Wittco TOUCHMASTER I Manual

LIMITED WARRANTY
Wittco warrants the Products that it manufactures to be free from defects in materials and
workmanship, under normal use and service, for the periods indicated below from the date of purchase
when installed and maintained in accordance with Wittco's written instructions. Buyer must establish
the 'Products' purchase date by returning Wittco's Warranty registration Card or by other means
satisfactory to Wittco in its sole discretion.
Wittco warrants its Products to be free from defects in materials and workmanship from the date of
purchase (subject to the foregoing conditions) for the period(s) of time and on the conditions listed
below:
Ninety (90) days Labor Warranty
One (1) Year Parts Warranty
THE FOREGOING WARRANTIES ARE EXCLUSIVE AND IN LIEU OF ANY OTHER WARRANTY,
EXPRESSED OR IMPLIED, INCLUDING BUT NOT LIMITED TO ANY IMPLIED WARRANTY OF
MERCHANTABILITY OR FITNESS FOR A PARTICULAR PURPOSE OR PATENT OR OTHER
INTELLECTUAL PROPERTY RIGHT INFRINGEMENT. Without limiting the generality of the foregoing,
SUCH WARRANTIES DO NOT COVER: Coated incandescent light bulbs or heat lamps, all glass
components, Product misuse, tampering, misapplication, application of improper voltage, or
recalibration of thermostats or high limit switches.
LIMITATION OF REMEDIES & DAMAGES
Wittco's liability and Buyer's exclusive remedy hereunder will be limited solely, at Wittco's option, to
repair or replacement by a Wittco authorized service agency (other than where Buyer is located outside
of the United States or Canada, in which case Wittco's liability and Buyer's exclusive remedy
hereunder will be limited solely to replacement of part under warranty) with respect to any claim made
within the applicable warranty period referred to above. Without limiting the generality of the
foregoing, all portable Products, as defined by Wittco, shall be delivered by Buyer, at its sole expense,
to the nearest Wittco authorized service agency for replacement or repair. Wittco reserves the right
to accept or reject any such claim in whole or in part. Wittco will not accept the return of any Product
without prior written approval from Wittco, and all such approved returns shall be made at Buyer's sole
expense. WITTCO WILL NOT BE LIABLE. UNDER ANY CIRCUMSTANCES, FOR CONSEQUENTIAL OR
INCIDENTAL DAMAGES, INCLUDING BUT NOT LIMITED TO LABOR COSTS OR LOST OF PRODUCTS
AND LOSS OF PROFITS RESULTING FROM THE USE OF OR INABILITY TO USE THE PRODUCTS.
wïttco
A A foodservice
equipment
PDF compression, OCR, web optimization using a watermarked evaluation copy of CVISION PDFCompressor

WITTCO TECHNICAL & PRODUCT SUPPORT
TECHNICAL SUPPORT & SERVICE INQUIRES MAY BE DIRECTED TO WITTCO BY:
CALLING DIRECTLY TO:
WITTCO FOODSERVICE EQUIPMENT TECHNICAL & SERVICE DEPARTMENT - (800)
367-8413
8:00 AM - 4:30 PM (CENTRAL TIME)
FAXING DIRECTLY TO:
WITTCO FOODSERVICE EQUIPMENT TECHNICAL & SERVICE DEPARTMENT - (414)
354-2821
DAILY 24 HOURS
MAILING DIRECTLY TO:
WITTCO FOODSERVICE EQUIPMENT INC.
7737 NORTH 81ST. STREET
MILWAUKEE, WISCONSIN 53223
USA
WHEN DIRECTING INQUIRIES TO WITTCO PLEASE HAVE THE FOLLOWING INFORMATION
AVAILABLE TO AVOID DELAYS
Wittco model number indicated on the equipment serial data plate located at the
electrical connection.
Wittco serial number indicated on the equipment serial data plate. The equipment
serial number will also have two (2) alpha characters immediately following the serial
number. These alpha characters are part of the serial
number. wittcc
A A foodservice
equipment
PDF compression, OCR, web optimization using a watermarked evaluation copy of CVISION PDFCompressor

