Explicit Peer to Peer Messaging No
I/O Peer to Peer Messaging No
Configuration Consistency Value No
Faulted Node Recovery No
Baud Rates 125K, 250K, 500K
Master/Scanner Yes
I/O Slave Messaging
•Bit Strobe No
•Polling Yes
•Cyclic No
•Change of State (COS) No
1.5.3 Current Consumption
Table 6
Inputs Active Outputs Active Current Draw1
0 0 50mA
4 0 62mA
4 1 80mA
4 2 100mA
4 1 85mA(XP)
4 2 110mA(XP)
1All current values acquired using a non-incendive
solenoid except where noted by an XP (explosion
Tech-309 1-8

2 Installation Instructions
Mounting 2-2
Pneumatic Connections 2-3
Tubing and Fittings 2-3
Porting 2-4
Maintenance 2-4
Switch Adjustment 2-5
Wiring Instructions 2-6
Wiring Diagram 2-7
DPAC Connector Pin-out Diagrams 2-8
DeviceNet Cabling Information 2-9
DeviceNet Supported Topologies 2-9
Tech-309 2-1

IMPORTANT: If the valve monitor is already in the field mounted on an actuator
and valve, please follow the field wiring instructions in Section 2.4.
Confirm that the area is known to be non-hazardous before opening the
cover of a network monitor and making or breaking any electrical connections.
2.1 Mounting
For steps 1-3 refer to Figure 2 below.
1. Attach the proper mounting bracket and adapter (if required) to the valve monitor
housing with the hardware provided.
2. Operate the actuator to full closed position.
3. Attach the valve monitor and mounting bracket to the actuator.
4. Note the position of the actuator/valve and confirm the Beacon position is
properly aligned, as shown in Figure 3 below while replacing the cover.
Figure 2
Tech-309 2-2

Figure 3
2.2 Pneumatic Connections
Personal injury and/or property damage may occur from loss of process
control if the supply medium is not clean, dry oil-free air or non-corrosive gas.
Instrument quality air that meets the requirements of ISA Standard S7.3-1975 is
recommended for use with pneumatic equipment in process control environments.
Westlock Controls recommends the use of a 20 micron filter with all Falcon solenoids.
2.2.1 Tubing and Fittings
The use of copper, stainless steel, nylon or polyethylene tube is recommended for piping
up air circuits and equipment. As a general rule, pipe threaded fittings should not be
assembled to a specific torque because the torque required for a reliable joint varies with
thread quality, port and fitting materials, sealant used, and other factors. The suggested
method of assembling pipe threaded connections is to assemble them finger tight and
then wrench tighten further to a specified number of turns from finger tight. The
assembly procedure given below is for reference only; the fitting should not be over
tightened for this will lead to distortion and most likely, complete valve failure.
1. Inspect port and connectors to ensure that the threads on both are free of dirt,
burrs and excessive nicks.
Tech-309 2-3

2. Apply sealant/lubricant or Teflon tape to the male pipe threads. With any sealant
tape, the first one or two threads should be left uncovered to avoid system
contamination.
3. Screw the connector into the port to the finger tight position.
4. Wrench tighten the connector approximately 1 - 2 turns (to seal) from finger tight.
Again this is only reference - the fitting should NOT be over tightened.
2.2.2 Porting
Figure 4
2.2.3 Maintenance
Routine maintenance is usually confined to the periodic replenishment of Dow Corning
III lubricant or equivalent to spool and spring.
Tech-309 2-4

2.3 Switch Adjustment
Switches are factory set. If you need to adjust switches for any reason follow
instructions below.
For steps 1-8 refer to Figures 1 and 5.
1. Refer to Figure 1 and note the approximate locations of the Open and Close
targets on the DPAC module.
2. With the valve in the closed position, lift bottom cam of the Close sensor trigger.
3. Turn cam until face of trigger is perpendicular to the target and sensor is activated
as evidenced by the lighting of the corresponding module LED.
4. Release the cam and the spring will push cam back onto the splined shaft.
5. Operate the actuator to the opened position.
6. Push down the top cam of the Open sensor trigger.
7. Turn cam until face of trigger is perpendicular to the target and sensor is activated
as evidenced by the lighting of the corresponding module LED.
8. Operate actuator from one extreme to the other several times to check Limit
Sensor operation.
Figure 5
Tech-309 2-5