INTRODUCTION
Wittco Foodservice Equipment's Touchmaster Cook and Hold Oven System is a basic
unit of food preparation equipment. It has found wide acceptance in both institutional and
commercial food service operations.
This manual has been produced to provide persons responsible for the operation and
maintenance of the oven with a simple but comprehensive understanding of its proper use.
We recommend that this manual be read and understood prior to placing the oven into
operation.
As with any piece of food service equipment, this oven system will require a minimum of
care and maintenance Suggestions for this procedure are contained in this manual and
should become a regular part of the operation of the unit.
NOTE: BEFORE USING THE OVEN IT SHOULD BE THOROUGHLY
CLEANED iN ACCORDANCE WITH THE INSTRUCTIONS CONTAINED IN
THIS MANUAL.
It is recommended that prior to placing the oven system into operation that it be operated
on the cook cycle for approximately two (2) hours at 350° F.
Should repair or adjustment of the unit become necessary, we suggest that procedures
described in this manual be followed. The operator may also contact the authorized Wittco
dealer who sold the product or an authorized Wittco service agency. If the needed repair
occurs during the warranty period, prior authorization is required from Wittco by the
service company before the work is commenced.
It is our sincere desire that you obtain the maximum benefit from your Cook and Hold
Oven System. If at any time questions arise or additional information is required, contact
Wittco at 800 367-8413.
DESCRIPTION
Operators have found that cooking foods utilizing low temperature methods reduces the
amount of product shrinkage and increases the amount of product yield. This is because
less moisture is cooked out of the food when it is prepared at 225° F. than when it is
prepared at 350° F. Because of this fact, the operator will serve a product that has greater
customer satisfaction because of the increased flavor and moisture this meat possesses.
UNCRATING
Each Wittco Foodservice Equipment oven is packed in a cardboard carton which, in turn,
is banded to a wooden pallet. When the cabinet is received by the operator, the carton
should immediately be inspected for any sign of visible exterior damage. If carton is
i
PDF compression, OCR, web optimization using a watermarked evaluation copy of CVISION PDFCompressor

punctured or dented, it may be an indication that the cabinet has sustained concealed
freight damage.
It is very important that any evidence of damage be noted on the Bill of Lading at
the time of receipt.
UNPACKING THE CABINET
Remove the banding material holding the carton to the pallet.
Remove the cardboard carton and the plastic bag covering the cabinet.
Carefully lift the cabinet off the carton bottom and pallet and place it on the floor.
Note: The casters for the Touchmaster III are shipped in a separate carton.
Remove it and install the casters on the oven.
Remove the box containing the cooking racks that are supplied with the oven.
Remove any packing materials which may have been used to hold the tray slides in
place.
Heat the oven at 35Ø0 Ffor approximately 2 hours before using.
CABINET LOCATION
PLACING THE OVEN IN THE PROPER LOCATION IS IMPORTANT FOR
EFFICIENT OPERATION. CHOOSE A LOCATION FOR THE OVEN IN AN
AREA WHICH WILL PROVIDE EASY LOADING AND UNLOADING
WITHOUT INTERFERING WITH THE FINAL ASSEMBLY OF FOOD
ORDERS. PROVIDE AT LEAST SIX INCHES OF SPACE ON EACH SIDE OF
THE OVEN FOR PROPER AIR CIRCULATION AROUND THE OVEN.
OPERATING CONTROLS
A complete explanation of the operating controls will be found in the Cook Guidewhich is
supplied with the oven.
All operating controls are located on the front control panel. This panel contains the on/off
button and the touch pad operating controls.
NOTE: IT IS RECOMMENDED THAT THE OVEN CONNECTION TO THE
POWER SOURCE BE DONE BY A LICENSED ELECTRICIAN.
NOTE: UPON CONNECTING THE CONTROL MODULE TOP TO THE
POWER SOURCE, THE COOLING FANS MAY NOT OPERATE. THESE FANS
WILL ONLY OPERATE WHEN THE THERMOSTAT TO WHICH THEY ARE
CONNECTED REQUIRES IT.
2
PDF compression, OCR, web optimization using a watermarked evaluation copy of CVISION PDFCompressor

ELECTRICAL REQUIREMENTS
Wittco Cook and Hold Ovens can be factory wired for 120, 208,220, or 240 volts AC,
single or three phase, 60 or 50 cycle service.
VERIFY THAT THE VOLTAGE AND PHASE OF THE POWER SOURCE IS
IDENTICAL TO THE OVEN SYSTEM DATA PLATE BEFORE CONNECTD4G.
The oven must be adequately and safely grounded before operation. A separate disconnect
switch or circuit breaker is recommended at a convenient location between the oven and
power source.
TESTiNG THE OVEN
Each oven is completely checked and tested prior to shipment. However, it is a good
practice to completely check the unit again after unpacking and installation.
Connect oven to power source.
Turn the oven on by depressing the power button.
Set the roasting oven temperature by depressing the up/down arrow touch pad
until the LED display reads 350° F and then depress the enter touch pad.
3
PDF compression, OCR, web optimization using a watermarked evaluation copy of CVISION PDFCompressor

Set the hold temperature by pushing the up/down arrow touch pads until the LED
display reads 1400 F and then depress the enter touch pad.
Set the roasting time by pushing the time touch pad and the up/down arrows until
the LED indicator shows 1:00 (one hour)
Depress the start cook touch pad.
The oven should immediately start heating. The red "heat" indicator light will
illuminate. At this time the LED will read 01:00 in the top section and the bottom
section will read 350. The Cook indicator light will also be illuminated. The oven
timer will begin to count down to 0:00 and when it reaches that point the oven will
switch from the roasting to the holding cycle.
If all of the functions perform satisfactorily, the oven is ready for operation.
CLEANING
The interior of the oven should be cleaned whenever a food spill occurs. Use a mild soap
and water to clean. Never use harsh chemicals or abrasive pads to clean the cabinet.
The simple cleaning process follows.
DISCONNECT THE OVEN FROM THE POWER SOURCE.
Remove the control module top and place it away from the oven cabinet.
CAUTION - THE OVEN INTERIOR COMPARTMENT SHOULD NEVER
BE HOSED DOWN WHEN THE CONTROL MODULE TOP IS ON THE
OVEN BODY.
Lift and tip the side tray racks toward the center of the cabinet. Remove them from
the cabinet. These racks should be taken to a sink or dish washer for a thorough
cleaning.
Remove the interior rear mounted air distribution tunnel and take it to a sink or
dish washer for cleaning.
Clean the interior oven cavity with soap and water.
Reassemble the oven.
REPLACEMENT OF ELECTRICAL COMPONENTS
It is highly recommended that only Wittco Foodservice Equipment replacement parts be
used to insure compatibility of component parts in the operation of cook and hold oven
4
PDF compression, OCR, web optimization using a watermarked evaluation copy of CVISION PDFCompressor

systems. All of the electrical components which may require servicing are in the control
module top.
WARNiNG: DISCONNECT THE OVEN FROM THE POWER SOURCE
BEFORE REMOViNG THE CONTROL MODULE TOP FROM THE OVEN
CABINET.
ON/OFF SWITCH REPLACEMENT
DISCONNECT THE OVEN FROM THE POWER SOURCE.
Remove the protective cover from the control module top.
3Notice the arrangement of all electrical leads and refer to the wiring diagram for
reference.
Disconnect the lead wires from the power switch
Remove the rear mount hex nut which holds the switch on the control panel.
Remove the switch assembly by pushing it from the rear through the control panel.
Install the replacement switch in the reverse order of above.
Reinstall the control module cover.
Test the oven as described in the TESTING THE OVEN section.
COOK/HOLD ELECTRONIC TOUCH PAD CONTROLLER REPLACEMENT
DISCONNECT THE OVEN FROM THE POWER SOURCE.
Remove the top cover by removing the retaining screws and lifting it off the
control module top.
Notice the arrangement of all electrical leads and refer to the wiring diagram for
reference.
Disconnect the electrical leads of the temperature control needing replacement
from the circuit board.
Carefully remove the four nuts which secure the circuit board to the back of the
control panel.
Remove the circuit board from the control panel.
5
PDF compression, OCR, web optimization using a watermarked evaluation copy of CVISION PDFCompressor

COOK/HOD ELECTRONIC TOUCH PAD CONTROLLER (CON'T)
Install the replacement circuit board following the reverse of the above procedure.
Reinstall the control module cover and screws.
Test the oven as described in the TESTiNG THE OVEN section.
FOOD PROBE CONNECTOR REPLACEMENT
DISCONNECT THE OVEN FROM THE POWER SOURCE.
Remove the top cover by removing the screws and lifting the cover off the control
module top to expose the food probe connector.
3Notice the arrangement and connection of all electrical leads and refer to the
wiring diagrams for reference.
Locate the food probe "female" connector mounted to the front of the control
panel and disconnect the wire harness from the circuit board assembly.
Remove the probe connector screw securing the connector to the control panel.
Install the replacement connector in the reverse order of above.
Reinstall the control module cover and screws.
Test the oven as described in the TESTiNG THE OVEN section.
COOLING FAN REPLACEMENT
DISCONNECT THE OVEN FROM THE POWER SOURCE.
Remove the top cover by removing the screws and lifting the cover off the control
module top to expose the cooling fans.
Notice the arrangement and connection of all electrical leads and refer to the
wiring diagrams for reference.
Disconnect the electrical plug to the cooling fan and remove it.
Install the replacement cooling fan.
NOTE: THE AIR FLOW DffiECTION ARROW MUST POINT TO THE
LEFT OR AWAY FROM THE CONTROL MODULE TOP.
Reconnect the electrical leads to the cooling fan.
6
PDF compression, OCR, web optimization using a watermarked evaluation copy of CVISION PDFCompressor