2.4 Wiring Instructions
All wiring must be in accordance with National Electrical Code
(ANSI-NFPA-70) for the appropriate area classifications.
All wiring must be in accordance with National Electrical Code (ANSI-
NFPA-70) for area classifications. The valve monitors are approved as nonincendive for
Class I, Division 2, Groups A,B,C and D; dust-ignition proof for Class II/III, Division 1,
Groups E,F and G hazardous (classified) locations; indoor/outdoor (NEMA type 4, 4X).
Always check the nameplate to make sure the agency approval ratings
coincide with the application.
The proper wiring diagram for your unit is shown on the inside of the enclosure
cover.
1. Wiring options for 7604, 7644 and 7679 are shown in Figures 6 and 7 below.
2. Replace the electronics housing cover or junction housing cover.
3. Unit is now ready for automatic operation. If any assistance is required, please
call Westlock Controls at (201) 794-7650.
Tech-309 2-6

Tech-309 2-7

2.4.1 DPAC Connector Pin-out Diagrams
Tech-309 2-8

2.5 DeviceNet Cabling Information
Correct termination of the trunk and total trunk and drop limits for the baud rate
the network is to run at must be observed or unreliable operation may result.
Table 7 Maximum Distance
Data Rate Flat Cable Thick Cable Med. & Thin Cable
125 kbd 420m (1378’) 500m (1640’) 100m (328’)
250 kbd 200m (656’) 250m (820’) 100m (328”)
500 kbd 75m (246’) 100m (328’) 100m (328’)
Table 8
Data Rate Maximum Cumulative Drop Length
125 kbd 156m (512’)
250 kbd 78m (236’)
500 kbd 39m (128’)
2.6 DeviceNet Supported Topologies
Figure 14
Tech-309 2-9