COOLING FAN REPLACEMENT (CON'T)
Reinstall the module control top cover and screws.
Test the oven as described in the TESTING THE OVEN section.
COOLING FAN THERMOSTAT REPLACEMENT
DISCONNECT THE OVEN FROM THE POWER SOURCE.
Remove the top cover by removing the screws and lifting the cover off the control
module top to expose the cooling fan thermostat.
Notice the arrangement and connection of all electrical leads and refer to the
wiring diagrams for reference.
Disconnect the electrical leads to the cooling fan thermostat and remove it.
Install the replacement cooling fan thermostat.
Reconnect the electrical leads to the cooling fan thermostat.
7Reinstall the module control top cover and screws.
8. Test the oven as described in the TESTING THE OVEN section.
BLOWER ASSEMBLY REPLACEMENT
DISCONNECT THE OVEN FROM THE POWER SOURCE.
Remove the top cover by removing the screws and lifting the cover off the control
module top to expose the blower assembly.
Notice the arrangement and connection of all electrical leads and refer to the
wiring diagrams for reference.
Disconnect the electrical leads to the blower assembly at the terminal strip.
Remove the protective fan grill located on the bottom of the control module top
exposing the blower cage.
Insert an "L-end" wrench into the set screw holding the blower to the motor shaft.
Remove the cage from the blower motor.
7
PDF compression, OCR, web optimization using a watermarked evaluation copy of CVISION PDFCompressor

BLOWER MOTOR REPLACEMENT (CON'T)
7Remove the three (3) hex nuts holding the blower motor housing to the oven and
remove it.
In stall the replacement blower motor by following the reverse of the directions
above.
Reconnect the electrical leads to the blower assembly.
Reinstall the module control top cover and screws.
Test the oven as described in the TESTING THE OVEN section.
HEATING ELEMENT REPLACEMENT
DISCONNECT THE CABINET FROM THE POWER SOURCE.
Remove the top cover by removing the screws and lifting the cover off the control
module top.
Remove all the insulation surrounding the heating element compartment and save it
for reuse.
Remove the screws from the heating element cover to expose the elements.
Notice the arrangement and connection of all electrical leads and refer to the
wiring diagrams for reference.
Disconnect the electrical leads from the heating elements
7Remove the nuts securing the heating element to the heating element compartment
and remove it.
Install the replacement heating element by following the reverse of the above
directions.
Reinstall the module control top cover and screws.
Test the oven as described in the TESTING THE OVEN section.
8
PDF compression, OCR, web optimization using a watermarked evaluation copy of CVISION PDFCompressor

ELECTRICAL RELAY REPLACEMENT
DISCONNECT THE CABINET FROM THE POWER SOURCE.
Remove the top cover by removing the screws and lifting the cover off the control
module top exposing the electrical relay.
Remove the defective relay but leave the wires attached. Notice the arrangement
and connection of all electrical leads and refer to the wiring diagrams for reference.
Install the new relay and move the wires from the defective relay to the terminal
screws on the replacement relay.
Reinstall the module control top cover and screws.
Test the oven as described in the TESTING THE OVEN section.
TEMPERATURE CONTROL SENSING PROBE REPLACEMENT
DISCONNECT THE OVEN FROM THE POWER SOURCE.
Remove the top cover by removing the screws and lifting the cover off the control
module top exposing the temperature sensing probe.
Notice the arrangement and connection of all electrical leads between the sensing
probe and the circuit board and refer to the wiring diagrams for reference.
Disconnect the probe lead wires from the solid state circuit board. These wires are
not polarity sensitive.
Remove the wire ties that hold the probe wires to the other wires.
Remove the wire ties that hold the sensing probe to the fan grill on the inside
of the oven.
7Remove the insulating grommet from the probe wires and gently pull the probe
through the access hole in the top of the oven compartment.
Install the replacement temperature probe by following the reverse of the above
directions.
Reinstall the module control top cover and screws.
Test the oven as described in the TESTING THE OVEN section.
9
PDF compression, OCR, web optimization using a watermarked evaluation copy of CVISION PDFCompressor

TROUBLE SHOOTING PROCEDURE
WARNING: EXTREME CAUTION MUST BE EXERCISED WHEN WORKING
AROUND ELECTRICAL EQUIPMENT TO PREVENT THE POSSIBILITY OF
ELECTRICAL SHOCK RESULTING IN INJURY OR DEATH. THESE TEST
PROCEDURES SHOULD ONLY BE DONE BY A LICENSED ELECTRICIAN
OR AN AUTHORIZED SERVICE AGENCY.
Always work in a safe manner. Be sure the power supply is turned off before touching any
wires or terminals to prevent the possibility of electrical shock or damage as a result of
electrical short by the meter probes.
No wires should be disconnected from the terminals without first disconnecting the power
source to the oven.
This procedure supplies a list of symptoms that may be observed and a reference section
that may be referred to locate and correct the problem.
TEST EQUIPMENT REQUIRED
The preferred piece of equipment required is a DVM (Digital Voltmeter) and a clamp-on
ammeter. If one of these is not available, on ohmmeter is necessary to determine if a short
circuit or a ground exists. The meter should be capable of reading O to loo k ohms full
scale.
NORMAL OPERATION
It is preferred that the technician has had the opportunity to observe the normal operation
of the oven so that when there is a malfunction, it may be easily recognized with a
minimum of testing.
In normal operation, as soon as power is applied to the oven and the power switch is
turned on, the HEAT and the COOK CYCLE indicator lights should be illuminated. In
addition, the air circulating fans inside the oven should start.
TROUBLE SHOOTING
I. NO HEAT IN THE HOLD CYCLE
Check that the oven is connected to the power source and the circuit breaker or
fuse is not tripped.
Check that the oven power switch is on.
If the power switch is in the on position and the heat indicator light is not
illuminated, remove the fuses and verify continuity with the ohmmeter. If the fuses
'o
PDF compression, OCR, web optimization using a watermarked evaluation copy of CVISION PDFCompressor

are defective, there is probably a shorted component or wire. Refer to Section A
for additional testing.
Replace fuses with the same type that were supplied with the oven. Use only
#SLC-3 current limiting fuse, Type G, 250 volt.
II. ERROR DETECTION
When a "000" is displayed in the lower LED display during a Cook or Hold cycle,
it indicates that the temperature sensing probe is open or shorted.
When a "000" is displayed in the lower LED display during a probe cook function,
it indicates that the product sensing probe is open or shorted.
SECTION A. TESTING FOR GROUNDS AND/OR SHORTED COMPONENTS
DISCONNECT THE OVEN FROM THE POWER SOURCE BEFORE
PERFORMING ANY TESTING WITH AN OHMMETER
TESTING FOR GROUNDS
Power switch in the off position.
Connect on lead of the ohmmeter to the metal oven top.
Touch the other lead to the following and observe that there should be an open
circuit in each case:
Ti on element contactor
T2 of element contactor
Wire 7 on vent fan switch
Wire 29 on power switch
Wire 50 on power switch
Wire 10 on power switch
Wire 29 on power switch
Any reading at all, indicates a component partially or completely shorted to
ground.
TESTING FOR SHORTED COMPONENTS
Test the following to determine which component is shorted. If any component has
significantly lower reading than is listed, it is suspect and should be replaced.
TESTING HEATING ELEMENTS
Test between Ti and T2 on the contactor with the ohmmeter and compare the
value to the table below:
11
PDF compression, OCR, web optimization using a watermarked evaluation copy of CVISION PDFCompressor

The basic element has a resistance of 23 ohms regardless of the voltage rating on
the oven. Because the number of elements in the oven effects the reading, compare
the number of elements in the oven to the following chart to determine if any
elements are open or shorted.
I element
23 ohms 2 elements
11.5 ohms
Reconnect the wires to the terminal strip.
WIRING INSPECTION
Check for frayed or touching wires on any terminal strip, especially on the set
point relay. Clean and dress up the wires as needed.
TESTING THE MOV VARISTOR
Lift one wire of each MOV from the terminal and check with an ohmmeter. If the
reading is less than 100K ohms, the unit is defective.
TESTING THE CONTACTOR COIL
Disconnect all wires from one side terminal of the contactor coil. The ohmmeter
should read approximately 675 ohms for a 208/240 volt unit or 235 ohms for a
120 volt unit. If the circuit is open or shorted, the contactor must be replaced.
TESTING THE ROASTING TIMER COIL
3 elements
7.7 ohms 3 elements 3 PH
L1-L2 15.3 ohms
L1-L3 15.3 ohms
L2-L3 15.3 ohms
TESTING COOLING FAN MOTORS
Test wire 7 to wire 50 on the cooling fan motors. A typical reading on a 120
volt oven is 47 ohms. A 208/240 volt oven will have 183 ohms.
NOTE: These readings are for two fans connected in parallel. A new replacement
fan will read double.
TESTING BLOWER MOTORS
1. Disconnect the blower motor wires from the terminal strip and test with an
ohmmeter to determine whether they are shorted or not. The reading should be
approximately as shown in the table below. Ifa discrepancy exists, check each
motor individually.
12
Voltage i Blower 2 Blowers 3 Blowers
120 Volt 19 ohms 9.5 ohms 6.3 ohms
208/240 Volt 70 ohms 35 ohms 23.3 ohms
PDF compression, OCR, web optimization using a watermarked evaluation copy of CVISION PDFCompressor