3 DPAC Configuration
Communication Settings 3-2
Baud Rate and Address via the DIP Switch 3-2
Baud Rate and Address via the Bus 3-4
Tech-309 3-1
This manual suits for next models
2
Table of contents
Popular Network Hardware manuals by other brands
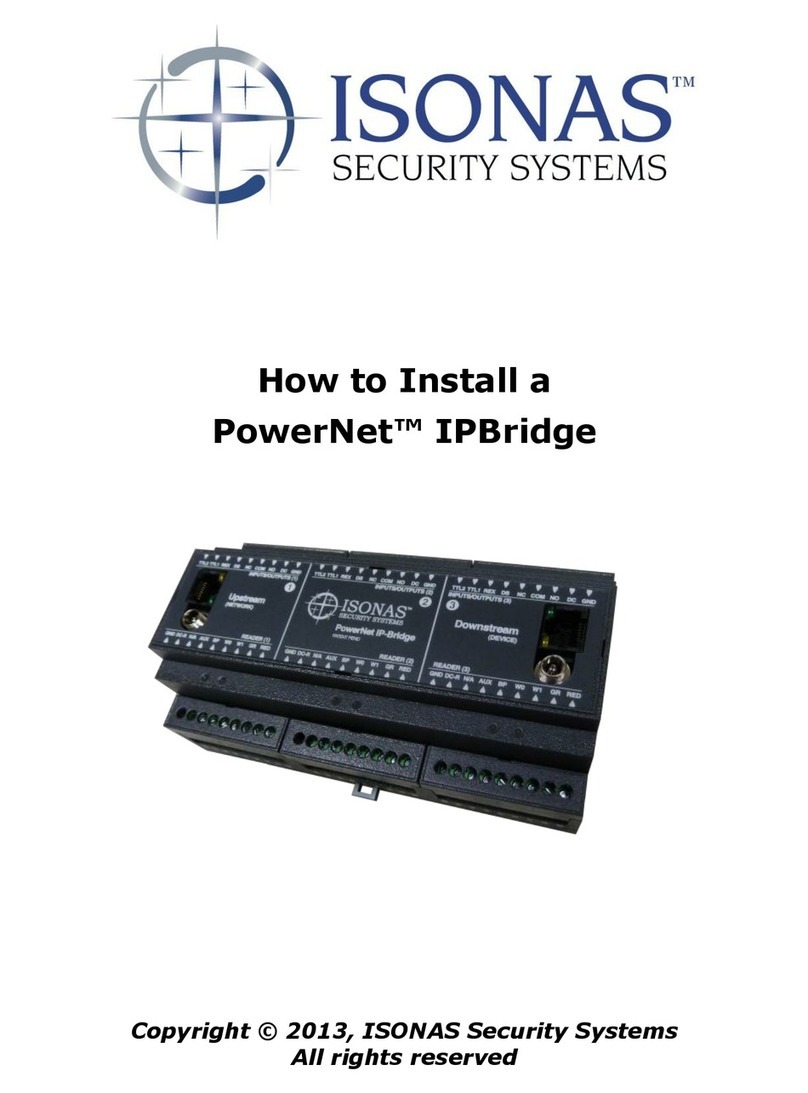
Isonas
Isonas PowerNet IP-Bridge Series How to install
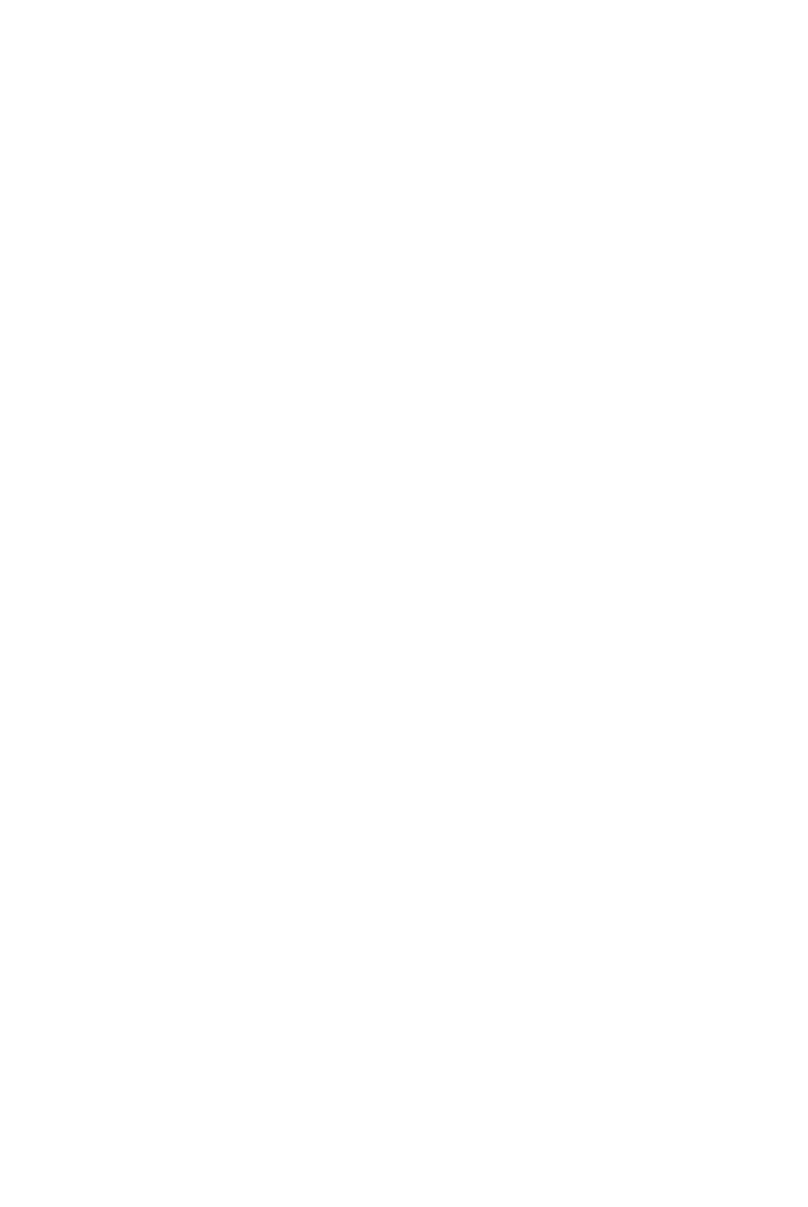
Crossbow Technology
Crossbow Technology CrossNet CN1100 Node Series user manual
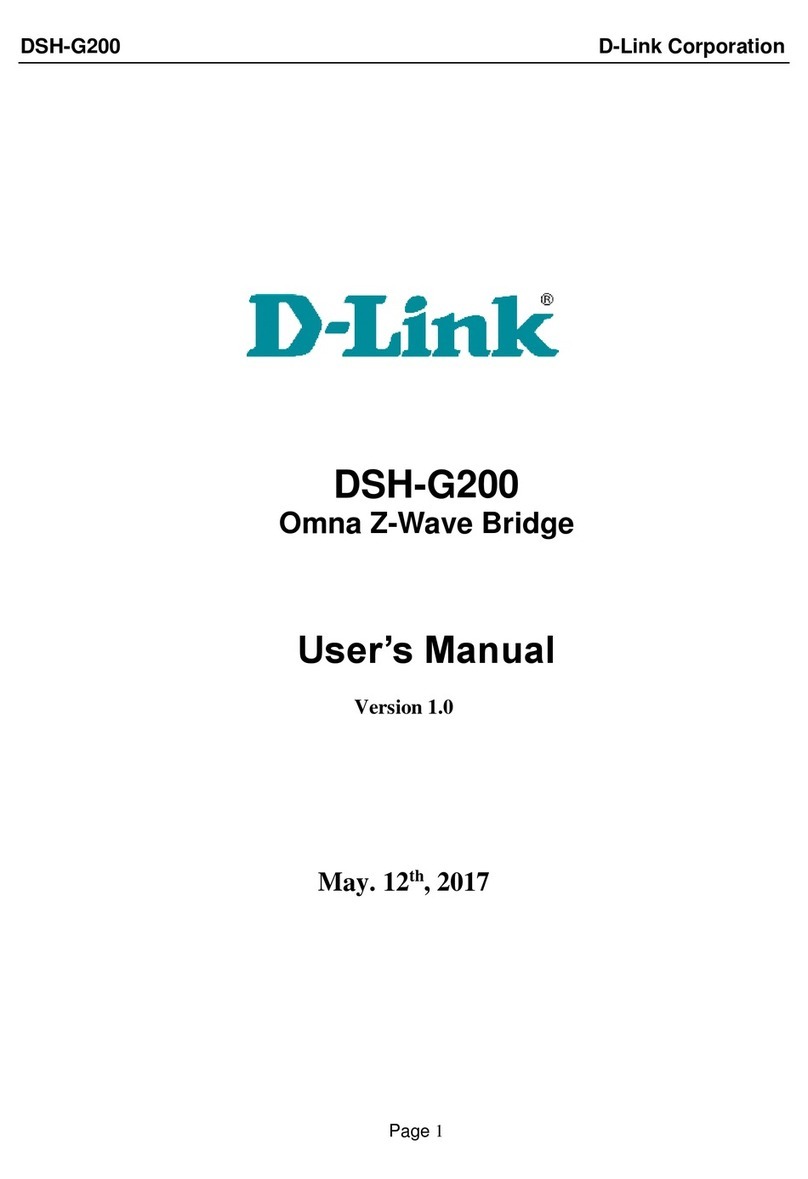
D-Link
D-Link DSH-G200 user manual