Disconnect all wires from terminal #1. The ohmmeter should read approximately
520 ohms for a 240 volt unit or 140 ohms for a 120 volt unit. If the circuit is open
or shorted, the timer must be replaced.
TESTING THE SET POINT RELAY COIL
Unplug the set point relay from its socket and measure coil resistance. Ohmmeter
should read approximately 17.2K ohms across relay coil contacts.
SECTION E GENERAL VOLTAGE TESTING
Test for line voltage between the following:
Li and L2 on the contactor.
Wires 29 and 50 on the power switch
Terminal 15 and 2 on the timer
Wire 47 on the contactor coil and 25 on the electronic circuit board
Connect one voltmeter probe to wire 47 on the contactor coil and the other to the
following wires in succession:
Wire iO on the power switch,
Terminal 14 on the timer,
Wire 25 on the circuit board.
If an intermittent loss of voltage, or a low voltage condition, the cause must be
determined and corrected.
SECTION F. CONTACTOR TESTS
If the contactor has line voltage on the coil but it is not picked up to close the
power contacts, the coil is failed open and the contactor must be replaced.
13
PDF compression, OCR, web optimization using a watermarked evaluation copy of CVISION PDFCompressor

POWER
CONNECTION
120V. 10,60Hz
1260w 10.5 AMPS GREEN
AIRFLOW
COOLING
FAN 1
INLINE
TAP
7ÏNLINETAP
DISTRIBUTION
BLOCK
47
ON-OFF SWiTCH
REAR WEW
10
3AFUSE
50
3AFUSE
CONTACTOR
TOP ViEW
4.4. .L
477 /
11
160
2 OHM
11W
CAVil?
PROBE
26
BLOWER
FAN
13
1310
TERMINAI. BLOCK
JUMPER INPUTS
120 VOLT
11
IIFOOD
PROBE
TEMP CONTROL
DRAWING TITLE
TOUCHMASTER I
WIRING DIAGRAM
120v, 1PH, 60HZ
QUICK
HEATING HEAliNG DISCONNECT
ELEMENT ELEMENT
9
COOLING
AIR FAN 2
FLOW
T2
,.ØLI T1Ø
o©
WHITE
K
COOLING FAN
THERMOSTAT 14
29
14
25
26
PDF compression, OCR, web optimization using a watermarked evaluation copy of CVISION PDFCompressor

WHITE
POWER
CONNECTION
10.60HZ GREENK
208v 1900W 9AMP
240V 2530w 10.SAMP
COOLING
AIR ÛFAN1
FLOW \I
COOLING
AIR flFAN2
FLOW ii i
INLINE
tTAP
7ÏNLINETAP
DISTRIBUTION
BLOCK
47
G
COOLING FAN
THR AT
ON-OFF SWITCH
REAR ',IEW
14
14
29
10
MFUSE
50
MFUSE
_JØLI T1Ø__
CONTACTOR
TOP ViEW
'!'4i 'L.
477/ 1
11
160OHM
1w
T2Ø
MFD
600V
CAVTIY
PROBE
26
HEATING
ELEMENT
-w-
BLOWER
FAN
13
25
26
TEMP CONTROL
J-T
1310
TERMINAL BLOCK
240 VOLT
Ti
.FOOD
fi PROBE
-«QUICK
DISCONNECT
DRAWING TITLE
TOUCHMASTER I
WIRING DIAGRAM
208V-240V, 1PH, 60HZ
,--C
W >Q)LQ)E
IJ wI--oOD'4-Q)
PDF compression, OCR, web optimization using a watermarked evaluation copy of CVISION PDFCompressor

FLOW
COOLING
FAN 2
INLINE
-TAP
ON-OFF SWITCH
REAR VIEW
14
29
10
50
11
CAVI1Y
PROBE
HEATING HEATING HEATING
ELEMENT ELEMENT ELEMENT
-- ----- --
13
BLOWER
FAN 1
25
26
PROBE
1310
g
TERMINAL
JUMPER INPUTS
120 VOLT
BLOCK
TEMP CONTROL
J_ I
11
FOOD
BLOWER
FAN 2
QUICK
DISCONNECT
DRAWING TITLE
TOUCHMASTER E
WIRING DIAGRAM
120V. 1PH, 60HZ
DISTRIBUtION
BLOCK
POWER WHITE
CONNECTION
120v, IØ,601-IZ BLACK T2Ø
CREEN T1Ø
ØLI
APPROX 20 AMPS 3A CONTACTO R
FUSE TOP EW
COOLING
frJR ()FANI
COOLING
THERMO FTAT
3AFUSE
47774, ¿
160
OHM
11W
jMFD
26
7ÏNLINETAP
47
FLOW \/ I
PDF compression, OCR, web optimization using a watermarked evaluation copy of CVISION PDFCompressor
This manual suits for next models
3
Table of contents
Other Wittco Oven manuals
Popular Oven manuals by other brands

Westinghouse
Westinghouse POR663 owner's manual

Wood Stone
Wood Stone WS-MH-RFG-IR Installation and operation manual
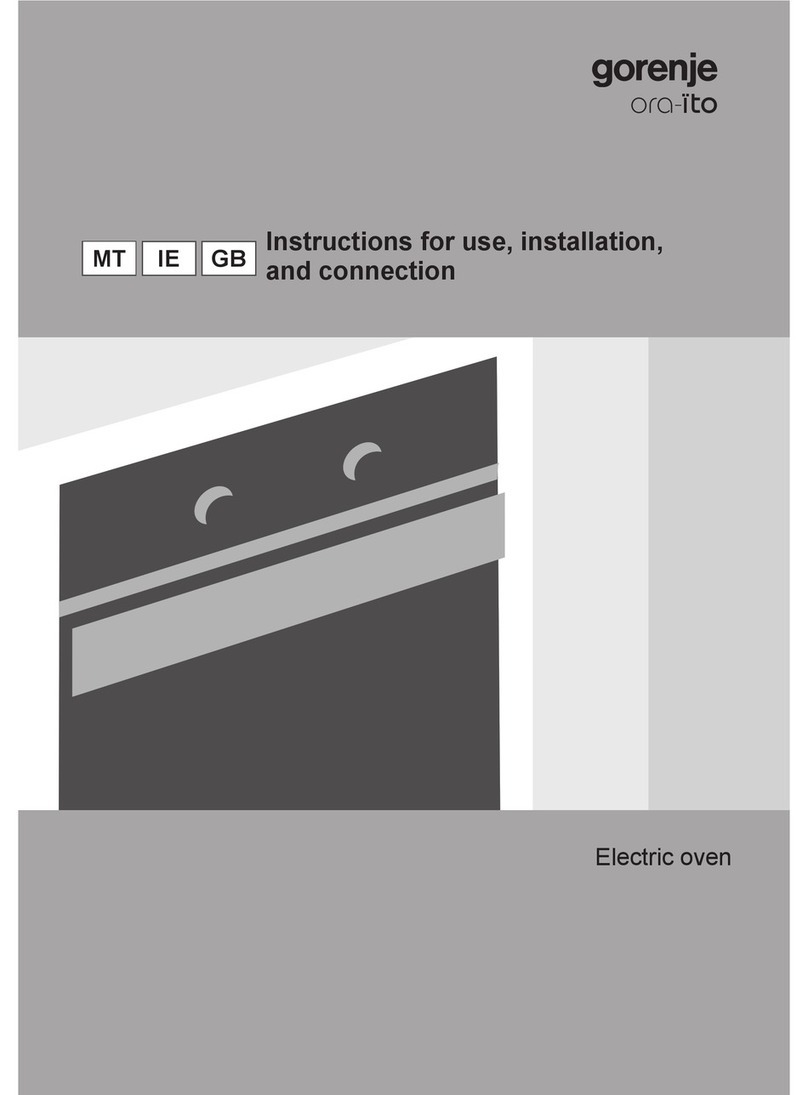
Gorenje
Gorenje ora-ito Instructions for use, installation, and connection