Dell
Dell SonicWALL NSA E6500 Getting started guide
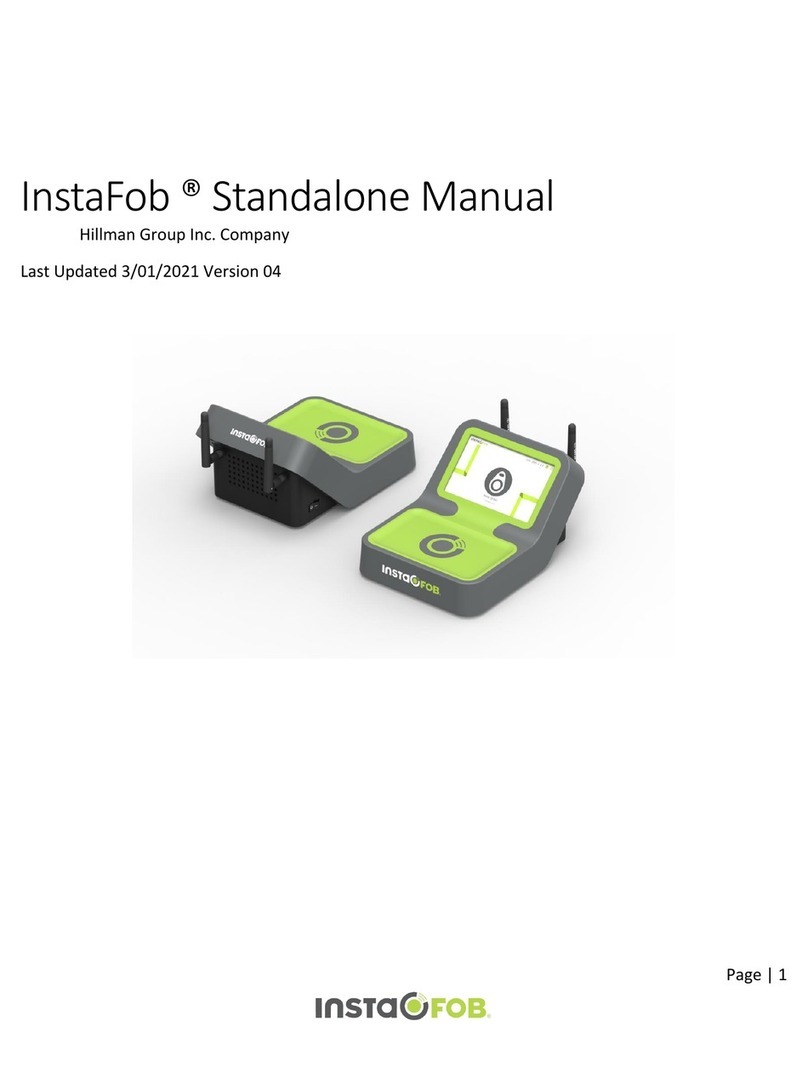
Hillman
Hillman InstaFob Standalone Manual
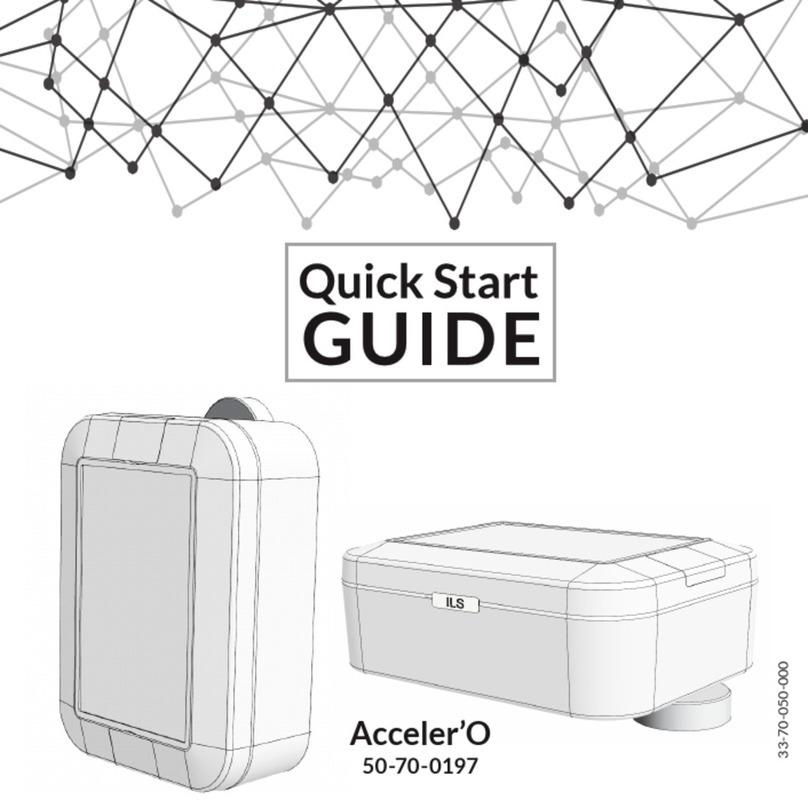
WATTECO
WATTECO Acceler'O 50-70-0197 quick start guide