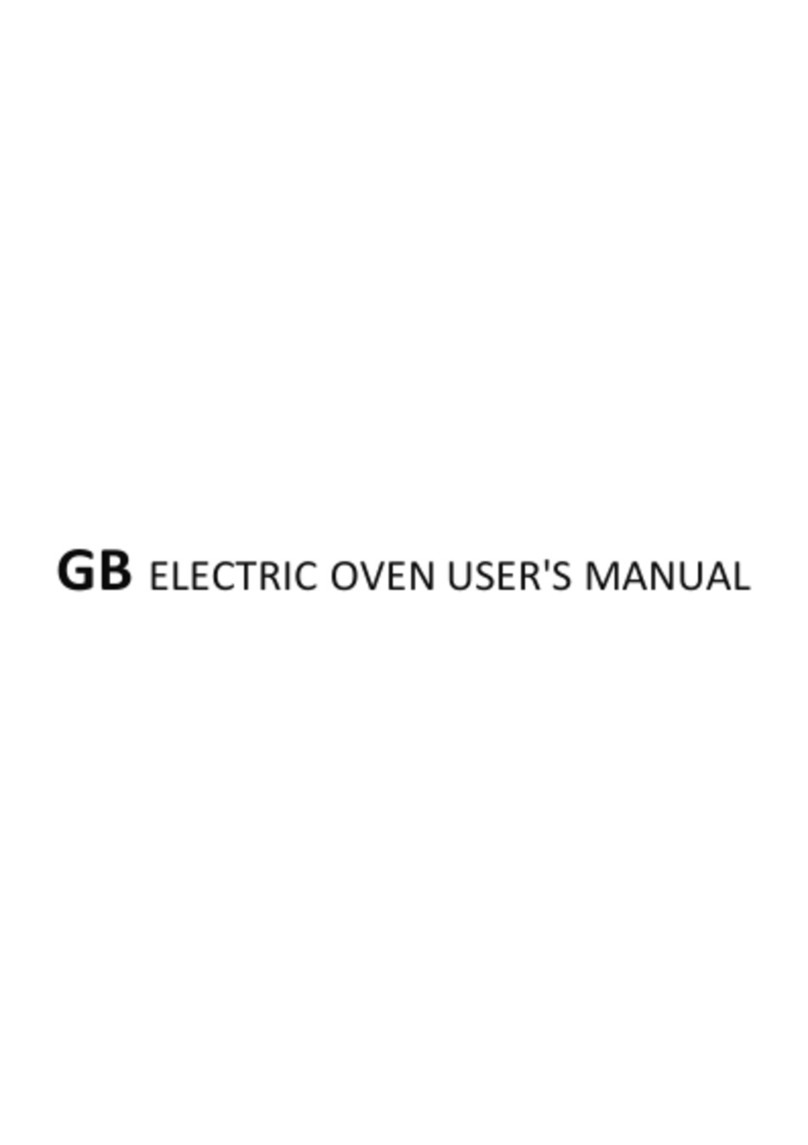
Simfer
Simfer MIDI OVEN 45 LT user manual
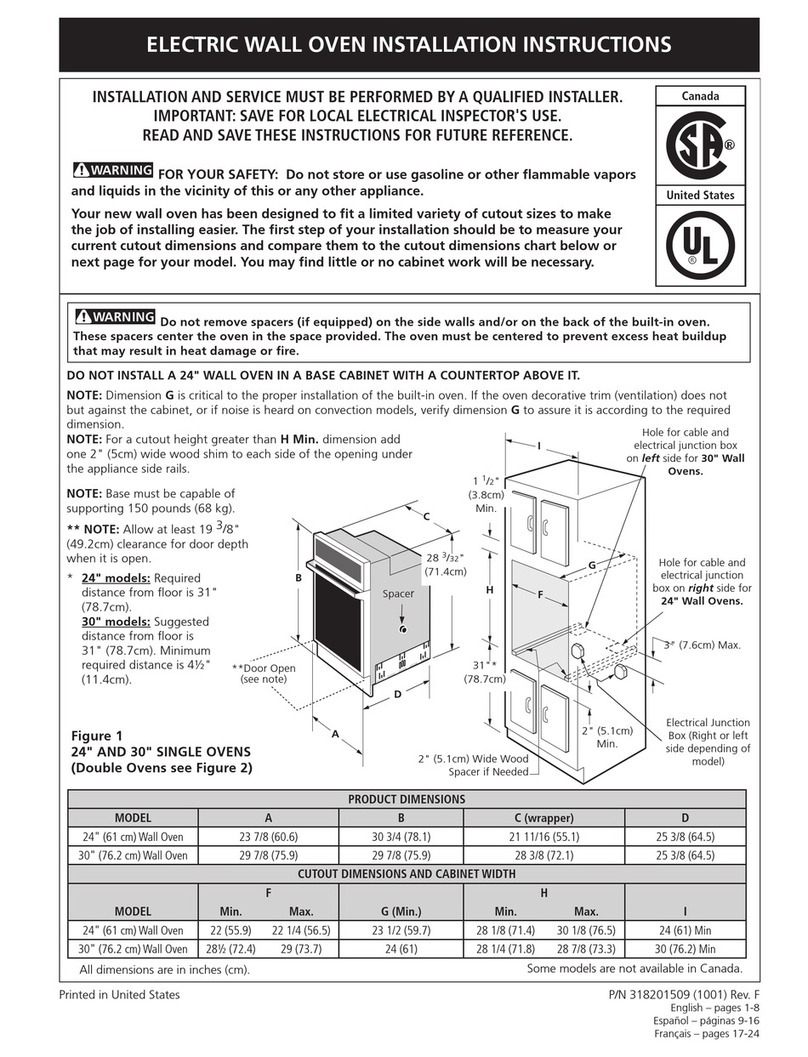
Frigidaire
Frigidaire FEB24S5AB installation instructions
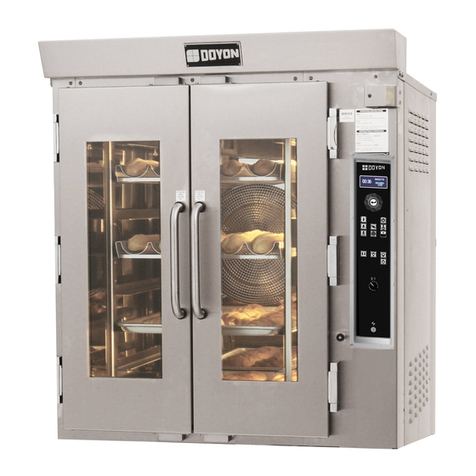
Doyon
Doyon JA8 manual